DESIGN OF BACKDOOR
Aim:
- To create a backdoor for an automobile out of sheet metal by following design guidelines and using the provided skin data.
- It is important to use design techniques while creating the backdoor and to add embosses, reinforcements, and Corner relief to the outer panel in order to improve their strength.
Back-Door:

-
The back door of a car is a part that hinges at the back of the automobile to cover the boot or luggage area, but it also serves other purposes that must be taken into account while designing it, such as rear view requirements and boot space.
-
Due to the sealant flange and other factors, as well as the fact that it will come into contact with the side body of the automobile, this component is typically constructed with the master section of the rear roof rail in mind.
-
Rear windscreen is fixed between the inner and outer panels, and in some back doors, a spare wheel can be mounted on it. It also features back lights, tail lights, and braking lights that are referred to as "third brake lights."
Design Considerations:
- Rear visibility for functionality and safety.
- Hinge and gasstay support structures, as well as power lifters.
- Regulation of rear crashes.
- Mounts for the wiper motor and lights in the boot Area.
- Strength standards.
- Draft Evaluation.
Class.A_Surface:
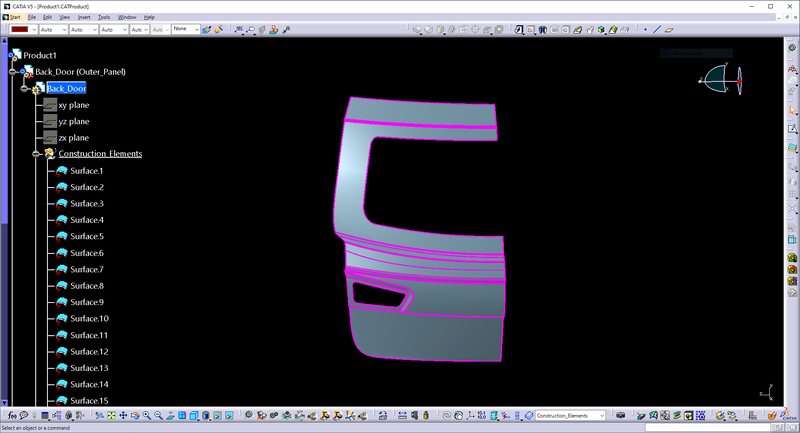
Class.A_Upper_Surface_Improvement:
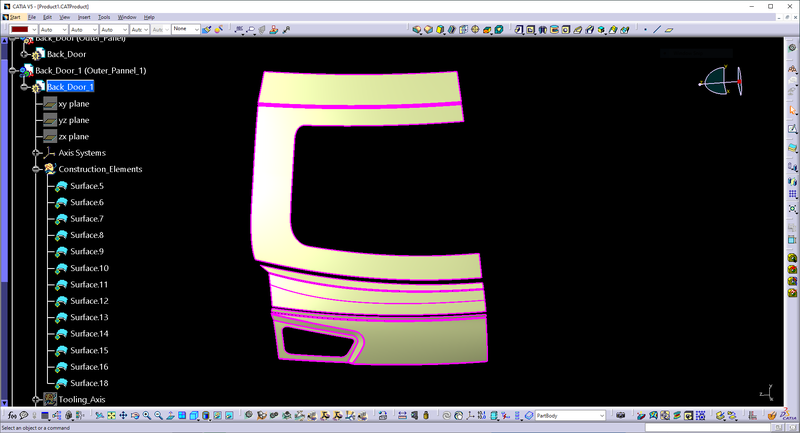
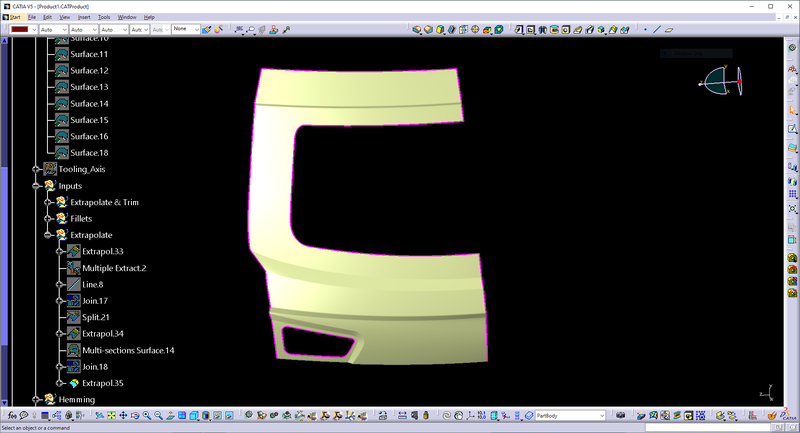
Tooling_Axis:
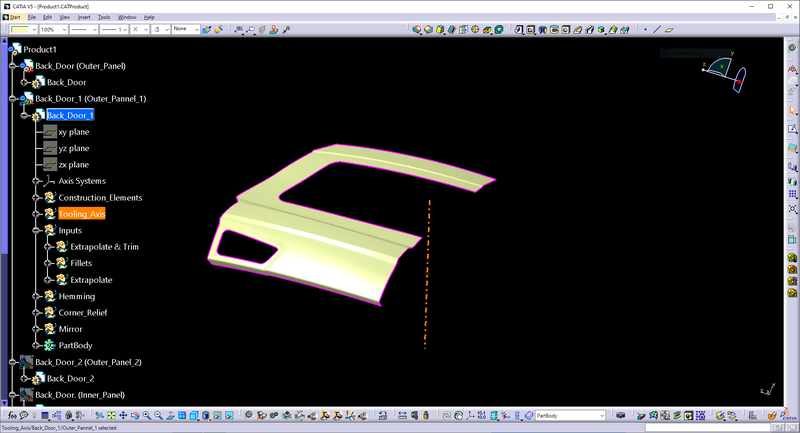
- First, we must determine whether the provided data has any surface abnormalities.
- If so, these irregularities must be repaired by applying a parallel curve and a thorough sweep.
- Next, a sealing flange is made. Typically, we will design the panel with the proper dimensions using a sketch.
- But because we designed it based on assumptions, there is no master sketch here.
Class.A_Lower_Surface_Improvement:
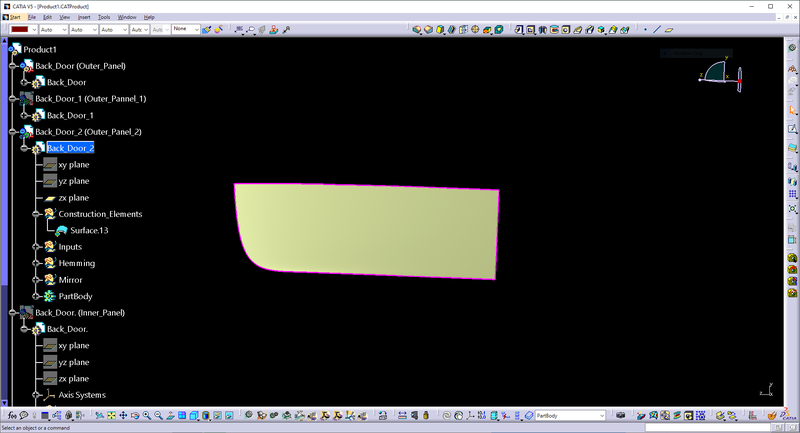
Procedure:
- First, we must determine whether the provided data has any surface abnormalities. If so, these irregularities must be repaired by applying a parallel curve and a thorough sweep.
- Next, a sealing flange is made. Typically, we will design the panel with the proper dimensions using a sketch. But because we designed it based on assumptions, there is no master sketch here.
Sealing_Flange:
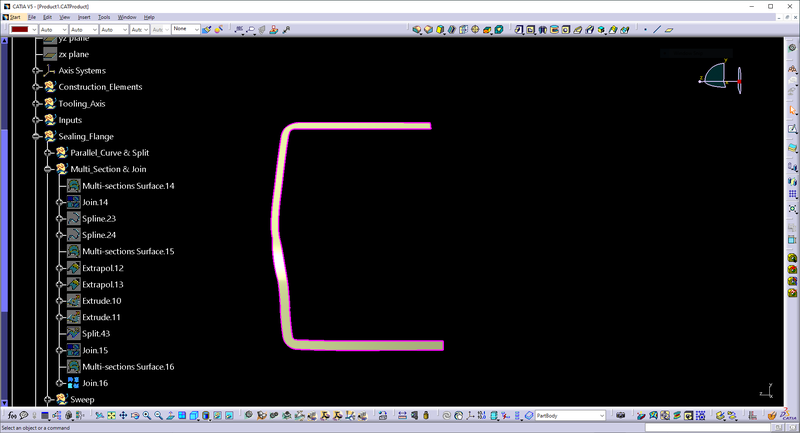
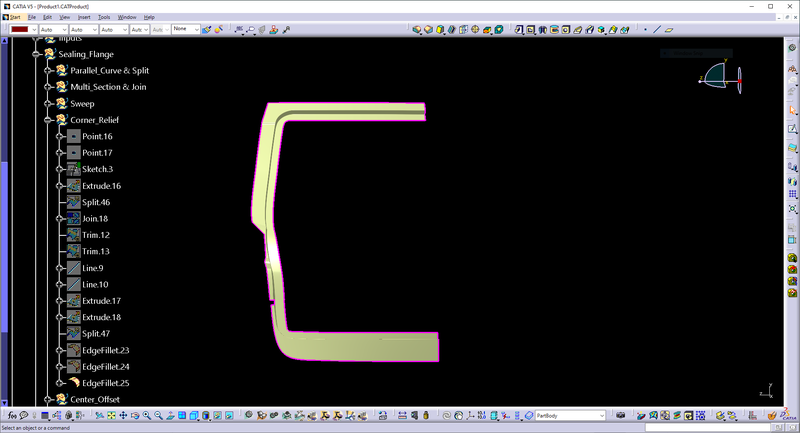
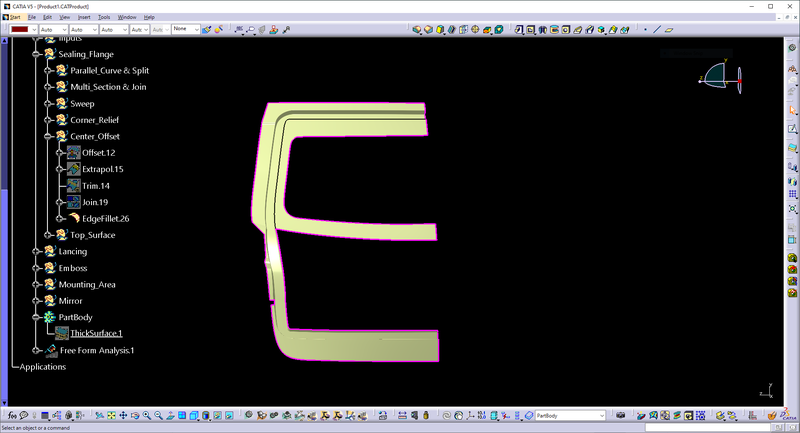
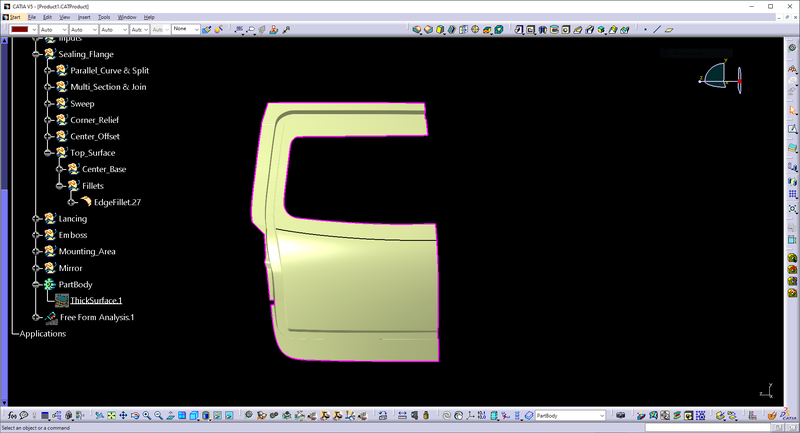
- In this instance, the sealing flange is made by keeping the inner panel's distance from it.
Lancing:
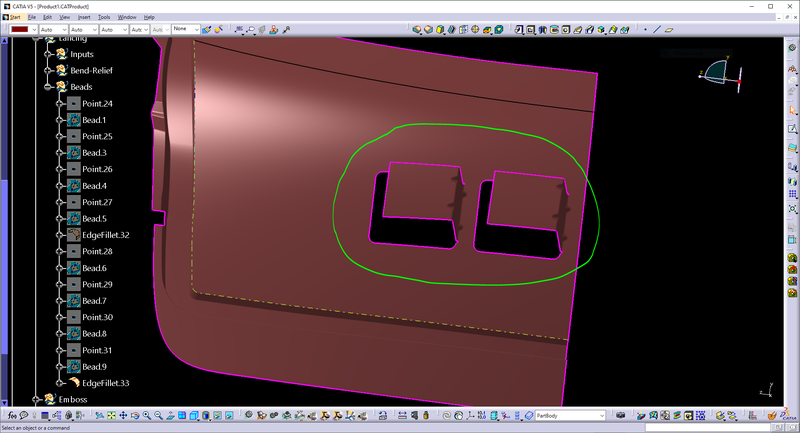
Mounting_Area's:
- Wiper Mounting.
- Striker Mounting.
- Hinge Mounting.
- Gastay Mounting.
Wiper Mounting:
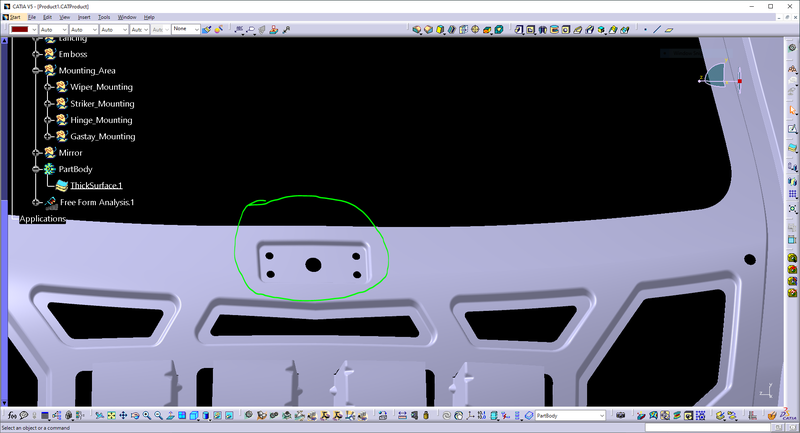
Striker Mounting:
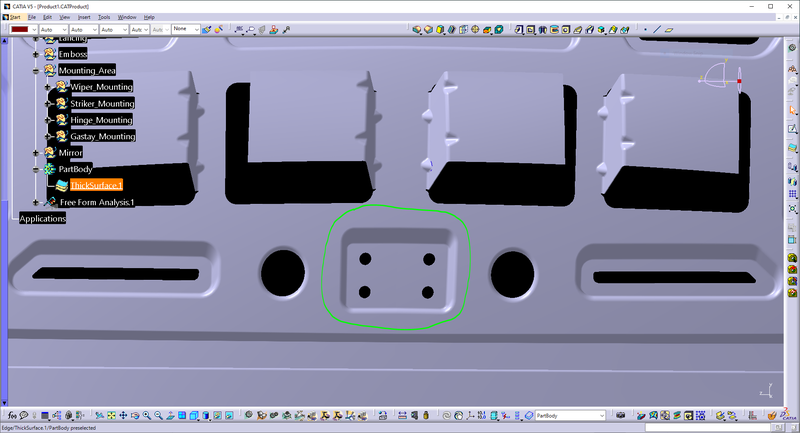
Hinge Mounting:
- The backdoor is an item that swings and is supported by hinges. To achieve this, place the hinges hesitantly, then choose a central point on the hinge axis. Once more, we measure the latch hole's approximate centre.
- We draw a circle using these two spots as a reference.
- The striker trajectory is represented by this circle, which must be perpendicular. The latch area can be rotated or the hinge axis can be moved back and forth to accomplish.
- Because the mounting area should be flat or have no radius of curvature, a plane was used. On that plane, a drawing was made.
- The hinge emboss feature was created by using the emboss command.
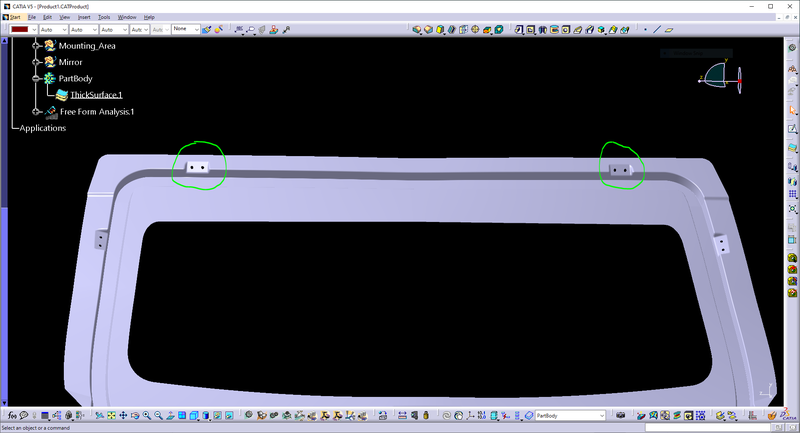
Gas-tay Mounting:
- The gas stay rod is held by it. Since gas stay rods are mostly utilised in back doors, they allow for easy opening and shutting.
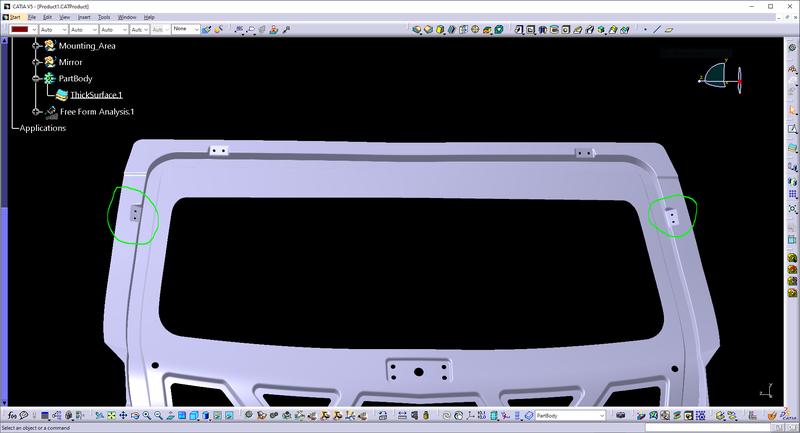
Inner Panel:
Force Proportionality:
- The impact force should diffuse to the exterior when the car is struck from behind.
- For this, we developed the embosses using a U/V, undercut, and mastics mix.
Mastication area:
- The inner panel of the backdoor has specified "mastic spots" where the door can readily distort.
- They assist in restoring the distorted outer panel of the backdoor to its original position. Mastic sealants are rubber-like rubber-like elastic materials.
- Mastic sealants are placed at specific locations in the space between the inner and outer panels over the embosses to help reduce vibrations and overall noise, vibration, and harshness (NVH) ( Noise, Vibration, Harshness).
- The sheet is then bent using a different die to create a "L"-shaped flange.
- As a result, the flange will have a rather uniform pattern and its length will entirely depend on the cut-out; if we need a longer flange, we must cut additional sheets.
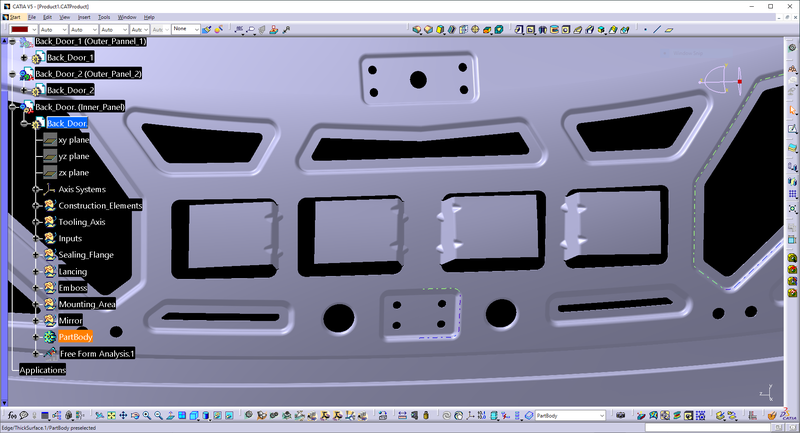
Emboses:
- With the distinctive cross-section, embosses are created. The embosses are used to increase the strength of the backdoor. While designing we should keep in mind that it should not be over strength. So we prefer to design big embosses rather than small embosses. These embosses are used to disipate the forces sideways.
Hemming_Process:

- In the process of hemming, sheets of metal are bent 180 degrees to link them together.
- Hemming is a procedure used to create automotive body panels and parts such deck lids, trunk lids, doors, hoods, and tailgates.
- Typically, a sheet is bent in three phases throughout this operation with the aid of an inner sheet.
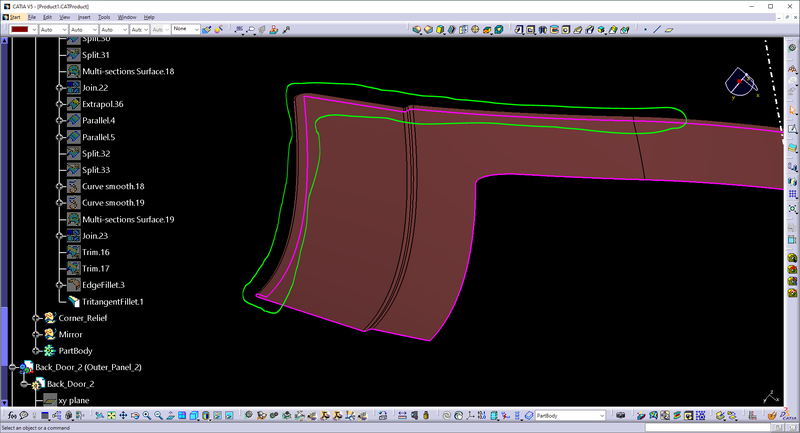
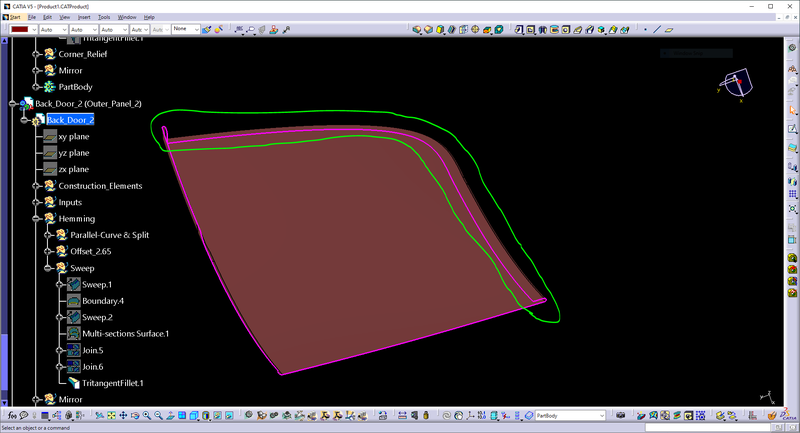
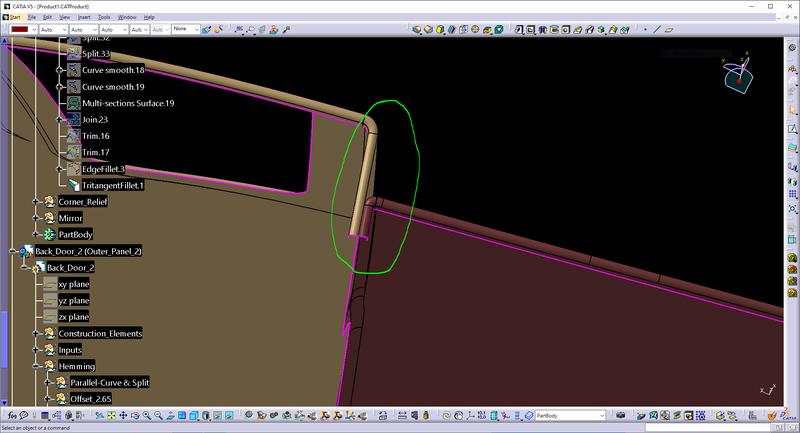
Corner_Relief:
- A Corner relief is just two tiny slits cut into a sheet of metal to release the metal between them.
- It divides the component's rest from the material you wish to be able to fold.
- Only when there is material on either side of a bend do you need it.
Draft_Analysis:
- By applying the draught condition, the draught analysis technique is utilised to determine whether our CAD-created part model is capable of being manufactured.
- Here, the component must be simple to remove from the panel dies or mould (if it is a sheet metal component) (in case of plastic)
Draft Analysis Of Outer_Panel:
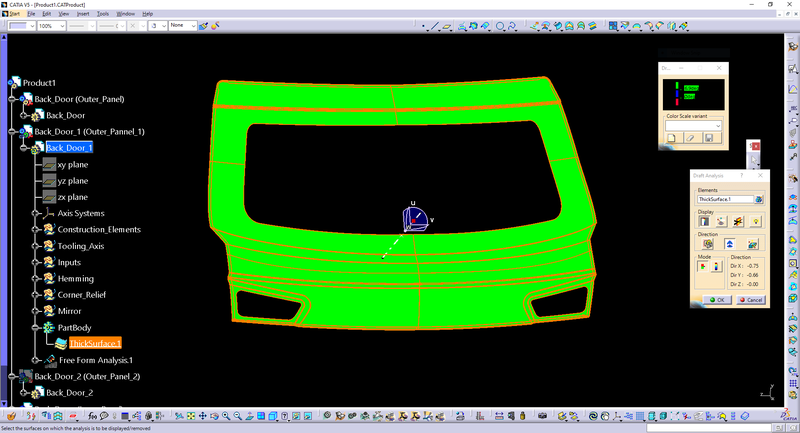
Draft Analysis Of Inner_Panel:
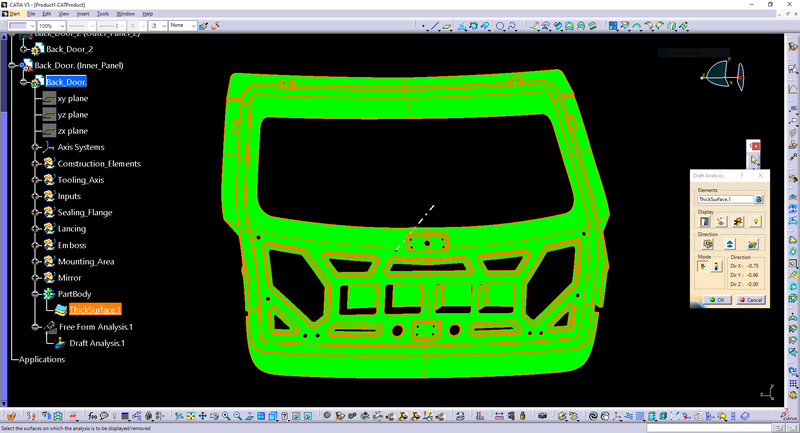
Final_Assembly Of Back_Door:
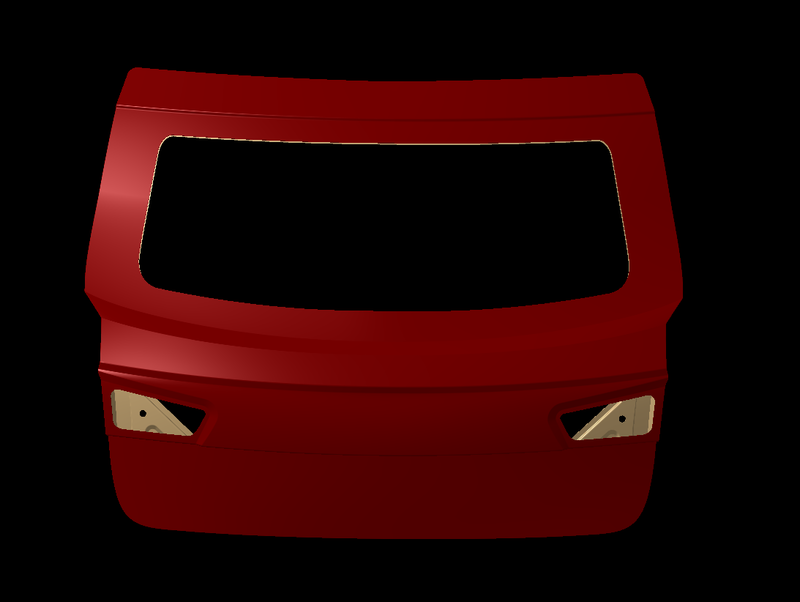
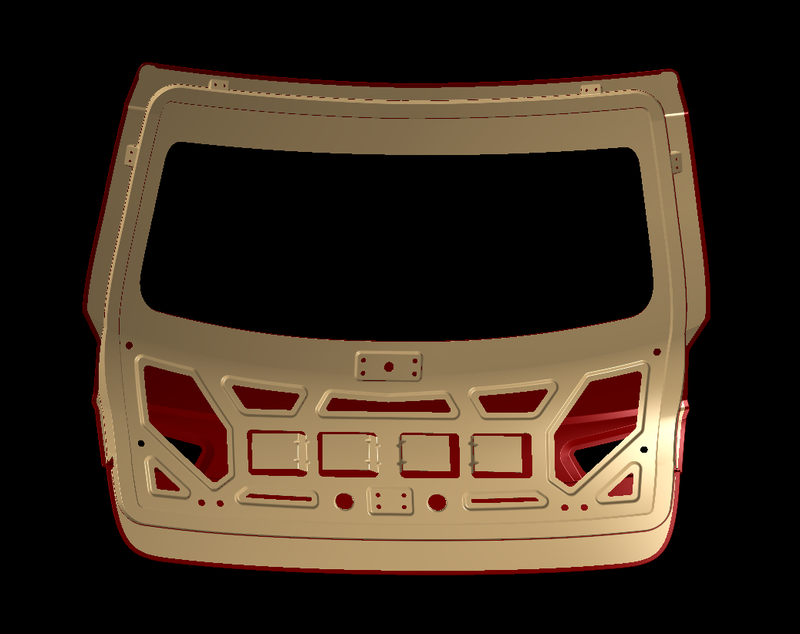
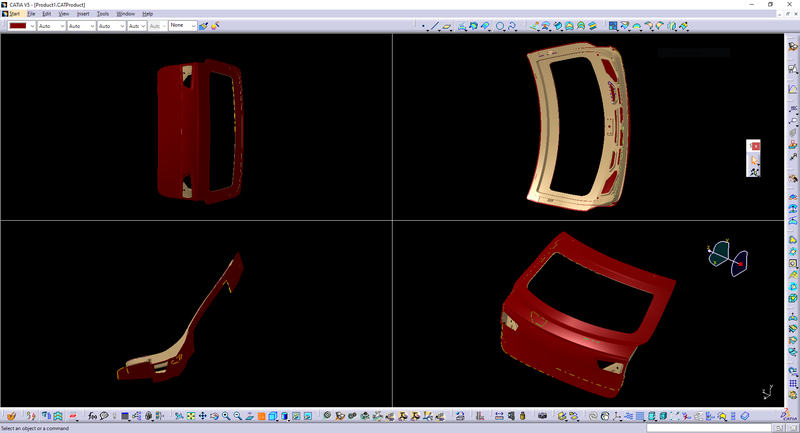
Conclusion:
-
The style surface along the tooling direction was used to assist in the design of the back door's outer and inner panels.
-
The inner panel underwent a draught study, and all of the reinforcements were created and positioned appropriately.