2D Meshing for Car Hood [SheetMetal Component]
Aim -
- To do a Pre-Processing on a given hood model using ANSA Software [Version 19.1.4].
Objective -
- To check the geometrical errors on the hood model.
- To extract a mid surface on the components such as Inner Extract,Outer Extract,Latch Reinforcement Extract and two Hinge Reinforcement Extracts.
- To generate 2D mesh on the components based upon the quality criteria given in the question.
- Assigning thickness to the respective components.
Theoretical Framework -
- ANSA [Automatic Net Generation for Structural Analysis] is a Pre-Processing Software.Pre-Processing comes under CAE.
- ANSA is a Pre-Processing tool which used for FEA and CFD in industries.
- ANSA is mostly used for CFD Meshing.
What is CAE ?
- Computer Aided Engineering is a stansard procedure in entire product engineering and development process from design and virtual testing with sophisticated analytical algorithms during product cycle.
- It supports the engineering process,allows to perform tests and simulations of the products physical properties without needing a physical prototype.
- There are three stages in CAE called Pre-Processing,Solving,Post-Processing.
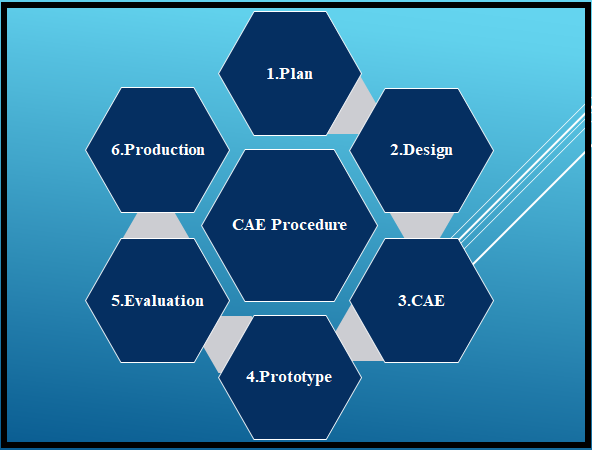
Three Stages in CAE-
1) Pre-Processing
2) Solving
3) Post-Processing
1) Pre-Processing:
- CAE pre-processors are employed to correct geometries, proceed with discretizing it, apply loads and constraints, and define the properties of the model’s materials.
- Ultimately a ready-to-run file is generated to be imported into the solver for its calculation. Since pre-processing consumes the majority of work-time for a simulation analysis, automation tools and customization capabilities are very important in reducing the overall analyst workload.
- Managing the imported data from CAD systems is also a big part of pre-processing due to differences in modeling between CAE software as well as differences in data handling between CAD systems and simulation systems.
- Ultimately the mesh quality of the discretized model and the definition of the physical problem determine the accuracy of the analysis, while the levels of automation and the case-specific modeling tools determine the time required for the modeling process.
- Most commonly used Preprocessors - HyperMesh,Beta CAE ANSA.
2) Solving:
- In solving,Various loads and constraints are added to the model to represent the loading conditions that the part(s) are subjected to.
- Different load cases can be defined to represent different loading conditions on the same model. Solver information is also added to tell the solver what kind of analysis is being run, which results to export, etc
- There are many solvers like Abaqus,Radioss,Optistruct,Pam Crash,Nastran,Patran,Ansys,SimScale,LS-Dyna etc.
- According to the type of analysis,the solver depends.For Example
- Abaqus-Durability Analysis
- Radioss,Pam Crash,LS Dyna-Crash Analysis
- Nastran-NVH Analysis
- Optistruct,Ansys Workbench-Structural Analysis.
3) Post-Processing:
- In Post-Processing,We will import the result files from the solvers and provide the environments and the tools to create comprehensive reports through model visualization and charts.
- With a vast amount of data coming from the solver, the preprocessor should provide the required tools to select, control, and properly display the results, while also provide the required automation to reduce the duration of this time-consuming process.
- Most Used Post-Processors:Meta Post,HyperView.
The term CAE (Computer Aided Engineering) includes the following types of analyses:
1) FEA [Finite Element Analysis]
2) MBD [Multi Body Dynamics]
3) CFD [Computational Fluid Dynamics]
4) Linear static analysis
5) Fatigue analysis
6) Nonlinear analysis
7) Optimization
8) Dynamic analysis
9) Buckling analysis
10) Crash analysis
11) Thermal analysis
12) NVH analysis
- Here we are going to do pre-processing on Car Hood Model.
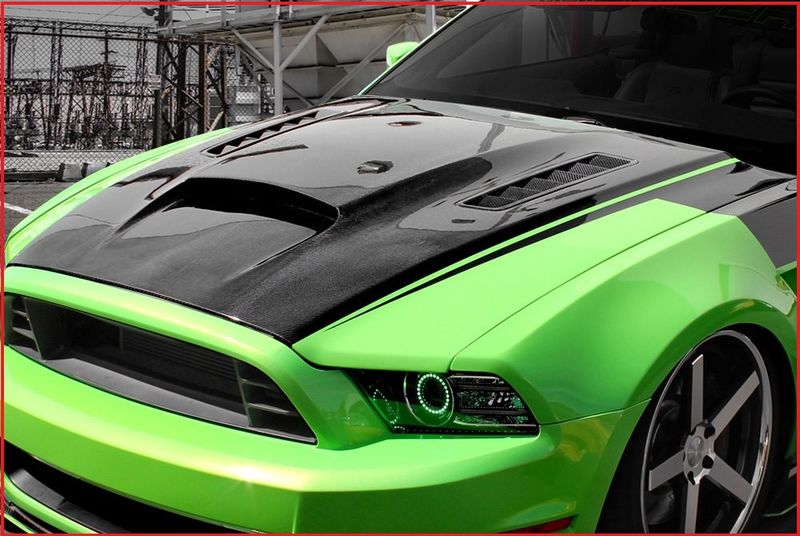
Car Hood-
- The hood or bonnet is the hinged cover over the engine of motor vehicles. Hoods can open to allow access to the engine compartment, or trunk on rear-engine and some mid-engine vehicles for maintenance and repair.
- The hood is made up of sheet metal.
- For sheetmetal and plastic components which are less than 6-8mm thickness,For that components,We should extract a midsurface and do a preprocessing on it.
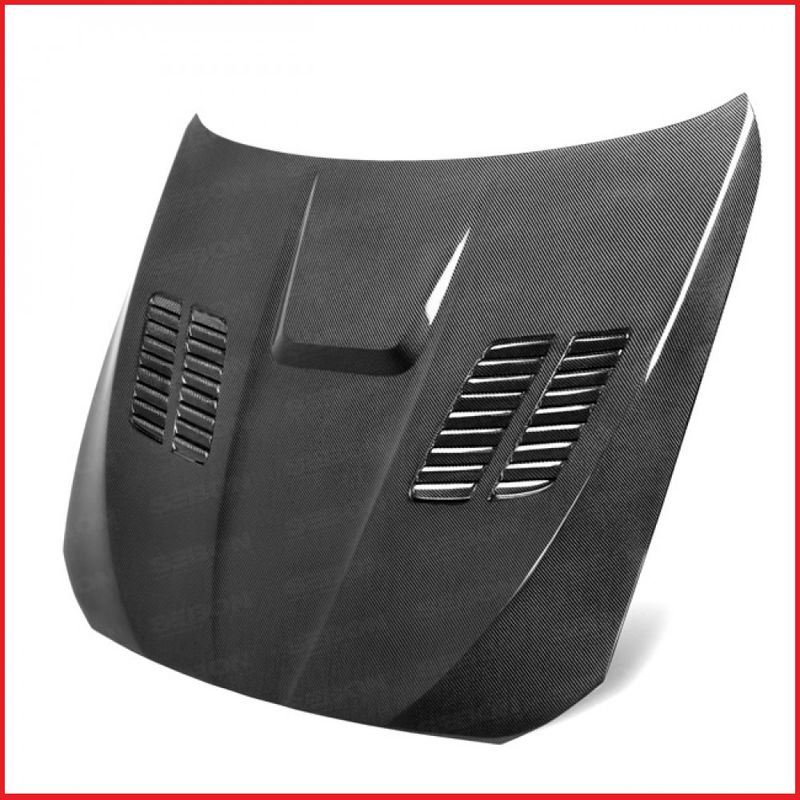
Figure 3-Hood Representation. |
Procedure -
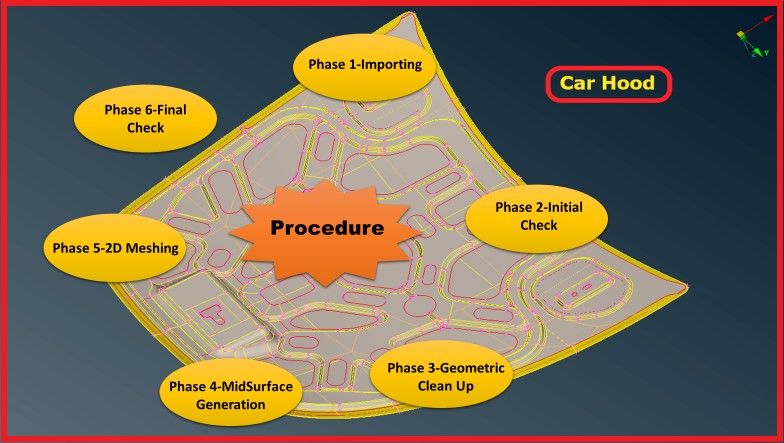
Phase 1-Importing the CAD Model
- Hence we are importing a given CAD geometry into the ANSA.
- There are file formates like IGES,STEP,Parasolid where we can import these file formats into any CAD,CAE Softwares.
- In ANSA we can import all the CAD Software file formates like
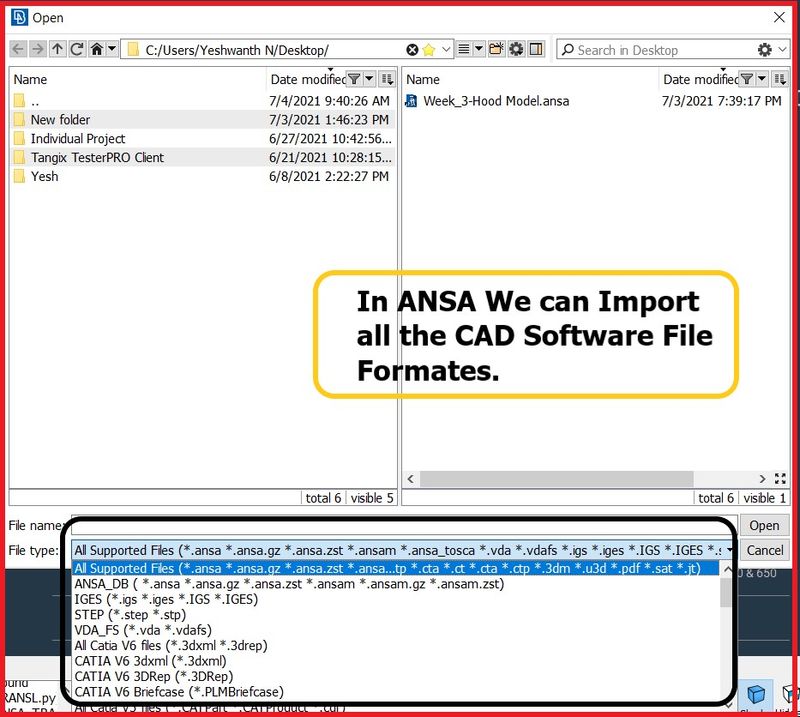
Figure 5-Supported File Formats. |
- IGES [Initial Graphics Exchange Specification].
- STEP [Standard for the Exchange of Product Model Data].
- Solidworks.
- Catia V5,V6
- Simens NX CAD
- Inventor
- Creo
- Solid Edge
- Rhinoceros 3D
- IGES,STEP,These two are standard file formats which are mostly used in industries.But now a days in industries,they are aslo using parasolid file format.
- Now import the model into ANSA GUI.The Model given to us is in STEP File Format.
- Go to Main Pull Down Menus >> File >> Open.

Figure 6-Importing/Opening the Model. |
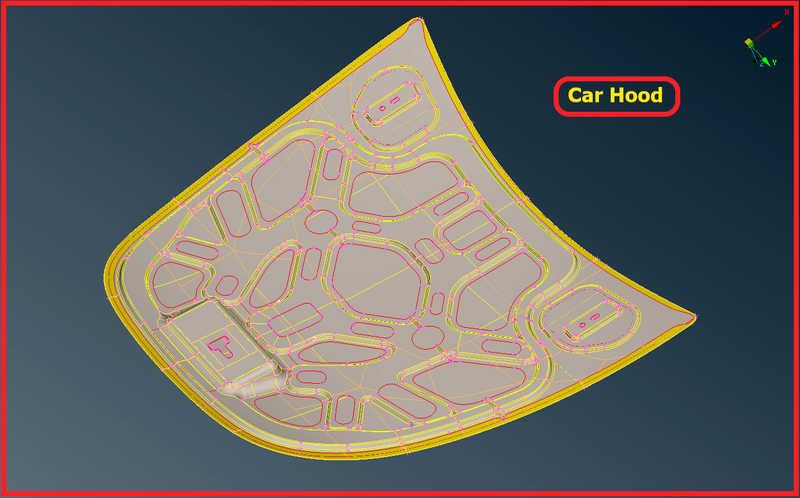
Figure 7-Model imported into GUI. |
- Now go to the the model browser by Tool Bar Menu >> Model Browser/Properties.
- To see how many components are availabale in the model.
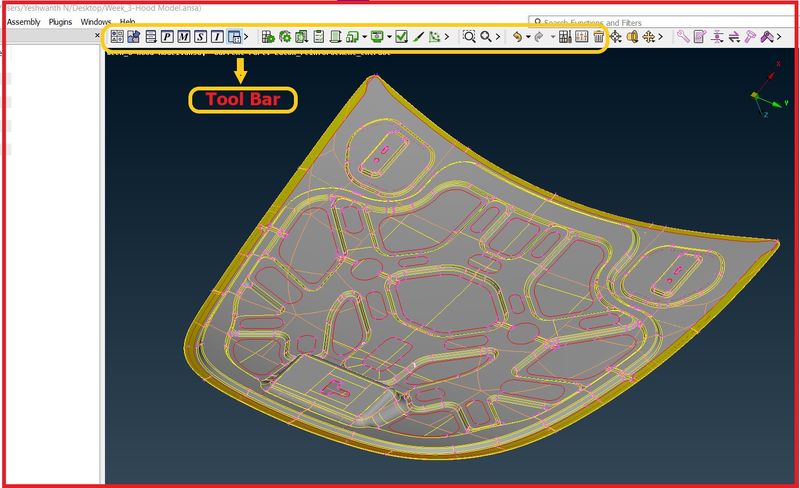
- Here we can see there are four components in the model browser.
- Now if you go to the properties browser,You can see 5 properties in the browser because the thinge component has 2 parts.
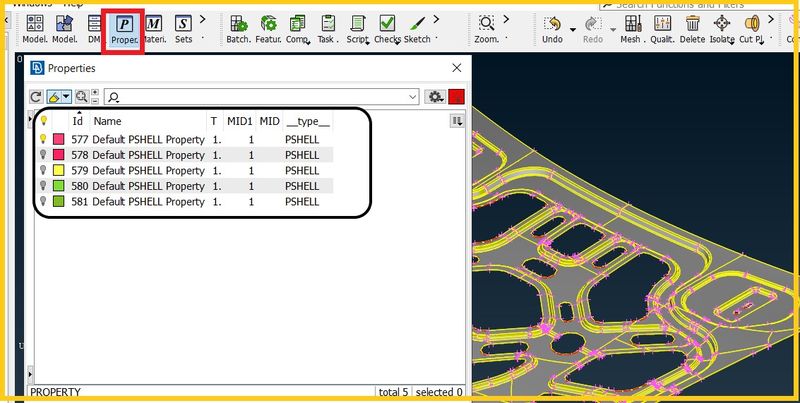
Figure 10-Properties Browser. |
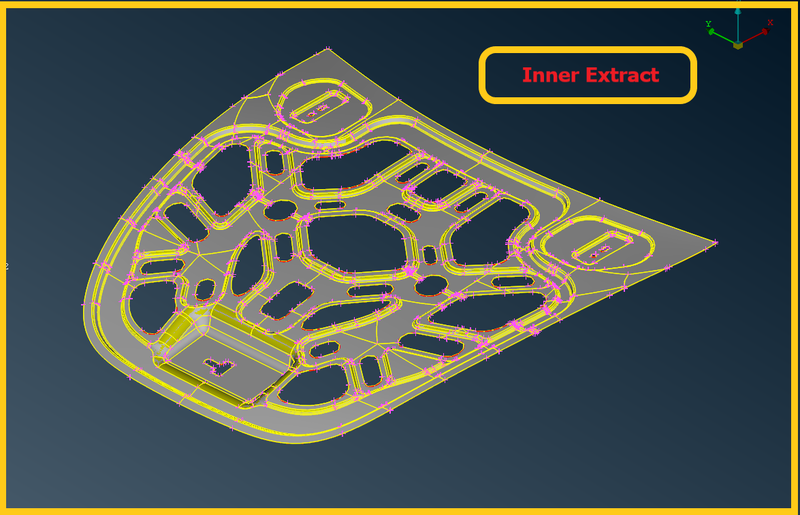

- Here the hinge has two properties,So transform that two hinges to one particular property.
- To transform,Create a new Property and name it as Hinge_Extract_Parent.
- Now make Hinge_Extract_1 and Hinge_Extract_2 visible in GUI.
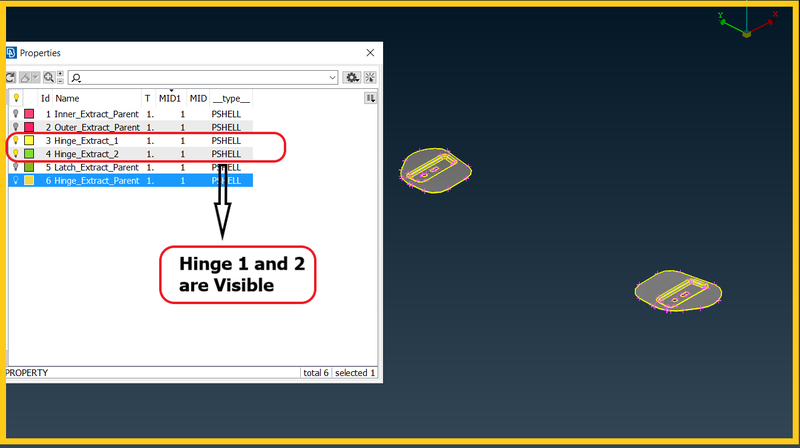
Figure 13-Hinge 1,2 are shown. |
- To transform,Create a new Property and name it as Hinge_Extract_Parent.
- Now make Hinge_Extract_1 and Hinge_Extract_2 visible in GUI.
- To transform that two hinges to Hinge_Extract_Parent Property.
- Right click on Hinge_Extract_Parent Property and click apply.
- After that select the two hinges by dragging a square box on tha hinges.
- Then click middle button to transform.
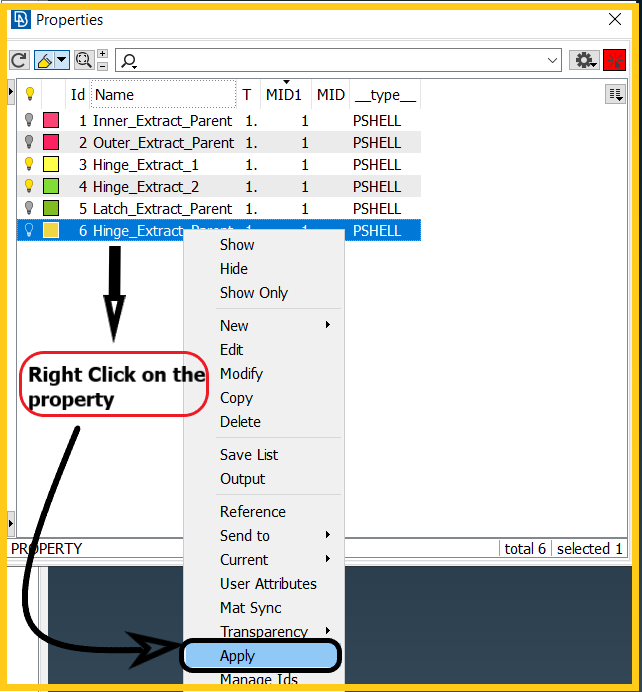
Figure 14-Transforming Process. |
- After clicking on apply,The software will state to select the face to apply property.

- Select the faces and click on mouse middle button to transform.

Figure 15-Square Box Select on the Hinges. |
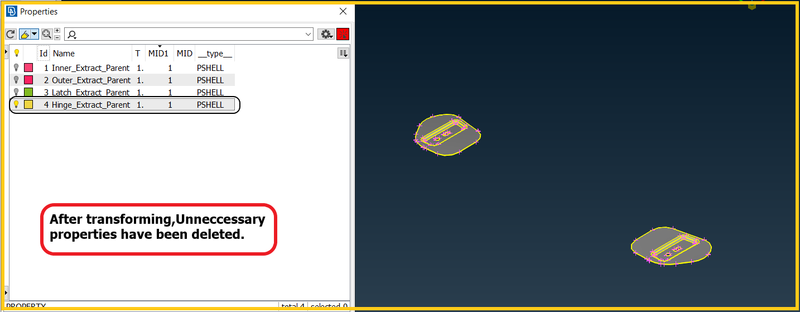
Figure 16-Hinges have been transformed to Hinge_Extract_Parent. |
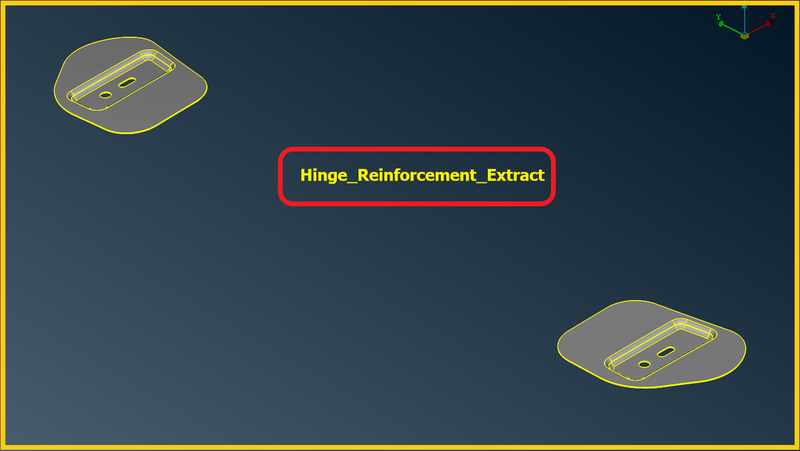
Figure 17-Hinge_Reinforcement_Extract. |

Figure 18-Latch_Reinforcement_Extract. |
Phase 2-Initial Check
- Before working on the model.We have to check the geometry if there are any errors like
- Damaged Geometry.
- Free edges in unnecessary areas.
- Unnecessary points on the lines.
- Unnecessary Connections and connectivity error.
- By assessing the hood model there are no errors in the geometry.
- If there are any unnecessary properties in the property browser,Delete them and then proceed.
- We have to some geometry clean up on the model,Cause there will be some minimal errors in the model.To solve that we should do some geometry clean up on the model.
Phase 3-Geometry Clean Up
- Here we will be doing some geometry checks on the parent component.
- We have to fix the geometrical errors in the parent component,Then only we will be able to extract auto midsurface using skinoffset.
- To fix the geometry checks go to Tool Bar >> Checks >> Geometry.
Step-1
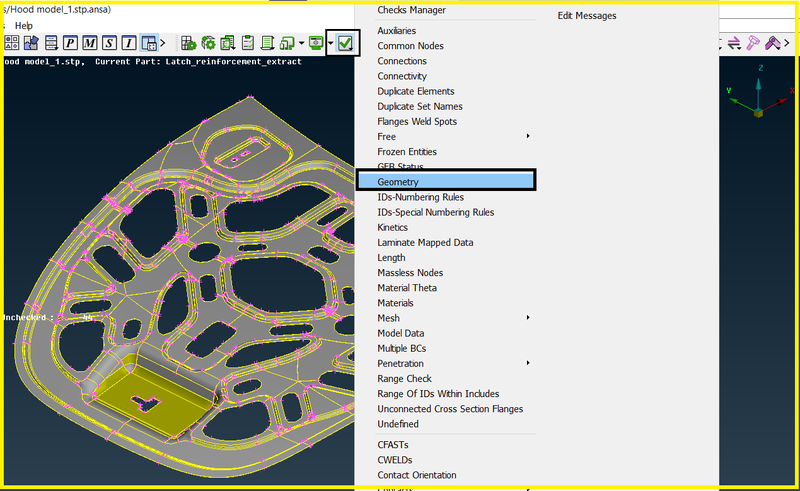
Figure 19-Checks Manager. |
- After clicking on the check geometry,The geometric errors will be displayed.
- We can fix that geometric errors by manually or automatically.
- For this hood model,We can fix that errors automatically by auto fix.
- While checking for errors in the geometry make sure to check this options in the checks manager.
Step-2
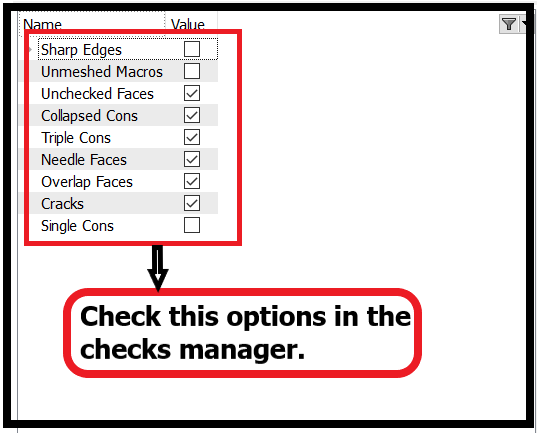
Figure 20-Check Geometry Options. |
Terminologies for Geomerty Options -
- Unchecked faces - Faces that failed for the shadow operation.
- Needle Faces - Degenerated faces are faces that have their opposite CONS coincident.
- Collapsed Cons - A CONS where it's starting and ending position coincide.
- Triple Cons - Areas where three or more faces have a common boundary.
- Cracks - Red CONS at inner areas.[Holes are excluded].
- Single Bounds - Red CONs at outer areas.[Holes included].
Step-3
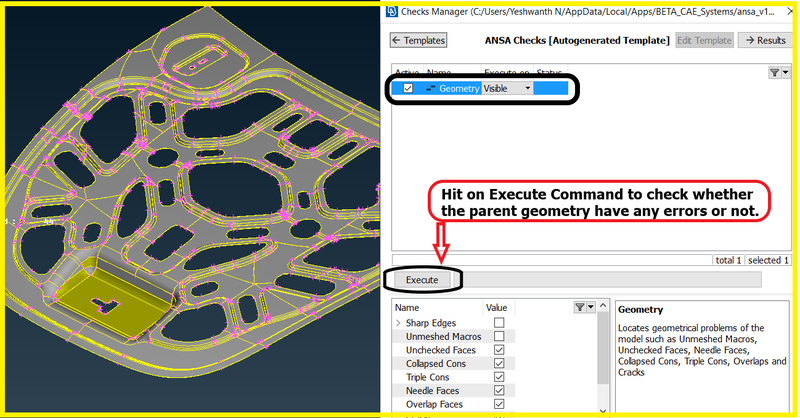
Figure 21-ANSA Check Manager. |
Step-4
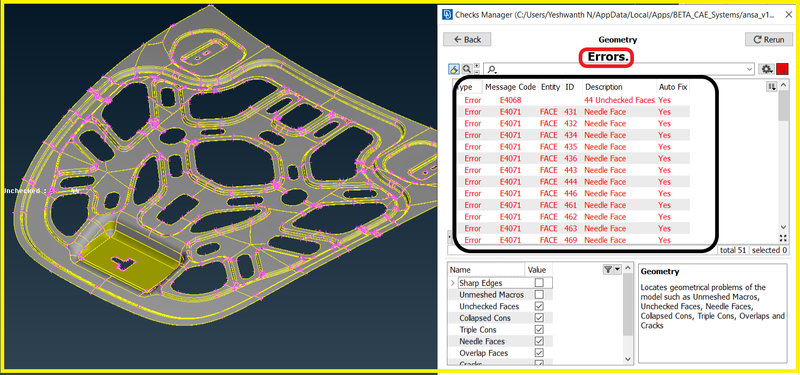
Figure 22-Geometric Errors. |
- Here in the Checks window all problems are reported with red color.
- Under Description column the kind of problem is explained.
- Focus functions are available in order to isolate geometrical problems and handle them easier.Select to fix all or specific reported problems by pressing right mouse button on the header of the list or one or more highlighted problems.
Step-5
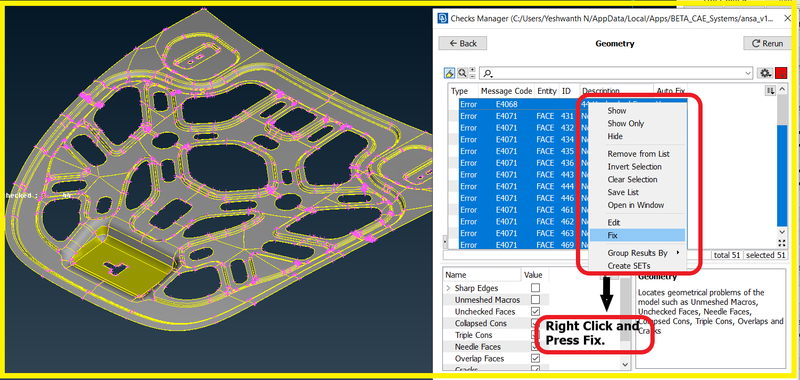
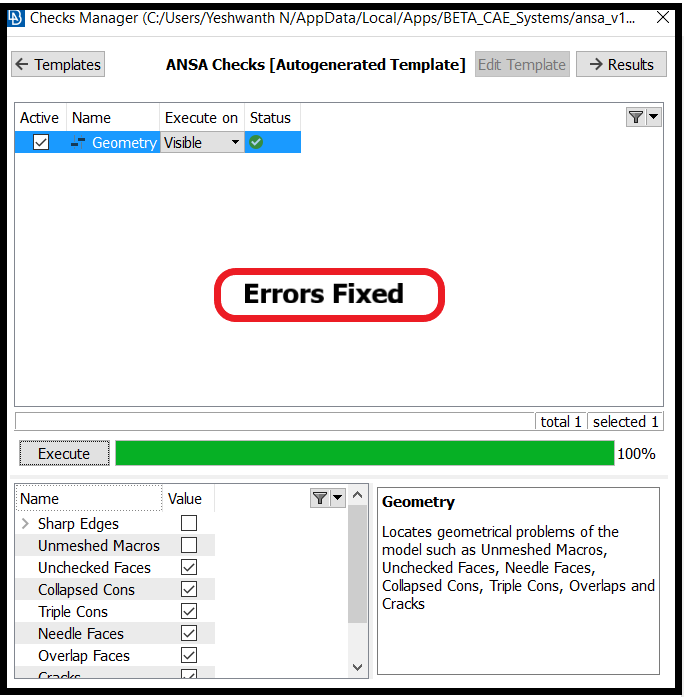
- [Note: All problems except triple CONS can be fixed by the automatic fixing.]
- [Note: Right mouse clicking on Check Geometry line, performs an action to all listed problems.In case where not all problems are fixed automatically, retry or proceed to fix them manually.For this component no need to fix manually because all the errors have been fixed with auto fix.]
- Similarly do the same process for the Outer Extract,Hinge Reinforcement Extract and Latch Reinforcement Extract.
- Here for the Outer Extract we have toggle the lines in the hemming regions because that hemming lines will be failing for minimum length,So we have to toggle that lines while meshing on it.
Phase 4-MidSurface Generation
- Before extracting the mid surface for the components we need to give perimeter and macros length on the components while extracting mid surface.
- This makes the component to get a desired shape,So it will be easy to extarct a midsurface without any errors.The possiblities of errors will be less.
- To give perimieters and macros length on the componets,
- Go to Mesh Module >> Perimeters >> Length.
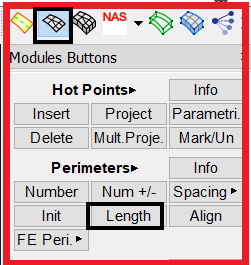
Figure 25-Permieter Length Tool. |
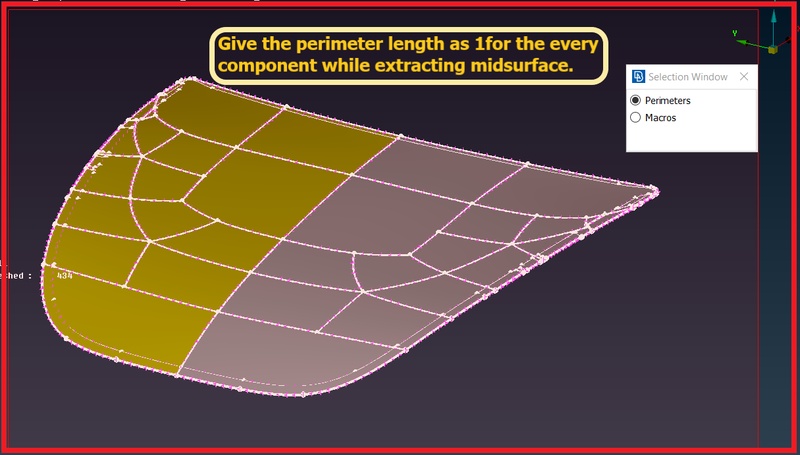
Figure 26-Selecting the cons to give perimeter length. |
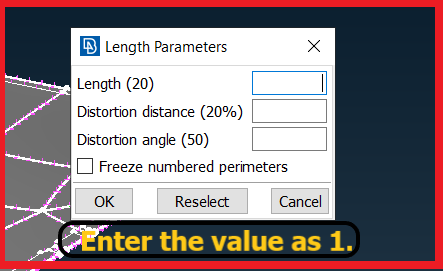
Figure 27-Enter the Value as 1 according to the component size. |
- Simillarly do the same thing for the macros also.
- Mesh Module >> Perimeters >> Length.
- This tool defines the element length on selected perimeter segments or macro areas.
- The element length may be explicitly declared or may be declared as a factor to be multiplied by the existing element length.
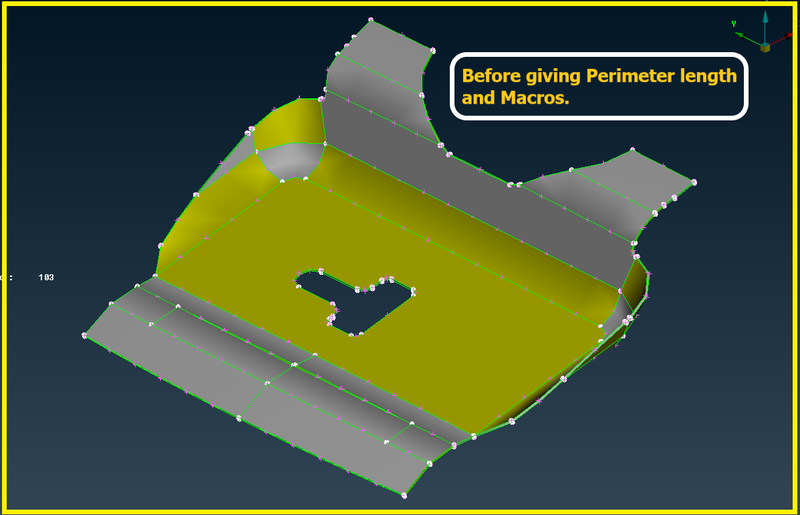
Figure 28-Before giving Perimeter Length and Macros. |
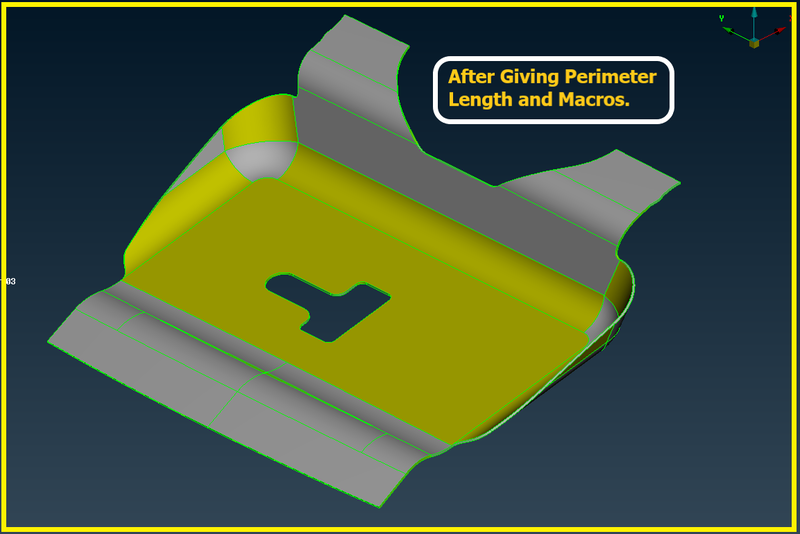
Figure 29-After giving Perimeter Length and Macros. |
- We can Extract Mid Surface by Two Methods called
- Using Skin MidSurface Option in Faces Panel in Topo Module.
- Using Offset Tool in Faces.
- But for this component,We will be extracting midsurface by using skin.
4:1 Why to Extract Mid Surface ?
- Before extracting the mid surface for every component,We should measure the thickness of the component and then we have to proceed to extract the mid surface.
- If the component thickness is less than 6mm then we will come to know it is a sheet metal component.
- For sheet metal and plastic components,Mid Surface extraction is must.
4:2 Generate Mid Surface
- To generate midsurface
- Go to Topo Module >> Faces >> Mid Surface >> Skin >> Selct the Face >> Give Offset Value and Direction.
- This tool turns the solid description of a thin part into thin shell description by isolating the outer or inner skin of the solid description.
- This Skin MidSurface tool works for only the sheetmetal components which are pressed and stamped.
- It works for the components which have uniform thickness.
- It dosen't works for the components which have varying thickness.
[Note:While extracting the midsurface,make sure to uncheck delete original faces option.]
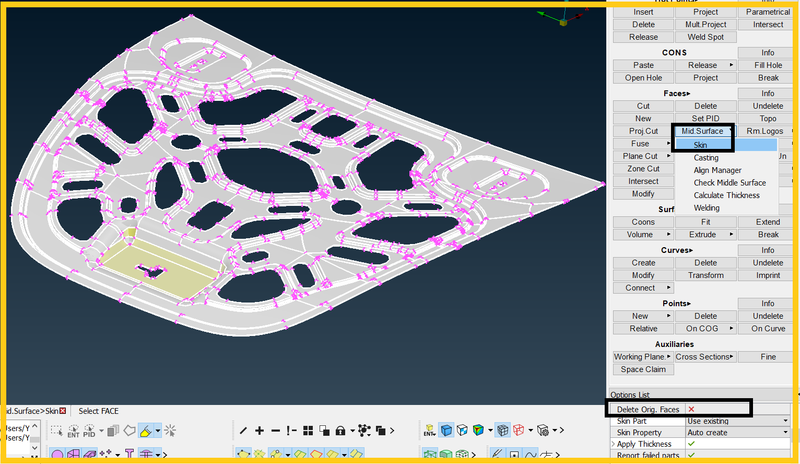
Figure 30-Extracting MidSurface. |
_1625407685.png)
Figure 31-Top and Bottom Surface Representation. |
_1625407888.png)
Figure 32-Blue Represents the Thickness. |
_1625407981.png)
Figure 33-Give the Thickness and and offset the surface to the appropriate direction. |
_1625408125.png)
Figure 34-Mid Surface Extracted. |
- Simillarly do the same thing for every component.
- Extract MidSurface for the Hinge,Latch and Outer Extract.
_1625408852.png)
Figure 35-Outer Extract MidSurface. |
_1625408742.png)
Figure 36-Latch,Hinge MidSurface. |
Phase 5-2D Meshing
- Once geometry cleanup is completed (e.g. surfaces are stitched together — no unwanted free surface edges inside the geometry), meshing is next.
Some rules of thumb when meshing:
- The mesh should look rather smooth and regular (keep in mind that the analysis is based on your mesh and the mesh quality is key.
- Use the simplest element type suited for the problem.
- Start with a coarse mesh and understand the modeling results; then use a finer mesh if needed.
- Try to keep mesh related uncertainties to a minimum if possible. Keep it simple as it can get more complicated on its own.
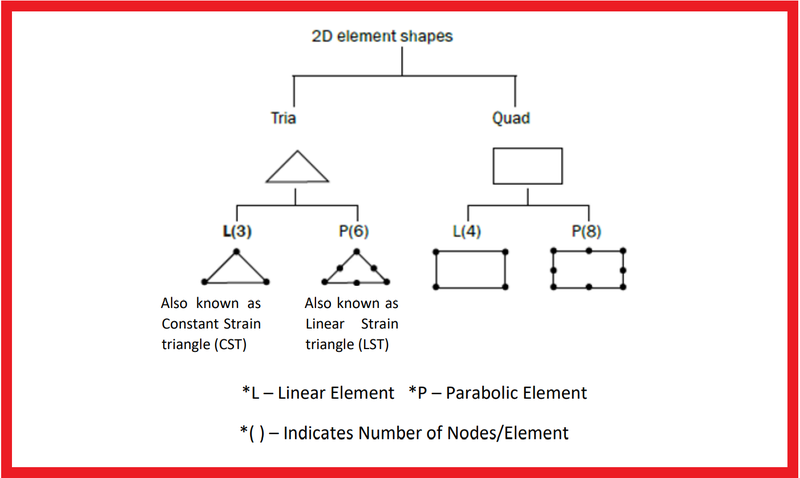
Figure 37-2D Element Shapes. |
- Different Element Type Options for Shell Meshing:
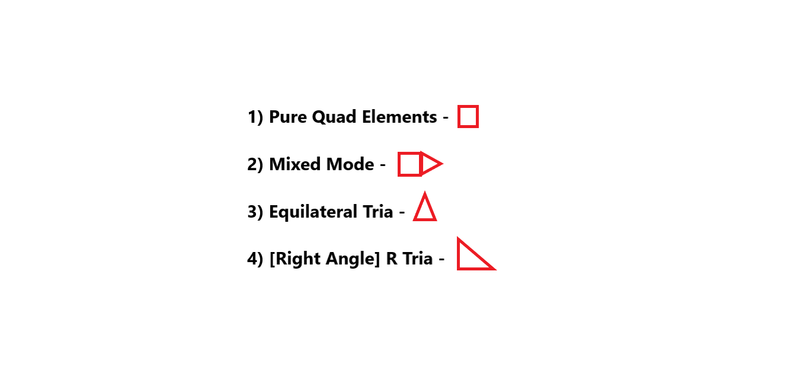
5:1 Enter the Parameter quality criteria what they given for the Hood Model
- Select and set the respective quality criteria for the corresponding elements to perform the Quality Checks (Hidden Mode). Also set the general presentation settings concerning the ANSA workspace
- Use the F11 key to open the Quality Criteria and Presentation Parameters management window (F11 Menu).
- Tool Bar >> Quality Criteria (F11) >> Enter the Values.
- Tool Bar >> Parameter >> Enter the Values.
Target/Average Length- 5 Units
Sl. No. |
Quality Criteria |
Function / Definition |
Value |
1 |
Aspect Ratio Ratio |
Ratio of Max. Length by Min. Length |
3 |
2 |
Skewness |
Deviation from the ideal shape |
45 |
3 |
Warping |
Angle between the 2 planes of the same element(Quad) |
15 |
4 |
Jacobian |
Transformation of Coordinate System. |
0.7 |
5 |
Min. Length |
Shortest length of any given element |
2 |
6 |
Max. Length |
Longest length of any given element |
7 |
7 |
Min angle Quad |
Minimum angle in any given Quad element |
45 |
8 |
Max angle Quad |
Maximum angle in any given Quad element |
135 |
9 |
Min angle Tria |
Minimum angle in any given Tria element |
30 |
10 |
Max angle Tria |
Maximum angle in any given Tria element |
120 |
11 |
Tria % |
Percentage of Tria on any meshed surface |
15 |
_1625410630.png)
Figure 39-Quality Criteria Panel. |
- Now enter the Mesh Parameters
- Go to Tool Bar >> Mesh Parameters >> Enter the Values.
_1625411112.png)
Figure 40-Mesh Parameters. |
[Note : Save the Mesh Parameter and Criteria file for that component and save it in any other drives,Cause whenever we open that component,we can open the Element Criteria file and Parameter file,So criteria and mesh paremeters will be applied habitually instead of entering again.]
1) Aspect Ratio
- This is the ratio of the longest edge of an element to either its shortest edge or the shortest distance from a corner node to the
opposing edge ("height to closest node").
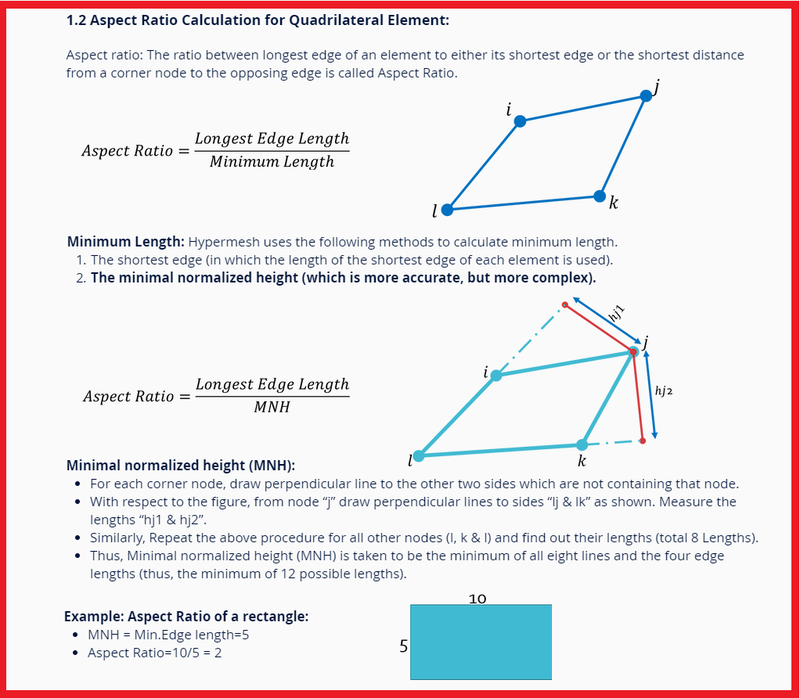
Figure 41-Aspect Ratio Calculation. |
2) Skewness
- Skew of triangular elements is calculated by finding the minimum angle between the vector from each node to the opposing
mid-side, and the vector between the two adjacent mid-sides at each node of the element.
- For Skewness: Ideal=0,But < 45 is acceptable.
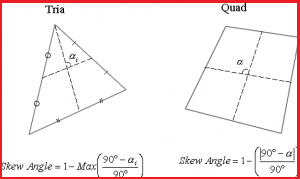
3) Warping
- This is the amount by which an element (or in the case of solid elements, an element face) deviates from being planar. Since
three points define a plane, this check only applies to quads. The quad is divided into two trias along its diagonal, and the angle
between the trias’ normals is measured.

4) Taper
- Taper ratio for the quadrilateral element is defined by first finding the area of the triangle formed at each corner grid point.These
areas are then compared to one half of the area of the quadrilateral.
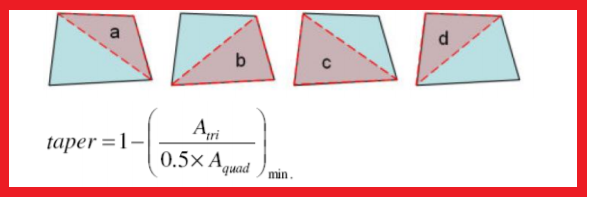
5) Minimum and Maximum Length
- The shortest distance from a corner node to its opposing edge (or face, in the case of tetra elements) referred to as height to
closest node.
5:2 Conditions to be followed while meshing
- Feature capturing is must while meshing.All the nodes must be connected to the shared edges.
- Avoig higher number of trias.
- Important Parameter's in tria management
- No trias in corner's or edge's.
- No opposite trias.
- No back to back trias.
- No trias in fillets or hemmings(We can have minimum but anyhow try to avoid).
- No rotational quads.
- No trias should share a boundary with feature line.
- Connectivity between elements.
- Split and perform the mesh.
- Use mixed type mesh for irregular shaped surfaces and quads only for rectangular/square surfaces(Opposite sides should be parallel and equal).
5:3 Begin meshing the surfaces
- Start meshing from the centre regions or from least free edges.You will get proper mesh density and proper mesh flow.
Why Meshing is Needed ?
- Finite Element Method reduces the degrees of freedom from infinite to finite with the help of discretization or meshing (nodes and elements). One of the purposes of meshing is to actually make the problem solvable using Finite Element. By meshing, you break up the domain into pieces, each piece representing an element.
How to Begin Mesh ?
- Start meshing form the least free edges,Like start meshing from the center.
- It will be easy to get proper mesh flow and we will get uniform mesh density.
- Don't mesh form the edges,It will be difficult and you will get many error,So start meshing from the center.
- Choose the element type while meshing.
- For this component we will be using mixed element type and working on it.
- We can also quads element type.This type can be used when we have rectangular surface.
- We can use Tria Element type.This type can be used for 3d tetra meshing.
Start Meshing
- To begin mesh,Switch form topo module to the mesh module.
- Before Meshing set the perimeter and macro length to the component.
- Here set the perimeter and macro length as target element size.
- It will split according to the target element size,So it will be easy for us to mesh.
- To Mesh >> Go to Mesh Module >> Mesh Generation >> Best Mesh >> Select the area.
- While Meshing Switch from shaded mode to the hidden mode,Then only we will be able to see the visibility element quality.
_1625413486.png)
Figure 45-Drawing Styles Panel. |
Latch Component-
- Now while meshing the component
- Set the perimeter and macr length as target element size given,So it will split the hot points according to that length and it will be easy for us to mesh.
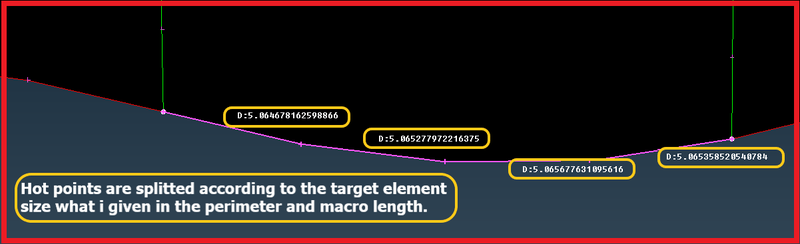
Figure 46-Hot Points splitted according to the length given in perimeter and macros. |
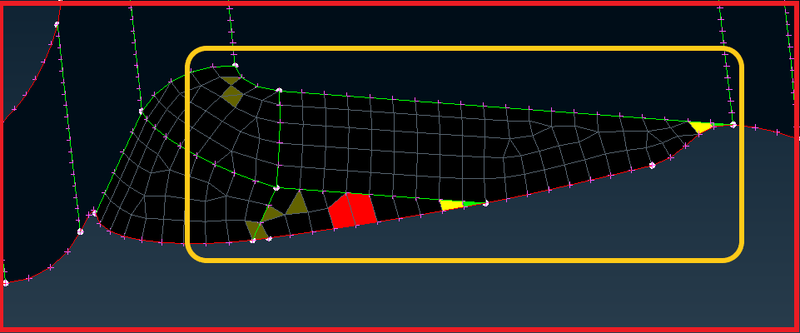
Figure 47-Elements failing. |
- Here in this region the elements are failing.
- To fix this spit the cons and try to mesh.
- To split the cons go to Macros >> Cut,and toggle the unneccessary cons.
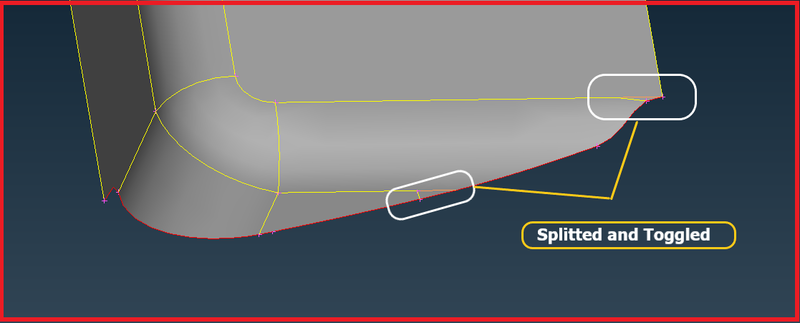
Figure 48-CONS Splitted and Toggled. |
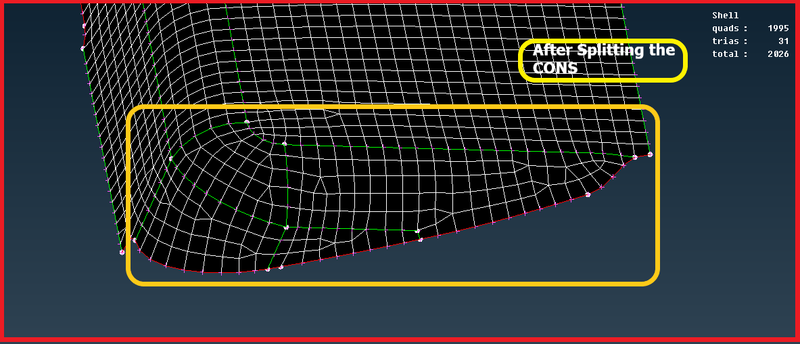
Figure 49-After Splitting the CONS. |
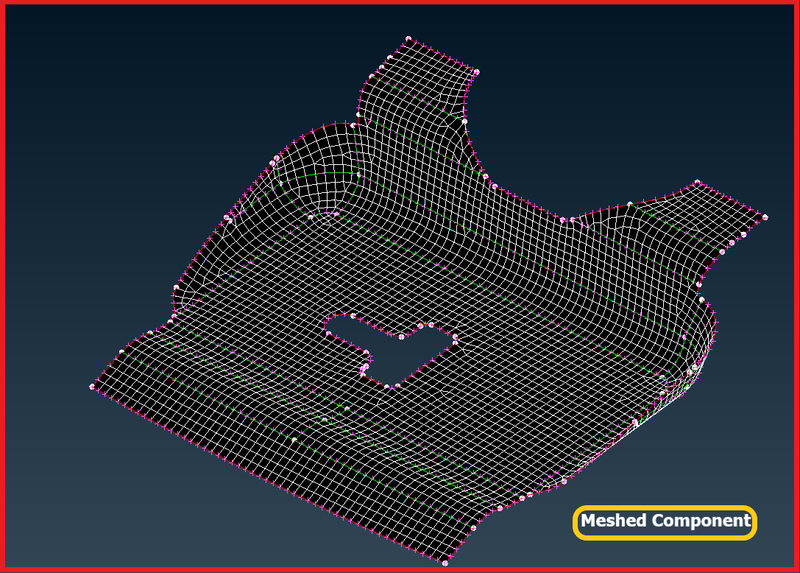
Figure 50-Meshed Component. |
Hinge Component-
- Here Hinge has 2 properties in the property browser,So create one new property and transform them into one hinge property.
- We will be reflecting the hinge to other side,So while reflecting in ANSA,The Surface and elements will aslo be reflected,So extract midsurface for one hinge.
- Toggle the unnecessary CONS which are failing for the minimum length.
- You can toogle the CONS by Right Click on the CONS.
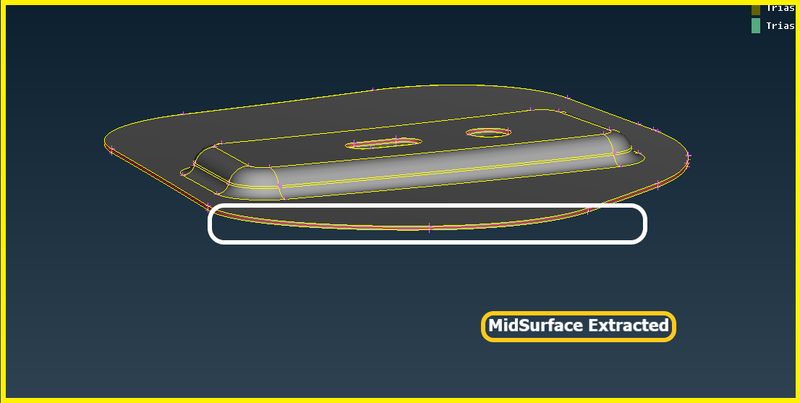
Figure 51-MidSurface Extracted. |
- Make the midsurface visible by pressing OR in Focus Panel.
- It will keep visible only selected entities.
- Switch to the PID Region and Select the entity to make the midsurface visible.
_1625461467.png)
Figure 52-Meshed on Hinge. |
- Now transform the hinge to the other side by using transform tool in the from the utilities menu.
- While transforming make outer extract parent component to be shown.
- Then only we will be able to select the symmetric points,So make outer extract parent to be shown in GUI.
_1625462076.png)
Figure 53-Outer Extract Parent Component has been Shown to select symmetric points. |
_1625462239.png)
Figure 54-Transform Tool to Mirror. |
_1625462564.png)
Figure 55-Selcted Hinge Entities to Reflect. |
_1625462851.png)
Figure 56-Points have been selected to reflect. |
_1625463034.png)
Figure 57-Hinge Entities Reflected. |
Outer Extract Component-
- In the outer extract component,After extracting the midsurface.
- Delete the surfces which are symmetric by using Rm.DBL tool in faces panel from topo module.
- This Rm.DBL tool is used to find the symmetric faces and delete one side of faces.
- There will be CONS in the hemming region which will be failing for the minimum length,So toggle that CONS while meshing.
- And toggle the unnecessary CONS on the outer extract midsurface.
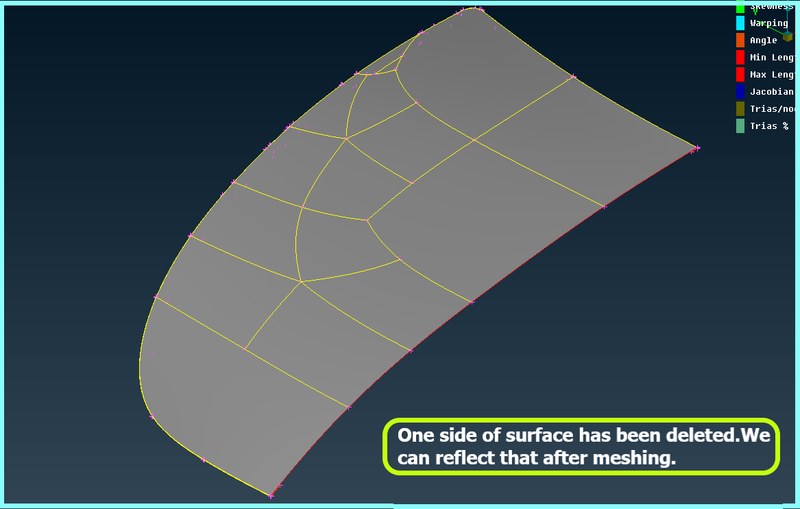
Figure 58-One Side of Surface Deleted. |
_1625464399.png)
Figure 59-CONS in hemming region toggled. |
_1625464673.png)
Figure 60-Unnecessary cons toggled and splitted into 4 regions. |
_1625464998.png)
Figure 61-Reflected to other side using default symmetry plane option in transform tool. |
Inner Extract Component-
- After extracting the midsurface,Delete the surfaces which are symmetric.
- After deleting the surfaces go to the mesh module.
- Now set the perimeter and macro length as target element length given,Because it will split the points according to that length.So it will be easy for us to mesh the component.
_1625465930.png)
Figure 62-Symmetric Surfaces Deleted. |
- Toggle the unnecessary cons in the component and start meshing the component.
_1625467797.png)
- Now reflect this entities to other side using transform tool.
- While reflecting select the symmetric surfaces to reflect on other side.
_1625470116.png)
Figure 64-Selecting Symmetric Surfaces. |
_1625470180.png)
Figure 65-Latch Top Surface has been Hidden. |
_1625470354.png)
Figure 66-Reflected Symmetric Surfaces. |
- Now topo the surfaces which are not connected.
- If topo dosen't work,Paste the cons manually.
- If we do this mesh will be erased in that particular regions,So mesh again in that surfaces.
_1625471318.png)
Figure 67-Meshed in Every Regions. |
5:4 Assign Thickness to the Components
- Go and assign thickness to the components.
- Go to properties browser and double click on the component which you want to assign the thickness,A new window will pop on the GUI.Give thickness value there.
- Simillarly do the same process for every component.
_1625471871.png)
Figure 68-Properties Browser. |
_1625472363.png)
Figure 69-Thickness Assigned. |
Phase 6-Final Check
- After Assigning Thickness,Check whether the thickness have been appplied or not.
- To check Go to Utilities >> Quality Criteria >> Presentation Parameters >> Draw Shell as Solid.
_1625472629.png)
Figure 70-Quality Criteria Panel. |
_1625472935.png)
Figure 71-Thickness Assigned. |
- Now check whether there is a proper mesh flow in every region.
- Check whether the elements have captured the feature lines properly.
- And check whether there are trias touching each other.
- To check this Go to Utilities >> Quality Criteria >> Edit Criteria Visibilty >> Check Triangles Per Node >> Apply.
_1625473401.png)
Figure 72-Check Triangles Per Node. |
_1625473573.png)
Figure 73-Shell Elements Panel. |
- 21 Trias are touching each other,
- Drag them backward.To drag tria backword use paste tool from grids to move them backward.
- To see the trais touching each other.Double click on the OFF.You will be able to see them.
_1625473975.png)
Figure 74-Trias Touching Each Other. |
Final CAD Model Images -
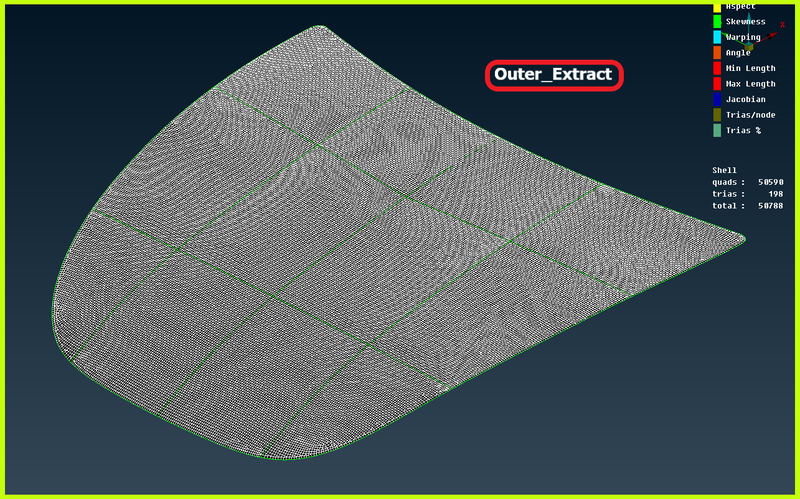
Figure 75-Inner and Outer Extract Final Image. |
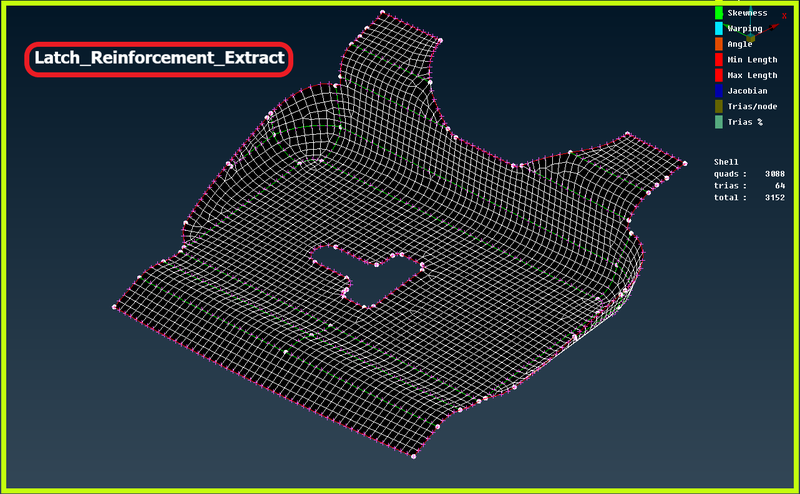
Figure 76-Hinge and Latch Reinforcement Extract Final Image. |
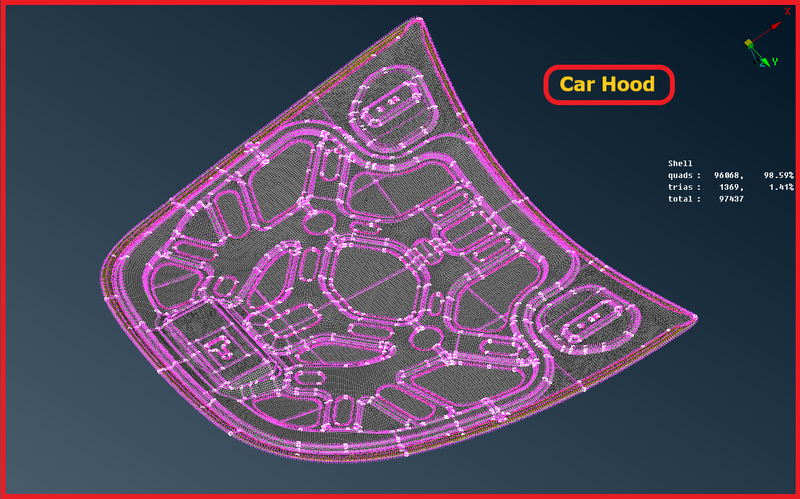
Figure 77-Final Meshed FE Image. |
_1625474998.png)
Result -
- Hence the mid surface has been extracted to the parent component.
- Hence there are no surface deformations in the geometry.
- A well connectivity has been established between the surfaces.
- The features have been captured properly.
- A good mesh flow have been achieved with the zero elements failing for quality
- Hence tria percentage with 1.4 % have been achieved.
Learning Outcome -
- In this Week 3 Car Hood Challenge,I came to know
- How to extract the mid surface automatically for the sheetmetal components.
- How to clean the geometry .
- How to generate a proper mesh flow with low tria percentage.
- How to assign thickness to the components.