SCREW BOSS AND DOG HOUSE DESIGN
INTRODUCTION:
- Boss features are commonly found in injection moulding designs. They are used to aid in the assembly of moulded parts by providing a channel for a screw.
- Dog house is a feature that helps you to avoid sink marks.
OBJECTIVE:
- To create the boss and dog house for the center console coin holder considering all the design rules.
METHODOLOGY:
- We get the component and with the help of the design rules for screw boss and dog house we design the following, then after that we do the draft analysis.
DESCRIPTION:
Screw boss design:
- Bosses find use in many parts designs as points for attachment and assembly. The most common variety consists of cylindrical projections with holes designed to receive screws, threaded inserts or other types of fastening hardware. As a rule of thumb, the outside diameter of bosses should remain within 2.0 to 2.4 times the outside diameter of the screw or insert.
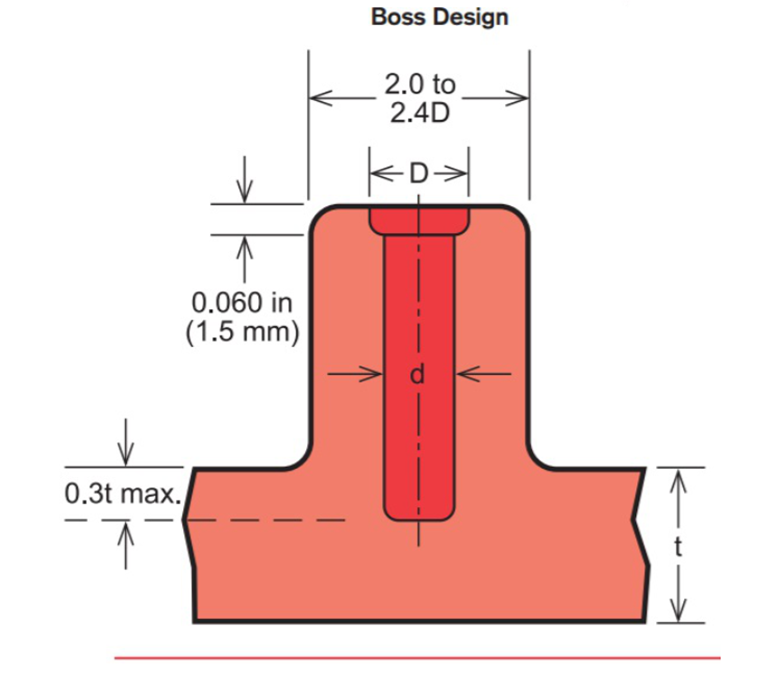
- To reduce stress concentration and potential breakage, bosses should have a blended radius, rather than a sharp edge at their base. Larger radii minimize stress concentration but increase the chance of sink or voids. Specifying smaller screws or inserts often prevents over lay thick bosses.
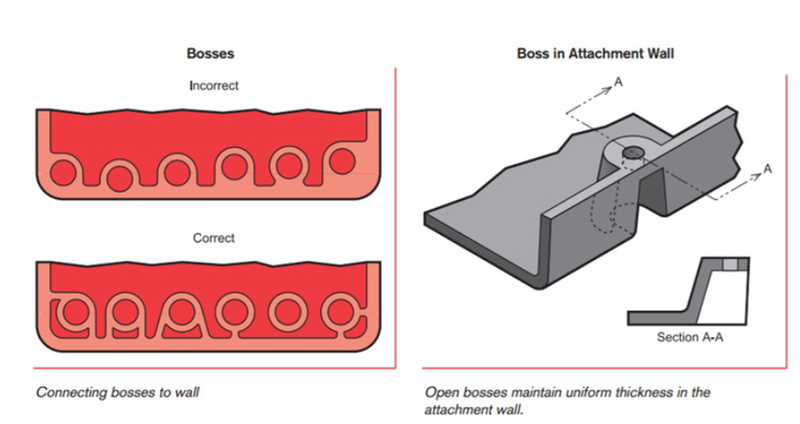
- Avoid bosses that merge into sidewalls because they can form thick sections that lead to sink. Instead, position the bosses away from the side walls and in needed, use connecting ribs for support.
- Consider using open boss design for bosses near a standing wall. Avoid bosses that merge into the side walls because they can form thick sections that lead to sink. Instead position the bosses away from the side wall and needed use connecting ribs for support. Consider using open boss design for bosses near a standing wall.
- Normally, the boss hole should extend to the base wall level, even if the full depth is not needed for assembly. Shallow holes can leave thick sections, resulting in sink or voids. Deeper holes reduce the base wall thickness, leading to filling problems, knit lines or surface blemishes. The goal is to maintain uniform thickness in the attachment wall because of the required draft, tall bosses those greater than 5 times their outside diameter can create a filling problems at their top or a thick section at their base.
Rules:
Measure base thickness of rib at tangent of radius if radii are modeled in.
The larger the area at the base of the rib, the more retained heat.
The retained heat causes more shrinkage which causes sink.
-
Optional rib fillet radius – 0.25mm maximum
- Must not violate 40% thickness requirement
-
Draft 0,5 degree on both inside and outside of the boss
-
Height to diameter ratio = H/B < 3
-
Boss gussets must meet rib guidelines
-
Need to plan ahead of ejection
Dog house design:
- Dog house is an engineering feature used in plastic trim design. Dog houses are used as supporting feature. Dog house is a feature that helps you to avoid sink marks.
Rules:-
Height of (B) should be between 3.0 – 6.0 mm
Minimum height (H) of dog house is 6mm
Less than 6mm causes weak steel condition.
3:1 ratio of steel width to height 2:1 is preferred.
Minimum dog house width (X) for dog house is 12mm.
Minimum draft (D) for dog houses 1.5 degree to die draw.
If a slide is being considered this requirement can change to 3 degrees minimum.
Tooling Axis:
- For the tooling axis we first inspect by taking a section and then decide which direction would be better for the tool axis.
- Then we create a point at the center of the base and create an axis system. Then we intersect the surface A with the YZ plane. With the intersection we get what we observe is that the side walls of the class A surface are parallel with the vertical axis i.e. there is 0 degree angle between them.
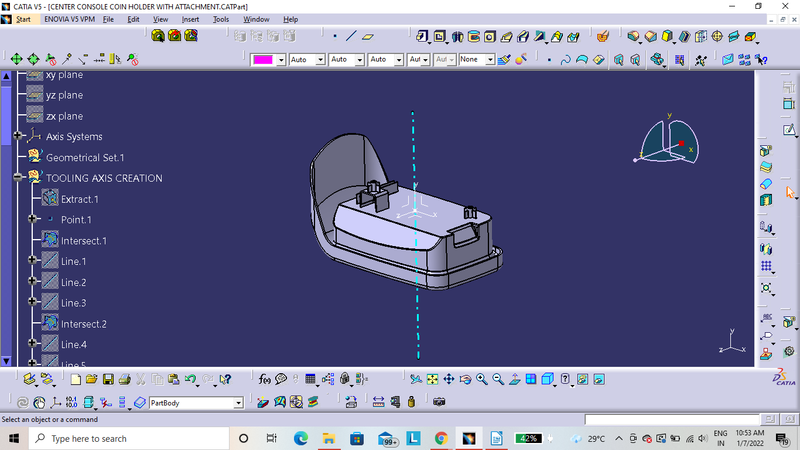
- But since it’s a class A surface we have to go the same design since we do not have the authority to change the class A surface design. So we have to go with this draft angle itself.
- We create a vertical line along the point created and the vertical axis and this will be our main tooling axis.
- For the dog house we will need a side core to we have to give a tooling axis to the side core as well which would be along the Z axis of the component.
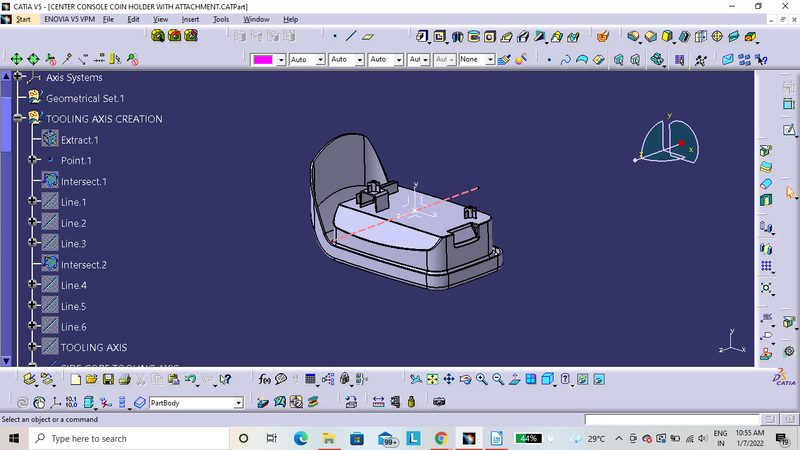
Procedure To Design Screw Boss & Dog House for Coin Holder:
Step-1:
- To design the Screw Boss and Dog house on the Coin Holder insert a new geometrical set in the construction features and name as Screw Boss and define the Geometrical for sketching
Step-2:
- In the geometrical set extract the coin holder bottom fact then insert a positioned sketch set with the vertical and horizontal axis in their position and start sketching in it. in my assumption, my screw diameter is 6mm for the tapping I left the 0.4mm thickness on both sides so the diameter of the hole is 5.2mm and the thickness of the hole is 0.6 x t of the main component for the hole we need to add the thickness on both sides and add with hole diameter, therefore (1.5 x 2 =3) and the final thickness of hole or outer dia is 5.2 + 3= 8.2mm
∴ 0.6 x 2.5=1.5mm
- After sketching the 2 circles insert the body and go to the part workbench and use the Pad command for giving the screw boss height there is a formula for the height of screw boss
- The height to diameter ratio = 3:1
∴ 3 X 5.2 =15.6MM
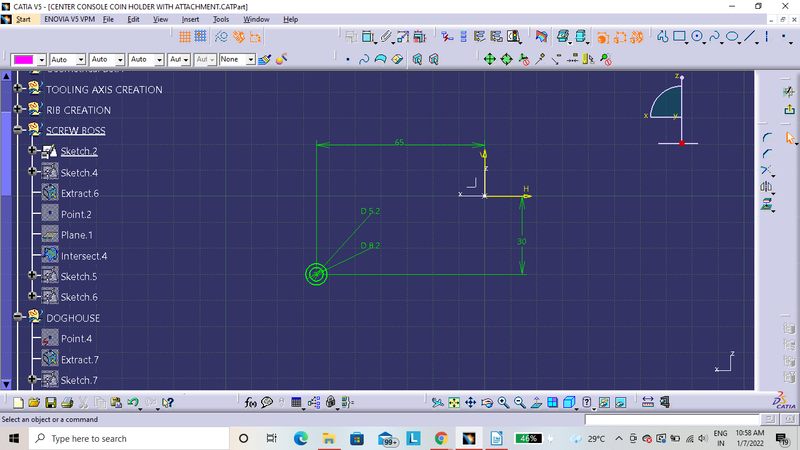
- But in our case if we are taking the height is 15.6mm is not getting enough strength so I am taking the height of the component is 12mm
Note: There are Guidelines for Design of Screw Boss
-
Draft
-
Thickness
-
Height to Diameter Ratio
-
Optional Radii
-
Boss Gussets
-
Coring Out Bottom
This is the points to be noted when design 0n Screw Boss.
Step-3:
- Use the pad command and enter the value of 12mm and in opposite direction take 1mm to merge with the component. And check the screw boss it satisfies the design parameters. And add the draft of 0.5 deg for the hole.
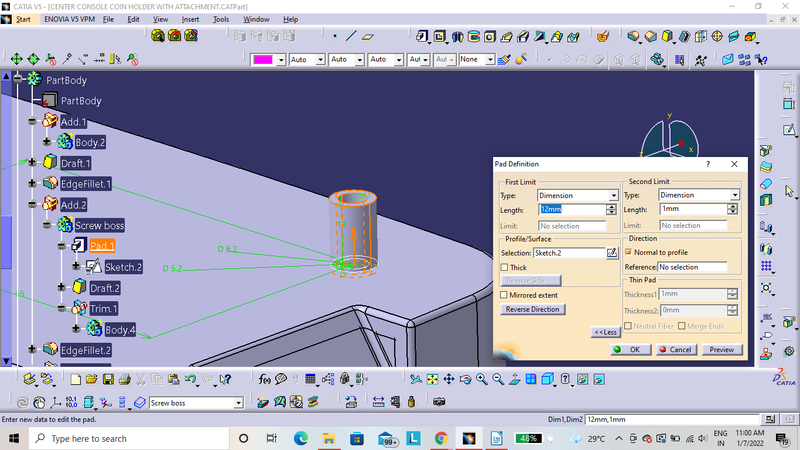
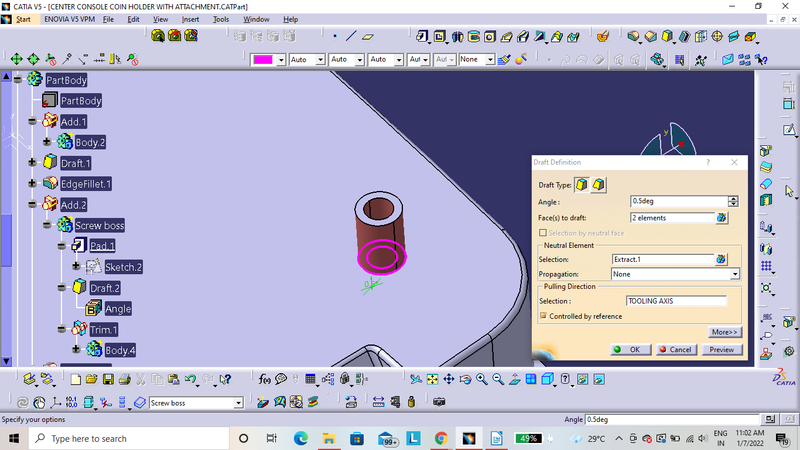
Step-4:
- Add the ribs Or Gussets them to strengthen the screw Boss and start with the sketching of line by taking screw boss sketch as reference and draw the two connecting lines and give the 20mm length and exit the sketch and use pad command with the height of 9mm and add the thickness of 1mm from the neutral axis of the sketch and use the Boolean in operation and with union trim command and aspirate the inner lines that connects the hole. And add the Drafts for the gussets with 0.5 deg angle for the with the base of component.
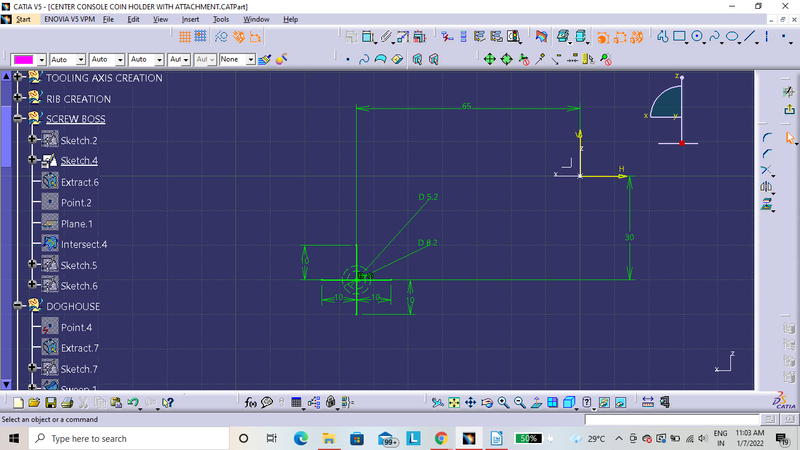
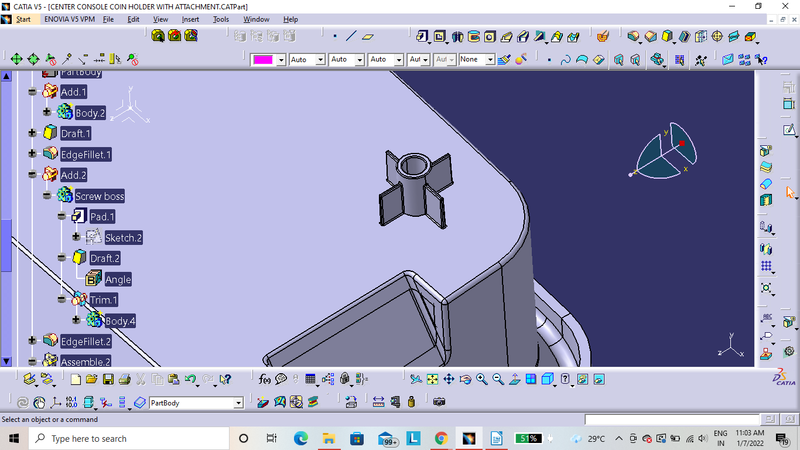
- Make an intersection with the Screw Boss and check the parameters of the screw boss. The final gives the fillets for the screw boss of a minimum of 0.25 radius. And use the translation option to make the object move from the required position.
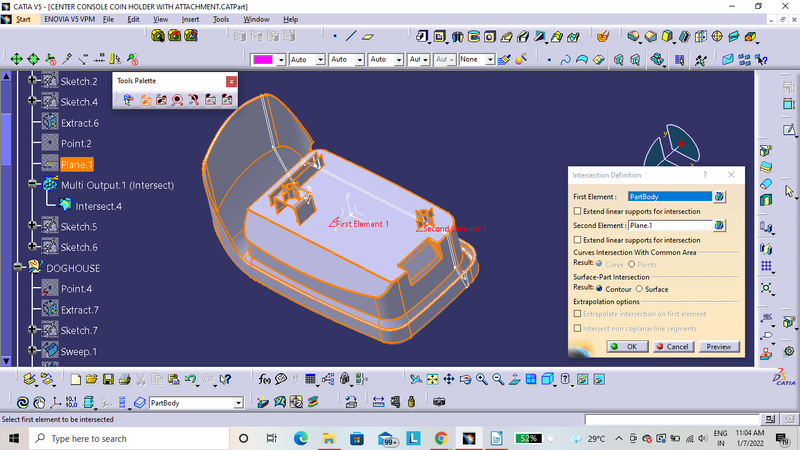
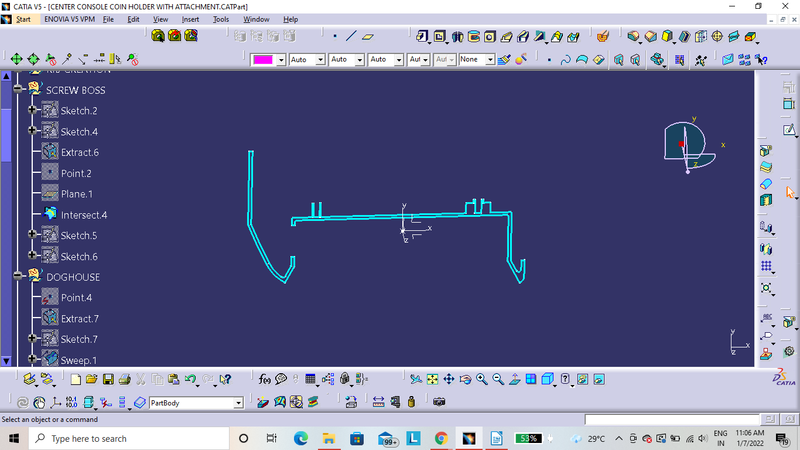
Step-5:
- Now start designing the Dog House for the component. The dog house is mainly used to avoid the sink marks on the component and to enlarge the extension of screw Boss up to certain heights.
Step-6:
- To start the Dog House insert a geometrical set and name as Dog House and start with the point at the center of the hole and use the point and create a plane in that plane start sketch on it draw a rectangle with 12mm of length and hide one side of the rectangle. And extract the line for extract the line use sweep command in sweep tool use Draft with Direction option with an angle of 1.5 deg select the tooling axis is the direction of pull in inside if the dog house with 21mm length and use the base extract and make an offset of 20mm from the base and trim the extra surface.
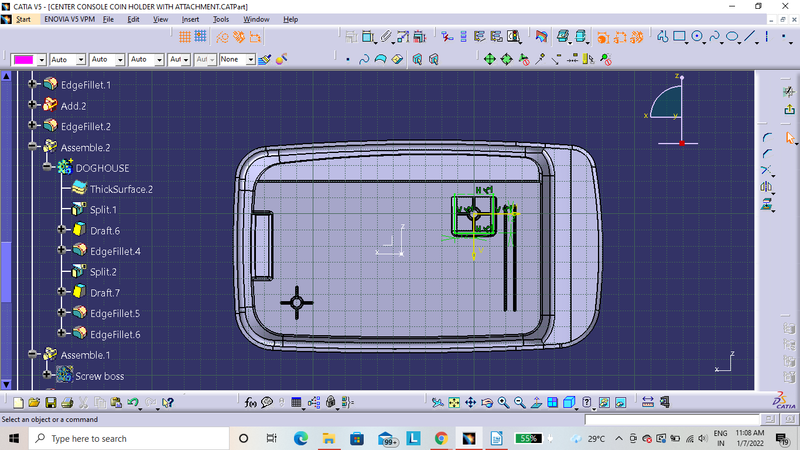
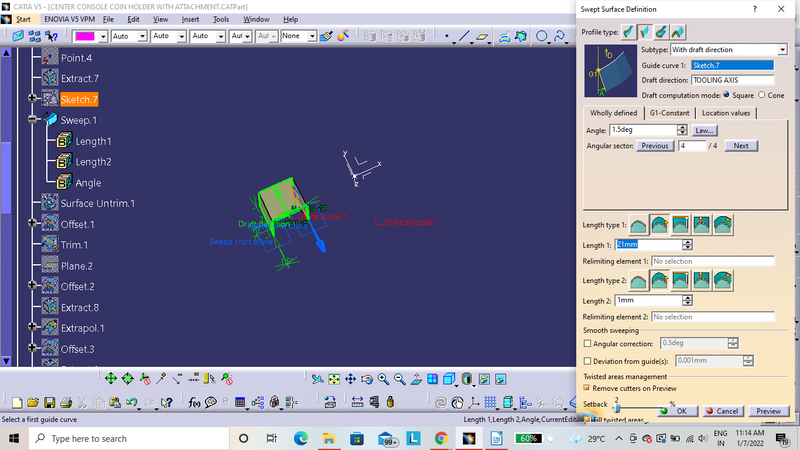
Step-7:
- Insert the Part Body and go to part design work-Bench and use thick surface command and add the thickness of 2mm on outside of sketch.
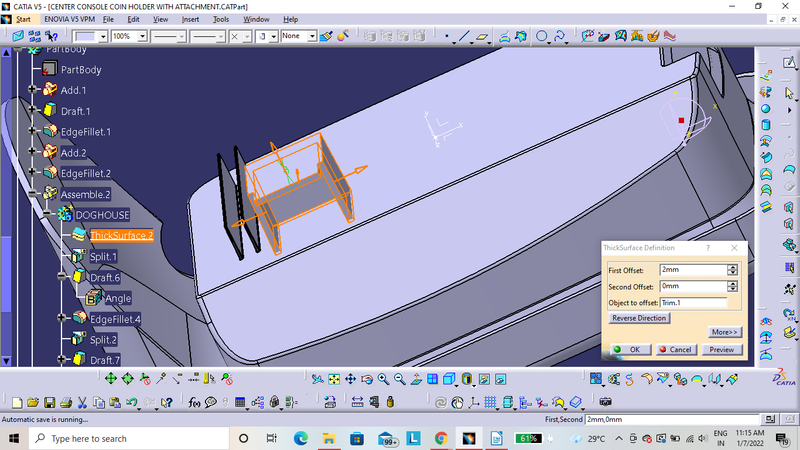
Step-8:
- Deactivate the screw boss features and edit the Dog House to add the extra features like a C & B if any issues in deactivating the Screw boss try to solve the issues and create the C and B feature on the Dog House.
Step-9:
- Before adding C and B Features check the Dog House is clearing the Tooling axis the main issue with the dog house it cannot clear the normal tooling axis of the component. we need to draw a Side Core Tooling axis for the Dog House. To create the side core tooling axis got the Tooling Axis geometrical set and select the line command and select the point in directions select the Z-axis in the direction of the line. Then give the Draft for the sides of the dog house and in the base keep the rare face for the axis of Draft select the side core tooling axis and check the draft is going to the component and select ok for the draft after giving the draft give the fillet for the dog house for inner face give the value of 1mm and for outer radius of the fillet is 1mm + thickness of component is 2mm= 3mm for the outer face.
Step-10:
- Next process for the dog house is to add the C & B features for the C feature it was given as 40% of the main component thickness.
∴2.5 x 0.4=1mm
- Take inner face as extract and make an offset of 1mm to outwards and for the B feature it the height can be taken as 3mm to 6mm in my case I am taking as 4mm and use cut with a surface command from the part-work bench and trim the inner part of the dog house and add draft for the cut top walls of the face at the draft value of 0.5 deg and at final add fillets for the final dog house.
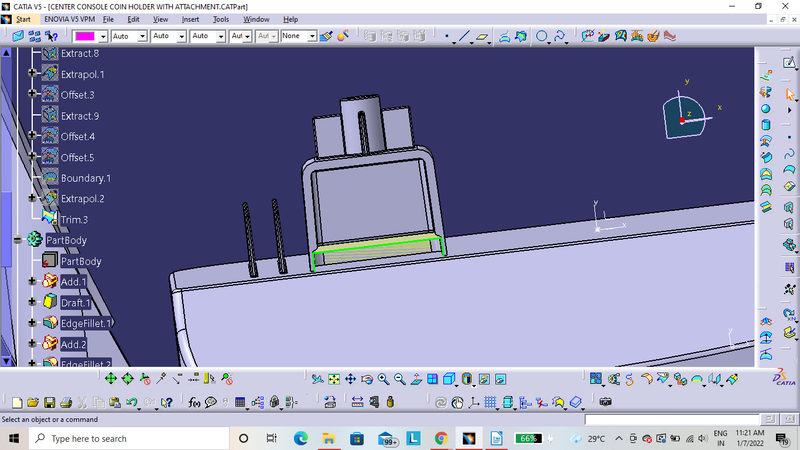
Step-11:
- At the final step of the dog House move the screw Boss features on the top of the Dog House by using the translate option to add the same feature in the component make a copy of the component and use the translate option and fix the features where ever it required.
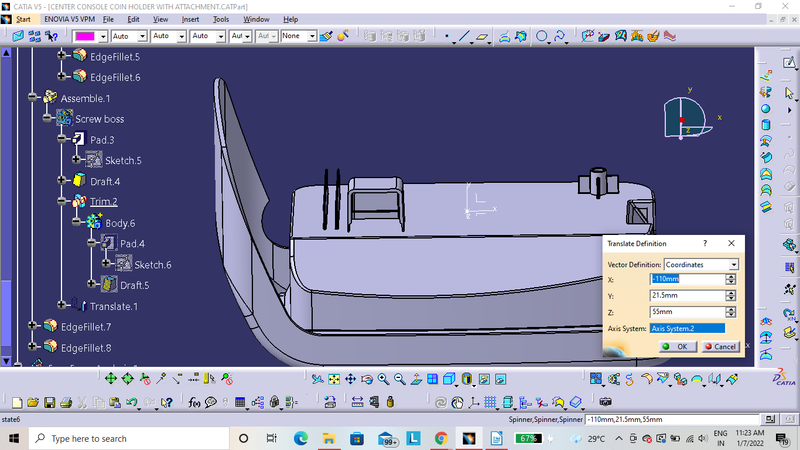
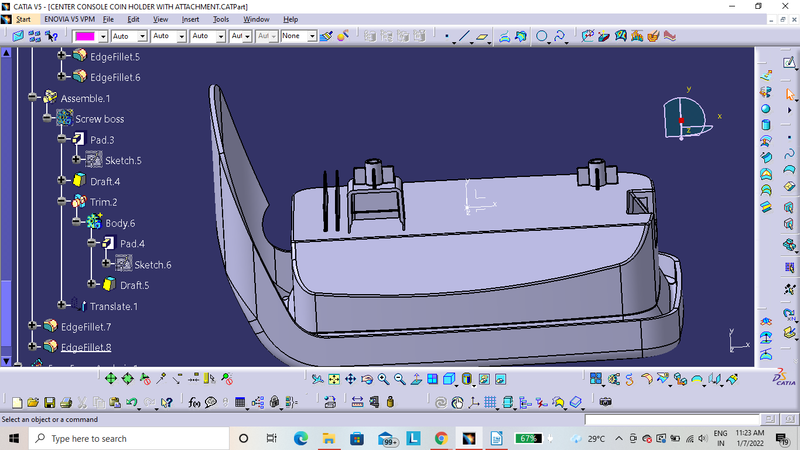
Step-12:
- Check the Draft analysis of the main component and Doghouse as well if there is any problem we can go to the previous step and rectify the problem. Draft analysis is also used to identify the problems in the component.
- For Draft, analysis select the Draft analysis tool in the Analysis command prompt the draft analysis tool opens and set the UCs icon lies on the Tooling axis and select the component and give an angle required for the component for the appearance of the component. Repeat the same process for the side core also.
Coin Holder Tooling Axis:
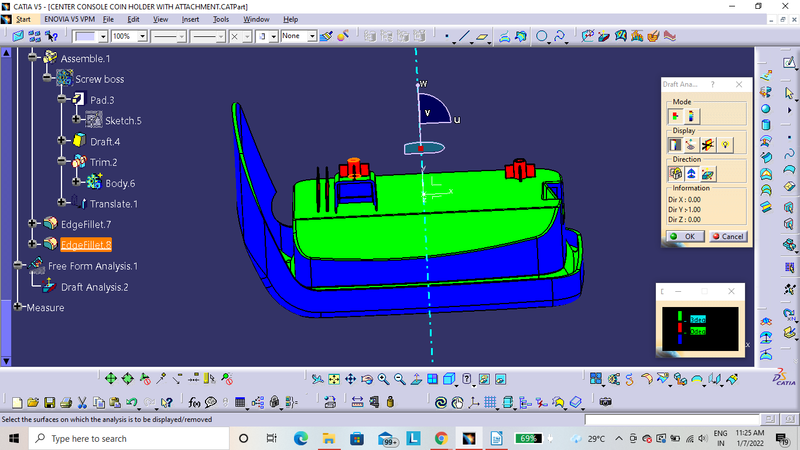
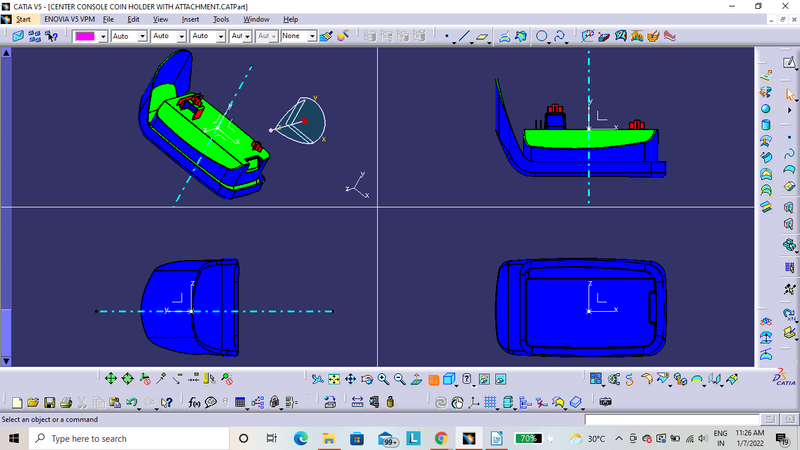
Side Core Draft Analysis:
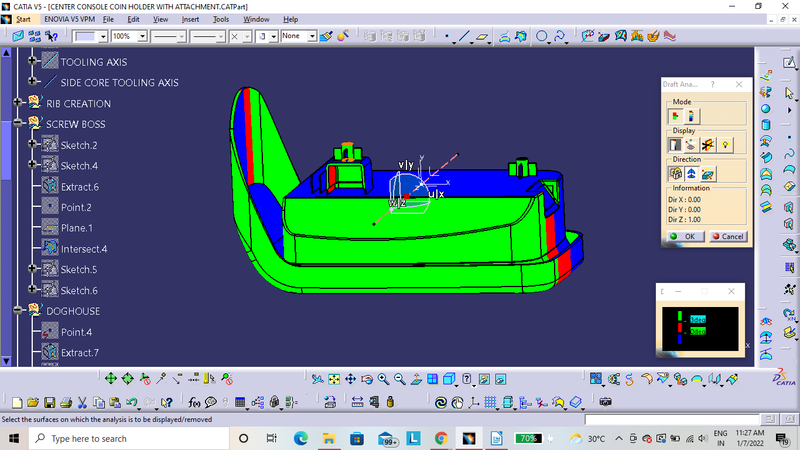
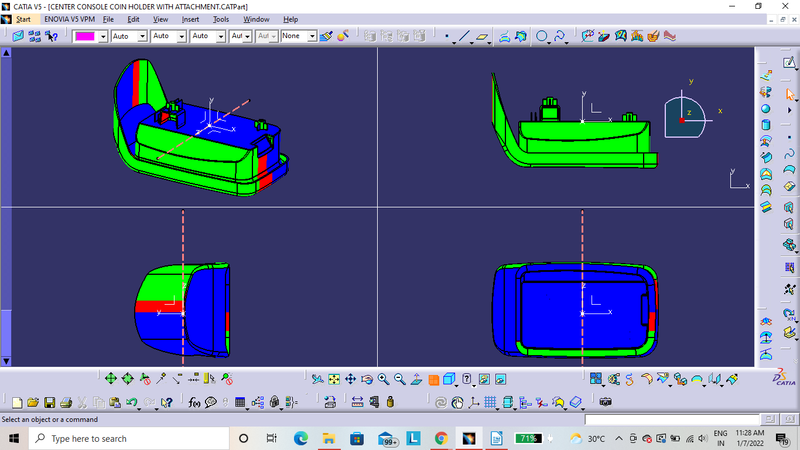
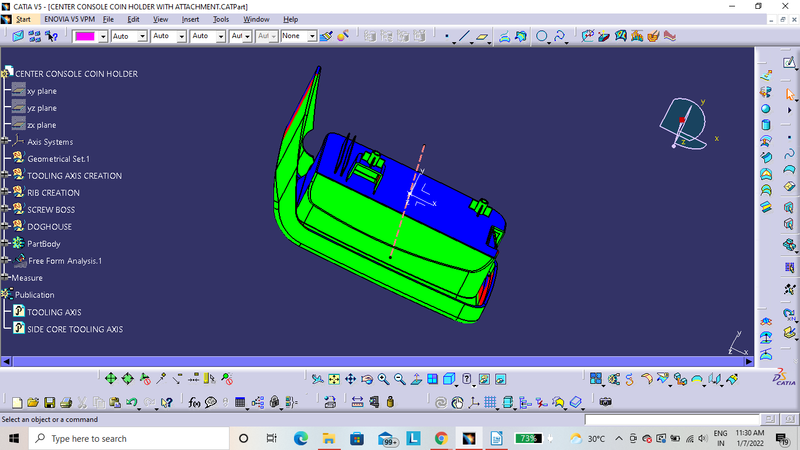
CONCLUSION:
- The Screw boss & Doghouse are created as per the design rules.