DESIGNING, MODELLING, ASSEMBLY AND PHOTO-REALISTIC RENDERING OF AN AMERICAN CHOPPER:
- OBJECTIVE:
- Being a Design Engineer I would like to design a American Chopper from scratch to final render with the help of SOLIDWORKS.
- INTRODUCTION:
- Project report is about to designing of an American Chopper:
- Designing of the individual parts of the American Chopper with fully defined shetches and appearances.
- Assemble all the individual parts if the American Chopper by proper mates.
- Rendering the American Chopper by adding the decals, lights, camera and scenes.
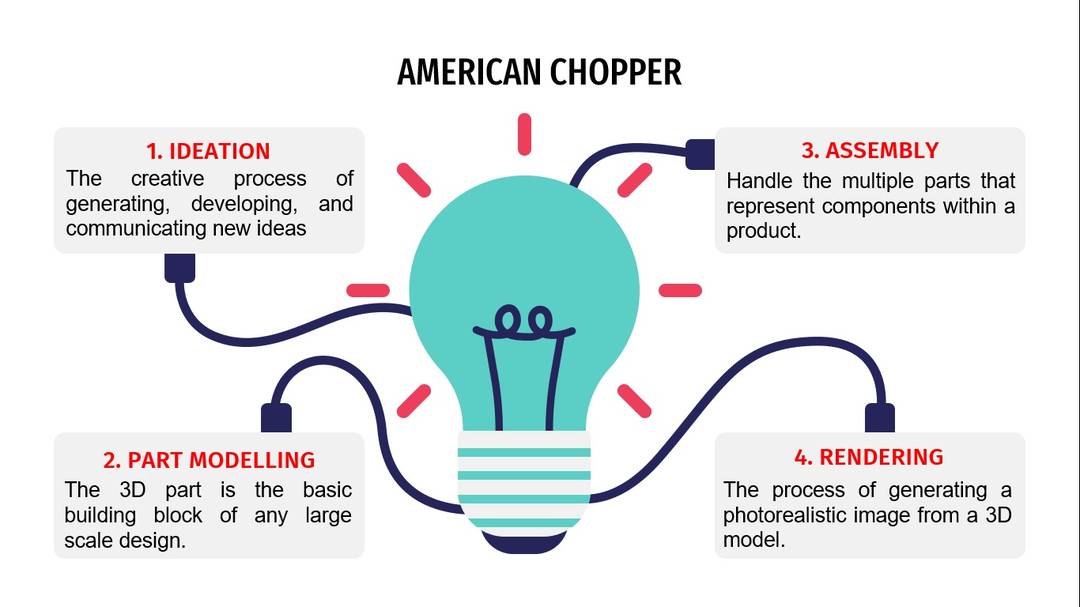
- DESCRIPTION:
- In this project I would like to describe how to create a part and assembly of an American Chopper.
- Software Used:
- Solidworks 2017
- Solidworks Visualize 2017.
- Parts of an American Chopper:
- Transmission Belt.
- Kick Stand.
- Front Fender.
- Rear Fender.
- Chain.
- Oil Tank.
- Pedal.
- Front Wheel.
- Rear Wheel.
- Front Fork.
- Chassis.
- Engine.
- Gas Tank.
- Commands Used:
- SKETCHING:
- Sketch
- Line
- Rectangle
- Circle
- Arc
- Spline
- Fillet
- Mirror
- Dynamic Mirror
- Sketch Picture
- Smart Dimension
- Offset Entities
- Convert Entities
- Intersection Curve
- Trim Entities
- Extend
- Linear Sketch Pattern
- Circular Sketch Pattern
- FEATURES:
- Extruded Boss: Extruded a sketch or selected sketch contours in one or two directions to create a solid feature.
- Revolved Boss: Revolves a sketch or selected sketch contours around an axis to create a solid feature.
- Swept Boss: Sweep a closed profile along an open or closed path to create a solid feature.
- Lofted Boss: Adds material between two or more profiles to create a solid feature.
- Extruded Cut: Cuts a solid model by extruding a sketched profile in one or two directions.
- Revolved Cut: Cut a solid model by revolving a sketched profile around an axis.
- Swept Cut: Cuts a solid model by sweeping a closed profile along an open or closed path.
- Fillet: Creates a rounded internal or external face along one or more edges in solid or surface feature.
- Chamfer: The chamfer tool creates a beveled feature on selected edges, faces, or a vertex.
- Shell: Removes material from a solid body to create a thin walled feature.
- Reference Geometry: It defines the shape or form of a surface or a solid.It includes items such as planes, axes, coordinate systems, and points. You can use reference geomentry in the creation of several kinds of features.
- Curves: You can create several types of 3D curves.
- Dome: Select one or more planar or non-planar faces you can apply domes to faces whose centroid lies outside the face this allows you to apply domes to irregularly shaped countours.
- Combine: It can manually combine the solid bodies.
- Split: It is able to split faces on multiple bodies.
- Pattern: Pattern repeats the selected features in an array based on a seed feature. You can create a linear pattern, a circular pattern, a curve driven pattern, a fill pattern, or use sketch points or table coordinates to create the pattern.
- Mirror: Mirror copies the selected features or all features, mirroring them about the selected plane or face.
- SURFACING:
- Surfaces are a type of geometry that can be used to create solid features. Surface tools are available on the Surfaces toolbar.
- Parts Modelled:
- Transmission Belt: Transmission Belt is used to drive a power from engine to gearbox.
- Features:
- Procedure:
- Sketch in front plane and gave fully defined sketch.
- Extruded a sketch and fillet is applied by selecting the edges.
- Matte rubber appearance is applied.
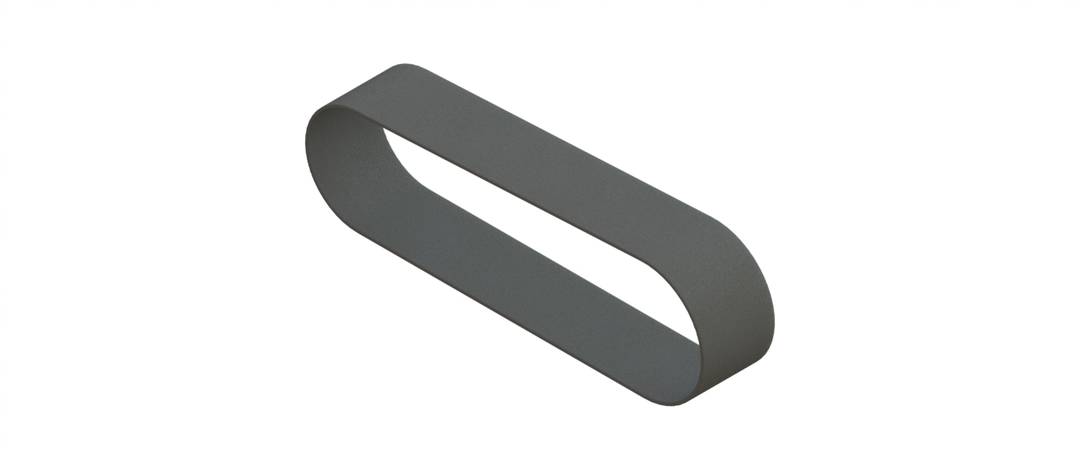
- Kick Stand: Kick Stand is used to support the chopper.
- Features:
- Loft
- Dome
- Cut-Extrude
- Split
- Boss-Extrude
- Fillet
- Procedure:
- Sketch Ellipse at Front plane.
- Sketch spline at midplane ensured the bottom spline handle is horizontal.
- Sketch a reference plane at the top end of the spline and ensured it is normal to it.
- Pierce relation is applied to the ellipse and spline.
- Apply loft boss base and adjusted green dots to snap at vertex of the ellipse and guided to follow the centerline spline.
- Apply domes at the respective faces of an ellipse.
- Cutout at the larger end of part by sketching rectangle at mid plane Give extrude cut and apply through all both option.
- Create mid point line at smaller end of the part and split the bottom face to make the part flat face.
- Sketched circle at top plane to create pivot point extrude the sketch to the surface and apply fillet.
- Chromium Plate appearance is applied.
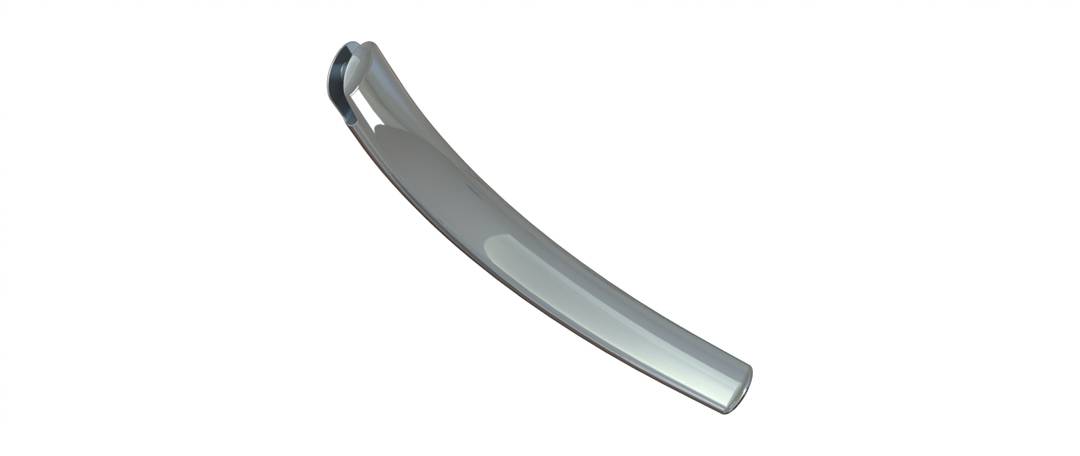
- Front Fender: Its primary purpose is to prevent sand, mud, rocks, liquids, and other road side from being thrown into the air by the rotating tire. And it is mounted above the Front Wheel.
- Features:
- Procedure:
- Create a three point arc and apply relations. Offset the entity to inside and enclose the edges of the arc using extend entities and power trim.
- Draw a reference sketch for axis of revolution, and give revolve extrude Using direction 1 and 2 option to make relevant sketch.
- Sketch spline using dynamic mirror entities at the front edge of the fender.
- Split tool is to cut the parts and followed same procedure for bottom edge.
- Apply fillet at the edges of fender.
- Siena appearance is applied.
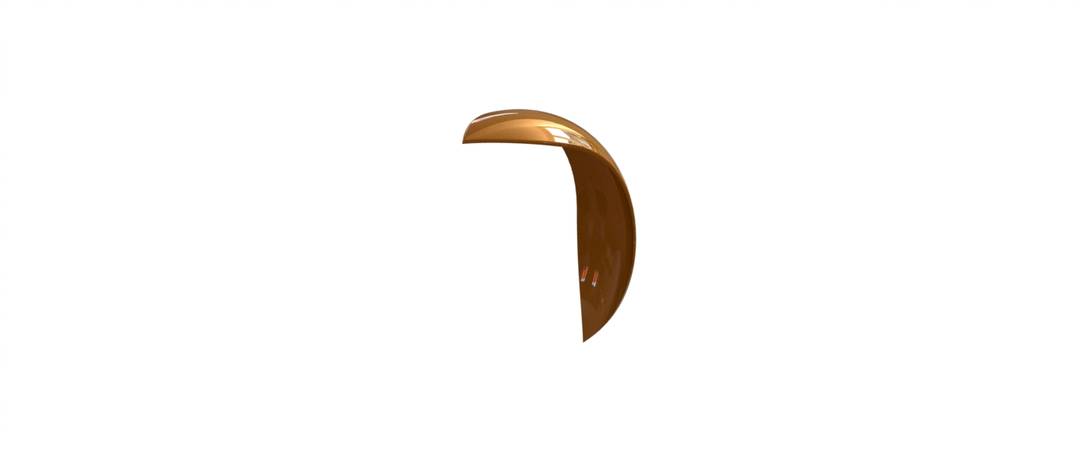
- Rear Fender: The use of Rear Fender is same as the Front Fender. It is mounted above the Rear Wheel.
- Features:
- Revolve
- Split
- Fillet
- Shell
- Procedure:
- Create a three point arc and apply relations. Offset the entity to inside and enclose the edges of the arc using extend entities and power trim.
- Draw a reference sketch for axis of revolution, and give revolve extrude Using direction 1 and 2 option to make relevant sketch.
- Sketch arc at the front edge of the fender.
- Split tool is to cut the parts and followed same procedure for bottom edge.
- Apply fillet at the edges of fender.
- Siena appearance is applied.
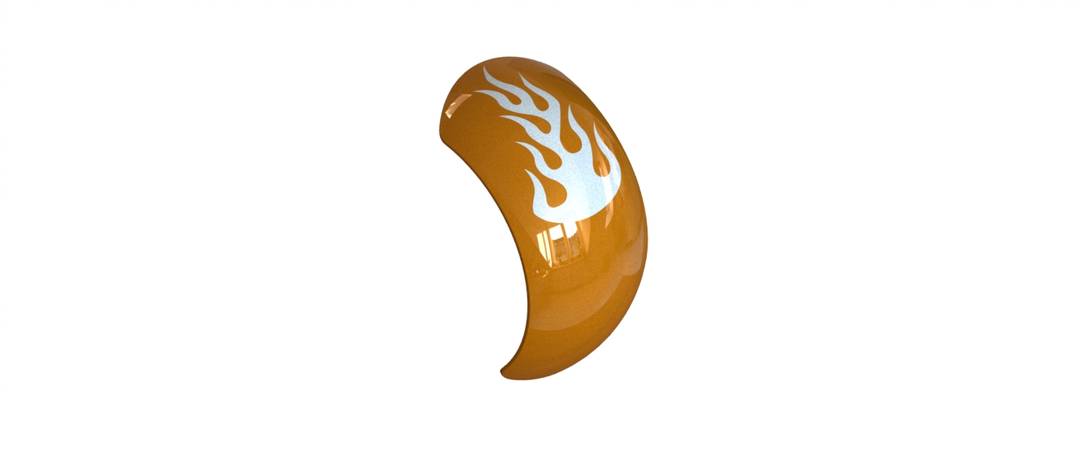
- Chain: Transfers the Power from the Engine to the drive wheel of a bike, thus propelling it.
- Features:
- Boss-Extrude
- Fillet
- Curve Driven Pattern
- Mirror
- Procedure:
- A runaway sketch is created at the midplane and the is used to save as separate blocks a chain 1 and 2.
- The blocks are inserted on to the 2D sketch created on the midplane and applied certain relations to make coincident with the curve The blocks are then extruded and fillets are applied at the faces of the pin.
- Curve driven pattern is applied along the curve and some extrudes are drawn manually to perfectly align with the chain path Later the solidbodies are classified into chain, plates and pin in separate folders and the chain plates are mirrored using mirror entity.
- Steel appearance is applied.
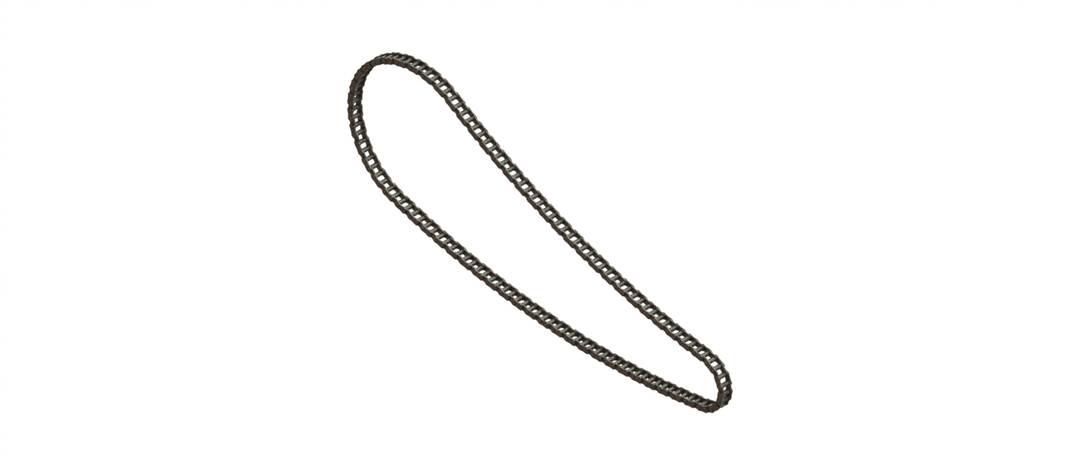
- Oil Tank: It is used to store the oil required to run the Engine.
- Features:
- Boss-Extrude
- Combine
- Fillet
- Shell
- Procedure:
- A sketch is created and then extruded on both directions.
- A new sketch is created and extruded through all both the directions.
- Combine feature is used to common both the extrudes.
- Fillets are applied at the edges and Shell feature is applied with thickness.
- Siena appearance is applied and white color is applied on the fillet faces.
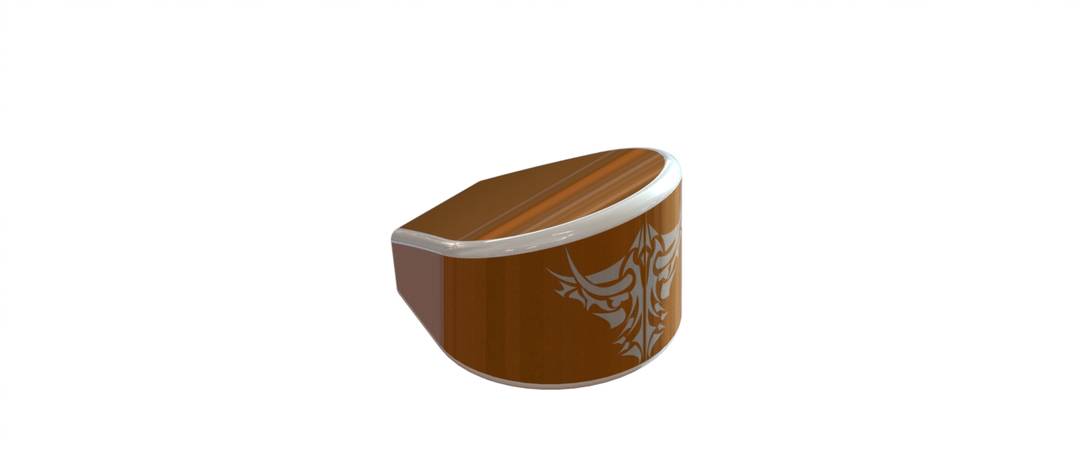
- Pedal: It is used to place the leg and attached in the Chassis. To give comfort to the rider.
- Features:
- Boss-Extrude
- Revolve
- Dome
- Chamfer
- Linear Pattern
- Fillet
- Procedure:
- 2D sketch is extruded and a new sketch is created and Revolve Boss feature is applied.
- Dome is applied at the end face of the revolved part and chamfer is applied to the other two parts.
- Create a new extrude on the two part and Linear pattern is applied to four instances.
- Ensure all the edges are applied with necessary fillet.
- Chromium Plate appearance is applied.
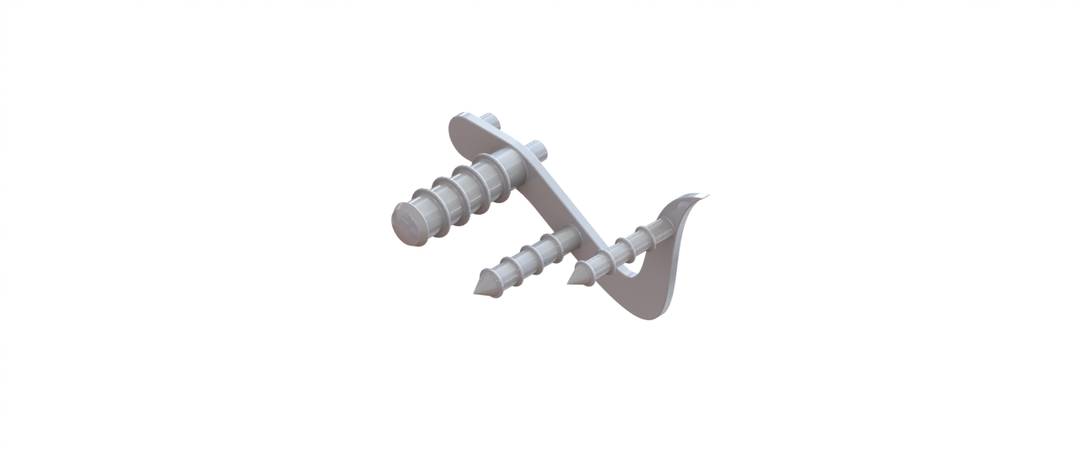
- Front Wheel: The model is the combinition of different solid bodies like Rim, Rotor, Caliper and Tyre.
- Features:
- Revolve
- Boss-Extrude
- Cut-Extrude
- Cut-Revolve
- Circular Pattern
- Fillet
- Chamfer
- Combine
- Procedure:
- Solid bodies are designed namely Rim, Rotor, Caliper, Tyre.
- Rim is developed using Revolve and circular pattern is applied to make spider web shaped rim wheel.
- Chromium Plate appearance is applied for Rim.
- Rotor is Designed and necessary pattern is sketched.
- Carbon Steel appearance is applied for Rotor.
- Caliper is designed on the rotor by applying necessary Chamfer features.
- Siena appearance is applied for Caliper.
- Tyre is designed above the Rim by applying cut extrude pattern.
- Matte Rubber appearance is applied for Tyre.
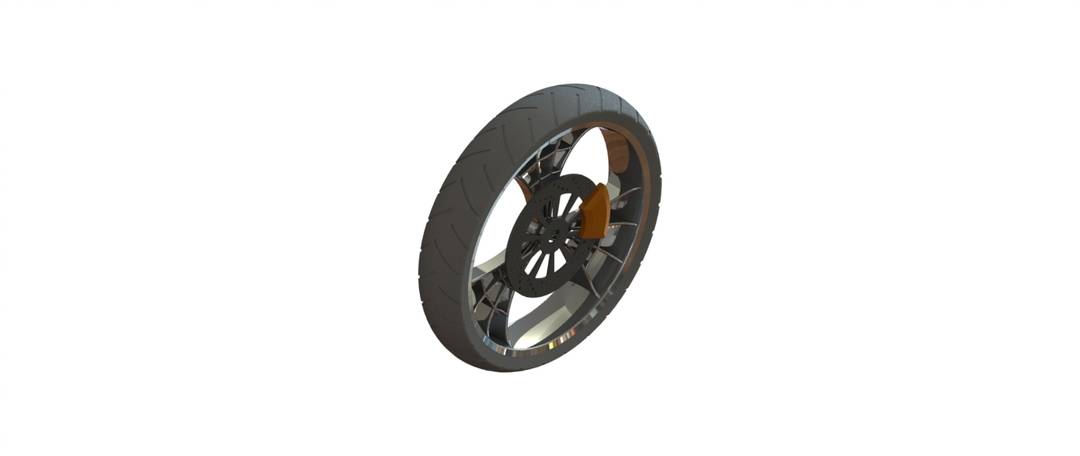
- Rear Wheel: The model is the combinition of different solid bodies like Rim,Sprocket, Rotor, Caliper and Tyre.
- Rear Wheel is designed as the same as by the Front Wheel.
- Sprocket is sketched over the the rim for chain assembly.
- Chromium Plate appearance is applied for Sprocket.
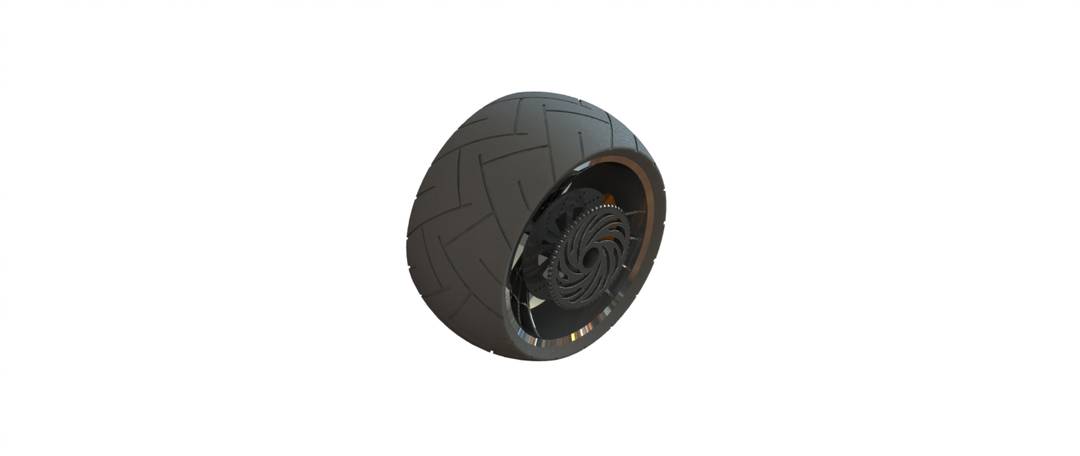
- Front Fork: connects a front wheel and axle to its Chassis, typically via a yoke, also known as a triple clamp, which consists of an upper yoke joined to a lower yoke via a steering stem, a shaft that runs through the steering head, creating the steering axis.
- Features:
- Revolve
- Boss-Extrude
- Cut-Extrude
- Dome
- Cut Revolve
- Sweep
- Fillet
- Mirror
- Combine
- Procedure:
- Front Axle frame, Handbar, Headlight are designed.
- This model is done by creating mirror fetaures by sketching one half.
- Front Axle frame is designed by applying exrtude revolve and cut solid bodies.
- The handle bar frame is designed with projected curve feature to sketch. And sweep is based on the circle and the projected curve
- The headlight model is designed and dome, chamfer features applied.
- Finally the model is mirrored and necassary appearnace are given to different parts.
- Visual Propagation is checked to apply the appearances on both sides.
- Chromium Plate appearance is applied for Axle Frame
- Matte Rubber appearance is applied for Handbar.
- Area Light is applied for Headlight.
- Luminous intensity is applied to the head light model for effective display when doing rendering.
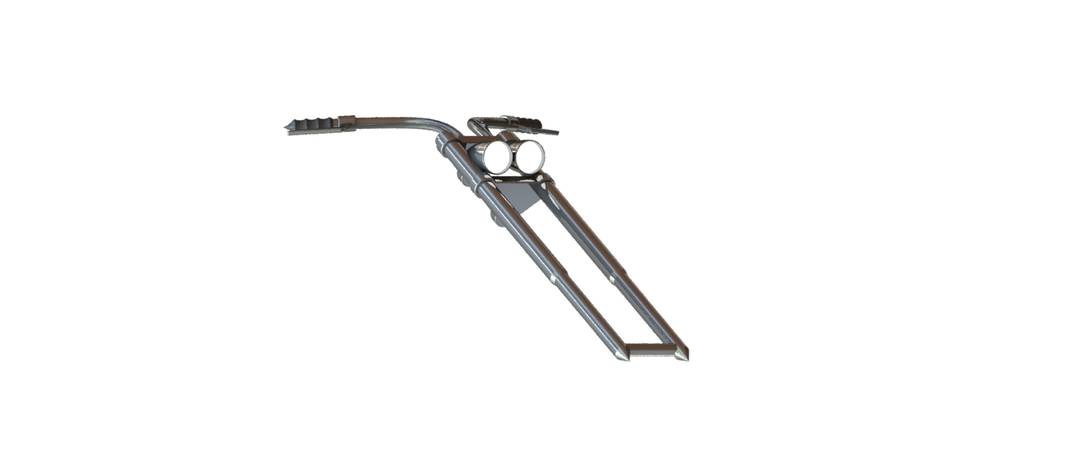
- Chassis: All the components of a motorcycle, like the suspension, wheels, fuel tank, seats, handlebars etc, are attached to this base structure which lends a motorcycle its strength and ability to handle well.
- Features:
- Sweep
- Boss-Extrude
- Dome
- Revolve
- Mirror
- Split
- Chamfer
- Fillet
- Mirror
- Combine
- Procedure:
- Insert Blueprint of chopper in the front plane ,adjust the location, transparency and sketch on it.
- Draw two concentric circles with an offset.
- Draw a horizontal & vertical line from origin. Then a spline connects the circle center and tangent to the horizontal line and gets a projected sketch.
- Sketch on Top Plane, draw a horizontal line parallel to the line and draw on the front plane connected with the spline to make it fully defined.
- Next Sketch on Right plane, draw a spline from top to bottom with relation to origin and make it fully defined.
- Remove the unwanted area using cut extrude, Mirror the bodies and combine.
- Fillets are applied at the edges
- Siena appearance is applied.
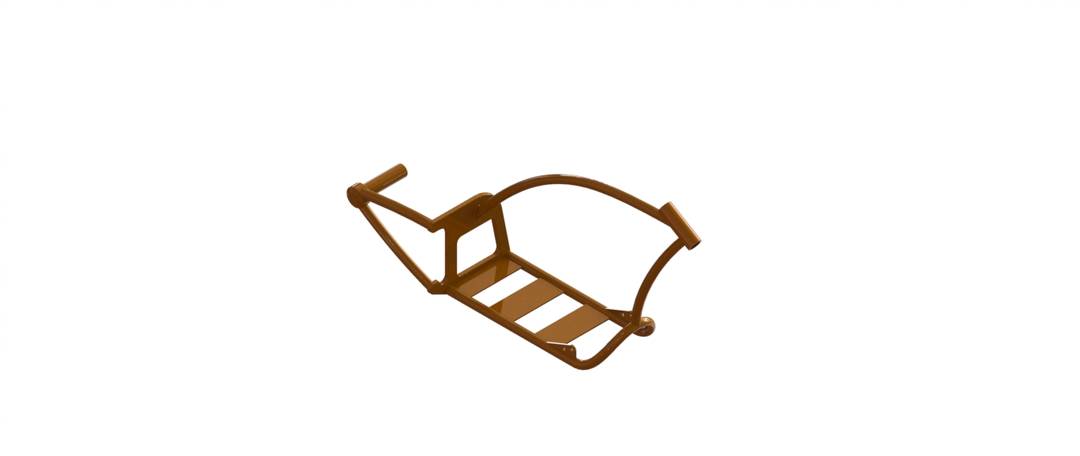
- Engine: It powers a motor cycle. It converts Chemical Energy to Mechanical Energy the rotatory motion of the engine is transferred to the Rear Wheel through Chain and Sprocket.
- Features:
- Boss-Extrude
- Revolve
- Dome
- Cut-Extrude
- Chamfer
- Circular Pattern
- Linear Pattern
- Split
- Mirror
- Swept Boss
- Combine
- Fillet
- Procedure:
- Insert Blueprint of chopper in the front plane ,adjust the location, transparency and sketch on it.
- Select the front Plane draw a diagram of base of engine by using line and 3 point arc, extrude it. The again extrude it on the large circle and small one.
- Sketch on the front plane by line entities then extrude it and give fillet to the base of the engine.
- Select a top plane, draw the pulley by line and then turn on a temporary axis to revolve it.
- Sketch on Pulley by selecting on edge then draw rectangle and extrude towards outside to next surface then select sketch and make circular pattern.
- Select the outer face of pulley and sketch on it, draw a circle inward then draw a small circle vertically to origin, use the circular pattern feature select the center point respectively and coincident Then use the cut extrude feature to remove the material.
- Select the front plane to create the cylindrical part of the engine. Draw a line from origin again draw a line which will be collinear to line. Generate the new plane by selecting the line and end point of the line. Sketch in a new plane, draw a rectangle and extrude it upward. Use fillet as well. Create an angle
rectangle to the new plane and use cut extrude.
- Draw a curve, sketch 2D Diagram in two different plane by ensuring the end point should be same, use the feature like convert entities, Construction line, Spline after getting projected curve, draw two concentric circles, make use of Pierce relation to curve then sweep it.
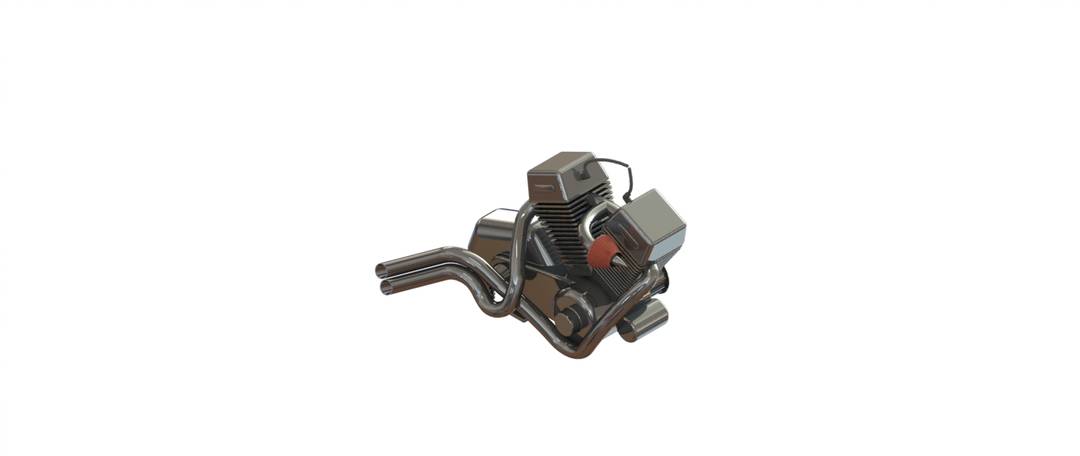
- Gas Tank: It supplies Fuel to the Engine.It is a safe container for flammable fluids. Part of an engine system in which the fuelis stored and propelled (fiel pump) or released (pressurized gas) into an Engine.
- Features:
- Surface Sweep
- Surface Trim
- Surface Loft
- Boundary Surface
- Mirror
- Surface Knit
- Surface Extrude
- Swept Cut
- Fillet
- Shell
- Procedure:
- Insert Blueprint in the front plane and give proper dimensions for locating and rename it. Sketch on front plane by drawing construction lines, Spline roughly as per sketch picture and give dimension to make it fully defined.
- Create a plane at the end point of the spline and sketch on it, by drawing another spline & make a pierce relation with sketch 1, then sweep the surface.
- Sketch on Top Plane by drawing a spline and lines. Trim the outside portion using a trim surface.
- Create one more plane using the front plane and end point of surface 2 as reference. Sketch on it, by drawing a spline and a vertical construction line to dimension it.
- Draw two sketches on Front Plane & Mid plane, using spline and line, then project curve and use lofted surface along projected curve.
- Repeat the procedure for sketching the remaining surface, mirror it & apply knit surface.
- For Seat - Select the outer edges and offset it and then extrude, apply fillet.
- Remove the unwanted surface using a swept cut and apply shell to the body.
- Siena appearance is applied to Gas Tank.
- Grey Cotton appearance is applied to Seat.
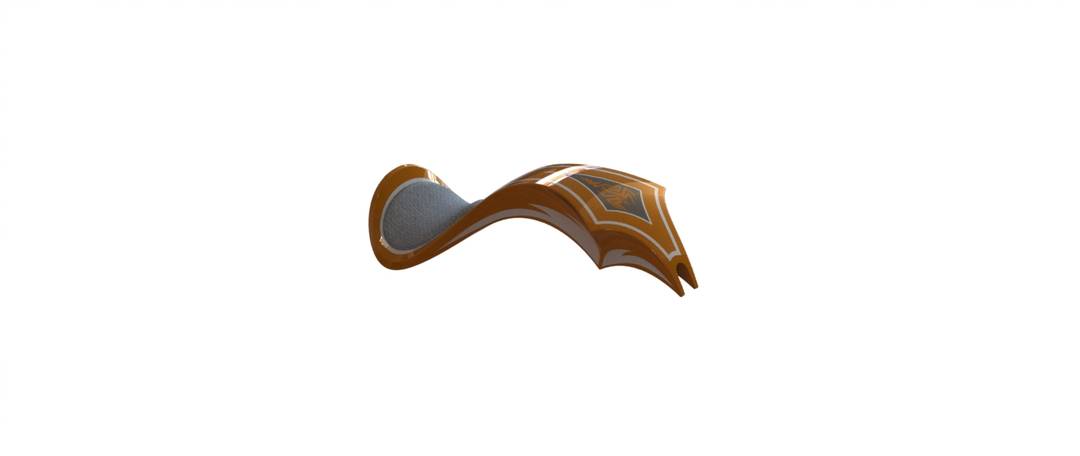
- ASSEMBLIES:
- Mates Used:
- Coincident.
- Distance.
- Concentric.
- Parallel.
- Limit Angle.
- Width.
- Procedure:
- Chassis is the first component inserted in to the assembly model and fixed with respect to the three planes.
- Based on Chassis all other models are assembled using apporiate mates to fully define the assembly.
- Engine is placed on the bottom of the chassis.
- Pedal is attached to side of the chassis and the component is mirrored to the other side.
- Kickstand is attached to the left bottom side of chassis.
- Transmission belt is fixed between the two gear drives and the ensured that tooth are meshed properly.
- Oil Tank is placed above the Engine casing
- Rear Wheel is attached to the Endframe of the Chassis.
- Rear Fender is placed using appropriate concentric mates with the Rear Wheel.
- Chain is Inserted between the rear wheel sprocket and Engine.
- The Gas Tank is placed over the top of the Chassis.
- The Front Fork is attached to the front shaft of the Chassis.
- Finally the Front Wheel and Front fender are attached to the Front Fork.
- The Axle, Front Wheel and Fender are given a angular mate to move on both sides.
- The Front Wheel and Rear Wheel are grounded to the Plane to create a realistic model view.
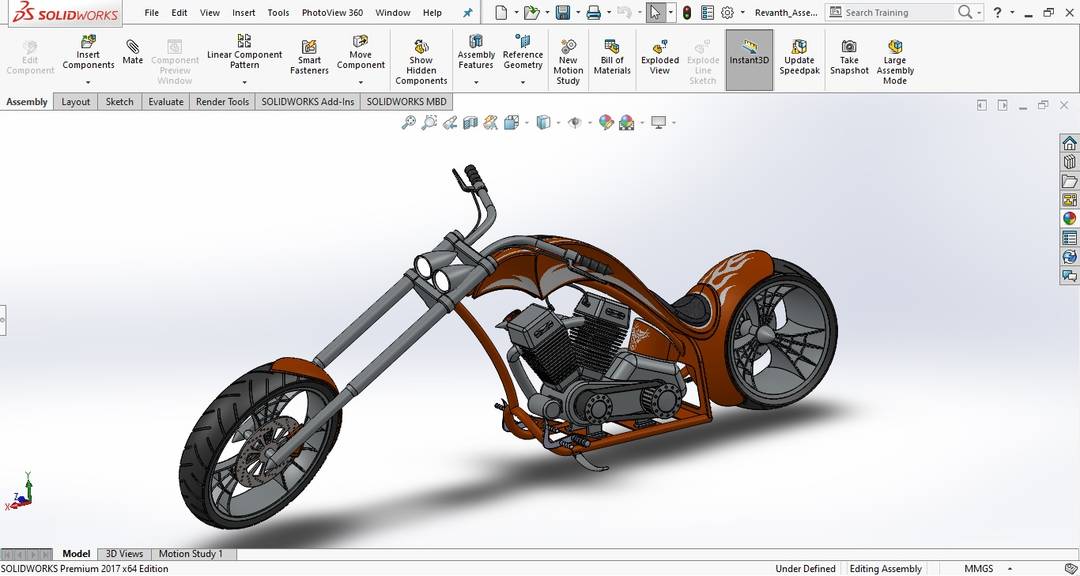
- FRONT VIEW:
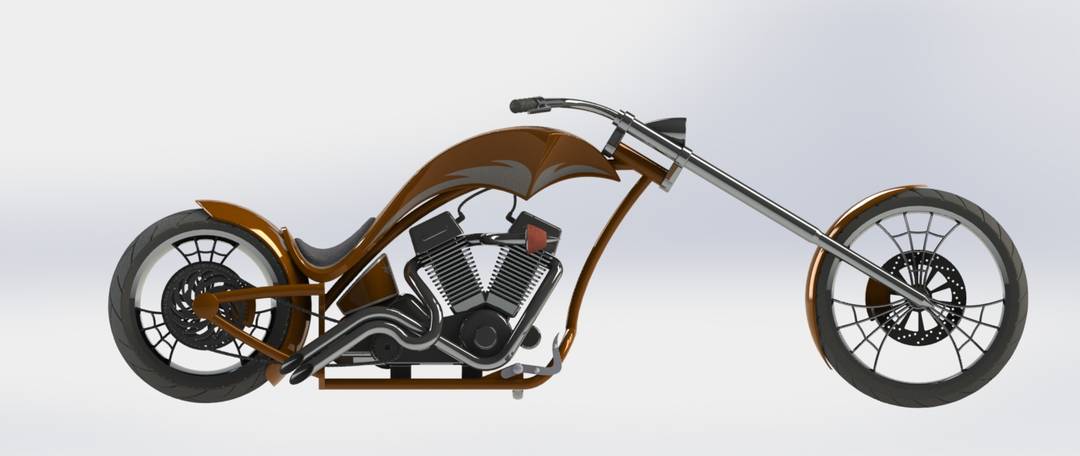
- SIDE VIEW:
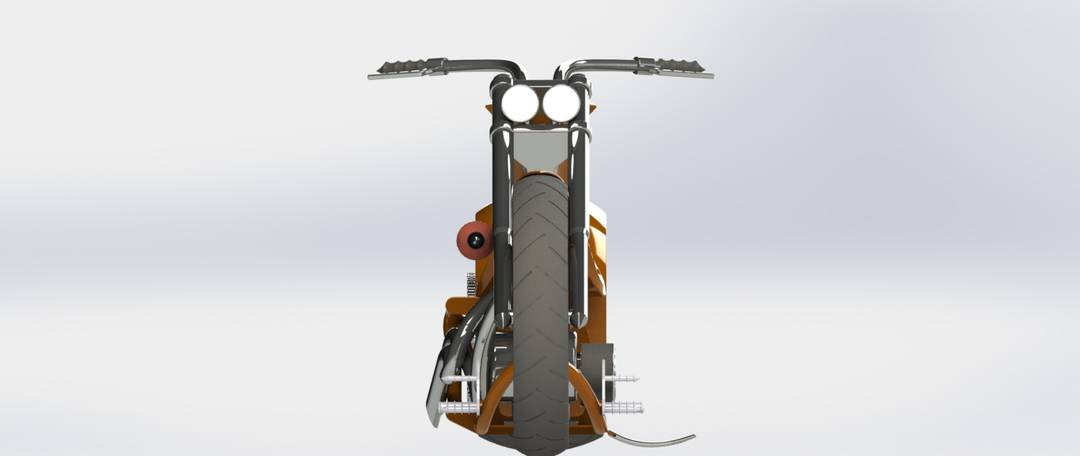
- TOP VIEW:
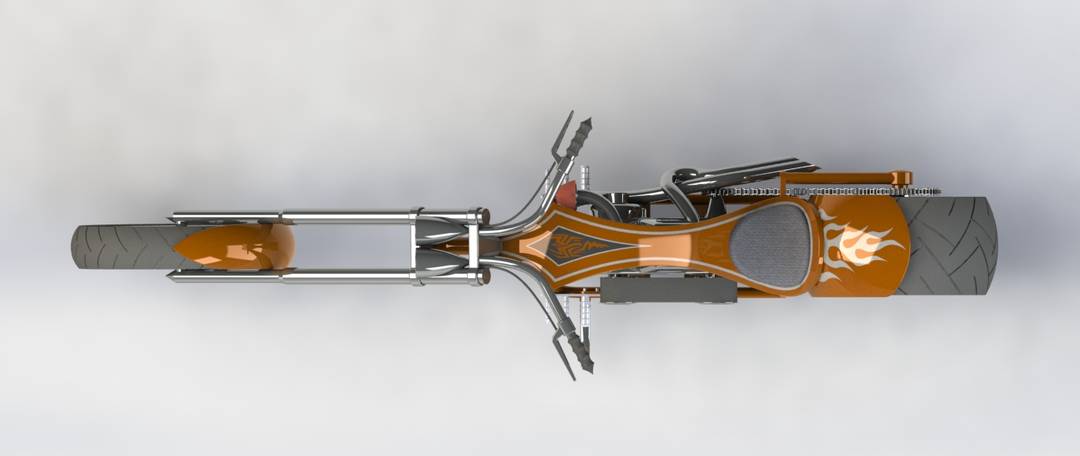
- ISOMETRIC VIEW:
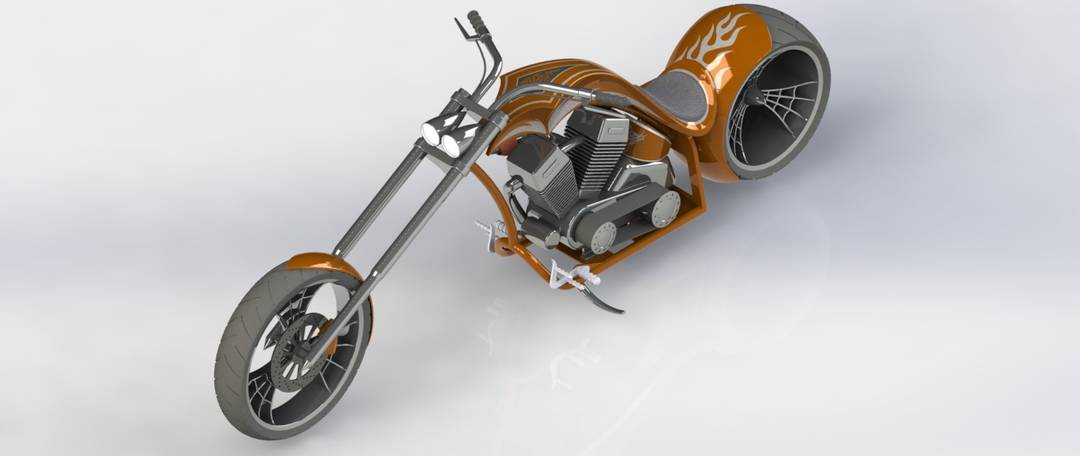
- PHOTORELASTIC RENDERING:
- The Final Assembly Model is rendered using Visualize and using Photoview 360.
- Different scenes were created by adding new camera views.
- Visualize project is used to create relaistic environment and the rendereing is done.
- The rendered images are attached below with different environment and backgrounds.
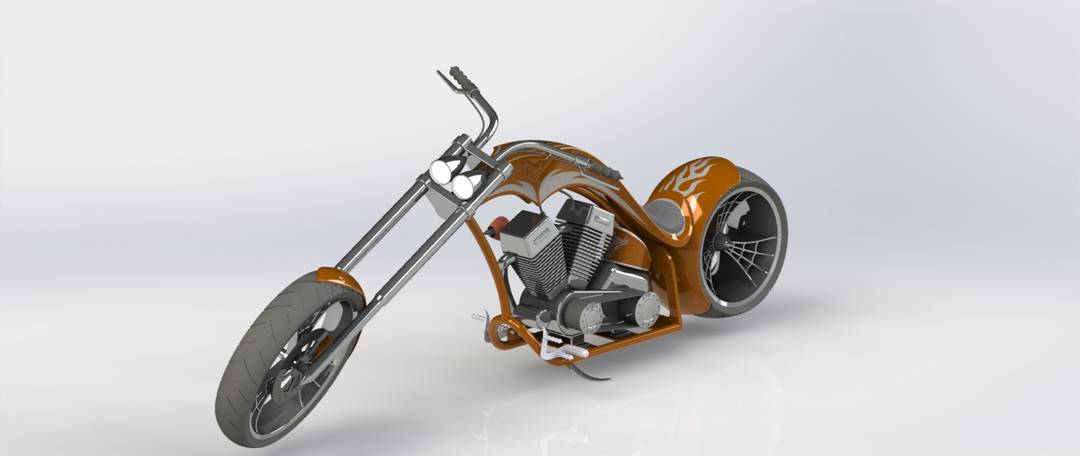
- CONCLUSION:
- Thus a complete American Chopper is modeling using SOLIDWORKS, Photoview 360 & Solidworks Visualize.