Objective 1:- For a defined driving cycle, calculate the energy required for braking.
For calculating the drive cyle i have taken an example of drive cycle where i have imported the excel value of Time(sec) & Velocity(mph) to calculate the braking energy.
Matlab Script:-
%program to find the braking energy for the drive cycle
drive_cycle=xlsread('drive_cycle');%loading drive cycle
speed=drive_cycle(:,2);%speed values extracted
time=drive_cycle(:,1);%time values extracted
Vf=[];%final speed array
Vi=[];%initial speed array
m=580000;%mass of vehicle
%for loop for picking the initial and final speed of deacceleration
for i=1(length(speed)-1)
if speed(i)>speed(i+1)&&speed(i+2)<speed(i+1)&&speed(i-1)<speed(i)
Vi=[Vi,speed(i)];
else if speed(i)<speed(i+1)&&speed(i+2)>speed(i+2)>speed(i+1)&&speed(i-1)>speed(i)
Vf=[Vf,speed(i)];
end
end
end
Vf=[Vf,0]; %adding zero to the last value of final speed
B=(0.5.*m.*(Vi-Vf).^2)/1000;% calculating the brakin energy for each step of deacceleration
x=sprintf('total braking energy=%o.2fKWh',sum(B)); %formating the data into string
disp(x) % displaying the total braking energy
%plotting drive cycle
plot(time,speed,'linewidth',2)
title('drive cycle')
xlabel('time')
ylabel('speed')
grid on
Result:-
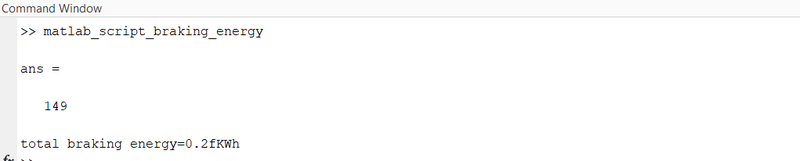
Drive cycle Graph:-
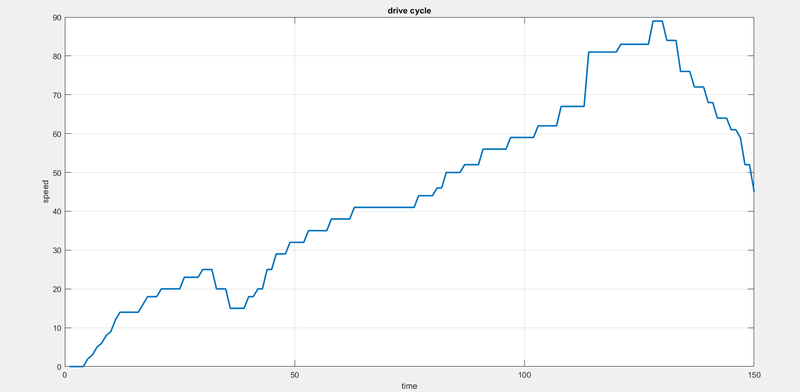
drive_cycle_Excel_link:- https://drive.google.com/file/d/1Cq9gj5NuP5YQk8E3Y9chWjsgGMm0rSal/view?usp=sharing
Matlab_link:- https://drive.google.com/file/d/1uKbWc4cYsS-t2K6ZQrAiVWU3kjpINe5r/view?usp=sharing
Onjective 2:- Why electric motor can’t develop braking torque at high speed similar to starting? How electric and mechanical brakes are coordinated?
Torque is the turning force through a radius - with the units Nm in the SI system and the units lb ft in the imperial system.
The torque developed by an asynchronous induction motor varies when the motor accelerates from zero to maximum operating speed.
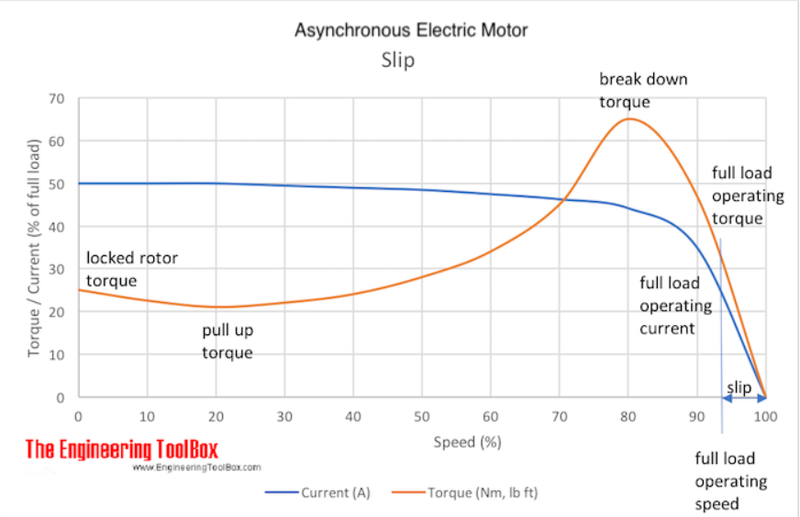
Locked Rotor torque:-
The locked rotor torque or Starting Torque is the torque an electrical motor develops when starting at zero speed.
A high Starting Torque is more important for application or machines hard to start - like positive displacement pumps, cranes etc. A lower Starting Torque can be accepted for centrifugal fans or pumps where the start load is low or close to zero.
Pull-up Torque:-
The Pull-up Torque is the minimum torque developed by an electrical motor when it runs from zero to full-load speed (before it reaches the break-down torque point).
When a motor starts and begins to accelerate the torque in general will decrease until it reach a low point at a certain speed - the pull-up torque - before the torque increases until it reach the highest torque at a higher speed - the break-down torque - point. The pull-up torque may be critical for applications that needs power to go through some temporary barriers achieving working conditions.
Break-down Torque:-
The Break-down Torque is the highest torque available before the torque decreases when the machine continues to accelerate to working conditions.
Objective 3:- Make a MATLAB program which plots contour of given motor speed, torque and efficiency values. Attach the code as a .m file attach a screenshot of all the plots.
Accelerating Torque:-
Accelerating Torque = Available Motor Torque - Load Torque
In imperial units the Full-load Torque can be expressed as
T = 5252 Php / nr (1)
where
T = full load torque (lb ft)
Php = rated horsepower
nr = rated rotational speed (rev/min, rpm)
In metric units the rated torque can be expressed as
T = 9550 PkW / nr (2)
where
T = rated torque (Nm)
PkW = rated power (kW)
nr = rated rotational speed (rpm)
Each motor should have a published torque curve or a chart that correlates torque to flow and pressure. Some systems can have a motor that performs as desired in one environment. However, when something as simple as the angle the system is sitting on changes, the motor can stall. This is because the amount of force acting against the motor alters the starting torque value. This is why users need to understand all the parameters of the system and how it will be operated.
A motor’s efficiency is a very important key in its starting torque. For example, while a vane motor has a very high efficiency when running at full speed, it does not have the same efficiency at lower speeds. Therefore, the starting torque is much worse than its running torque. The operating speed of the system is also a very crucial factor to consider. Users should understand the torque output and efficiency it will have while running. Gear, vane, and geroler motors often have the worst starting torque due to their poor efficiencies at low speeds. A piston motor has great efficiencies in both low and high-speed applications and often has the best starting torque.
Why electric motor can't devlop high torque at rated speed.
When the rotor rotate, there is a change in magnetic flux, causing what we call back EMF. This back EMF “oppose” the voltage we applied to the motor, thus reducing the current in the winding. Higher RPM means higher rate of change in magnetic flux, means lower current and torque.
As a simplistic approximation:
- TORQUE = constant1*CURRENT
- POWER = constant2*TORQUE*RPMS …
- … or TORQUE = POWER/[constant2*RPMS]
And there are two limits on motor operation. There is a maximum current before there is danger of melting the coils, and there is a maximum power that it can produce. So torque is limited by the smaller of:
- constant1*CURRENT_MAX
- POWER_MAX/[constant2*RPMS]
The result is that torque is constant up to the point were these two are equal, with power increasing linearly over that range. Then power becomes constant, with torque decreasing as the inverse of RPM.
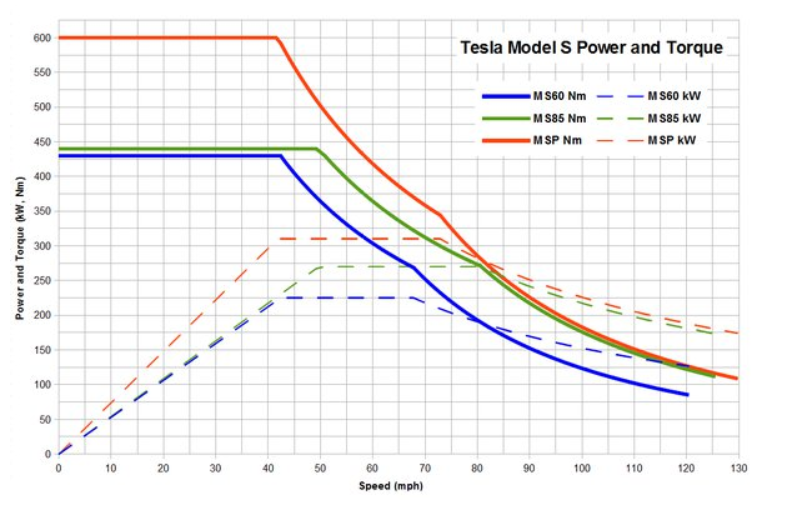
That’s due to what is called back EMF. The motor starts generating a voltage in reverse which acts against the supply voltage. Thus the current flow is reduced which, in turn, reduces the strength of the magnetic field which provides the turning torque.
It’s an inherent feature of any wound motor.
I should add that’s the model for a simple electric motor. The sort found in EVs has very complex power controllers which will do things like limit current to avoid burning out motors. For instance, the current at low RPM is likely to be limited to avoid burning out the coils. Up to a certain RPM the controller might be able to maintain the current level and thus torque. However, at a certain point the back EMF will be too high to be fully compensated for and then torque will start to fall away with higher RPM.
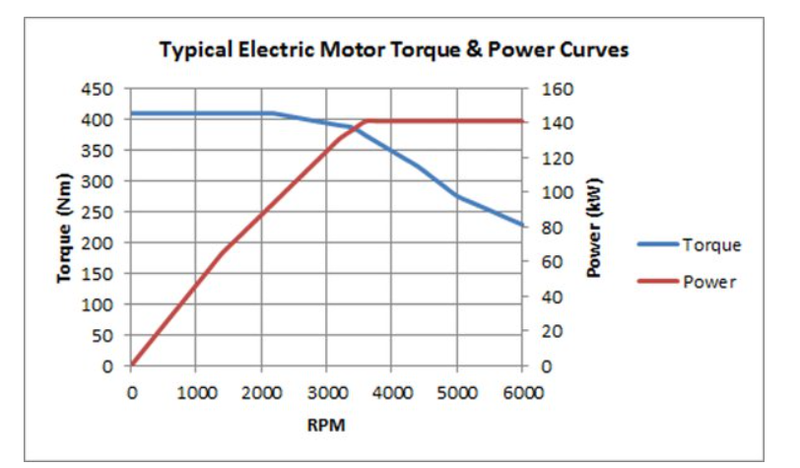
In practice, power will start to drop off too as that back EMF effect becomes more significant. There are ways round this by using a gearbox, but one of the advantages of EVs is avoiding the need for such a device in the power train.
nb. it is the same phenomena that causes back EMF that is used in regenerative braking.
How electric braking cordinate with mechanical braking.
Mechanical braking:-
Before we dive into the difference between car brakes, let’s describe the hydraulics behind braking. The hydraulic brake circuit consists of a fluid-filled master cylinder, which connects to a separate slave cylinder. The brake pedal connects to the master cylinder and when pushed, depresses the piston in the master cylinder, forcing fluid along connected pipes. The fluid reaches the slave cylinders at each wheel, which in turn forces the piston to apply the brakes.
The surface area of the combined slave pistons, where the brake-pedal force is applied, is greater than that of the master-cylinder piston. Hence, the master piston has to travel a greater distance to move the slave pistons compared to the fraction of distance required by the slave pistons to apply the brakes. This setup allows for the exertion of a large force by the brakes, comparable to how a long-handled lever can lift a heavy object a short distance.
The hydraulic system used during braking delivers hydraulic fluid from the reservoir to the brake caliper pistons to slow down and stop the brake disc.
In most modern cars, the master cylinders use twin hydraulic circuits in tandem for redundancy purposes. The circuits can be arranged to control different pairings of breaks: one circuit for the front pair and the other for the back pair; or one circuit for one in front and one in back, and the other circuit for the other side.
By design, rear brakes are less powerful to prevent the rear wheels from locking and skidding. A load-sensitive pressure-limiting valve prevents locking in most cars by controlling high rises in hydraulic pressure. Limiting valves help prevent brake locking situations, along with anti-lock brake systems which monitor wheel locking. Modern cars also apply power-assisted brakes.
A servo unit, using the pressure difference between the partial vacuum in the inlet manifold and the outside air, provides braking assistance via a pipe connection to the inlet manifold. The servo is fitted between the master cylinder and the brake pedal. When a driver pushes on the brake pedal, it in turn pushes on the master-cylinder piston and a set of air valves.
A large diaphragm connects to a master-cylinder piston. Prior to applying the brakes, both sides of the diaphragm are exposed to the vacuum from the manifold. Applying the brakes closes the valves that link the rear side of the diaphragm to the manifold and opens a valve to let in outside air. The high pressure of the outside air pushes the diaphragm forward on the master-cylinder piston to assist the braking effort. If the brake pedal is kept in place, the air valve stops drawing on the outside air, keeping the brake pressure constant.
Disc and Drum Brakes
The image above is an example of a typical disc brake with a caliper that applies pressure to the friction or brake pads. This friction force slows down the wheel and allows the car to stop.
Disc brakes are typically located on the front two wheels. A caliper straddles a disc and the disc turns with the wheel. Small hydraulic pistons in the caliper operate via pressure from the master cylinder. Friction pads clamp against the disc once the small hydraulic pistons apply the pressure, which slows down the disc and the wheel.
The pistons only move a small distance to apply the brakes, and when released, the friction pads barely clear the disc since they have no return springs. The small gap is maintained by allowing the pistons to slip forward gradually as the pads become worn down. Rubber sealing rings around the pistons make this possible, preventing constant brake adjustment. Modern cars use wear sensors to indicate when pads need replacement.
Inside the drum brake are two curved brake shoes. When hydraulic pressure is applied, the brake shoes are forced outward, causing the linings to apply a friction force against the drum. The drum is connected to the wheel and slows down as a result.. The drum is connected to the wheel and slows down as a result.
The rear wheels typically use drum brakes, which use a hollow drum that turns with the wheel. A stationary back plate covers the open back of the drum. The back plate has two curved brake shoes carrying friction linings. Hydraulic pressure provided by pistons in the brake wheel force the shoes outward, causing the linings to press against the inside drum and thus making the wheel slow down or stop completely. As opposed to disc brakes, return springs are used to pull the brake shoes back when the brake is released. Drum brakes have a tendency to fade if applied repeatedly in a short time—they heat up and lose their efficiency until the heat dissipates.
Electric braking or regenrative braking:- As mentioned earlier, a conventional braking system’s disc and drum brakes use friction to slow and stop modern cars. However, most hybrid and electric vehicles use regenerative brakes due to the added benefit of recharging electric batteries.
Vehicles with regenerative brakes achieve braking by driving the motor in reverse. As the driver steps on the brake pedal, the vehicle’s electric motor is placed in reverse mode, causing it to run backwards. This operation not only slows the car’s wheels, but also acts an electric generator for the car. The reverse motion produces electricity that feeds into the car’s battery. Hybrid and electric vehicles also have friction brakes that act as a backup system when the regenerative braking is not supplying enough power to stop the vehicle.
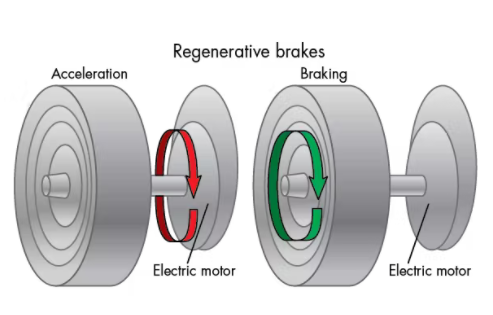
Reverse motor motion can be achieved by using the vehicle’s own momentum. The electronic circuitry and the car’s onboard computer determine when to use the conventional frictional brake system or whether to put the motor into reverse. A slight reduction in the car’s momentum, determined by the driver’s force on the pedal, causes the vehicle’s electronics to activate the regenerative brakes and place the motor in reverse. In contrast, if the vehicle needs to come to a quick stop, to avoid a collision for example, the conventional brakes will be engaged.
Working:- When the electric motor reverses direction, it becomes a generator that stores the energy in the vehicles battery.A brake controller controls regenerative braking. Brake controllers are electronic devices that determine when, via remote control, braking begins and ends, as well as the speed of application. Similar to an ABS controller that monitors the rotational speed of the wheels in relation one another, the brake controller can calculate how much torque is available to generate electricity as well as monitor wheel speed.
The brake controller directs the electricity produced into the batteries or capacitors during braking. This ensures delivery of optimal amounts of electricity, and prevents overloading of the batteries or capacitors. Ultimately, the brake controller decides which brake system to use. If the required braking force is too great for the regenerative brakes, the brake controller activates the friction brake to avoid possible accidents.
Efficiency:-(Coordination of electrical and mechanical braking) The table shows how energy is lost in a vehicle and the percentage of energy regained from regenerative brakes. Source: Argonne National Laboratory data, SAE 2013-01-1462, and presentation.
Regenerative brakes work best at specific speeds, particularly in stop-and-go driving situations. The energy lost due to heat through friction is around 80%. Regenerative braking can recapture half that energy lost and reduce fuel consumption by 10% to 25%.
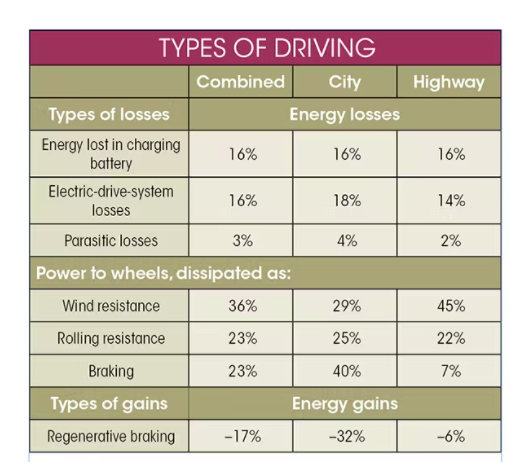
The future of efficient braking lies in hydraulic hybrids and hydraulic power assist (HPA) braking. Hydraulic hybrids replace electric motors and batteries with motor-pumps and accumulators. HPA slows down a vehicle by using its kinetic energy to power a reversible pump, which sends hydraulic fluid from a low-pressure accumulator to a high-pressure type. The pressure is achieved by compressing nitrogen gas in the accumulator as the fluid is pumped into the empty space formerly occupied the nitrogen. The decrease in hydraulic pressure in the motor-pump helps slow down the vehicle. Hydraulic hybrids have the potential to reduce fuel consumption by 25% to 45%.
Objective 3:- Make a MATLAB program which plots contour of given motor speed, torque and efficiency values. Attach the code as a .m file attach a screenshot of all the plots.
clear all
%Program for plotting efficiency contour for electric motor
x=linspace(1,1500);%speed in rad/sec
y=linspace(1,500);%Torque in Nm
%allocate motor loss constant
Kc=0.2; %copper loss
Ki=0.008%iron loss
Kw=0.00001%windage loss
C=20;%constant motor loass
[X,Y]=meshgrid(x,y);
output_power=(X.*Y);%torque x speed = power
c_1=(Y.^2)*Kc; %copper loss
i_1=(X.*Ki);%iron loss
w_1=(X.^3)*Kw;%winding loss
input_power=output_power+c_1+i_1+w_1+C;
z=output_power./input_power;
v=[0.80 0.85 0.60 0.65 0.70 0.75 0.80 0.85];
box off
grid off
contour(X,Y,z,v);
xlabel('speed(rad/sec)');
ylabel('torque(N/m)');
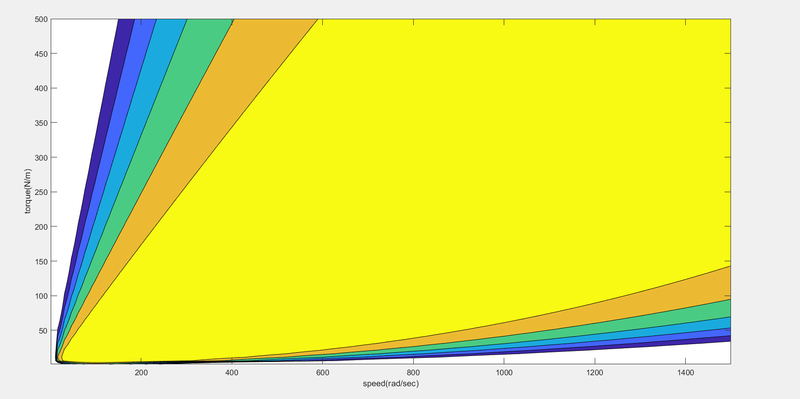
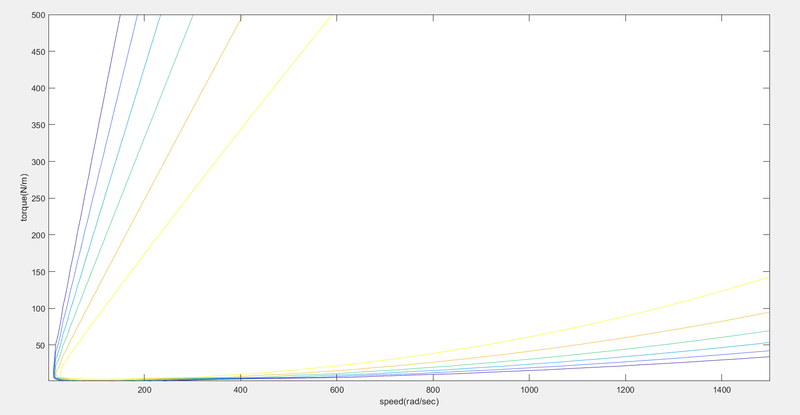
Matlab_script_link:- https://drive.google.com/file/d/1xjiRz0f8wrg85F-taJCC6k0FrAlVWsLJ/view?usp=sharing