1. RADAR MAST
Fig 1.1: Feature Tree 1 of Radar_Mast_Mahesh_Kumar
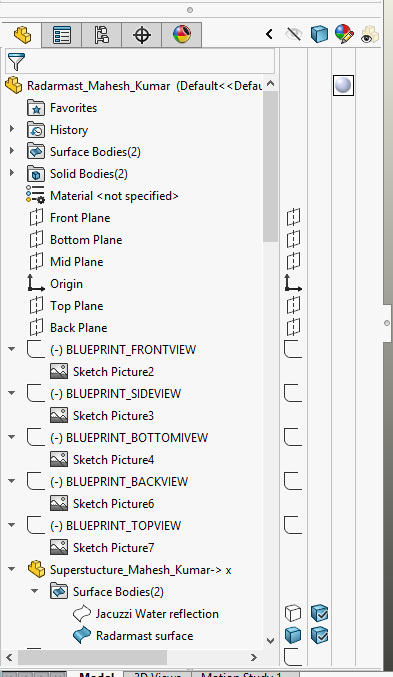
Fig 1.2: Feature Tree 2 of Radar_Mast_Mahesh_Kumar
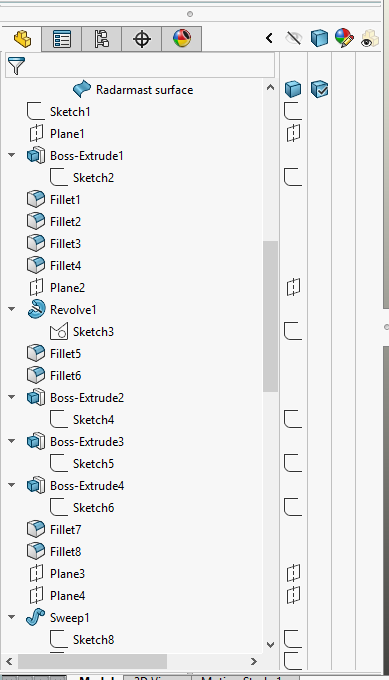
Fig 1.3: Feature Tree 3 of Radar_Mast_Mahesh_Kumar
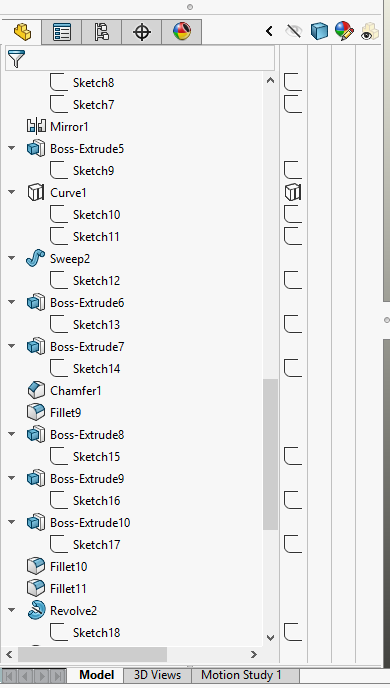
Fig 1.4: Feature Tree 4 of Radar_Mast_Mahesh_Kumar
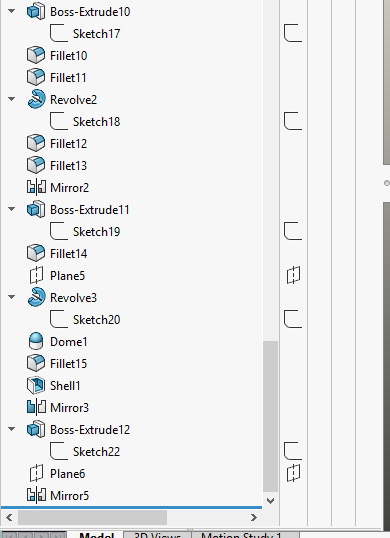
Fig 1.5: Front View of Radar_Mast_Mahesh_Kumar
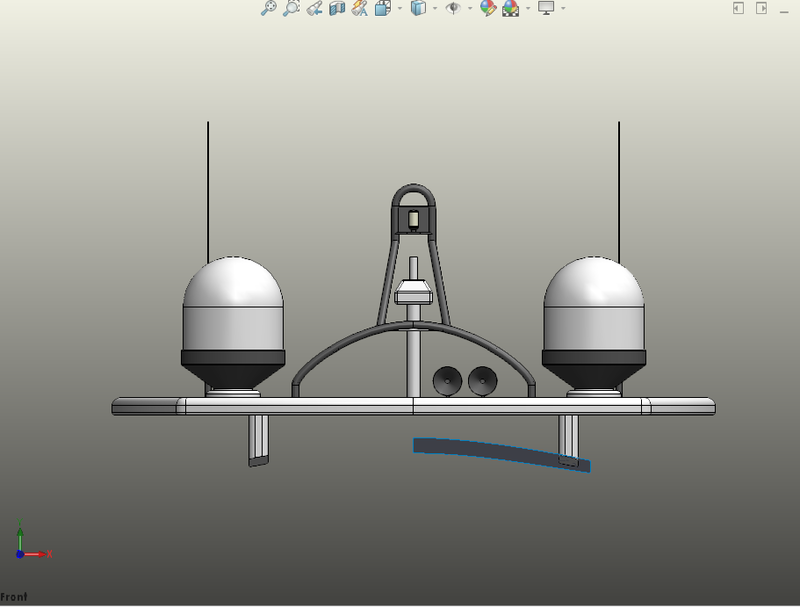
Fig 1.6: Back View of Radar_Mast_Mahesh_Kumar
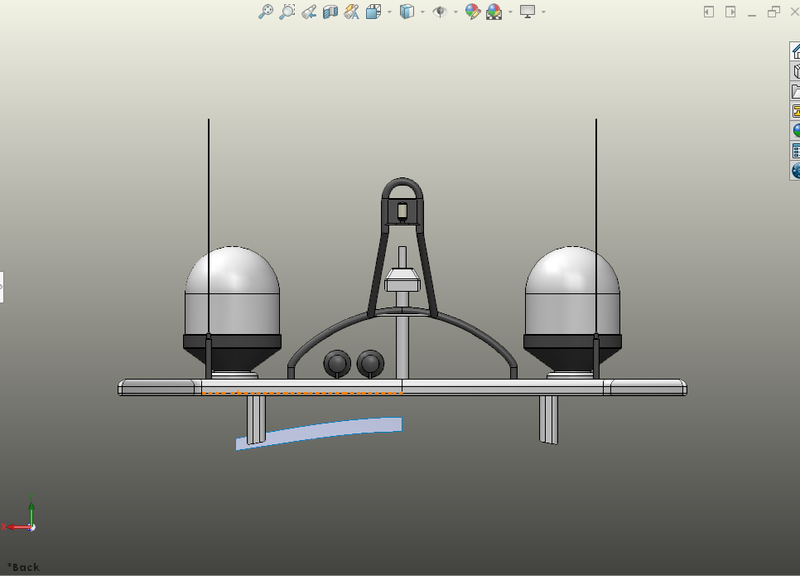
Fig 1.7: Left side view of Radar_Mast_Mahesh_Kumar
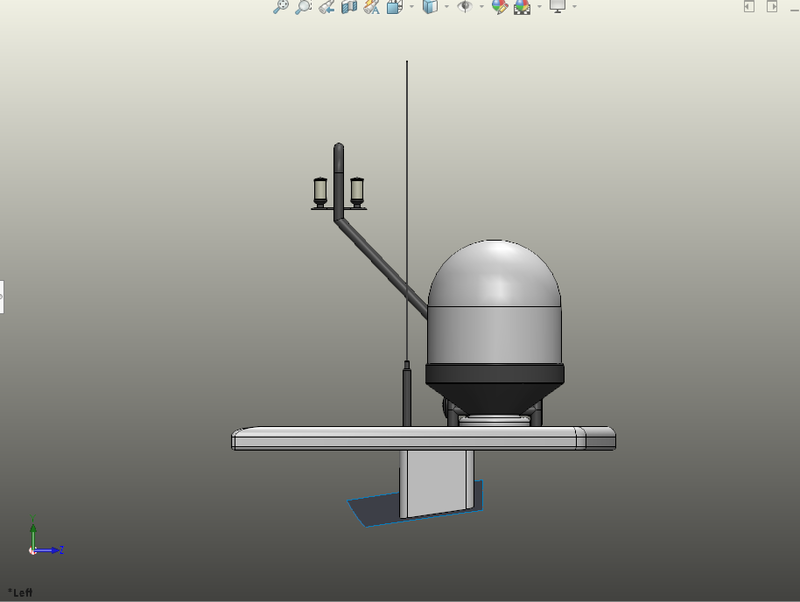
Fig 1.8: Right side view of Radar_Mast_Mahesh_Kumar
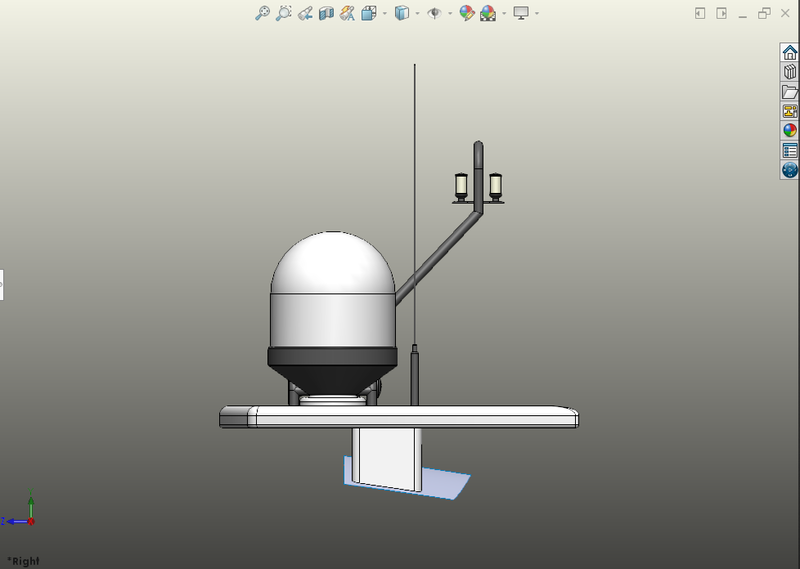
Fig 1.9: Top View of Radar_Mast_Mahesh_Kumar
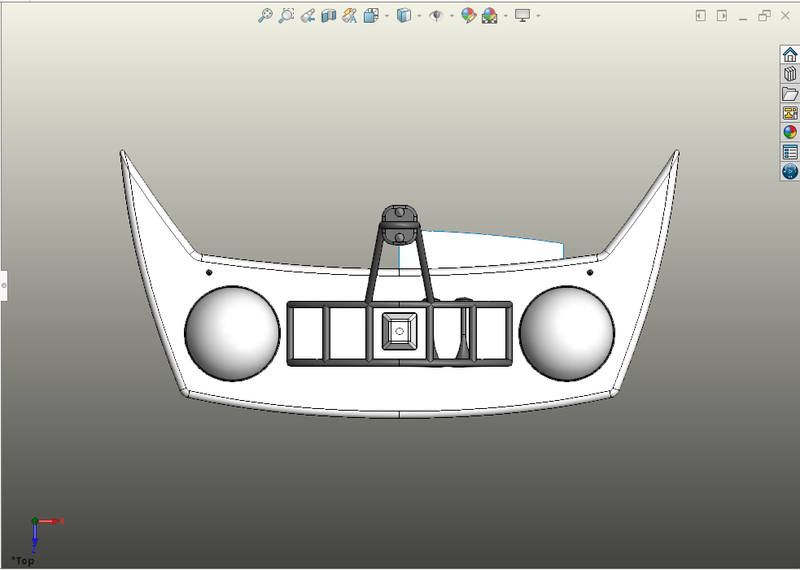
Fig 1.10: Isometric View of Radar_Mast_Mahesh_Kumar
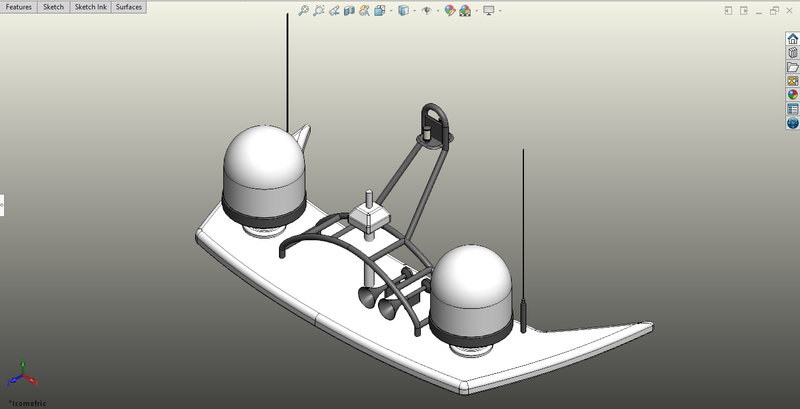
2.) ASSEMBLY OF SUNSEEKER PREDATOR YACHT
Fig 2.1: Assembly Mates Tree 1 of Assembly_Yacht_Mahesh_Kumar
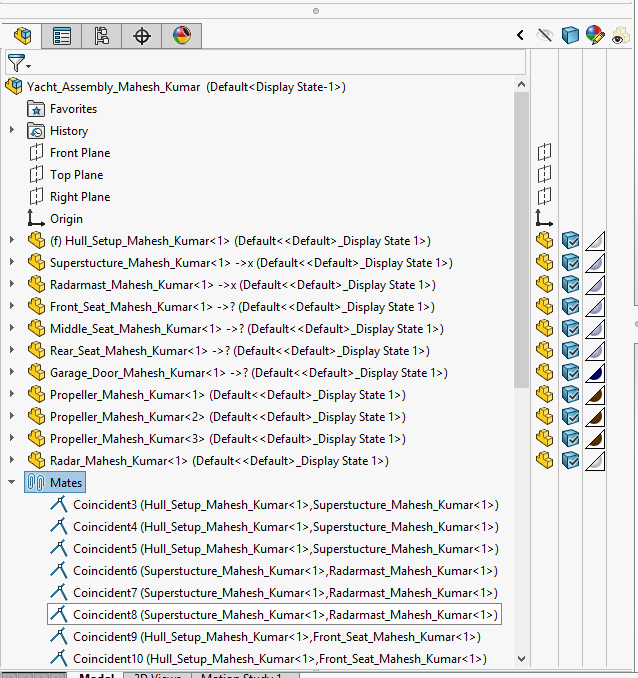
Fig 2.2: Assembly Mates Tree 2 of Assembly_Yacht_Mahesh_Kumar
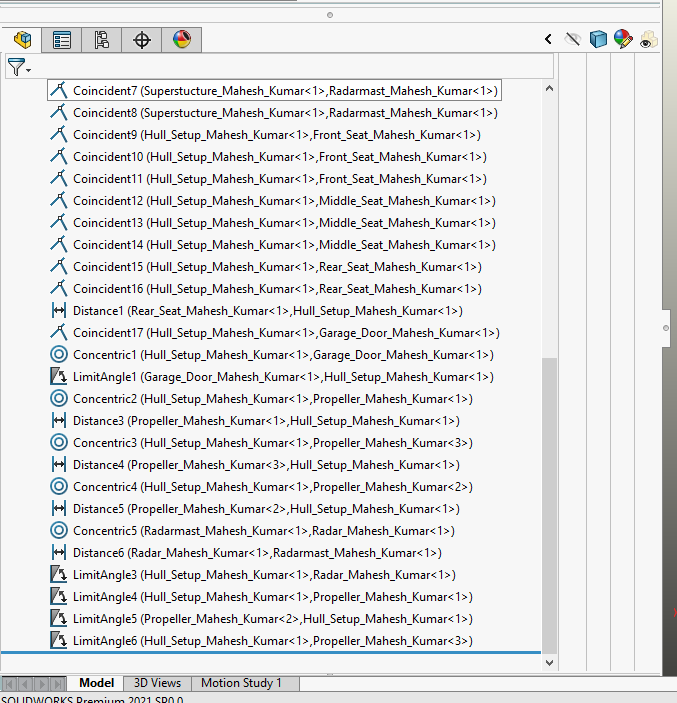
Fig 2.3: Front View of Assembly_Yacht_Mahesh_Kumar
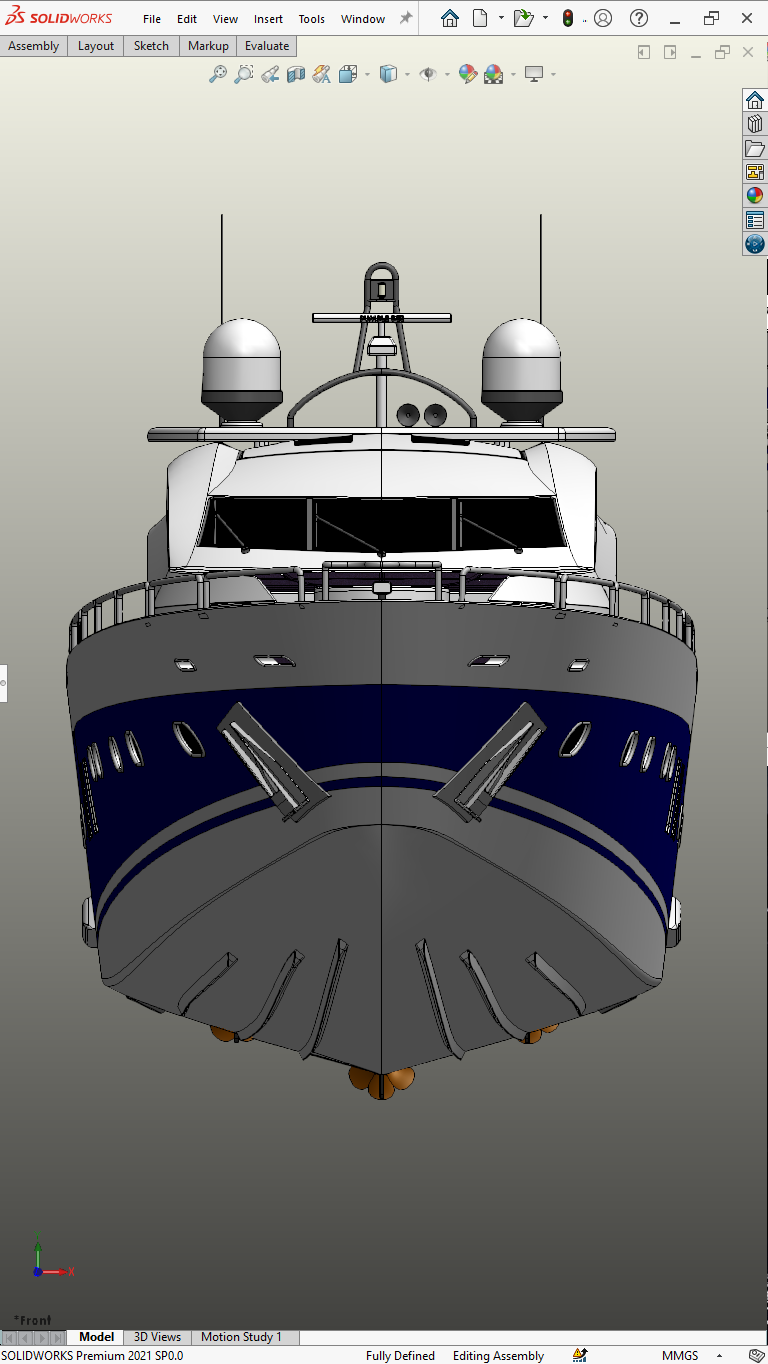
Fig 2.4: Back View of Assembly_Yacht_Mahesh_Kumar
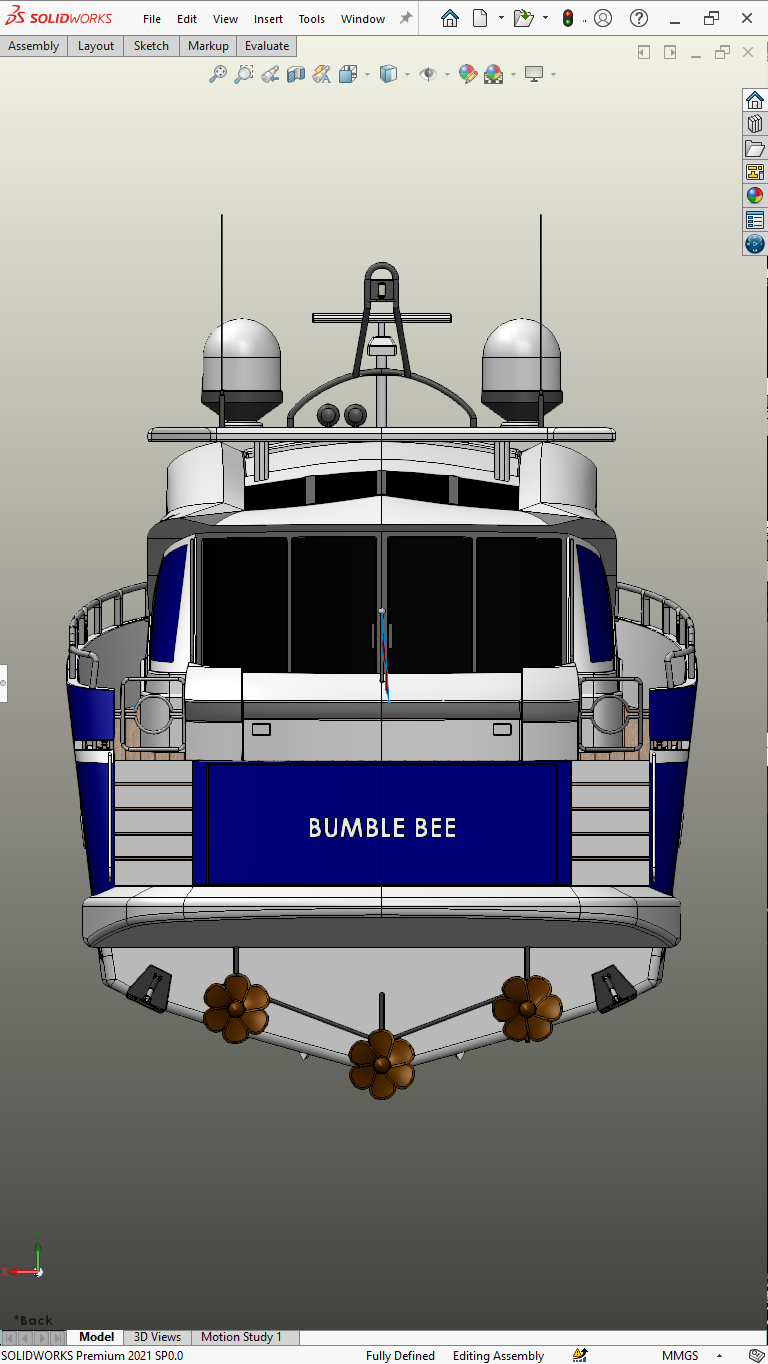
Fig 2.5: Leftside View of Assembly_Yacht_Mahesh_Kumar
Fig 2.6: Rightside View of Assembly_Yacht_Mahesh_Kumar
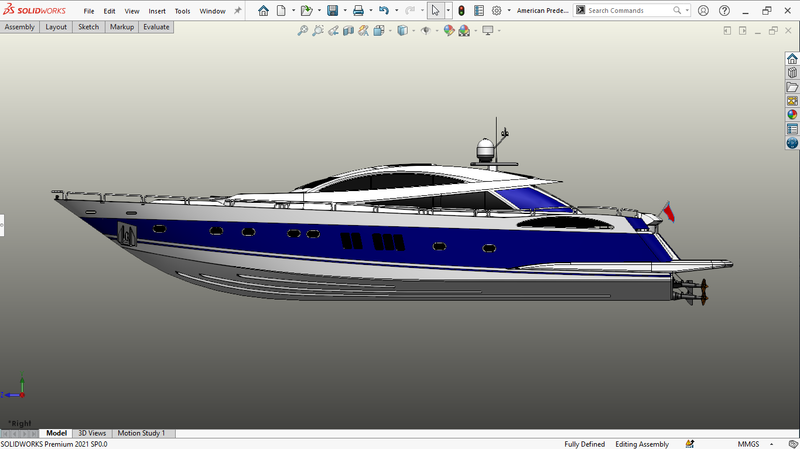
Fig 2.7: Top View of Assembly_Yacht_Mahesh_Kumar
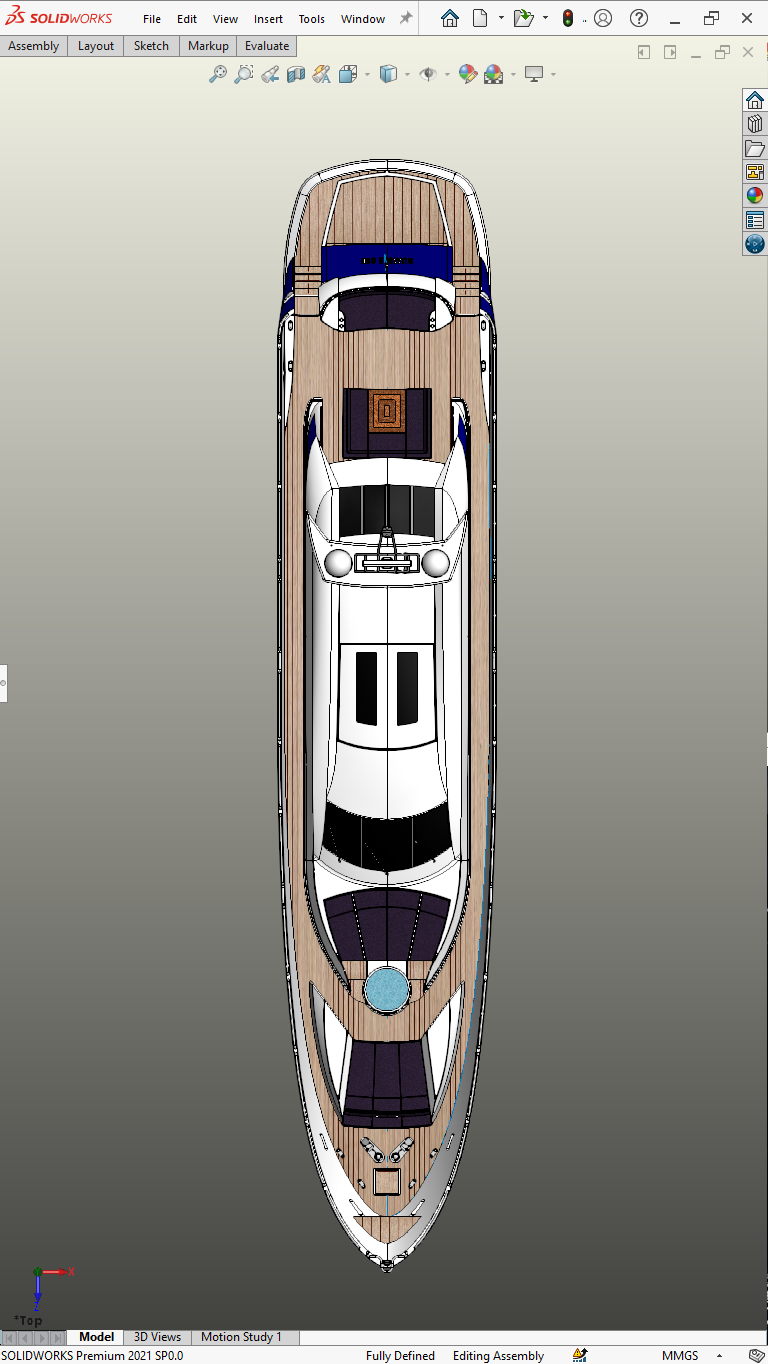
Fig 2.8: Bottom View of Assembly_Yacht_Mahesh_Kumar
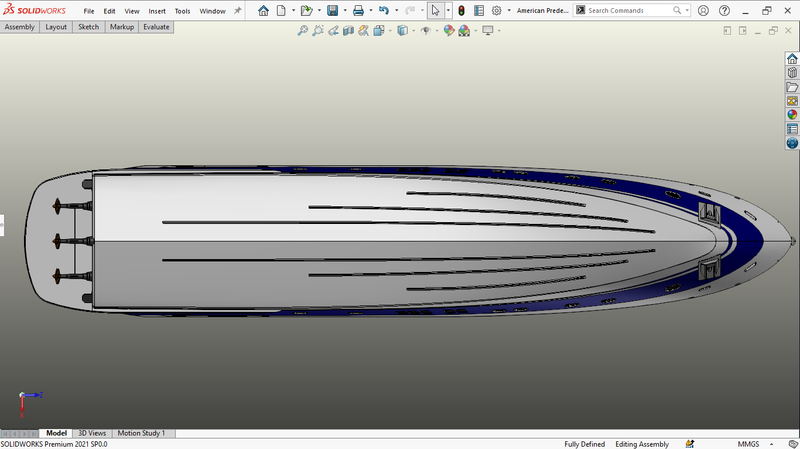
Fig 2.9: Isometric View of Assembly_Yacht_Mahesh_Kumar
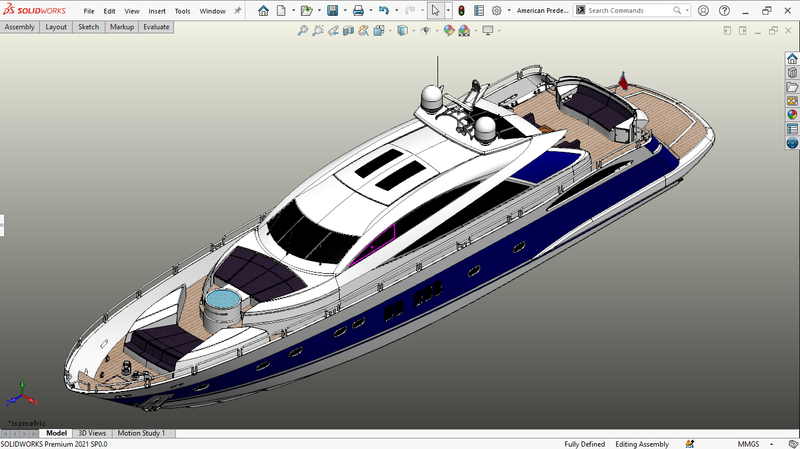
Fig 2.10: Camera View of Assembly_Yacht_Mahesh_Kumar
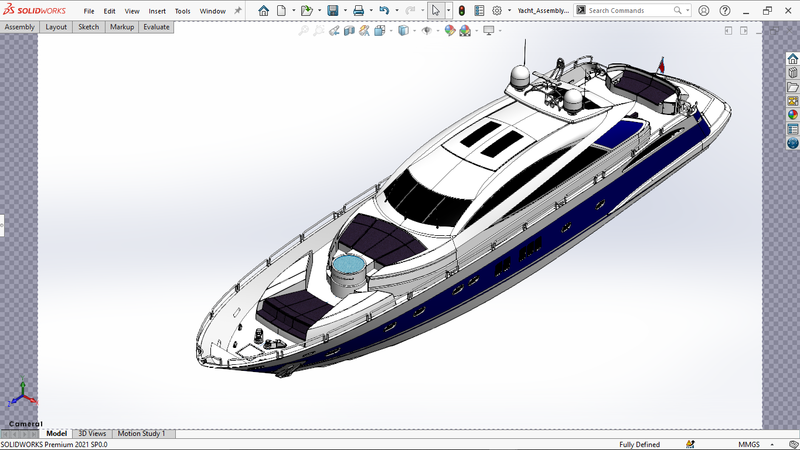
Designing Report of Sunseeker Predator Yacht model in Solidworks
Objective:
- Designing individual parts of the Sunseeker Predator Yacht with fully defined contained values & applying suitable appearances in part designing workbench in Solidworks.
- Assemble all the Individual parts of the Sunseeker Predator Yacht by using appropriate mates, modifying part shapes as required & giving constraint values in the Assembly workbench in Solidworks.
- Rendering of the Sunseeker Predator Yacht by Adjusting the appearances, decals, cameras & background scenes in Solidworks Visualize.
Introduction:
Solidworks: SolidWorks is a solid modeling computer-aided design and computer-aided engineering application published by Dassault Systèmes. SolidWorks software is used for everything from rapid prototyping to designing & is crucial to many engineering and drafting methods. It is also useful for developing new, innovative products. Some applications of SolidWorks are Manufacturing: Turning designs into products, including machine modules.
Sunseeker Predator Yacht: Sunseeker Yachts are widely considered a good boat builder as they are often recognized through marine industry awards, like the World Yacht Trophies, but there have also been more than 450 used Sunseekers sold since the beginning of 2021.
- Propeller
- Radar
- Blueprint Setup
- Hull
- Garage Door
- Front Seat
- Middle Seat
- Rear Seat
- Superstructure
- Radar Mast
FLOWCHART
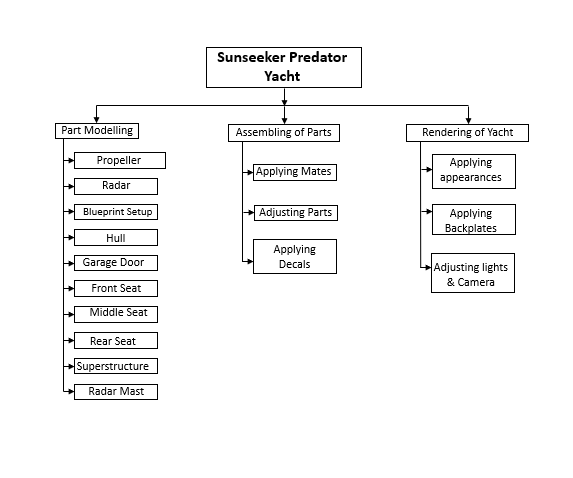
Description
1.) Propeller: A propeller (colloquially often called a screw if on a ship or an airscrew if on an aircraft) is a device with a rotating hub & radiating blades that are set at a pitch to form a helical spiral which, when rotated, exerts linear thrust upon a working fluid such as water or air.
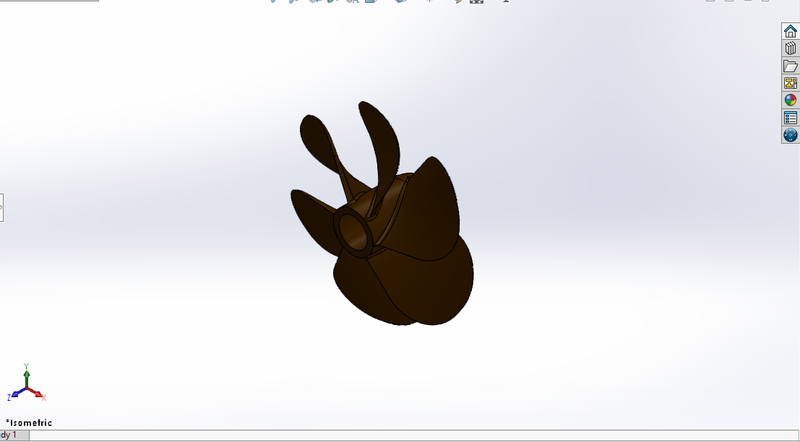
Features used to create a Propeller:
- Sketch
- Line, Spline, Plane, Rectangle
- Revolve, Loft, Cut Extrude, Circular Pattern
- Fillet
- Appearance
Procedure
- Open a new file in Solidworks & start sketching on the Right plane. Sketch by using the line and spline tools.
- Create a Revolve by using the sketch.
- Now create your 3-point rectangle on top view. Create a plane at distance on the top view & sketch as same which is shown in the ebook.
- Use the Loft Option to create a blade for the propeller. To give a good shape Use the fillet option.
- Make a Cut extrude on the plane surface of the propeller cylinder. Use a circular pattern to multiply the blades.
- Now apply the appearance and save the part file.
2.) Radar: They are electronic navigation instruments that use a rotating antenna to sweep a narrow beam of microwaves around the water surface surrounding the ship to the horizon, detecting targets by microwaves reflected from them, generating a picture of the ship's surroundings on a display screen.
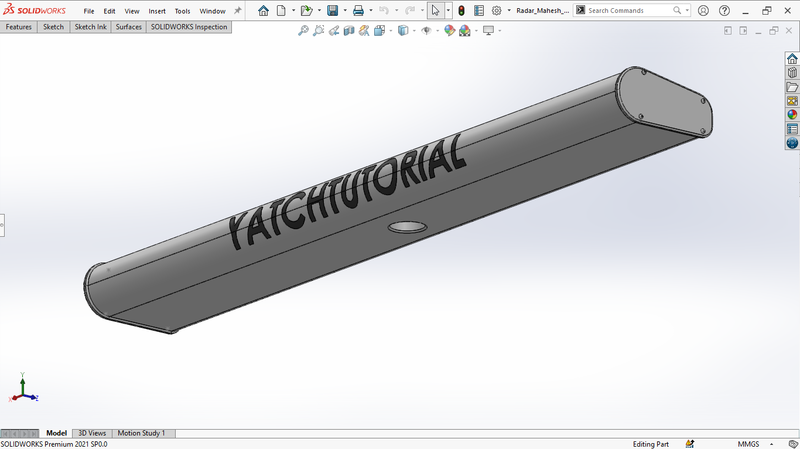
Features used to create a Radar:
- Boss-Extrude
- Cut-Extrude
- Fillet
- Sketch Driven Pattern
- Mirror
- Convert Entities
- Split line
Procedure
- Right Plane - Draw a sketch using lines as shown in the ebook & extrude it.
- Sketch on the Face of the previous extrudes by converting sketch 1 entities & extrude it.
- Sketch on Face of Sketch extrude by drawing a circle at a distance of 60mm from the lower edge converted entity & extrude it.
- Draw a circle on the Previous extruded face & cut extrude.
- Use Sketch point to locate the previous extrude at the required place and make a sketch pattern.
- Now mirror across Right Plane.
- Draw a circle at the lower edge of the Radar face & do cut extrude.
- Sketch on the Outer face of the Radar using a line, insert text as of choice & split across the line.
- Finally, give it Appearance to it & save the part file
3.) Hull: The design of a ship hull is based on the specific geometric definition of a hull which influences the hydrostatics, general arrangement, strength & aesthetics of the vessel. A naval architect has to apply his combined knowledge of designing & draftsmanship to arrive at the optimum hull form.
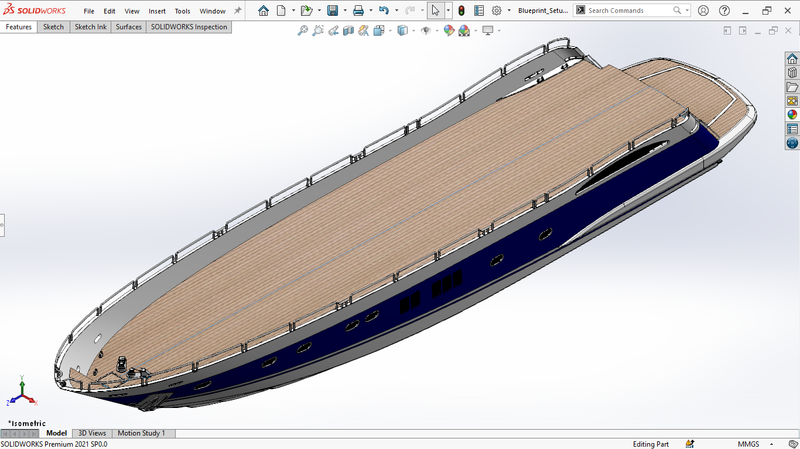
Features used to create a Hull:
- Lofted Surface
- Extend Surface
- Filled Surface
- Extruded Surface
- Trim Surface
- Knit Surface
- Reference Plane
- Revolve
- Cut-Extrude
- Projected curve
- Line
- Spline
- Rectangle
- Fillets
- Straight slot
- Circle
- Trim
- Convert Entities
- Extend Entities
- Offset Entities
- Split line
- Shell
- Copy
- Delete faces
- Boss Extrude
- Mirror
- Helix
- Swept
- Chamfer
- Linear Driven pattern
Procedure
- Insert all views, including top, side, bottom, & front views, by giving them the appropriate X, Y, & Z direction measurements in the blueprint configuration.
- Create Back Plane & the Top Plane by using the Front & bottom planes as references.
- Draw a horizontal line & a spline with a midpoint on the bottom plane & provide relations and dimensions to make it completely defined.
- Draw a vertical centerline, an inclined line in the direction of z, & a spline with two midpoints on the midplane. Drag the arrows to verify that it follows the blueprint.
- By combining the two sketches above, make a projected curve.
- Draw sketches using lines & splines on the Midplane and Bottom Plane to create an even more projected curve similarly.
- Draw a spline on the backplane, then use a pierce relation to join it to the projected curve.
- Create one more spline in the midplane and apply the pierce relation once more.
- Use the two sketches from above to create a lofted surface.
- Similarly, by using splines to generate sketches on Midplane and Back Plane, create another surface loft.
- Create a vertical line in the midplane and cut the extra surface along it.
- Draw a spline parallel to the surface loft in the midplane, then do the surface loft.
- To make the surface extrusion in the midplane, draw a horizontal line and a vertical line.
- Extra surfaces can be cut off and knit together. Make sure all lines turn out to black color which indicates proper knitting.
- To close the hole using the filled surface and a Mid Plane drawing. Now Knit Surfaces and create Shell.
- Mid Plane - To construct a closed surface, offset the produced surface entities inwards and draw a line. Use Trim entities to remove excess entities, then extrude them.
- Draw a sketch using splines on the Bottom plane and cut extrude. Apply Fillets and Chamfers to respective edges.
- Draw a rectangle with four lines for the side windows on Plane 1, Fillet the corners, then do the linear pattern. Create a cut extrude and remove the extra window that was created.
- Draw a straight slot for a port hole on Plane 1, clone the slot to another port hole using the copy feature by the blueprint, and then cut and extrude the copied port hole. Draw a circle in the new plane to produce a 2D sketch, and then convert port hole entities to a 3D sketch to build a profile. Make a strong sweep now. Create the remaining port holes by repeating the same steps.
- Create a sketch for the lower deck using splines & lines to extrude in line with a blueprint on the top plane.
- Create a sketch for the staircase on Top Plane by drawing a line in a rectangle shape and performing cut and extrude. Draw a few connecting ramp horizontal and vertical lines on the extruded right face, then extrude it up to the next/up to the surface.
- Create a plane for the bottom of the hull that is 3000 mm offset from the bottom plane. Create three splines and align their arrows in line with the blueprint. Extrude it, offset the splines, and close them with lines.
- Sketch an anchor house on the top face of the hull by connecting two circles with lines and trimming the inner half of the circles to form the lower surface of the anchor house. Using the preceding sketch as a guide, draw a vertical line and a horizontal line on a new plane, then revolve it. Sketch by adding lines, circles, and extrusions. Make a sketch and cut an extrude to eliminate a part of the previous extrude.
- Draw a helix for the rope, use it as a guide to making a plane, and then draw a circle at the end of the helix. Sweep using a circle as the profile and a helical route. To connect the rope from the house to the helix you just made, make one more sweep.
- With the use of a few designs, add a few extra port holes to the front and back of the ship, then extrude them using a linear pattern to pattern them.
- Create a new plane for the handrailing that is offset from the left face of the connected piece of the stairs. Draw a rectangle with a 3 Point Center and add fillets to the upper two corners. Using the rectangle's lower left endpoint as a starting point, create a circle on another plane. Now sweep using a circle's profile and a rectangle's route, respectively.
- To draw the midplane for the side railing, offset the inner border of the hull in one direction and out the other. By the plan, draw a few vertical lines. Remove any unnecessary material to create a chain. Put fillets on the end part and make another drawing in the plane where the inner margins of the hull are displaced. Next, use the two sketches from above to build a projected curve. Draw a circle on a new plane after the produced sketch to use as a railing reference, then sweep utilizing the circle and projected curve.
- To create the caliper's surface, draw out a few lines on the backplane for the calipers. Choose the Caliper sketch's surface according to the blueprint, then rotate it.
- Create a sketch of the propeller shaft on the back of the hull by drawing lines following the blueprint and rotating it. Utilizing a Pattern direction drawing, pattern it accordingly.
- Draw a line connecting the two holes in the propeller shafts on a 3D sketch for the connecting rod and extrude it.
- Draw a drawing of the anchor on the midplane at the front of the hull using lines and splines following the design, then extrude and mirror it across the appropriate face.
-
Draw a corner rectangle and execute a cut and extrude on the midplane to create a sketch for the garage door.
By transforming the prior sketch into entities cutting extrude, sketch extrude the left face and sketch on it.
Now, using split, cut out the necessary piece and save it as the garage door.
- Draw a circle on the previously extruded face, then extrude it to create a pin.
- Draw Splines and offsets in the upper and downward directions to create a new sketch on the Mid Plane. Select all of the faces to separate using the Split line.
- Finally, mirror the entire body across the Mid Plane to ensure that all appearances are correctly applied. And save the part file.
4.) Garage Door: An large door in a garage called a garage door can be opened manually or by an electric motor (a garage door opener). Often, garage doors are big enough to fit cars and other types of vehicles. Single panels that tilt up and back across the garage ceiling can be used to create small garage doors.
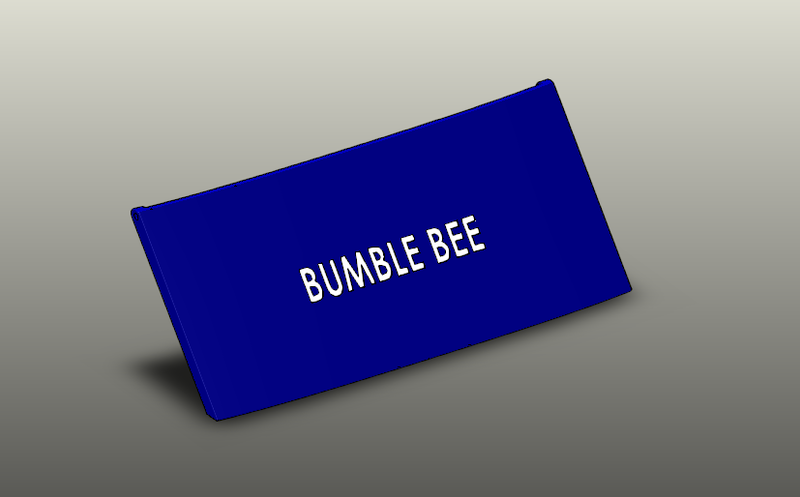
Features used to create a Garage door:
- Boss Extrude
- Cut Extrude
- Fillet
- Swept
- Mirror
- Split Line for Text
Procedure
- Open the portion of the garage door that was saved for the hull design.
- Draw lines and execute a cut extrude to create a sketch on the right face of the stock.
- By choosing certain stock faces, apply Shell.
- By selecting the stock's side face and doing a cut and extruding to make a hole, draw a circle at the top.
- Apply fillets across the right plane, then mirror. Offset Front Plane and use it as a reference to create a plane.
- Create a sketch on the plane using the Horzintal Centerline, text in the Text box, and cut and extrude. Give a final appearance to the door and the text.
- Save the Part file.
5.) Front Seat: Front Seat is positioned at the front end of the Hull and is often used for relaxing and enjoying the view.
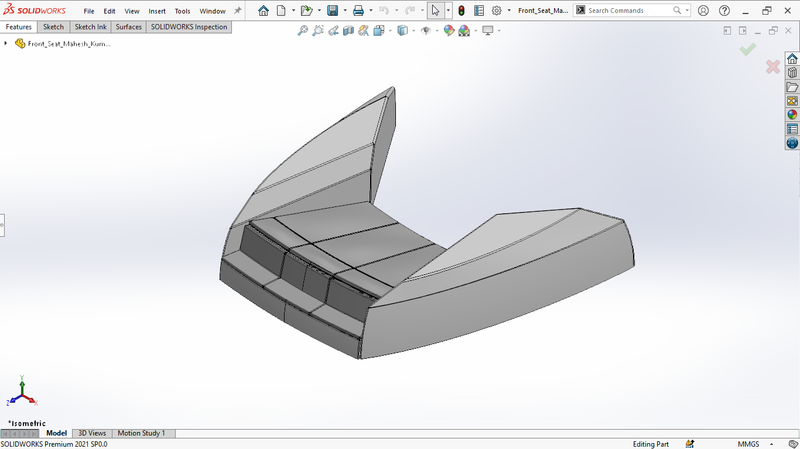
Features used to create a Front Seat:
- Revolve
- Cut-Extrude
- Fillet
- Dome
- Mirror
- Line
- Spline
- Convert Entities
- Lofted Surface
- Swept Surface
- Extruded Surface
- Filled Surface
- Trim Surface
- Knit Surfaces.
Procedure
- Insert all perspectives, such as top, side, bottom, and front views, by giving them the appropriate X, Y, and Z direction dimensions, in the blueprint configuration.
- Make two new aircraft Front and bottom planes are used as references for the back and top planes.
- By selecting the surface bodies, insert the Hull part.
- Produce a sketch on the deck face using a spline, and another sketch on the formed plane using a line to create a swept surface.
- Draw two lines, join them to the surface that was previously generated, and then extrude the surface.
- Trim the extra surface, then add a filled surface to the gap.
- Sketch up a few ideas to trim unnecessary surfaces.
- Use the two sketches from above to create a Surface loft.
- Knit it together after trimming the extra surfaces.
- Draw the necessary lines to make the seat, then rotate it by around 10 degrees.
- Apply filters, then reflect the bodies.
- Apply Dome to the chairs to complete the appearance and save the part file.
6.) Middle Seat: The middle seat, which is also utilized for seating and relaxing, is located right after the back of the superstructure.
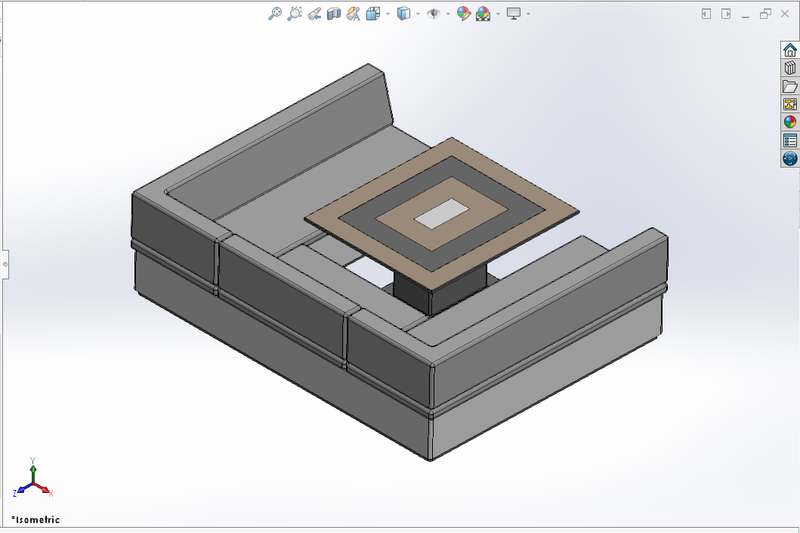
Features used to create a Middle Seat:
- Boss-Extrude
- Cut-Extrude
- Fillet
- Mirror
- Line
- Convert Entities
- Offset Entities.
Procedure
- Insert all views, including top, side, bottom, and front views, among others, into the blueprint setup by giving them the appropriate X, Y, and Z direction dimensions.
- Make two planes Front and bottom planes are used as references for the back and top planes.
- By selecting the surface bodies, insert the Hull part.
- On the deck's face, use lines to draw an L shape, then extrude the lowest part of the seat.
- Create a sketch that offsets the face and extrudes on the extruded face above.
- Offsetting at a 5mm distance will create a plane on the upper extrude face. Draw lines on it in line with the blueprint and extrude them.
- By choosing Knit Surfaces and combining solids, you may mirror the bodies across the Mid Plane.
- By deselecting Knit Surfaces and merging solids, you can mirror seats throughout the Mid Plane.
- Select a table's face using the lines and fest entities.
- Apply fillets to the top surface of the table by creating a Cut Extrude.
- Then, apply the appearance to the table & the chairs and save the part file.
7.) Rear Seat: The Hull's rear seats are where passengers may sit and enjoy the view.
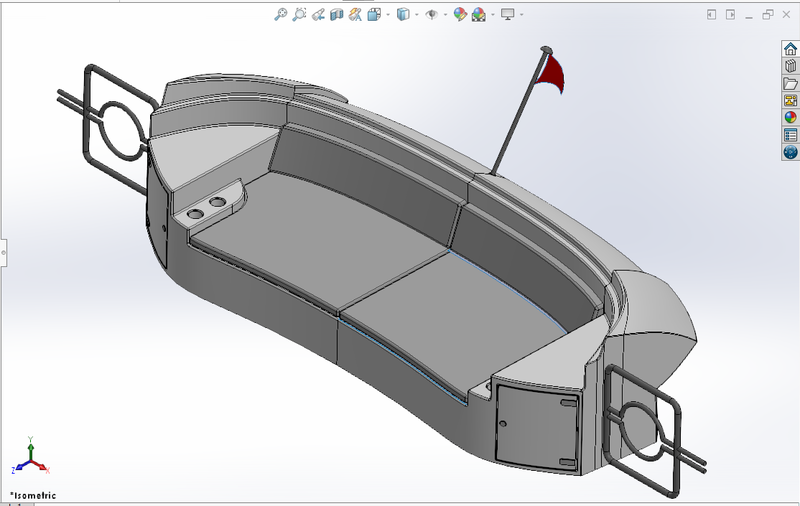
Features used to create a Rear Seat:
- Line
- Spline
- Boss-Extrude
- Revolve
- Cut-Extrude
- Fillet
- Chamfer
- Mirror
- Convert Entities
- Offset Entities
- Trim Entities
- Lofted Surface
- Swept Surface
- Offset Surface
- Ruled Surface
- Surface-Trim
- Surface-Knit
Procedure
- Insert all views, including top, side, bottom, and front views, among others, into the blueprint setup by giving them the appropriate X, Y, and Z direction dimensions.
- Make two planes Front and bottom planes are used as references for the back and top planes.
- By selecting the surface bodies, insert the Hull part.
- Draw two spline lines in the middle of the plane according to the blueprint's dimensions.
- Deck face and spline vertex can be used as references for creating a plane.
- Draw a spline to add another sketch to the new plane.
- Do a Surface Sweep using the two sketches shown above.
- By choosing the appropriate faces, create an offset surface using the earlier sketches.
- Trim the Extra Surface by making sketches that follow one other.
- Knit everything while extending the surface using a ruled surface.
- Utilizing Splines, which are used to reduce surfaces, create a sketch on Plane 1.
- By using convert entities and splines, create a few planes and do some sketches. Use these sketches to perform a surface sweep.
- Knit the undesirable surfaces after extending them and trimming them with surface trim.
- Make a couple of 3D sketches, then loft the surface.
- By converting the relevant entities, adding a spline with the midpoint, and extruding it, you can doodle on the deck face.
- Create a sketch on the previously extruded face for the hand resting by choosing the face and converting entities. Draw a few lines per the blueprint to extrude any excess entities.
- Draw lines on the front plane to create a cut-out for doors and drawers.
- Set the proper faces aside to create the seats. Split the surfaces by trimming them while maintaining the selection.
- Create a Boss Extrude for upper seats by sketching on an offset surface and using convert entities and lines. Apply the appropriate fillets and chamfer.
- Draw and extend lines to create a sketch for the lights on Plane 4.
- Create a few planes as needed for locking gates and make designs using circles and lines. These sketches are used to sweep and reflect it.
- By using knit surfaces and merging solids, you can mirror the entities across the midplane.
- By deselecting Knit Surfaces & Merge solids, you can separately mirror the seats and gates across the Mid Plane.
- Create a sketch for the flag stand on the midplane by angling the lines and rotating it.
- Draw four 3D sketches of the flag, each with a spline with midpoints, and loft the surface.
- Give Appearance to Seats, Lower Surface, Flag, Hand resting, Drawers & gates.
- Finally, save the part file in SolidWorks.
8.) Superstructure: A superstructure is an upward extension of an existing structure above a baseline. This term is applied to various kinds of physical structures such as buildings, bridges, or ships.
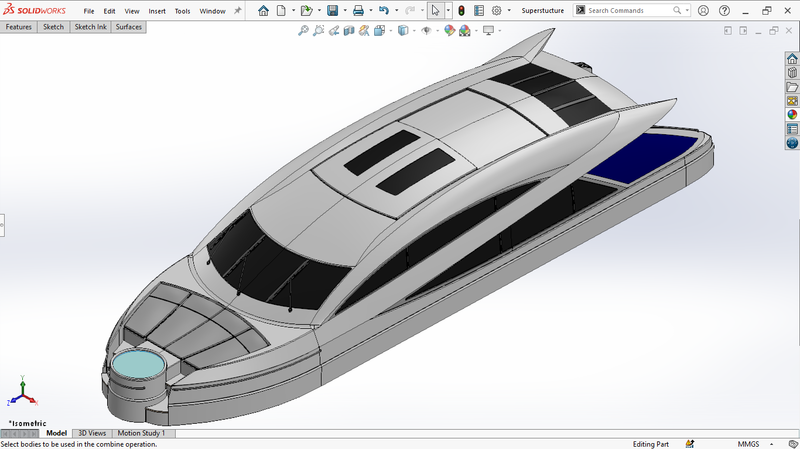
Features used to create a Superstructure:
- Sketch
- Project Curve
- Swept Surface
- Loft Surface
- Extruded Surface
- Extend Surface
- Fill Surface
- Surface Knit
- Surface Trim
- Delete Surface
- Extrude
- Mirror
- Cut Extrude
- Fillet
- PatternSplit
Procedure
- Insert all views, including top, side, bottom, and front views, among others, into the blueprint setup by giving them the appropriate X, Y, and Z direction dimensions.
- Make two planes Front and bottom planes are used as references for the back and top planes. By selecting the surface bodies, insert the Hull part.
- Draw two splines, a line, and a sketch on the deck surface following the blueprint, then extrude the surface.
- Make a plane after Establish Surface Extrude.
- Draw sketches using lines (horizontal) on the generated plane to produce a surface sweep, then apply the pierce relation to the extruded surface. a 3D sketch created by treating the outer surface as an entity.
- Trim the additional surface after extending the outer edge of the surface using the ruled surface at an angle. Knit on every surface.
- By utilizing Splines and lines to create two sketches on the appropriate Planes, you may create another Projected Curve that will be utilized to create Lofted Surface.
- By sketching on the generated Plane with lines (horizontal), construct a second surface sweep and apply the pierce relation to the extruded surface. a 3D sketch created by treating the outer surface as an entity.
- By making sketches on the corresponding faces or planes, remove any unnecessary surfaces.
- By utilizing splines to sketch on the midplane and corresponding edges to transform it into a 3D sketch, you may create a swept surface.
- Cut off any superfluous surfaces.
- Similar steps must be taken to generate surfaces on top.
- Draw two sketches on the appropriate Planes to obtain a projected curve following the blueprint, which is then utilized to produce a lofted surface.
- For side windows, choose the superstructure's outer surface and extend it using the ruled surface. Trim the additional surfaces.
- By adding sketches on the generated Plane utilizing lines (horizontal), apply piercing relation with the extruded surface, and produce one more surface sweep. Using the outer surface as entities, create a 3D drawing.
- By sketching on the corresponding faces or planes, remove the surfaces that are not needed.
- You may create a swept surface by utilizing splines to sketch on a midplane and converting the corresponding edges to 3D sketches.
Trim the additional surfaces.
- Draw two sketches on the appropriate Planes to construct a Projected Curve by the Blue Print, which is then utilized to create a Lofted Surface for surfaces on top.
- For side windows, choose the superstructure's outside surface and use the ruled surface for an extension. Clean up the extra surfaces.
- Draw a few lines in the appropriate horizontal and vertical directions, then extrude them. Trim the Additional Surfaces.
- Draw a horizontal line on the deck surface and perform surface extrusion to make it solid.
- Knit the surfaces together after trimming the superfluous surfaces to create a Solid.
- Create a surface offset at the front end of the mattress, trim any unnecessary surface, and thicken the surface by choosing the appropriate faces.
- Add domes and fillets to a cut extrusion after creating it.
- Create a sweep for the railing (front and side) by sketching on the appropriate planes using circles and splines.
- For the door (at the back end), offset the rear face inwards to create a cut extrusion. To create the handle, draw an Acute angle then extrude it.
- For frames, draw two vertical lines on the respective face and convert the top and bottom edges of the glass. Extrude and trim unwanted entities.
- Create a sketch on Top Plane by drawing a line and Spline, then cut and extrude.
- Create a sketch for Top Frames by offsetting respective edges and removing unwanted entities with Trim entities. It should be extruded.
- Create windows and frames for side faces by drawing a few sketches and using cut and boss extrude.
- Sketch Midplane Offsetting the respective faces and do a split line for the rear portion.
- For Wipers Holders, draw one circle and a half circle on the top face of the Superstructure. Boss-extrude them.
- Over the Midplane, reflect the bodies.
- To create an offset surface for the radar mast reference, choose the back portion of the top face of the superstructure and give it a new name.
- Create a rectangle on the appropriate plane and do boss extrude for wipers.
- Repeat three more times at the correct locations. Apply a chamfer, move the side faces outward, and execute a cut extrude.
- Do the same with the remaining wipers. Create a 3D design by connecting the holder and wiper with a line, then extruding that line to create a connecting rod. For the remaining ones, repeat.
- Apply appearance to the superstructure, railings, mattresses, doors, frames, wipers, water, and windows.
- Save the part file as superstructure.
9.) Radar Mast: Marine radars are X-band or S-band radars on ships, used to detect other ships and land obstacles and to provide bearing and distance for collision avoidance and navigation at sea. On a mast, a self-leveling mount will only work when the radar is mounted forward of the mast, but as the radome is not rigidly fixed, the sail won't snag it as easily. It's worth being aware that mounting a radome close to the mast can sometimes cause a blind spot where the mast obstructs the beam.
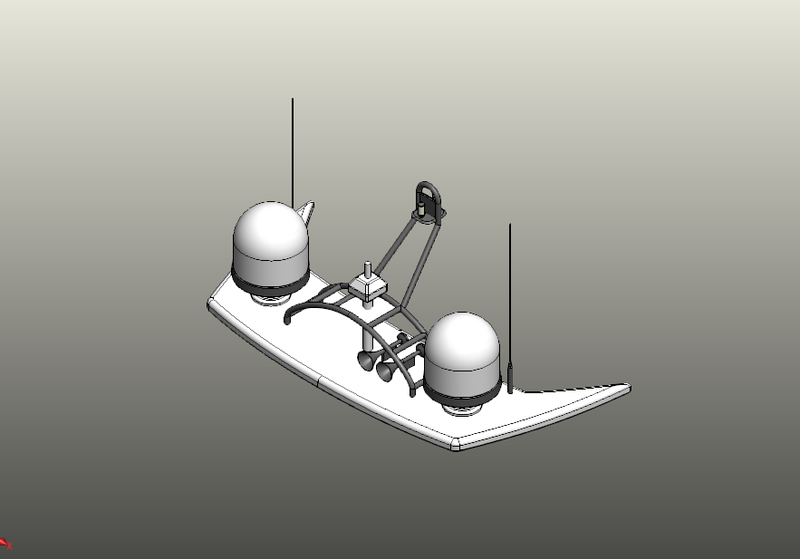
Features used to create a Radar Mast:
- Sketch
- Boss-Extrude
- Revolve
- Sweep
- Cut Extrude
- Fillet
Procedure
- Insert all views, including top, side, bottom, and front views, among others, into the blueprint setup by giving them the appropriate X, Y, and Z direction dimensions.
- Make two planes Front and bottom planes are used as references for the back and top planes. By selecting the surface bodies, insert the Hull part.
- Select the surface bodies to insert the Superstructure part.
- Draw a horizontal line 160mm from the surface of the radar mast to create a sketch, and then add fillets to the outer and inner edges of the line.
- Following the blueprint, construct a plane and extrude it using 4 splines and a line.
- For radar indicators, sketch a three-point arc and line on the top face of the previous extrusion and rotate it. On the extruded face, draw a circle, then extrude it. Put on fillets.
- Draw a circle on the Extrude1 face and extrude it to create a sketch for the antenna. On the extruded face, draw another circle and extrude it.
- Create a circle and perform one more extrude on the previous extrude face.
- By sketching a sketch on a newly formed plane using a spline and a circle on a 3D sketch, you may make a sweep.
- Draw three circles on the sweep and extrude them to join them by mirroring the sweep above over Plane 2.
- Using sketches on the appropriate Planes, create a Projected curve in accordance with the requirements. Draw a circle at the projected curve's edge to create a sweep.
- Draw a few lines and splines for the horn according to the blueprint. Rotate. Apply a shell to one end and a dome to the other.
- Mirror everything across the middle plane, excluding the horn. Draw a straight slot on Extrude 1 face and extrude up to Horn Face for Horn Support.
- Using the right extruded face from above, create a plane and offset it. Across the newly constructed plane, reflect the Horn and its support.
- Finally, give the radar mast, antenna, horn & indicators attention and save the file at last.
Procedure for Assembly of Sunseeker Predator Yacht
- Open all Individual parts in SolidWorks.
- Then open a new assembly file in SolidWorks.
- Now apply the appropriate mates by using the mate option.
- After applying the mate option, apply the decals to the body parts as required to the Hull, Garage Door, Propeller, Radar, Radar Mast, Superstructure, Front Seat, Middle Seat & Rear Seat.
- Now open photoview 360 in the add-ins option. Apply decals as required and ensure that those are correctly arranged.
- Now add a Rearview Isometric of the Yacht and save the Rear view of the Yacht in the view section and add a camera view.
- And save the file now.
Rendering Pictures
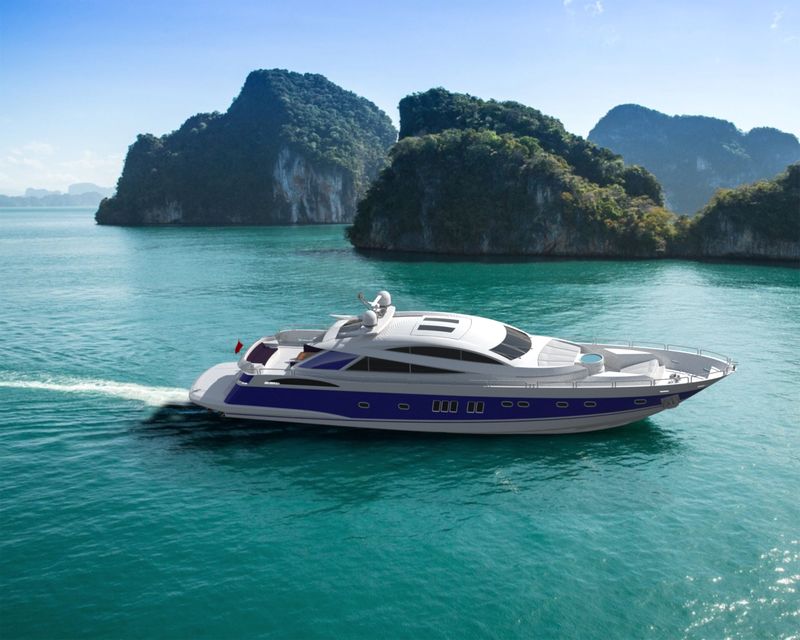
Picture 1
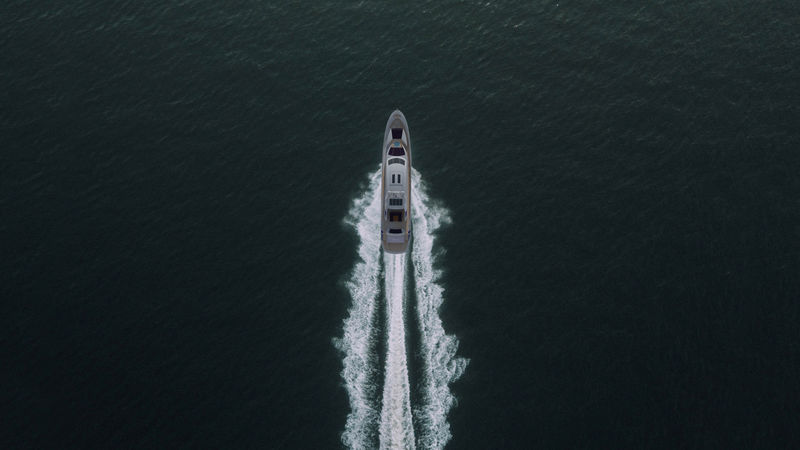
Picture 2
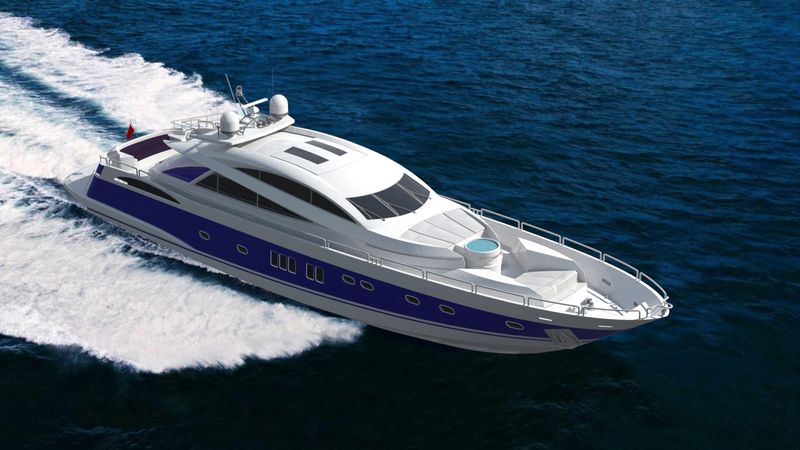
Picture 3
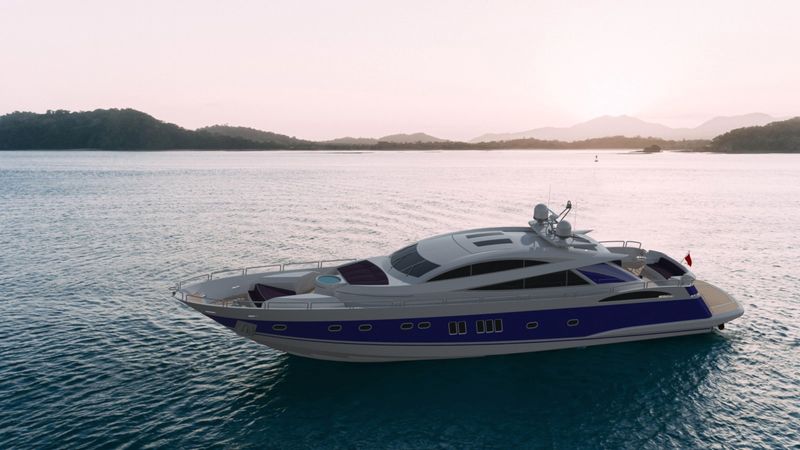
Picture 4
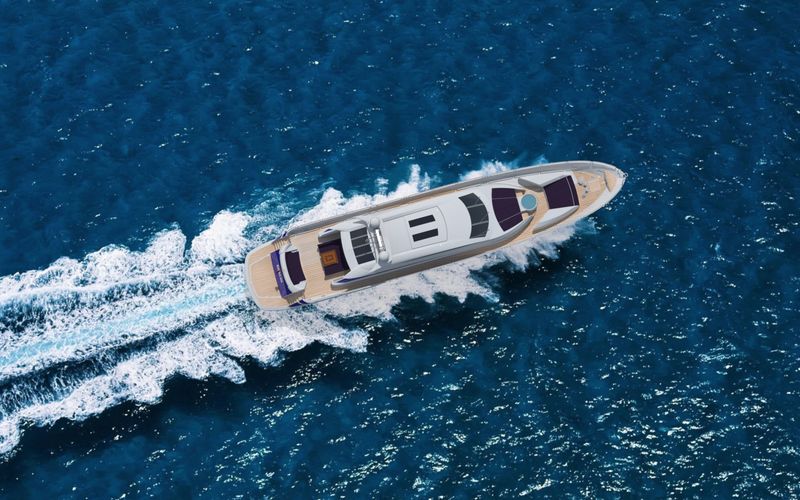
Picture 5
Note: In rendering, backplates are used as water backgrounds, as no HDR environments are available.
CONCLUSION
Solidworks was used to model and assemble the Sunseeker Predator Yacht, and Solidworks Visualize has been used to provide photorealistic renderings of the Yacht.
Note: All the part files, assemble files and rendered files have been uploaded to this link below.
Yacht_Assembly_Mahesh_Kumar