RADIOSS INTERFACES & STUDY OF EFFECT OF NOTCHES
INTRODUCTION
The boundary condition nonlinearity of complex dynamic contact problems is effectively resolved by the explicit analysis method. To accurately capture contact interaction between bodies, accurate modelling of contact interfaces is necessary. Numerous contact types offered by RADIOSS are appropriate for a wide range of applications. The slave node set and master segment are defined while creating an interface in RADIOSS. Parts components, elements, contact surfaces, and node surface sets can all be found in the master segment, whereas node sets and parts components can be found in the slave entities. Every time a step, the contact algorithm will look for any signs that a slave node might have entered through a master segment. If penetration is found, the contact is handled using the Lagrange multiplier or penalty methods.
- Penalty method interfaces are based on the treatment of master and slave. Only a set of master segments and a set of slave nodes can make contact. Depending on the kind of element they rest on, master segments have different definitions. The segment is the element's surface depending on whether the shell has three or four nodes. A face is defined as a segment if it is a solid element. Lastly, the segment is a side if the element is a 2D solid (quad). To ascertain whether a node is in contact with a segment, a gap distance is defined. There are spring elements between the slave node and its projection that provide resistant forces in response to penetration. The material and properties of the slave node and master segment are automatically taken into account when calculating the spring stiffness. The stiffness of the interface could have an impact on the time step. Because a spring is attached to the slave node during the penetration, the stiffness of the spring needs to be added to the total stiffness operating on the node (stiffness from all parts linked to this node). To compensate for the spring stiffness, the nodal time step needs to be lowered. When the penetrated node is fully forced out of the gap, contact stops. Consequently, the response force and the elastic spring are eliminated. The contact interfaces with the penalty approach are entirely compatible with any kinematic conditions (rigid body, imposed velocity, etc.), it is important to mention.
- The Lagrange Multiplier approach is entirely mathematical and does not require physical components, such as springs, to mimic touch, in contrast to the penalty method. Contact conditions are taken into account by solving a nonlinear system of equations. Because of the high interface stiffness, there is no time step collapse; nonetheless, completing a single cycle requires additional CPU time since a nonlinear solver must solve each new set of equations. The technique has the benefit of perfectly satisfying the contact condition at the contact surface, where slave nodes are stopped; the friction, however, cannot be calculated.
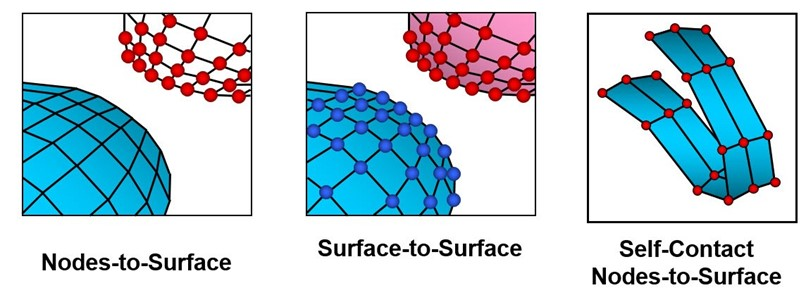
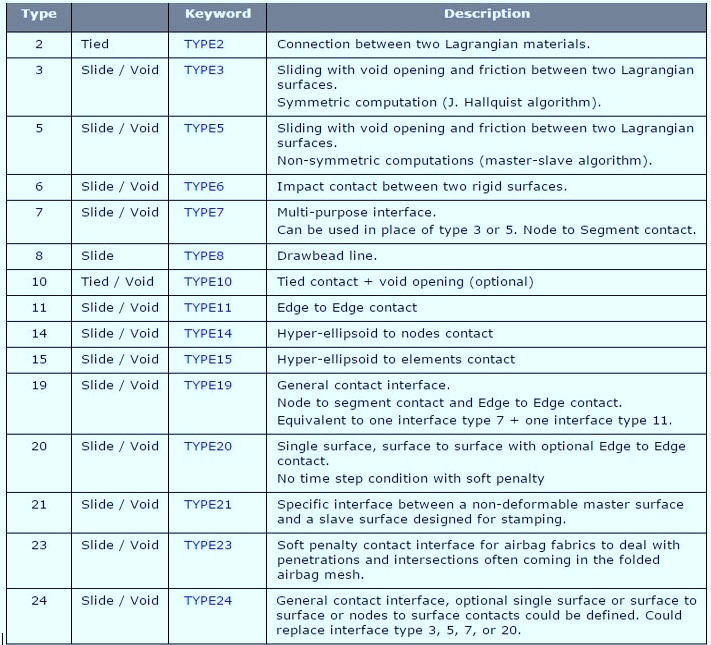
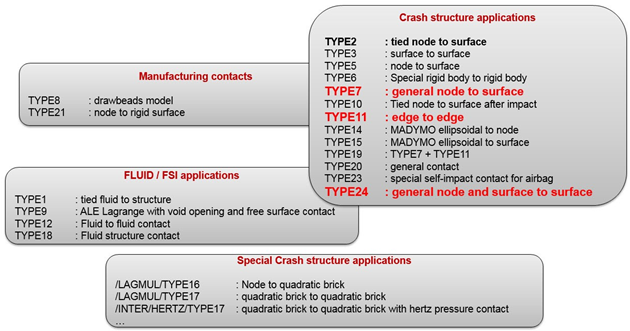
- In mechanical components, notches are tiny incisions or nicks that can lead to stress concentrations. The chance that the material may yield can rise with these concentrations. For fatigue investigations, transient stress and strain can be computed via finite element analysis (FEA). In structural components, notches are frequently the cause of fatigue failure and stress concentration.
OBJECTIVES
- Create the mesh for bumper assembly, mesh size should be 6mm.
CASE 1: Run the crash tube model as it is.
CASE 2: Change the Inacti=6 and run.
CASE 3: Create the type 11 contact and run.
CASE 4: Remove both notches and remove the boundary condition on the rigid body node then run.
CASE 5: Create a new notch in the middle, select the whole section and run.
CASE 6: Create a new notch with nodes only from opposing 2 faces and run.
- Plot RWALL forces, contact forces, and internal energy Create TH/PART for all parts and compare results for all cases.
- Comment your thoughts on why there is a change in the internal energies.
- How does the notch affect the results?
- Plot energies and note any difference.
PROCEDURE
- Import the geometry into the hypermesh and examine it in detail before meshing. There are a lot of geometrical errors in the components of the model. The geometric cleanup is done using tools from sub-panels like surface edit, surfaces, and quick edit panels as described in the pictures below.
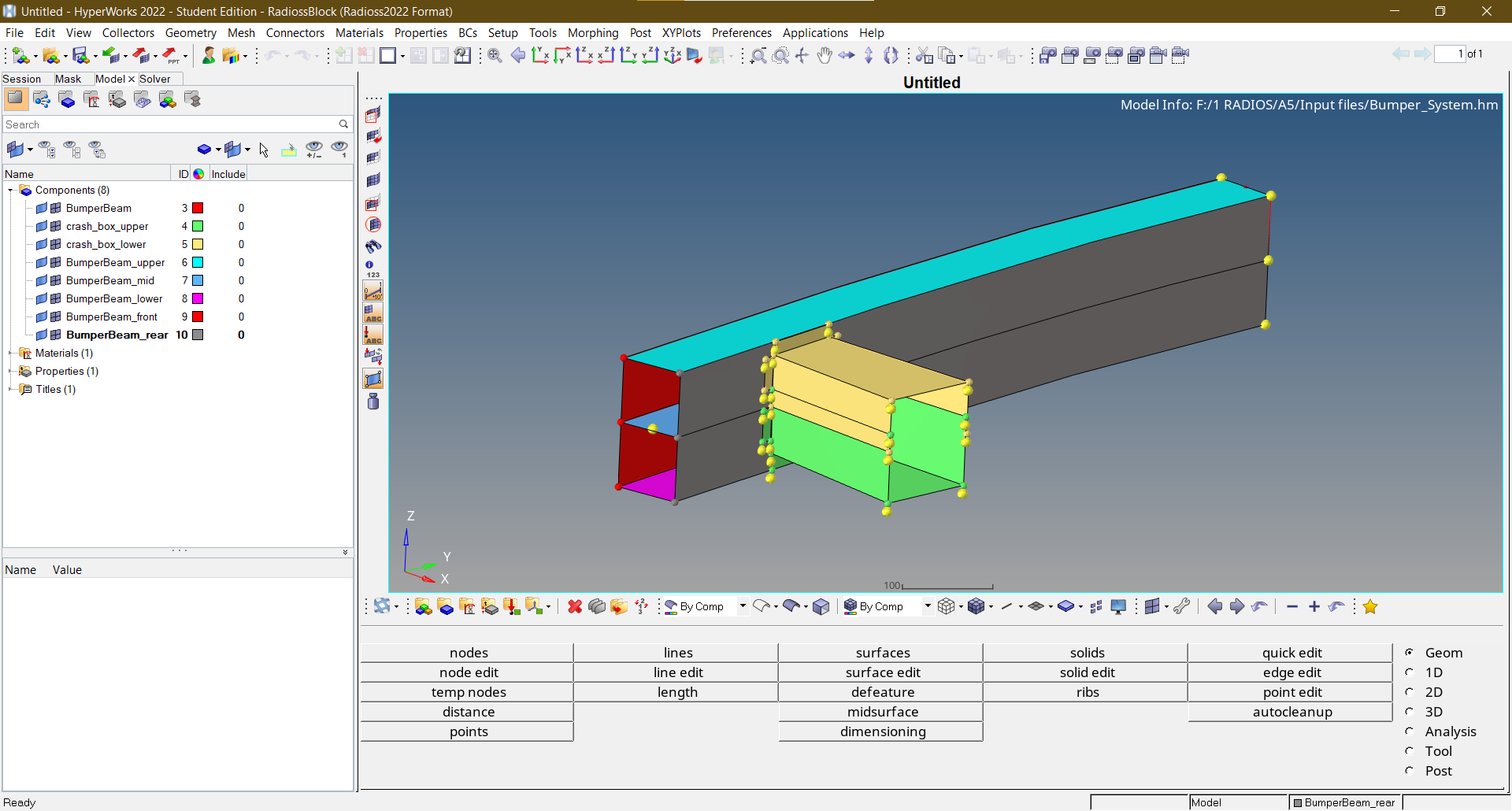
- More than two surfaces are stitched together using the self-intersecting option in the surface edit tool.
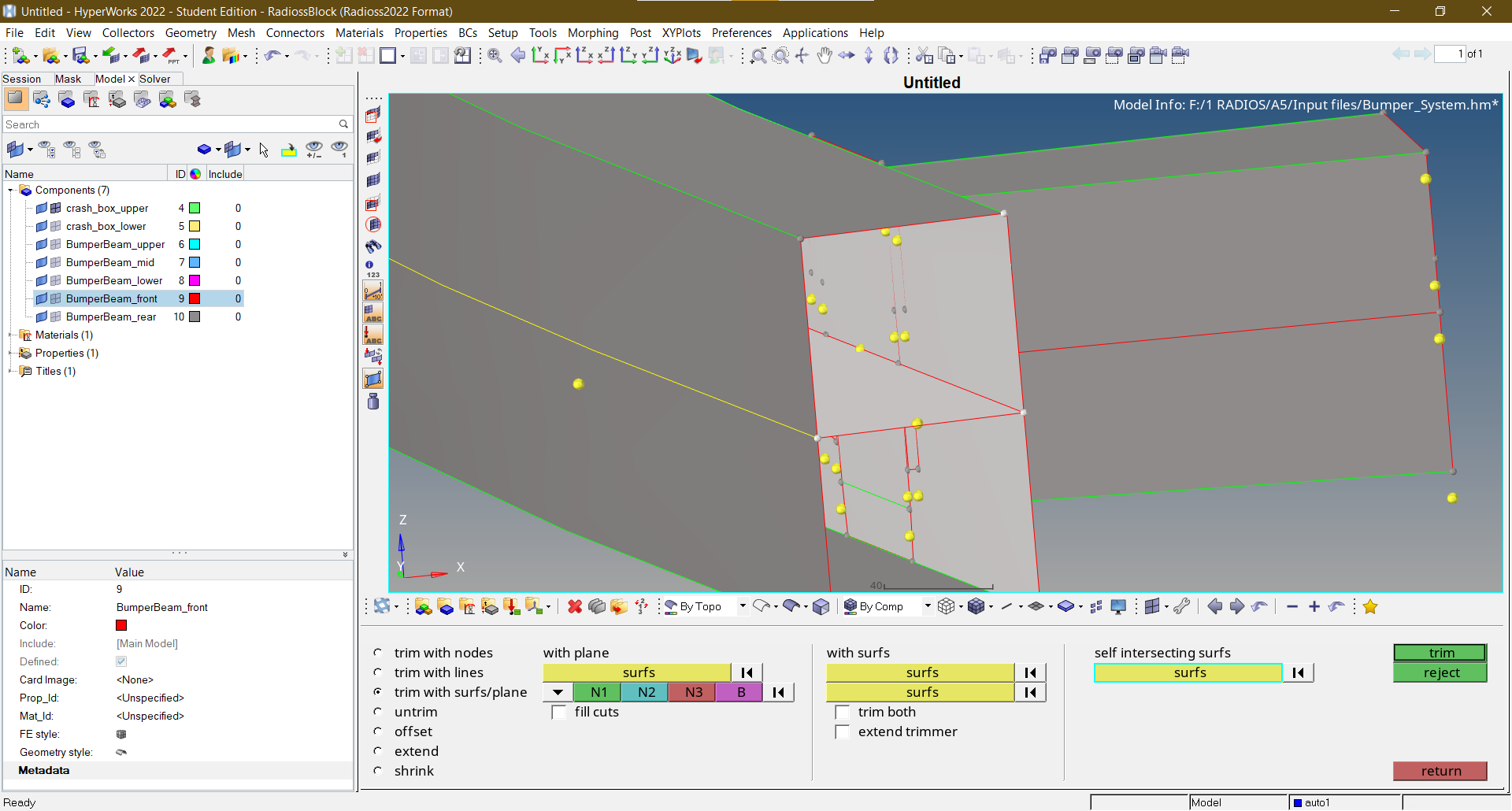
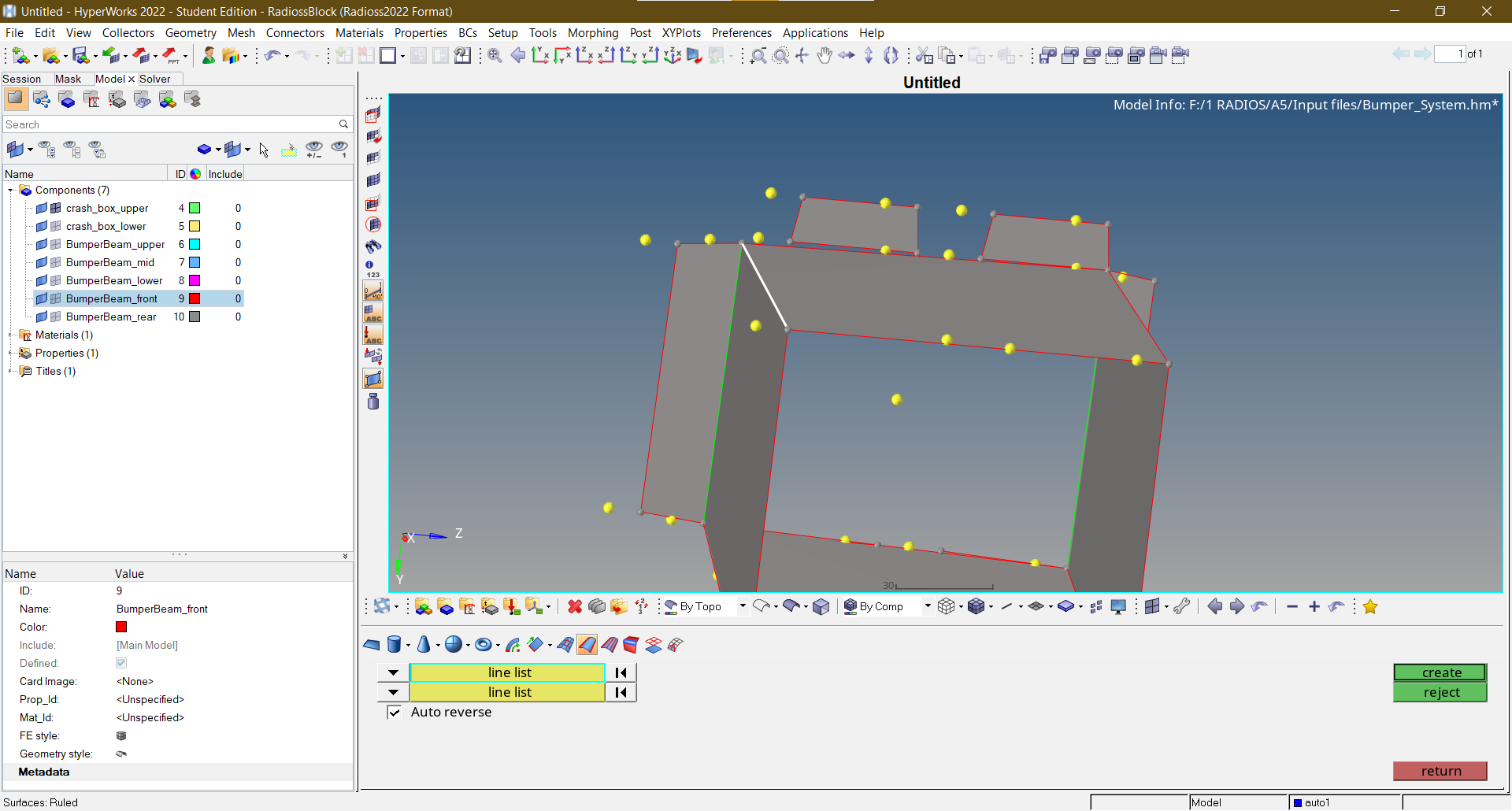
- The outer covers of the crash box are combined with the main surface with the help of points.
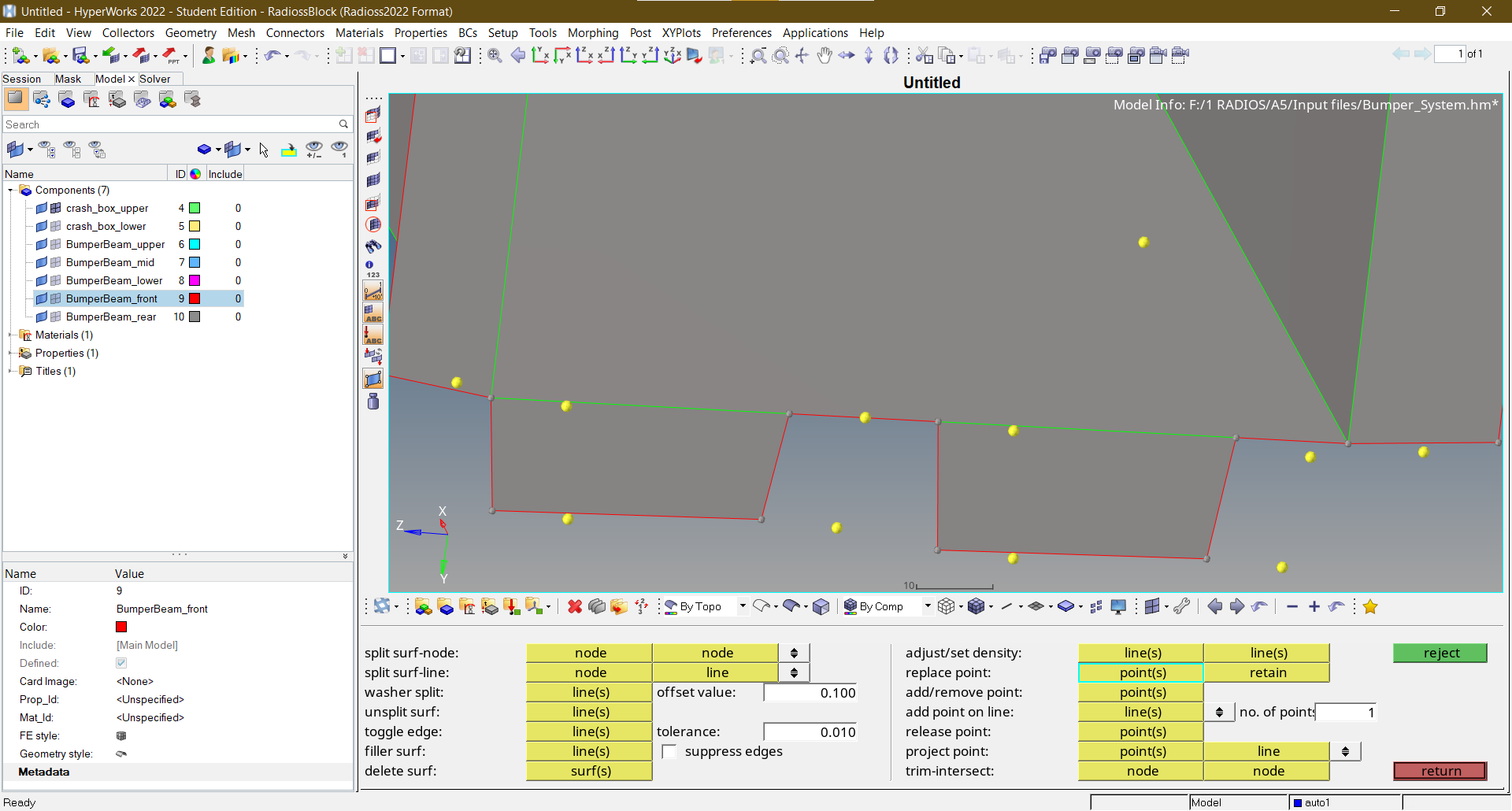
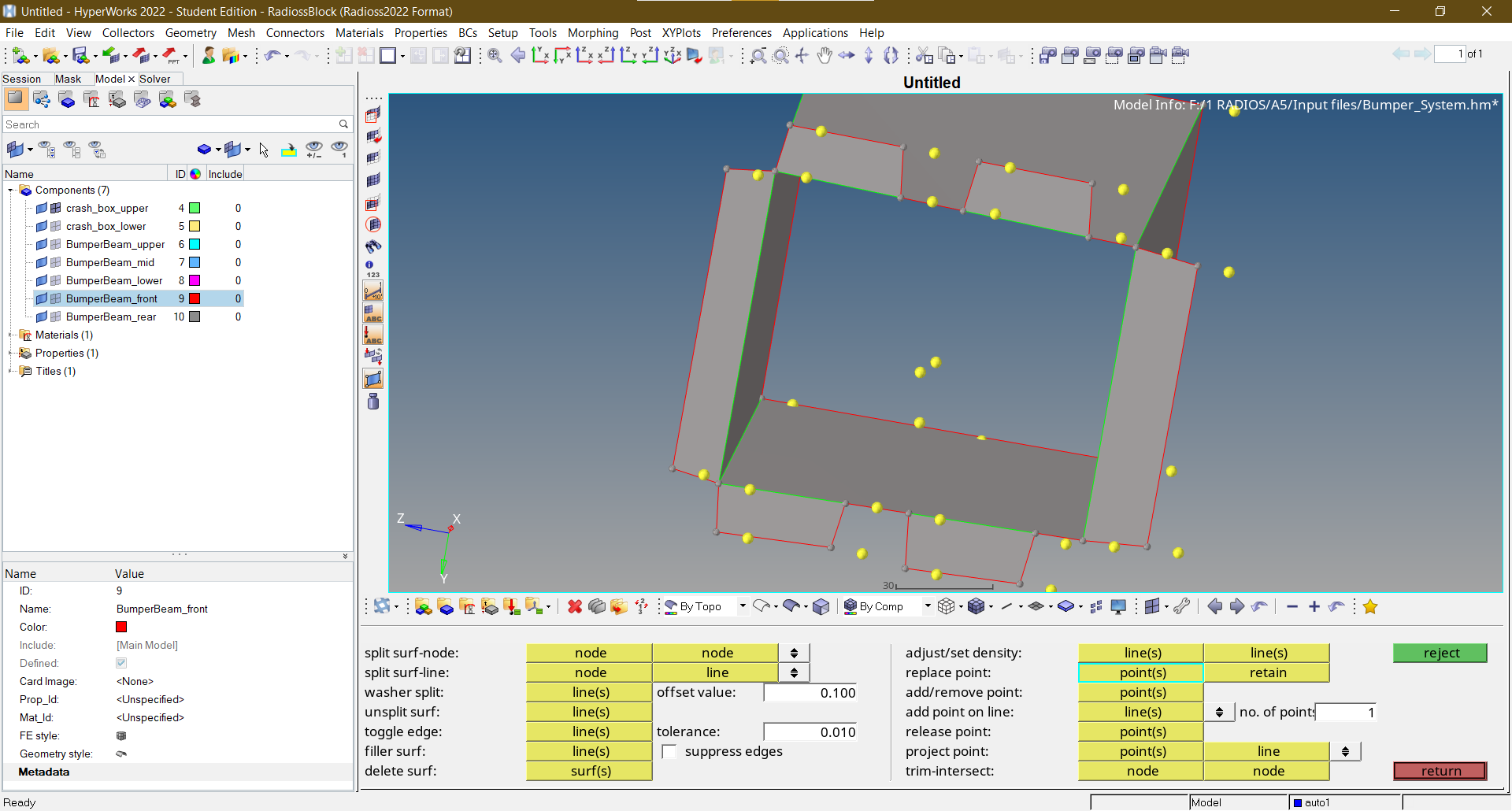
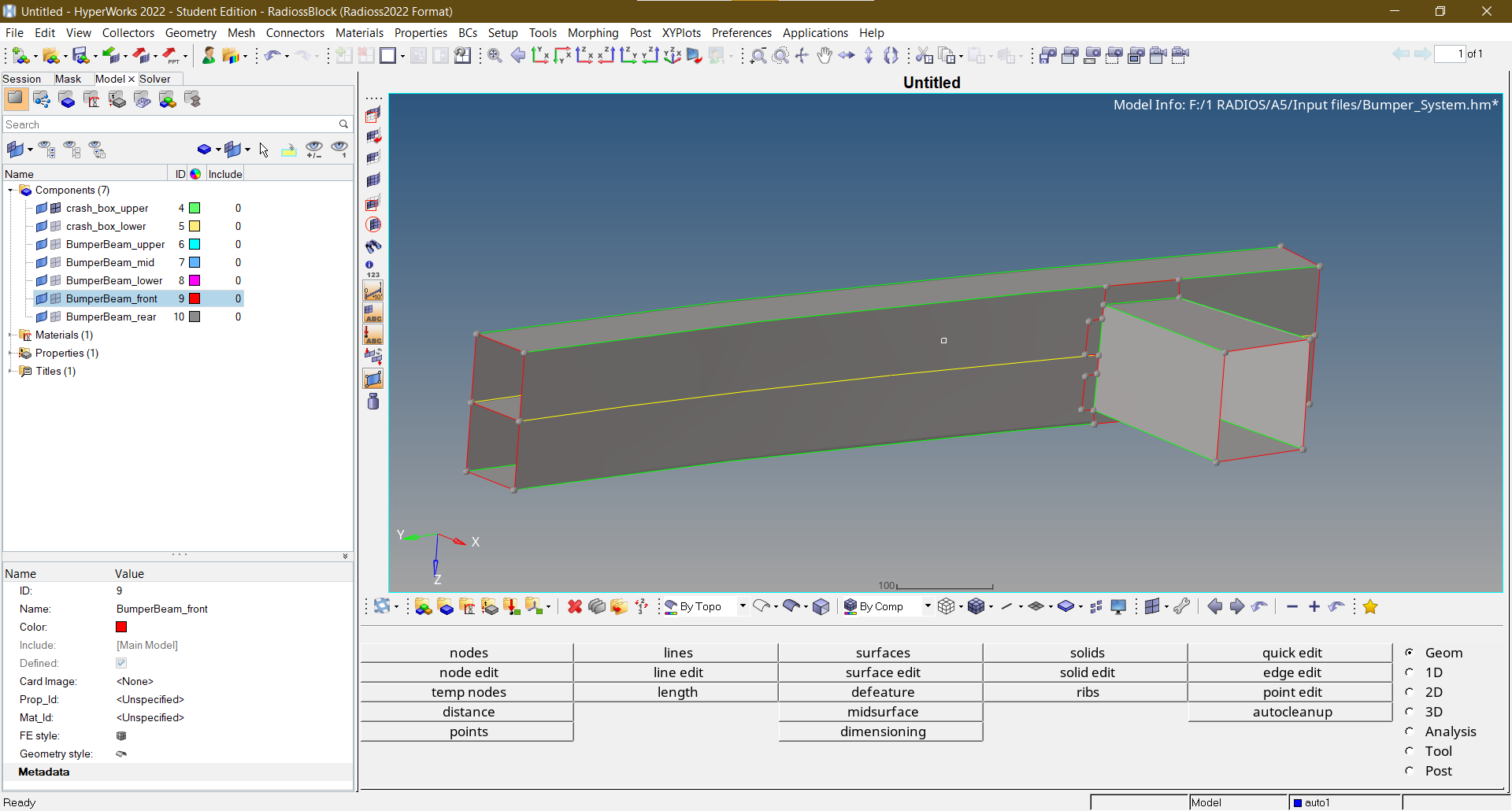
- Since the geometrical cleanup is done the meshing is started using the Auto mesh tool in the 2D menu panel. The mesh size of 6mm is provided as given in the assignment. The mesh density is altered corresponding to the shape of the surface and all tria's are eliminated with ease.
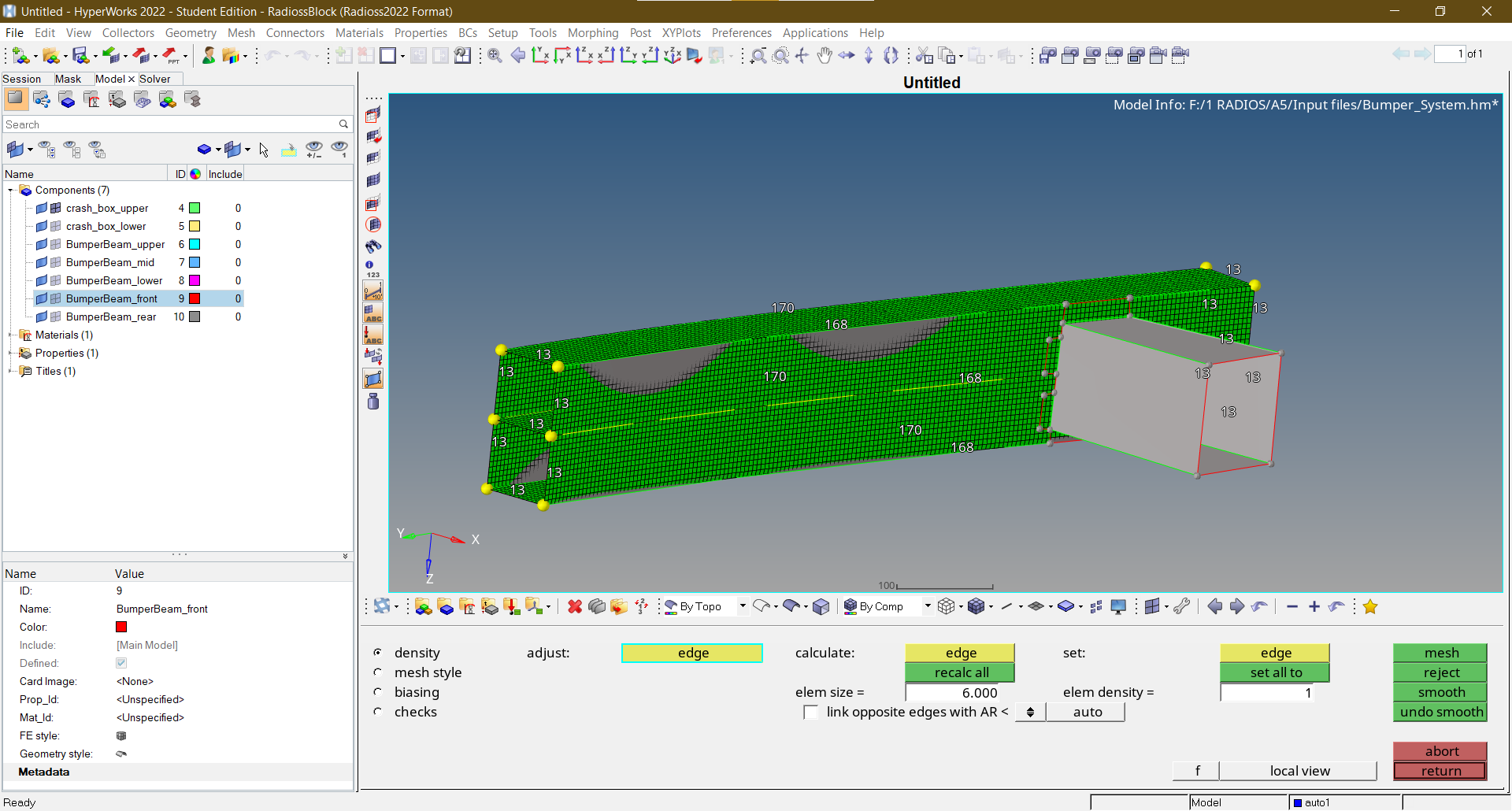
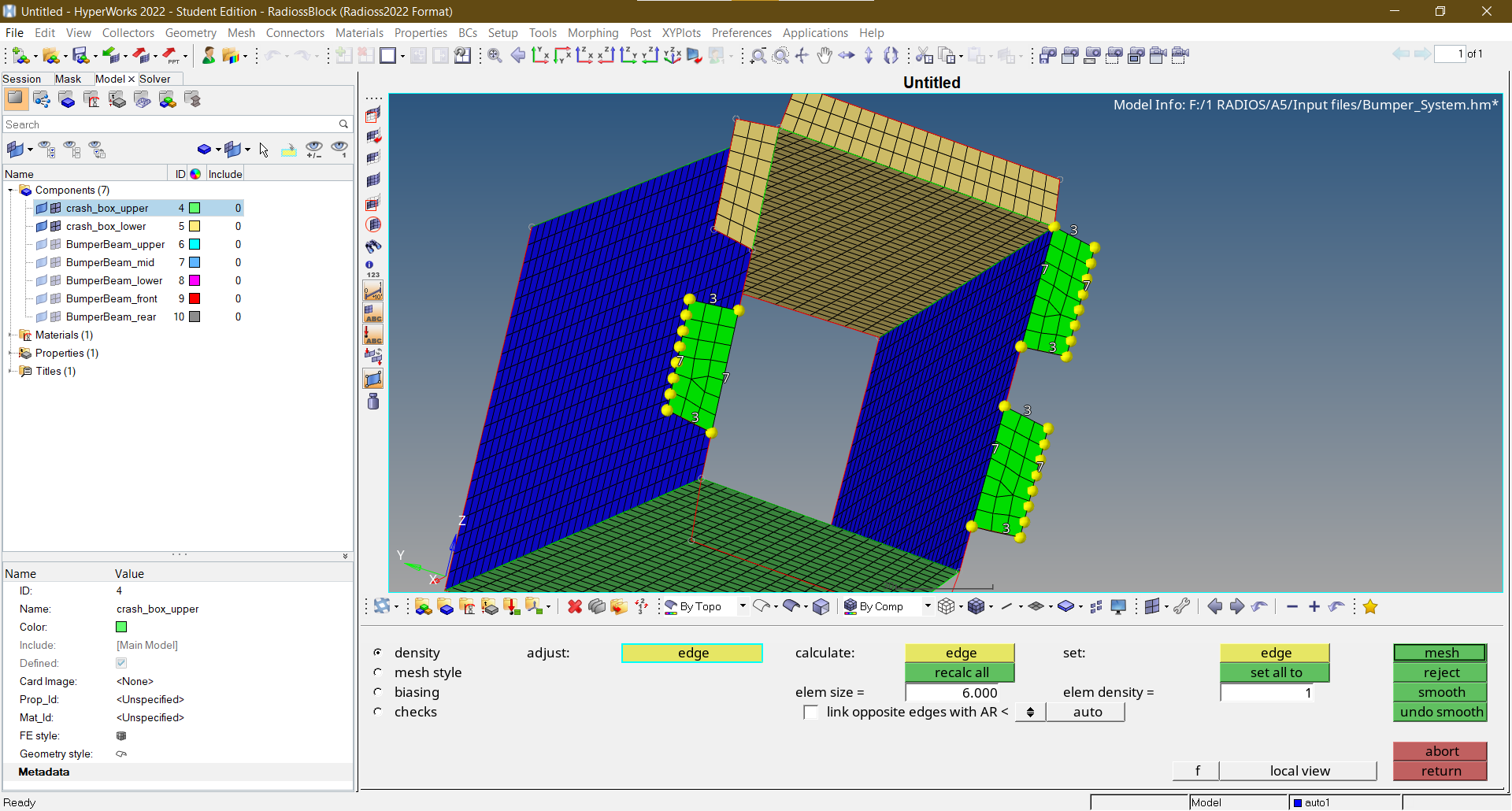
- However, the good quality mesh and geometry were generated in the final image as portrayed below.
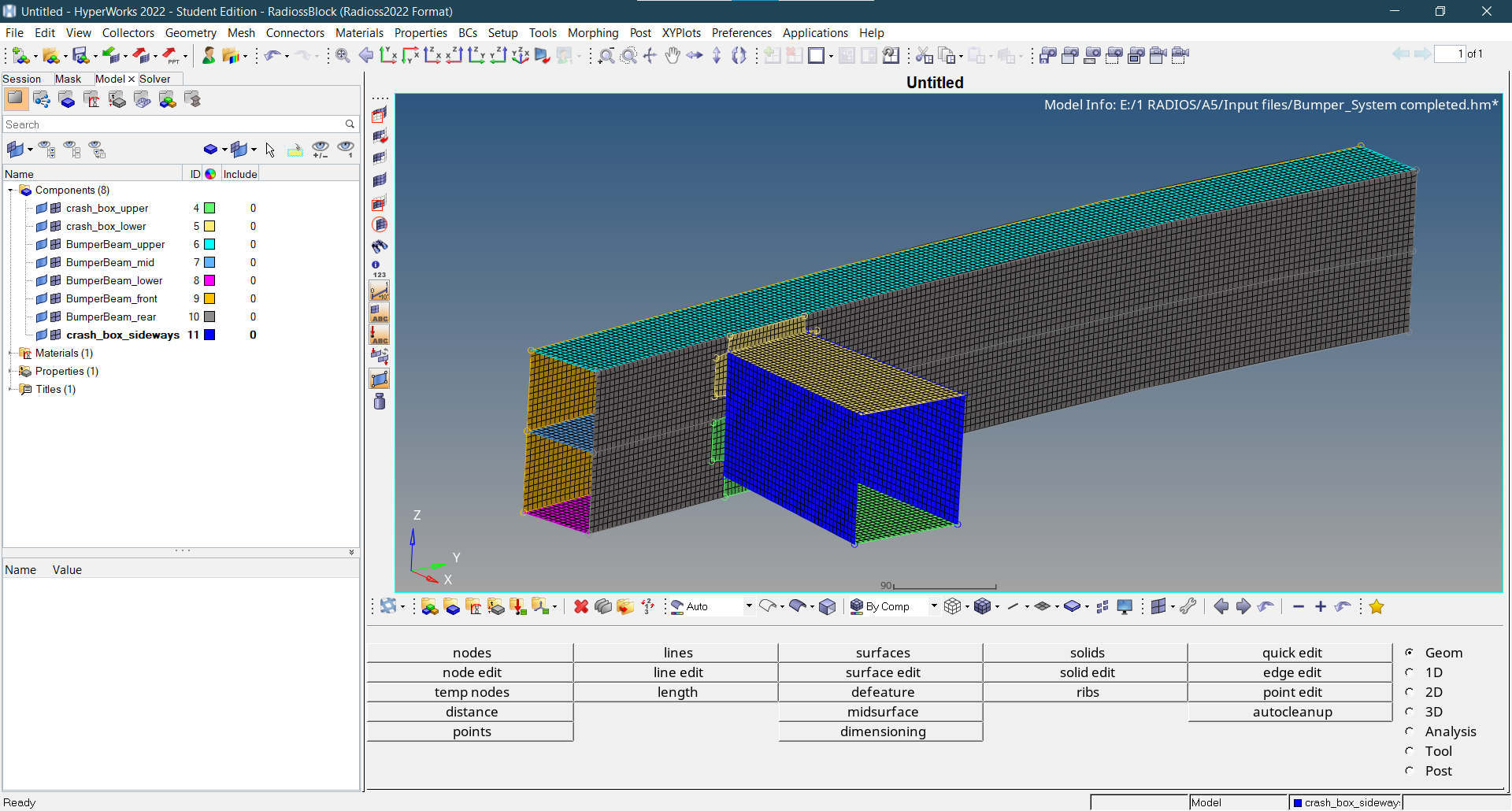
CASE 1:
- Import the crash tube model in the solver deck option of the RADIOSS user profile. The crash tube comprises 4 surfaces, one rigid body and a rigid wall. In this case, the solver is directly run in the analysis panel without making any changes. The standard unit system used for this assignment in this model is Kg-mm-ms-KN-MPa.
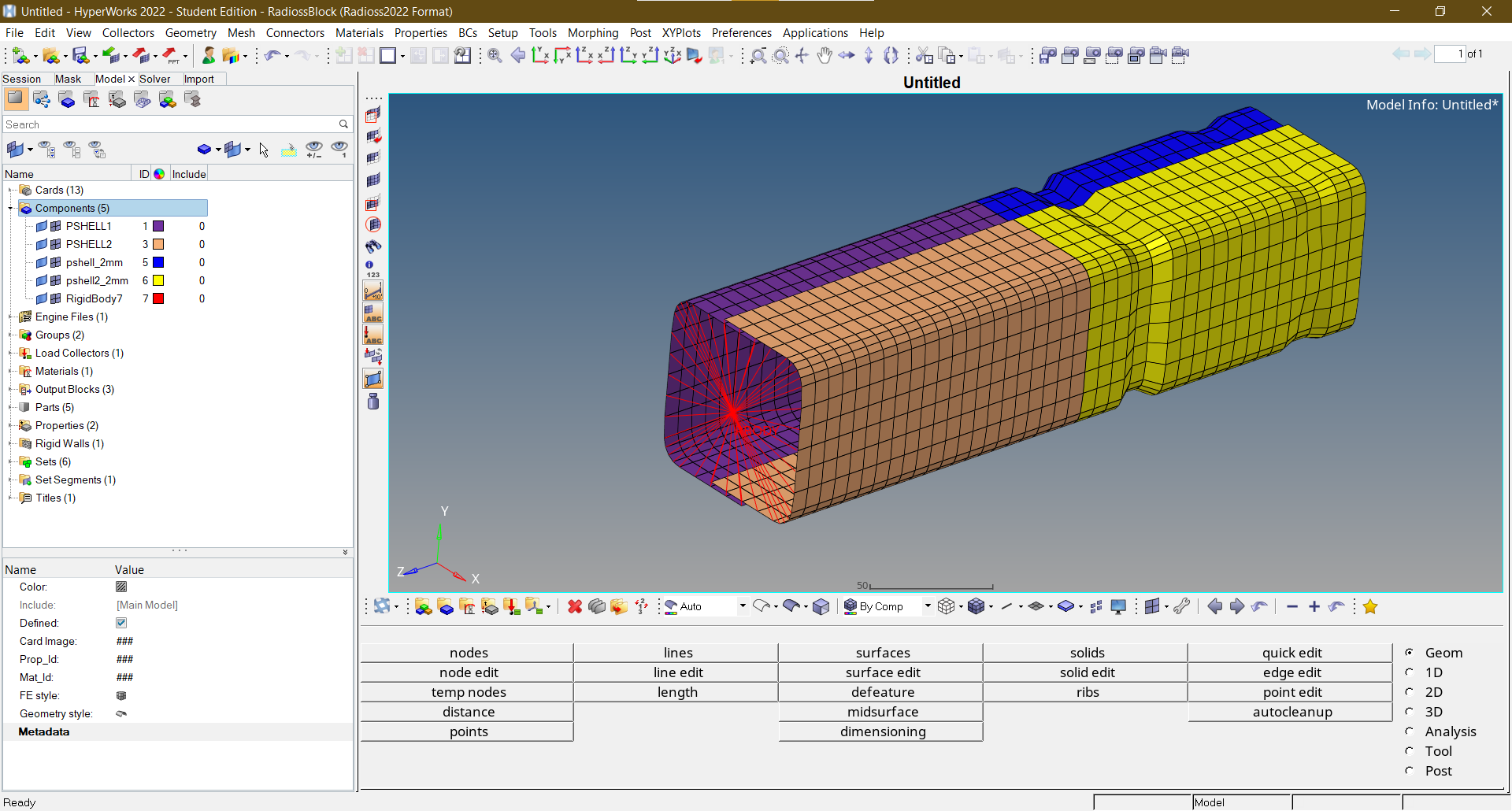
- The default type 7 interface used in this case is a Nodes-to-surface contact. The contact gap can be either constant or variable. The automatic node-to-surface contact interface uses a penalty approach with variable stiffness. A gap is formed around the slave nodes and the master segment. To prevent slave nodes from entering the contact gap, resistive forces are used. To ensure stability, the interface time step is calculated.
- A group of nodes and a master surface can have any kind of influence simulated using interface type 7, which is a general-purpose interface. Interface type 7 is non-oriented, and slave nodes may be a part of the master surface, in contrast to interface types 3 and 5. As a result, this interface can mimic auto-impact, particularly buckling in a fast-moving collision. Interface types 3 and 5 have all of their issues and constraints resolved by interface type 7. A direct search technique is used to find the closest segment; as a result, all potential contacts are detected and no search restrictions apply. A cylindrical gap is used around the edges to eliminate the energy jumps caused by a node colliding from the shell's edges.
- Last but not least, interface type 7's primary benefit is that its stiffness varies with penetration, preventing the node from passing through the shell's mid-surface. This resolves a lot of incorrect contact treatments, which are prevalent when utilizing interface types 3 or 5. Compared to the earlier interfaces, interface type 7 uses a somewhat different gap. The mid-surface of the shell has a gap on both sides, and a cylinder-shaped gap is added around the borders. The primary benefit of the interface type is that, to prevent the node from passing through the shell mid-surface, the stiffness increases with penetration and is not constant. This resolves a lot of incorrect contact treatments, which are prevalent when utilizing interface types 3 or 5.
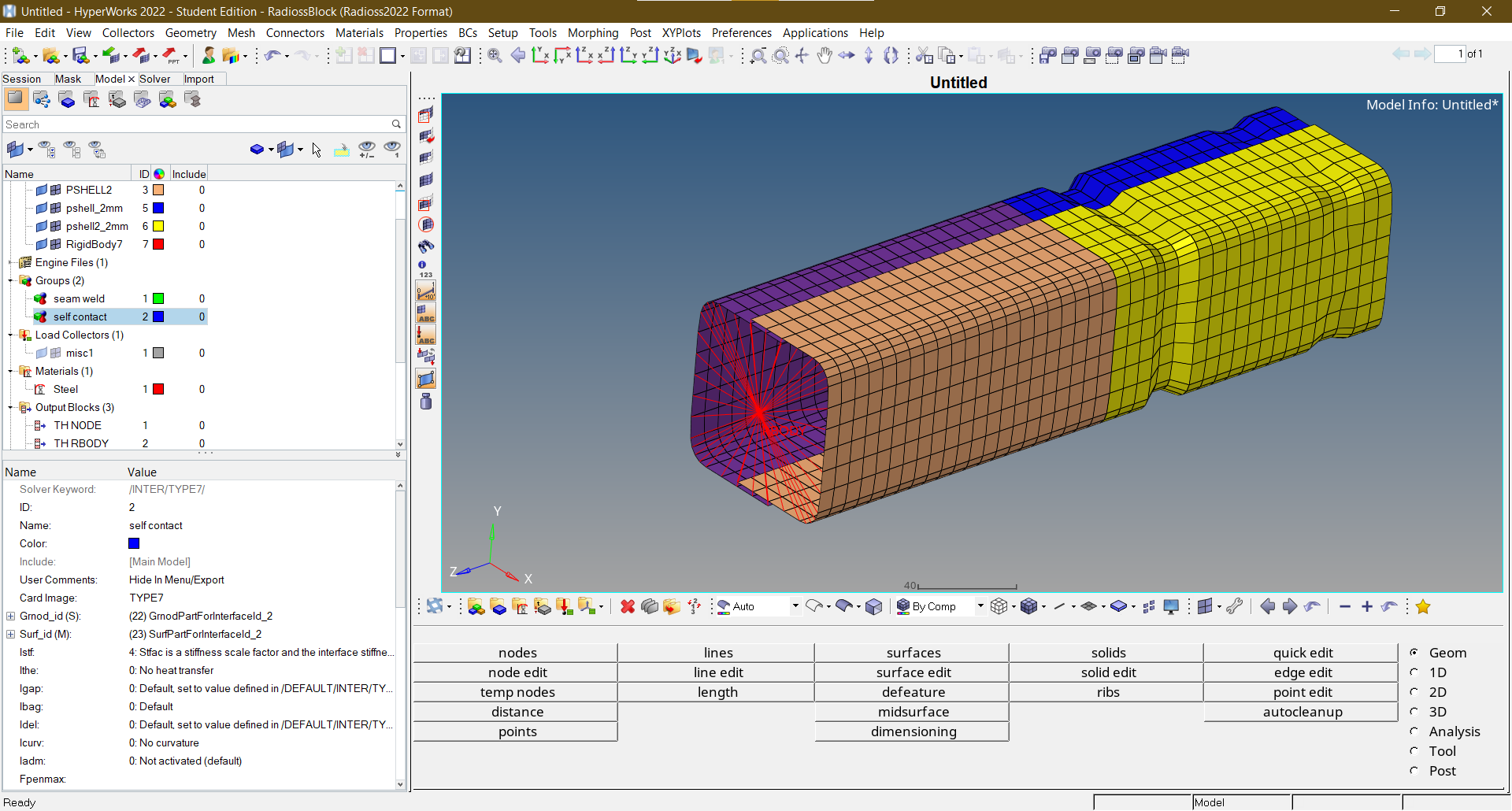
- In the solver tab, create TH/PART for all parts to compare internal energy in all cases.
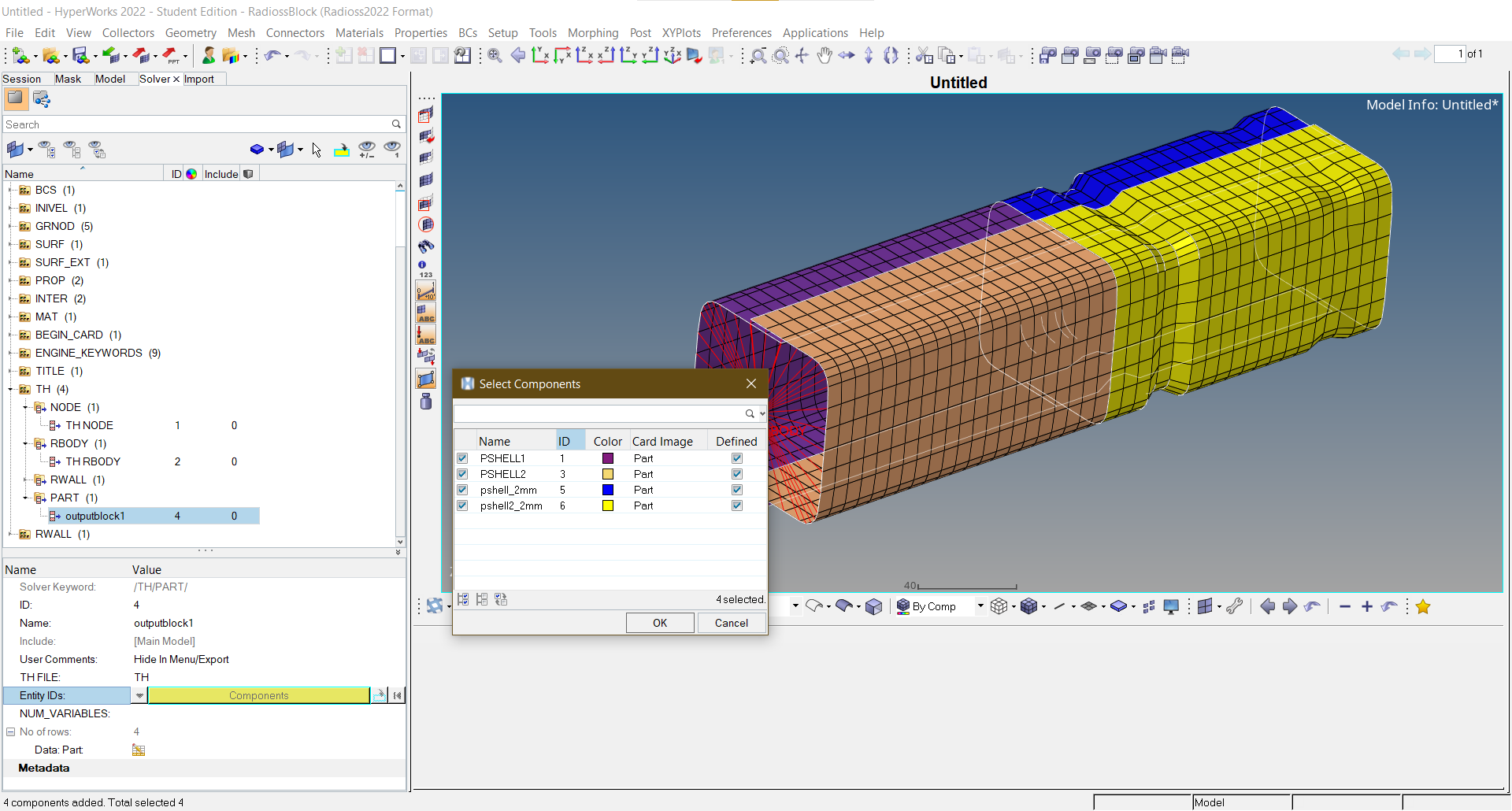
- The contact force plot is achieved by creating INTER in the TH category of the solver tab. The specific interface for the contact force is assigned from the group type.
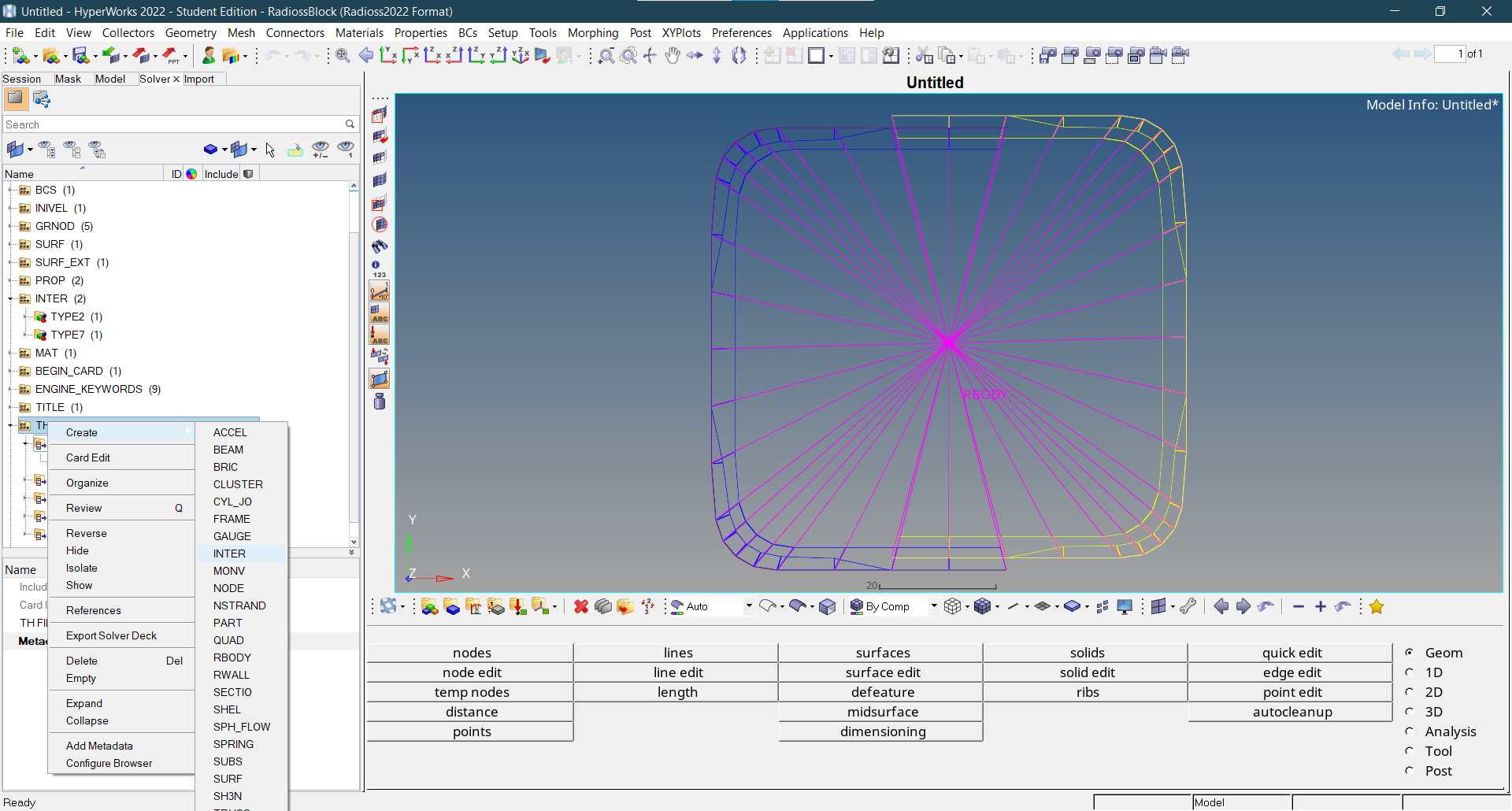
- Henceforth the solver is run and the job is completed within the following simulation time.
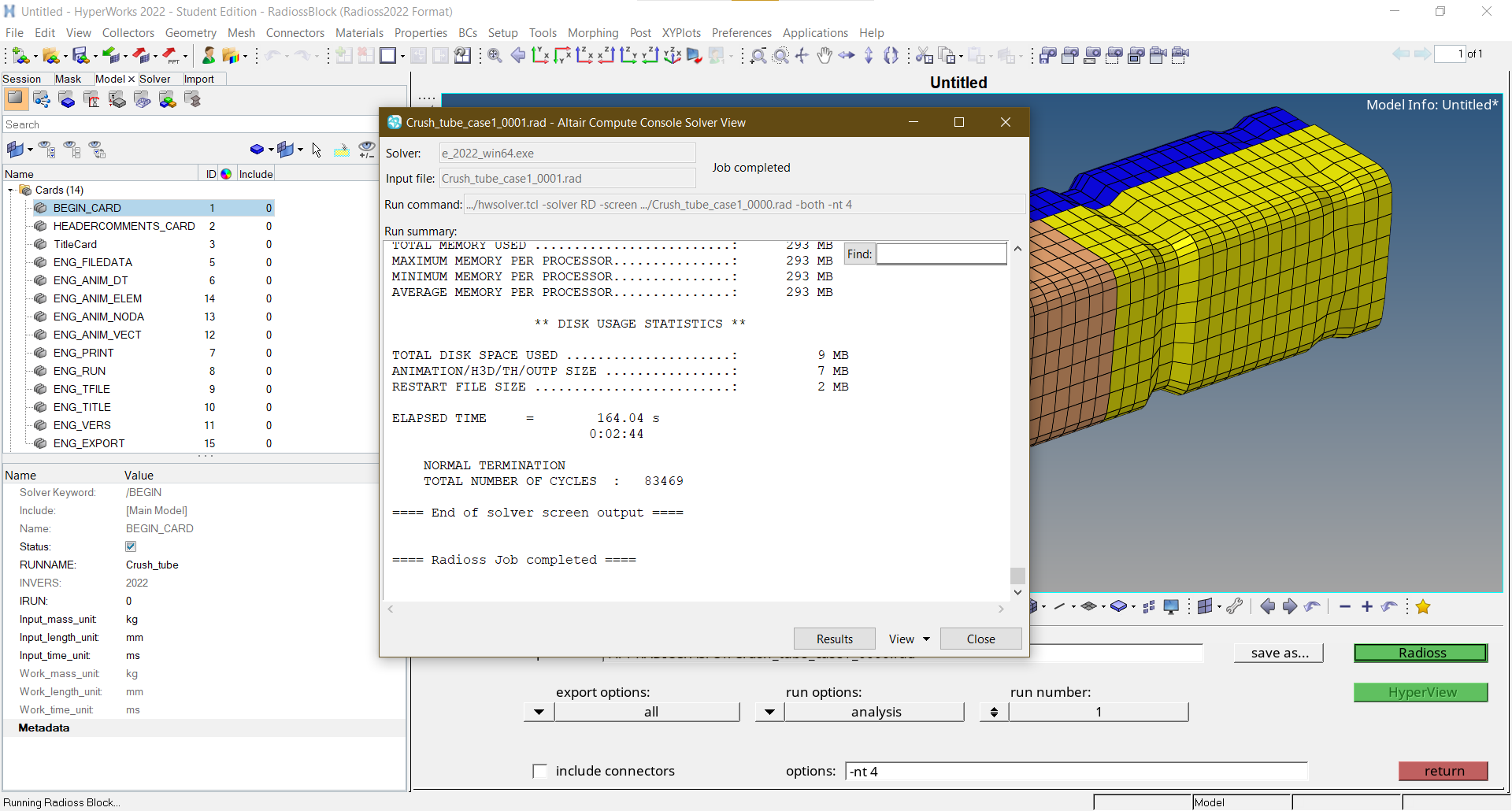
- No mass error is identified in this case while energy is released from the crash tube during simulation. So energy error of -3.8% is found which is within specific limits.
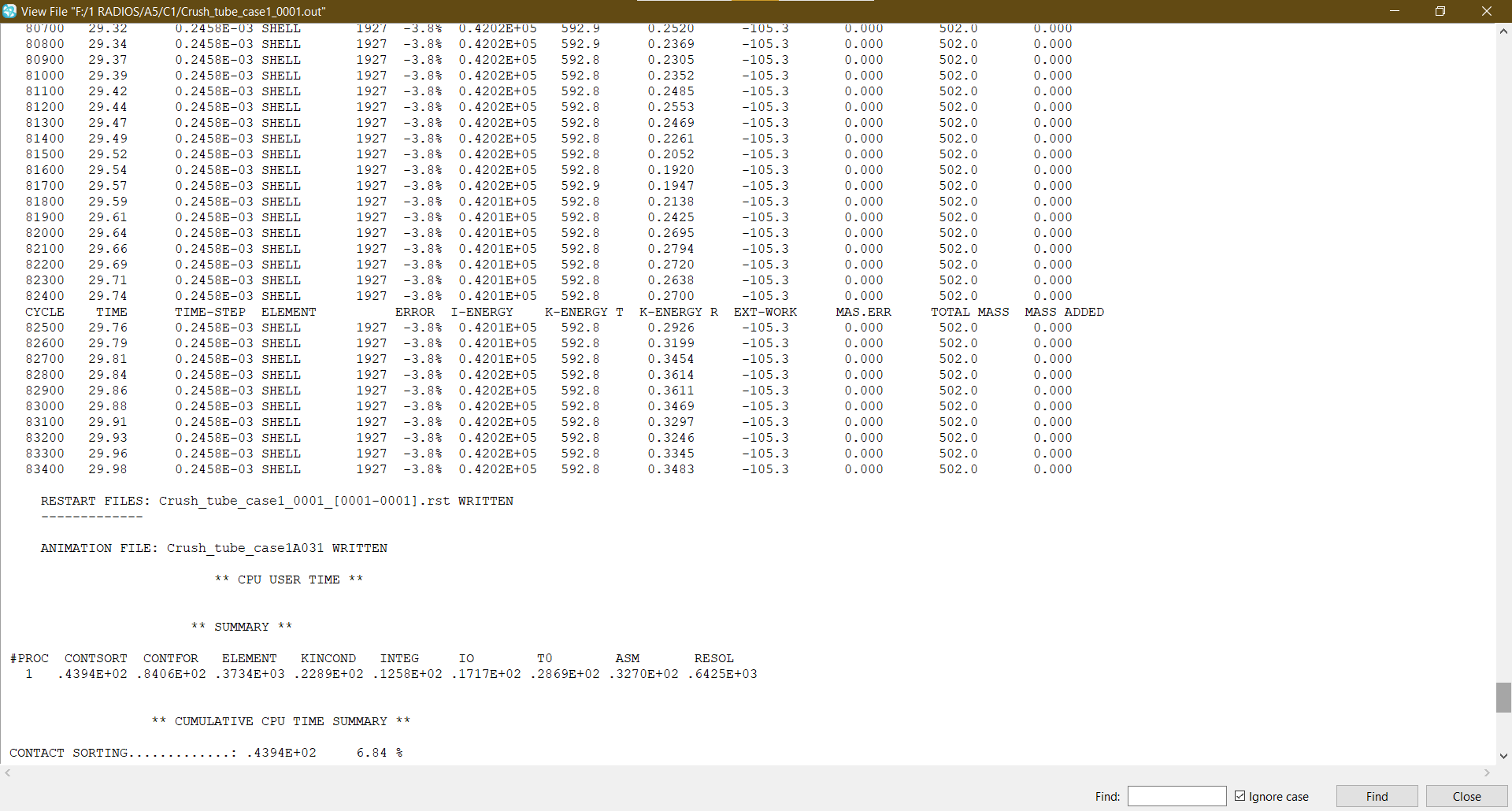
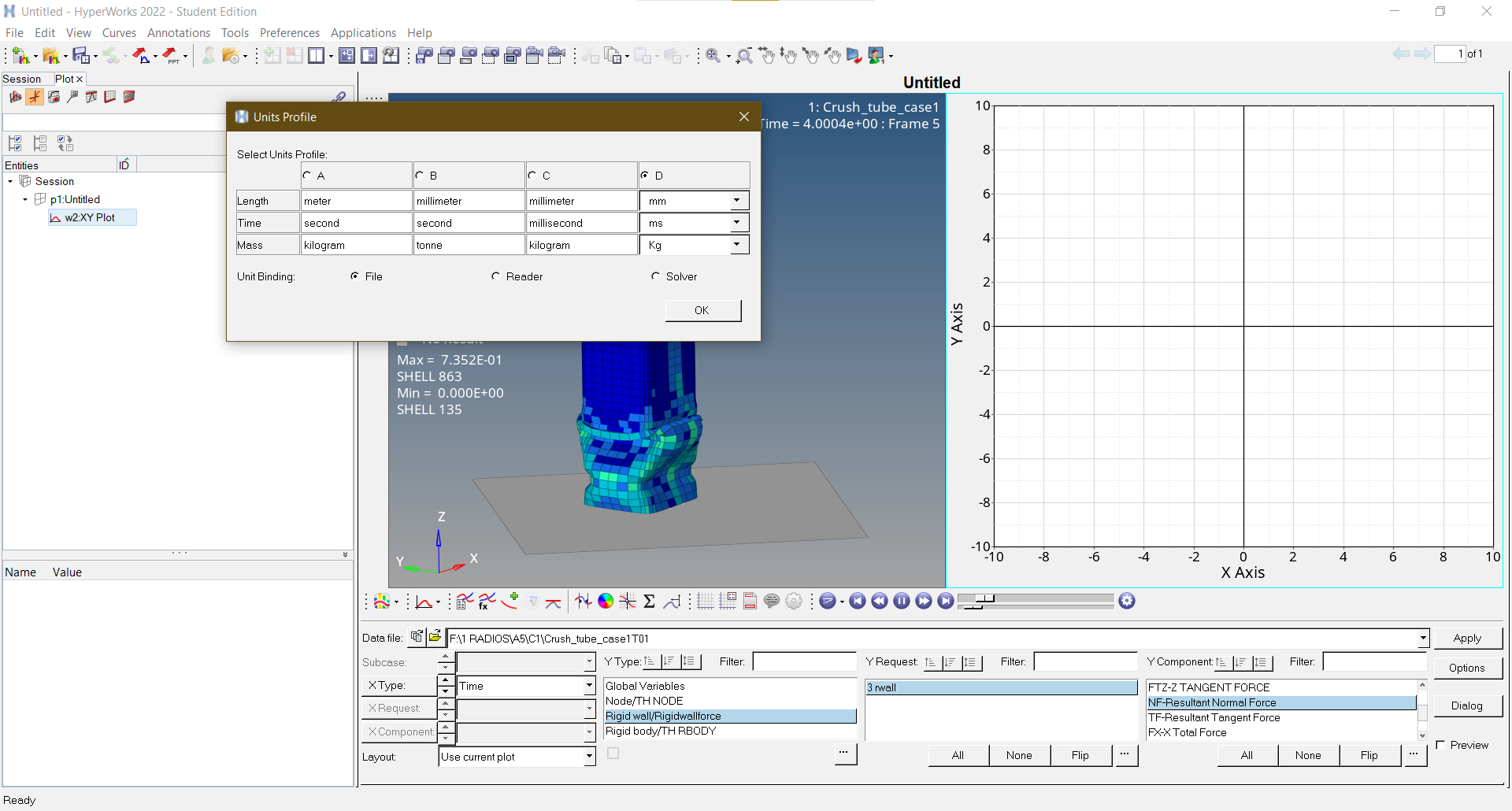
CASE 2:
- In this case, only inacti option is modified to 6 for the interface as displayed below. The rest of the things are kept unmodified and the simulation is initiated. The case 1 radioss starter file is imported in this case.
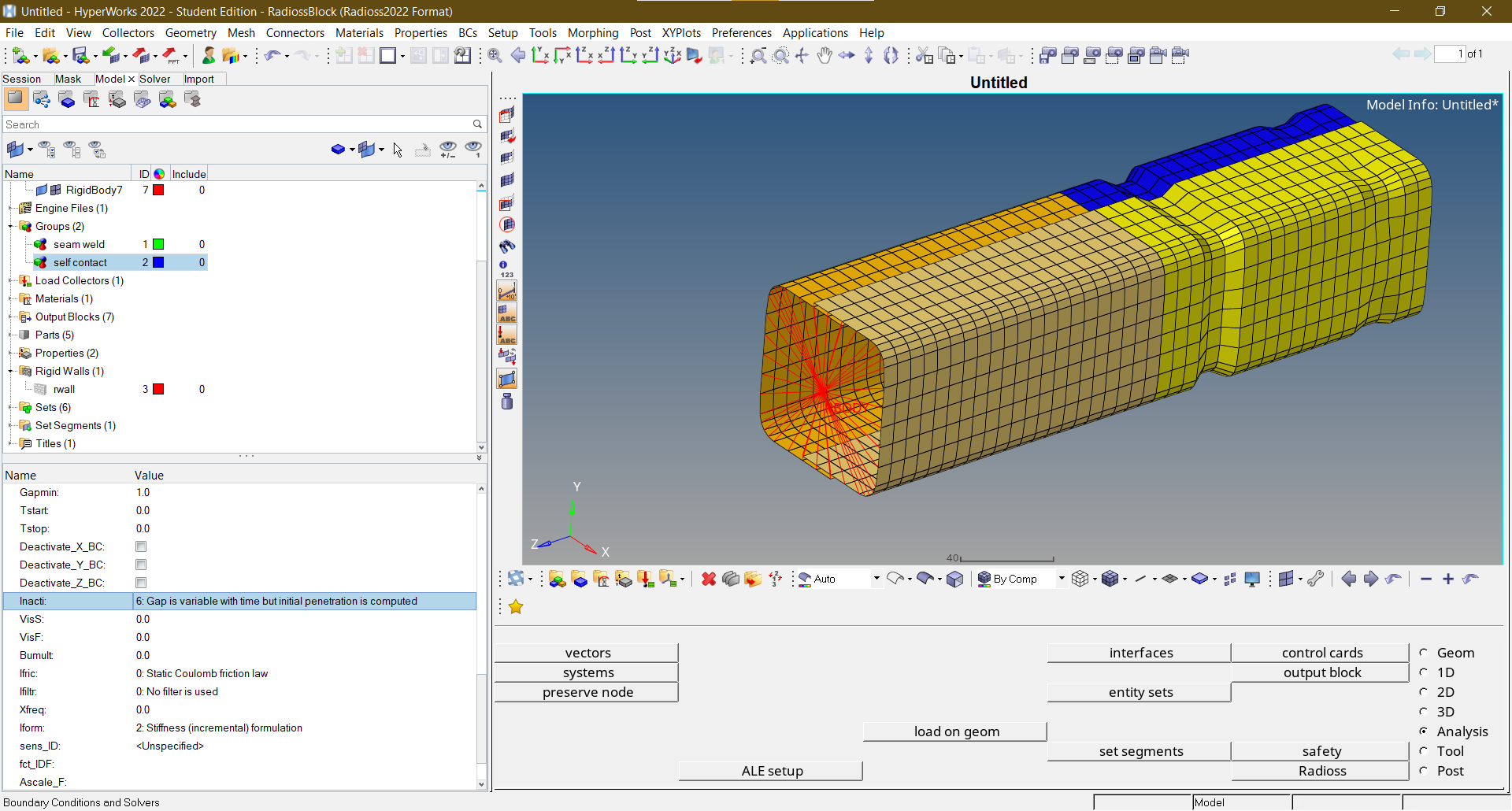
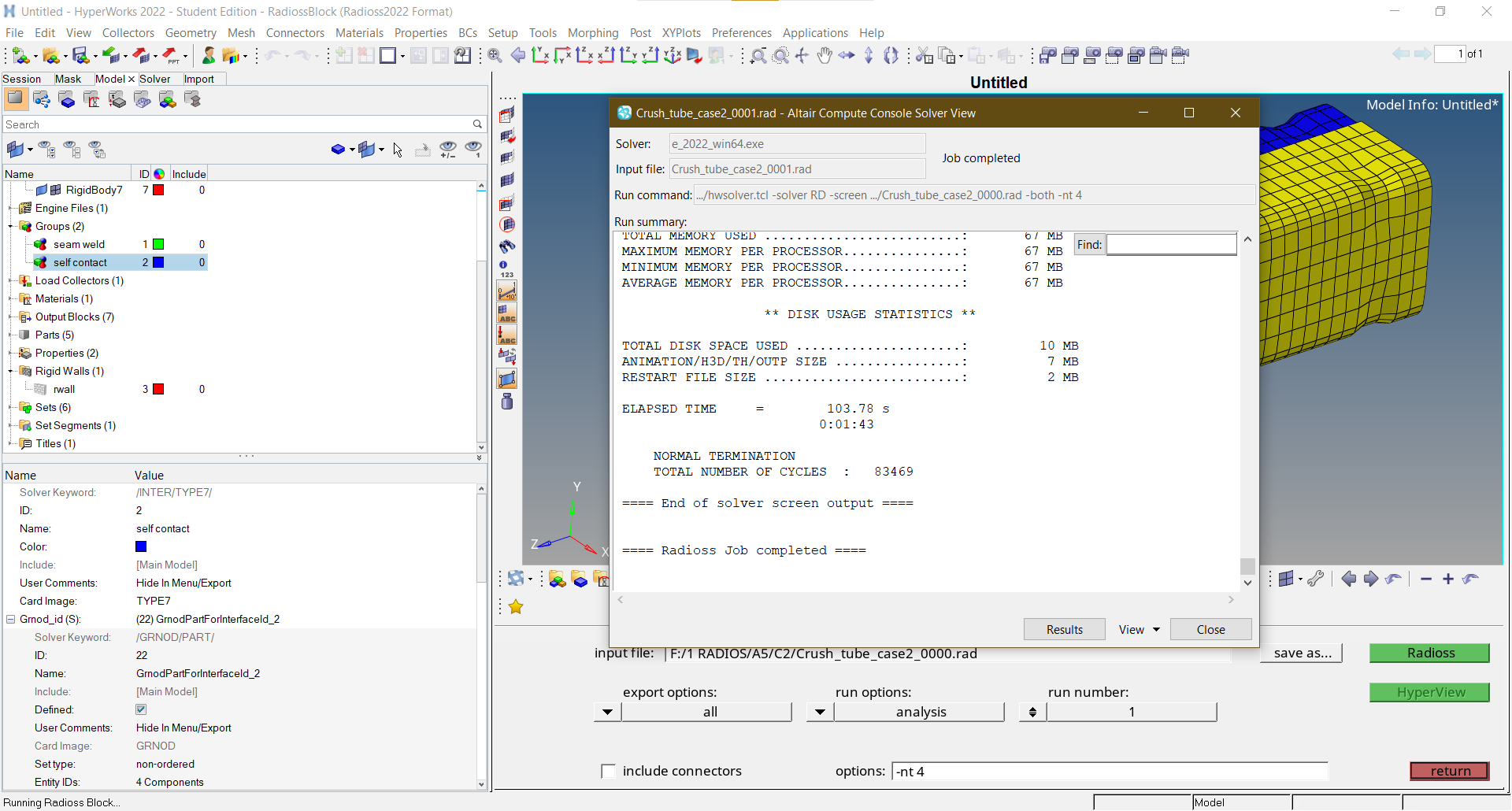
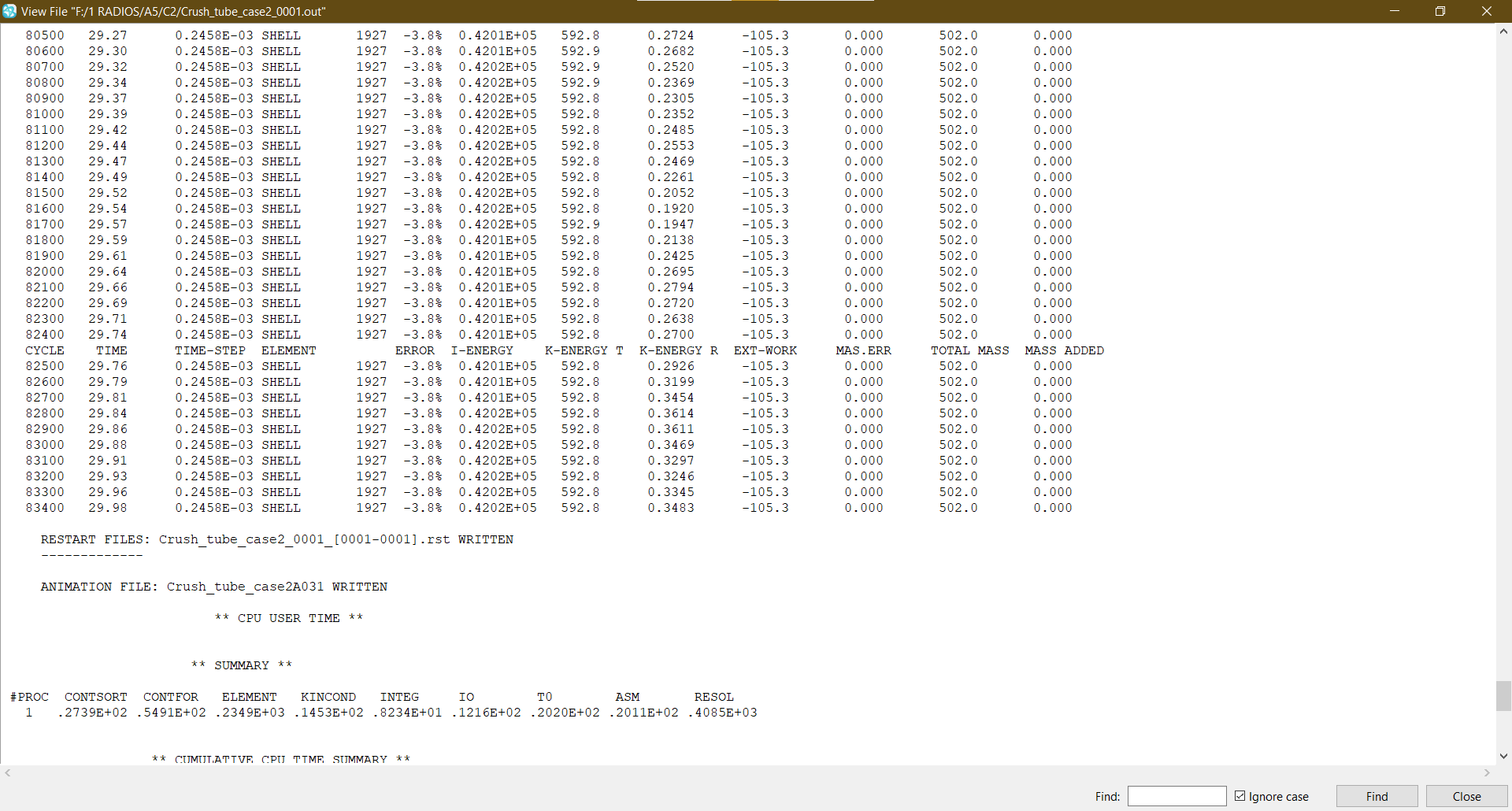
CASE 3:
- In this case, the type 7 contact is removed and the type 11 contact is assigned with default values. The case 2 radioss starter file is imported in this case.
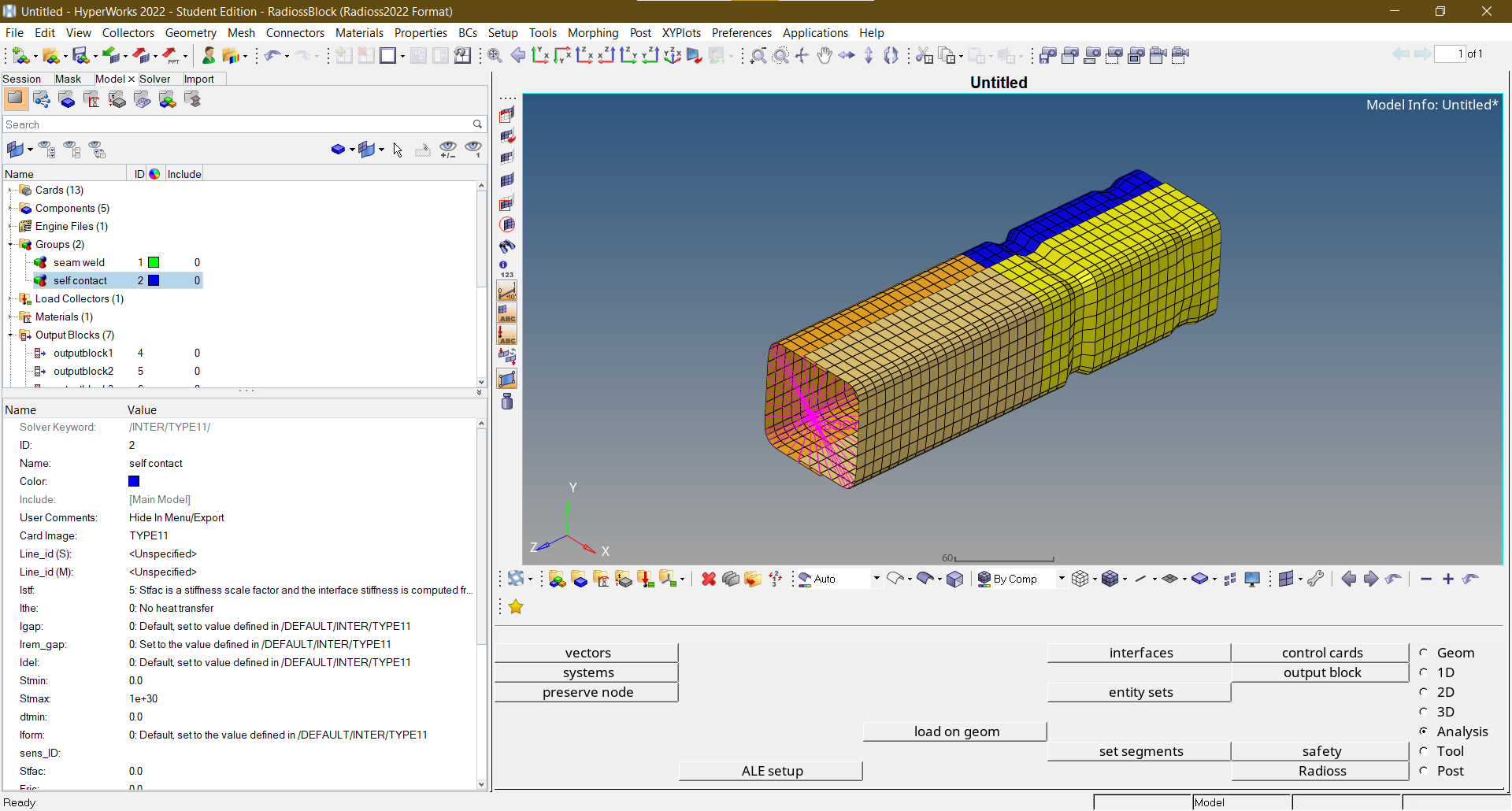
- This interface mimics the effect of lines or edges touching one another. A line can be made up of spring elements, shell edges, beams, or truss elements. The locking scenarios are resolved via interface TYPE11 in conjunction with interface TYPE7. Identified as the edges of the master and slave lines. There are impacts between the slave and master lines. One or more master lines may be impacted by a slave line. Both the master and the slave sides may have a line. Self-impact is made possible by this. Functions similarly to Type 7 in terms of defining gaps, formulating penalties, and search methods. Because it makes use of intricate mathematical techniques, it is strongly encouraged to only utilize it when essential. A large TYPE 11 interface may cause the computation to lag.
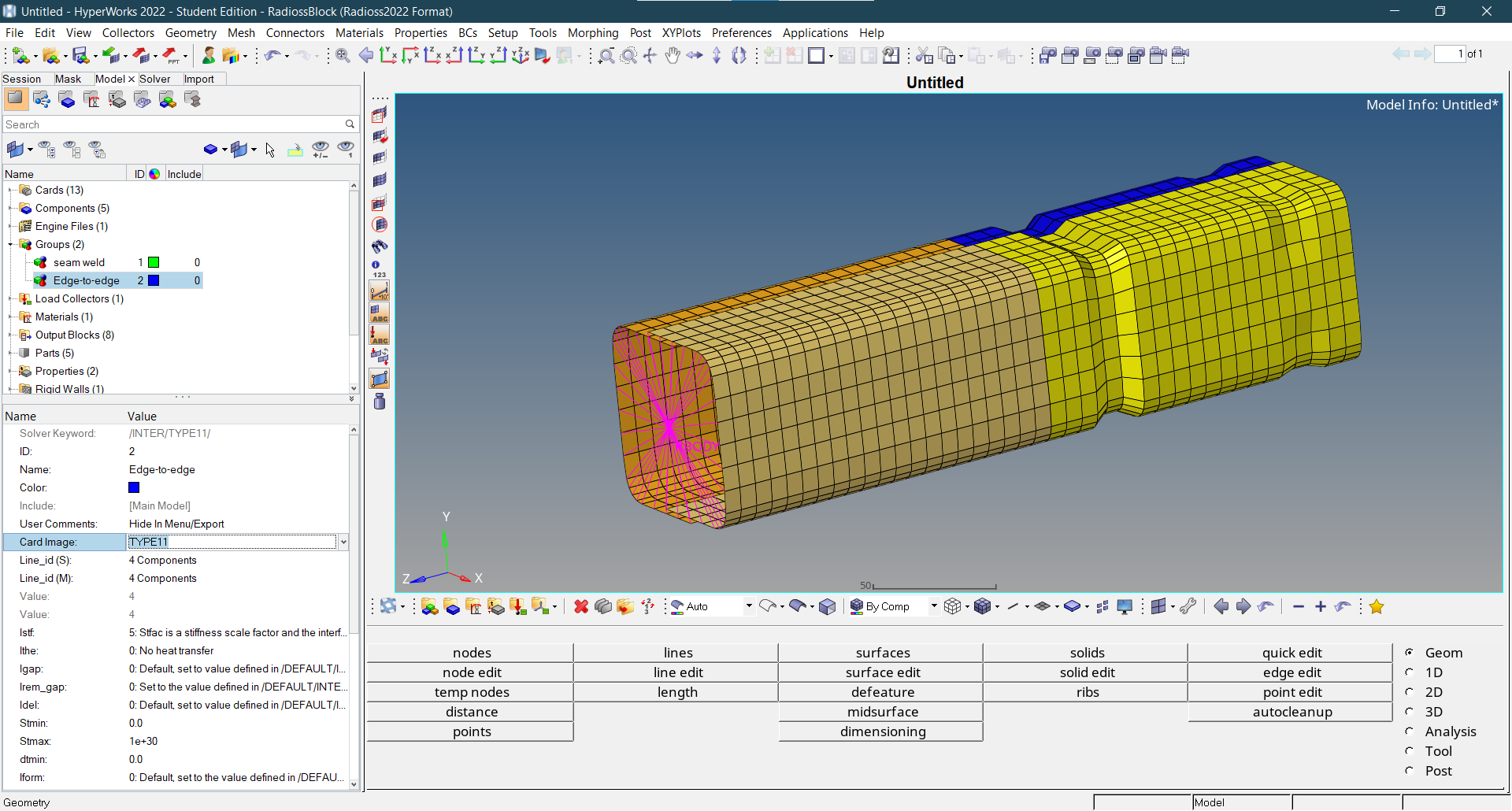
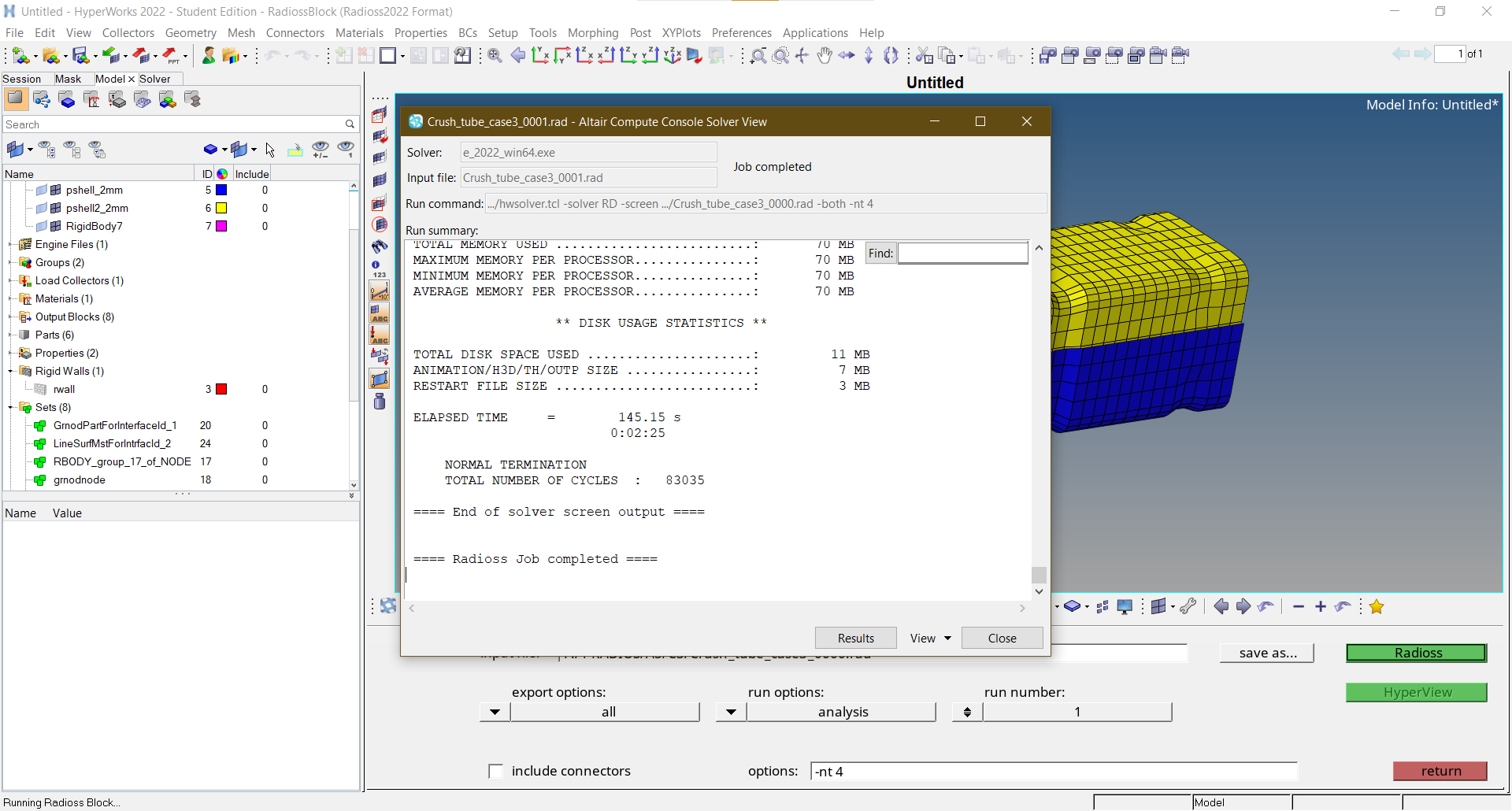
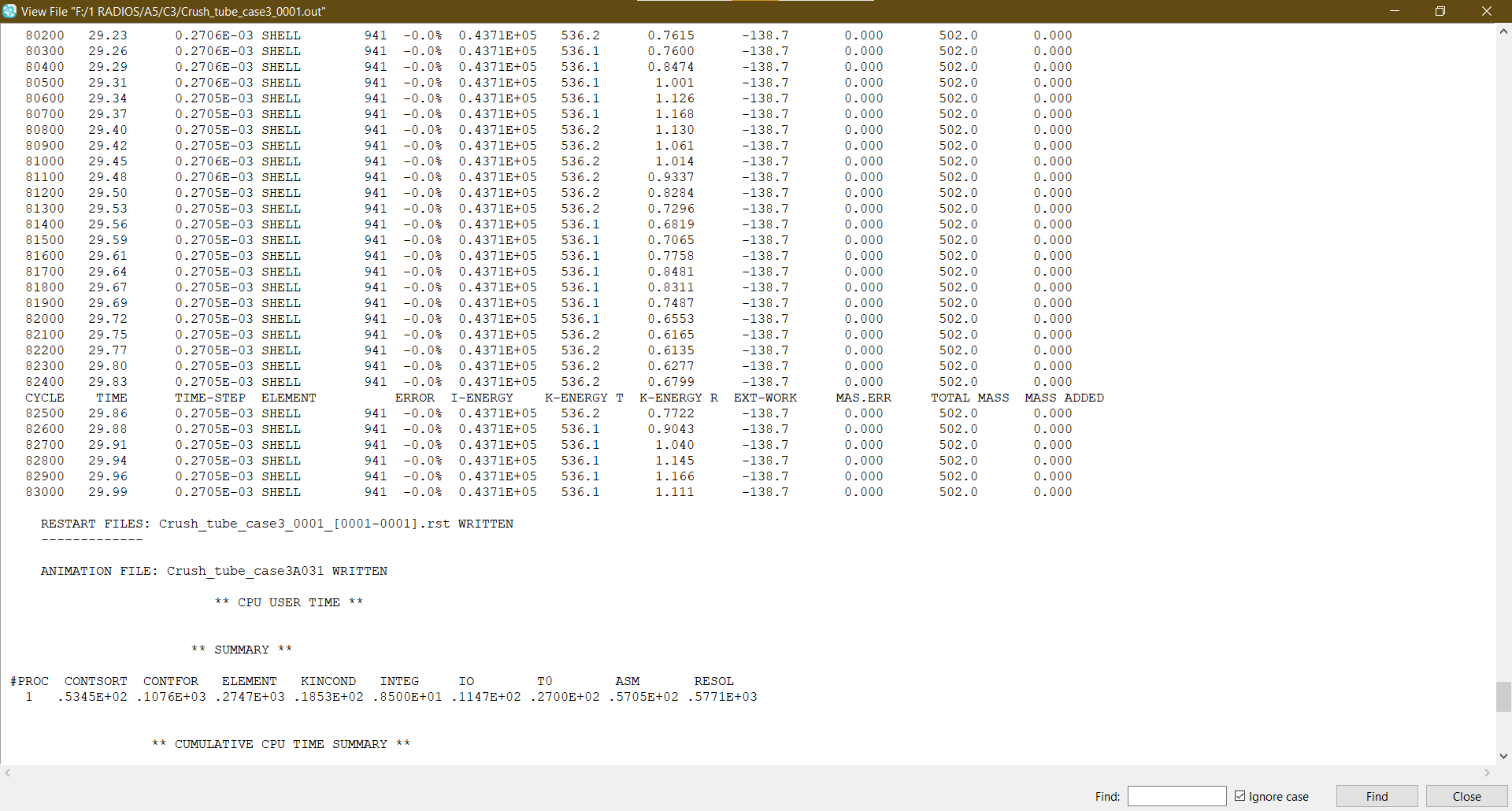
CASE 4:
- The case 3 radioss starter file is imported in this case. In this case, both notches and boundary conditions on the rigid body are removed.
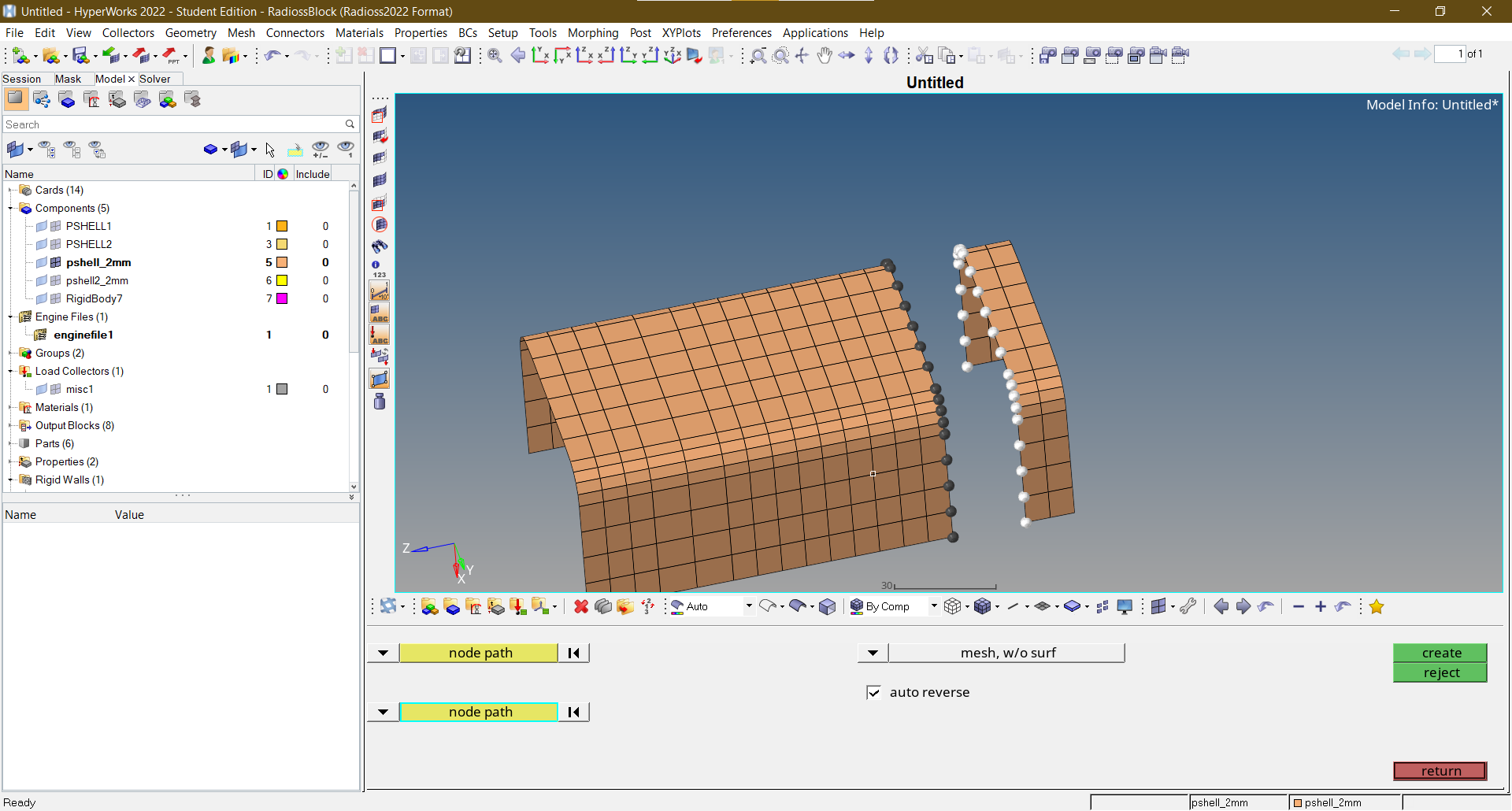
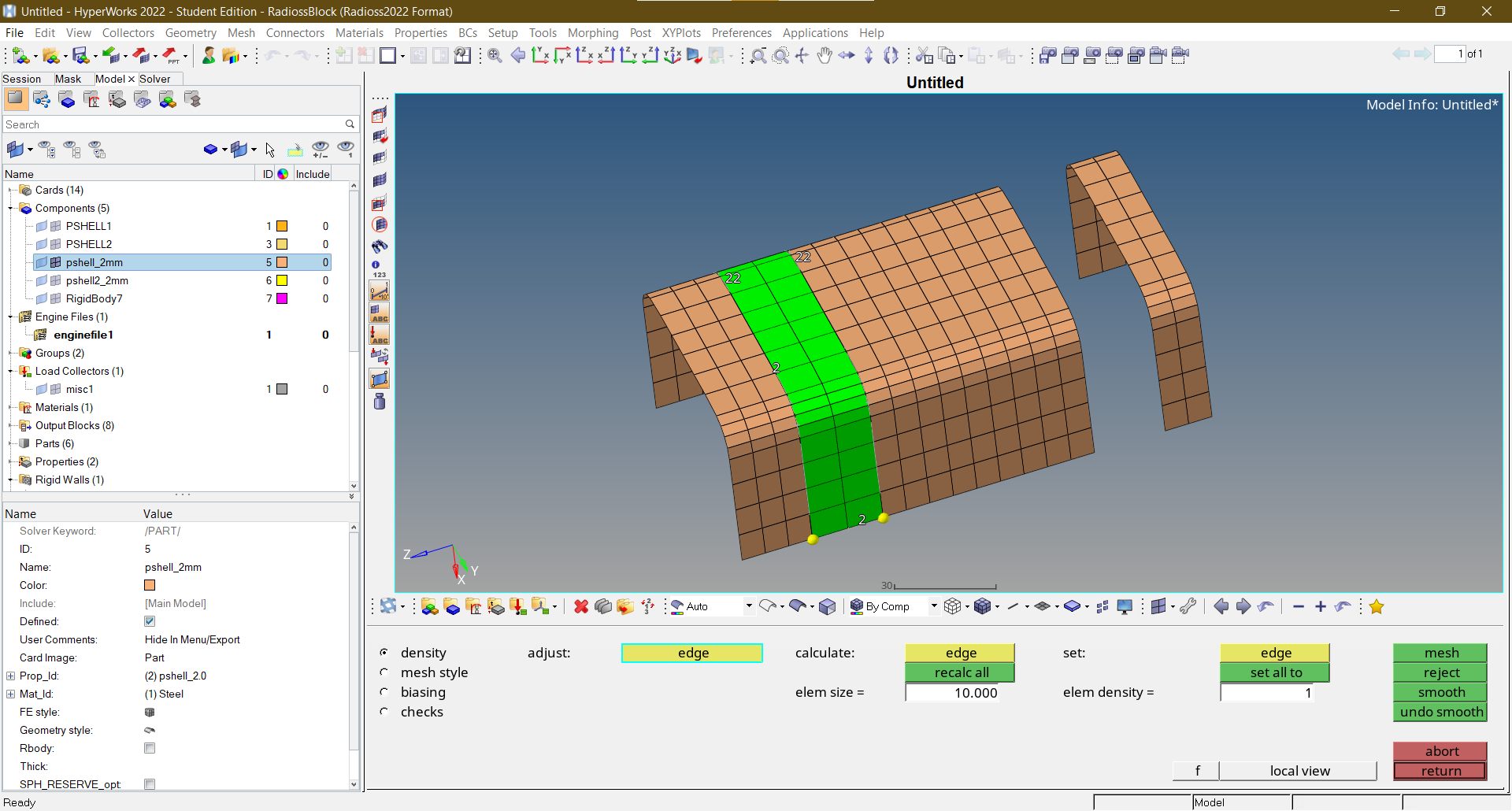
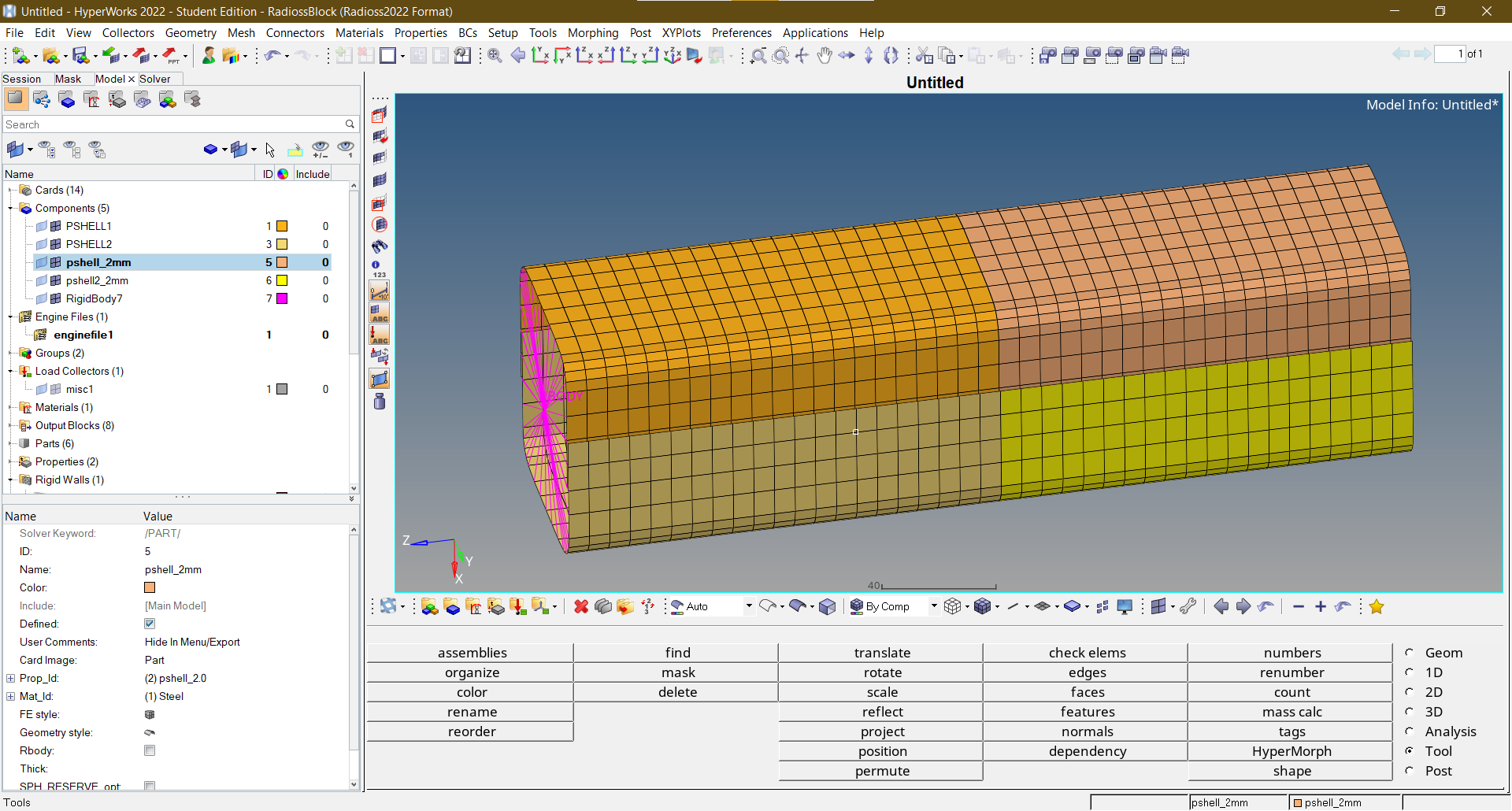
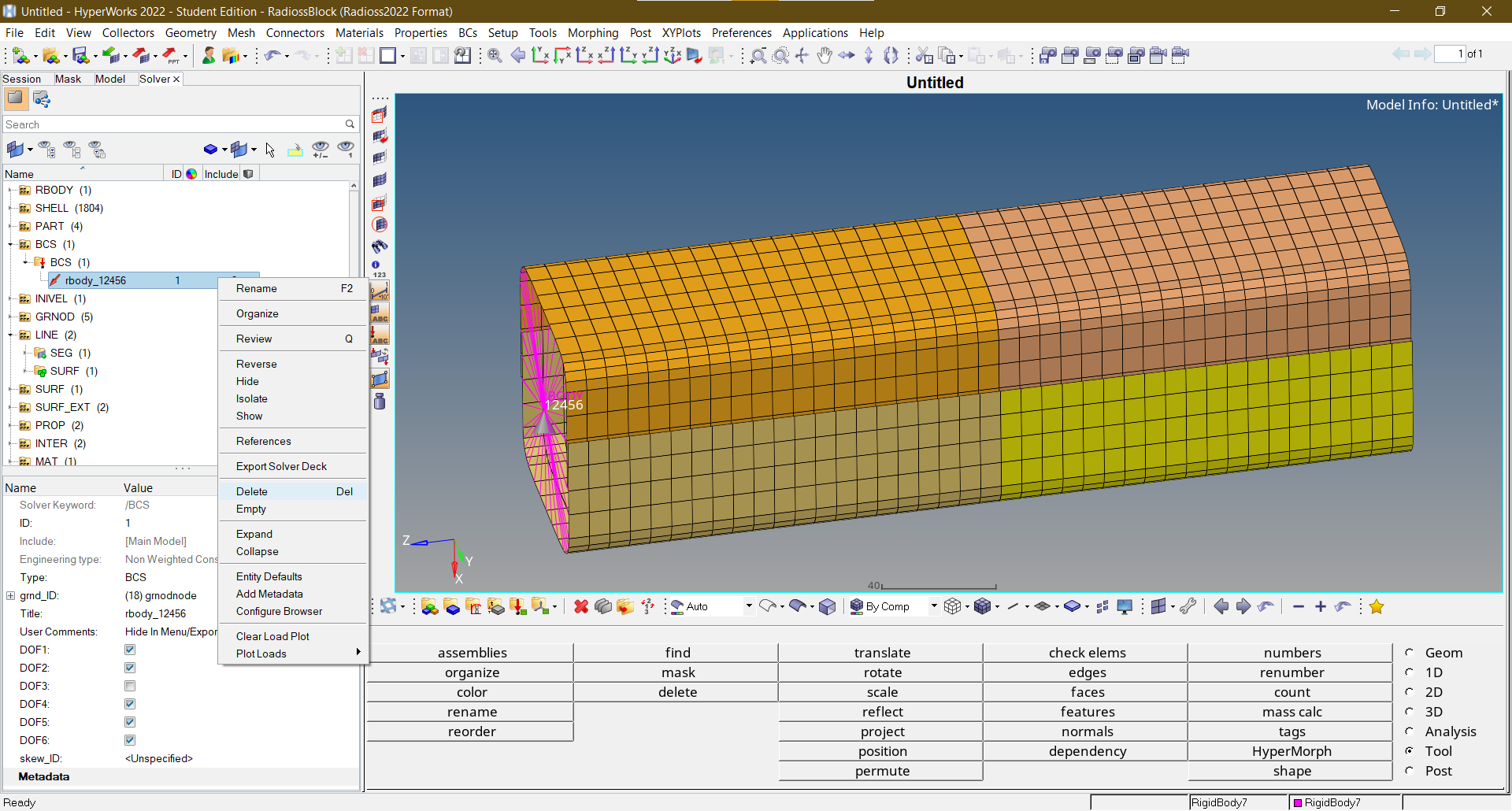
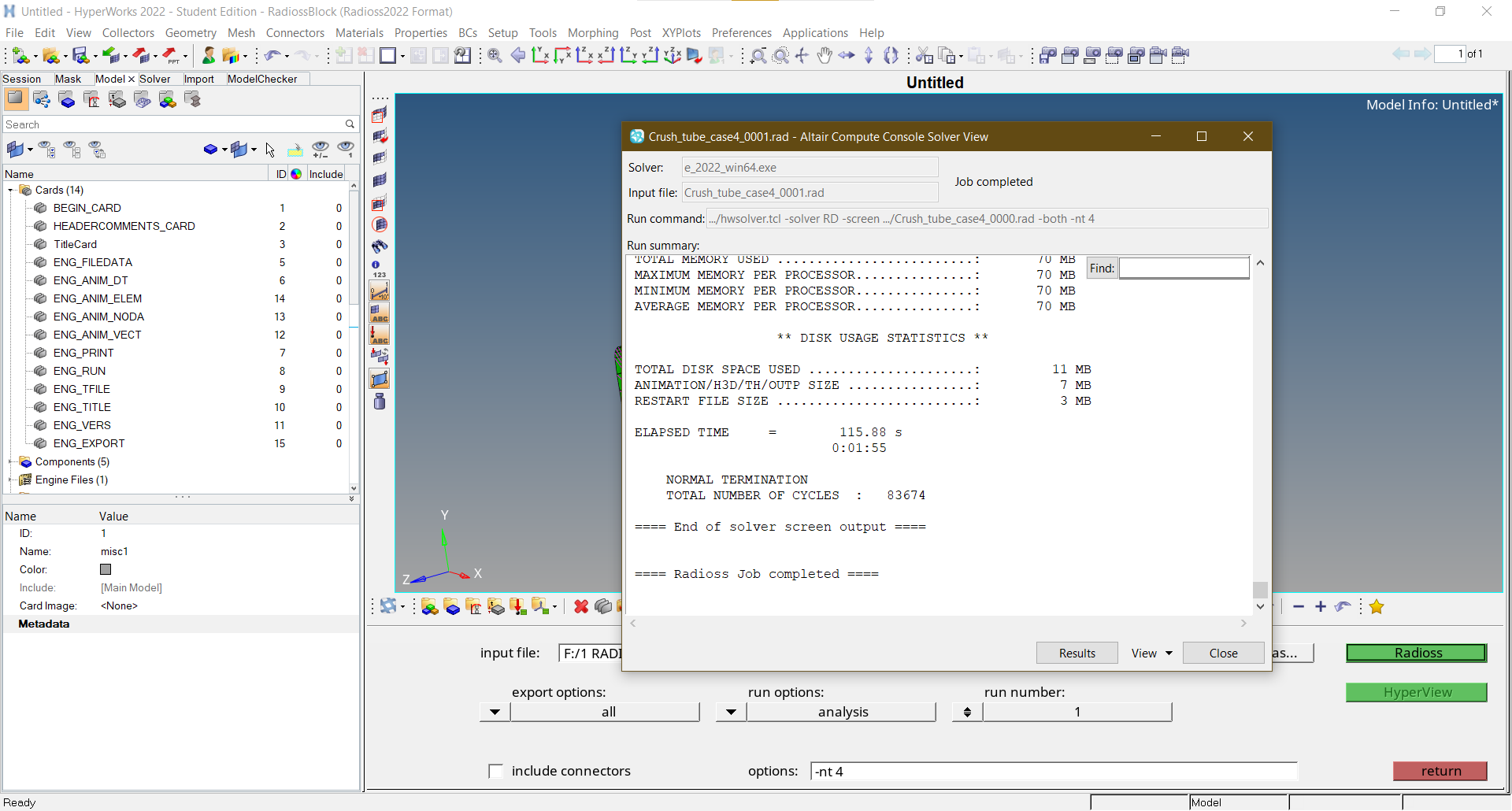
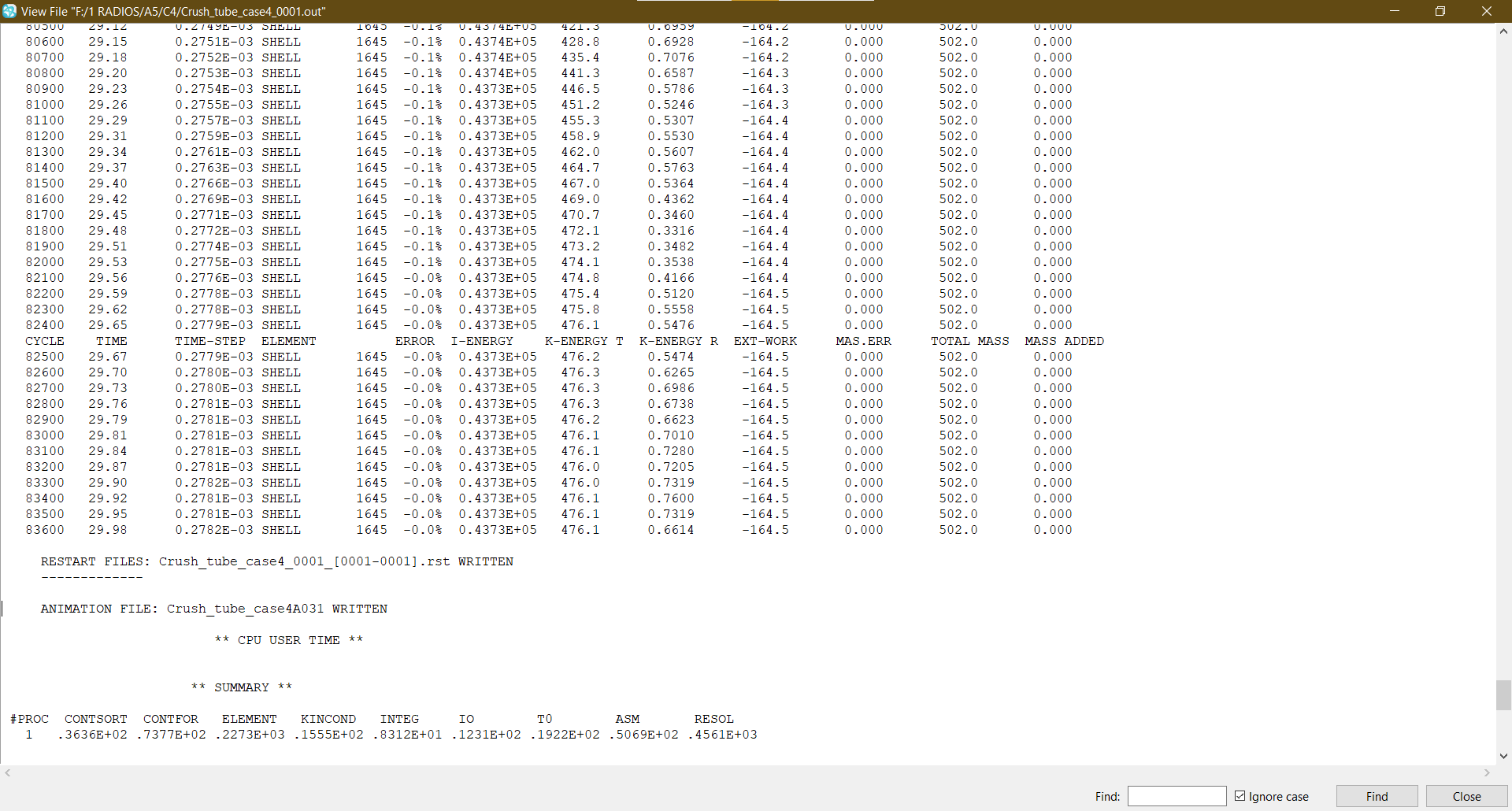
CASE 5:
- The case 4 radioss starter file is imported in this case. In this case, a notch is created in the middle of 4 connecting crash tube FEs. The element offset tool is used to perform this operation using significant height.
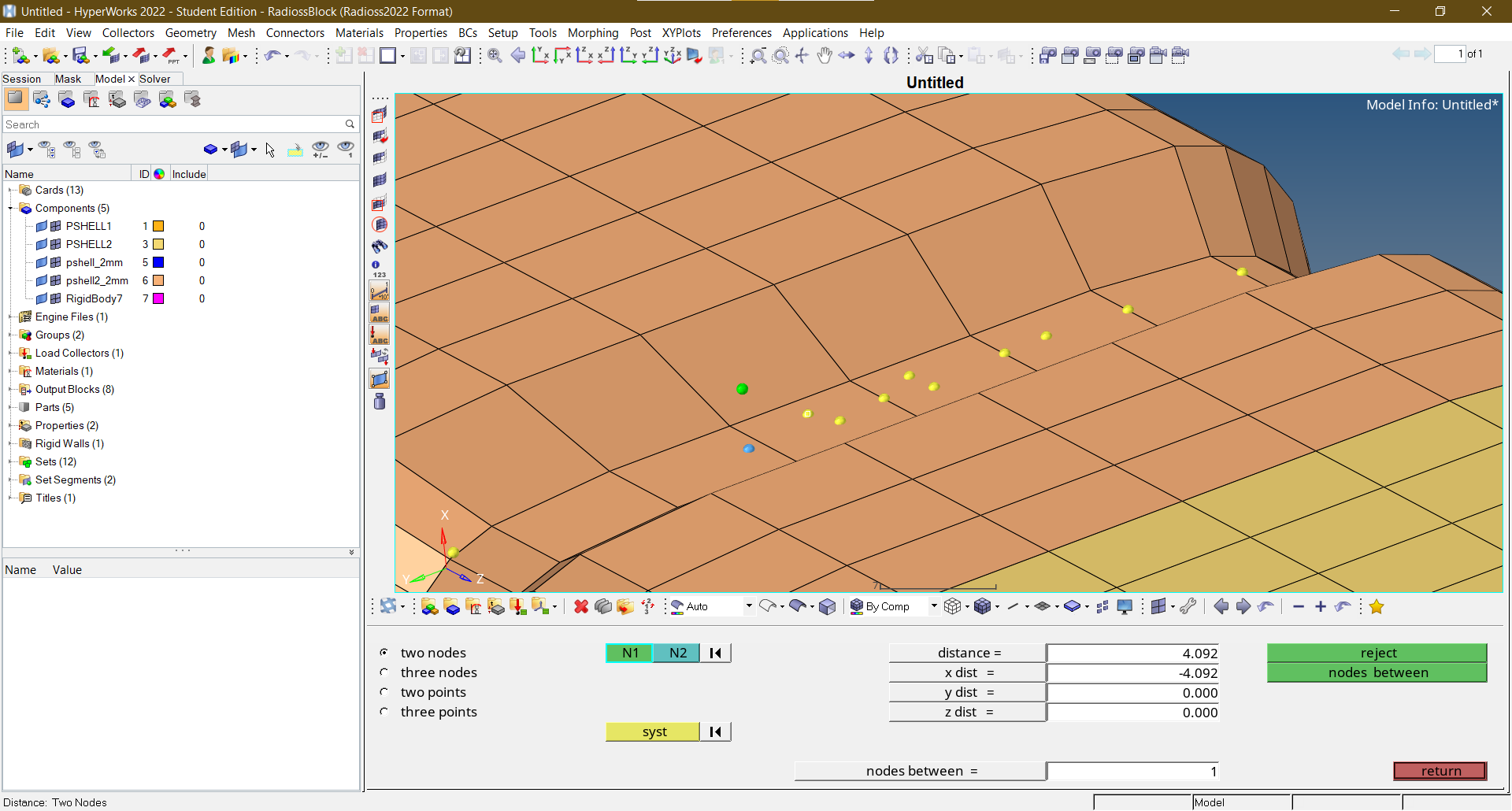
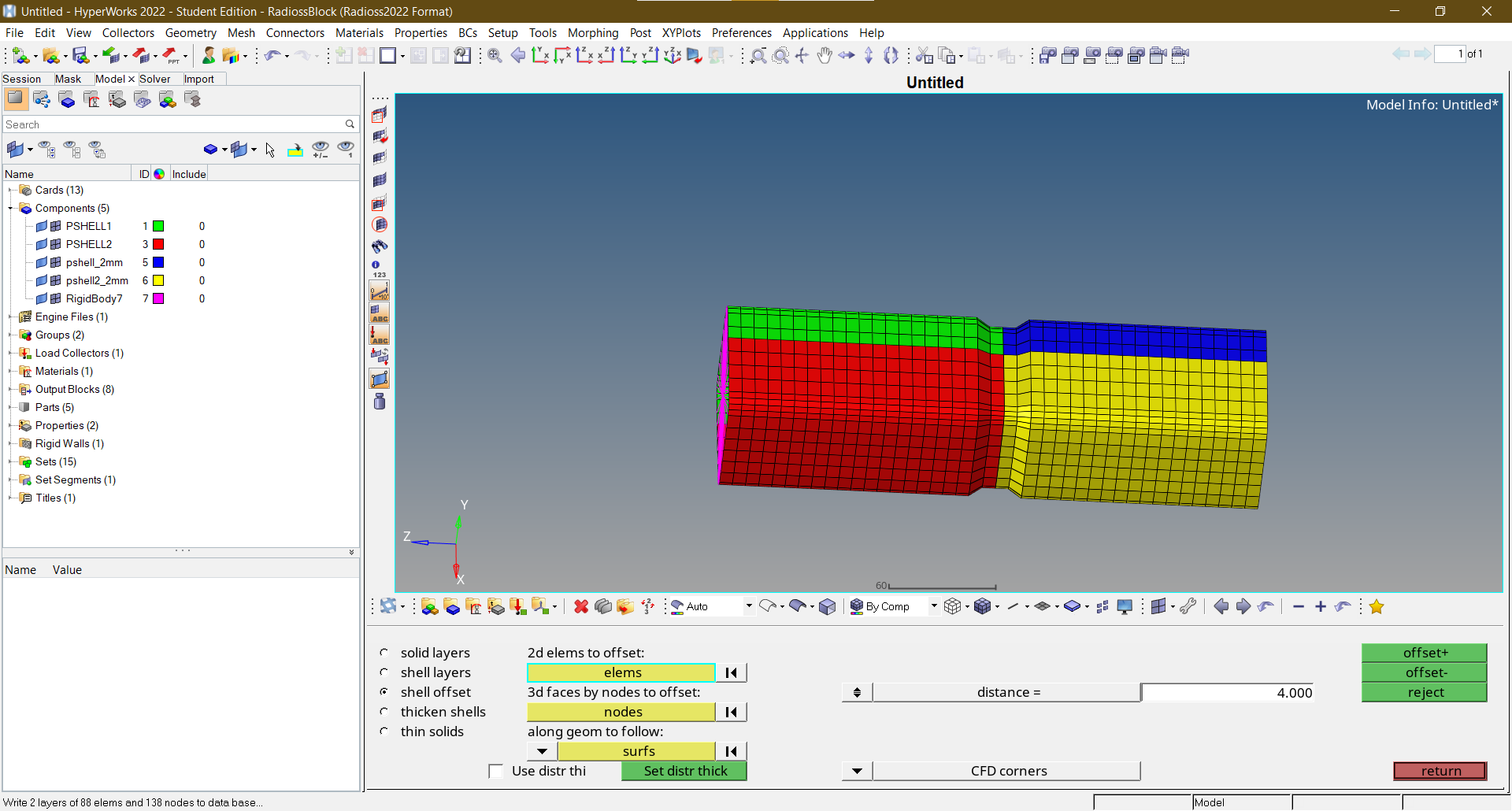
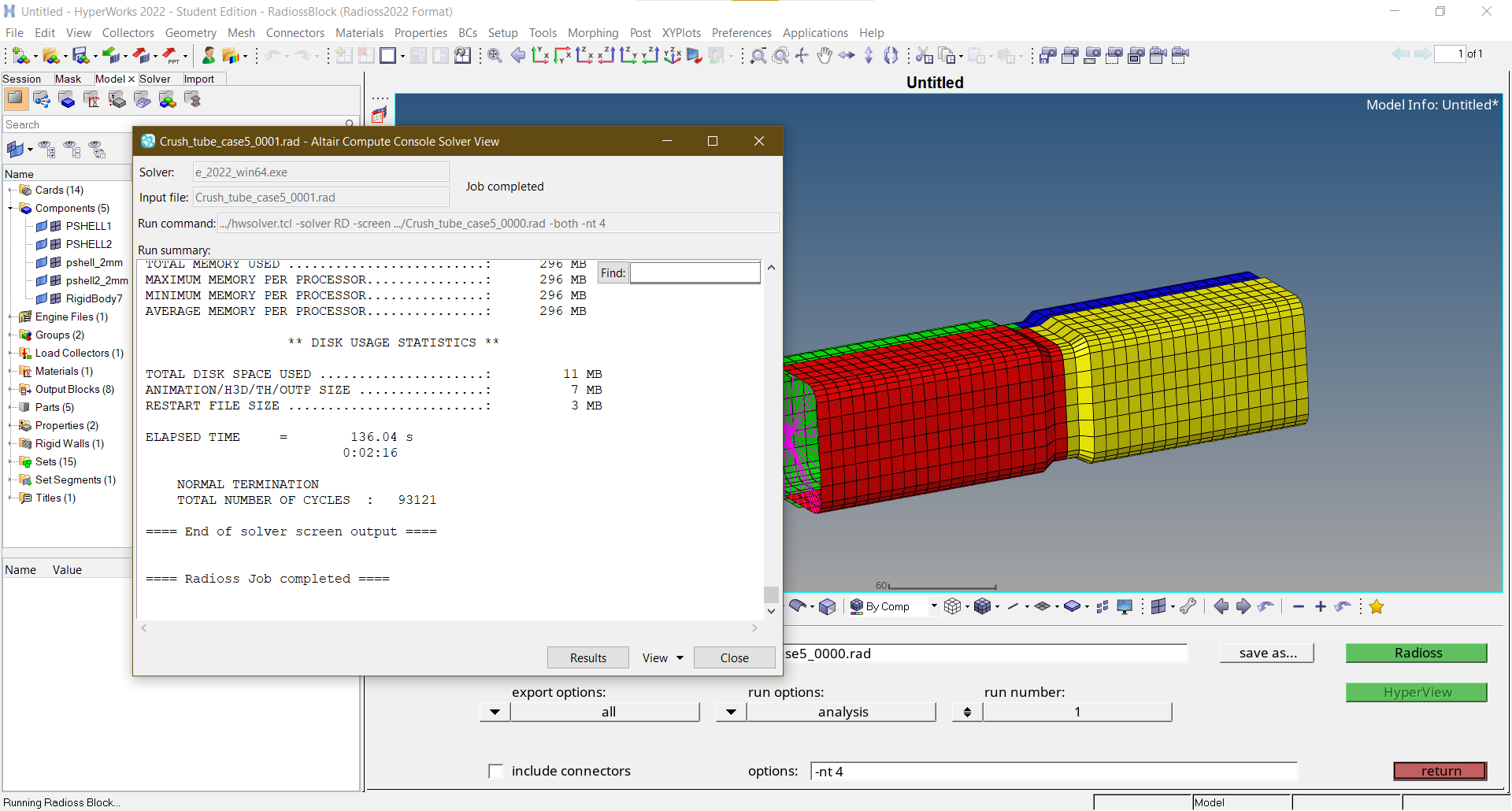
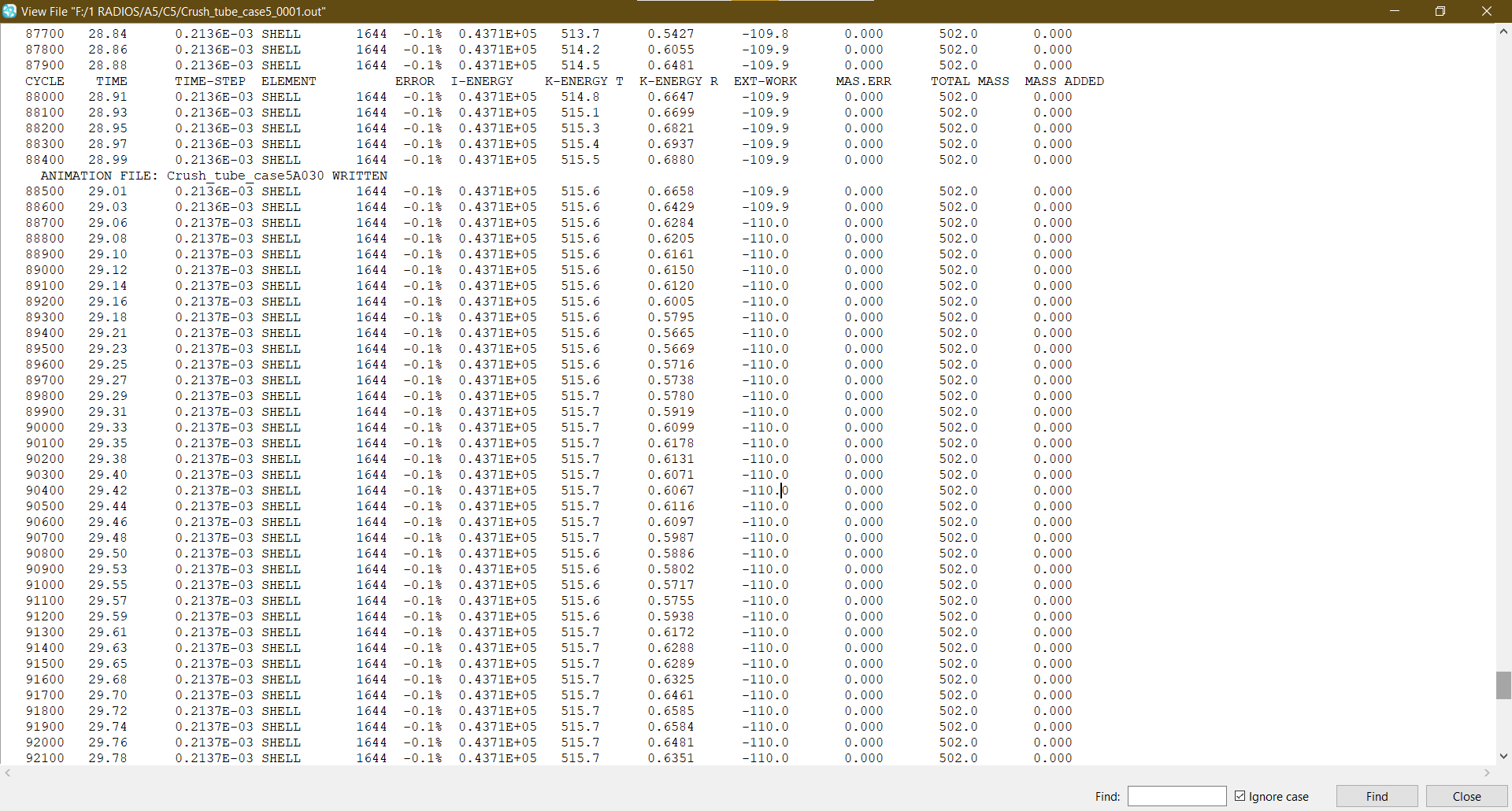
CASE 6:
- The case 5 radioss starter file is imported in this case. In this case, a notch is created with nodes only from opposite face.
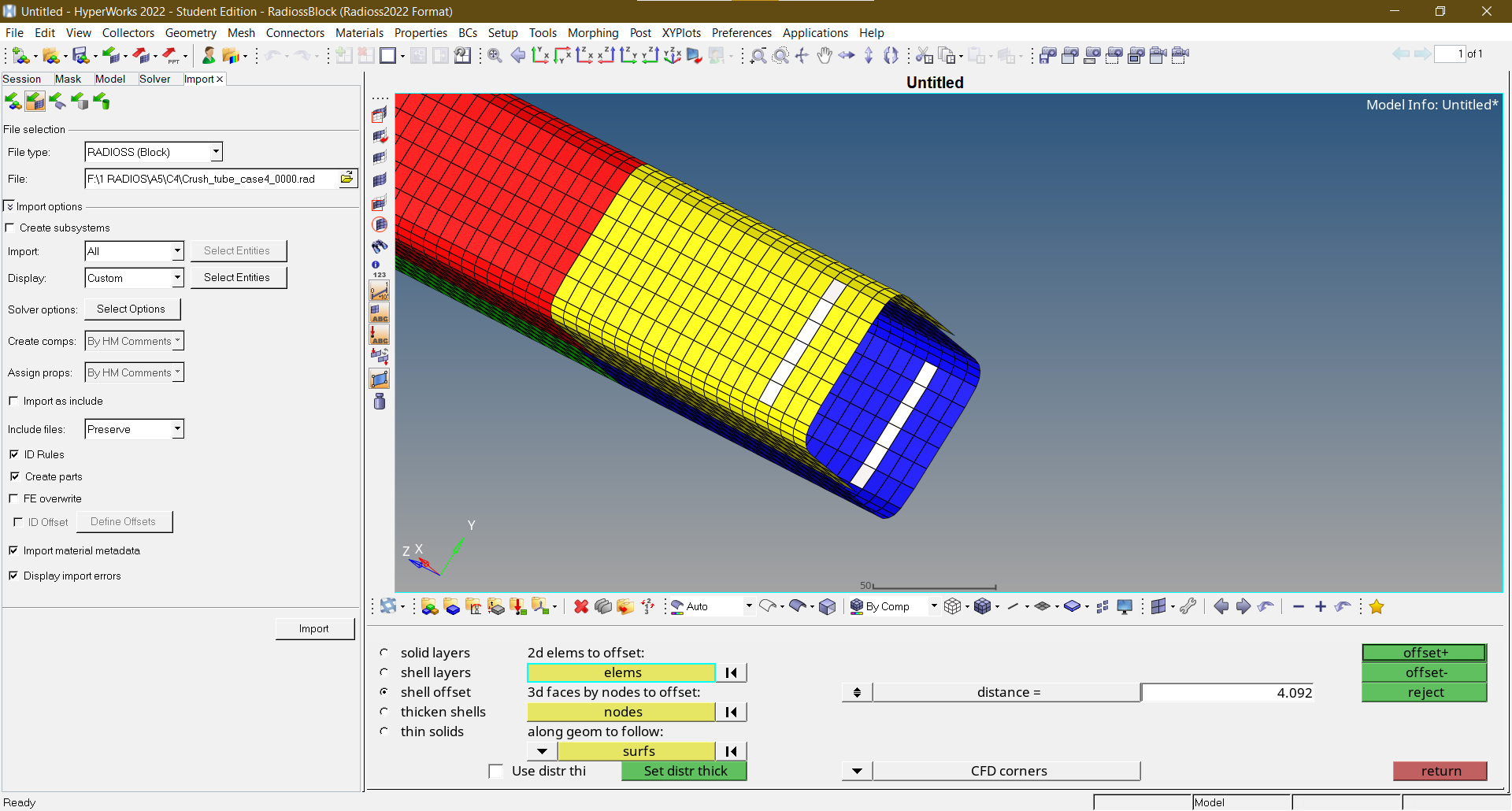
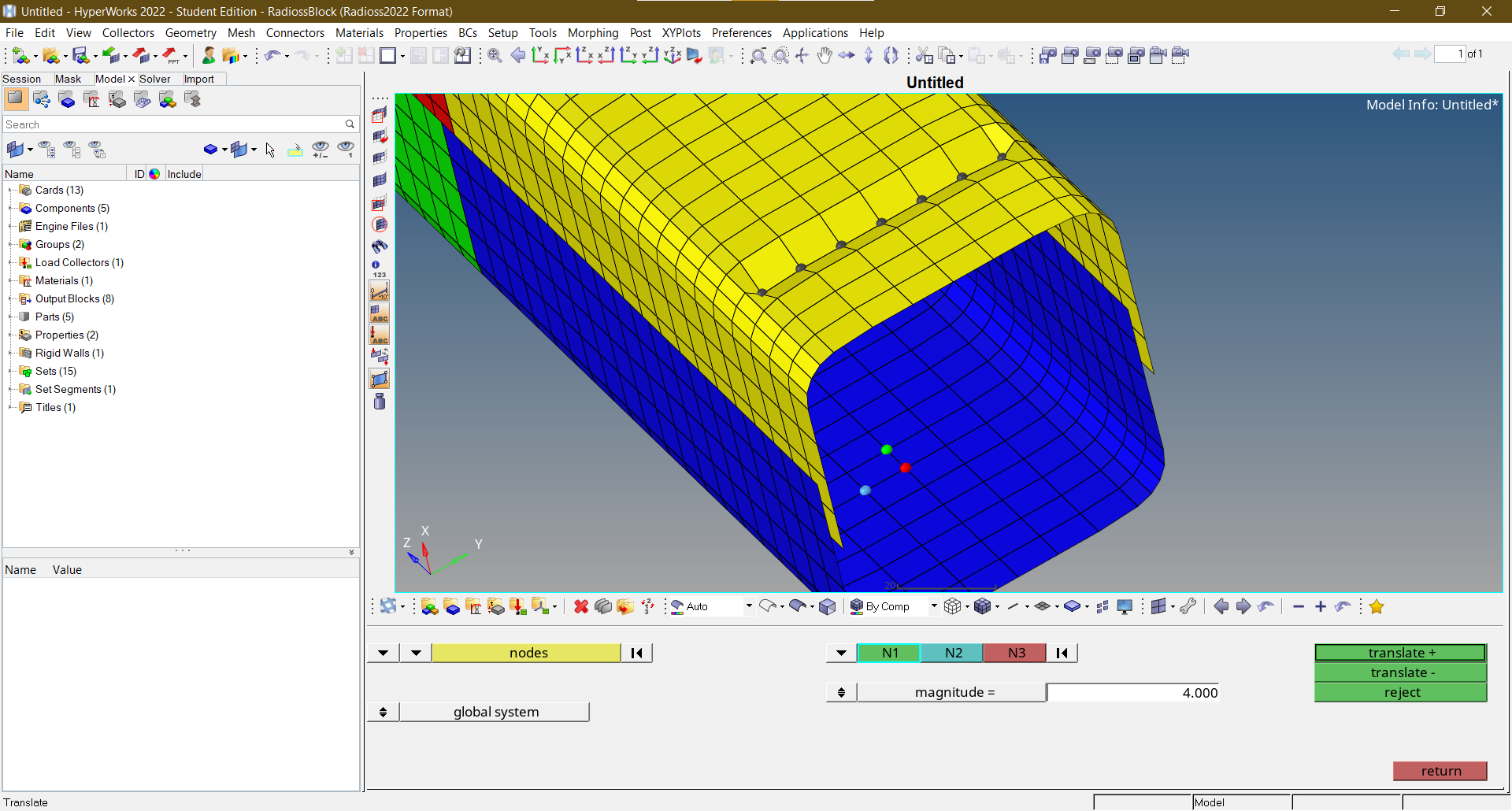
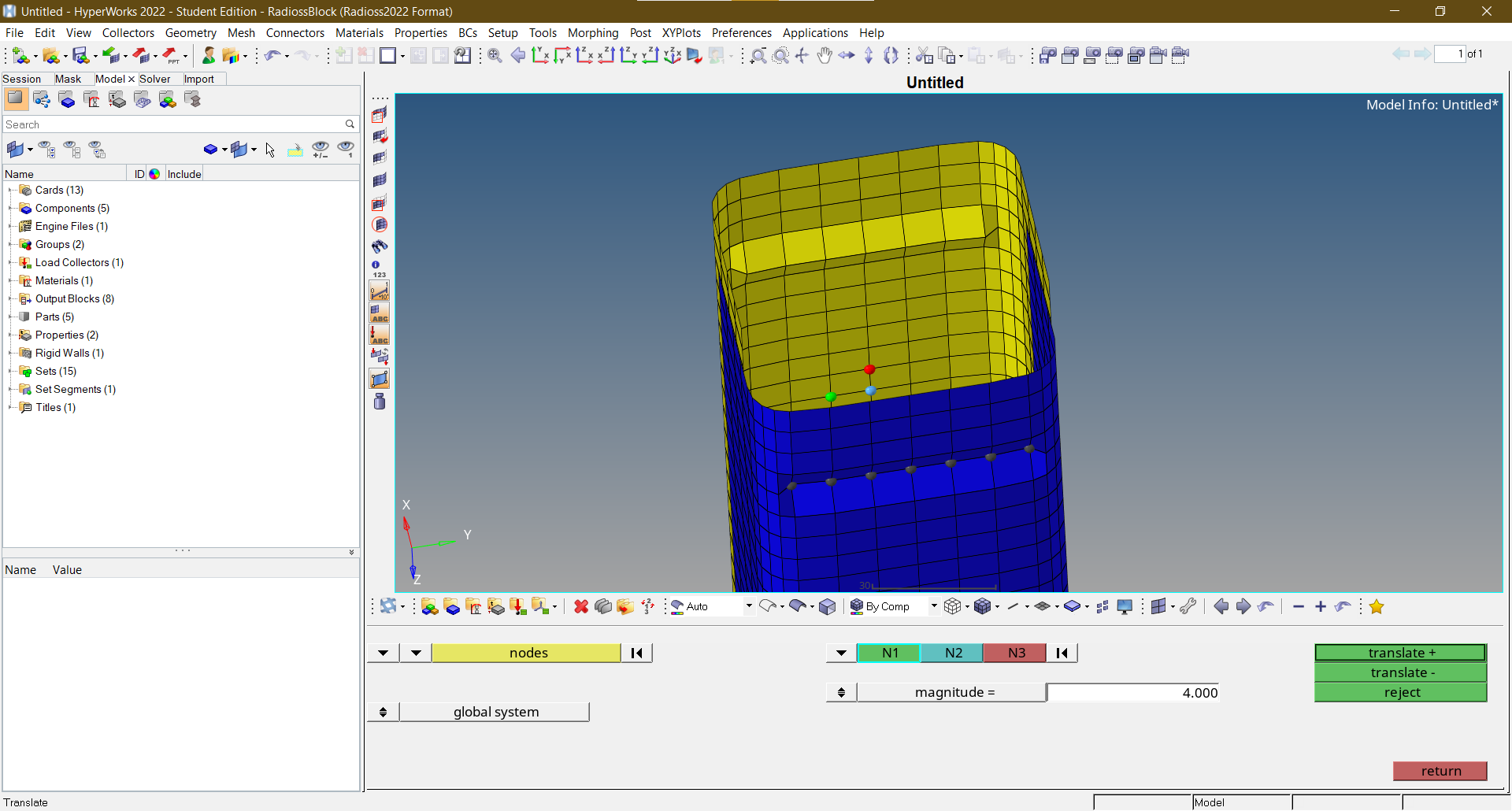
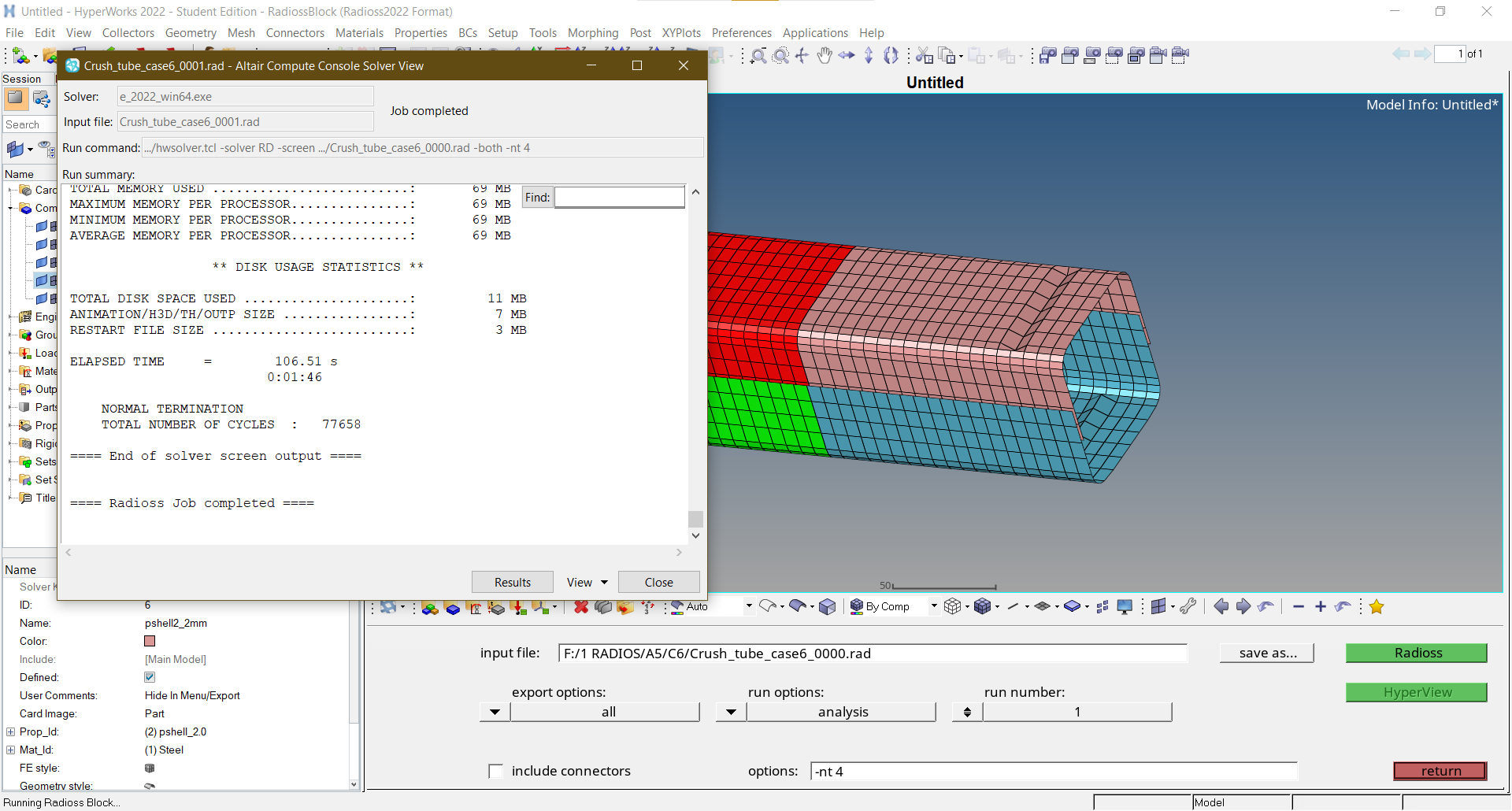
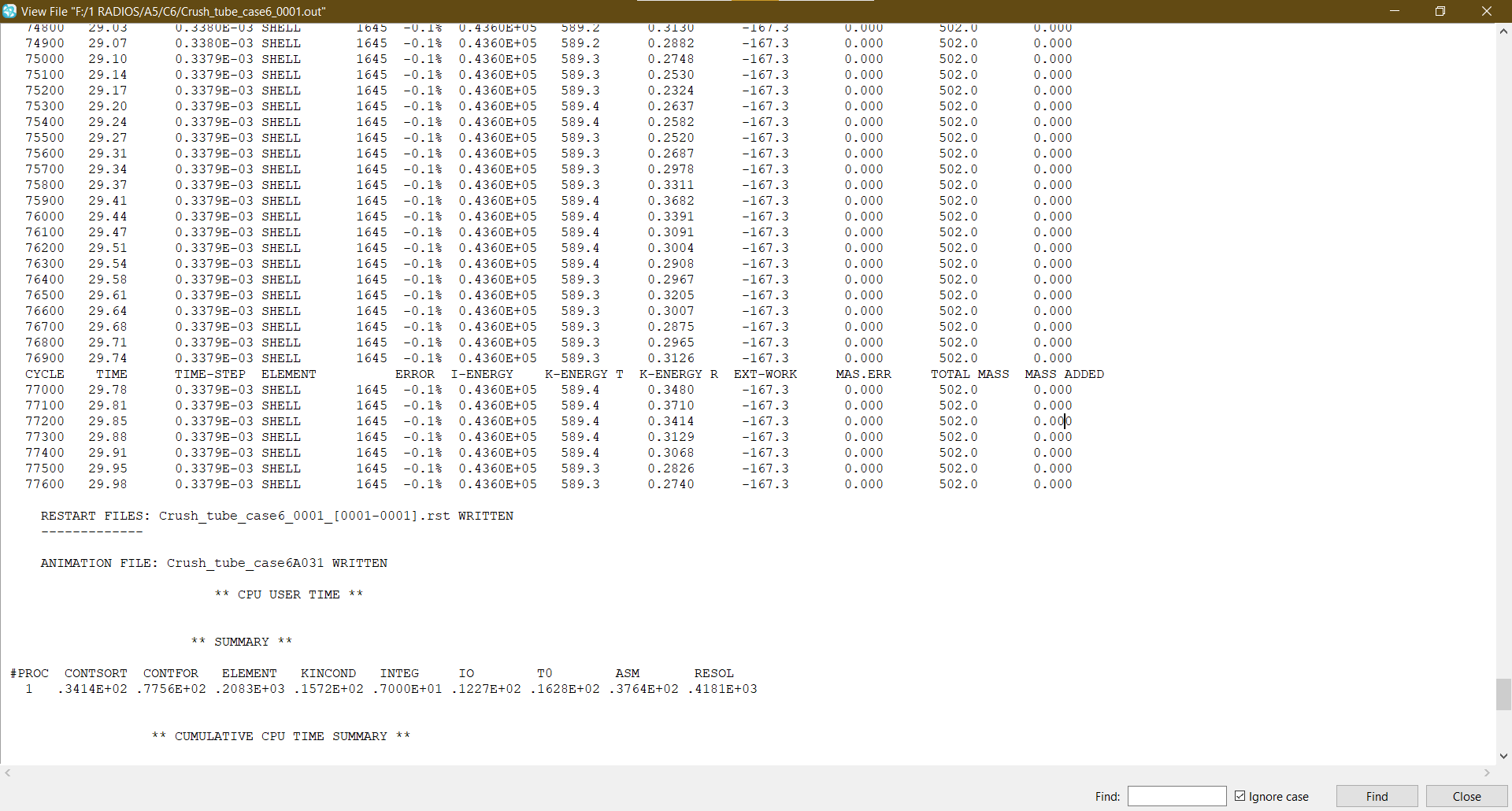
RESULTS
CASE 1:
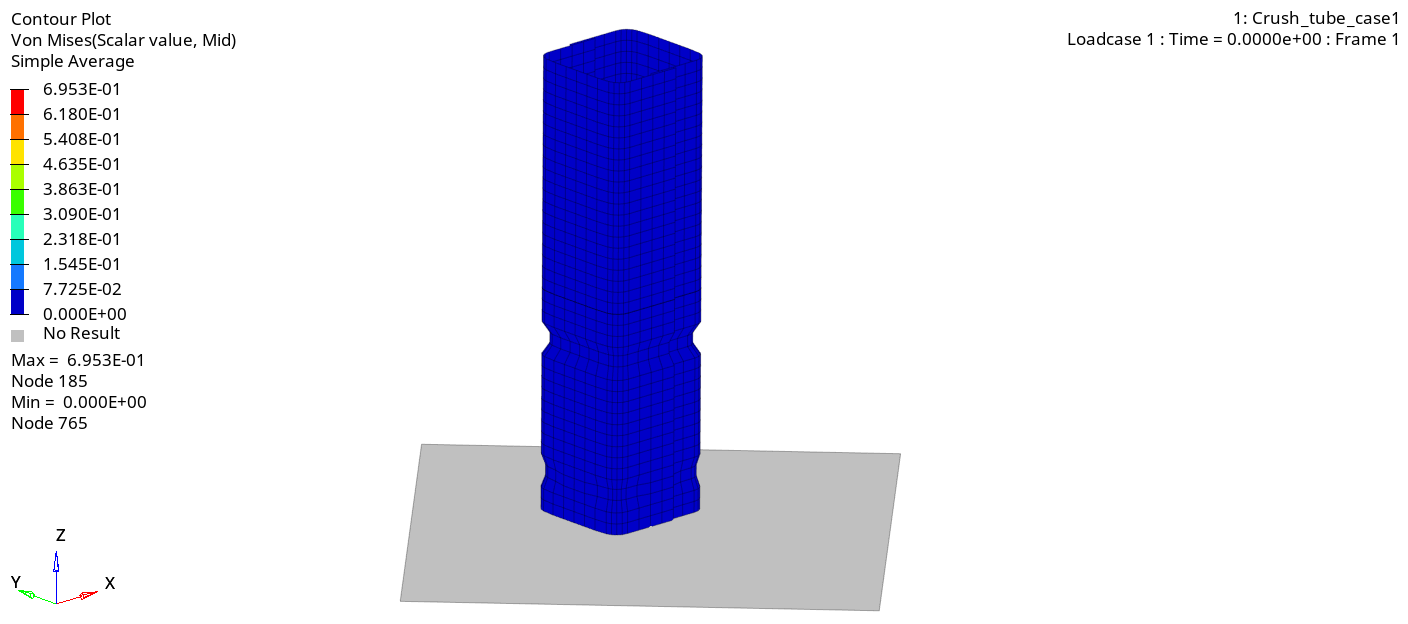
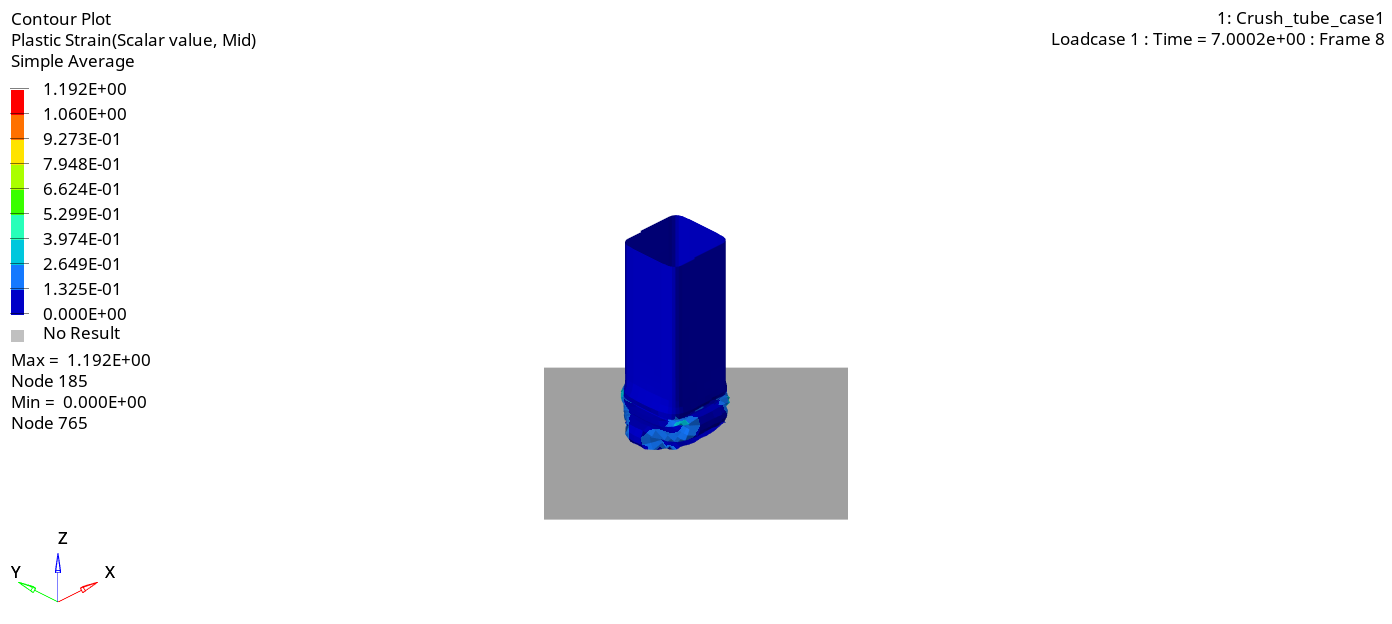
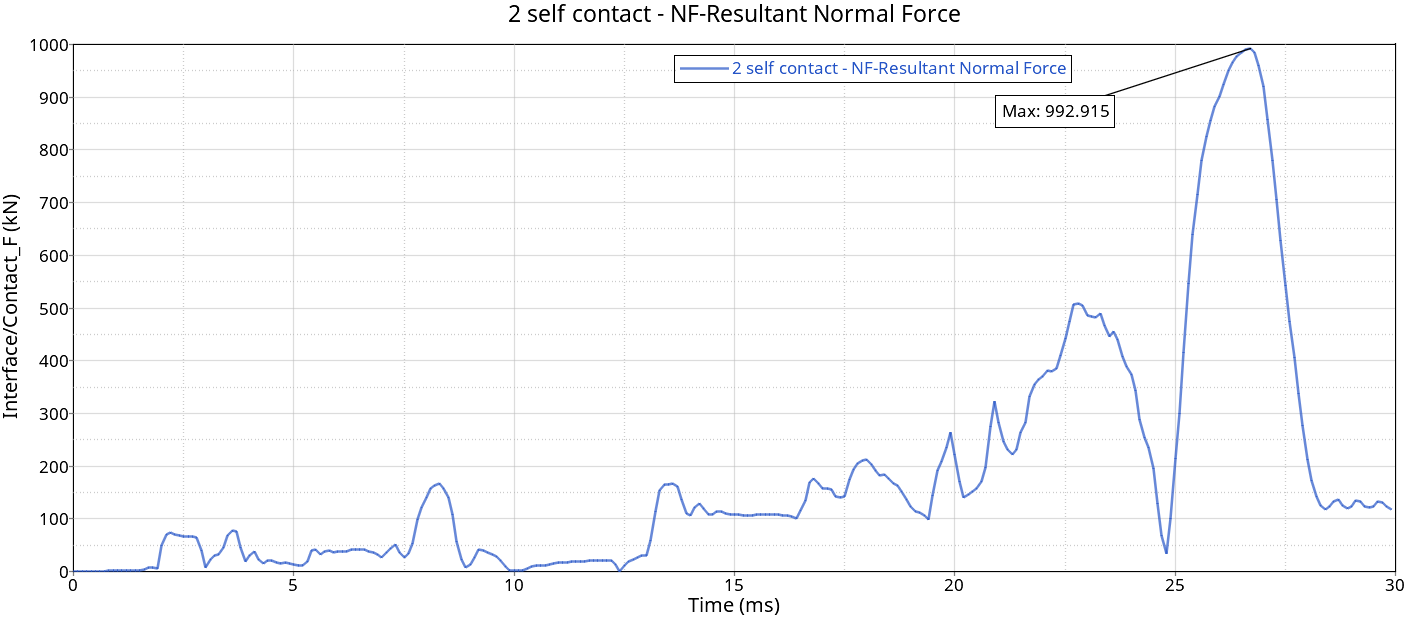
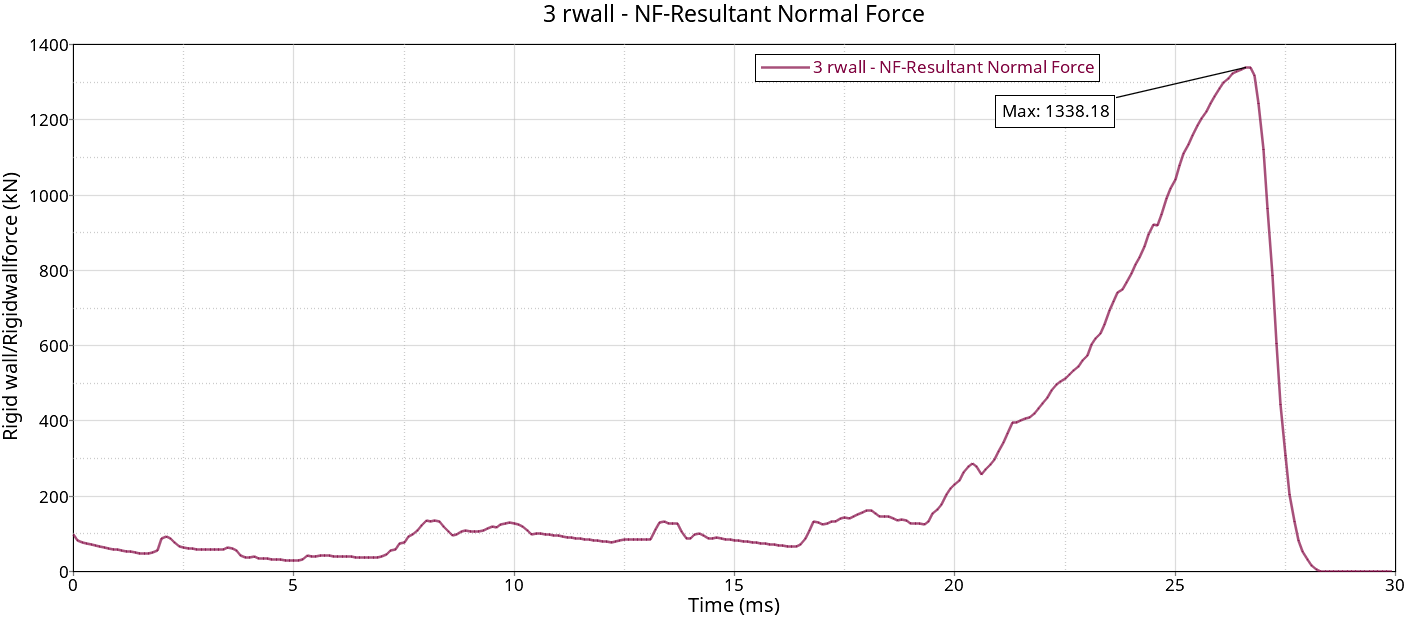

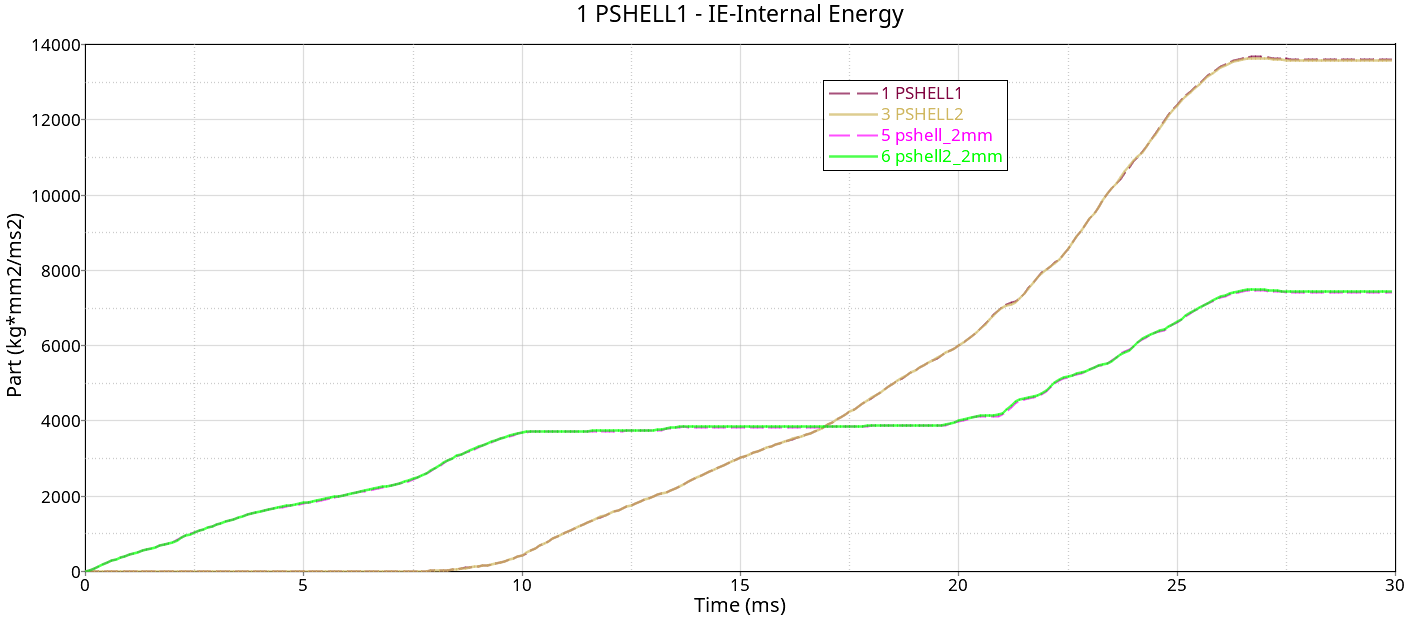
CASE 2:
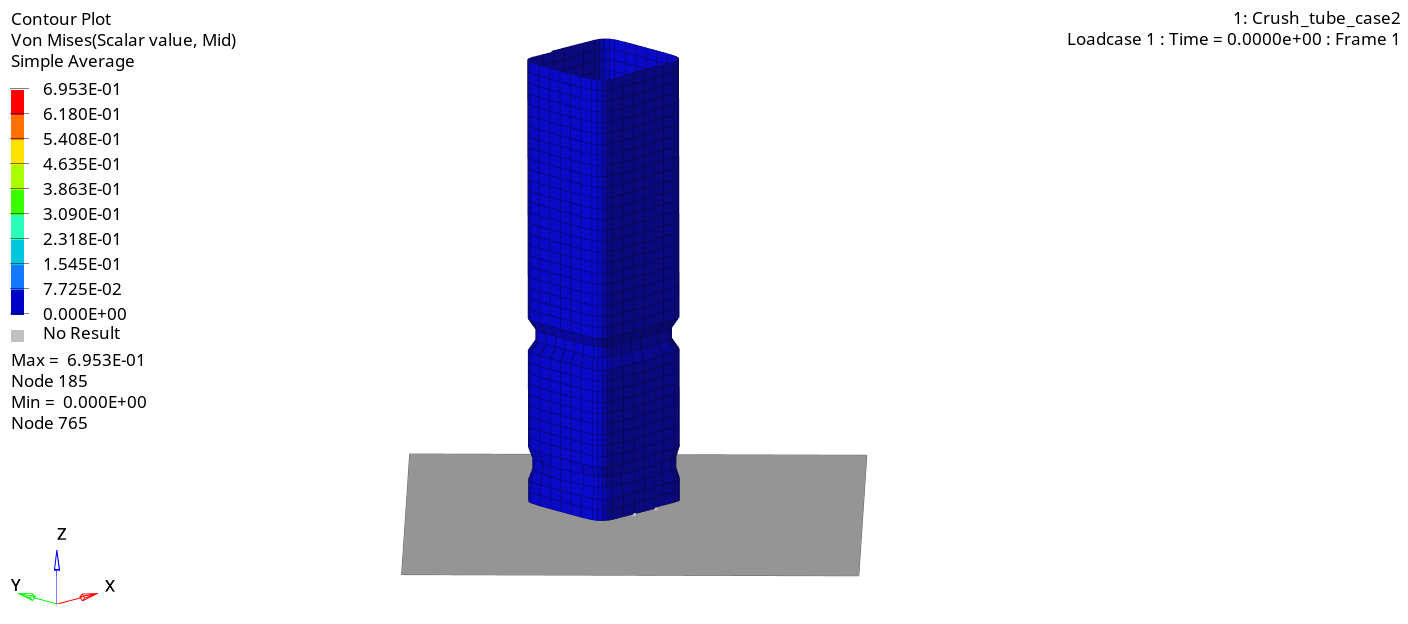
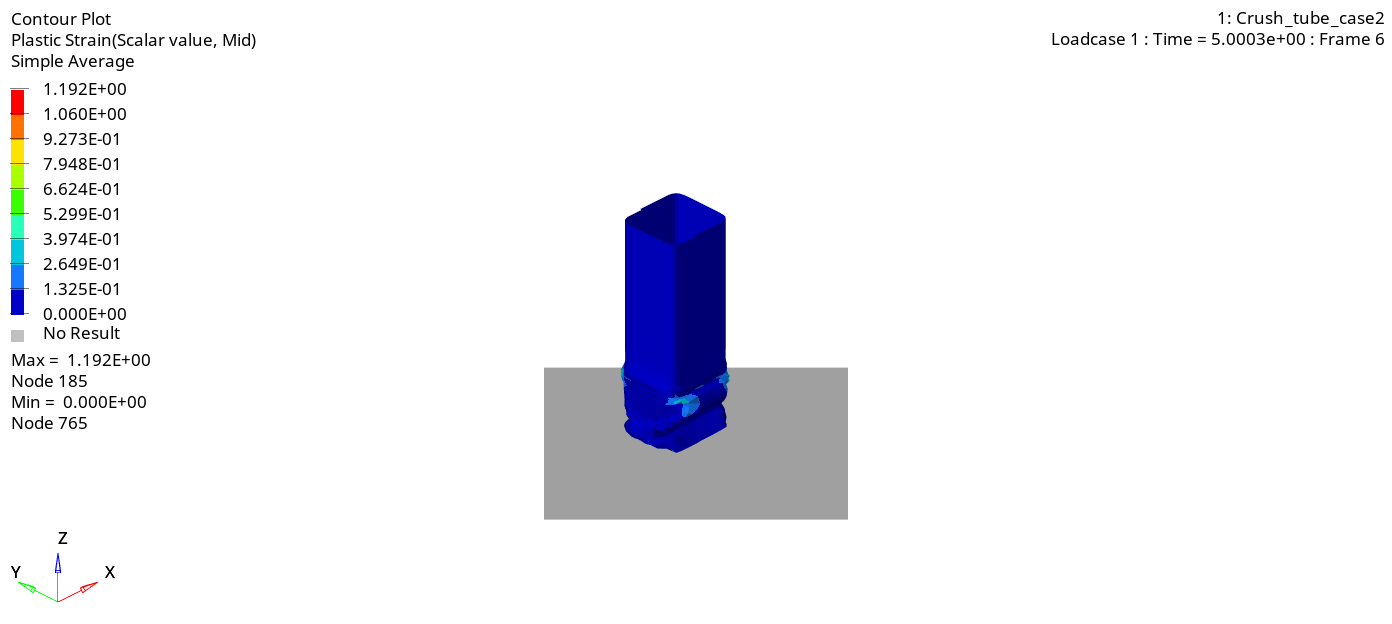
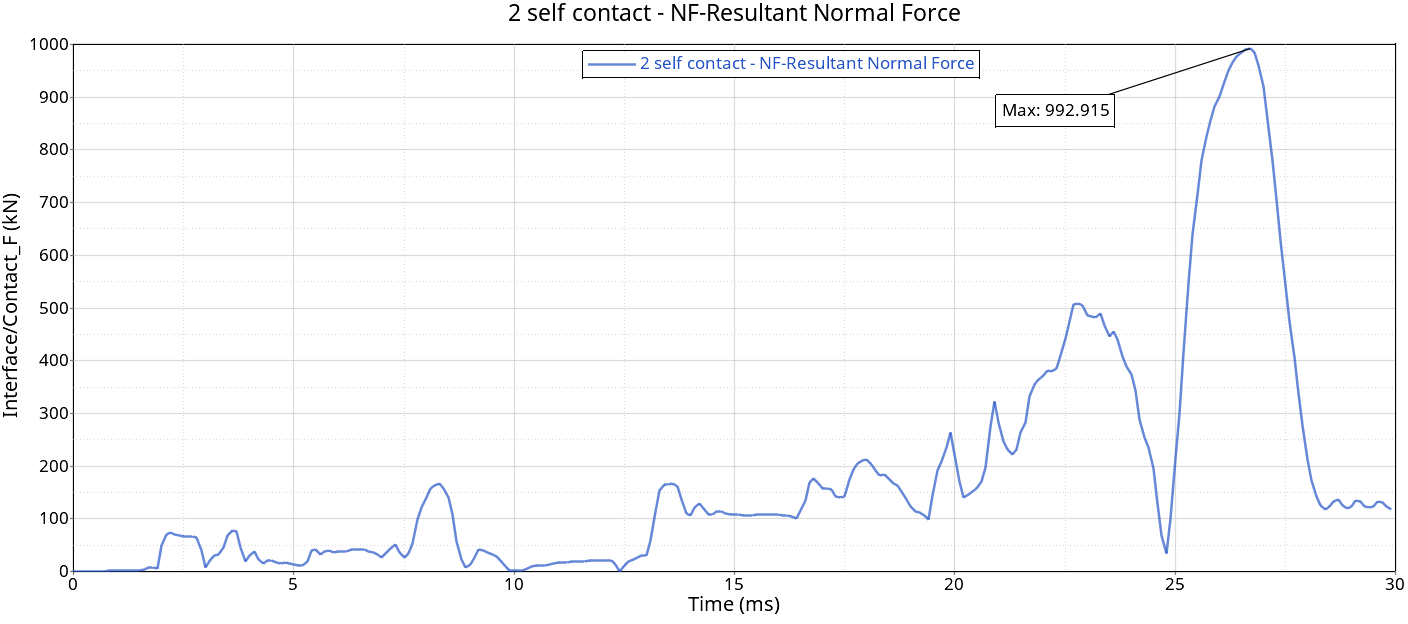
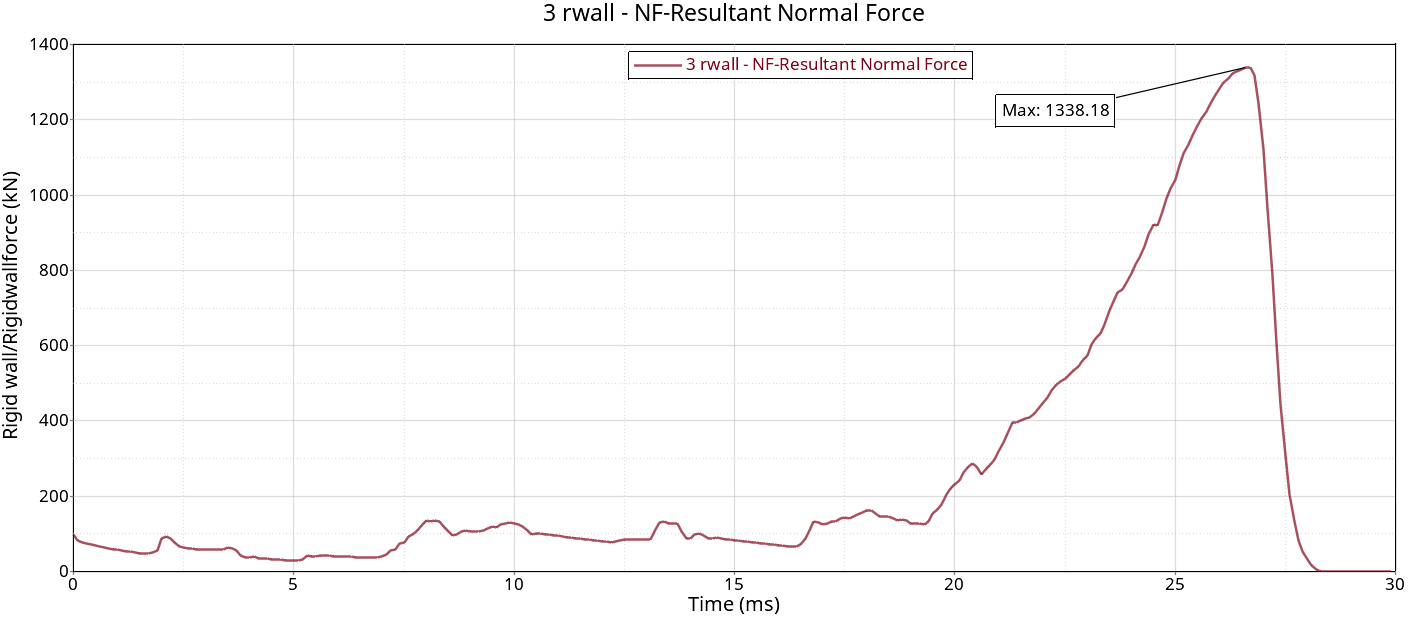
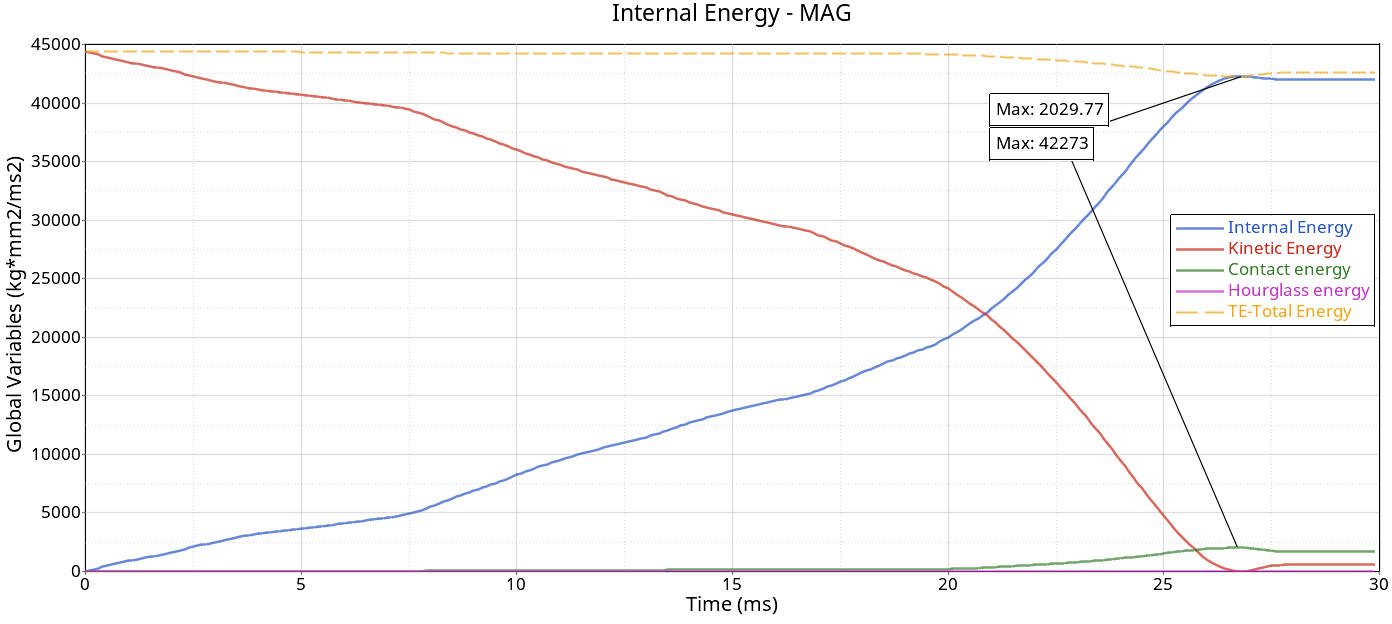
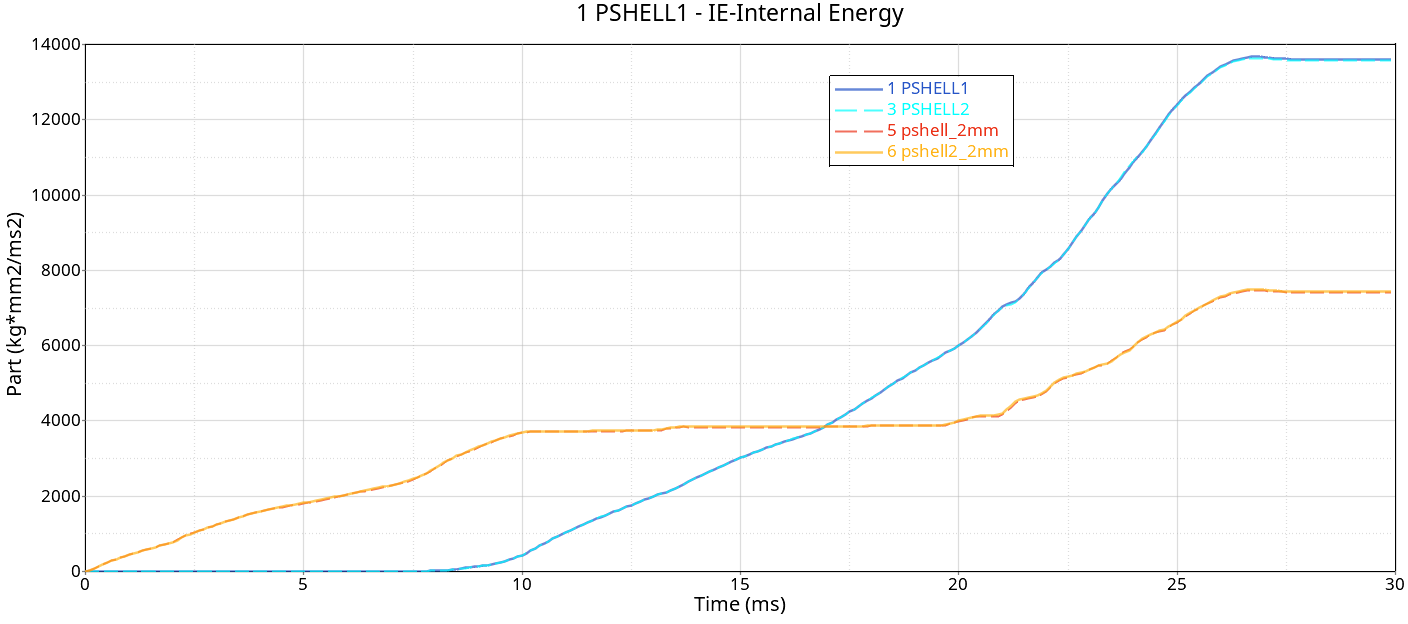
CASE 3:
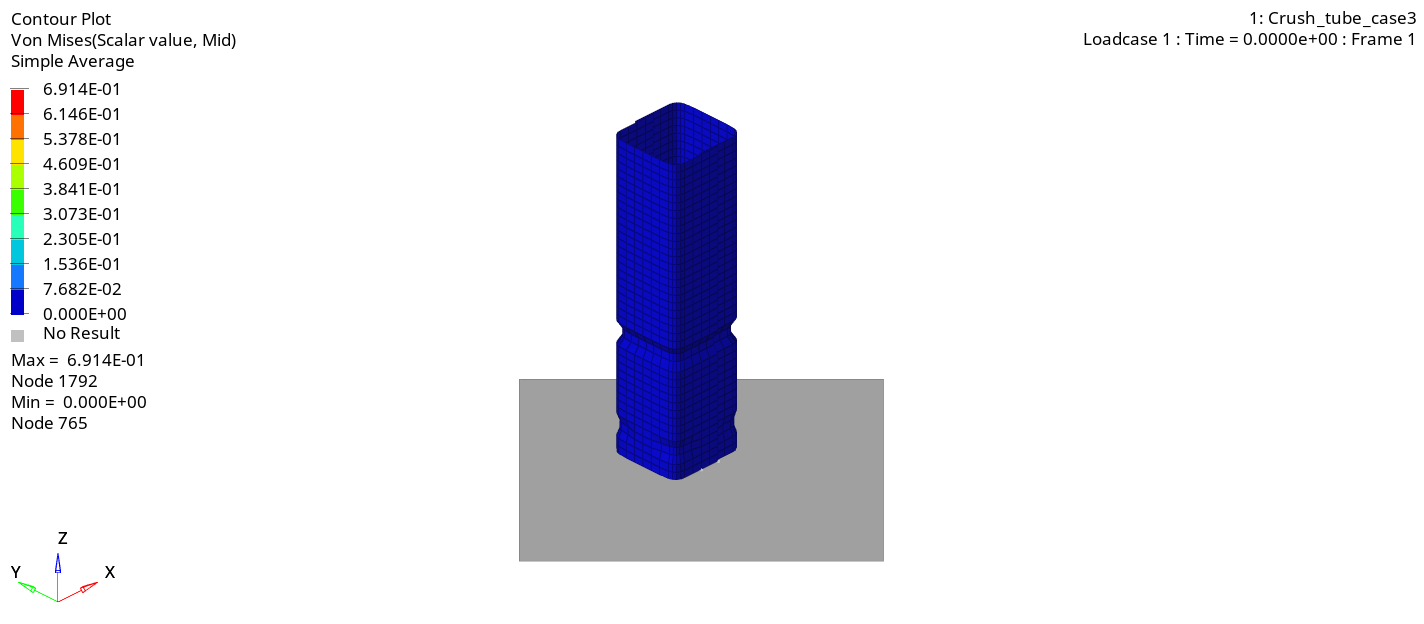
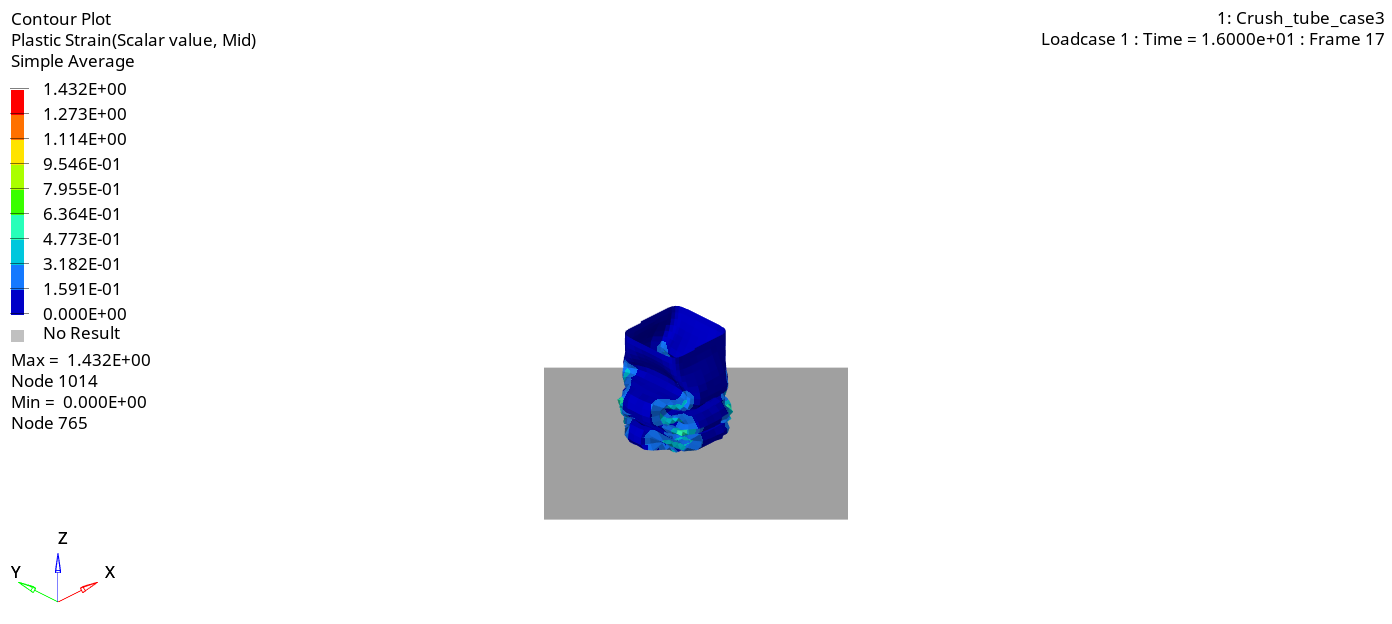
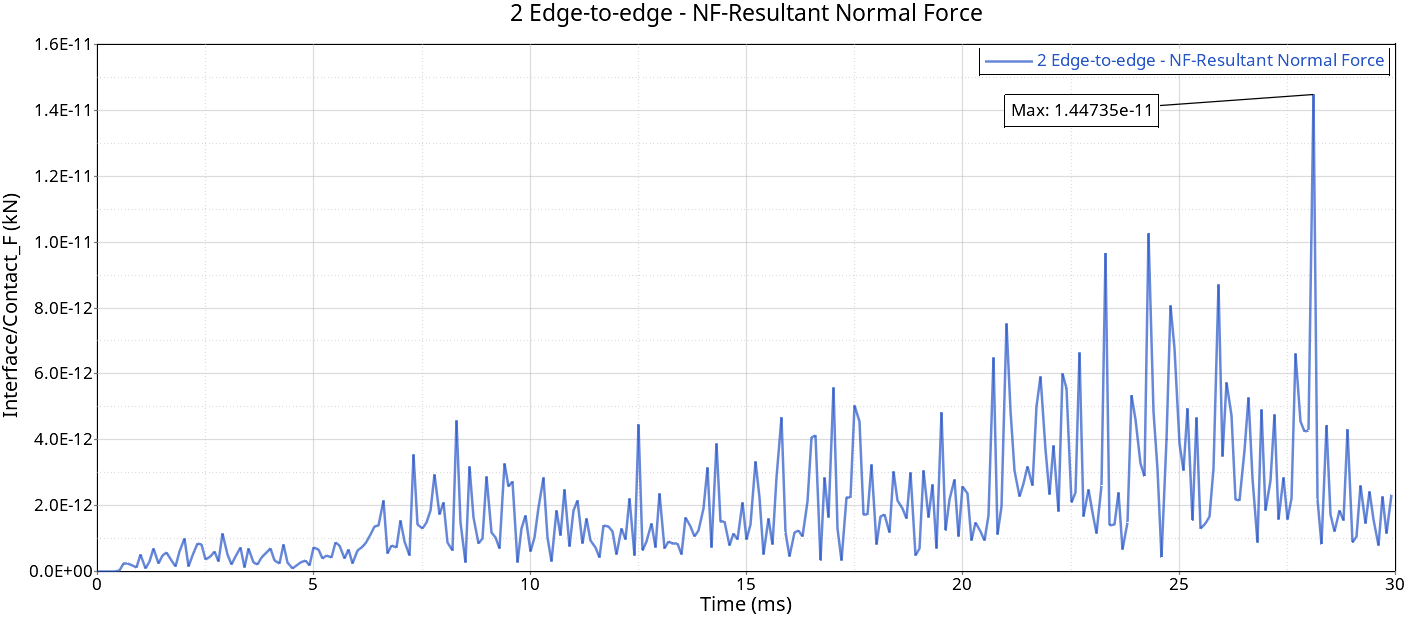
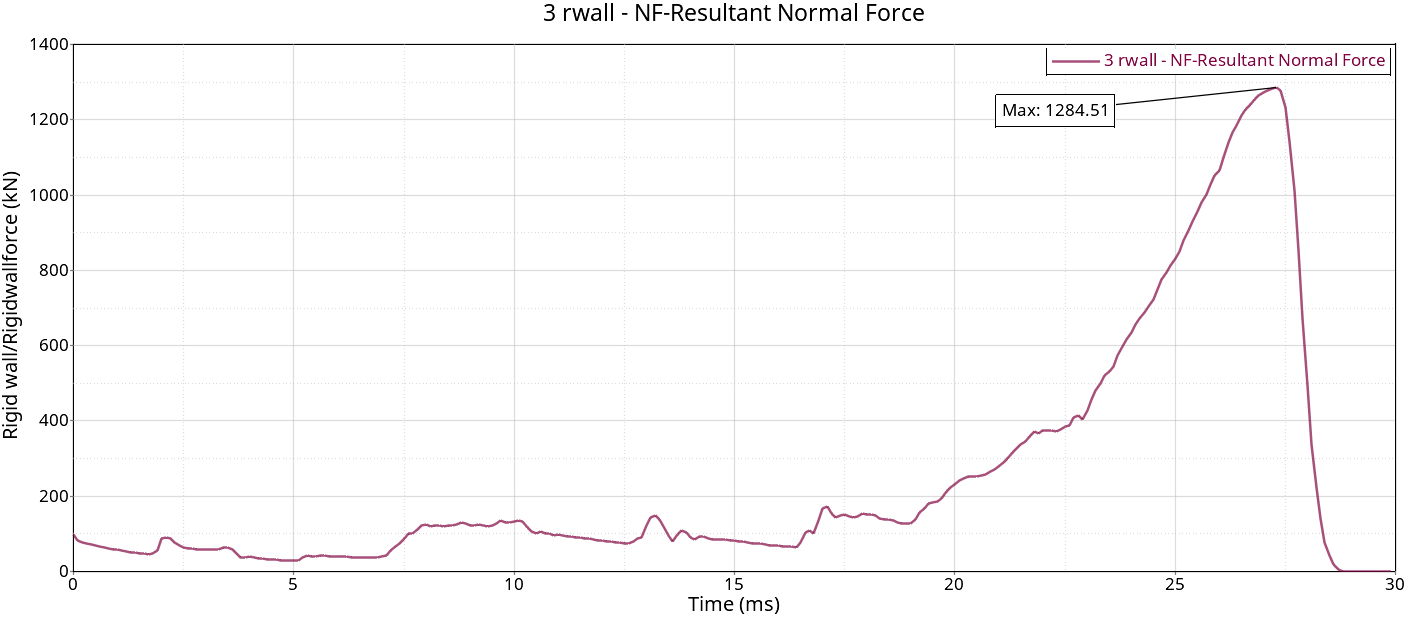
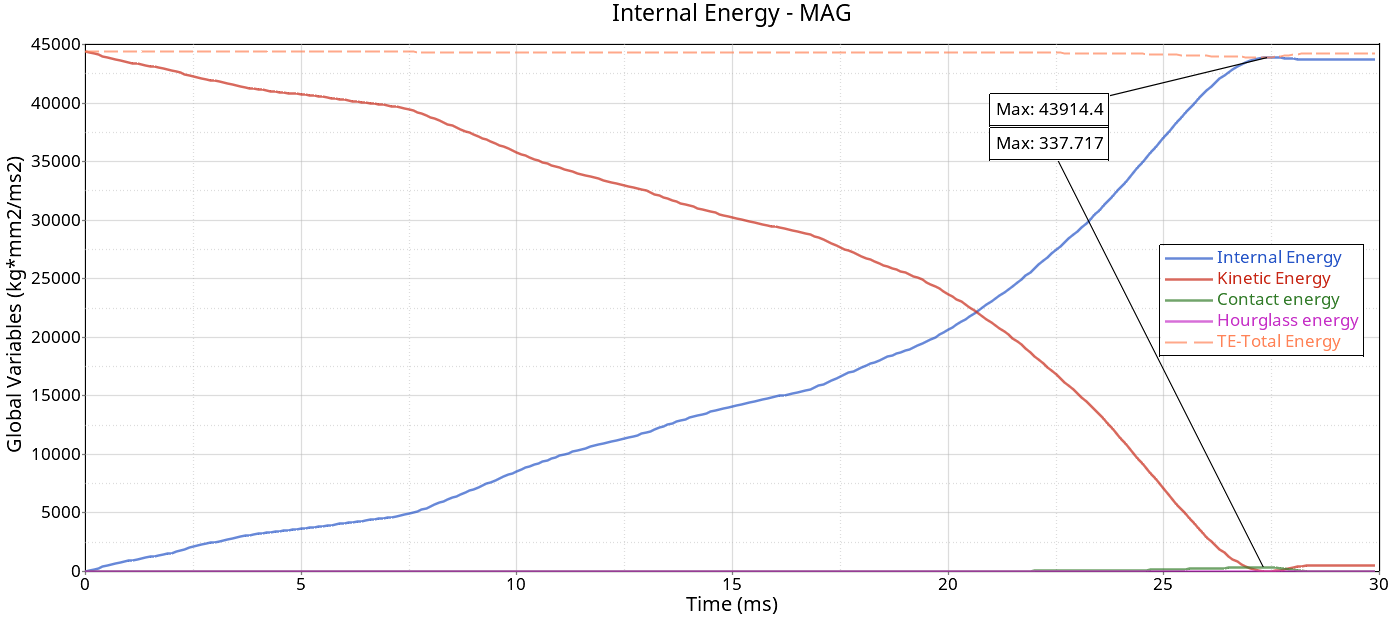
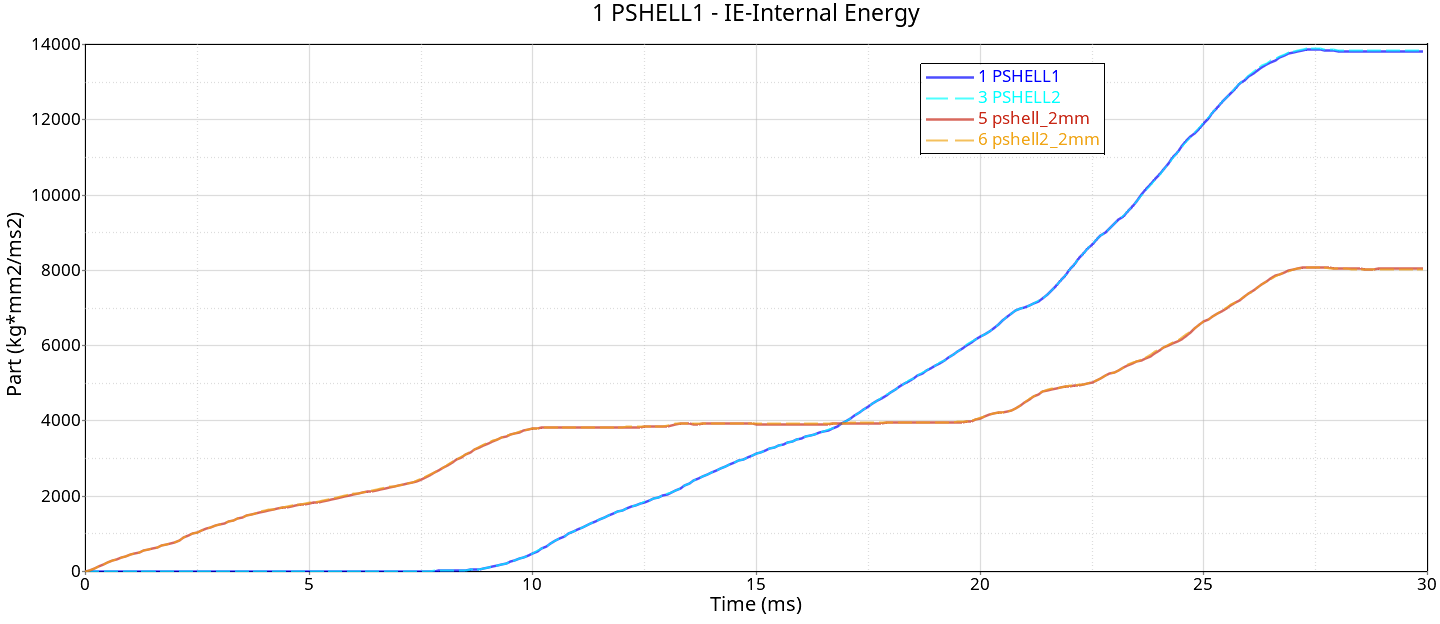
CASE 4:
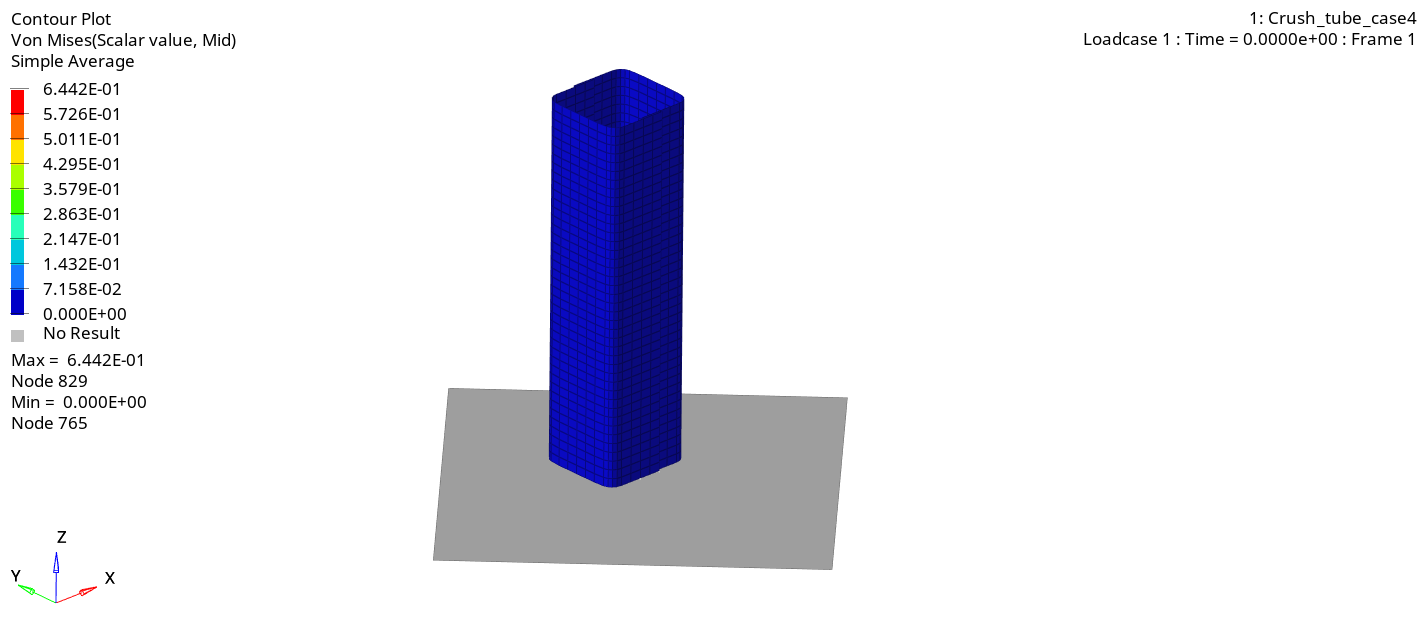
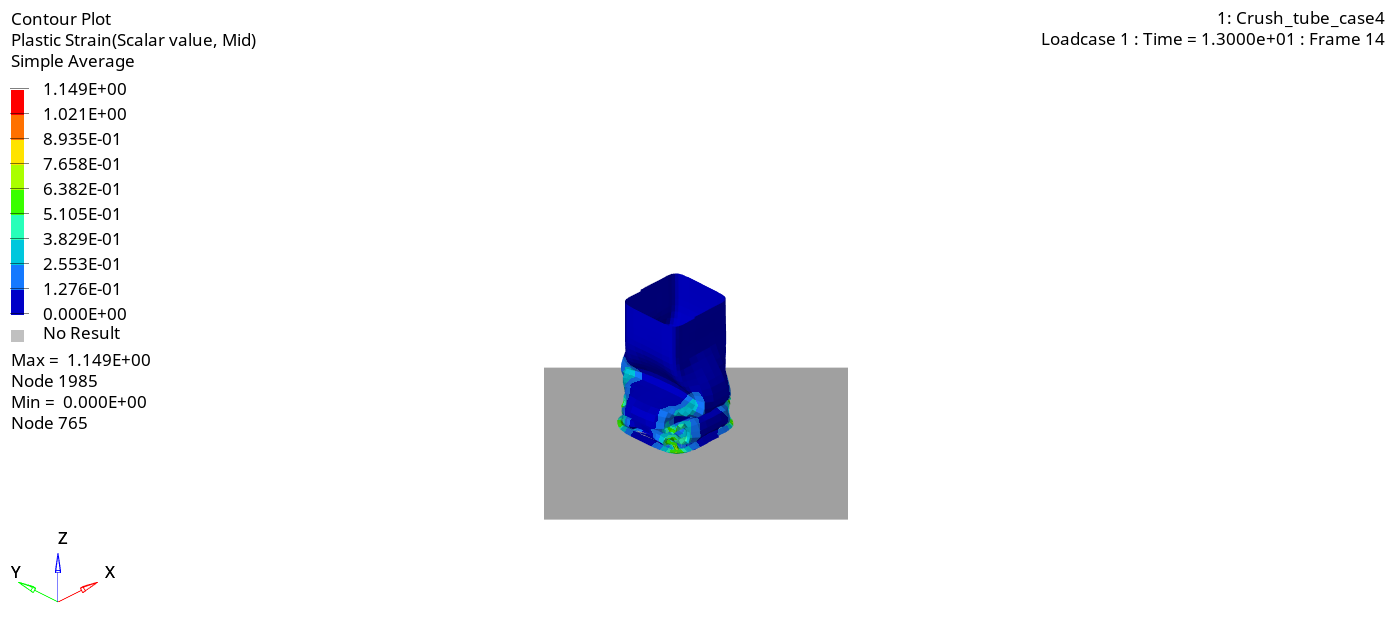
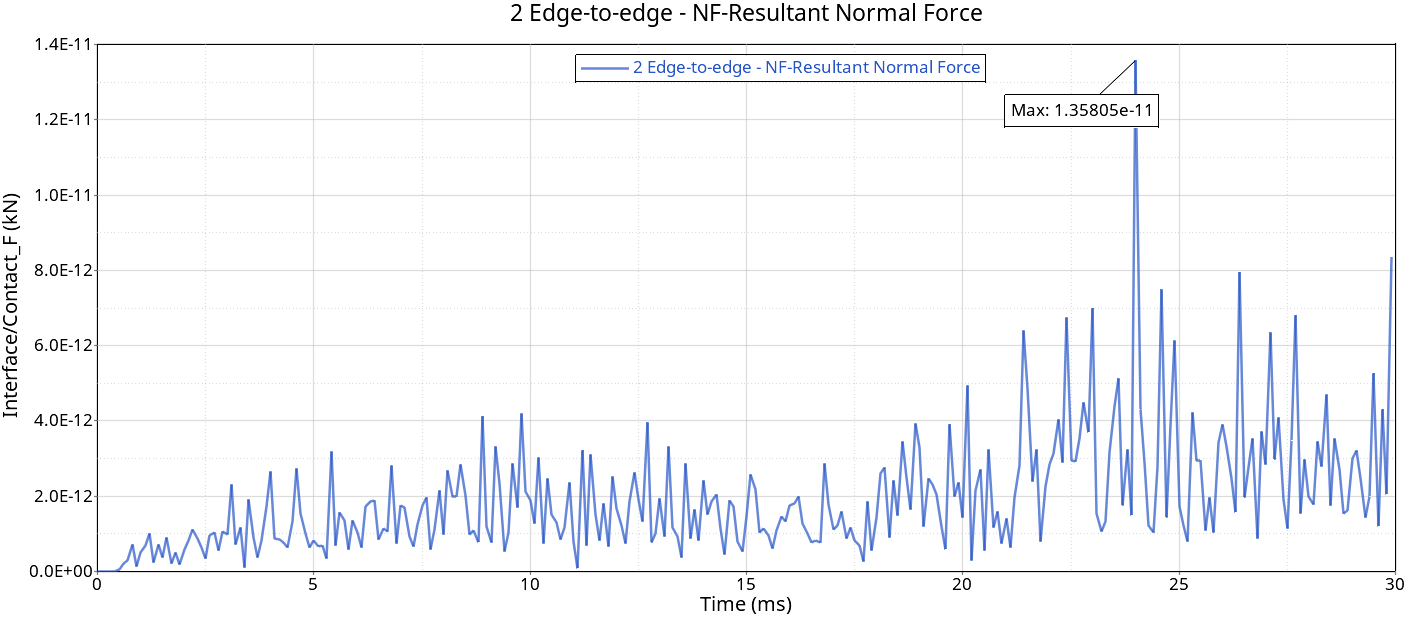
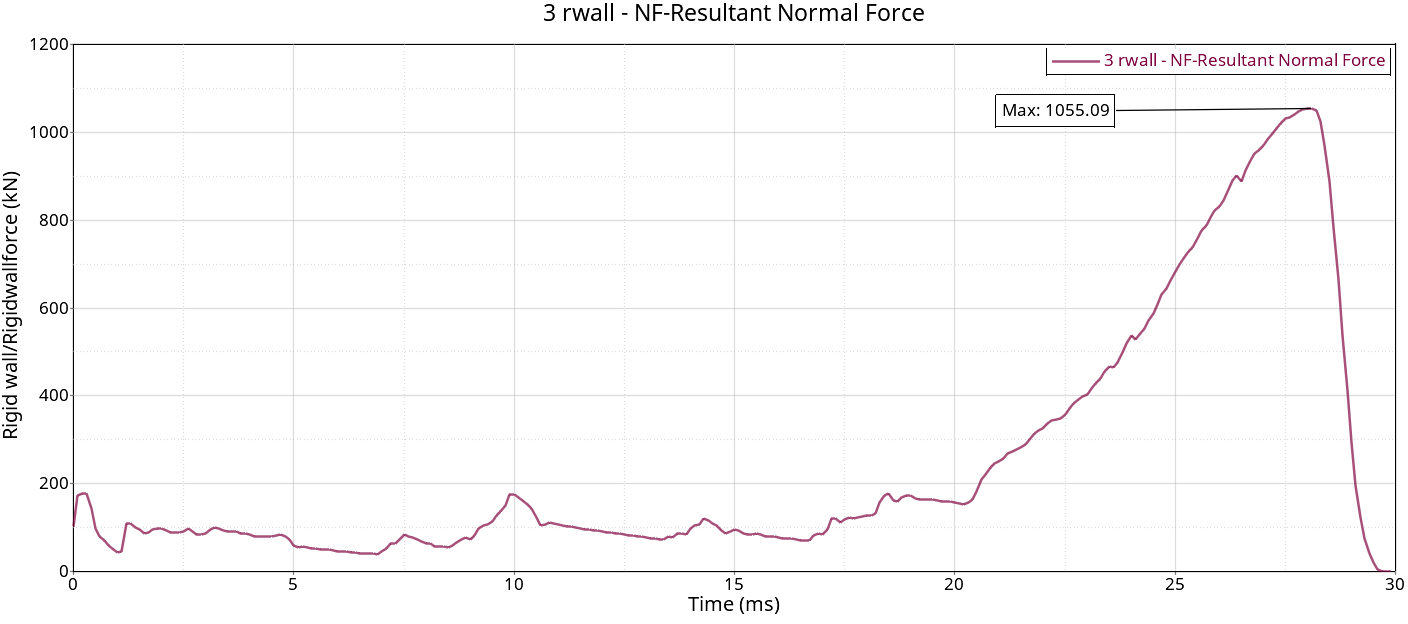
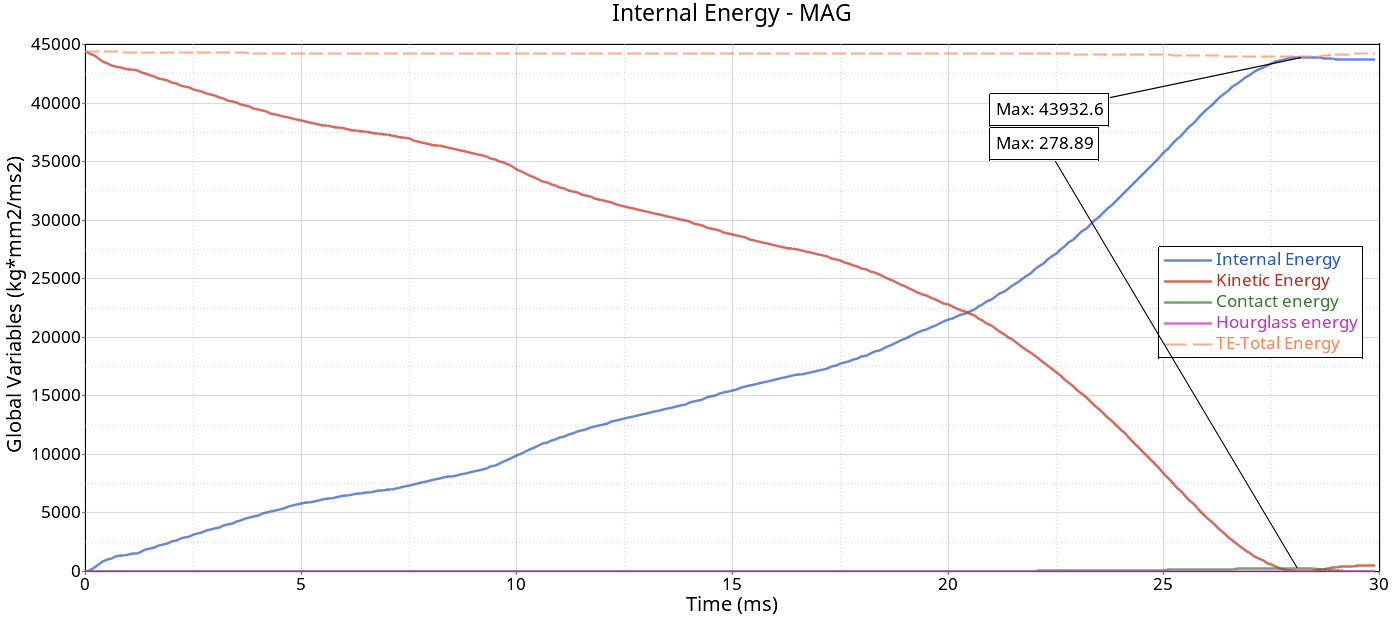
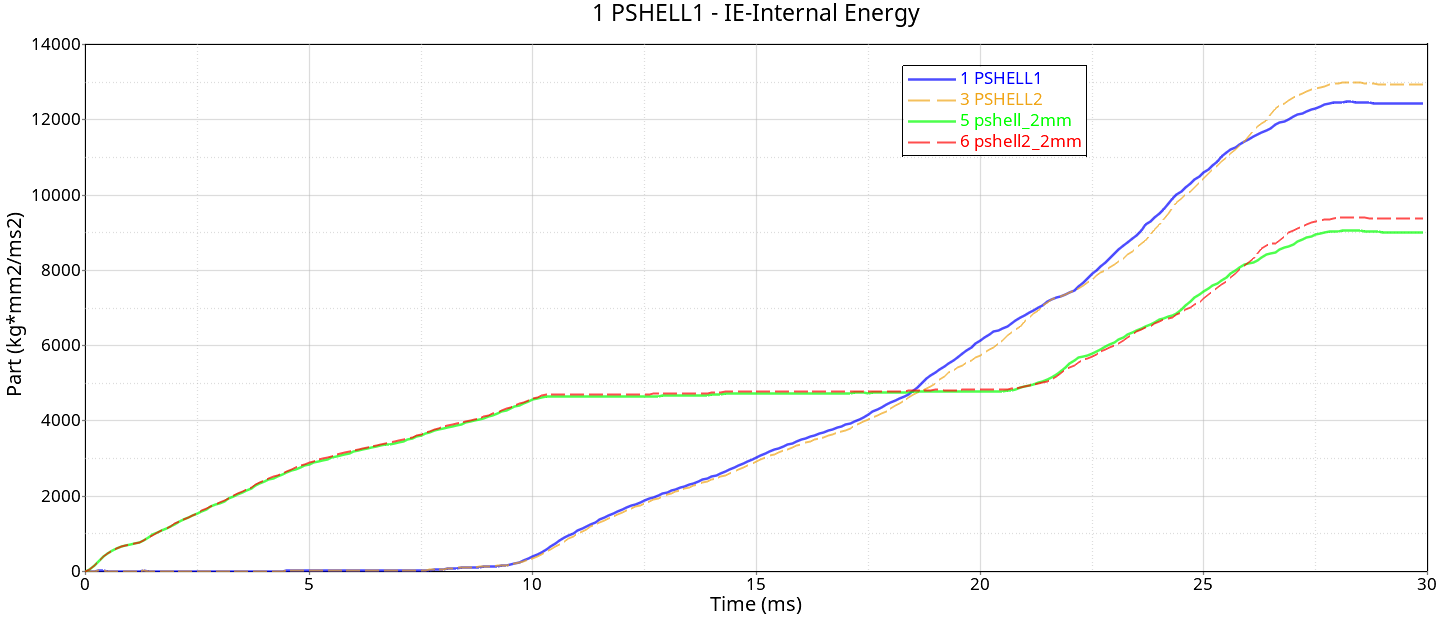
CASE 5:
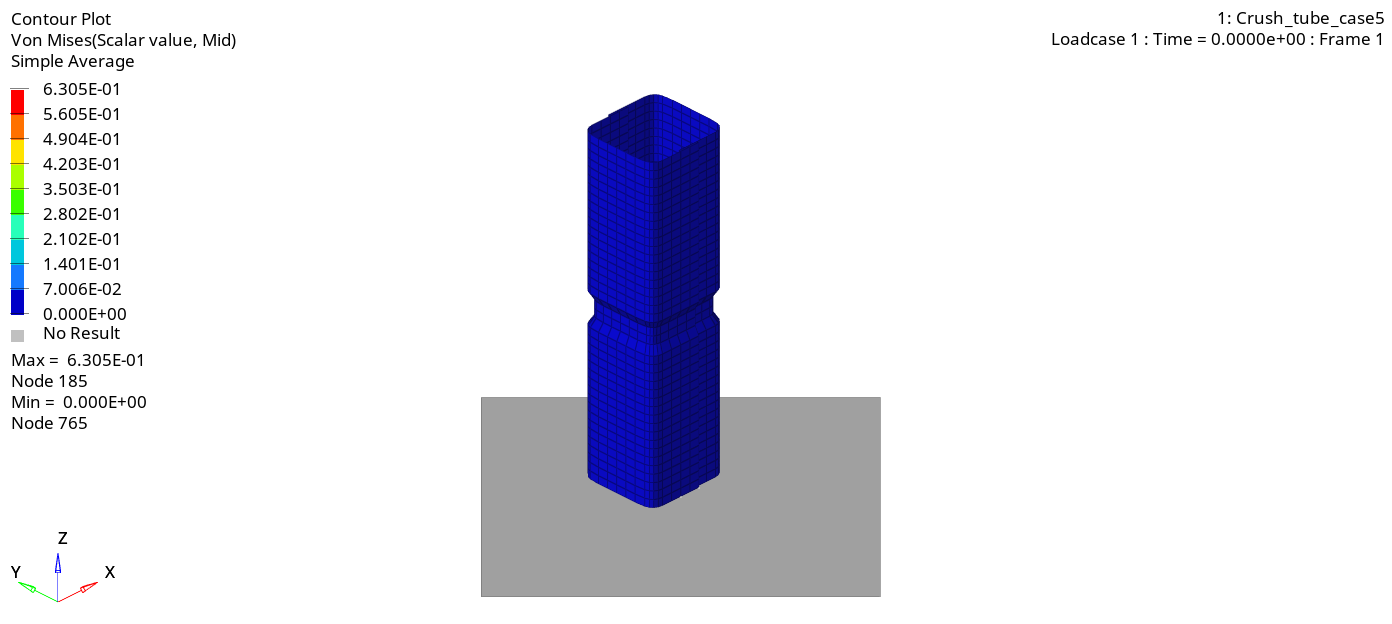
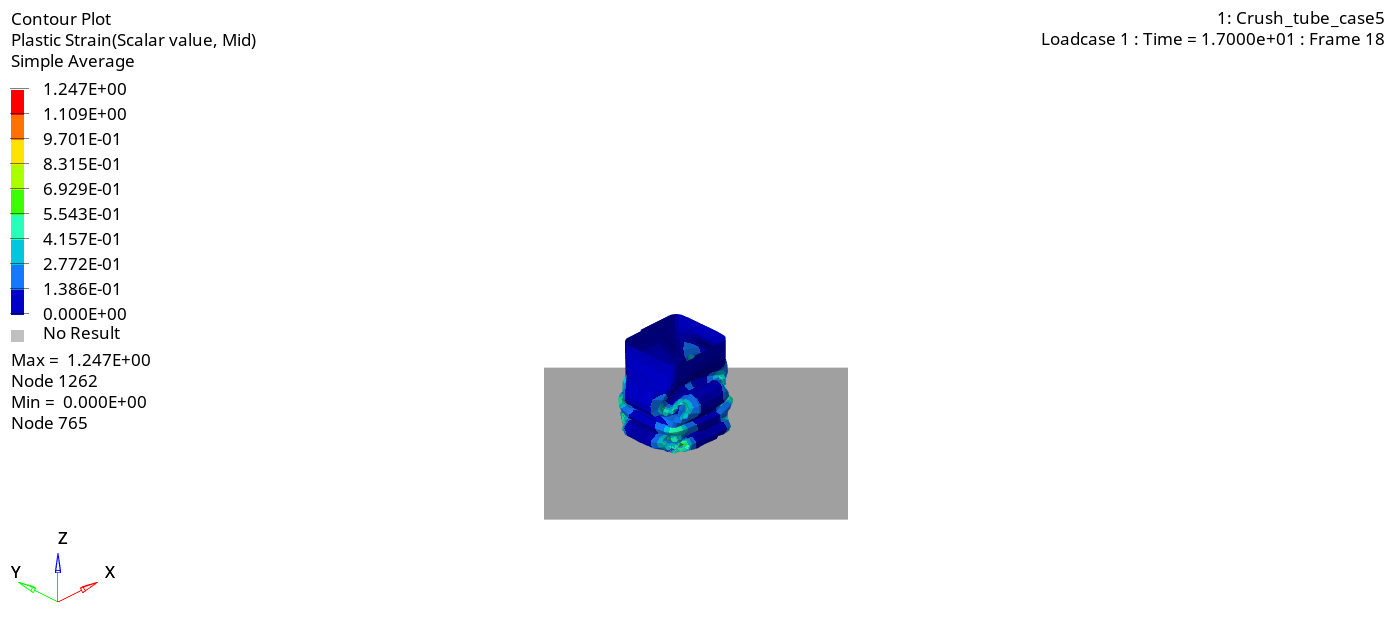
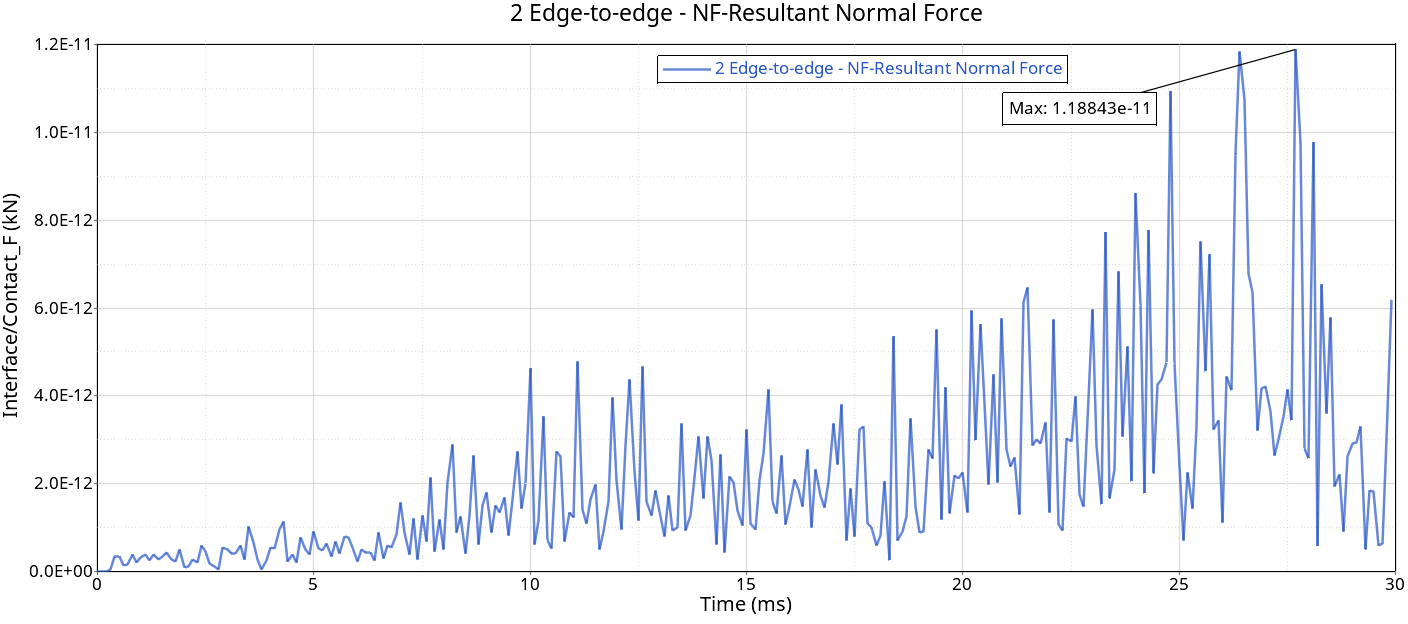
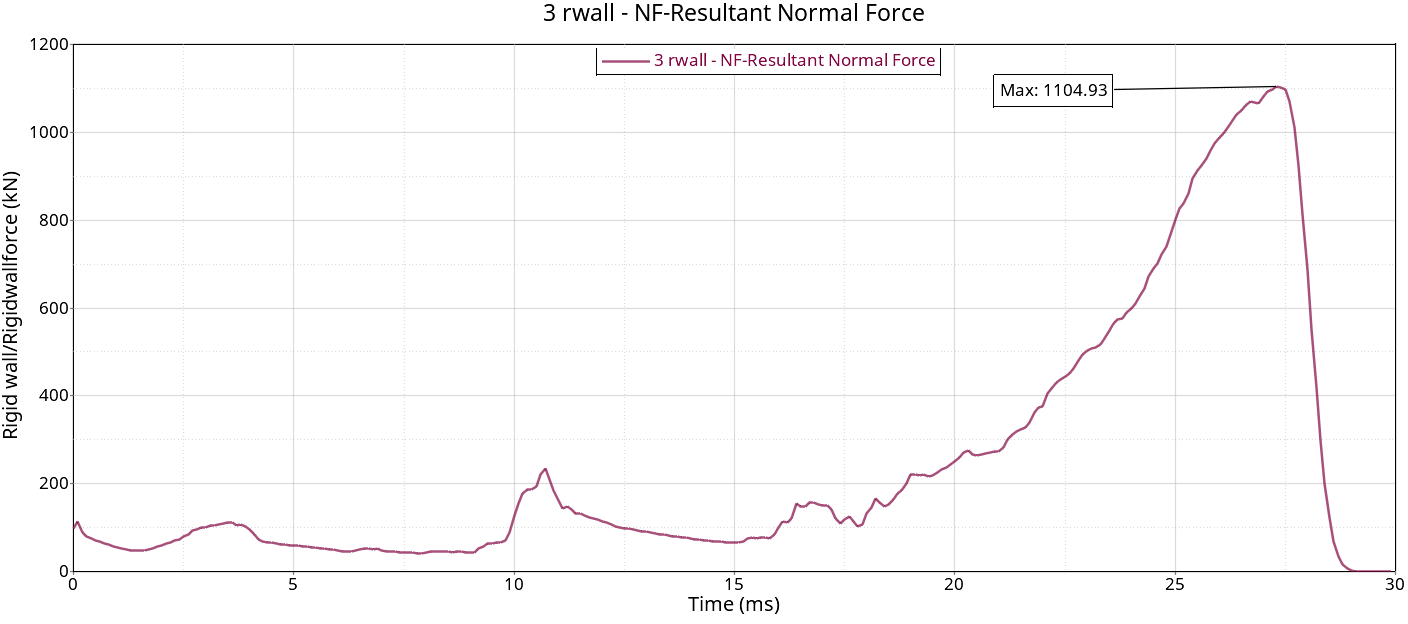
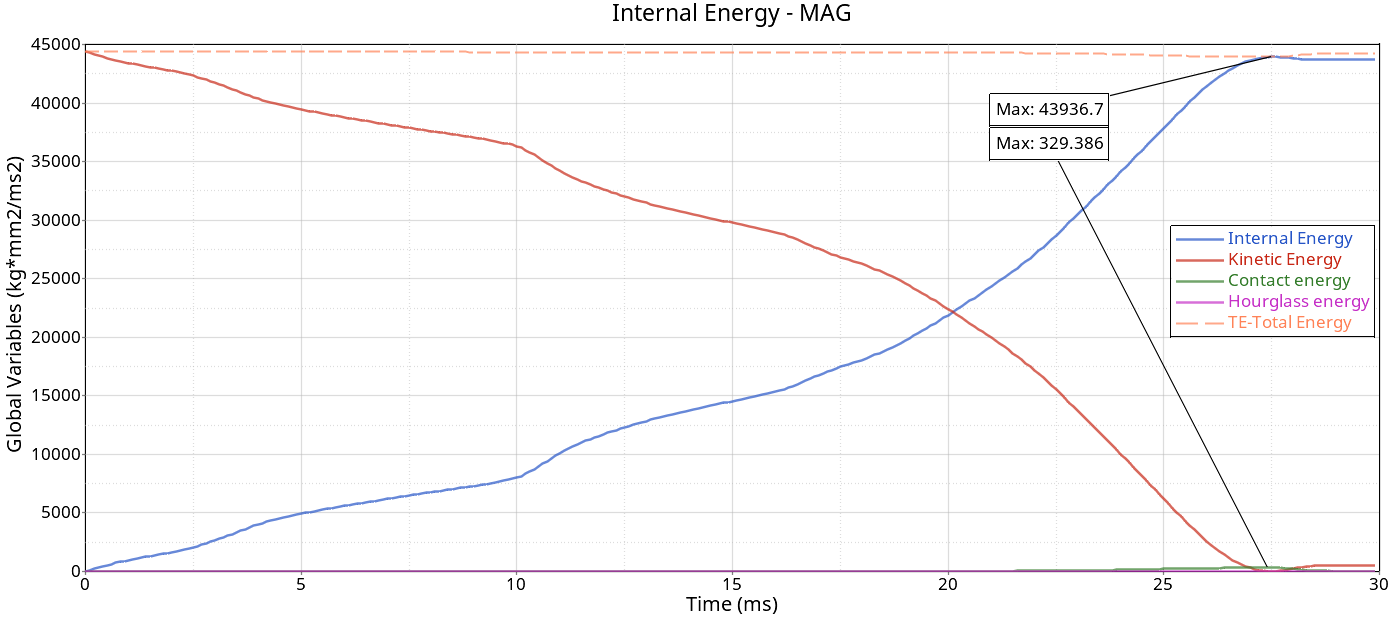
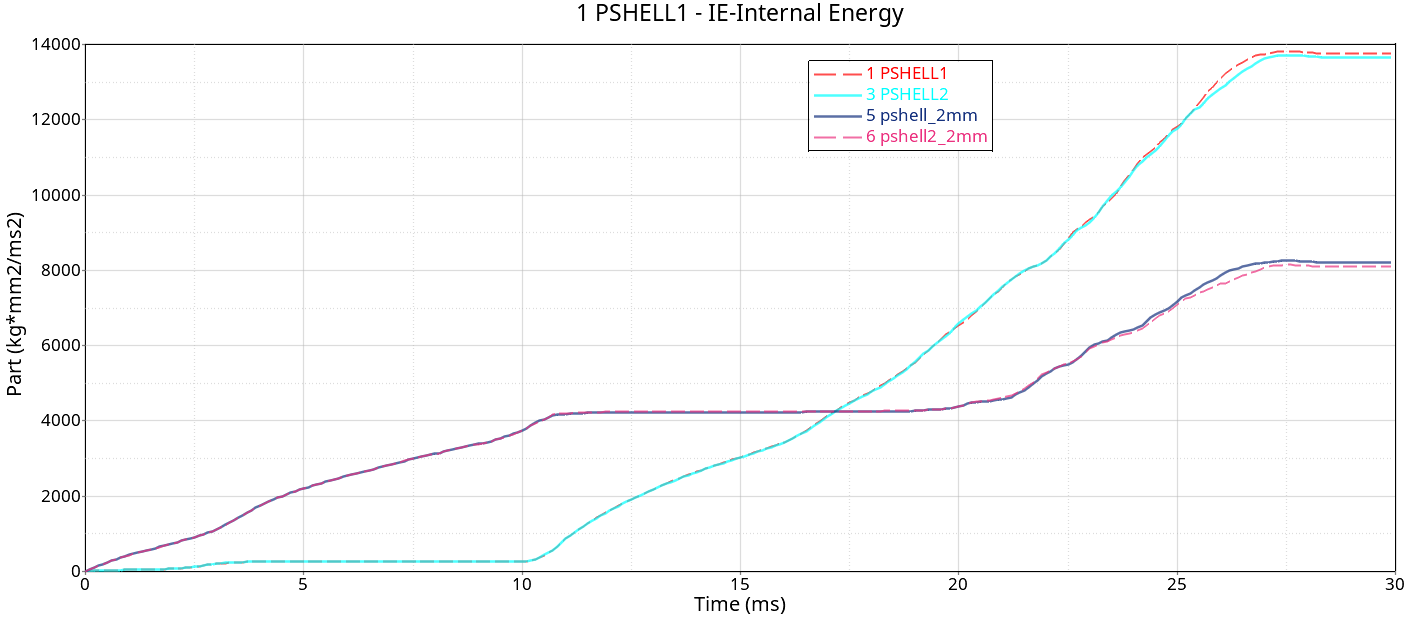
CASE 6:
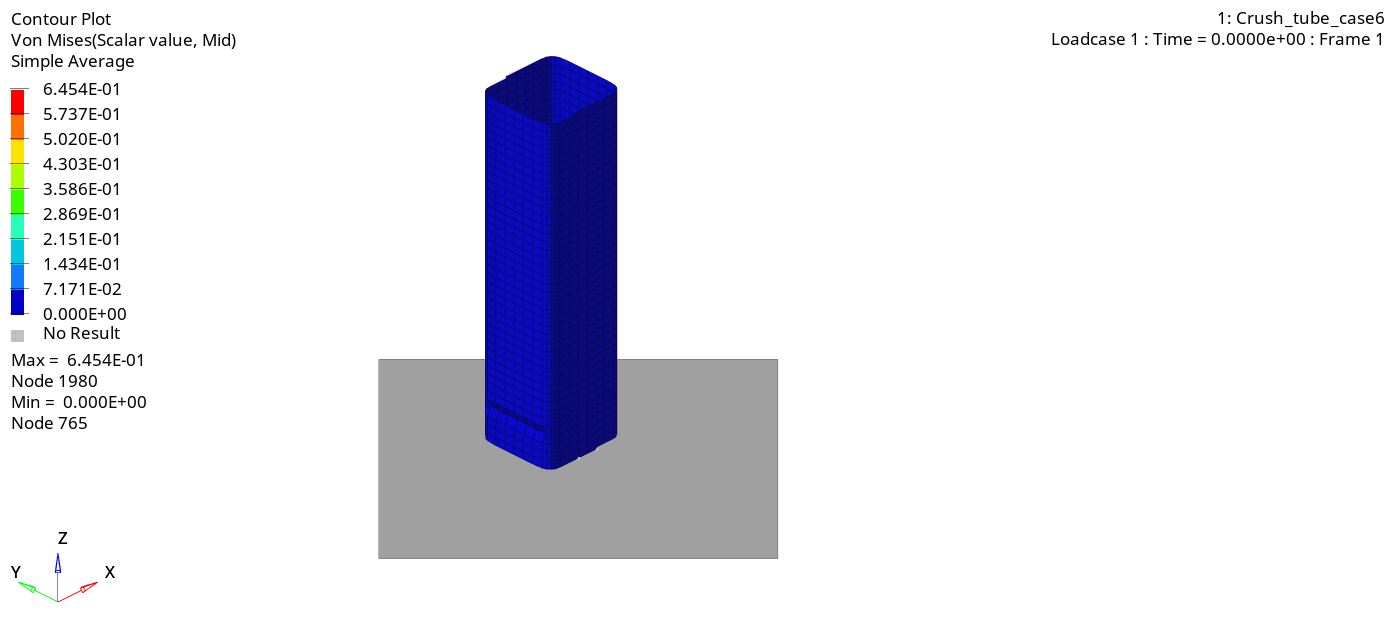
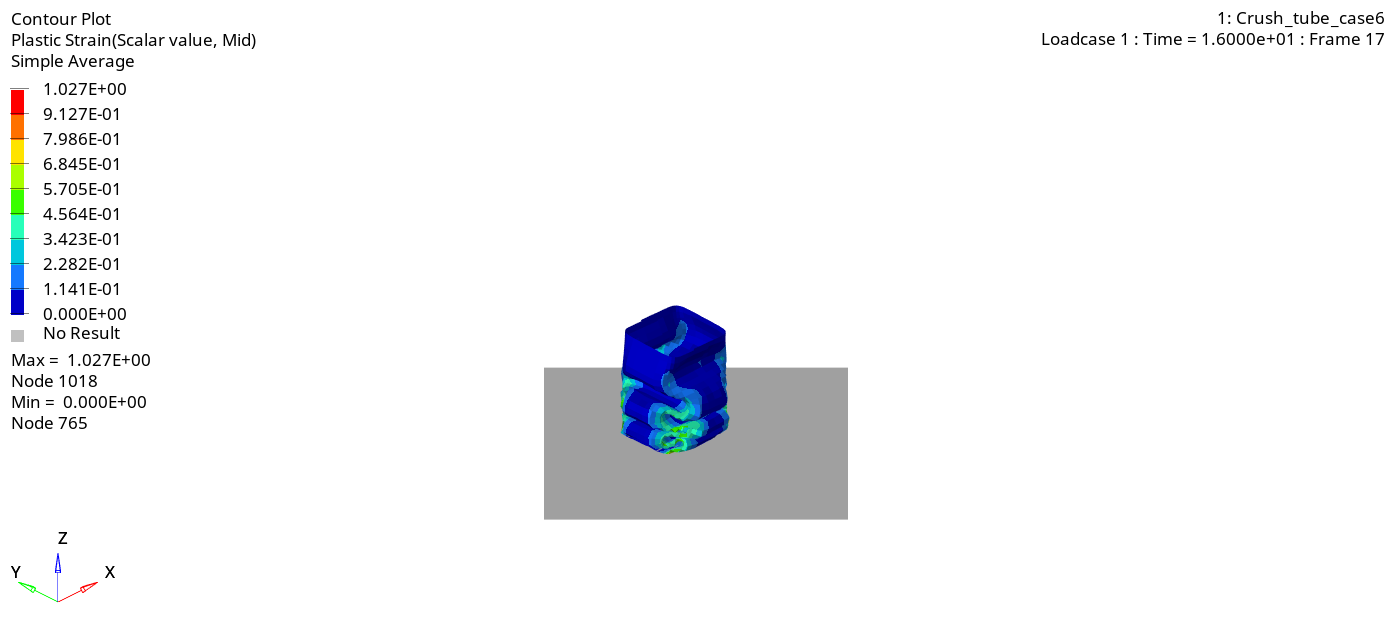
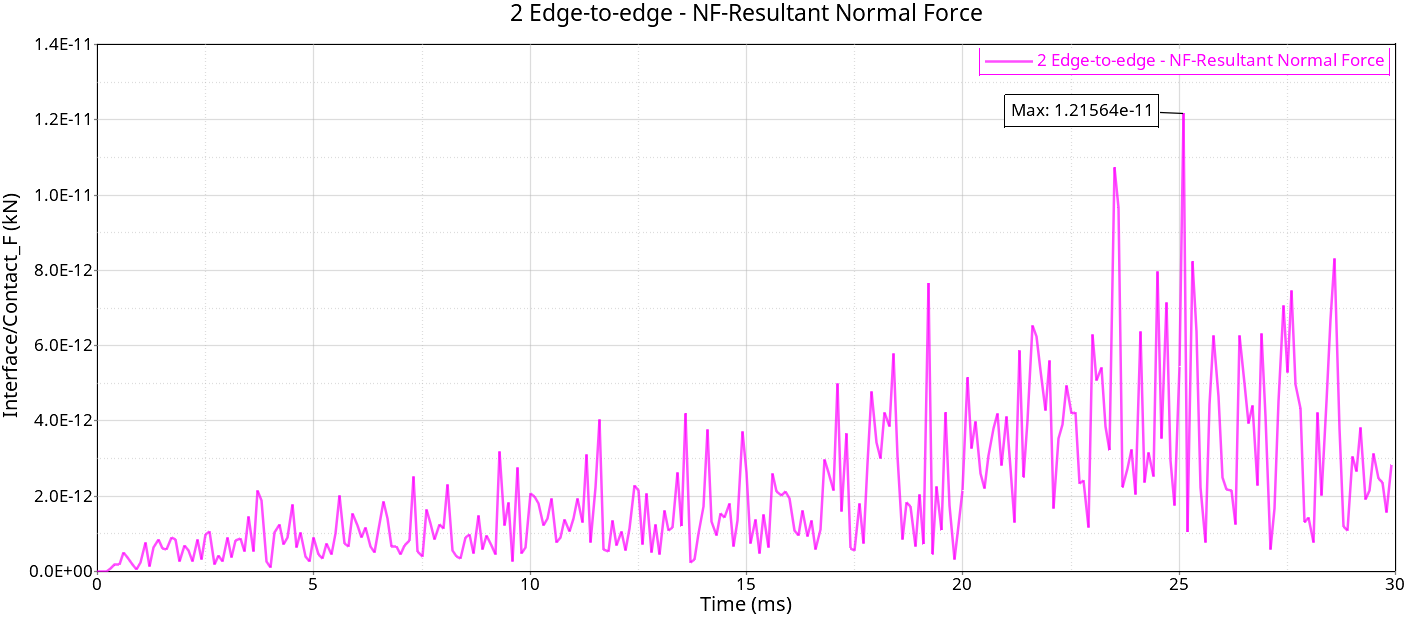
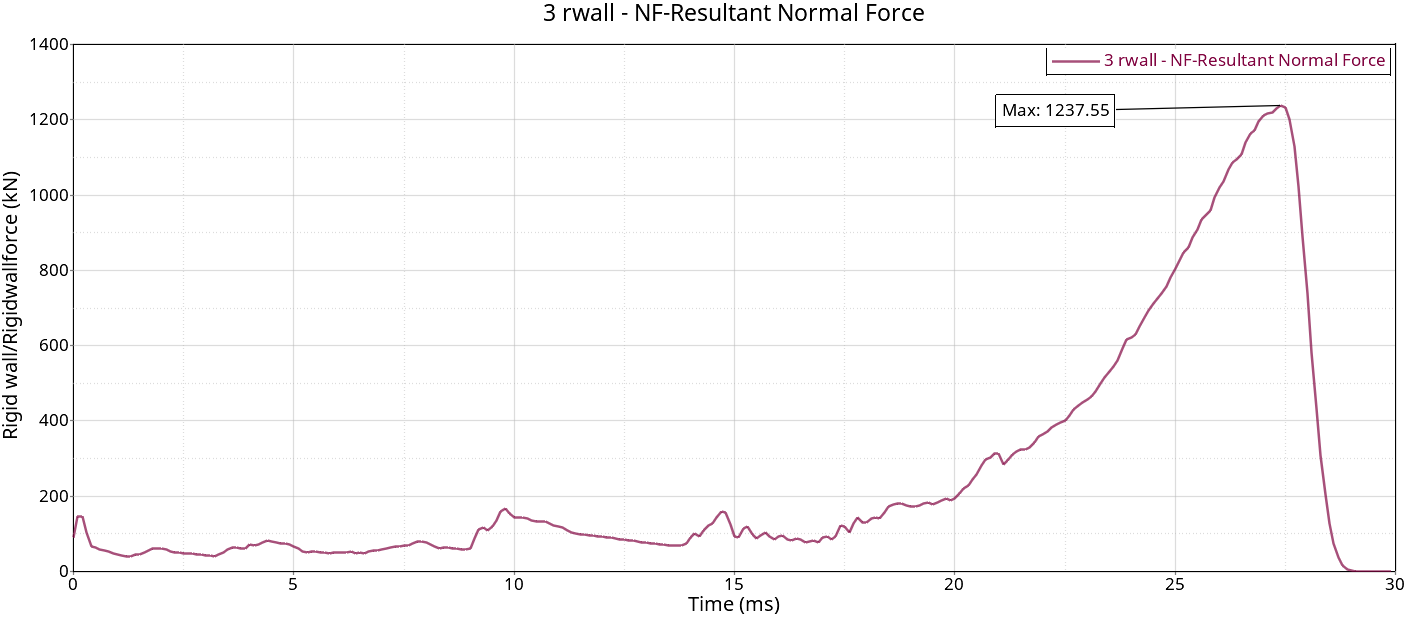
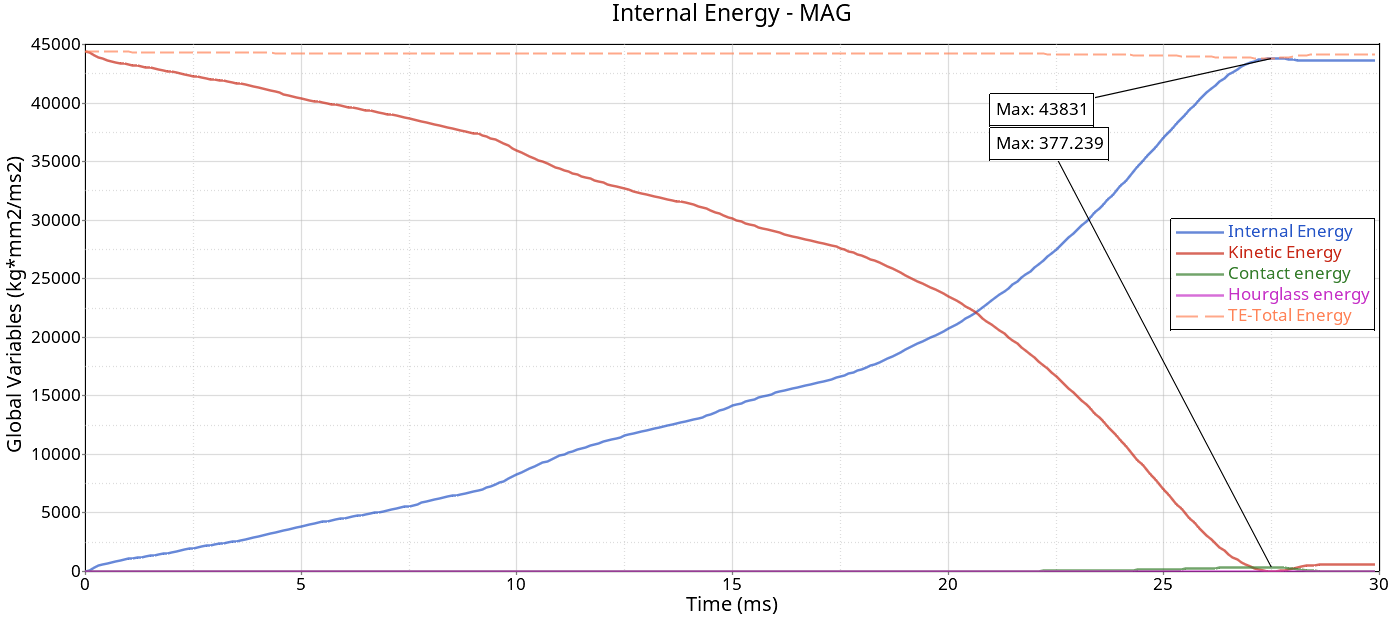
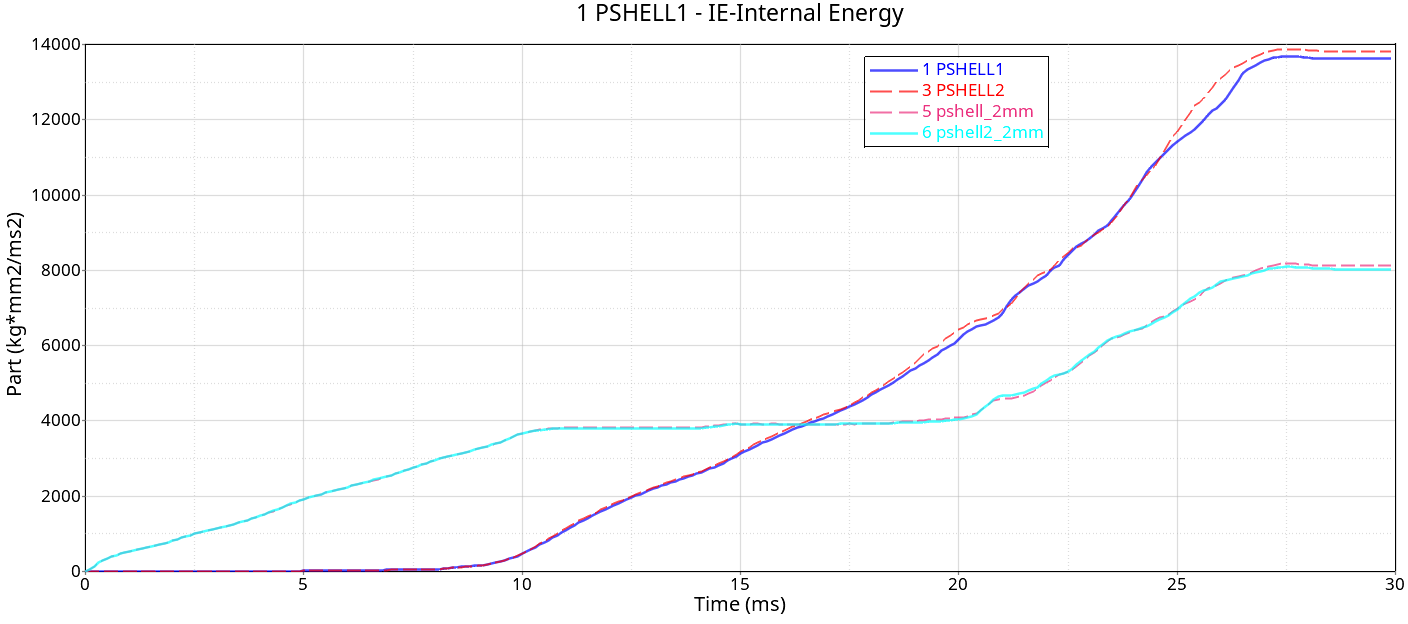
CONCLUSION
CASES |
VON-MISES STRESS (MPa) |
PLASTIC STRAIN |
INTERNAL ENERGY (Kg-mm2/ms2 = Joules) |
CONTACT FORCE (KN) |
RIGID-WALL FORCE (KN) |
TYPE OF CONTACT |
NOTCH TYPE |
ENERGY ERROR (%) |
CONTACT ENERGY (Joules) |
CASE-1 |
0.69 |
1.192 |
42273 |
992.9 |
1338.18 |
7 |
2 element-type notches on two opposite surfaces/FE's of the crash tub |
-3.8 |
2029.77 |
CASE-2 |
0.69 |
1.192 |
42273 |
992.9 |
1338.18 |
7 |
2 element-type notches on two opposite surfaces/FE's of the crash tub |
-3.8 |
2029.77 |
CASE-3 |
0.69 |
1.432 |
43914 |
1.4 e-11 |
1284.5 |
11 |
2 element-type notches on two opposite surfaces/FE's of the crash tub |
0 |
337.717 |
CASE-4 |
0.64 |
1.149 |
43932.6 |
1.35 e-11 |
1055.09 |
11 |
No notches |
0 |
278.89 |
CASE-5 |
0.63
|
1.247 |
43936.7 |
1.18 e-11 |
1104.93 |
11 |
1 element type notch in the middle of the crash tube |
-0.1 |
329.386 |
CASE-6 |
0.64 |
1.027 |
43831 |
1.2 e-11 |
1237.55 |
11 |
1 node type notch on the opposite faces of two surfaces/FE's |
-0.1 |
377.239 |
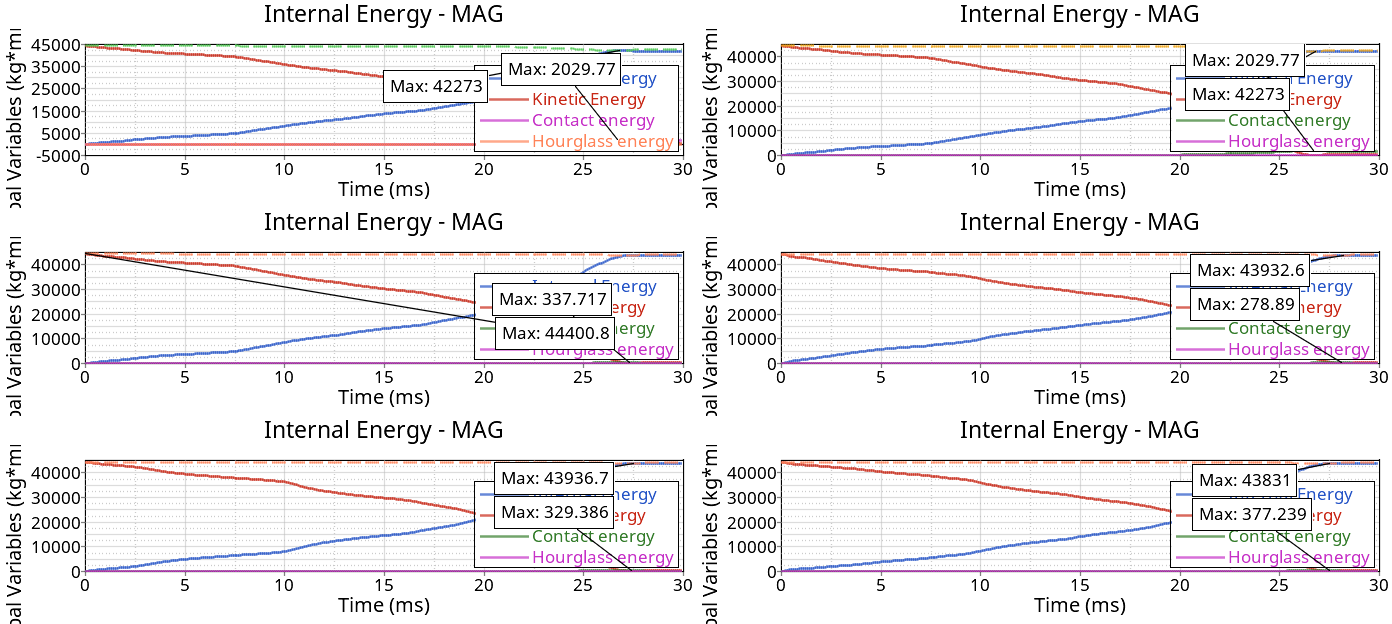
- The energy is dissipated in all cases for this assignment. As we know Energy error should be 0.0 <Energy Error < -5.0 %. The energy error for the type 7 interface ( General node to surface) in 2 cases is -3.8% which is within normal standards. But for the type 11 interface ( Edge-to-Edge) in 4 cases it is approximately 0%. So notches don't affect the error percentage in all the above-mentioned cases.
- The normal value for contact energy is 0% to 5% of the total energy. So in Case 1 and Case 2 the contact energy is high as compared to other cases. It means around 4.8% contact energy of total energy is observed in type 7 interface cases. In the type 11 interface cases, 0.6-0.7% contact energy of total energy is examined. The contact forces are also found quite high in the type 7 interface while very low contact forces are developed in the type 11 interface. Eventually, in most of the factors type 11 seems to be more effective in comparison to the type 7 contact in shell components
- The internal energy is found maximum for two opposite shell components that are in contact with a rigid body in the presence of notches for all cases. In the absence of notches, the internal energy for two shell components in contact with rigid walls increases and the two shell components in contact with a rigid body decreases. However, the overall internal energy of the whole model is found lesser in the type 7 interface as compared to the type 11 interface.
- The notch in the middle of the crash tube displays lower stress results as compared to the first 3 cases having 1 full notch and one half notch on the opposite shell components in contact with the rigid wall. The no notch case and last node-notch case also portray lesser stresses contrary to the first 3 cases. The strains found in the first two cases are lower and after contact change in 3rd case, it increase. In 4th case, notches are removed and it decreases. In 5th case, it increases due to the incorporation of element type notch in the middle of the crash tube. In 6th case lastly, it decreases when a node type notch is provided. The rigid wall force monitored is lower in the no notch case and notch in the middle of the crash tube case.