DOOR ARM REST DESIGN FROM CLASS A - AUTOMOTIVE PLASTIC COMPONENT
OBJECTIVE:
This report demonstrates the design of a Door Arm Rest an Automotive Plastic Component using industry principles such as Draft angles, Draft Analysis, Determining and implementing of Tooling Axis, Class A, Class B, Class C surfaces and Maintaining the Thickness of the part at 2.5mm. The component is designed using Surface Design and Solid Design techniques in CAD package CATIA V5.
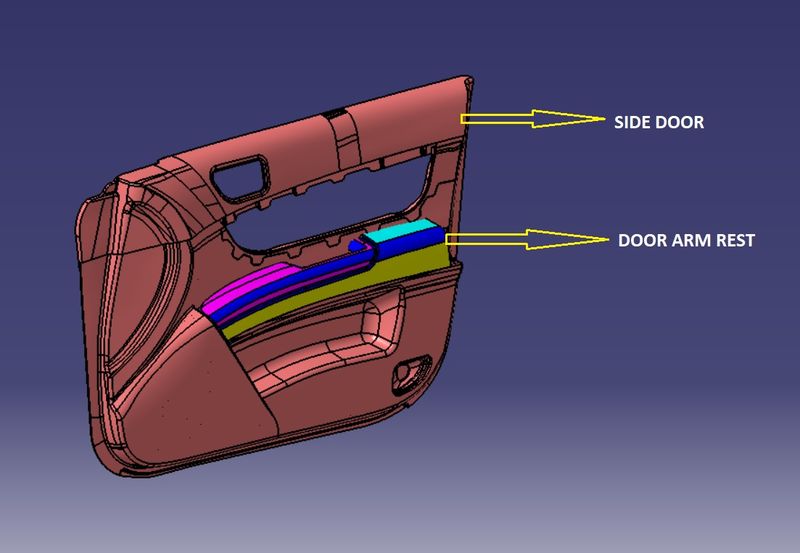
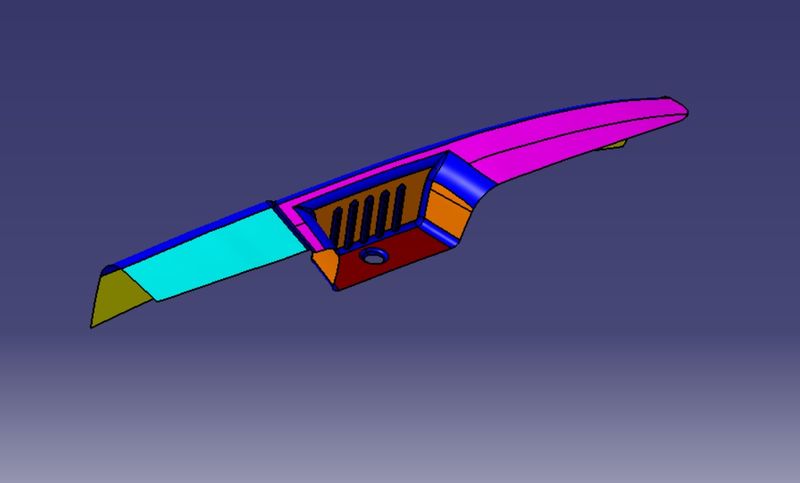
Draft:
- Draft is an angular tapering given at the design stage to every Plastic Component that has to be manufactured.
- It is given in the direction of the Mold Movement.
- The Draft allows the parts to release easily from the mold without creating friction between the surface of component and the core and cavity plates.
- When a Plastic component cools down inside the mold, the natural tendency of it is to shrink and attach to the core or cavity half.
- The movement of mold opening causes friction on the walls of the component as well as the core/cavity blocks.
- This reduces the life of the mold as well as the component itself.
- The component may also have rough surface finish as well as weak structure due to this.
- This problem can be solved by giving draft to the component.
- Most applications require minimum draft angles of around 0.5º to 1º , however 3º draft angles are widely accepted for cost saving purpose.
- 7ºDraft angles are given to textured surfaces like Instrument Panels.
- Minimum possible draft angles are given to screw bosses, ribs and stiffeners due to their critical nature.
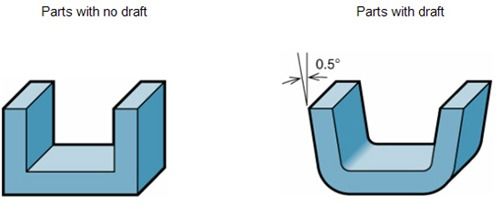
fig: Draft Angle
Tooling Axis:
- Tooling Axis is the direction in which the Mold opens and closes. Part Drafts are generally given along this axis.
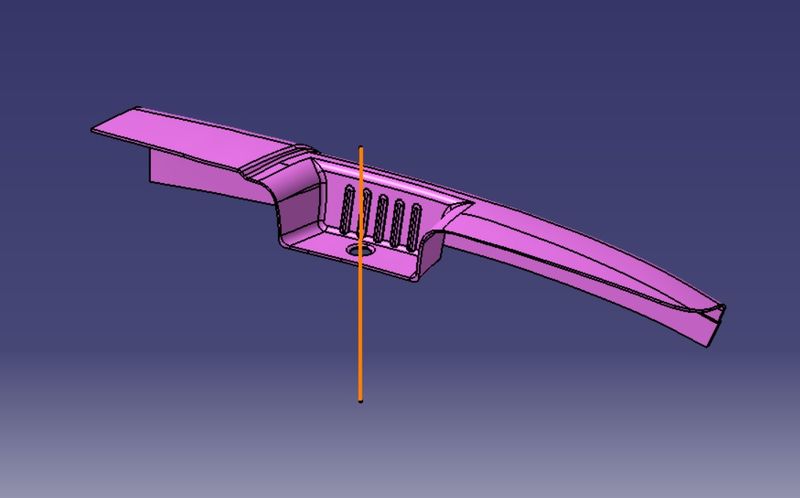
fig: Tooling Axis
Class- A Surface:
- In automotive design, a class A surface is any of a set of freeform surfaces of high efficiency and quality.
- It is the visible aesthetic surface of any automotive component.
- Class A surface refers to those surfaces which are visible and abide to the physical meaning, in a product.
- This classification is primarily used in the automotive and increasingly in consumer goods industry.
- It is a requirement where aesthetics has a significant contribution.
- For this reason, the exterior of automobiles is deemed Class-A.
Class- B Surface:
- Class B surfaces are Engineering Surfaces which are invisible to the eyes or often on the back side of the Class A surfaces.
- It is mainly the thickness of the component or Class A.
- These surfaces need to be designed as per the Class A surface i.e., the continuity, thickness of the component, functionality etc should be maintained.
- These surfaces include the main engineering features such as Screw bosses, Ribs, Snaps, Stiffeners and fixations.
- B surfaces also do not contain any aesthetic styling content and textures since it is not visible to eyes.
Class- C Surface:
- Class C surfaces are connectors between Class A and B surfaces.
- This surface connects both A and B surfaces along the Tooling Axis.
- It contains the draft as per the design.
- It is basically the thickened surface between both A and B surface.
- Below Figure 6 shows class A,B and C surfaces: Blue surface is Class A, Orange surface is Class B and Purple surfaces are Class C surfaces.
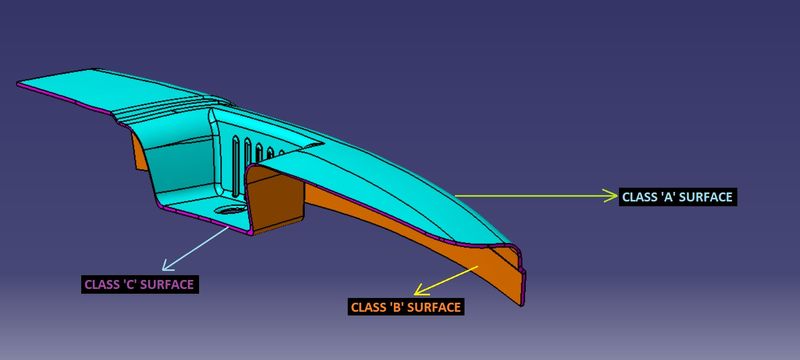
fig: Final Trims of Class A, B & C Surfaces of Door Arm Rest
DOOR ARM REST DESIGN:
Procedure to be followed:
Step 1: Design Check (Pre Check) on received Class A:
- After receiving the Class-A for the Coin Holder check for the connectivity of the surfaces on it.
- Use boundary operation and disassemble.
- Check for discontinuous Surfaces.
- The check is over if any discontinuities do not arise.
Step 2: Determine the Tooling Axis:
- Identify faces which can potentially create problems while manufacturing.
- Surfaces at angles along a desired Tooling Axis.
- Extract a plain surface and create a point on its center for Axis system creation.
- In this case Z axis can be a possible Tooling Axis Direction.
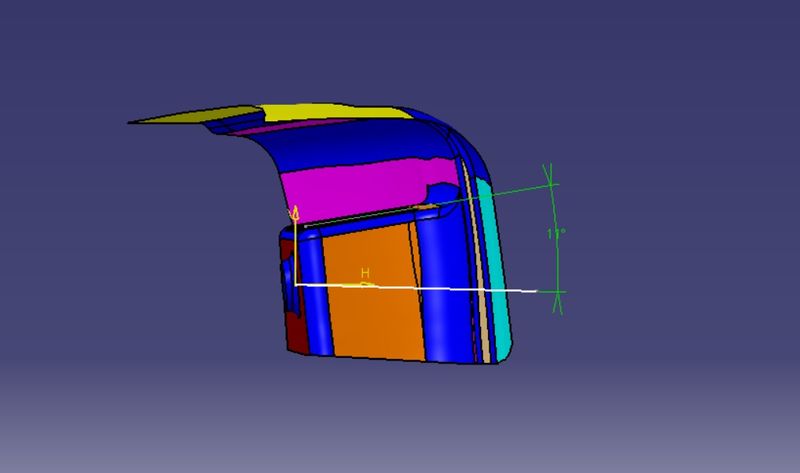
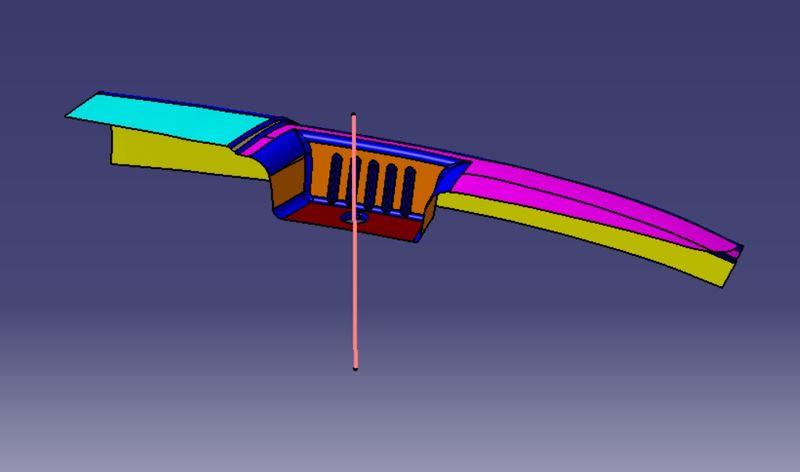
Step 3: Draft Analysis on Class A and Possible Creation of Side Tooling Axis:
- Change View Mode Customization to Material mode
- Go to INSERT ---> ANALYSIS ---> FEATURE DRAFT ANALYSIS and move the compass to the Tooling Axis.
- Change the range to 3º. Apply the settings as shown in below image.
- The input Class A also has walls having negative angle to the tooling axis.
- This can be an issue while manufacturing the component as it would be very difficult to draw from the molds.
- So, this design needs to consider Various Side Tooling Options.
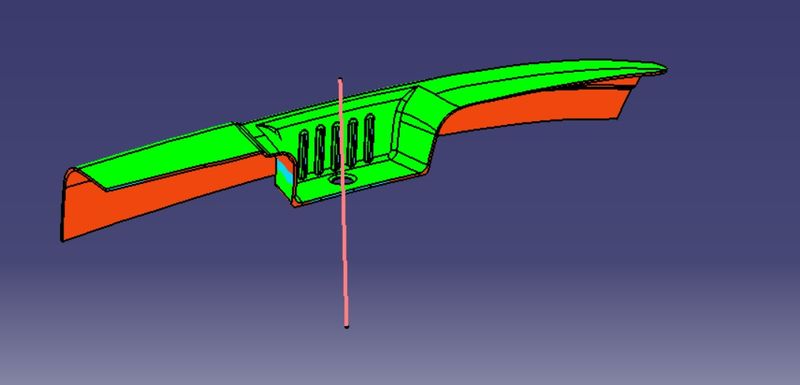
fig:Draft Analysis along Tooling Axis
Step 4: Class B Surface Creation:
- Extract The Class A Surfaces for example the Bin Base.
- Untrim it to obtain a continuous surface.
- Extrapolate the obtained surface to a value such that it passes the class A bin.
- Offset the Surface to value 2.5 on B Side which is downwards in this case as shown in below Figure
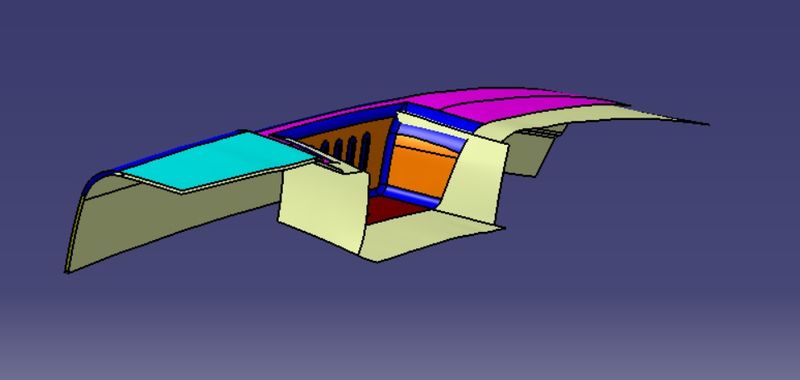
fig: B Surface Creation as Offsetting 2.5mm from Class A Surface
- Use Similar options for Side Walls and Upper Surface.
- Use Extrapolate option only on required Direction to obtain the Surface trims as shown in Figure 18.
- Use Fillets so as to maintain Wall Thickness to 2.5mm
- Create Fillets while maintaining the part thickness of 2.5mm between the Class A and Class B surfaces.
- The Value of Fillet is given by the equation (B surface fillet = A surface fillet +(or)- Thickness of the Part).
- The sign + or – must be decided so as to maintain the part thickness which in this case is 2.5mm.
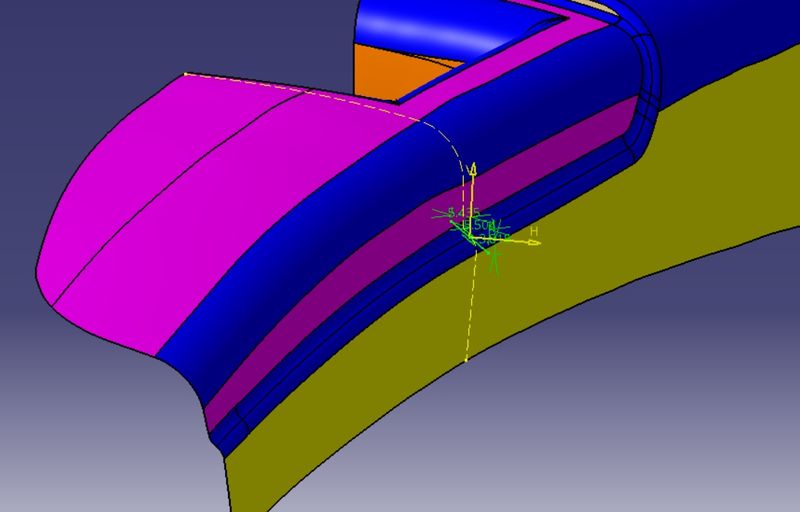
fig: Sketch for Connecter at B surface for Arm Rest Face and Side Wall.
- To create a Connecting Surface for the Class B Create a Axis System on the Extract Point as shown in Figure.
- Intersect the Class A with the YZ plane.
- Create a Line Tangent to the Fillets on the Intersection
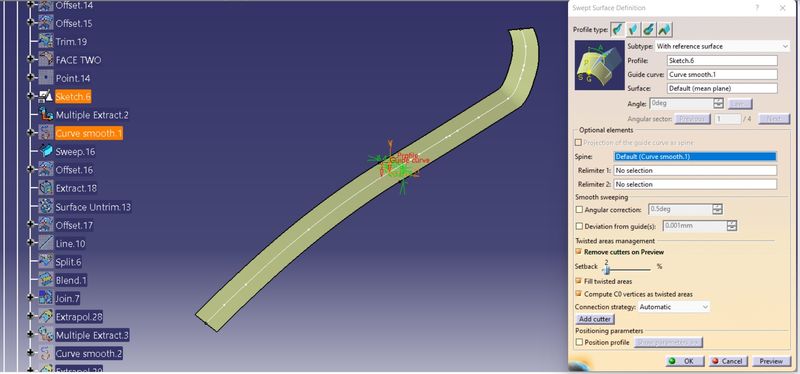
- Use Sweep operation along the Line for the Smooth Curve.
- The obtained sweep is shown in Figure.
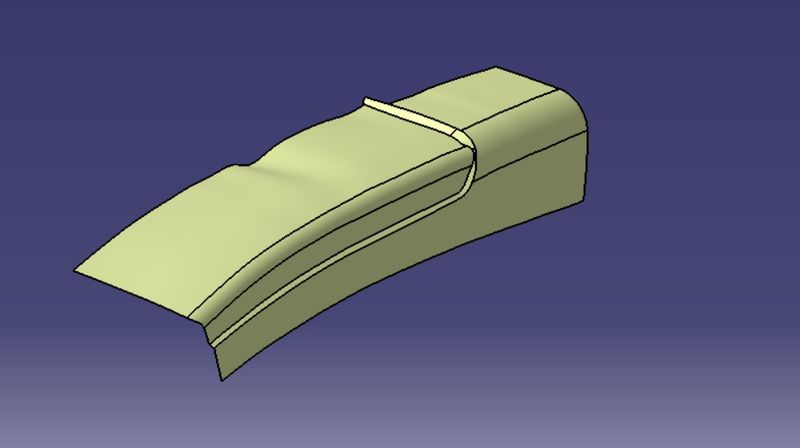
- Trim the Connectored with other pre created B surfaces.
- Make adjustments as per requirement.
"B Surface Trims"
- Create appropriate Fillets as per the rules.
- Create features aesthetic Ribs on B Surface.
- Create the Hole in Bin offseted to that on the Class A Surface.
- The Final B Surface Obtained is shown in Figure .
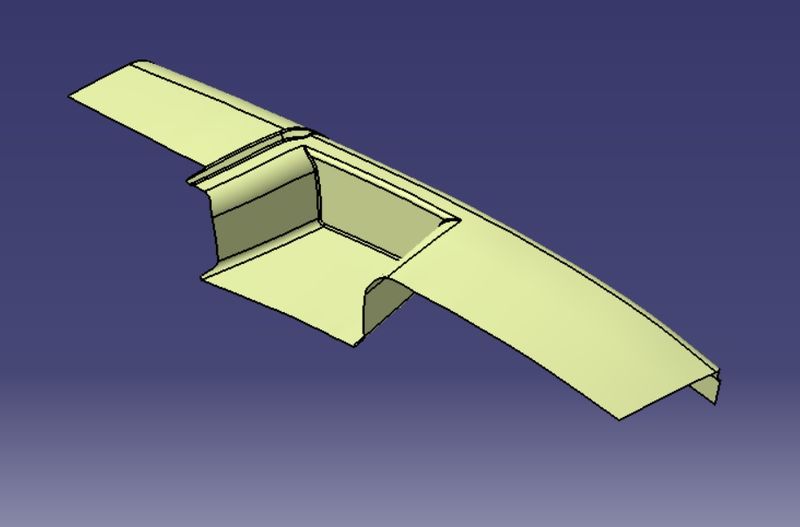
Step 5: Class C Surface Creation:
- Extract Class A boundary and convert to Smooth Curve.
- Sweep this curve at 90 degress to the Class A.
- Sweep value should be greater than the Thickness required for Part.
- The obtained sweep is shown in Figure.
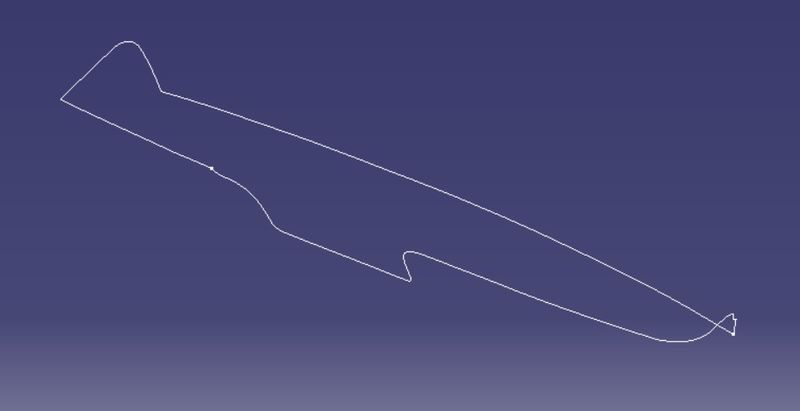
fig: Outer Boundary of Class A surafce
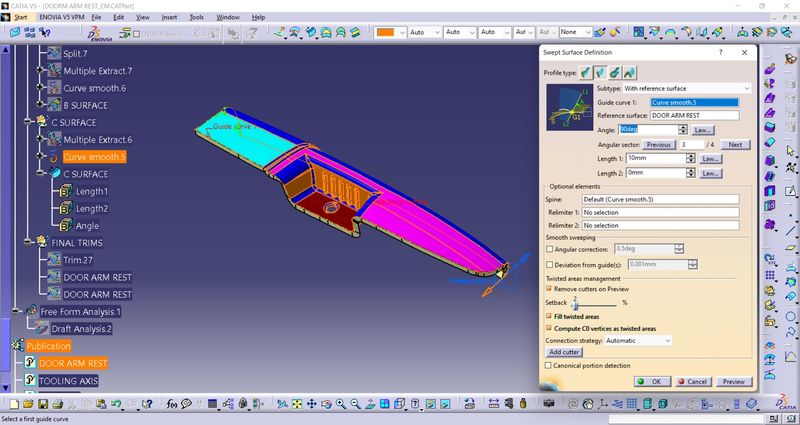
fig: Class 'C' Surface Creation
- Join the Class A Surface with the Class C Surface to create a single surface entity.
- The obtained surface is shown in Figure .
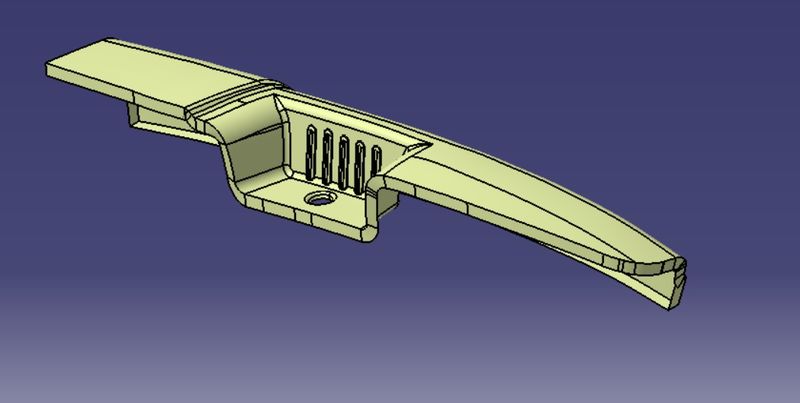
fig: Class A and C Surface
Step 6: Enclosed Surface Creation:
- Trim the obtained surface with Class B surface.
- Make Slight Adjustments by extrapolating small values and trimming to obtain a final Enclosed Surface
- The Final Enclosed Surface Obtained is shown in Figure.
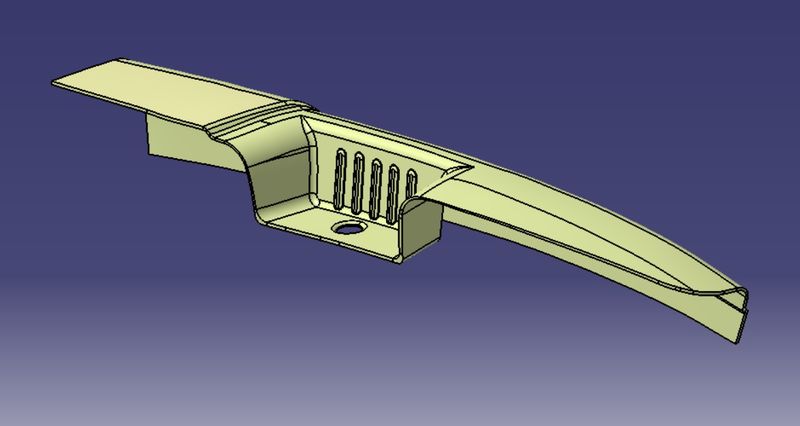
fig: Class A,B and C Join making the final Enclosed surface of Arm Rest.
Closed Surface:
Make the final trim to Solid part using close surface
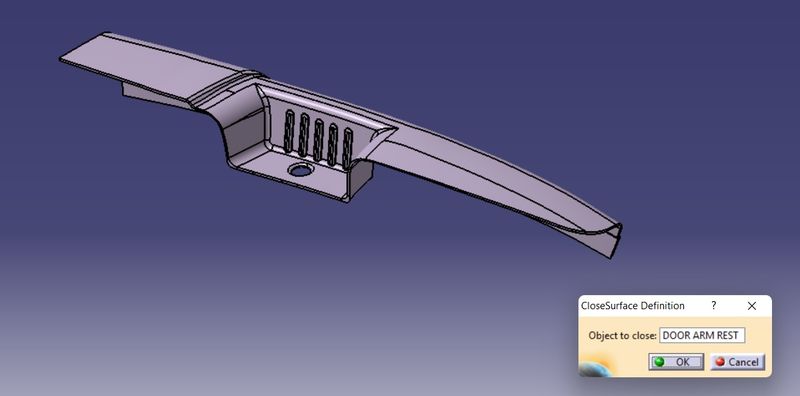
fig: Closed Suface (Solid Body)
Step 7: Perform Draft Analysis on Final Enclosed Surface:
- Change View Mode Customization to Material mode
- Go to INSERT ---> ANALYSIS ---> FEATURE DRAFT ANALYSIS and move the compass to the Main Tooling Axis.
- Change the range to 2.9º. Apply the settings as Shown in Figure.
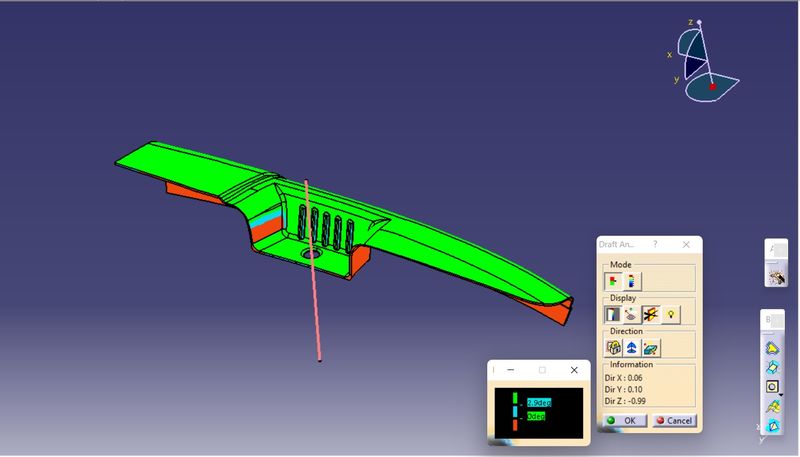
fig: Draft Analysis on Final Enclosed surface along Main Tooling Axis.
Draft Analysis by Side Core Tooling Axis:
Perform Draft Analysis along other Side Tooling Axis
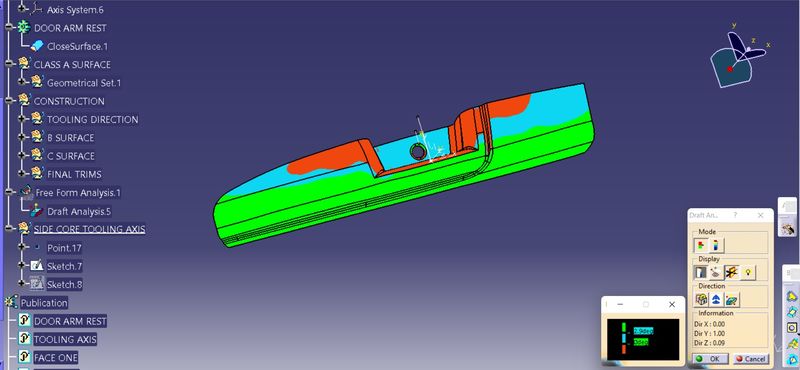
Model Views:
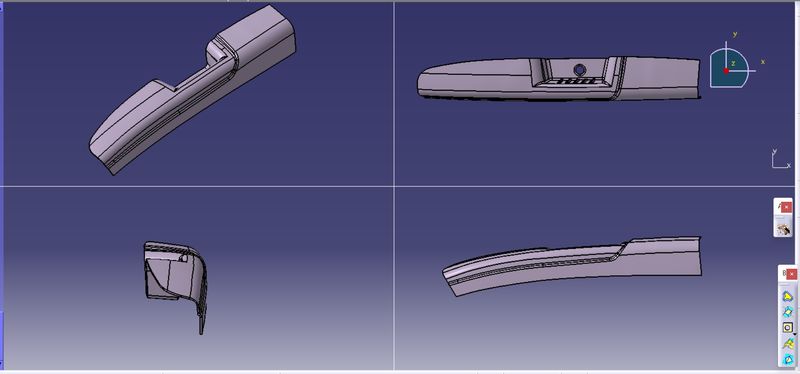
Conclusion:
The Design of Automotive Plastic Component – Door Arm Rest from Class A as input is completed using concepts of Draft angles, Draft Analysis, Determining and implementing of Tooling Axis, Side Core Axis, Class A, Class B, Class C surfaces and Maintaining the Thickness of the part at 2.5mm and finally converting the enclosed Surface into solid Part.
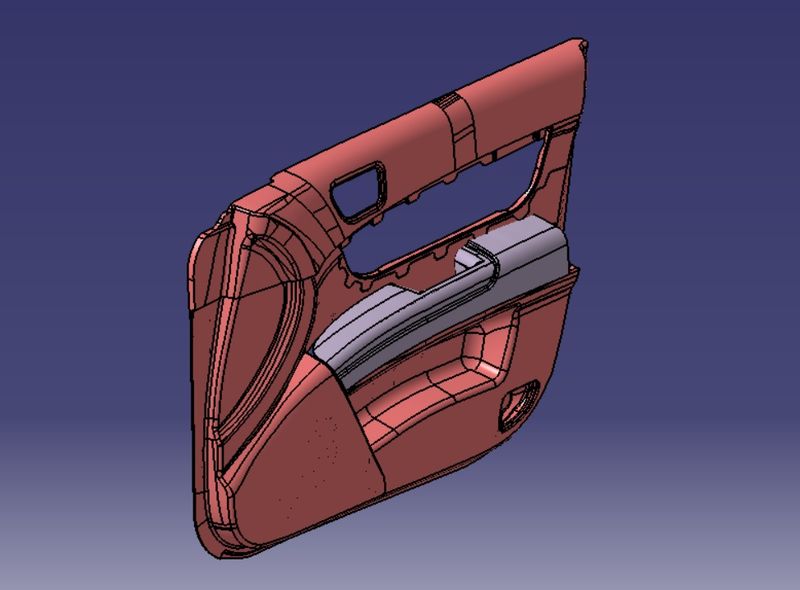