Static Structural Analysis on the Bevel Gear :
Aim -
- To perform static structural analysis on the Bevel Gear and solve for Von Misses Equivalent stress,Equivalent Elastic Strain and Total Deformation.
Objective :
- To perform a Structural Analysis on the Bevel Gear for all three cases with the material Structural Steel.
- To perform grid dependency test on the bevel gear.
- To add the required materials to the case set up from the Engineering data source.
- To compare the simulation results for all the three materials.
- To compare the results of all the three cases of Total Deformation, Von-Mises Stress and Equivalent Elastic Strain and find out the best.
Theoretical FrameWork :
- A bevel gear is a toothed rotating machine element used to transfer mechanical energy or shaft power between shafts that are intersecting, either perpendicular or at an angle. This results in a change in the axis of rotation of the shaft power. Aside from this function, bevel gears can also increase or decrease torque while producing the opposite effect on the angular speed.
- A bevel gear can be imagined as a truncated cone. At its lateral side, teeth are milled which interlock to other gears with its own set of teeth. The gear transmitting the shaft power is called the driver gear, while the gear where power is being transmitted is called the driven gear.
- The number of teeth of the driver and driven gear are usually different to produce a mechanical advantage. The ratio between the number of teeth of the driven to the driver gear is known as the gear ratio, while mechanical advantage is the ratio of the output torque to the input torque.
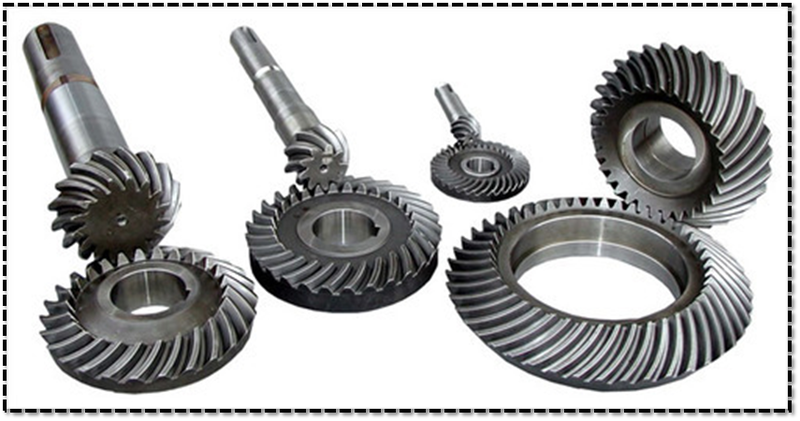
Grid Dependency Test :
- Grid dependency test ia a method used in FEA to get the optimum results by reducing mesh density in a given component.Mesh refinement, mesh convergence are the other names used to define Grid dependency test.
- The grid dependency test is a process used to find the optimal grid condition that has the smallest number of grids without generating a difference in the numerical results based on the evaluation of various grid conditions.
- This test incorporates the most basic and accurate way to evaluate mesh quality, which is to refine the mesh until a critical result such as the maximum stress in a specific location converges: meaning that it doesn’t change significantly as the mesh is refined.
Use of Grid Dependency Test :
- The simulation softwares does not provide us the accurate mesh size for our model to get the optimum results, their work is to provide the results by conducting simulation based on the mesh size entered by us. Thus our job is to enter the correct mesh size to begin a simulation that results in optimum value. As a human we don't know the correct mesh size to get the optimum results. Hence we are undergoing grid dependency test.
- Here in grid dependency test we start the simulation with coarse mesh or a greater mesh element size and then we reduce the mesh element size step by step till we get the optimum result after which there won't be any changes in the optimum results even though we further refine the mesh.
Procedure :
Phase 1- Material Set Up :
- To set up the material for the spur gear model. First, drag and drop the static structural analysis workspace into the project schematic from the analysis system. This is shown in below Figure 2.

Figure 2-Ansys Workbench Workspace. |
- After deploying the static structural analysis system in the project schematic workspace.
- Define the Engineering Data and geometry, To define the Geometry and Engineering Data, Right Click on the Engineering Data and click to edit, it will take to the Engineering Tab.
- There Right Click on the Material Tab, A window will Pop-Up stating Engineering data sources.
- Click on the Engineering Data Sources, There go and select the material to define the engineering data. This is shown in below Figures 3,4,5.
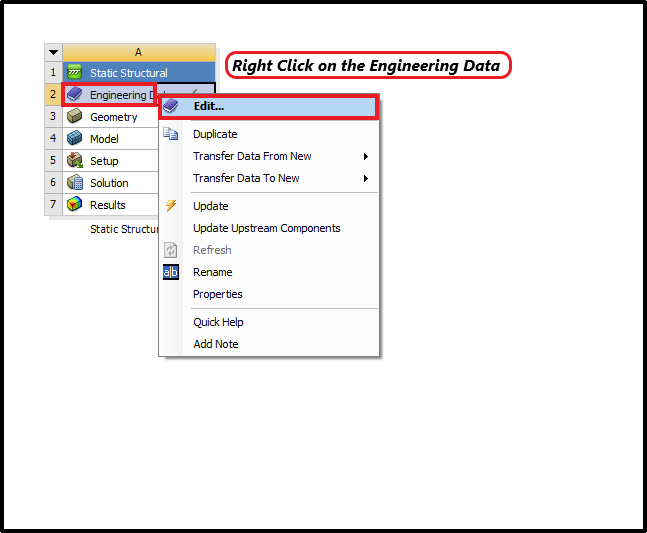
Figure 3-Right Click on the Engineering Data. |
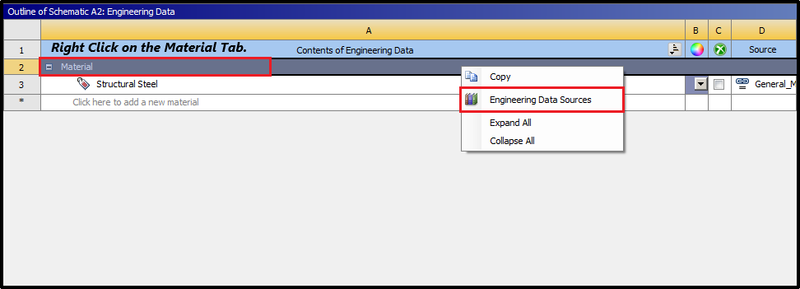
Figure 4-Right Click on the Material Tab. |
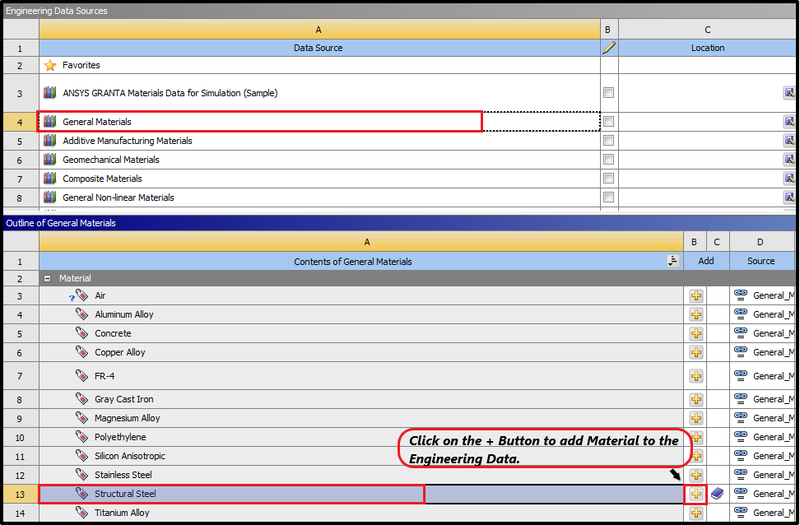
Figure 5-Select the Material as Structural Steel to Define the Engineering Data. |
Phase 2-Geometry Set Up :
- Next set up the geometry. To set up the geometry, Right-Click on the Geometry option >> Import Geometry. This is shown in below Figure 6.
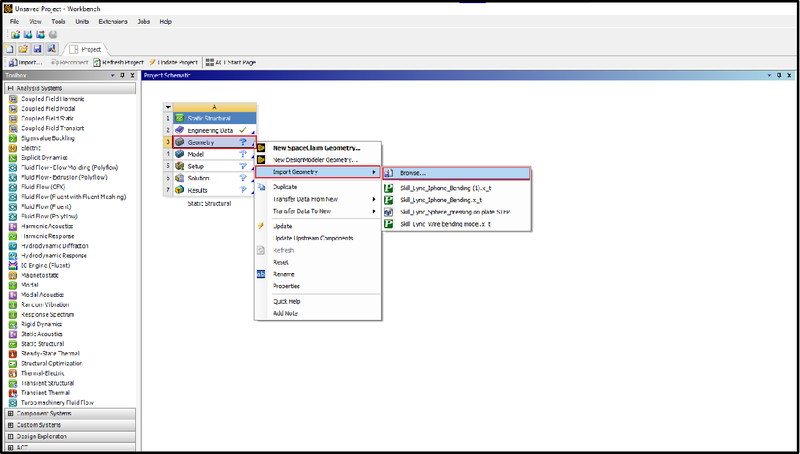
Figure 6-Importing Geometry. |
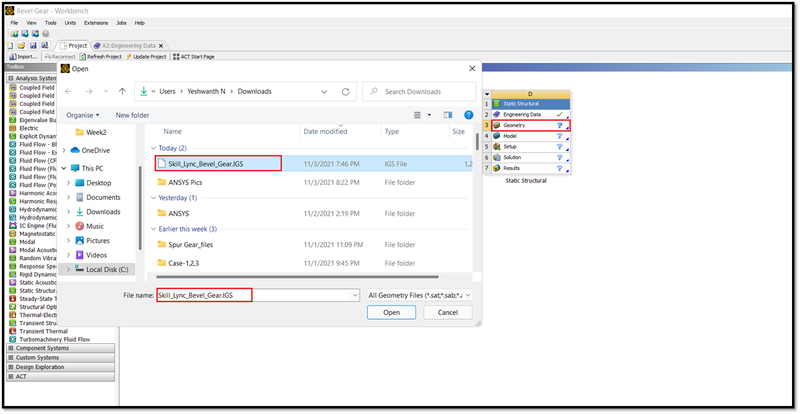
Figure 7-Selecting the Geometry to Import. |
- Next double click on the geometry to check, Whether the model imported is spur gear or not. Space Claim Workspace will open.The model will be imported in the space claim,Which is shown in below Figure 8.
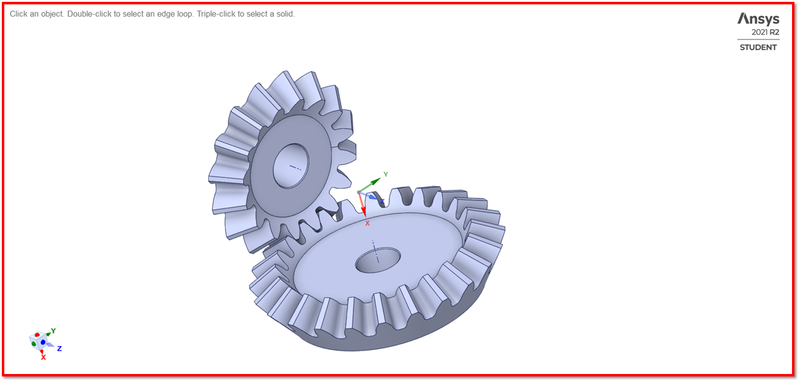
Figure 8-Bevel Gear in the Space Claim. |
- Next we have to do some modifications to the geometry,We have to do pocket on the both the gears.
- To do pocket,Go to the Sketch >> Circle >> Select Face >> Draw a Circle with 25mm dia.Which is shown in below Figure 9.
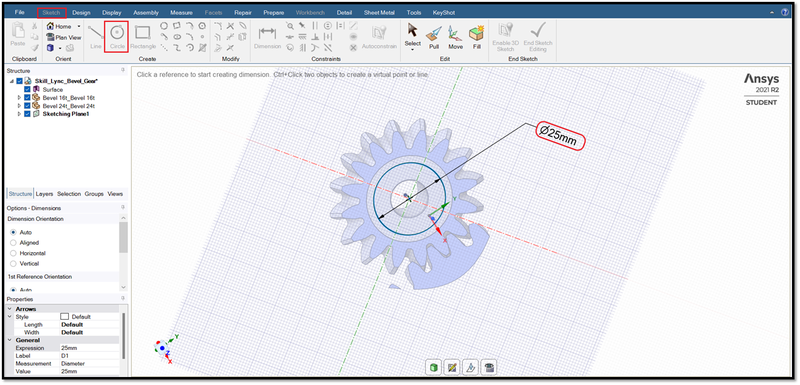
Figure 9-Create a Circle with 25 mm Dia. |
- Simillarly draw circle on the other gear with 45 mm Dia and remove the material.Which is shown in below Figure 10.

Figure 10-Create a Circle with 45 mm Dia. |
- After removing the material with 25 and 45 mm dia,The Modified Geometry is shown in below Figure 11.
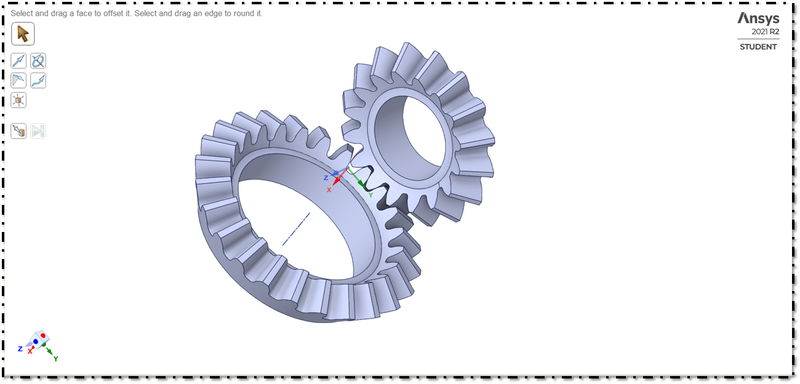
Figure 10-Geometry Modified. |
Phase 3-Model Set Up :
- Next, define the model, Double click on the model, The Mechanical Workspace will open, There go and define the material,set up the load case for all three cases.
- The Model loaded in the mechanical workspace is shown in below Figure 11.
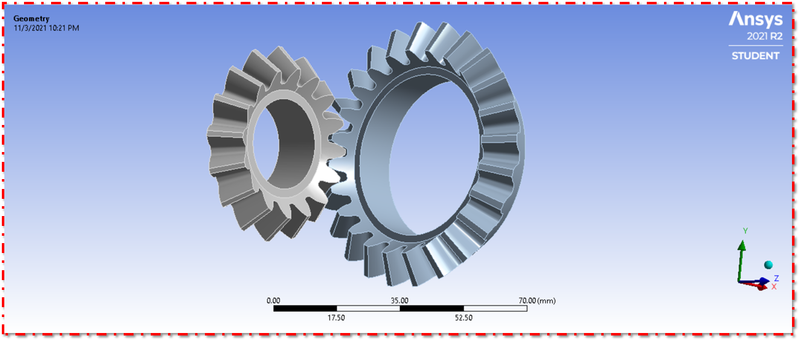
Figure 11-Model Loaded in Mechanical Workspace. |
3:1 Assign Material :
- Next define the material as structural steel for the bevel gear which is shown in below Figure 12.
- Simillarly define the material for all the cases.The material properties is shown in below Figures 13.
- To assign a material,Click on the Geometry Bevel Gear >> Parameter Window >> Assignment >> Structural Steel.
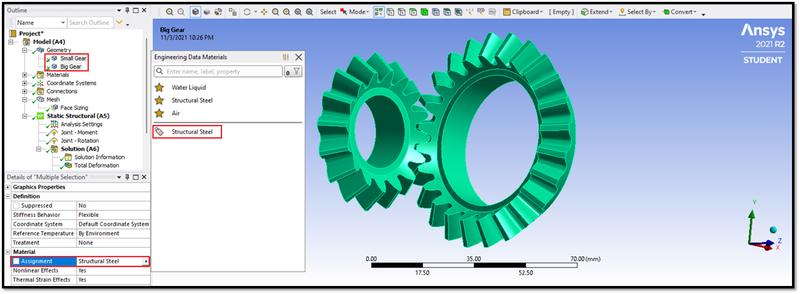
Figure 12-Define Material. |
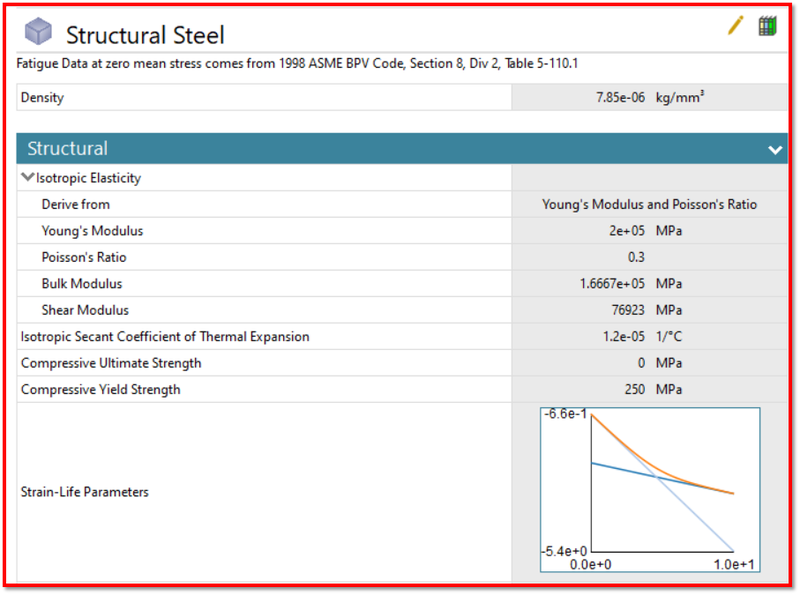
Figure 13-Mechanical Properties of Structural Steel. |
3:2 Define Connections :
- Next after defining the material,Now define the contact for the bevel gear.
- To define a contact,First right click on the default contact and rename it as rename based on definition,Which is shown in below Figure 14.
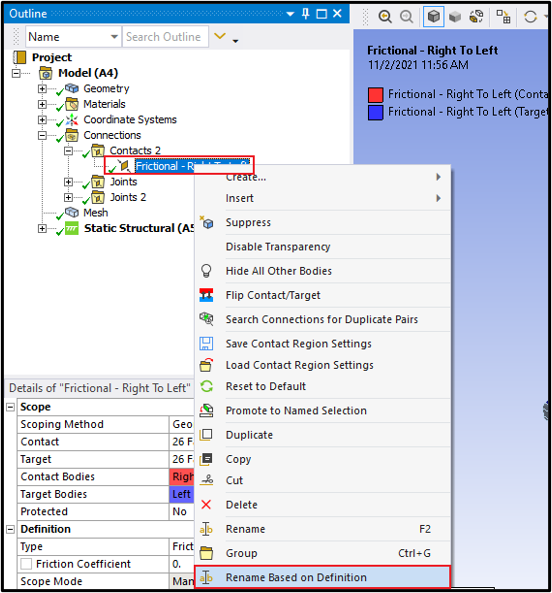
Figure 14-Rename Based on Definition. |
- Now define the contact which is shown in below Figure 16.
- Select the Contact and Target faces of the gear which is shown in below Figure 16.
- Select the tooth faces for the small gear as a contact and click the apply.
- Select the tooth faces for the big gear as a Target.
- In the Paremeter Window,
- Keep Frictional as a contact type, which maintain frictional force between the contact surface based on Friction coefficient.
- Keep Symmetric as a behavior of the contact, which assume contact faces and Target faces are same.Cause,it leads to quick convergence.
- Keep Formulation as Augmented Lagrange Algorithm which help to increase the stiffness of the contact and resists the penetration between them.
- Keep Interface Treatment as Adjust to Touch, which make touch to each other instead of gaps between them and also avoid the penetration between them.
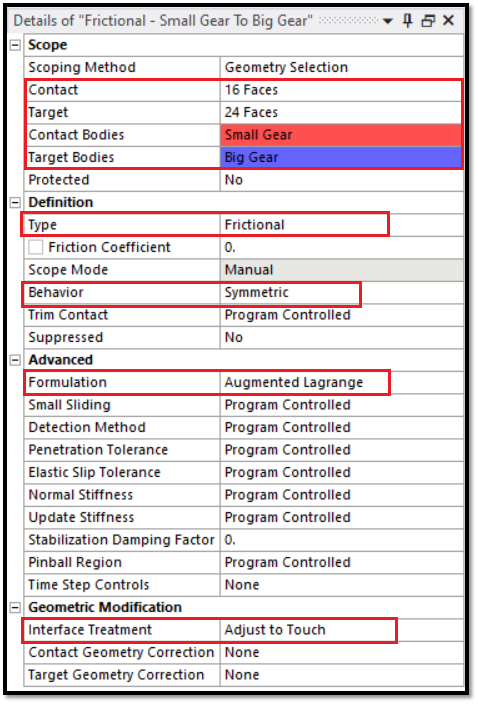
Figure 15-Connection Parameters. |
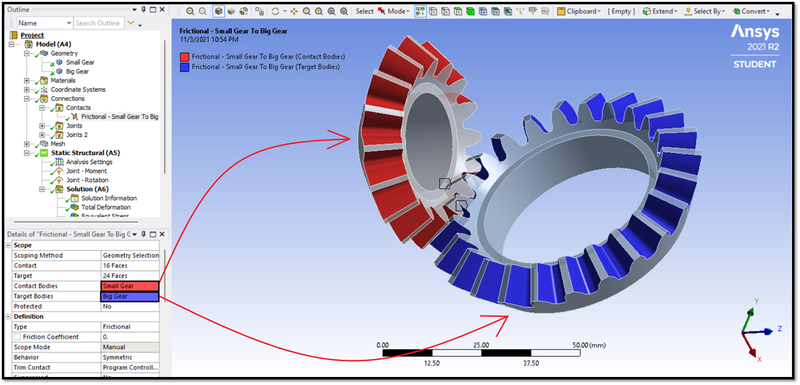
Figure 16-Define the Contact. |
3:3 Define Joints :
- After defining the contact, We have to deploy joints for the spur gear.
- To create a joints,Right Click on the Connections >> Insert >> Joint.Which is shown in below Figure 17.
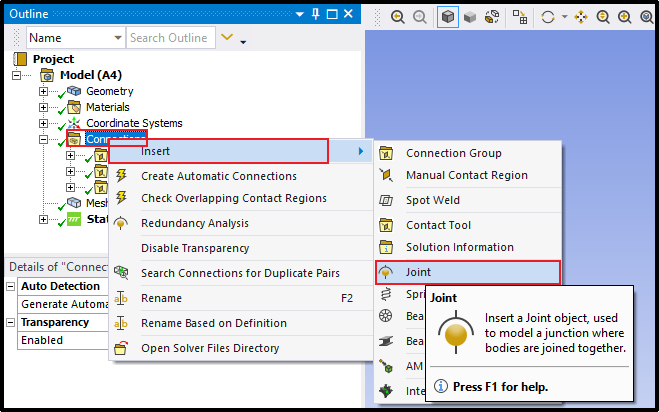
- Next in the parameters window, We have to select the type as Body-Ground for both joints in the connections panel.
- And select the scope, Which is shown in below Figure 19 and 20.
- All the parameters should be entered is shown in below Figure 18.
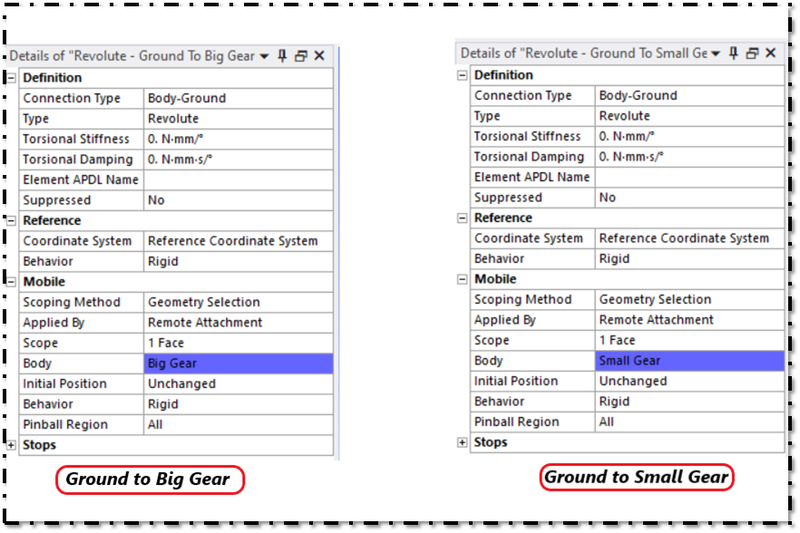
Figure 18-Parameters Windows of Two Joints. |
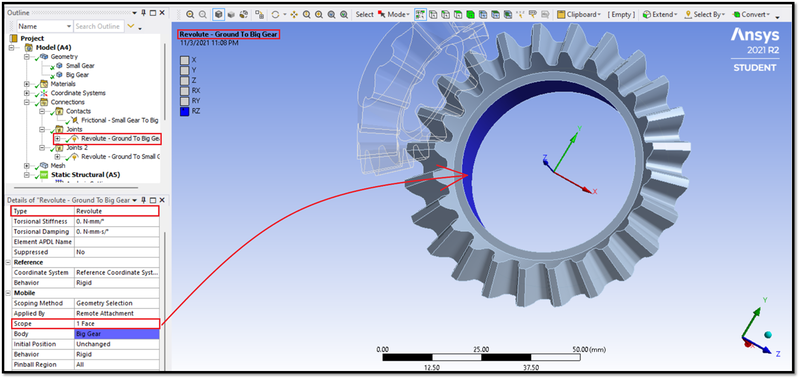
Figure 19-Select the Faces for the Scope. |
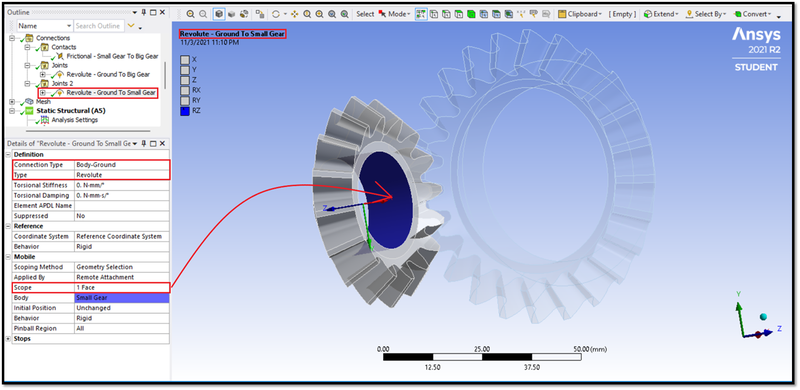
Figure 20-Select the Faces for the Scope. |
3:4 Meshing :
- After defining the joint in the connections panel,We have to define mesh for the spur gear.
- To define Mesh,Click on the Mesh >> Give Mesh Size as 4 mm.Which is shown in below Figure 21.
- Here we are refining the mesh for the tooth faces,Cause we have to see the stress developed at the tooth faces,So we are refining the mesh for the tooth faces.
- To refine a mesh,Click on the Mesh >> Insert >> Sizing >> Select the Faces of Tooth >> Mesh Size as 1.75 mm.Which is shown in below Figures 21 and 22.
- Element Size = 6 mm.
- Face Mesh Element Size = 1.75 mm.
- Mesh Method = Volumetric meshing with Tetrahedrons.
- No of Nodes = 25892.
- No of Elements =13844.
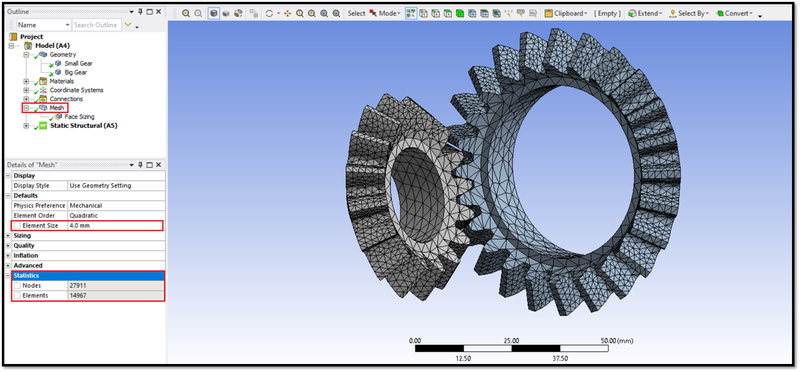
Figure 21-Meshed Bevel Gear with 4 mm Size. |
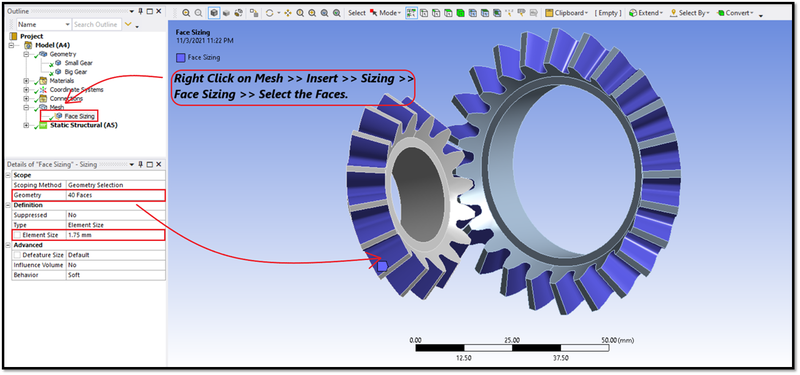
Figure 22-Refined the Mesh with 1.75 mm. |
3:5 Analysis Settings :
- Next, we have to give some parameters in the analysis settings.Which is shown in below Figure 23.
- To give the parameter's value, Click on the analysis Settings and the give the values.
- Increase the number of time step = 6
- Auto Time Stepping = On
- Define By = Time
- Initial Time Step = 0.2 sec
- Minimum Time Step = 5e-003 sec
- Maximum Time Step = 1 sec
- Large Deflection = On
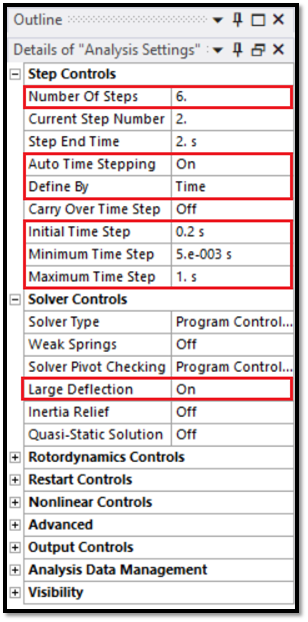
Figure 23-Analysis Settings. |
3:6 Boundary Conditions :
- After giving some parameters in the analysis settings,We have to give boundary conditions.
- Create a two joints,One for Rotation and Other for Moment, Which is shown in below Figures 24 and 25.
- To create Joint Loads, Right Click on the Static Structural >> Insert >> Joint Load.
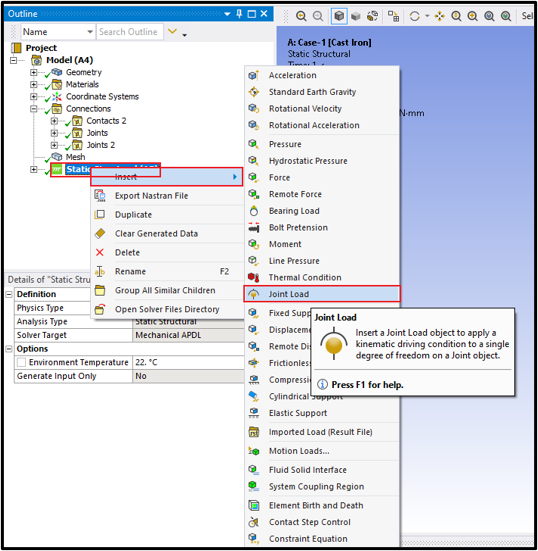
Figure 24-Create Joint Loads. |
Joint - Rotation :
- Joint = Revolute Ground to Small.
- Type of Joint = Rotation.
- Degree of Freedom = Rotation about Z axis.
- Magnitude = Tabular data.
- Tabular data = Rotation is 0 degree to 120 degree.
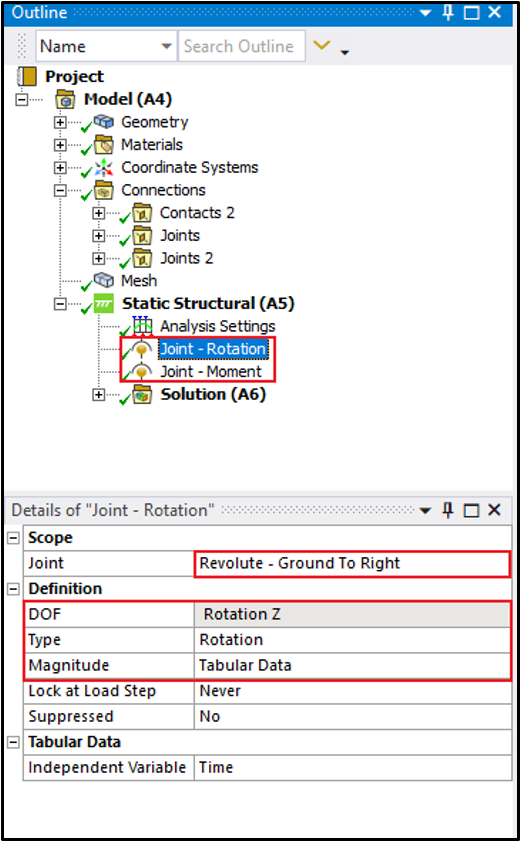
Figure 25-Joint Load for Rotation. |
Joint - Moment :
- Joint = Ground to Big.
- Type of Joint = Moment.
- Degree of Freedom = Rotation about Z axis.
- Magnitude = Tabular data.
- Tabular Data = 10 KN for all the 6 time steps.
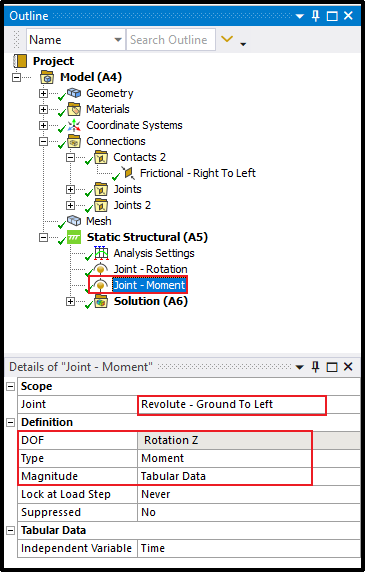
Figure 26-Joint Load for Moment. |
- Next, select the Joint Load Rotation, We have to give values for that, Which is shown in below Figure 27.
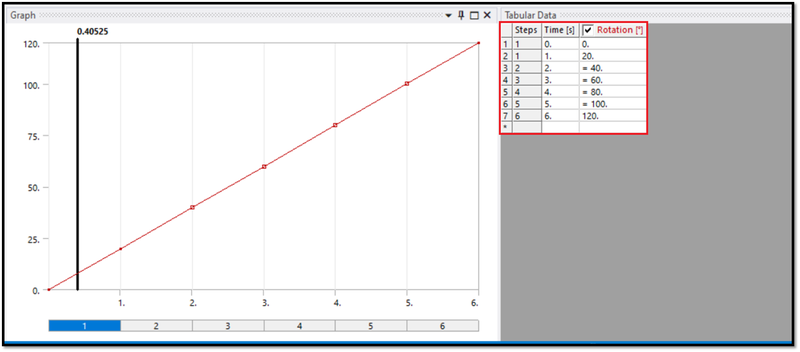
Figure 27-Give the Values for the Rotation. |
- Next, select the Joint Load Moment, We have to give values for that, Which is shown in below Figure 28.
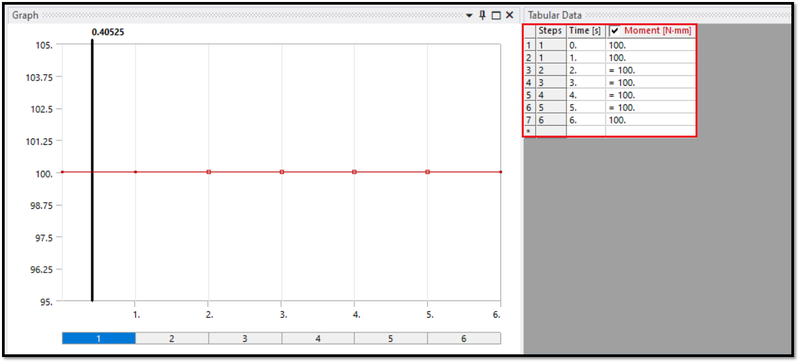
Figure 28-Give the Values for the Moment. |
- The Joint Loads created is shown in below Figure 29.
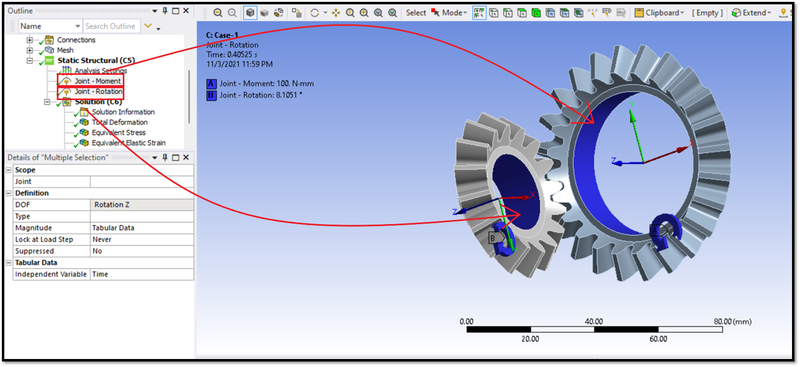
Figure 29-Joint Loads Created. |
Phase 4-Request for the Outputs :
- Here we have to request outputs for the VonMisses Stress, Strain, and for Total Deformation.
- To request Output for Stress,Right Click on the Solution >> Insert >> Stress >> Equivalent Von Misses Stress.
- To request Output for Strain,Right Click on the Solution >> Insert >> Strain >> Equivalent Von Misses Strain.
- To request Output for Total Deformation,Right Click on the Solution >> Insert >> Deformation >> Total Deformation.
- This is shown in below Figure 30.
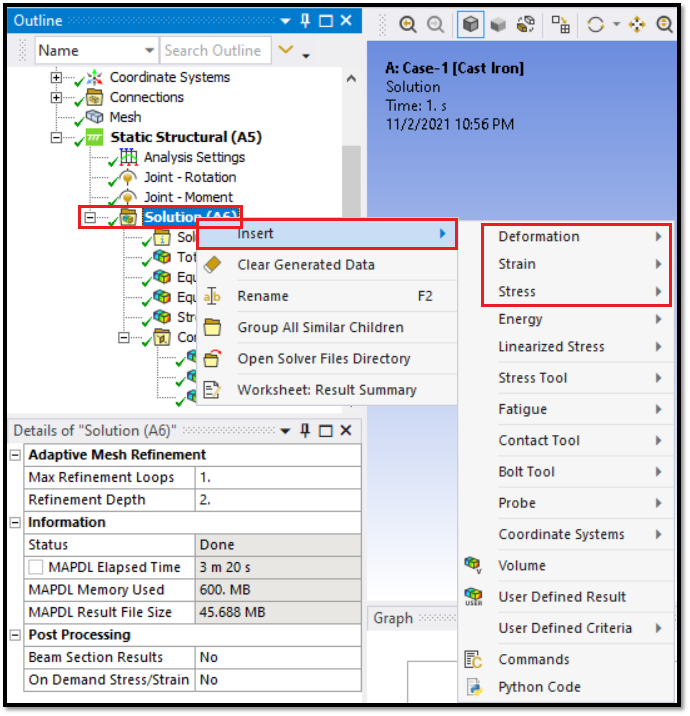
Figure 30-Requesting Outputs for the Stress, Strain, and Deformation. |
- Next request output for the contact.
- To request Contact Tool >> Right Click on the Solution >> Insert >> Contact Tool >> Pressure >> Status >> Frictional Stress.Which is shown in below Figures 31 and 32.
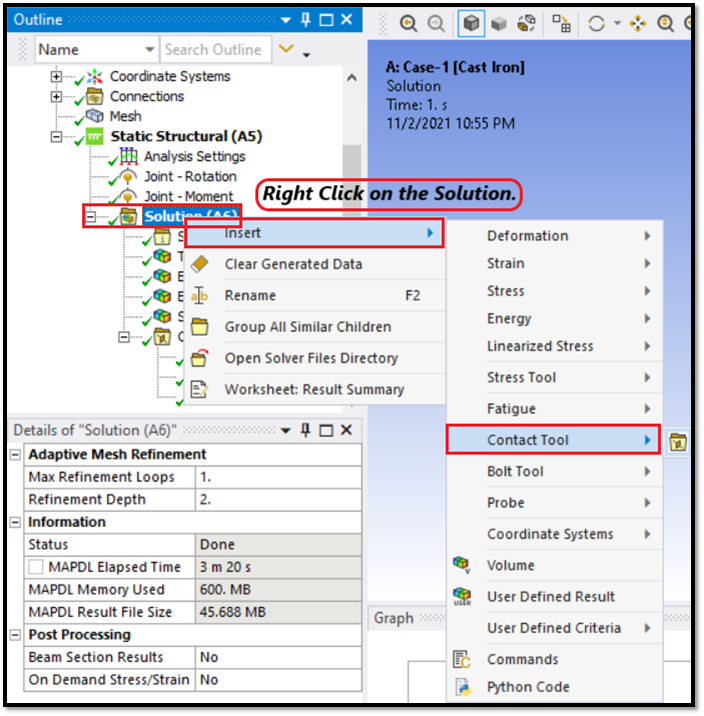
Figure 31-Requesting Output for Contact. |
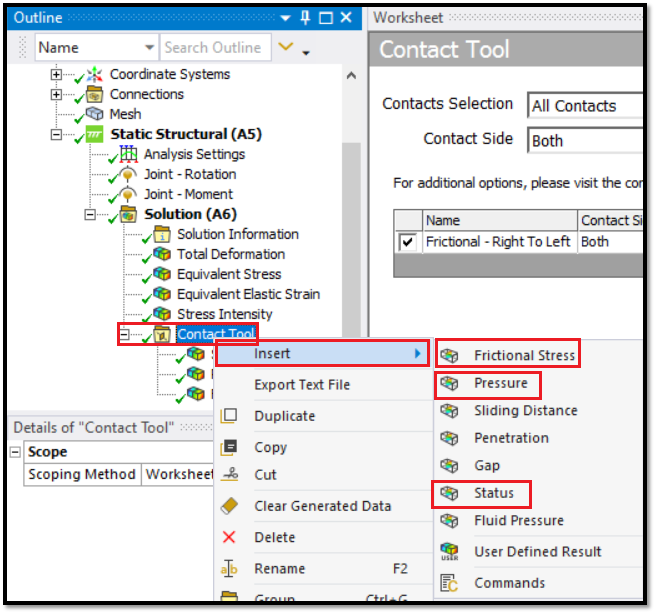
Figure 32-Requesting Outputs for Contact Tool. |
- Simillarly request the outputs for the Stress Tool and Fatigue Tool.
- The Output requested for the Bevel Gear is shown in below Figure 33.
- After requesting all the outputs which is shown in below Figure 33. Run the Simulation.
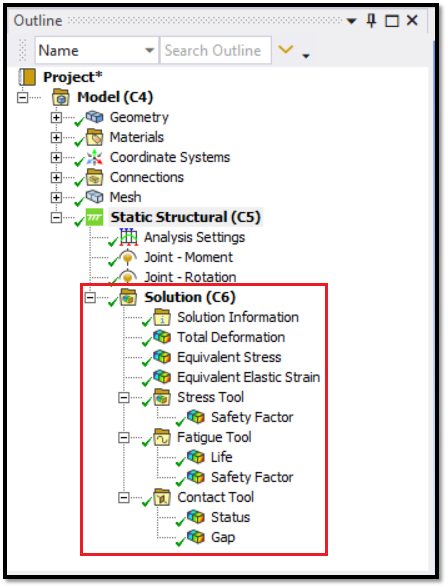
Figure 33-Required Outputs Requested. |
Phase 5-Run the Simulation for all the three Cases :
- To run the simulation, Right Click on the Solution >> Solve. This is shown in below Figure 34.
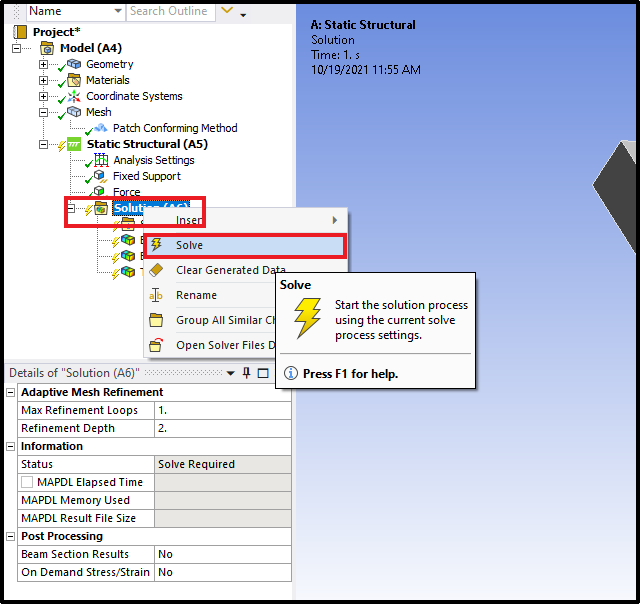
Figure 34-Solve all the Outputs Requested. |
- After solving the outputs requested, the simulation results for all the three cases is shown in the below Figures.
Equivalent Von Misses Stress [Case 1-With 6 mm Mesh Size] :
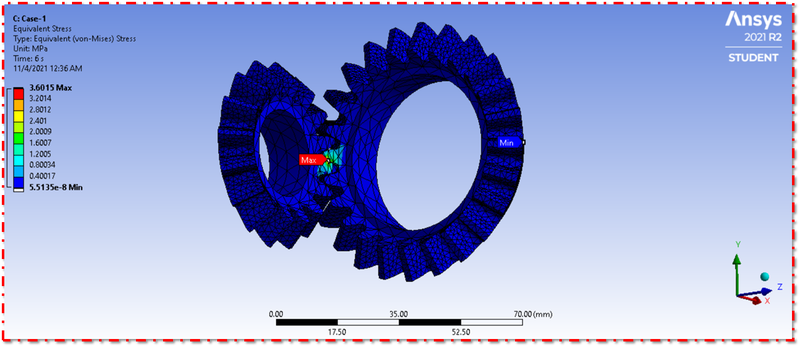
Figure 35-Equivalent Von Misses Stress Case 1 [6mm Mesh Size]. |
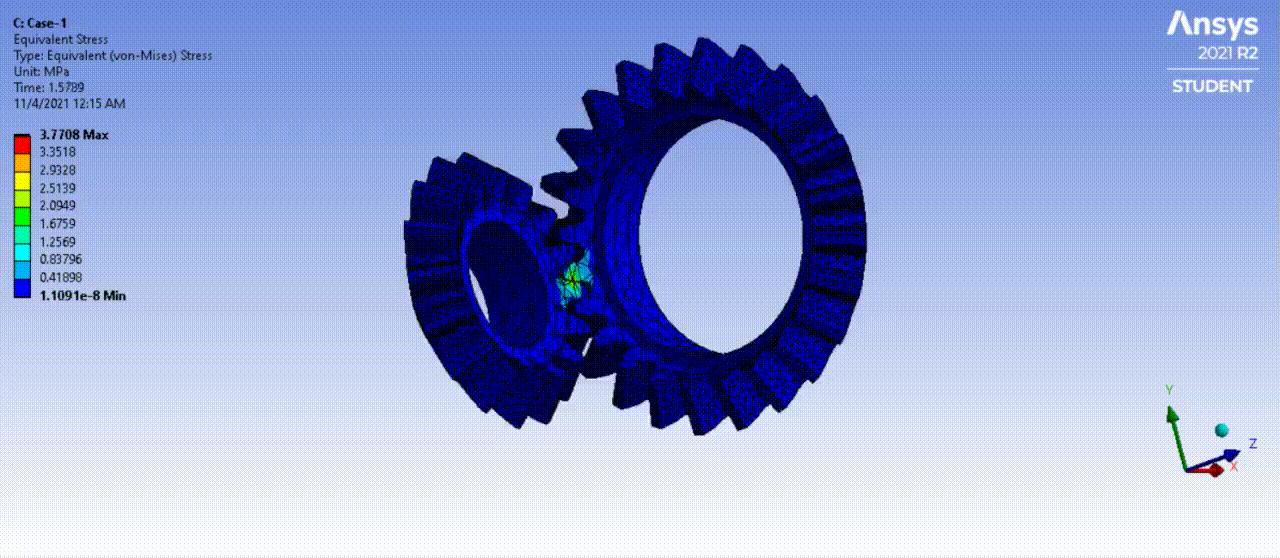
Figure 36-Equivalent Von Misses Stress Simulation Animation Case 1 [6mm Mesh Size]. |
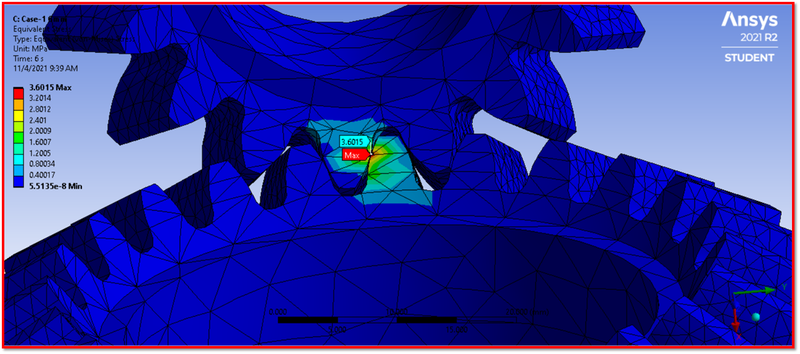
Figure 37-Maximum Stress at the Tooth Contact [Case-1]. |
Equivalent Von Misses Stress [Case 2] :
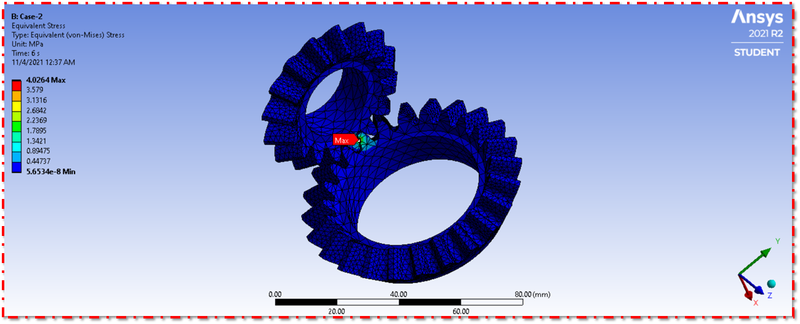
Figure 38-Equivalent Von Misses Stress Case 2 [5 mm Mesh Size]. |
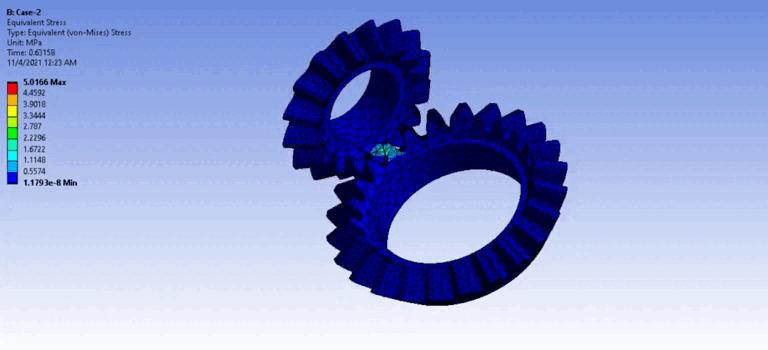
Figure 39-Equivalent Von Misses Stress Simulation Animation Case 2 [5 mm Mesh Size]. |
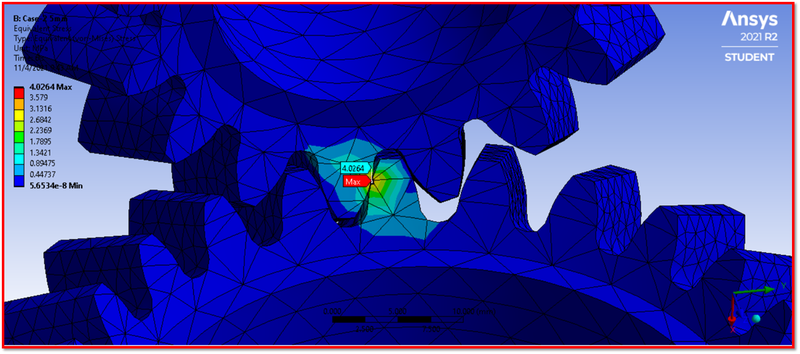
Figure 40-Maximum Stress at the Tooth Contact [Case-2]. |
Equivalent Von Misses Stress [Case 3] :
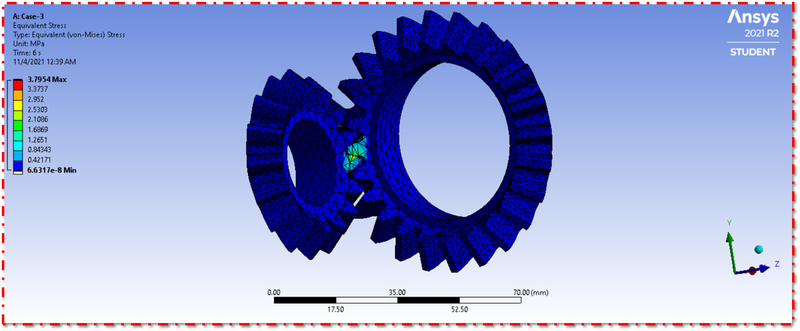
Figure 41-Equivalent Von Misses Stress Case 3 [4 mm Mesh Size]. |
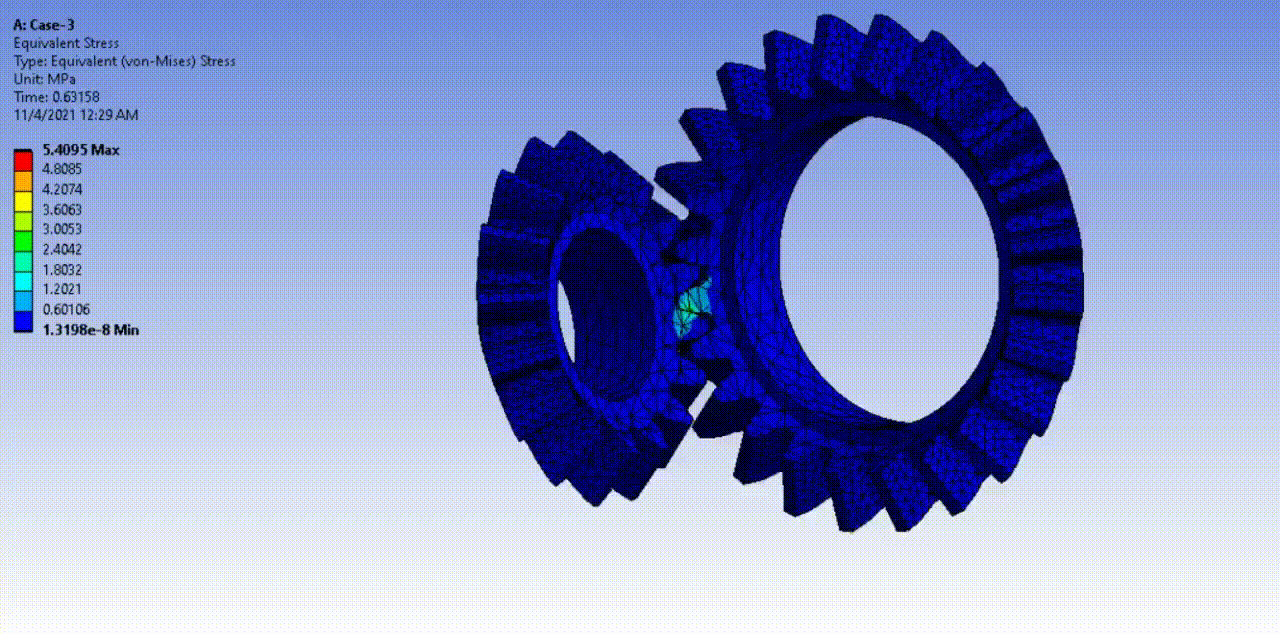
Figure 42-Equivalent Von Misses Stress Simulation Animation Case 3 [4 mm Mesh Size]. |
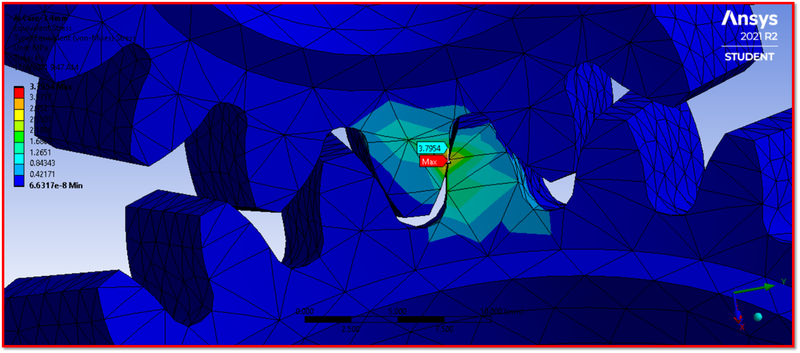
Figure 43-Maximum Stress at the Tooth Contact [Case-3]. |
Equivalent Elastic Strain [Case 1] :
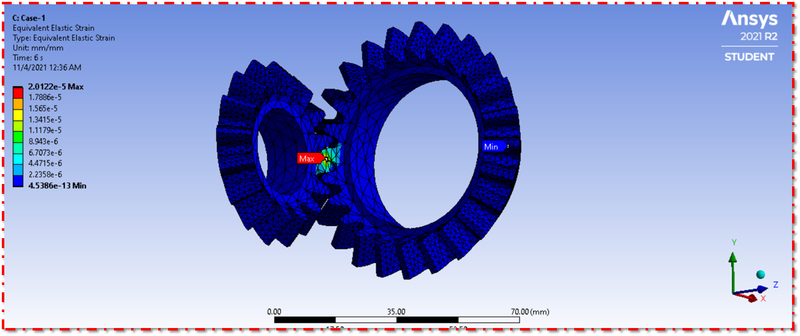
Figure 44-Equivalent Elastic Strain Case 1 [6 mm Mesh Size]. |
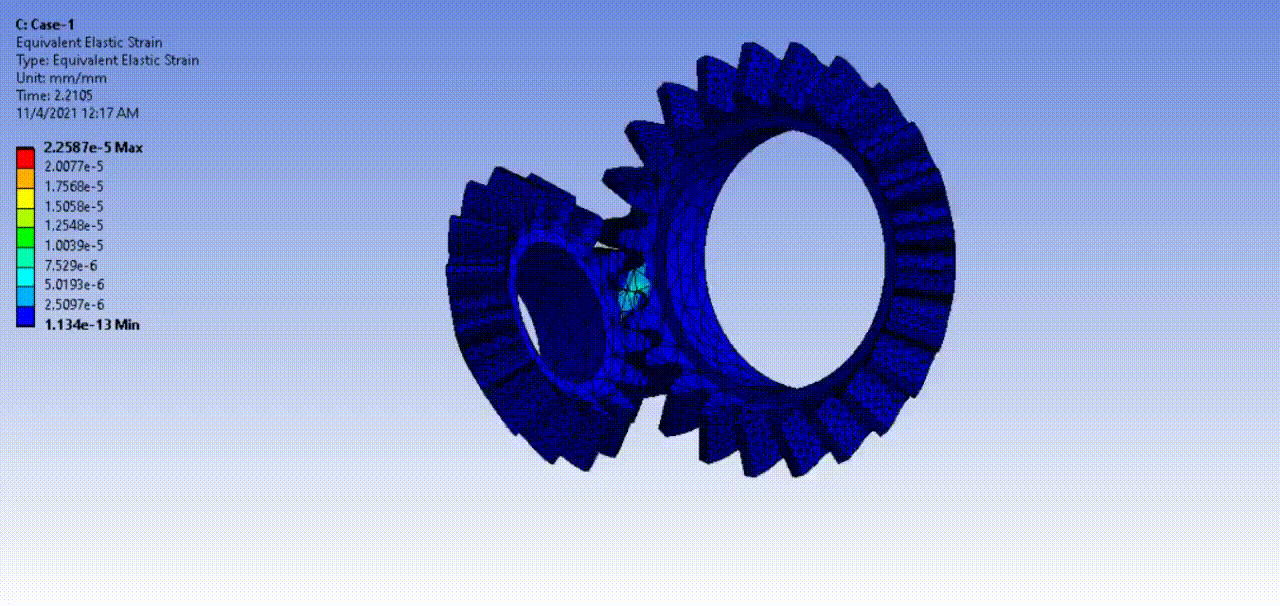
Figure 45-Equivalent Elastic Strain Simulation Animation Case 1 [6 mm Mesh Size]. |
Equivalent Elastic Strain [Case 2] :

Figure 46-Equivalent Elastic Strain Case 2 [5 mm Mesh Size]. |
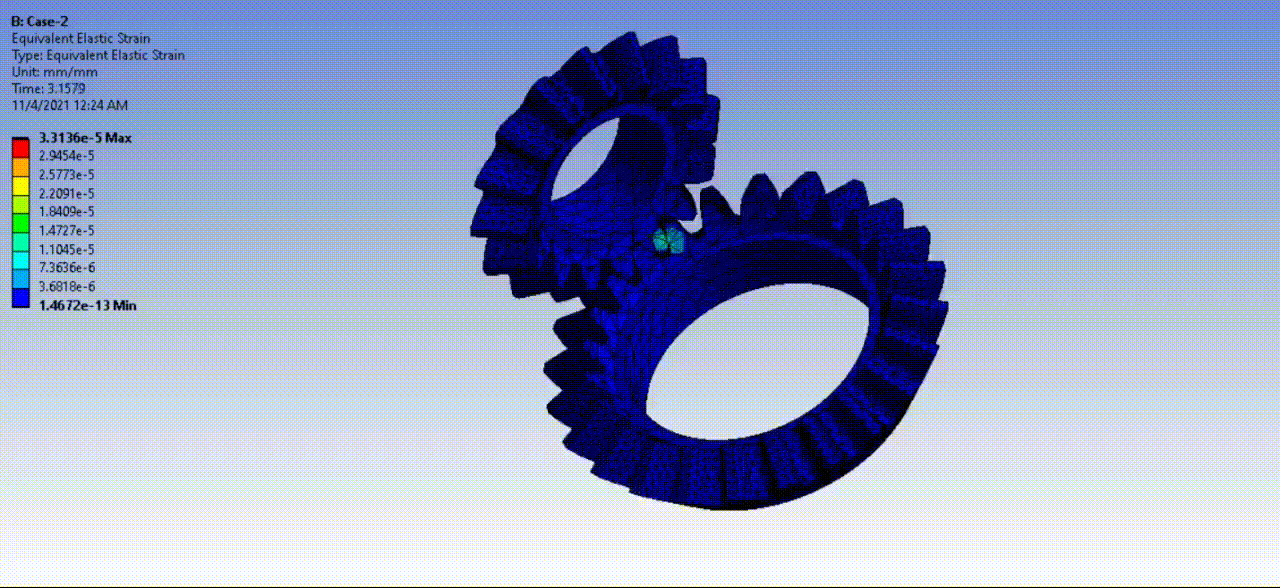
Figure 47-Equivalent Elastic Strain Simulation Animation Case 2 [5 mm Mesh Size]. |
Equivalent Elastic Strain [Case 3] :
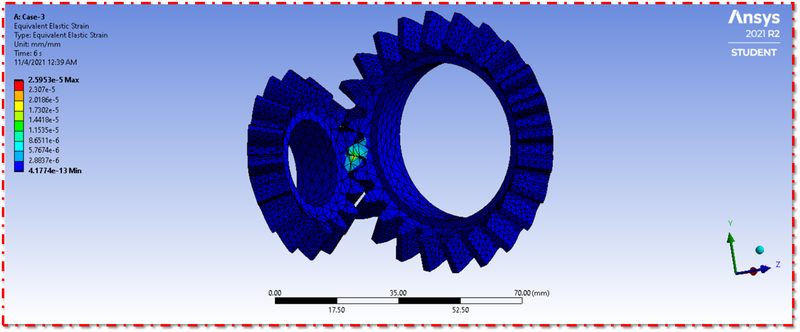
Figure 48-Equivalent Elastic Strain Case 3 [4 mm Mesh Size]. |
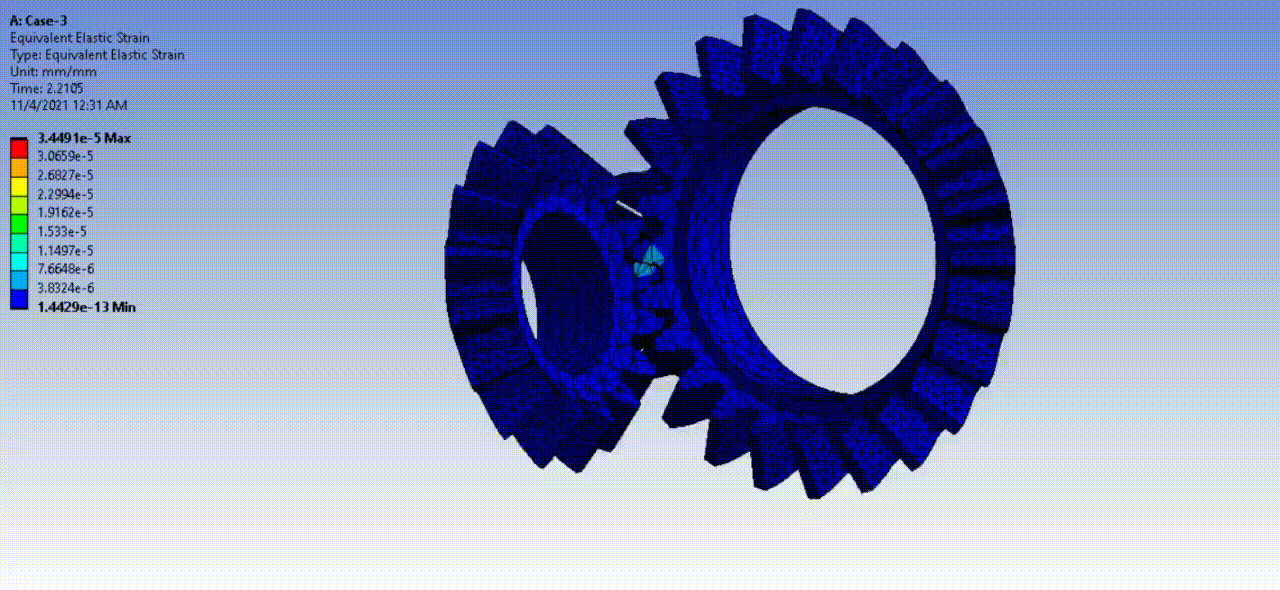
Figure 49-Equivalent Elastic Strain Simulation Animation Case 3 [4 mm Mesh Size]. |
Total Deformation [Case 1] :
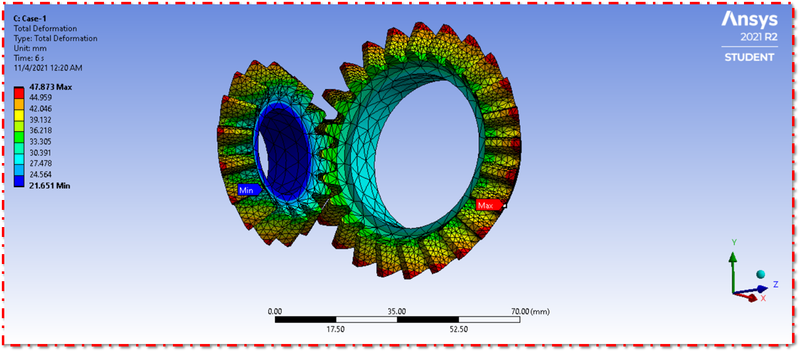
Figure 51-Total Deformation Case 1 [6 mm Mesh Size]. |
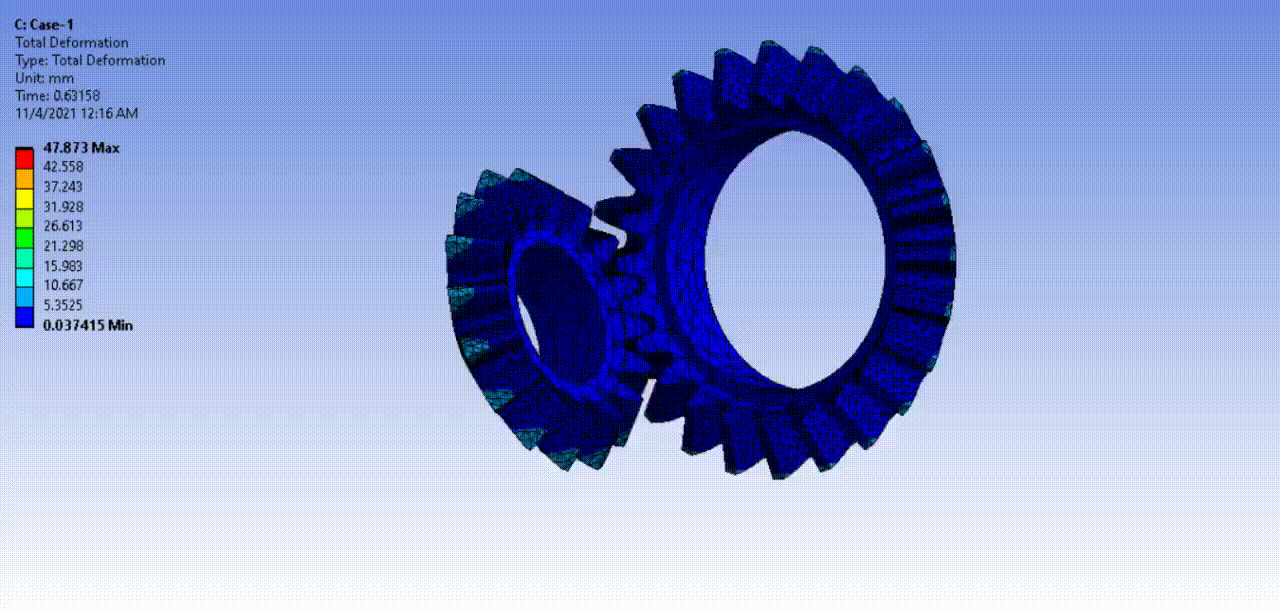
Figure 52-Total Deformation Simulation Animation Case 1 [6 mm Mesh Size]. |
Total Deformation [Case 2] :
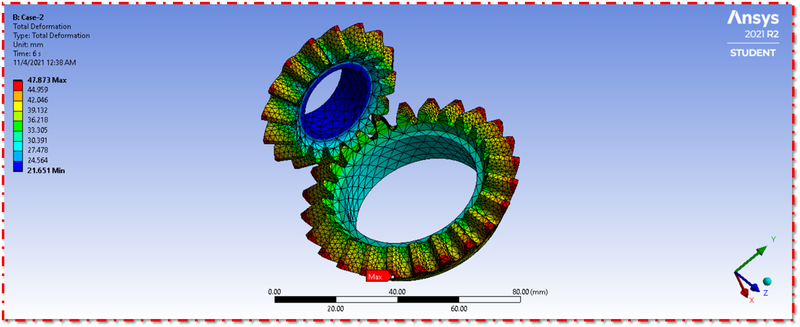
Figure 53-Total Deformation Case 2 [5 mm Mesh Size]. |
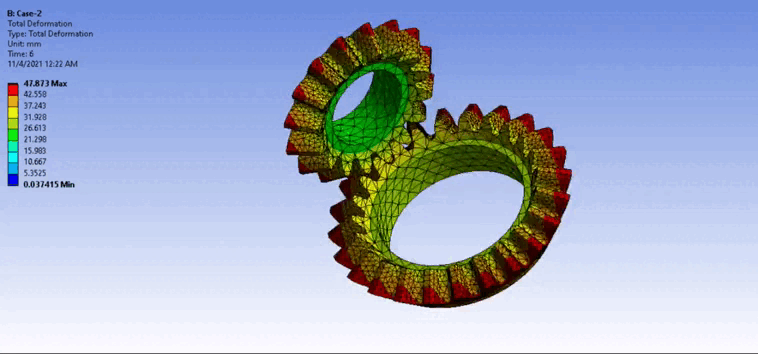
Figure 54-Total Deformation Simulation Animation Case 2 [5 mm Mesh Size]. |
Total Deformation [Case 3] :
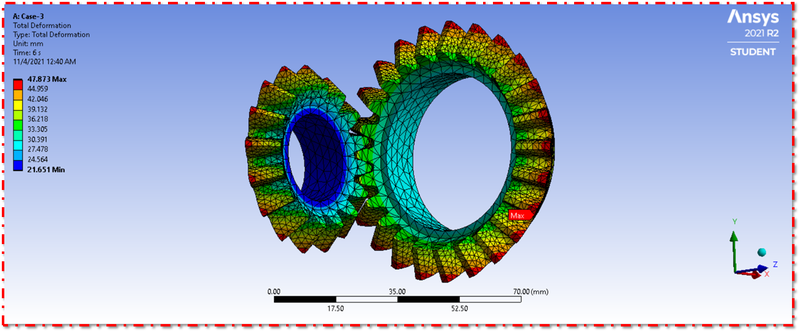
Figure 55-Total Deformation Case 3 [4 mm Mesh Size]. |
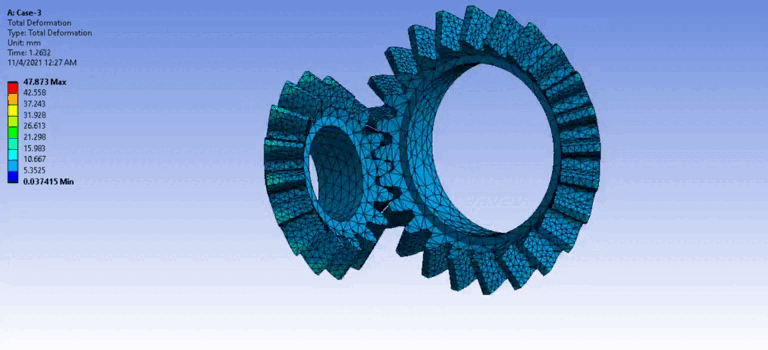
Figure 56-Total Deformation Simulation Animation Case 3 [4 mm Mesh Size]. |
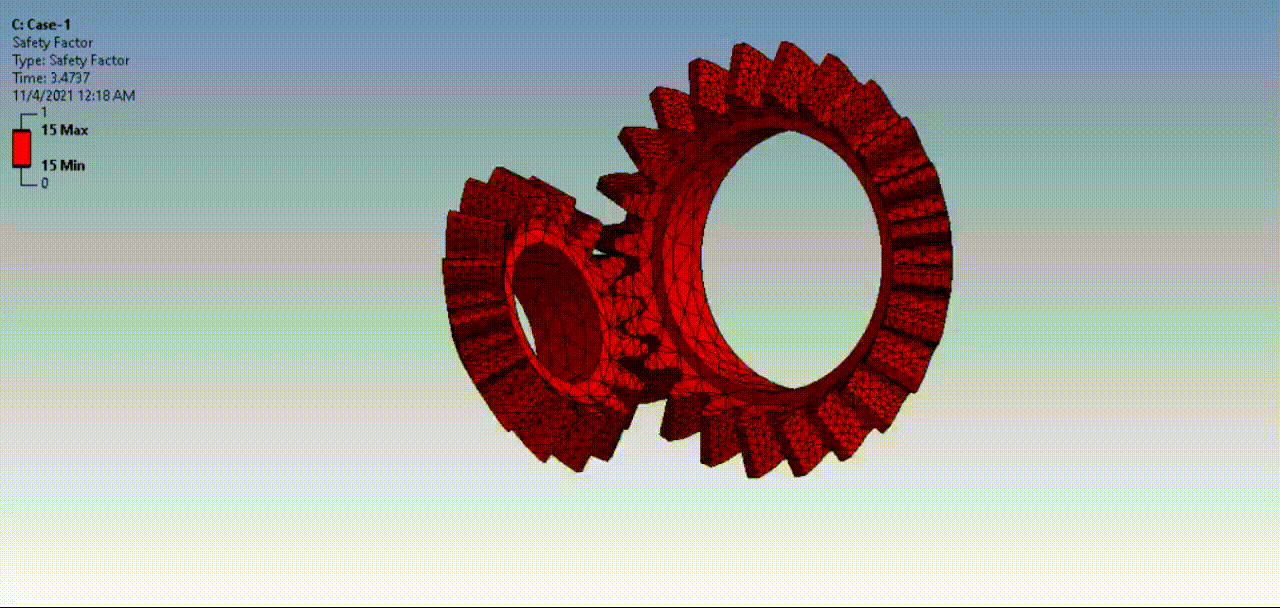
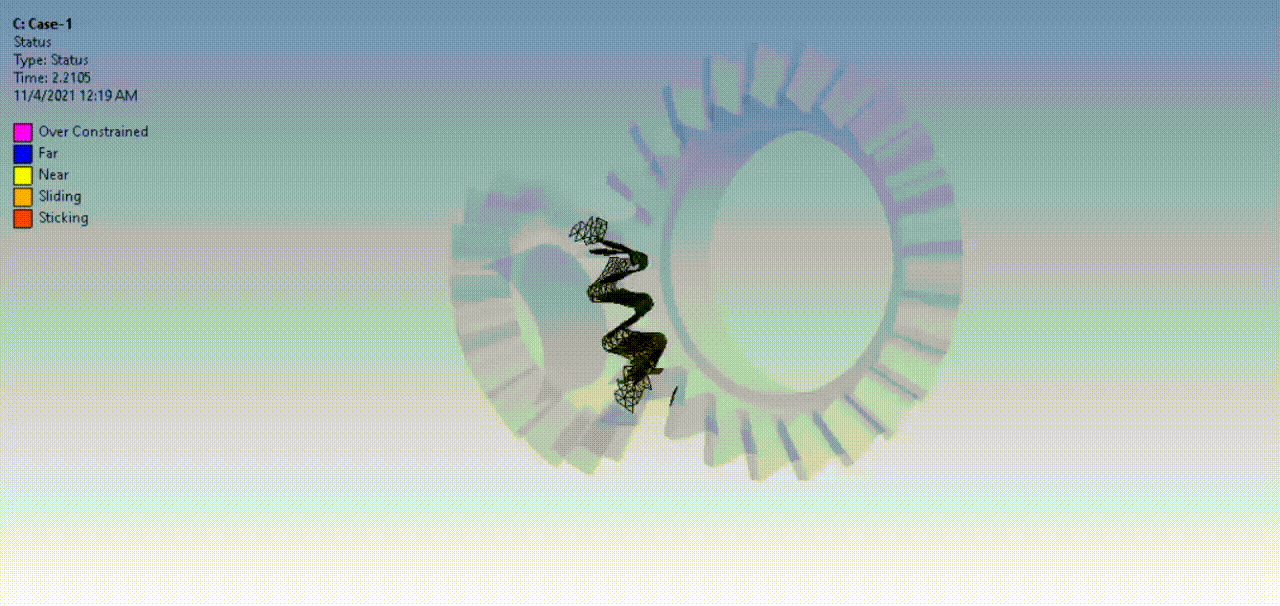
Figure 58-Contact Animation. |
Force Convergence Graph [Case-1] :
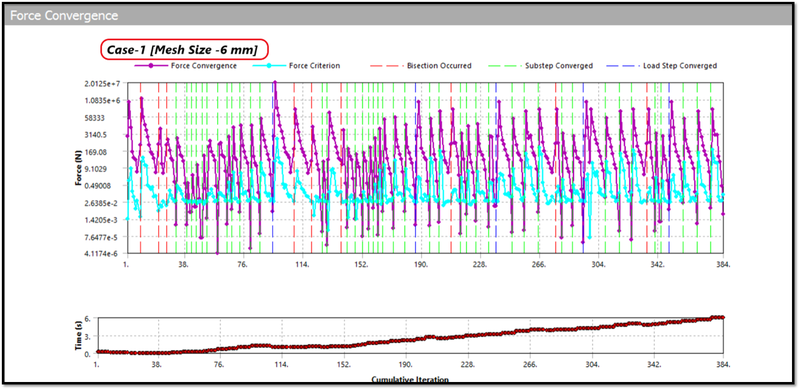
Figure 59-Force Convergence Graph [Case-1]. |
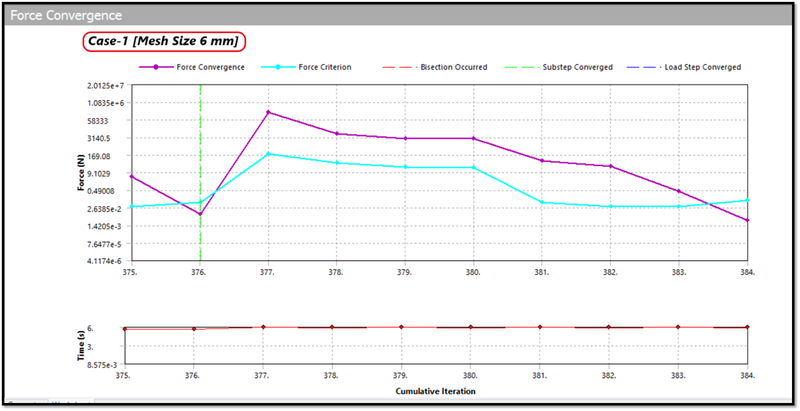
Figure 59:1-Force Convergence Graph [Case-1]. |
Force Convergence Graph [Case-2] :
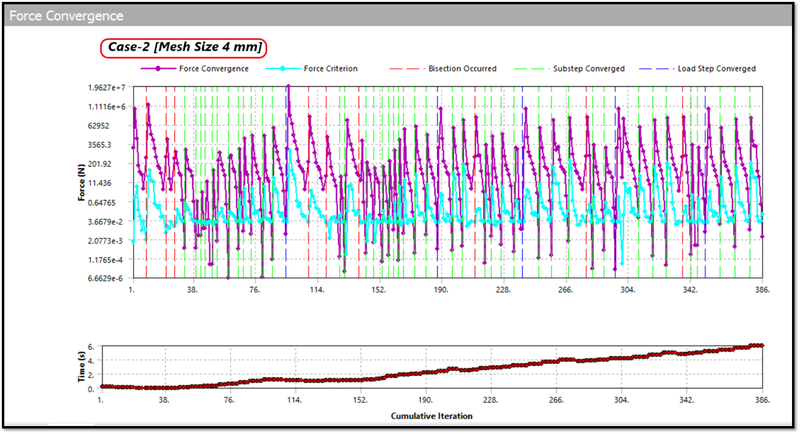
Figure 60-Force Convergence Graph [Case-2]. |
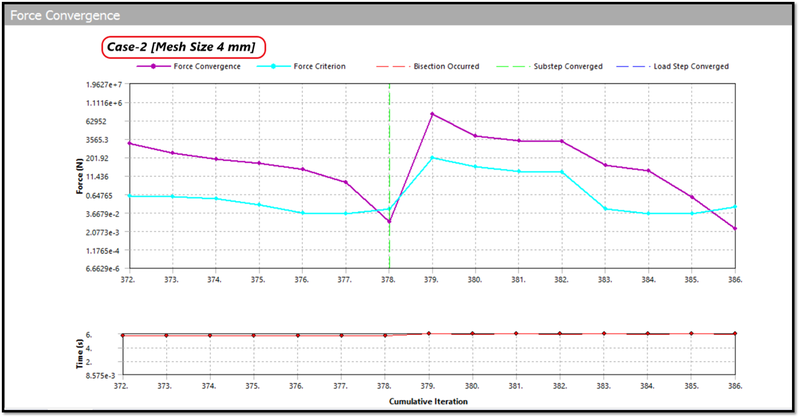
Figure 60:1-Force Convergence Graph [Case-2]. |
Force Convergence Graph [Case-2] :
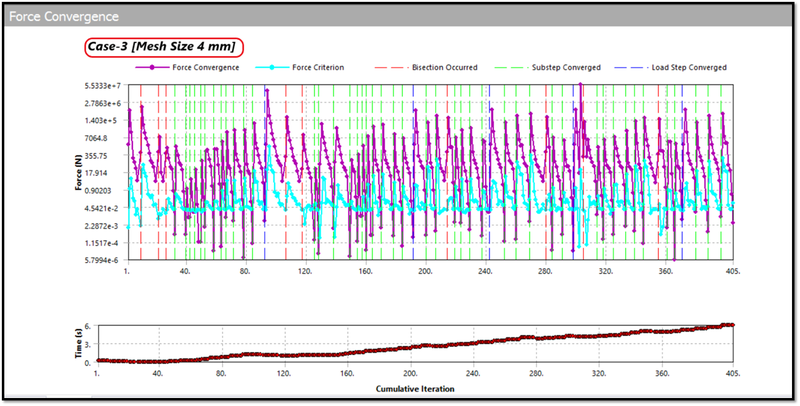
Figure 61-Force Convergence Graph [Case-3]. |
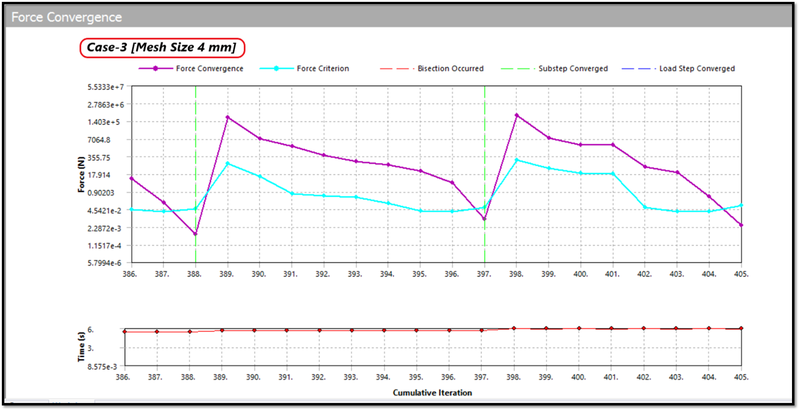
Figure 61:1-Force Convergence Graph [Case-3]. |
Comparison of Results :
Cases
|
Von-Misses Stress (MPa)
|
Total Deformation (mm)
|
Equivalent Elastic Strain (MPa)
|
Max.
|
Min.
|
Max.
|
Min.
|
Max.
|
Min.
|
Case-1
|
3.6015 MPa
|
5.5135e-8 MPa
|
47.873 mm
|
21.651 mm
|
2.0122e-5 Mpa
|
4.5386e-13 Mpa
|
Case-2
|
4.0264 MPa
|
5.6534e-8 MPa
|
47.873 mm
|
21.651 mm
|
2.7596e-5 Mpa
|
3.6167e-13 Mpa
|
Case-3
|
3.7954 Mpa
|
6.6317e-8 Mpa
|
47.873 mm
|
21.651 mm
|
2.5953e-5 Mpa
|
4.1774e-13 Mpa
|
- Here we have performed mesh with different element size for every cases.
- The maximum value of Von-Misses Stress is developed in Case-2,The minimum value of Von-Misses Stress is developed in Case-1.
- The maximum and minimum deformation is same for all the three cases.
- Here the mesh size we used for the Case-3 is 6 mm,But here we are not getting accurate results when compared to the Case-2.The maximum stress developed in the Case-3 is 3.7954 Mpa,It is low when compared to the Case-2.
- The maximum stress developed in the Case-2 with 5 mm Mesh Size is 4.0264 Mpa.It is high when compared to the other two cases,So we can conclude that Case-2 with 5 mm Mesh Size is preferred,Cause here the results which we are getting is accurate,We Meshed with 6 and 4 mm Mesh Size,In that two cases,the results what we are getting is not accurate.
- The Recommended Element Size with 5 mm is Preferred,Cause the results what we get will be accurate,So I'm conclusing that Element Size with 5 mm is preferred for the Bevel Gear.
[Note: We can't say this case is preferable, this case is not preferable, Anyhow it depends on the application. Here in the report, I have said, Case-2 with Mesh Size 5 mm is preferable due to accurate results and Case-1 and Case-3 is not preferable due to the results what we are getting is not accurate in both these two cases,Here,I have told the Case-2 is preferrable and other two cases is not preferrable according to the question and the model given to us, But in real life, It entirely depends on the applications.]
Factor of Saftey :
Case-1 [Mesh Size=6 mm] :
- The factor of Saftey = Yield Strength/Working Stress
- Tesnsile Yield Strength of Structural Steel=250 Mpa
- Working Stress [Maximum Stress]=3.6015 Mpa
- FOS=2503.6015
- FOS=69.41
- Here the FOS what we got is 69.41,It is entirley ok,The material will not fail,It is Safe.If we mesh the bevel gear with 6 mm mesh size,The material will not fail.The Standard FOS ranges from 1-5 in industries.
Case-2 [Mesh Size=5 mm] :
- The factor of Saftey = Yield Strength/Working Stress
- Tesnsile Yield Strength of Structural Steel=250 Mpa
- Working Stress [Maximum Stress]=4.0624 Mpa
- FOS=2504.0624
- FOS=61.53
- Here the FOS what we got is 61.53,It is entirley ok,The material will not fail,It is Safe.If we mesh the bevel gear with 5 mm mesh size,The material will also not fail.The Standard FOS ranges from 1-5 in industries.
Case-3 [Mesh Size=4 mm] :
- The factor of Saftey = Yield Strength/Working Stress
- Tesnsile Yield Strength of Structural Steel=250 Mpa
- Working Stress [Maximum Stress]=3.7954 Mpa
- FOS=2503.7954
- FOS=65.86
- Here the FOS what we got is 65.86,It is entirley ok,The material will not fail,It is Safe.If we mesh the bevel gear with 4 mm mesh size,The material will also not fail.The Standard FOS ranges from 1-5 in industries.
Result :
- Hence the material Structural Steel has been defined for all the three cases.
- Hence the model has been meshed with the different element size 4 ,5 and 6 mm.
- Hence the model has been solved for Von-Misses Stress, Equivalent Elastic Strain,Stress Intensity,Contact Tool and Total Deformation by applying appropriate boundary conditions.
- Hence the maximum value of Von-Misses Stress is developed in Case-2 [Mesh Size 5 mm].
- Hence the maximum deformation has occurred in all the three cases.It is similar.
Conclusion and Learning Outcome :
In this Week 2 Bevel Gear Challenge, I came to know about
- Learned about Grid Dependency Test.
- Learned why we are doing grid dependency test for the models.
- Learned how to assign materials to the model.
- Learned how to apply boundary conditions to the model.
- Learned how to request outputs and solve them.
- Learned about the Force Convergence.