Section Modulus and its Calculation and Optimization
Section Modulus:
- A geometric characteristic for a specific cross-section that is employed in the design of beams or flexural members is called section modulus.
- The area for tension and shear, the radius of gyration for compression, the moment of inertia, and the polar moment of inertia for stiffness are further geometric properties employed in the design.
Procedure:
- Using the intersection of the inner and outer hood as a guide.
- It should be closed after the boundary regions are removed.
- The fill command is used to close the inner surface in the boundary areas.
- Same as for the side collision.
Formula to Calculate the Section Modulus:
S = I/Y
- S - Section Modulus
- I - Inertia
- Y - Distance from the neutral axis
Section Modulus in Hood:
- In this hood, we take two sections of modulus frontal and side.
- To improve the strength of the hood.
- When designing beams, the cross-sectional shape's section modulus is quite important.
- It provides a precise indication of the beam's strength.
- A beam will be stronger and able to bear heavier loads if it has a higher section modulus than another beam.
Bending Moment Formula:
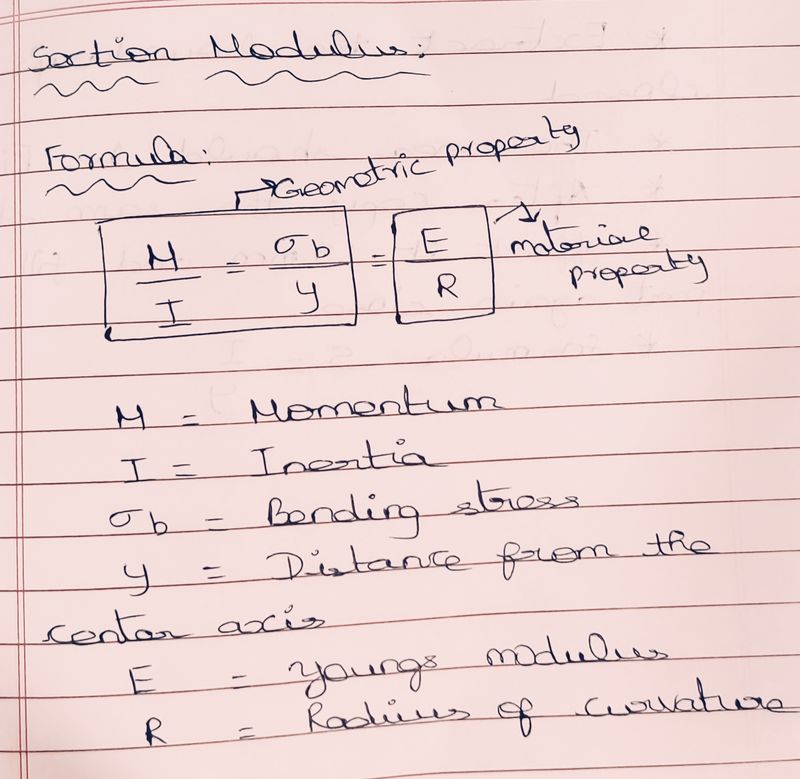
Moment of Inertia:
- The moment of inertia of a rigid body, also known as the mass moment of inertia, angular mass, second moment of mass, or, more precisely, rotational inertia, is a quantity that determines the torque required for a desired angular acceleration about a rotational axis, in the same way, that mass determines the force required for the desired acceleration.
- The body's mass distribution determines it and the axis is chosen, with more significant moments necessitating more torque to change the body's rate of rotation.
Section Modulus for Frontal Collision:
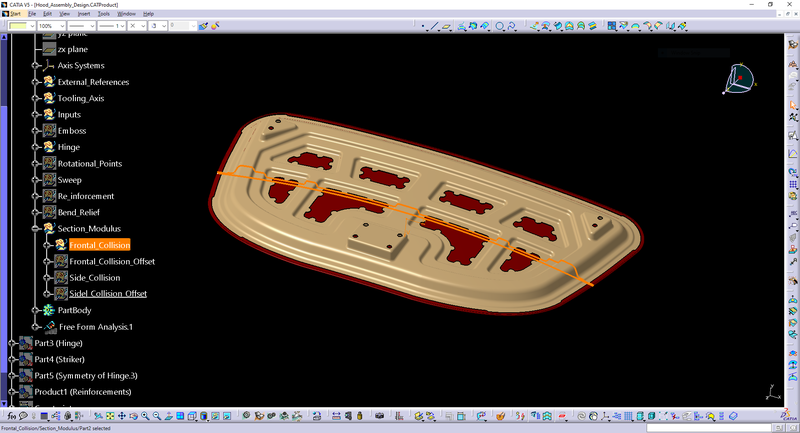
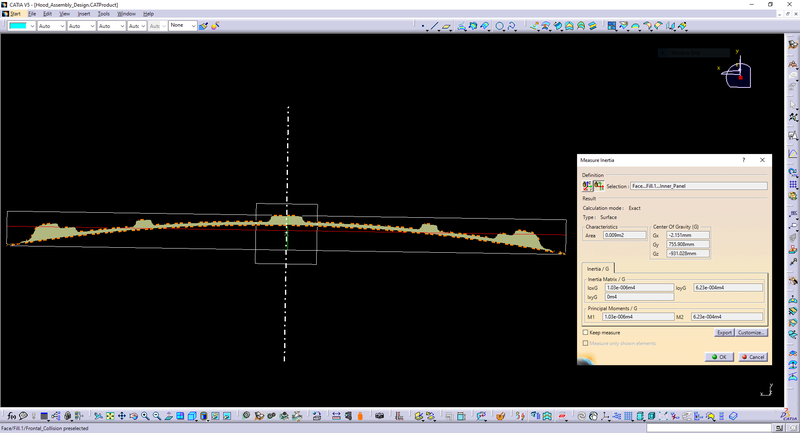
- Distance from the neutral axis
Section Modulus for Frontal Collision Offset:

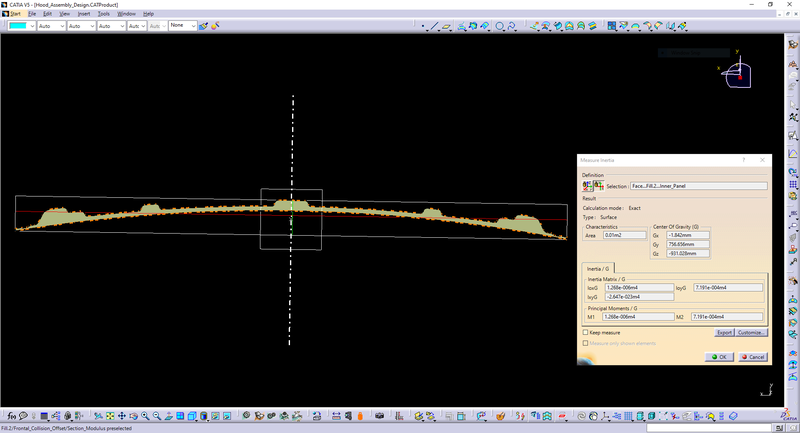
- Optimized distance from the neutral axis
Section Modulus and its calculation for the Frontal Collision:
1.) Section Modulus for Frontal Collision:
Moment of inertia(min) = 1.958×10^-6×10^12
Moment of inertia(max) = 7.155×10^-4×10^12
Y=874.244/2=437.122mm
S=I/Y
S1=1958000/437.12= 4479.29mm
S2=715500000/437.12=163684.804mm
Results:
- After the calculations of the above 2 cases, the section modulus of an S1(Minimum) and S2(Minimum) difference is 4479.29mm.
- After the calculations of the above 2 cases, the section modulus of an S1(Maximum) and S2(Maximum) difference is 163684.804mm.
- The section modulus value of case 2 is higher than case 1 for both Maximum & Minimum
- As we increase the section area, the moment of inertia & section modulus increase which means strength and load material also increase. Which is the moment of inertia directly proportional to the strength of the material.
Section Modulus for Side Collision:
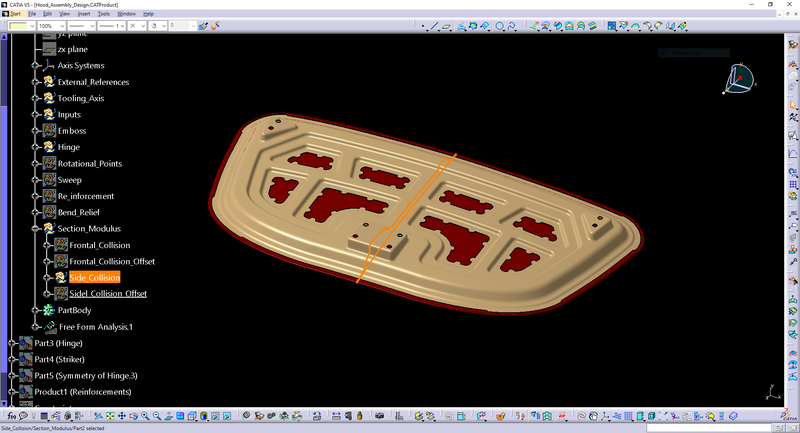
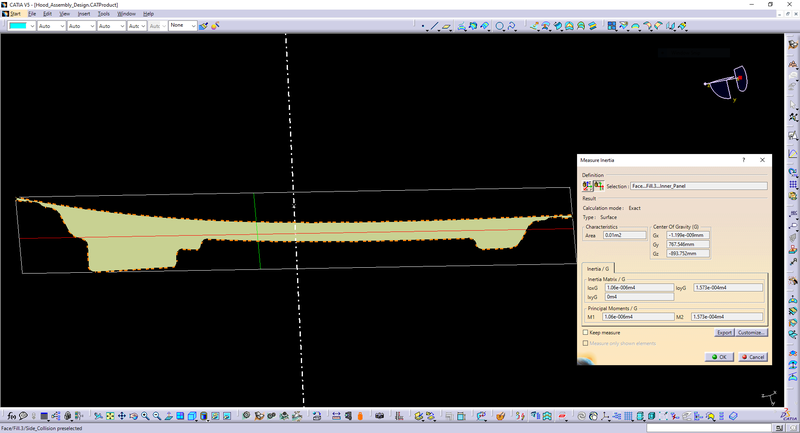
- Distance from the neutral axis
Section Modulus for Side Collision Offset:
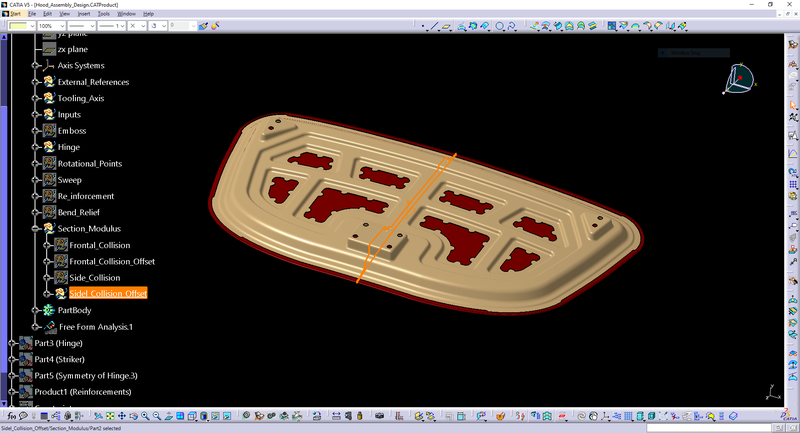
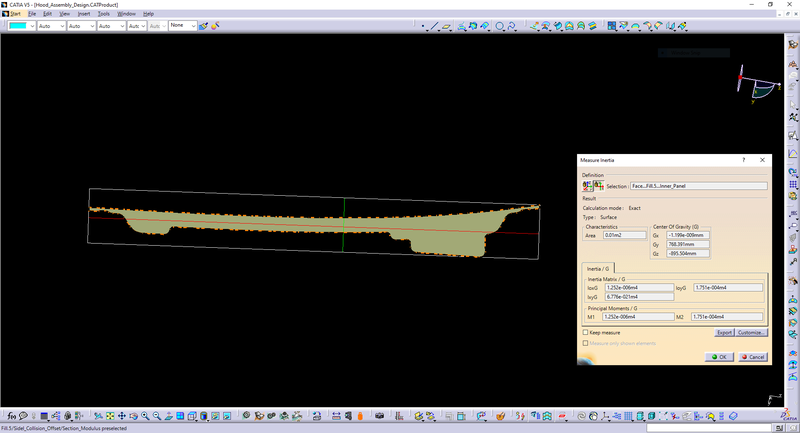
- Optimized distance from the neutral axis
Section Modulus and its calculation for the Side Collision:
1.) Section Modulus for Side Collision:
1.218×10^-6×10^12
Moment of inertia(max) = 1.529×10^-4×10^12
Y=475.462/2=237.731mm
S=I/Y
S1=1.218000/237.731= 5123.43mm
S2=152900000/237.731=643163.91mm
Results:
- After the calculations of the above 2 cases, the section modulus of an S1(Minimum) and S2(Minimum) difference is 5123.43mm.
- After the calculations of the above 2 cases, the section modulus of an S1(Maximum) and S2(Maximum) difference is 643163.91mm.
- The section modulus value of case 2 is higher than case 1 for both Maximum & Minimum
- As we increase the section area, the moment of inertia & section modulus increase which means strength and load material also increase. Which is the moment of inertia directly proportional to the strength of the material.
Conclusion:
- I had taken the section module for the outer panel and boss in the given hood for pedestrian safety and driver safety.
- The section module was derived from the front and side crushness of the designed outer panel and emboss, which I designed. For the Purpose Of Calculation the Section Modulus Of the Designed Hood of the geometry cross section of the outer panel and the internal emboss of the front and side wewe taken.
- I offset the inner panel by 2 mm to find the best section modulus for front and side crushness in order to achieve good strength and bending stress.
- Finally, as the section modulus increases, the amount of bending stress and moment for designed outside panels and embossed inner panels will decrease.