Automotive Plastic Component: B Pillar RH Cover - Creating CAD Part from Master Sections and Class A as Input
This report demonstrates the design of B Pillar RH Cover and Automotive Plastic Component. The component has been designed from the Class A and Master Sections as Input. Industry principles such as Draft angles, Draft Analysis, Determining and implementing of Tooling Axis, Side Core or Lifter Axis, Class A, Class B, Class C surfaces and Maintaining the Thickness of the part at 2mm. B side features such as Ribs for strength of the cover, Dog Houses for hosting the locators and 4 Way Locators are also incorporated in the design. The overall design follows the Master Sections to create B surface and B side Features. The component is designed using Generative Shape (Surface) Design and Solid Design techniques in CAD package CATIA V5.
Design Rules for Plastic Components:
- Nominal wall thickness of a plastic component is 3mm. For a strength component such as Instrument Panel, Bumper , door trims the values of thickness are larger than 4mm. For example, Thickness of IP may lie between 5-6mm, for Bumper it may be 6-8mm.
- For smaller components the thickness may be between 2-3mm as in this case of Coin Holder.
- Deviation of `30% from the wall thickness is allowed with gradual increase or decrease to avoid any plastic defects while manufacturing.
- For example: A component having wall thickness 3mm should deviate within the range of 2.1 mm minimum and 3.9 mm maximum.
- Ideal draft angle should be 3º for the overall component along for the faces lying in the tooling direction.
Ribs Design:
- Rib is a B-Side Engineering feature which provides a means to economical Stiffness and Strength in Plastic Molded parts without increase in overall wall thickness.
- Rib also facilitates locating and arresting components of an assembly.
- It provides alignment in Mating Parts.
- It acts as Stop and Guides for Mechanisms.
Guidelines For Rib Design:
- Proper Rib design is necessary to avoid plastic defects which involves the following critical issues that needs to be considered which are:
- Draft angle
- Rib Thickness at base
- Thickness at Top of the Rib
- Rib Height
- Location of Ribs and Spacing between 2 Ribs
- Optional Radius or Fillet Radius
- Rib Root Diameter
- Quantity of Ribs
- Manufacturability
- These guidelines are separate for Show and No – show surfaces.
- The below table gives specific values for both cases.
- Consider ‘t’ as wall thickness of base for component.
Table1: Rib Design Guidelines*
Rib Specification
|
No-Show Surfaces
|
Show Surfaces
|
Draft Angle
|
Min 0.5º per side,
Recommended 1.5º per side
|
0.5º per side
|
Rib Thickness at Base (w)
|
0.5 * t
|
0.4 * t
|
Rib Thickness at top
|
Min 0.75mm
|
Min 0.75mm
|
Rib Height (y)
|
Max 5*t
|
Max 5*t
|
Spacing Between 2 Ribs (x)
|
2*t
|
2*t
|
Fillet Radius (r)
|
0.125*t
|
Max 0.25mm
|
Rib Root Dia
|
± 30 % of t
|
± 30 % of t
|
y/x ratio for multiple ribs
|
3:1
2:1 preferred
|
3:1
2:1 preferred
|
*some guidelines may change as per the OEM or the industry requirements.
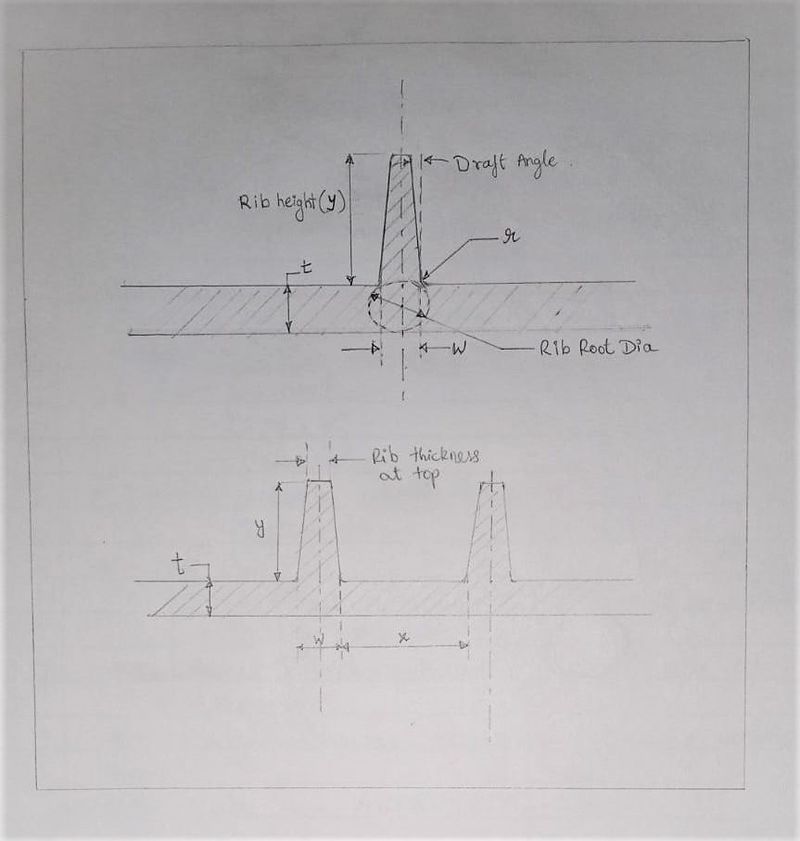
Figure2: Rib Design Nomenclature
Dog House Design:
- Dog House is a B surface engineering feature used to avoid sink marks primarily.
- Its secondary use is to place an offset B side feature such as boss or locators on it.
- The cross section for dog house near the B surface is less and then increases rapidly.
- It can be extended to have another feature on it.
- Also, if Bosses are perpendicular to the B surface Dog houses are used to place it.
Guidelines and Design rules for Dog House:
- Proper Dog House design is necessary to avoid plastic defects which involves the following critical sections and design rules that needs to be considered:
- Draft angle
- Doghouse Walls Section
- Part Surface
- Bottom of Doghouse
- Wall Thickness
- Height and Width
Figure3: Dog house wall section.
- B = 3 to 6mm, C <= 0.4 x T
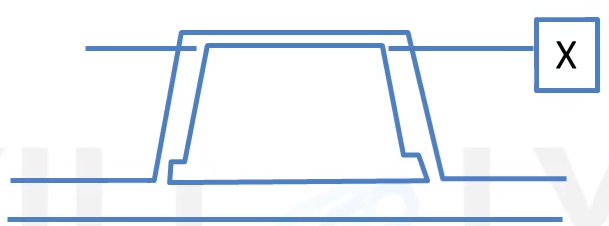
Figure4: Dog house width.
- Dog House width (X) = 12mm Minimum
- Height (H) = 6mm Minimum
- X/H = 3:1 or 2:1
- Draft of 5º minimum to draw direction, if slide is considered then this can change to 3º minimum.
Draft:
- Draft is an angular tapering given at the design stage to every Plastic Component that has to be manufactured.
- It is given in the direction of the Mold Movement.
- The Draft allows the parts to release easily from the mold without creating friction between the surface of component and the core and cavity plates.
- When a Plastic component cools down inside the mold, the natural tendency of it is to shrink and attach to the core or cavity half.
- The movement of mold opening causes friction on the walls of the component as well as the core/cavity blocks.
- This reduces the life of the mold as well as the component itself.
- The component may also have rough surface finish as well as weak structure due to this.
- This problem can be solved by giving draft to the component.
- Most applications require minimum draft angles of around 0.5º to 1º , however 3º draft angles are widely accepted for cost saving purpose.
- 7º Draft angles are given to textured surfaces like Instrument Panels.
- Minimum possible draft angles are given to screw bosses, ribs and stiffeners due to their critical nature.
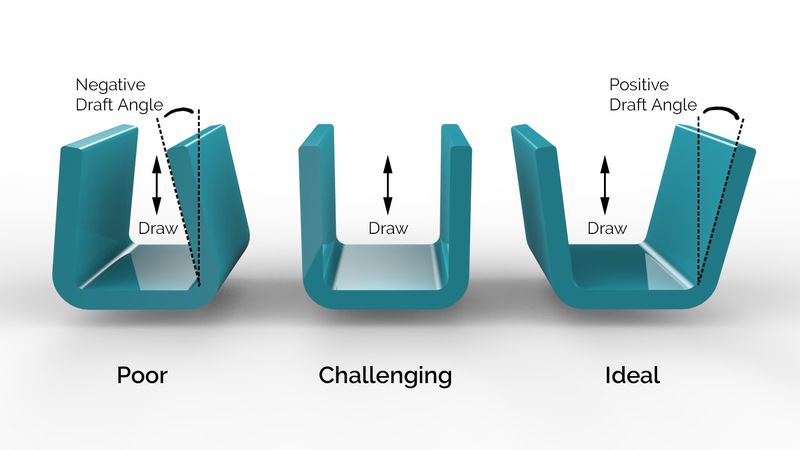
Figure5: Draft Angles
Tooling Axis:
- Tooling Axis is the direction in which the Mold opens and closes.
- Part Drafts are generally given along this axis.
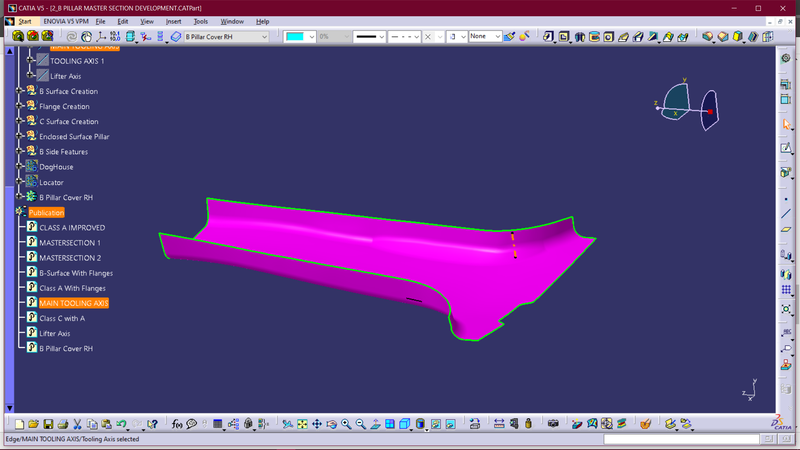
Figure6: Tooling Axis
Side Core Axis or Lifter:
- Some features or walls are difficult to clear by the Main tooling axis itself.
- These features may have negative draft angle or are a part of a sub feature which is an important part and cannot be ignored.
- These features need a different tooling direction for clearing the part in the mold.
- This tooling direction is called Side Core Axis which often tends to clear the sub features or walls at different angle with rwspect to the Main Axis.
- The Pillar Cover requires a Lifter Axis for the clearinf of the Dog Houses which have internal walls that cannot be cleared along main tooling direction.
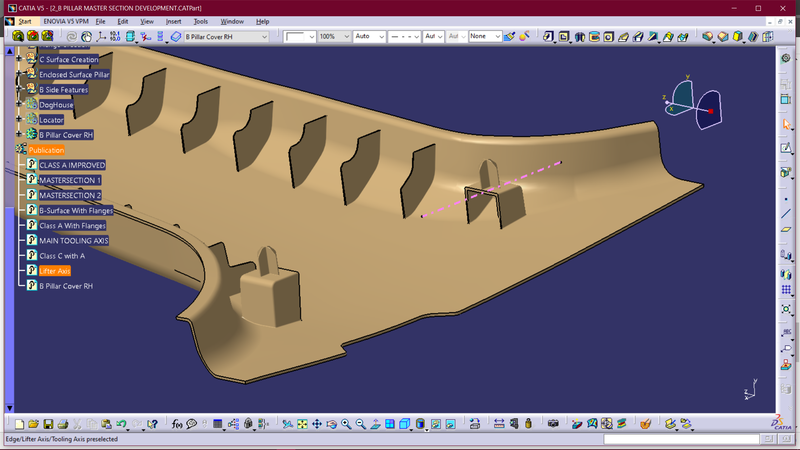
Figure7: Lifter Axis for Dog House Clearing
Draft Analysis:
- Draft Analysis is a tool in CATIA which identifies the zones which deviates from the specified values of angles along a defined draft direction using colour codes.
- It highlights the regions of draft using colours.
- Draft analysis is the first step performed after receiving the Class A of the component.
- Draft analysis should be passed in order to make the plastic component manufacturable.
- Since it is the factor which decides perfect the ejection of part from the Mold.
- Acceptable draft angles are used as range for draft analysis.
- Acceptable ranges are decided before planning to manufacture the product and it may vary from product to product.
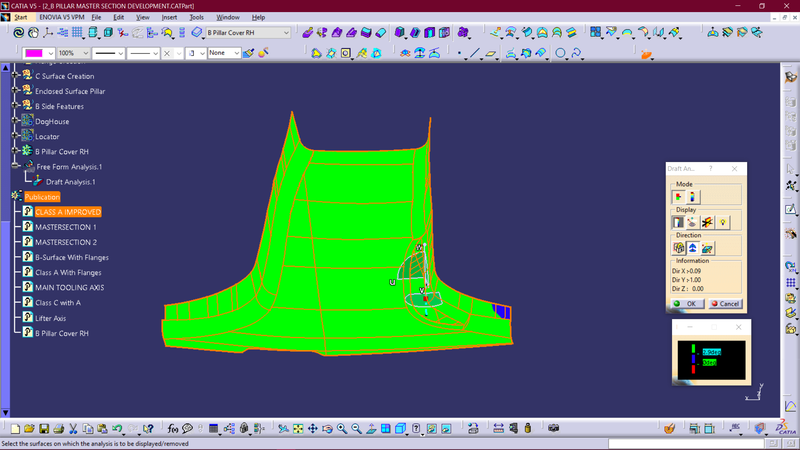
Figure8: Draft Analysis on Class A of B-Pillar RH Cover along Main Tooling Axis.
Class- A Surface:
- In automotive design, a class A surface is any of a set of freeform surfaces of high efficiency and quality.
- It is the visible aesthetic surface of any automotive component.
- Class A surface refers to those surfaces which are visible and abide to the physical meaning, in a product.
- This classification is primarily used in the automotive and increasingly in consumer goods industry.
- It is a requirement where aesthetics has a significant contribution.
- For this reason, the exterior of automobiles is deemed Class-A.
Class- B Surface:
- Class B surfaces are Engineering Surfaces which are invisible to the eyes or often on the back side of the Class A surfaces.
- It is mainly the thickness of the component or Class A.
- These surfaces need to be designed as per the Class A surface i.e., the continuity, thickness of the component, functionality etc should be maintained.
- These surfaces include the main engineering features such as Screw bosses, Ribs, Snaps, Stiffeners and fixations.
- B surfaces also do not contain any aesthetic styling content and textures since it is not visible to eyes.
Class- C Surface:
- Class C surfaces are connectors between Class A and B surfaces.
- This surface connects both A and B surfaces along the Tooling Axis.
- It contains the draft as per the design.
- It is basically the thickened surface between both A and B surface.
- Below Figure 9 shows class A,B and C surfaces: Purple surface is Class A, Brown surface is Class B and Red surfaces are Class C surfaces.
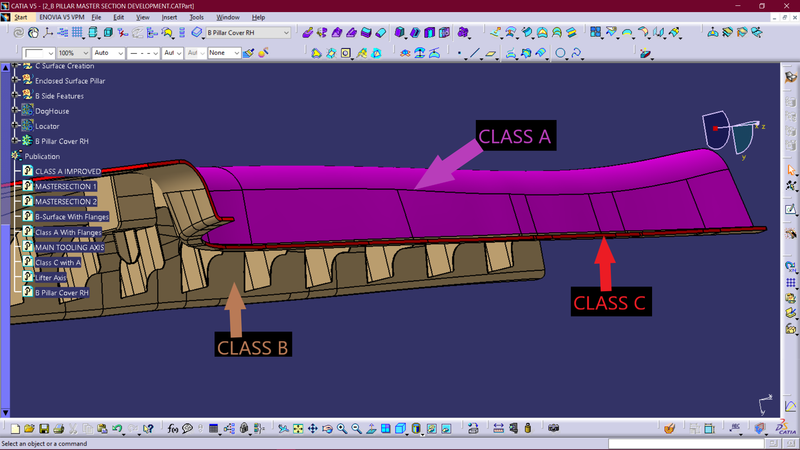
Figure9: Depiction of Class A, Class B and Class C surfaces
Master Sections:
- During the period of Vehicle Concept Design, the evaluation of master section performance mostly depends upon reference vehicle data and experience of structural design engineers.
- Master Sections are created at the Concept Validation and Feasibility Check Stages.
- Each Sub Assembly is provided with a section view of the member which it is going to assemble into.
- These Sections help create a part from Class A of the sub assembly components.
- It helps decide the thickness of the Component, the location and thickness of B side features such as Dog House, Locators.
- Things decided while creating master sections are:
- Gaps and Flsuhness
- The Feasibility of all components and its environment.
- Feasibility such as Clearances with Driver/Passenger, Clearances with Mechanisms and Clearance with the environment.
- Fixation Strategy of components.
- Once the Master Section is developed it is forwarded to the NPD team to work on 3D Part development.
- In short the Master Sections helps to dedcide the Fixation Strategy, Feasibility, Clearance and the Packagong of the component before working on 3D.
- Figure 10 shows the Master Sections provided as input along with Class A for the B pillar Cover.
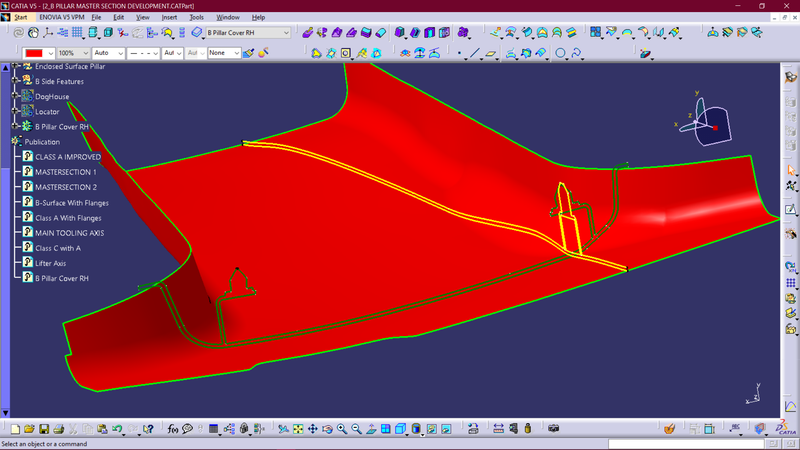
Figure10: Master Sections highlighted in Yellow and Green along with Class A
B-PILLAR COVER RH DESIGN:
Procedure to be followed:
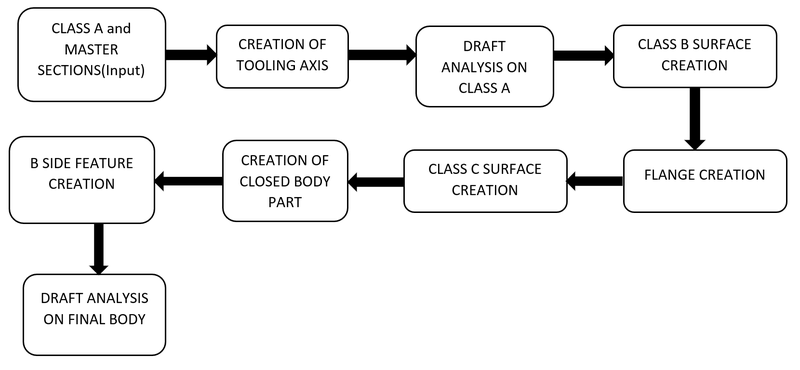
Figure11: Procedure for Design
Step 1: Design Check (Pre Check) on received Class A:
- After receiving the Class-A for the Pillar Cover check for the connectivity of the surfaces on it.
- Use boundary operation and disassemble.
- Check for discontinuous Surfaces.
- The check is over if any discontinuities do not arise.
Step 2: Determine the Tooling Axis:
- Identify faces which can potentially create problems while manufacturing.
- Surfaces at angles along a desired Tooling Axis.
- Extract a plain surface and create a point on its center for Axis system creation.
- In this case Y axis can be a possible Tooling Axis Direction.
- The tooling Axis is created from the Master Sections references.
- Extract the Master Section B features on a plane.
- Use Bisecting Lines and Choose the Main tooling Axis which clears the Draft Analysis.
- In this case the Tool Clearing for X passes the Draft Analysis.
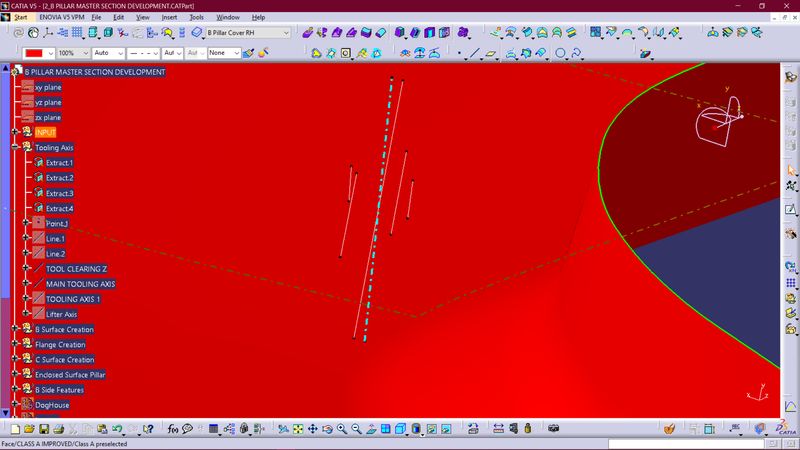
Figure12: Extracts from the Master Sections for the Tooling Axis Creation
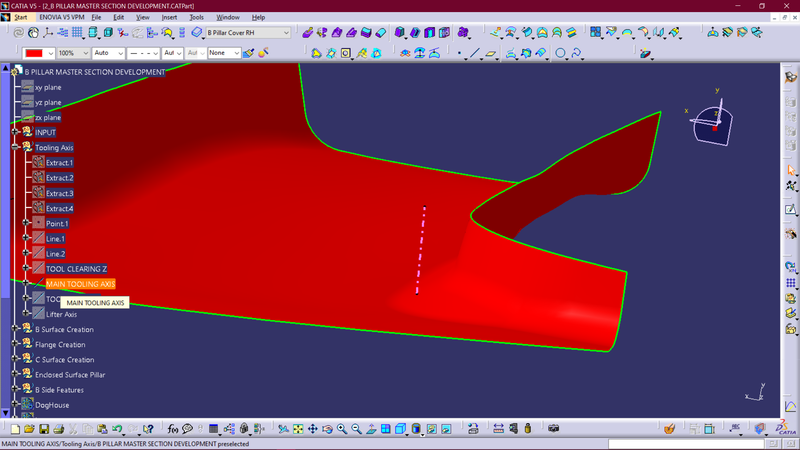
Figure13: Main Tooling Axis
Step 3: Draft Analysis for Class A:
- Change View Mode Customization to Material mode
- Go to INSERT ---> ANALYSIS ---> FEATURE DRAFT ANALYSIS and move the compass to the Tooling Axis.
- Change the range to 2.9º.
- Apply the settings as Shown in Figure 14.
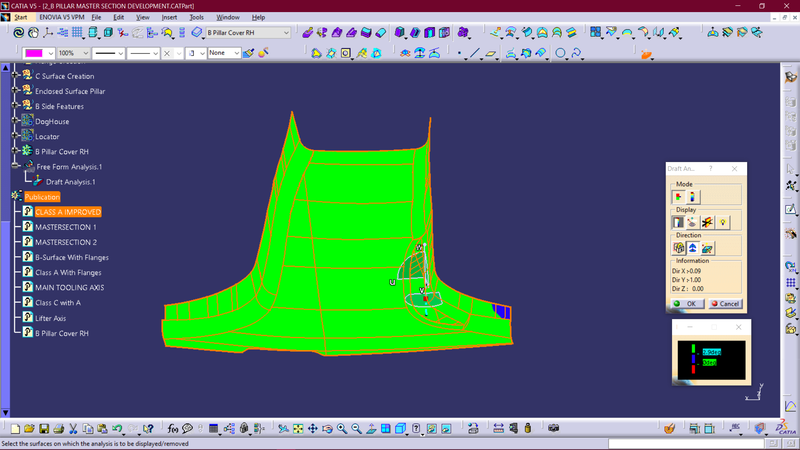
Figure14: Draft Analysis along Main Tooling Axis.
- The Figure15 shows areas which are having around 1º of drafts along the Main tooling Direction
- This is not much of a problem as minimum required draft is 0.5º and the area of consideration is too small.
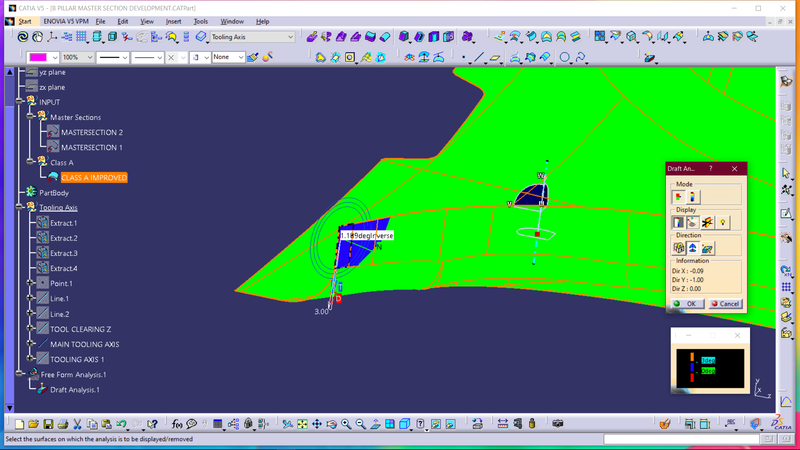
Figure15: Analysis along Main Tooling Axis showing walls having less draft anle.
Step 4: Class B Surface Creation:
- Offset the Class A Surface with the Thickness value of 2mm as per the Master Section.
- For faces which do not offset use Multi Section Surfaces and Splines to fill those gaps.
- Figure 16 shows the Class B surfce.
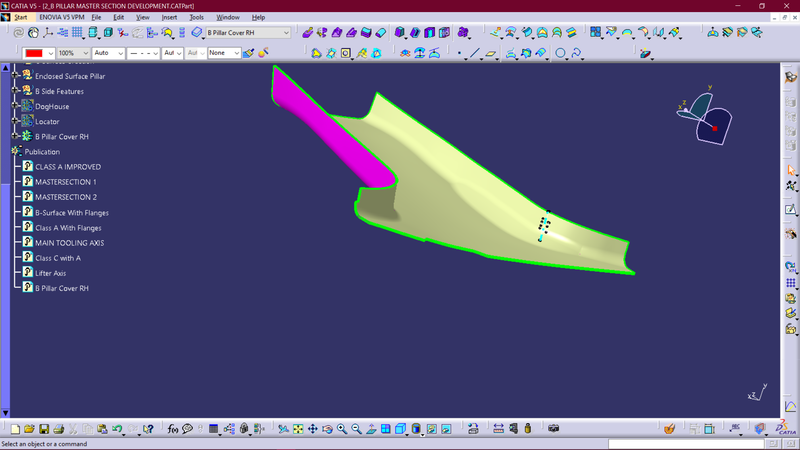
Figure16: Class B Surface in Beige colour.
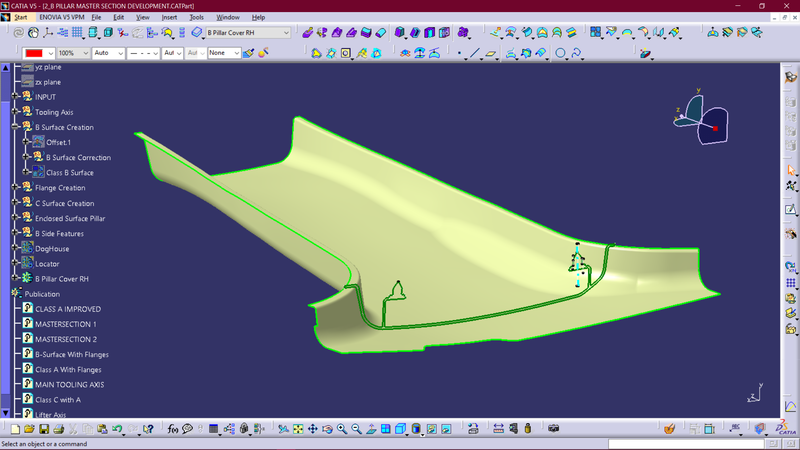
Figure17: Class A surface with Flange.
Step 5: Class C Surface Creation:
- Extract Class A boundary and convert to Smooth Curve.
- Sweep this curve at 3 degress with respect to the Draft Direction.
- Sweep value should be greater than the Thickness required for Part.
- Join the Class A and C.
- The obtained product is shown in Figure 18.
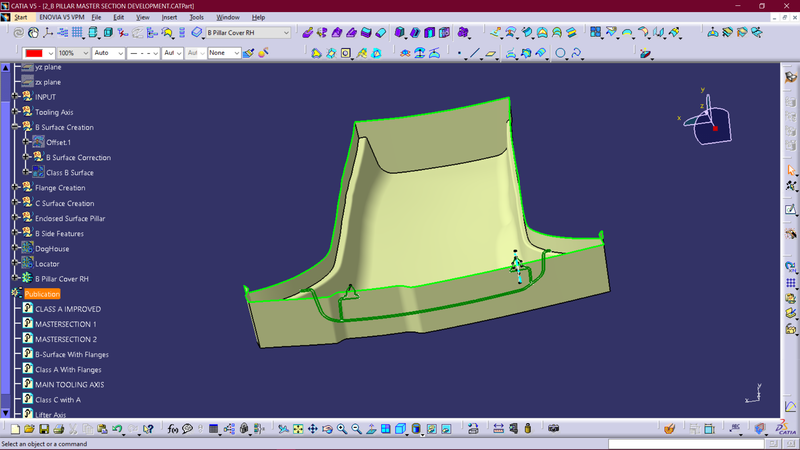
Figure18: Class C surface with Class A.
- Trim the above product with Class B Surface.
- The obtained product is the Enclosed Surface for the B Pillar Cover as shown in figure19
- Switch to Part Design workbench.
- Use Closed Surface Command to Create a Solid Part for the RH B Pillar Cover.
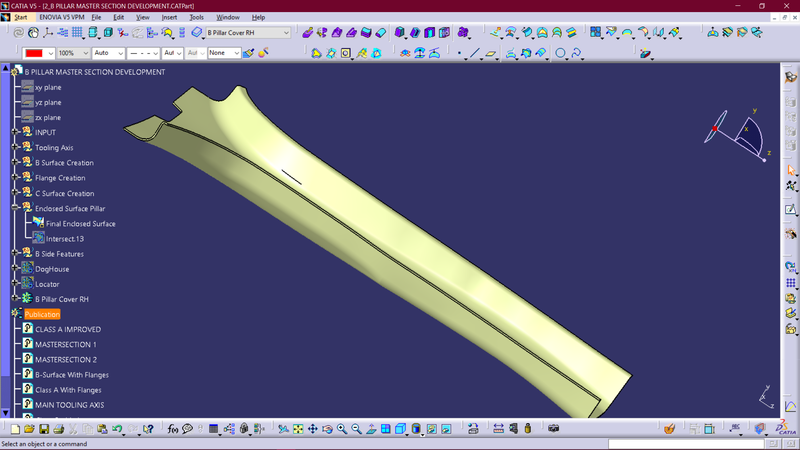
Figure19: Enclosed Surface for B Pillar Cover.
Step 6: B side Feature Creation:
- B side Features suc as Dog House and the 4 way locators to be designed following the Master Section.
- Maintain the Wall thickness with the reference as the Master Section.
- Make sure the Features are drafted along the Main tooling axis.
- Creation for Side /Lifter axis comes into play here.
- Create a Lifter Axis along the X direction and dro draft analysis on the Features.
- Create Ribs 50mm apart from each other following the Rib Design rules.
- Apply appropriate Fillets and Chamfers.
- The Final Component obtained is shown in Figure 20.
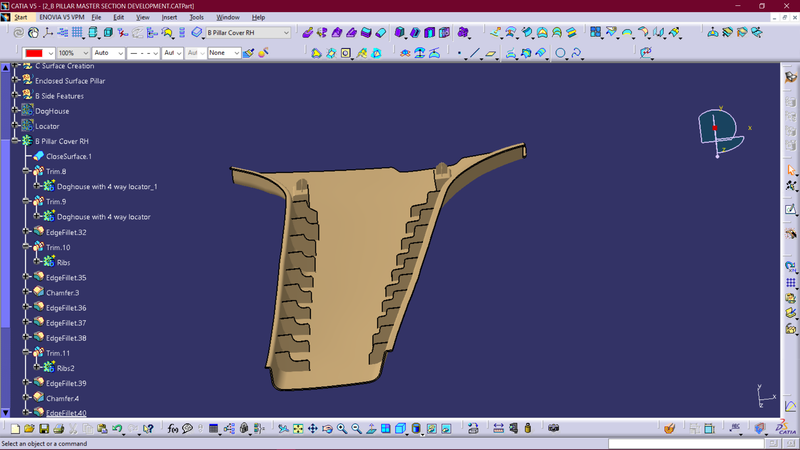
Figure20: Final Component with all the B side Features.
Step 7: Draft Analysis for Final Component:
- Change View Mode Customization to Material mode
- Go to INSERT ---> ANALYSIS ---> FEATURE DRAFT ANALYSIS and move the compass to the Main Tooling Axis.
- Change the range to 0.5º.
- Apply the settings as Shown in Figure 21.
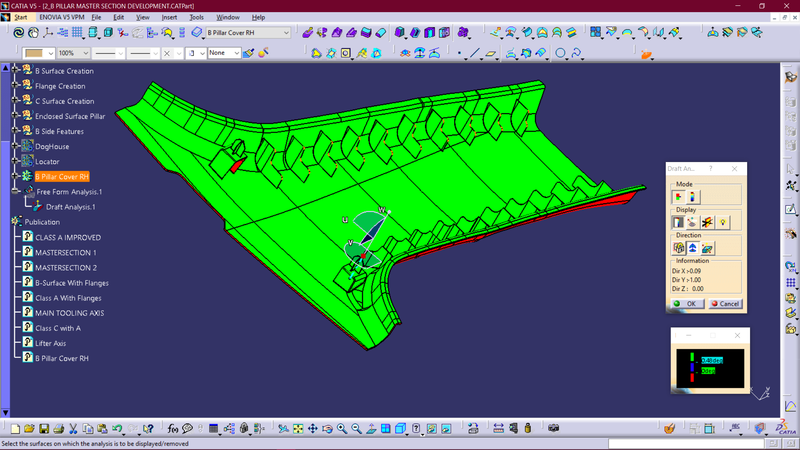
Figure21: Draft Analysis on Final component along Main Tooling Axis.
- Reverse the draft analysis direction for the Clearing of Class A Surface and the C surface walls as shown in Figure 22.
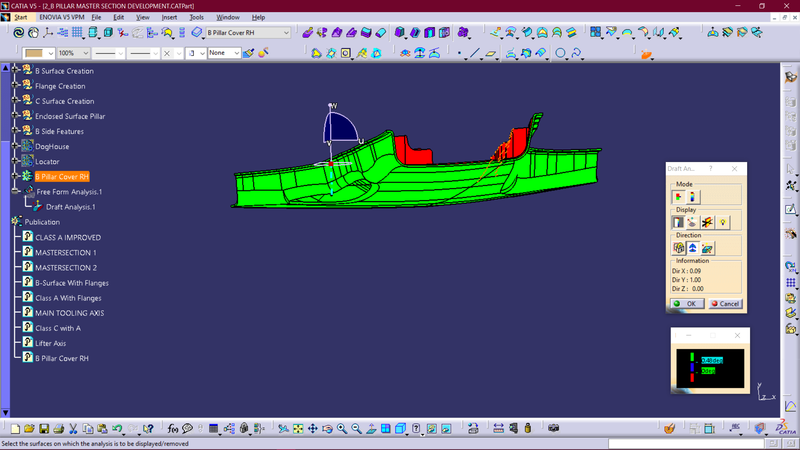
Figure22: Draft Analysis on Final component along Main Tooling Axis for Class A and C surfaces.
- Perform Draft Analysis along the Lifter Axis to check clearance for the inner Walls of the Dog House as shown in Figure 23.
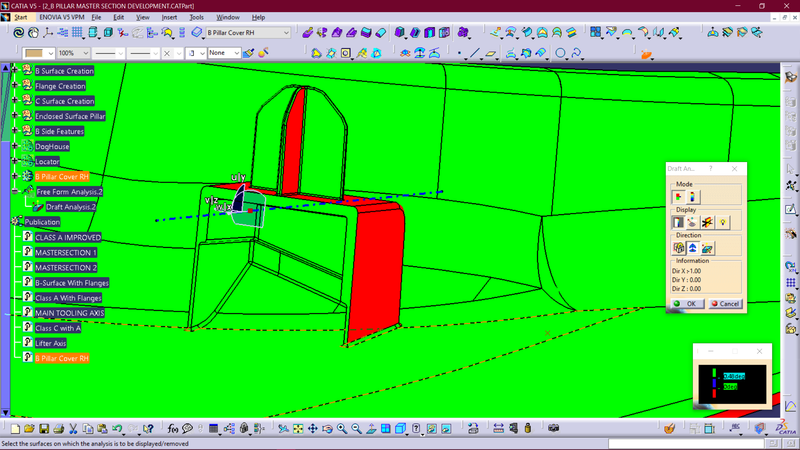
Figure23: Draft Analysis on Doghouse inner Walls.
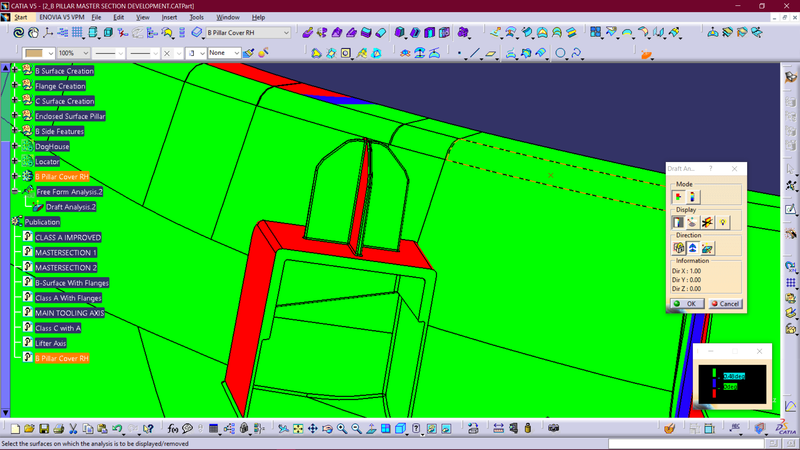
Figure24: Draft Analysis on Doghouse 2 inner Walls.
Conclusion:
The Design of Automotive Plastic Component – B Pillar Cover Class A and Master Sections as input is completed using concepts of Draft angles, Draft Analysis, Determining and implementing of Tooling Axis, Side Core Axis, Class A, Class B, Class C surfaces and Maintaining the Thickness of the part at 2mm and finally converting the enclosed Surface into solid Part along with strenthening and Locating features on B side.