Project - TESLA (DUMMY) CYBERTRUCK VOLUME MESH
OBJECTIVE:
Check and solve all geometrical errors and assign appropriate PIDs. Perform meshing with the suitable target length and element quality criteria. Target lengths for the different parts of a model can be decided on your own. Meshing wind tunnel volume with tetra elements may take up to 2 days of time (so that is not compulsory to perform). As this is a major project, it is advisable to mesh that completely by taking some days of time. Write a detailed report for the same. Note: All the 2D elements (triads) in your model should clear the quality criteria (i.e. Off elements should be zero).
PROCEDURE:
HOW TO START THE WORK?
- First of all, we have to understand the objective of the challenge. And to access that step fig 1 & 2 will clearly show. Fig 1 helps to start the challenge with the reference to follow-up for the Project and the contents of the report with a particular deadline (which will award an extra 10% marks, if you score somewhat less). While fig 2, is a challenging objective, it clearly characterises all the important steps to be tracked to achieve an outstanding result (volume meshed cybertruck).
Fig.1
Fig.2
- In fig 2, we can observe a link to download the pre-designed model, where we will find a G-drive link to download a file for work, that file is already in '.ansa' format, so we don't need to make any extension changes over the model file. As CFD domain (ANSA) analysts, here for these challenges, we have to extract a drafted model (as in fig 3).
- After opening the model we will get the 'launcher' (fig 4) where we have to select 'Layouts - CFD' & 'arguments - ~performane_mode 3' (fig 5).
- 'Argument - ~performance_mode 3' is been used to levitate CPU & GPU memory usage.
Fig.3
Fig.4
- After opening the model, the command prompt redirects to the 'ANSA - Recent files' layout (fig 5).
- From there if our file is in recent folders, we can open it there itself else we have to search for a particular file location where the file is saved (fig 6).
- In 'file type' we can see all the formats ANSA support as a standard to open any file which includes .igs, .step, .3dxmi and etc. From fig 6 we get to know that this software (ANSA) can be used to mesh any model drafted in any of the other software like Solidworks, NX or others.
Fig.5
Fig.6
STARTING WITH CYBERTRUCK...
- After opening the model, the by-default view for the model is fig 7, while we recast the wireframe mode along with shadow mode (in layers dropdown), we get the model in fig 8.
- In fig 7, we can see all cons are reflected as red ones only. But that not seems to be correct, as any model cannot be depicted as a broken model (we say a broken model because red cons project that two or more surfaces are not joined together).
- Just by viewing fig 7 (wireframe mode), we cannot understand, 'how the model looks like?'.
- So, we have to enable the 'shadow mode' to view surfaces over the cons. And by analysing the model now, we can clearly say that the model is having surfaces stitched but maybe due software not being able to read the model properly it's highlighting all cons by red only.
- To overcome this error, we have to use the 'TOPO - Faces - Topo' command to make the software understand that the surfaces are stitched & GUI works properly to enable cons produced perfectly (figs 9 & 10).
Fig.7
Fig.8
Fig.9
Fig.10
- Now we have got the desired model to proceed further (fig 11), but this model is a complete set. On this, we cannot effectively work, as the whole body looks perfectly symmetric, so we can opt for 'plane cut - single' by choosing the middle hot points.
- By doing 'plane cut' the model is divided into two halves (fig 13). Now we can universally delete the half portion of the body (fig 14).
Fig.11
Fig.12
Fig.13
Fig.14
- Half-portion of the model was obtained, which we can proceed with for further procedures. In this model, after parting it symmetrically we perform a 'Topo' operation to stitch two surfaces (fig 16) if the software didn't analyse it.
Fig.15
Fig.16
- From step 1 till now, we have seen in all figures that the model is not smooth. So, to make the model smooth we will dedicate a 'macro' all over the model (fig 17) with an adequate target length to smoothen the curvatures.
- The function of macro over here is pretty easy, this 'macro' operation is used not to perimeters but only to surfaces, which handles the curvature smoothness.
Fig.17
Proceeding for Geometry Cleanup:-
- In this challenge, we do external CFD of the body, which ensures that the model gets ready for 'Wind Tunnel' analysis.
- The basic methodology to proceed with geometry cleanup is to move from the front end to the back end (or in reverse chronology). This procedure drives the behaviour of a model and allows the user to minimize the use of 'geometry check - utility.
- Starting from the front end, we get this extended flange, which creates extra volume for mesh & also it will create an intersection error which mirrors another half.
- From "fig 18 to 23" is the first set of cleanup at the front end of the light section.
- Figure 18 is the lower end of the light, which is enveloped by 5 faces, among them three were extremely small faces. Effectively selecting & eliminating the small faces is really a challenge.
- This figure is attached with a light engraved section, the section is highlighted with a very small edge over it which can't either be deleted or ignored. So to correct it, we create a very face & the geometry of figure 18 is cleaned.
- In a similar way for figures 19 to 21, we have proceeded. All 4 figures below are located in the cut-plane area.
- The fig 22 this small extra face is joining the L-shape surfaces. After deleting the fig 22 element, fig 23 is generated. And to correct this fig, we use the 'Paste' command to merge these two cons.
Fig.18
Fig.19
Fig.20
Fig.21
Fig.22
Fig.23
- Now, this complex item is to sort, this element is really a hell crack to me, it took about 75-80 minutes to solve and smooth the curvatures.
- Figure 24, is having a patched hole, that was easily filled with the 'fill hole' command & we get fig 25, but fig 26 gets me off.
- Fig 26 is a solved one, "forgot to take error geometry shot", we can see a perfectly straight line coming to the right side of the brown shade area. That part was having a convex con error.
- For instance, we can think easily to sort concave con but dealing with convex con is a bit of a challenge.
- To solve this convex con error, we cut the upper perpendicular face around 6 degrees, which helped to create a new negative inclined plane and solve that convex con.
Fig.24
Fig.25
Fig.26
- For the front end of cyber, we have cleaned the geometry, now it's the turn of inspection of geometry.
- After initiating the 'geometry check', we checked for the visible front side, and it reflected two mixed cons which we can see clearly in fig 27.
- To correct this mixed con, we delete the lower hood face and recreate it. But then also 'mixed con' error is reflected, so we cut off the perpendicular face by 8mm downwards and then a new face is created, which allowed a perfect curvature. And again going for 'geometry check', we left out only red cons, which are cut-plane edges (as we can see in fig 29).
- Now the question is.... what's the matter with fig 28...?
- This fig 28, if we observe carefully, we note that this inside punched face is lined out of the cut plane area (it's an extra part). And we cannot let it be aside, because later it will create an intersection error in the mirror and volume meshing.
- So, to omit this extra part, we project-cut a hot point near it all across the plane to con on another side. Now, this makes a cut on it and divides them for removing it. That is how we cut off the extra part & get a perfect-shaped front face.
Fig.27
Fig.28
Fig.29
- As we are over with all the errors on the light section area, now we will sort this bumper edge issue.
- It's really difficult to find any errors in fig 30, but we have a lot of intersecting bodies over there, also in one of the faces this notch running through (fig 31).
- As bodies are intersecting, we have a very initial step to start with, use 'face - intersect', to intersect bodies and make a con over running through surfaces.
- After the extra bodies are created by intersection, we can now delete them and patch new surfaces if any hole is formed. Also, this notch is cleared by making a cut from its top side to the end of the face and having a new face over it. Also the horizontal long face, after solving all necessary geometry errors, we get the mixed con on it. So, we made a cut on some other areas of the face & deleted & created a new one.
- With this, we also cleaned this bumper side error and got fig 32 as ready.
Fig.30
Fig.31
Fig.32
- Now the inner side of the footpeg & tyre liner has faces overlapped (fig 33 & 34). This is an easy task to solve.
- Easily those faces are deleted & patched with the fill hole command (fig 35).
Fig.33
Fig.34
Fig.35
- The below figures are inserted liner between doors & windows (fig 36 to 39). There is just a small error which is not highlighted in the geometry check but will create an error while meshing. The indented part surface is overlapping with the bottom side, so while meshing it will definitely highlight either min height error or skewness.
- So to rectify this error, we have deleted these surfaces & and created a new individual one, so no intersection or merging or height or skewness error occurs.
- This is how all these figures are corrected.
Fig.36
Fig.37
Fig.38
Fig.39
- Always there is one portion in any material or subject which is extremely easy, and this is one of those. Here we just have to fill this empty hole and that has been done by using 'fill-hole'.
Fig.40
- This error is highlighted in the geometry check utility, this error is of a sharp edge, and this sharp edge is present at the start of the rearview mirror side.
- To solve this convex con, we have to remove this pointed con & convert it to a straight one. And this we have done by cutting the mirror with the front glass parting line & projecting it in a perpendicular way to eliminate corners. Also, the body face gets a hole over it, so the entire face is been deleted & a new one was created to make smooth curvature.
Fig.41
Fig.42
- With this we have achieved a perfect body of the cyber truck as our meshing subject, by seeing the error content in 'geometry check' for single cons & the area highlighted along with it shows that the model is completely solved for geometry errors (fig 43 represents a perfect model).
Fig.43
- As the body is rectified, we have just one error in tyres, that is this empty hole (fig 44), which is easily filled with 'fill-hole' and with this, the wheel work is also completed.
- Now in geometry check, we can see lots of convex con errors popped, but this error can't be omitted, as these are part of the grip provided to tyres. So we have to ignore these errors and our tyre is also completed (fig 45).
Fig.44
Fig.45
Assigning PIDs-
- As the geometry error work is completely sorted, now the time has come to provide proper identification to various parts of the cyber and that is done by assigning PID.
- Fig 46 shows, we have both defaults & assigned PID but we only have to proceed with assigned PID as the default PID bulbs are also not glowing whereas the complete model is in the 'show stage'. That is generally because those PIDs are assigned to other ones & they became empty.
- And empty PID is not deleted normally, we have to use 'compress' to delete all unwanted empty ones.
- Also if we observe carefully we note that the lights & windows are having transparency but they are not completely transparent, the lights are dense while the windows are light.
- With this, the 'topological' work for the cyber truck is been completed with PID assigned properly.
Fig.46
Fig.47
SURFACE MESHING OF CYBERTRUCK
Note- All meshing done is unstructured mesh element.
- As the body is achieved a zero error in itself, now we can move to mesh this half body.
- But before meshing it, we have to define the 'Quality parameters' & 'Target length'.
- Quality Parameters - For this project, we will constrain a single parameter for the quality of the whole body. Also, only three parameters are defined for Cybertruck (i.e. skewness = 0.5, minimum length = 0.1 & maximum length = 6).
- For any target length, we will use these single-defined quality parameters only but the target lengths will be defined for them individually.
Fig.48
- Assigning target lengths to individual PID and trying to solve all the off-elements of meshed body.
- Also, we have to define a wind tunnel for this body, so we have to assign mesh in CFD mesh type only and target length for 'parameters' & 'macros' are assigned using the 'spacing tool' instead of using the normally 'length' option.
- Figures 49 to 62, define the meshing of each PID along with their target length, also the individual PID off-elements were cleared in themselves.
- Starting with "Tyre = 2mm", "Lights = 4mm", "Window & Hood= 2mm", "Body = 2mm".
- All the off-elements that happened in the entire meshing system were skewness. Because there were many places where edges were a little bit sharp but can't be reshaped, it will distort the model very badly.
- To clear off the off-elements, we have used the 'improve' command with 'reconstruct' & 'fix quality' features only for both the 'edges' & 'nodes'. And wherever the offs are not cleared (left to 5-10 elements), those are cleared manually by moving the grids.
Tyres (all off elements were rectified by 'improve -reconstruct')
Fig.49
Fig.50
Fig.51
Lights (only this single skew element was present after 'improve - reconstruct')
Fig.52
Fig.53
Fig.54
Window & Engine Hood (all off elements were corrected by 'improve - reconstruct & fix quality')
Fig.55
Fig.56
Fig.57
Body (after using 'improve - reconstruct & fix quality', here left off, off elements were skewed, and those were cleared by moving the grid)
Fig.58
Fig.59
Fig.60
Fig.61
Fig.62
- Every PID has meshed properly with zero-off elements (we can see that in fig 63).
Fig.63
Mirror of Body
- This is just a quick & easy step, in which the half model is copied symmetrically opposite to its cut plane.
- And this is done by using, 'transform - copy - symmetry - mirror 3 point plane'. And we define the 3 points about which we have to mirror it exactly (those points are extreme edge on red cons - fig 64).
- Then we get the single ready model with zero off-elements (fig 65).
- Also to ensure there is no intersection in the body, we perform a quick geometry check and apart from the convex con of the tyre no other errors are observed (fig 66).
Fig.64
Fig.65
Fig.66
MODELLING OF WIND TUNNEL
- Before starting the work for the 'wind tunnel' we have to find the length & width of the vehicle about which the tunnel will be created.
- The modelling of wind tunnel dimensions are as follows - front surface (4*length of the body from the extreme front end), the rear surface (6*length of the body from the rear end), side surfaces (1*width of the body from side extreme end), the top surface (3*height of the body from extreme hight of the body) & bottom surface (just below the tires with some clearance).
- To hold up these values, first, we create a hot-point locally at the centre of the vehicle and another point relative to it just below the wheels.
- By using the wheel below the point as a reference, we will create points on the front & rear sides at certain distances as calculated.
- Now, by using the bottom surface, we will offset it at a distance high.
- And by using free cons we will create side surfaces.
- With this, our wind tunnel is created.
Fig.67
Fig.68
Fig.69
Fig.70
Fig.71
The surface meshing of the Wind Tunnel
- In a similar way with no quality criteria to these, we will provide a target length of 50mm to the bottom face & 300mm to the top face, following the side an incremental rate of 1.2 from 50mm to 300m.
Fig.72
Fig.73
Fig.74
Fig.75
The volume meshing of the Wind Tunnel
- As surface meshing must be done before volume meshing & then we can define a body, and delete unwanted volumes.
- With the required volume we can proceed with unstructured meshing with the "Tetra CFD" type and with an elapsed time of 1 day 17 hrs, the mesh has been completed.
Fig.76
Fig.77
Fig.78
Fig.79
Fig.80
- But before performing meshing, a few quality checks need to be performed. The first one is 'Penetration - Intersection' and 'Volume - Duplicate', while to check the body for single & triple cons, we have used this elate procedure (Utilities - Isolate - Bounds - Single / Triple).
Fig.81
Fig.82
Fig.83
- Here we have provided a growth rate of 2mm, while with the initial model of 30mm base surface, this below error popped & dump files get created.
Fig.84
Fig.85
- This volume meshed body is obtained, but as the size of the model is around 7.5 Gb, so the off-elements of the volume meshed body were 11709 elements (fig 86), which were cleared by just a single command, 'improve - reconstruct - solids'.
- And the majority of off-elements were on the tyre grip portion (fig 87).
- With this, we have achieved a perfect volume meshed body (fig 88 & 89).
Fig.86
Fig.87
Fig.88
Fig.89
LEARNING OUTCOMES
- The surface meshing of complicated geometry & wind tunnel.
- Volume meshing of the cyber truck with the wind tunnel.
RESULT
The geometry cleaned body, the surface meshed body, the surface meshed wind tunnel & the volume meshed complete system, all are shown below in the pictorial form, which clearly shows that the challenge was accepted & completed with great output for volume mesh.
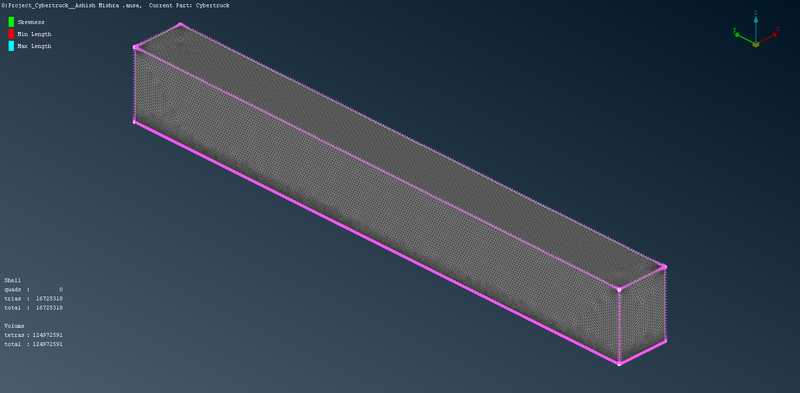
The link for the model (in g-drive) is below,
https://drive.google.com/file/d/1LbHVDbB30SK1r_ISO3utTblU1OVJZrql/view?usp=sharing
CONCLUSION
The geometry cleanup of the body is completed along with surface & volume meshing. With this project work, I have learned all the basic tools for meshing a body in Surface & Volume mesh and surface wrap.