AIM: To perform surface wrap meshing in an assembled model with the entire geometric cleanup.
PROCEDURE:
- The 'aim' of this challenge is to perform cleanup geometry for all three models individually & then assemble them and apply surface wrap mesh (target length = 3mm).
- Download all three models - Engine, Gearbox & Transmission.
- Then individually clean their geometries with no single or triple cons & overlapped surfaces. Always try to find appropriate deletion of surface, and solve red cons with coons or fill hole operations.
- As it's a surface wrap challenge, we have to take care of the outer surfaces mostly. Only for non-complex parts, we can proceed to clean geometry for those options.
- We have three different files, we will first proceed with Gearbox following Transmission & then to Engine (a complex one).

- For this challenge, we have three different models as we see, which need to assemble with an engine.
- Surface Wrap - A meshing of models surface only, that mesh model can be used for understanding & analysing effects over outermost peel of model (or in easy language - 'External flow simulation'). In almost all gadgets we are using in our daily life, the surface mesh really helps a lot to analyse effects over it.
- Let's start with Gearbox.
Gear Box:
- To have a controlled desired power output over wheels we have a gearbox.
- The initial model seems to have just a few red & blue cons, which puts it in a group of ultra-easy challenges.
- We have errors over gear knob screws, turning shaft area & support stand of transmission.
- There are 5 uncheck surfaces in this model, which shows the error is present over these 5 formed surfaces only. We have to eliminate all unwanted cons externally.

- We observe here that mostly triple joined surfaces (blue cons) are only present, and these are the rings used to form perfect fillets at edges. The rest are overlapping surfaces and omitted faces.
- By eliminating, adding & editing a few surfaces of the model externally, we have achieved a perfect outer model cleaning.
- Also in the cleaned model, we can observe that the supporting stand in having a triple con over one of its parts. This con is basically in the inner side of the body, which as a part of this challenge we can ignore.
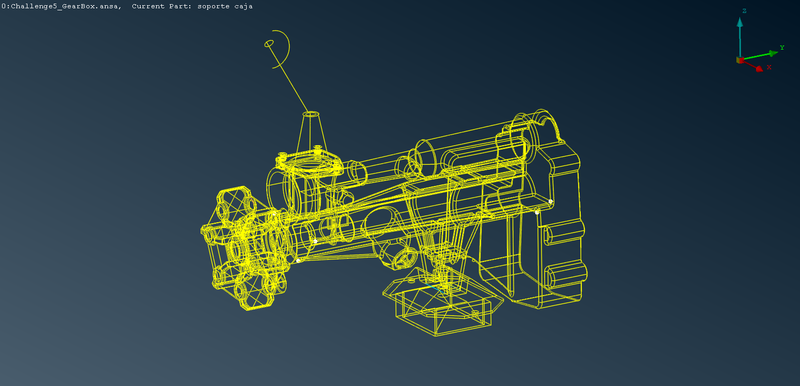
Transmission:
- This automotive component is used to transmit power from the engine to the gearbox.
- Here we have triple cons present in the clutch-coupling casing. And also in between the casing of the clutch & transmission box.
- In this model, we have '10 unchecked' faces. Basically, unchecked faces are those parts of the model which in shadow mode and not represented by any colour.
- In some areas, rings are used to form fillets while the other sort of triple cons is from three surfaces joined together. Over the bolt area in the transmission box, we have some overlapping surfaces. The coupling disc is having much of triple cons & few red cons.
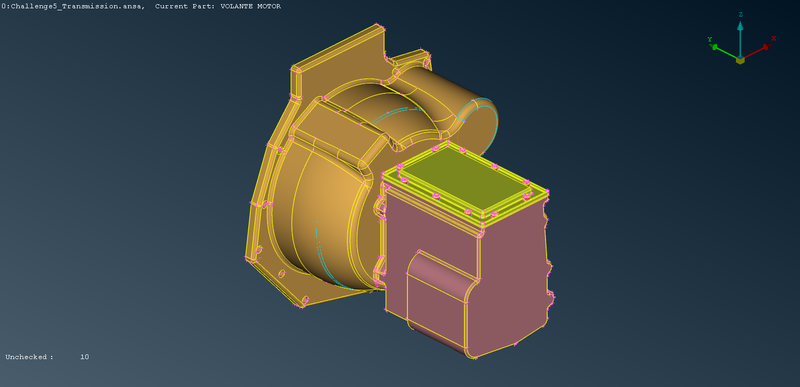
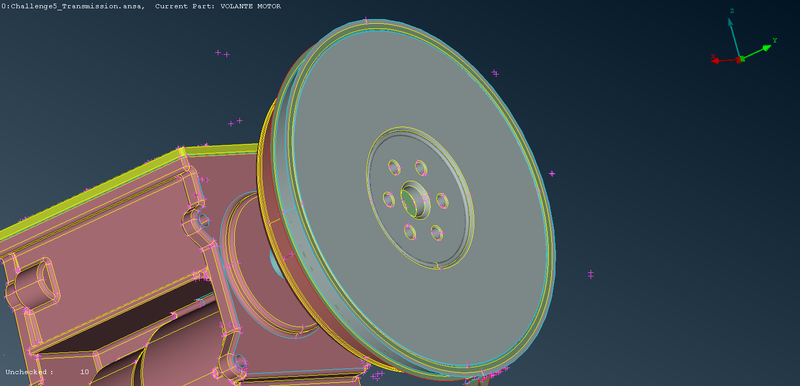
- As we have tried to clean up a geometry almost all from the outside, a few of the red & blue cons are hooked up internal of a body. With all elimination of overlapped surfaces.
- With this, the topological solution for both transmission & gearbox is been achieved.
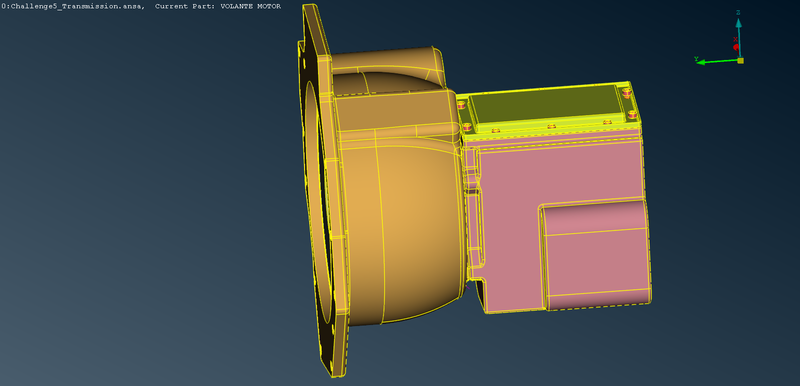
ENGINE:
- The heart of any vehicle is an engine, which receives input as fuel and produces power through it in form of turning of the shaft (rpm) by converting translation into rotation output.
- In this project, an engine is covered with bunches of undesirable parts all over the model, particularly in the form of rings which are fundamentally used to form fillets over edges.
- This model majorly needs a topo cleanup first by cleaning all the rings we have which are engraved all over parts, deletion of these parts in it is a sort of a challenge.
- We can see here that the balls, rings, washers, belts and all these items are not required for the surface wrap, step-by-step elimination starts.
- There are several ways to conquer a model of the engine only but here we are using the 'not' option in PID mode to hide all required items and delete unnecessary ones.
- It takes lots of complexity to clean all unnecessary parts and we have attained a model on which surface mesh can be performed.
- Initially, the model is full of red cons (describing that surfaces are not intact) but by using "TOPO" over a complete model, the whole scenario gets changed and we get the model mixed with both red & blue cons.

- The obtained geometry is having much of red cons as we can see in the figure below. At a first glance, these red cons appear to be a bit challenging task but before commenting, first, we need to perform topo to the whole model.
- Now the geometry seems to be pleasant and most of the red cons are converted into blue ones.
- And we know blue or triple con depicts the overlapping surfaces. To solve these cons problems, carefully deletion of surfaces takes place.
- All the pipe inlet grooves are packed with triple con which may be three different entities merging or those rings are present over there.
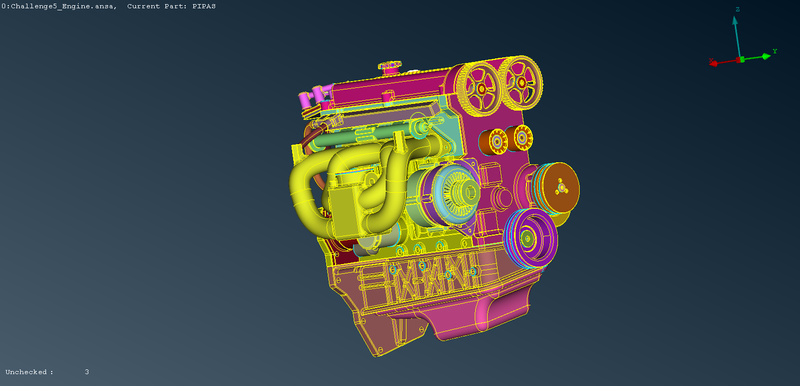
- From the three unchecked faces & geometry errors, we have achieved a better-looking model to proceed further.
- The model for an engine obtained is perfectly cleaned for geometric errors (complete externals & internals - required ones only).
ASSEMBLY:
- As all three model topo are cleaned for geometry errors external to a body, so we can proceed with assembling them in a sequence.
- The assembling is done by merging two models in one and that's been done by 'File - merge - file location' and after a few check boxes over dialogue, the pop-up needs attention. That the 'auto fit models (merge with current model)' & 'merge parts & MB containers (define whether incoming & existing MB can be merged)' are checked.
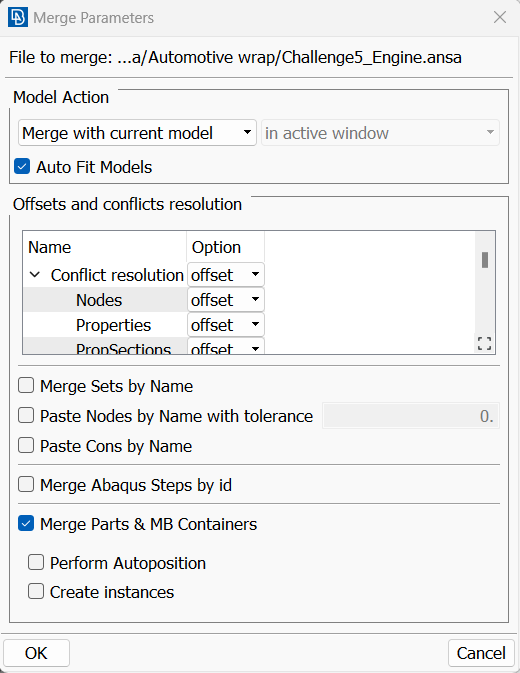
- And when we will proceed further with the right selection, we get the parts merged & a pop-up showing errors, warnings & messages of the merged body. We must take care that there not be a single error & warning reflected in the pop-up. If in case, something shows up we have to get rid of that error & warning, and then only we can proceed.
- Here as the assemblies were defined already, so we didn't have much work to perform and it easily attached the model perfectly on position.
- Before moving to surface wrap we have to close all the holes or open sides to even the surface flow for the complete assembly, so we don't get much extremely distorted wrap over the model.
SURFACE WRAP:
- A new mesh type in this entire challenge range. With the help of surface wrap, we mesh over the external peel only to a model making it available for external simulation & analysis.
- To mesh this model we use 'Octree - wrap - constant length'. But it's not the only method to perform surface wrap.
- There are two methods to perform the surface wrap - 'Octree - wrap', first, by using 'Classic mesh methodology and secondly, by 'Wrap mesh methodology'.
- To understand a brief difference between the constant & variable length of warp mesh, pictorial representation is shown below to highlight somewhat of the differences.
- This shows how for a particular model the constant mesh & variable mesh perform. It's not the correct position to tell which is the best fit for this model but is used on basis of the application of the model.
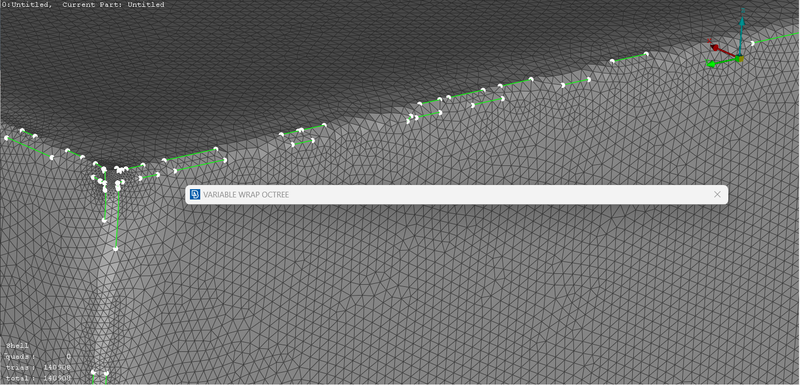
- At the constant length of wrap, we at the start need to define the 'CFD parameters' & 'contents' over Octree editing dialogue box.
- In CFD Parameter - we assign the name for the wrap and define the value of the target length.
- In Contents - we pick all the required PIDs (to carry mesh) and shift them to the selection box by clicking a green tick.
- After these procedures are over, we can directly hit "Run" and initiate the wrap mesh process until the wrap is complete & status (constant wrap dialogue) is changed from 'empty' to 'ready'.
- Now to improve the mesh elements we can provide the quality criteria (optional), here I have provided skew = 0.5, min length = 0.2mm & max length = 5.5mm, by considering the model thoroughly.
- After this, we achieved a perfect wrapped model with no off-elements.
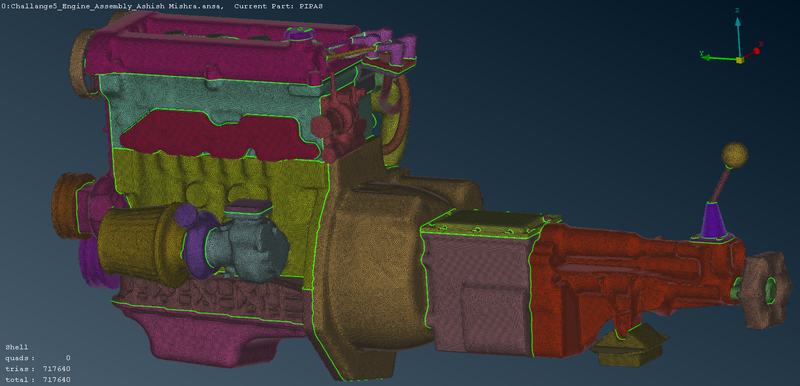
LEARNING OUTCOMES:
- Analysing a model for unwanted object deletion and picking up perfect parts required for meshing a model.
- A surface meshed model with an 'octree wrap' at a constant length of 3mm with little astonishing quality criteria.
- Quality criterion plays a skilful role to improve mesh quality & providing input values for quality is a task and that can be achieved by acknowledging the model for min & max mesh length a model can sustain.
RESULT:
The meshed model of an Automotive component is been attached below in a 'G-drive' link as the size of the model exceeds 100Mb. Also, the figure of the resulting model is attached both unmeshed & meshed.
https://drive.google.com/file/d/1F-cbgHBCk26KZDGYr5l0ixrDt55QKOr6/view?usp=sharing
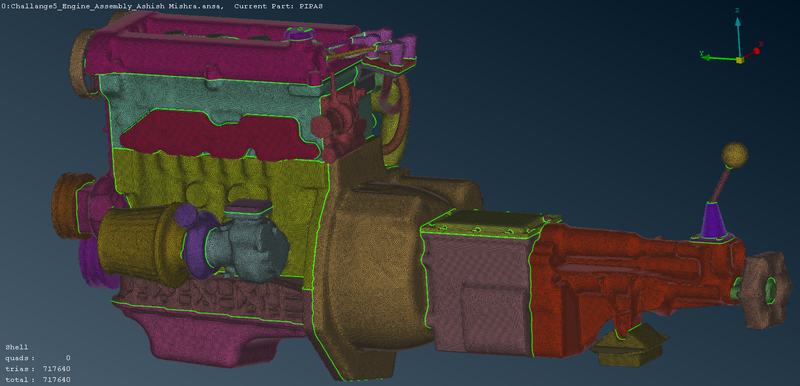
CONCLUSION:
Surface mesh for an assembled model (with almost perfect topological cleanups) is achieved with the target length of 3mm as per the rules of the challenge.