AIM: Check & solve all geometric errors, surface meshing with the given target length for half portion of the model and assign PIDs appropriately. Look for the perfect element Quality criteria by clearing off elements to zero and then performing a complete volume mesh. Surface & volume meshing of the wind tunnel.
PROCEDURE:
- Download the model and check the objective of the challenge properly. The geometry clearance with nice smooth curves of the model and mesh is perfect for both surface & volume with zero off elements in Quality criteria.
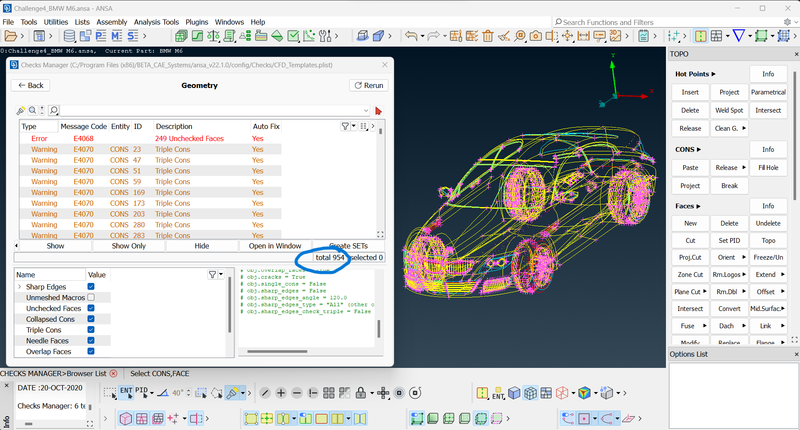
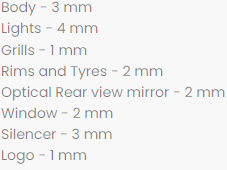
- The above picture is a part of the aim we have to proceed with for meshing a surface. From here we got data that we have to segregate entire in these eight different PIDs. So now will try to clean the geometry of the model and assign a new PID to each one accordingly.
- Apart from "Silencer", all other parts are having some or other geometry errors which need to clean before proceeding with mesh.
- Here we have a total of 954 errors with single cons, triple cons, mixed cons, needle face, distorted surfaces and overlapped surfaces. The grills, lights, logo, wheels, rearview mirror and body.
- Here we have a total of 954 errors with single cons, triple cons, mixed cons, needle face, distorted surfaces and overlapped surfaces. The grills, lights, logo, wheels, rearview mirror and body.
- Single cons - these are missing or deleted surfaces of a model where additional work is required. A freshly complete model looks to have plenty of single cons and the easiest way to deal with the same is to 'topo' model over 'face - dialogue box'.
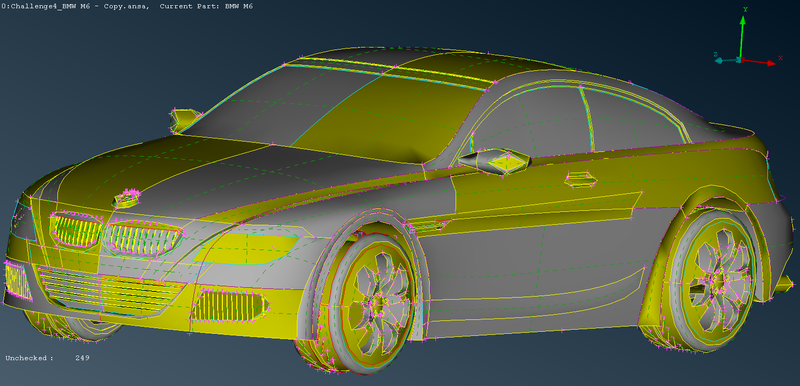
- The above image clearly depicts that the model is distorted badly, curves are even a bit smooth to perform any cleanup tool for clearing any geometric errors. But we will try to smooth out the distorted model.... this can be done by various methods. Here, we will use "Mesh - Length - Macros - .05". The parametrical length or target length to smooth out this model is been provided with a 0.05mm dimension. This will just help us to fit edges with perfect curvatures. The 1mm can also do almost the same work. But to process for this step my system can bear such pressure, so I moved to 0.05.
- In simple, such cases we have to first sort the "Resolution error". Initially, its value will be of high specified parametric length, which as per the complexity of the model & system capability we can refine to the finest.
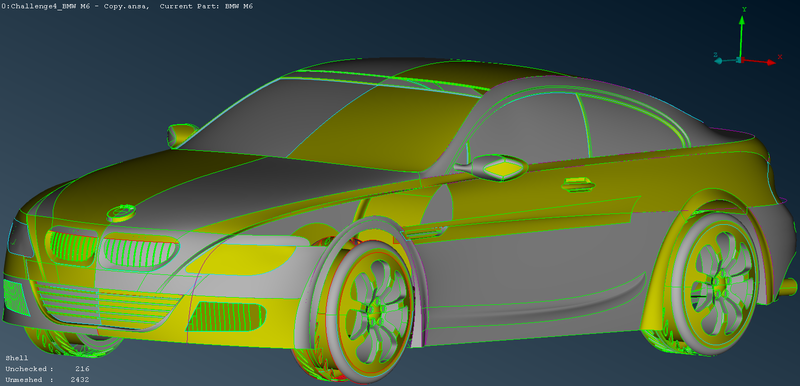
- After smoothing the surface we can see some faces on the right side of the model... puff. And by understanding a model we can say at many areas unspecified red cons have appeared.
- The complete model looks symmetric about an axis, and it also has huge errors. To complete this challenge (time-based) we will use only half of the vehicle at once to eliminate all geometric errors arising in the model.
- And then we do some quick cons refection testing by releasing & joining them "{Cons - Release} - {Face - Topo}".
- Initiating the hatch grids over the model makes it easy to select faces very small in size.
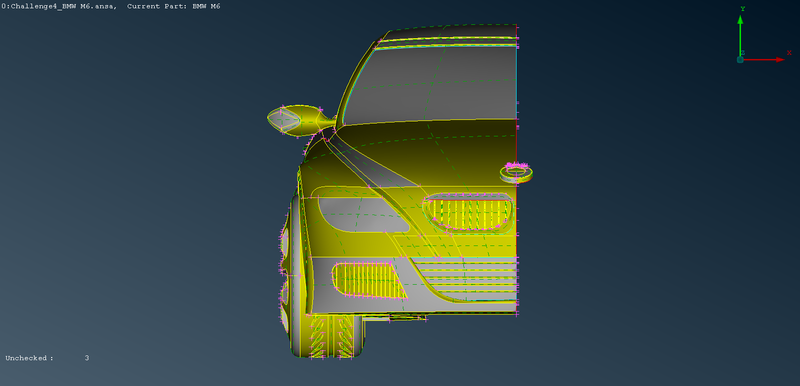
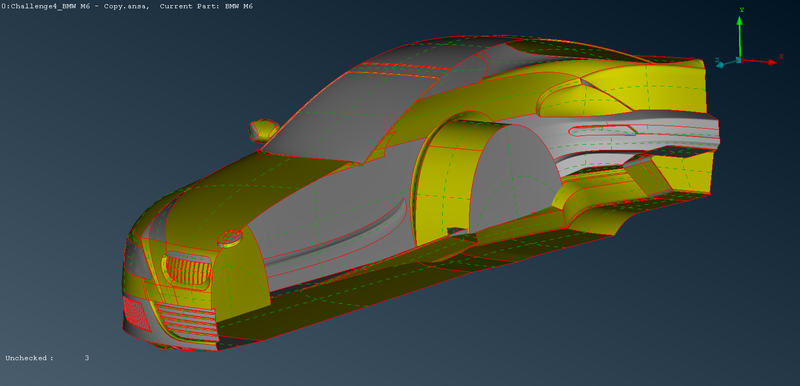
- This is where we 'release cons' to make a complete model browsed properly by software.
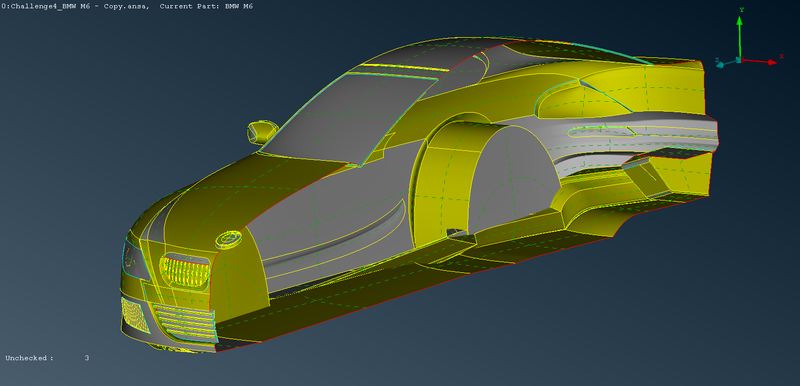
- From the above two images, we can clearly level out the things which are sorted. Also, we need to keep in mind while doing with logo, that alone part is not symmetric in nature. So, it needs to be withheld as it is for future processes.
- The below step is not required as a complete model needs verification of its elements. But I have made a geometry check here to have a proper understanding, of which all parts 'ANSA' need us to work on.
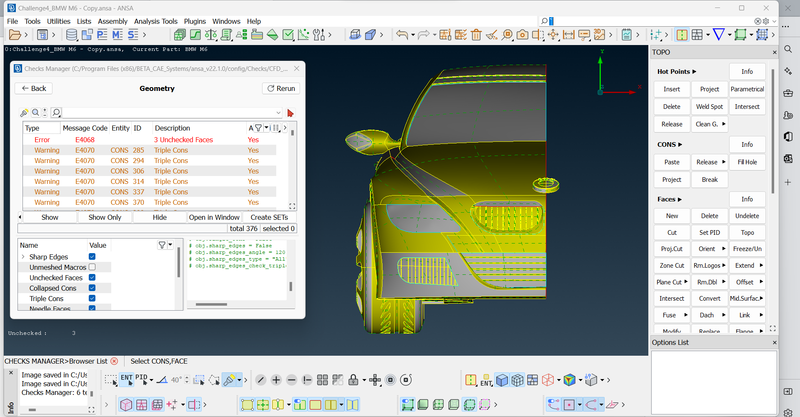
- By comparing the first figure and the above one, we get an overview of the total number of errors they have. Also, it relives our work towards solving geometrical errors while working on just half one. And copying the other side when a complete surface mesh is been completed.
- Here we will modify, delete and add various surfaces, I am here understanding the PIDs which are assigned by default by the user to the model already. So we can't mess up their properties while clearing geometry errors.
- In this model, we need to make the model mesh in a way to study it for External CFD of 'BMW' held within a 'wind tunnel'. For that, we have to eliminate all unnecessary inside surfaces & drafted items. And to study volume mesh we close all the inlet air flow areas.
- First, we will start with "Grills". We will isolate it in such a way that while editing other elements of different parts are not disturbed.
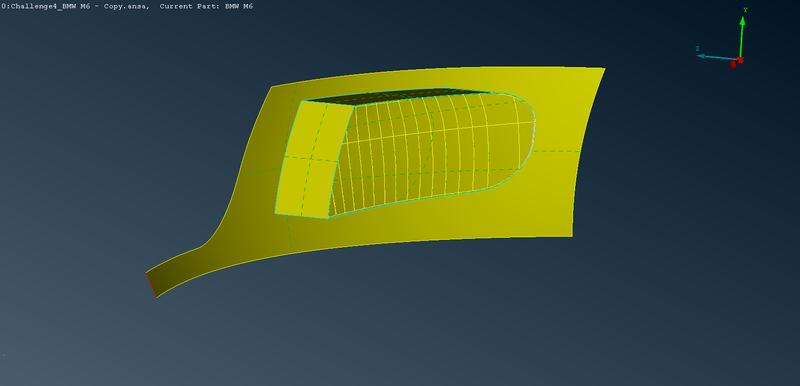
- The figure shows the extra grill is packed with extra volume and surfaces which are there to refine its design but we have to clean all such unnecessary elements. The side and back surfaces are overlapped ones, with the fins of the same also isolated properly. We will try to resolve these errors by deletion some surfaces and creating new ones with 'external flow' work as the main aim.
- To close grill fins and attain a single volume model, we will delete all extra surfaces. And to make this quickly escalate our way, we try to offset the grill's back surface '.02 par' (here 'par' divides the entire 1mm length to defined par value while '~' divide the curve as per scale value) inside and create a new surface. And required surface with an almost accurate volume model is achieved without altering the real one.
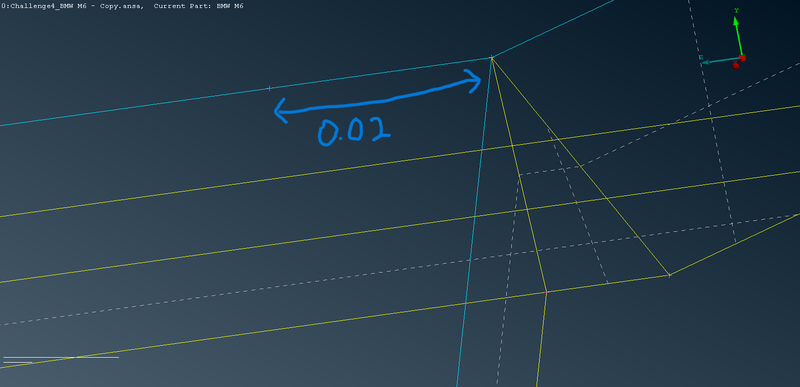
- In very small measured areas, I am applying measurements in very small values to avoid excess volume deletion to have a 'Perfect volume study'.
- By making cuts along these hot points and creating a new surface, we need to provide properties to such parts. This time we get an advantage of 'isolating a part', only this isolated part is highlighted which gets easier to allocate the properties to part.
- To create this geometry cleaned different tolls are been used like "Face - new/delete/cut/proj.-cut/intersect/topo", "Hot point - intersect/project/parametrical/delete/release", "Cons - paste/project/release".
- The fins adjustment is a complex part and among them, the most left side fines at curved faces are a little tricky part here. And just by adding faces with defined cons, we get this perfect required grill.
- Using various tools as a required catalogue once at a time. And we have the grills on. With the geometry check, we have cleared all geometry errors here.
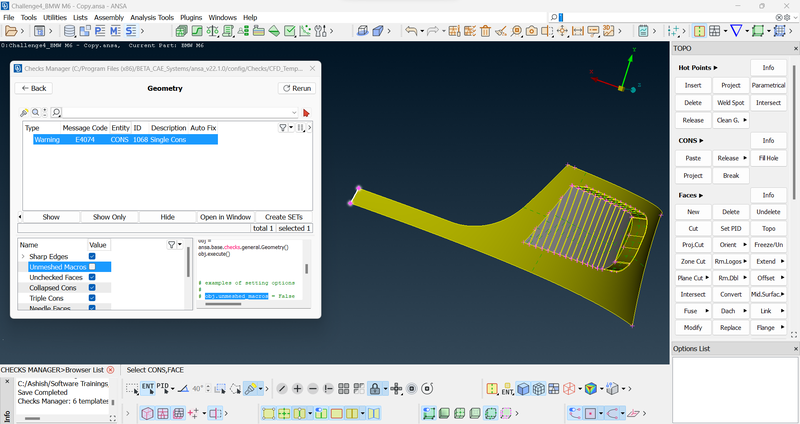
- In a similar way, "Grill 2" & "Grill 3" is also will be done.
- Grill 2 has a cutout as we can see, which is covered with different layers of unwanted surfaces. In this grill, this is a challenge. And to do this we will first delete the side faces of the cutout, and hide the backfaces whenever required to clearly understand what the model requires.
- The upper face of the cutout is attached to the back support face but most of the bottom one is free. To join them with a back face we use 'extend' to make perfect curvature cracks free.
- With this, the cutout is formed perfect but the other face of the cutout is covered with a foreign face which again needs to be sorted. And it's done by some projection of cons over foreign face and deletion of same.
- Now with some more cosmetic steps, we have achieved a perfect shape of the grill, this 'grill 2' is also completed.
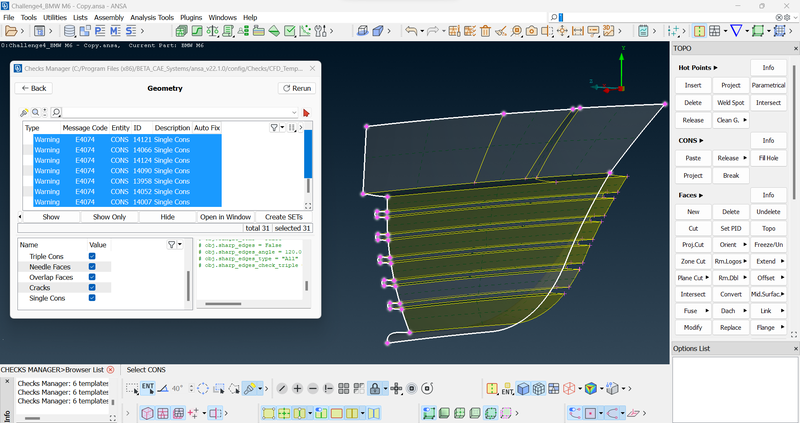
- The last grill, 'grill 3' work is started. This is the most complex grill among all three as this has some serious hardcore curves which require great attention to solve errors. The congested curve area grill is an awesome brain booster to work with.
- First, we will try to project that small flat surface con on top of the fin to cut those extra fins hidden behind. And from that reflected con we add more curves by 'project-cut' over face toolbox. This tool cuts the elements perpendicularly to any predefined cuts.
- Then we will focus on the congested curve area to make cuts over that tool also but in a very alert manner. A small mistake there will cost a meshing error which will be very bad.
- All these cut fins we can now join by creating faces in small patches. And to do so, first, we will project some hot points on the very opposite con. Then construct parametric cuts and create very fresh faces.
- By following this intense procedure we have accomplished this grill work.
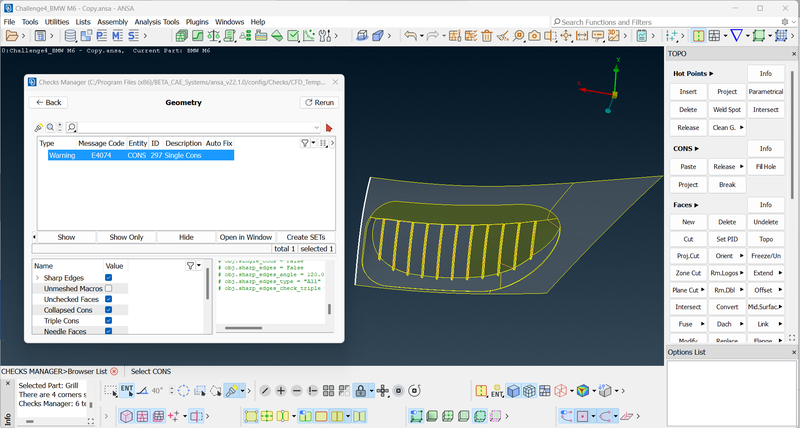
- Now as all three grills are geometrically error-free with highlighted red cons which are a half-cut portion of a model. We can assign a single PID to entire grills, to make work easy for sorting other model errors and meshing.
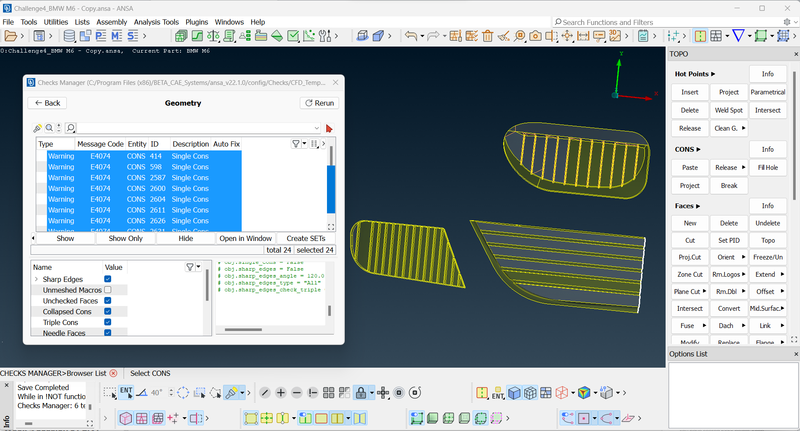
- Further to front headlights. The front face of the headlight seems perfect now we need to delete the inside items to remove extra volumes.
- Just some three joining faces are there which are depicted with 'triple cons' and playing with triple cons really fantastic approach.
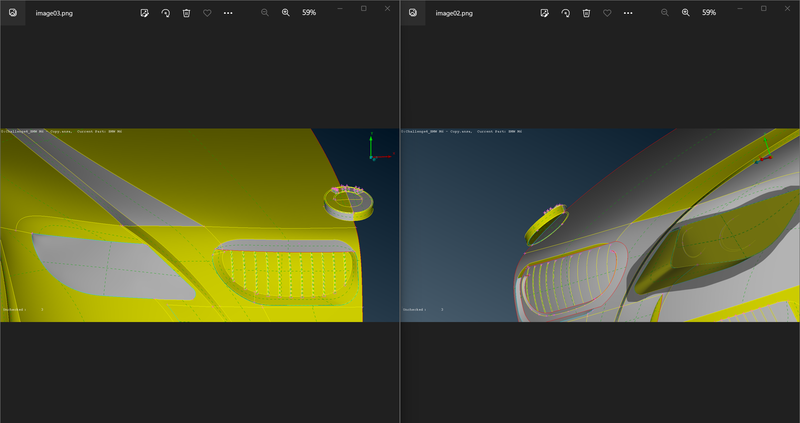
- The above figure shows that the front side headlight is perfect but the back highlighted part we have to clear out. And the rear light & indicator lamps are also much easier geometry cleanups in this project. We need to just make the correct selection of sub-parts before eliminating triple cons.
- Here just the deletion of surfaces is done and we get our required headlight, backlights and indicator lamps and different PID assigned.
- From the front side of a car, we have a "logo" a small item pending. With some error modification 'logo' is also been error-free with a separate PID assigned to it.
- On the logo's back side we have a few unwanted surfaces but before that, we isolate the front hood to work later. Then we will easily eliminate all these extra faces over back. And also the middle face cross have a glitch of the red con, which is cleared by joining these faces by a topo.
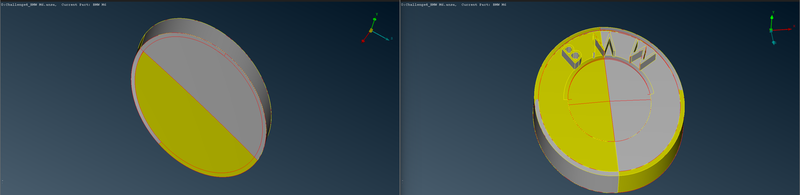
- The logo here is very extremely distorted edges with the letter initials "BMW", which is converted into perfect shape with cleanups.
- With this, we have achieved a perfect logo. Also, the geometry error is analysed and all single cons are highlighted, which are part of half model with an assigned PID.
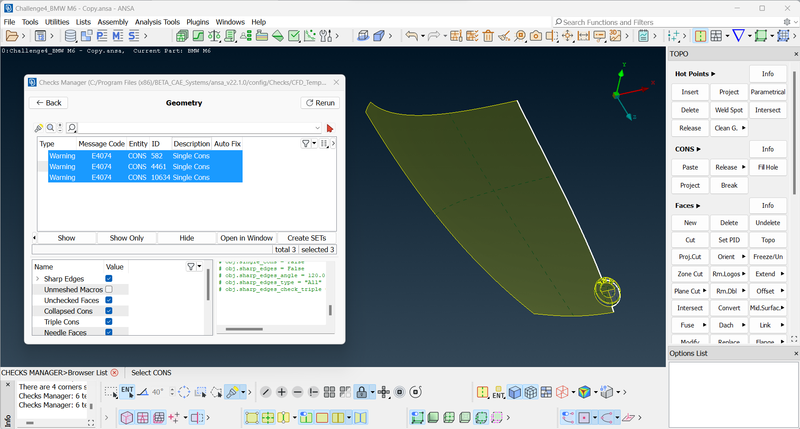

- Now is the time to play with the Rearview mirror. We can see here that the model is having various glitches along with triple cons and extra surfaces. We have to make some geometry clearance here too.
- The glass area is having some extra faces which we have deleted. And the locking position of complete rearview with body side glass is opaque initially but hollow from the internal area, which is extra volume addition. This extra volume creation is avoided by projecting the attached cons on glass and deleting the extra surface.

- All the geometry is cleaned with no error pop-up along with the newly assigned PID. Extra faces, overlapped surfaces and triple cons are eliminated.
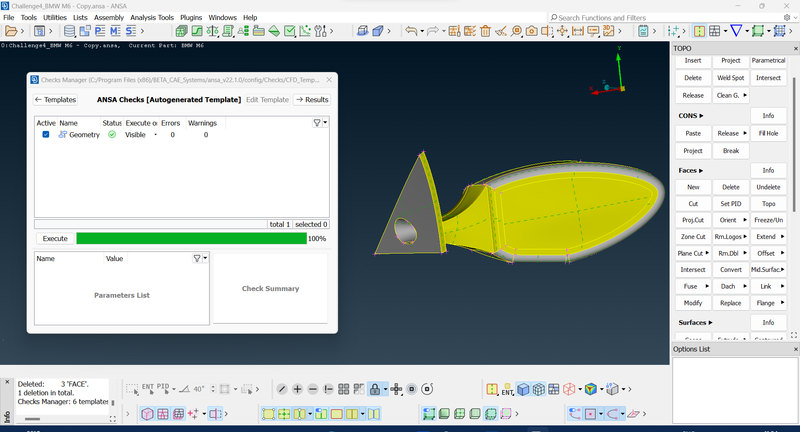
- Similarly here we will proceed in an exact way for the "wheels" which are aligned here with some triple cons and intersect with the floor liners. The elimination of floor liners is not an easy task which can be seen here. Many surfaces have been removed with a few new matches aligned too.
- The rims have some triple cons, which show that the object has some extra or overlapping surface. And the similar item is observed on the opposite face of the rim. These are removed by isolating the front face and deleting the unwanted surface by selecting only the non-required faces.
- These intersecting floor liners are a hell thing to work on. It has a twisted surface which is a puzzle but has been done by isolating, deletion, the addition of different surfaces. And while working on floor liner we have to make a notice of not much disturbance in the body.
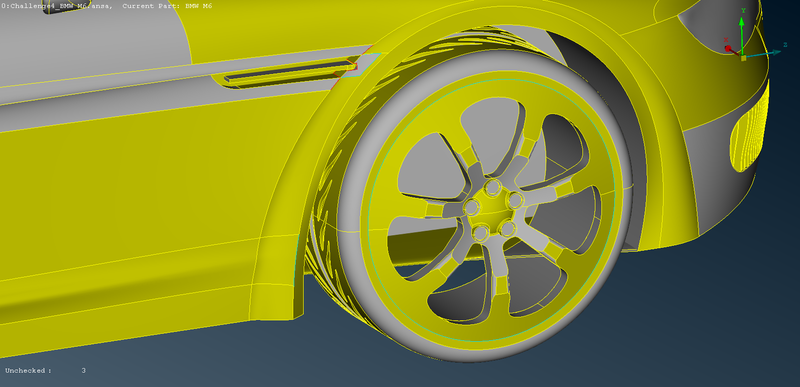
- With tons of hard work here for floor liners at last we have achieved a perfect wheel along with almost smooth arches for both front & rear position wheels also the wheels are shown free from the intersection with floor liners. Single PID is assigned to both sets of wheels.
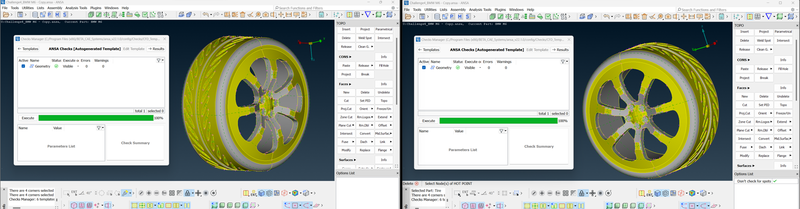
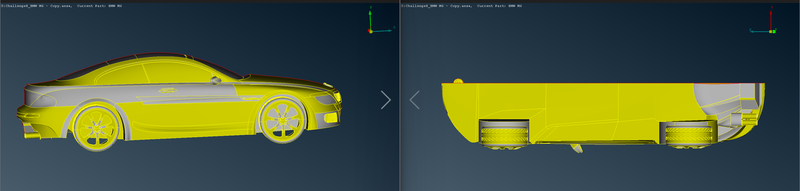
- In the name of child parts, we have an element on the list "Windows". No major cleanup is required here, just a few extra faces are been eliminated and a perfect geometry is obtained and PID assigned, one of the easiest parts to work on.
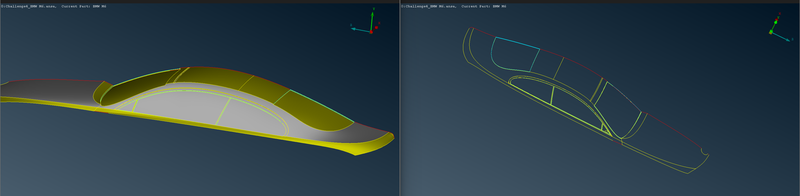
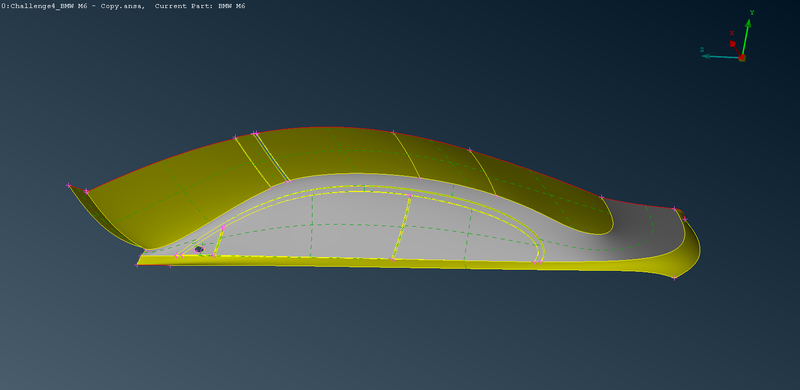
- As of now "all seven models are been identified & geometry cleanup work is done". We have just a major part, "Body" left off, which is having plenty of overlapped surfaces laid over the floor.
- The indented air intake foil, floors, grab handles, silencer, all these areas are the most complex and tricky elements over body geometry cleaning.
- First, we will proceed with the air intake indented manifold, which is have been integrated with the wheel arches to have it work we intersected the face of a small fin-like structure on the inner side to the middle plane and deleted unwanted objects. But work is not over yet, we have extended the inclined faces towards box-like features and the overlapped surfaces are also deleted, leaving a perfect shape of the air intake manifold.
- Second, comes the grab-handles which is having a convex con (one of the faces at the con is shaping a convex mirror). This con is eliminated by adding some cutting to the curved surface to break the curved nature of the handle.
- The silencer area is also forming a concave con which produces an unexpected error with the convex con over the indicator light casing. But the indicator light is fixed in a similar way to the handle being performed but here fragments of the workpiece are more. And concave nature model is lifted with a few cuts to segregate the entire surface in a few parts and the new face over there is also a challenging part as the face always tries to make a concave con only. To avoid this repetitious error we have used planar faces instead of cooned faces. It has been frustrating, it became a continuous error through the machine, and this has been eliminated with different trial-error dogged faces. In this area along silencer is also been completed.
- The time-taking process of geometry cleanup is altering 'floor liners'. It's been seen here that there is a number of overlapped and overlapped surfaces. And to achieve a perfect floor, isolating, lots-of deletion and creating new faces are just the only way to get the work done. So helping with errors over the floor will certainly be difficult but it's been purely synchronised to achieve perfect floor liners. With this work, we had satisfied the need of the body and the process of meshing must go on.
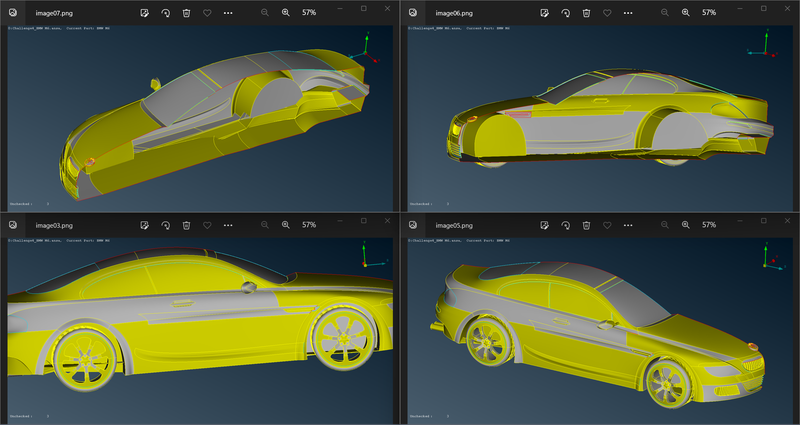
- The complete model is rectified and freed from errors along with the perfect floor. The handles & silencer area also seem to be fine. As the model is ruled out of errors, we can now assign it a new PID.
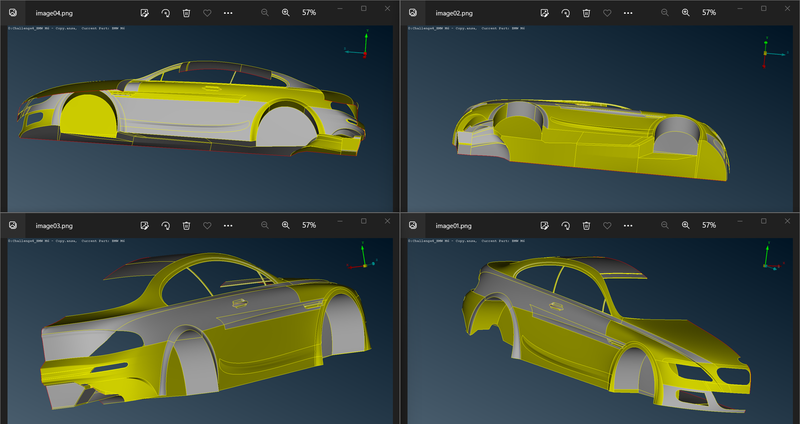
- With this the complete model is cleaned from geometry errors and also each sub-parts are assigned with dedicated PIDs by compressing all other unwanted or empty PIDs. Also in the below figure, we can clearly see highlighted portion of the model with red cons depicted as the cutout portion.

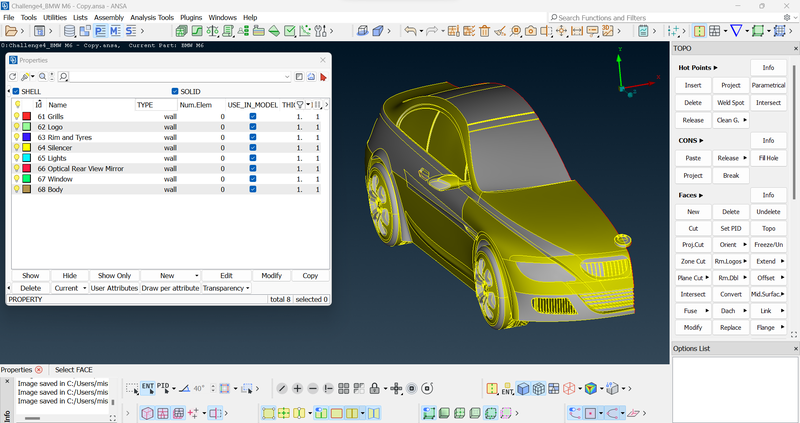
- Starting surface mesh.
- The most interesting portion of this challenge is about to start with meshing its surface. But this time we will just not make a normal meshing as were doing earlier, here we will define a few 'quality criteria' as the base input parameters for all individual PIDs. And this value is been assigned with some technical concepts in mind. The skewness is defined by triads with an average input value of 0.5 while the minimum & maximum heights are defined by acknowledging the model's smallest area and by considering the largest target length. And the 'mesh properties' will change for each PID as they have been assigned with different PIDs.
- In 'Quality criteria, we have assigned only skewness, min length & max length only.
- Here we can see that, the input values assigned are 'skewness - 0.5', 'min length - 0.2' & 'max length - 6'. With these input parameters, we have tried to create a universal 'quality criterion' for the different PIDs.
- The input values of the 'quality criterion' define the mesh element properties, and how the element will behave and perform for the meshed model. The skewness is a measure of the symmetry of the distribution of the mesh triad. In an asymmetrical distribution, a negative skew indicates that the tail on the left side is longer than on the right side (left-skewed), conversely, a positive skew indicates the tail on the right side is longer than on the left (right-skewed). The minimum & maximum length of a mesh element describes the high & low pitch of triads. If any element gets off these triads, an error will be highlighted with particular colours which need to be altered either by changing the geometry or moving the grids.
- The Mesh parameter for any of the individual models is assigned according to the required mesh criterion in CFD mesh.
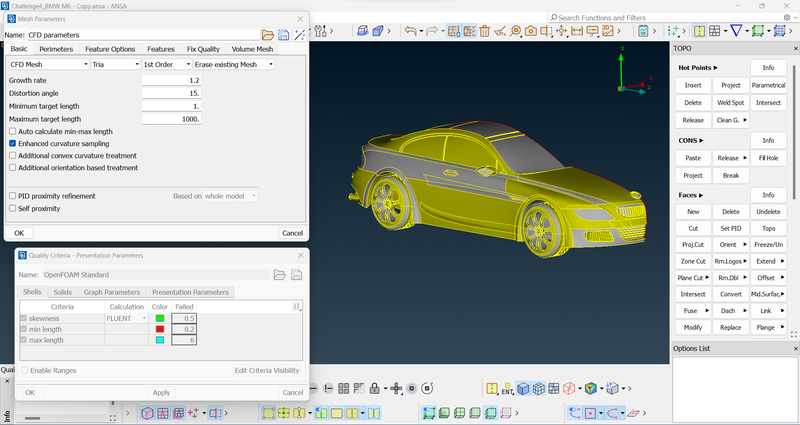
- Now we know the importance of Mesh parameters & Quality criteria. But in this project for each PID we will sustain a single input value of 'quality criterions' but the mesh properties will be different for different sub-parts. We are using pre-defined target lengths, so we will individually assign input values for minimum & maximum target lengths in CFD mesh properties but the range must be defined by analyzing the model.
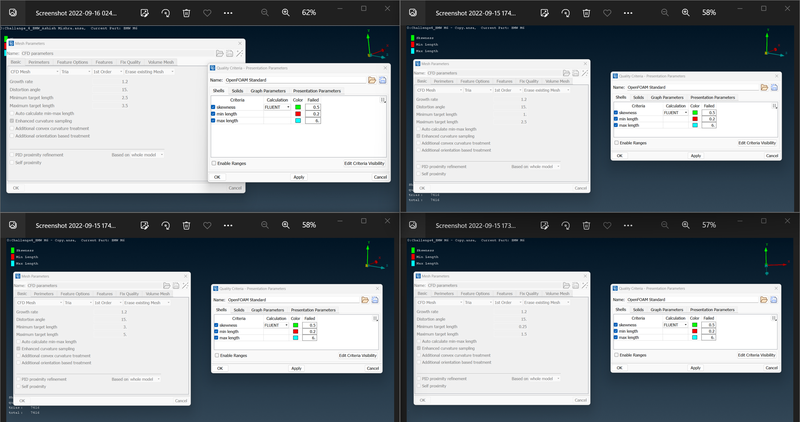
- All input parameters given are shown above, but we will implement the mesh parameter & apply type - CFD mesh. The reason to use CFD mesh instead of any other mesh type is as we are making this available for external body flow analysis. The study for flow externally is prefered to perform CFD mesh.
- When we create a mesh over a visible part it will initially it will highlight only meshed & unmeshed macros but when using 'hidden framework' instead of 'shadow', we will get the quality criteria shown over. And then the main work in the mesh will start, it will start showing off-items (off-items are triads which are overruled the limits of quality criteria). And those off elements can be improved automatically by using reconstruction, reshaping or other feasible features to improve the triad.
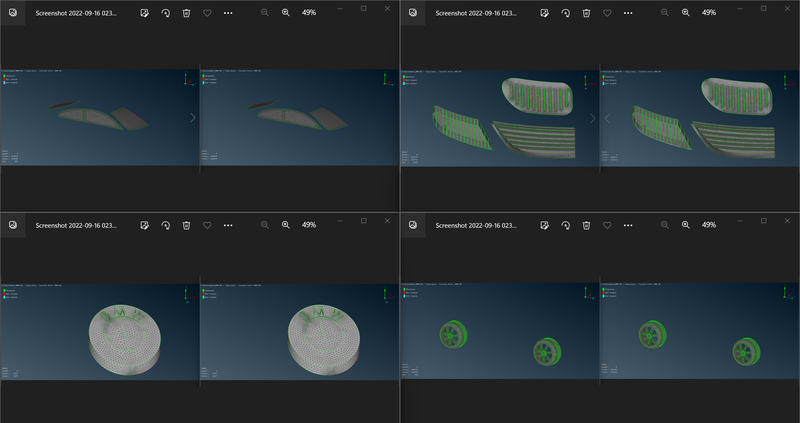

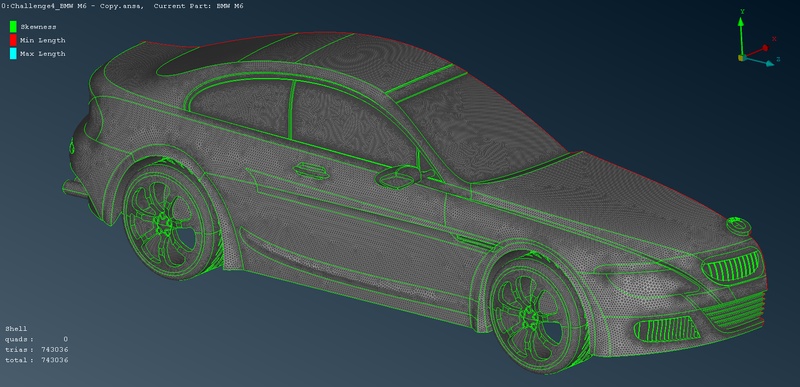
- We have obtained a perfectly meshed half body. But the main issue we have to take care of is that after meshing when we assemble parts some parts of the body may feel mesh oversize error & automatically one or more surfaces mesh will be deleted. To avoid such mistakes we will use the freeze/unfreeze option to sustain that item.
- Now we will copy the body to form a whole one, which is done by using 'transform - copy - entities - symmetry - mirror 3 point plane' and we will get the desired copy of a model.
- Now we will go for a geometry check and verify while copying any error popped or not. If yes, we will try to fix it by considering that the mesh also doesn't move off.
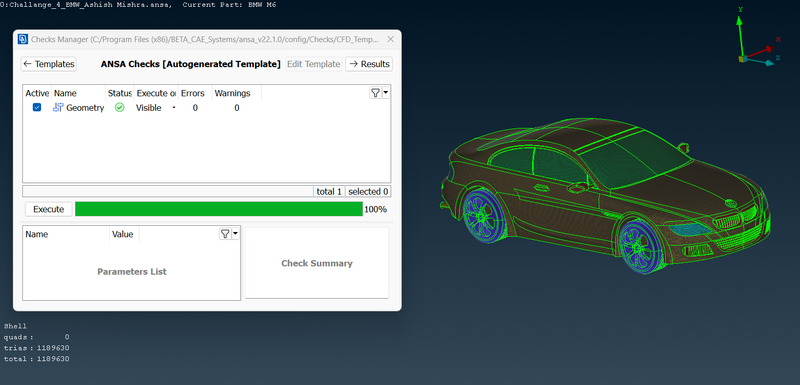
- Initiating Volume mesh.
- But before that, we need to make a wind tunnel to simulate a body over CFD - external flow analysis.
- First, we have to measure the length of a body (denoted as 'x') for calculating & creating the wind tunnel.
- The spec for wind tunnel is very easy. Dimensions for creating a wind tunnel are as follows:
- From front nose = 4 * x
- From rear-end = 6 * x
- From top end = 3 * x
- At sides = x
- All these dimensions are from the outermost edge of a model but we have taken a middle point of a model as a reference. Using that different points are been projected with the required dimensions for creating a base surface of the tunnel. Those points are created by 'topo - points - relative'. And to produce a line we sketch it using curve options and that curve is been connected with each other.
- Using this sketched bottom face, the top face is obtained by off-setting the surface to a specified distance.
- And then these reference points and curves are deleted. Continuing with side faces formed using a new face.
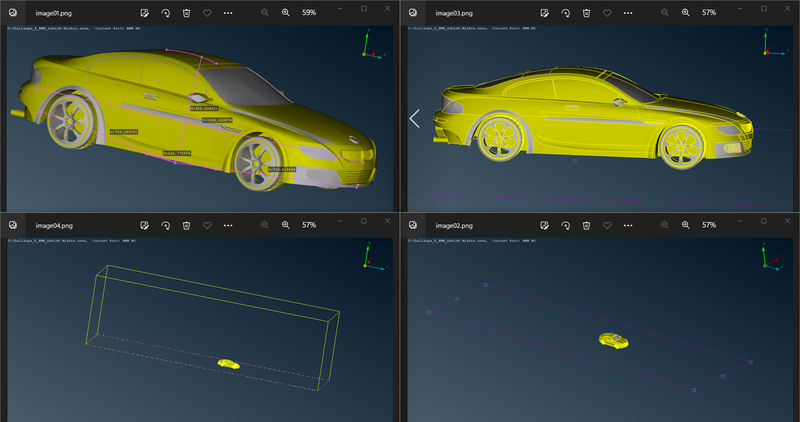
- As the tunnel is sketched perfectly. We will first check for any errors. Then will define a model under tetra volume mesh. But we can't go for a mesh here as the computing time to such a model will be too much.
- Now by defining a model we get 8 different lists assigned as different volumes. But in all these, we just need a single volume to encompass both tunnel & BMW cars.
- When we compress those unwanted volumes, the volumes of single obtained reflect their own PIDs as shown here.
- The work for the model is completed.

LEARNING OUTCOMES:
- Complex geometry cleanup
- Eliminating & creating overlapped surfaces
- Meshing model without altering other model mesh
- Extracting or copying body over a symmetric axis
- Exploration of various new tools
- Understanding spacing mesh parameter
RESULT:
The BMW model is been meshed (complete geometry cleanup, fully surface meshed and created a single volume of the body without meshing "meshing such complex structure will take lots of time & good system configuration") with the file attached in 'g-drive format' as the size of the file is large to be uploaded.
https://drive.google.com/file/d/1Wnmyo86j1-1l_DfRWjsYribtIeK5FFFj/view?usp=sharing
CONCLUSION:
Geometry cleanup, surface mesh & volume mesh (initial stage) has been completed. Comprehend various unique tools with a great extent of advancement. Different complex geometry cleanup helps to learn various techniques to solve errors.