Objective: To model a F1 car concept using SolidWorks. Creating Photo Realistic Renders using SolidWorks Visualize.
Abstract:
- The objective of this project is to use Solidworks and Solidworks visualize to design, model and create photorealistic renders of the completed assembly.
- The modelling is done using both solid and surface modelling tools available in Solidworks.
- The technical properties of the design like tolerances, dimensions and the performance of the design are not deliberated in this design.
Introduction:
- A Formula 1 car is an open wheeled, open cockpit and single seater racing car.
- Current F1 car have a substantial Front and Rear wing to create high downforce which helps the car to have traction while cornering at high speed which produces high G-force.
- Due to this high G-force, the car needs to have a stronger chassis which is made up of carbon fibre and honeycomd structure.
- As change in ride height or roll during cornering may hinder the performance of aerodynamic components, the suspension needs to be stiffer which is achieved using bell crack mechanism
- The main power house of the engine is a 1.6L Hybrid V6 engine which is capable of producing 875–1,000 + 160 hp (652–746 + 119 KW) @ 15,000 rpm, The additional power is provided by the hybrid system integrated in the power unit which consists of MGU-k and MGU-H.
- MGU-K stands for Motor Generator Unit Kinetic, Which converts kinetic energy from braking to electrical energy and store in Energy Store.
- The MGU-H - Motor Generator Unit, Heat - uses heat from the car’s waste exhaust gases to drive a generator which is stored in Energy Store, and used to reduce turbo lag.
- These two systems are used to drive an electric motor which gives extra power.
Regulation changes (performance) for upcoming era of Formula 1.
- Due to the Aerodynamics on present car there is high level of dirty air created by the leading which intern reduces the chances of the trailing car to have grip while cornering as the trailing car cant produce enough downforce, So future generation are said to reduce the amount of dirty air crated by the leading car.
- Their is also a substatial amount of under body aero dynamics like ground effect.
My design is about the concept of future F1 car. (This model is not the accurate representation of the aerodynamics elements of the actual F1 car.)
Parts to be modelled:
- Front Wing
- Body (rear wing included)
- Front Swing Arm
- Rear Swing Arm
- Front Wheel
- Rear Wheel
- Front Tire
- Rear Tire
- Steering Wheel
- Seat
Modelling:
Front Wing:
- Front wing is responsible for ensuring that there is sufficient grip and traction for the front end of the car.
- It is also responsible for the airflow around the car as it is the first part of the car ro come in contact with air. So it has influence on overall aerodynamics of the car.
- it consists of various components
- End Plate -> Controls the air flow around the car.
- Wing Flaps -> Produces the required downforce according the angle that they are arranged.
Model:
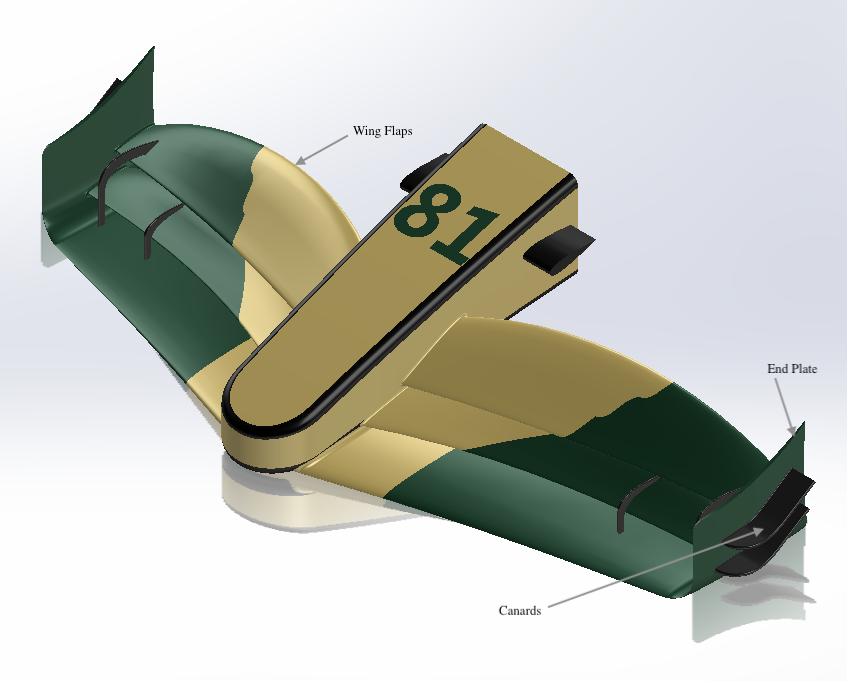
Tools Used:
- Refernce plane: used to create planes with provided constraints
- Project Curve: Merges two sketches on different planes to create a 3D curve.
- Loft Boss/Base: Add material between two profiles to create a solid feature.
- Mirror:Mirrors features, faces or bodies about a plane surface.
- Extruded Cut: Cuts a solid feature using a skecth profile
- Extruded Boss/Base: Creates a solid body by extruding a sketch contour.
- Fillet: Used to create rounded corners or edges
- Combined: used to merge bodies.
- Split: split the body based on a sketch or face.
- Split line: Used to Split a face by projecting a sketch profile.
Body (Rear Wing Included):
- The body consists of Chassis, Engine, Transmission, Floor, Rear Wing, T-wing, Halo, Cockpit, Diffuser.
- Chassis: It is the main structural member of car, it holds every components in place with the help of the fastners, Now, it is made up of light weight carbon fibre which can with stand high G-Forces produced by the car.
- Engine: It is a 1.6L Hybrid V6 engine which can rev at 15000 RPM and produces nearly 1000 HP.
- Transmission: It is a 8-speed seamless-shift Semi automatic paddle, sequential gearbox, longitudinally mounted with hydraulic system for powershift and clutch operation. Fixed gear ratios with a multiplate clutch system.Hand-paddle behind steering wheel below gear shift paddle.
- Floor: The under body of the car is highly retricted by the regulations by the FIA as ground effect is banned, but this is said to be changed for new regulations as ground effect is said to be implemented.
- Rear Wing: About a third of the car's total downforce can come from the rear wing assembly. The rear wings are the ones that are varied the most from track to track. As the rear wings of the car create the most drag the teams tailor the rear aerodynamic load to suit a particular track configuration. DRS is part of the rear wing that can be opened on some parts of the track to help the trailing car to acquire high speed.
- T-Wing: It is the highly effective generator of downforce and it has a high aspect ratio.
- Halo: In 2018 FIA introduced the halo as a part of crash protection system and safety, it is made up of Titanium and weights nearly 7 kg.
- Diffuser: It increases the velocity of air under the body which creates a low pressure area and creates a downforce.
Model:
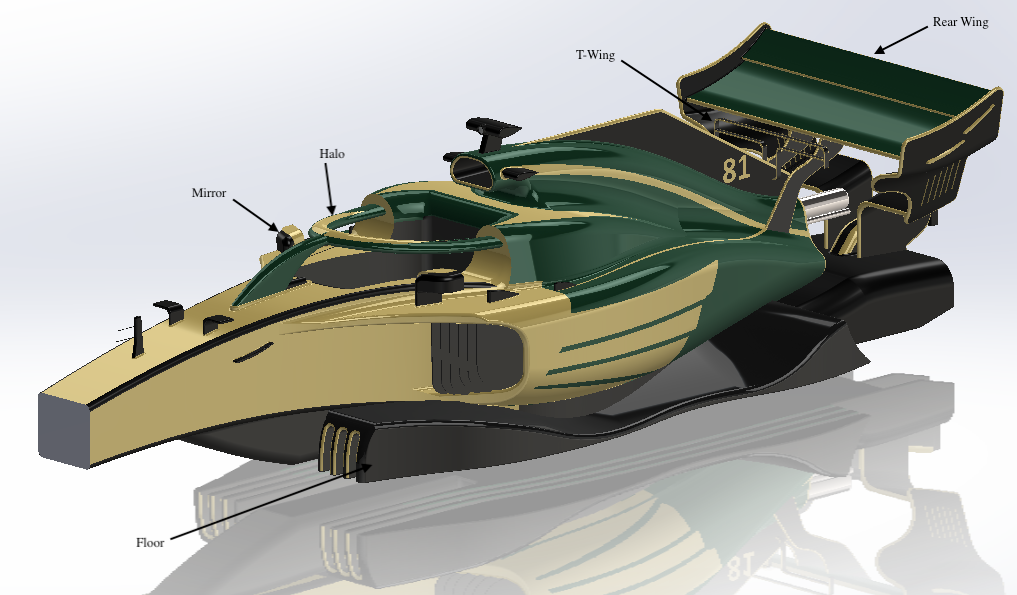
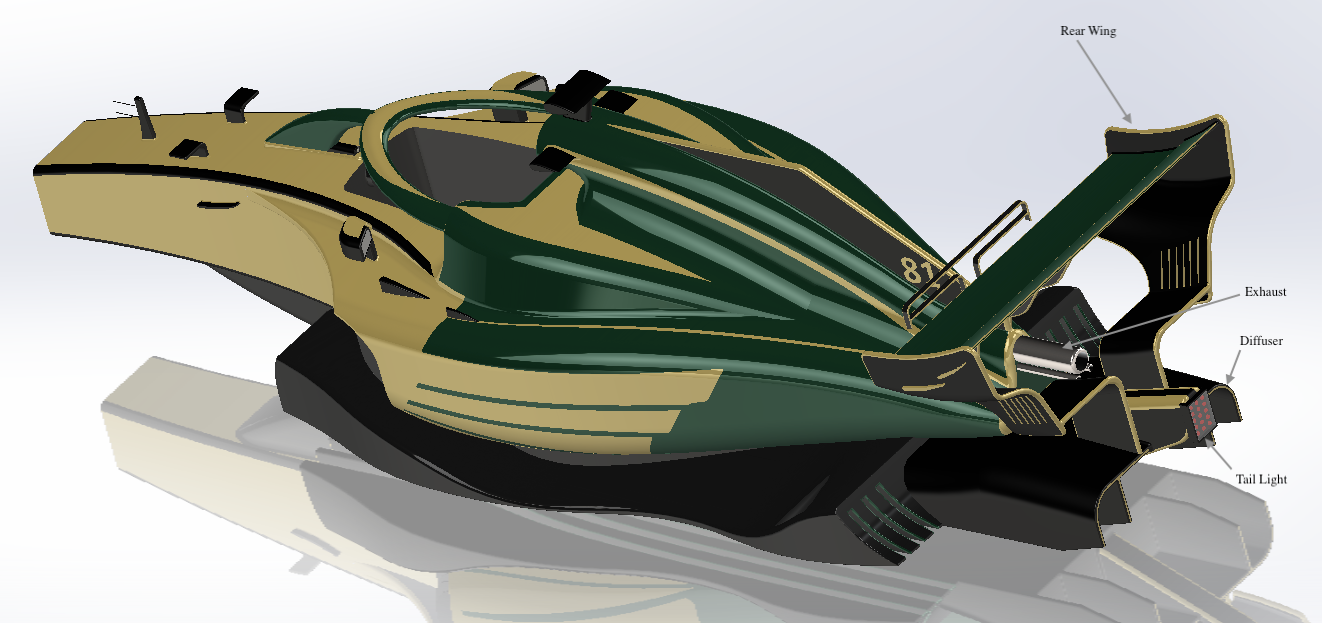
Tools used:
- Refernce plane: used to create planes with provided constraints
- Project Curve: Merges two sketches on different planes to create a 3D curve.
- Loft Boss/Base: Add material between two profiles to create a solid feature.
- Mirror:Mirrors features, faces or bodies about a plane surface.
- Extruded Cut: Cuts a solid feature using a skecth profile
- Extruded Boss/Base: Creates a solid body by extruding a sketch contour.
- Fillet: Used to create rounded corners or edges
- Combined: used to merge bodies.
- Split: split the body based on a sketch or face.
- Split line: Used to Split a face by projecting a sketch profile.
- Chamfer: creates a beveled feature on selected edges, faces, or a vertex.
- Thicken: Creates a Solid Feature using surfaces.
- Surface Offset: Offset any continuous surface.
- Dome : creats a dome feature on a selected flat surface.
Front Swing Arm:
- It is the part of the front suspension assembly.
- It is a bell crank mechanism, so the lateral forces are taken by the Swing Arms and vertical are taken by push rod which is connected to bell crank lever.
- The steering mechanism is also included in this
Model:
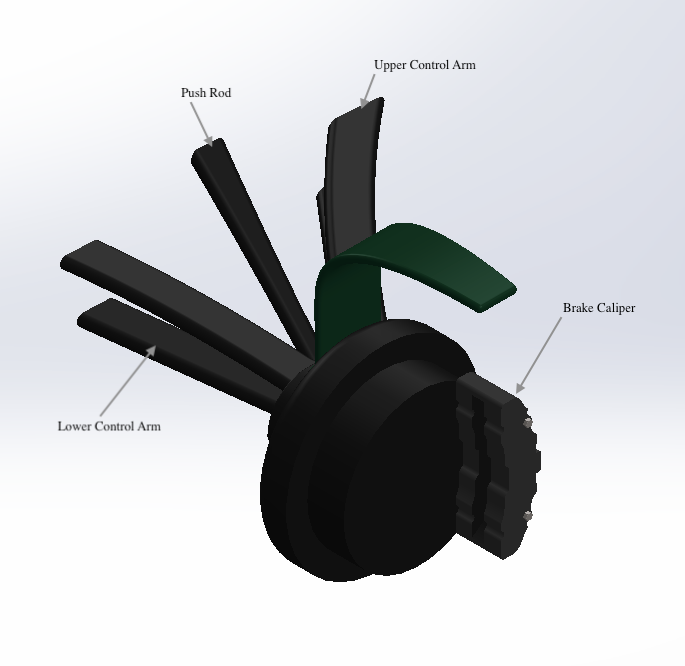
Tools Used:
- Insert Part: import another part file in to the current file
- Refernce plane: used to create planes with provided constraints
- Project Curve: Merges two sketches on different planes to create a 3D curve.
- Loft Boss/Base: Add material between two profiles to create a solid feature.
- Mirror:Mirrors features, faces or bodies about a plane surface.
- Extruded Cut: Cuts a solid feature using a skecth profile
- Extruded Boss/Base: Creates a solid body by extruding a sketch contour.
- Fillet: Used to create rounded corners or edges
- Combined: used to merge bodies.
- Split: split the body based on a sketch or face.
- Split line: Used to Split a face by projecting a sketch profile.
- Swept Boss/Base: Sweeps a closed or open profile along a path and creates a solid feature.
- Surface Offset: Offset any continuous surface.
Rear Swing Arm:
- it is a part of rear suspension assembly.
- It contains upright along with two wishbones and a halfshaft (drive axle) for power delivery
Model:
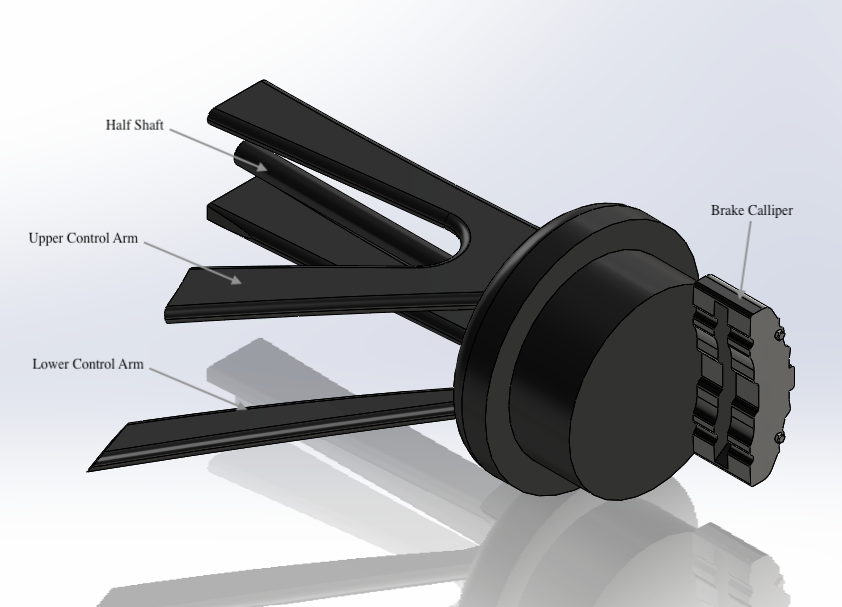
Tools Used:
- Insert Part: import another part file in to the current file
- Refernce plane: used to create planes with provided constraints
- Project Curve: Merges two sketches on different planes to create a 3D curve.
- Loft Boss/Base: Add material between two profiles to create a solid feature.
- Mirror:Mirrors features, faces or bodies about a plane surface.
- Extruded Cut: Cuts a solid feature using a skecth profile
- Extruded Boss/Base: Creates a solid body by extruding a sketch contour.
- Fillet: Used to create rounded corners or edges
- Combined: used to merge bodies.
- Split: split the body based on a sketch or face.
- Split line: Used to Split a face by projecting a sketch profile.
- Swept Boss/Base: Sweeps a closed or open profile along a path and creates a solid feature.
- Surface Offset: Offset any continuous surface.
Front Wheel:
- Today Formula 1 wheels are made from AZ70 or AZ80 magnesium alloys and 13in in diameter and 305 mm in width.
Model:
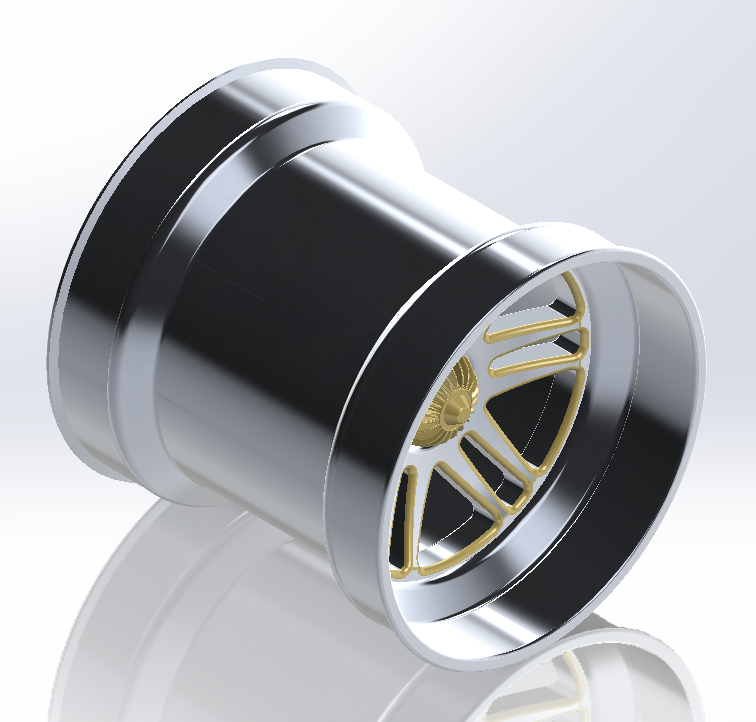
Tools used:
- Insert Part: import another part file in to the current file
- Refernce plane: used to create planes with provided constraints
- Extruded Cut: Cuts a solid feature using a skecth profile
- Extruded Boss/Base: Creates a solid body by extruding a sketch contour.
- Fillet: Used to create rounded corners or edges.
- Split line: Used to Split a face by projecting a sketch profile.
- Surface Offset: Offset any continuous surface.
- Revolve Cut: Revolves a sketch profile aroung a axis to cut a solid part.
- Pattren: Pattrens a features ,faces and bodies along a path linearly or circularly.
Rear Wheel:
- Today Formula 1 wheels are made from AZ70 or AZ80 magnesium alloys and 13in in diameter and 405 mm in width.
Model:
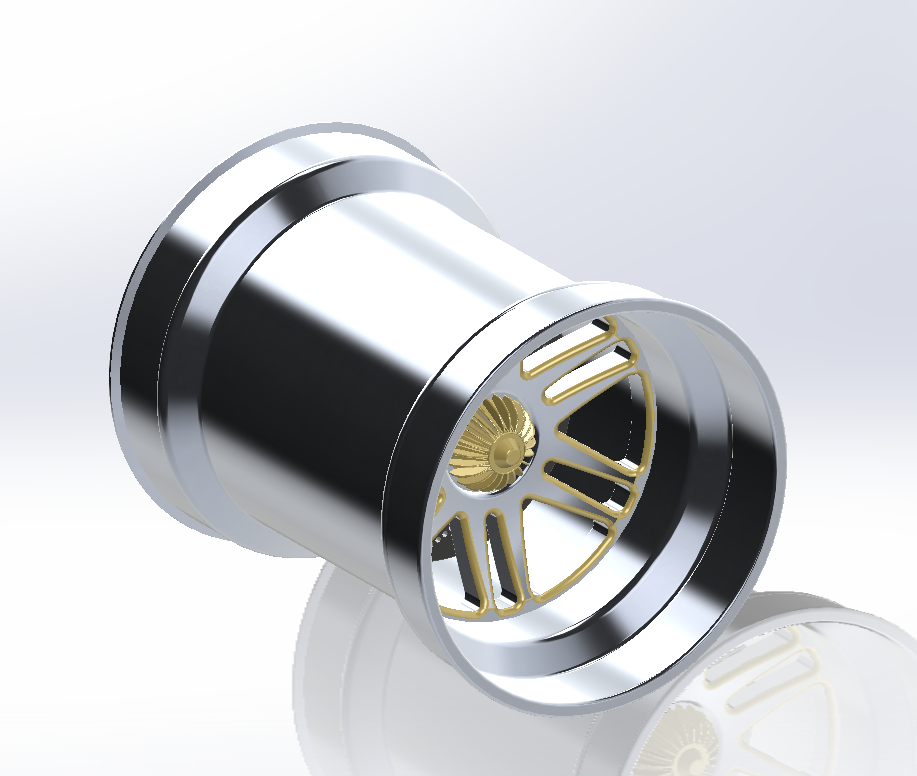
Tools used:
- Insert Part: import another part file in to the current file
- Refernce plane: used to create planes with provided constraints
- Extruded Cut: Cuts a solid feature using a skecth profile
- Extruded Boss/Base: Creates a solid body by extruding a sketch contour.
- Fillet: Used to create rounded corners or edges.
- Split line: Used to Split a face by projecting a sketch profile.
- Surface Offset: Offset any continuous surface.
- Revolve Cut: Revolves a sketch profile aroung a axis to cut a solid part.
- Pattren: Pattrens a features ,faces and bodies along a path linearly or circularly.
Front Tyre:
- There are tyres are divided into slicks,intermediates and wets.
- Slicks are furter divided into hards, mediums and soft compounds which have C1,C2,C3,C4,C5 level of hardness.
- Now, Pirelli is the manufacturer of the tyres.
- The wear on these tyres is pretty high as they won't last for one complete race distance, they pit and chnge the tyres.
- The current tyre size is 13in in diameter and 305mm in width. In 2022, it is said to change to 18in
Model:
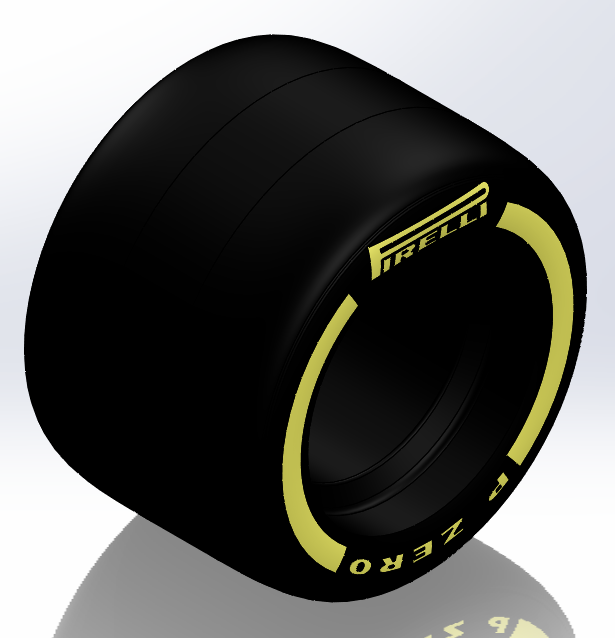
Tools used:
- Insert Part: import another part file in to the current file
- Revolve Boss/Base: Revolves a sketch around an axis to create a solid feature.
- Fillet: Used to create rounded corners or edges
- Shell: Hallows a parts of desired thickness.
- Split line: Used to Split a face by projecting a sketch profile.
Rear Tyre:
- There are same construction and compounds as front tyre.
- The current tyre size is 13in in diameter and 405mm in width.in 2022, it is said to increase to 18in.
Model:
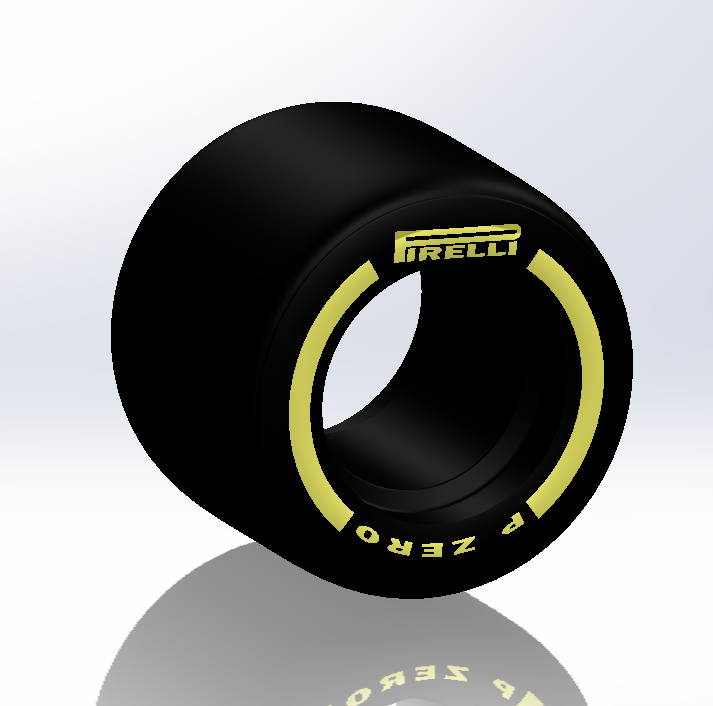
Tools used:
- Insert Part: import another part file in to the current file
- Revolve Boss/Base: Revolves a sketch around an axis to create a solid feature.
- Fillet: Used to create rounded corners or edges
- Shell: Hallows a parts of desired thickness.
- Split line: Used to Split a face by projecting a sketch profile.
Front Wheel Subassembly:
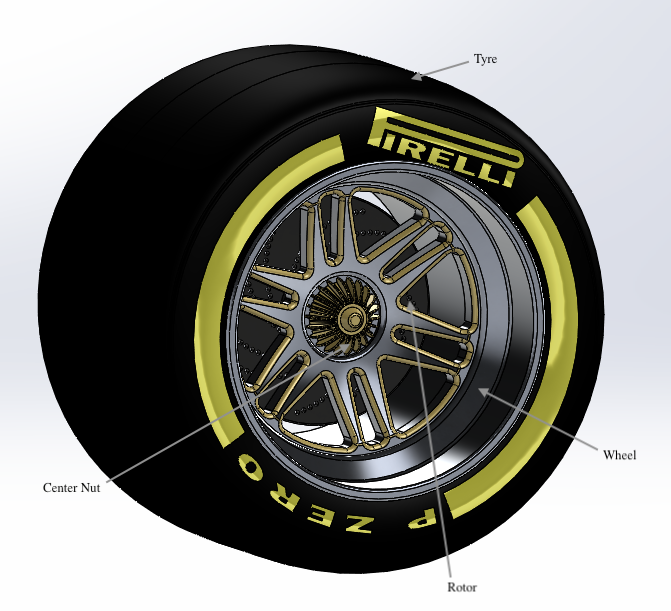
Rear Wheel Subassembly:
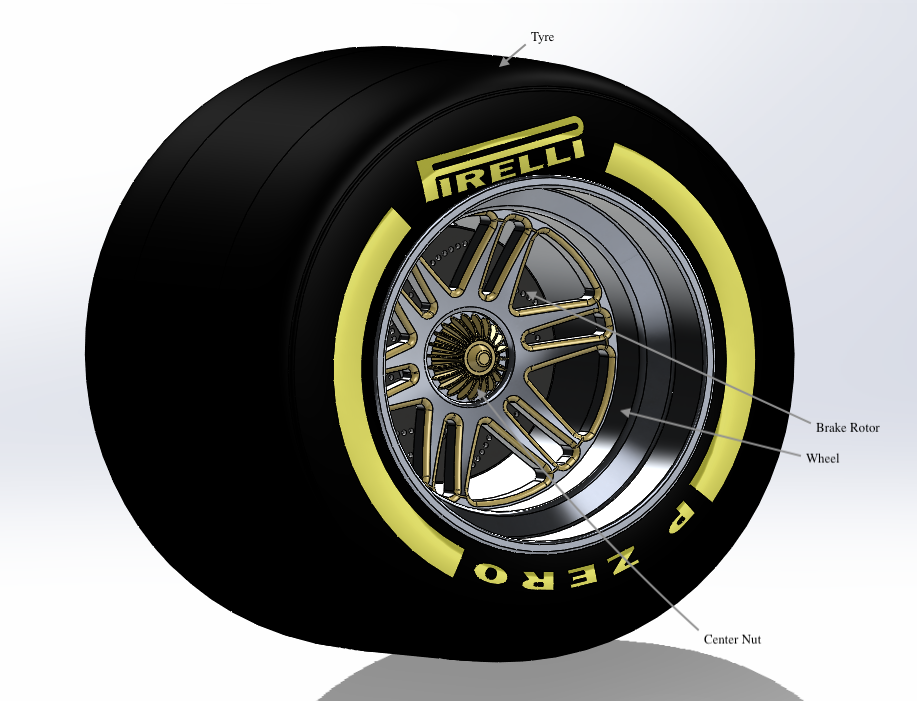
Steering Wheel:
- F1 steering wheel does more than just turn the car. It controls every aspect of the car.
- It controls Engine Mapping, DRS(Drag Reduction System), Coms, Brake Bias, ERS, Differential Locking and many more.
- The Shifting padel and Clutch are incorperated with the steering wheel.
- The main materials are carbon fibre, fibreglass, silicon, titanium and copper.
- The design of steering wheel involves the respective driver to give inputs regarding the steering.
Model
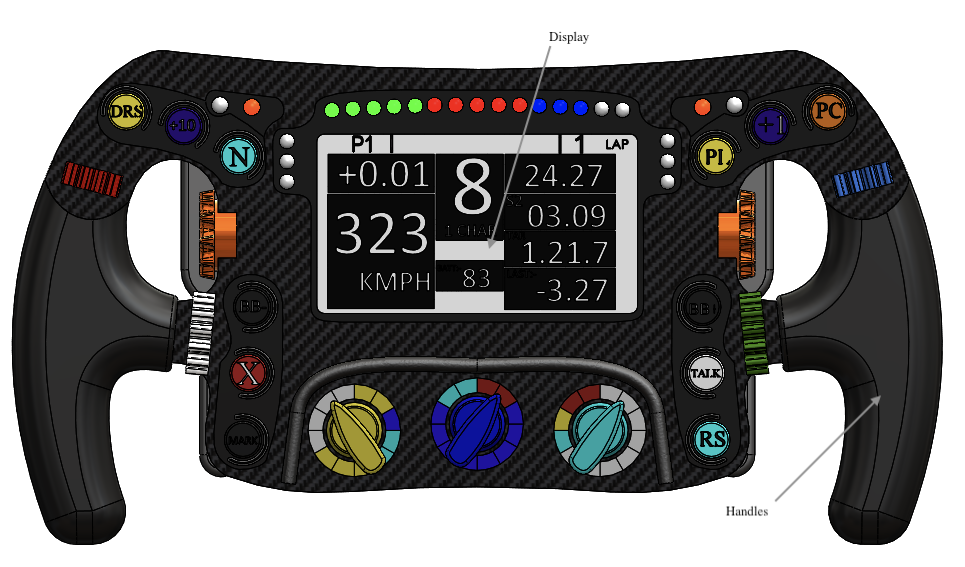
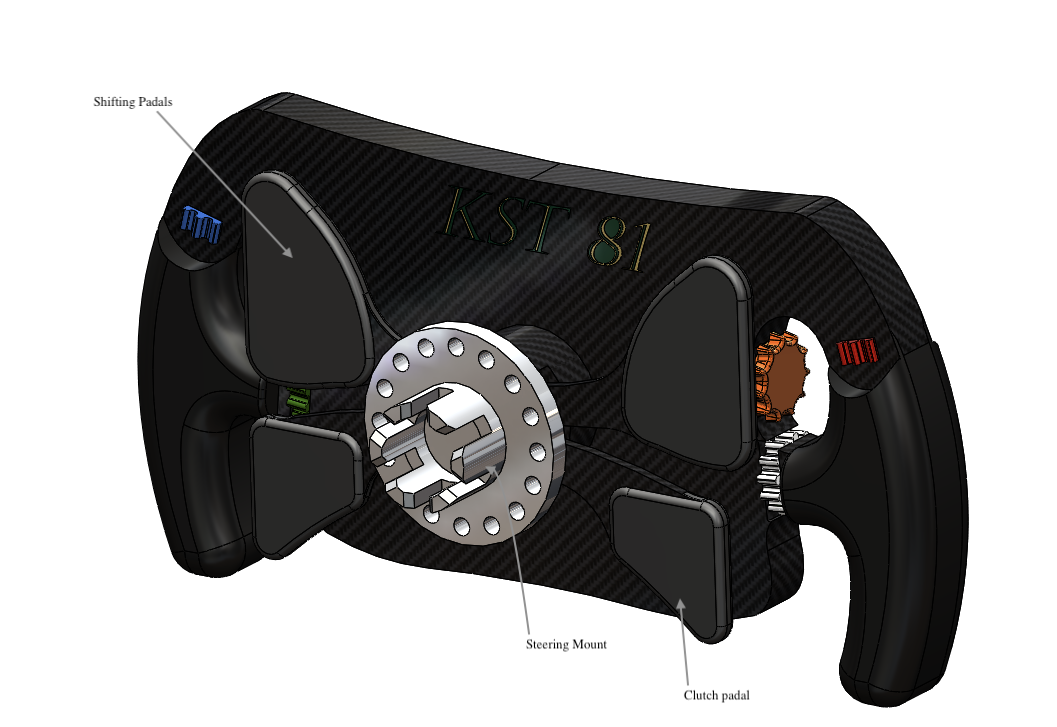
Tools used:
- Refernce plane: used to create planes with provided constraints
- Project Curve: Merges two sketches on different planes to create a 3D curve.
- Loft Boss/Base: Add material between two profiles to create a solid feature.
- Mirror:Mirrors features, faces or bodies about a plane surface.
- Extruded Cut: Cuts a solid feature using a skecth profile
- Extruded Boss/Base: Creates a solid body by extruding a sketch contour.
- Fillet: Used to create rounded corners or edges
- Combined: used to merge bodies.
- Split line: Used to Split a face by projecting a sketch profile.
- Dome : creats a dome feature on a selected flat surface.
- Swept Boss/Base: Sweeps a closed or open profile along a path and creates a solid feature.
- Pattren: Pattrens a features ,faces and bodies along a path linearly or circularly.
Seat:
- The seat is made up of carbonfibre and honeycomb structure which makes it light and rigid.
- It is made by making a mold which is made by the mold obtained by 3d scan of the imprint of the driver with the help for certain material and resin.
- The seat is made in such a way that in case of an accident it can be removed along with the driver with out causing any injury.
Model:
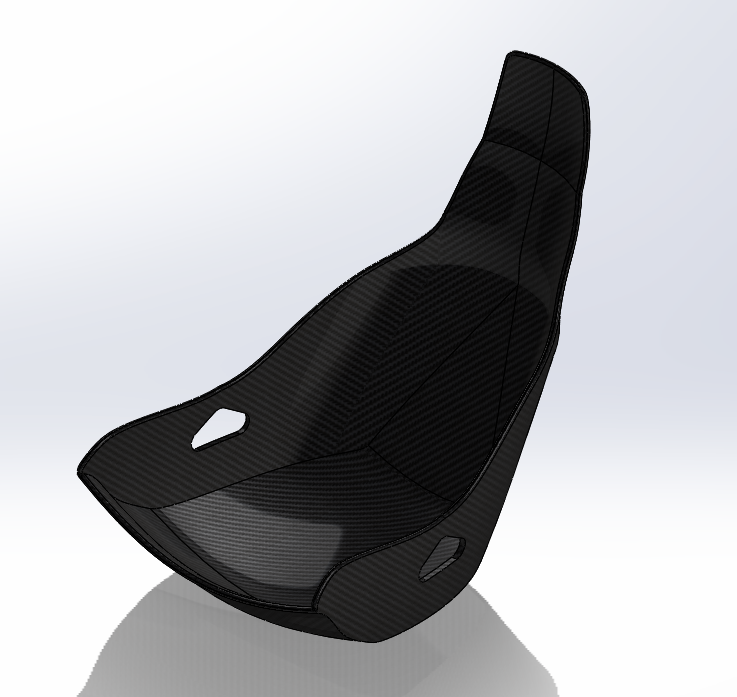
Tools Used:
- Refernce plane: used to create planes with provided constraints
- Project Curve: Merges two sketches on different planes to create a 3D curve.
- Split: split the body based on a sketch or face.
- Mirror:Mirrors features, faces or bodies about a plane surface.
- Boundary surface: Creates a suirface between two sketch profiles
- Fillet: Used to create rounded corners or edges
- Split line: Used to Split a face by projecting a sketch profile.
PhotoRealistic Rendering:
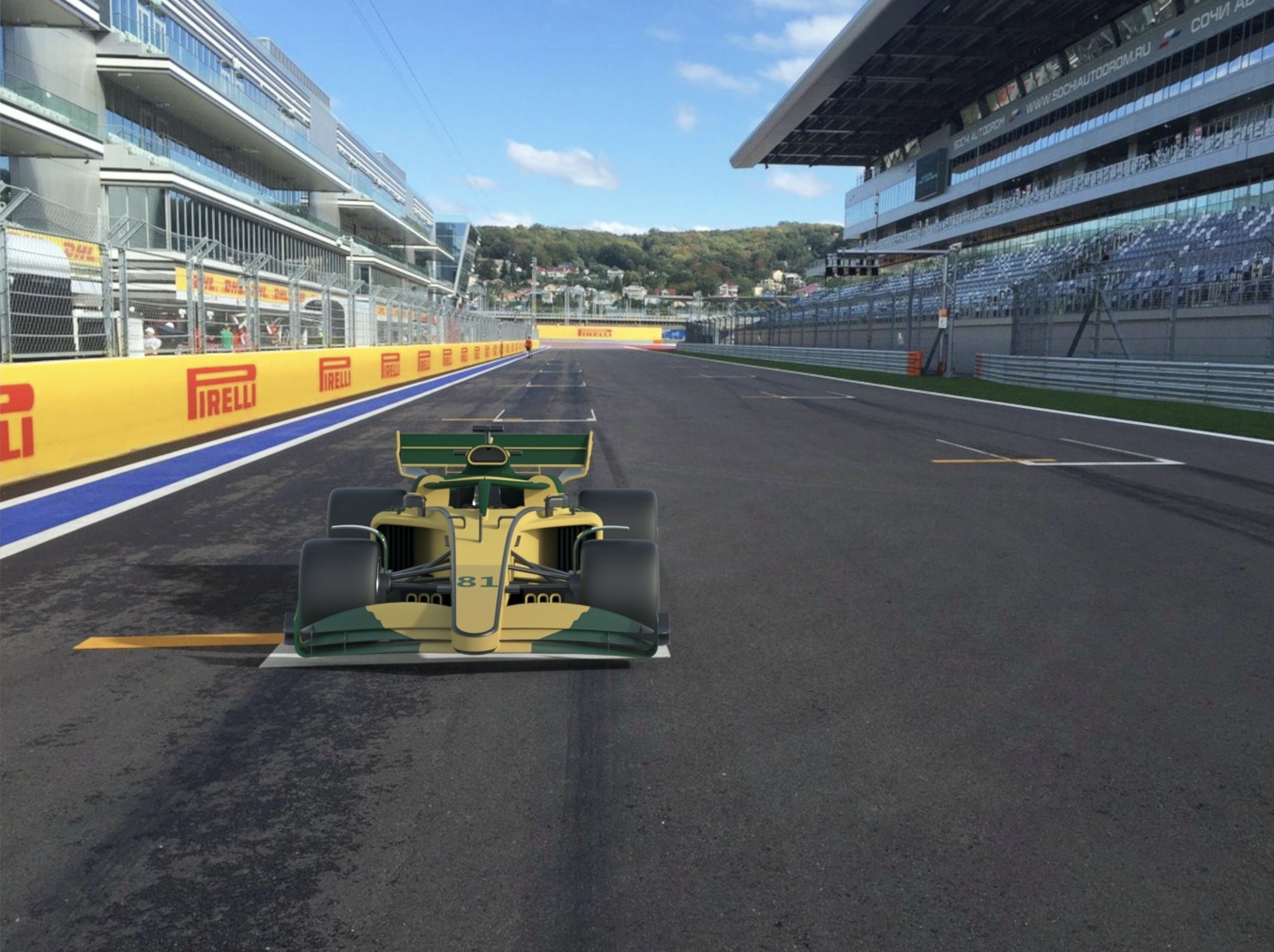
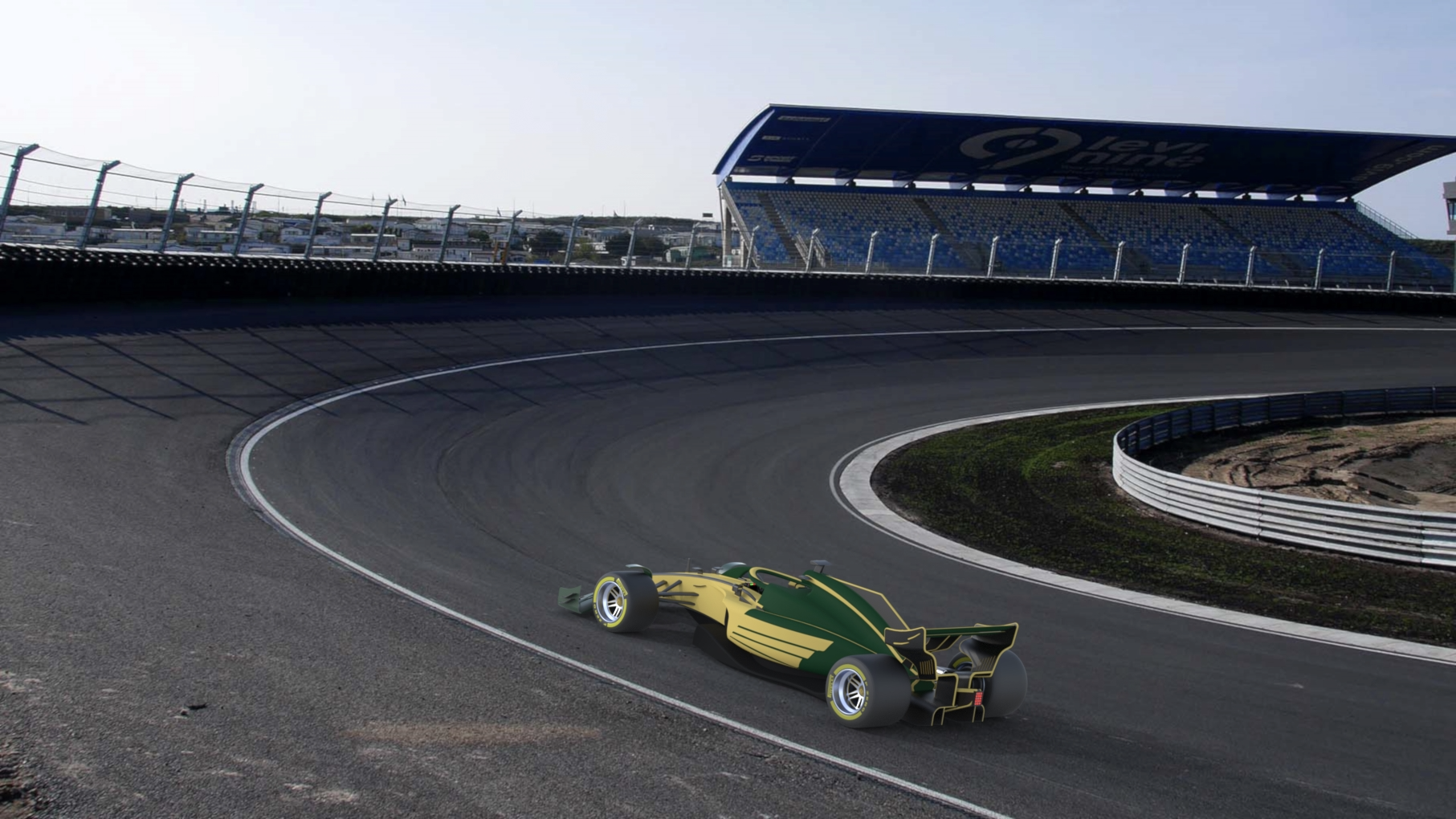
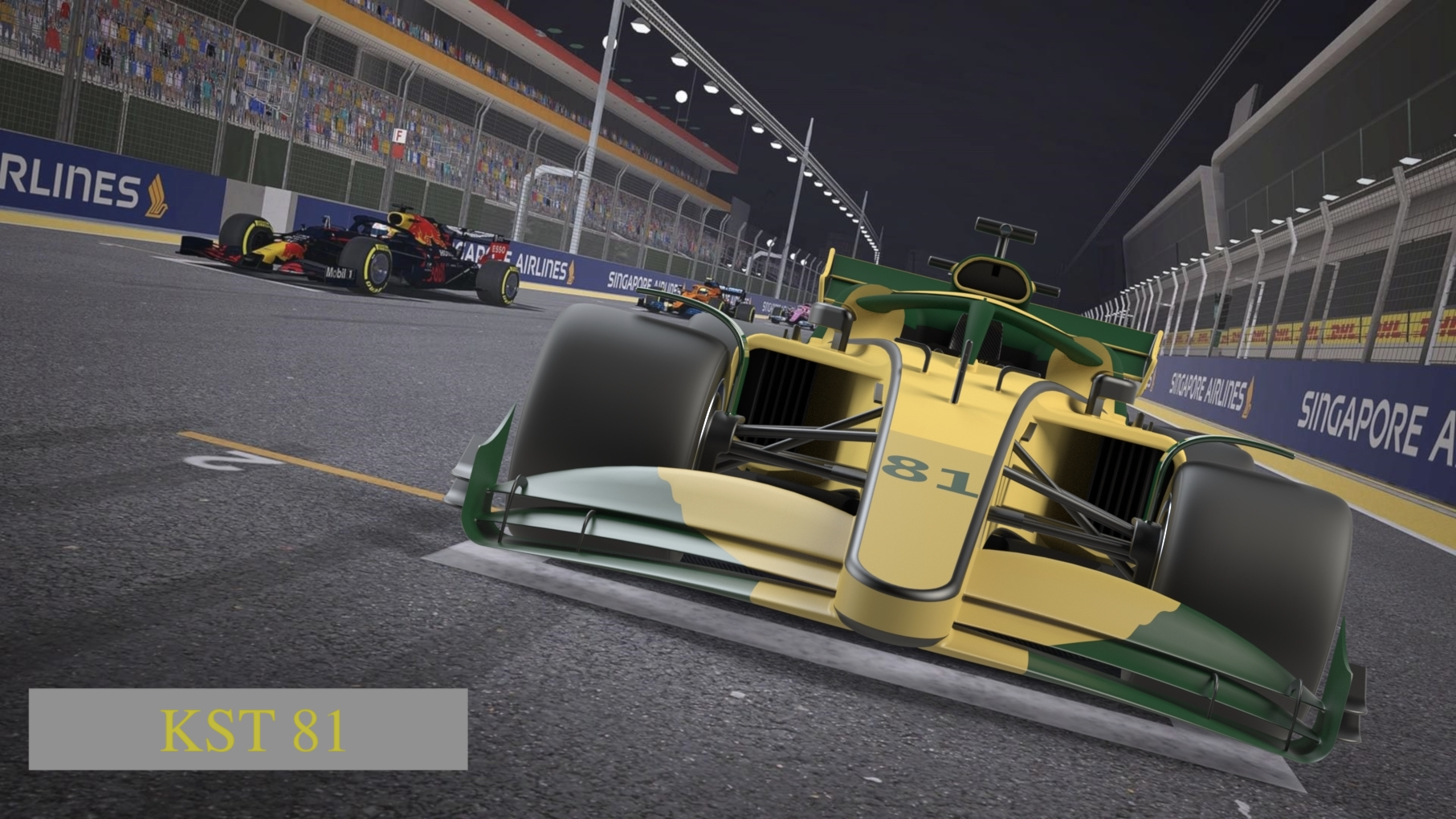
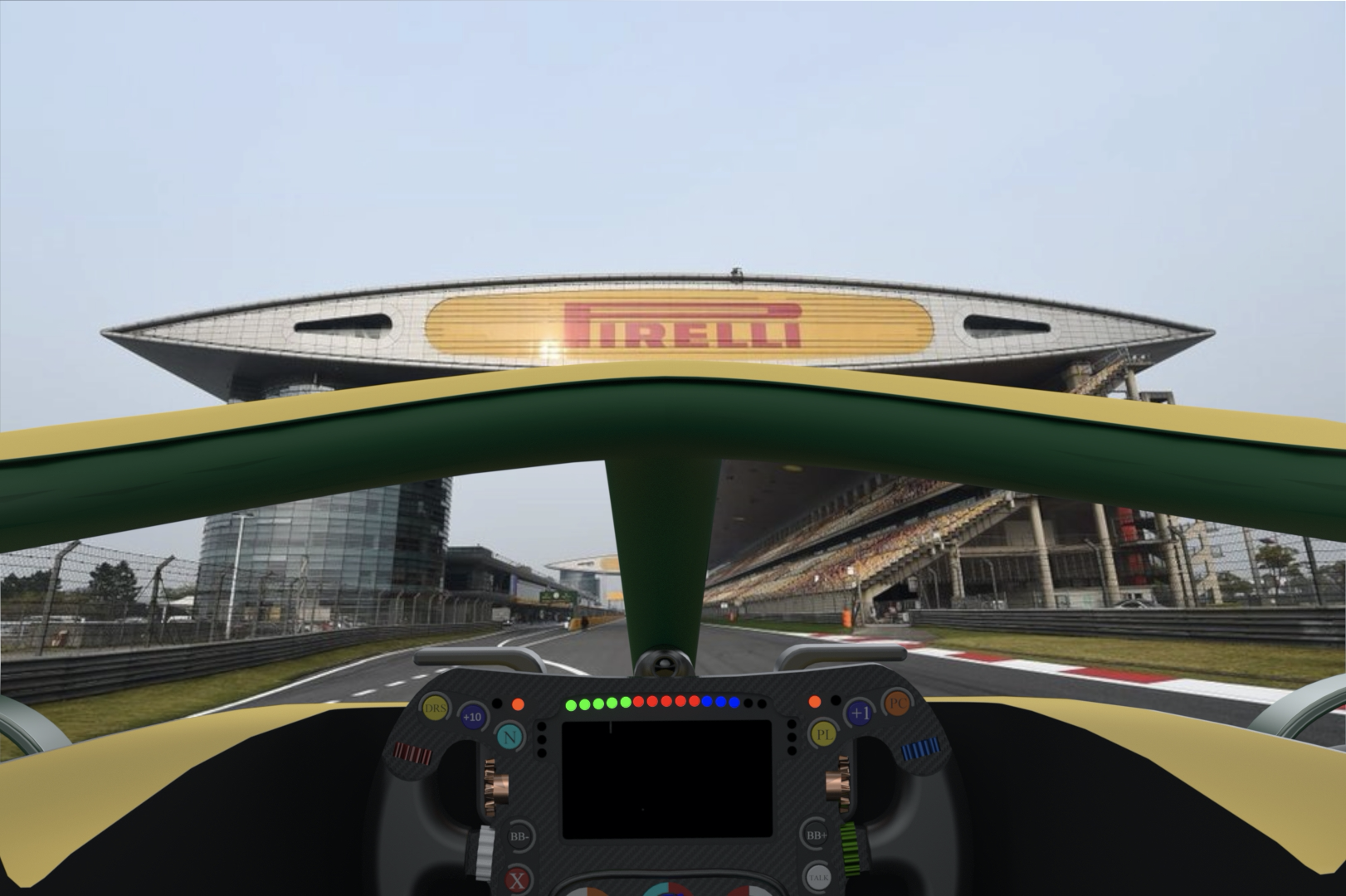
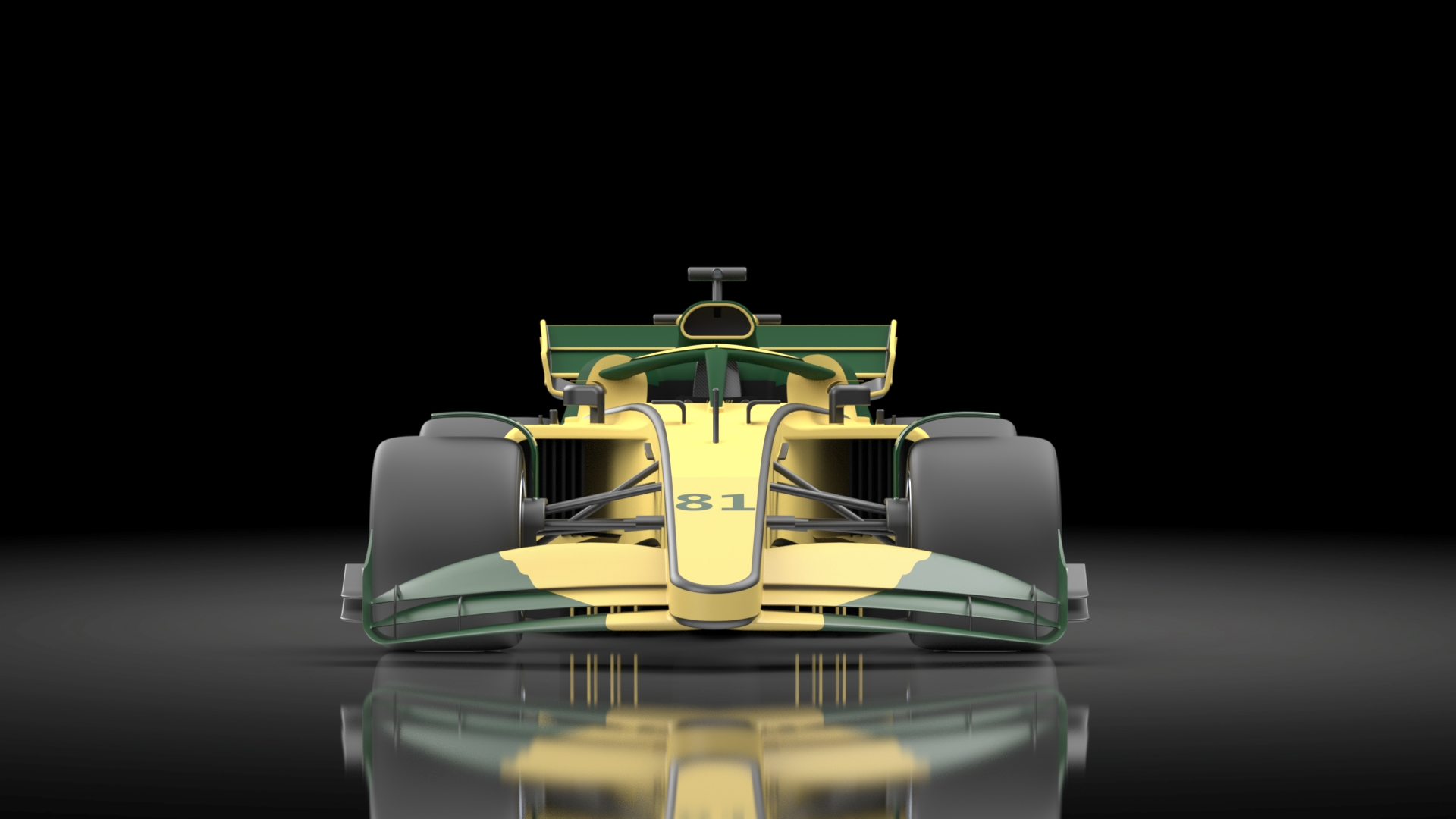
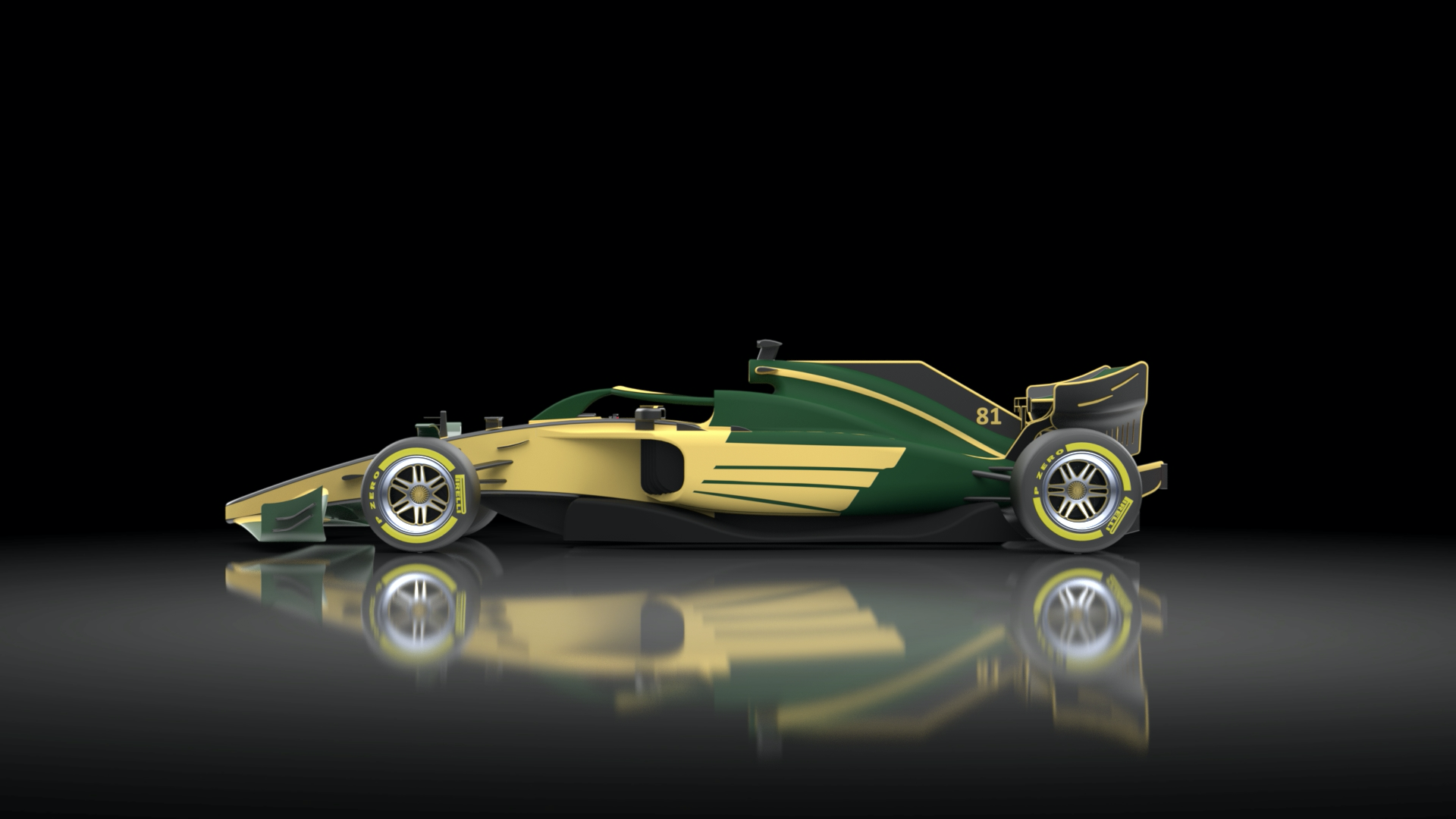
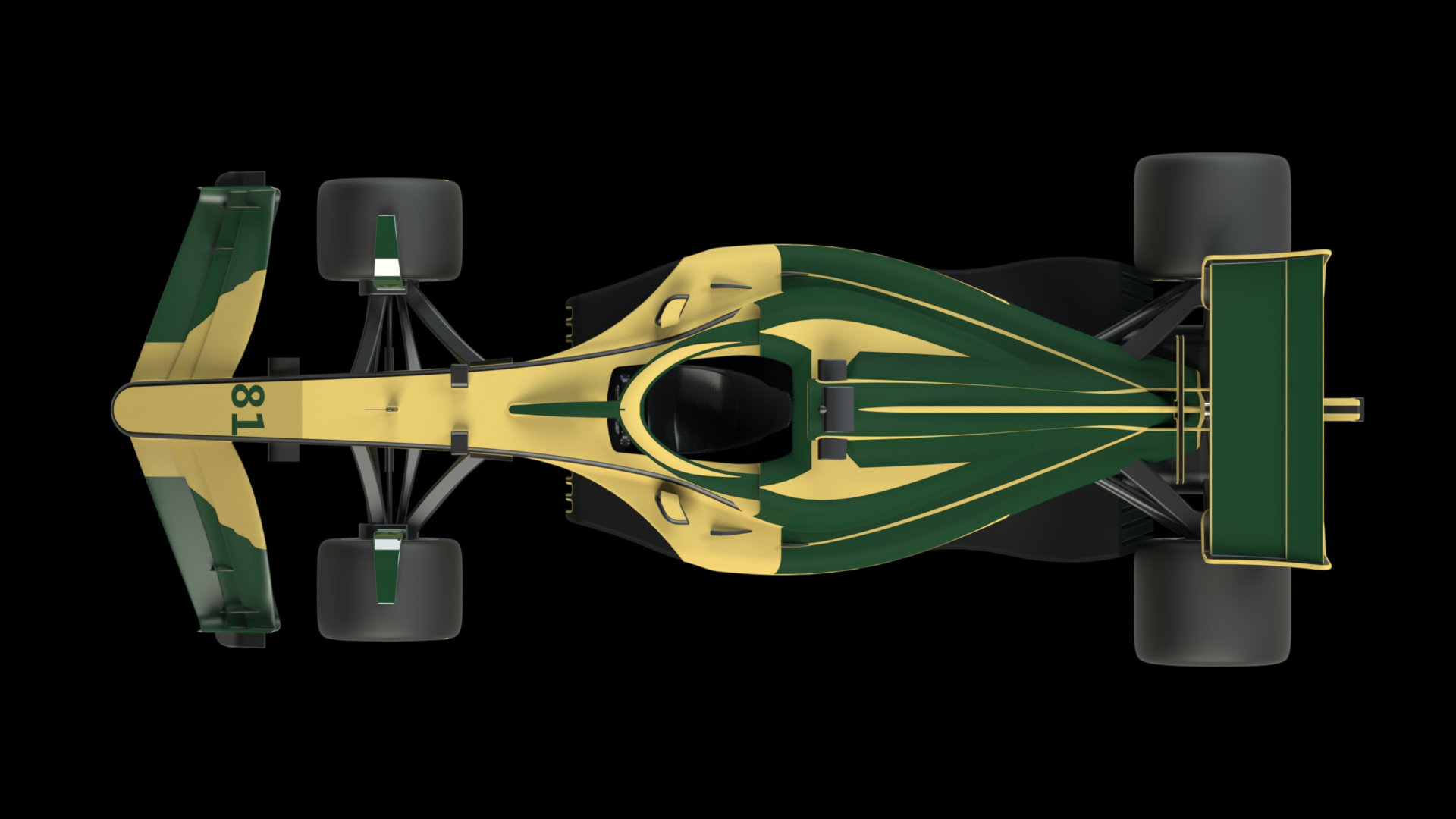
The renders are made in SolidWorks Visualize using backplate environment.
Conclusion:
- All the parts are modelled in Solidworks.
- Most of the parts are modelled using solid modelling tools. Some parts of the body and seat are modelled using surface modelling.
- The final assembly is made using Solidworks assembly tools and the mates available in the workspace
- Photorealistic renders are done in Solidworks visualize using backplate function
Project Scope:
- The existing model can be improved by putting the design through analysis.
- The dimensioning and tolerances can be calculated and improved on the model.
- The aero dynamic aspects can be improved by doing CFD analysis.
- Some mechanism can be implemented to control steering aspect of the wheel and control some aero dynamic surfaces such as DRS.