OBJECTIVE:
- To run the Radioss engine file and compare the result between all the 7 cases
Case Setup:
Case 1 (LAW2_epsmax_failure)
- In this case let us import the Failure_johnson_0000.rad file
- In first case without aking any change to the model , run the file in Analysis>radiosss>save it in desired directory
- The material property is shown in below image
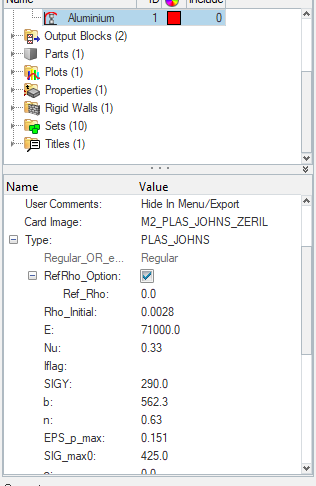
- After running the file, open the output file from the saved location
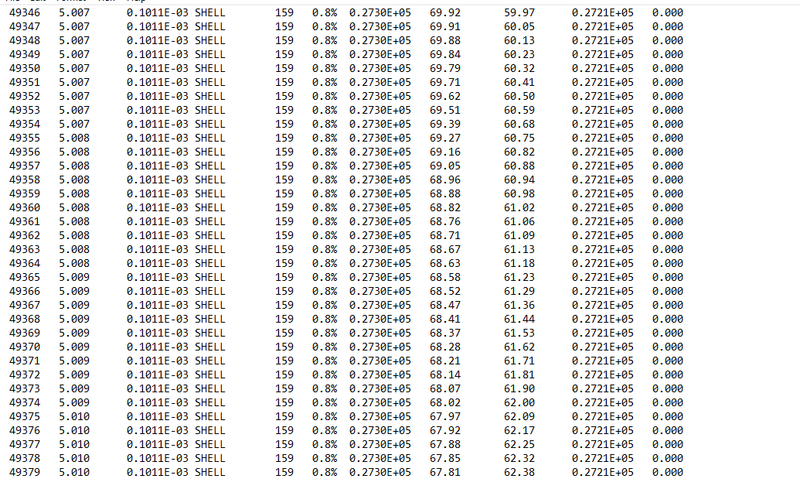
Total run time=116.66 seconds
Total number of cycles=49380
Energy error=0.8%
Mass error=0
- The energy error can be accepeted because it is less than 15%, now we can proceed with further steps
- Look at the displacement and von mises stress generated in the model, by going to Hyperview window
Displacement
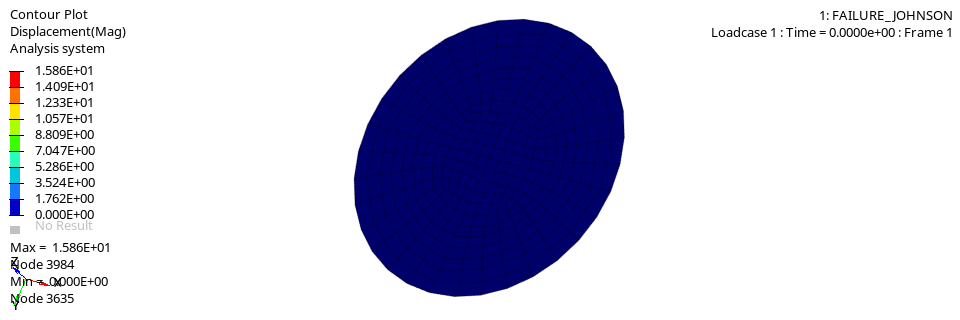
Max displacement=1.586E+01 node 3984
Von mises:
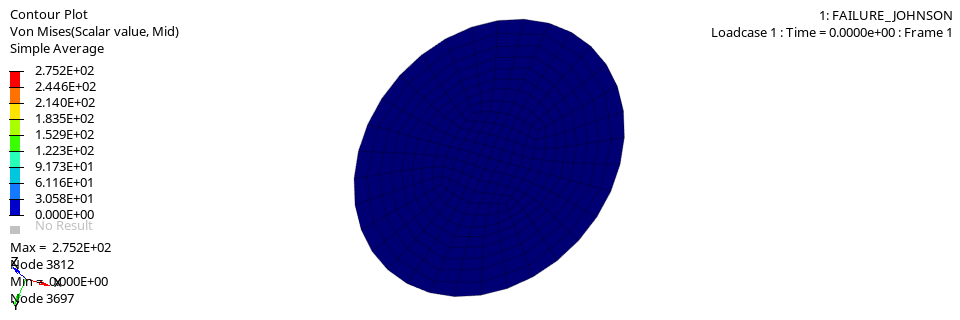
Max=2.752E+02 node 3812
Velocity:
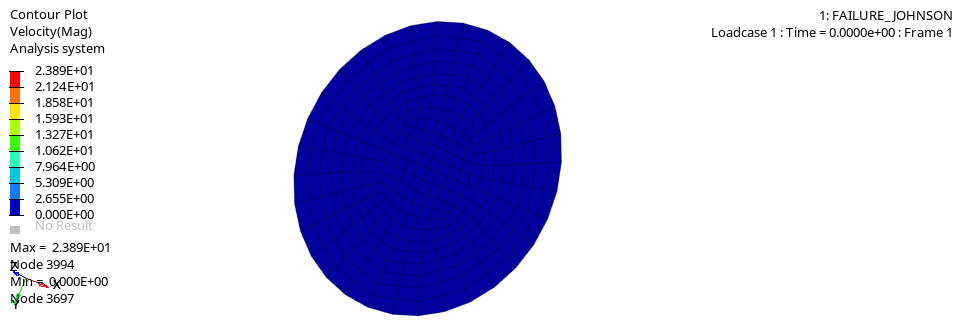
Max=2.389E+01 node 3994
Percentage of thickness reduction
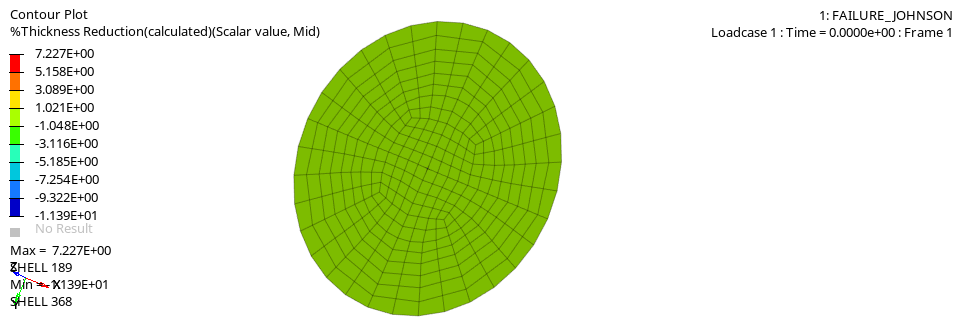
Plastic strain along thickness:

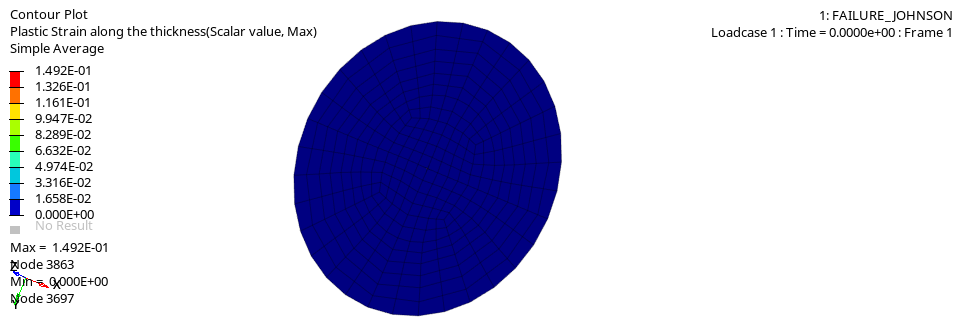

- Now we should plot the graph for Time v/s Energies, for that go to hyper graph2d window
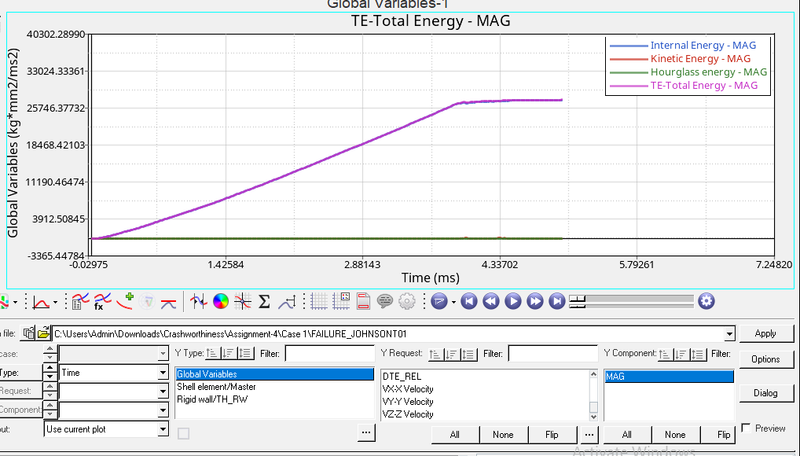
Internal energy => Max=2.7E+04; min=0;
Kinetic energy=>Max=179.25; min=0.004367;
Hourglass=0(formation of hourglass energy is avoided)
Total energy=> Max=2.7E+04; Min=0.004367;
Case 2 (LAW2_epsmax_crack)
- In this case the we should change some values in failure card like shown in below image
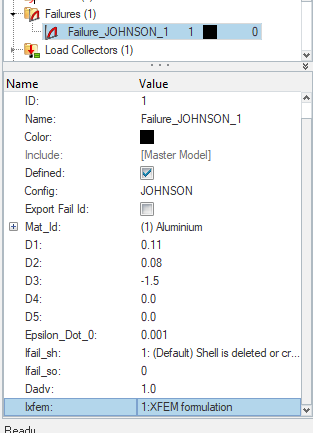
- Run the file like done in previous case, open the output file for this case
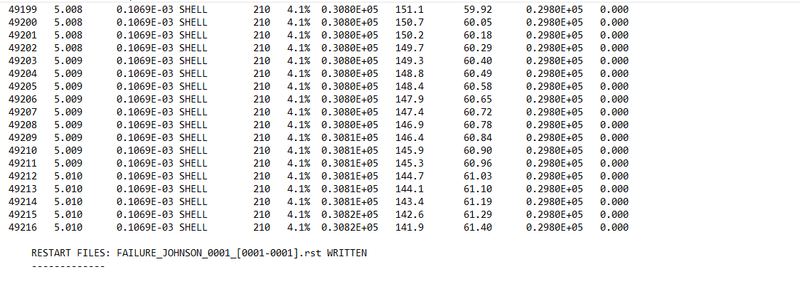
Simulation time=69.75sec
Total number of cycles=49217
Energy Error=4.1%
Mass Error=0
- Now the energy error generated in this case is acceptable, we can proceed with next step
- Open hyperview to see all the 5 animation
Displacement
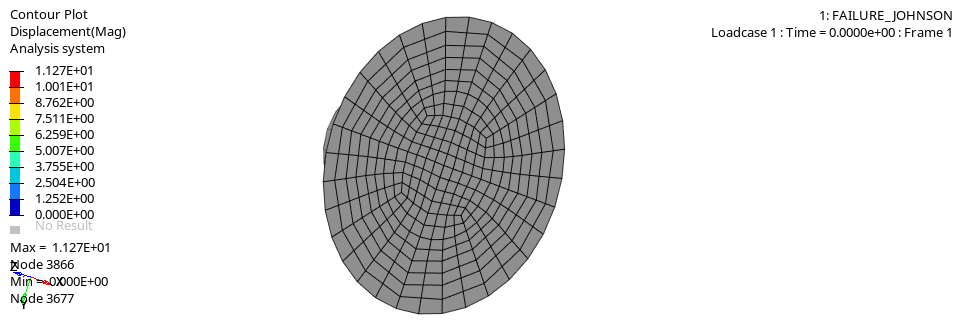
Vonmises
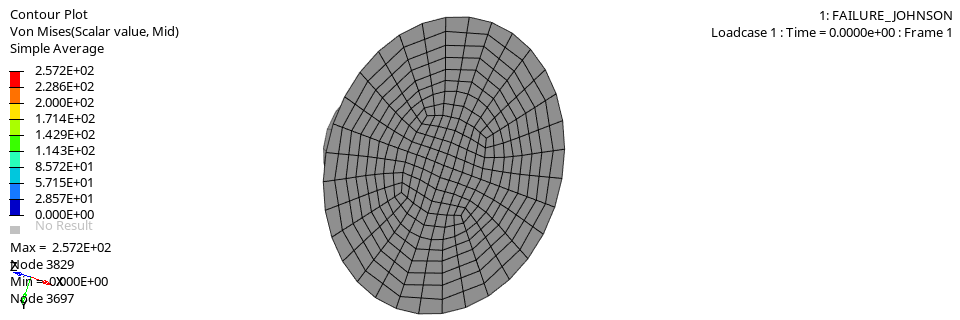
Velocity
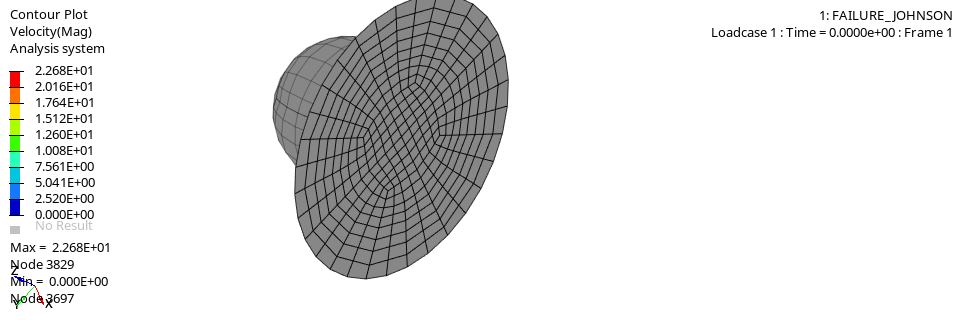
Percentage of thickness reduction
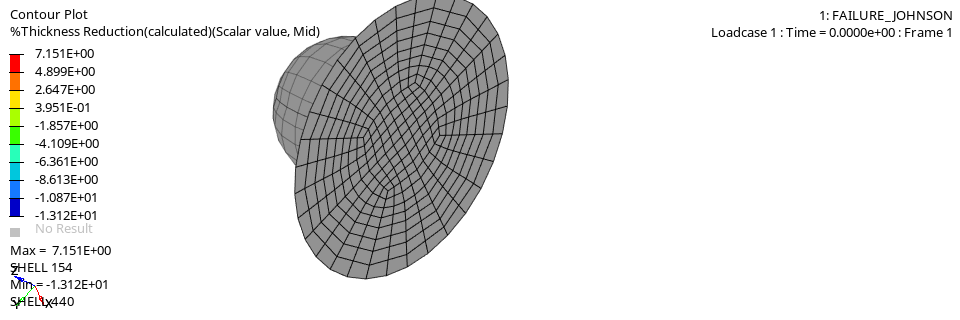
Plastic strain along thickness
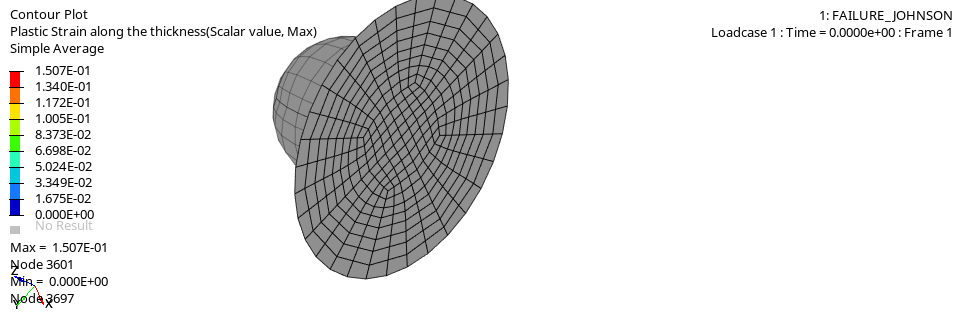
- Now plot the graph for Time v/s energies in hypergraph2d
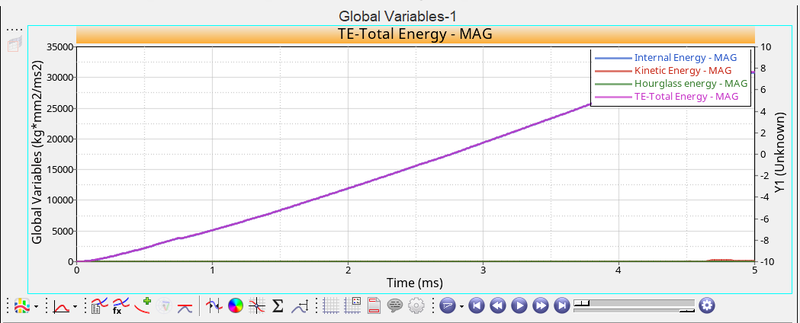
Internal energy => Max=3.08E+04; min=0;
Kinetic energy=>Max=210.28; min=0.004367;
Hourglass=0(formation of hourglass energy is avoided)
Total energy=> Max=3.08E+04; Min=0.004367;
Case 3(Law2_epsmax_nofail)
- Open the previous case file, now delete the failure johnson card
- Run the file like previous case, save the model in desired location
- Open the output file from the location you have saved,
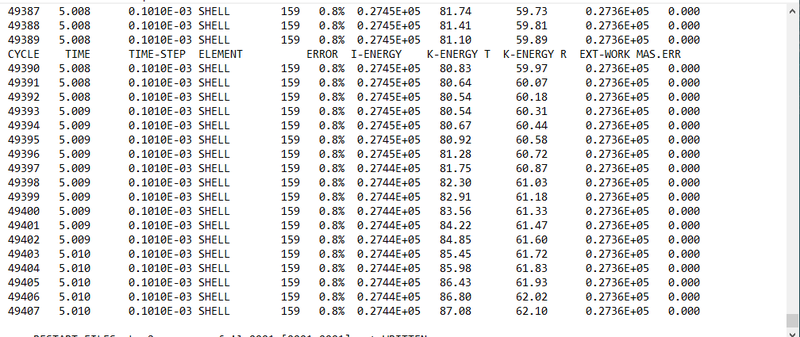
- Simulation time=56.04sec
Total number of cycles=49408
Energy Error=0.8%
Mass Error=0
- Now the energy error generated in this case is acceptable, we can proceed with next step
- Open hyperview to see all the 5 animation
Displacement
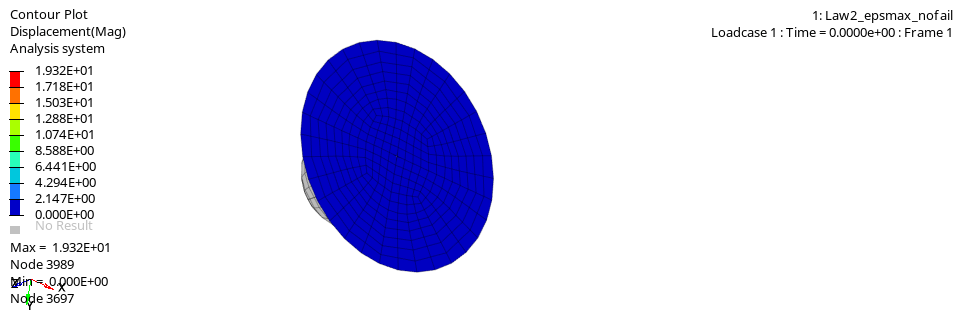
Vonmises
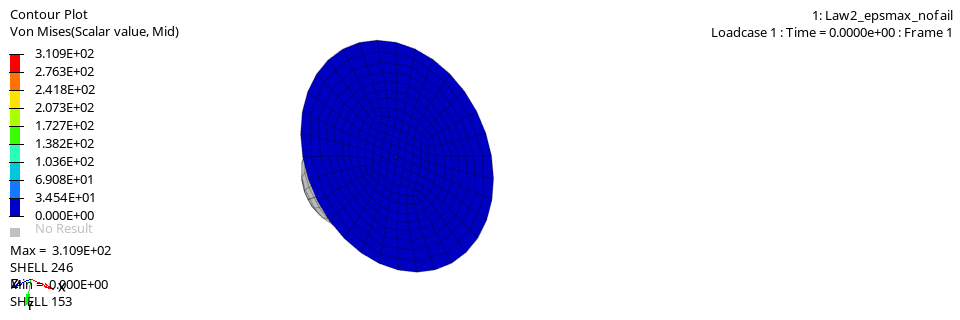
Velocity
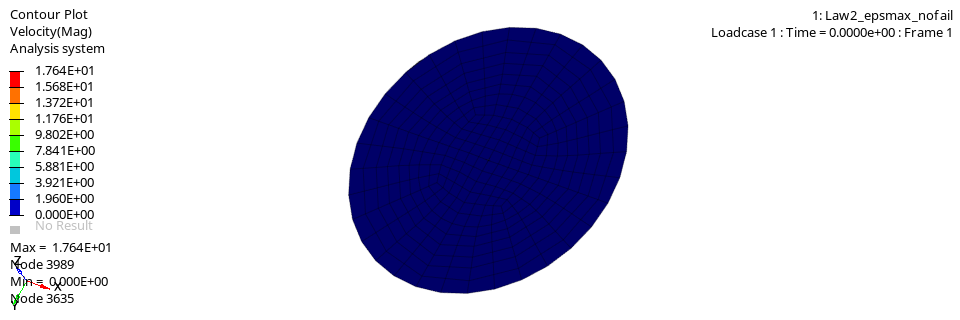
Percentage of thickness reduction
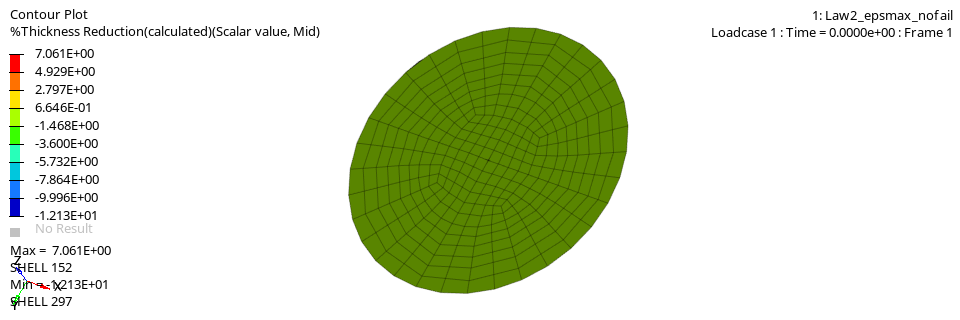
Plastic strain along thickness
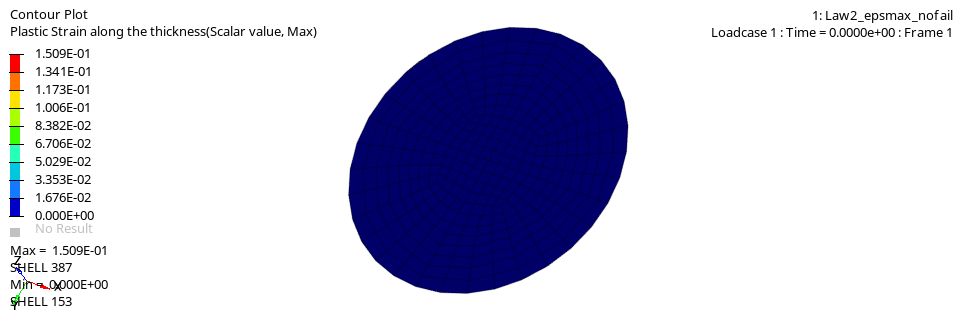
- Now plot the graph for Time v/s energies in hypergraph2d
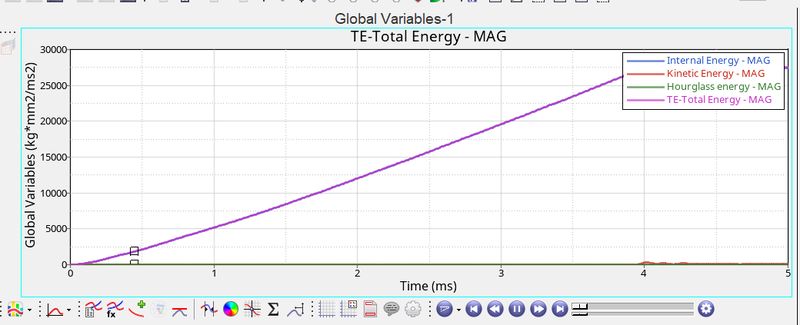
Internal energy => Max=2.74E+04; min=0;
Kinetic energy=>Max=332.072; min=0.004367;
Hourglass=0(formation of hourglass energy is avoided)
Total energy=> Max=2.74E+04; Min=0.004367;
Case 4(Law_2)
- In this case delete eps_max value and run the file
- Open the respective output file , we can find the mass error,number of cycles and time taken
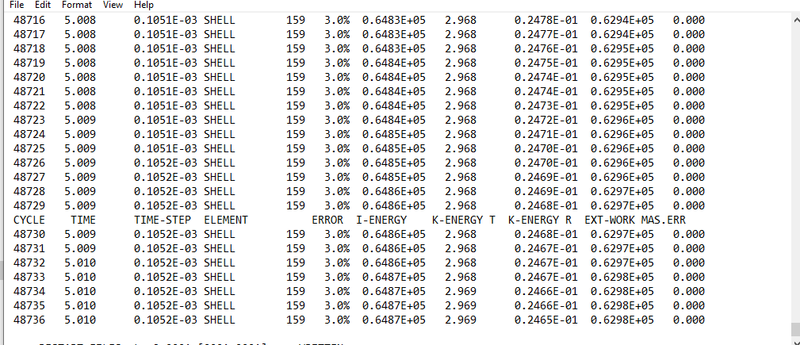
- Simulation time=56.37sec
Total number of cycles=48737
Energy Error=3%
Mass Error=0
- Now the energy error generated in this case is acceptable, we can proceed with next step
- Open hyperview to see all the 5 animation
Displacement
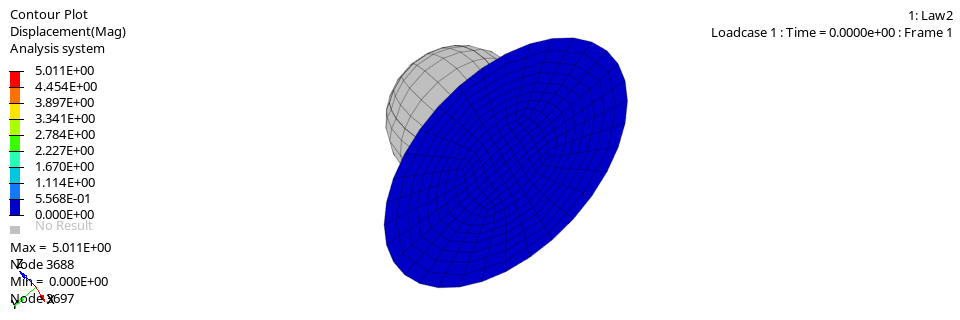
Vonmises
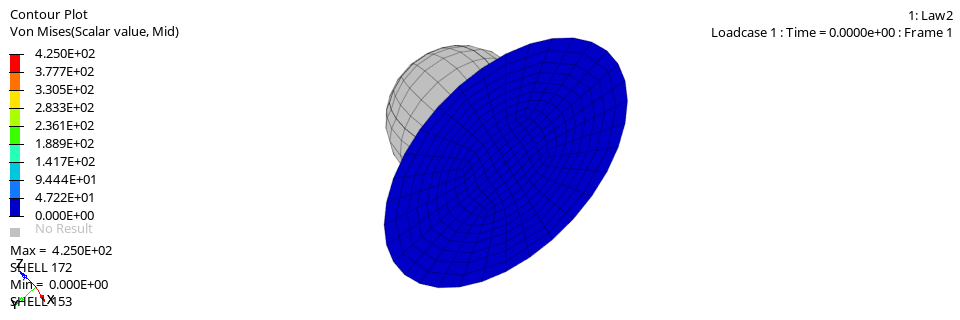
Velocity
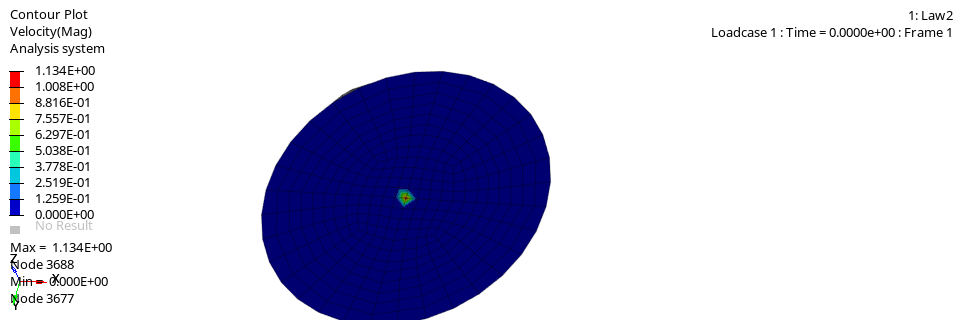
Percentage of thickness reduction
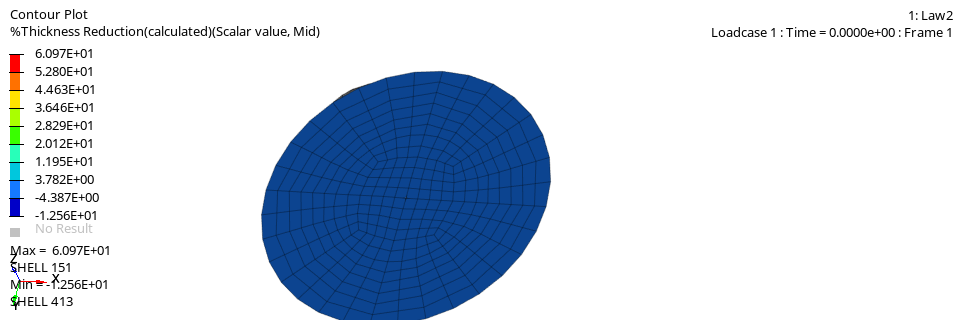
Plastic strain along thickness
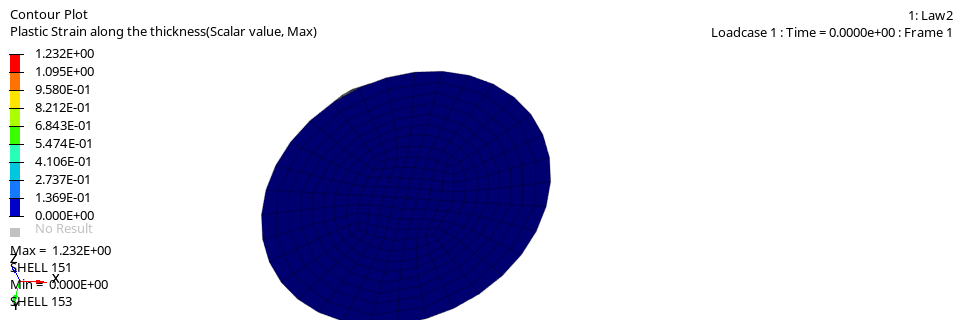
- Now plot the graph for Time v/s energies in hypergraph2d
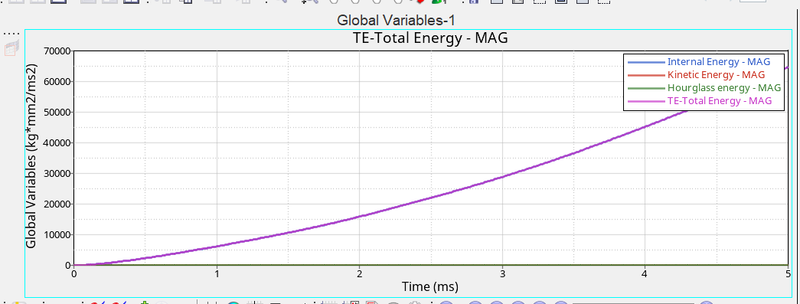
Internal energy => Max=6.4E+04; min=0;
Kinetic energy=>Max=3.77; min=0.004367;
Hourglass=0(formation of hourglass energy is avoided)
Total energy=> Max=6.4E+04; Min=0.004367;
Case 5(Law_1)
- In this case open the previous case file, change the material card to Law1, like shown in below image
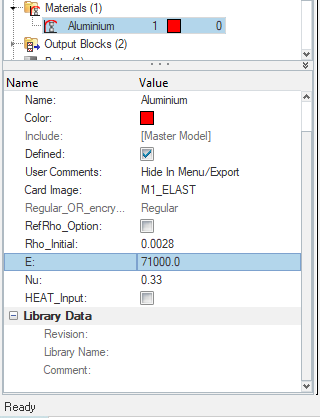
- Run the file with above material card
- Open the output file to find out mass error
- Simulation time=51.20sec
Total number of cycles=47699
Energy Error=1.3%
Mass Error=0
- Now the energy error generated in this case is acceptable, we can proceed with next step
- Open hyperview to see all the 5 animation
Displacement
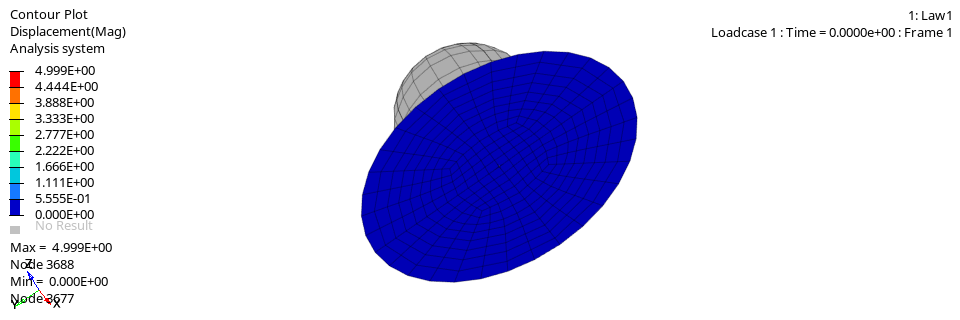
Vonmises
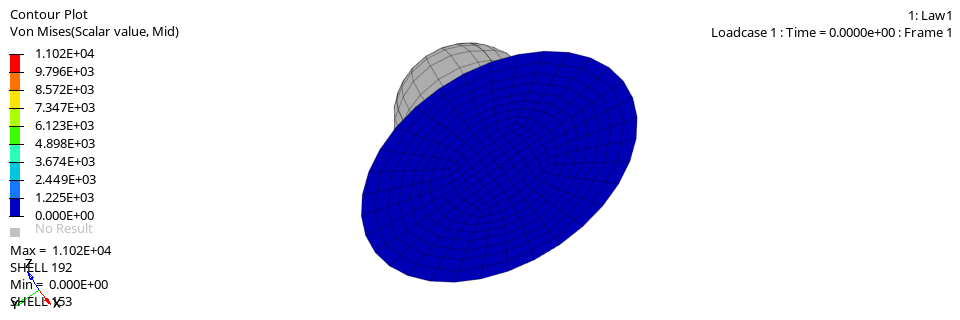
Velocity
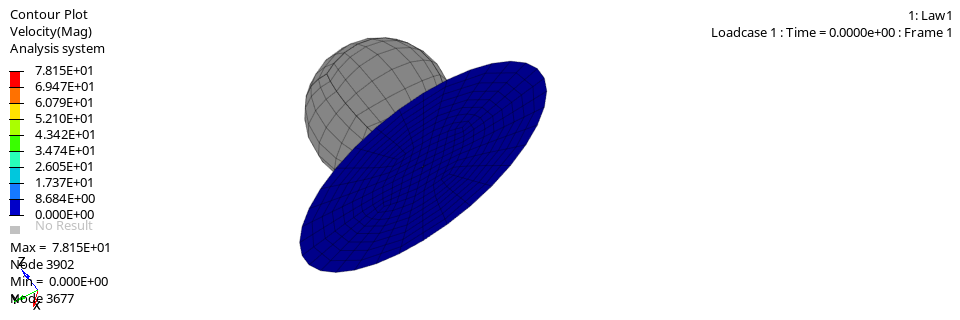
Percentage of thickness reduction
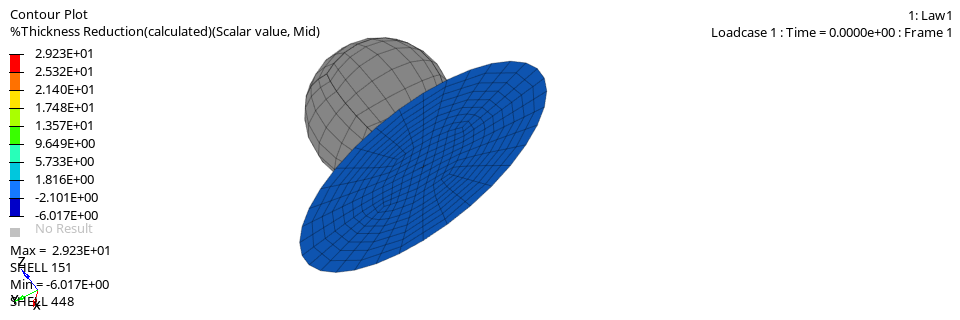
Plastic strain along thickness
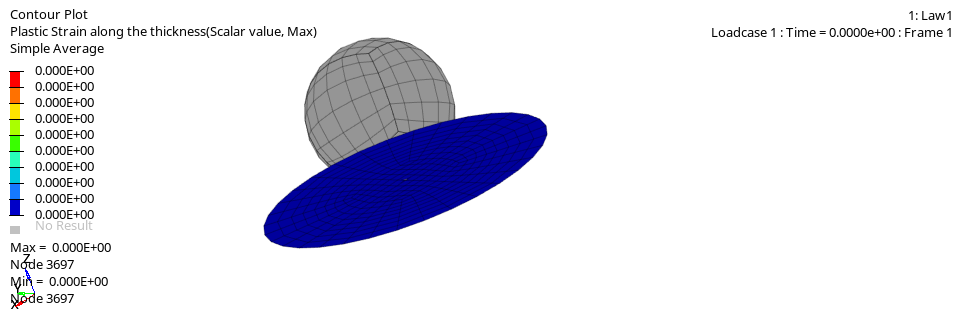
- Now plot the graph for Time v/s energies in hypergraph2d
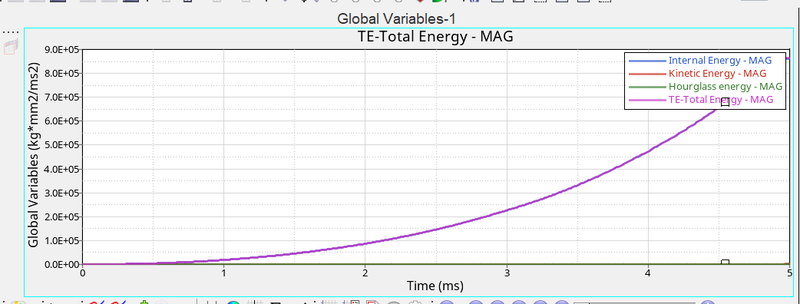
Internal energy => Max=8.625E+05; min=0;
Kinetic energy=>Max=3245.7; min=0.004367;
Hourglass=0(formation of hourglass energy is avoided)
Total energy=> Max=8.625E+05; Min=0.004367;
Case 6(Law_27)
- In this file open the law_27_0000.rad file
- Change the material card to Law_27 like shown below
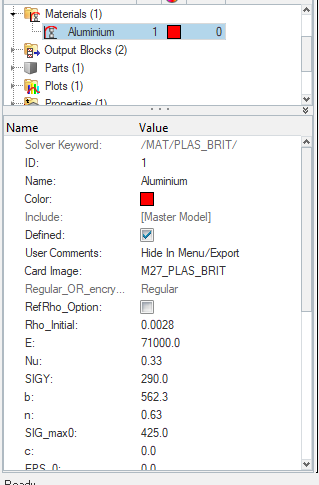
- Edit the Shell property to the recomended shell properties like in previous assignment
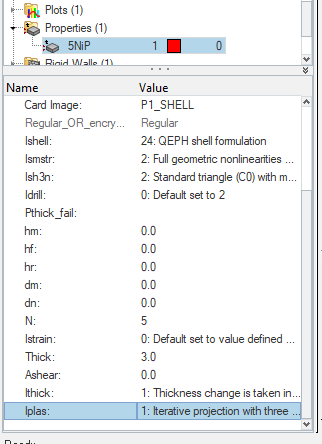
- Now run the file like previous cases, and open the output file
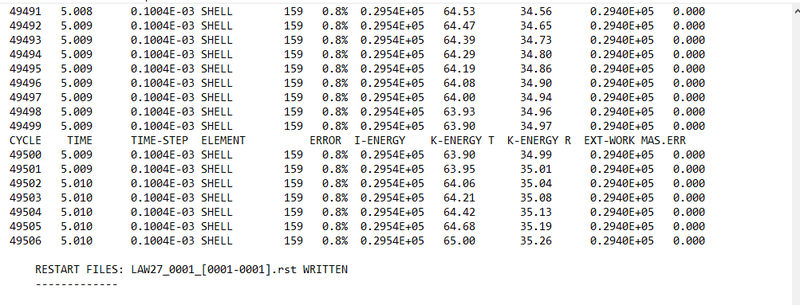
- Simulation time=54.36sec
Total number of cycles=49508
Energy Error=0.8%
Mass Error=0
- Now the energy error generated in this case is acceptable, we can proceed with next step
- Open hyperview to see all the 5 animation
Displacement
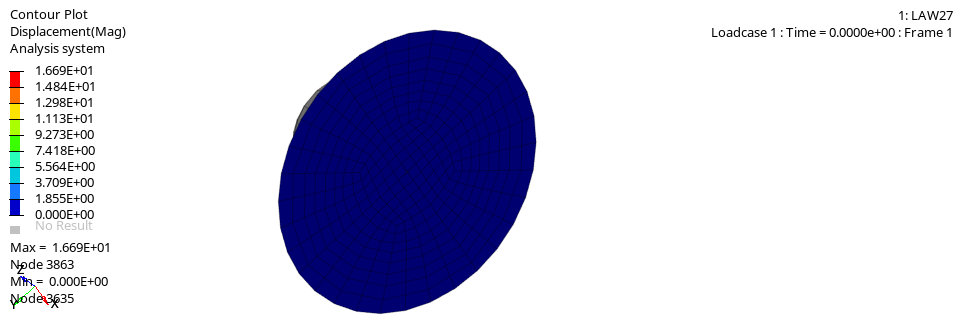
Vonmises
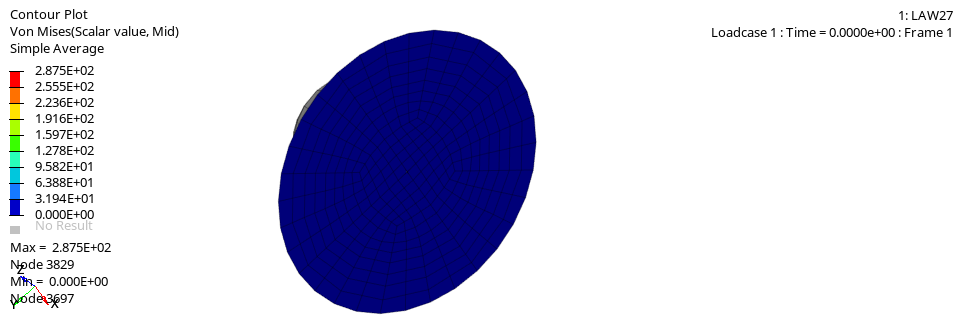
Velocity
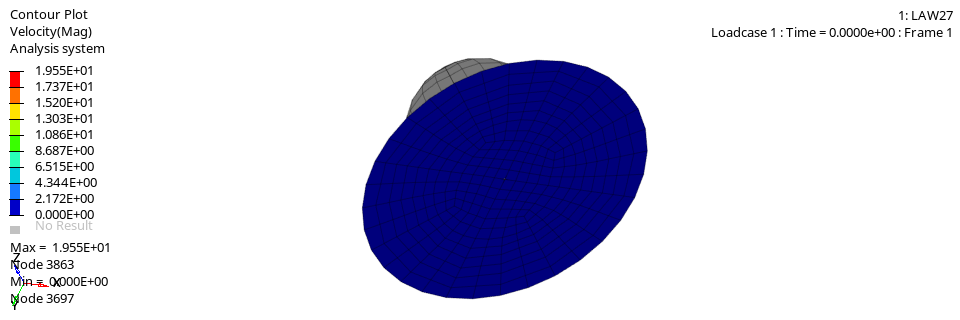
Percentage of thickness reduction
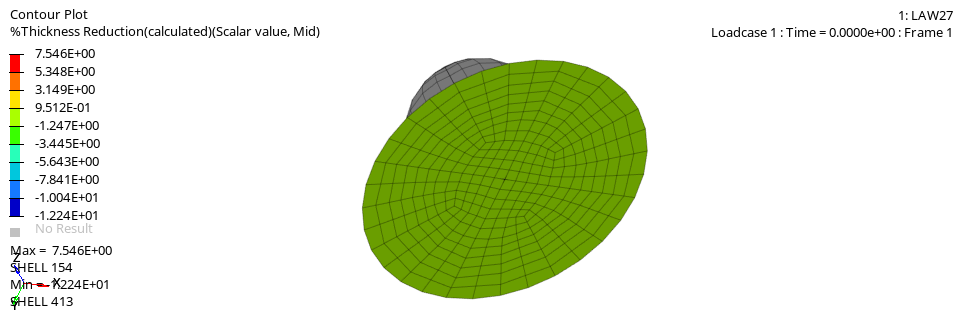
Plastic strain along thickness
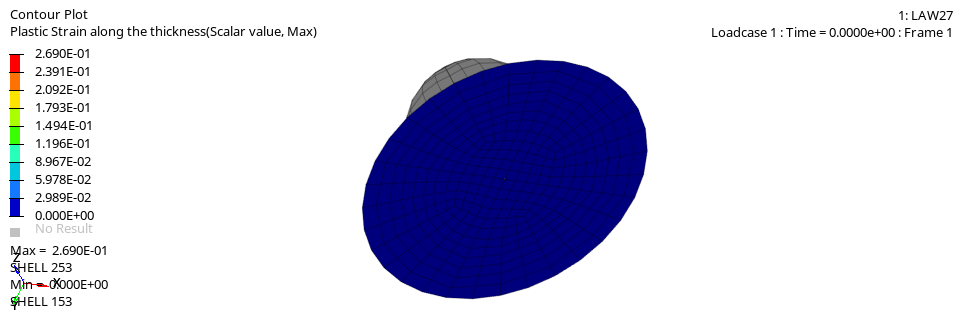
- Now plot the graph for Time v/s energies in hypergraph2d
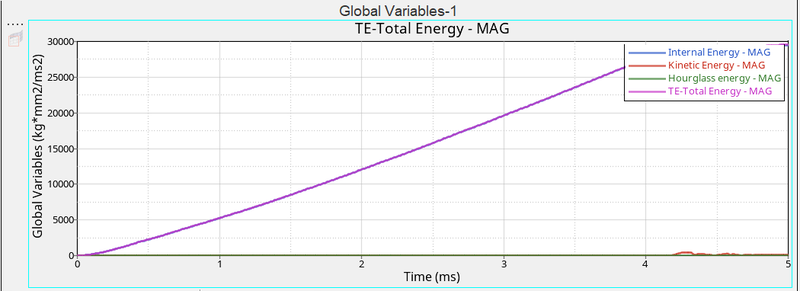
Internal energy => Max=2.9E+04; min=0;
Kinetic energy=>Max=425.88; min=0.004367;
Hourglass=0(formation of hourglass energy is avoided)
Total energy=> Max=2.95E+04; Min=0.004367;
Case 7(Law_36)
- In this case we will be using law 36 material card, use the same properties as shown in slide
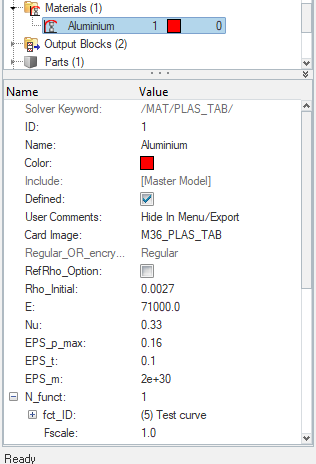
- In this case we should create a new function card with the given x and y values from slide
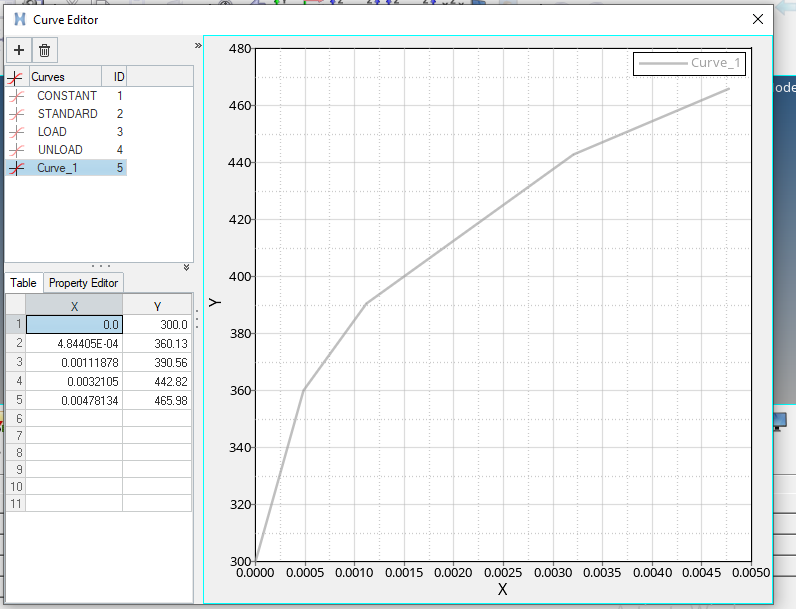
- After creating the test curve , run the radioss file in desired location and repeat the steps from previous cases
- After completing the simulation, open output file we can get to know the results like mentioned below

- Simulation time=60.48sec
Total number of cycles=53157
Energy Error=0.9%
Mass Error=0
- Now the energy error generated in this case is acceptable, we can proceed with next step
- Open hyperview to see all the 5 animation
- Displacement
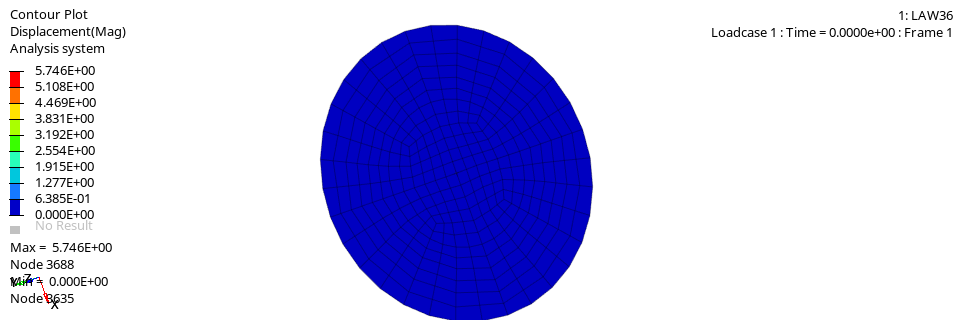
Vonmises
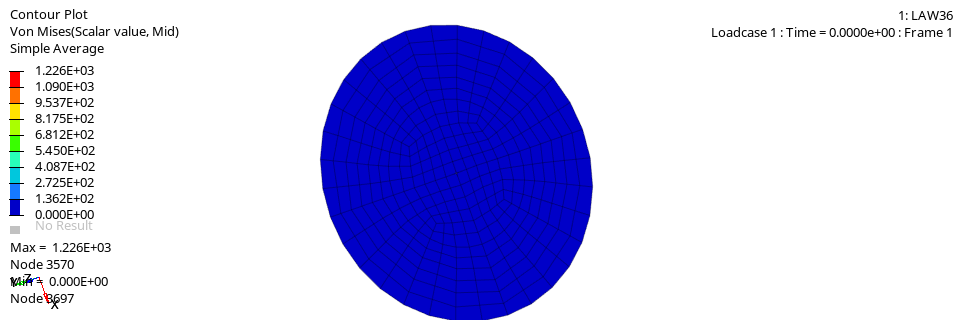
Velocity
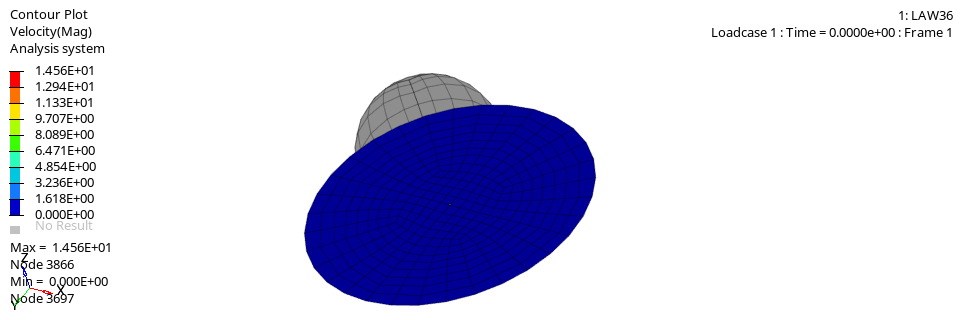
Percentage of thickness reduction
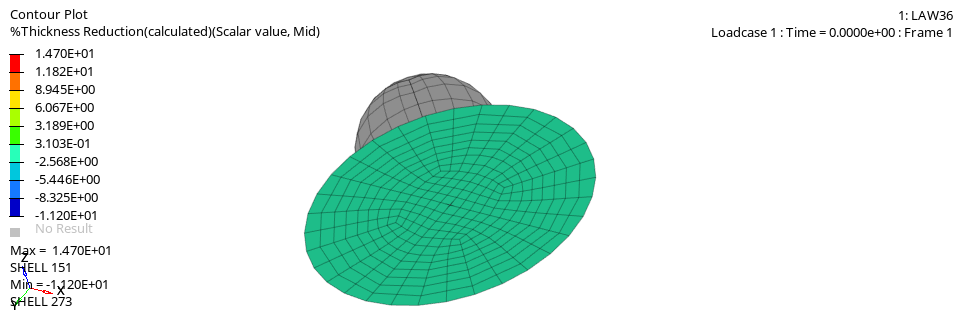
Plastic strain along thickness
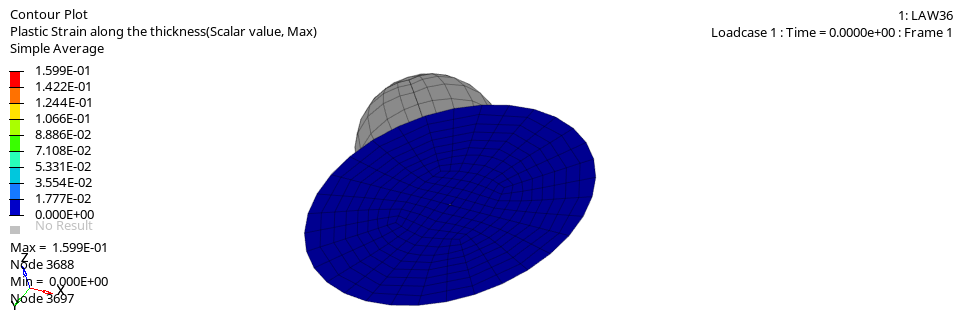
- Now plot the graph for Time v/s energies in hypergraph2d
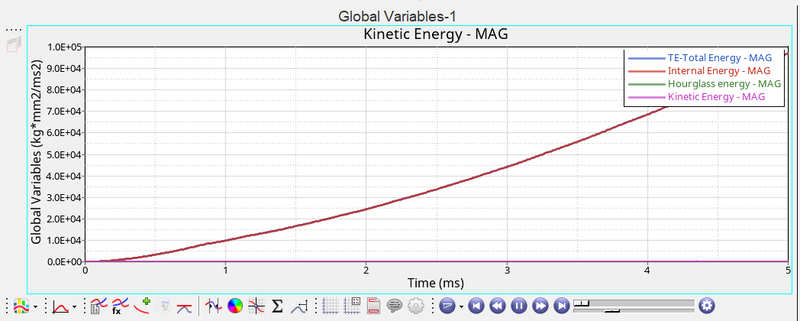
Internal energy => Max=9.6946E+04; min=0;
Kinetic energy=>Max=178.42; min=0.004211;
Hourglass=0(formation of hourglass energy is avoided)
Total energy=> Max=9.6976E+04; Min=0.004211;
CONCLUSION:
-
|
Displacement |
Von mises |
Internal Energy |
Case 1 |
1.58E+01 |
2.752E+02 |
2.7E+04 |
Case 2 |
1.1277E+01 |
2.57E+02 |
3.08E+04 |
Case 3 |
1.932E+01 |
3.1E+02 |
2.74E+04 |
Case 4 |
5.011E+0 |
4.205E+02 |
6.4E+04 |
Case 5 |
4.99E+0 |
1.102E+04 |
8.625E+05 |
Case 6 |
1.699E+01 |
2.875E+02 |
2.9E+04 |
Case 7 |
5.34E+00 |
1.226E+03 |
9.6946E+04 |
- From the above tabulated result, we can see the von mises stress is high in case4, in that case there is no eps_max value,
- since the value is deleted, we can observe the animation there is no crack generated in the model, that causes more amount of stress in the body without crack
- It is important to mention the Eps_max value , so case 4 will not be suitable for real life case.
- We can see there is no hourglass energy is formed because the recomended shell properties are used, like previous assignment
- By the process we come to know that , even if the materials are same, one single parameter can make big diffrence
- It is important to know the suitable properties for each cases