Center Console Coin Holder Design with Rib Design– Automotive Plastic Component
This report demonstrates the design of an Automotive Plastic Component – Coin Holder for Center Console with Ribs using industry principles and Design Rules. Concepts such as Rib Root Thickness, Draft angles, Draft Analysis, Determining the Tooling Axis, Class A, Class B and Class C surfaces. The component is designed to manufacture maintaining a wall thickness of 2.5mm using Surface Design and Solid Design techniques in CAD package CATIA V5.
Figure1: Coin Holder
Design Rules for Plastic Components:
- Nominal wall thickness of a plastic component is 3mm. For a strength component such as Instrument Panel, Bumper , door trims the values of thickness are larger than 4mm. For example, Thickness of IP may lie between 5-6mm, for Bumper it may be 6-8mm. For smaller components the thickness may be between 2-3mm as in this case of Coin Holder.
- Deviation of `30% from the wall thickness is allowed with gradual increase or decrease to avoid any plastic defects while manufacturing. For example: A component having wall thickness 3mm should deviate within the range of 2.1 mm minimum and 3.9 mm maximum.
- Ideal draft angle should be 3º for the overall component along for the faces lying in the tooling direction.
Ribs Design:
- Rib is a B-Side Engineering feature which provides a means to economical Stiffness and Strength in Plastic Molded parts without increase in overall wall thickness.
- Rib also facilitates locating and arresting components of an assembly.
- It provides alignment in Mating Parts.
- It acts as Stop and Guides for Mechanisms.
Guidelines For Rib Design:
- Proper Rib design is necessary to avoid plastic defects which involves the following critical issues that needs to be considered which are:
- Draft angle
- Rib Thickness at base
- Thickness at Top of the Rib
- Rib Height
- Location of Ribs and Spacing between 2 Ribs
- Optional Radius or Fillet Radius
- Rib Root Diameter
- Quantity of Ribs
- Manufacturability
- These guidelines are separate for Show and No – show surfaces.
- The below table gives specific values for both cases.
- Consider ‘t’ as wall thickness of base for component.
Table1: Rib Design Guidelines
Rib Specification
|
No-Show Surfaces
|
Show Surfaces
|
Draft Angle
|
Min 0.5º per side,
Recommended 1.5º per side
|
0.5º per side
|
Rib Thickness at Base (w)
|
0.5 * t
|
0.4 * t
|
Rib Thickness at top
|
Min 0.75mm
|
Min 0.75mm
|
Rib Height (y)
|
Max 5*t
|
Max 5*t
|
Spacing Between 2 Ribs (x)
|
2*t
|
2*t
|
Fillet Radius (r)
|
0.125*t
|
Max 0.25mm
|
Rib Root Dia
|
± 30 % of t
|
± 30 % of t
|
y/x ratio for multiple ribs
|
3:1
2:1 preferred
|
3:1
2:1 preferred
|
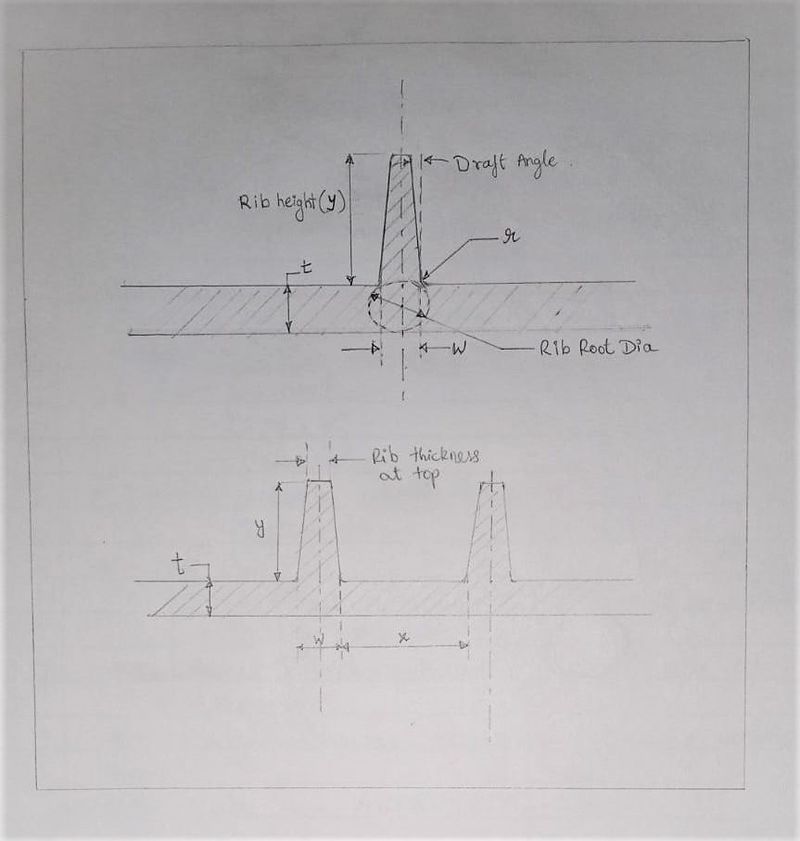
Figure1.2: Rib Design Nomenclature
Screw Boss Design:
- Screw Bosses are Class B side engineering features which find use in many part designs as point for attachment and assembly.
- Most common variety consists of cylindrical projections with holes designed to receive screws, threaded inserts or other types of fastening hardware.
Guidelines For Screw Boss Design:
- To reduce stress concentration and potential breakage the bosses must have blended radii rather than sharp edges at the base.
- Larger radius reduces stress concentration but also increases chance for sink or void.
- Specifying smaller screws or inserts often prevents overly thick bosses.
- Normally, the boss hole should extend the base wall level even if the full depth of is not needed for assembly.
- Shallow holes can lead to thick sections at wall resulting in sink marks or voids.
- Deep holes lead to thin walls which are difficult to fill during molding.
- Because of draft requirement the tall bossed (>5 x outer diameter of Boss) can create filling problem at their top or thick section at the base.
- Proper Boss design is necessary to avoid plastic defects which involves the following critical sections and design rules that needs to be considered:
- Draft angle
- Thickness at base (w)
- Height/Diameter Ratio (H/D)
- Optional Radii for fillets (r)
- Boss Gussets or Ribs for support
- Root Diameter
- Planning ahead for type of Ejection
- The figure 1.3 shows the critical sections.
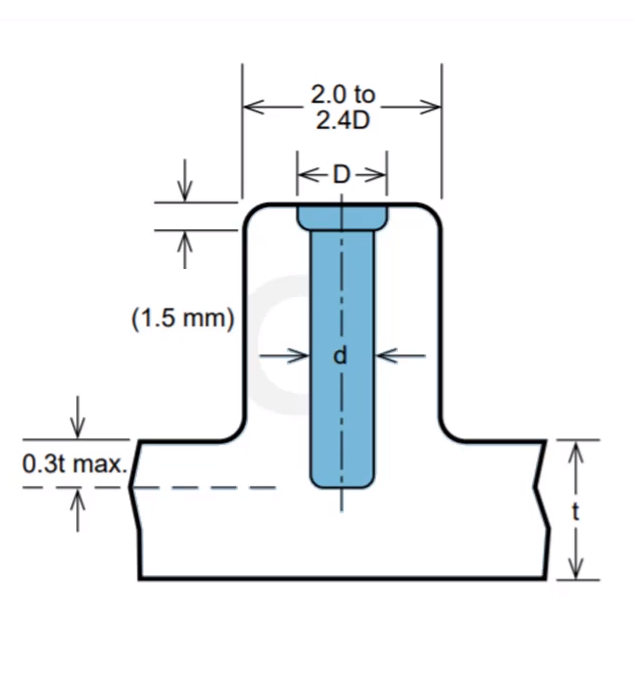
Figure1.3: Screw Boss Design critical Sections
- Design Rules considering above critical sections are as follows:
- Thickness (w) = 0.6 x t.
- Should be measured at base.
- Should be measured at the tangent of the fillet.
- Larger base area could lead to higher heat retention.
- Retained heat could lead to higher shrinkage.
- Optional Radii (r) = 0.25mm Max.
- Must not violate `40% thickness requirement for the base thickness.
- Draft = 5º on both inner and outer walls.
- Different rule used for Sleeve ejection that needs to be planned for
- H/D ratio should be 3:1 or 2:1
- Boss Gussets should meet Rib Design Rules
- Planning for Ejection:
- If height of Boss < 25mm then draft is not required when sleeve ejection is used.
- If height of Boss > 25mm then draft should be done only on outside wall for sleeve ejection.
- If Sleeve Ejection is not used then draft of 0.5º is required on all walls.
- If Boss Wall thickness must exceed the recommended ratio, consider adding recess around the base of the boss to reduce the severity of sink.
- Avoid bosses that merge into the side walls because they can form thick sections that lead to sink marks. Instead position the bosses away from the side walls, and if needed connect it with ribs as shown in Figure 1.4.
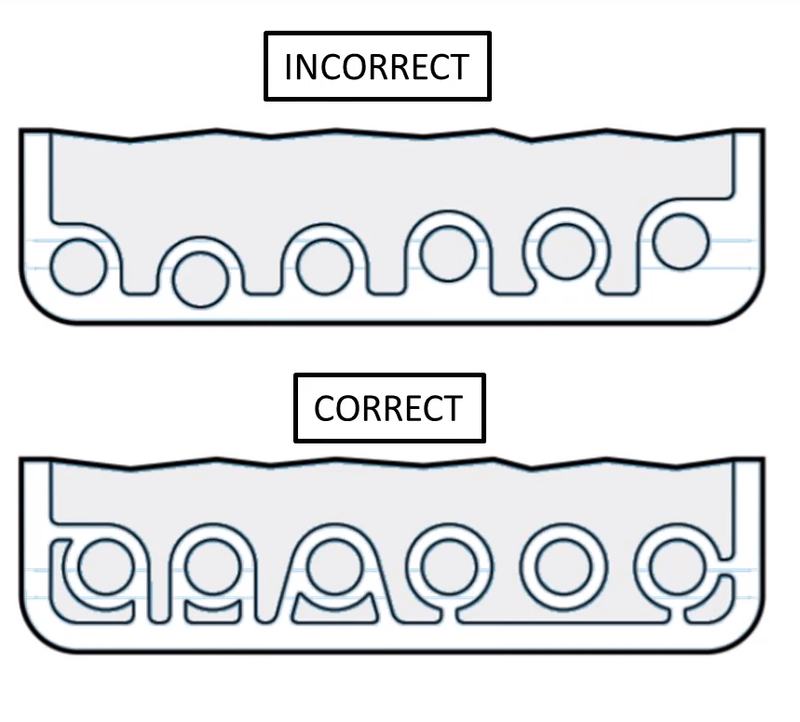
Figure1.4: Screw Bosses near walls.
Dog House Design:
- Dog House is a B surface engineering feature used to avoid sink marks primarily.
- Its secondary use is to place an offset B side feature such as boss or locators on it.
- The cross section for dog house near the B surface is less and then increases rapidly.
- It can be extended to have another feature on it.
- Also, if Bosses are perpendicular to the B surface Dog houses are used to place it.
Guidelines and Design rules for Dog House:
- Proper Dog House design is necessary to avoid plastic defects which involves the following critical sections and design rules that needs to be considered:
- Draft angle
- Doghouse Walls Section
- Part Surface
- Bottom of Doghouse
- Wall Thickness
- Height and Width
Figure1.5: Dog house wall section.
- B = 3 to 6mm, C <= 0.4 x T
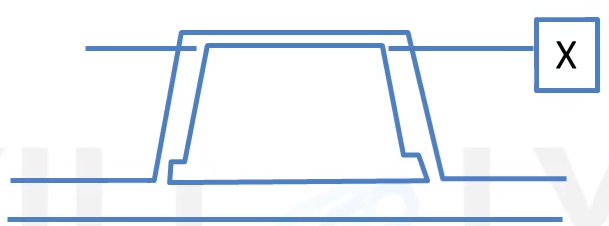
Figure1.6: Dog house width.
- Dog House width (X) = 12mm Minimum
- Height (H) = 6mm Minimum
- X/H = 3:1 or 2:1
- Draft of 5º minimum to draw direction, if slide is considered then this can change to 3º minimum.
The terms are briefly explained below:
Draft:
- Draft is an angular tapering given at the design stage to every Plastic Component that has to be manufactured.
- It is given in the direction of the Mold Movement.
- The Draft allows the parts to release easily from the mold without creating friction between the surface of component and the core and cavity plates.
- When a Plastic component cools down inside the mold, the natural tendency of it is to shrink and attach to the core or cavity half.
- The movement of mold opening causes friction on the walls of the component as well as the core/cavity blocks.
- This reduces the life of the mold as well as the component itself.
- The component may also have rough surface finish as well as weak structure due to this.
- This problem can be solved by giving draft to the component.
- Most applications require minimum draft angles of around 0.5º to 1º , however 3º draft angles are widely accepted for cost saving purpose.
- 7º Draft angles are given to textured surfaces like Instrument Panels.
- Minimum possible draft angles are given to screw bosses, ribs and stiffeners due to their critical nature.
- Walls having 0º or negative draft are difficult to manufacture thus, are required to redesign from the Class A stage.
Figure2: Draft Angles
Tooling Axis:
- Tooling Axis is the direction in which the Mold opens and closes.
- Part Drafts are given along this axis.
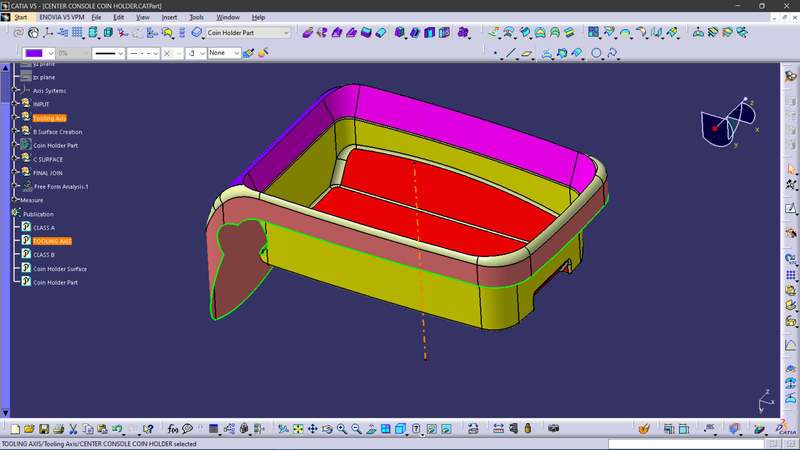
Figure3: Tooling Axis
Draft Analysis:
- Draft Analysis is a tool in CATIA which identifies the zones which deviates from the specified values of angles along a defined draft direction using colour codes.
- It highlights the regions of draft using colours.
- Draft analysis is the first step performed after receiving the Class A of the component.
- Draft analysis should be passed in order to make the plastic component manufacturable.
- Acceptable draft angles are used as range for draft analysis.
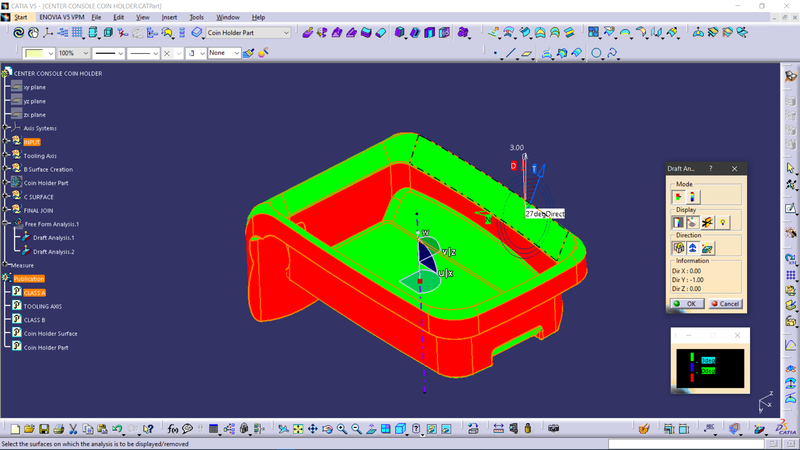
Figure4: Draft Analysis showing one of the faces having acceptable 27º draft angle
Class- A Surface:
- In automotive design, a class A surface is any of a set of freeform surfaces of high efficiency and quality. It is the visible aesthetic surface of any automotive component.
- Class A surface refers to those surfaces which are visible and abide to the physical meaning, in a product.
- This classification is primarily used in the automotive and increasingly in consumer goods industry.
- It is a requirement where aesthetics has a significant contribution.
- For this reason, the exterior of automobiles is deemed Class-A.
Class- B Surface:
- Class B surfaces are Engineering Surfaces which are invisible to the eyes or often on the back side of the Class A surfaces.
- It is mainly the thickness of the component or Class A.
- These surfaces need to be designed as per the Class A surface i.e., the continuity, thickness of the component, functionality etc should be maintained.
- These surfaces include the main engineering features such as Screw bosses, Ribs, Snaps, Stiffeners and fixations.
- B surfaces also do not contain any aesthetic styling content and textures since it is not visible to eyes.
Class- C Surface:
- Class C surfaces are connectors between Class A and B surfaces.
- This surface connects both A and B surfaces along or angled to the Tooling Axis.
- It contains the draft as per the design.
- It is basically the thickened surface between both A and B surface.
- Below Figure 5 shows class A,B and C surfaces: Purple surface is Class A, Cyan surface is Class B and Red surfaces are Class C surfaces.
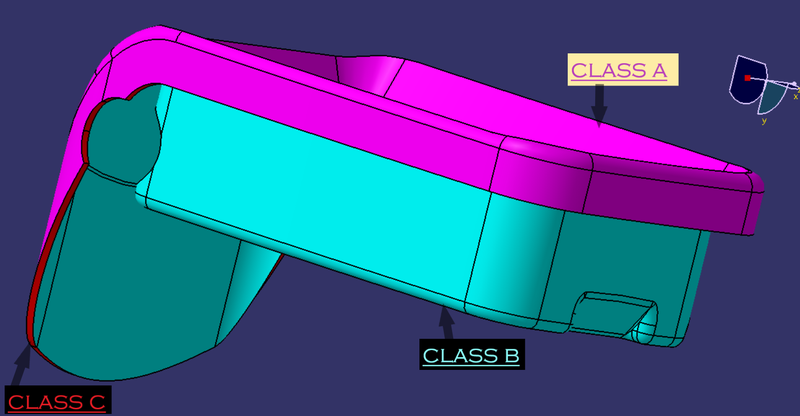
Figure5: Depiction of Class A, Class B and Class C surfaces
COIN HOLDER DESIGN:
Procedure to be followed:
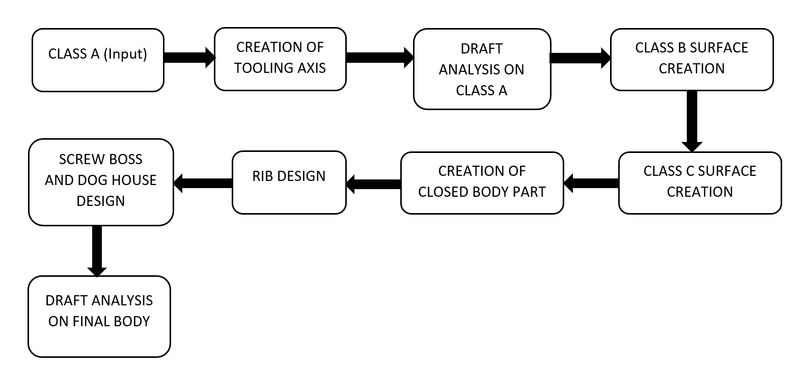
Figure6: Procedure in designing Coin Holder
Step 1: Design Check on received Class A:
After receiving the Class-A for the Coin Holder check for the connectivity of the surfaces on it. Use Join operation, boundary operation and disassemble. The check is over if any discontinuities do not arise. Delete the operations after the check.
Step 2: Determine the Tooling Axis:
- Identify faces which can potentially create problems while manufacturing.
- Surfaces at angles along a desired Tooling Axis.
- Extract a plain surface and create a point on its center for Axis system creation.
- In this case Y axis can be a possible Tooling Axis Direction.
- The highlighted coloured faces can be a problem in terms of draft analysis Figure 7 demonstrates the steps.
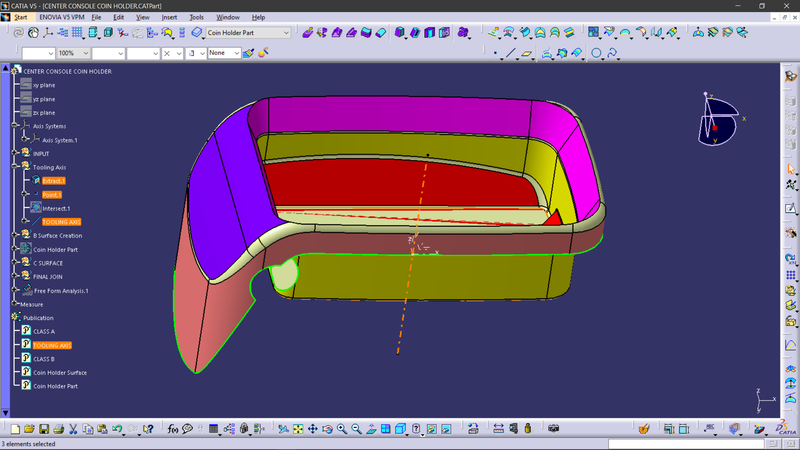
Figure7: Base Extract, Highlighted Faces for Draft Analysis and Tooling Axis
- Intersect the YZ Plane with the Class A.
- Since Most of the Faces from the Intersect are either parallel or at 90º or having comfortable draft angles, the Tooling Axis will be created in direction normal to the Base surface along the origin of the Axis System.
- It is shown in Figure 8 and 9.
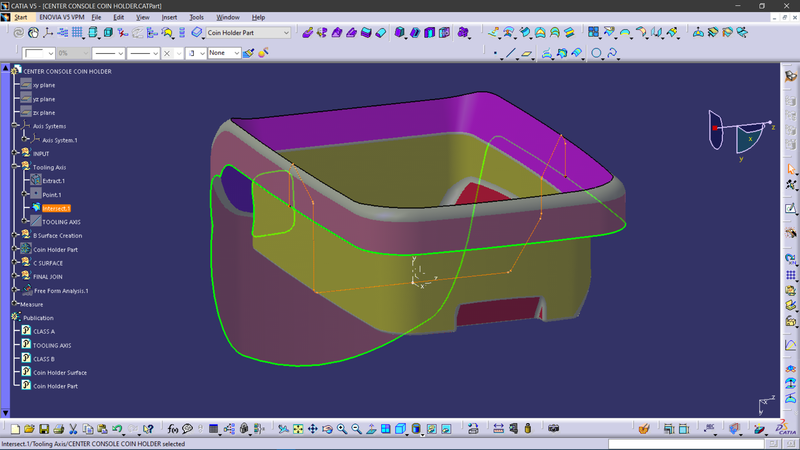
Figure8: YZ plane sketch for Tool Clearing for Y.
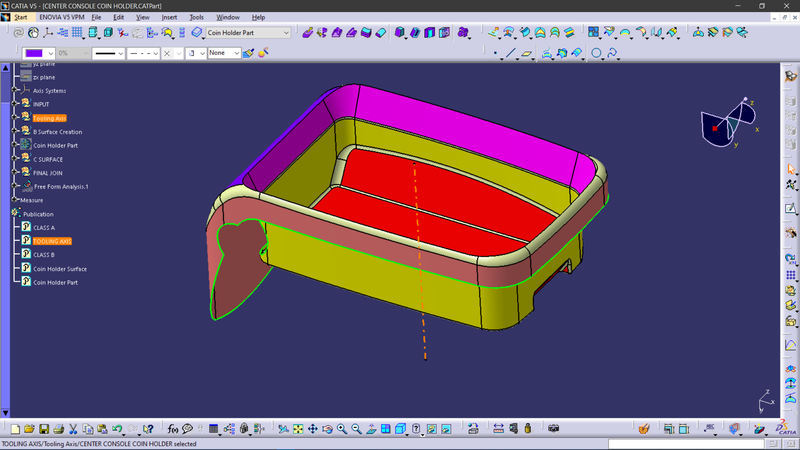
Figure9: Tooling Axis.
- Publish the Tooling Axis as well as the Class A for easy access using Insert ---> Publication as shown in Figure 10.
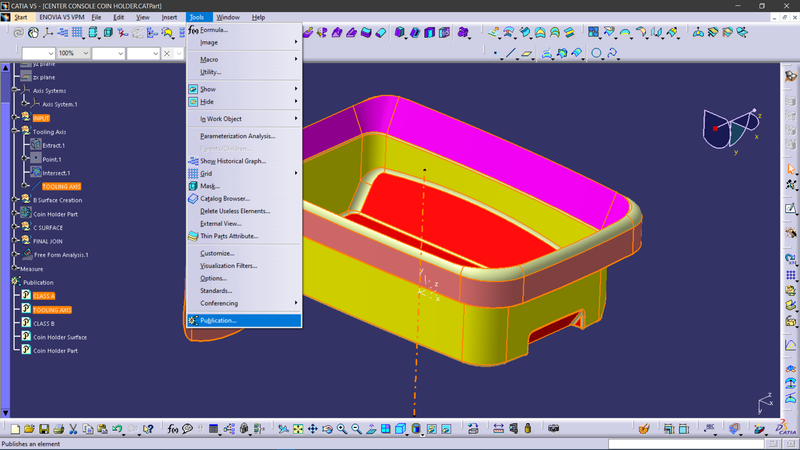
Figure10: Publication of Tooling Axis and Class A surface.
Step 3: Perform Draft Analysis on Class A Surface:
- Change View Mode Customization to Material mode
- Go to INSERT à ANALYSIS à FEATURE DRAFT ANALYSIS and move the compass to the Tooling Axis. Change the range to 3º. Apply the settings as Shown in Figure 11.
- As shown the target area has 27º draft angle on a face.
- The input Class A also has walls having negative angle to the tooling axis and some having 0º too.
- This can be an issue while manufacturing the component as it would be very difficult to draw from the molds.
- So, this design needs to be reconsidered at the Class A Styling stage where improvising on the draft angles is required.
- Minimum positive drafts can be considered while styling after which it can be considered to be thickened and manufactured.
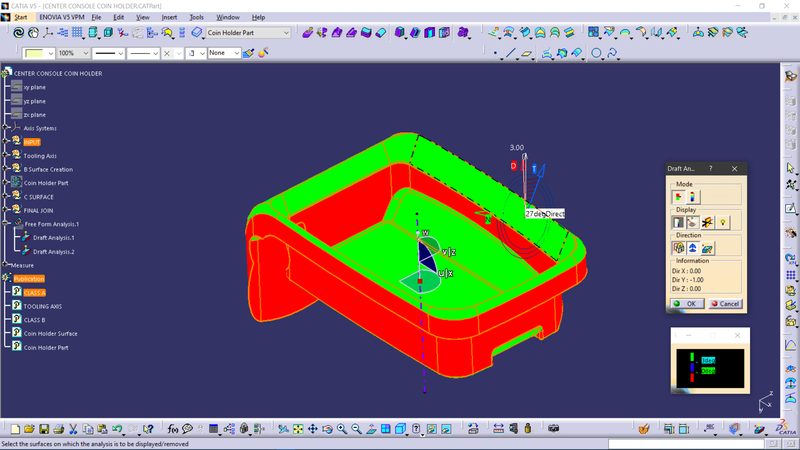
Figure11: Draft Analysis on Class A of Coin Holder.
Step 4:Class B Surface Creation:
- Extract the relevant surfaces from Class-A surface which excludes the Fillets and holes.
- Here the selected faces consist of Side Walls, Base, Top Walls and External Flange surfaces.
- Extract of these surfaces is shown in the Figure 12.
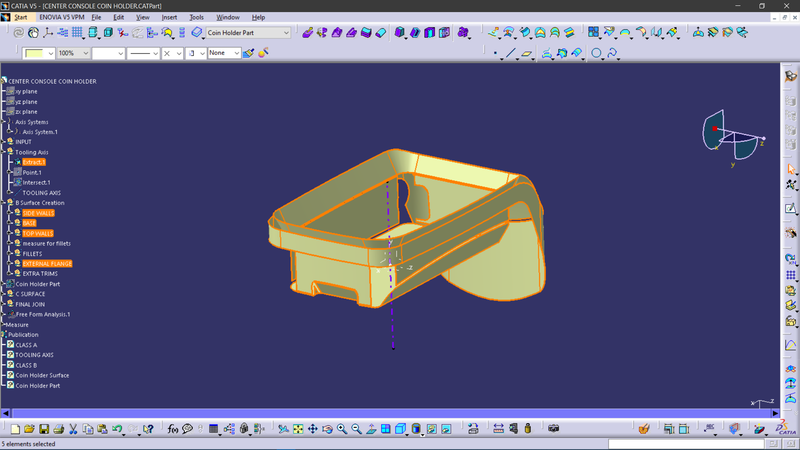
Figure12: Extract of surfaces from Class A of Coin Holder.
- Use Untrim Command to untrim the extracted surfaces and create a natural extend.
- It is shown in Figure 13.
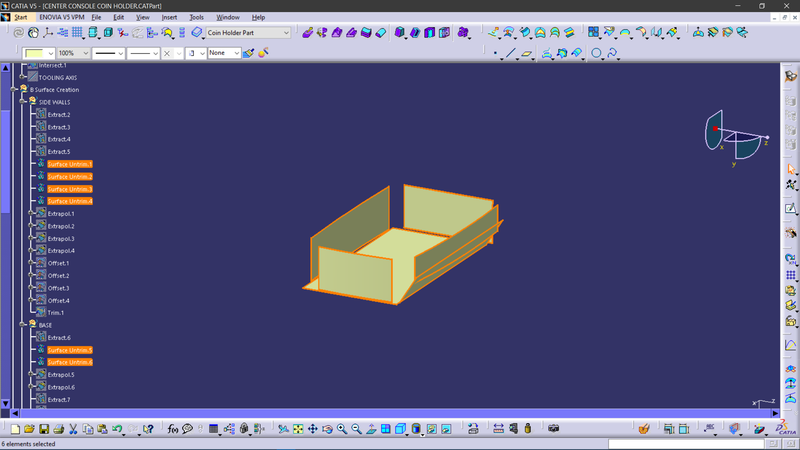
Figure13: Untrim of Extracted Surfaces.
- Extrapolate the untrimmed surfaces so that each of them intersects clearly and pass way forward than the Class A which will help in its trimming in further operations.
- The operation is shown in Figure 14.
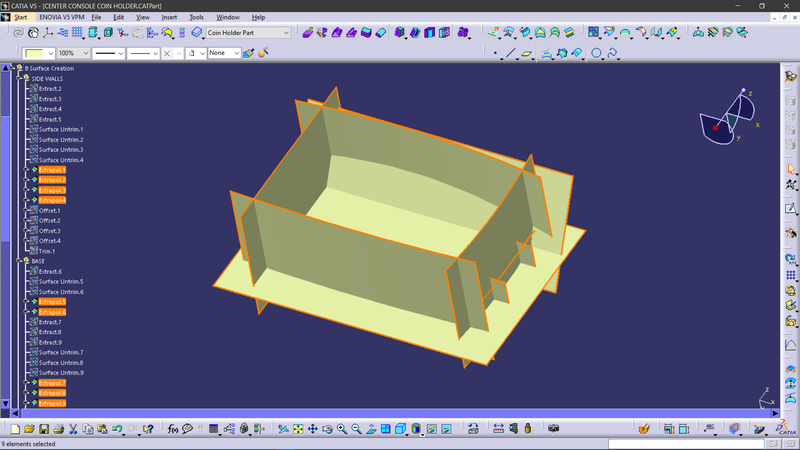
Figure14: Extrapolated Surfaces created from Untrimmed Surfaces.
- Offset the extrapolated surfaces to the value of required Thickness of the Part.
- In this case of Coin Holder, the thickness value is 2.5 mm.
- The offset faces are the part of B-Surface.
- The operation is shown in Figure 15.
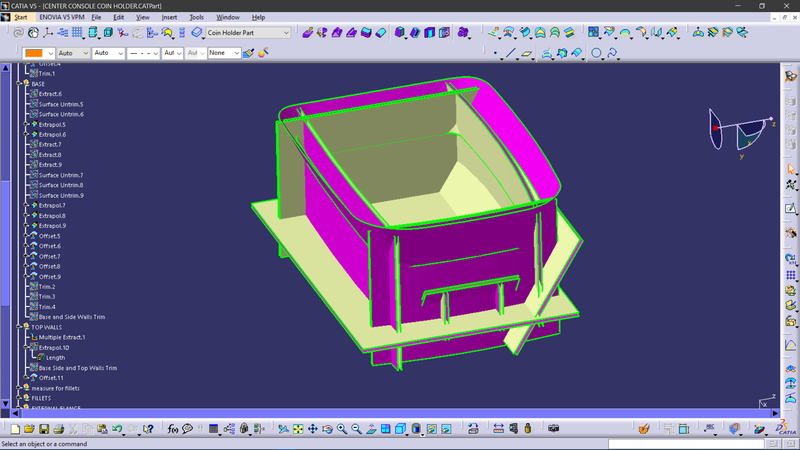
Figure15: Offset highlighted in Purple.
- Trim the extra surfaces to obtain similar extended surfaces as in Class A.
- The surface obtained after trim is shown in Figure 16.
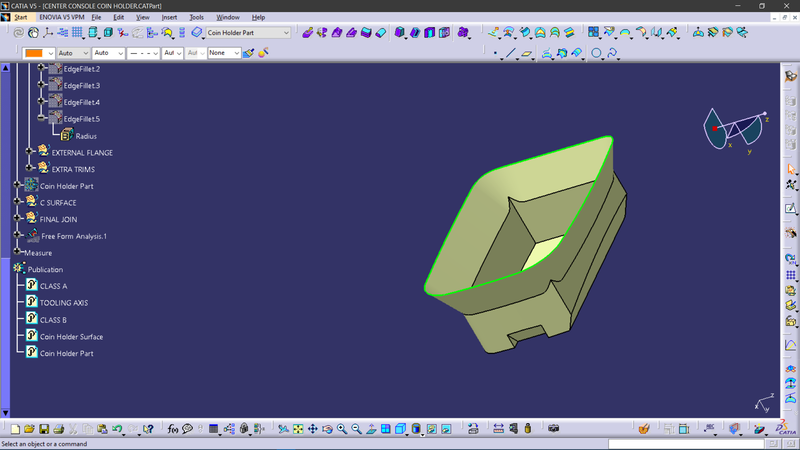
Figure16: Surface obtained on Trimming of Extrapolated Surfaces.
- Create Fillets while maintaining the part thickness between the Class A and Class B surfaces.
- The Value of Fillet is given by the equation (B surface fillet = A surface fillet ` Thickness of the Part).
- The sign + or – must be decided so as to maintain the part thickness which in this case is 2.5mm.
- The operation is shown in Figure 17.
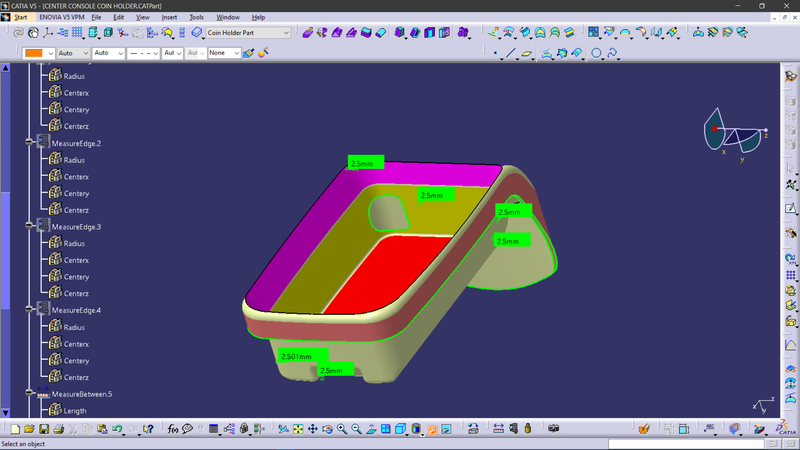
Figure17: Fillets to be created as per the Part Thickness (in this case 2.5mm).
- The obtained surface is the required Class B Surface highlighted in Light Brown as shown in Figure18.
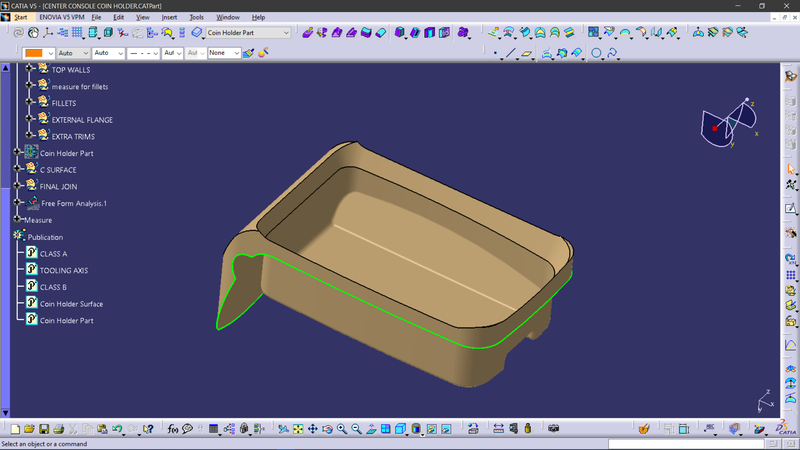
Figure18: Class B surface of Coin Holder highlighted in Light Brown.
Step 5: Class C Surface Creation:
- Use Boundary Feature to extract the outer boundary of the Coin Holder Class A surface in Figure 19.
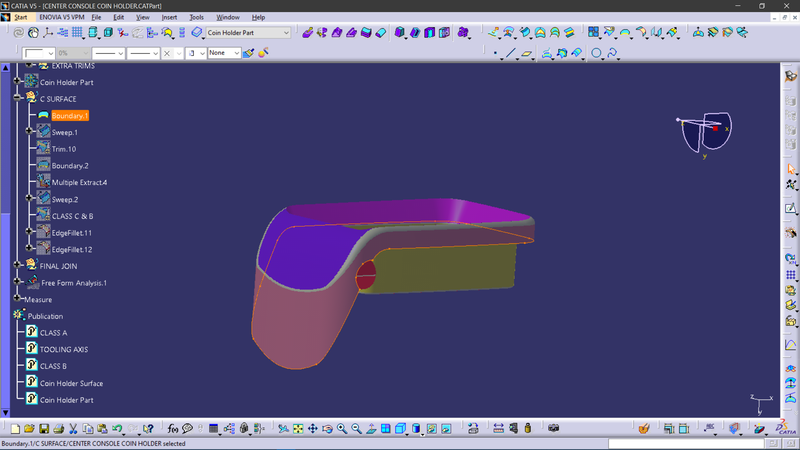
Figure19: Boundary for Class A of Coin Holder.
- Use Sweep Operation to extrude the boundary using the ‘With Reference Surface’ option and selecting the boundary for Guide curve and the Multiple extract of External Flange Walls as Reference Surface.
- Use angle as 90º and select inward direction i.e., towards B surface with appropriate length say 4mm as shown in Figure 20.
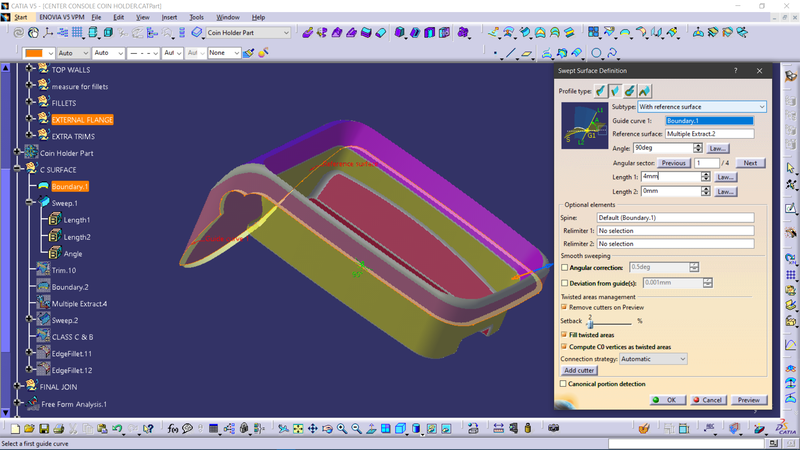
Figure20: Sweep operation for C Surface.
- Use similar Boundary and Sweep option for the Cut Section in the coin holder.
- Multiple extract the reference surfaces and sweep outwards 90º to the extract towards B surface as shown in Figure21.
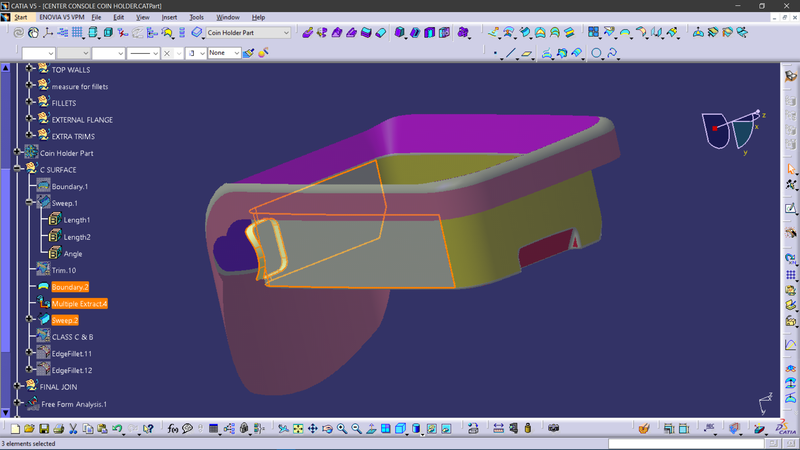
Figure21: Class C surface for Cut section.
Step 6: Final Closed Surface Creation:
- Join all the Swept surfaces along with the Class B Surface.
- The Final trim should be one single Surface Entity without any gaps as shown in Figure 22.
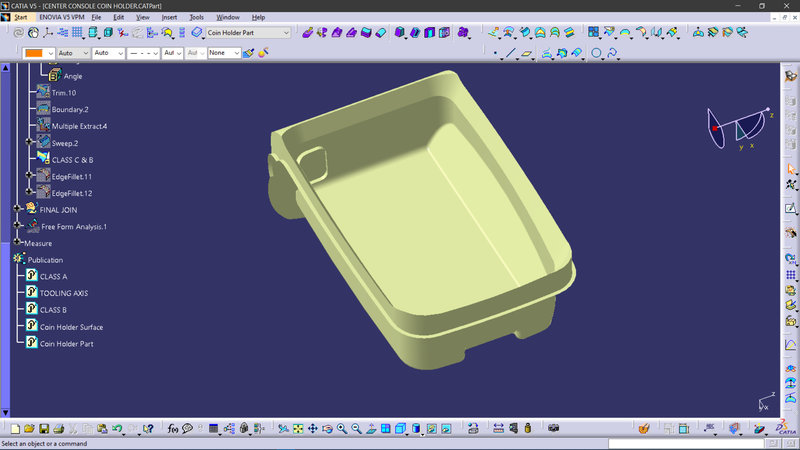
Figure22: Final trim of Class B and Class C surfaces.
- Join the Final Trim Surface with the Class A surface to obtain the final enclosed Surface for the Coin Holder as shown in Figure 23.
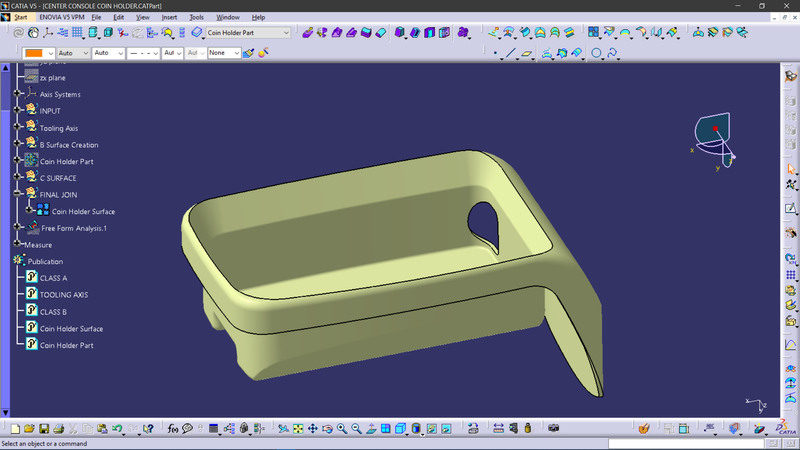
Figure23: Final Closed Surface for Coin Holder.
Step 7: Create a Closed Body Part from Final Closed Surface:
- Switch to Part Design Workbench and use Closed Surface option to create a Solid Part from the final obtained surfaces.
- The part created is the required Coin Holder designed from a Class A.
- The obtained solid Part is shown in Figure 24.
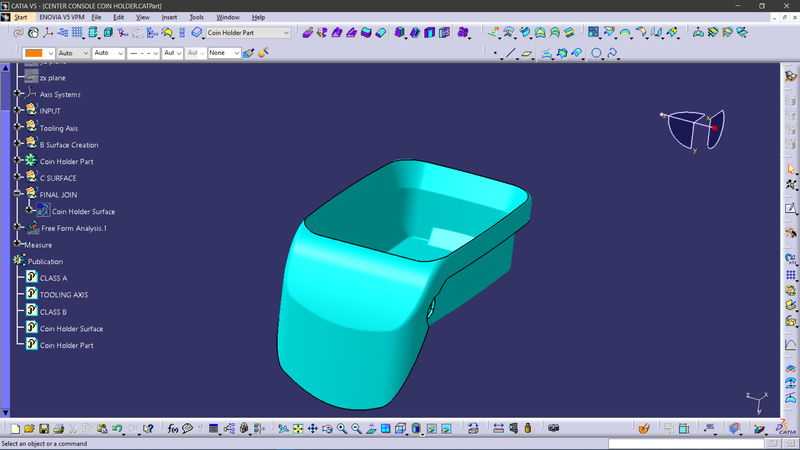
Figure24: Final Closed Surface - Part of Coin Holder.
Step 8: Rib Design for the B side:
- In generative Shape Design Workbench, Extract the base from B Surface and Create a Plane on it as shown in Figure 25.
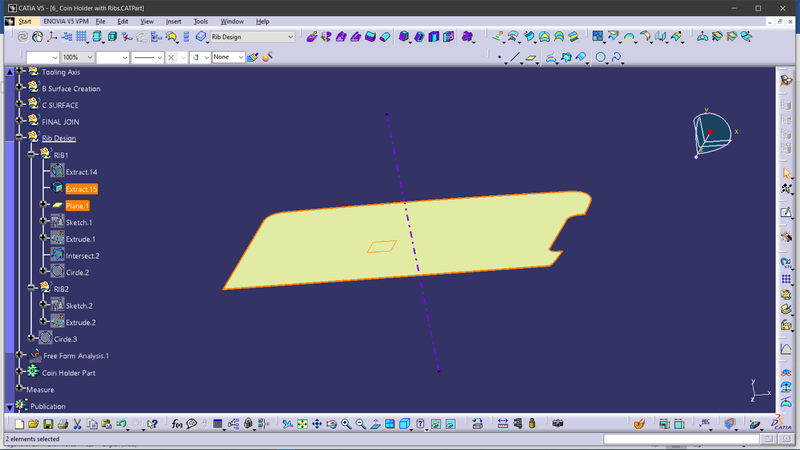
Figure25: Extract of base of B surface and Plane Creation on it.
- Create a Sketch on the Plane for the rib as shown in Figure 26
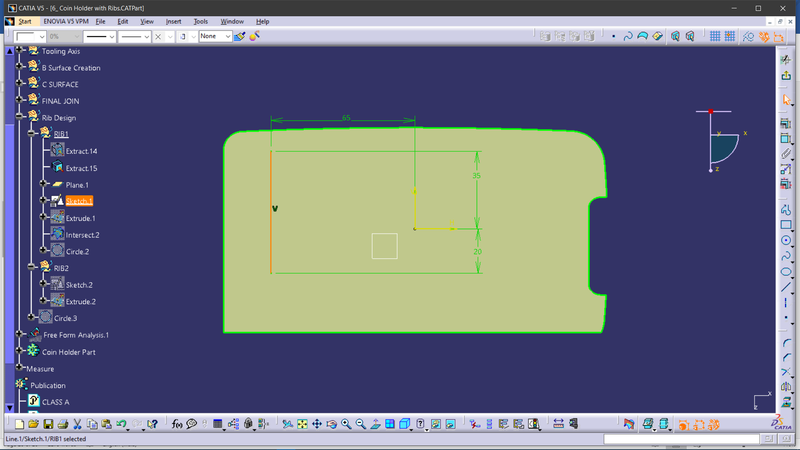
Figure26: Sketch for Rib.
- Extrude the sketch to the value of 12.5mm following the Design rule of Height of Rib <= 5 x thickness of base = (5 x 2.5 = 12.5mm).
- Also extrude it 1 mm below the surface so that it intersects the base.
- Extrude shown in Figure 27.
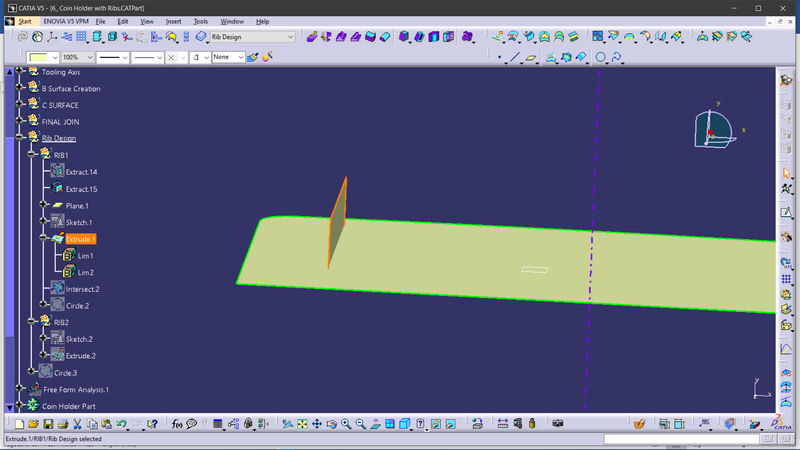
Figure27: Extrude for Rib.
- Switch to part design workbench and thicken the rib to a base thickness value as per design rule.
- Thickness should be 0.5 times the base wall thickness (i.e., 0.5 x 2.5 = 1.25mm).
- Thicken it 0.75mm on each side.
- Thicken shown in Figure 28.
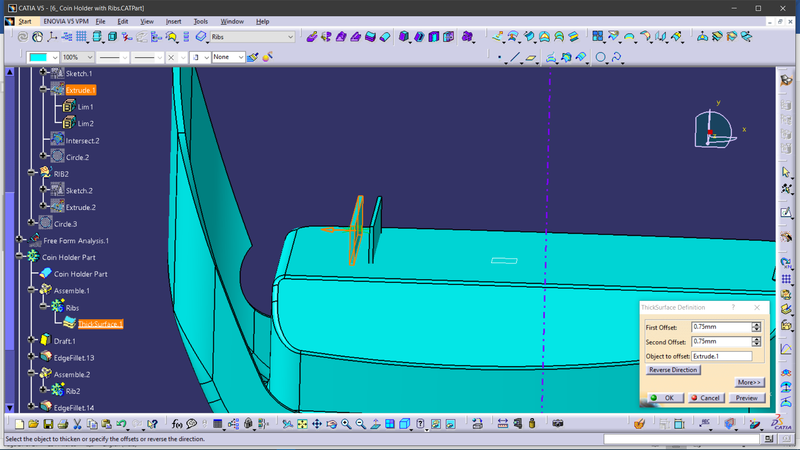
Figure28: Thicken For 1st Rib.
- Assemble the Rib to the main Coin Holder Part.
- Use draft of 0.5º on all the walls which are along the Tooling Direction.
- Also give fillets of 0.25mm to all the edges.
- Do similar operations for the 2nd Rib by keeping in mind the spacing between the ribs to follow the design rules which is height to spacing ratio to be 3:1 or 2:1.
- The Rib shown in Figure 29 shows the above operations.
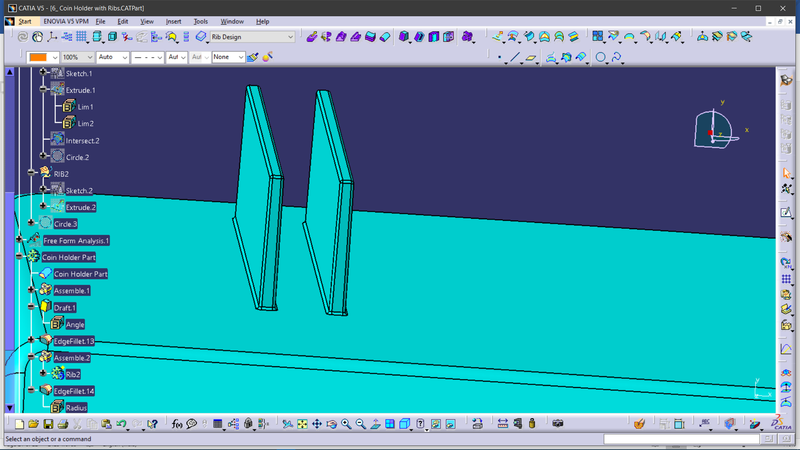
Figure29:Assembly of Rib1,Draft and Fillets on it.
- Take a section of the Final Part with the XY plane to check the application of Design rules of the Ribs are satisfied.
- The Figure 30 shows the considerations being satisfied according to the Rib Design Rules.
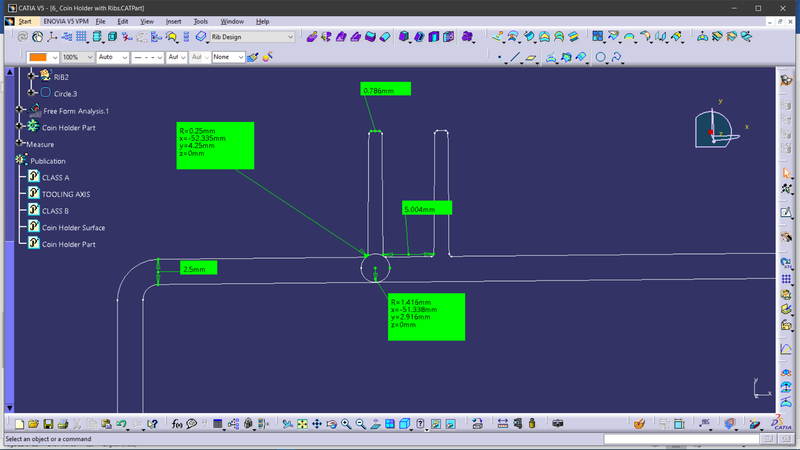
Figure30:Design Considerations for Ribs shown with measure on Intersect.
Step 9: Screw Boss and Dog House Design for the B side:
SCREW BOSS
- In generative Shape Design Workbench, Extract the base from B Surface and Create a Plane on it as shown in Figure 31.
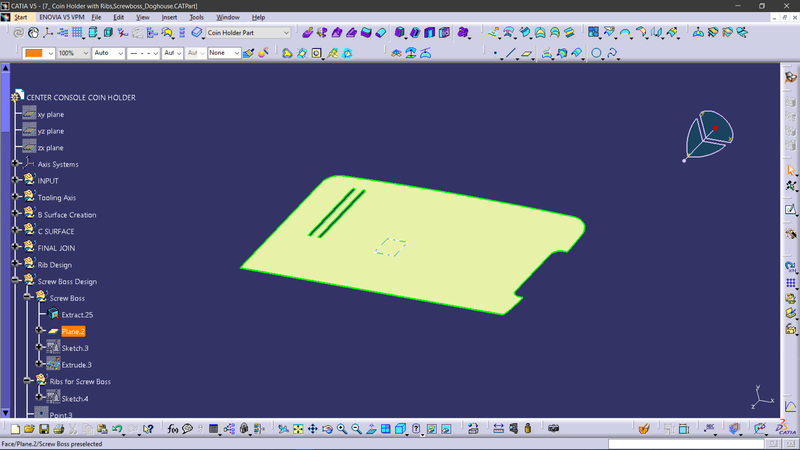
Figure31: Extract of base of B surface and Plane Creation on it.
- Create the sketch as shown in Figure 32 with Outer circle diameter as 9.8mm.
- This value of diameter is derived from wall thickness rule in case of M8 (6.8mm diameter) hole.
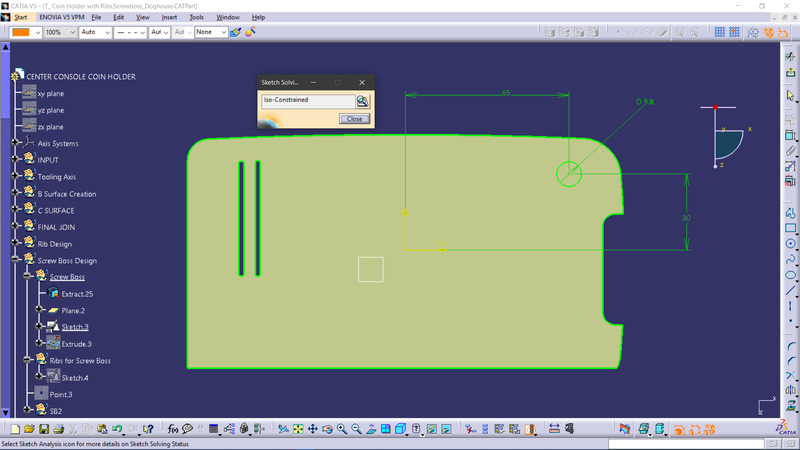
Figure32: Sketch for Screw Boss.
- Extrude the Boss to 12.5mm as shown in figure 33.
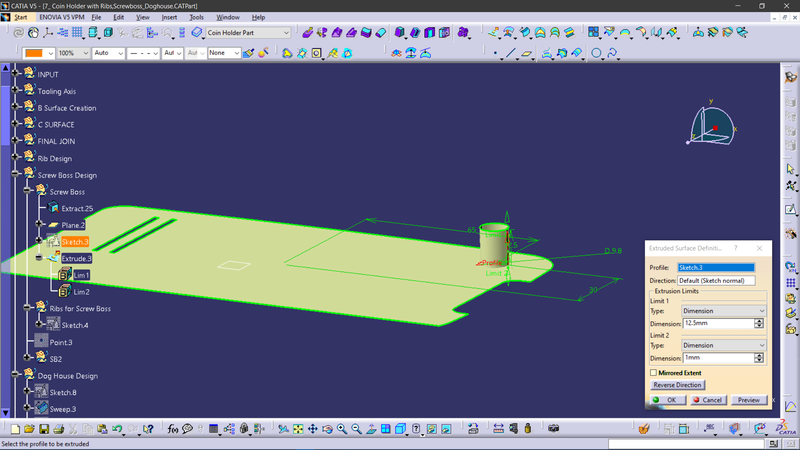
Figure33: Extrude for Screw Boss.
- In Part Design workbench Thicken the extrude to value of 1.5mm.
- Sketch the Ribs for the Screw Boss Support as shown in Figure 34
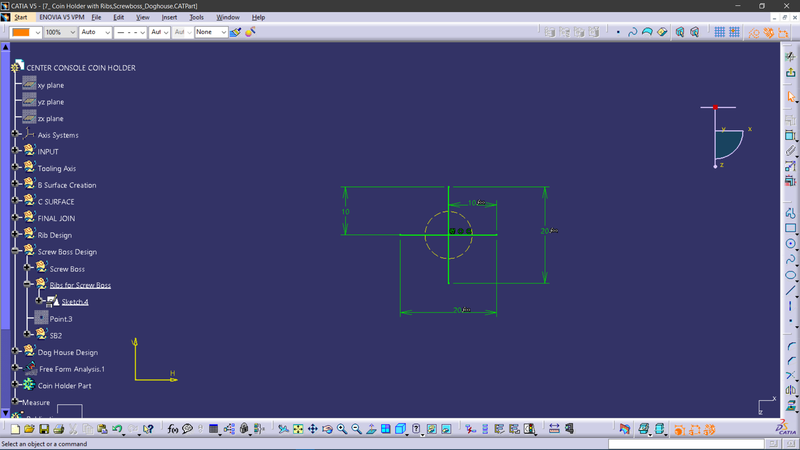
Figure34: Sketch for support Ribs for Screw Boss.
- Extrude and thicken it to the Rib design rule and obtain the Screw boss as shown in Figure 35 by using Union Trim for internal faces to be removed.
- Provide Draft in tooling direction and also give fillets as per optional radii rule.
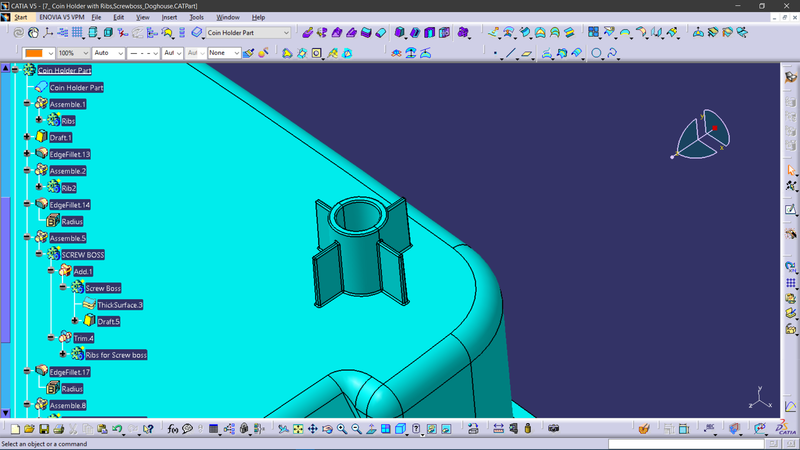
Figure35: Screw Boss.
DOG HOUSE
- Create a point on the B side Surface and Create a plane on the surface with point as reference.
- Create a sketch as shown in Figure 36 for the Dog house.
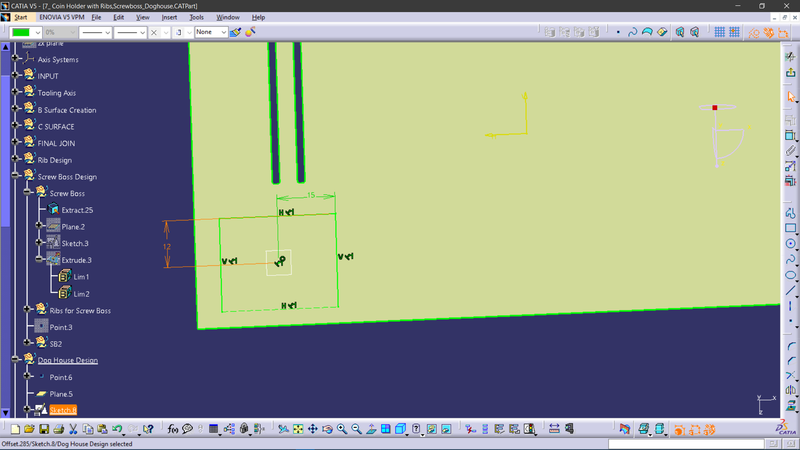
Figure36: Dog House Sketch.
- Use Sweep along draft direction for the Dog House Sketch and choose the tooling axis as draft direction as shown in Figure 37 .
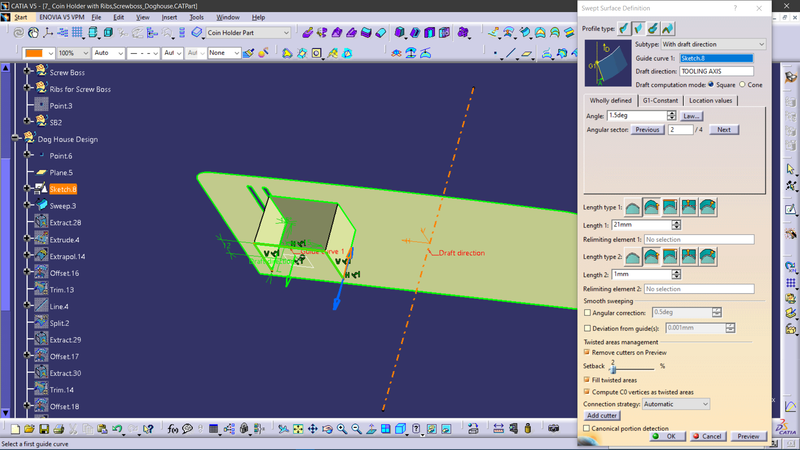
Figure37: Sweep for Dog House Sketch.
- Close the top by offsetting the surface and trimming it.
- Thicken the Dog House by giving wall thickness as per design Rules.
- Now create a thin section at base of the Dog house as per the rules.
- Create the section as shown in Figure 38 and use split in Part workbench.
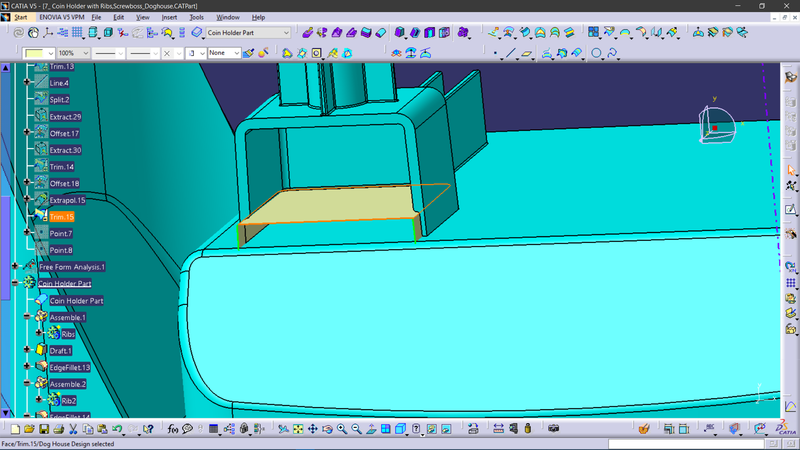
Figure38: Cut Section for base wall of Dog House.
- Create a point on the top of the Dog house center for the placement of the Screw Boss on top of it.
- Use Point to Point Translation for the screw boss and place it on the top of Dog House.
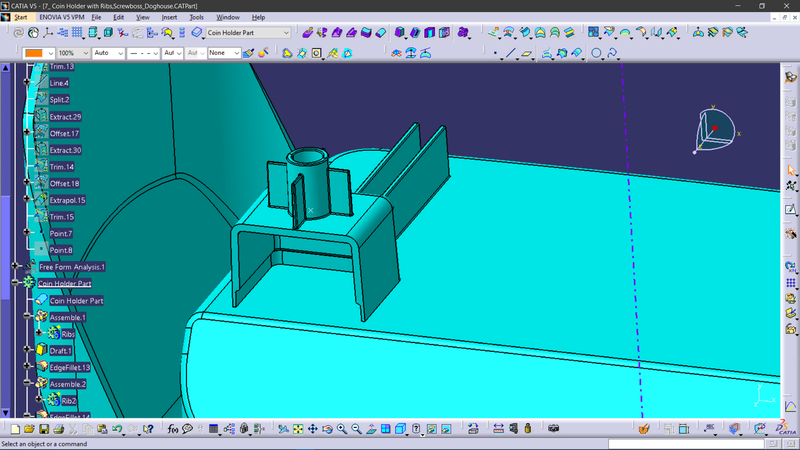
Figure39: Placement of Screw Boss on top of Dog House.
- Create appropriate Drafts and fillets on Doghouse and the boss. Use Assemble to the Coin Holder.
Step 10: Perform Draft Analysis on the Final Closed Surface:
- Change View Mode Customization to Material mode
- Go to INSERT à ANALYSIS à FEATURE DRAFT ANALYSIS and move the compass to the Tooling Axis. Change the range to 0.45º. Apply the settings as Shown in Figure 40.
- The Final Draft analysis passes on the Ribs, Screw Boss and the Dog House along the Main Tooling Axis but does not pass on the Side walls since the class A contained Parallel walls and walls without draft. This component will be costly to manufacture or may even fail causing loss in Time and Cost.
- The design for the Walls should be reconsidered by the Class A design team
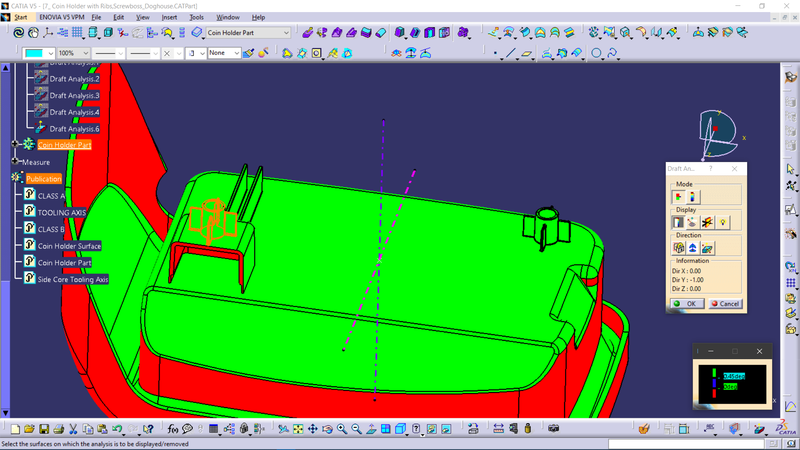
Figure40: Draft Analysis on Coin Holder along main tooling axis.
- Draft Analysis should also be done along the side core axis for the dog house Side walls to clear the tooling
- Create the Side Core Tooling Axis in clearing direction of the Dog House passing perpendicular to the Main Tooling Axis and publish it
- The Draft analysis along the Side Core Axis is shown below in Figure 41.
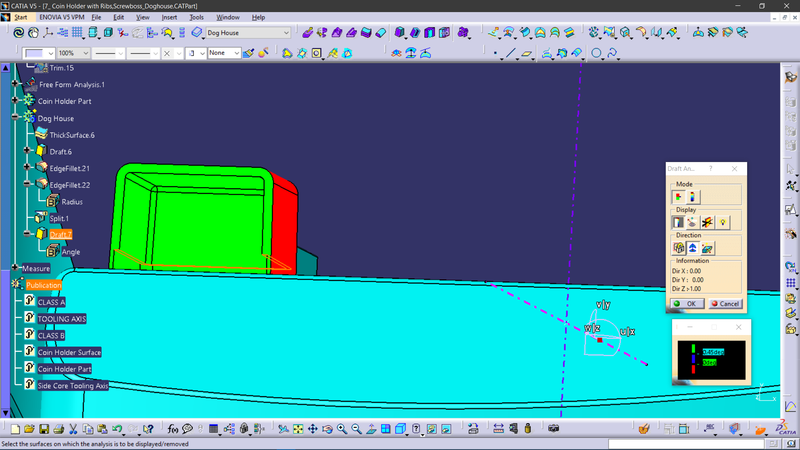
Figure41: Draft Analysis on the dog house along the side core axis.
Conclusion:
The Design of Automotive Plastic Component – Center Console Coin Holder from Class A with B surface feature such as Ribs, Screw Boss and Dog House is completed using concepts of Rib root thickness, Draft angle, Draft Analysis for Class A and Final enclosed surface, Tooling Axis creation and implementation, Class B and Class C creation and conversion to a solid part.