Q1 Ans
BIW - Body In White
- BIW refers to the welded sheet metal components which form the structure of the vehicle to which the other components (like engine, chassis, exterior & interior trims) will be married or assembled.
- The stage in automotive design or automobile manufacturing in which the car body sheet metal components are been assembled by welding & by another joining process.
- The structural performance of an automobile can be determined by the performance of the body, referred to as BIW. BIW is the steel structural shell composed of generally steel panels welded together. BIW structure supports the overall other subsystems in the vehicle.
- To achieve an efficient car design it is necessary to have the BIW design with optimized mass. BIW connected all the components in the vehicle like Powertrain, driveline.
- BIW encloses, protects the passengers & cargo. The BIW design needs to be stiff to support the mass & securely keep them all integrated. Further, it needs to resist & absorb energy during the event of a vehicle crash.
- BIW design also needs to be lightweight structure so that there can be a possibility of reduced fuel consumption & increased performance.
- The structure is made from Steel or Aluminium panels (0.7 - 2.0 mm thickness). The panels are stamped into shape and then the spot is welded together.
- BIW constitutes about 27% of a car’s weight.
Figure 1. Exploded view of BIW components 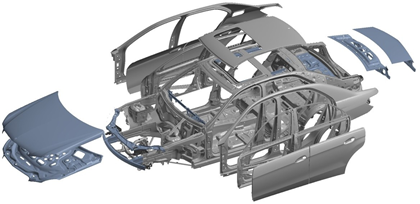
As shown in Figure 1, In general, the BIW consists of nearly 300 - 350 components.
In the new advanced BIW architecture, the entire body was designed with 58 major parts.
MAJOR INFLUENCING FACTORS OF BIW DESIGN:
- Number of parts.
- Materials.
- Internal structural reinforcements.
The Principles that should always be Considered in BIW designs are:
- Effective load paths in the BIW architecture with a minimum number of components in the design. Material distribution in the BIW considering the bending & torsion stiffness of the BIW.
- Internal Reinforcement location could be lead to an efficient performance increase.
- Material optimization method on a full vehicle crash analysis.
There are two types of Body Structures in use, They are:-
- Monocoque Body
- Frame Mounted Body
1.MONOCOQUE BODY STRUCTURE:
In this type of Body structure, Chasis is inbuilt in the BIW itself and there is no separate chassis. Wheels are directly mounted to the BIW with the help of a suspension system.
Figure 2. Monocoque Body structure 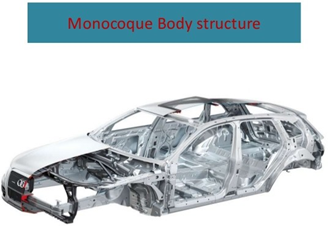
2.FRAME-MOUNTED BODY STRUCTURE:
In this type of body structure, the Body is mounted on separate chassis or frame & wheels are mounted on the chassis, not to the body.
Figure 3. Frame Mounted body structure 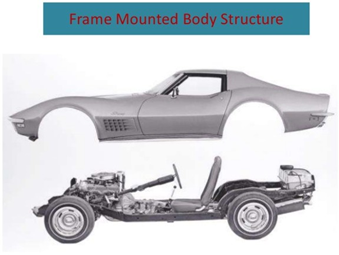
BIW PARTS:
Figure 4. Classifications of BIW parts
BIW structures can be divided into the following sub-structures:
- Underbody structure.
- Front End Structure.
- Body side structure.
- Closures.
- Roof.
- Reinforcement
Figure 5. BIW Parts 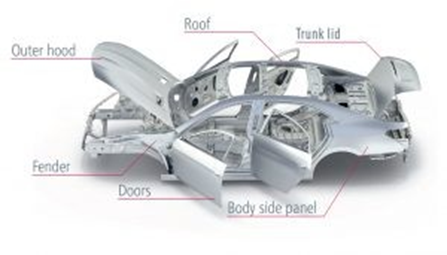
All those substructures consist of the following major panels:
1. UNDERBODY STRUCTURE:
- Dash panel - Provides partition between Engine & the driver
- FRT Floor - Provides a base for the
- Raiser - Connects front floor to Rear floor by providing a level
- Rear Floor - Floor on the rear of the car & provides partition from ground and base for the rear
- Rear-wheel
Figure 6. UNDERBODY STRUCTURE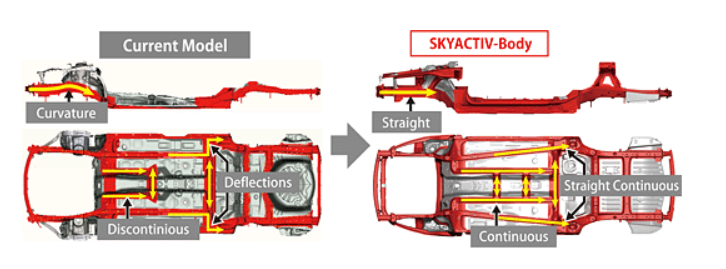
2. FRONT END STRUCTURE:
- Plenum Panel - A chamber located between throttle body & runners of the intake
- FRT Wheel House (Fender) - Is an encasement around the Front
- Wing Panel - Outermost side panel in the
- Cowl - Portion of the body bounded by the front fenders, the base of the windshield, and the rear edge of the
- Upper Tie Bar - Upper panel in front connecting the two sides of the front
- Lower Tie Bar - Lower panel in front connecting the two sides of the front
Figure 7. Outer Panels, Inner panel, Underbody panel 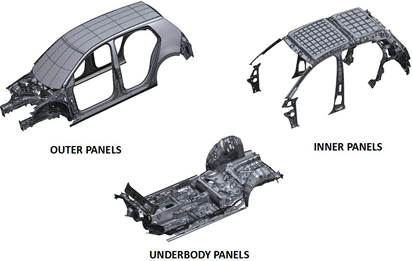
Figure 8. Upper body 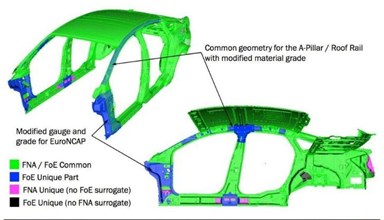
3. BODY SIDE STRUCTURE:
- A-Pillar - Front most support to the A-pillar is the most stylistically interesting for a car fans Other notable aspects of the A-pillar
- B Pillar - Second support to the B - pillar plays a key role in providing strength to a midsection to a vehicle.
- C Pillar - C is rearmost support to the roof in case of a two-row seating system, it will be the third C-Pillar is often the most heavily leveraged pillar from a styling perspective. BMW has made the C - PILLAR their own distinctive curved C - pillar called the Hoffmeister kick that appears in some format in all of their cars. Coupes also rely heavily on the C-pillar to create streamlined shapes. one of the most iconic is from Ford Mustang.
Drip rails / Gutters - An exposed channel applied to the roof over the side windows to direct water away from the windows
- D Pillar - D is the fourth support usually the rear side of quarter D pillar is really the end of the line in many ways this pillar is designed for the necessity to house the rear door in a wagon or SUV.
- Ring Panel - A structured panel connecting the rear & front
- Quarter Panel - Rearmost panel of a bodyside
- Drip rails / Gutters - An exposed channel applied to the roof over the side windows to direct water away from the windows.
Figure 9. Classification of Pillars 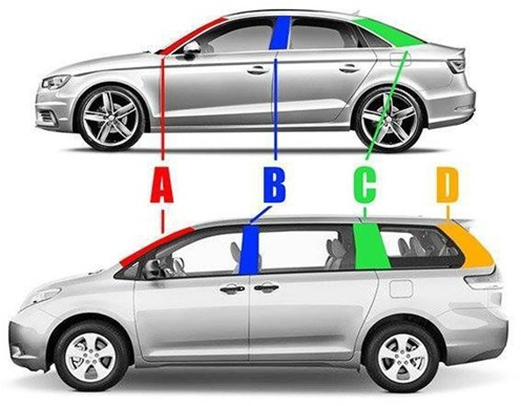
From the above picture, the Placements of the A, B, C, D pillars can be easily understood.
Figure 10. B-Pillar 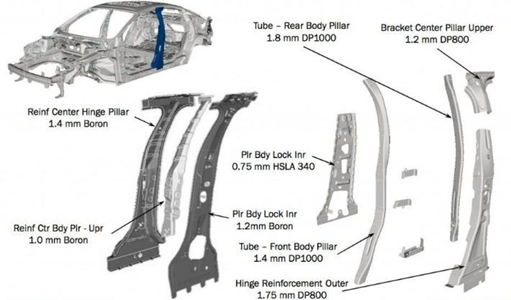
B - Pillar design and details are shown in the above picture.
Figure 11. BIW parts including all types of pillars. 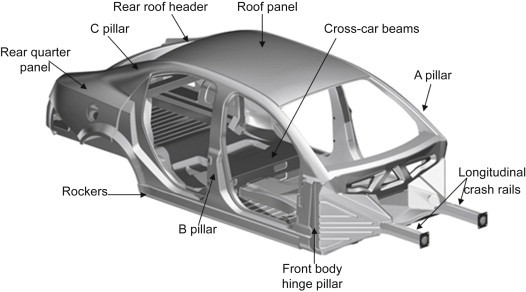
From the above picture, the Roof panel & Rear quarter panel can be seen
4. CLOSURES:
- All Doors
- Hoods / Bonnets - A hinged panel providing access to the engine
Figure 13. Doors 
Figure 13. Hood/Bonnets 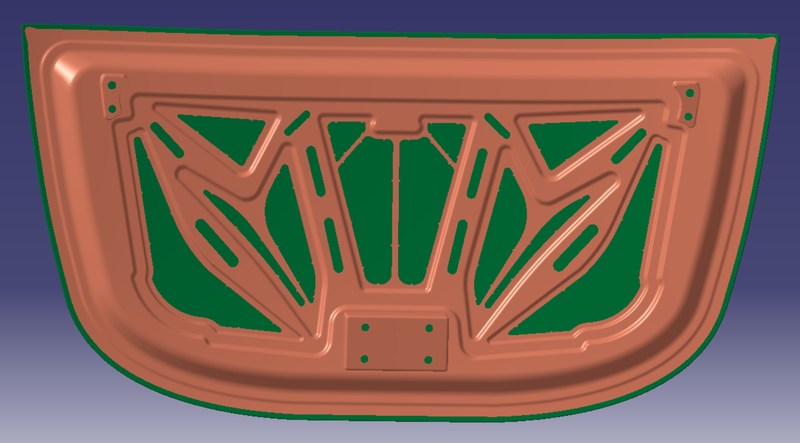
5. ROOF STRUCTURE
- Roof.
- Headers - Structural member above the windshield at the juncture with the forward edge of the roof panel.
- Bows.
Figure 14. Roof, Bows, Headers 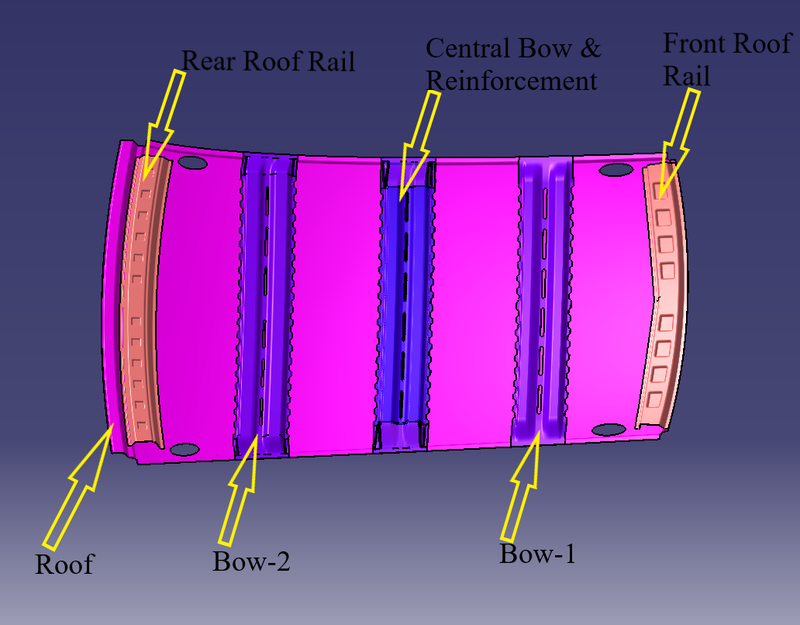
6. Reinforcement
The part which is used to support and provides stiffness and strength to other components of BIW is known as the Reinforcement component. Some of the reinforcement components are shown below in the picture.
Figure 15. Reinforcement Components 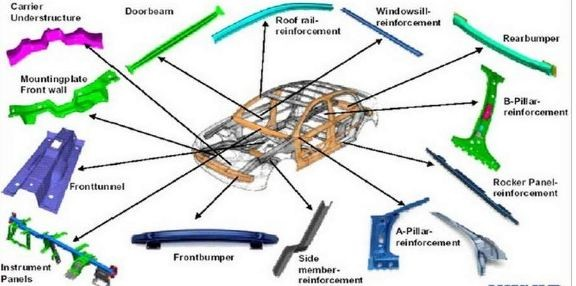
-----------------------------------------------------------------------------------------------------------------------------------------------------------------------------------------------------------------------------------------------------------------------
Q2 Ans
DEFENITION OF NOMENCLATURE:
- The devising or choosing of names for things, especially in a science or other discipline.
- In formal, the term or terms applied to someone or something.
BIW NOMENCLATURE:
- Hence from the definition of nomenclature, we came to know that the terms/names applied to the BIW COMPONENTS are known as BIW NOMENCLATURE.
- The terms are standard but they differ in some countries.
- As automotive industries spread worldwide, the terms and standards will be different for similar components.
- For example, One component of BIW is known as inner wing pannel in the UK description another side the same component of BIW is known as the Motor compartment side panel in the US description.
- Below I have been attached some common terms of BIW which differs from the UK to US descriptions.
Figure 1. BIW NOMENCLATURE 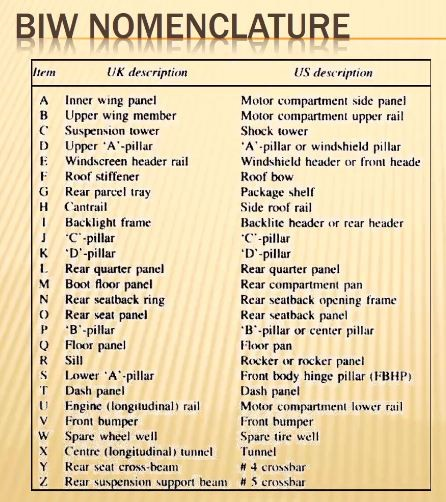
Figure 2. Picture of BIW 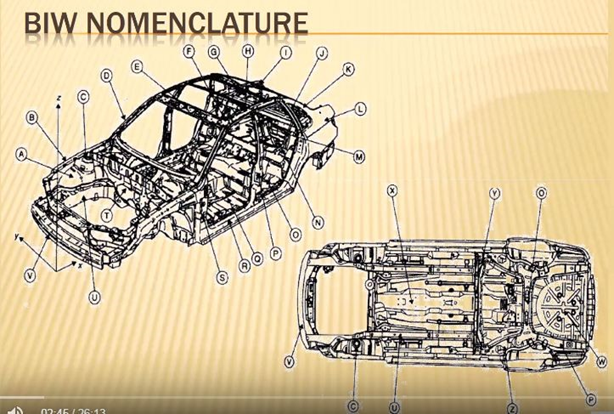
--------------------------------------------------------------------------------------------------------------------------------------------------------------------------------------------------------------------------------------------------------------------
Q3 Ans
FIXTURE:
- A fixture is a device that holds the workpiece to be processed (welded) by using the 3-2-1 Principle.
- In general, a welding fixture tool consists of a number of units together to hold the car pannel and is mounted on a base unit.
- The fixture has to be quite stable and rigid to withstand the welding stresses.
- Welding fixtures are used to hold the parts in the required shape and are used from smaller parts to larger parts of a plane. Before welding, the parts are placed and positioned for the required shape. After clamping the parts by means of clamping unit welding work will be carried out.
Figure 1. Fixture 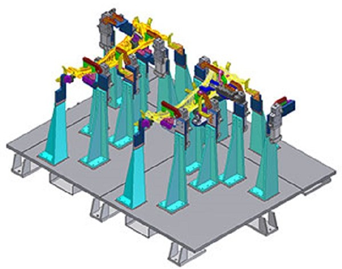
Figure 2. Fixture 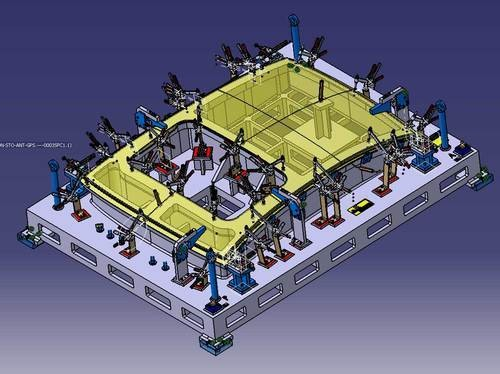
BIW Fixture Types:-
- Production fixtures
- Pre-production operation fixtures(PPO)
- Checking fixtures
1. Production fixtures
This fixture is used for mass production It requires high consistency through its operation to maintain the geometry of the parts so the material used is well tested for hardness & aesthetics. The quality for maintaining the dimensions & tolerances are also checked. The production fixtures need to easy for maintenance purposes. The fixture needs some maintenance after completing no. of operations. The time requires for assembly & disassembly should be as low as possible which saves lots of time.
Figure 3. Production Fixtures 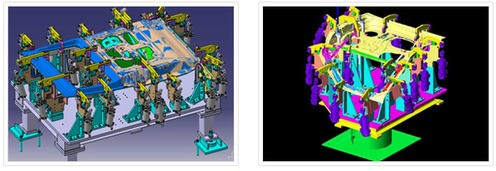
2. Pre-production operation fixtures(PPO)
These fixtures are designed as a prototype fixture to check the feasibility of initial batch production & to check which things need to be improved before starting the These fixtures can be taken as the base fixtures which sets the benchmark & criteria which help us to rectify the errors that we could get from preproduction operation fixtures. In this many manual operations are involved, many engineers & quality-related persons are required. It has a large cycle time as compared to production fixtures. It requires lots of time & cost also. We have to maintain the cost of the car as low as possible so we directly go to the production fixture by considering standards, a checklist to maintain the error-free production.
3. Checking fixtures
As the name suggests these fixtures are used for checking No operations like welding gluing or hemming are carried out in these fixtures. The gauges are used in these fixtures to get the dimensions & the tolerances part having & the data is compared with the designed dimensions to check whether the part is ok or not. The geometry of the welded parts is also checked in these fixtures to ensure the parts maintain the required dimensions & geometry.
Figure 3. Checking Fixtures 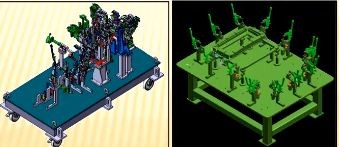
-----------------------------------------------------------------------------------------------------------------------------------------------------------------------------------------------------------------------------------------------------------------------
Q4 Ans
3-2-1 principle is used for the design of the fixtures
- For a fixture designer, the major portion of design time is spent deciding how to locate the workpiece in the fixture.
- You know that any free body has a total of twelve degrees of freedom as below:
6 translational degrees of freedom: +X, -X, +Y, -Y, +Z, -Z And
6 rotational degrees of freedom:
- Clockwise around X-axis (CROT-X)
- Anticlockwise around X-axis (ACROT-X)
- Clockwise around Y-axis (CROT-Y)
- Anticlockwise around Y-axis (ACROT-Y)
- Clockwise around Z-axis (CROT-Z)
- Anticlockwise around Z-axis (ACROT-Z)
Figure 1. Showing Degrees of Freedom 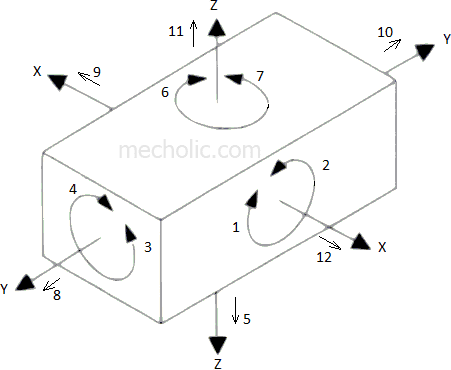
PRIMARY LOCATOR:
First, the three locators or supports are placed under the workpiece. It will be positioned on the primary locating surface also known as a datum. It will restrict 5 degrees of freedom.
- Axial Movement downward along Z-axis ( No.6 in Fig 1 )
- Rotation about the X & Y axis ( No. 7, 8, 9 & 10 in Fig 1)
Figure 2. Primary Locators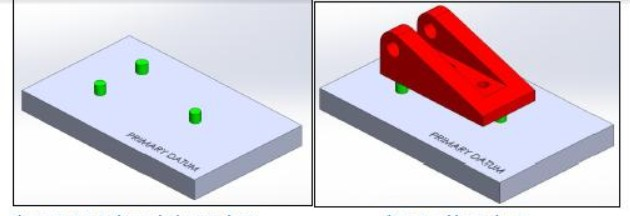
SECONDARY LOCATOR:
The next two locators are normally placed on the secondary surface, restricting an additional 3 degrees of freedom.
- Axial movement along the Y+ axis ( No.3 in Fig 1 )
- Rotation about the Z-axis ( No. 11 & 12 in Fig 1 )
Figure 3. Secondary Locators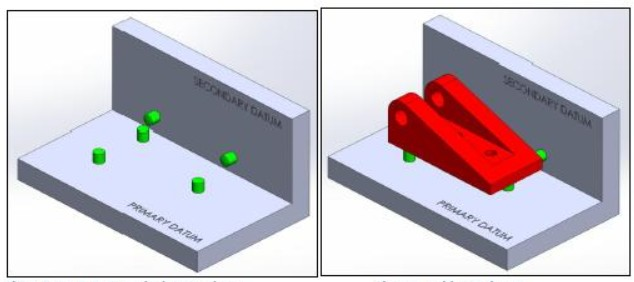
TERTIARY LOCATOR:
This locator is positioned at the end of the part. It restricts 1 degree of freedom
- Axial movement along the X-axis ( No.2 in Fig 1)
Figure 4. Tertiary Locator 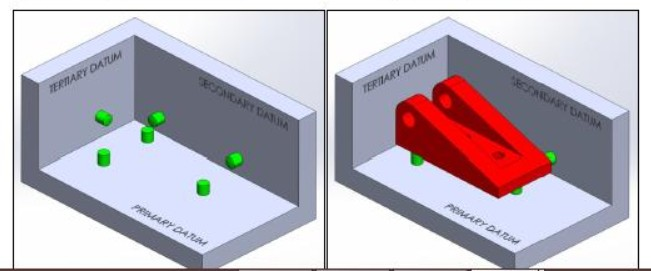
- All these 6 locators will restrict a total of 9 degrees of freedom. The remaining 3 degrees of freedom ( 1, 4 & 5 ) will be restricted by the clamps.
- To minimize the time consumption in assembly and disassembly, Have to use minimum numbers of pins to arrest a maximum number of degrees of freedom.
- The jig and fixture are tools used for holding the workpiece in a correct location for mass production. Various types of fixtures (like drilling fixtures, milling fixtures, and welding fixtures) are used in industry. The 3-2-1 method is the fundamental principle for all types of fixture design.
-----------------------------------------------------------------------------------------------------------------------------------------------------------------------------------------------------------------------------------------------------------------------
Q5 Ans
Elaborate types of BIW Stations:-
BIW Station is the part of BIW assembly line. The BIW assembly line is divided into zones & these zones are again divided into stations.
The BIW stations are further divided into following
- Tool stations
- Gripper stations
- Stand station
- Miscellaneous stations
1. Tool Stations
A) Geo Fixtures:-
- In BIW we consider Tack / Geo In Geo fixture tack welding done for all the parts to be assembled in that fixture. The geo fixture defines the geometry of the part.
- All the parts must be located with two locating pins ( Pin can be common for two or more )
- These Jigs have a tight accuracy standard. In the case of the Geo fixture, all the machine parts individually should be made with max tolerance of ± 0.02 mm. Whereas positional accuracy of the pin should be within -0.15 mm.
Figure 4. shows the accuracy requirements of geo fixture 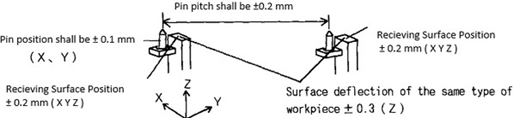
- In Geo fixture spots/ MIG welding done in such sequence that after taking out from the fixture it achieve the desired accuracy and doesn’t get disturbed during transportation from Geo fixture to re-spot Geo fixture control the sub assy accuracy in all the 3 axis.
Figure 5. shows the Bodyside geo fixture 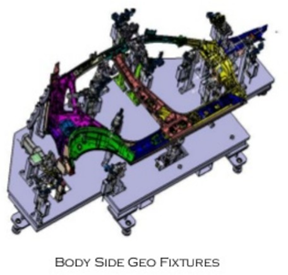
B) Re-spot Fixtures
- In BIW we consider Re-spot In Re-spot fixture remaining tacks are completed.
- Suppose in an assembly we need 50 welds On one station we cannot complete all these operations because it will take more time & another station relative to the assembly will be in ideal condition.
- In this type of case, we carefully choose some weld tack points which will define the geometry of the part & also the assembly will not get deformed after opening the clamping or in transportation due to the welding
- The remaining weld tacks will be completed in a Re-spot fixture as per By performing this kind of operation no station will be ideal Hence we use Re-spot fixtures.
- Re-spot fixtures also have very tight positional Re-spot jig pin tolerance will be -0.28 mm.
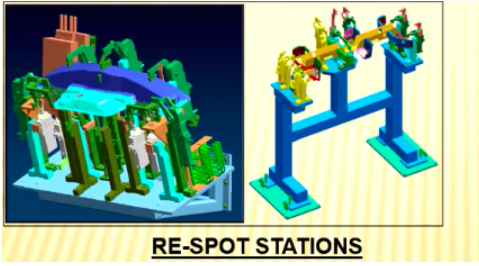
C) Marriage/Hemming Fixture
- As the name suggests the marriage of different assemblies is carried out in this
- In different zones of the assembly line, different assemblies are completed like underbody, Side body, Front body, Rear body, etc.
- After this, all the parts come to the station where all parts are gets assembled by using various joining techniques like welding, Gluing, Riveting This station is called a marriage tool.
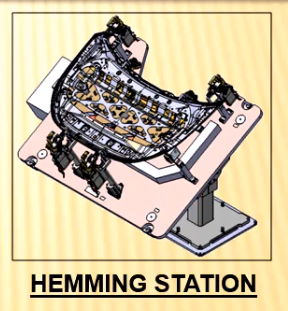
D) Framer Fixture
- Framer fixture is next station after the marriage.
- In framer fixture, the roof is attached to the output of the marriage fixture & it forms like a frame hence it is called a framer

E) Checking Fixture
- These are used to check the assembly of parts, Tolerance, Dimensions &
- It can be of gauge type, Fixed type of automated checking.
- A checking gauge is a tool where the workpiece is held & different measuring gauges are introduced to ensure dimensions & repeatability.
- A fixed type checking fixture is used where the workpiece is fixed with clamps & pins & CMM is used which measures the coordinates of the different points of the panel or Then is compares with the CAD data & gives a report.
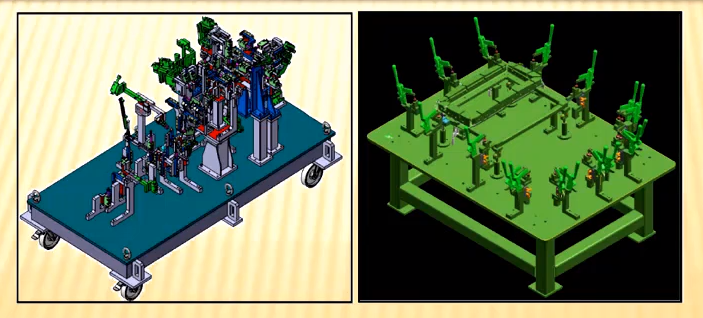
2. Grippers Stations
A gripper is a device that enables the holding of an object to be manipulated. The easier way to describe a gripper is to think of the human hand. Just like a hand, a gripper enables the holding, tightening, handling, and releasing of an object. A gripper is just one component of an automated system. A gripper can be attached to a robot or it can be part of a fixed automation system.
Different grippers are used in BIW as follows,
A) Material handling gripper
- As the name suggests These grippers are used for material
- These grippers can pick assembly from one station & will drop the assembly at another
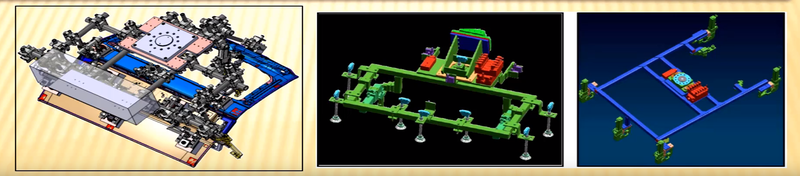
B)Process grippers
- These grippers are used to carry out some specific processes like gluing, welding, riveting in addition to material handling.
- The gripper will go under gluing stand in case of gluing process & will goes under the pedestal weld stand in case of the welding process.
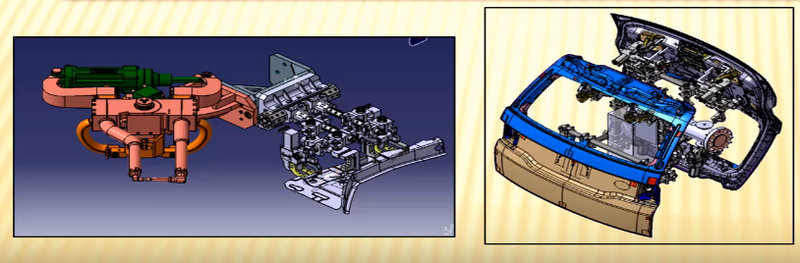
C)Combo Gripper
- Combo grippers are the ones which can carry out multiple tasks like it can do material handling & also it can carry out some specific process like gluing, welding as well.
- Weld gun + Gripper
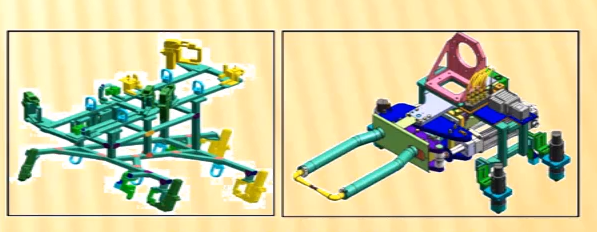
D) Dual Gripper
- These are two-sided In case when we want one LH & one RH part, these grippers are used. It can handle the material from one station to another station
- Gripper + Gripper
3) Stands Stations
Stands are used to hold the part when not in use or also it is used to mount some parts or bodies on it.
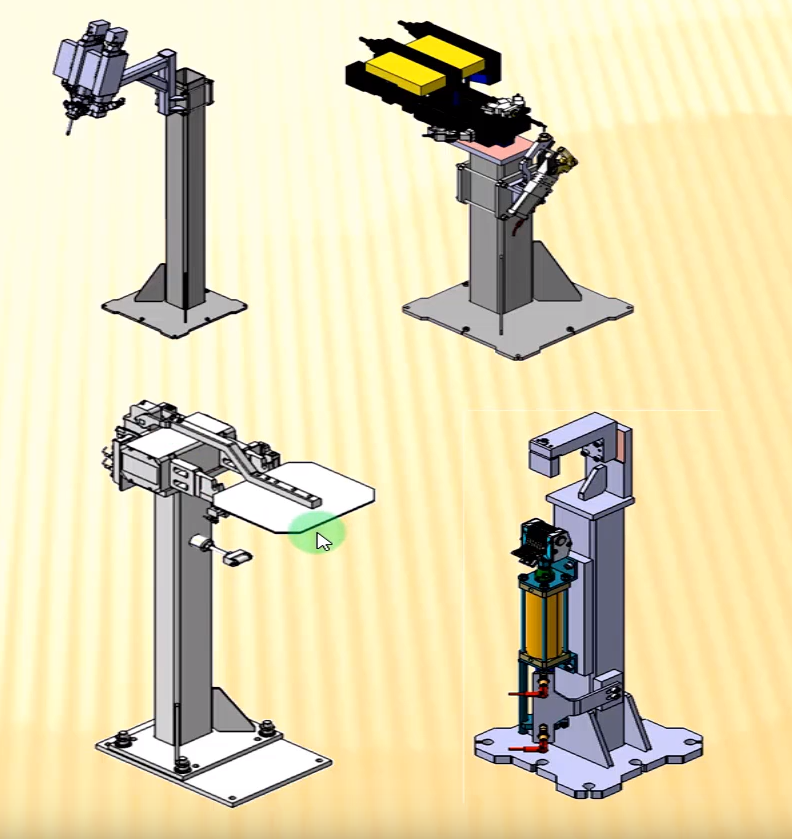
Different stands are used in BIW
A) Pedestal stands
- Weld gun is mounted on the fixed stand which is mounted to the floor The gripper can carry the panel under the stand to do the operation.
B) Gluing & sealer stand
- Gluing gun or sealer gun is fixed to a welded or a standard stand which is grouted to the floor
C) Docking stand
- The robots have some limitations such as the payload capacity of the robot & also due to lack of
- When we select the robot for multitasking it can't do both the task simultaneously due to
- In this kind of case, we add a docking stand to put some equipment that is not in use for the current operation but will be required for next
- Hence the robot can drop a gripper or gun & pick the next operation equipment to complete the task from the docking
D) Date stamp stand
- Every manufactured product has some data to stamped or to be embossed on it like serial no, batch no, Date for some future reference, or for data collection.
- The required data is stamped or embossed by using the stamping device mounted on the
4) Miscellaneous stand
A) Curing
- After gluing it needs some time to cool down, so we put the assembly on some belts & it will take the panel to another station & meanwhile gluing will cool down.
B) Buffer stand
- After some operation, we can put the no. of assemblies in this stand which is buffer stock & it can be transported to another station in easy They are also used to store the inventory while the machine is undergoing some maintenance.
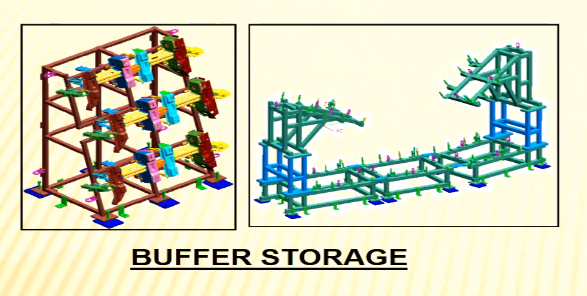
C) Take out trolleys
- It used to take out some panels for inspection to rectify the process is going in the right or not between the cycle.
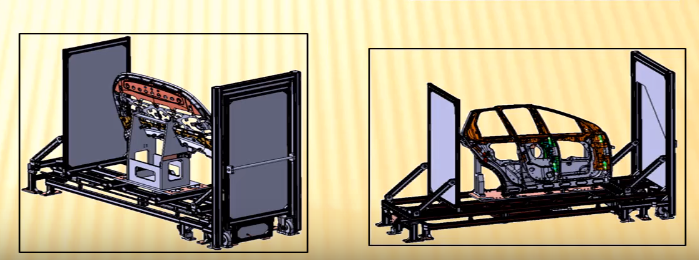
D) Conveyor
- The conveyor is the rotating path that transports the parts to the next station which are kept over it.
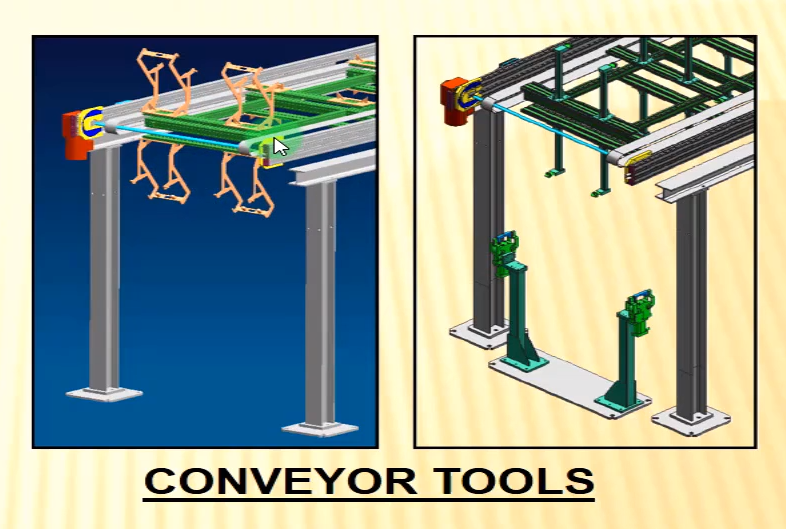
-----------------------------------------------------------------------------------------------------------------------------------------------------------------------------------------------------------------------------------------------------------------------
Q6 Ans
Basic terminologies used in the BIW fixture
- The following terminologies are used in BIW
A) NC/Mylars/Fingers
- Mylars are the component that holds the panel while These are placed from topside & from the bottom side also. The top side Mylars called Clamping Mylars & the bottom side Mylars called Resting Mylars. Every clamping Mylars have resting Mylars. It doesn't allow deformation of the part due to welding stresses.
B) Principle locating point (PLP)
- These are the points that are used for the accurate location of the part to maintain the geometry of the There is lots of holes on the panel which are not accurate due to stamping operation. The PLP are defined in the drawing. The positional dimensions or relative dimensions are very precise in stamping & in fixtures also.
C) Risers
- Risers are of different types like L-typer rises, Square tube riser Riser is the manufacturing part which gives height to the assemblies.
D) Blade
- Blades are plates mounted on the Other parts like cylinder, arms, etc are mounted on the blade.
E) Shims
- Shims are the small part that comes with the thickness of 0.1mm, 0.2mm, 0.5mm, etc. These will compensate for the stackup tolerance which reflects at the panel holding part called We give tolerance to all the parts of the fixture. Due to this tolerance, the Mylars will either lift up or goes down from their defined position.
- If the Mylars go down from the defined height it will make an impression or dent on the panel.
- If the Mylars lift up then there will be a distorsion due to welding stress. To adjust the Mylars At its defined position we use shims so the panel won't be deformed & also don't get any impression on it.
F) Rough locators
- The operator can place the part in the wrong orientation The rough locator will work as a guide while placing the part in the fixture & the part will be loaded in the desired orientation. It is a part of foolproofing.
G) Hardware
- Hardware is like the Hex head bolts, Allen Bolts, Hex nuts, Spring washers, Self-locking nuts
H) CMM
- CMM stands for coordinate measuring It is a device that measures the geometry of physical objects by sensing discrete points on the surface of the object with a probe. It generates a report by comparing the data with the CAD file data.
I) Unit
- The fixture is the assembly of different types of units to form a There are different units like pin unit, base unit, clamping unit, etc.
J) Number plates
- The number plate is the aluminum embossed plate placed on each unit for easily recognizing the
K) Nameplate
- The data like manufacturing company name, fixture type, Fixture weight is embossed on the plate & joined to the fixture.
L) Clamp Arm
- The clamp arm is the part of the clamp unit which moves an Over clamp arm the Mylars are mounted.
K) Pivot
- It is an axis about which the clamp arm will
L) Class A Surface/Skin surface
- The outer panels of the car like a hood, door, backdoor, fender, roof are visible to the customer.
- The outer panels should be aesthetically very good. No scratches or dent is acceptable over it.
- While designing the fixture to the skin surface the clamping material should be soft, so that it could not able to left any impression or dent over the skin. generally, nylon or PU material is used for clamping purposes.
O)Reed switches & sensors
- These are the electric components used in automated The reed switch is an electrical switch operated by an applied magnetic field. The detects the panel is loaded or not is done by sensors.
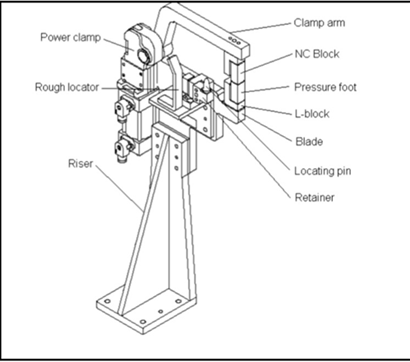