Aim :
1) To study the different types of interfaces and to compare the results of radioss simulation for each interface case.
2) To create a mesh with the size of 6mm for bumper assembly.
Scope of the project:
1) In this project first we have performed 2d meshing on bumper assembly with an element size of 6mm.
2) For crush tube we have considered six different cases to study different interface types.
3) Type 11 contact is created for crush tube and simulation results are compared with type 7 contact
4) Effect of Inacti is observed by changing its value and performing radioss analysis.
5) Effect of notches on crush tube simulation is observed.
6) For each case different contours and plots are observed to study the interface types.
Meshing of Bumper Assembly :
- First, the given model is imported to Hypermesh and using automesh(F12) meshing is performed with the required element size of 6mm.
- Appropriate connectors are used in some places.
- All the mesh errors are removed.
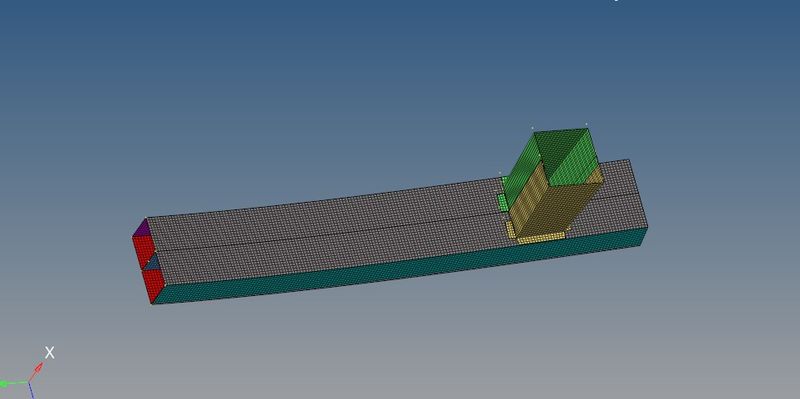
The Six different cases in this project include:
- Run the crash tube model as it is.
- Change the Inacti=6 and run.
- Create the type 11 contact and run.
- Remove both notches and remove boundary condition on rigid body node then run.
- Create a new notch in the middle, select the whole section and run.
- Create a new notch with nodes only from opposing 2 faces and run.
Case 1:
- In this case, the model is imported and run as it is without making any changes to the default settings & file parameters.
- From the 0001.out file we can track the energy error of the simulation model, it can be observed that the energy error at the start of the simulation is 0.0% as the simulation progresses the negative energy error increases in the negative value and reaches -4.6% and at the end of the simulation the energy error is at -3.8%, the energy error value is under the required limit and the result is acceptable.
- The interface type 7 is used, which is a node to surface interaction, and the gap for the simulation is at 1mm, there is no initial penetration in the model, as the gap between the parts is 2.1mm is maintained.
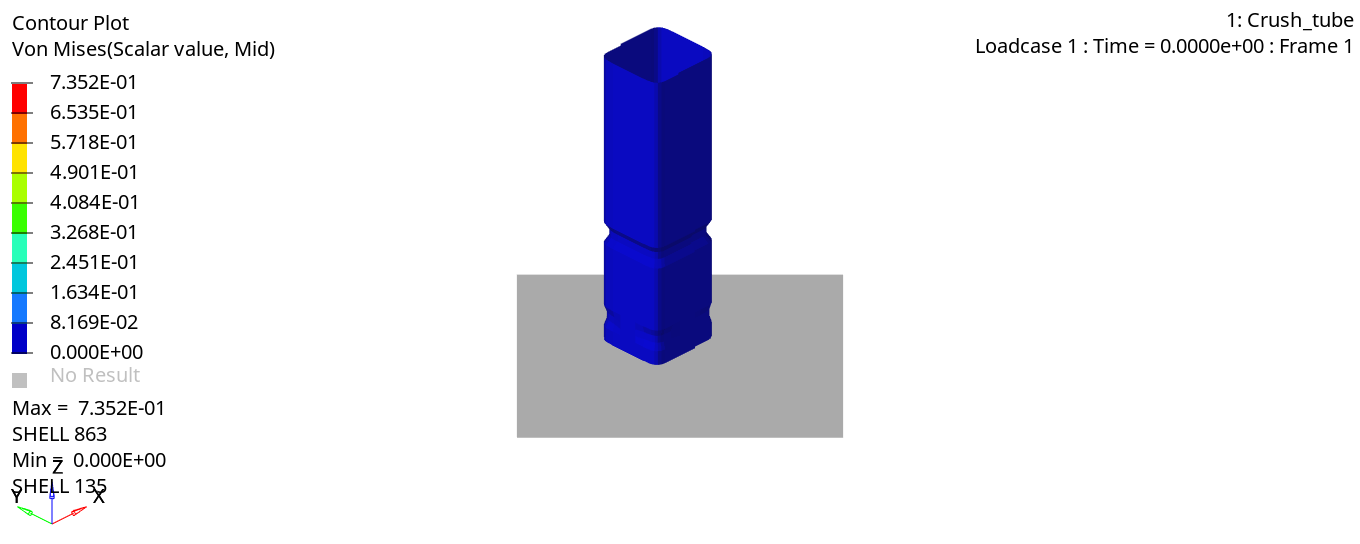
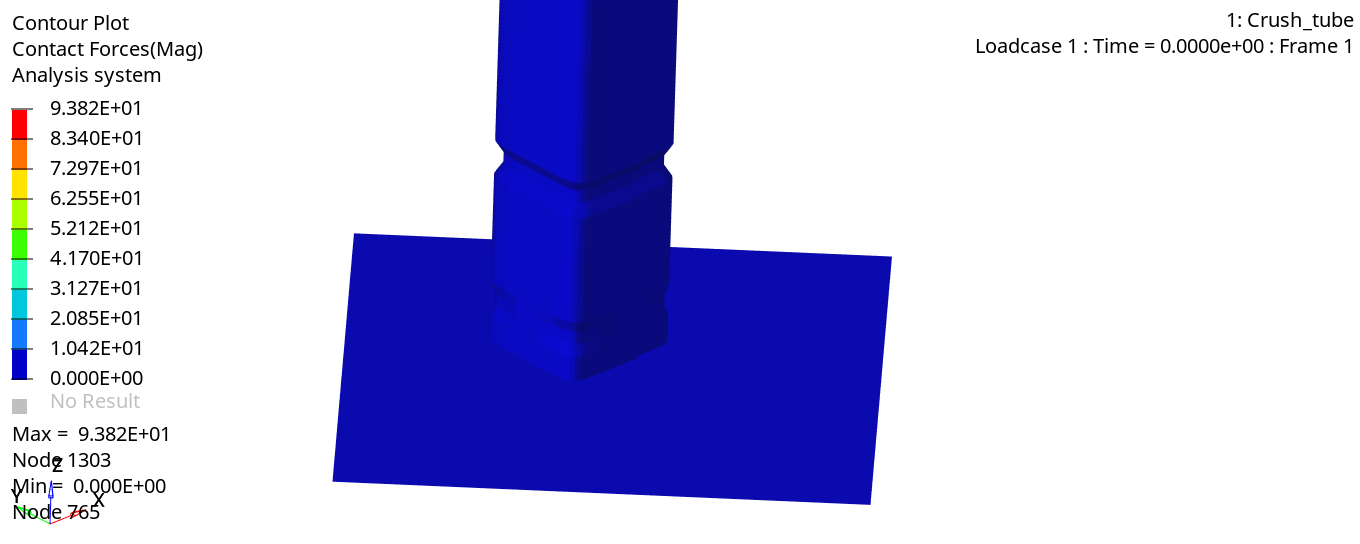
- The above simulation video shows the von misses stress and contact forces developed during the simulation which is high at the end of the simulation.
- As the tube is crushed under load, due to self impacting the slave nodes tries to enter the defined gap due to which the resistive force is activated between the master segment and the slave nodes, which contributes to the energy being dissipated by the master segment to stop the slave nodes from reaching the mid surface, which can be seen in the energy error image above. The negative value indicates that some energy has been dissipated.
- Mass error observed is 0.
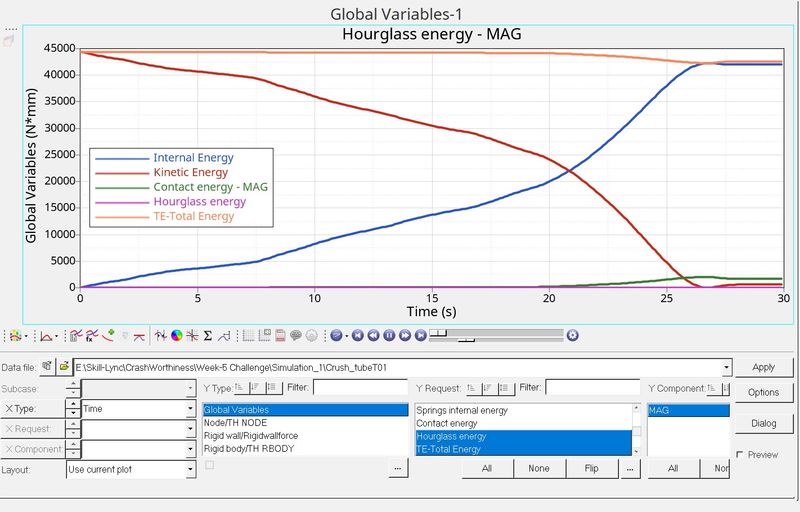
- The above graph shows the contact forces developed in the simulation, it is observed at the end of the simulation at 27ms time, when the whole tube is crushed against the wall.
- The contact forces is in accordance with the internal energy.
- The graph shows the contact energy of the simulation model, it increases with time and reaches the peak near the end of the simulation at 27ms, since contact forces at the end are higher the contact energy at the end is also at higher values.
- The internal energy increases with time, and kinetic energy has the opposite trend to that of internal energy, as the applied force crushes the tube the kinetic energy is transformed as internal energy and it stored as strain energy.
- The total energy in the system stays almost constant due to resistive forces developed to keep the slave nodes out some of the energy is dissipated by the model.
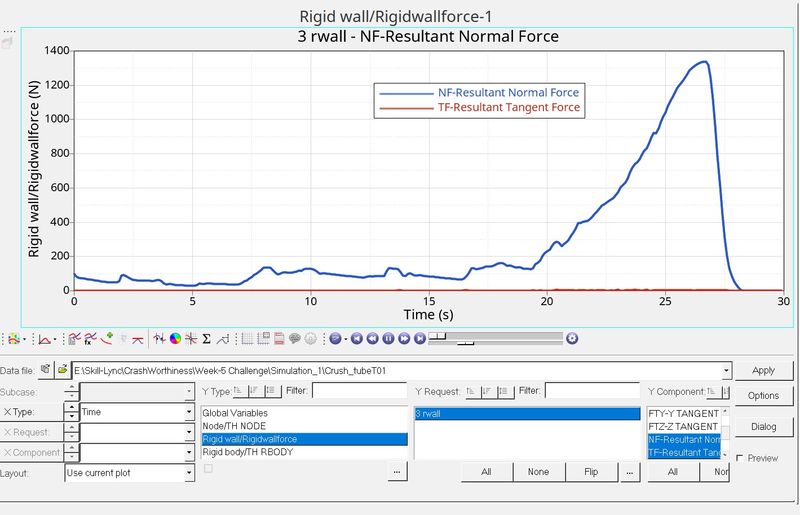
- The graph shows the rigid wall forces, at the start of the simulation forces on the rigid wall is minimal because at the start of the simulation much of the forces due to the applied velocity is being absorbed by the materials due to which they deform, and when the tube is crushed completely against the wall that is when we see all the forces being transformed to the wall, which is what seen in the graph.
Case 2:
- For this case, the model is imported. Then the ‘inacti’ parameter is changed to 6 from the default setting. The parameter ‘inacti’ is used to remove initial penetrations in the model during the analysis. With this setting, the analysis is started.
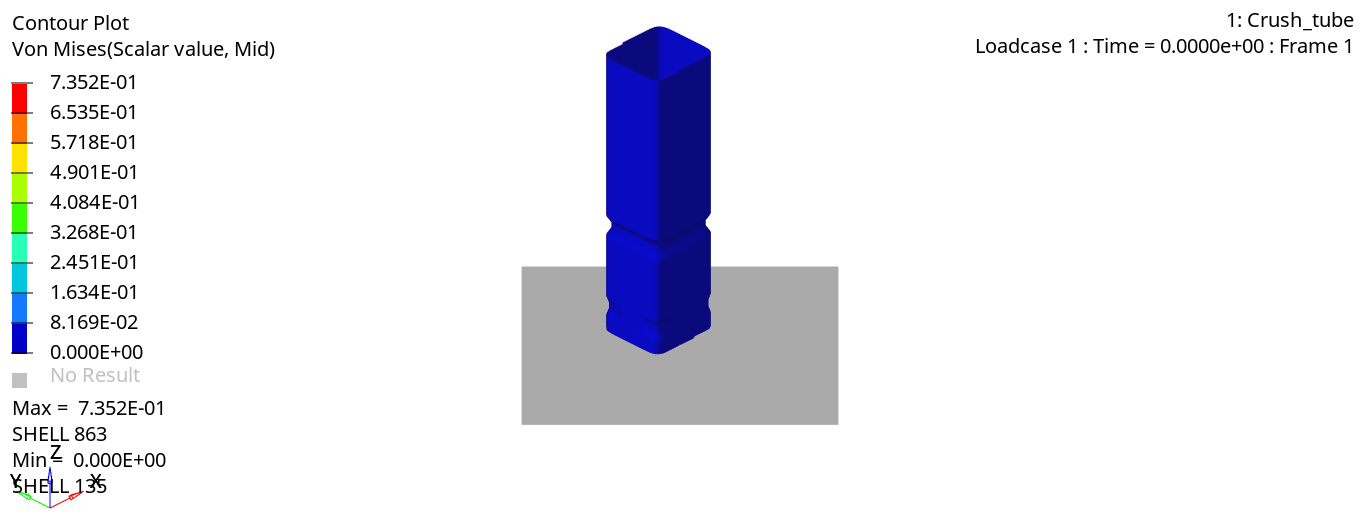
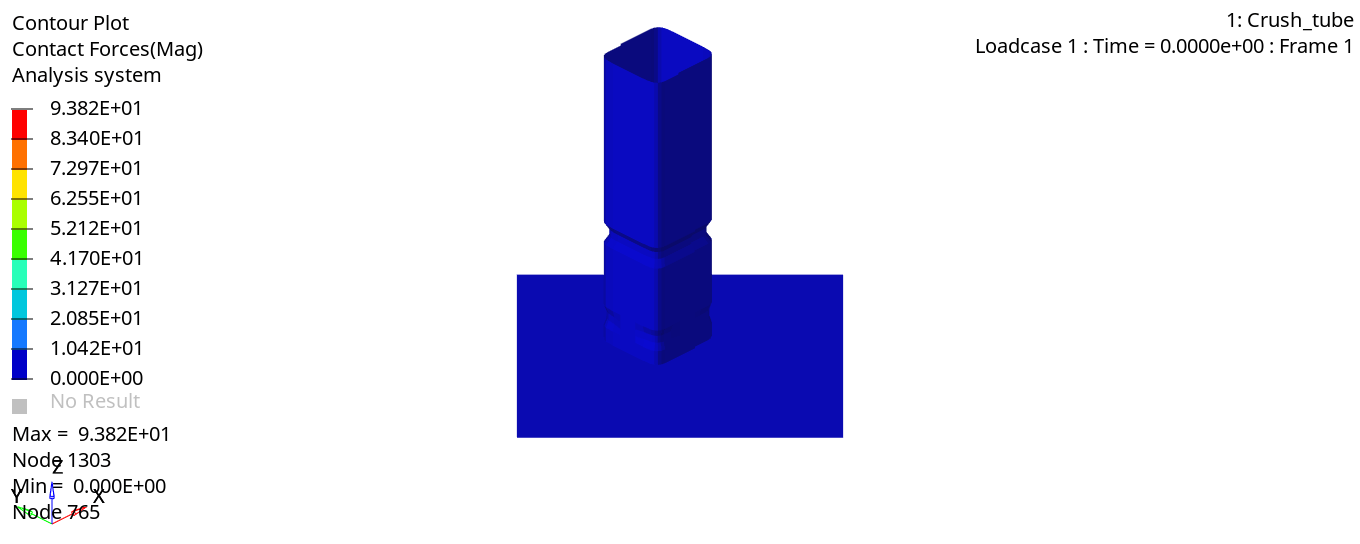
- The above simulation video shows the von misses stress and contact forces developed during the simulation.
- From the 0001.out file we can track the energy error of the simulation model, it can be observed that the energy error at the start of the simulation is 0.0% as the simulation progresses the negative energy error increases in the negative value and reaches -4.6% and at the end of the simulation the energy error is at -3.8%, the energy error value is under the required limit and the result is acceptable.
- The contact forces are in accordance with the internal energy.
- The contact forces are observed at the end of the simulation similar to case 1, and the contact force values are also similar to that of case 1.
- since there was no initial penetration their is not much noticeable change in the energy error, the only change is in the simulation time which is due to activating the inacti=6, which will help in reducing the calculation by providing some space for initial penetration. mass error is 0.
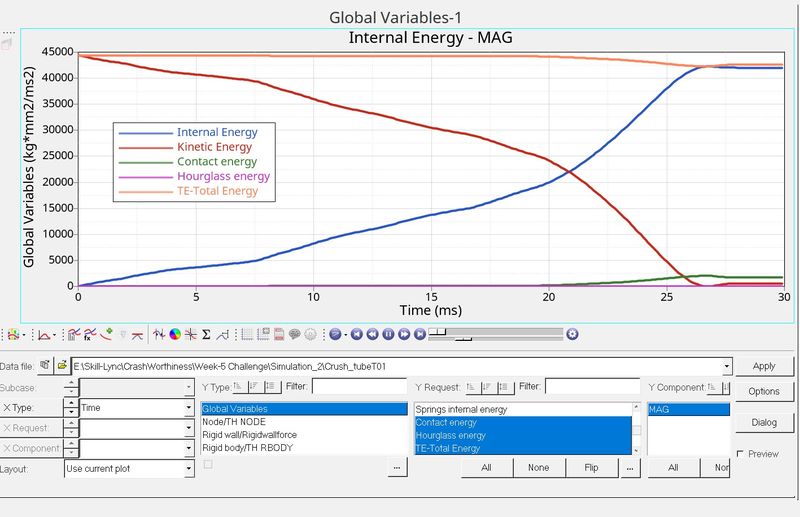
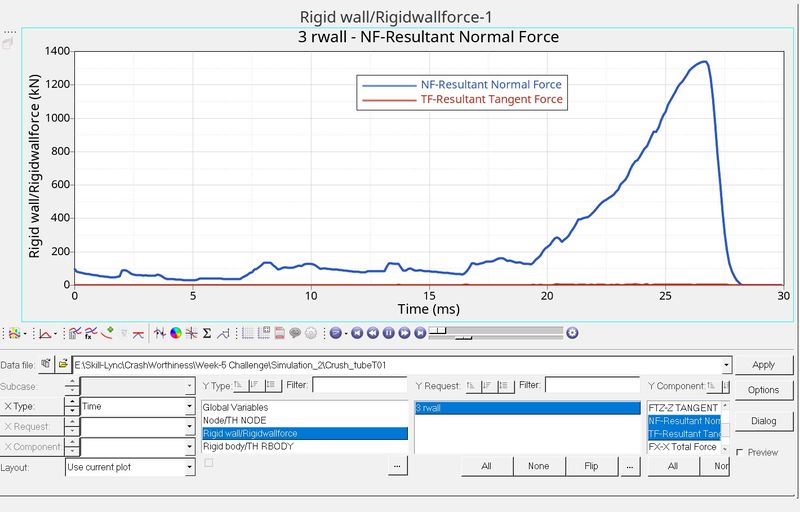
- In all the above two graphs similar trend is seen as in the case 1 simulation, and the values remain similar to that of case 1.
- Rwall forces reach a peak of 1350 kN, which is the same as the previous case.
- since there is no change in the notch areas and the material properties the simulation is similar to case 1, with the first notch being deformed first and progressing to the second notch and then finally deforming the upper tubes.
Case 3:
- For case 3, a type 11 contact is created between 2 edges. The recommended parameters for type 11 contact are set and then the analysis is run.
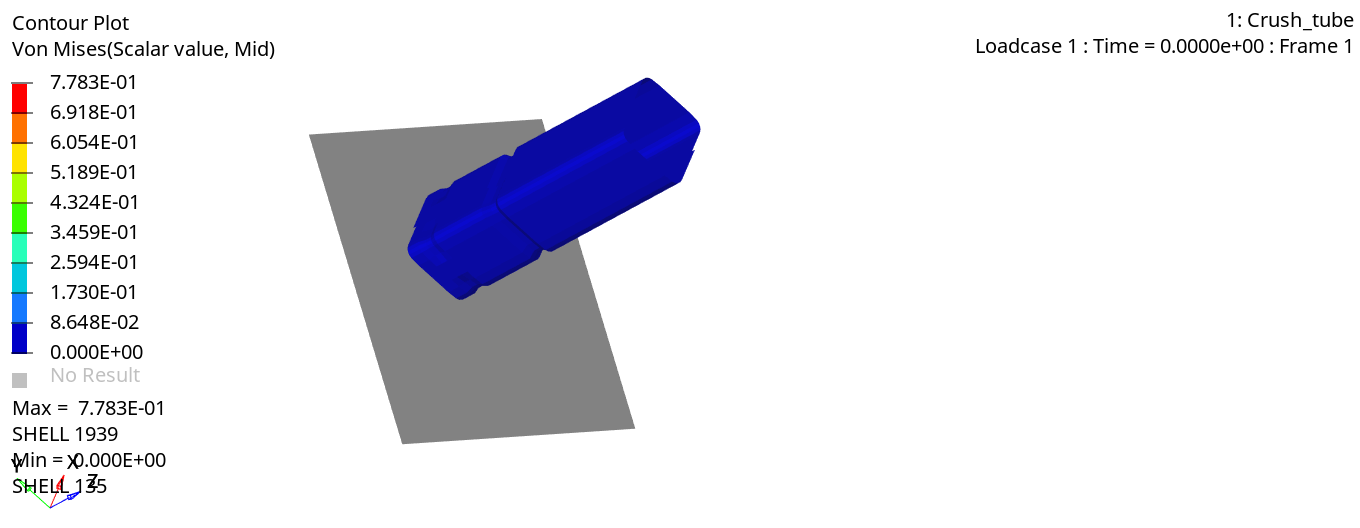
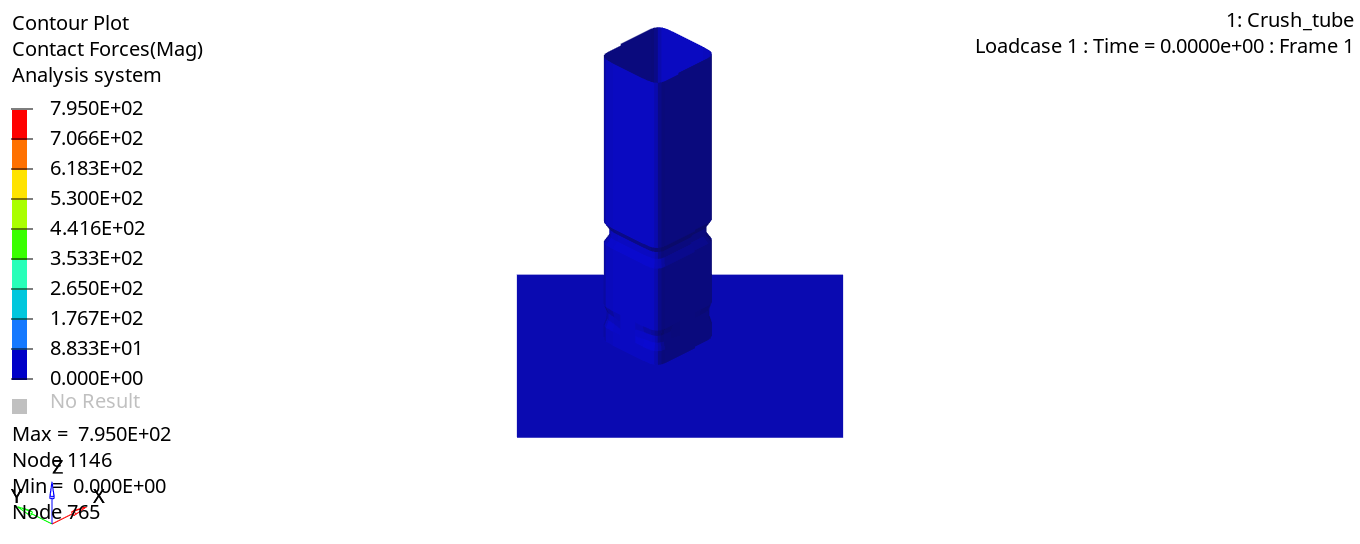
- The above simulation video shows the von misses stress and contact forces developed during the simulation.
- since there is no change in the placement of the notches, the simulation follows the same trend as the previous two cases.
- For case 3 simulation, the energy error is decreased to -2.6%, which can be due to the introduction of Type 11 contact in the simulation, which takes into account the edge to edge contact. mass error is 0.
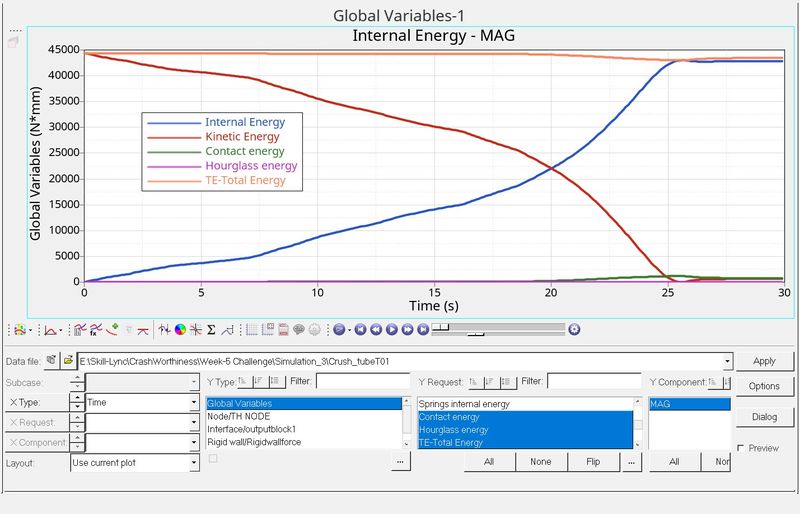
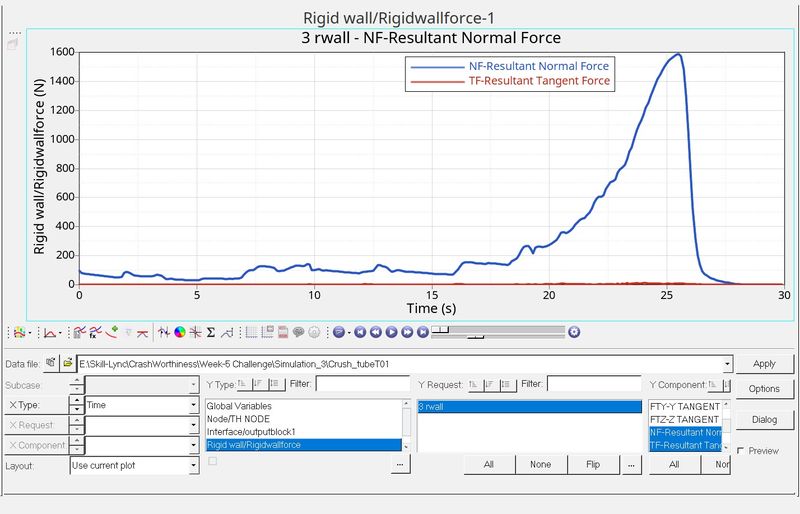
- The contact forces are in accordance with the internal energy.
- From the above simulation, the contact forces in this simulation are less than in the previous cases. since due to reduced contact forces the energy dissipated by the model is less, hence, the energy error is less compared to the previous two cases.
- The resultant normal force is high in this case as compared to the other two cases.
- since it has type 7 and type 11, contacts defined, the simulation time is higher than the previous two cases.
Case 4:
- For this case, the notches in the model are removed and the boundary conditions are also removed. This is done to see the effect of notches in the model. With this setup, the analysis is started.
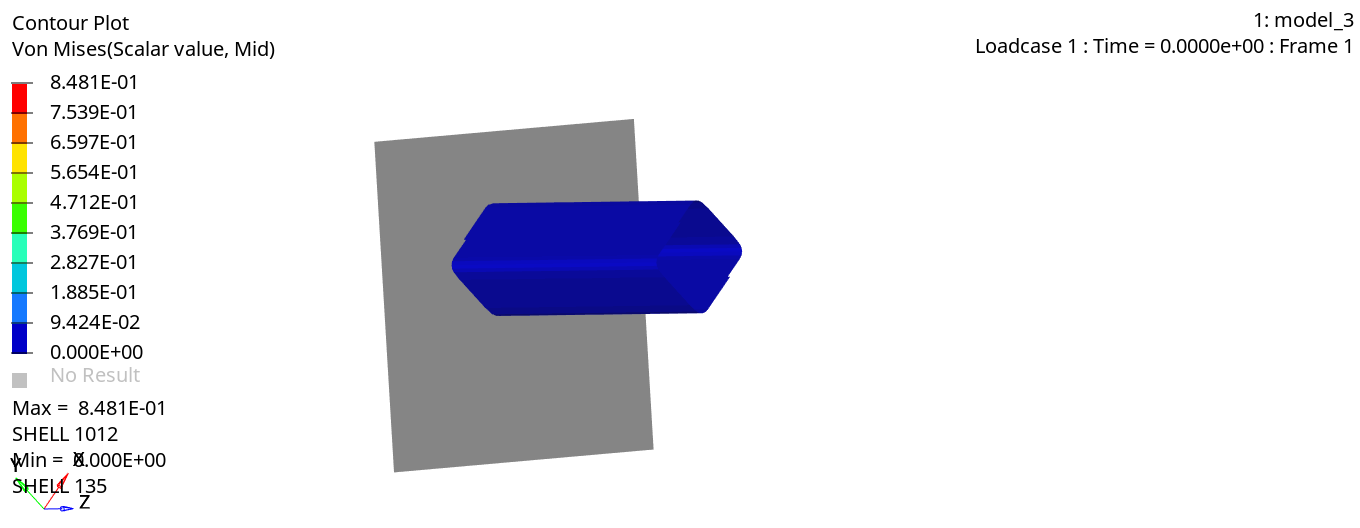
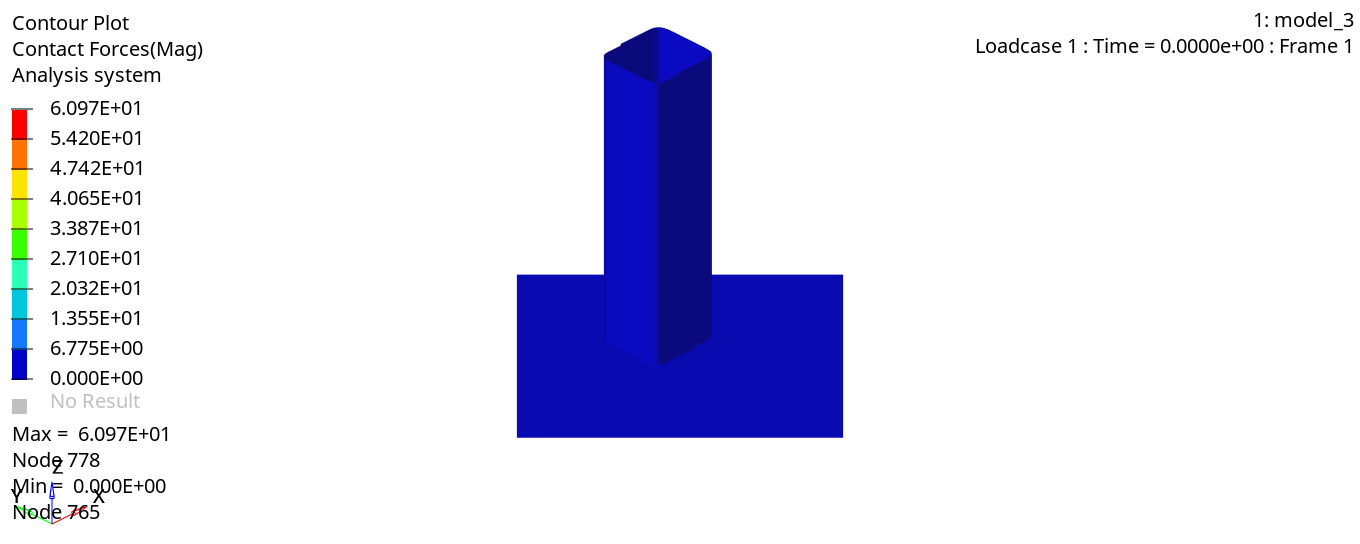
- The above simulation video shows the von misses stress and contact forces developed during the simulation.
- From the 0001.out file we can track the energy error of the simulation model, it can be observed that the energy error at the start of the simulation is 0.0% as the simulation progresses the negative energy error increases in the negative value and reaches -3.7% and at the end of the simulation the energy error is at -3.0%, the energy error value is under the required limit and the result is acceptable.
- Mass error is 0 throughout the analysis.
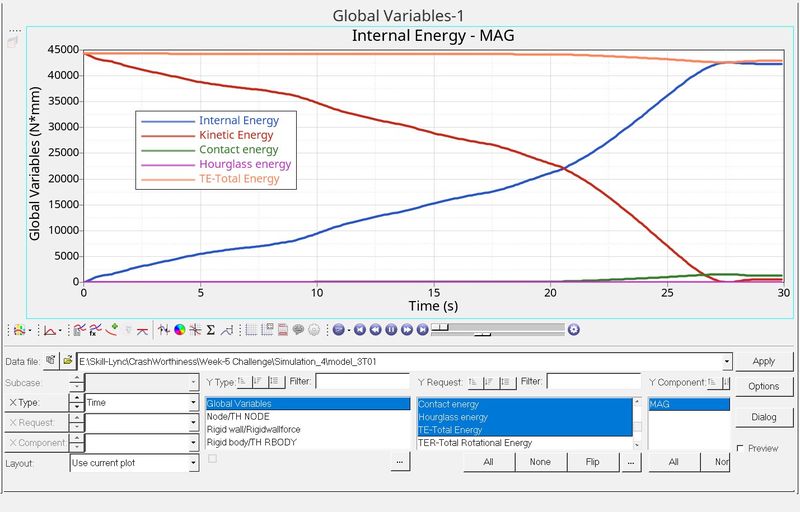
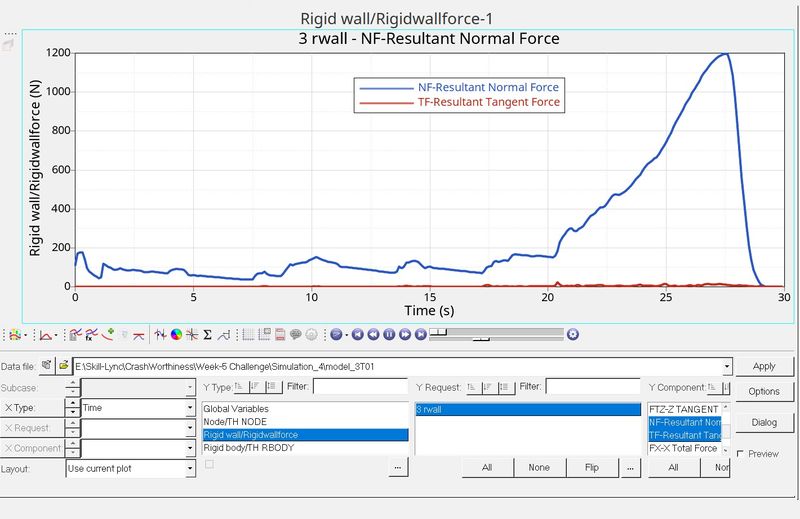
- The contact forces are in accordance with the internal energy.
- The contact forces are highest near the end of simulation time similar to what was observed in all the previous cases, but the contact forces are smaller compared to those of previous cases, this is due to the absence of notches in the model.
- since all the load cases are similar, there is no change in the trend of energies and rwall forces for case 4. The maximum Rwall forces value is at 1180 N, which is the lowest compared to previous simulation values.
Case 5:
- For the 5th case, a new notch is created in the middle. Other notches are removed and then the analysis is run.
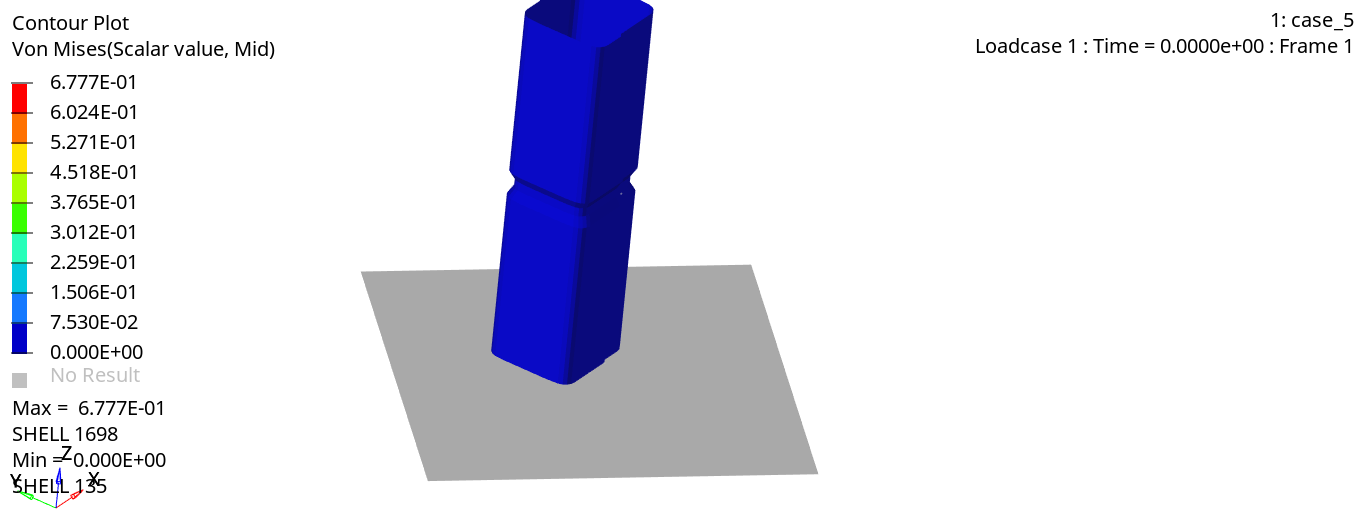
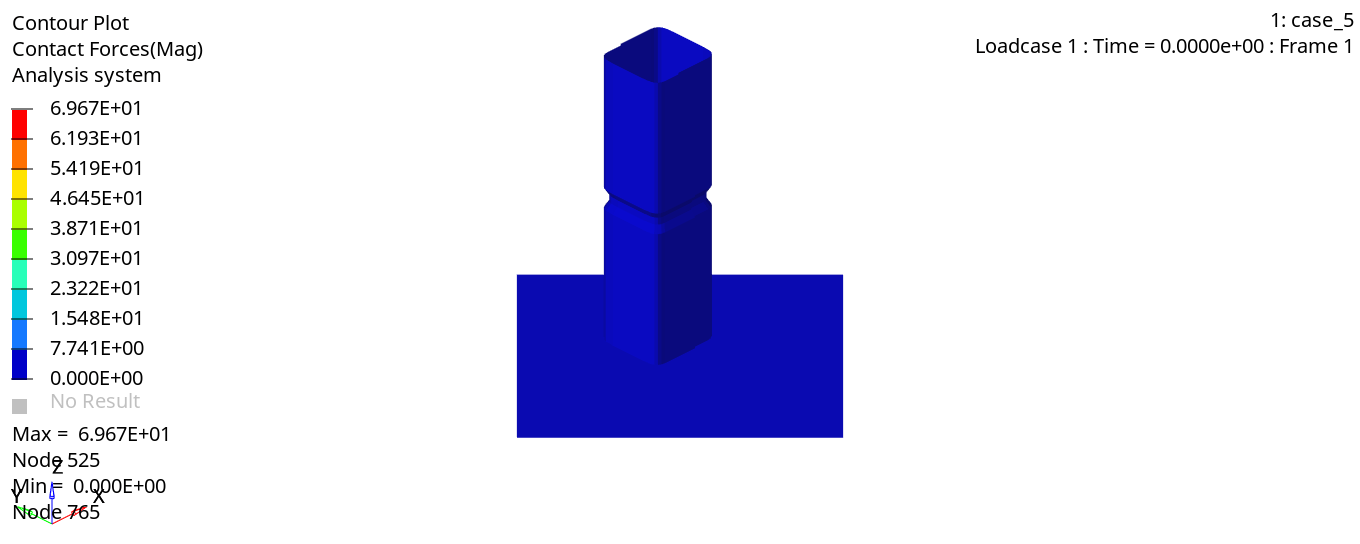
- The above simulation video shows the von misses stress and contact forces developed during the simulation.
- The first deformation in The model occurs at the notch area and then at the bottom of the tube before the upper part of the notch finally deforms and crushes the tube against the wall, which is as seen in the simulation above.
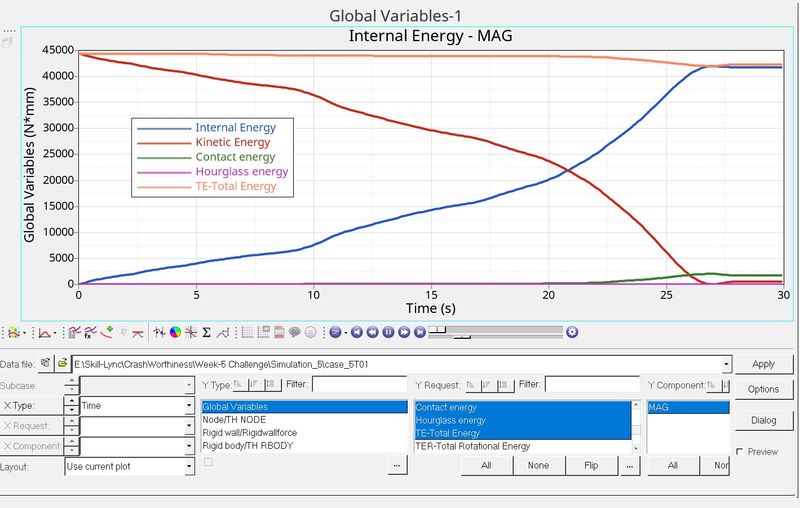
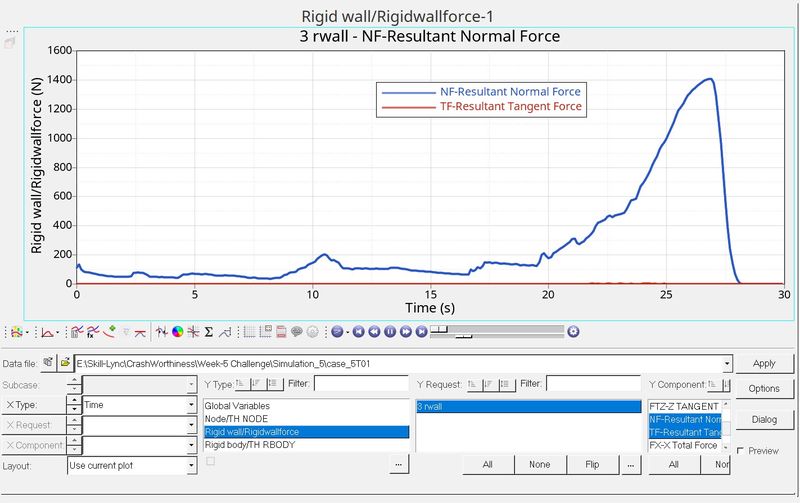
- The Resultant normal force is higher as compared to the previous case.
Case 6:
- For the 6th case, the notch is created with the nodes from 2 opposite faces. Then the analysis is run.
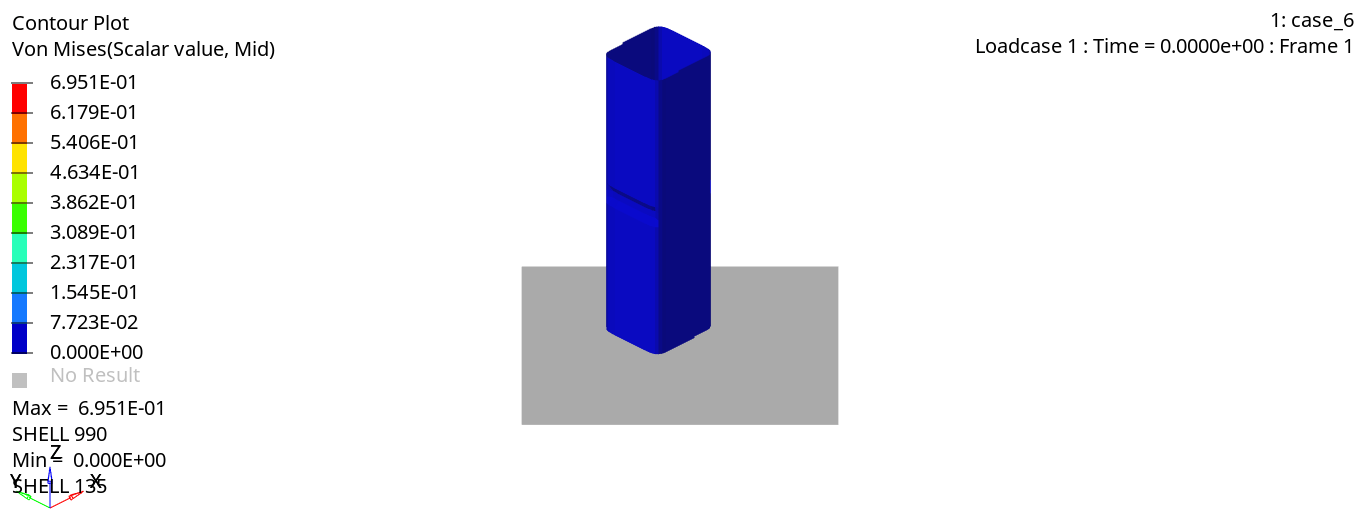
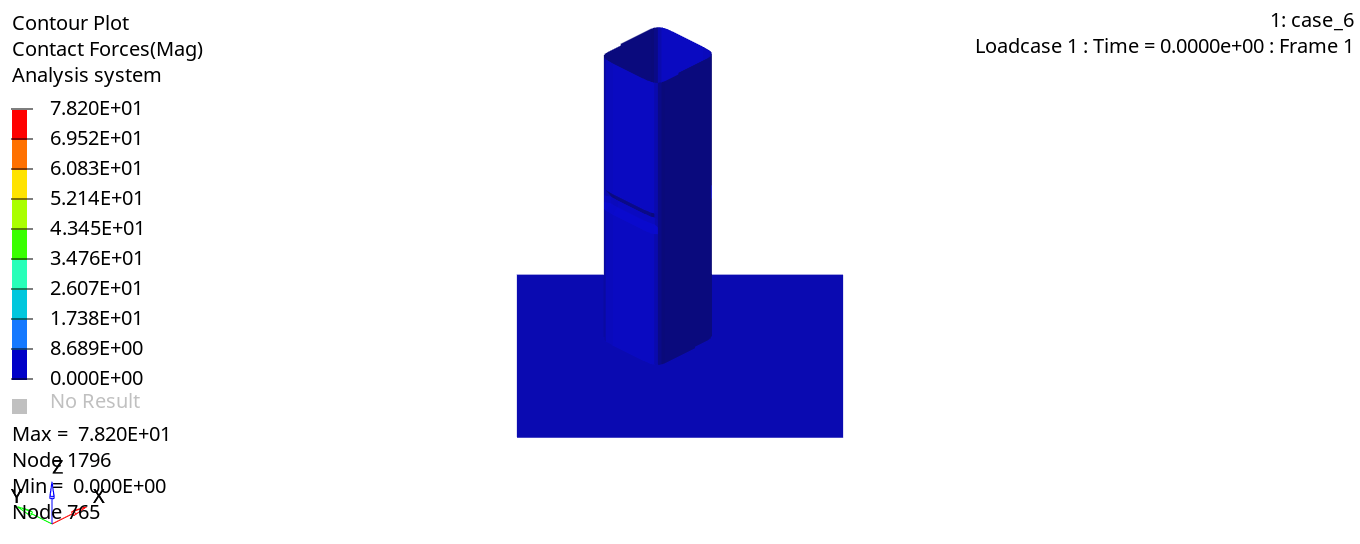
- The above simulation video shows the von misses stress and contact forces developed during the simulation.
- The first deformation in the model occurs when at the notch area, then progresses at the bottom of the model after which the upper part of the model is deformed.
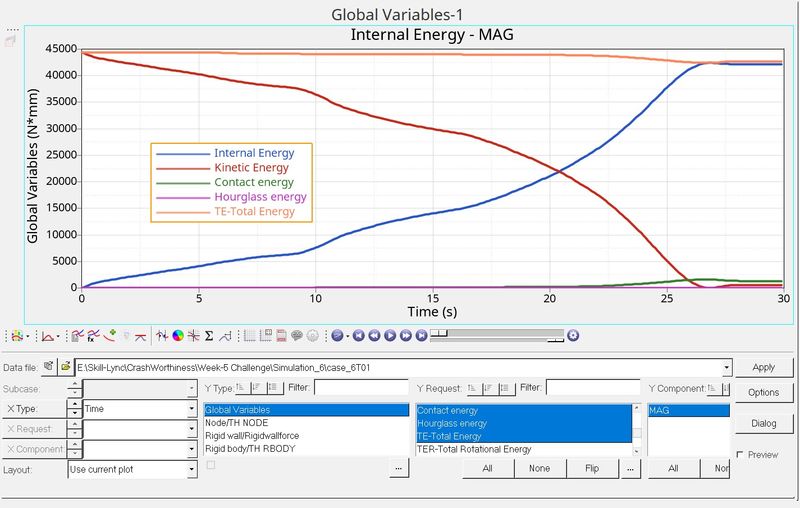
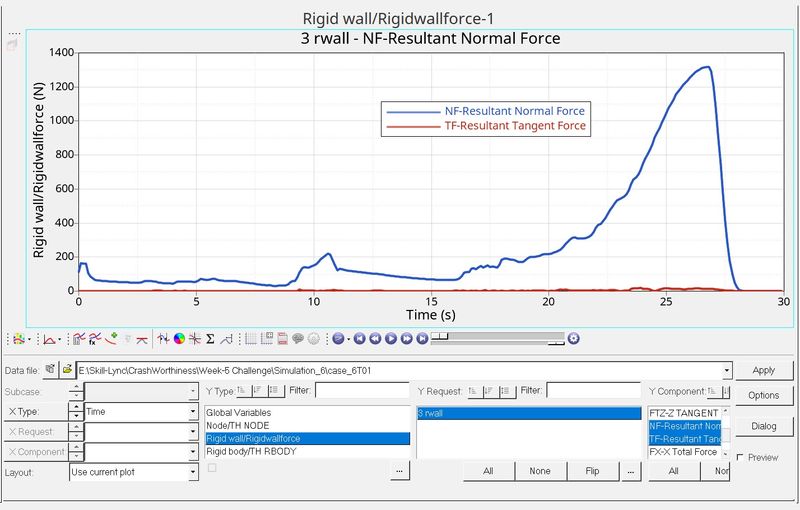
- The resultant normal force is less as compared to the previous case.
Comparison of different cases:
1) We have separated the first 3 cases as contact type and the second 3 cases based on notches.
2) In the first 3 cases, we find that no differences were noted between Cases 1 and 2 because there were no initial penetrations in the model for the Inacti to have an effect. The has increased no of cycles and increase other because we have defined a Type 11 edge to edge contact.
Case |
Case Definition |
Contact type |
No of cycles |
Elapsed time(sec) |
Max Energy Error(%) |
Mass Error |
Von misses stress(Gpa) |
Contact Forces(KN) |
1 |
Running Simulation using default parameters |
Type-7 |
83469 |
193.59 |
-4.6 |
0 |
0.735 |
93.82 |
2 |
Inacti value is changed to 6 |
Type-7 |
83469
|
195.14 |
-4.6 |
0 |
0.735 |
93.82 |
3 |
The contact interface type is Changed to |
Type-11 |
128088 |
374.72 |
-1.8 |
0 |
0.778 |
79.5 |
3)There are no physical differences in the path of the curve of the internal energies only difference is present in the values of it which are obtained according to the case definition.
4)There is no hourglass energy since there are recommended properties i.e. shell formulation inputted by default.
Case |
Case Definition |
No of cycles |
Elapsed time(sec) |
Max Energy Error(%) |
Mass Error |
Von misses stress(Gpa) |
Contact Forces(KN) |
4 |
Remove both notches and remove boundary condition on rigid body node. |
78390 |
100.75 |
-3.7 |
0 |
0.848 |
60.97 |
5 |
Create a new notch in the middle, select the whole section and run.
|
85163
|
104.17 |
-4.6 |
0 |
0.677 |
69.67 |
6 |
Create a new notch with nodes only from opposing 2 faces and run.
|
96775 |
123.45 |
-3.7 |
0 |
0.695 |
78.2 |
Conclusion:
We have also simulated the given cases and compared the results of segregating them into two sub-divisions i.e. type of contact and notches.