TITLE: ASSEMBLY AND PHOTOREALISTIC RENDERING - AMERICAN CHOPPER BIKE
OBJECTIVES:
The main objectives of this project are-
- Modelling all the parts of the American Chopper bike, which include - Chain, Transmission belt, Front/rear wheels, Front/rear fenders, Chassis, Engine, Front fork, Gas tank, Oil tank, Kickstand and Pedals using Solidworks.
- Assembling the parts using Solidworks.
- Adding decals and appearances to the model.
- Photorealistic rendering of the assembly using Photoview 360
INTRODUCTION:
Designing is the first step to creating a model and bringing an idea to life. Solidworks is a software that helps to make designing a much faster and easier process by offering various tools and accessories that are dynamic in nature and prove to be quite helpful. In this project, Solidworks was used to design and model all the parts of the American Chopper bike. The parts were then put together using the Solidworks Assembly feature. Add-ins provided in the software like Photoview 360, were also used to render and make a photorealistic model of the same.
DESIGN METHOD AND APPROACH:
The designing of American Chopper was done in the following dominant steps:
- Designing of parts:
The parts were modelled in the following order;
Transmission belt -> Kickstand -> Front fender -> Rear fender -> Chain -> Oil tank -> Pedal -> Front wheel -> Rear wheel -> Front fork -> Chassis -> Engine -> Gas Tank
The various sketching tools and features offered by Solidworks were used for modelling the parts, which will be discussed in the further stages of the report.
Appropriate appearances to individual parts were added after each part was created. This would help in making the design more realistic.
- Assembly of all the parts:
All the modelled parts were put together using Solidworks Assembly.
Various mates like concentric, distance, co-incident, limit angled, width, parallel, perpendicular were used to put together all the parts in the right orientation with respect to the chassis of the bike.
Some changes in a few parts were also made to avoid any interference of parts.
For example, exhaust of the bike was modified to avoid its interference with the chassis of the bike.
- Adding decals and editing appearances:
Decals were added to the bike on the Gas tank, Rear fender and Oil tank to give it a more realistic look.
The two methods used to apply decals on the parts were:
1. Projection
2. Label
*[Note: Decals on gas tank are not visible due to a possible software bug. Unrendered images have also been added to show applied decals.]
- Setting the bike up in the environment:
Mates of the front wheel, rear wheel and kickstand were made with the Bottom plane to set up the bike in a way that it appears to be resting on the floor.
The kickstand was modified (made shorter) in a way that it would be tangential with the bottom plane and the bike would rest without any interference with the floor.
- Photorealistic rendering:
The Photoview 360 add-in provided by Solidworks offers a variety of Render tools and rendering options.
It was used to set up the environment that the Chopper was placed in, and to edit the scenes.
A camera was added to set perspective and to view the bike cleary.
The lights in the scene were modified.
Various rendering options were used to set the render parameters like Bloom, Caustics, Gamma value, Scene brighness, Ambient occlusion, etc.
Final renders of the bike were made in different views, (Front view, Top view, Isometric view, LHS/RHS view and Camera setup view)
Rendered part images were also taken to view each part clearly.
The above steps were followed to make the American Chopper bike model from scratch.
DESCRIPTION:
Solidworks offers a wide range of tools and supporting features to make the designing process easier and more DYNAMIC.
The tools and features used to make the American Chopper Bike Model have been listed below:-
- Sketch tools:
These tools are used to draw a sketch on any of the 3 planes (Top plane, Front plane, Right plane). They are the FIRST step for making any model. Any feature to be applied is directly or indirectly linked to the sketches made using sketch tools. Sketches can also be made on reference planes created using the 'reference geometry' option. The most common sketch tools used are as follows:
Circle- Drawing a circle.
Line- Drawing a line. [It can also be used to draw construction lines that help in giving dimensions and references in the sketch.]
Spline- Used to draw curves having a specific curvature weight and angle that are tangential at certain intermediate points called spline points.
Rectangle- Drawing a rectangle.
- Snapping features:
This feature comes very handy for adding relations in the sketches and to view existing relations.
The most common relations displayed under this feature are: Perpendicular, Co-incident, Parallel, Tangent, Horizontal, Vertical, Midpoint, Concentric.
- Extrude boss:
This feature is used to take a 2D sketch and turn it into a 3D figure. It helps to add thickness to the sketch to give it the third dimension. The thickness of the extrude can be set. It can also be given a draft. Various options for extrude are available.
- Revolved boss:
This feature is similar to an extrude boss. However, it takes a 2D sketch and turns it into a 3D model by revolving the sketch about a specific axis and creating a solid.
The angle of the revolve can be changed depending upon the design requirements.
- Swept boss:
This feature is similar to the extrude boss. However, it is a bit more complicated. It requires 2 main elements- A closed profile and a path starting from the profile.
The feature takes the closed profile and gives it a thickness or extrudes it along the path. Thus, the path is an important parameter that drives the curve of the Swept Boss.
- Extrude cut:
This feature is like the opposite of the Extrude boss. It removes material in the specified directions from a solid model, based on the sketch that is used to initiate the feature.
- Revolved cut:
This feature, too, is used to remove solid material from the model. However, based on the initiating sketch, the cut is made about a specified axis of rotation for the sketch.
- Reference geometry:
This is a very important feature that allows us to create reference lines or planes. This helps in making complicated designs that have a lot of curvatures and profiles.
New sketches can be drawn on the planes that are added. The new reference elements are added in relation to pre-existing elements in the model.
- Split feature:
This feature is used to split different parts of the same solid model based of the selected intersections. It can also be used to cut out and eliminate the split parts to make changes to the model.
Thus, it helps to cut out bodies in cases where extrude cuts may be difficult to use.
It is a very handy tool to consume bodies based on other intersections.
It is also beneficial to use because in case of changing the dimensions of your design, you need to control fewer sketches and the task becomes easier.
- Shell feature:
This feature is used to turn solid bodies into hollow objects. The thickness of the shell can be easily monitored.
- Curve driven patterns:
This feature is used to take sketches/features/solid bodies and replicate them along a curve, known as the driving curve. The number of instances of the replicated elements and the distance between them can be easily controlled.
- Sketch blocks:
This is a very handy tool that helps us save time. It helps to take a sketch, isolate it, and save it separately. It can then be imported in any other file as well. This eliminates the need to make the same sketches again and again. The sketch to be used would be earlier saved as an .sldblk file and can be imported into the part document easily.
- Combine feature:
This feature is used to take 2 or more solid bodies and combine them to make one single body.
- Sectional view tab:
This is a very handy feature that helps us obtain the section view of the solid model. The direction of the sectioning can be selected. It can be along any of the standard views as well as other reference planes.
- Linear pattern:
This is similar to curve driven pattern. However, in this case, the driving curve is a straight line.
- Circular pattern:
This, again, is an example of a curve driven pattern. However, the driving curve can be any circular element concentric with the required circular pattern which is to be obtained.
- Mirror:
This tool allows us to mirror elements such as sketches/features/bodies about a mirroring axis. The axis can be a line, a face or a plane.
- Fillets:
This feature helps to remove sharp edges in the model by giving them a curvature. The radius of the curvature can be easily monitored.
- Chamfer:
This feature takes sharp edges and cuts away a right angled edge or corner to provide a sloping edge. This feature helps to add details to the model.
- Dome:
It helps to add a dome on faces. The domes can either be circular or elliptical.
- Intersection curves (projected curves):
This is a very important feature. It takes 2 curves from mutually perpendicular profiles and turns their intersection into a curve. The end result is a 3D curve.
It is slightly compicated to use.
It takes a minimum of 2 sketches from mutually perpendicular profiles. Each of the sketches would be a projected view of the required 3D curve, from the 2 different profiles.
The selected two 2D sketches then give a 3D curve.
It is a very important feature that helps us add 3D curvatures to a solid model.
- Composite curves:
This tool helps to select two or more touching 2D/3D curves and convert them into one single curve.
- Converted entities:
This tool comes handy while sketching. It brings the selected sketch onto the plane/face that a new (current) sketch is being made.
- Surface tools:
These tools are usually used for surface modelling. Some of them are mentioned below:
Surface extrude- This tool takes a 2D curve and protrudes it (similar to extrude boss) to make a surface.
Revolved surface- It is used to make a surface about an axis.
Swept surface- It extrudes a surface along a guiding curve.
Lofted Surface- It creates a surface loft based on the sketch profiles selected and the guiding curve.
- Mates in assembly:
This feature is used to assemble the parts together in Solidworks.
It helps to add relations in order to fixate different parts relative to each other and/or the principal planes.
The different mates usually used are: concentric, distance, co-incident, limit angled, width, parallel, perpendicular.
RENDERED IMAGES OF PARTS:
- Transmission belt
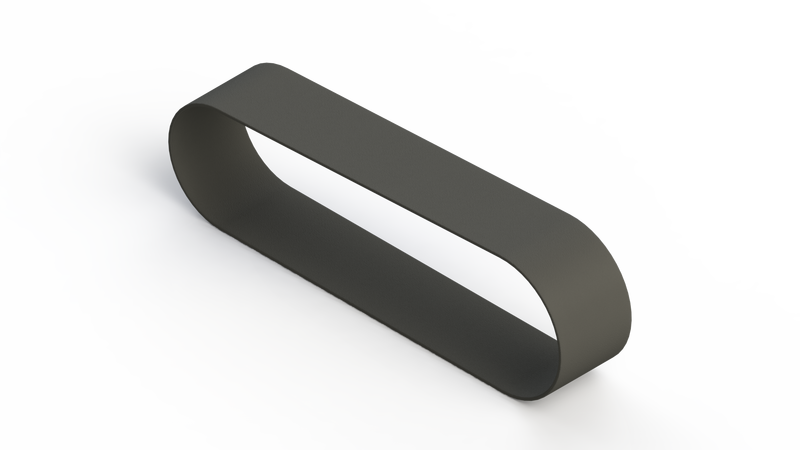
- Chain
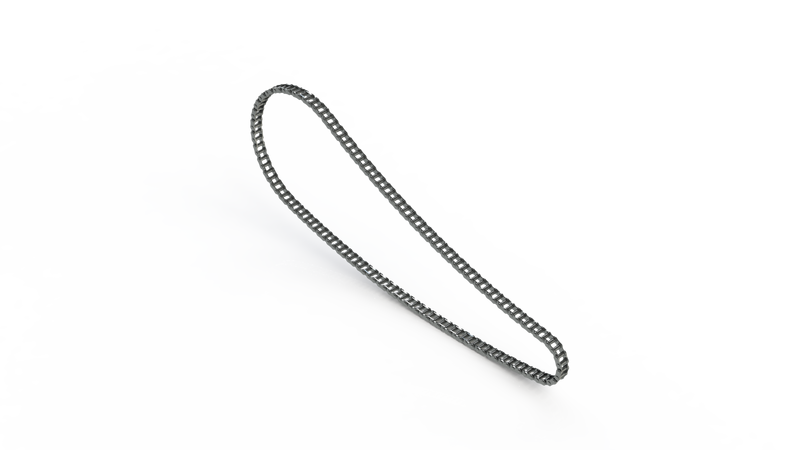
- Front wheel
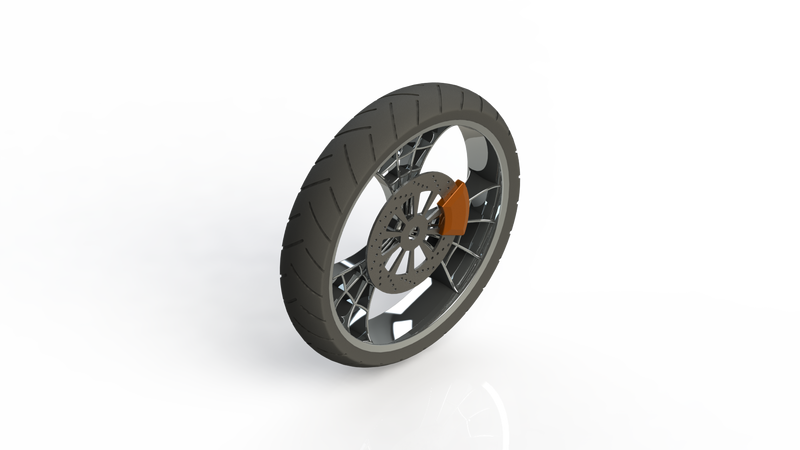
- Front fender

- Rear wheel

- Rear fender
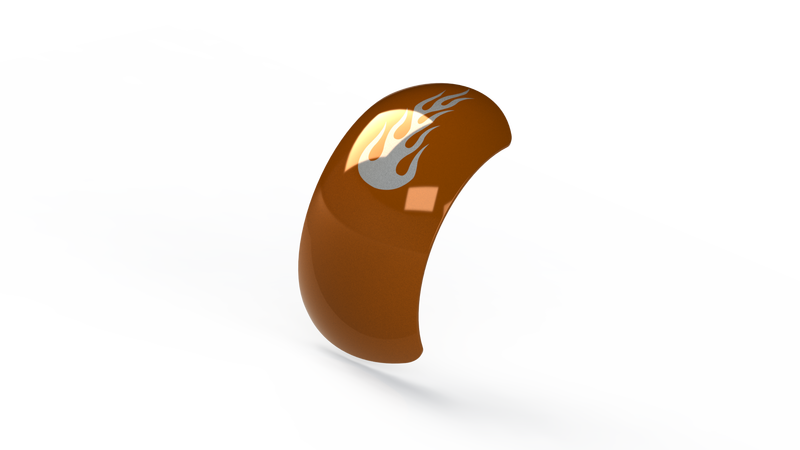
- Front fork
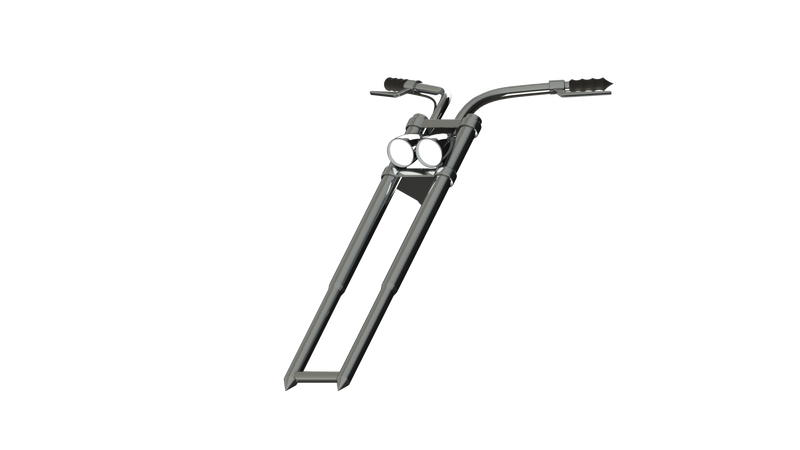
- Kickstand
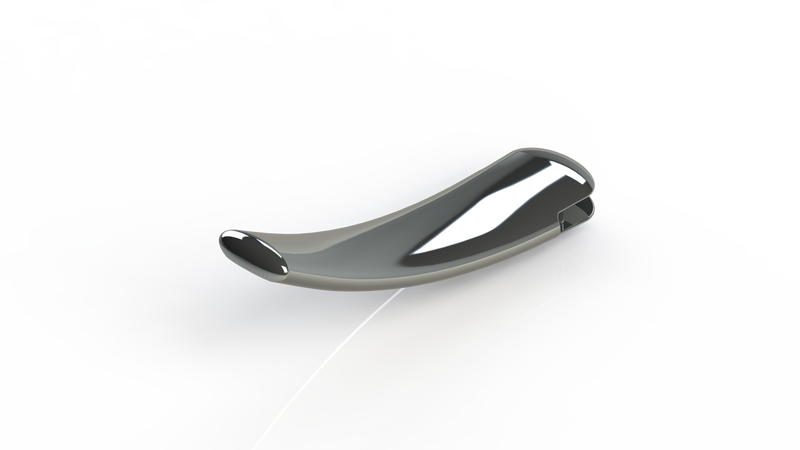
- Pedal
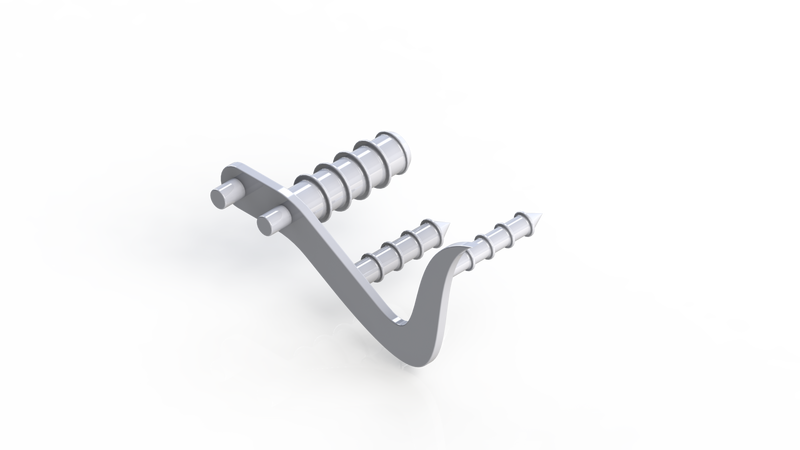
- Oil tank
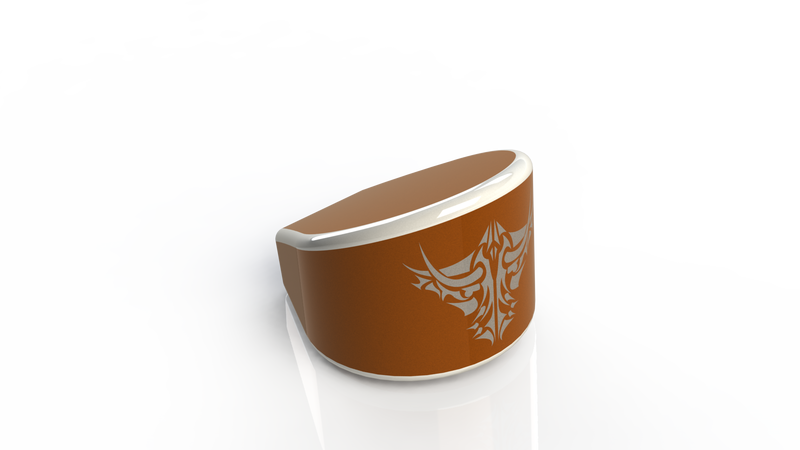
- Gas tank
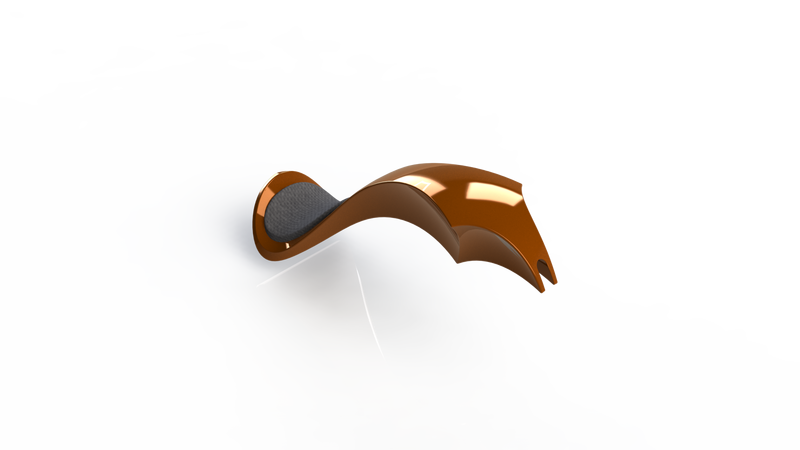
- Chassis
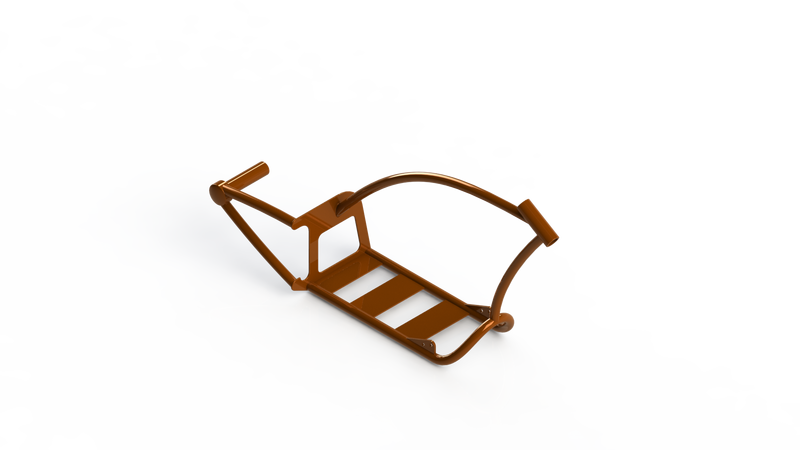
- Engine
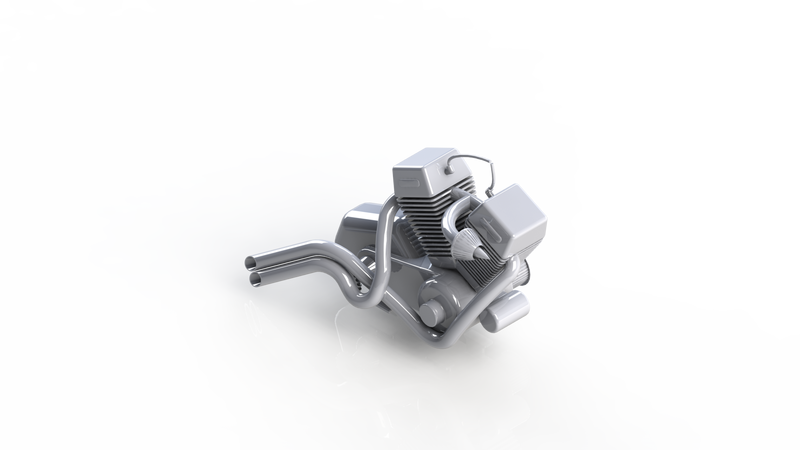
IMAGES OF THE ASSEMBLY (UNRENDERED) :
- Front View
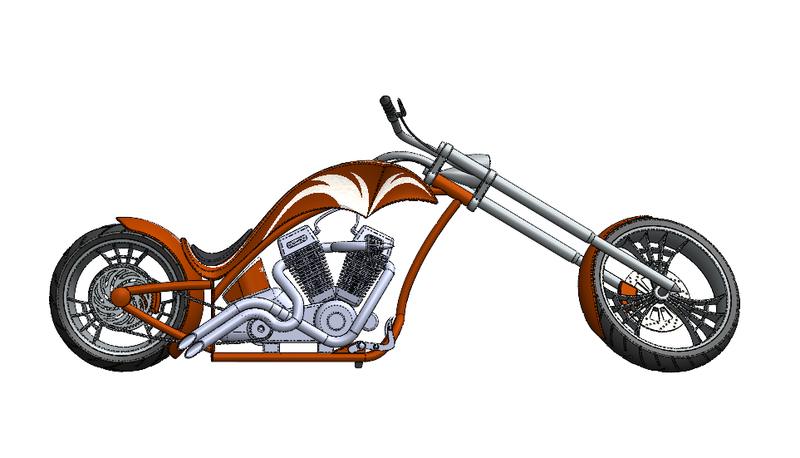
- Top View
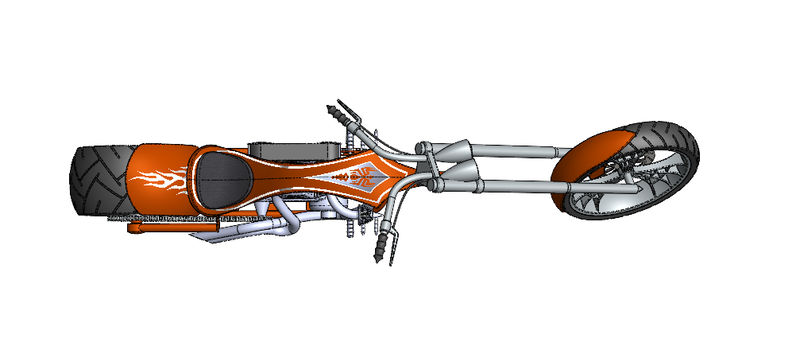
- LHS View (back of bike)
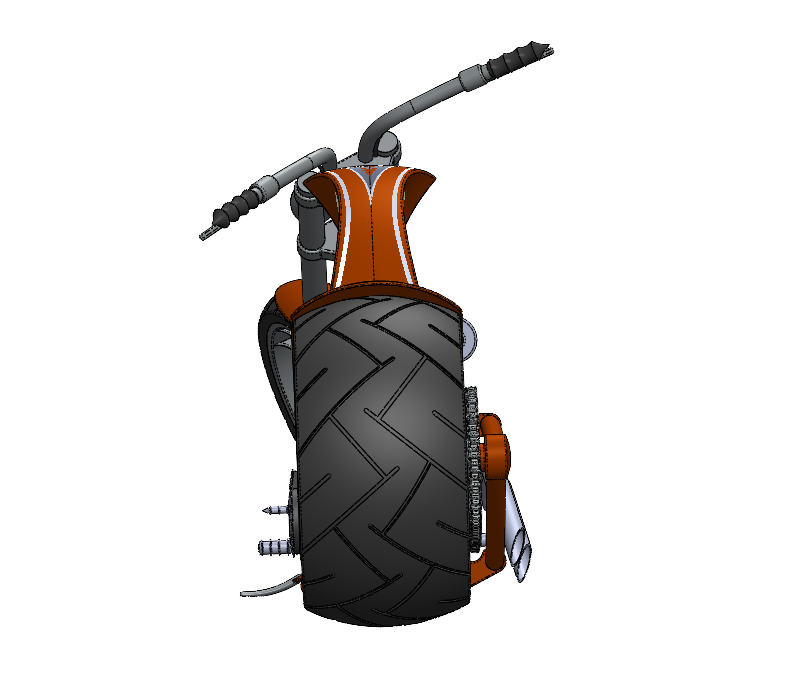
- RHS View (front of bike)
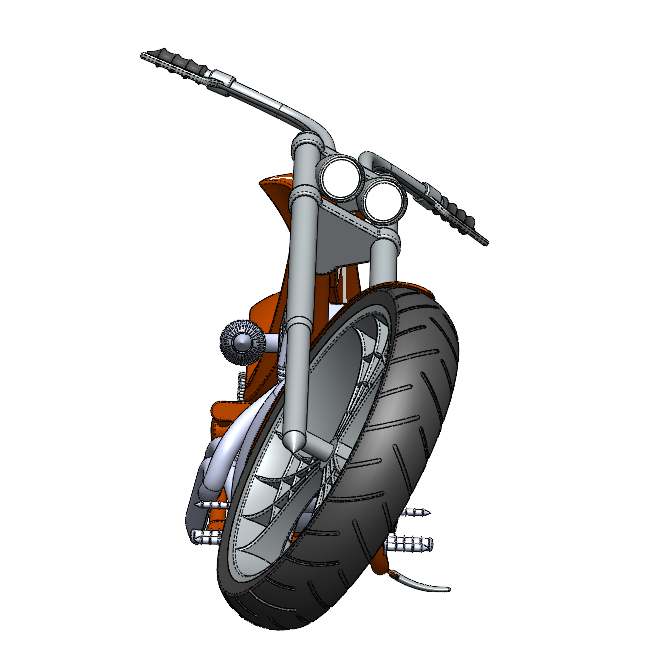
- Isometric View
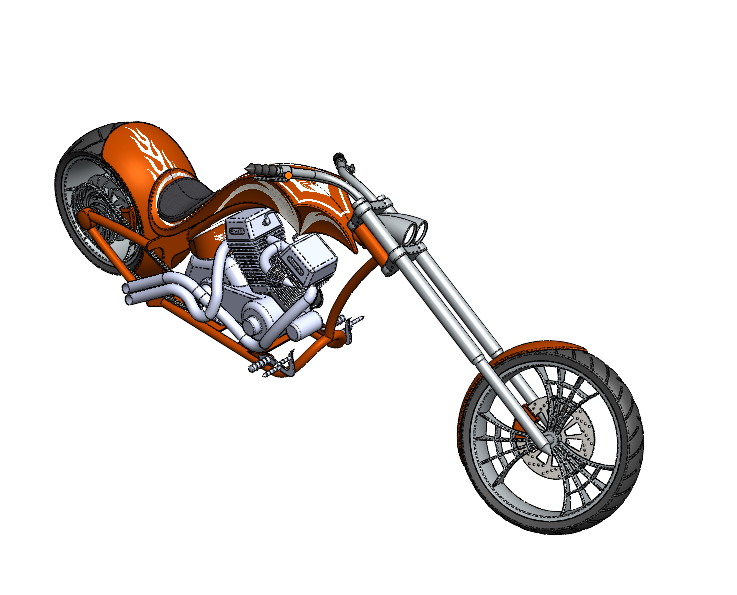
- Camera Set-up View
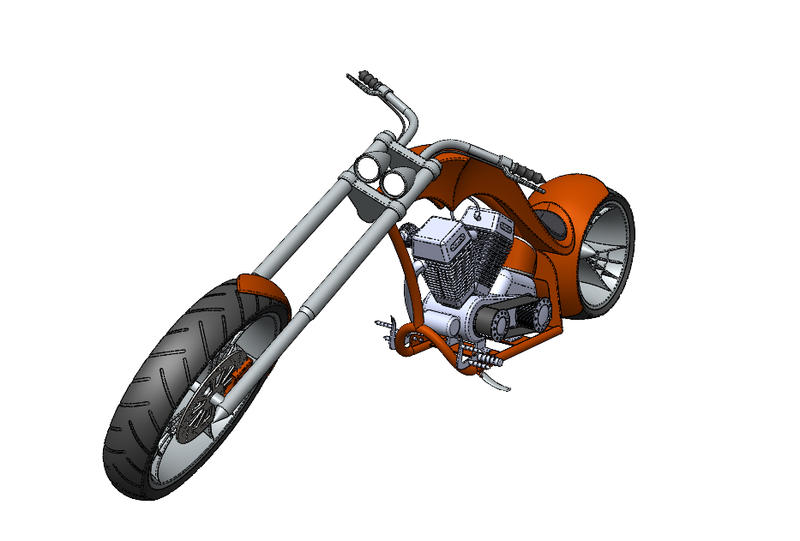
FINAL RENDERED IMAGES OF AMERICAN CHOPPER:
- Front View
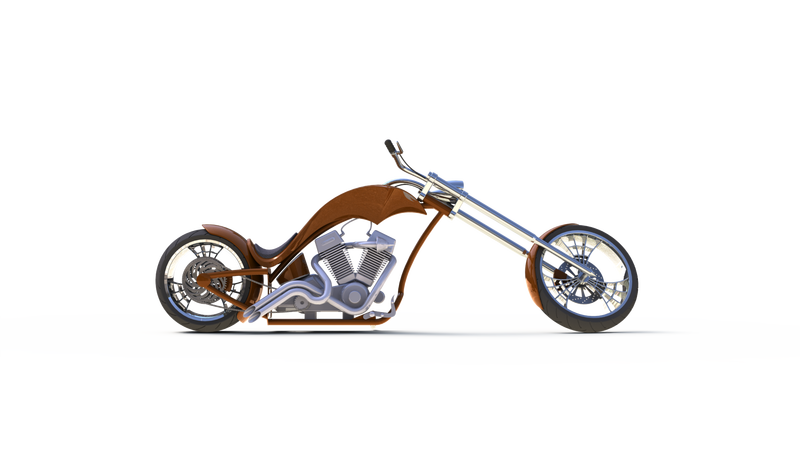
- Top View
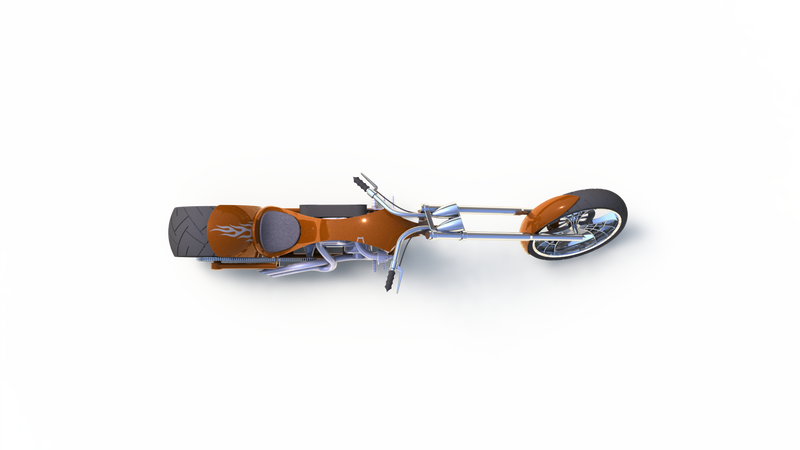
- LHS View (back of bike)
_1617110873.png)
- RHS View (front of bike)
_1617110893.png)
- Isometric View
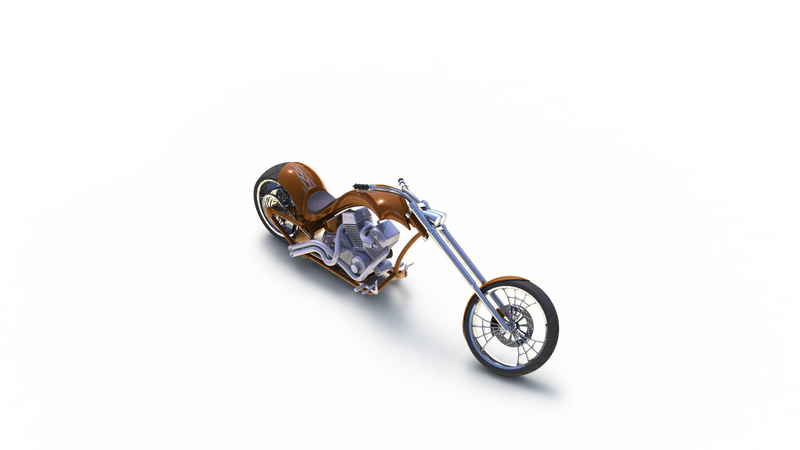
- Camera Set-up View

CONCLUSION:
A wide range of sketch tools and additional features in solidworks were studied to model all the parts of American Chopper.
Assembly of the parts using different mates in Solidworks was done and rectifications in the model were made accordingly.
Decals, Appearances and Scene set up in Solidworks was studied to make the model more realistic.
Photoview 360 was studied to make realistic renders of the American Chopper.
A good understanding of the software was obtained to model, assemble and realistically render parts to complete the American Chopper Bike model.