Modeling and Rendering of the Yacht
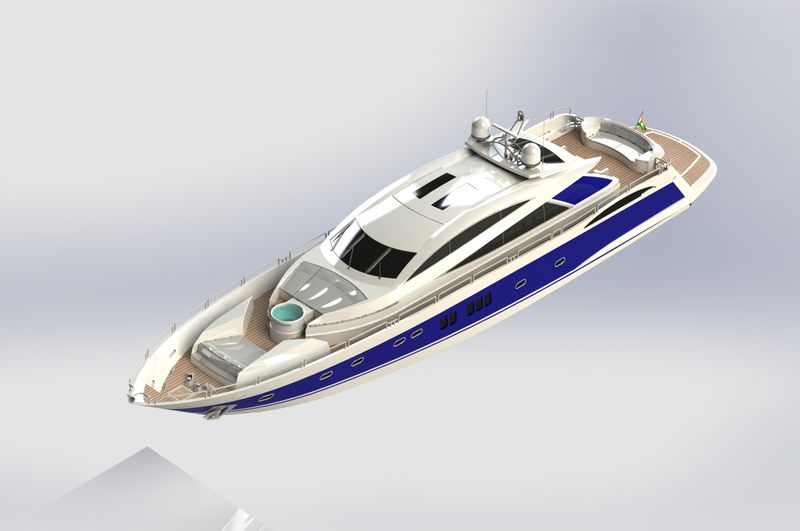
Objective
The objective of this project is to design and model the various parts of the Yacht using SolidWorks. Finally, rendering the assembly of the Yacht in SolidWorks PhotoView 360 and SolidWorks Visualise.
Introduction
This report contains all the details about the modeling of the yacht. The parts of the yacht are modeled according to the blueprint by using surface and solid modeling tools.
The parts to be modeled include:
- Propellers
- Radar
- Hull
- Garage door
- Front seat
- Middle seat
- Rear seat
- Superstructure
- Radar mast
SolidWorks is used throughout the entire process, which is a solid modeling Computer-Aided Design (3D CAD) software.
Design Methodology
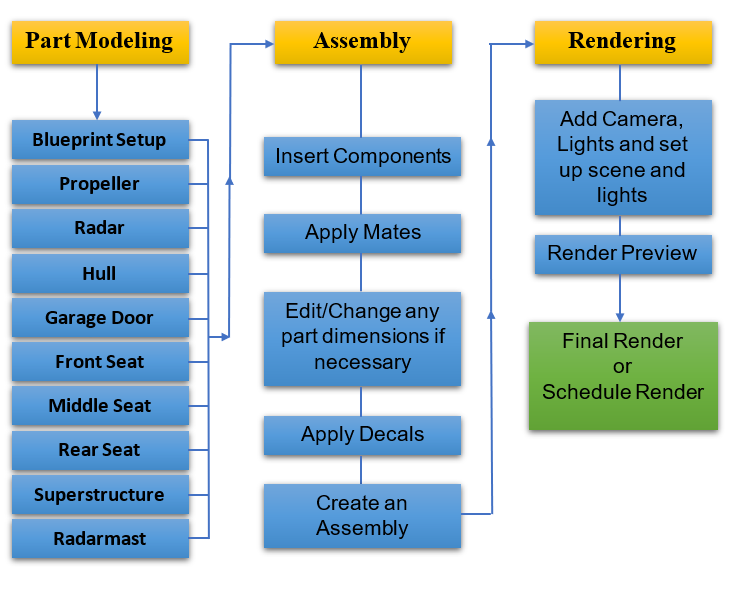
Description of the features/tools used
- Sketch (2D sketch)
- A 2D sketch is a basis for a 3D model. It represents the shape of the object when viewed from various standard directions, such as front, top, side, and so on.
- We can create drawing geometry using the 2D sketch, on an existing plane, surface of a model, or assembly by applying relations with the existing plane, sketch, model, or assembly.
- The 2D Sketch tool used in modeling the yacht include: Line, Circle, Spline, Rectangles such as Corner Rectangle/ Center Rectangle/ 3 Point Corner Rectangle, Arcs such as 3 Point Arc/ Centerpoint Arc, Ellipse, Text, Straight Slot, Polygon, Point, Sketch fillet, Trim Entity/Extend Entity, Convert Entity, Offset Entity, Mirror Entity, Linear Pattern, and Copy/Move Entities.
- This sketched geometry can be controlled by relations (collinear, perpendicular, parallel, tangent, concentric, pierce, vertical, horizontal, fix, and so on), as well as parametric dimensions.
- 3D SKETCH
- In a 3D sketch, new geometry can be created in three dimensions by referencing bodies, planes, surfaces, or vertices which already exist. A 3D sketch can be created free hand, with/without any reference. This can be as simple as converting edges or clicking on vertices for starting and ending points of the geometry. We can also apply relations (along x/y/z, fix, collinear, perpendicular, parallel, tangent, concentric, and so on) as well as parametric dimensions.
- Fillets
- Fillet/Round creates a rounded internal or external face on the part. We can fillet all edges of a face, selected sets of faces, selected edges, or edge loops.
- Chamfer
- The chamfer tool creates a beveled feature on selected edges, faces, or a vertex.
- Curves
The Split Line tool projects an entity (sketch, solid, surface, face, plane, or surface spline) to surfaces or curved or planar faces. It divides a selected face into multiple separate faces. We can split curves on multiple bodies with one command.
We can project a sketched curve onto a model face to create a 3D curve. We can also create a 3D curve that represents the intersection of two extruded surfaces generated by creating sketches on two intersecting planes.
We can create a helix or spiral curve using this tool.
- Reference Geometry
- Reference geometry defines the shape or form of a surface or a solid. Reference geometry includes items such as planes, axes, coordinate systems, and points. We can use reference geometry in the creation of several kinds of features such as planes, axes, coordinate systems, and points, which are used to create a required geometry, surface, or solid body.
- Surface Bodies
- Surfaces are a type of geometry that can be used to create a solid body. The surface body is a general term that describes connected zero-thickness geometries such as single surfaces, knit surfaces, trimmed and filleted surfaces, and so on. We can have multiple surface bodies in a single part.
- Surface features used in modeling the yacht include:
This is used to extrude a sketch or sketch contours in one or two direction to create a surface feature. You can control where the extrude starts from, and define its direction and extent.
This is used to revolve a sketch or sketch contours around an axis to create surface feature. We can define the axis or revolution and the direction and extent of the revolved surface.
This is used to sweep a closed profile along an open or closed path to create a surface feature.
This is used to create a lofted surface between two or more profile or sketch. We can specify the start and end constraints and add guide curves to control the path shape.
This is used to patch a surface within a boundary defined by edges, sketches, or curves. We use constraint curves to fill surfaces and adjust resolution control to improve surface finish.
This is used to create an offset surface using one or more contiguous faces. This tool creates an offset surface with gap. We can repair the gaps manually or adjust the offset distance value and run the tool again. This tool is also used to create a surface copy.
This is used to insert a ruled surface in a specified direction from edges. We can trim and knit the surface and remove connecting surfaces.
This is used to delete a face or multiple faces from solid body or surface bodies. We can also delete and patch faces to form continuous surface, or delete and fill to replace with single face.
This is used to extend one or more edges or faces on a surface, based on end conditions and extension type.
This is used to trim where a surface intersects with another surface, a plane, or sketch. We can select a trim type, trim tool, and surface to keep or remove.
This is used to combine two or more adjacent nonintersecting surfaces into a single surface body. The surfaces must join at an edge. If the resulting knit surface encloses a volume, we can create a solid body.
This is used to create a solid feature by thickening one or more adjacent faces.
- Solid Bodies
Features used in modeling the yacht include:
This is used to extrude a sketch or selected sketch contours in one or two directions to create a solid feature. We can control where the extrude starts from, its direction and extent.
This is used to revolve a sketch or selected sketch contours around an axis to create a solid feature. We can define the axis of revolution, and define the direction and extent of revolution.
This is used to sweep a closed profile along an open or closed path to create a solid feature. We can use options such as guide curve, profile orientation options, and twist to create a wide variety of shapes.
This is used to add material between two or more profiles to create a solid feature.
This is used to cut a solid model by extruding a sketched profile in one or two directions. If the cut affect multiple bodies in multibody parts, then we can select which bodies to keep in the Bodies to Keep dialog box.
This is used to hollow out a part, leaving open the faces we select, and creating thin walled features on the remaining faces. If we do not select a face, shell creates a closed hollow model.
This is used to create a dome that is tangent to the adjacent cylindrical or conical face. We can also apply domes to faces whose centroid lies outside the face. This allows us to apply domes to irregularly shaped contours or noncylindrical or nonconical face.
This is used to mirror features, faces, surfaces and bodies about a plane or a planar face. In assemblies, we can mirror assembly feature.
This is used to pattern features, faces, and bodies in one or two linear directions. We can select reference geometry to define the pattern. We can also skip instances.
Description of modeled parts
- Blueprint Setup
- A Blueprint is a design plan or a technical drawing or a mechanical drawing. It is a two-dimensional set of drawings that provides a detailed visual representation of a part, model or something which is to be done or made.
- We rename the Top Plane as Bottom Plane and Right Plane as Mid Plane.
- Now, we create 2 additional planes by using Reference Geometry >> Planes. Name the first plane as the Back Plane with a distance of 32920.00mm from the Front Plane. Name the second plane as the Top Plane with a distance of 10000.00mm from the Bottom Plane.
- Now, insert the blueprints by Tools >> Sketch Tools >> Sketch Picture. Here the blueprints are arranged with respect to the Front Plane, Back Plane, Top Plane, Bottom Plane, and Mid plane.
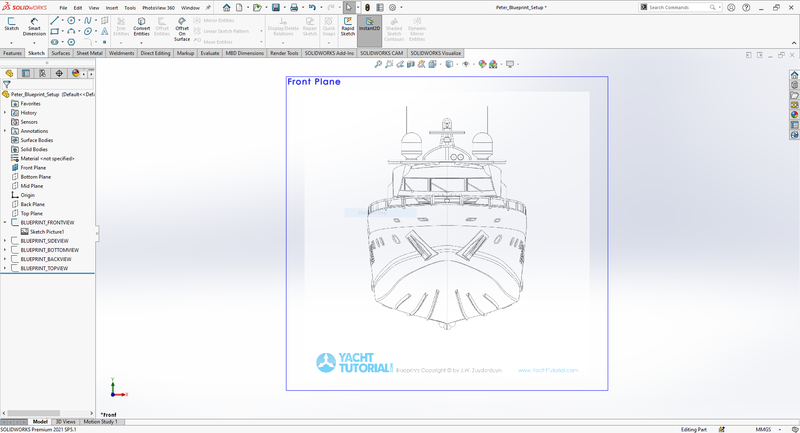

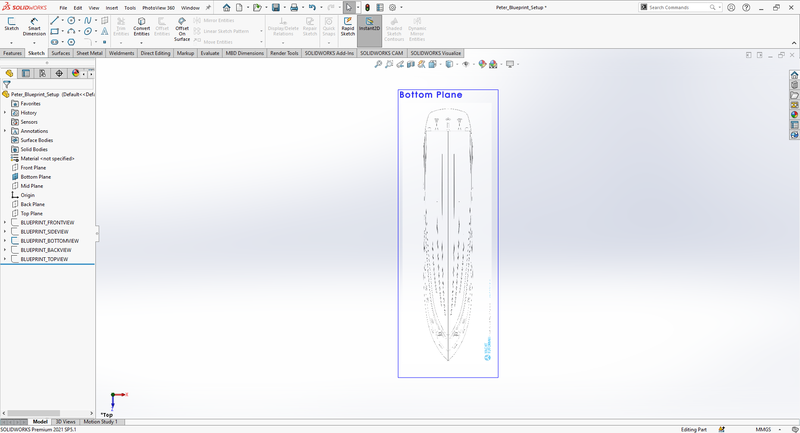
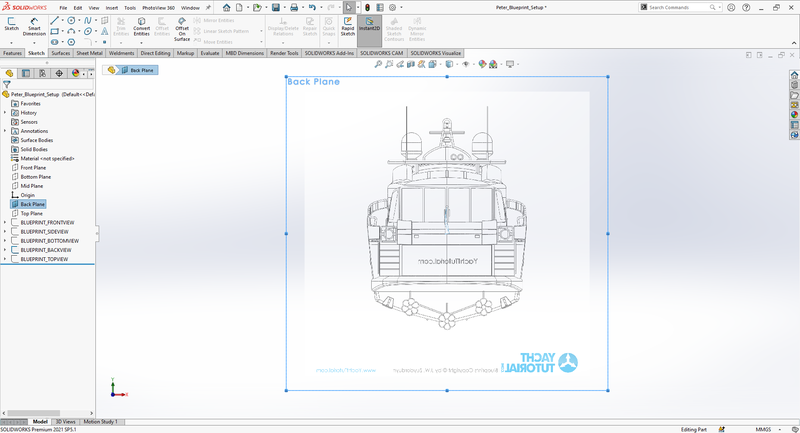
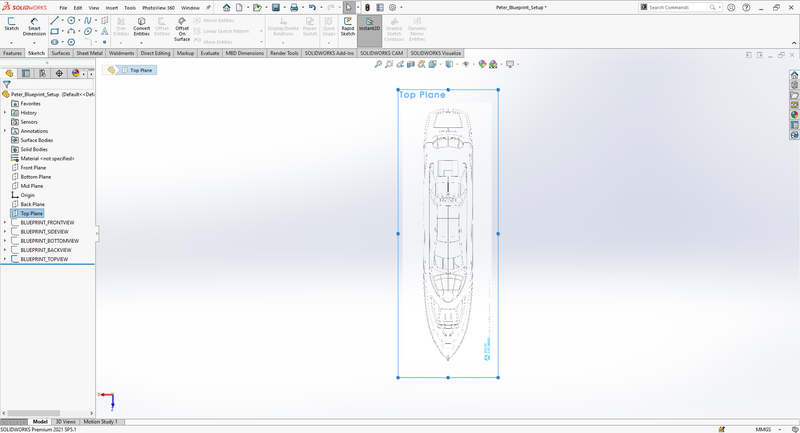
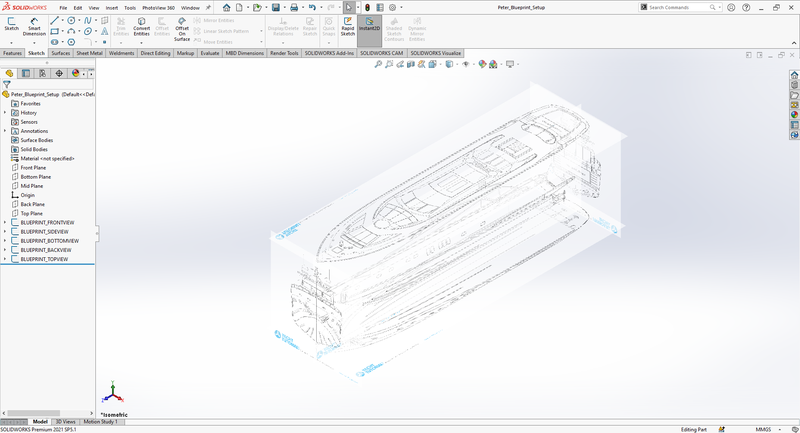
- Propeller
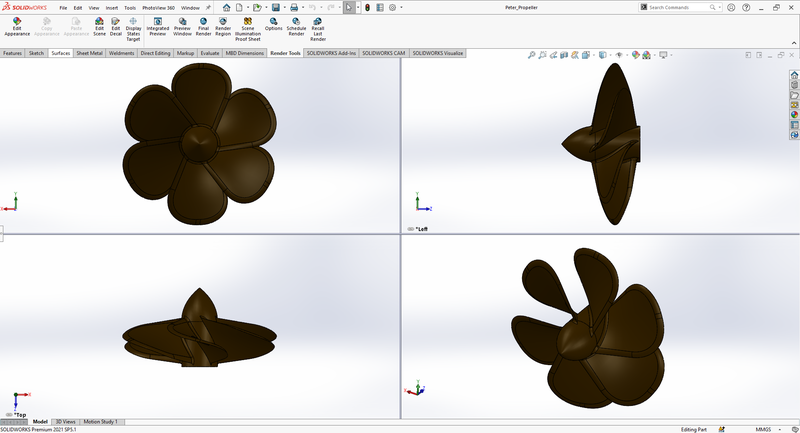
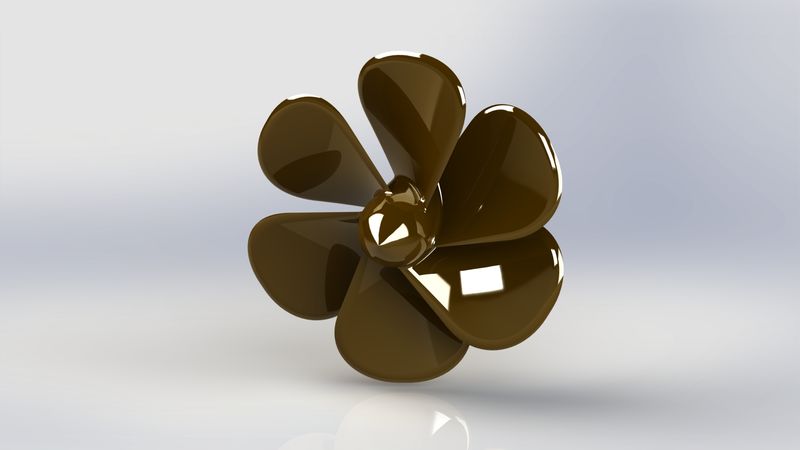
Tools/Features used
- Sketch: Line, Spline, 3 Point Corner Rectangle, and Circle.
- Revolved Boss/Base
- Lofted Boss/Base
- Extruded Cut
- Fillet
- Circular Pattern
- Appearance: Custom brown (71,45,0).
- Radar
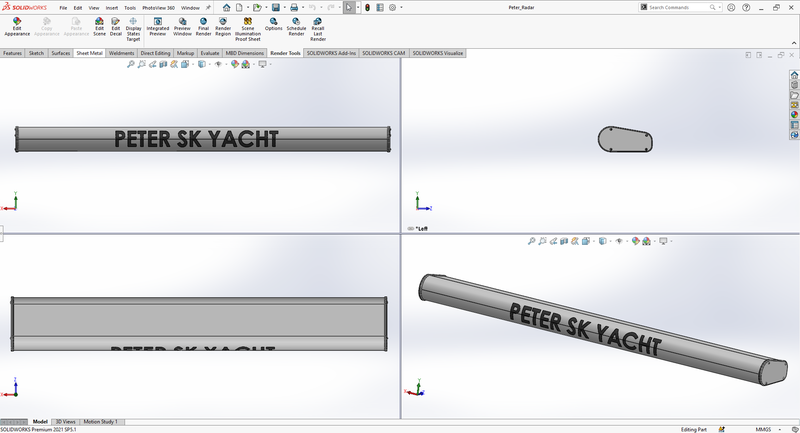
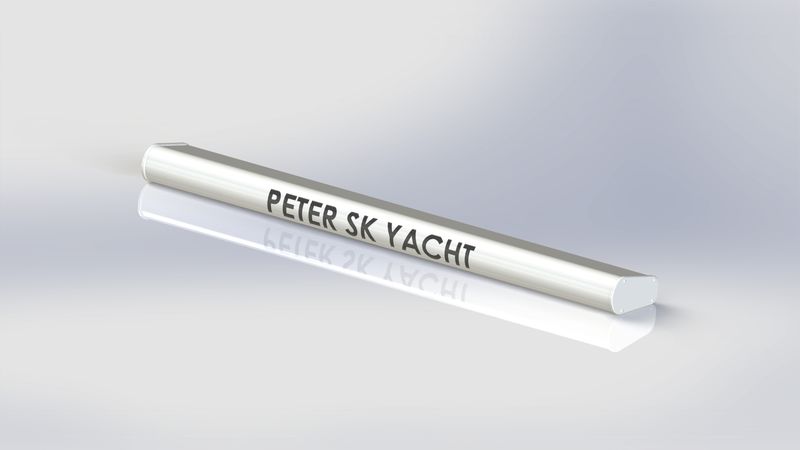
Tools/Features used
- Sketch: Line, Offset Entities, Circle, Polygon, Point, and Text.
- Extruded Boss/Base
- Extruded Cut
- Fillet
- Mirror
- Curves: Split Line
- Appearance: White (255,255,255) and custom dark grey (70,70,70).
- Hull
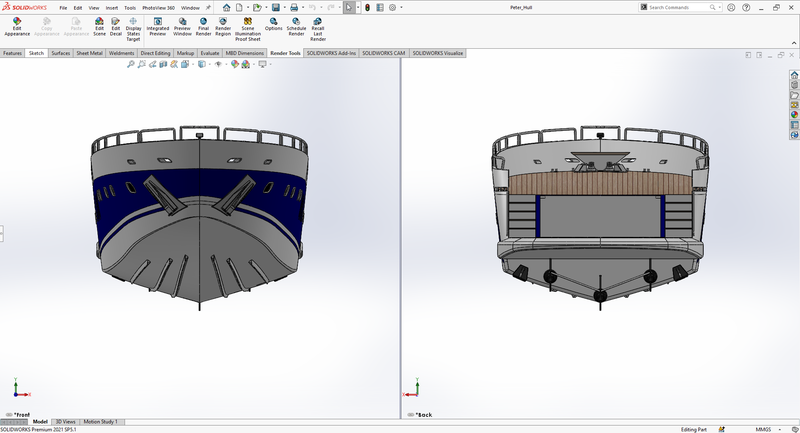
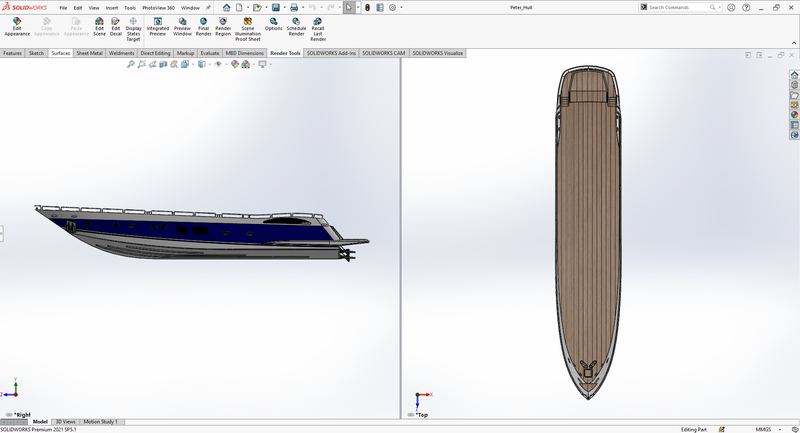
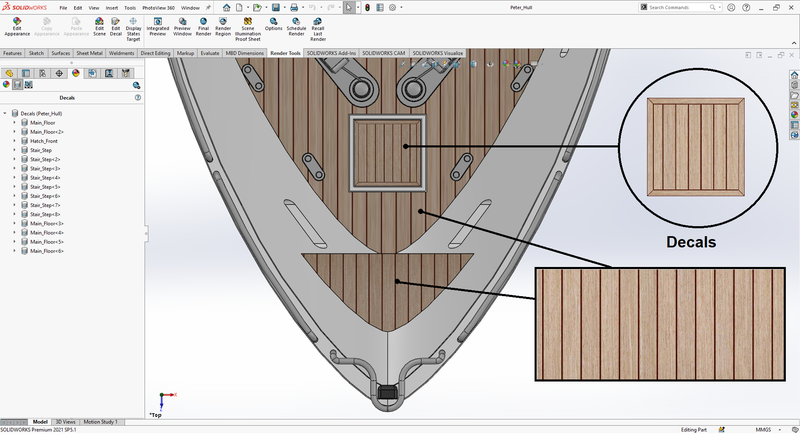
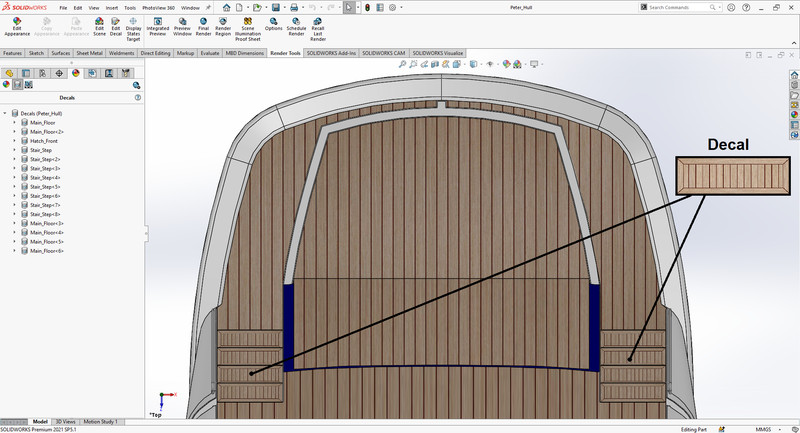
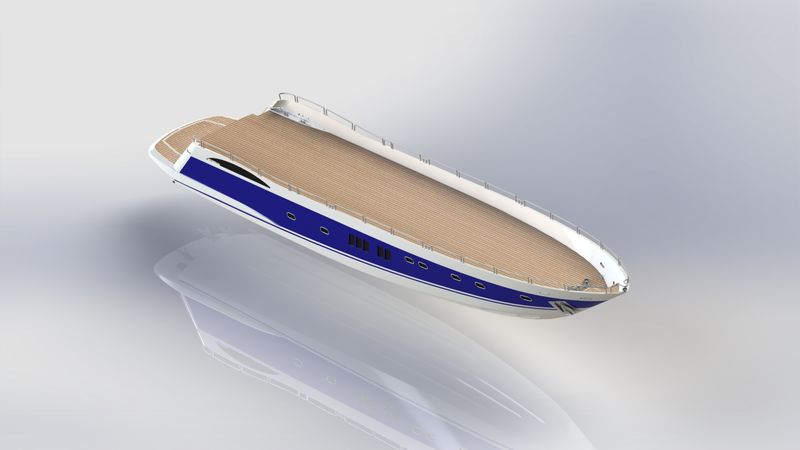
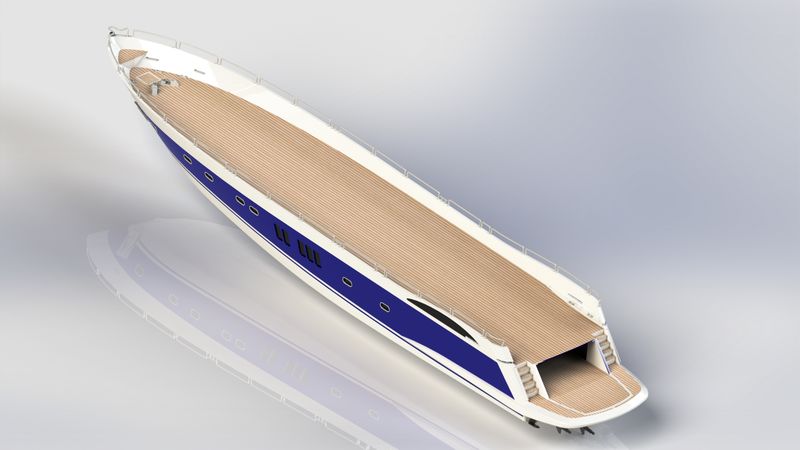
Tools/Features used
- Sketch: Line, Spline, Circle, Arcs, Straight Slot, Ellipse, Rectangles, Convert Entities, and Offset Entities.
- 3D Sketch
- Reference Geometry: Plane.
- Curves: Project Curve and Helix and Spiral.
- Lofted Surface
- Trim Surface
- Knit Surface
- Filled Surface
- Shell
- Extruded Boss/Base
- Extruded Cut
- Swept Boss/Base
- Revolved Boss/Base
- Fillet
- Chamfer
- Dome
- Linear Pattern
- Delete Face
- Mirror
- Curves: Split Line
- Copy Surface
- Appearance: White (255,255,255), black (0,0,0), custom dark blue (0,0,128), dark grey (64,64,64), light grey (192,192,192), grey (128,128,128)
- Decal: PhotoView 360 >> Edit Decal or DisplayManager >> View Decals >> Right click >> Add Decal. Apply decals on the hull floors, hatch, and stairs.
- Garage Door
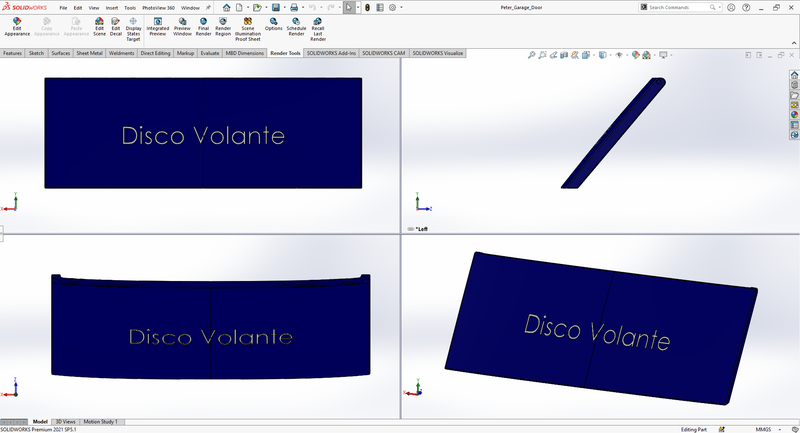
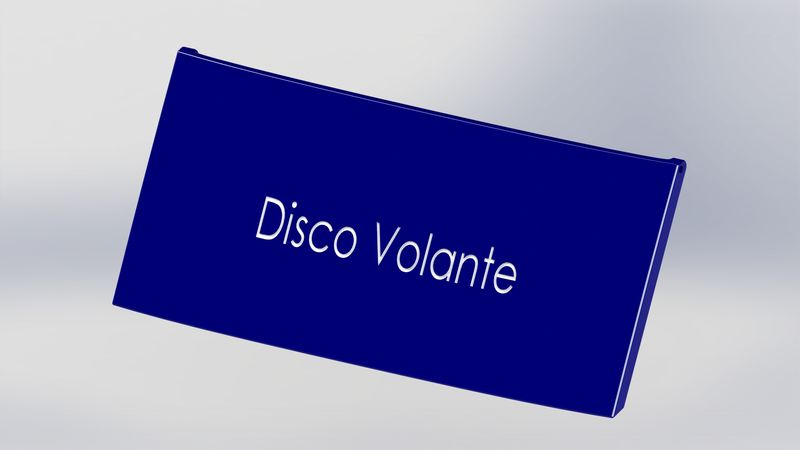
Tools/Features used
- Sketch: Line, Circle, and text.
- Extruded Cut
- Shell
- Fillet
- Mirror
- Reference Geometry: Plane.
- Appearance: Custom dark blue (0,0,128) and white (255,255,255).
- Front Seat
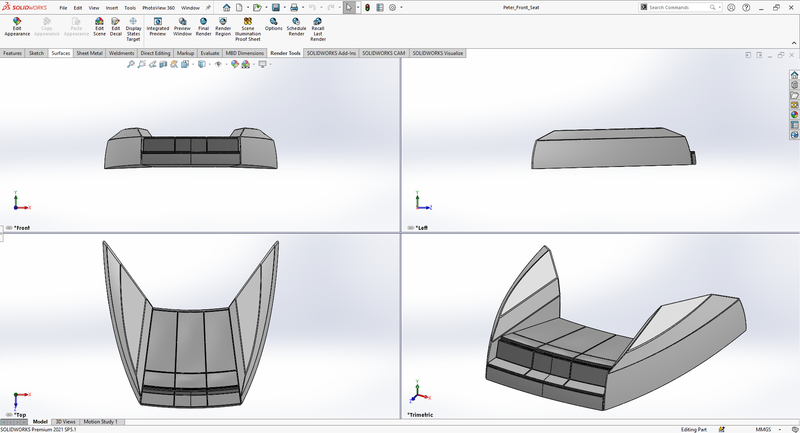
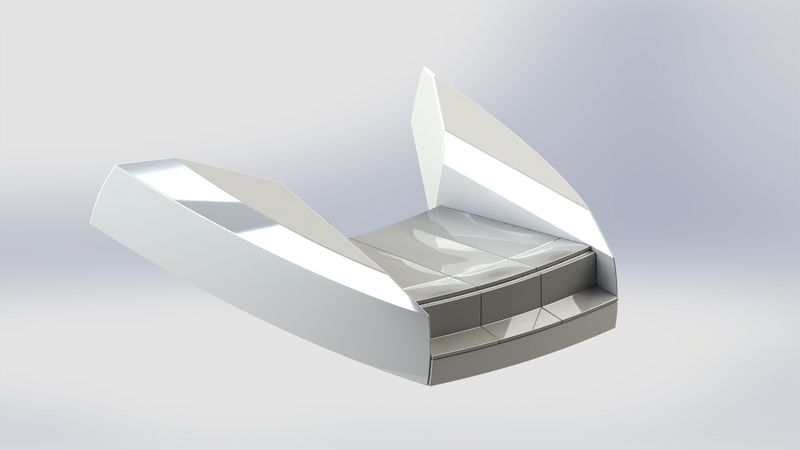
Tools/Features used
- Sketch: Line, Spline, Convert Entities and Offset Entities.
- Swept Surface
- Extend Surface
- Trim Surface
- Filled Surface
- Knit Surface
- Lofted Surface
- Revolved Boss/Base
- Extruded Cut
- Fillet
- Chamfer
- Mirror
- Dome
- Appearance: White (255,255,255) and light grey (192,192,192).
- Middle Seat
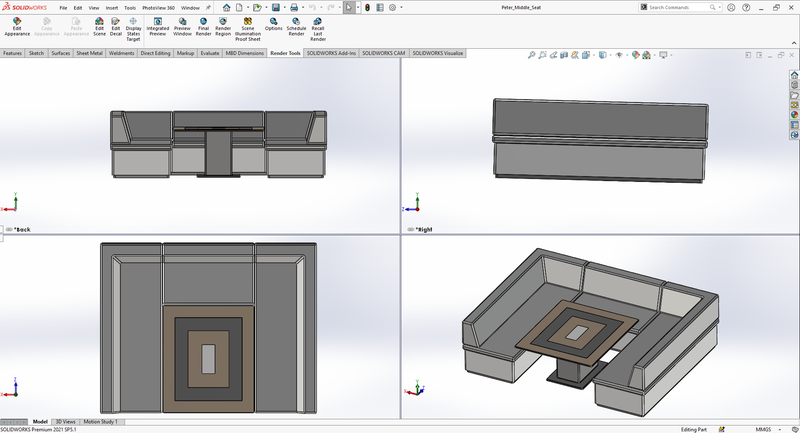
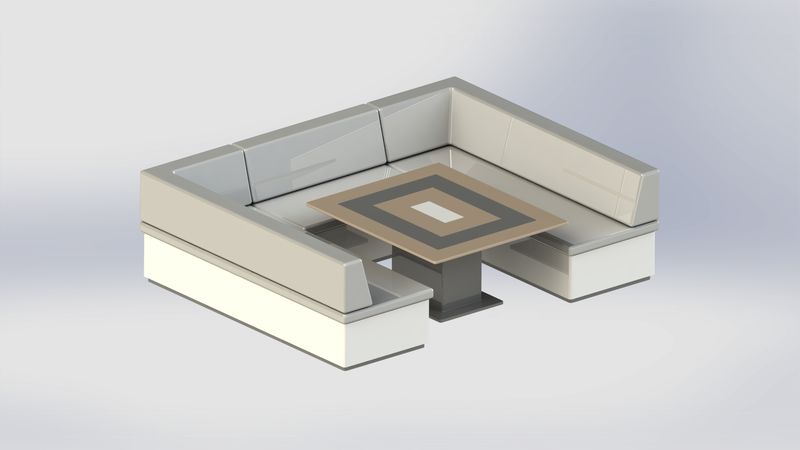
Tools/Features used
- Sketch: Line, Convert Entities, and Offset Entities.
- Extruded Boss/Base
- Extruded Cut
- Fillet
- Chamfer
- Mirror
- Reference Geometry: Plane.
- Mirror
- Appearance: White (255,255,255), light grey (192,192,192), custom grey (120,120,120), light brown (190,169,146).
- Rear Seat
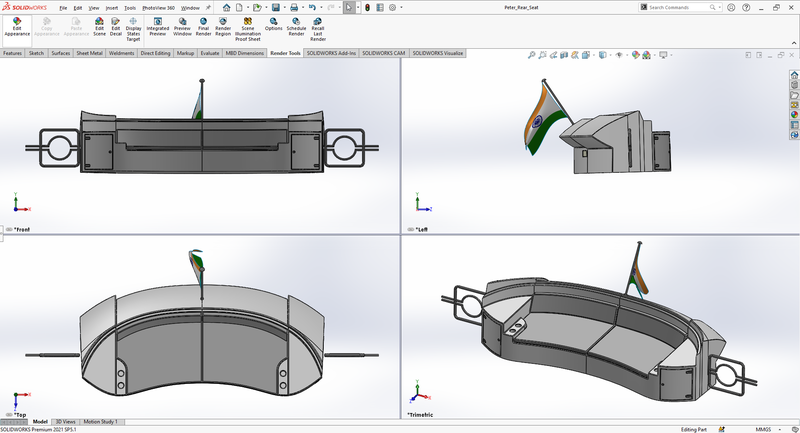
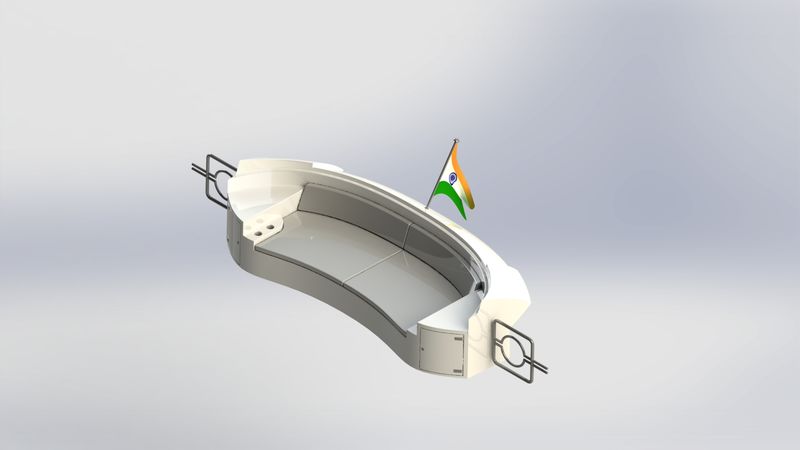
Tools/Features used
- Sketch: Line, Spline, Circle, Sketch Fillet, Convert Entities and Offset Entities.
- 3D Sketch
- Swept Surface
- Offset Surface
- Trim Surface
- Ruled Surface
- Knit Surface
- Reference Geometry: Plane.
- Extend Surface
- Extruded Surface
- Lofted Surface
- Extruded Boss/Base
- Extruded Cut
- Offset Surface
- Fillet
- Chamfer
- Swept Boss/Base
- Mirror
- Revolved Boss/Base
- Appearance: White (255,255,255), grey (128,128,128), red (192,0,0), light grey (192,192,192), light yellow (255,255,227).
- Decal: We can apply a decal of the Indian flag or any flag on the flag surface if we want to, PhotoView 360 >> Edit Decal or DisplayManager >> View Decals >> Right click >> Add Decal. Apply the decal of any flag on the flag surface.
- Superstructure
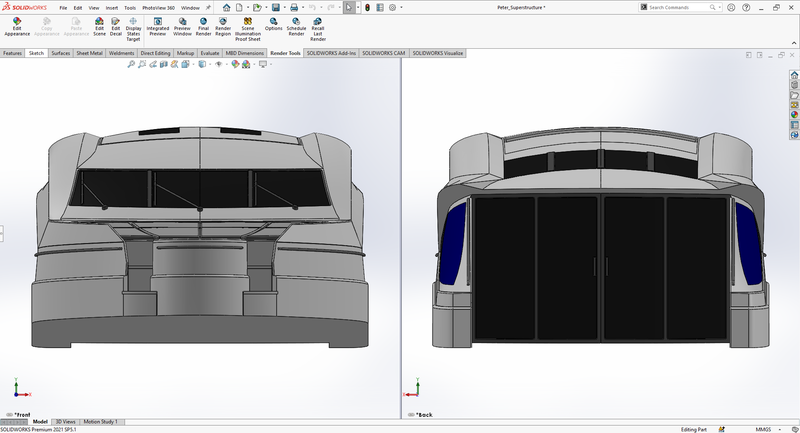
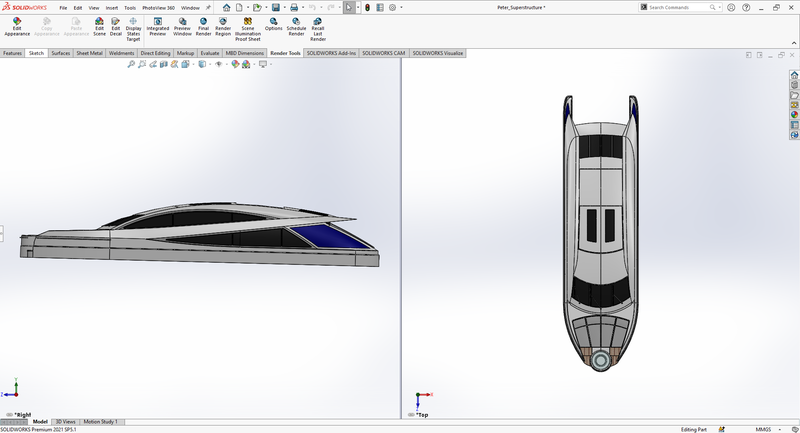
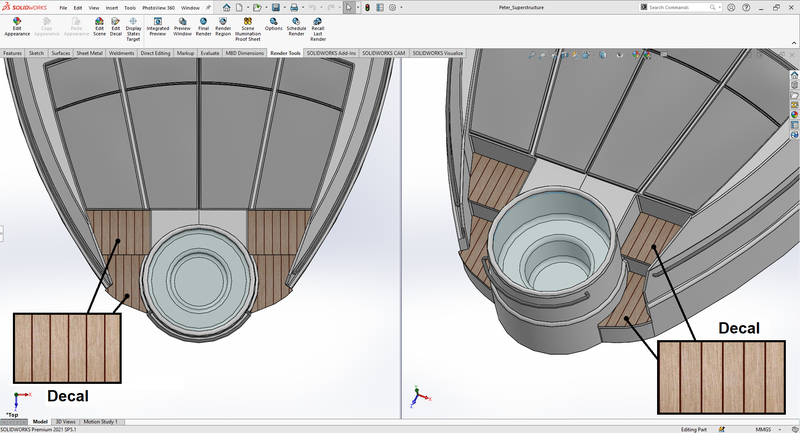
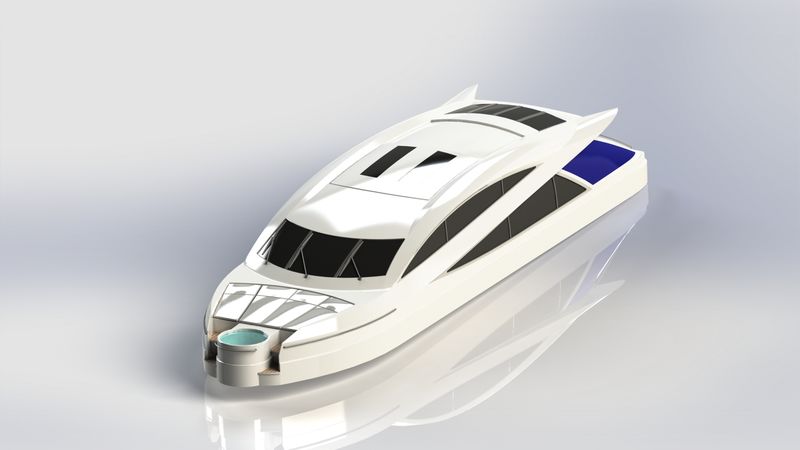
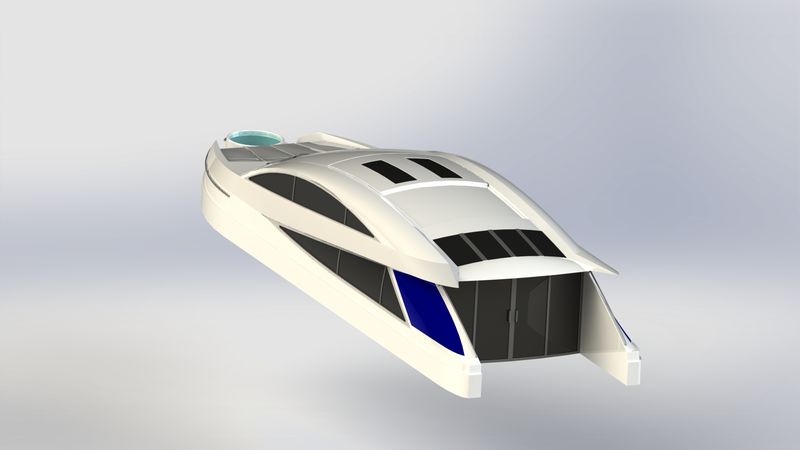
Tools/Features used
- Sketch: Line, Spline, Circle, Convert Entities and Offset Entities
- 3D Sketch
- Extruded Surface
- Reference Geometry: Plane.
- Swept Surface
- Knit Surface
- Ruled Surface
- Trim Surface
- Curves: Project Curve and Split Line
- Lofted Surface
- Filled Surface
- Extend Surface
- Delete Face
- Extruded Boss/Base
- Extruded Cut
- Offset Surface
- Thicken
- Dome
- Swept Boss/Base
- Mirror
- Fillet
- Chamfer
- Appearance: White (255,255,255), light grey (192,192,192), light cyan (192,255,255), custom black (30,30,30), dark blue (0,0,128), grey (128,128,128), custom dark grey (92,92,92), Custom grey (115,115,115).
- Decal: PhotoView 360 >> Edit Decal or DisplayManager >> View Decals >> Right click >> Add Decal. Apply decals on stairs.
- Radar Mast
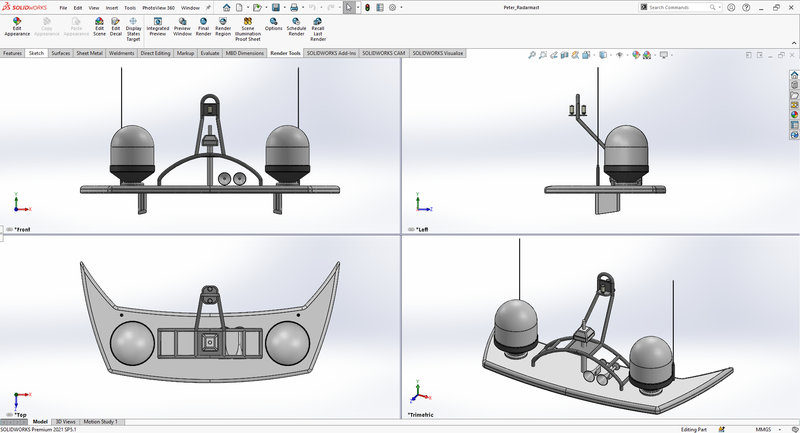
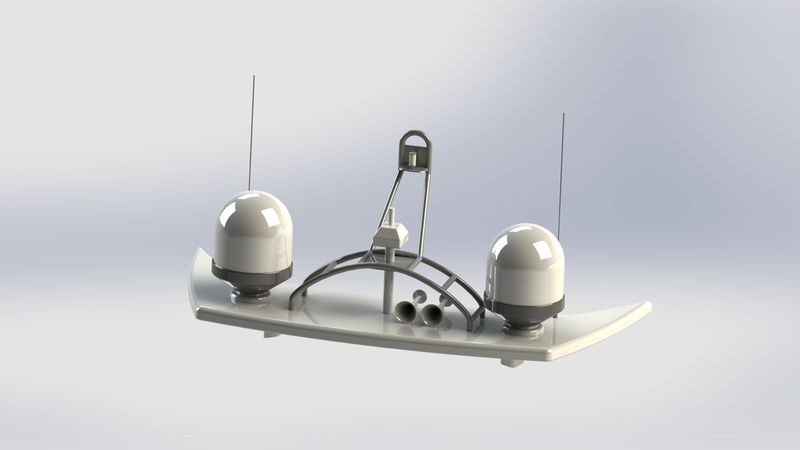
Tools/Features used
- Sketch: Line, Spline, Arc, Rectangle, Circle, Straight Slot, Convert Entities and Offset Entities
- Reference Geometry: Plane.
- Extruded Boss/Base
- Revolved Boss/Base
- Swept Boss/Base
- Curves: Project Curve
- Mirror
- Fillet
- Chamfer
- Dome
- Shell
- Appearance: White (255,255,255), dark grey (92,92,92), custom dark grey (100,100,100), light grey (150,150,150), light yellow (255,255,227).
Assembly
An assembly is a 3D arrangement of one or more parts or assemblies.
To create an assembly: Go to
File >> New >> Assembly.
Or
Start >> Programs >> SolidWorks >> Assembly.
After creating an assembly workspace, we start inserting the modeled parts one by one and applying the Mate relation.
We insert the parts into our assembly by browsing and opening the modeled parts saved in a specific Location/Folder.
Insert >> Component >> Existing Part/Assembly.
Or
Insert Components >> Browse >> Existing Part/Assembly.
- We first insert the Hull by Insert Components >> Hull.SLDPRT.
- We click OK after browsing and opening the hull, which makes the Hull fixed automatically in the assembly.
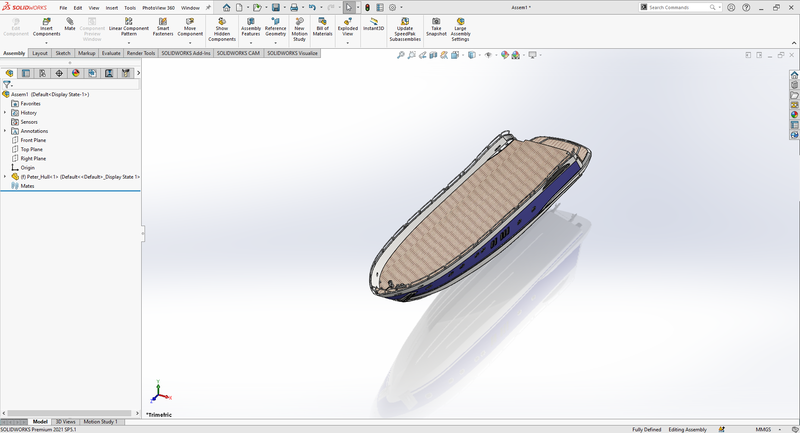
- We insert the Hull by Insert Components >> Superstructure.SLDPRT.
- We click OK after browsing and opening the superstructure, which makes the superstructure fixed automatically in the assembly.
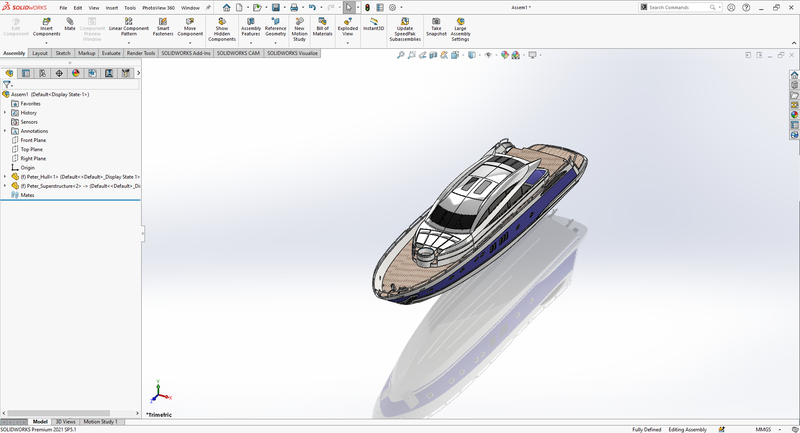
- We insert the Radarmast by Insert Components >> Radarmast.SLDPRT.
- We click OK after browsing and opening the superstructure, which makes the superstructure fixed automatically in the assembly.
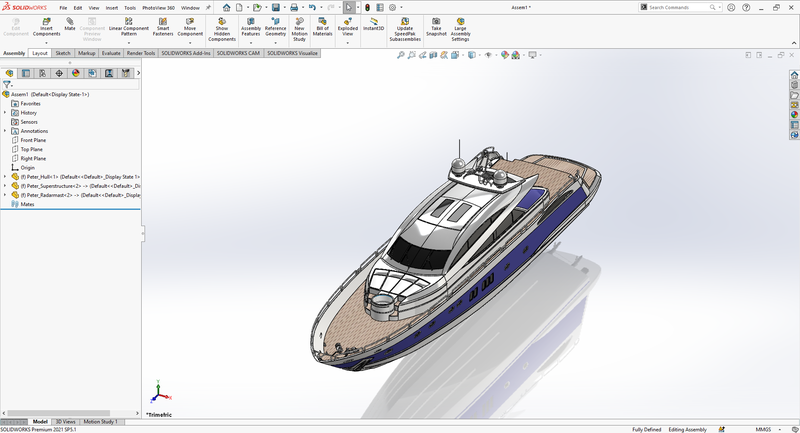
- We insert the Front Seat by Insert Components >> Front_Seat.SLDPRT.
- We click OK after browsing and opening the front seat, which makes the front seat fixed automatically in the assembly.
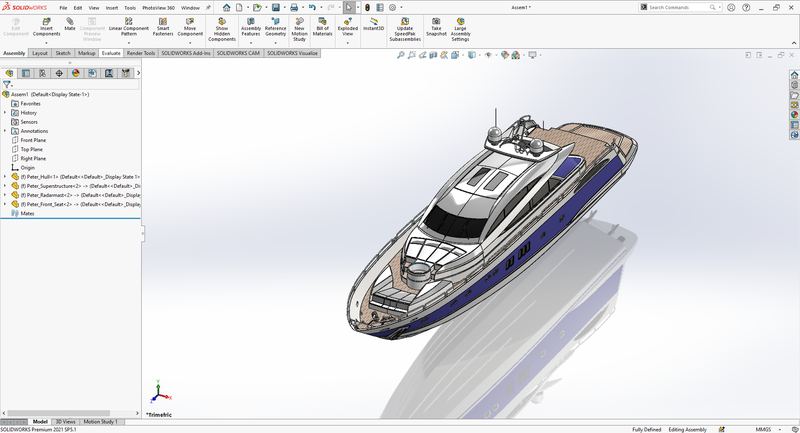
- We insert the Middle Seat by Insert Components >> Middle_Seat.SLDPRT.
- We click OK after browsing and opening the middle seat, which makes the middle seat fixed automatically in the assembly.
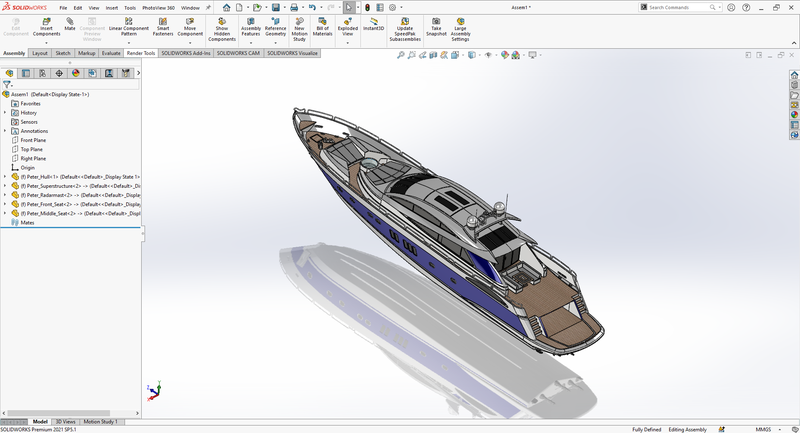
- We insert the Rear Seat by Insert Components >> Rear_Seat.SLDPRT
- We click anywhere on the working screen to add mates manually.
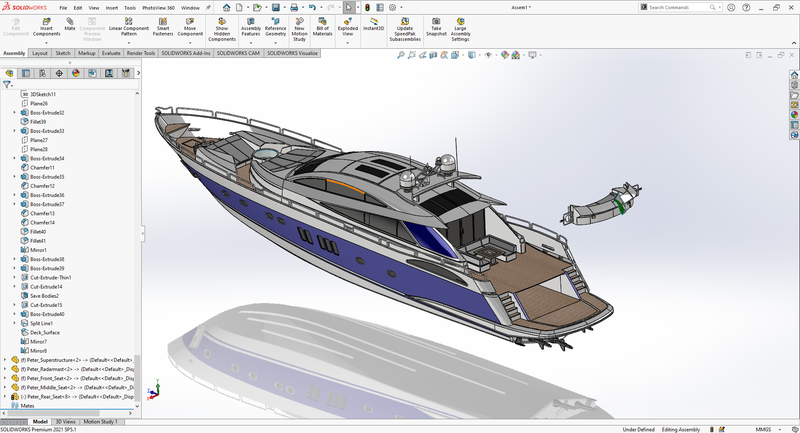
- Create a Coincident mate between the desk surface of the hull and the bottom surface of the rear seat.
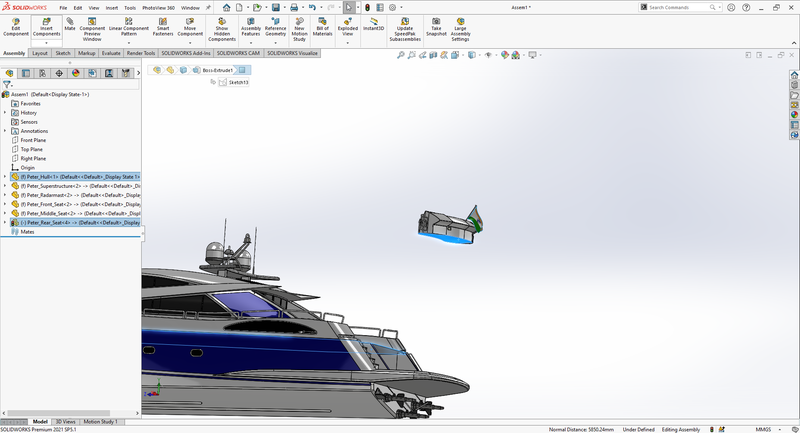
- We add Coincident mate by control selecting Hull surface and bottom surface of rear seat >> Right click >> Mate >> Coincident.
Or
Insert >> Mate >> Select the two surfaces to mate in Mate Selections dialog box >> Coincident.
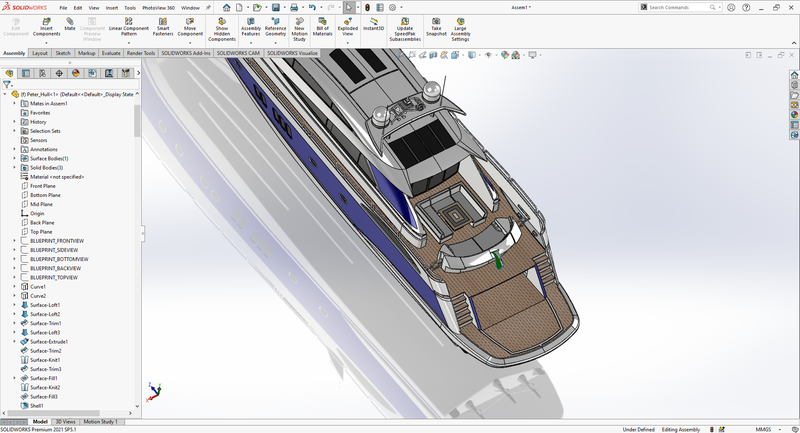
- Insert >> Mate >> Select the Mid Plane of the hull and the Mid Plane of the rear seat in the feature tree >> Coincident.
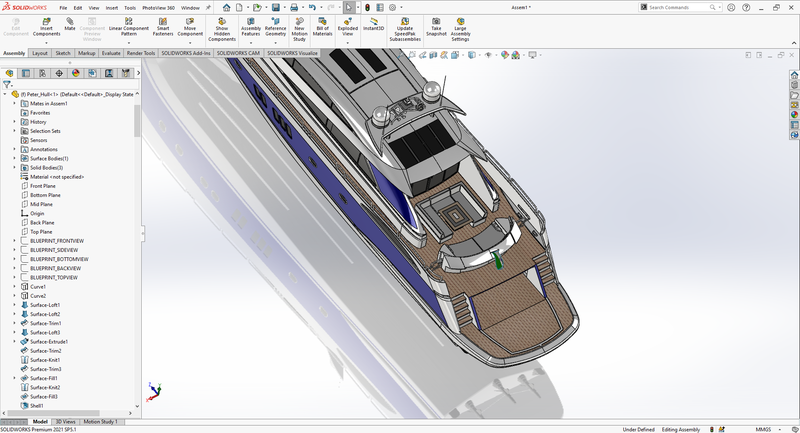
- Insert >> Mate >> Select the black point of the hull and black point of the rear seat as shown and add Distance relation of 50.00mm
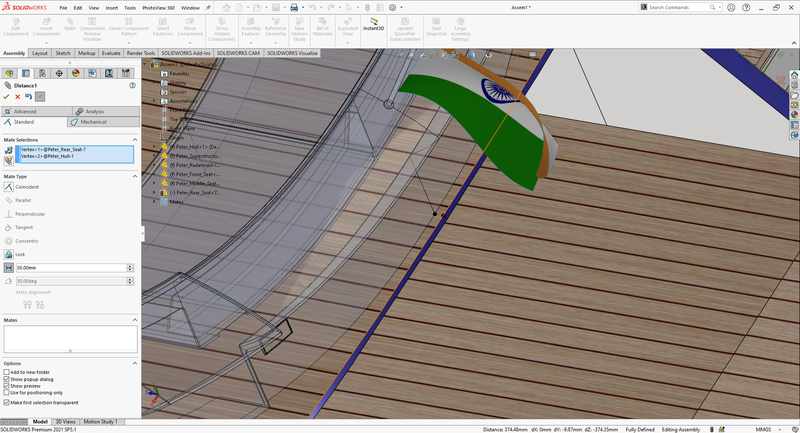
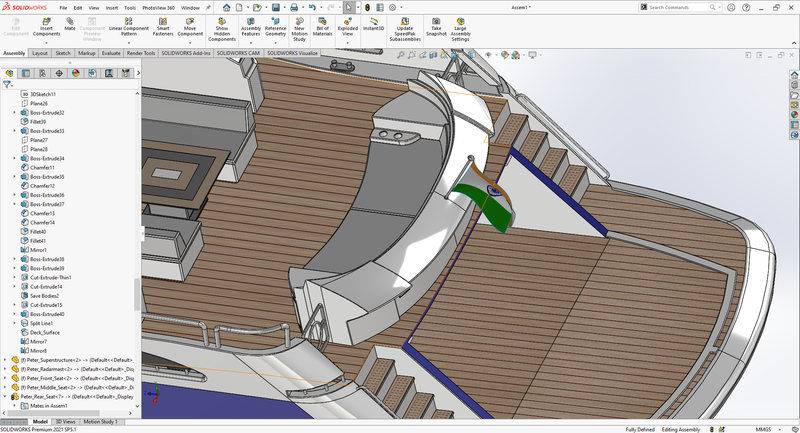
- We insert the Garage Door by Insert Components >> Garage_Door.SLDPRT
- We click anywhere on the working screen to add mates manually.
- Insert >> Mate >> Select the Mid Plane of the hull and the Right Plane of the garage door in the feature tree >> Coincident.
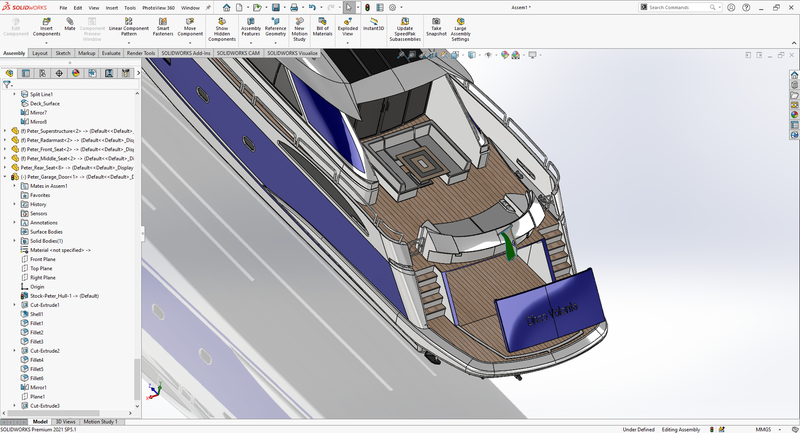
- Insert >> Mate >> Select the blue hinge tube of the hull and blue hinge hole of the garage door in the Mate Selections dialog box >> Concentric.
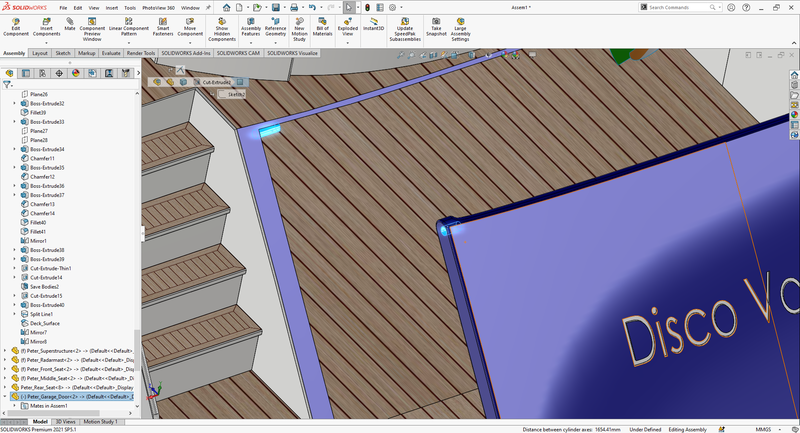
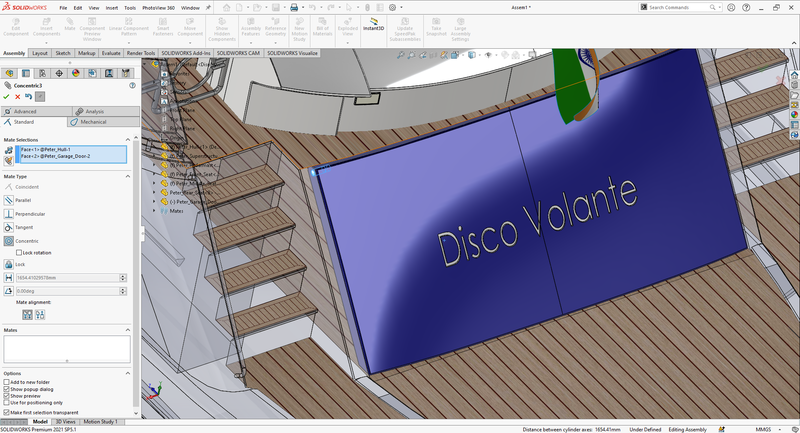
- We insert the Propeller by Insert Components >> Propeller.SLDPRT
- We click anywhere on the working screen to add mates manually.
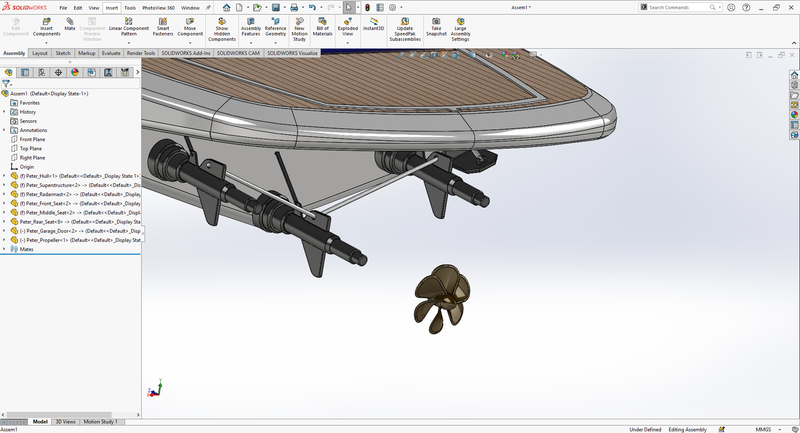
- Insert >> Mate >> Select the blue axis of the hull and blue propeller hole of the propeller in the Mate Selections dialog box >> Concentric.
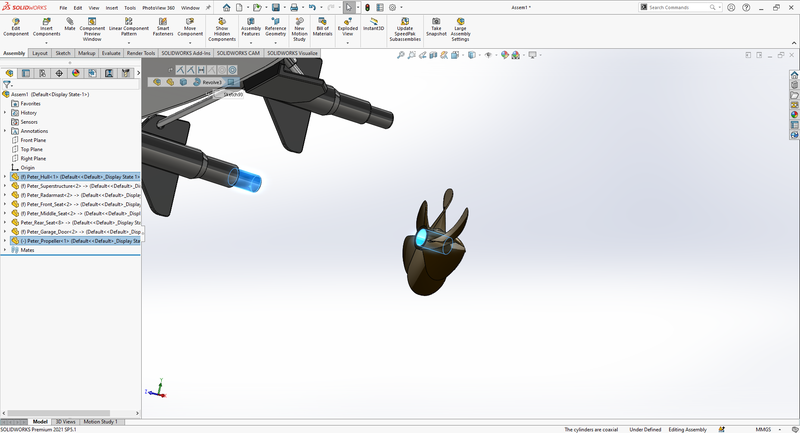
- Insert >> Mate >> Select the blue surface of the hull axis and the blue surface of the propeller >> Coincident.
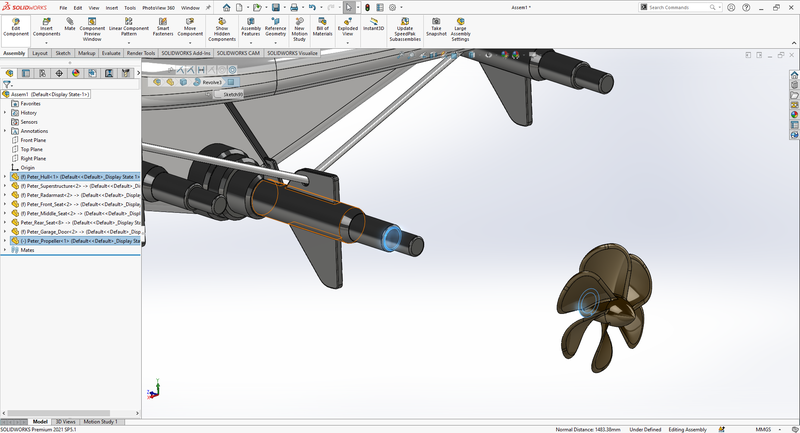
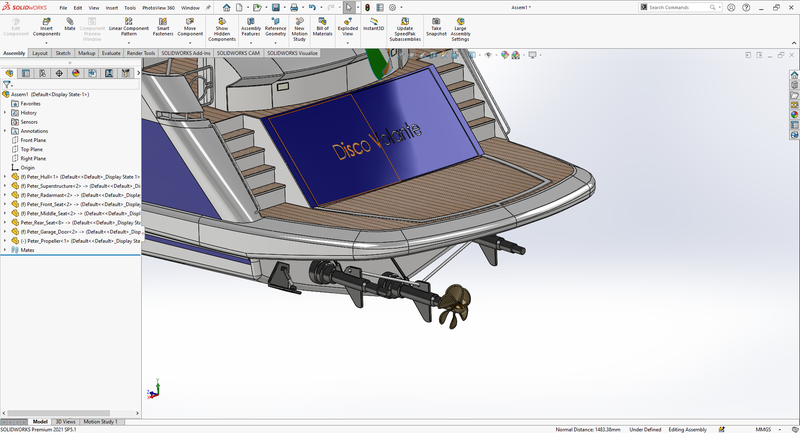
- Insert and mate the other two propellers in the same way.
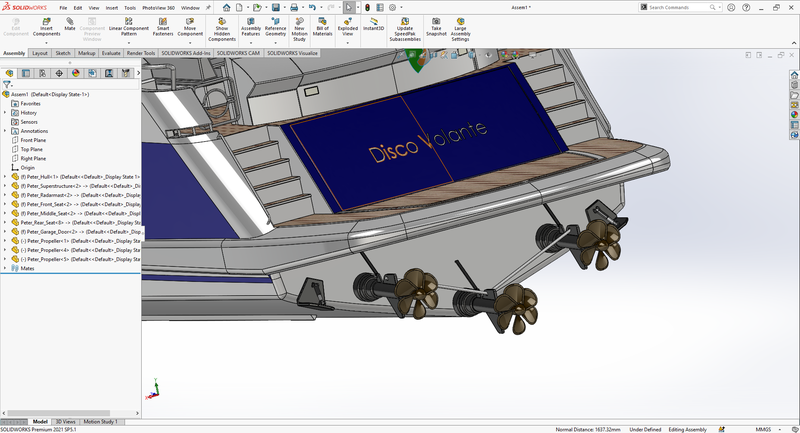
- We insert the Radar by Insert Components >> Radar.SLDPRT
- We click anywhere on the working screen to add mates manually.
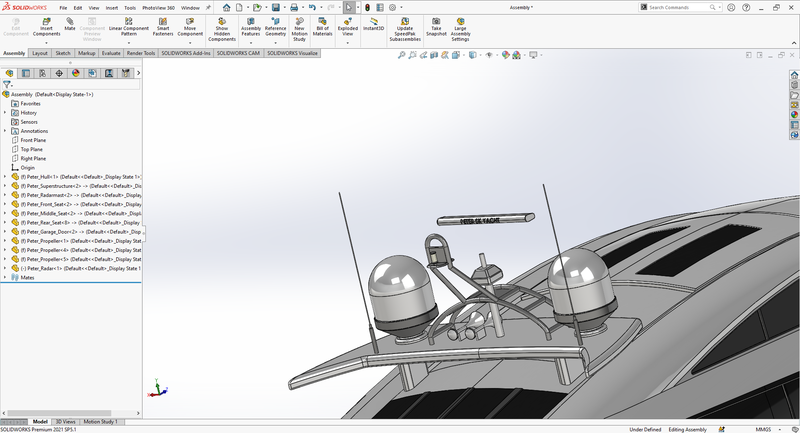
- Insert >> Mate >> Select the blue axis of the radarmast and blue hole of the radar in the Mate Selections dialog box >> Concentric.
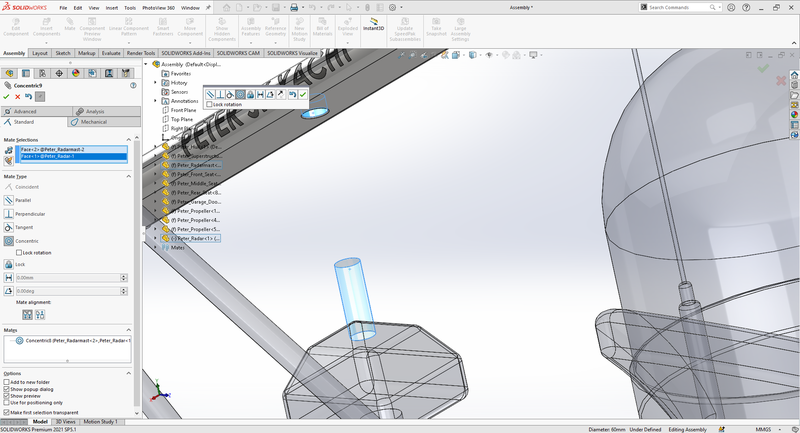
- Insert >> Mate >> Select the blue surface of the radarmast axis and the blue surface of the radar hole >> Coincident.
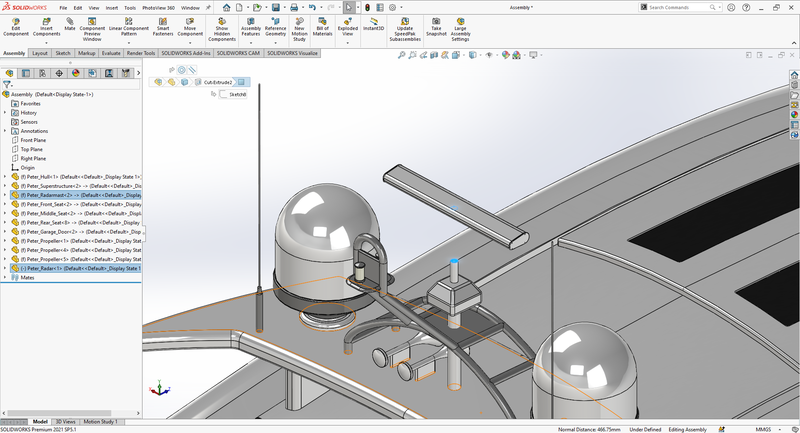
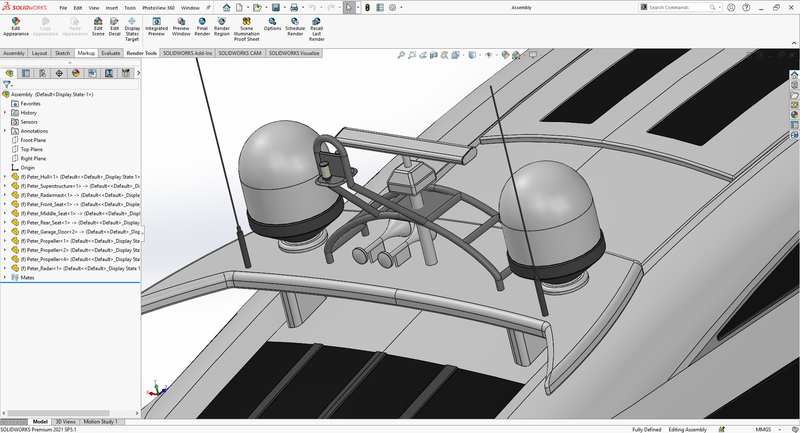
Rendering
PhotoView 360 and SOLIDWORKS Visualize are used for rendering the assembled model.
- Rendering in Photo View 360: Rendering the assembly in SolidWorks with the help of PhotoView 360. PhotoView 360 is a SolidWorks add-in that is used to produce photo-realistic renderings of a created model. The rendering tools help to enhance and produce a realistic chopper model with any scene and environment.
- SOLIDWORKS Visualise: Solidworks Visualize is also a rendering software used only for rendering purposes. It creates a better render than the rendering in the Solidworks PhotoView 360.
Rendering Setup: DisplayManager >> View Scene, Lights, and Cameras
- Camera:
- We can add cameras to model documents and view the model from the camera perspective.
- We can specify the positions of targets and cameras, attach cameras to objects, and sketch entities. The camera can then show motion or move with the entity.
- We can place cameras inside models or Roll cameras to specified angles, and control properties of field of view and depth of field.
- Cameras are used for rendering or animations.
- Here, we are adding a custom camera view to our model by View >> Lights and Cameras >> Add Camera.
- Adjust the camera view to any suitable view by dragging the yellow camera dot and the red dot. We can also input numeric values.
- After getting a suitable view click OK.
- We can also add multiple camera views.
- We can edit them by going to DisplayManager >> View Scene, Lights, and Cameras >> Camera and double clicking on the camera view to be edited.
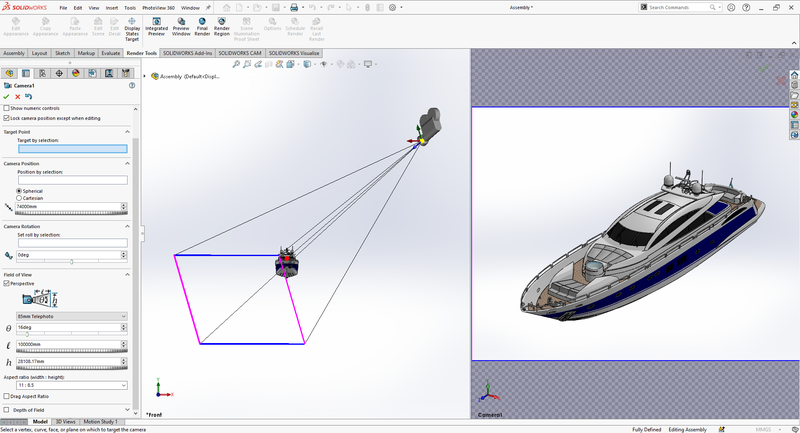
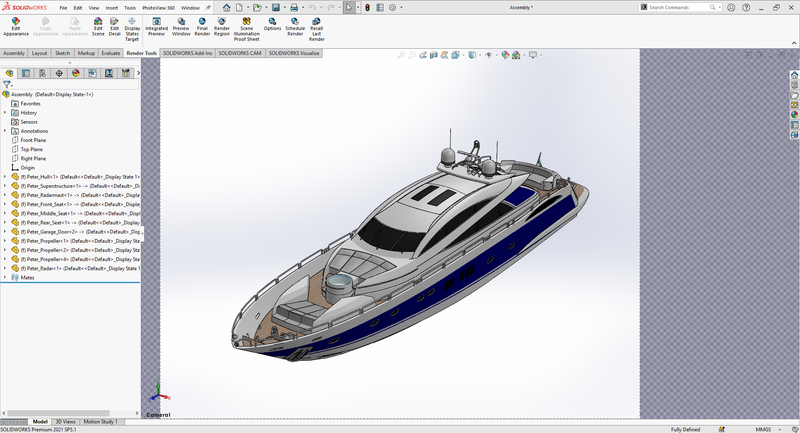
- Scene
- Scenes provide a visual backdrop behind a model. In SOLIDWORKS, they provide reflections on the model. With PhotoView 360 added in, scenes provide a realistic light source, including illumination and reflections, requiring less manipulation of lighting. The objects and lights in a scene can form reflections on the model and can cast shadows on the floor.
- We can add scenes by going to DisplayManager >> View Scene, Lights, and Cameras >> Scene >> Scene and double clicking on the scene or right click >> Edit Scene.
Or
Go to Appearance, Scenes and Decals located in the right-hand corner of the screen
- Here we can select a scene of our liking or a custom scene. Change the Background and Environment.
- Select a suitable background, change the floor offset and click OK.
- Lights
- Scenes and their lighting schemes are closely connected. Lighting works differently in SOLIDWORKS than in PhotoView 360. We can adjust the direction, intensity, and colour of light in the shaded view of a model. We can add light sources of various types, and modify their characteristics to illuminate the model as needed.
- We can change the appearance of the model to enhance or reduce the effect of lighting properties.
- To add a custom light, go to View >> Lights and Cameras >> Select Ambient light, Directional light, Point light or Spot light.
- To edit the SolidWorks or PhotoView 360 lightings go to DisplayManager >> View Scene, Lights, and Cameras >> PhotoView 360 Lights or SOLIDWORKS Lights.
- Here, we are using the default and a few custom light settings.
- Rendering in PhotoView 360
- After selecting and adjusting decals, scene, lights, and cameras, go to Render Tools.
- Click on Options and make the required adjustments.
- Click on Preview Window and check if the render preview is according to our liking. If not then go back and make some adjustments in decals, scene, lights, cameras, or PhotoView 360 Options.
- After Getting a suitable Render preview schedule a render by clicking on Schedule Render. Enter a file name, location, and time and click OK.
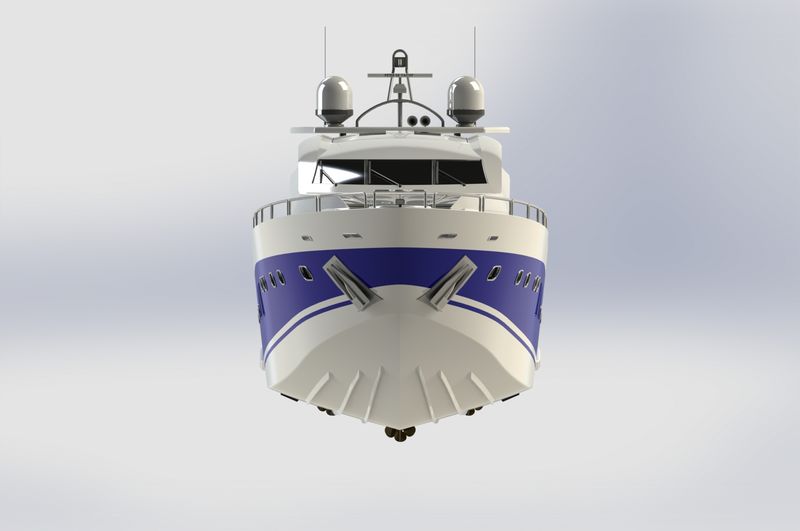
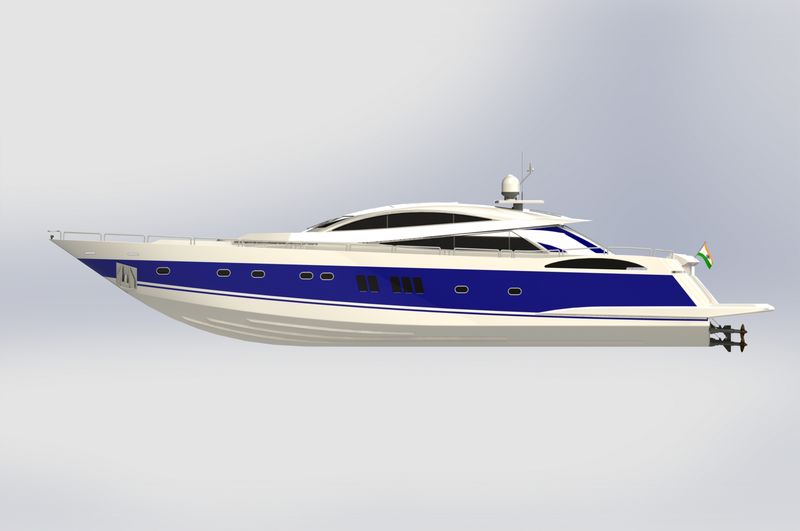
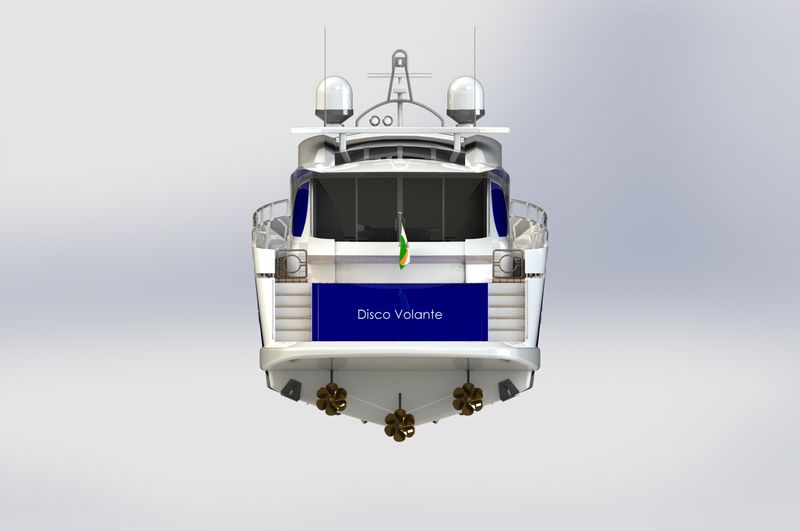
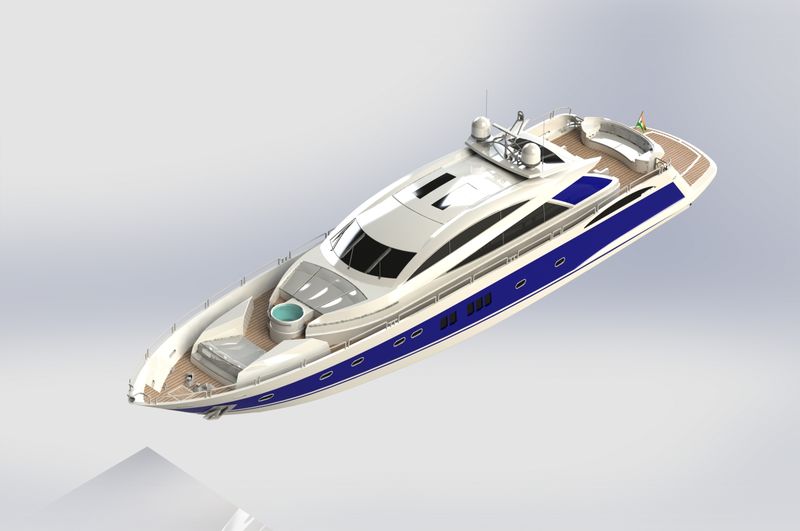
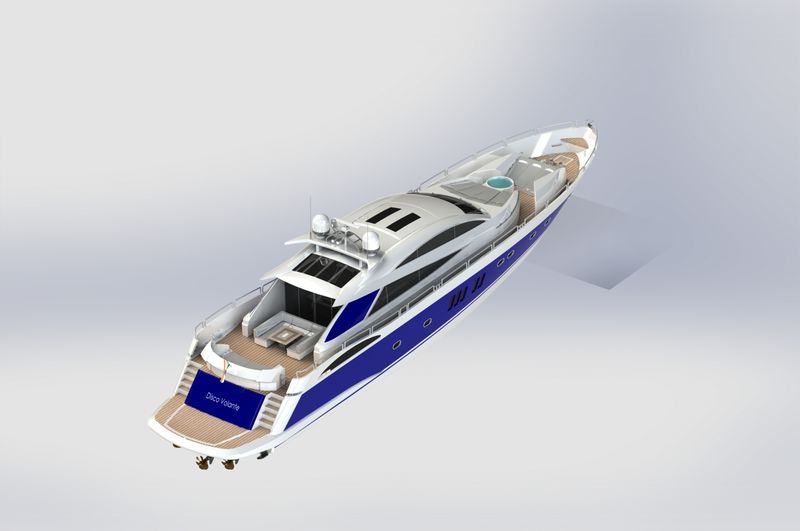
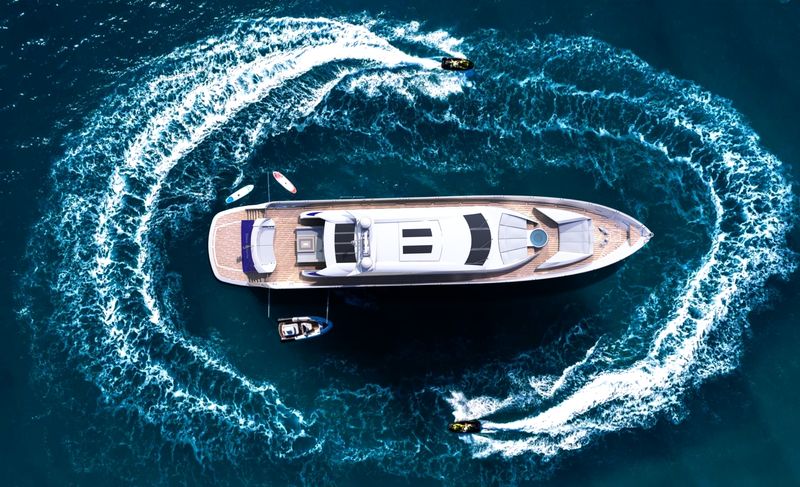
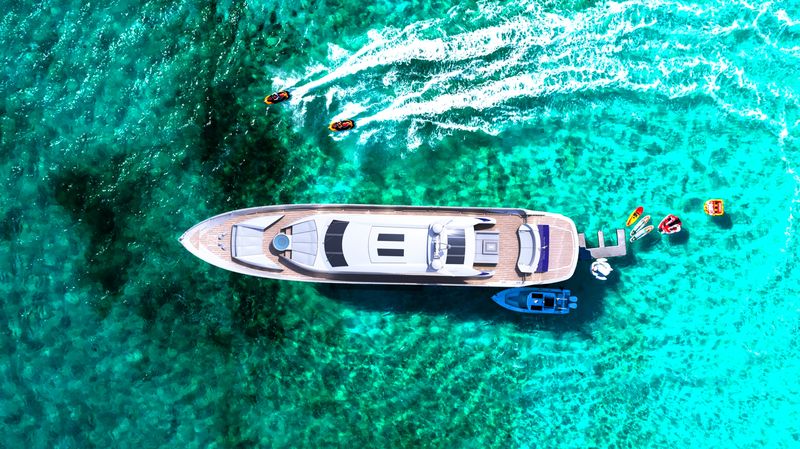
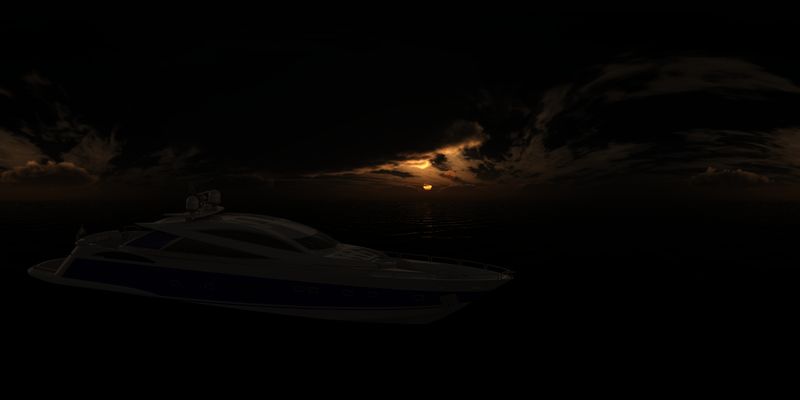
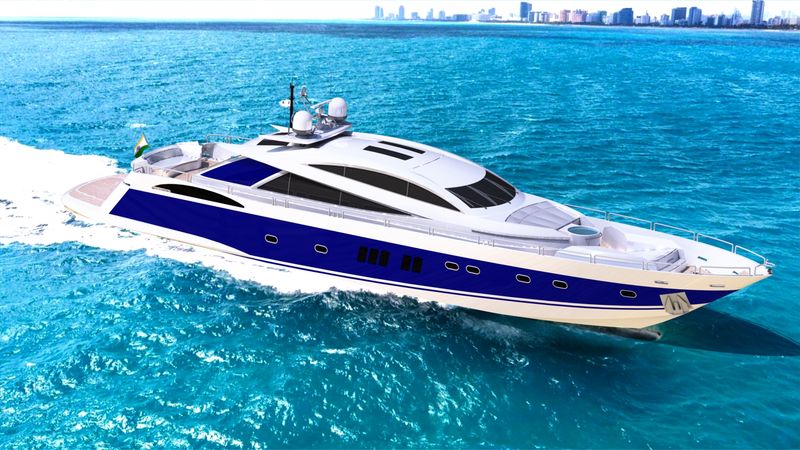
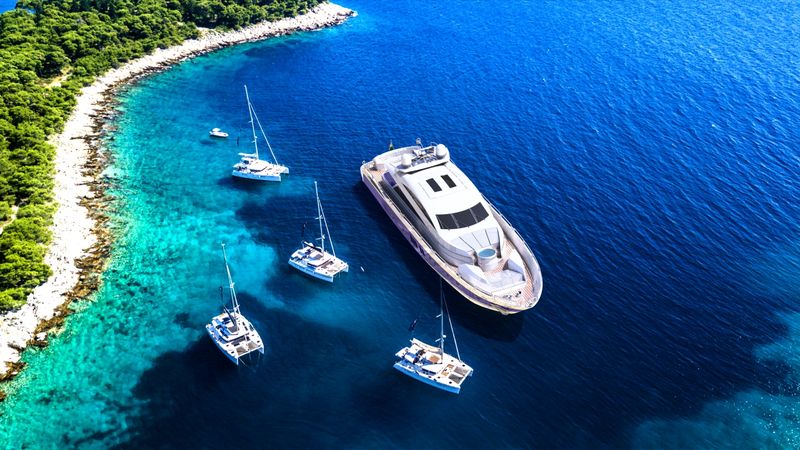
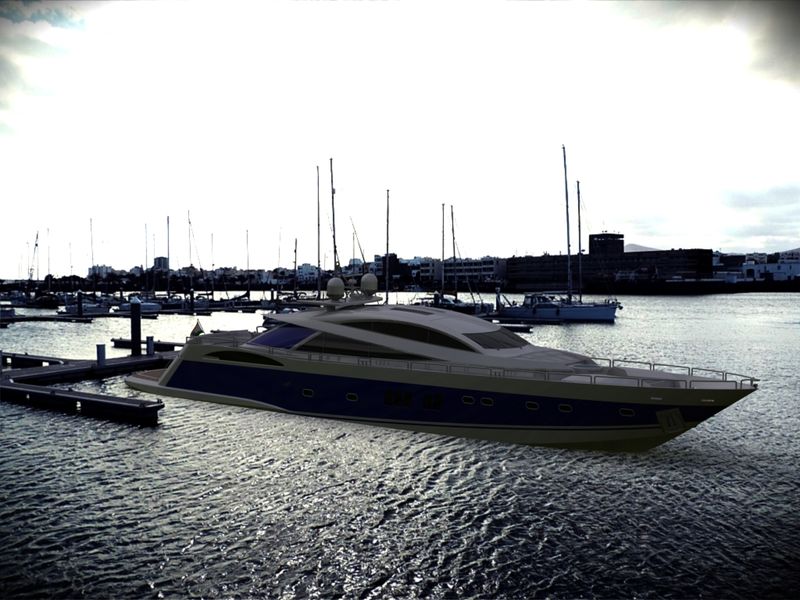
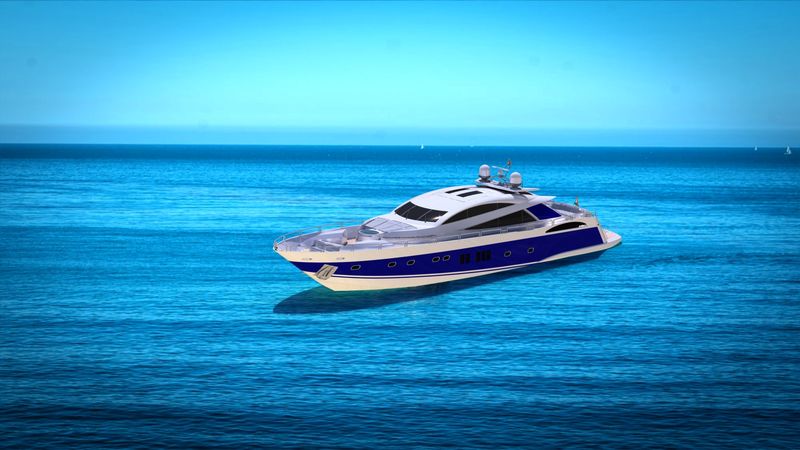
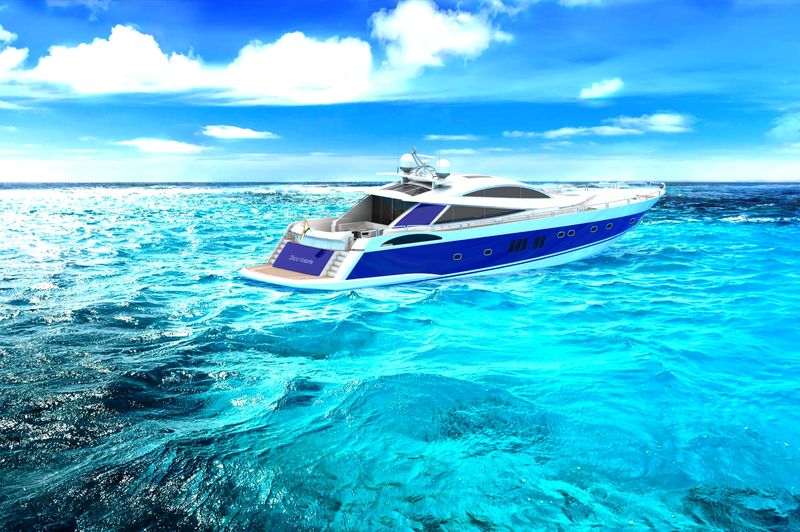
Conclusion
The 3D model of the Yacht is ready from designing each part to assembling each part and is given a realistic look using renders.