AIM
- In this challenge, we are required to do a literature review of various turbulence models and explain why DNS isn’t feasible according to Kolmogorov's scale.
- For the below geometry performs a 3D simulation and explain the recirculation region using velocity vectors.
- Consider the flow direction of air, the ball is traveling opposite to it at 60m/s. Explain in which direction the ball will curve by visualizing the wake region.
Solutions
1. Literature review of Turbulence models and explaining why DNS isn't feasible according to kolmogrov's Scale
Before moving on to the discussion of Turbulence models let's first understand whta is Reynolds number, as reynolds number plays a huge role in turbulence of fluid may it be air or liquid.then laters let's discuss about the definition and its breif exlaination of turbulence models and its types and how are we going to implement these models along with real life case sceniarios. Then later lets find why DNS isn't Feasible according to Kolmogrov's Scale.
What is reynolds Number?
Ans:-
- Reynolds number is a dimensionless quantity Which is used to determine the type of flow pattern as laminar or turbulent.
- Therefore Reynolds number is defined as ratio of inertial forces to that of viscous forces.
Re = ρvdμ
Where,
- Re is the Reynolds number
- ρ is the density of the fluid (kg/m3)
- V is the velocity of flow (m/s)
- D is the pipe diameter (m)
- μ is the viscosity of the fluid (kg/m.s)
Note:
- When the viscous forces are dominant (slow flow, low Re), they are sufficient to keep all the fluid particles in line, then the flow is laminar.
- When the inertial forces dominate over the viscous forces (when the fluid flows faster and Re is larger), the flow is turbulent.
- The Reynolds number can be used to compare a real situation (airflow around an airfoil and water flow in a pipe).
How is the Reynolds number calculated?
- First step is we need to Determine the type of flow (internal, external, etc.).
- Calculate the lenght or diameter
- From tables, determine the viscosity and the density of the fluid.
- For given flow velocity, calculate the Reynolds number.
- If we have kinematic viscosity then kinematic viscosity is defined as dynamic viscosity / density
What is the critical Reynolds number?
The critical reynolds number is associated with the laminar-turbulent transition, in which a laminar flow becomes turbulent.
- For flow over a flat plate, the generally accepted value of the critical Reynolds number is Re ~ 500000.
- For flow in a pipe of diameter D, experimental observations show that for “fully developed” flow, laminar flow occurs when Re < 2300, and turbulent flow occurs when Re > 3500.
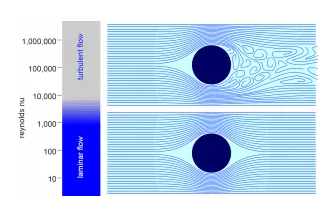
Fig 1 : Representing Laminar flow and turbulent flow using Re number
Application of Reynolds Number
The Reynolds number plays an important part in calculations in fluid dynamics and heat transfer problems.
- Used calculate the friction factor in a few of the equations of fluid mechanics.
- Used for heat transfer calculations since many other characteristic numbers (ex - Nusselt Number) depend on the flow regime.
- It is used when modeling the movement of organisms swimming through water.
- It is used to predict the transition from laminar to turbulent flow and is used to scale similar but different-sized flow situations, such as between an aircraft model in a wind tunnel and the full-size version.
- The predictions of the onset of turbulence and the ability to calculate scaling effects can be used to help predict fluid behavior on a larger scale, such as in local or global air or water movement and thereby the associated meteorological and climatological effects.
Laminar flow
|
turbulent Flow
|
1. Re is less than 2000
|
1. Re is larger than 4000
|
2. Low Velocity
|
2. High Velocity
|
3. Fluid particles move in straight line
|
3. Flow is characterised by irregular movement
|
4. Rare in practise in water systems
|
4. The most common type of flow
|
Now lets Understand What is turbulence models, and its types and its significants in CFD Modelling
What is turbulence?
Unsteady, irregular (aperiodic) motion in which transported quantities (mass, momentum, scalar species) fluctuate in time and space
- Identifiable swirling patterns characterize turbulent eddies.
- Enhanced mixing (matter, momentum, energy, etc.) results
Fluid properties and velocity exhibit random variations
- Statistical averaging results in accountable, turbulence related transport mechanisms.
- This characteristic allows for turbulence modeling.
Contains a wide range of turbulent eddy sizes (scales spectrum).
- The size/velocity of large eddies is on the order of mean flow.
- Large eddies derive energy from the mean flow
- Energy is transferred from larger eddies to smaller eddies
- In the smallest eddies, turbulent energy is converted to internal energy by viscous dissipation.
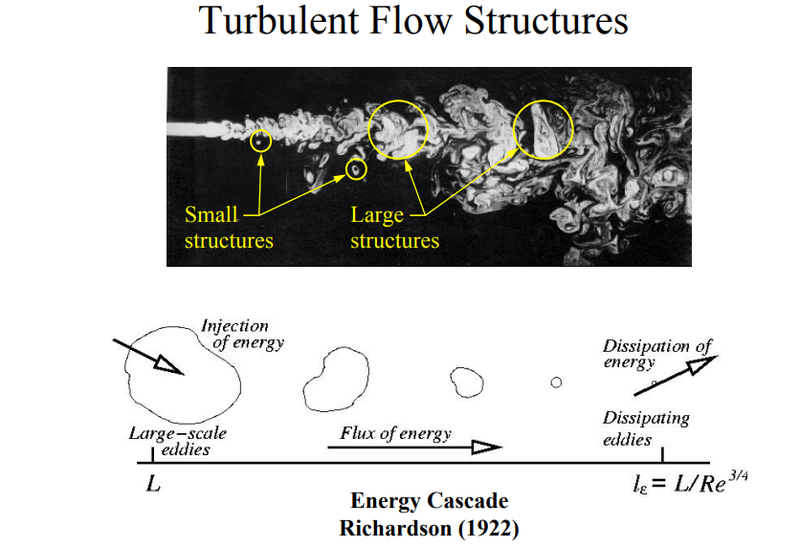
Figure - 2 Turbulent flow structures (Source ansys)
Types of Computational approach
- DNS - Direct Numerical Simulation
- LES - Large Eddy simulation
- RANS - Reynolds Averaged Navier stokes simulation
1. DNS (Direct Numerical Simulation)
- Numerically solving the full unsteady Navier stokes equation
- Resolves the whole spectrum of Scales
- No modelling is required
- But the cost is too prohibitive
- Not practical for Industrial applications
2. LES (Large Eddy simulation)
- Solves the filtered Navier stokes equation
- Some turbulence is directly resolved
- Less expensive than DNS
- Efforts and computational resources needed are still too large for most practical applications
- Available in fluent
- resolves large scales in flow field models small scales (so faster than DNS)
3. RANS (Reynolds Averaged Navier stokes simulation)
- Solves Time - Averaged Navier stokes equation
- All turbulent motion is modeled
- For most problems the time averaged flow (and level of turbulence) are all that is needed
- Many different models are available
- This is the most widely used approach for industrial flows
Turbulance Models Available in Fluent
1. RANS Based models
One quation models
Two Equation models
- Standarad k−ε
- RNG k−ε
- Realizable k−ε
- Standard k−ω
- SST k−ω
Reynolds stress Transport models
2. Detached Eddy simulations
3. Large eddy Simulations
DETAILS
1.First Order Models:
First order models assume analogy between laminar & turbulent flows. They assume that the average turbulent flow field is similar to the laminar flow field which results in lower accuracy.
It has three subtypes of models based on the number of equations the model is solving.
- Zero Equation Models
- One Equation Models (Spalart Allmaras model)
- Two Equations Models (K-epsilon model & k-omega model)
2. Second Order Models:
These models are solving the transport equations additionally to derive Reynolds stress terms in 3D.
As these models are solving additional equations to work in 3D & also PDEs are of the 2nd order, it has the highest accuracy but computationally very expensive. And because of large number of extra equations, these models are sensitive to boundary conditions as well. These models are commonly used in the industries.
This type also has subtypes.
- Algebraic Stress Model
- Reynolds Stress Model
NOTE: -
The main difference between first order & second order model
- Is that first order model uses the PDEs of 1st order to derive Reynolds stress terms while the second order models are using the PDEs of 2nd order
- Because of that the accuracy of the second order models are more than the first order models but computationally more expensive.
Zero Equation Model:
- No PDE is used to solve the turbulent viscosity.
- Fails to account for transient behaviour of turbulent viscosity which leads to lower accuracy results.
- Directly solves turbulent viscosity using a Mixing length model.
- Mixing length model assumes eddy viscosity terms to be dimensionally similar to two scales: Kolmogorov length scales & Kolmogorov velocity scales
1. RANS Based models
Spalart Allmaras
One Equation Model
Linear Eddy Viscosity Modeling
- The Spalart–Allmaras model is a one-equation model that solves a modelled transport equation for the kinematic eddy turbulant viscosity.
- In its original form, the model is effectively a low-Reynolds number model, requiring the viscosity-affected region of the boundary layer to be properly resolved ( y+ ~1 meshes).
- The Spalart–Allmaras model was developed for aerodynamic flows. It is not calibrated for general industrial flows, and does produce relatively larger errors for some free shear flows, especially plane and round jet flows.
- Incorrect for Shear flow, Separated Flow, or decaying Turbulence
- It solves a transport equation for a viscosity-like variable
as another equation. This is called as the Spalart–Allmaras variable.
- no wall functions and smaller near-wall gradients
- low memory requirements
- stable
- less sensitive to numerical error from non-layered mesh near wall
- shows good convergence
TWO EQUATION MODELS
These models solve two PDEs to determine following quantity based on the model used.
- Turbulent Kinetic Energy & Turbulent Dissipation Rate (K-epsilon Model)
- Turbulent Kinetic Energy & Specific Dissipation Rate (K-omega Model)
- K-epsilon Model
This model has three different variants:
- Standard K-epsilon (k-ε)
- Realizable K-epsilon model
- Renormalized Group(RNG) model
1. Standard K-epsilon (k-ε)
turbulence model is the most common model used in CFD to simulate mean flow characteristics for trubulant flow conditions. It is a two equation model that gives a general description of turbulance by means of two transport equations (PDEs).
- best for free-shear layer flows with small P gradients
- It uses wall functions to calculate epsilon near wall.
- low memory requirements
- shows good convergence
- The first transported variable is the turbulent kinetic energy (k).
- The second transported variable is the rate of dissipation of turbulent kinetic energy (ε).
- inaccurate for adverse pressure gradients, strong curvature, and jet flow
- valid only for fully turbulent flow
2. Realizable K-epsilon model
k—turbulent kinetic energy
ε—rate of dissipation of kinetic energy
- Realizable & RNG types of K-epsilon models modify the existing epsilon equations to detemine Reynolds Stress terms.
- It solves some of constraints on Reynolds stresses.
- It shows consistent results with physics of turbulent flows.
- better for rotation, strong adverse pressure gradients, recirculation, mixing, channel and BL flows
- predicts spreading rate around planar and round jets
- produces nonphysical turbluent viscosity in situations with both rotating and stationary fluid zones (multiple reference frame systems)
3. Renormalized Group(RNG) model
k—turbulent kinetic energy
ε—rate of dissipation of kinetic energy
- generally more accurate and reliable than k–ε: especially for rotating flows (incl. time-dependent turbulent vortex shedding)
- favorable for indoor air simulations formula for turbulent Pr number
- inaccurate for vortex evolution
- unstable in steady-state solutions
- 10–15% more CPU time
k-omega Model:
It has two types of variants: one is Standard K-omega model & the other is SST K-omega model.
(a) Standard K-omega model:
- no wall functions
- low memory requirements
- often accurate where k–ε model fails
- This model does not contain terms that are defined at the wall. Hence, wall functions are not required at the wall to capture turbulence flows.
- k—turbulent kinetic energy
- ω—specific dissipation rate
- It is widely adopted in aerospace & turbomachinery components.
- inaccurate for adverse pressure gradients, strong curvature, and jet flow
- oversensitive to inlet free-stream turbulence properties
- sensitive to initial guess
(b) SST (Shear Stress Turbulence) K-omega model:
- It is go-to model in all the other industries than the aerospace & turbomachinery.
- SST model uses a blending functions to transition from standard k-omega model to a higher Reynolds model away from the wall to better approximate turbulent flows.
- no wall functions , accurate near wall
- k—turbulent kinetic energy
- ω—rate of dissipation of kinetic energy
- overestimates turbulence in regions with large normal
- strain (better than k–ε, however)
- converges slowly (use other model for initial guess)
RSM (Reynolds stress transport model)
- k—turbulent kinetic energy
- ω—rate of dissipation of kinetic energy
- good for anisotropic turbulence (highly swirling flows; stress-driven secondary flows)
- moderately computationally expensive (50–60% more CPU time; 15–20% more memory over k–ε)
- Converges slowly
Second-Order Models:
Solves transport equations for the Reynolds stress terms. These models give the most accurate results and are highly sensitive to boundary conditions. They are also computationally expensive.
algebraic Reynolds stress model is developed from the modeled dynamic equations for the Reynolds stress.
RSM is more offers better accuracy in flows with high degrees of anisotropy, significant streamline curvature, flow separation, zones of recirculating flow, or flows influenced by rotational effects for which k-omega and k epsilon gives unsatisfactory results.
Large Eddy Simulation (LES)
RNG–LES
- CS—Smagorinsky constant
- resolves large scales in flow field
- models small scales (so faster than DNS)
- CS not universal
- computationally expensive
Detached Eddy Simulation (DES)
- DES (Detached Eddy Simulation)
- hybrid treatment using RANS approach near wall and
- LES approach in bulk flow (typically Spalart–Allmaras for RANS)
- omplicated grid generation
why DNS isn’t feasible according to Kolmogorov's scale
- More time needed to converge
- Very fine meshes which results in more computational resources needed to run Hence industries dont preffer this method as its inefficient
First lets understand what is Kolmogrov's Scale
- Kolmogorov’s theory describes how energy is transferred from larger to smaller eddies.
- How much energy is contained by eddies of a given size.
- How much energy is dissipated by eddies of each size.
The challenge in turbulence modeling is the modeling of the eddies.
- Eddy is the swirling of a fluid and the reverse current created when the fluid is in a turbulent flow regime i.e when the flow around the body exceeds critical velocity.
- Larger eddies break into smaller eddies on consuming smaller eddies
- Sometimes smaller eddies combine to form larger eddies This process is called energy cascading.
- Large eddies size∝(LU∞) . Larger eddies gain energy from the mean flow.
- Small eddies size∝(LRe34). Smaller eddies gain energy from large eddies.
- Kolmogorov's length scale is the smallest η=(ν3ε)14
- ε=(U3L) is the rate of dissipation of turbulent kinetic energy.
- Kolmogrov time scale tn=(νε)12, To detrmine turn over time of particular eddie)
To check the feasibility of the DNS
The ratio of the largest to the smallest eddies is given below
(Lη)=⎛⎝L(ν)34⎞⎠ε14
(Lη)=⎛⎝L(ν)34⎞⎠⎛⎝(u)34L14⎞⎠
(Lη)=⎛⎝L(u)34ν⎞⎠
(Lη)=Re34
- To model the vortex they are divided into cells containing grids and this is easy for the large vortex.
- the same size of the grid is not useful to resolve a small vortex, for a smaller vortex we need to reduce the size of the grid.
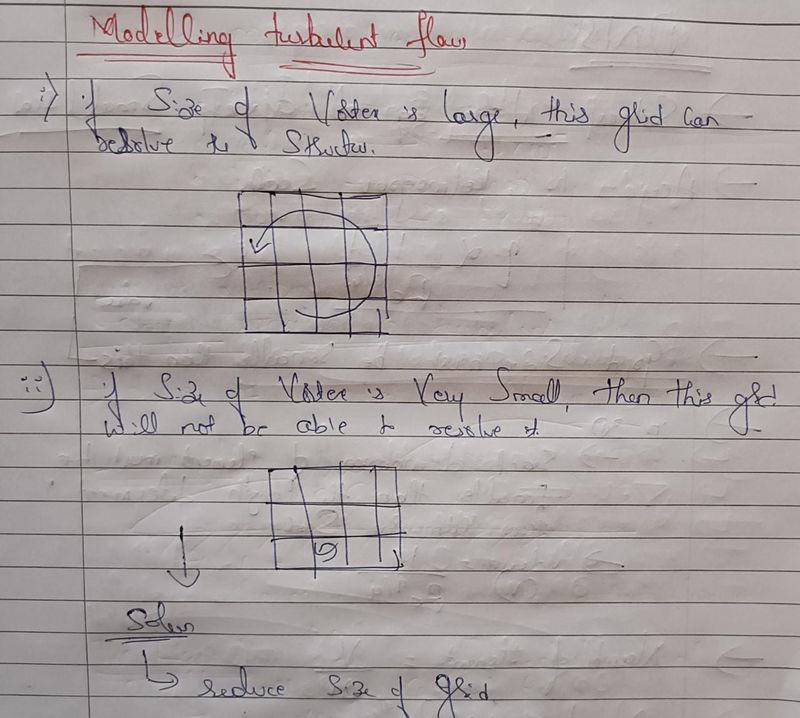
- The challenge always is to model the smaller vortex as the grid size is reduced the number of the grids will increase which in turn increase the computational costs.
- In the DNS (Direct Numerical Simulations) N-S equations are solved in a very small scale.
- Grid size must be smaller than the scale and in 3-D Each dimension must be smaller than the length of scale determined from Kolmogorov's scale.
- So for the volume Volume(V)=1Re94 .
- which is a very small value. Kolmogorov's length scale describes the smallest dissipation-scale eddies.
- The number of grid points necessary to resolve a turbulent flow in a numerical model is therefore proportional to R9/4.
- the number of elements = VΔV
- Number of elements ∝Re94
- This leads to a very large number of 3D elements which demands more computational power and computational time.
- So DNS is mostly avoided but still performed in 2D simulations for some scientific applications.
- The usage of DNS in industrial applications impossible keeping in mind the complexities of the design and the size of the domains present.
To understand Golf Ball Dynamics, First Let's Understand its fluid dynamics and force acting on it (I.e Drag)
Golf ball dimples and their impact on the ball traveling through the air can be described using fluid dynamics.
Basically, there are two types of fluid dynamics flow:
In general, many real-life applications are turbulent in nature. This can generally be obtained from a factor called Reynolds number.
In the current scenario, when the ball is smooth, it gives rise to something close to a laminar flow. In this case, the fluid flow downstream detaches from the surface of the ball in the form of vortices. This phenomenon is called flow separation, which gives rise to a viscous wake behind the ball that slows it down.

Figure 4 - Separation of flow
What do golf ball dimples do?
- The dimples act as artificial turbulators, creating turbulence next to the ball surface and creating two layers of air going around the ball.
- The top layer is going faster than the bottom layer, i.e., air clings to the ball’s surface, which creates turbulence.
- This reduces the drag and helps the ball to travel farther than a smooth one.
- This is another new term: drag.
- Drag is a force component which arises as a result of a difference in velocity of a solid and fluid body, and it opposes the solid motion through the air—in this case, the golf ball.
- A dimpled golf ball probably only has about half the drag of a smooth one

figure - 5 - Ball with Dimples and without dimples
- when a body is moving in the air it experiences drag force and lift. Drag force is in the opposite direction to the body's relative motion, and the lift is a total upward force on the body.
- Drag is divided into pressure and friction drag, pressure drag is due to the pressure difference between the front and back of the body. The friction drag is due to the surface friction (due to no-slip near the surface there will be boundary layer formation with a gradient of velocity).
- Pressure Drag is significant in bluff bodies like spheres and friction drag is more significant in streamlined bodies.
- So more streamlining also increases friction drag.
- The number of dimples on the golf ball is usually between 330 and 500.
- Golf balls are usually covered with dimples in a highly symmetrical way.
- The ball will wobble if it’s not symmetrical, or its flight will depend on which part of the ball faces forwards or sideways as the ball spins.
- The turbulent flow increases the mixing or interchanging of energy in the boundary layer, which helps the flow to be attached for the delay of flow separation.
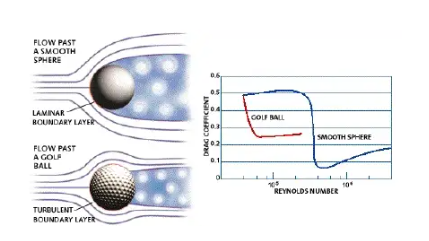
Figure - 6 - Flow modifications imposed by addition of dimples
2 Simulation - For the below geometry performs a 3D simulation and explain the recirculation region using velocity vectors.
- Import the geometry model and create the enclosure.
- Meshing is performed with the proper sizing and element size and see that the number of elements to be less than 5 lakh(Because of student version).
- Naming is done with inlet, outlet, and symmetry to walls.
- Then solver setup is done by giving the boundary conditions
- the solver is selected as K-epsilon with standard wall function.
- For viewing the results in proper planes are created and plots for velocity are created.
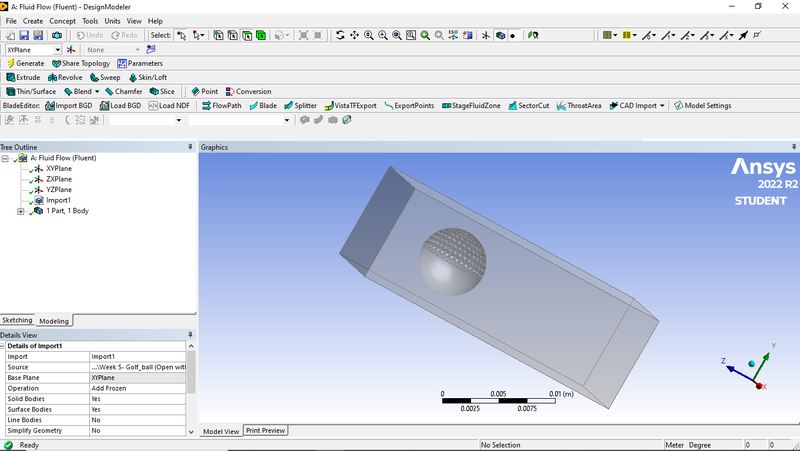
Figure 7 - Design Modeller Geometry of dimpled golf ball enclosed , Cut section image
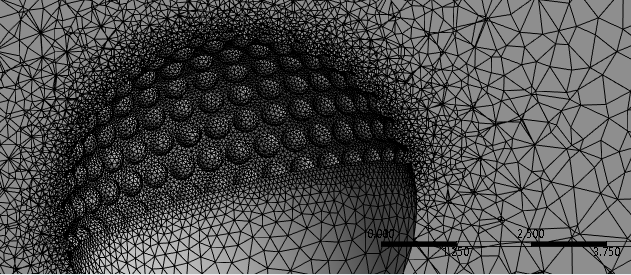
Figure 8 - Mesh model of golf ball
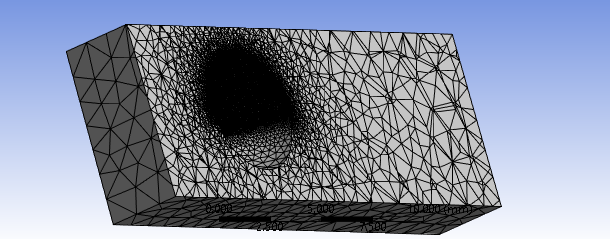
Figure 9 - Mesh model of cut section plane

Figure 10 - Mesh details 1
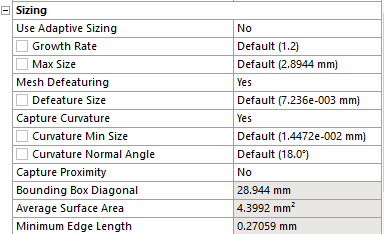
Figure 11 - mesh details 2
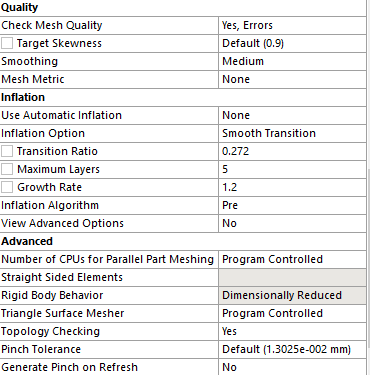
Figure 12 - Mesh details 3

Figure 13 - mesh details 4
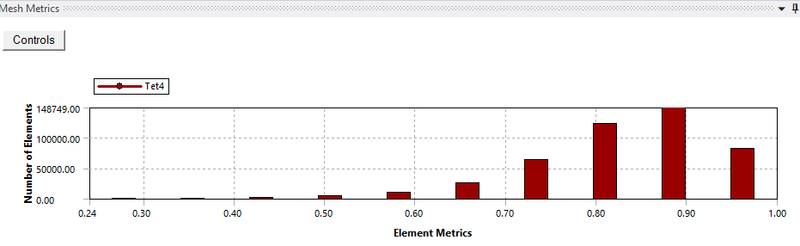
Figure 14 - Mesh Quality
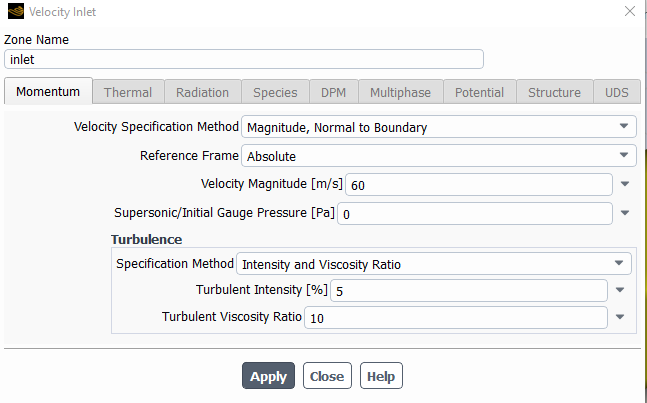
Figure 15 - Boundary conditions
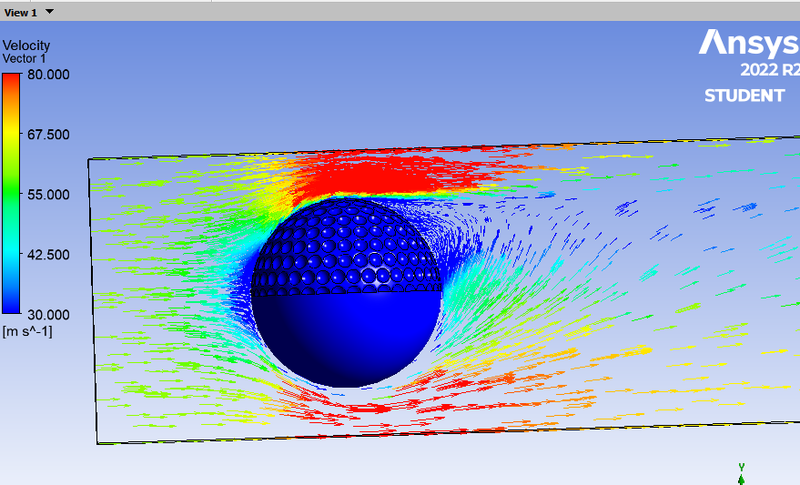
Figure 16 - Velocity Vector
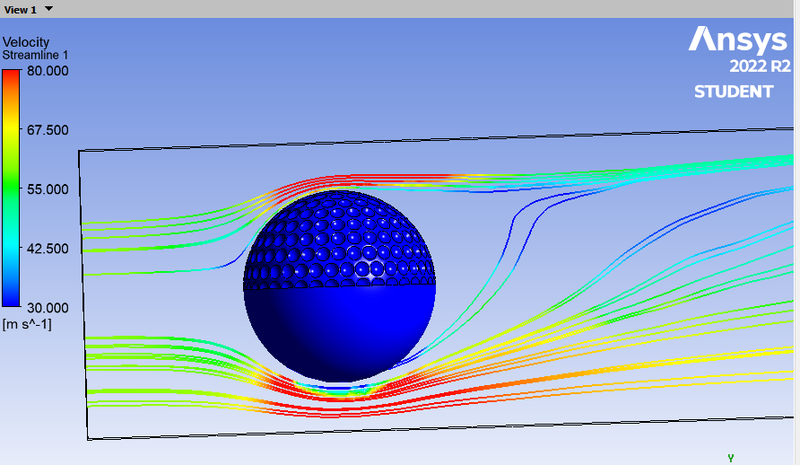
Figure 17 - Velocity Stream line
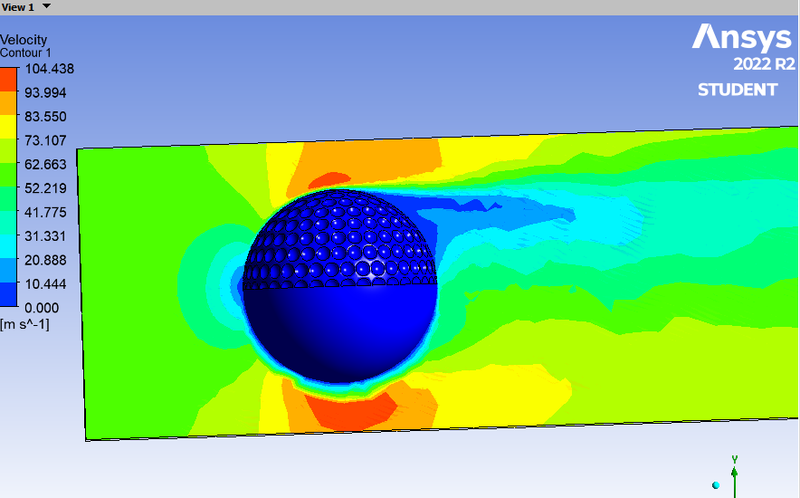
Figure 18 - Velocity contour plot
3. Analysis - Consider the flow direction of air, the ball is traveling opposite to it at 60m/s. Explain in which direction the ball will curve by visualizing the wake region.
- From above velocity vector plot, and contour plot, we can conclude that the ball will go or curve downward.
- The wake region or recirculation region at the back side of ball shows the direction of arrow circulating downward.
- The recirculation region also helps the flow seperating from the ball.
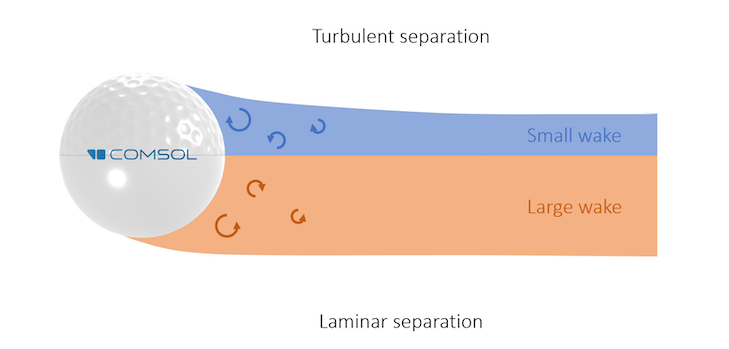
Generally the term 'wake' is used to describe any downstream disturbance to flow caused by an obstacle.
Recirculation is a specific condition where the flow separates from the body of the obstacle. This creates a low pressure area immediately downstream which sucks fluid back into this region from the main flow with the net result of creating a circulating vortex or pair of vortices. This condition creates marked increase in drag compared to situations where the flow remains attached to the surface.