Ultimate SOLIDWORKS Course
Title:
To model and assemble of an American Predator Yacht using and solid and surface modelling in solid works.
OBJECTIVE
The main objective of this project is to design and model all the parts of an American Predator Yacht and assemble it to create the Photo-Realistic rendering of the yacht.
INTRODUCTION
In this project the American Predator Yacht was taken as a conceptual model, to understand the 3D modelling methodology of Solid modelling and Surface modelling. every part of the yacht was designed and modelled by using SOLIDWORKS. Then the modelled parts are assembled to create the Photo-Realistic rendered image of the Yacht.
SolidWorks: Solid works is a solid modelling computer aided design and computer aided engineering computer program that runs primarily on windows.
DESIGN OBJECTIVE
In this project, we will be able to sketch and build an entire American Predator Yacht using SOLIDWORKS to understand the 3D- Modelling methodology of Surface Modelling.
In this project we’ll learn, curve generation, surface creation from curves and sketches, different types of surfaces - boundary surfaces - lofted surfaces - filled surfaces - ruled surfaces- reference planes - surface trims - surface knit - move/copy surfaces - mirror surfaces etc.
The main key parts/models we will deal with in surface modelling using SOLIDWORKS.
- Blueprint set-up
- Modelling of propellers, radar
- Modelling of the hull, garage door
- Modelling of rear seats, middle seats, front seats
- Creation of the superstructure
- Final assembly model of the Predator Yacht.
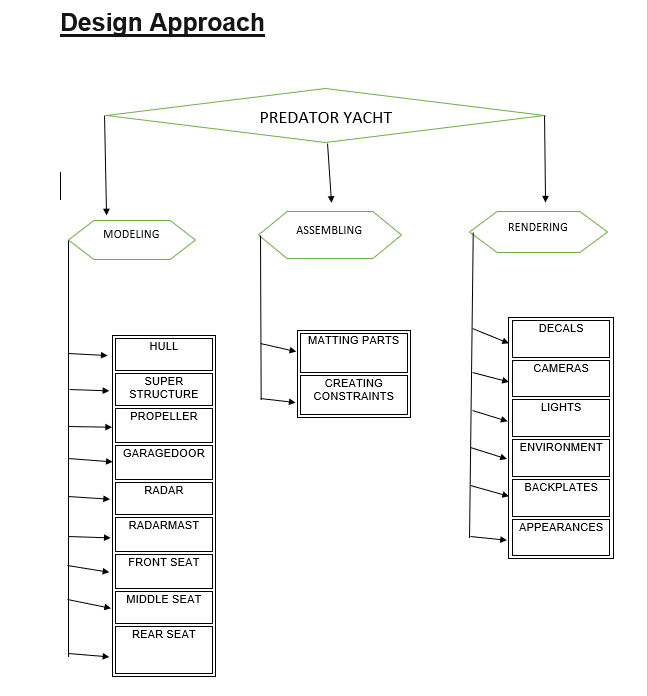
COMMON TOOLS USED IN MODELING OF CHOPPER
- PLANE: -Here the section view of the model is to be sketched.
- SKETCH: -It gives the work base to create 2D & 3D sketches.
- 2d sketch: 2d sketch is the basic command which takes one to the sketching template. It is here where we make the sketches required to make solid body or part. We have to select a plane from 3 predefined planes namely Front Plane, Top Plane and Right plane.
- 3d sketch: In 3d sketch, we make a sketch in a 3dimensional space rather than in a 2dimensional plane
- SMART DIMENSION: -By using this easy to provide the dimension value to the sketch to get the desired shape.
- FILLET: -It provides round shape at corners edges.
- CHAMFER: -It provides sloping edges at corners.
- CONVERT ENTITIES: -Using this easy to get sketched into the other plane or same plane with the same dimension value.
- OFFSET: -It Adds 3D sketches on faces.
- SHELL: -The shell tool hollows out a part.
- EXTRUDE BOSS/BASE: -used to get a solid body in one or two directions.
- REVOLVED BOSS/BASE: -Used to revolve the sketch with the reference of axis or lines in the solid form.
- EXTRUDE CUT: -Used to remove materials from the solid body.
- SWEPT BOSS/BASE: -It proved a solid body by closed profile along an open and closed path.
- PATTERN: -It features the object in a particular direction or path.
- PROJECTED CURVE: -It combines two 2D Continuous curves into a 3D curve.
- TRIM: -It is used to cut the extra line of the surface.
- APPEARANCE: -Using this can get a different look & apply different materials.
- DECALS: - Using this tool painted stickers to be applied.
- VIEW: -Following command comes under this
- Zoom to Area
- Previously view
- Section view
- View orientation
- Display style
- Hide Item
Split – Line or any sketch entity is used to divide model faces into two. They can be one or more connected sketch entities. Sketches are oriented so that they will pass through model faces when projected normal to the sketch plane.
Dome - It can add one or more domes to the selected planar or non-planar faces. The software automatically calculates the distance using the radius of the arc as a basis for the dome.
Pierce Relationships - The Pierce relationship is used in sweeps. It can be termed as a 3D Coincident relationship. In our spring, the circle will follow the helix. If we stick the wire through the paper at the centre of the circle, this would be a pierce relationship. When we perform the sweep, the paper will move along the wire and grasp at the pierce point.
Composite Curve - We can create composite curves by combining two projected curves, sketch geometry, and model edges into a single curve. Composite curve basically used as a guide curve when creating a loft or a sweep.
Surface modelling
Surface modelling is one of the for creating planar or non-planar complex geometry which has zero thickness. This zero-thickness geometry is known as surface. These surfaces are generally used for creating models of complex shapes. We can convert surface models in solid models. We can also extract a surface from a solid model using the tools available for surface modelling.
Advantages of Surfaces:
- Surfaces give mush more flexibility when creating complex shapes that cannot be done using solid features.
- Surfaces can be used to build a shape face-by-face rather than all at once.
- Surfaces can be used as reference geometry.
- Surfaces can be more efficient than solid features depending on object.
Disadvantages of Surfaces:
- Modelling with surfaces is almost always more work than modelling with solids.
- There is a much more complex workflow when creating surfaces and then converting to solids.
SURFACE COMMANDS used in this modelling.
- Lofted Surfaces – Creates a lofted surface between two or more profiles or sketches. Specify start and end constraints and add guide curves to control the path shape.
- Boundary Surfaces – The boundary surface feature lets us to create surfaces that can be tangent or curvature continuous in both directions (all sides of the surface). In most of the cases, this delivers a higher end quality results than the loft tool.
- Extruded Surfaces – Extrudes a sketch or selected sketch contours in one or two directions two create a surface feature
- Revolved Surfaces – Revolves a sketch or selected sketch contours around an axis to create a surface feature.
- Swept Surfaces – It Sweeps a closed profile along an open or closed path to create a surface feature. It uses a tangent plane at the end of the path so that the path is normal to the swept surface.
- Filled Surfaces – Patches a surface within a boundary defined by edges, sketches, or curves. We can also use curves to fill surfaces and adjust resolution to improve surface finish.
- Ruled Surfaces – Inserts ruled surfaces in a specified direction from edges, Tangent to surface, Normal to surface, tapered to vector, perpendicular to vector or sweep can be selected for inserting ruled surfaces. We can also trim and knit the surfaces and remove any connecting surfaces.
- Trim Surface – It trims the surfaces where a surface intersects with another surface, a plane or a sketch
- Knit Surface – It combines two or more adjacent, non-intersecting surfaces into a single surface body. The surfaces must joint at an edge. If the resulting knit surface encloses a volume, we can create a solid body from the Property Manager
- Move/copy surfaces – Moves or copy surfaces about a plane or a sketch.
- Offset Surface – Offsets surfaces using one or more contiguous faces. This tool helps us to create an offset surface with gaps.
- Extend Surface – Extends one or more edges or faces on a surface, based on end conditions and extension type.
- Mirror surfaces – A mirror feature is a copy of a selected feature, mirrored about a plane or planar face. A mirror sketch entity is a copy of a selected sketch entity that is mirrored about a centreline. If any of the original feature or sketch is modified, the mirrored copy is update automatically to reflect the change.
- Reference plane – We can create planes in part or assembly documents. We can use these reference planes to sketch, to create a section view of a model, for a neutral plane in a draft feature, and so on.
- Projected curve – A projected curve is typically used either in sweeps and lofts as path or guide curve. There are two types of projected curves:
- Sketch on Sketch: Use two sketches to make a single curve.
- Sketch on surface: Use a sketch to project on a surface.
- Split line – The Split Line tool projects an entity (sketch, solid, surface, face, plane, or surface spline) to surfaces, or curved or planar faces. It is used for dividing a selected face into multiple separate faces. We can split curves on multiple bodies with one command.
- Split point – We can split a sketch entity to create two sketch entities. Conversely, we can delete a split point to combine two sketch entities into a single sketch entity.
- Fillet - A fillet is an internal rounding of a corner or edge in a sketch, or an edge on a surface.
PART MODELLING DESCRIPTION
BLUEPRINT:
A blueprint can be a reproduction of a technical drawing or engineering drawing using a contact print process on light-sensitive sheets. blueprint can be used as a guide for making a design or pattern that can be followed. They were easier to read and faster to make due to the use of blue print.
The above shown Blueprint was used to model the Yacht in a fully defined constraint. Blueprint is setup by using the Sketch pictures option and placed the different blueprints at the required planes.
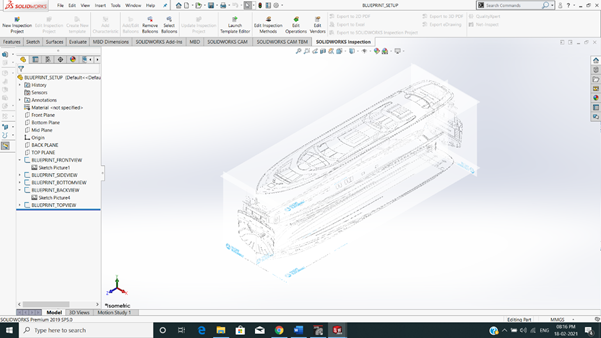
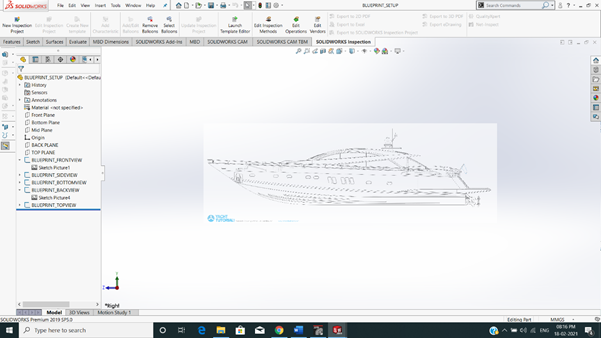
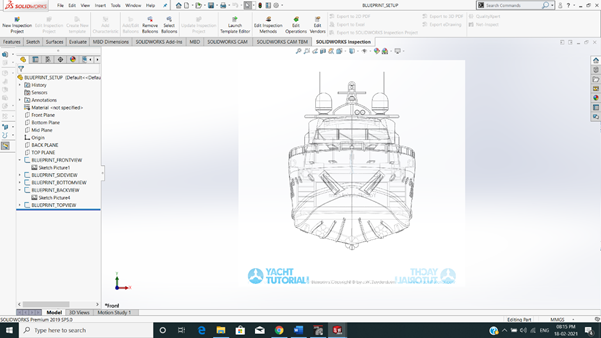
- HULL:
A hull is the watertight body of a ship or boat. The hull may open at the top (such as a dinghy), or it may be wholly or partially covered with a deck. ... The line where the hull meets the water surface is called the waterline.
The hull of a ship is the most notable structural entity of the ship. To define the hull, it can be said that it is the watertight enclosure of the ship, which protects the cargo, machinery, and accommodation spaces of the ship from the weather, flooding, and structural damage.
- The hull is a watertight body of a vessel which may be open or may be partly covered with a deck.
- Hull has several watertight decks and bulkheads as the major transverse membrane.
- The intermediate member of the hull consists of girders, webs and stringers.
- Depending on the structural arrangements, there may be longitudinal members for strengthening purpose.
COMMANDS USED TO MODEL
In Sketch
- Line
- Spline
- Circle
- Rectangle
- Arc
- Slot
- 3-D Sketch
- Sketch picture
In Surfaces
- Extruded Surface
- Revolved Surface
- Lofted Surface
- Surface Trim
- Surface Fill
- Surface Knit
- Delete Face
In Features
- Project Curve
- Chamfer
- Fillets
- Reference Plane
- Split
- Split Line
- Extruded Boss Base
- Extruded Cut
- Mirror
MODELLING PROCEDURE
- The first step for modelling the Yacht was creating a blueprint of it.
- the blue print was placed on the required planes, by using blue prints first the hull was designed.
- To create the shape of the hull, projected curves are produced by drawing the required sketch using splines with the help of blueprint.
- Then the projected curves were lofted to create a lofted surface and the remaining unwanted surface was trimmed using surface trim option.
- Then the back portion of the hull were the propeller needs to be placed was extruded using Extruded Surface and all the surface created must be Knitted together to remove the gaps between the surfaces.
- Then the offset option is used and another surface was created and each surface was filled using surface fill to create the outer shell of the hull which will be converted into a solid body using knit surface option.
- Shell feature is used to create shell in the front portion of the hull.
- Then the deck surface is created using Extruded option.
- Then the required chamfers and fillets were created as shown in the pdf.
- All the windows and Portholes were designed using Extruded Cut. Then Fillets were added around the edges.
- For creating the round edges around the berth window, the reference planes were created and a circle for required dimensions were make pierced and then swept around the edge of the windows to make them round.
- The Rails at the bottom of the yacht were created using Extruded Boss/Base and the chamfers were applied both the sides.
- The Cable Rollers were created using Extruded Boss/Base and Swept Boss/Base and the head part of it was created using Revolved Boss/Base and Extruded Cut was used to cut through the extrude and a Dome was created over it.
- Helix/Spiral sketch was created to sweep the rope around the Cable Rollers.
- By using Slot option, the Rope hangers were extruded and the dome was applied and then the Linear Pattern was used to create one more.
- The window bars were created using Extruded Boss/Base.
- The staircase was created by using extruded boss/base and the hand support bar was created using Swept Boss/Base.
- The Railings around the Hull was generated with the help of blueprint and the projected curve was produced and the railing reference was swept using Swept Boss/Base.
- The Axles the propeller and the surfer were created using Revolved Boss/Base option and using the 3d sketch.
- The Anchors are created by sketching the first half and extruded with the use of Extruded Boss/Base and the other half was mirrored.
- Finally, the Garage Portion was created by using Extruded Cut and the portion was saved for later use by using Split option.
- With the use of Split line option, the Painting portion for our hull was split separately.
- Then the other half of the Hull and the Axle of the surfer and propeller was mirrored to generate the complete hull using Mirror tool.
- And the part was saved by adding proper appearances and fillets.
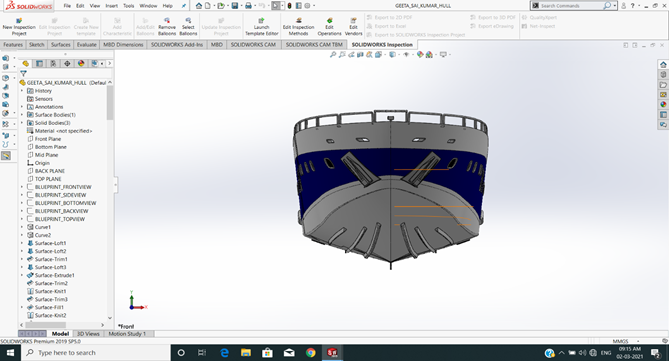
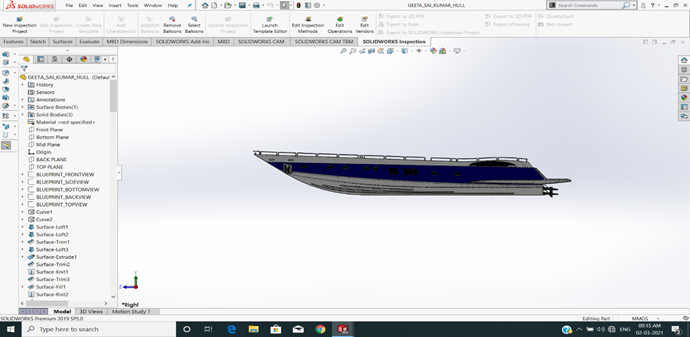
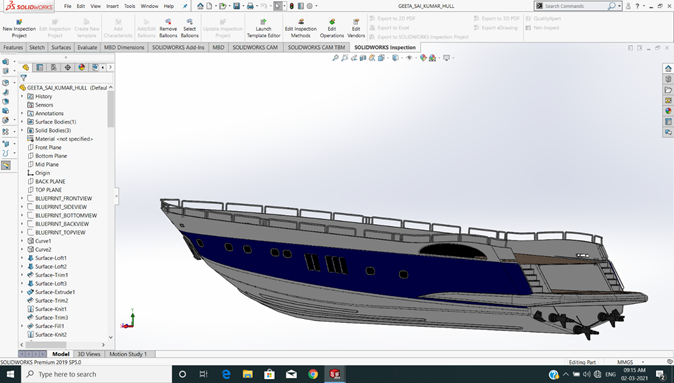
- SUPER STRUCTURE
A superstructure is an upward extension of an existing structure above a baseline called ground level and it usually serves the purpose of the structure's intended use. A superstructure is a decked structure on the freeboard deck expanding from side to side of the ship.
COMMANDS USED TO MODEL
In Sketching:
- Sketch Picture
- 3D Sketch
- Line
- Spline
- Circle
- Rectangle
- Centre Point Arc
In Surfaces:
- Extruded Surface
- Swept Surface
- Ruled Surface
- Knit Surface
- Trim Surface
- Extend Surface
- Filled Surface
- Lofted Surface
- Revolved Surface
- Fillet
- Chamfer
In Features:
- Project Curve
- Reference Curve
- Convert Entities
- Split
- Split Line
MODELLING PROCEDURE:
- The deck surface from the hull was imported and the superstructure was modelled over it.
- The side surface of the Superstructure is created using Extruded Surface, Lofted Surface, Filled Surface, Trim Surface and Knit Surface.
- The Front side of the Superstructure was designed to have four rest beds which were created using Extruded Boss/Base, Fillets and Dome.
- The front edge of the superstructure was provided with a Water Feature which was formed using Extruded Boss/Base, Extruded Cut, and filled with water appearance.
- The Windshield was created by Extruded Cut and the wipers were created by using 3D sketch and reference plane was created using Swept Boss/Base.
- The Portholes for the Superstructure are formed by using Extruded Surface, Trim Surface and Extend Surface.
- The left-out edges were filled using the ruled surface.
- The Back Doors of the Superstructure was formed using Extruded Cut, Fillets and Reference Plane.
- After all the surfaces generated were Knitted together to form a solid body.
- The Superstructure consist of two surface bodies and five solid bodies.
- One of the surfaces was the Deck Surface the other one was used to place the Radar Mast so it was renamed as Radar Mast reference Surface.
- Then the other half was mirrored and the proper fillets and appearance was added and lastly the part was saved.
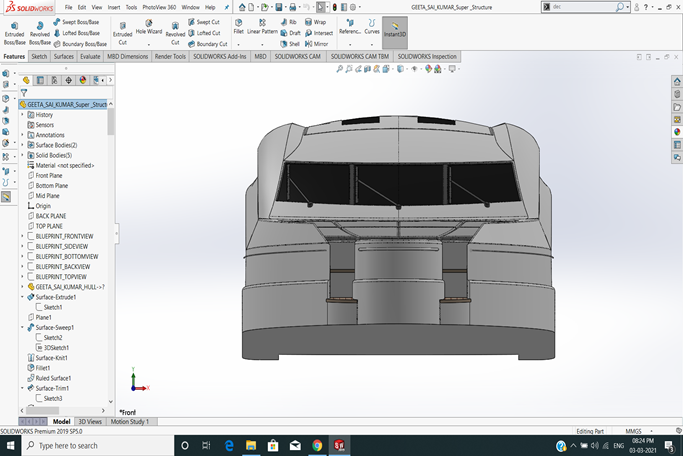
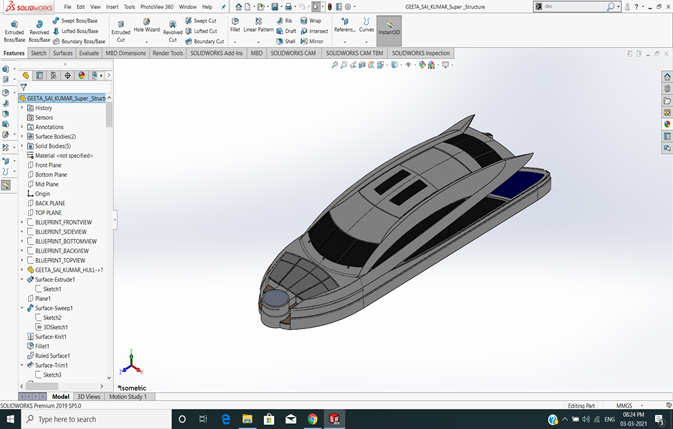
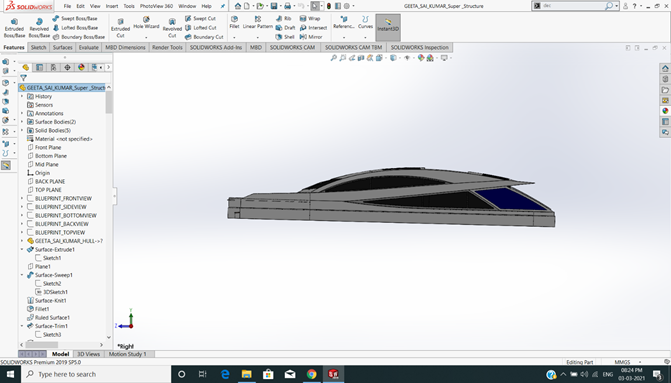
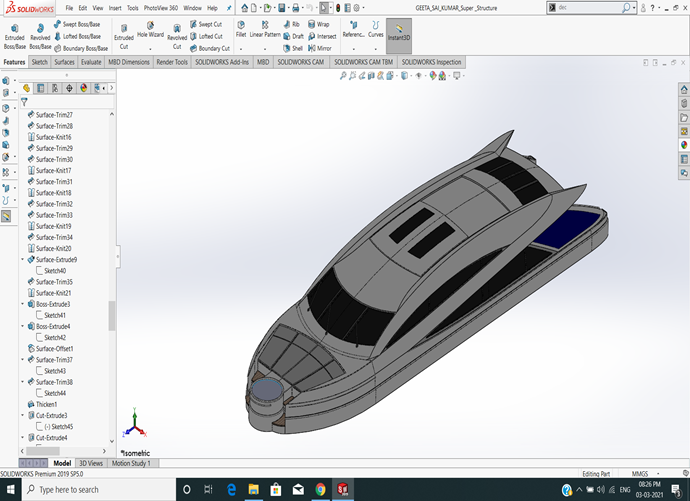
- PROPELLER:
There can be one, two or three propellers. It is the most important part of the ship without which a ship can't move. So, the main function of propeller is to propel the ship in the forward direction by producing thrust on water. Its working principles are Newton's third law of motion and Bernoulli's theorem.
COMMANDS USED TO MODEL
In Sketch
In Features
- Revolved Boss/Base
- Lofted Boss/Base
- Extruded Cut
- Reference Plane
- Circular Pattern
- Fillet
MODELLING PROCEDURE:
- The centre portion of the Propeller was sketched and revolved using Revolved Boss/Base.
- Then the Blades were created using the Reference Plane, Lofted Boss/Base and Fillet.
- Then the remaining five blades were created by using Circular Pattern.
- Then the centre circular portion was removed using Extruded Cut option.
- Finally, the part was saved by adding the proper appearance.
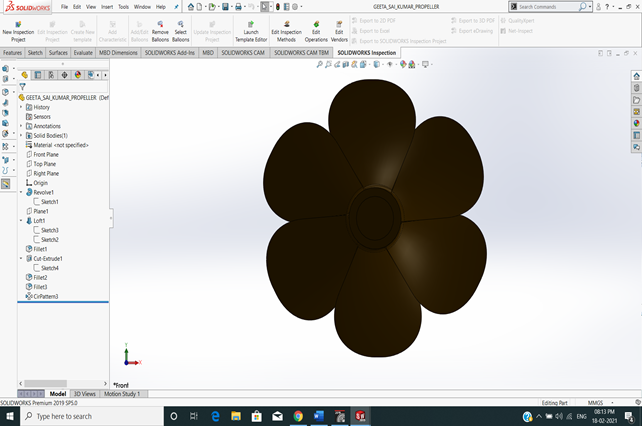
- GARAGE DOOR
A garage door is a large door on a garage that opens either manually or by an electric motor (a garage door opener). Garage doors are generally large enough to accommodate automobiles and other vehicles. The operating mechanism is spring-loaded or counterbalanced to offset the weight of the door and reduce human or motor effort essential to operate the door. Seldomly, some garage doors slide or swing horizontally. Doors are made of wood, metal, or fiberglass, and may be insulated to prevent loss of heat.
COMMANDS USED TO MODEL
In Sketch
In Features
- Extruded Cut
- Reference Plane
- Fillet
- Shell
- Mirror
MODELLING PROCEDURE
- The solid body split while manufacturing the Hull was imported to model the Garage Door.
- By using the Extruded Cut the Chamfered face for the door was produced.
- Then by using the shell feature the solid body for our garage door was formed and proper fillets were applied.
- After the door holders on both sides were created using Extruded Cut.
- Then the other half of the Garage Door was placed using Mirror tool after applying the required fillets.
- Then the text over the garage door “HAKUNA MATATA” was created using the text option in sketch feature.
- At last, the part was saved by applying proper appearance.
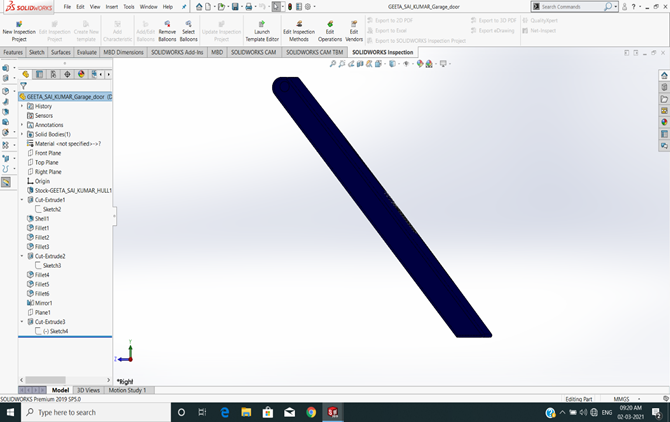
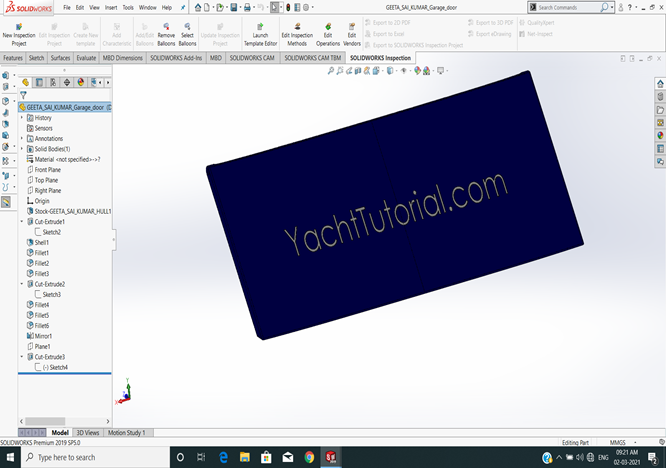
- RADAR:
Marine radars are X band or S band radars on ships, used to detect other land obstacles and ships, to provide bearing and distance for collision avoidance and navigation at sea. They are electronic navigation instruments that use a rotating antenna to sweep a narrow beam of microwaves around the water surface surrounding the ship to the horizon, detecting targets by microwaves reflected from them, generating an image of the ship's surroundings on a display screen.
COMMANDS USED TO MODEL
In Sketch
In Features
- Extruded Boss/Base
- Extruded Cut
- Sketch Pattern
- Fillet
- Mirror
- Split Line
MODELLING PROCEDURE
- By drawing the required sketch, the body of the Radar was created using Extruded Boss/Base.
- By using the Sketch Pattern, the four Dotted holes were created using Extruded Boss/Base and Extruded Cut.
- The Radar has a circular slot underneath which was created using the Extruded Cut.
- The other half was mirrored with the help of mirror tool.
- The Text over the Radar was created using the Text option in sketch and then the Split Line was used to produce over the face of the radar.
- At last, the radar must be filleted around the edges of the body and also around the four holes.
- Finally, the part was saved by adding proper appearance.
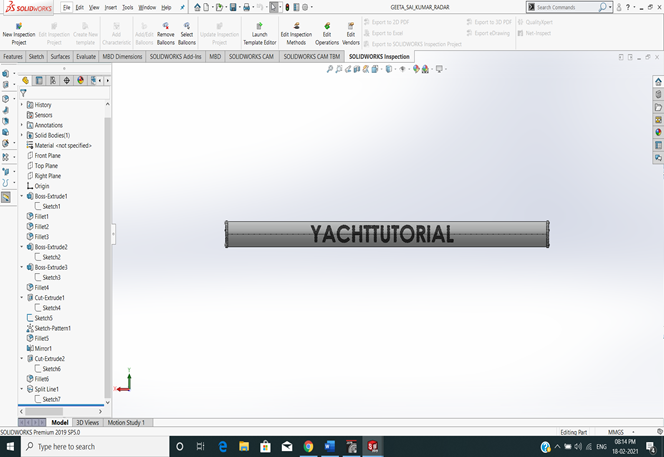
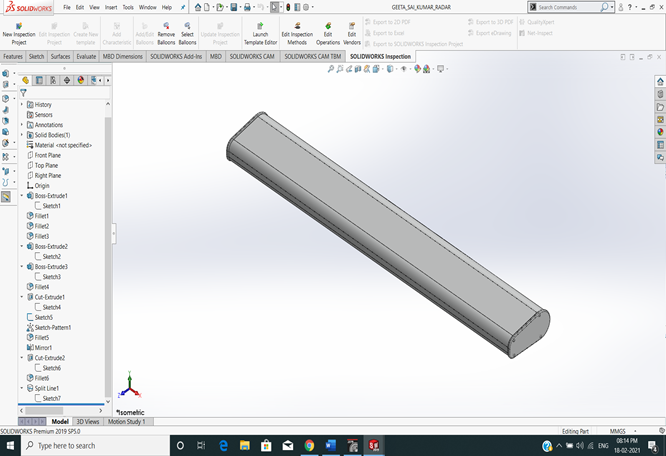
- RADARMAST:
A mast is a vertical ship structure mounted on top of bridge and forward of the forecastle towards the ship’s bow. It accounts for the support platform for the ships derrick and hold mandatory equipment’s such as radars, navigation light and ships horn in case of foremast. They are made up of high tensile steel with added rigidity depending on the size of derricks it holds. Other than that, a ships main mast is also used in hoisting ships flag.
Out of various parts of ship the chief job of mast is to hold necessary equipment such as radar receiver, navigation lights, ships horn, flags and derricks in some case.
COMMANDS USED TO MODEL
In Sketch
- Sketch Picture
- Line
- Spline
- Rectangle
- Arcs
In Feature
- Extruded Boss/Base
- Lofted Boss/Base
- Revolved Boss/Base
- Swept Boss/Base
- Reference Plane
- Projected Curve
- Fillet
- Mirror
- Dome
- Shell
MODELLING PROCEDURE
- The first half of the Radar was Modelled with the help of blueprint and then the second half was mirrored with the help of Mirror tool.
- The body of the Radar was created with Extruded Boss/Base and Revolved Boss/Base.
- The antenna of the radar was also created using the Extruded Boss/Base.
- The lamp stand along with the connecting rod were designed using the Swept Boss/Base and Mirror tool.
- The lamp was created using the projected curve and then the curve was swept using swept boss/base.
- The horns were designed using the Revolved Boss/Base, Dome and Shell.
- After the fillets and chamfers were applied wherever necessary.
- In the end, the part was saved by applying appropriate appearances.
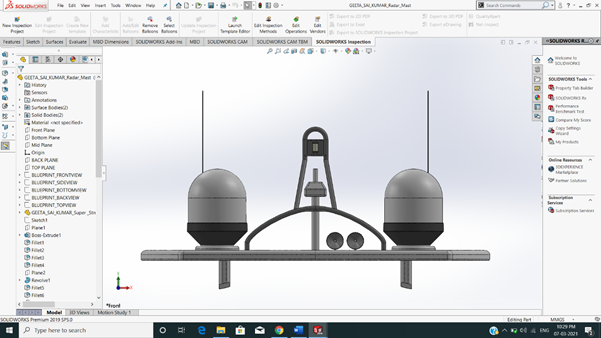
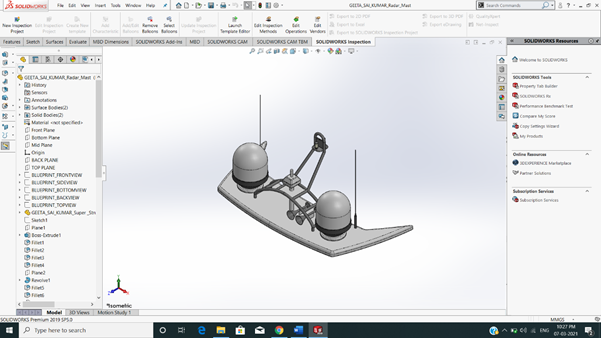
- FRONT SEAT:
Front seats feature two connected seats that are built back-to-back from one and the other. They have a built-in storage unit underneath them. Lounge seats can also fully recline right back to make it easier for you to kick your feet up and get more cosy. The front seat in our model was placed before the superstructure and also it has sun pads to lean on it. Sun pads are a great way to reclaim lost space on our boat.
COMMANDS USED TO MODEL
In Sketch
- Sketch Picture
- Line
- Spline
- Circle
- Arcs
In Surfaces
- Extruded Surface
- Lofted Surface
- Trim Surface
- Filled Surface
- Knit Surface
- Swept Surface
- Revolved Surface
In Features
- Extruded Cut
- Revolved Boss/Base
- Chamfer
- Fillet
- Mirror
- Dome
MODELLING PROCEDURE
- The Front seat of the Yacht was also created using Blueprint.
- The first half was modelled and the next half was mirrored using Mirror tool.
- Next the front seat was placed before the Superstructure facing the Water Feature of the Superstructure and the back end must be placed on the bow of the Yacht.
- The body of the Front Seat was modelled using Swept Surface, Extruded Surface, Filled Surface, lofted surface and the unnecessary part was removed using Trim Surface.
- Later the four Rest Beds were created using Extruded Boss/Base and the dome was created over the face of the beds separately.
- Then the required fillets and chamfers were created with the extruded thin surfaces.
- Finally, the part was saved by adding proper appearances.
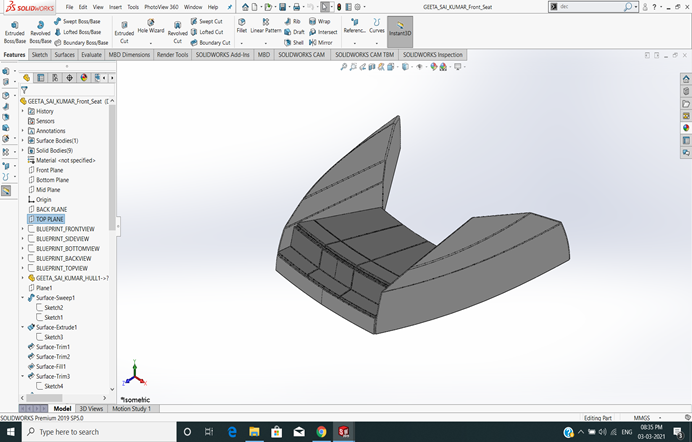
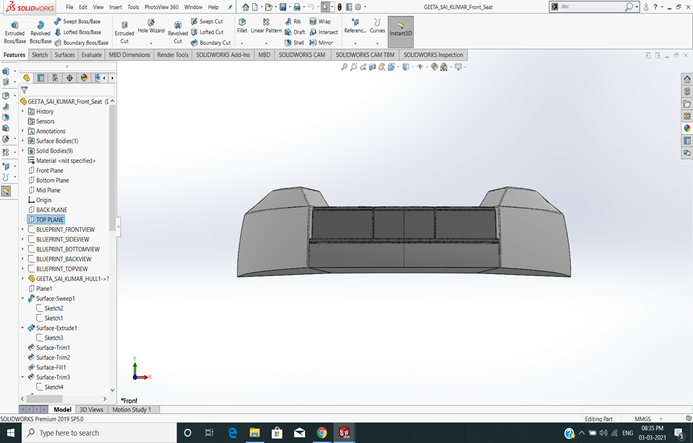
- MIDDLE SEAT:
The middle seat in our model was adjusted just behind the superstructure. It is provided with a luxury table for dining. It can also be used to have casual conversations with co-passengers.
COMMANDS USED TO MODEL
In Sketch
- Sketch Picture
- Line
- Rectangle
In Features
- Extruded Boss/Base
- Chamfer
- Fillet
- Mirror
- Reference Plane
MODELLING PROCEDURE
- The Middle Seat was created using the Extruded Boss/Base and by applying the Chamfers and fillets as wanted.
- All the surfaces created must be Knitted together by using the option Knit Surface.
- The Dining Table was created using Reference Plane, Extruded Boss/base, Off-set, Chamfers and Mirror.
- Then the other half of the Middle Seat must be mirrored symmetrically.
- At last, the part was saved by applying the proper appearances.
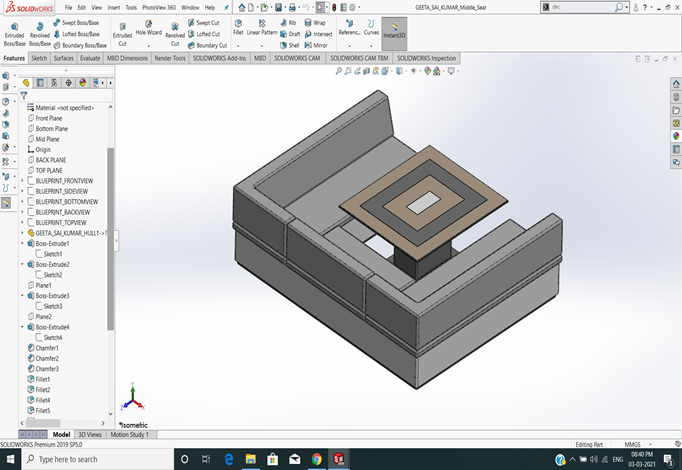
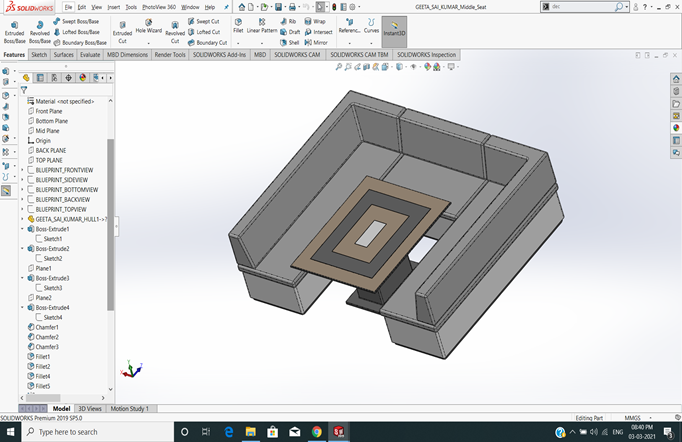
- REAR SEAT:
The rear seat was placed at the end of the deck surface. The rear seat consists of locker racks and steel doors for our stairs. The flag was also placed behind the rear seat as it’s the end part of our yacht. To have a nice view from the yacht while having a drink the rear seat was also provided with a slot to rest the glass or mug.
COMMANDS USED TO MODEL
In Sketch
- Sketch Picture
- Line
- Spline
- Circle
- Arcs
- Rectangle
In Surfaces
- Swept Surface
- Extruded Surface
- Off-set Surface
- Filled Surface
- Knit Surface
- Ruled Surface
- Lofted Surface
In Features
- Reference Plane
- Extruded Boss/Base
- Revolved Boss/Base
- Fillet
- Mirror
MODELLING PROCEDURE
- The chief body of the Rear Seat was modelled with the help of Swept Surface, Off-set Surface and the remaining portion was trimmed using Trim Surface tool.
- By using the Reference Plane, the Seats were created with the help of surface trim, lofted surface and Extended Surface.
- The Flag Post was created with the help of Revolved Boss/Base and the Flag was created by drawing the required 3D sketch and then the 3D sketches were lofted to form the Flag.
- The Tail Lamps were created using Extruded Boss/Base, mirror tool and fillets
- The Steel Gates for Stairs were designed by using the reference plane and the Swept Surface.
- To remove the gaps the all the Surfaces must be Knitted together with the help of Knit Surface.
- The required fillets and chamfer were created before mirroring the second half using Mirror tool and after mirroring the uncreated areas were filleted once more.
- Finally, the part was saved by adding suitable appearances.
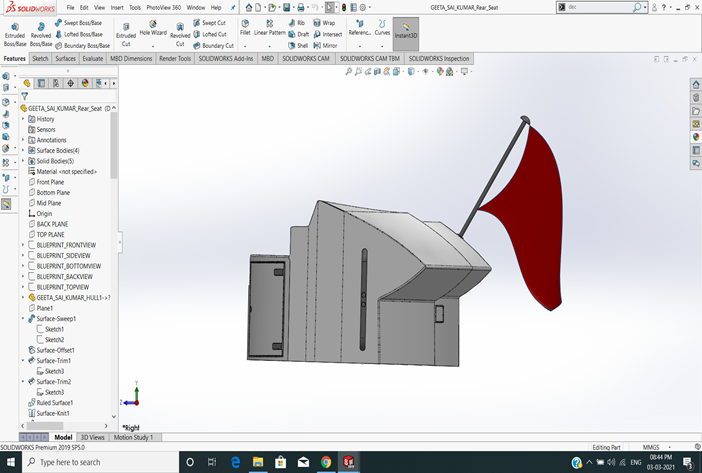
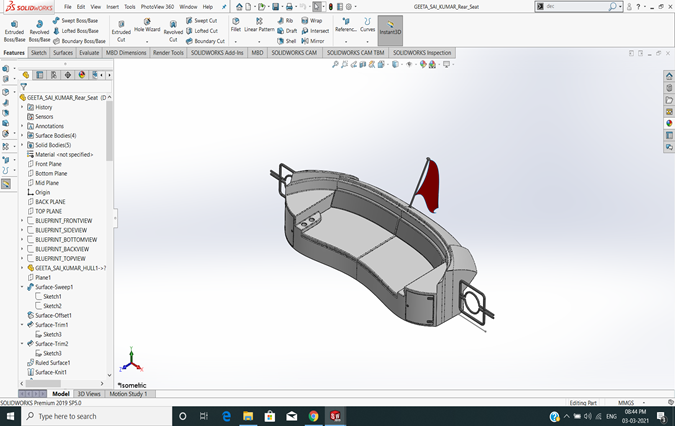
ASSEMBLY:
An assembly is a document in which features, parts, and other assemblies i.e., sub-assemblies are mated together. The parts and subassemblies existed in documents separate from the assembly. For instance, in an assembly, a piston can be mated to other parts, such as a connecting rod or cylinder. This new assembly can then be utilized as a sub-assembly in an assembly of an engine. The extension for a SolidWorks assembly file is named as SLDASM.
ASSEMBLY COMMANDS:
- Smart mate: It is an assembly mating relation that is created automatically.
- Mate: A mate is a geometric relationship, such as coincident, perpendicular, tangent, and etc, between parts in an assembly.
- Mate group: A mate group is a collection of mates that are solved together. The order in which the mates appear within the mate group is not of any significance.
- Sub-Assembly: It is an assembly document that is part of a larger assembly. For instance, the steering mechanism of a car is a subassembly of the car.
- Insert Components – One can insert multiple instances of the group of components without closing the Property Manager.
Assembly Procedure:
- Import all the parts manually using the option Insert Components.
- Next fix the Hull part by applying the coincident mate to the Top, Right and Front planes of the Assembly and Hull respectively.
- Then for each part apply the necessary mates required by the Blueprint using Coincident mates, Angle Mates, Distance mates etc.
- Advanced mate was also used wherever required.
- The final assembly of “AMERICAN CHOPPER” in the Garage was designed as my last project.

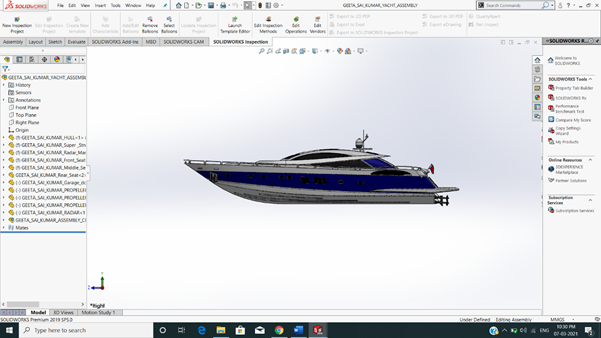
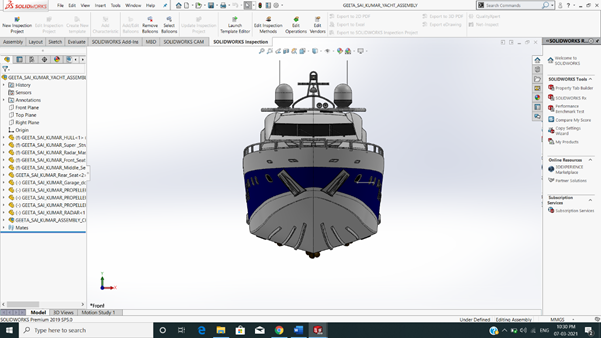
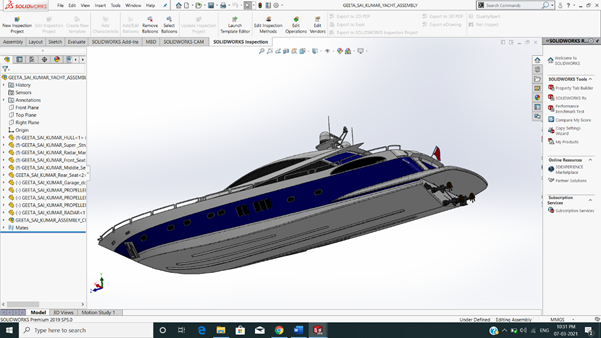
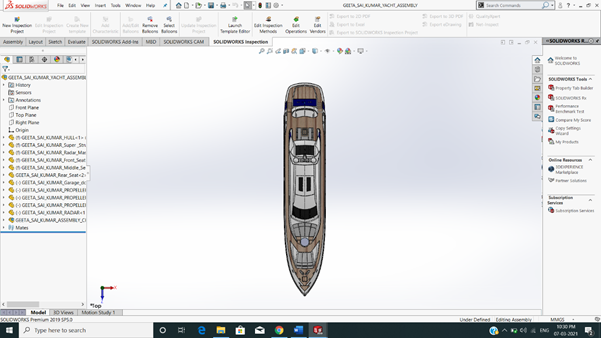
RENDERING
Rendering of the Solid works model is made using Photo View 360 and Solid works Visualize.
Photo View 360 is a visualization and rendering solution included with SOLIDWORKS. Providing a highly interactive environment for viewing designs and for creating photo-realistic renderings it can be used to showcase our designs.
SOLIDWORKS Visualize (previously known as Bunk speed) provides a suite of standalone software tools that combine industry-leading rendering capabilities with visual design-oriented features and workflows, allowing easy and fast creation of visual content that communicates a design's emotion, vision and passion.
Photo View 360
Photo View 360 is a software package, separate to Solid works, which generates digital lifelike images (photorealistic images) from SolidWorks files. Photo View 360 is an easy and quick way to produce high quality photorealistic images.
- Environments - Environments can be looked upon as backdrops and can be applied in the same manner as the appearances are applied to faces or parts
- Appearances - There are a wider range of appearances in Photo View 360 than in SolidWorks. If we want to change an appearance just drag and drop the chosen appearance onto the part and it will replace the existing one.
- Lighting - Lights may be added in the same way a photographer adds lights while taking photographs. Photo View 360 uses the exact lights as SolidWorks but also uses lighting from the rendering environment or scene. Photo View 360 has the sophistication to trace light rays and reflections.
- Scenes - Each SolidWorks model is associated with a Photo View 360 scene, for which you can specify properties such as environments and backgrounds. Scenes help to put products in context.
- Decals - Images, like company logos, can be applied to models.
- Output - The rendered output from Photo View 360 can be viewed on the screen, or saved to a graphics file.
- Options - Photo View 360 has its own options. Options allow you to customize the Photo View 360 settings to reflect your preferences. Options are classified into Output Image Settings, Render Quality, Bloom, Contour Rendering and Direct Caustics.
SOLIDWORKS Visualize
Swiftly and easily create professional, photo-quality images, animations, and other interactive 3D content to get your products to market faster.
SOLIDWORKS Visualize allows the user to leverage our 3D CAD data to create photo-quality content in the quickest and the quite easiest way we can–from images to animations, interactive web content, and immersive Virtual Reality. It brings our products to life. SOLIDWORKS Visualize is the “camera” of our CAD data.
Some renderers are fast but produce low-quality images. Some produce great quality but take six months or even more to learn. Others are very easy to use, but take four hours to render an image. SOLIDWORKS Visualize provides the right combination of quality, speed, and ease Full Animation Suite (parts, models, appearances, cameras & environments)
- Easy one-click 360-degree turntable animations make this type of output a breeze to create.
- Part/Group/Model animations for animated exploded views, sequence animation, and more to explain complex mechanical movements and detailed designs.
- Camera animations with unique Animation Ribbon, which is an intuitive 3D representation of how the camera moves through the scene, making camera fly’s a snap to create.
- Sun Study output type allows Visualize users to see what the play of light looks like across their model throughout an entire day. This is perfect for interior designers who need to see how sunlight casts shadows from their interior concept throughout a complete day sun-cycle.
Custom camera Post-Processing (camera filters)
Unleash our creativity and add additional effects to your Visualize content with customizable camera filters and the new Bloom Filter, perfect for glowing LEDs, lights and sun highlights.
Render Queue
Similar to a printer queue, stack up render jobs to send all at once, for example at the end of the day, to remain productive during work hours and allow all the renders to cook overnight. The integrated Render Queue instantly boosts productivity allowing us to never wait for a render to finish again.
Procedure for creating visualization
With its simple, instinctive user interface, SOLIDWORKS Visualize needs virtually no learning curve and lets users produce content quickly. Even amateurs can start creating amazing content instantly.
- Create new project by importing the necessary assembly or models into the Solid works Visualize
- Add the essential appearance, environments, backplates and lights
- By using the camera tool position the designed model in a realistic view
- Make sure that the model touches the floor. This can be achieved by using snap to the floor option on Models
- By applying the essential settings, the required outputs can be rendered using output tool of use and is the best render
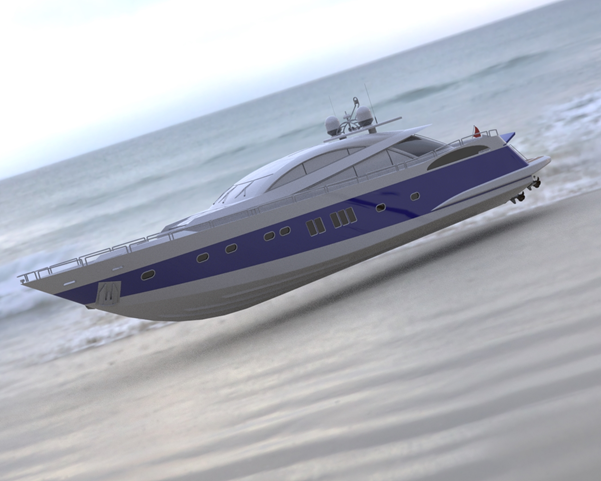
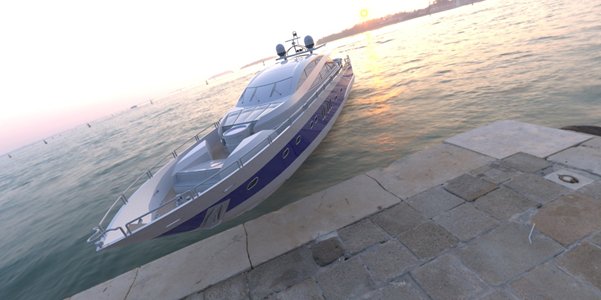





