Challenge 4 – Conjugate Heat Transfer Analysis on an Exhaust Port
Aim – To study the wall heat transfer coefficient when air flows through an exhaust port and perform conjugate heat transfer analysis
A brief description of why and where a CHT analysis is used.
- CHT analysis, which is the short form of Conjugate Heat Transfer Analysis is mainly used in many areas to analyse the heat transfer coefficient, conduction and convection in cooling applications.
- The term 'conjugate heat transfer' refers to a heat transferprocess involving an interaction of conduction within a solid body and the convection from the solid surface to fluid moving over the solid surface.
- CHT analysis can accurately predict heat transfer by simultaneous solving all the relevant solid and flow field heat transfer processes
- In many cases the flowing fluid also has a certain temperature which may adversely affect the durability of the components around it.
- One excellent area where CHT analysis can be performed is on a graphics card to measure the heat distribution on the fins and the processor.
- As the processor runs, it gets heated up and this may affect the thermal stability of other components such as the graphics card and the fins present for cooling purposes
- Hence, a CHT analysis is carried out to analyse the solid conduction and convection between solids and the surrounding air
- For this particular simulation, an enclosure is created around the graphics card and air is forced through the inlet square of the enclosure.
- A volumetric heat generation source is applied to the processor since it is the main component responsible for heat generation.
- Using CFD post, the temperature contours on the outer surface of the graphics card can be observed and modifications can be made.
- Hence, this is one good example where CHT analysis can be deployed
Solving and Modelling Approach –
- Firstly, the model of the Exhaust port is imported into Ansys Spaceclaim.
- Before using the volume extract for extracting the fluid domain, any extra edges that may cause inconsistency in the geometry need to be removed using the repair edges option.
- Afterwards, the fluid domain can be generated by selecting the 4 inlet circles and one outlet circles using the edge select in volume extract option.
- Hence, a new fluid domain can be seen in the components section of the feature tree.
- The solid and fluid domain is selected and then moved to another component in the design tree.
- Another important step is to share topology between the solid and fluid domain, otherwise the mesh will not match at the interface leading to non-conformal mesh which will be inaccurate.
- The design was then proceeded with meshing.
- For a baseline mesh, a size of 40mm was given to the entire domain including the fluid and solid region.
- An inflation layer with scoping method as the fluid domain and the boundary as the interface between solid and fluid was given and the first layer thickness was varied based on the y plus value
- Furthermore, separate body sizing was given to the solid and fluid domain with a size of 20mm.
- Lastly, an edge sizing with 40 divisions was given on the 4 inlet edges and the single outlet edge to refine the mesh properly.
- The total mesh count came out to be 370261.
- Coming to the named selection, the 4 inlet circles were named as inlets and the single outlet circle was named as outlet.
- The outer surface of the exhaust port was named as outer-wall-convection since we needed to observe the temperature on the outer wall.
- The inner wall was named as inflation-layer-wall which was also the interface between the solid and the fluid.
- Mesh settings –
- Global mesh size –40 mm
- Body sizing – solid – 20mm
- Body sizing – fluid – 20mm
- Edge sizing – inlet and outlet circles - 40 divisions
- Inflation – First layer thickness varies according to y plus value
_1615887893.png)
_1615887934.png)
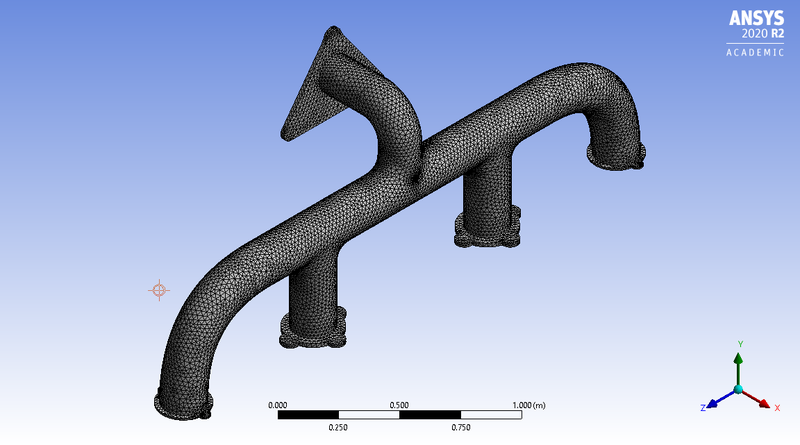
INLETS -
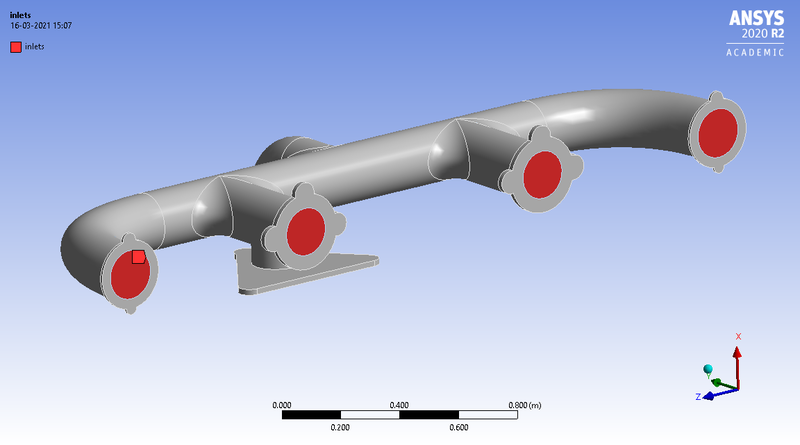
OUTLET -
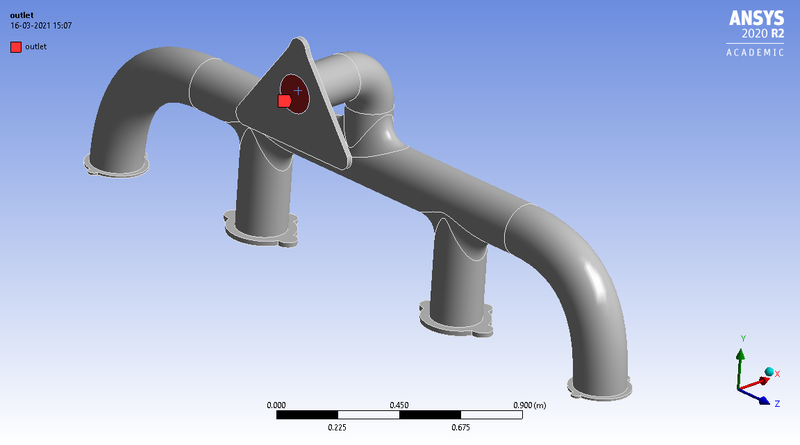
OUTER WALL CONVECTION
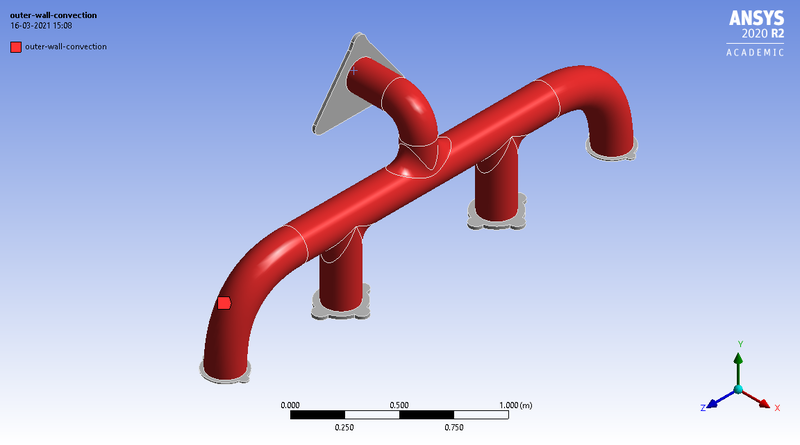
INFLATION LAYER BOUNDARY -
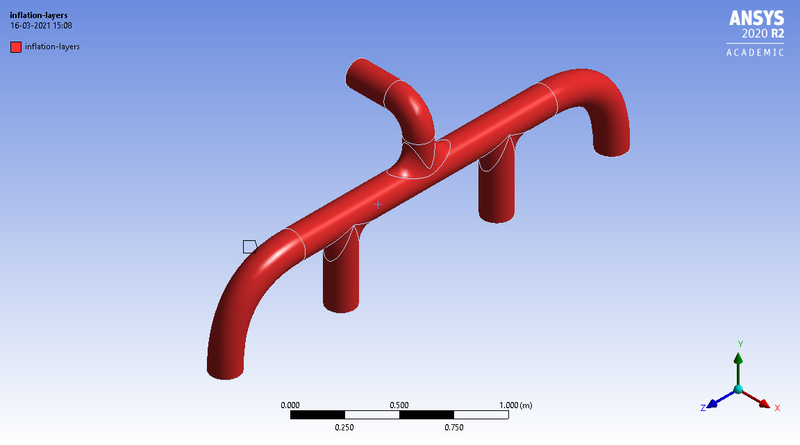
PRE-PROCESSOR AND SOLVER SETTINGS --- Setting up the case in Ansys Setup –
- Since the inlet velocity was taken to be 5m/s and is very small as compared to the velocity of sound, the Mach number is < 0.3 and hence a pressure based solver was used since there are low chances of compression.
- The problem was analysed in a steady state manner since we are only analysing the end results
- Since, this problem deals with wall related analysis, the k-omega SST turbulence model was chosen and the y plus value was altered between 0 – 5.
- Accordingly, the first layer thickness was calculated using the y plus calculator and put in the inflation specifications.
- Air which is the default material was chosen as the fluid medium in the cell zone conditions.
- On the other hand, aluminium was chosen as the default material for the solid domain in the cell zone conditions
- The inlet velocity was given as 5m/s and the outlet was specified as a pressure outlet in the boundary conditions sections
- The outer wall was given as a convection thermal condition with a heat transfer coefficient of 20W/m^2K.
- All other walls were specified with a heat flux thermal condition and the heat flux was given as 0, thus indicating that the walls are adiabatic.
- After initialising the solution using hybrid initialisation, a temperature contour on the outer convection wall was created to observe the temperature along the wall
- Also, a solution animation was generated which was recorded after every 10 iterations.
- Finally, the solution was run for a total of 500 iterations
_1615888070.png)
_1615888094.png)
_1615888108.png)
_1615888131.png)
_1615888141.png)
_1615888161.png)
_1615888177.png)
_1615888188.png)
Results –
- y+ = 0.1 --- 000005600635239514978m
Max temperature = 492.4K
Max velocity = 37.94m/s
Heat transfer coefficient = 9411W/m^2K
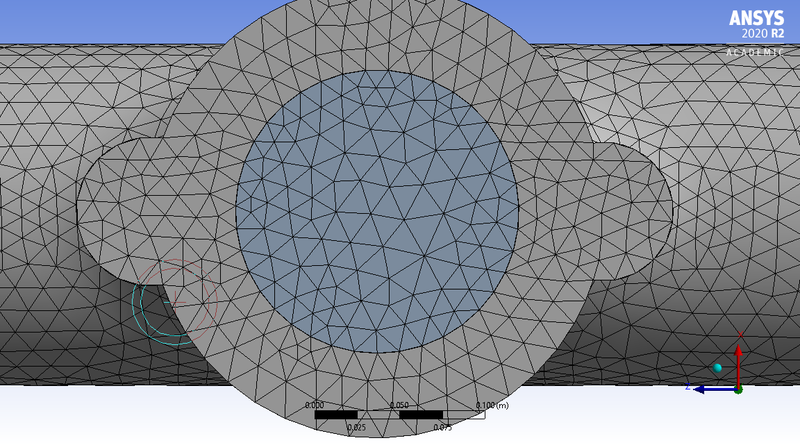
_1615888238.png)
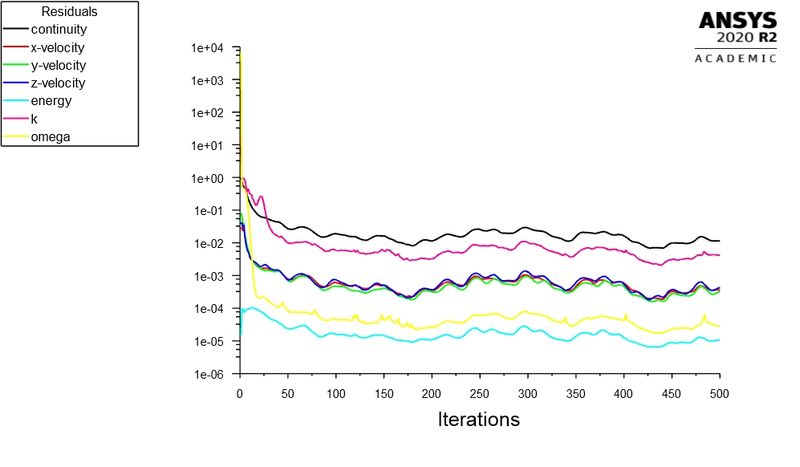
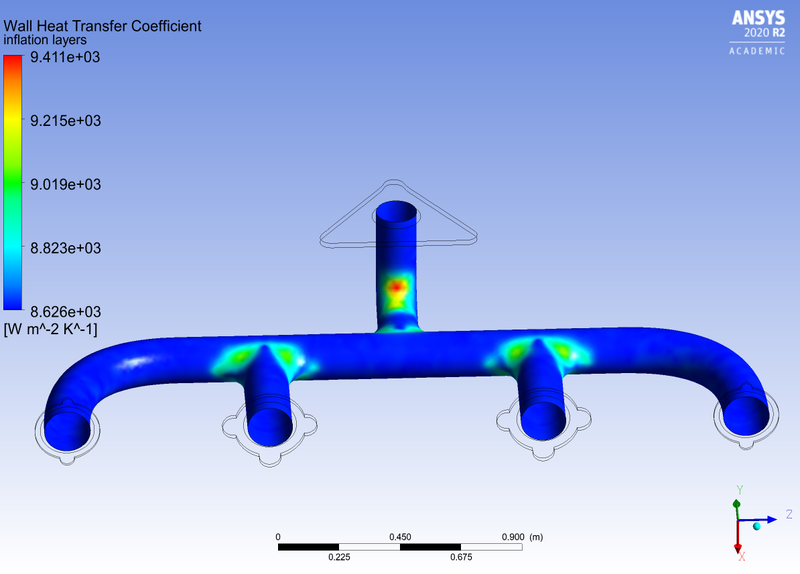
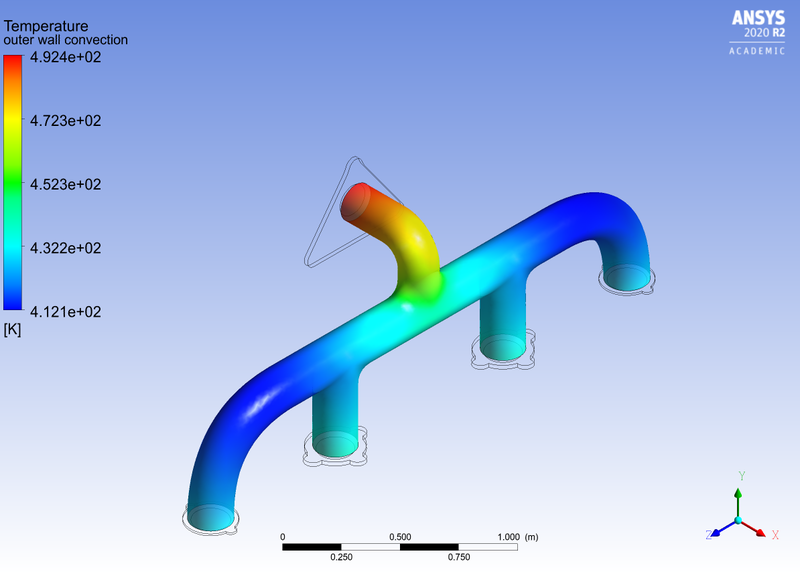
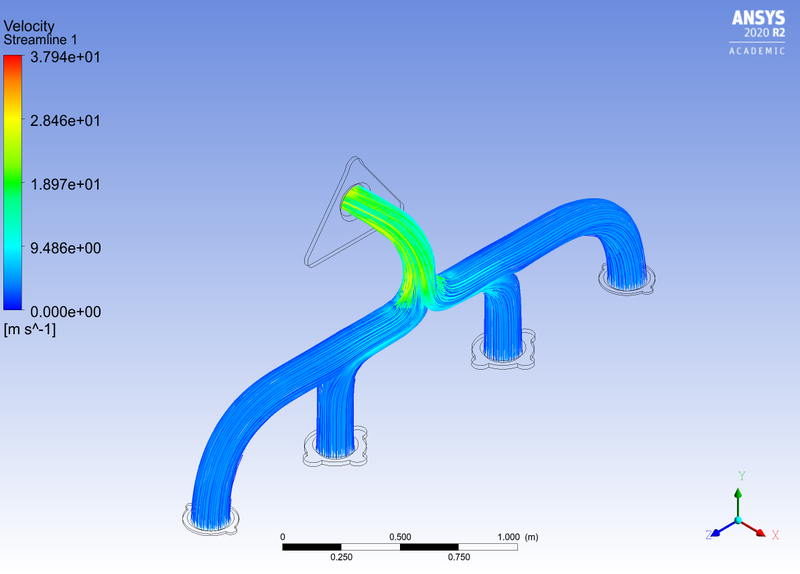
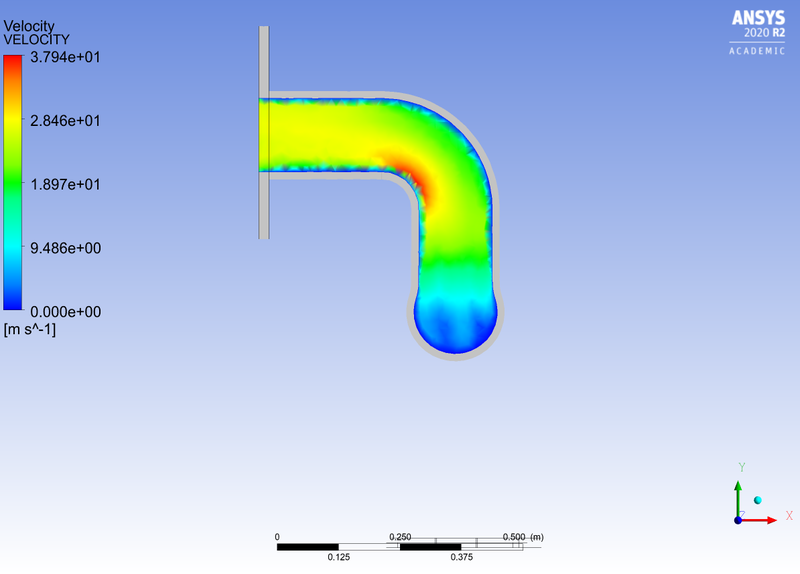
- y+ = 0.5 --- 000028003176197574888m
Max temperature = 577.2K
Max velocity = 36.88 m/s
Heat transfer coefficient = 1862 W/m^2K
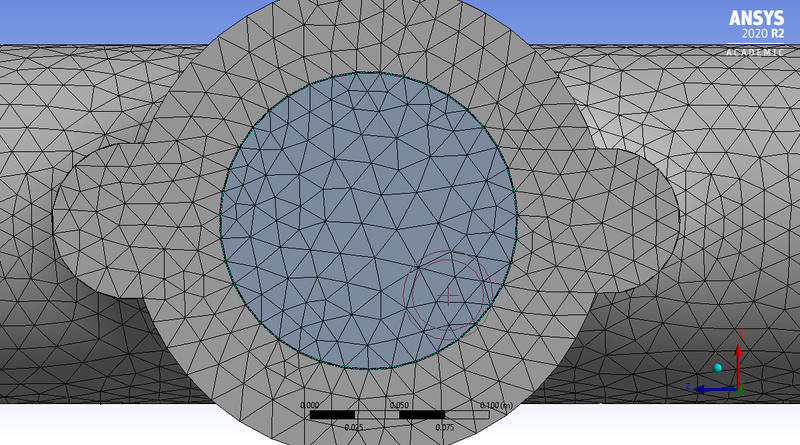
_1615888348.png)
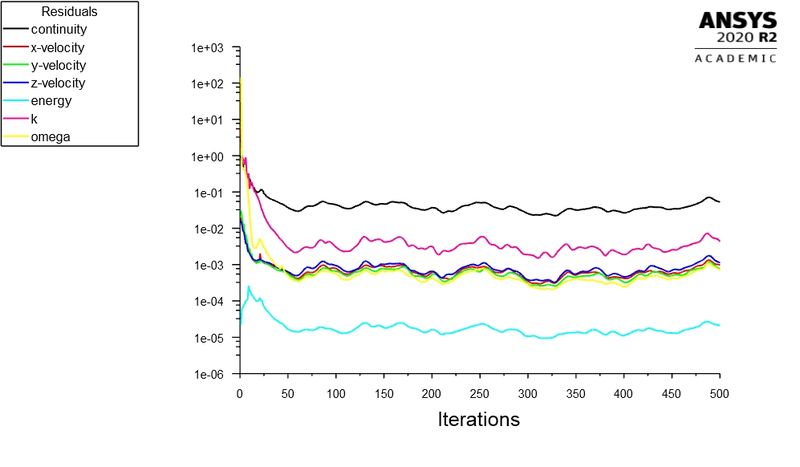
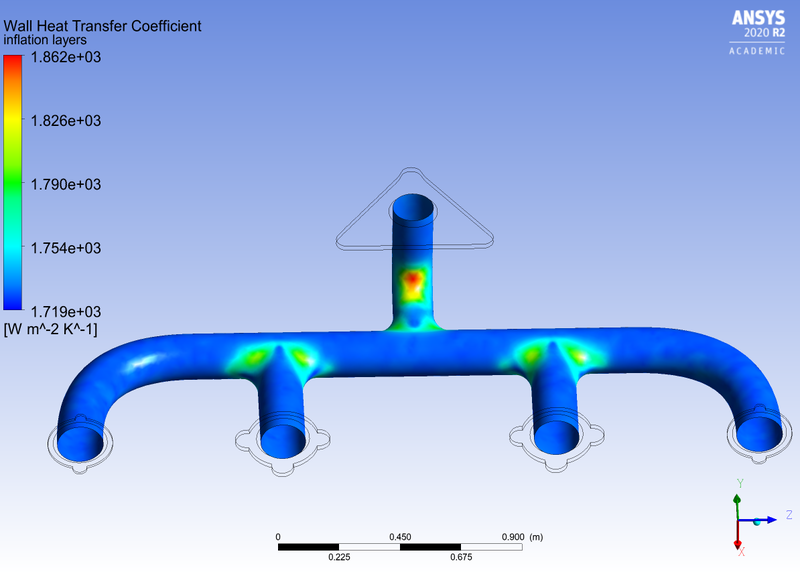
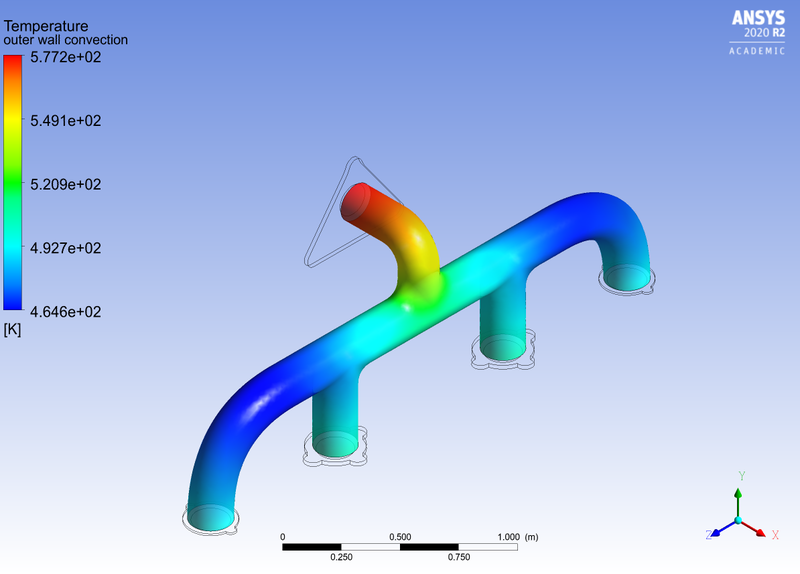
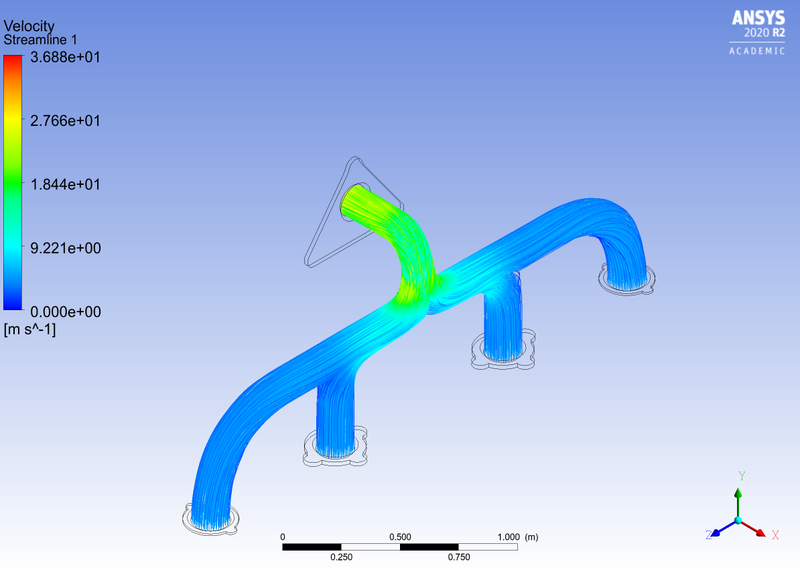
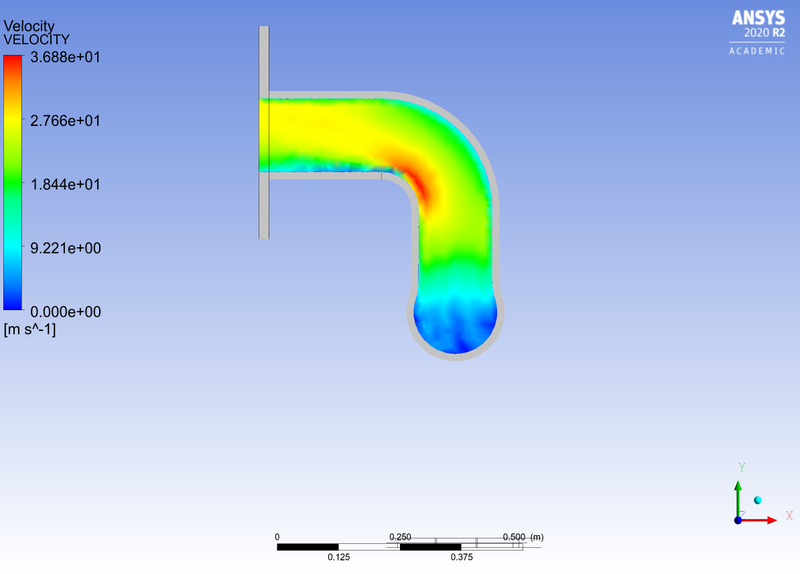
- y+ = 1 --- 000056006352395149776m
Max temperature = 584.5K
Max velocity = 37.8 m/s
Heat transfer coefficient = 1005 W/m^2K
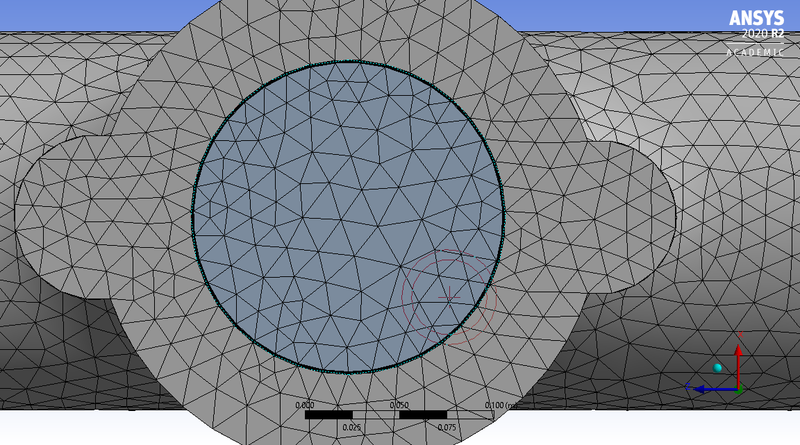
_1615888449.png)
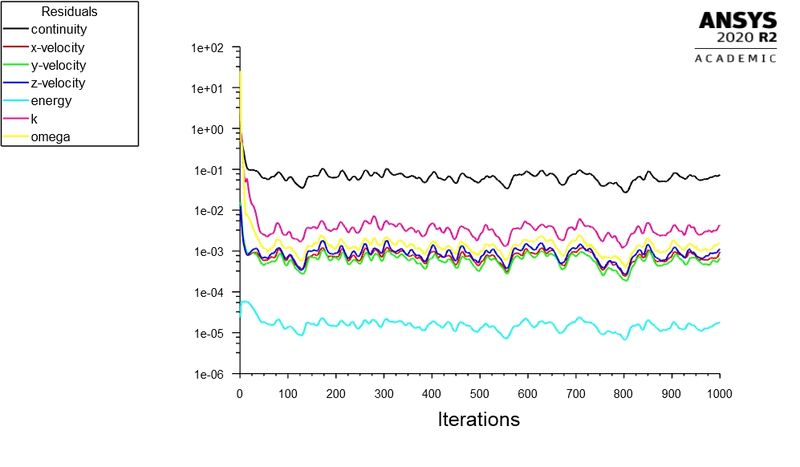
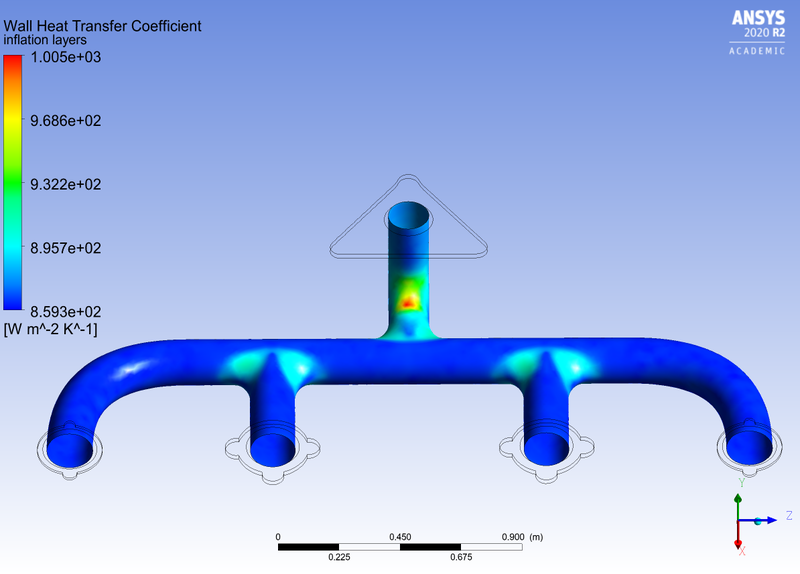
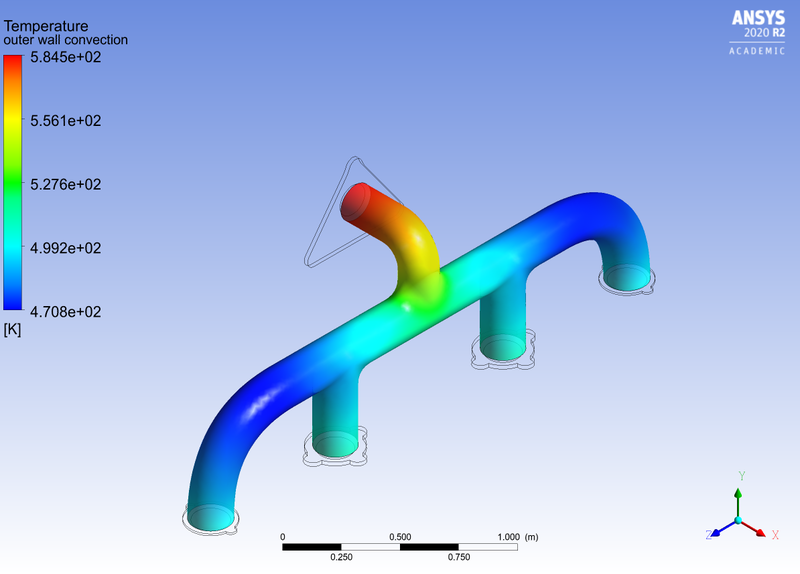
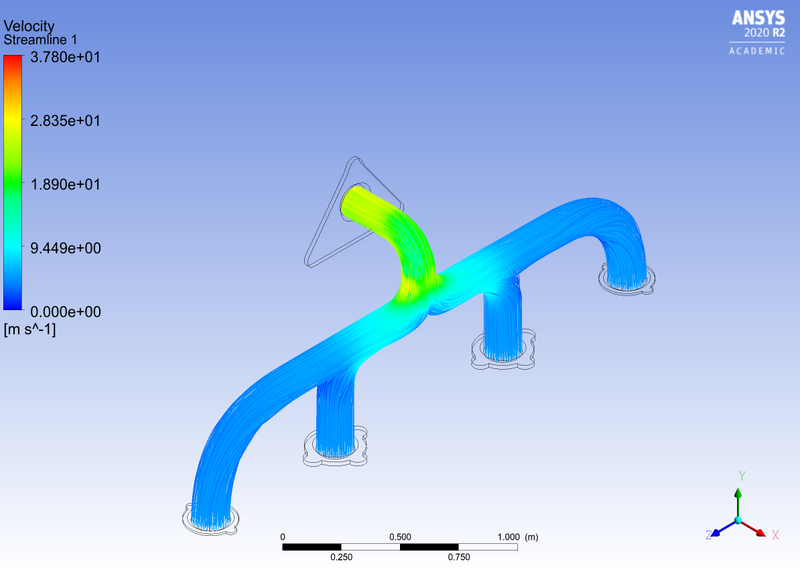
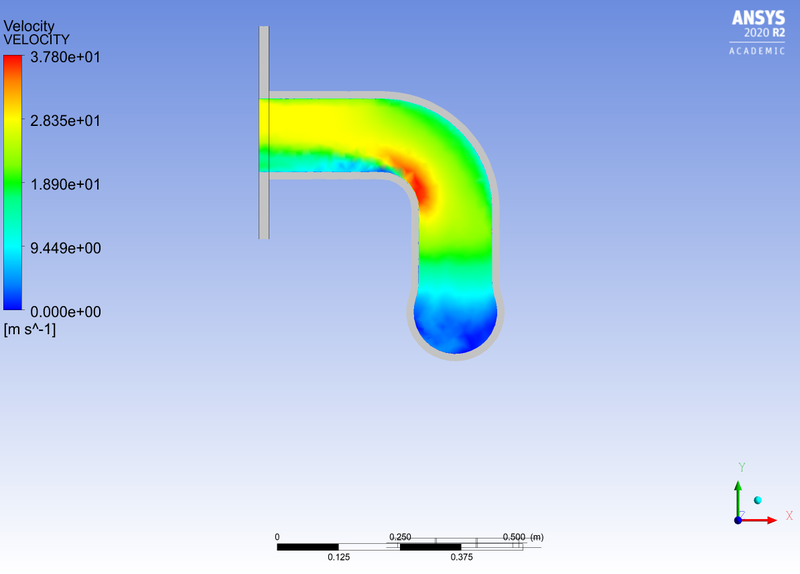
- y+ = 5 --- 0002800317619757489m
Max temperature = 591.8K
Max velocity = 41.36 m/s
Heat transfer coefficient = 319.6 W/m^2K
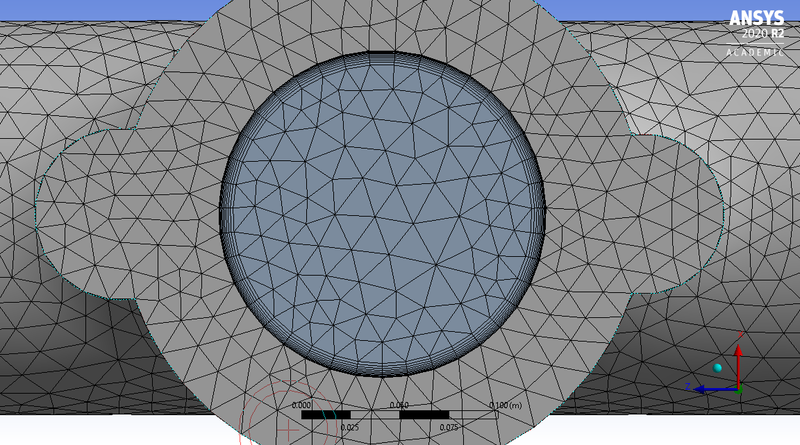
_1615888561.png)
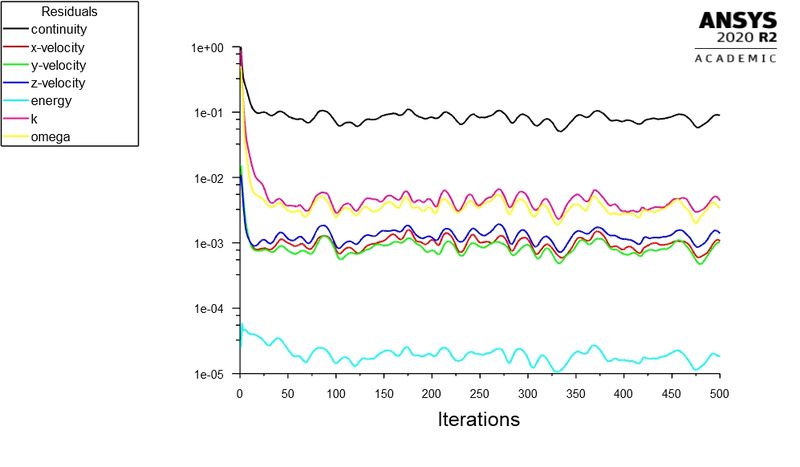
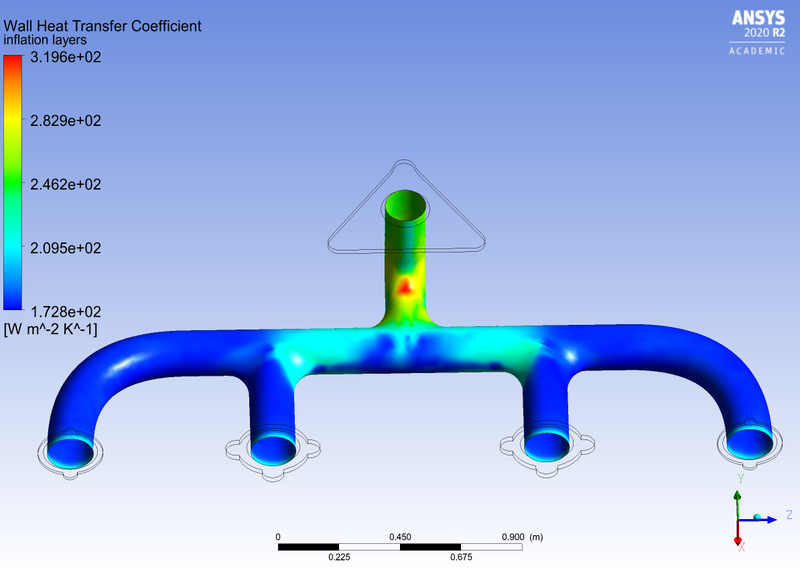
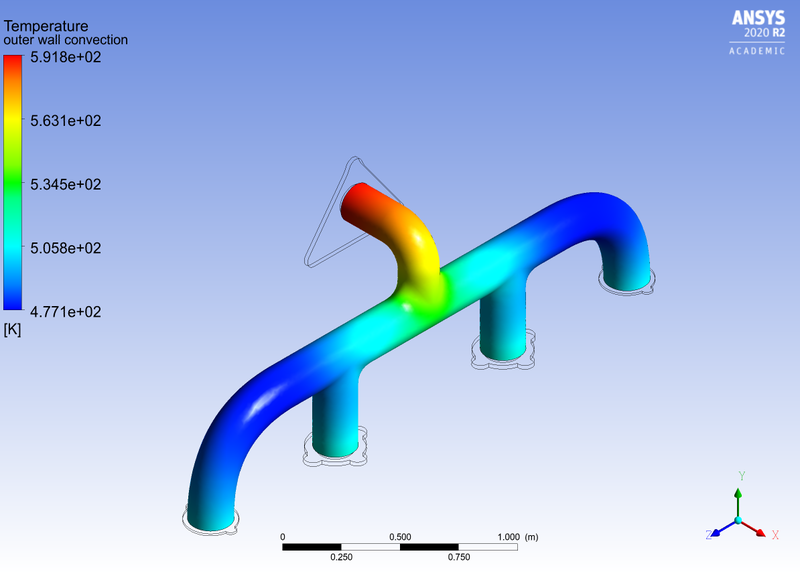
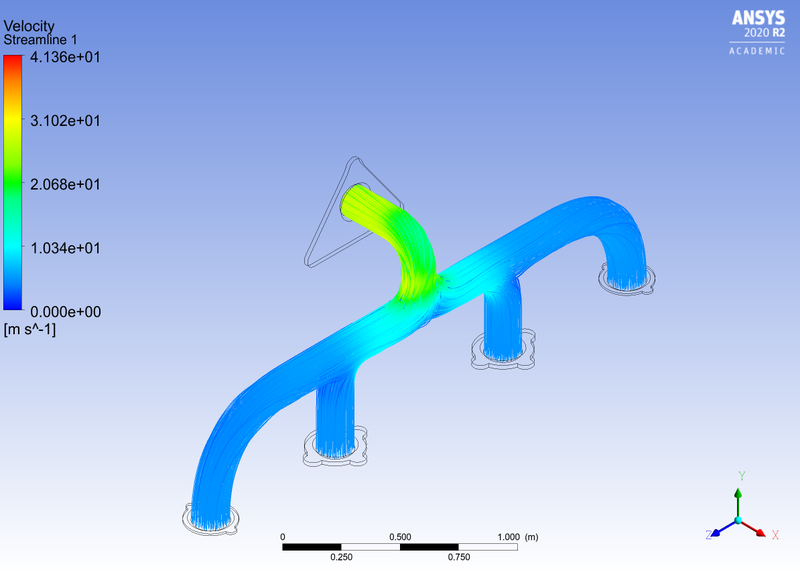
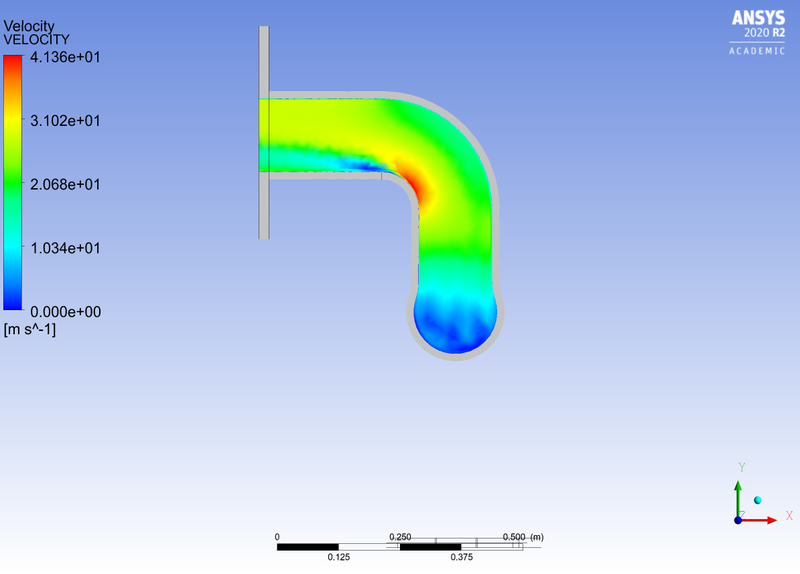
- y+ = 30 --- 0016801905718544933m
Max temperature = 602.4K
Max velocity = 41.2 m/s
Heat transfer coefficient = 194.5 W/m^2K
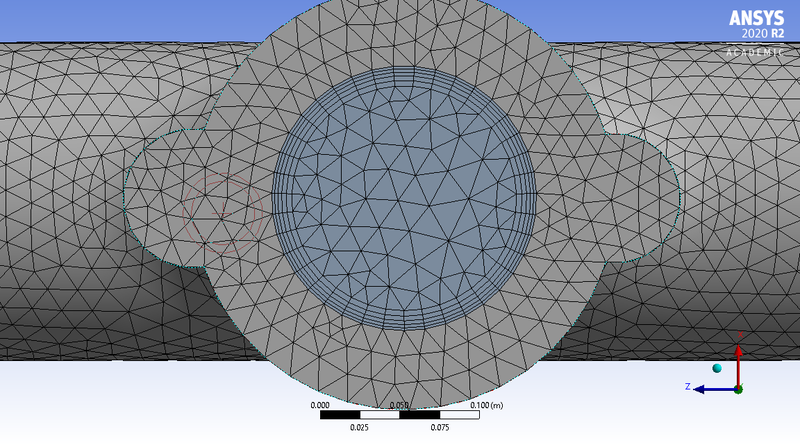
_1615888714.png)
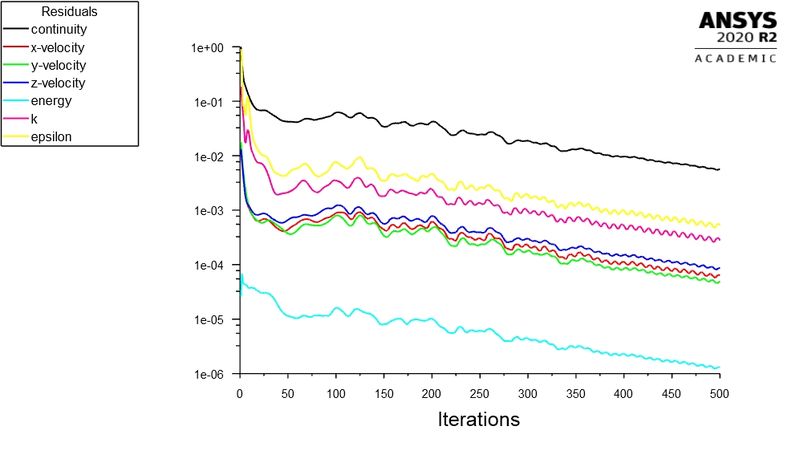
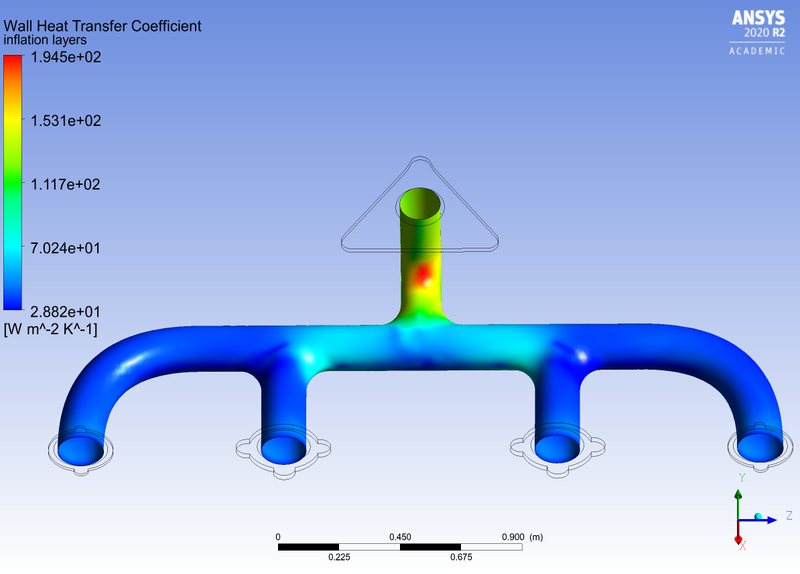
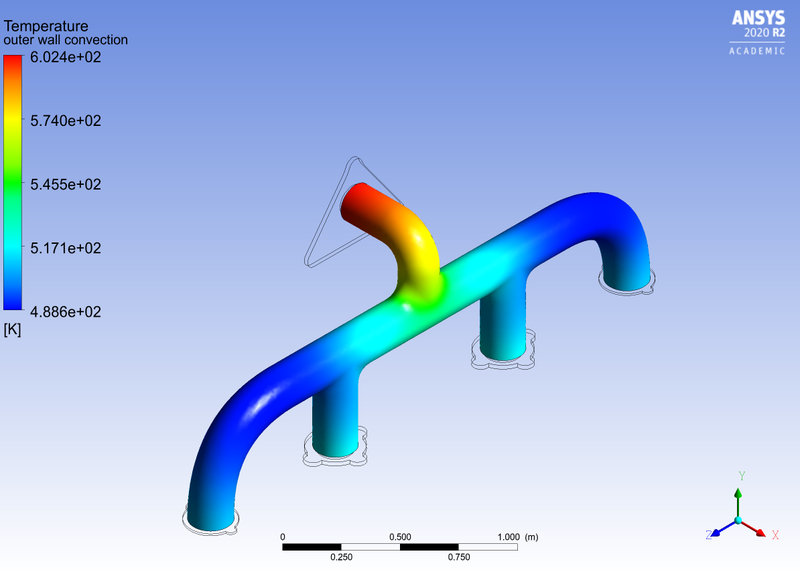
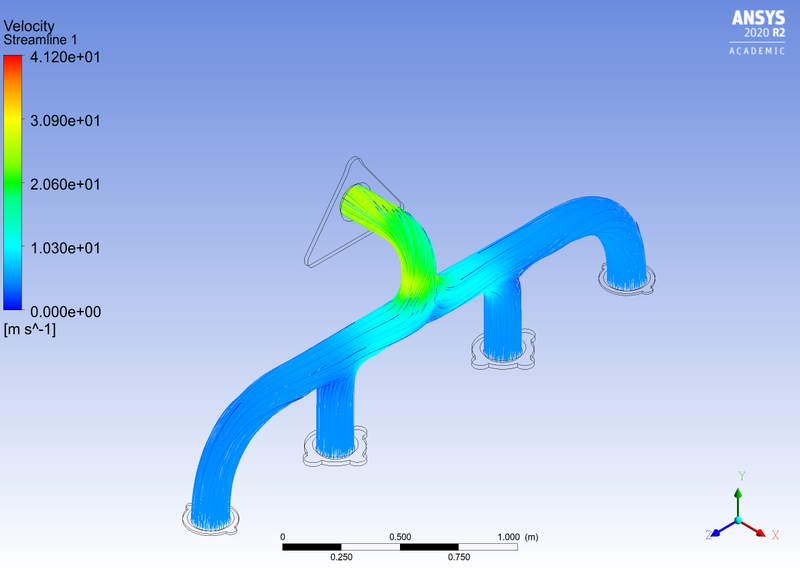
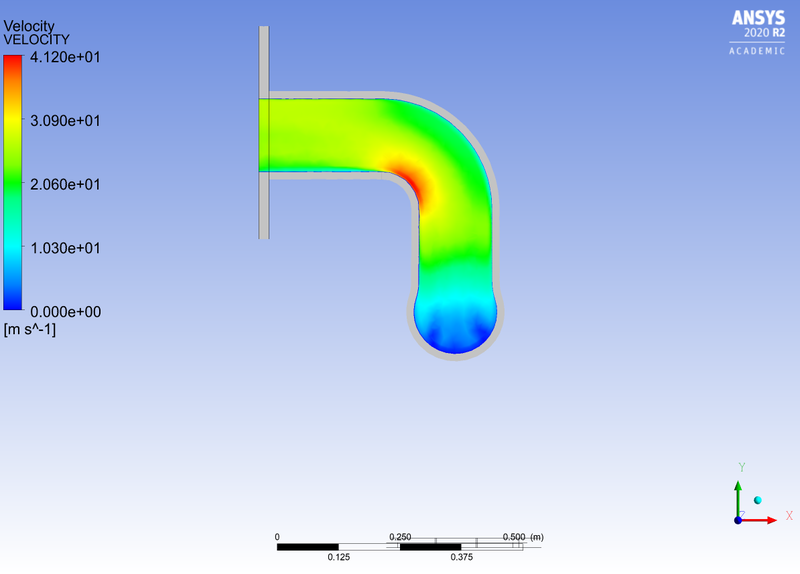
- y+ = 50 --- 002800317619757489m
Max temperature = 606.9K
Max velocity = 39.67 m/s
Heat transfer coefficient = 169.8 W/m^2K
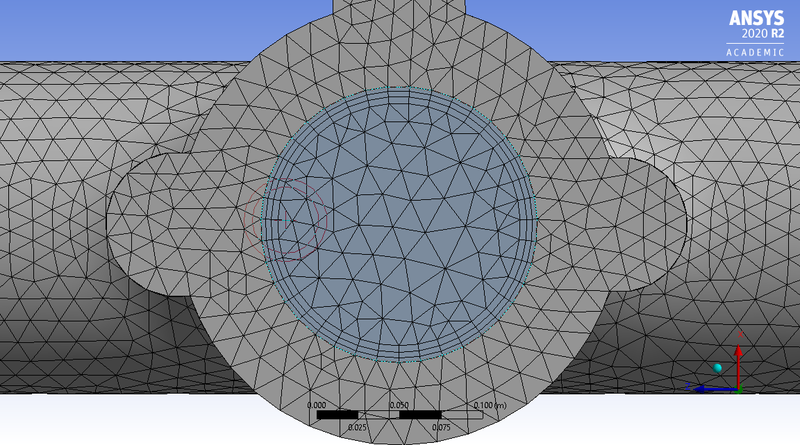
_1615888839.png)
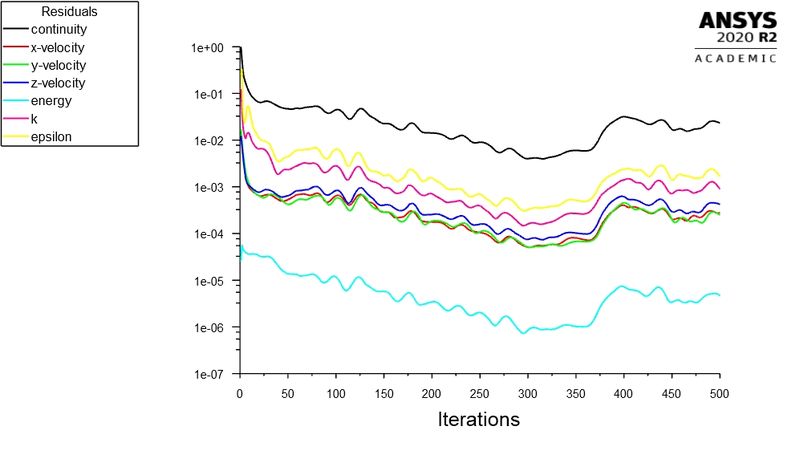
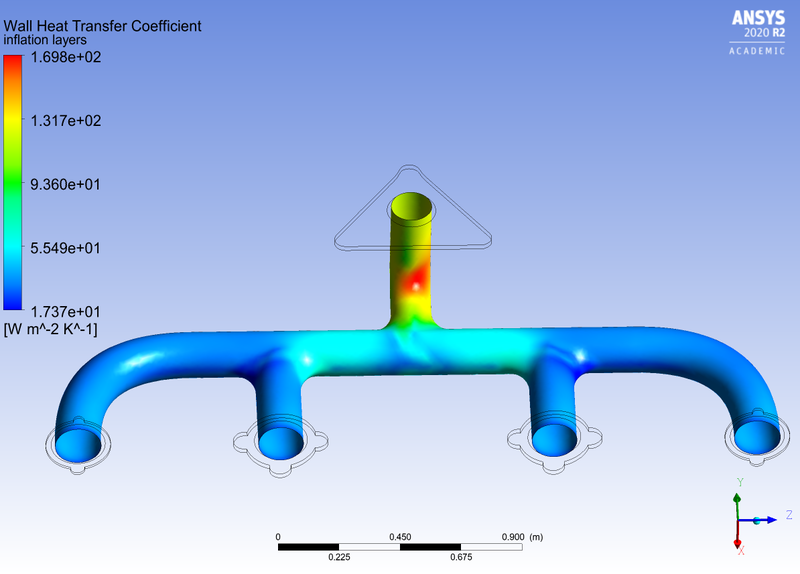
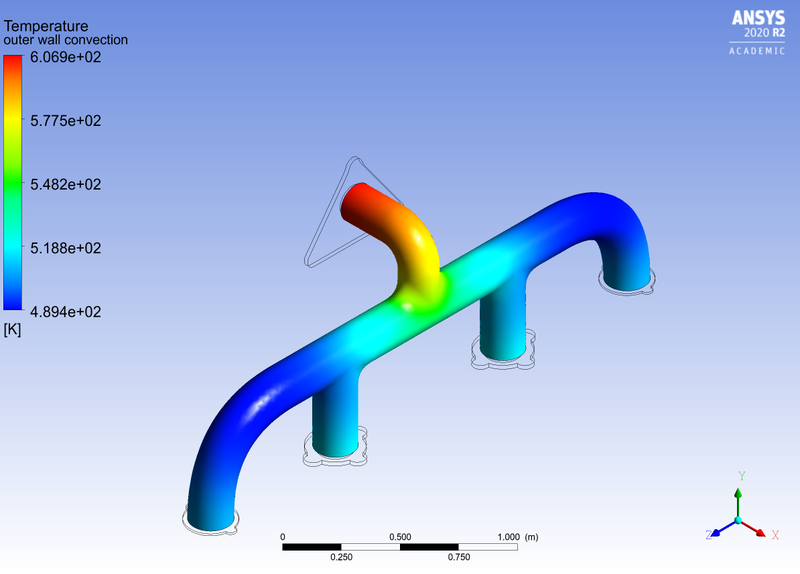
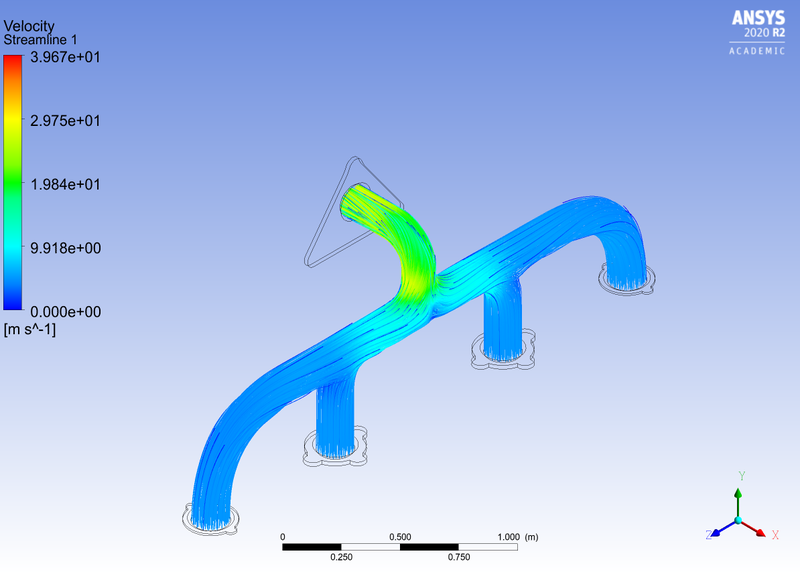
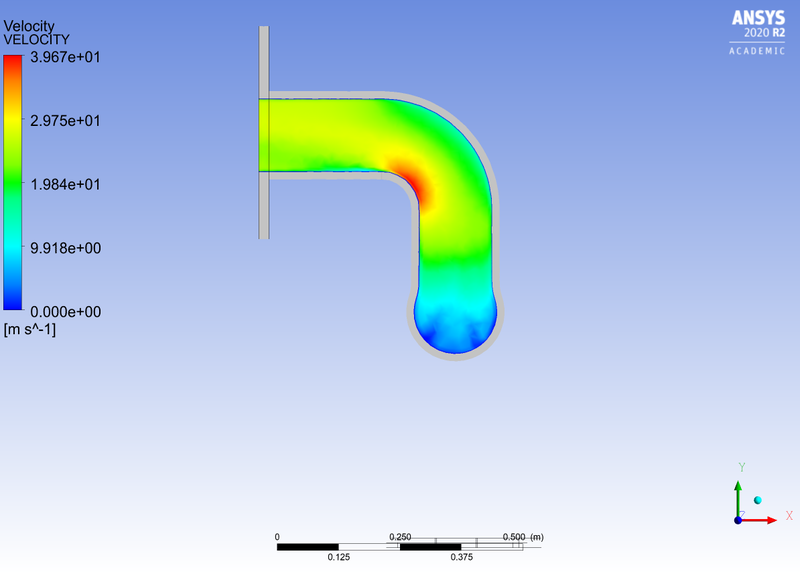
Verification –
- Verification of the simulation results can be done analytically by calculating the Nusselt number
- Nu = 0.023*(Re^0.8)) Pr^n – the Reynolds number is known and the Prandtl number can be calculated from taking the ratio of momentum diffusivity and thermal diffusivity.
- Nu = h.D/K
- h = wall heat transfer coefficient can be calculated accordingly for verification
Conclusions - What factors does the accuracy of the system depend on?
- The most important factor that affects the accuracy of the system is mesh refinement.
- A finer mesh will be able to capture more details pertaining to the boundary layer as compared to a coarse mesh.
- This study involved analysing the wall heat transfer coefficient for different value of y+.
- The lower the y plus value, the better the refinement.
- The y+ values of 0.1, 0.5, 1, 5, 30, and 50 were analysed.
- It can be observed that y+ values of 30 and 50, using a k-epsilon standard wall function model, resulted in a very coarse inflation layer and did not capture the boundary effects properly.
- Hence, these results can be stated as inaccurate
- On the other hand, y+ values of 0.1, 0.5 and 1 (with k-omega model) generated the best results since the low y+ value allowed more refinement and accurate capturing of boundary effects.
- Temperature on the other hand did not experience a drastic change on the refinement of the mesh.
- This is mainly because the temperature contours were plotted on the outer convection wall which was far away from the inflation layers.
- Since the velocity near the bent portion at the outlet was the highest, the highest heat transfer coefficient was observed at that point in all iterations.
- However, the absolute value of HTC varied as per the y+ value and mesh refinement.