What is meant by Turbocharger??
- A turbocharger, (or turbo), is a turbine-driven forced induction device that increases an internal combustion engine’s efficiency and power output by forcing extra air into the combustion chamber.
- This improvement over a naturally aspirated engine’s power output is due to the fact that the compressor can force more air—and proportionately more fuel—into the combustion chamber than atmospheric pressure alone.
- In naturally aspirated piston engines, intake gases are “pushed” into the engine by atmospheric pressure filling the volumetric void caused by the downward stroke of the piston (which creates a low-pressure area), similar to how liquid is drawn up into a syringe.
- The objective of a turbocharger is to improve an engine’s efficiency by increasing the density of the intake gas (usually air), thereby allowing more power per engine cycle.
- The turbocharger’s compressor draws in ambient air and compresses it before it enters into the intake manifold at increased pressure. This results in a greater mass of air entering the cylinders on each intake stroke. The power needed to spin the centrifugal compressor is derived from the kinetic energy of the engine’s exhaust gases.
- A turbocharger may also be used to increase fuel efficiency without increasing power. This is achieved by recovering waste energy in the exhaust and feeding it back into the engine intake. By using this otherwise wasted energy to increase the mass of air, it becomes easier to ensure that all fuel is burned before being vented at the start of the exhaust stage.
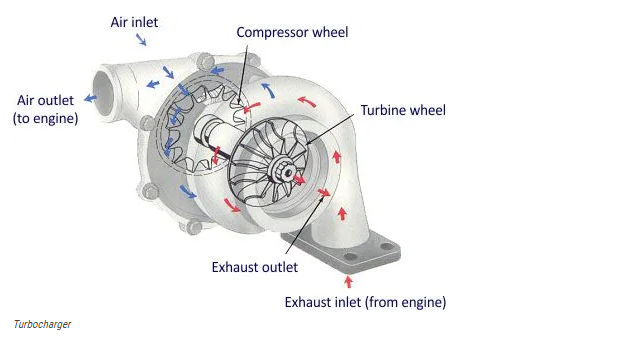
Turbocharger Working:

- The turbine powers the compressor as they both are mounted on the same shaft.
- The compressor sucks in air from the atmosphere and compresses it and forces the compressed air into the engine.
- One end of the turbo’s air inlet is connected to the air filter that takes in the air.
- So, this air passes through the compressor and voila! turbo compresses the atmospheric air. (on an average, a turbocharged engine from a factory compresses the air by up to 4-5psi).
- This is where the atmospheric air experience a rise in the temperature due to compression and exhaust gas temperature.
- The air now passes through an intercooler to cool the air down. Well, hot air may lead to pre-ignition or knocking in the engine.
- From the intercooler, the air now enters the intake manifold and then into the engine.
- As the fuel is injected combustion takes place in the power stroke.
- And next during the exhaust stroke, the exhaust gasses force the turbine to spin and the cycle repeats again.
There are a number of different types of turbocharger used within the automotive industry:
- Single- Turbo
- Twin-Turbo
- Twin-Scroll Turbo
- Variable Geometry Turbo
- Variable Twin Scroll Turbo
- Electric Turbo
Single- Turbo:
- Single turbochargers are what most people think of as turbos. By differing the size of the elements within the turbo, completely different torque characteristics can be achieved. Large turbos provide higher levels of top end power, whilst smaller turbos can spool faster and provide better low-end power. They are a cost-effective way of increasing engine power and efficiency, and as such have become increasingly popular, allowing smaller engines to increase efficiency by producing the same power as larger naturally-aspirated engines, but with a lower weight. They do however tend to work best within a narrow RPM range, and drivers will often experience ‘turbo-lag’ until the turbo starts to operate within its peak rev band.
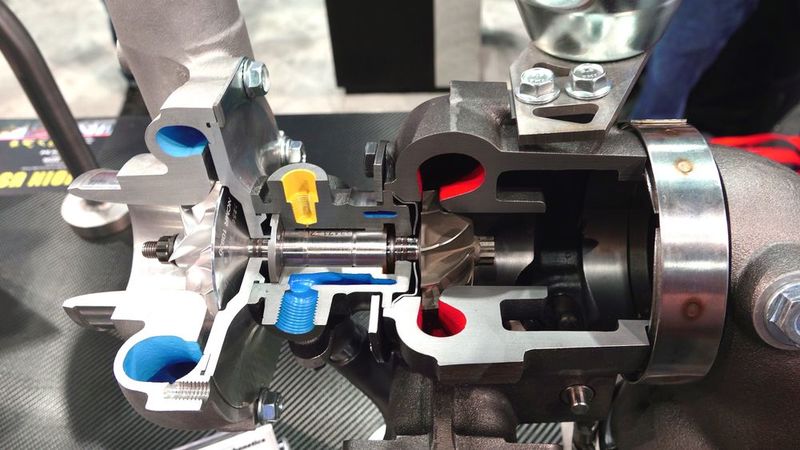
Twin-Turbo:
- As the name implies twin-turbos mean adding a second turbocharger to an engine. In the case of V6 or V8 engines, this can be done by assigning a single turbo to work with each cylinder bank. Alternatively, one smaller turbo could be used at low RPMs with a larger turbo for higher RPMs. This second configuration (known as twin sequential turbocharging) allows for a wider operating RPM range, and provides better torque at low revs (reducing turbo lag), but also gives power at high RPMs. Unsurprisingly, having two turbos, significantly increases the complexity and associated costs.
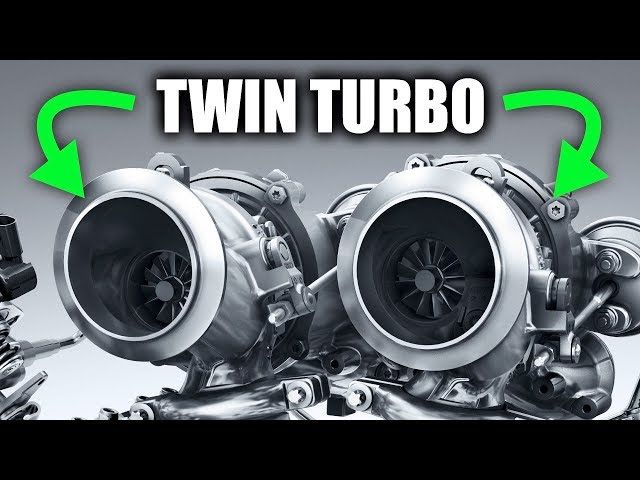

Twin-Scroll Turbo:
- Twin-scroll turbochargers require a divided-inlet turbine housing and exhaust manifold that pairs the correct engine cylinders with each scroll. independently. For example, in a four-cylinder engine (with a firing order 1-3-4-2), cylinders 1 and 4 might feed to one scroll of the turbo, while cylinders 2 and 3 feed to a separate scroll. This layout provides more efficient delivery of exhaust gas energy to the turbo, and results and helps provide denser, purer air into each cylinder. More energy is sent to the exhaust turbine, meaning more power. Again, there is a cost penalty for addressing the complexity of a system requiring complicated turbine housings, exhaust manifolds and turbos.
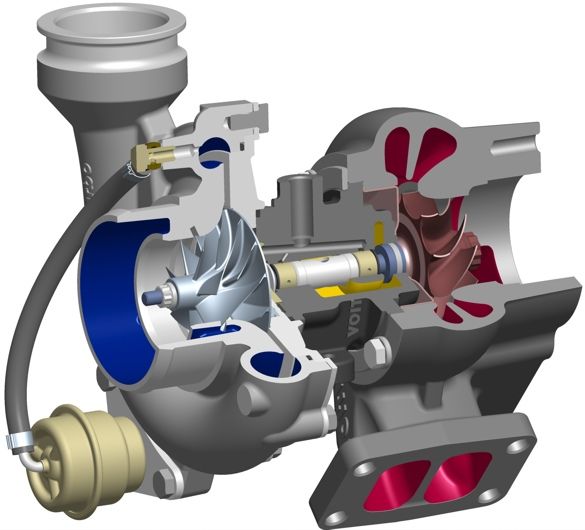
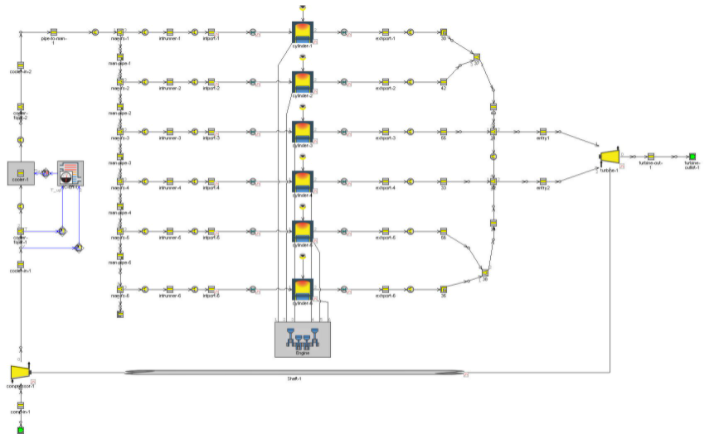
Variable Geometry Turbo:
- Typically, VGTs include a ring of aerodynamically-shaped vanes in the turbine housing at the turbine inlet. In turbos for passenger cars and light commercial vehicles, these vanes rotate to vary the gas swirl angle and the cross-sectional area. These internal vanes alter the turbos area-to-radius (A/R) ratio to match the engines RPM, and so give peak performance. At low RPM, a low A/R ratio allows the turbo to quickly spool up by increasing exhaust gas velocity and. At higher revs the A/R ratio increases, ther4eby allowing increased airflow. This results in a low boost threshold reducing turbo lag, and provides a wide and smooth torque band.
- Whilst VGTs are more typically used in diesel engines where exhaust gases are lower temperature, until now VGTs have been limited in petrol engine applications due to their cost and the requirement for components to be made from exotic materials. The high temperature of the exhaust gases means that the vanes must be made from exotic heat-resistant materials to prevent damage. This has restricted their use to applications within luxury, high performance engines.
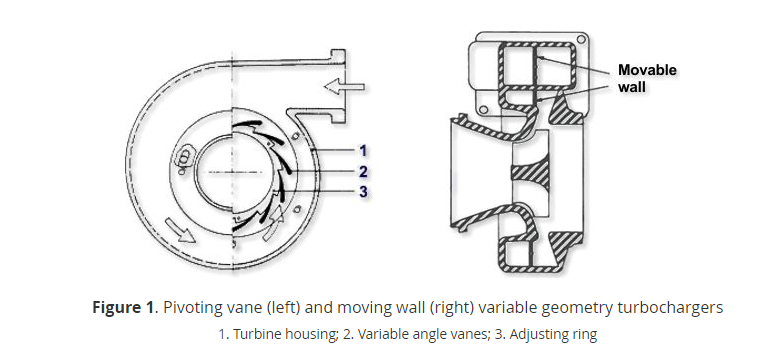
_1619675617.gif)
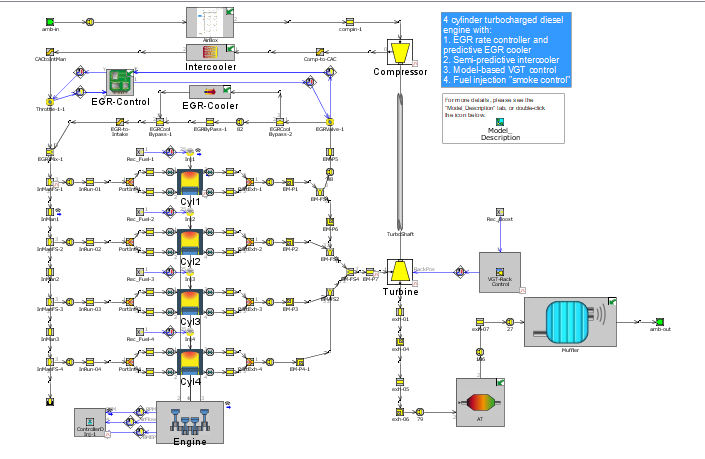
Variable Twin Scroll Turbo:
- As the name suggests a VTS turbocharger combines the advantages of a twin-scroll turbo and a variable geometry turbo. It does this by the use of a valve which can redirect the exhaust airflow to just a single scroll, or by varying the amount the valve opens can allow for the exhaust gases to split to both scrolls. The VTS turbocharger design provides a cheaper and more robust alternative to VGT turbos, meaning it is a viable option for petrol engine applications
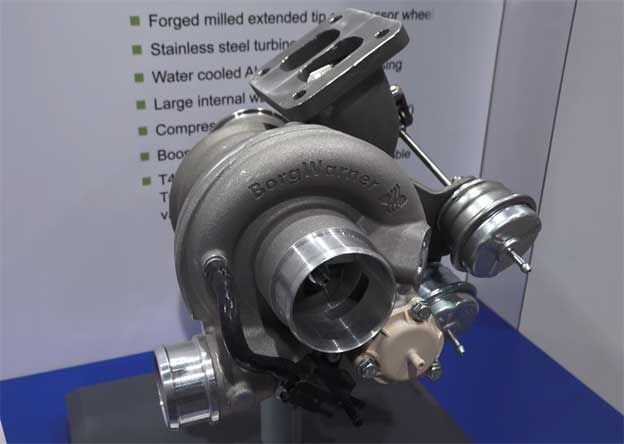
Electric Turbochargers:
- An electric turbocharger is used to eliminate turbo lag and assist a normal turbocharger at lower engine speeds where a conventional turbo is not most efficient. This is achieved by adding an electric motor that spins up the turbo’s compressor from start and through the lower revs, until the power from the exhaust volume is high enough to work the turbocharger. This approach makes turbo lag a thing of the past, and significantly increases the RPM band within which the turbo will efficiently operate. So far, so good. It appears that electronic turbos are the answer to all the negative characteristics of conventional turbochargers, however there are some disadvantages. Most are around cost and complexity, as the electric motor must be accommodated and powered, plus also cooled to prevent reliability issues.
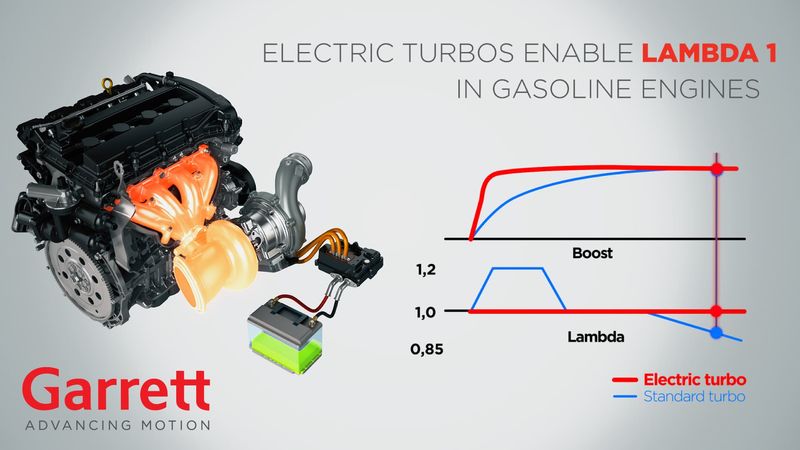
Waste Gate Turbocharger:
- A waste gateis a valve that controls the flow of exhaust gases to the turbine wheel in a turbocharged engine system
- Diversion of exhaust gases regulates the turbine speed, which in turn regulates the rotating speed of the compressor. The primary function of the wastegate is to regulate the maximum boost pressure in turbocharger systems, to protect the engine and the turbocharger. One advantage of installing a remote mount wastegate to a free-float (or non-WG) turbo includes allowance for a smaller A/R turbine housing, resulting in less lag time before the turbo begins to spool and create boost
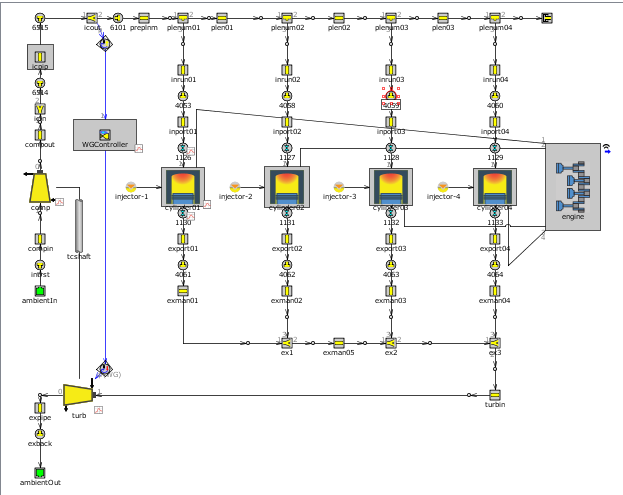
Tutorial-6:
- This model consists of 6 cylinders with the implementation of Turbo Charger i.e. 2 inlets to the turbo as we see in the form of two end environments at the right side and compressor outlet at the bottom in the form of end environment. Generally, Twin Turbine inlets are used with more than 3 cylinders. In this case, we have 6 cylinders where 3 outlets of cylinders share on the turbine inlet. We were able to combine the outlets of different cylinders with the help of Flow Split Template. Here, as there is no physical shaft connecting the turbine and compressor, we directly input the outlet pressure (Absolute) values for the turbine as well as compressor. Here the inputs for the turbine and compressor are absolute pressure, temperature and composition of air.
- In the below image we can see the 6 Cylinder engine
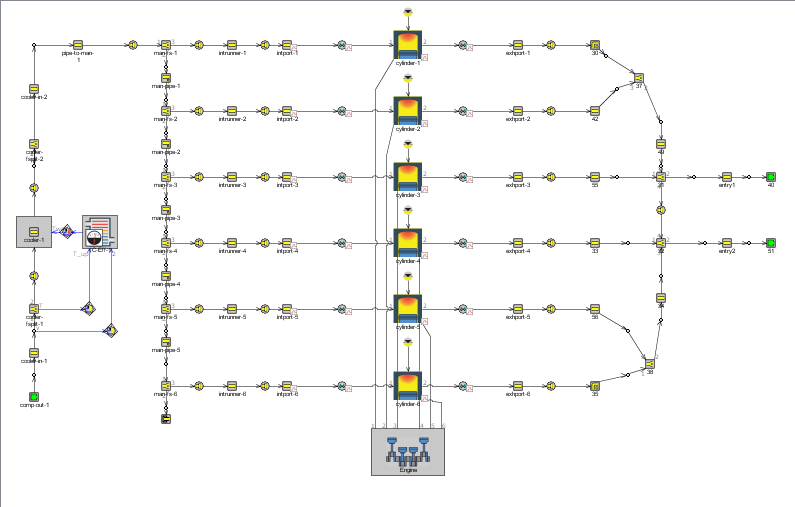
Tutorial-7:
- In this model again we have 6 cylinders’ diesel engine with the two inlets to the turbocharger which is a collection from 6 cylinders splitting into 2 inlets. This model is conceptually same as the above model in tutorial no. 6 with actual turbocharger setup implemented here, where the turbine is connected with the compressor impeller with the rotating shaft as seen in the image below. Here for the turbine and compressor inputs, we have a turbine map and compressor map which is a contour plot of Pressure ratio v/s Mass flow rate. This turbine and compressor map data consists of parameters like Rotational speed, Mass flow rate, Pressure Ratio and efficiency.
- In the below image we can see the 6 Dual twin Turbocharger Cylinder engine
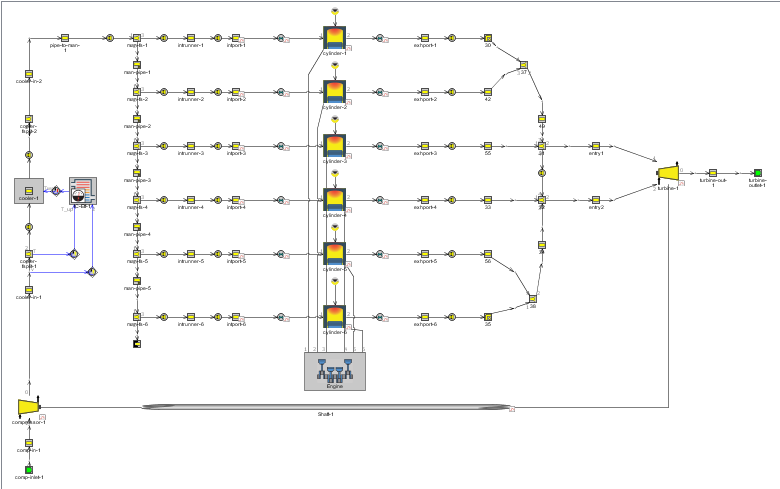
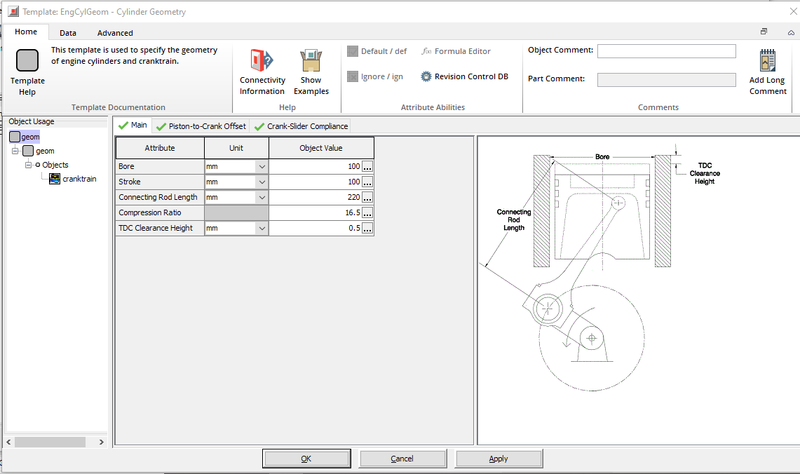
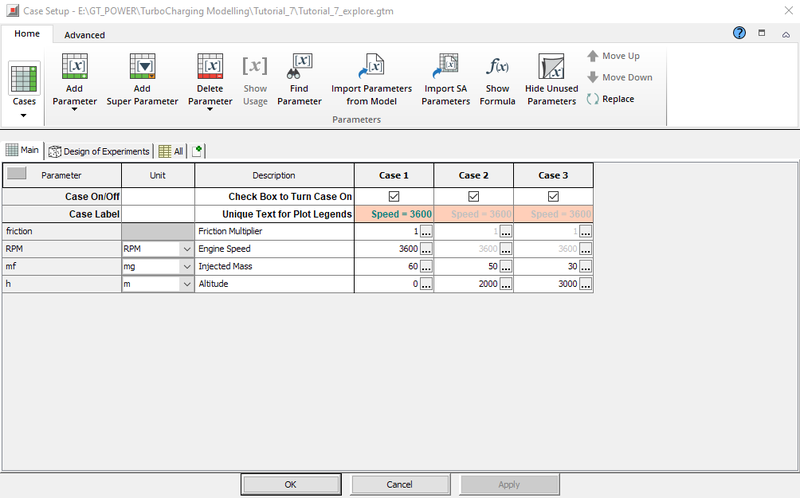
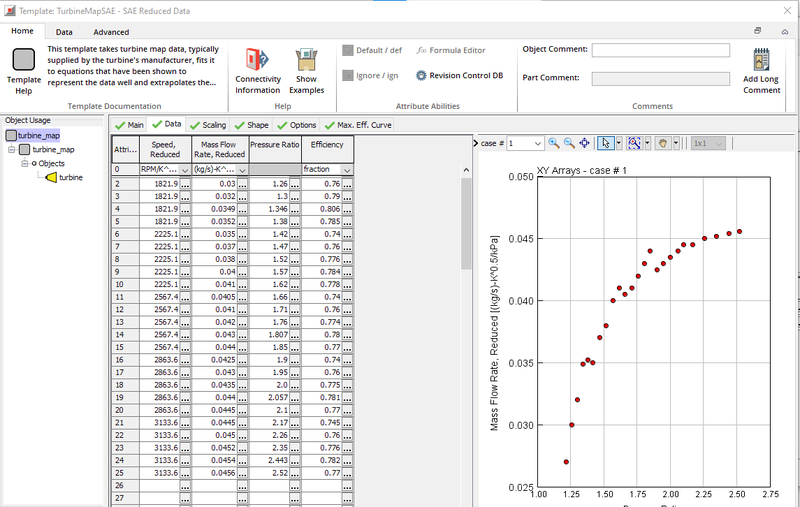
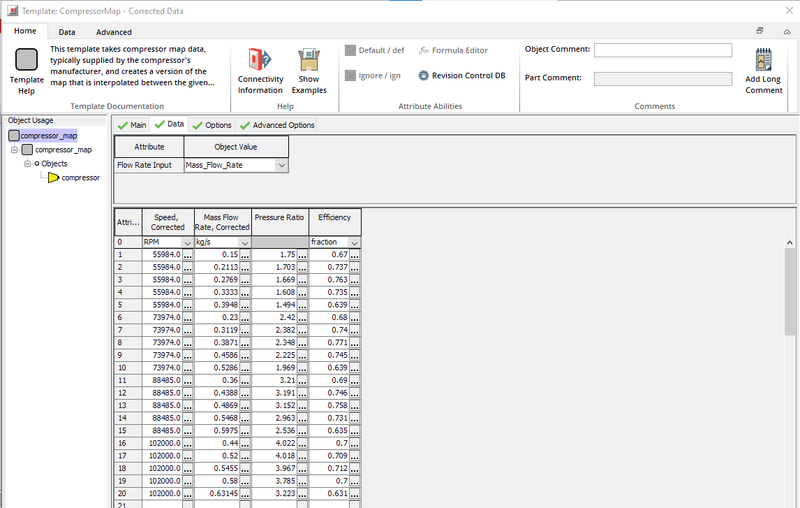
Understanding Compressor Maps- Sizing A Turbocharger:
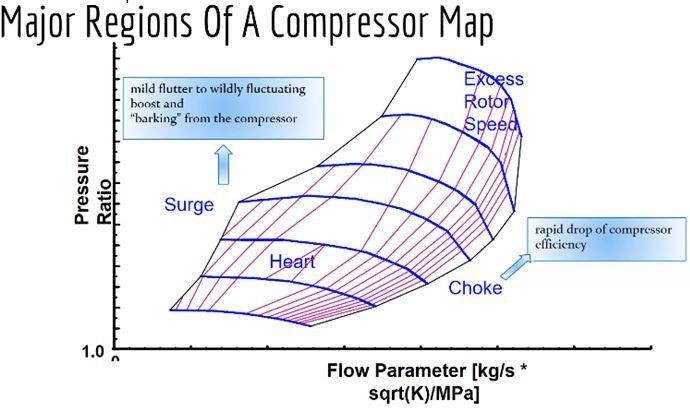
Horizontal Axis:
- The bottom axis represents the corrected mass flow. This is how much air the turbocharger flows per unit of time. This could be rated in Kilograms per second or pounds per minute
Vertical Axis:
- The vertical axis represents the pressure ratio of the compressor. It is calculated by taking the absolute outlet pressure and dividing by the absolute inlet pressure. (Note, most gauges read in gauge pressure i.e. zero psi at atmospheric when it is actually around 14.7 or so psi.) Due to how this is calculated, there are no units associated with this axis. “Pressure ratio is how much pressure the compressor stage will generate at a given speed relative to atmospheric pressure along with inlet conditions (filter restrictions). Pressure ratio is used instead of boost because atmospheric pressure changes with altitude and weather conditions” explains Temple.
The Data:
- If you are familiar with a topographical map, then the data may look familiar. If you aren’t, each ring represents a specific level or in this case efficiency. As the efficiency increases, the rings get smaller and smaller.
- Within the turbocharger industry, these rings are called efficiency islands. The efficiency of a turbocharger is measured by its ability to compress the air without adding excessive heat. The higher the efficiency, the cooler the outlet temperature for a given boost pressure (it will still be above ambient temperature).
Left Hand Boundary:
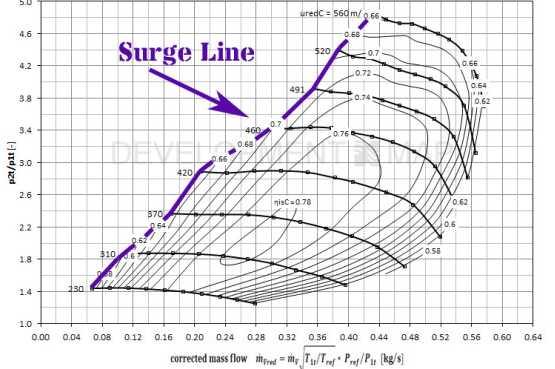
- The surge line of a compressor map is the left hand boundary. This line represents the maximum amount of pressure the turbocharger can produce while flowing the least amount of mass (air).
- Surge can occur in a couple of different ways. The most common and more obvious occurs when the throttle is lifted while under boost which results in an audible chirping/coughing sound. As the throttle is lifted while under load, the pressure that is built up in the piping system needs to be discharged.
- “This is taken into consideration on OE applications and the appropriate turbo is sized for the power rating and surge margin. This type of surge is more severe on engines equipped with a post turbo throttle body. Throttle bodies are mostly used on gasoline applications, but with newer emissions standards, more diesel engine manufacturers are using them as part of their emission control strategy. On throttle body equipped engines, when the throttle plate physically closes the pressure must be released and unfortunately, the only place it has to go is back through the compressor inlet creating an instability in pressure and flow”.
- This is why many OE manufacturers integrate a compressor recirculation valve within their system in effort to avoid this condition. This is also what drove the need for aftermarket external blowoff valves. These help discharge the pressure that is built up within the piping system allowing the turbo speed to decrease at a more gradual rate, which helps extend the turbo life.”
Right Hand Boundary:
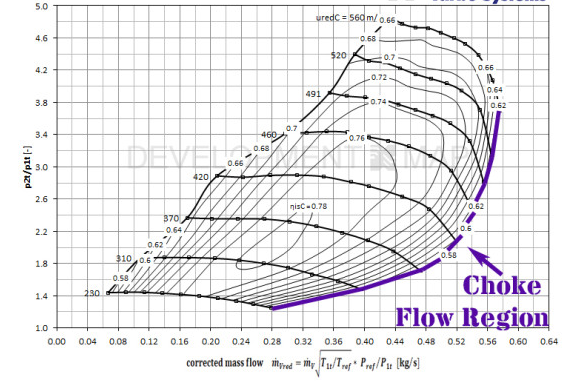
- The opposite of surge is choke. Choke is basically the maximum amount of air that the compressor side can flow at a given pressure ratio.
- “When a compressor begins to run into the choke region of the map, the compressor outlet temperatures will rapidly increase, as will shaft speed. This occurs when you have reached the maximum flow limit of the turbo. Typically, a turbocharger is sized to give sufficient surge margin, while also keeping the operational points on the compressor map at areas above 65-percent,” explained Rufini.
Speed Lines:
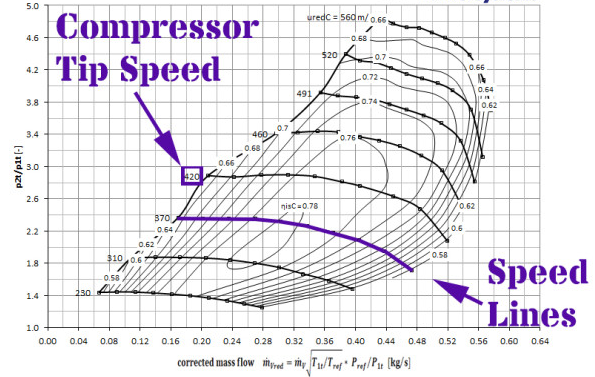
- Speed lines are the last additional bit of information contained within the compressor map. The speed lines run from left to right across the efficiency islands and represent a specific speed of the compressor. These speed lines are typically measured and identified in meters per second, feet per minute, or rotational speed.
Operating points on compressor and turbine maps:
Turbine_Plots:
Efficiency Vs Pressure Ratio Vs Reduced Speed

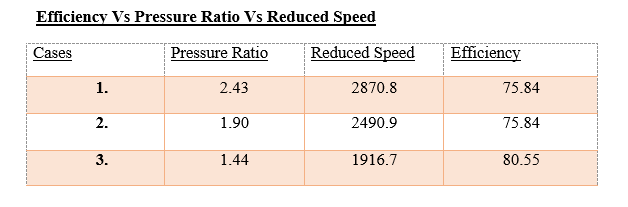
Reduced Mass Flow Rate Vs Pressure Vs Efficiency
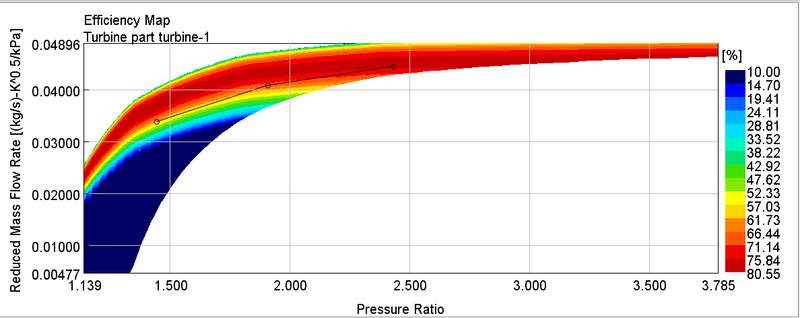
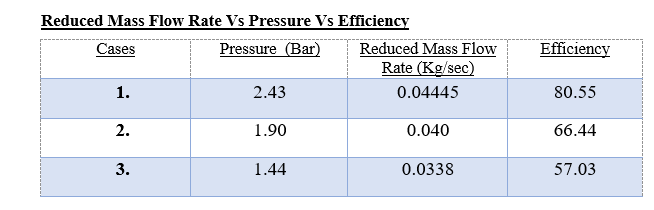
- Above is the Efficiency map for a turbine with Mass flow rate v/s pressure ratio. For the 1st case, we get a pressure ratio of 2.43 for the mass flow rate of 0.045kg/s.
- For 2nd case, we get a pressure ratio of 1.9 for the mass flow rate of 0.040kg/s and for the 3rd case, we get a pressure ratio of 1.44 for the mass flow rate of 0.0338kg/s. Here the mass flow rate remains the same but the pressure ratio decreases for 3600 RPM. From the contour plot, we may conclude that the turbine efficiency achieved falls in the maximum zone i.e. 80.55%.
Compressor Plots:
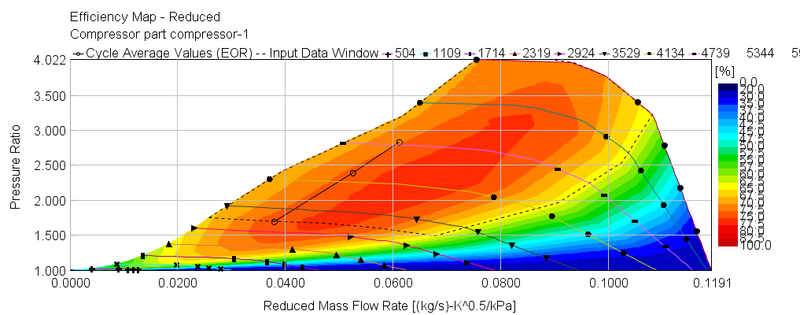
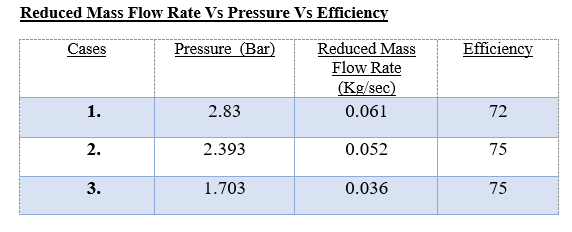
- The above compressor map is pressure ratio vs Reduced Mass flow rate. The graph has efficiency like structure represented in colour bands and black lines as RPM of the compressor.
- Speed achieved by compressor which turbine also operates as both are coupled is around 5156 RPM .
- Surge line is the operating threshold for turbo i.e. to the left boundary of the dome, operating beyond this boundary leads to fluttering vibrations.
- Choke line is the maximum operating condition for turbo i.e. to the right boundary of the dome causing to damage it and wear out faster. Also from the graph we can see that compressor operates at near to 72-75 % Efficiency.


Corrected Mass Flow Rate Vs Pressure Vs Speed


Corrected Mass Flow Rate Vs Pressure Vs Efficiency


- The above compressor map is pressure ratio vs Corrected Mass flow rate. The graph has efficiency like structure represented in colour bands and black lines as RPM of the compressor.
- Speed achieved by compressor which turbine also operates as both are coupled is around 88400 RPM .
- Surge line is the operating threshold for turbo i.e. to the left boundary of the dome, operating beyond this boundary leads to fluttering vibrations.
- Choke line is the maximum operating condition for turbo i.e. to the right boundary of the dome causing to damage it and wear out faster. Also from the graph we can see that compressor operates at near to 72-75 % Efficiency.
In which application Variable Geometry Turbine is beneficial?
- VGTs tend to be much more common on diesel engines, as lower exhaust temperatures mean they are less prone to failure. Early gasoline-engine VGTs required significant pre-Charge Cooling to extend the turbocharger life to reasonable levels, but advances in technology have improved their resistance to high-temperature gasoline exhaust, and they have started to appear increasingly in gasoline-engined cars
- Typically, VGTs are only found in OEM applications due to the level of coordination required to keep the vanes in the most optimal position for whatever state the engine is in. However, there are aftermarket VGT control units available, and some high-end aftermarket engine management systems can control VGTs as well.
- VGT devices are designed to increase boost pressure at low speeds, reduce response times, increase available torque, decrease the boost at high engine speeds to prevent over-boosting, reduce engine emissions, improve fuel economyand increase the overall turbocharger operating range
- This design is mostly limited to small engines and light-duty applications (passenger cars, race cars and light commercial vehicles).
Diesel VGT EGR:
- The variable geometry turbine allows significant flexibility over the pressure ratio across the turbine. In diesel engines, this flexibility can be used for improving low speed torque characteristics, reducing turbocharger lag and driving EGR flow.
- Variable geometry turbochargersare designed to: increase intake air boost pressure at low engine speed. improve the response time of the turbocharger during transient engine operation phases. increase the availability of the maximum engine torque.
- Engine downsizing through turbocharging is a proven method of improving fuel economy by using a smaller engine operating at higher levels of specific engine load and higher efficiency. Turbocharging is more challenging for the gasoline engine than the diesel engine due to the higher variability in the flow rate of air and the higher exhaust gas temperature. Although the variable geometry turbine offers the potential for improving the low-end torque, lowering part-load fuel consumption and delivering a fast transient response on a downsized gasoline engine, the cost, durability and the limited allowable turbine inlet temperature on the currently available devices present challenges to widespread application
- The Diesel VGT EGR model is shown below:
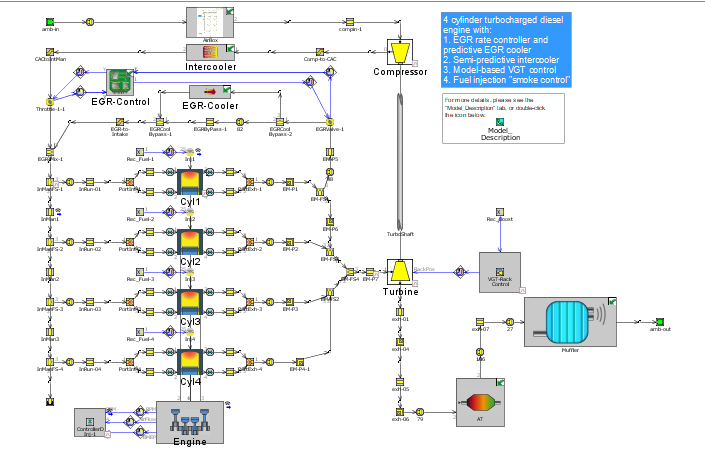
Working of a Diesel VGT EGR:
- This is a 4 cylinder and 16 valve engine with EGR cooler and VGT.
- The ambient air is sucked through the inlet and then the air is passed through the air filters where dirty air and dust particles can be purified and pure air passed into the compressor from compressor the compressed air is passes through the Intercooler.
- In the intercooler the temperature of the air is decreases and increases in the density of the air and thus we will have higher airflow rate than the flow rate of the Ambient air.
- The air from Intercooler passed through the throttle valve where air is passed through this if the throttle valve open means the drive inputs is 90 and if the throttle valve Close means the drive inputs is 0.
- From the throttle valve the air is passed through the two inlet ports into cylinder where combustion takes places during the Power stroke.
- During the exhaust Stroke the exhaust gases and air passes through the exhaust manifold from the exhaust manifold some of the air went to the turbine and some of air went through the Exhaust Gas Recirculation (EGR) in order to reduce the emissions of the NoX.
- The turbine and Compressor are connected to the single shaft from the turbine the air is passed through the wall flow filter (where the diesel and Gasoline particles filters) from there it passes through the Muffler and gases went into atmosphere through it.
The Engine:
- The engine is a 4-cylinder, four-stroke, direct injection, 2L diesel engine. The engine runs in "speed" mode, where the engine speed is entered by the user and the engine torque is calculated.
- Combustion is modeled by the DI Pulse method, a predictive combustion model using the detailed injection profiles. In-cylinder heat transfer is modeled using the Woschni model. A FE model is used to predict the cylinder, head and piston temperatures. This simulation will run until it reaches steady-state convergence for six different engine speeds at full load, three part load operating points, and an additional idle point (total of 10 cases).
The Intake System:
- The intake system consists of the air piping upstream of the compressor inlet, and contains a simple model of an air box. The air box is modeled as a group of interconnected flow splits that represent the total volume of the air box. At the inlet and outlet of the air box, "bell mouth" orifice connections are used to model smooth transitions.
The Intercooler:
- The intercooler is found downstream of the compressor outlet. This intercooler is an air-to-air intercooler that is modeled using a "semi-predictive" method based on heat exchanger effectiveness.
- Note that if heat exchanger performance data is available, it is generally preferred to model the heat exchanger using 'Hx Master' and 'Hx Slave' parts (which will use the available data to create non-dimensional Nusselt correlations defining heat exchanger performance). This approach will generally extrapolate better than an assumed effectiveness to conditions beyond those present in the heat exchanger data. However, if heat exchanger data is not available (or if the simulation will be run at conditions where HX effectiveness is well known), the semi-predictive effectiveness method is appropriate
The Intake Manifold:
- The intake manifold is modeled as aluminium using heat conduction objects to calculate the wall temperatures. This is important in turbocharged models since wall temperatures may change substantially at different operating points, thus influencing the cylinder inlet temperature. The orifices that connect. The initial conditions are different from ambient conditions. The initial temperatures and pressures are specified at the expected boost pressure in order to decrease the convergence time.
The Fuel Injection System:
- The fuel is injected directly into the cylinders. Both the injection timing and the injection profile are looked up using an RLT Dependence' as a function of engine speed and injection rate. There is a simple control system that determines the total injected fuel mass (mg/stroke). This control system begins with a 'Signal Generator' part that imposes an accelerator pedal position input. The "requested fuel mass" is then looked up as a function of engine speed and pedal position. In some cases, the requested fuel mass may produce excess smoke if the boost pressure is not high enough to provide enough air. Therefore, the maximum allowed fuel mass is looked up as a function of the engine speed and the boost pressure. A 'Min Max' part is used to take the smaller of the requested fuel mass and the smoke limited fuel mass. This value is then imposed on the injectors using an actuator.
The Exhaust System:
- The Exhaust manifold is modelled as Cast iron using heat conduction objects to calculate the wall temperatures. This is very important in the exhaust manifold since wall temperatures change substantially between full load and idle condition, thus influencing the turbine inlet temperatures and turbine power. The orifices that connect the exhaust ports to the runners do not allow heat to be conducted between the pipe walls of the adjacent parts. This is necessary because the wall temperature is calculated in the exhaust pipes, while it has been imposed in the port (the imposed value is artificially high to account for heat transfer from the valve). The initial conditions are different from ambient conditions. The initial temperatures and pressures are specified at the expected backpressure in order to decrease the convergence time. The turbine part references a map file from which map data is read.
The EGR System:
- The model includes an exhaust gas recirculation (EGR) system to transport exhaust gases from the exhaust manifold back to the intake manifold. The EGR flow is driven by a positive pressure difference between the exhaust manifold and intake manifold and is controlled by an orifice connection (EGR-valve). The EGR-valve diameter is imposed by an actuator, and is determined automatically by an 'Controller EGR Valve' part to achieve a target EGR fraction. The desired EGR fraction is mapped as a function of engine speed and the requested BMEP. EGR rates in the model are as high as 40% at some operating points. Because of the high EGR rates, it is desirable to cool the EGR gases using a heat exchanger (EGR-cooler). When the pressure drop across the EGR system is not sufficient to achieve the target EGR rate, a throttle in the intake system, controlled by a PID controller, increases the pressure difference. This controller is only active, if the EGR-valve is fully open.
The EGR cooler is modeled using 'HxMaster' and HxSlave' parts. Coolant side boundary conditions are imposed. The heat exchanger model inputs include geometry along with measured heat transfer and pressure drop performance data. During model pre-processing, the measured data is used to generate non-dimensional correlations for heat transfer that allow the model to accurately predict heat transfer rates at any operating condition. The pressure drop data is use to automatically calibrate physical characteristics (friction multiplier, orifice Cd) of the heat exchanger so that the data is well matched.
The Turbocharger and Boost Controller:
- The turbocharger in this model contains a fixed geometry compressor and a variable geometry turbine (VGT). For the VGT, there are 5 different sets of turbine map data entered at each of 5 VGT rack positions. The VGT rack position is determined by a control system to achieve a target boost pressure upstream of the intake manifold. The boost pressure is sensed and is then filtered using a Moving Average' part to produce an average pressure signal. The model based controller compares the sensed boost pressure to the target boost pressure and then adjusts the VGT rack position accordingly.
The Exhaust System:
- A full vehicle exhaust system is modeled downstream of the turbine outlet. The geometry of a Diesel Oxidation Catalyst (DOC) is modeled using a 'CatalystBricR part. In this example only the pressure drop across the DOC is of interest, so no chemical reactions are modeled in the DOC. The inlet and outlet of the DOC must be modeled using flow splits because the DOC is effectively a bundle of very small pipes.
Just downstream of the DOC is a Diesel Particulate Filter (DPF) using a 'DieselParticFilter' part. In this example, only the geometry attributes are specified so that proper pressure drop across the filter is modeled, but there is no soot accumulation or regeneration modeled. Similar to the DOC, the inlet and outlet of the DPF must be modeled using flow splits.
Downstream of the DOC is a muffler. This muffler was modeled using GEM3D, which enables complex muffler geometry to be entered in a CAD tool and automatically discretized into a GT-POWER model. The muffler in this example is a tri-flow type muffler with two baffles. The center chamber between the two baffles is filled with wool, and various internal pipes and baffles include perforation. The .gem file is included in the directory and can be opened in GEM3D to see the muffler. The output of the GEM discretization is stored within an internal subassembly to keep the main project map clean.