Ultimate SOLIDWORKS Course
Title:
To model and assemble of American chopper using and solid and surface modeling in solid works.
Objective:
Drafting and designing the American chopper bike using solid works.
Introduction:
The design of the American chopper bike involves creating the individual parts initially and assembling them with proper connections and alignment.
SolidWorks: Solid works is a solid modeling CAD computer program that runs primarily on windows.
American chopper: A chopper is a type of custom motorcycle. The chopper perhaps the most extreme of all custom styles, often using radically modified steering angles and lengthened forks for a stretched-out appearance. Some features of the chopper are long front ends with extended forks often coupled with an increased rake angle, hardtail frames, very tall “ape hanger” or very short “drag” handlebars, lengthened or stretched frames, and larger than stock front wheels.
Choppers were built in America are tended to be based on Harley-Davidson motorcycles.
It is not about performance-oriented modifications, choppers are more about achieving a certain look. The main purpose of this project is to create an aesthetic model of a chopper using Solid works.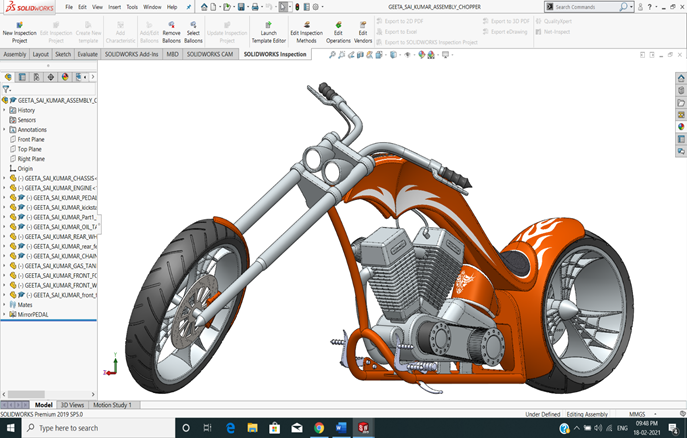
_1613751031.png)
COMMON TOOLS USED IN MODELING OF CHOPPER
- PLANE: -Here the section view of the model is to be sketched.
- SKETCH: -It gives the work base to create 2D & 3D sketches.
- 2d sketch: 2d sketch is a basic command on a sketching template. It is here where we make the sketches required to make a solid body or part. We have to select a plane from Front Plane, Top Plane, and Right plane.
- 3d sketch: In 3d sketch, we sketch on a 3dimensional space other than in a 2dimensional plane
- SMART DIMENSION: -By using this easy to provide the dimension value to the sketch to get the desired shape.
- FILLET: -It provides a round shape at the corners edges.
- CHAMFER: -It provides sloping edges at corners.
- CONVERT ENTITIES: -Using this easy to get sketched into the other plane or same plane with the same dimension value.
- OFFSET: -It Adds 3D sketches on faces.
- SHELL: - The shell tool hollows out a part to create hollow parts with thickened walls.
- EXTRUDE BOSS/BASE: -used to get a solid body in one or two directions.
- REVOLVED BOSS/BASE: -Used to revolve the sketch with the reference of axis or lines in the solid form.
- EXTRUDE CUT: -Used to remove materials from the solid body.
- SWEPT BOSS/BASE: -It proved a solid body by closed profile along an open and closed path.
- PATTERN: -It features the object in a particular direction or path.
- PROJECTED CURVE: -It combines two 2D Continuous curves into a 3D curve.
- TRIM: -It is used to cut the extra line of the surface.
- APPEARANCE: -Using this can get a different look & apply different materials.
- DECALS: - Using this tool painted stickers to be applied.
- VIEW: -Following command comes under this
- Zoom to Area
- Previously view
- Section view
- View orientation
- Display style
- Hide Item
- cameras
- lights
American Chopper Parts
- Transmission Belt
- Kickstand
- Front Fender
- Rear fender
- Oil Tank
- Chain
- Pedal
- Front Wheel
- Rear-wheel
- Front Fork
- Chassis
- Engine
- Gas Tank
Parts modeling
Transmission Belt:
A transmission belt is a loop of flexible material used to transmit power by the means of pulleys. Belts transmit power efficiently through the pulleys. They are the cheapest means used for power transmission. Advantages of the belt are noiseless working, shock absorption during work due to rubber, no lubrication required, minimal maintenance, high tolerance for misalignment.
Steps for modeling of Transmission Belt:
- Select the front plane and click on the line tool from the Sketch tab.
- Draw a line from the origin to right and in the end, draw an arc tangent to the line Previously drawn.
- From the end of the first arc draw another line towards the left and draw another arc such a way that it joins that starting point of the first line.
- Then check the sketch relations by using the symbols. Then correct the relations.
- After correcting the relations give the dimensions to each of the lines using the Smart Dimension tool.
- Then offset the original figure using the Offset Entities option.
- Now create an extrusion of the shape using Extrude Boss/Base tool from the Features tab.
- Create fillet throughout the edges of the part using the Fillet tool.
- After creating part five a matte black appearance to the part using the Appearances tool.
Tools Used in Above Process:
- Sketch
- Offset
- Extrude
- Fillet
- Appearances
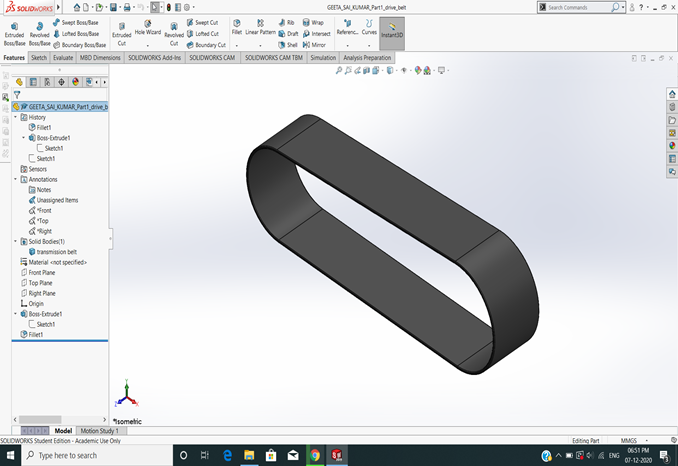
Kickstand:
The kickstand is a device used to keep the bike in an upright position. It is a metal piece that flips down to touch the ground and provides support to the bike.
Steps for Modelling Kick Stand:
- First, draw an ellipse in the front plane using the Ellipse tool and align it with the origin.
- Create a spline from the origin on the midplane using the Spline tool and give dimensions to it.
- Create a new plane normal to the spline using the Plane tool from Reference Geometry options.
- Then create another ellipse on the newly generated plane such that its center aligns with the ending of the spline.
- After that using the Lofted Boss/Base tool generate a solid by clicking on the two ellipses and then using Centreline Parameters to make the solid align with the spline.
- Then make 2 domes on either side of the part using the Dome feature from the Features tab in the given dimensions.
- Now on one side make an extruded cut by drawing a rectangle on the Mid Plane and then extruding it by Through All-Both options.
- After that draw a line on the plane that was created previously using the Midpoint Line tool and align it horizontally and vertically with the origin.
- Then using the Split features from the Features tab slice of a small piece of the part.
- Now using Extruded Boss/Base tool extrude a circle that is drawn on the Top plane by selecting the Up to Next option for both directions.
- After that for creating fillets on the parts, select the Fillet tool and click on the edges where the fillets have to be made.
- Finally, a chrome appearance is given to the part using the Appearances tab.
Tools Used in Above Process:
- 2d sketch
- ellipse
- spline
- pierce
- loft
- cut extrude
- Boss extrudes
- split
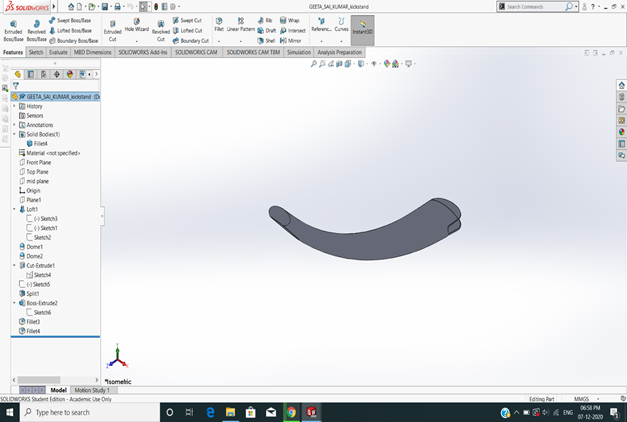
Front Fender:
Front Fender is a part of the automobile that covers the front wheel. The fender's function is to contain the various material such as stones, mud, liquids on the roads which otherwise would have sprayed themselves onto the inside of the car or the pedestrian behind the car. The front fender is used as the front-wheel cover. The fender is also known as a mudguard.
Steps for Modelling Front Fender:
- Draw a 3-Point arc in the Front Plane using the 3 Point Arc tool from Sketching Tab with the given dimensions.
- Then make offset arc inward using the Offset Entities tool from Sketch Tab.
- Join the two arcs using the line tool and Trim Entities.
- After that drawn line from the center on the same plane and make it is one end vertical to one end of the arc.
- By using the Revolve tool revolve the Shape to create a front fender part.
- To give an appearance using the appearance tool and then select Siena from the Plastic tool.
- Now draw another arc in the Top plane on either side of a line drawn from the origin using the Dynamic Mirror tool and select the Split tool from the features list and then trim the part that is not needed.
- Similarly, draw another arc on the Front Plane and the using Split tool remove the remaining material.
- By using the fillet tool round the edges of the part for smooth-looking and to remove sharp edges.
Tools used in the above modeling:
- 2d sketch
- 3-point arc
- offset
- Extend
- Trim
- Revolve
- spline
- Fillet
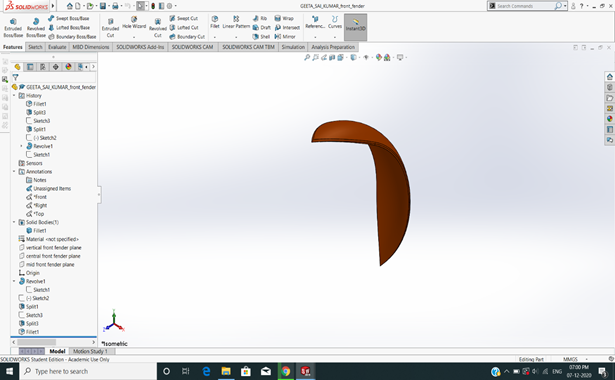
Rear Fender:
Rear Fender is part of automobiles that frames the Rear wheel. The fender's purpose is to contain the various material such as stones, mud, liquids on the roads which otherwise would have sprayed themselves onto the inside of the car or the pedestrian behind the car. The rear fender is used for the rear wheel. The fender is also known as a mudguard.
Steps for Modelling Rear Fender:
- Draw a 3-Point arc on the Front Plane using the 3 Point Arc tool from Sketch Tab with the given dimensions.
- Then offset arc inward using the Offset Entities tool from Sketch Tab.
- Join the two arcs using the line tool and trim extra Entities.
- After that drawn line from the center on the same plane and make it is one end vertical to one end of the arc.
- By using the Revolve tool revolve the Shape to create a rear fender part.
- To give an appearance using the appearance tool and then select Siena from the Plastic tool.
- Now draw another arc in the Top plane and select the Split tool from the features list and then trim the part that is not needed.
- By using the fillet tool round the sharp edges.
Tools used for the above model:
- 2d sketch
- 3-point arc
- Extend
- Trim
- Revolve
- spline
- Fillet
- Shell
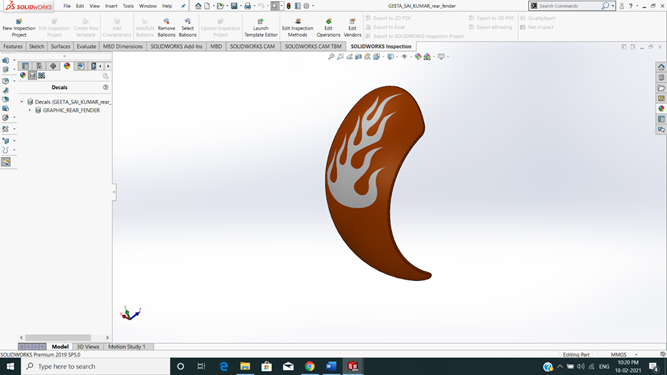
Oil Tank:
An oil tank or fuel tank (also called a petrol tank or gas tank) features a safe container for flammable fluids. Any storage tank for a flammable fuel may be so-called, the term is typically applied to part of an engine system in which the fuel is stored and supplied or propelled (fuel pump) or released (pressurized gas) into an engine.
Steps for modeling oil tank:
- Draw a horizontal line on Top Plane. draw two lines from both ends of the first line. After that draw a 3-point arc connecting the two lines.
- Extrude the figure using Extruded Boss/Base tool.
- Now draw another sketch of a quadrilateral on the Midplane and then extrude that too with through all feature turned on.
- Then using the combine tool combines both the extrusions to make a single piece.
- After that give fillets to the body using the fillet tool.
- To give a hollowness use the shell tool.
- To change the appearance of a body as well as the fillet use the appearance menu.
Tools used for the above modeling:
- Lines
- 3-point arc
- Boss Extrude
- Combine
- Fillet
- Shell
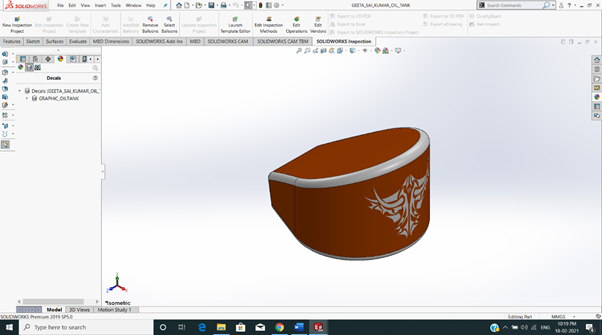
Chain:
The Chain drive is used to transfer power from one place to another, similar to a transmission belt. A chain drive is a positive drive motion since there is no slippage between the belt and gear. Drives are made of metal, followed by plastic and rubber. They are very efficient in power transmission. Lubrication is important since the drives wear out quickly without proper lubrication. Chain drives suffer from speed controlling since the drives are made from metal, they have significant self-weight which gives rise to inertia during rotation. Hence special care has to be taken to avoid such situations, which in turn will reduce the chances of vibration and increase the life of the chain drive. In most cases, either the shafts accelerated and deaccelerated accordingly, or the sprocket is speed controlled. Sometimes Chains are often narrower than belts, and this can make it easier to shift them to larger or smaller gears by varying the gear ratio. Multi-speed bicycles with derailleurs make use of this. The more positive meshing of a chain makes it easier to build gears so they can increase or shrink in diameter, by altering the gear ratio.
Steps for modeling Chain:
- Start sketching on the midplane by drawing two circles and connecting them by line. Then remove the unwanted lines using the Trim Entities tool.
- After that in the same plane draw the two-chain links and save them as blocks.
- By using the Insert Block tool add the links and extrude them and give fillets to each pin so it is created. Then to copy the parts through the lines use the Curve Driven Pattern tool and then select the lines to need.
- After that select all the pins parts from the Solid Bodies sub menu and add them to a folder.
- By using the mirror option create the joints on the other side of the plane.
- Now to change the appearance using the appearance tool and then finally save the project.
Tools used in the above modeling:
- 2d sketch
- circles
- 3point arc
- Slot
- Block
- Fillet
- Curve Pattern
- Mirror
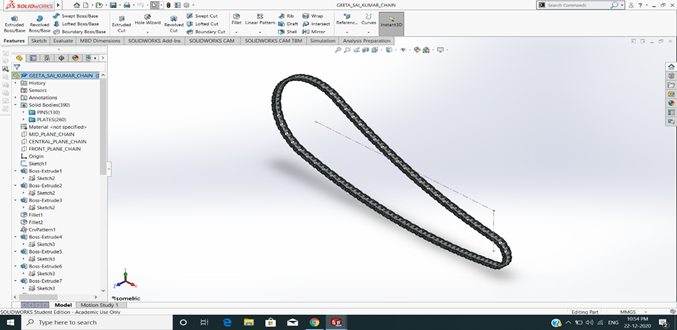
Foot Pedal/Pegs:
Footpegs can be developed or manufactured from a variety of materials; some are made from aluminum, steel, and also titanium. Some of them are stamped, cast, mechanized, or forged form. Most of the above footpegs are both heats treated, or they are anodized. We have main facets of footpegs that aa the charge of mud retention. These are draft, thickness, nooks, and crannies. Let us seem to be at each of them and how it influences mud retention.
Draft- when a footpeg has a fantastic draft it virtually potential that the lower opening is better than the one at the top. This implies that we are probable to experience minimal mud traps.
Thickness- normal foot pegs normally make use of extra manufacture material, this in most instances creates deeper cavities that lure a lot of mud. On the different hand, super-thin foot pegs best in seasoned circuit units. They are most desired here they are magnificent skinny and they, therefore, don’t supply any room for mud to be trapped.
Nooks and crannies- simplified difficult and crossbeams footpegs do not entice any mud as antagonistic to their different counterparts
Steps for modeling Foot Pedal/Pegs:
- Sketch the given shape using the given geometry on the Front plane using various tools like Line, Circle, and Spline Tools.
- Extrude the shape to a given distance. Now extrude the two smaller circles on one side to a particular distance.
- Now fillet the first piece that we have created. After that draw a sketch on the top plane using construction line and normal line.
- Then Revolve that shape for the construction line.
- Now Create a dome over that revolved part using the Dome tool from the features list for appearance.
- Now fillet the dome edges and the small circle extrusions that were previously created.
- Then Extrude the other two circles on the same side as that of the revolved extrusion.
- Now give Chamfer to both the newly created extrusions using the Chamfer tool.
- Draw an offset sketch of the outer edges of the newly created extrude on the Front Plane and then extrude it with an offset.
- Now add a fillet to it and using the Linear Pattern method copy the extrusions across the parts.
- Finally, give fillets to where ever necessary.
Tools used for the above Modelling:
- 2d sketch
- Lines
- Circles
- Fillets
- Revolve
- Dome
- Chamfer
- Linear Pattern
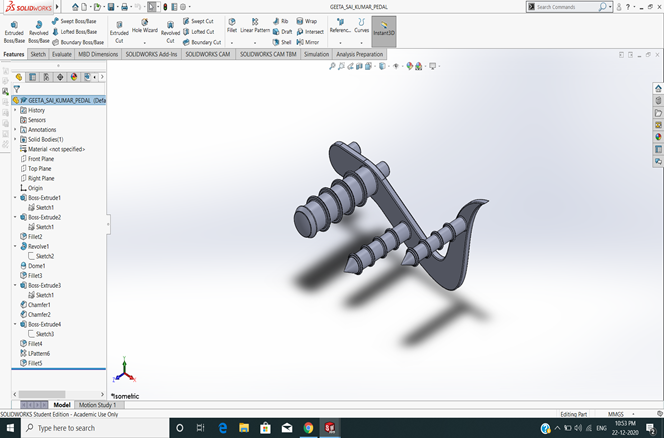
Front-wheel:
A wheel may be a circular block of a tough and sturdy material at whose center has been bored a circular hole through that is placed Associate in Nursing shaft bearing concerning that the wheel rotates when torque is applied along its axis. When placed vertically below its supporting platform or case, the wheel turning on the horizontal shaft makes it doable to move significant loads. once placed horizontally, the wheel turning on its vertical shaft makes it doable to regulate the spinning motion accustomed form materials (e.g. a potter's wheel); once mounted on a column connected to a rudder or a chassis mounted on different wheels, one will manage the direction of a vessel or vehicle (e.g. a ship's wheel or steering wheel); once connected to a crank or engine, a wheel will store, release, or transmit energy
Steps for modeling Front wheel:
- Start sketching on the front plane and draw two shapes on the plane -one for the rim and the other for the center part and revolve it.
- Now on the Right plane. sketch, the shape of the spoke using the Spline and Line tools, and then extrude it.
- After that draw another sketch on the same plane and use the extrude cut tool to create cuts in the shape that is created.
- Now draw another sketch on the same plane to make a web-like structure that has to be extruded using the Extrude Boss/Base tool.
- Now start sketching on the Front Plane to cut some parts of the spokes and the center part of the wheel.
- By using the Circular Pattern tool to create the same spokes throughout the wheel.
- Combine the spokes and the center part using the combine tool.
- Give fillets to the combined part using the Fillet tool.
- Now for creating the disc, we have to draw a circle on the Right plane and then extrude with the offset option turned on.
- To give holes to the disc, sketch the Right plane and then the Extrude Cut as selected.
- By using the Circular Pattern tool copy the Extrude cuts throughout the disc.
- Draw another sketch on the same plane and use Extrude Cut option as selected and then fillet is created for the cut. And use a circular pattern.
- A hole is created in the disc as well as the Centre part by drawing a circle on the right plane and by selecting the extrude cut option.
- Caliper sketch is created on the Right plane and extruding it. Chamfers are given on both the faces of the caliper.
- Now various fillets are given.
- The sketch is drawn on the Front Plane at a particular distance from the origin and is then revolved.
- For threads on the tire, Thread patterns are drawn using the Rectangle Tool on the Front Plane and the using Extrude cut material is removed to make the pattern.
- Fillets are given to the inner edge of the pattern and using the Circular Pattern tool the threads are copied throughout the surface of the tire.
- Appearances are given to different parts using the Appearance tool
Tools used for the above modeling:
- 2d sketch
- Straight lines
- 3-point arc
- sketch fillet
- revolve
- spline
- extend
- trim
- cut extrude
- offset
- cut revolve
- circular pattern
- chamfer
- fillet
- corner center point rectangle

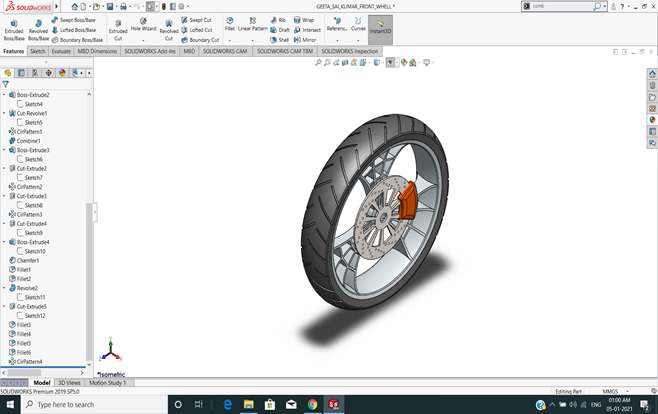
Rear Wheel:
A wheel may be a circular block of a tough and sturdy material at whose center has been bored a circular hole through that is placed Associate in Nursing shaft bearing concerning that the wheel rotates when torque is applied along its axis. When placed vertically below its supporting platform or case, the wheel turning on the horizontal shaft makes it doable to move significant loads. once placed horizontally, the wheel turning on its vertical shaft makes it doable to regulate the spinning motion accustomed form materials (e.g. a potter's wheel); once mounted on a column connected to a rudder or a chassis mounted on different wheels, one will manage the direction of a vessel or vehicle (e.g. a ship's wheel or steering wheel); once connected to a crank or engine, a wheel will store, release, or transmit energy
Steps for modeling Rear Wheel:
- Sketch on the front plane so that it can be revolved at a particular axis to form the rim of the rear wheel and the shaft of the rear wheel.
- On the right plane draw an arc using the 3 Point arc tool and make a shape and then it is extruded at a particular distance from the middle towards either side of the plane.
- sketch on the right plane using drawing tools and then using the Extruded cut option to make spokes for the rim.
- Then draw a sketch that connects the spokes on the same plane and extrudes them.
- Use the Circular Pattern tool to select the spoke that was made previously and then by selecting an axis to make spoke throughout the rim.
- After that combine all the parts (rim, spokes, and the shaft).
- Sketch on the front plane by selecting the intersection curve option on the rim for that plane. Now draw a shape so that it can be used to extrude cut a certain number of materials from the spokes and the shaft.
- Fillet the spokes and other parts that are created till now.
- At the center of the rim draw a small circle on the right plane and then use the extrude cut option.
- Then draw another sketch on the front plane and is then revolved to create the part that forms the shaft.
- Draw another circle on the right plane and then extrude it with an offset. And this forms the disc for the brakes and to make holes another shape is drawn on the plane of the disc. By using the linear pattern option make patterns of them at a particular angle. Now extrude cut all 4 of them.
- By using the circular pattern tool create the same holes throughout the disc.
- Then sketch the same disc plane and using the circular pattern tool make copies of it throughout the disc.
- Fillets are given to the parts that are created above.
- Now on the right plane sketch, the caliper and is extruded. Then Chamfers are given to either side of the chamfer.
- Fillets are given to certain edges of the caliper.
- To make the sprocket for the chain a circle is drawn on the right plane and is extruded, and give chamfers on the edges.
- Now another sketch is drawn on the plane of the sprocket to create the cut for the gear and each of the cuts is copied throughout the part using the circular pattern option.
- Another pattern is drawn and extruded on the same plane to create a design on the sprocket.
- Again, the fillets are given to the sprocket.
- A sketch is drawn on the front plane and is then revolved using the revolved boss tool.
- For making threads to the tire shapes are drawn on the front plane and are then extruded and the fillet is applied.
- Using the circular pattern tool, the thread is made to spread throughout the tire.
- Appearances are given to each part using the Appearances tool in the feature tab.
Tools used for the above Modelling:
- 2d sketch
- Straight lines
- 3-point arc
- sketch fillet
- revolve
- spline
- extend
- trim
- cut extrude:
- offset
- cut revolve
- circular pattern
- chamfer
- fillet
- corner center point rectangle
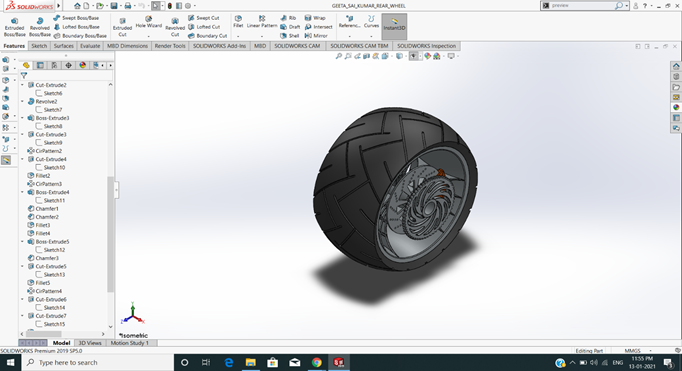
Front Fork:
Front Fork connects the front wheel and axle to the rest of the frame. The yoke is one of the main parts of the front fork. The front fork contains a front brake and front suspension.
The fork establishes the critical geometric parameters of rake and trail, which play a major role in defining how a motorcycle handles and dives during braking. The standard telescopic fork arrangement is found In mainstream street motorcycles since the 1970s, historically there have been many variations, including trailing or leading link, springer, Earless, girder, and others, as well as non-fork steering such as hub-center steering.
Steps for modeling Front Fork:
- Sketch the fork on the front plane and then revolving it.
- Sketch on the right plane and then extrude it. Now fillets are given to different edges.
- By using the Linear pattern tool make a copy of the part.
- Draw a circle sketch on the front plane to make an extrude that joins the ends of the fork.
- After that draw another sketch on the part that was previously created and is then extruded to connect the copies of the part.
- Then a sketch is drawn on the front plane that can be revolved to make the headlamp of the motorcycle.
- Sketch on the part to make a small extrude for the lights and fillets are given on the edges.
- For creating the bulb-like shapes to the light, a dome is created on the extruded surface.
- Again, certain fillets are applied, and then a sketch is created on the front plane to create a chamfer on the inside of the headlight.
- By using the Body Move option the light is moved to a particular distance and angle.
- The curve is drawn using the spline tool on the front plane and another spline also. By using the projected curve option, a curve is obtained.
- A circle is drawn on the handle joints and is used for creating the handles of the chopper bike by Sweeping through the projected curve from the circle.
- Create a New plane. On that, a sketch is drawn on the end of the handle.
- The sketch is drawn on the newly created plane and is then revolve cut.
- Another sketch is made on the top plane and revolved over the handle.
- A new plane is created on the handle to sketch the brake lever.
- The sketch is extruded and the fillet is applied.
- By using the projected curves tool, the brake cables are created by drawing splines and a circle that is swept to form the cable.
- Whole parts are mirrored about the face of the handle joint.
- Parts are combined using the combine tool and each of the parts is given its appearances using the Appearance tool.
Tools used for the above model:
- 2d sketch
- Straight Lines
- Revolve
- circle
- Fillets
- Linear Pattern
- spline
- Cut Extrude
- Dome
- Move Body
- Curve
- sweep
- plane
- mirror
- combine
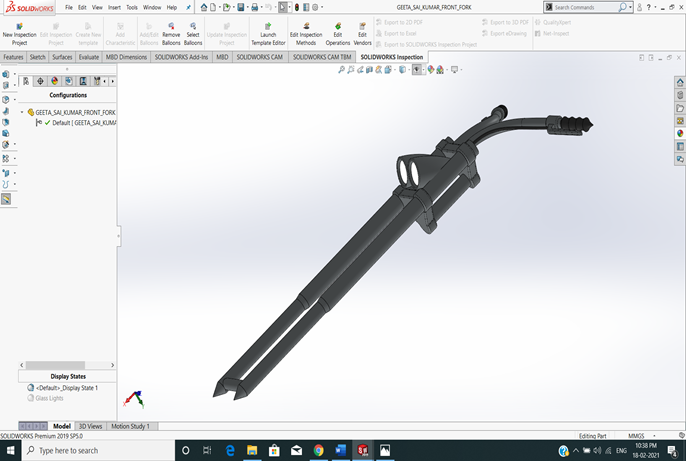
Chassis:
A chassis is the load-bearing framework of an artificial object, which structurally supports the object in its construction and function. An example of a chassis is a vehicle frame, the underpart of a motor vehicle, on which the body is mounted; if the running gear such as wheels and transmission, and sometimes even the driver's seat, are included, then the assembly is described as a rolling chassis.it is also known as the backbone of the Bike.
Steps to model Chassis:
- Add the blueprints to the sketch picture In the midplane.
- Draw curves on both the Bottom plane and the midplane and by using the projected curve tool to make a projected curve.
- Draw, another sketch on the right plane and again using the projected curve make a curve.
- By using the swept boss tool sweep a body through the curve and a sketch is created on the midplane.
- We use the mirror option to make copies of the part over the midplane.
- Create a sketch on the Right plane and extrude it.
- Sketch the part created and use extrude cut option to remove some material from the part.
- After that, a small chamfer is given to one edge of the part and various fillets are given to some edges using the fillet tool.
- A plane is created using a Reference geometry option and then draw a sketch of two concentric circles on the plane and also draw a curve on the midplane curve. Use the sweep tool to make a part.
- Using the split tool cut the part at the end.
- Create another sketch on the bottom plane and draw another sketch on it and also draw a curve on the midplane. After that using the sweep option makes a swept part.
- Use the split option to remove certain material from the part.
- Now combine all the parts that are created till now.
- Sketch on the midplane and use revolve boss option to create a revolved part.
- Again, using the split tool removes some parts.
- Once more the combined tool is used and the whole parts are combined.
- Sketch on the Midplane and extruded with the merge option turned on.
- After that various fillets are given.
- The sketch is drawn on the midplane and extruded to make a part.
- A split tool is given to remove some material.
- Fillets are given and by using the mirror feature, copy the part for fitting the kickstand and the brake lever on either side of the midplane.
- Draw a sketch on the right plane and then it is extruded and filets are applied.
- A sketch is drawn on the surface of the part that is created above and cut extruded and then appearance is given to the whole part using the appearance tool.
Tools used for modeling chassis:
- sketch pictures
- splines
- curves
- mirror
- boss extrudes
- cut extrude
- chamfer
- dome
- split
- revolve
- combine
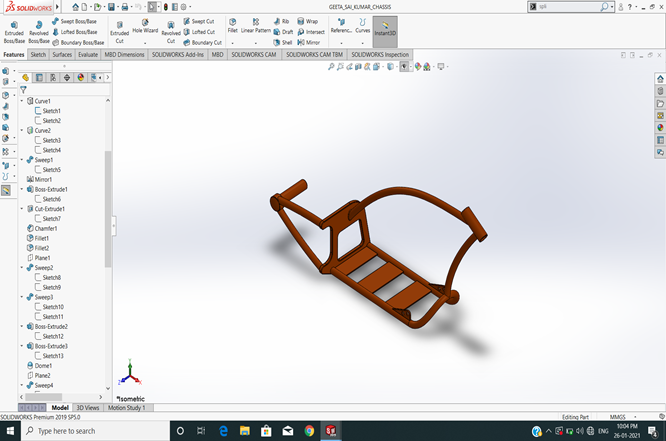
Engine:
An engine or motor is a machine designed to convert one form of energy into mechanical energy which turns a crankshaft.
More recently, some have automatic or semi-automatic gearboxes
Steps for modeling Engine:
- Blueprints of the motorcycle are added to the front plane.
- The sketch is drawn on the front plane and is then extruded and fillets are given.
- The sketch is drawn on the right plane and revolved to make a part.
- Then make a new plane concerning the right plane and draw a sketch on the plane and revolve.
- After that sketch the front plane and extrude.
- By using the circular patter option teeth for the chain are made.
- Do the same on the other sprocket.
- Create domes on the parts that are created recently.
- Then a sketch is drawn on the front plane and is cut extruded to make holes on the sprocket. The same steps are done on the other sprocket too.
- Now fillets and chamfer are given to the parts.
- The sketch is drawn on the front plane and then extruded. The sketches are drawn on the same plane to make a connecting part.
- Then a new sketch is drawn on the front plane and a new plane is created concerning the sketch that is drawn.
- The sketch is drawn on the newly created plane and is then extruded.
- Fillets and chamfers are given.
- The sketch is drawn on the same new plane and is then cut extruded to create a shape.
- To copy the shape the linear pattern option is used.
- After that various fillets are applied.
- The sketch is drawn on the cylinder that is created and then extruded outward and a dome is given.
- The shape is mirrored on either side of the cylinder.
- The sketch is drawn on the front plane and extruded and fillets are applied.
- By using the split option, some parts are removed.
- Copy the cylinder on to other side using the mirror tool.
- Now some fillets are given to the edges.
- New sketches are drawn on the top plane and extruded and some fillets are given.
- Sketches are drawn on the front plane and extruded and chamfered.
- The sketch is drawn on the sprocket and extrude cut and the fillet is given.
- By using the circular pattern option copy and cut throughout the sprocket.
- Again, some chamfers are given.
- The sketch is drawn on the front plane and one on the right plane.
- By using the sweep tool make the exhaust tube.
- After that, the tube is mirrored.
- Now all the made parts are combined.
- A new plane is created concerning the top plane.
- The sketch is drawn on the front plane and a curve is drawn previously. This sketch is used to make a swept part.
- The sketch is drawn on the front plane and revolved to make an air intake.
- Various filets are applied to the part.
- The sketch is drawn on the top plane and is then cut extruded and by using the circular pattern tool the cut is copied throughout the part.
- For the exhaust tube, four curves are drawn on two different planes, by using the projected curves option make a curve and using the swept option make a sweeping part.
- Similarly, make another part using the same procedure.
- The sketch is drawn on the top plane so that it can cut the exhaust tip using the split tool.
- Then sketch the face of the spark plug and another curve on the front plane so that it can be used to make the wire for the spark plug.
- Similarly, make the same wire on the other spark plug using the same procedure as above.
Tools used for modeling Engine:
- 2d sketch
- sketch pictures
- straight lines
- circles
- boss extrudes
- fillet
- revolve
- plane
- dome
- circular pattern
- chamfer
- linear pattern
- mirror
- cut extrude
- combine
- mirror
- curve
- composite curve
- spilt
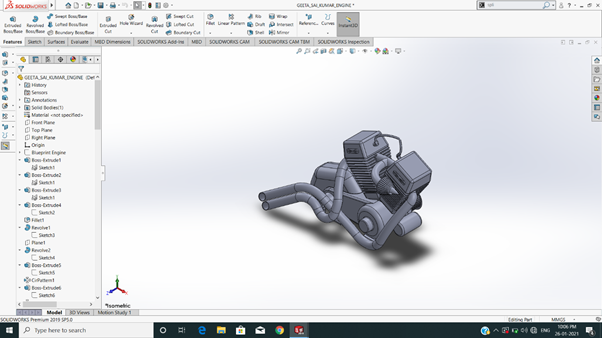
Gas Tank:
A gas tank (or petrol tank) is a protected container for flammable fluids. Though any storage tank for gasoline may additionally be so-called, the period is generally utilized to a section of an engine machine in which the gas is saved and propelled or launched into an engine. Fuel tanks vary in measurement and complexity from the small plastic tank of a butane lighter to the multi-chambered cryogenic Space Shuttle exterior tank.
Steps used for modeling Gas Tank:
- First, the Underlay image of the chopper is added to the midplane.
- Then a plane is created concerning the front plane.
- After that, a sketch is newly created on the midplane and is used to create a swept surface using the Sweep Surface tool.
- Now another sketch is drawn on the Bottom plane and is used to trim certain material using the Surface Trim option.
- Then another plane is created concerning the Midplane and a sketch is drawn.
- Again, make another plane and draw a sketch. Sketch another plane that was created previously and using the two sketches make a projected curve.
- Sketch on the plane that was created previously and using the Surface Loft tool make a surface loft.
- Now make another plane concerning the front plane and draw a sketch. Sketch on the Bottom plane and these two sketches are used to create a projected curve.
- For creating a boundary surface draw two sketches on the midplane and then using the Surface Boundary tool to make it.
- By using the mirror tool make a mirrored version of the part over the midplane.
- By using the surface knit option knit all the surfaces.
- Then for making the seat sketch the Bottom plane and the split line option are used to combine with the gas tank body.
- By using the surface extrude seat is generated.
- Later some fillets are given to the seats.
- Again, the boundary surface is created for the seat.
- Now a surface loft is made at the bottom of the gas tank using the loft option from the surface window.
- By using the surface knit option knit all the surfaces.
- After that, some fillets are applied.
- Now draw a sketch on the midplane as well as on the plane that was created concerning the front plane and using the cut sweep option cut the part.
- Fillets are applied and the whole part is made into a shell.
- After that, appearances are given to the part and the seat separately.
Tools used for modeling Gas Tank:
- 2d sketch
- spline
- surface sweep
- surface trim
- surface boundary
- surface loft
- curve
- mirror
- surface knit
- surface extrudes
- fillet
- cut extrude
- shell
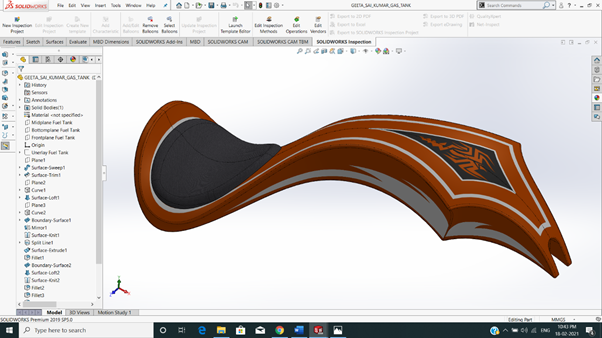
ASSEMBLY OF CHOPPER
Assembly:
All the above individual parts are assembled with appropriate joint features to form the final output of the American chopper bike as shown below using the features
- inserts parts
- mates
1.Insert part is used for bringing in the part models which we designed individually into the assembly so that the part can be assembled and rendered.
2.mates are used to create relations in between the part models so that they act as a combined part and work as desired and lock the movement in the desired position. And to fully define the part model.
Steps for assembling the part models of the chopper:
- All the parts are added that are created in the SolidWorks software and keep them open and then start assembling by creating a new assembly file.
- By using the insert component option chassis is added to the window and then make it coincident mate using the mate option for the midplane and the front plane of the assembly.
- After that add the engine and make its bottom stand coincident with the flat bottom surface of the chassis. Then make a distance relationship between the front surface of the bottom stand and the front surface of the holding part of the chassis.
- Now add the pedal to the window and make its two cylinders concentric with the holes given on the chassis and make its one side coincident with the chassis. After that, the pedal is mirrored on the other side of the chassis.
- Now kickstand is added to the window and make its inner surface coincident with the outer surface of the part that is on the chassis.
- Now give a concentric mate to the kickstand and the chassis.
- To limit the movement of the kickstand a limit angle is given to the kickstand concerning the chassis.
- Then the transmission belt is added and a width mate is given to it concerning the engine and also a concentric mate is given to it.
- After that, an angle is given to the transmission so that it stays fixed.
- Now oil tank is added and coincident relation between its face and the face of the engine near the seat is given. Again, a coincident relation is given to the edge of the tank and the surface of the engine.
- Then another coincident relation is given concerning the midplane of the tank and the chassis.
- The rear wheel is added and given a concentric relation between the chassis and the wheel. Now a coincident relation is also given between the midplanes of the chassis and the wheel.
- For fixing the position parallel relation is given between the front plane and the side of the chassis just after the wheel.
- The rear fender is added and made concentric with the disc of the rear wheel. And a coincident relation is added to the midplanes of the rear fender and the chassis.
- After that, a parallel relation is given to the front plane of the rear fender and the side of the chassis.
- The chain is added and given a width relation between the one side of the chain-link and one side of the sprocket.
- Now the other side of the chain is fixed using the parallel relation between them.
- Then the gas tank is added and is given a distance relation between its front plane and the front plane of the chassis.
- After that, some coincident relations are given to align with the chassis of the chopper.
- The front fork is added and given a concentric relation between its axis and the chassis to fix it.
- After that, a width relation is given to the two surfaces of the fork and the chassis.
- The angle of tilt is limited using the angle relation between the plane of the fork and the chassis to prevent over-rotating.
- After that, a parallel relation is given to the chassis and the fork so that whenever we want, we can position it in a straight position.
- The front wheel is added and given a concentric relation between the fork and the front wheel.
- The front wheel is given a coincident relation between the planes of the wheel and the fork.
- The front fender is added and given a coincident relation between various planes of the fender and the fork to position it.
- Rebuild the chopper to update any change and save the file.
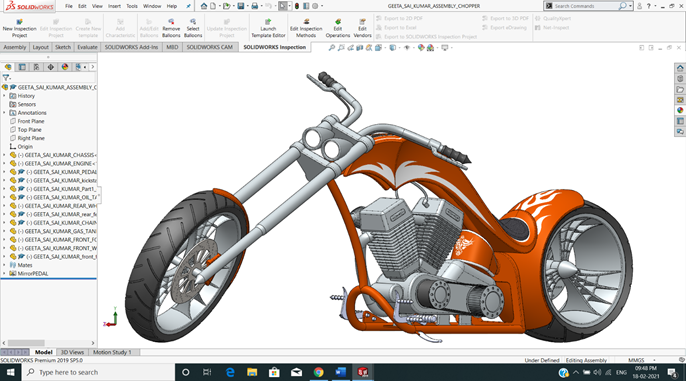
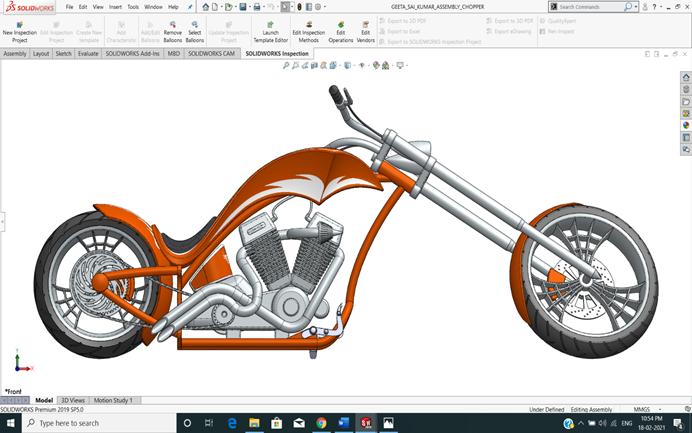
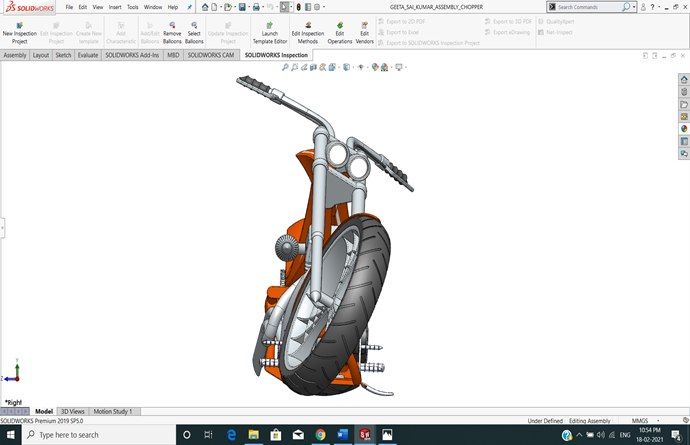
Rendering:
get the realistic viewing effect using photoview360 or SOLIDWORKS Visualize. where we can adjust the viewing direction using the camera option and place the model in a realistic environment and render the image to get the real-life viewing angles and shadows, etc...
- Environment
- Decals
- Lights and Cameras.
- Snapshots.
- Plates
- Textures
- Render preview window.
- Final Render.
Environment: In this, we use HDR images to generate rendering it is a type of real environment in which shadows of the environment are projected onto the model. To create a real-life image.
Decals: It is used to create labels or logos on the part to make it look like a laser-cut logo.
Lights and Cameras: these are used to capture the view and Lights are used to increase lighting and to create artificial sunlight.
Render preview window: It is used to view the rendered image before doing the final rendering as final rendering takes so much time.
Final Rendering: when we think of the rendering, the preview is ok and giving a good result we use the final render to generate a high-quality image.
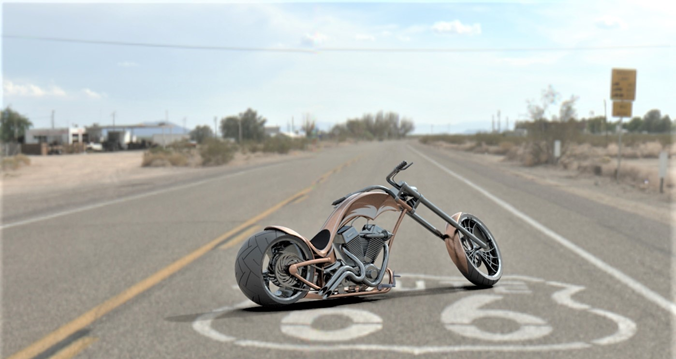
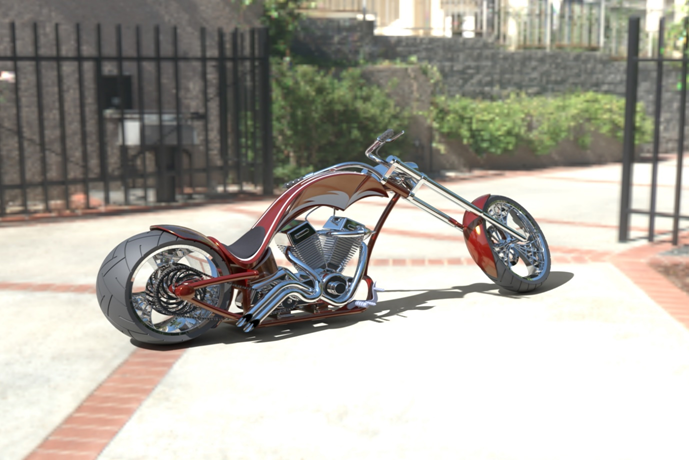
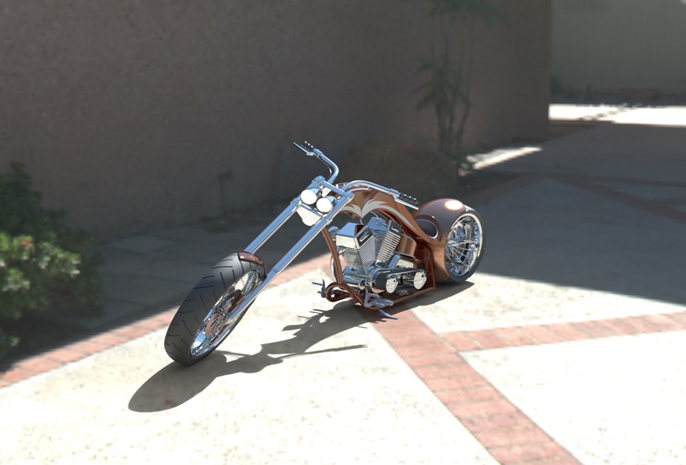
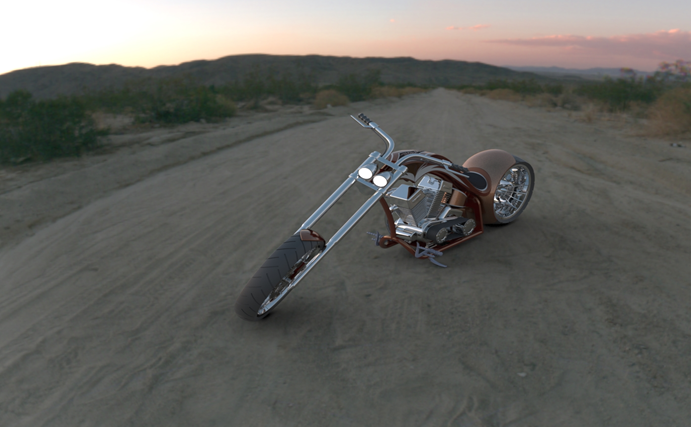
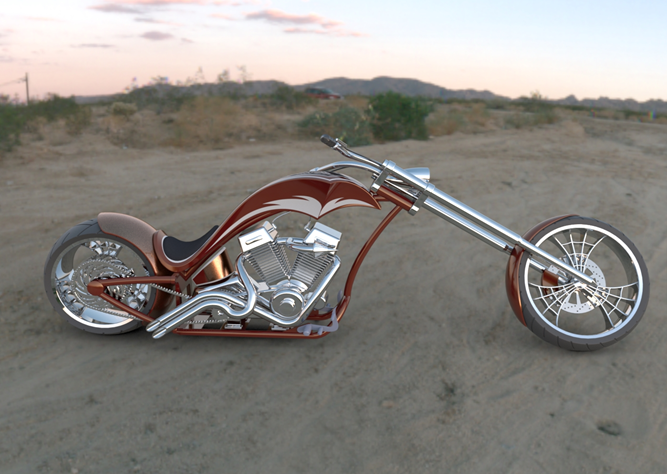
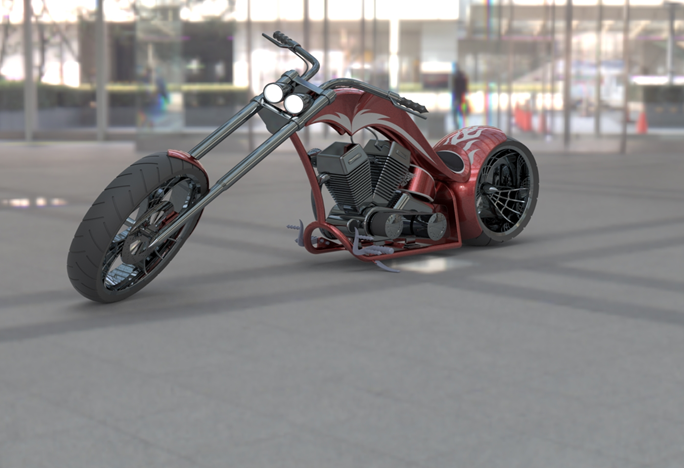
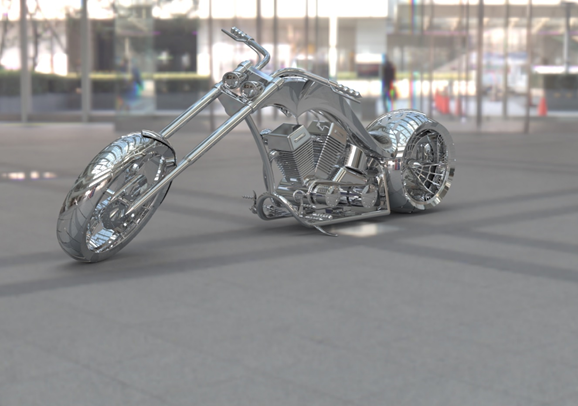
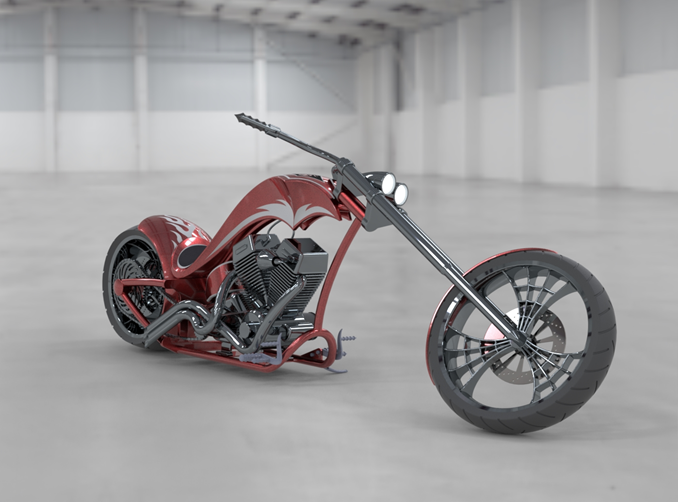
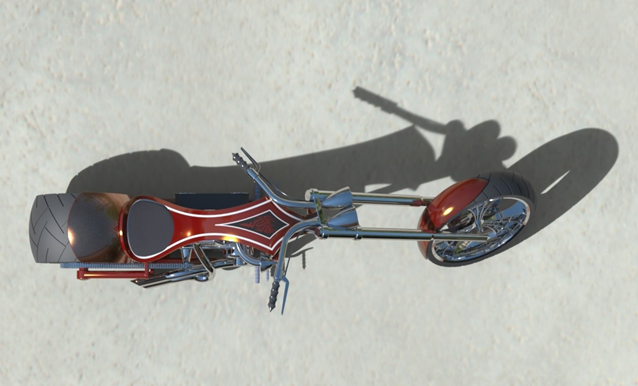
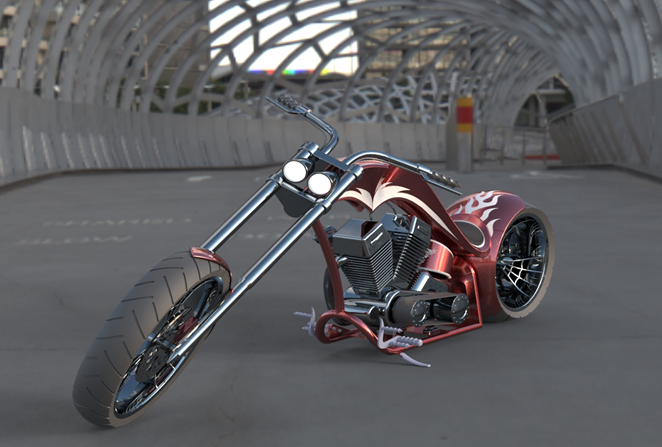