Analyze and design a steel building to 10T CRANE as per IS standard code in TEKLA STRUCTURAL DESIGNER. Refer the attached plan and elevation. Provide bracings and moment connection for lateral stability.
Consider dead, live, equipment and wind loading. Consider the brick wall loading for 150mm thick and 1.5 KN per sq m for wall and roof cladding.
Assume wind loading basic speed as 39m/s
Report of each member to be generated and extract drawings of structural plans from the software
AIM:- To analysis and design a steel building with 10T crane load from the attachment as per IS code in TEKLA STRUCTURAL DESIGNER.
INTRODUCTION :- The industrial steel building is provided with crane for lifting heavy machine. Tekla Structural designer is used for modelling the structure by assigning steel members, and thereafter loads are applyied to model to check if it could withstand under different load conditions and combinations. Analysis and design of the model is carried out to check the serviceability, durabillty and strength of the structure.
PROCEDURE:-
- Open the TEKLA STRUCTURAL DESIGN 2022 software on the desktop. A workspace appears on the screen.
- Click on NEW to open a new file under ribbon tab. Save under new name.
- Go to SETTINGS under HOME TAB to check setting under Indian standards and also check other criteria like design settings and analysis settings. Click OK.
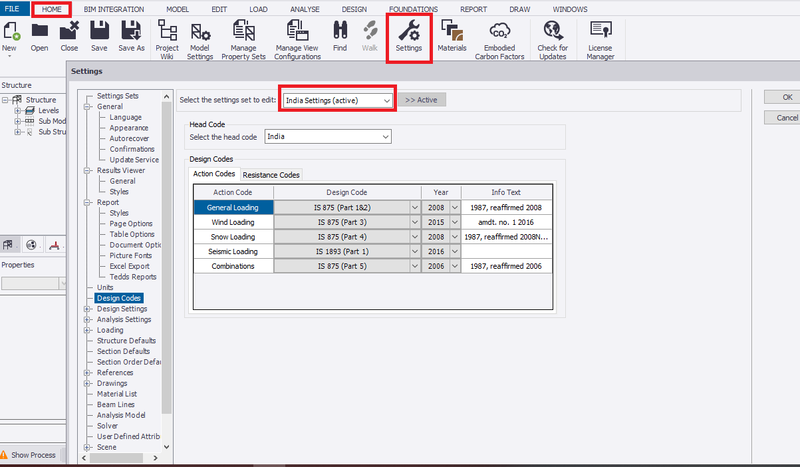
- Study the structural layout of the structure.
TO CREATE CONSTRUCTION LEVEL
- Assume foundation level to ground floor level is 0.5m.
- Go to MODEL tab. Select CONSTUCTION LEVEL. Set base level to 0m as shown below.
- As from drawing, set ground floor level to first floor level as 5m and 1st floor to top beam level as 7m.
- Height of roof, tan 18= height of roof/ (span of roof /2)
Tan 18= height of roof/ (38/2)
Therefore, Height of roof= tan 18 x (38/2)= 6.1734m
Approxmatively, take Height of roof= 6.2m
- Set construction level as shown below.
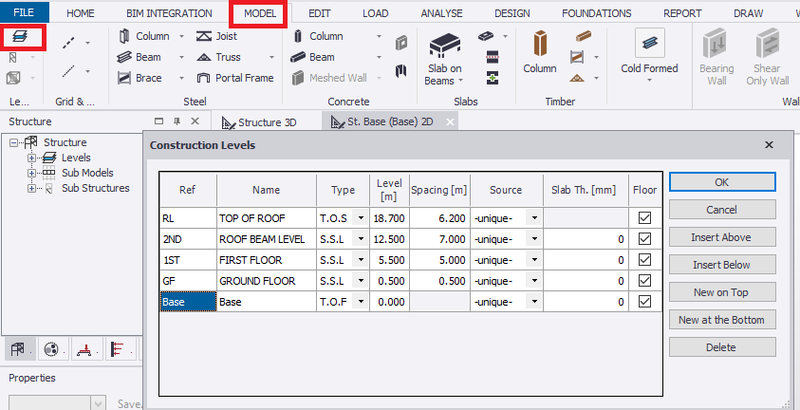
TO CREATE GRID LINE
- Select grid line from MODEL tab.
- From the ground floor drawing ,
- Add grid line by picking the first point on scene view and drag down to pick the second point.
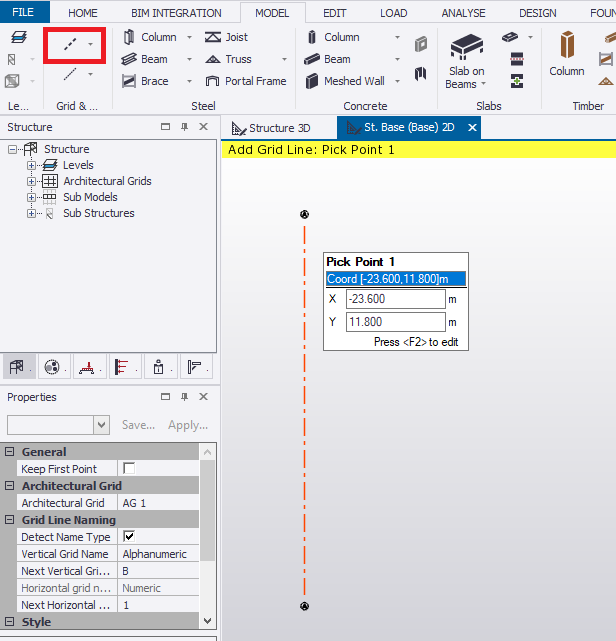
- To create parallel grid line from 1 to 16,select quick parallel grid line. Similarly, construct perpendicular grid line by selecting grid line 1 to create grid line A.
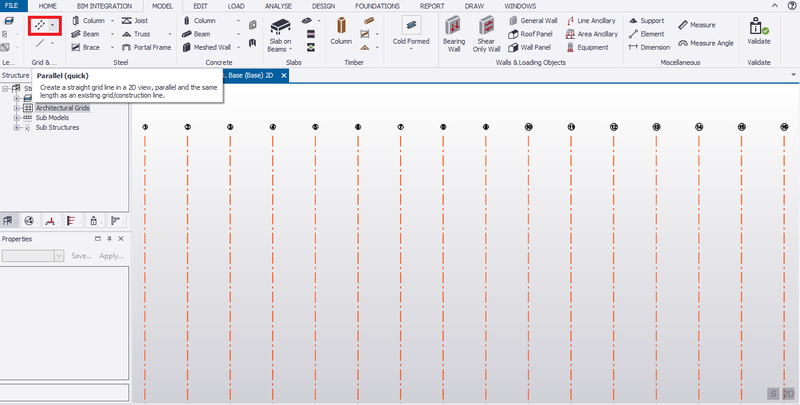
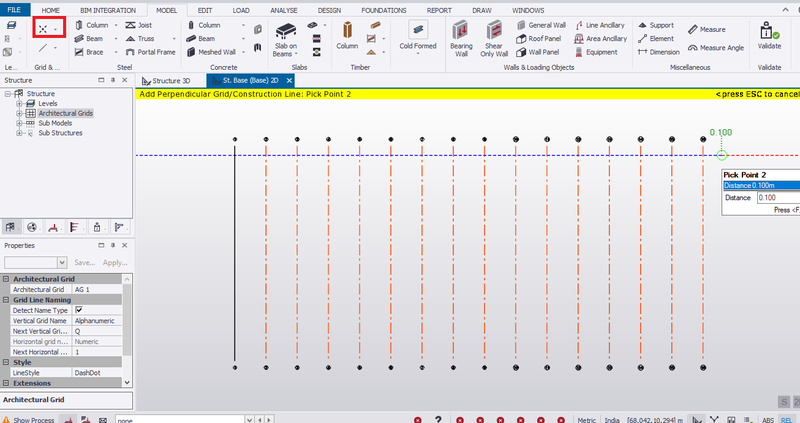
- Similarly, construct parallel grid line by selecting grid line A as reference line as shown below.
_1662971181.png)
TO MODEL CONCRETE PEDESTAL FOOTING
- Under HOME tab, select MANAGE PROPERTY SETS. Select NEW, CONCRETE COLUMN from MEMBERS. Rename to PF1.
- Set grade of concrete as M25 and size to 500mm x1000mm. Check releases as Fixed and nominal cover to 50mm.
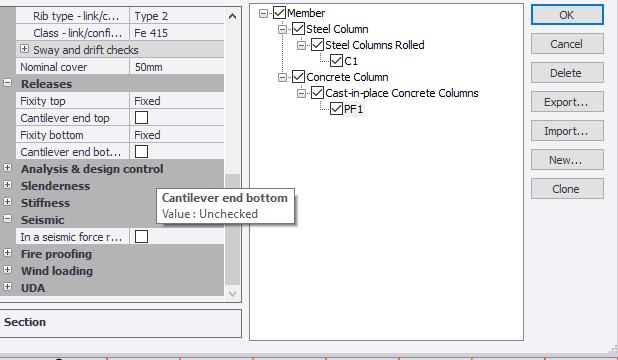
- Under MODEL tab, select concrete column.
- Select PF1 in the property window, check base level and change top level as ground floor level. Also, check other properties. Pick the point to create column position.
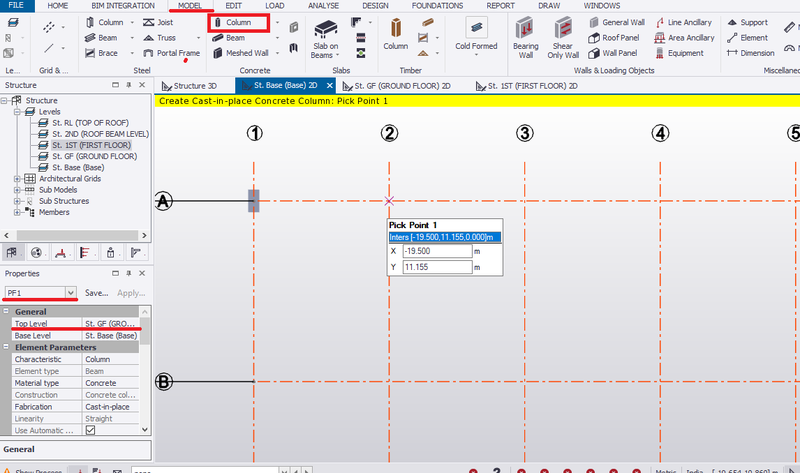
- Similarly, create columns on the position as shown below, ie, on grid line A, B, xx (between D and E) and G.
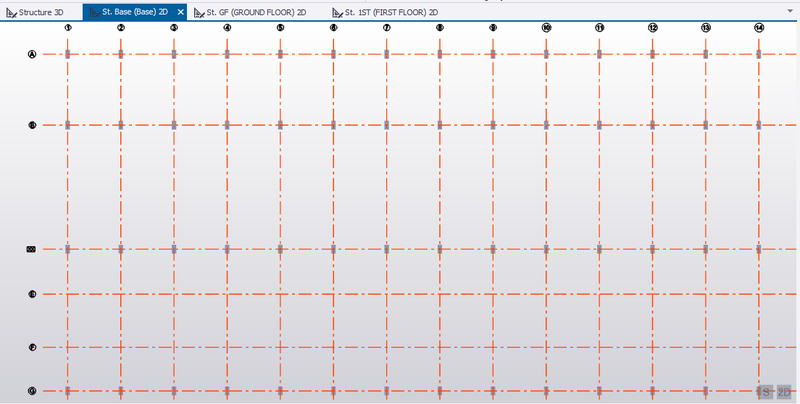
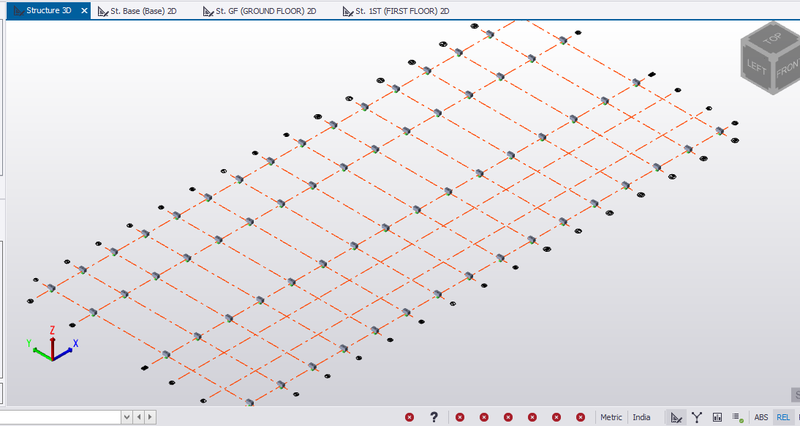
TO MODEL STEEL COLUMN
- Under HOME tab, select MANAGE PROPERTY SETS. Select NEW, STEEL COLUMN from MEMBERS. Rename to C1.
- Set grade of steel as Fe410 and steel section as MB500. Check releases, top fixity as Fixed and bottom fixity as pinned.
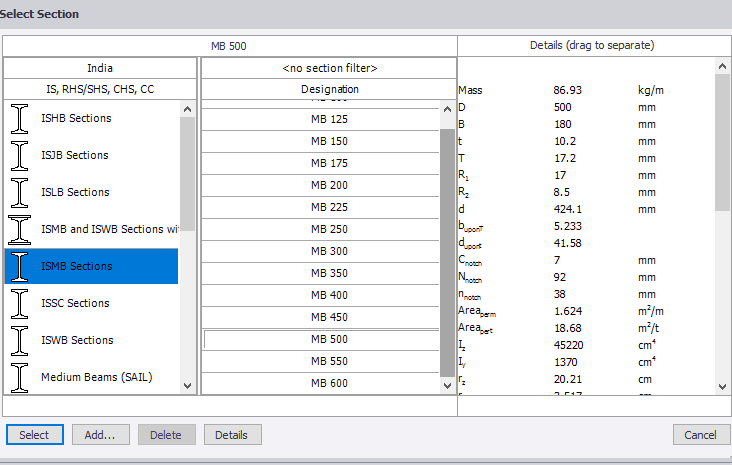
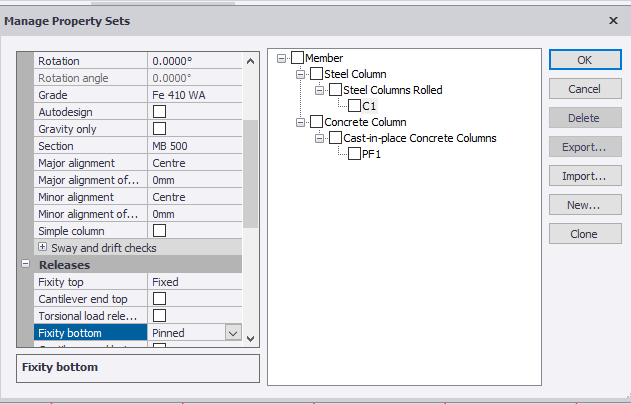
- Go to ground floor in the scene view.
- Select C1 from the property window. Change base level as ground floor level and top level as top of beam level.
- Pick the point to create steel column on grid line A and G.
- Toggle to 3D view to see column position.
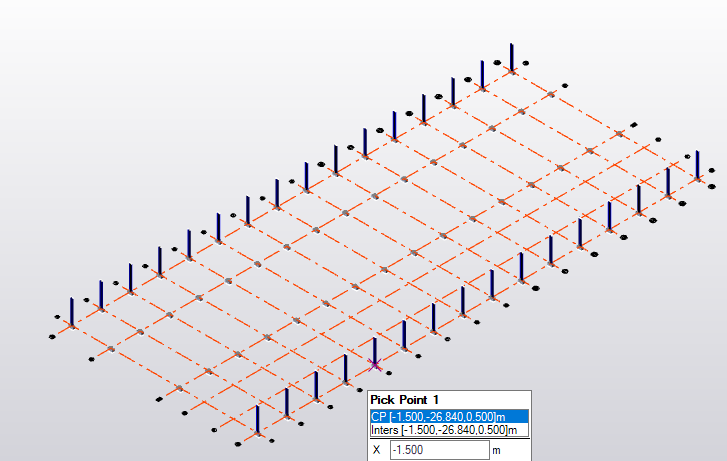
- Similarly, position of column in inside has longer columns height. Therefore, provide two more levels in the construction level as shown below.
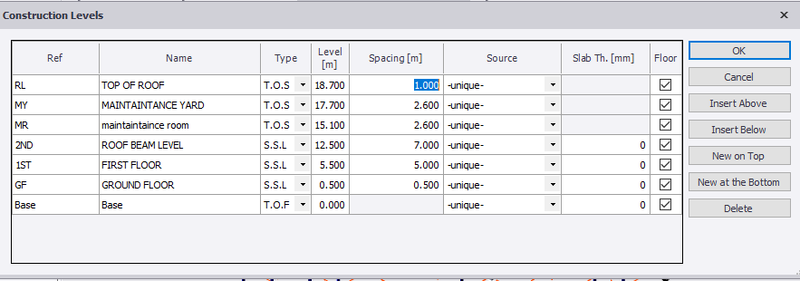
- Go to manage property sets to create another sets of column property, ie, C2 of MB 600 steel section.
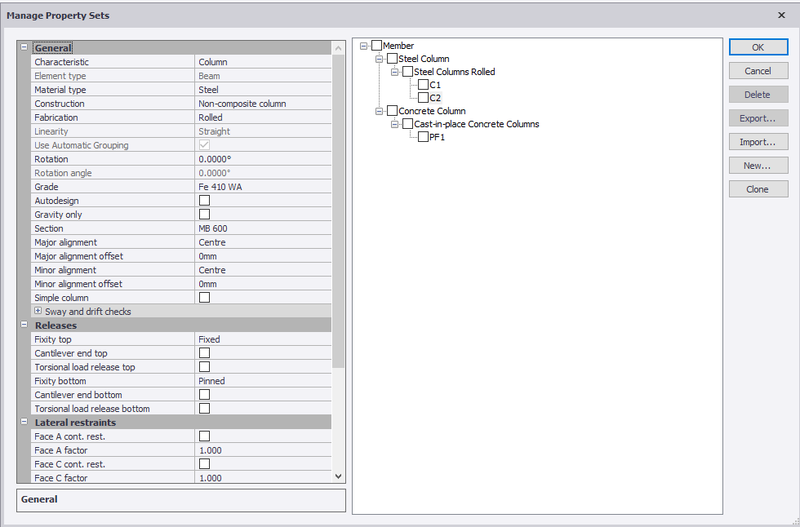
- Go to MODEL, select steel column. Select C2 in property window, change top level to Maintainance room level as shown below to provide higher column. Provide these sets of column on grid line B.
- Similarly, create columns C2 on the grid line xx from ground floor level to maintainance yard level.
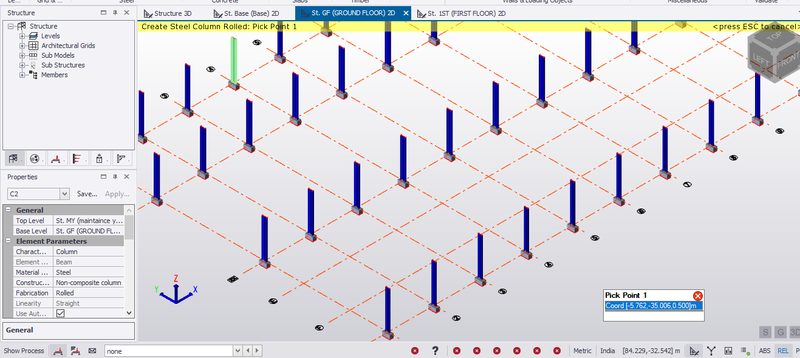
- Validate the model. hence, no error found in column modeling.
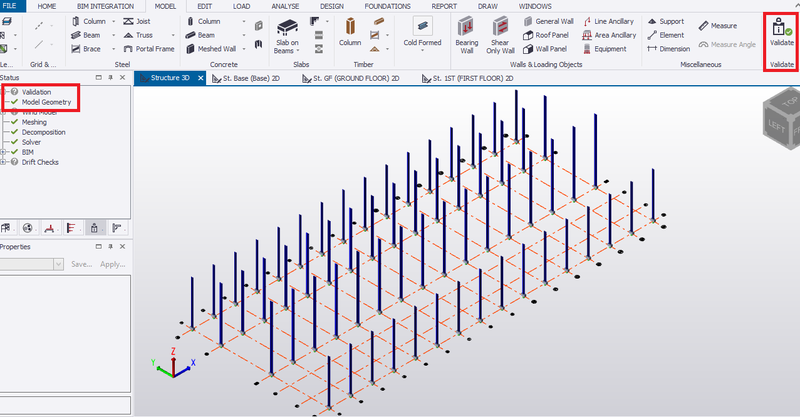
TO MODEL STEEL BEAMS
- Under HOME tab, select STEEL BEAM from MANAGE PROPERTY SETS. Rename to B1
- Set section section as MB500 and major alignment to bottom.
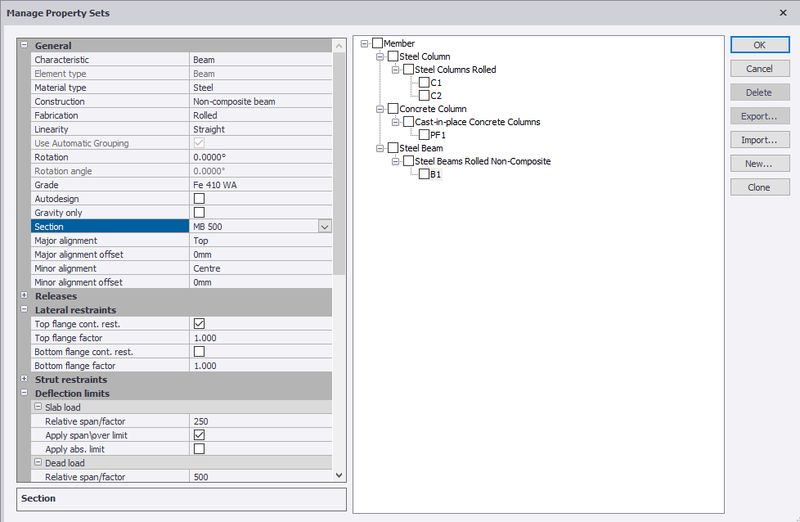
- In MODEL tab, select steel beam. Select B1 from property window.
- GROUND FLOOR
- To create steel beams in ground floor, pick column to column to create primary steel beams.
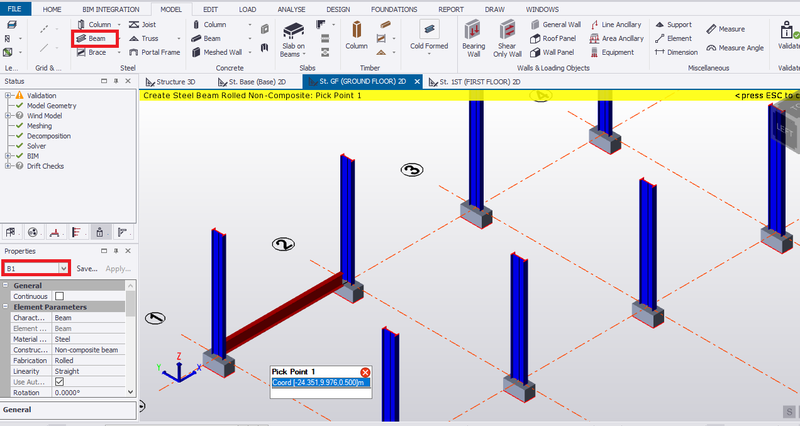
- Similarly, model primary beams from column to column as shown.
_1663069921.png)
- Construct secondary beams on the grid line between A and B by copying beams from the grid line A. On validation no error in model geometry.
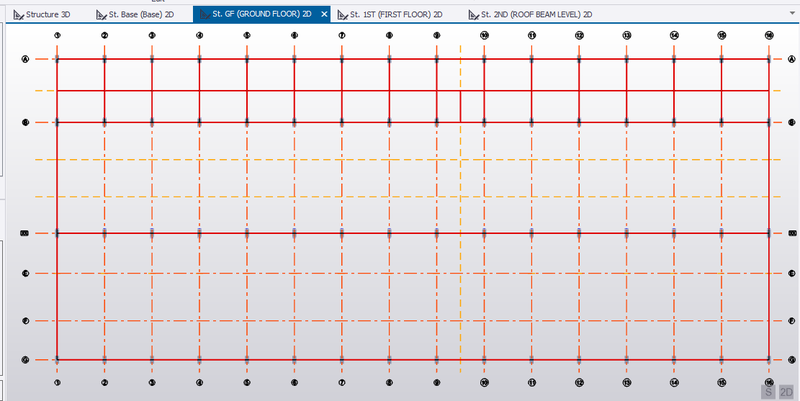
Beam supporting the staircase
- A staircase is provided 3m away from gridline 9.
- Create a quick parallel line 3m from gridline 9.
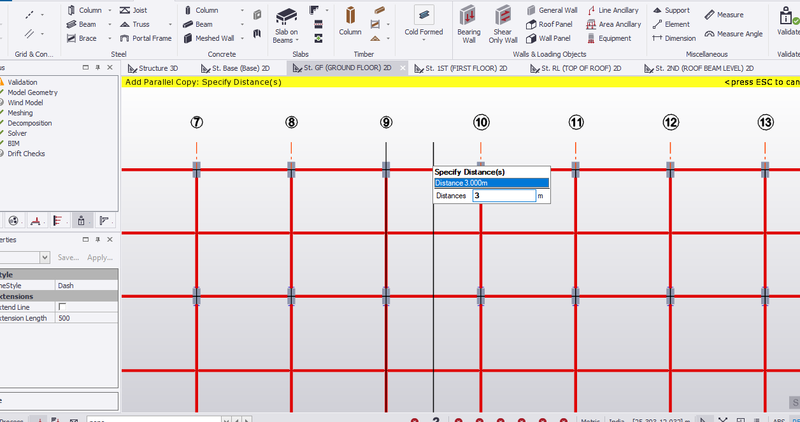
- Create a secondary beam between gridline 9 and 10 as shown below. Change property of beam to B1.
ii. FIRST FLOOR
- Go to first floor in scene view.
- Create steel beam in the first floor as created in the ground floor but no primary and secondary beams are provided from grid line B to G that is, workshop area and maintaince yard because it is an open area.
- Secondary beam B1 is provided at 6m from grid line A as shown and also another beam is provided from grid line 9 for straircase provision.
- Select beam B1 from the property window and B1 is provided to region shown below.
- Validate the model.
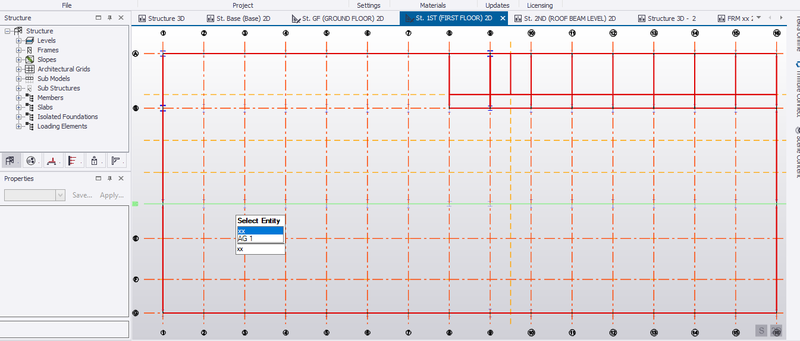
ii. SECOND FLOOR (TOP OF BEAM LEVEL)
- Go to top beam level in scene view.
- Create steel beam in the first floor as created in the first and ground floor but primary and secondary beams are provided between grid line B and G that is, workshop area and maintaince yard because it is an open area.
- Provide beam B1 on grid line A, B and G.
- Select beam B1 from the property window and B1 is provided to region shown below.
- Validate the model. No error in model geometry.
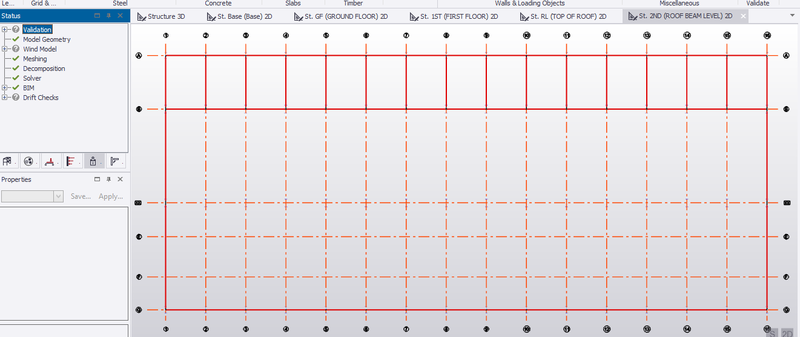
- In 3D structural scene view.
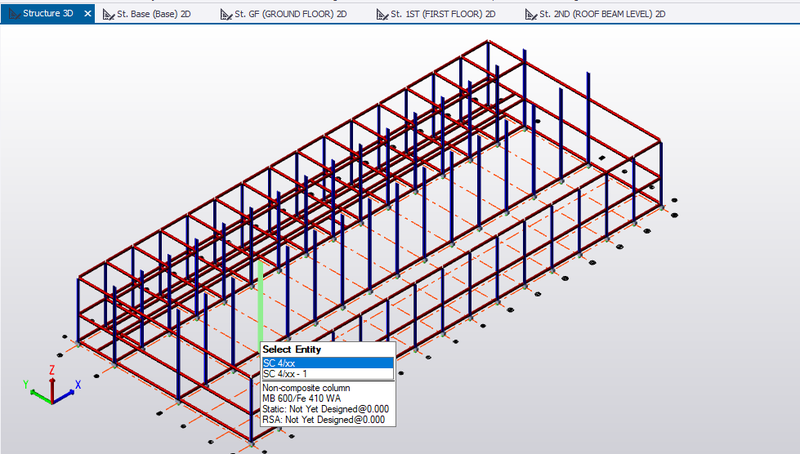
TO CREATE RAFTER BEAM
- Firstly, under model, select frames to create frames by picking the gridline.
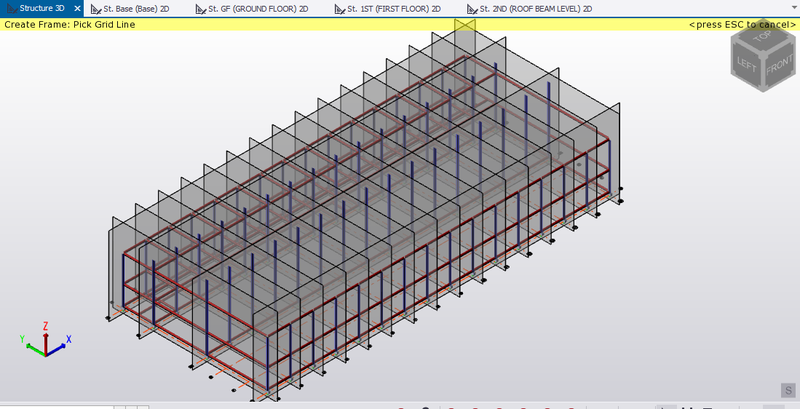
- Select frame 1 from the project window and then MANAGE PROPERTY SETS from HOME.
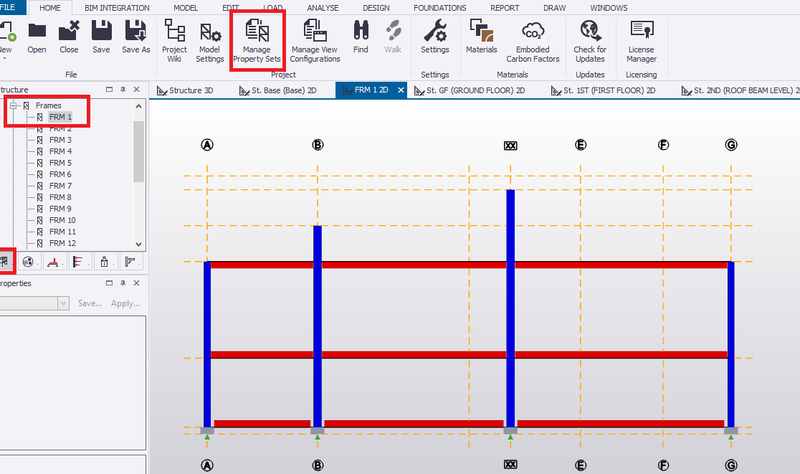
- Under manage proprty sets, set properties for rafter beam with member section of MB500 and end releases as FULLY FIXED.
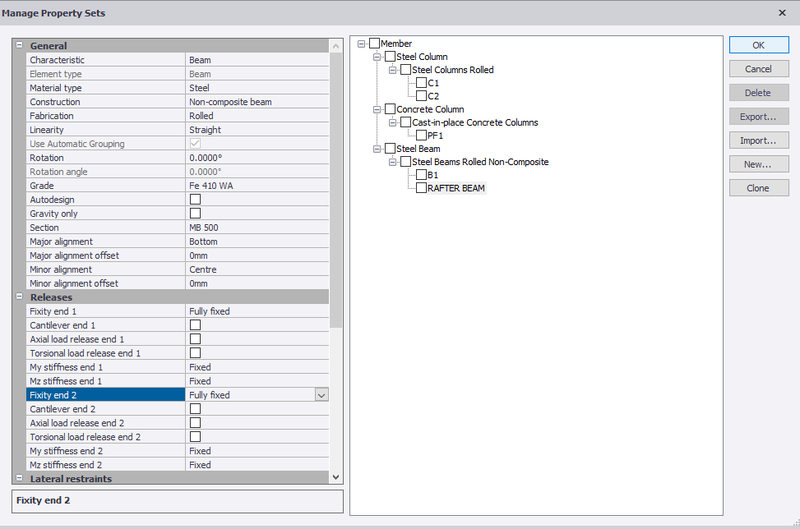
Select steel beams from MODEL tab. Select RAFTER BEAM in the property window. Pick the position of beam at each column end as shown. 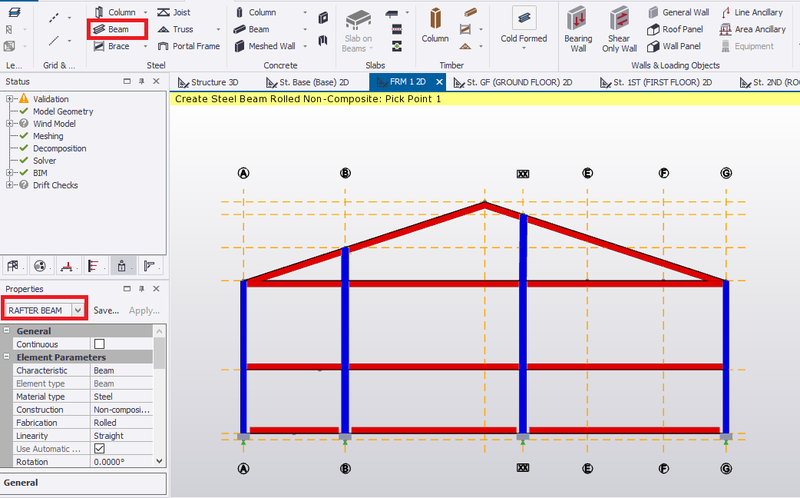
- Next, copy these rafter beams by picking the reference node to other grid line section from structural 3D view.
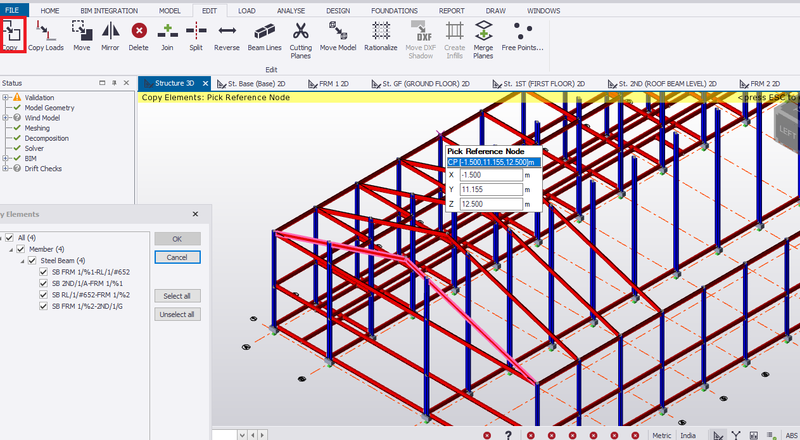
- Check frame 2 to see rafter beam.
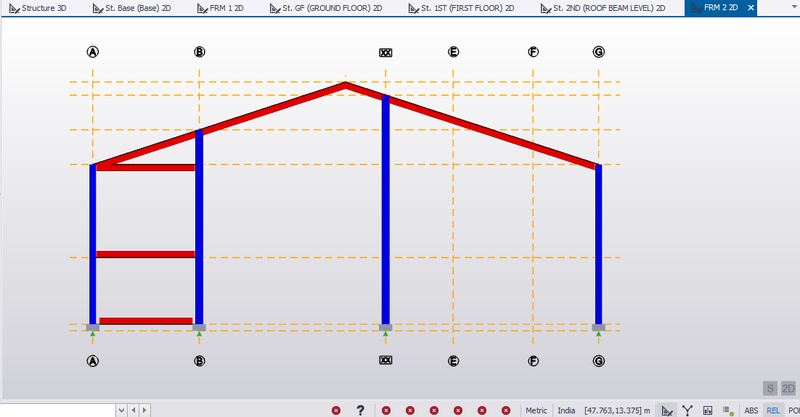
- Create ridges for roof beam. Go to manage property sets to create property for ridge beam to support roof sheets connecting from column to column.
- Set ridge section of MB350 and releases as pinned.
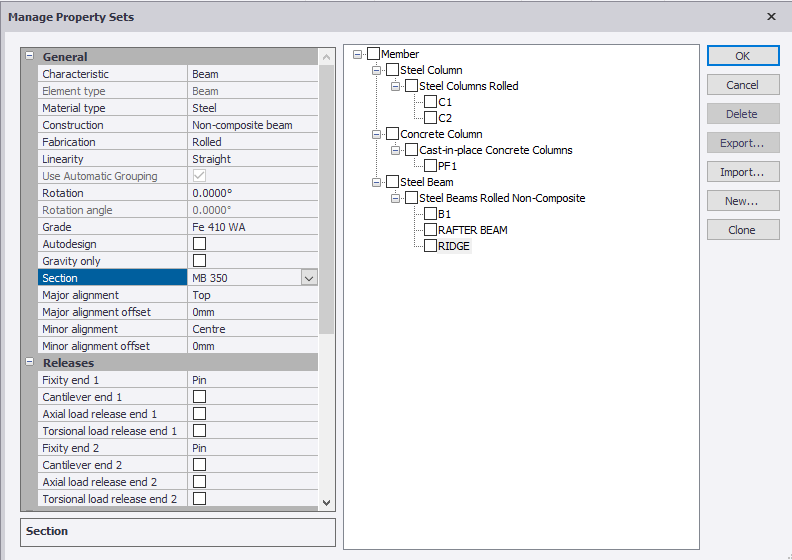
- Go to model, select steel beam. Select ridge from property window.
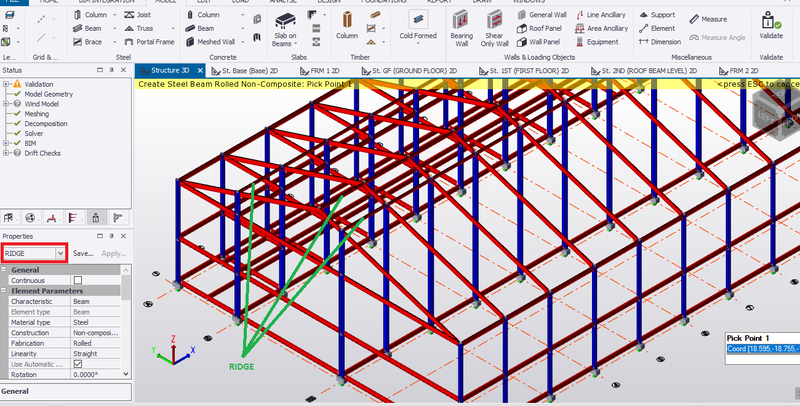
SLAB ON BEAM
- To create slabs on beam, first set property in manage property sets by selecting general slabs. Select slab type as slab on beams(RCC) and decomposition as 2 way slab.
- Provide overall depth of slab as 150mm and grade of concrete as M25. Select top and bottom reinforcement of 10mm diameter with 150 mm spacing and cover of 30mm.
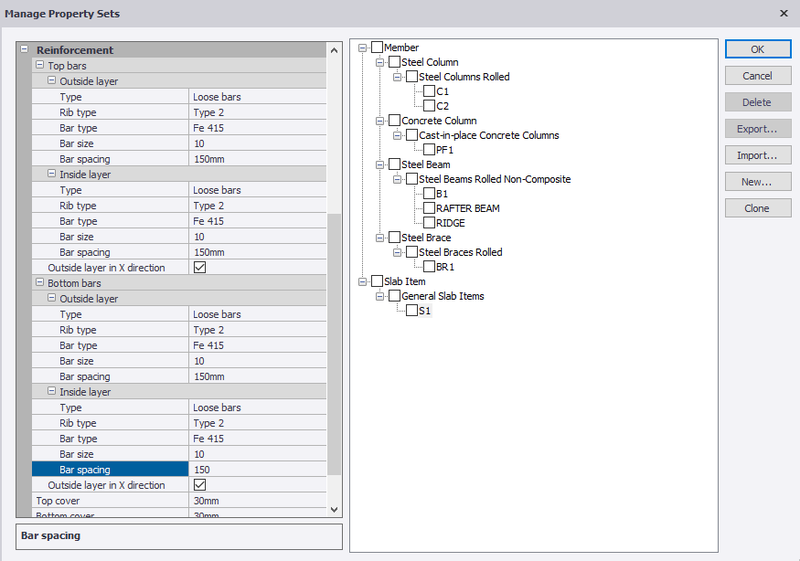
- Go to ground floor in the scene view, select slab on beam from the model tab
- Select S1 from the property window. Select the bay where slab is to be selected.
- Avoid the staircase area.
- Go to first floor in the scene view, select slab on beam from the model tab
- Select S1 from the property window. Select the bay where slab is to be selected as shown.
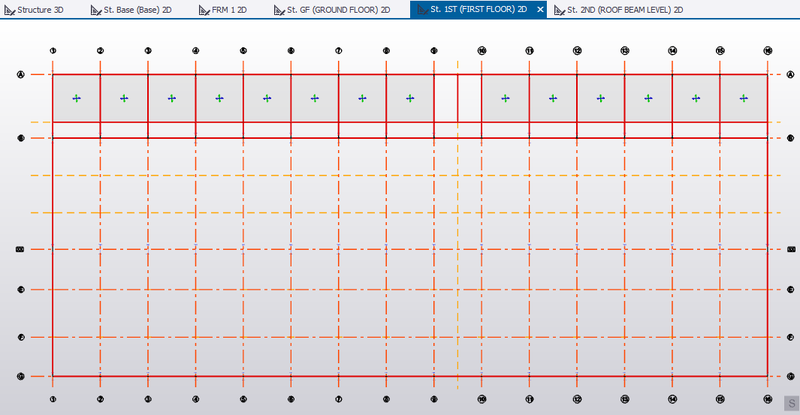
- Next, to provide 1 way slab to slabs where lx/ly>2
- Set property for 1 way slab with overall thickness 150mm and reinforcement diameter of 10mm and spacing of 150mm.
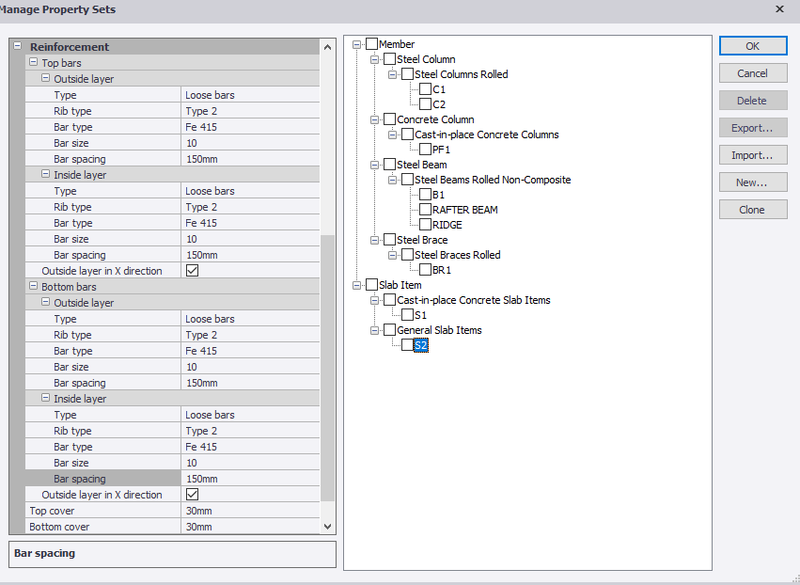
- 1 way slabs are provided as shown below.
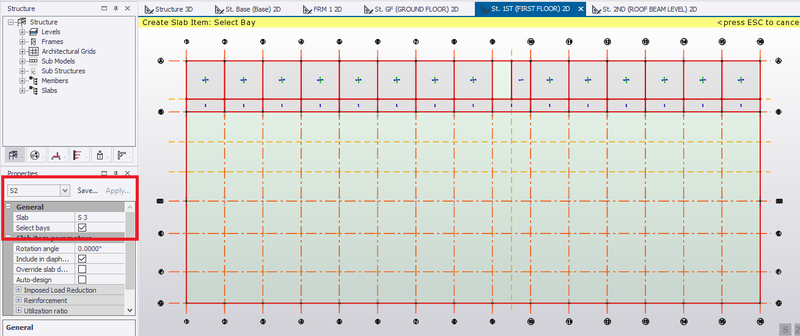
- Go to top of roof beam level in the scene view, select slab on beam from the model tab
- Select S1 from the property window. Select the bay where slab is to be selected as shown.
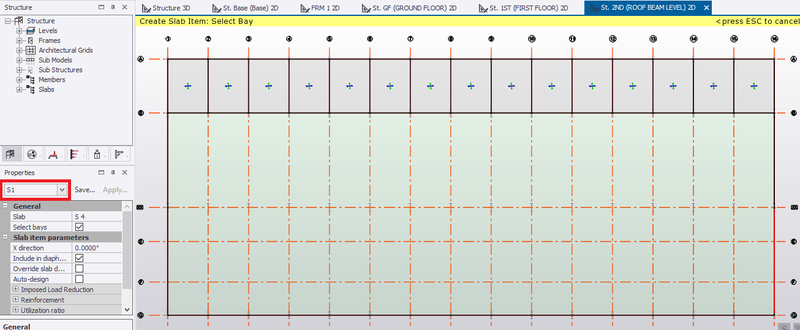
BRACINGS FOR LATERAL STABILITY
- Set property for steel braces in manage property sets by selecting steel braces from members and name it as BR1.
- Select brace section of ISA 75x75x8
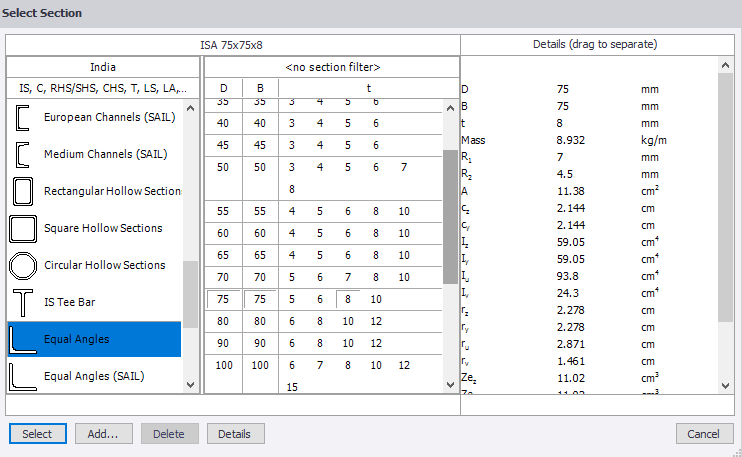
- Select frame A from the project window and provide X bracings to required position.
- Bracings are created by picking first corner of the frame and move to pick four corner in the rectangular shape to form a X bracing.
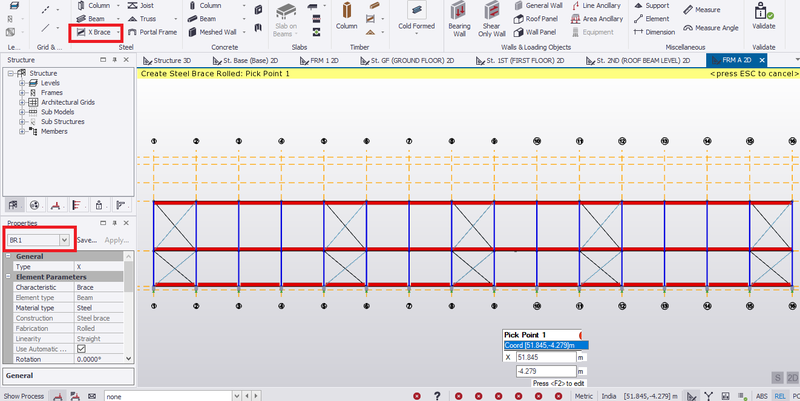
- Similarly, create braces BR1 for frame G.
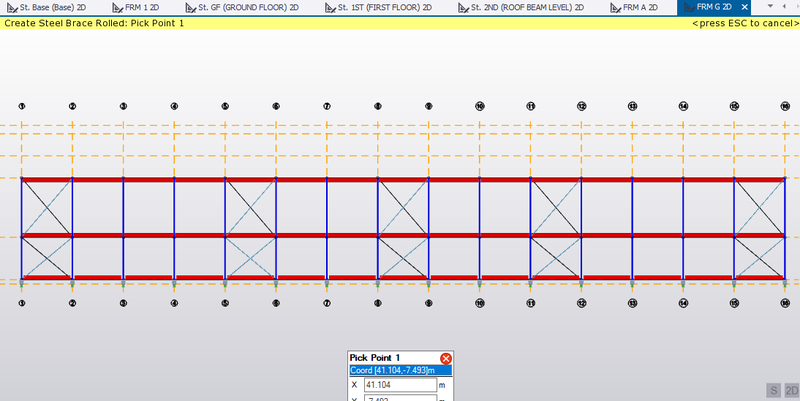
TO CREATE WALL PANEL
- Wall are created by selecting wall panel ribbon from the model tab.
- Pick the corner position of the frame A and then pick the opposite corner position of frame,ie, pick the 4 corners of the frame to form wall panel.
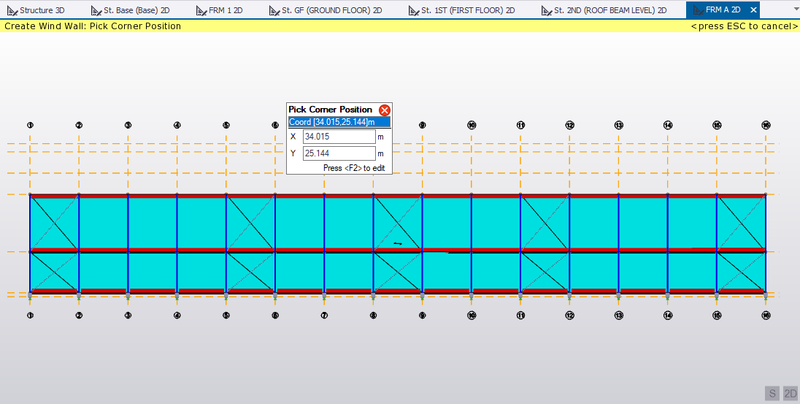
- Similarly, create wall panel for frame G, 1 and 16
WALL PANEL FOR FRAME G
WALL PANEL FOR FRAME 1
WALL PANEL FOR FRAME 16
ROOF PANEL
- To create roof panel, select the roof panel ribbon from model tab.
- Pick the corners of the roof to create roof panel.
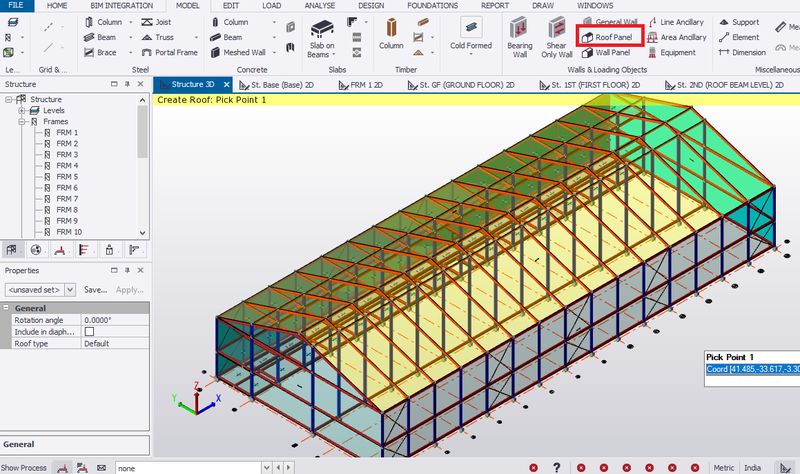
CRANE LOAD SUPPORT
- Go to roof beam level in the scene view to provide Brackets connecting from column to support crane
- Select parallel construction line 1m from grid line B and xx.
- Select steel beam from model tab with steel section MB 500.
- Pick the point on the grid line B to 1m far construction line to create cantilever beam(ie, brackets) which is fixed to columns.
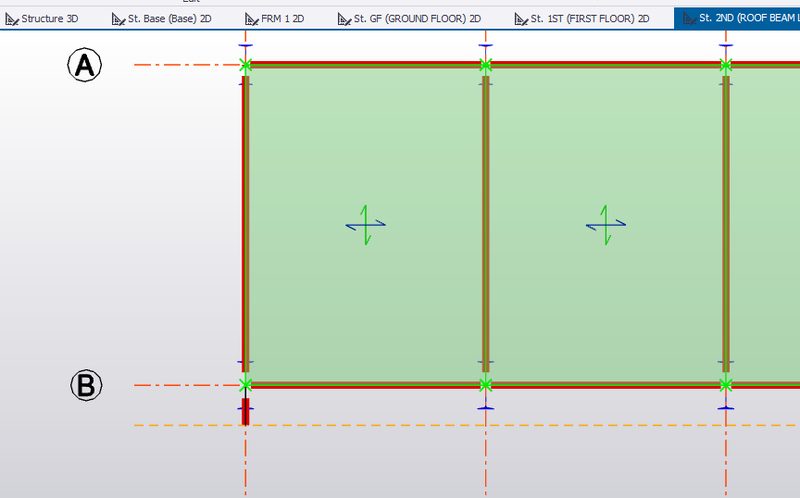
- Double click the beam to change the property. Under releases at end 2, tick on cantilever end
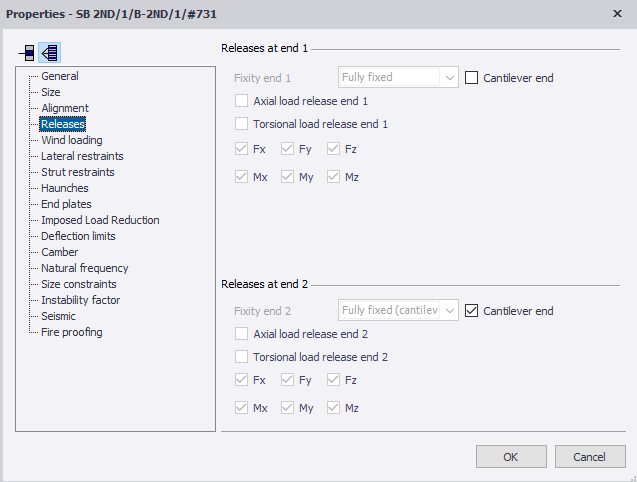
- Validate the model. Hence ,no error in model
- Copy this cantilever beam to rest of the column ends from grid line 1 to 16.
- End of the gantry girder, ie, the cantilever beams are mirrored from grid line xx
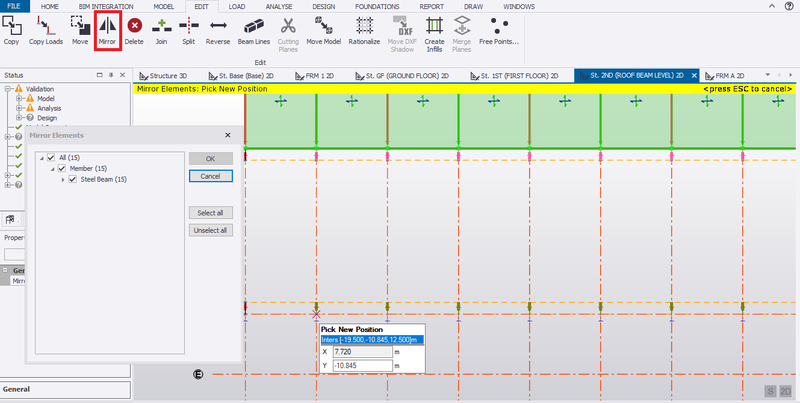
- Validate the model. Hence no error
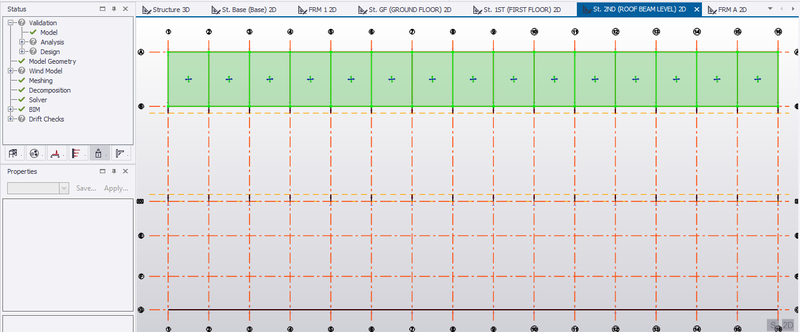
LOADING
- Create Loadcases under the load tab.
- Add wind load and seismic load along with dead load, live under loadcase. Click ok.
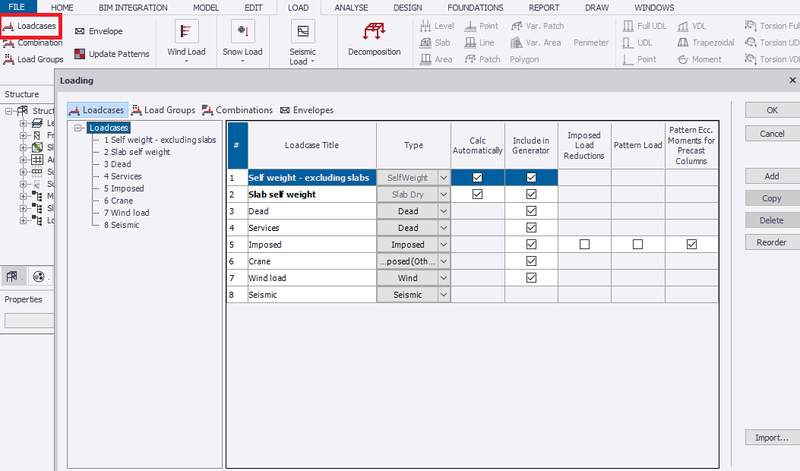
- Then generate load combination.Click next.
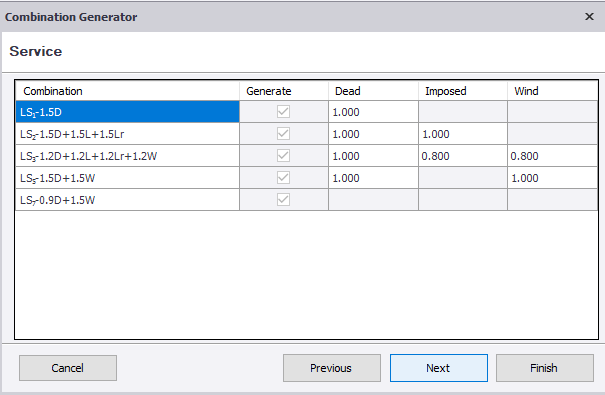
- Therefore, load combinations are generated.
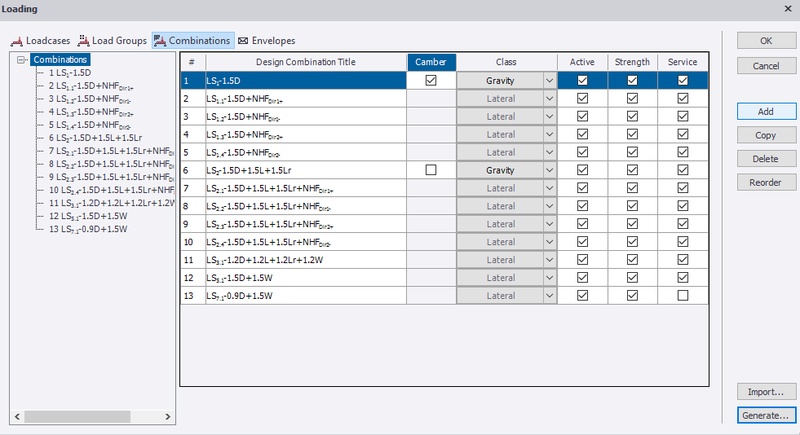
DEAD LOAD
- Data for dead load are calculated in MS excel
- Consider, Floor Finish of 50mm thickness for both first and ground floor.
- Therefore, floor finsh load= Thickness of finish x density of concrete =0.05 x 24= 1.2kN/m^2.
- Given, brick wall thickness of 150mm and consider unit weight of brick as 20 kN/m^2 as per IS 875(Part1)
- Calculation for Brickwall loading= unit weight of brick x brickwall thickness x floor height
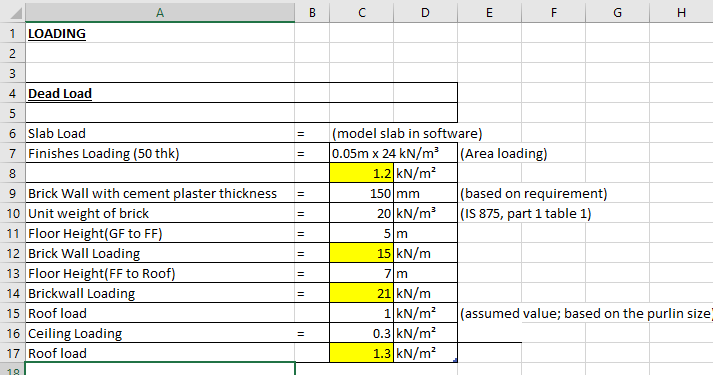
Ground floor
- To apply dead load(ie, floor finish load) on ground floor, select dead from loading window.
- Select area ribbon from load tab and change load intensity to 1.2kN/m^2.
- Then pick the area where load is to be applied.
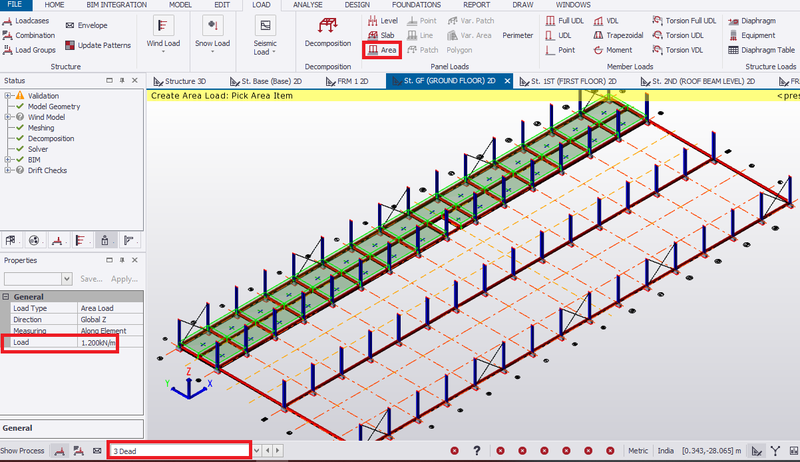
- To apply brick load on the beam, select the full UDL from the load tab.
- Apply a load of 15kN/m on the walls where the beams lay below
- Also apply load of 15 kN/m to inside wall as shown below
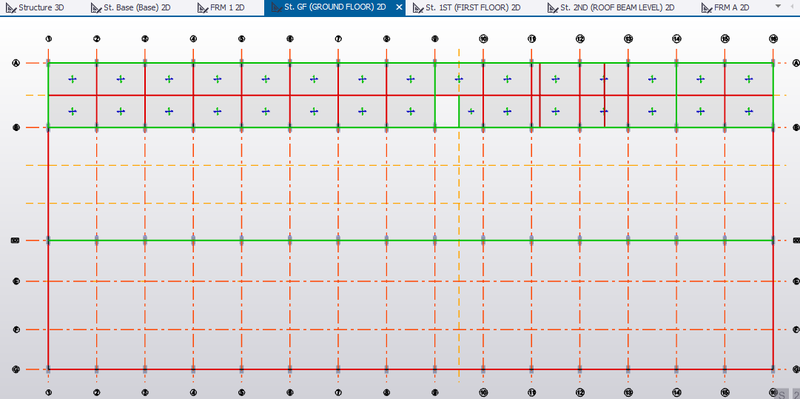
First floor
- To apply dead load(ie, floor finish load) on first floor, select dead from loading window.
- Select area ribbon from load tab and change load intensity to 1.2kN/m^2.
- Then pick the area where load is to be applied.
FLOOR FINISH LOAD ON SLABS
- To apply member load/ brick load of 21 kN/m on the floor is shown and no error in loading during validation.
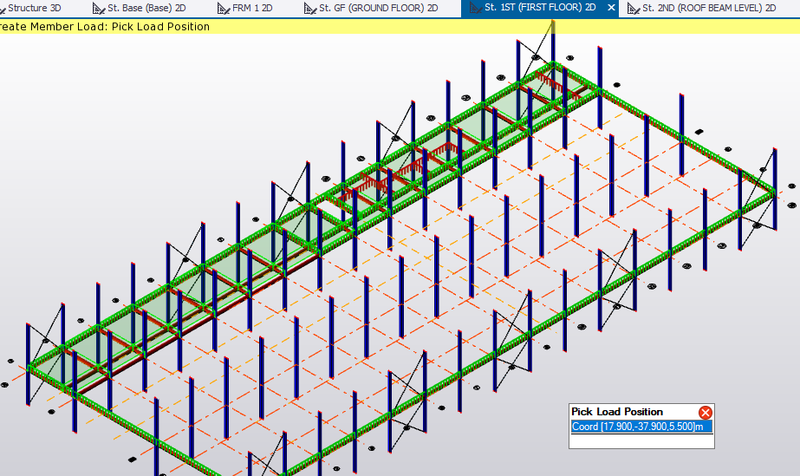
Top of Roof Beam floor
- To apply floor finish load, select dead from loading window.
- Select area ribbon from load tab and change load intensity to 1.2kN/m^2.
- Then pick the area where load is to be applied.
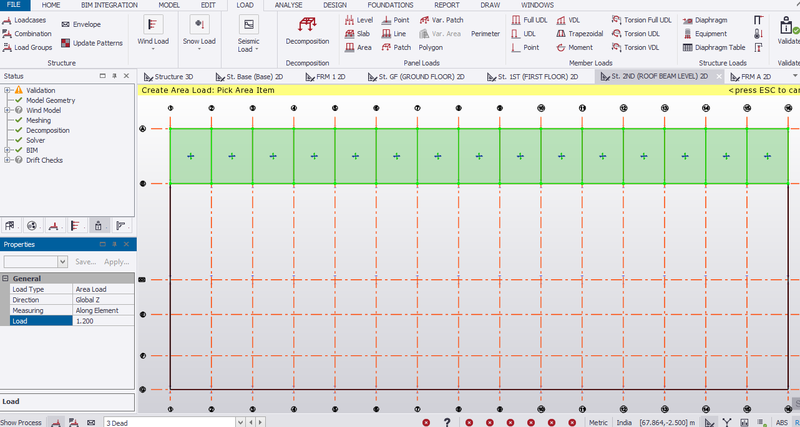
Roof load
- Go to structural 3D in the scene view. Select dead in the loading window
- Pick the roof panel to provide a roof load of intensity 1.3kN/m^2 on the roof.
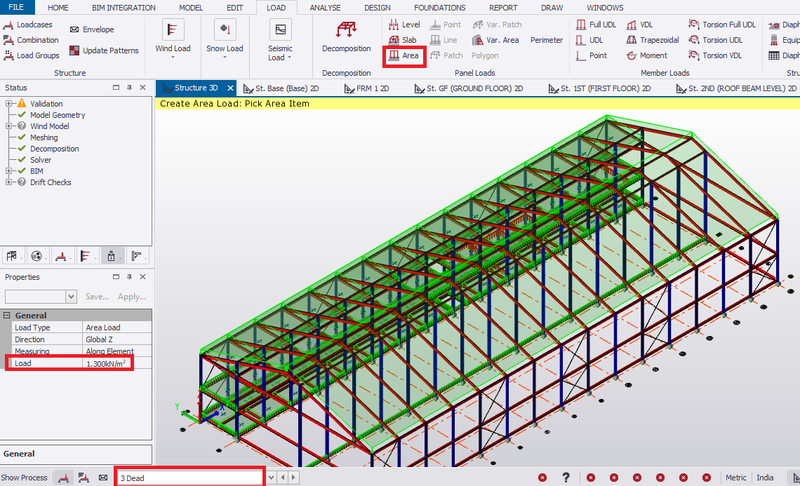
LIVE LOAD
- Data for live load in each floor is noted in MS excel which are refered from IS 875 part2
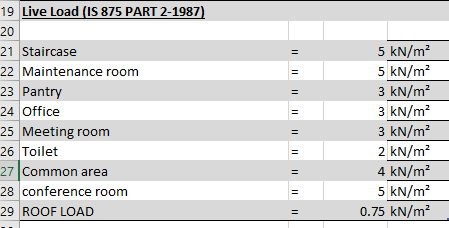
Ground floor
- Select imposed load from the loading window
- Select area load from ribbon tab. Change the load intensity to 5kN/m^2 for maintenance room and apply from grid 1 to 8 on referring from drawings and values shown above.
- Similarly, apply imposed load intensity of 3 kN/m^2 for office and likewise for all rooms.
_1663315333.png)
First floor
- Select imposed load from the loading window
- Select area load from ribbon tab. Change the load intensity to 5kN/m^2 for conference room and apply from grid 10 to 16 on referring from drawings and values shown above.
- Similarly, apply imposed load intensity of 4 kN/m^2 for rest of the slabs.
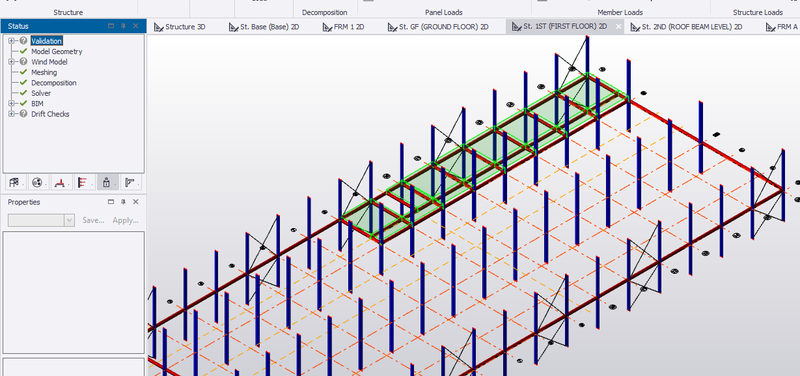
Roof floor
- Select imposed load from the loading window
- Change the load intensity to 2kN/m^2 and apply from grid 1 to 16.
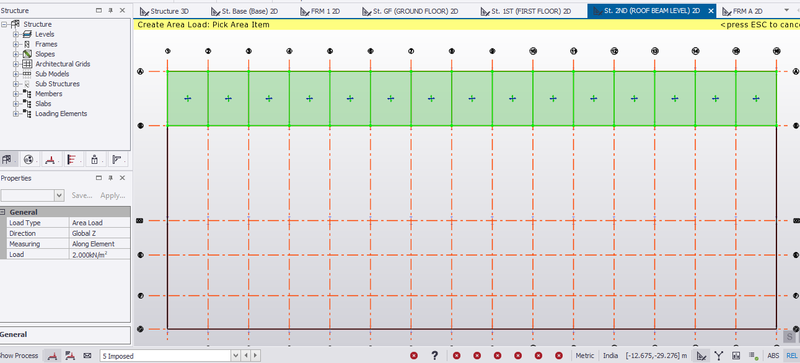
Roof load
- Go to 3D view in scene view. Turn on the roof panel.
- Apply an imposed load of 0.75kN/m^2 to the roof panel.
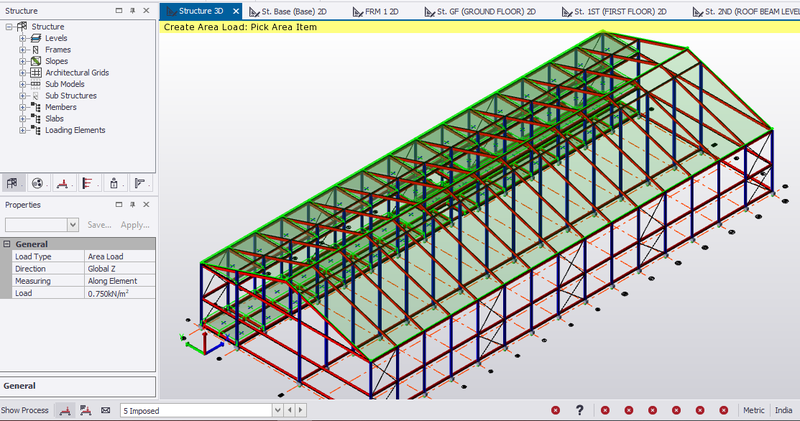
CRANE LOAD
- Design of gantry girder for 10T crane load.
- Generate manual calculations for crane loading.
- Given Crane capaity = 100kN
- Consider
- Weight of crab = 35 KN
- Number of wheels = 4
- Wheel base = 3m
- Distance between c/c of gantry rail =14m
- Number of wheels on each side = 2
- Weight of the crane = 160 kN
- c/c distance between two column = 6 m
- Maximum hook approach =1m
- Max. wheel load
- Max concentrated load on the crane = crane capacity+ weight of crab = 100+35 = 135kN
- Self weight of crane will act as UDL= 160/14 = 11.5 kN/m
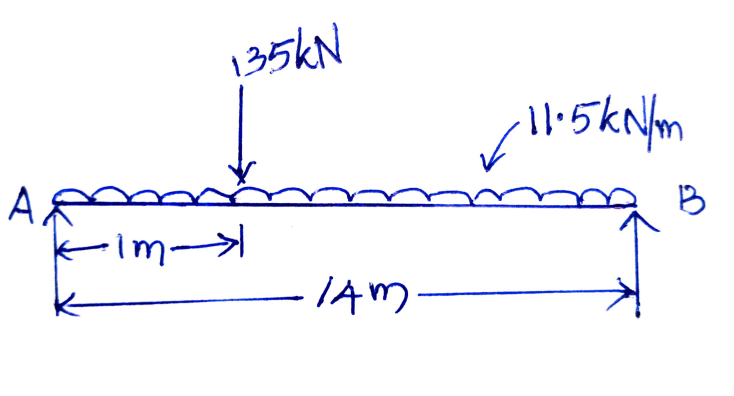
Taking moment about B,
(11.5 x 14x 7) + (135 x 13)= RA x14
RA=205.86kN
Taking moment about A,
(11.5 x 14x 7) + (135 x 1)= RA x14
RB=90.15kN
- Reaction from crane girder is disturbed equally on 2 wheels at the end of crane girder
- Maximum wheel load on each wheel =RA/2 = 205.86/2= 102.93 kN
Assume self weight of gantry girder = 1.5 kN/m
Assume self weight of rail = 0.3 kN/m
Total dead load = self weight of gantry girder + self weight of rail =1.5+0.3 =1.8kN/m
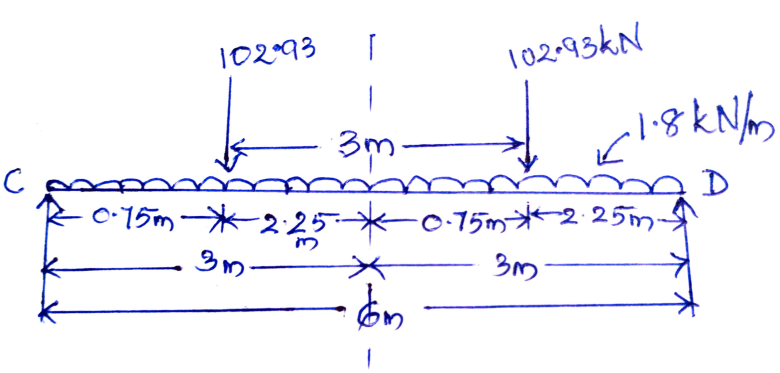
taking moment about D
Rc x6= (102.93x2.25)+ (102.93 x(3+2.25))
Rc =128.67 kN
Taking moment about C
RD x6= (102.93x0.75)+ (102.93 x(3+0.75))
RD =77.2 kN
Rc +RD= 128.67+77.2 =205.9kN
Bending Moment (BM) under wheel due to Live Load = 2x RD =2 x 77.2 = 154.4 kNm
BM due to impact= 10% increase due to MOT = 0.1 x154.4= 15.44 kNm
BM due to Live Load and impact =154.4 +15.44 = 169.84 kNm
BM due to Dead load = wl2/8 = (1.8 x6 x6)/8 = 8.1 kNm
Maximum BM = 169.84+ 8.1 = 178 kNm
For max. shear force, one of the wheel should be at the support
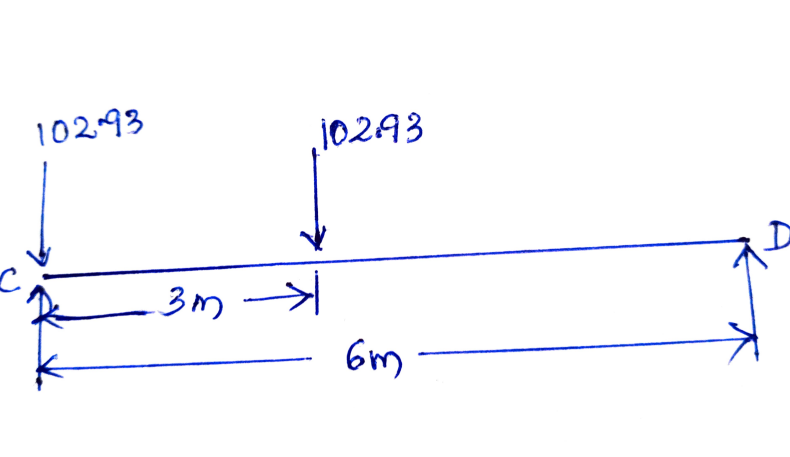
At D, Rc x 6 = (102.93 x 3) + (102.93 x6)
Rc = 90.8 kN
Max. shear force due to wheel load= 154.4 kN
Lateral force transverse to rail = 5% of weight of crab and weight lifted
= 0.05 x( 35+100) = 6.75kN
Lateral force on each wheel = 6.75/2= 3.375 kN
Horizontal reaction due to lateral force by proportion at C
= lateral force x reaction at C due to vertical load/ maximum wheel load due to vertical load
=3.375 x 77.2/102.93 = 2.53 kN
At D, load= 6.75- 2.53= 4.22 kN
Bending Moment due to lateral force by proportion at C =3.375x 154.4/102.93= 5.063 kNm
- After calculation, go to roof beam level in scene view.
- Select Crane load from loading window.
- Select the point load from the load tab.
- Under the property window, change load type to Nodal load and coordinates to (102.9,5, 154) as shown below.
- Then pick the end of all the cantilever beam to apply load.
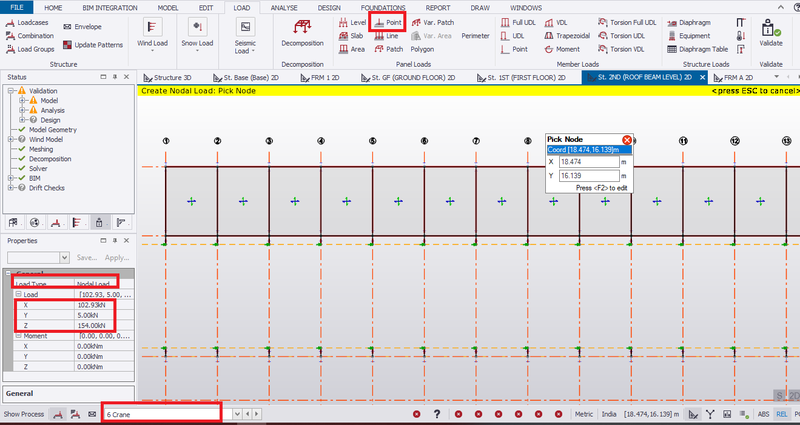
- Check in 3D view to see load acting at cantilever ends
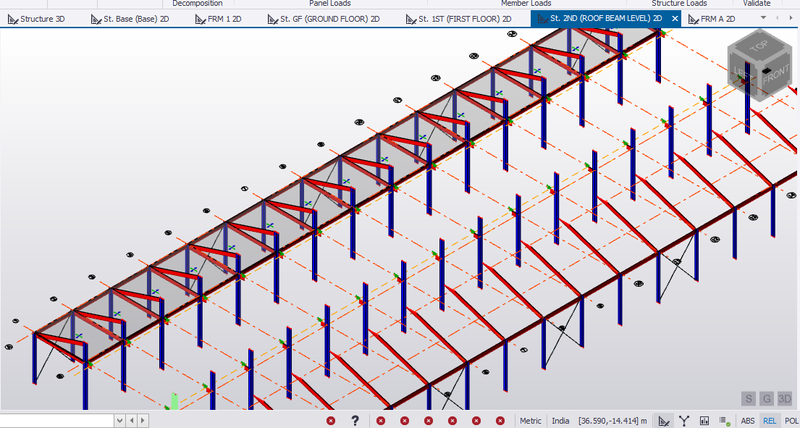
WIND LOAD
- Under loadcase, create wind load as shown below.
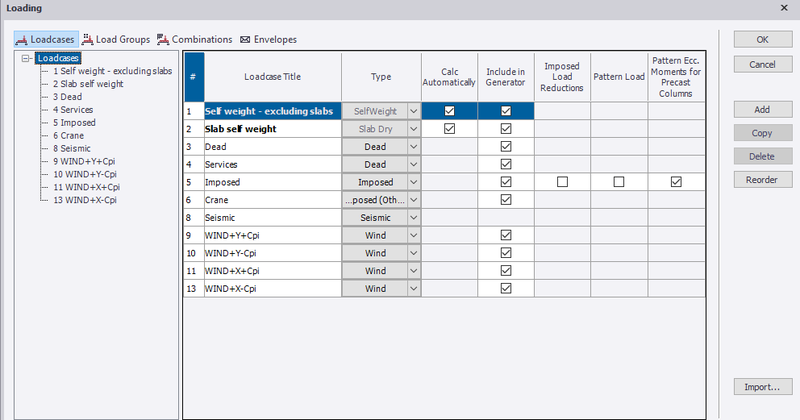
- Wind load calculation is based on IS 875, part 3
- Given basic wind speed as 39 m/s.
- Consider,
- Life of the building =50 years
- Class of the structure= A
- Total length of the structure, l= 42 m
- Total width of the structure,w = 38 m
- Height of the structure, h= 18.7m
- Therefore, l/w= 1.105, h/w= 0.5
Step 1:- External pressure Coefficient, Cpe
As per IS 875-3, Table 5
- Building height ratio=1/2
- Building plan ratio=1<1.11<1.5
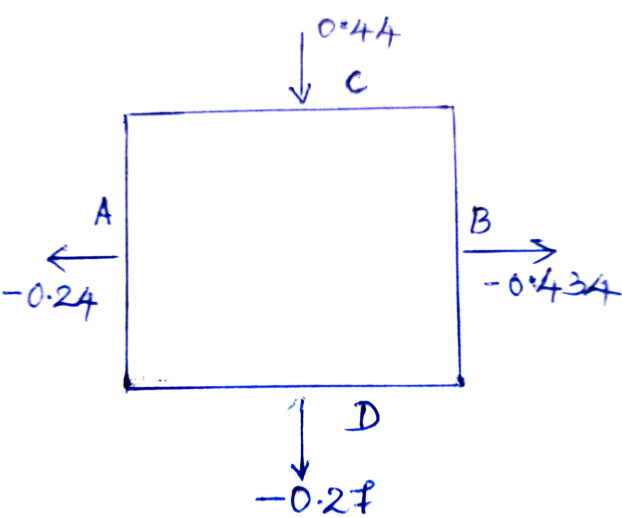
Step 2:- Find factors (k1,k2,k3,k4)
- From table 1 for wind speed= 39m/s, k1=1
- From table 2 with terrain category 2 and class of building A
- Building height= 18.7m
- For 15m and 20m tall building, k2 value is 1.05 and 1.07 respectively.
- Therefore, 16.88 m tall building, k2= 1.065 (on interpolating)
- From Cl. 6.3.3, Topography Factor, k3= 1
- From Cl 6.3.4, Importance Factor, k4= 1.15 (for industrial building)
Step 3 :- To calculate Design Wind Speed (from Cl 6.3)
Vz= Vb x k1 x k2 x k3 xk4= 39x 1 x 1.065 x 1 x 1.15 , Vz= 47.77 m/s
Step 4 :- Design wind Pressure (from Cl 7.2)
Pz = 0.6 x Vz^2 =0.6 x 47.77^2 = 1369.18 N/m^2
Pz =1.37 kN/m^2
Step 5 :- Wind direction (upto roof level)
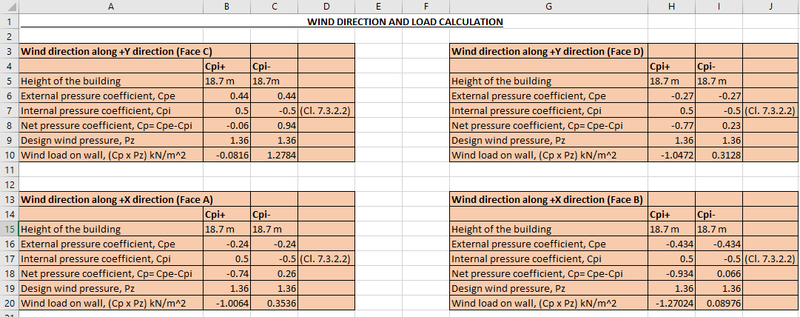
a. Wind+Y +Cpi
- In structural 3D scene view, select Wind+Y+Cpi from loading window.
- Select Area from load tab. Under property window, change load direction to Y and load intensity to -0.082kN/m2. Pick frame A as load area to apply the load
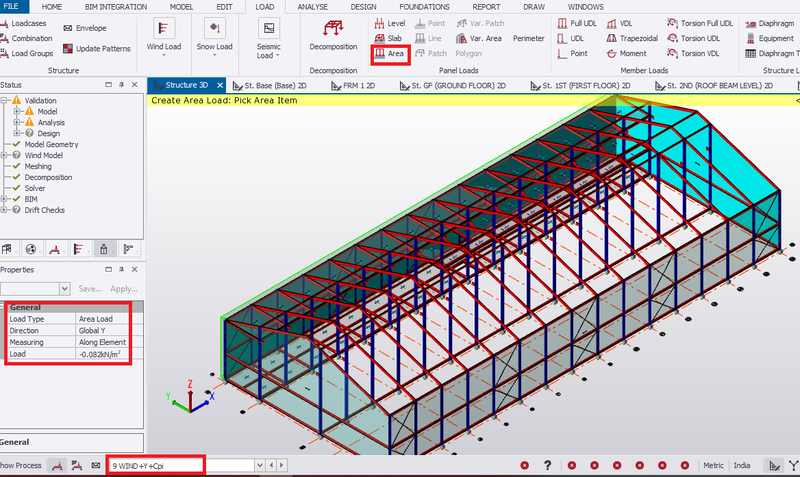
- Similarly, apply a +Y direction load along frame G with a load of -1.05kN/m2 (ie, face D as shown in table above) .
- Next, to apply internal pressure along X direction
- Apply a internal pressure of -1.01kN/m2 at frame 1 along -X direction ie, face A.
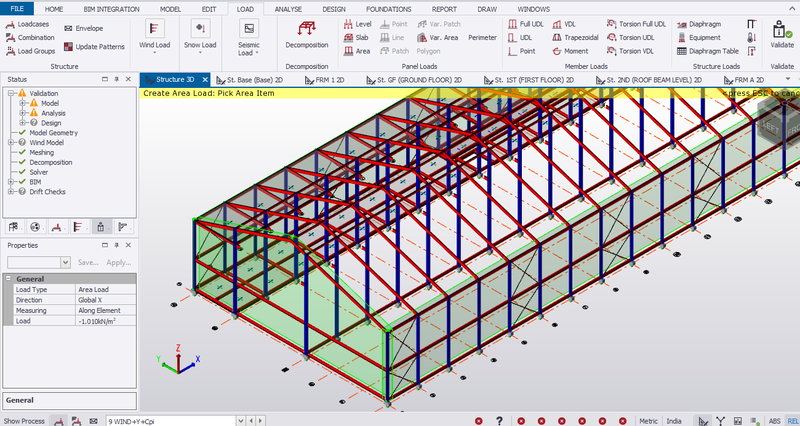
- Similarly, apply a load of 1.3kN/m2 at frame 16 along +X direction (face B)
- Therefore, load distribution for Wind+Y+Cpi is shown below.
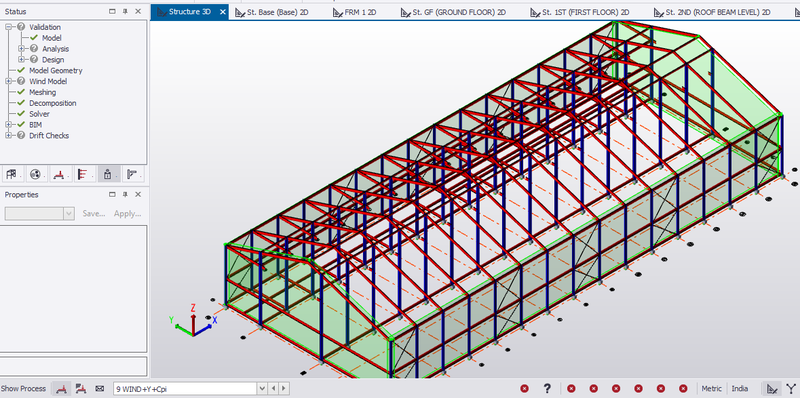
b. Wind+Y -Cpi
- In structural 3D scene view, select Wind+Y-Cpi from loading window.
- Select Area from load tab. Under property window, change load direction to Y and load intensity to 1.3kN/m2. Pick frame A as load area to apply the load
- Similarly, apply a +Y direction load along frame G with a load of 0.32kN/m2 (ie, face D as shown in table above) .
- To apply internal pressure along X direction of -1.01kN/m2 at frame 1 along -X direction ie, face A.
- For face B, apply an internal pressure of 0.09kN/m2 along +X direction
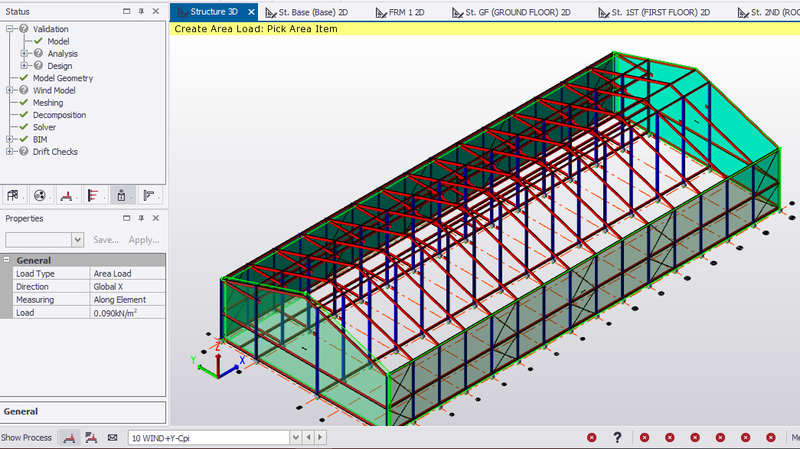
c. Wind+X +Cpi
- In structural 3D scene view, select Wind+X+Cpi from loading window.
- Select Area from load tab. Under property window, change load direction to X and load intensity to -1.01kN/m2. Pick frame 1 (ie, face C) as load area to apply the load
- Similarly, apply a X direction load along frame 16 with a load of -1.3 kN/m2 (ie, face D as shown in table above) .
- To apply internal pressure along Y direction of 0.09kN/m2 at frame A along Y direction ie, face A.
- For face B, apply an internal pressure of -1.05kN/m2 along -X direction
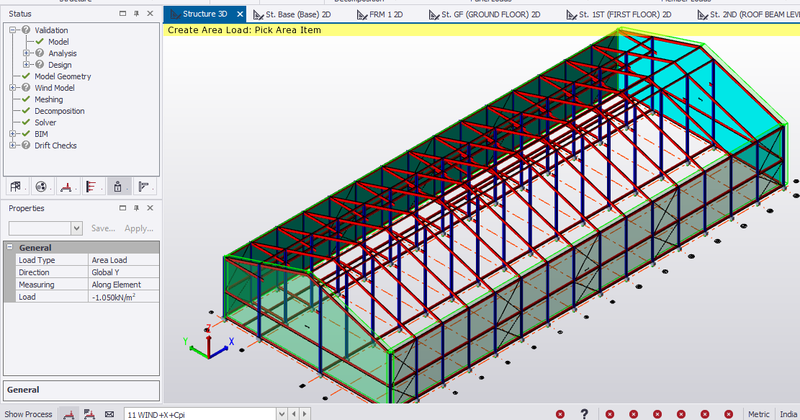
d. Wind+X -Cpi
- In structural 3D scene view, select Wind+X-Cpi from loading window.
- Select Area from load tab. Under property window, change load direction to X and load intensity to 0.36kN/m2. Pick frame 1 (ie, face C) as load area to apply the load
- Similarly, apply a X direction load along frame 16 with a load of 0.09 kN/m2 (ie, face D as shown in table above) .
- To apply internal pressure along Y direction of 1.3kN/m2 at frame A along Y direction ie, face A.
- For face B, apply an internal pressure of -0.32kN/m2 along -X direction
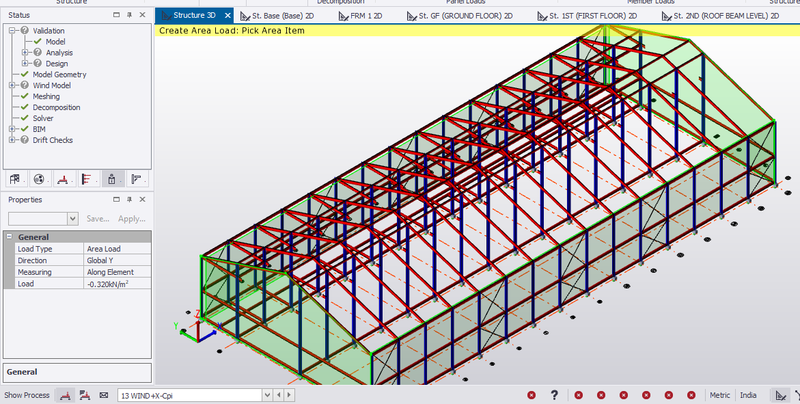
Step 6: Roof Calculation
External Pressure Coefficient for pitched roof, Consider Table 6, where h/w = 0.5 and roof angle is 18.
By interpolating method,
(-0.4+1.2)/(20-10)= (x+1.2)/(18-10)
x= -0.56
Also, x= -0.4
Therefore, EF= -0.56 ; FG= -0.4
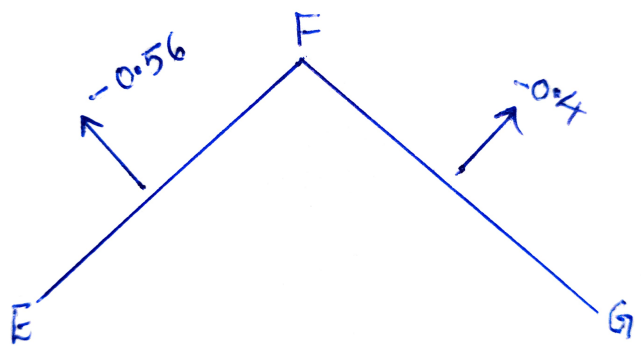
Step 7: Wind load along +Y direction

a. Wind+Y +Cpi
- Turn on the roof panel in the scene view.
- Change the wind load to Wind+Y+Cpi in the loading window
- Select the area load from the load tab.
- In the property window, change global direction to Z and wind load intensity to -1.45kN/m2 along face EF
- For face GH, change load intensity to -1.23kN/m2
- Turn off the members and roof panel in scene view
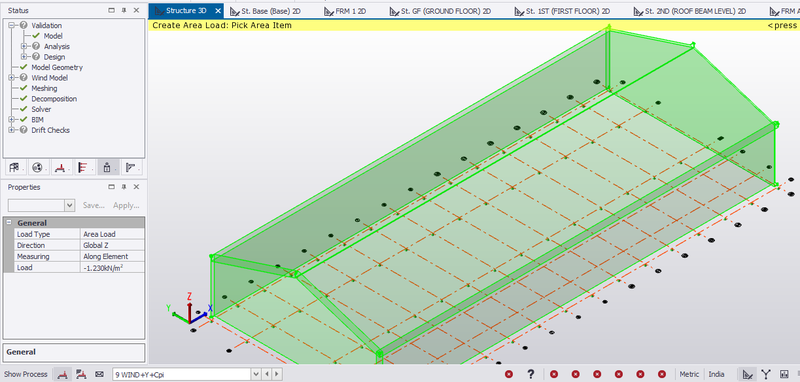
b. Wind+Y -Cpi
- Turn on the roof panel in the scene view.
- Change the wind load to Wind+Y-Cpi in the loading window
- Select the area load from the load tab.
- In the property window, change global direction to Z and wind load intensity to -0.09kN/m2 along face EF
- For face GH, change load intensity to 0.14kN/m2
- Turn off the members and roof panel in scene view
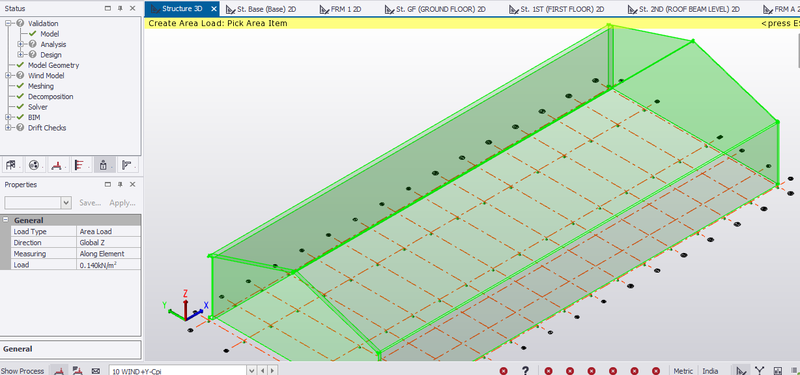
SEISMIC LOAD
- Select seismic load (seismic wizard) under load tab.
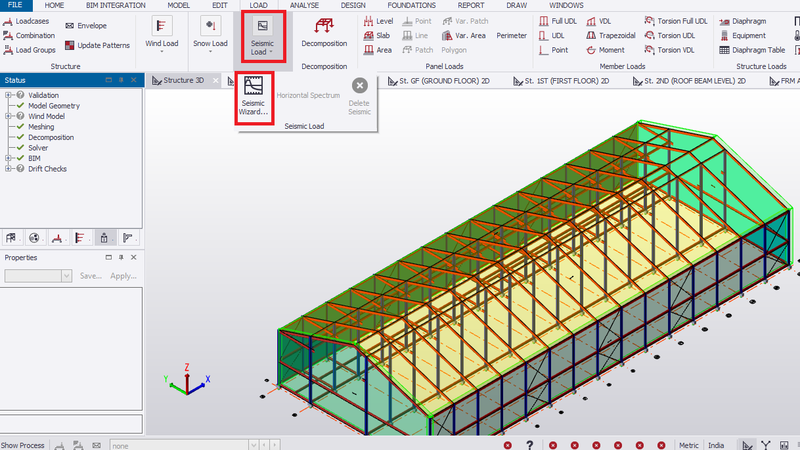
- Select code spectra. set the basic information as shown below
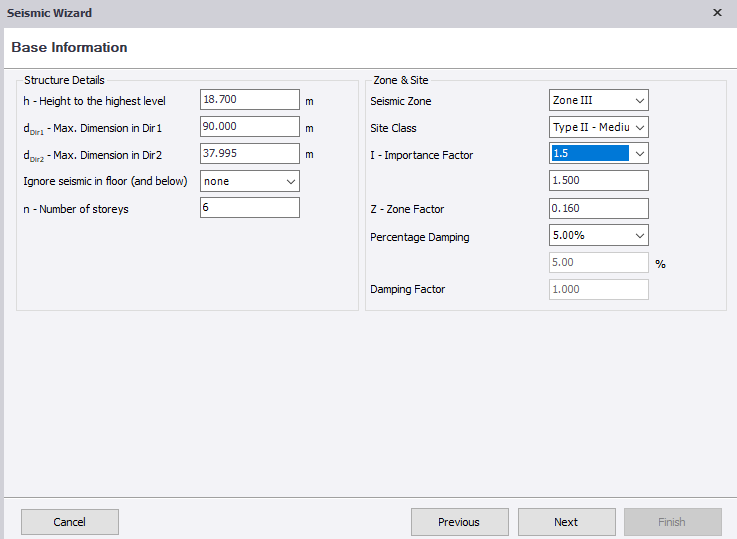
- Mention no irregularities in the structure and also fundamental period as shown below.
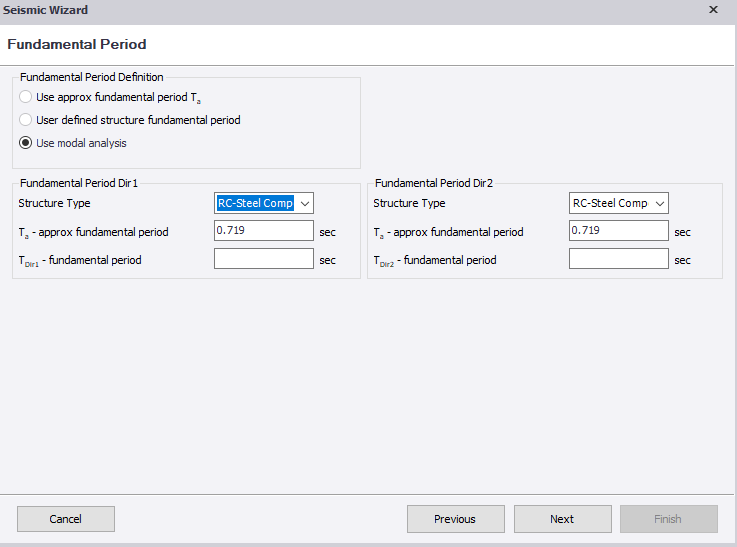
- Set seismic force resistance system with Moment frame system and braced frame system as shown below.
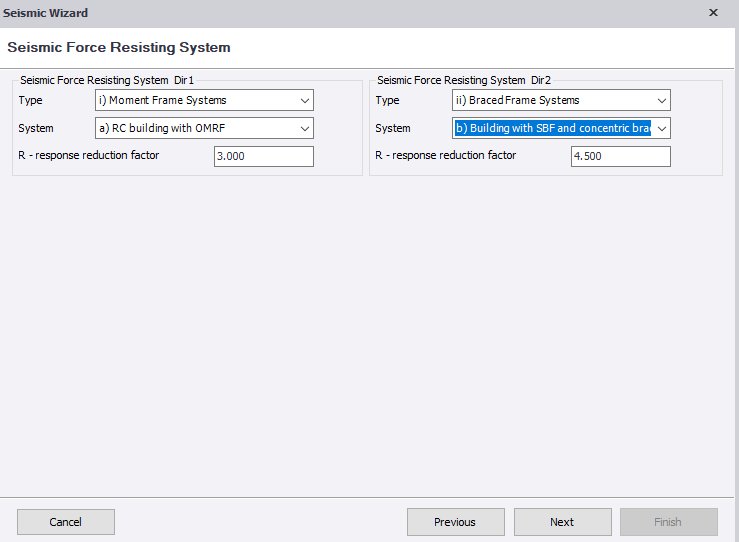
- Set effective seismic weight as shown and then click finish
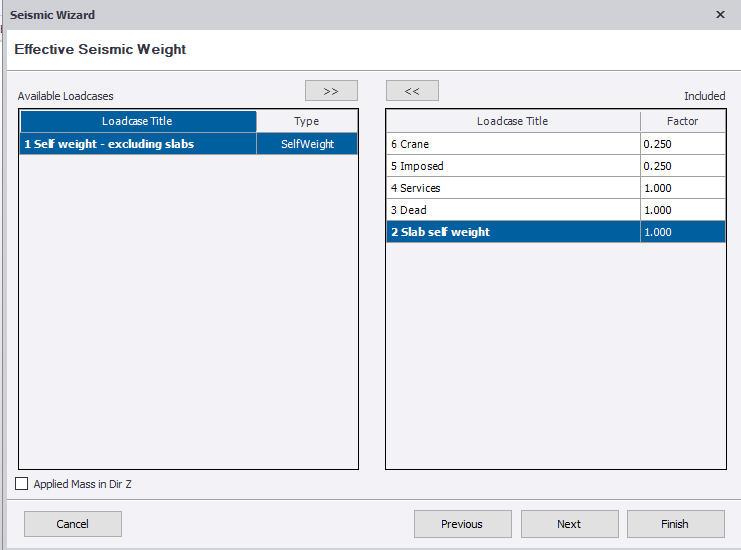
- Load combinations are generated
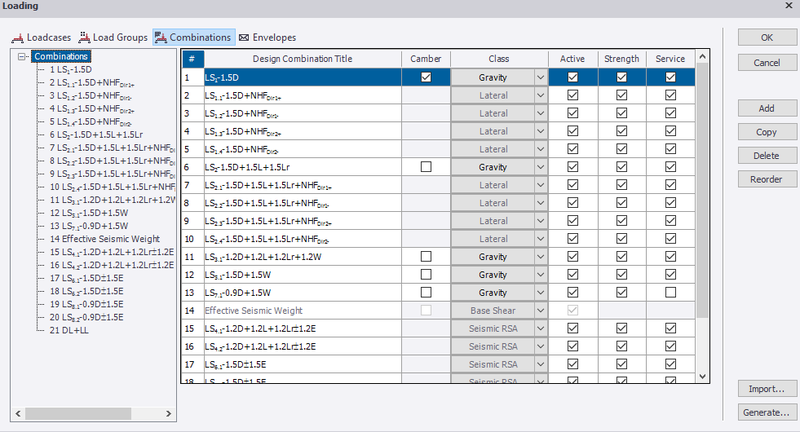
ANALYSIS
- Validate the model. Hence, no error the model
- Go to analyse tab, pick 1st order linear analysis.
- Select all the load combinations, click OK to run analysis.
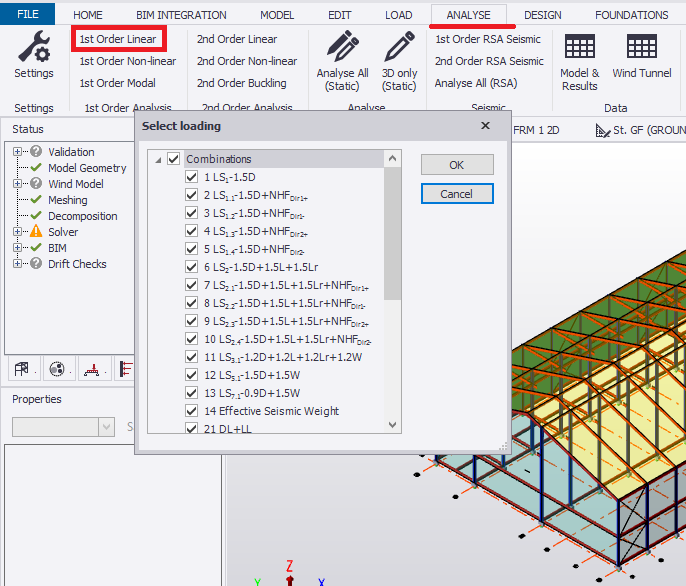
- There is some warnings shown in solver mode in project window.
Deflection
- After run analysis, in 3D structural view, go to result view.
- Select deflection along Z direction and load combination as DL+LL in loading window.
- Check the maximum deflection acting along Z direction and it is seen maximum deflection acts in frame 8
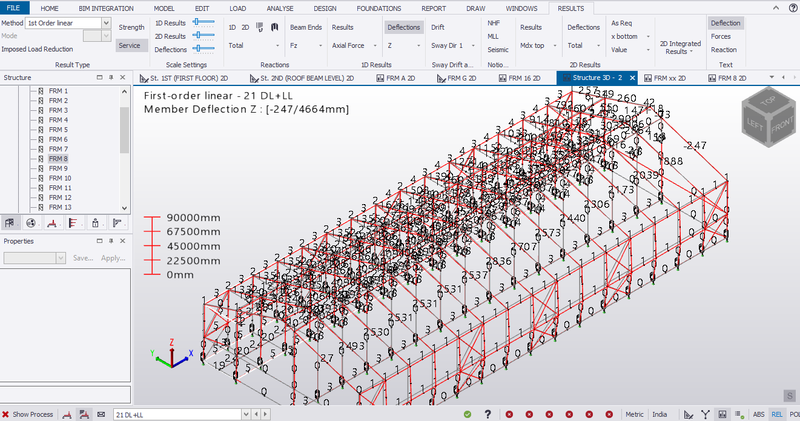
- In frame 8, it is seen that maximum deflection acts at rafter beam
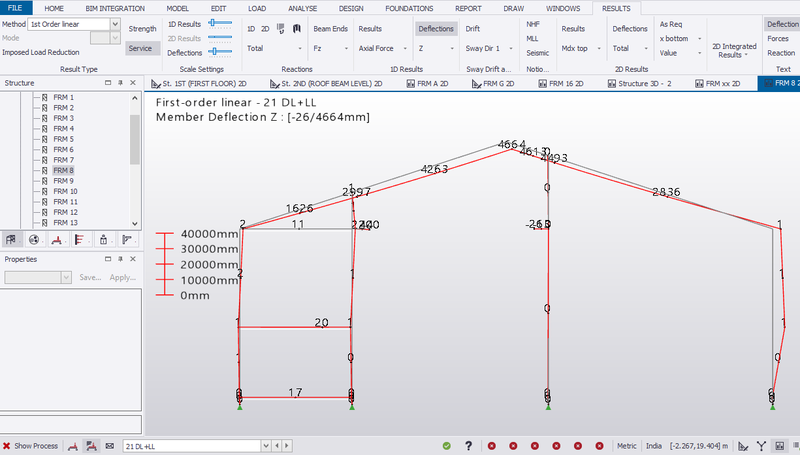
- consider rafter beam with deflection along z direction as 1626 mm which is high.
- Therefore, provide a larger section beam by designing it statically. But beam MB 600 does not satisfy the design condition as shown below.
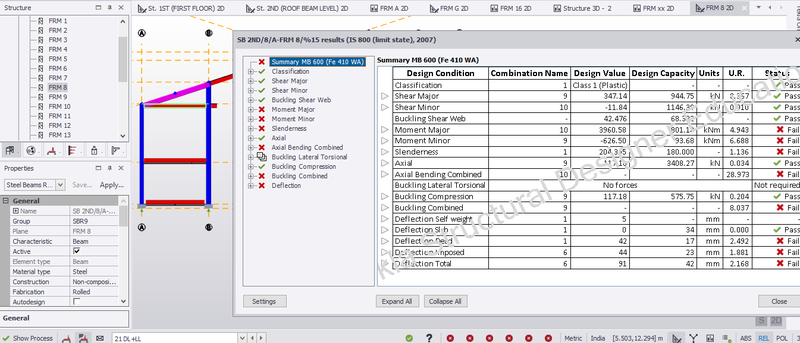
- Therefore, provide larger beam section from property window that is the universal section from UK.
- Again the section does not follow the design condition
- Therefore it is seen that braces were not provided in the roof. So roof braces of size ISA 75x 75 x 8 are provided which reduces the deflection on the rafter beam.
BRACES ON ROOF
DEFLECTION ON THE STRUCTURE
- Consider deflection on the ground floor with load combination DL+LL
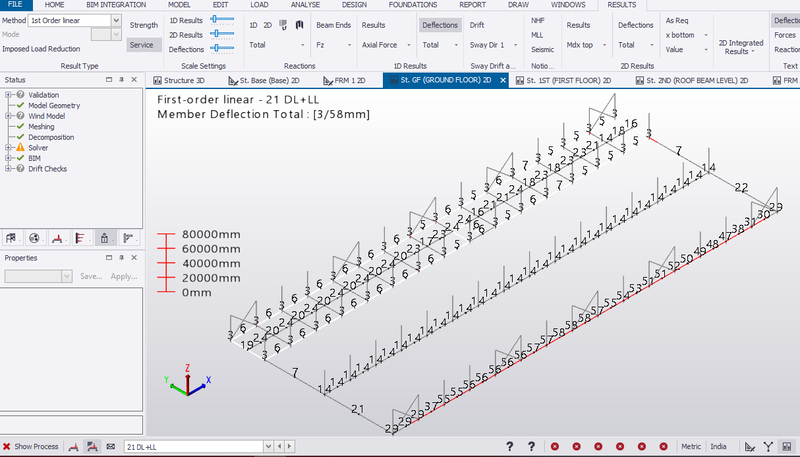
- Similarly, check deflection for other floor as well.
Bending moment
- In 3D structural view, select result view, from 1D result select major moment.
- Therefore, bending moment diagram in load combination DL+LL is shown below.
- As from the picture below, it is seen that maximum bending moment is 4871.03 kNm
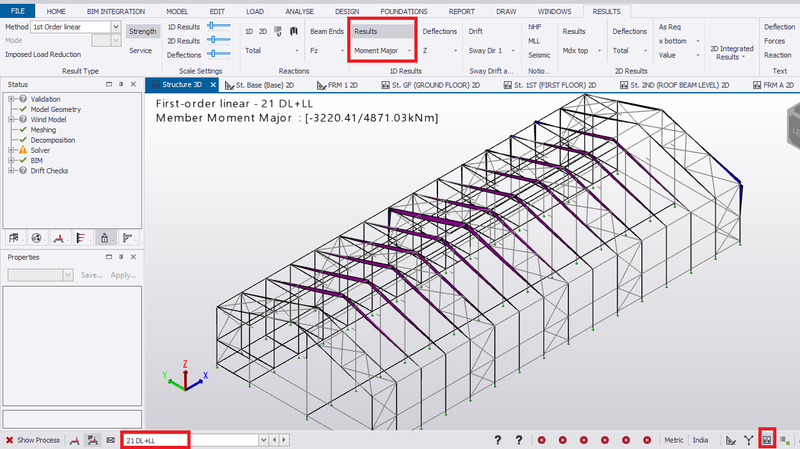
BM in ground floor
- Maximum bending moment in ground floor is 770.21kNm for load combination shown below.
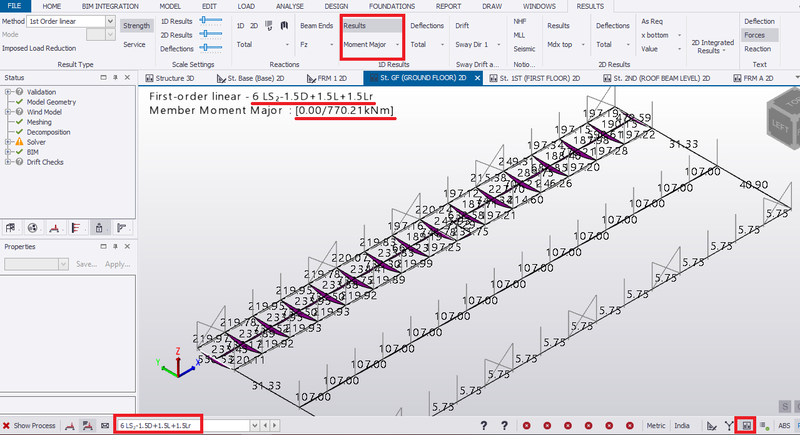
- Similarly, check bending moment for rest of the frames
Shear force diagram
- In 3D structural view, select result view, from 1D result select shear major.
- Therefore, shear force diagram in load combination DL+LL is shown below.
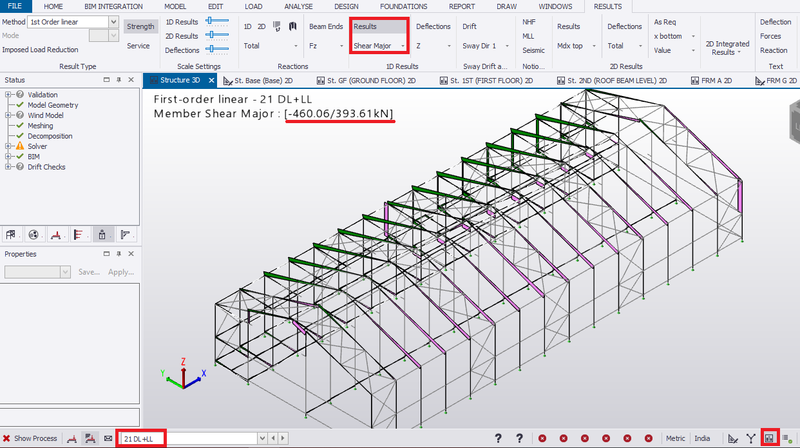
- As from the picture below, it is seen that maximum shear force is 280.33 kN for ground floor
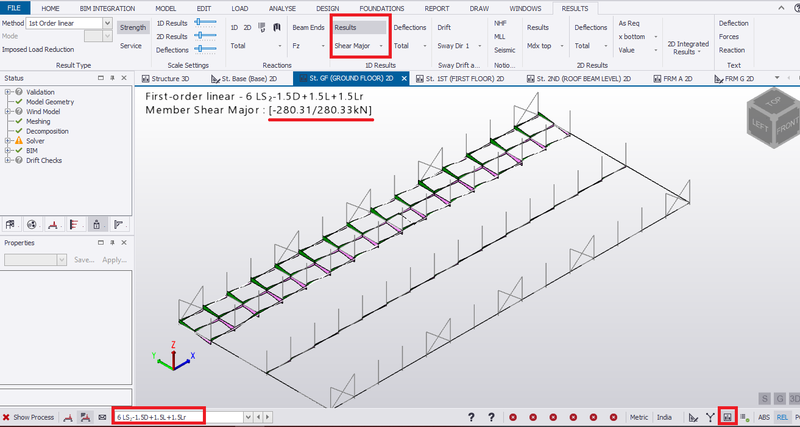
- Similarly, shear force diagram for frame A is shown below with max. SF 251.53 kN for load combination DL+LL
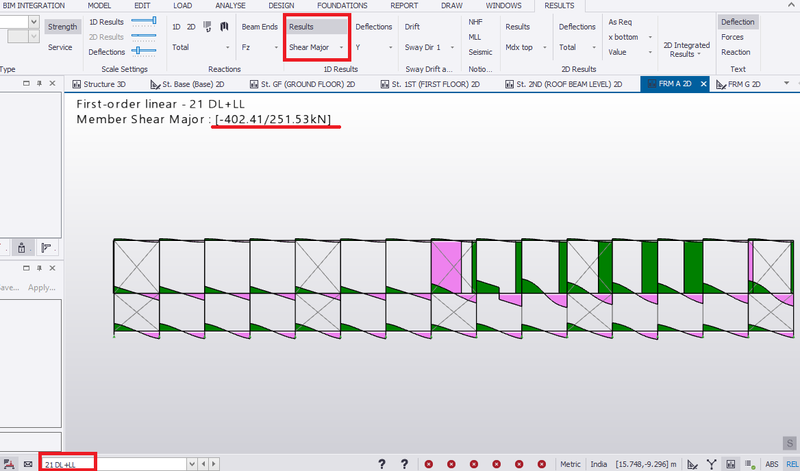
Axial force
- Select frame A to check the axial force for different load combinations
- Braces are also subjected to axial force
- There are compressive force(highlighted in yellow) and tension force(in red)
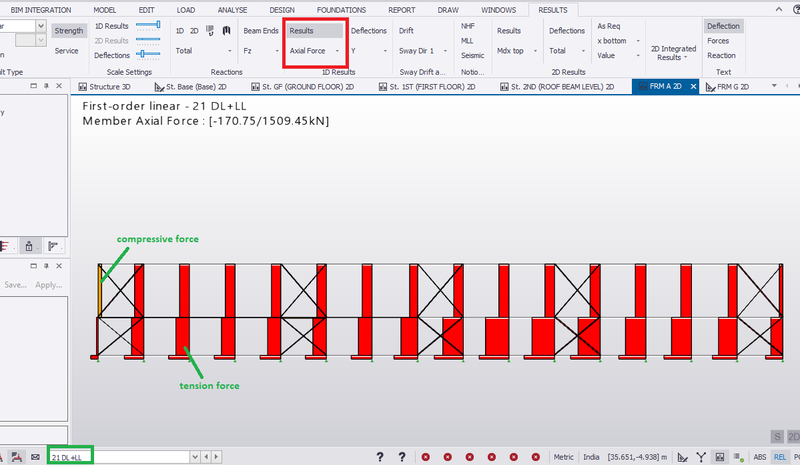
Member design
- Select frame 9 in scene view and check its deflection in Z direction which shows rafter beam has maximum deflection
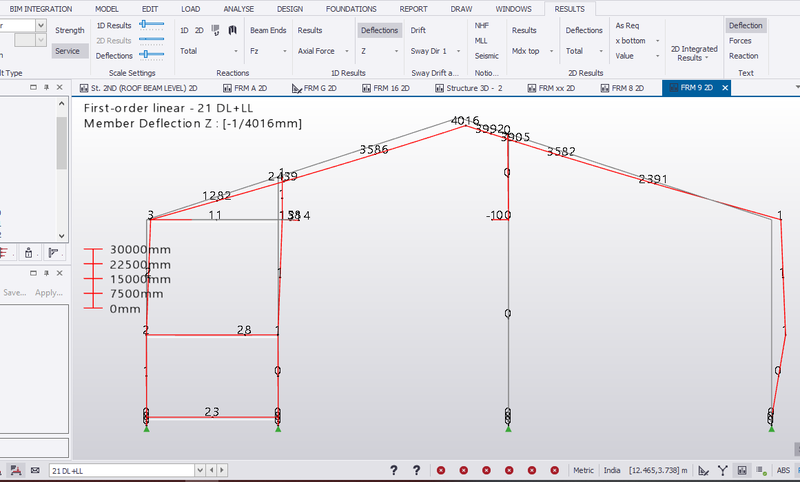
- Member section is needed to changed. Go to the structural view, select the beam in the ground floor and right click the member to design (static).
- Therefore, the member automatically design with section MB 600 which satisfy the design condition
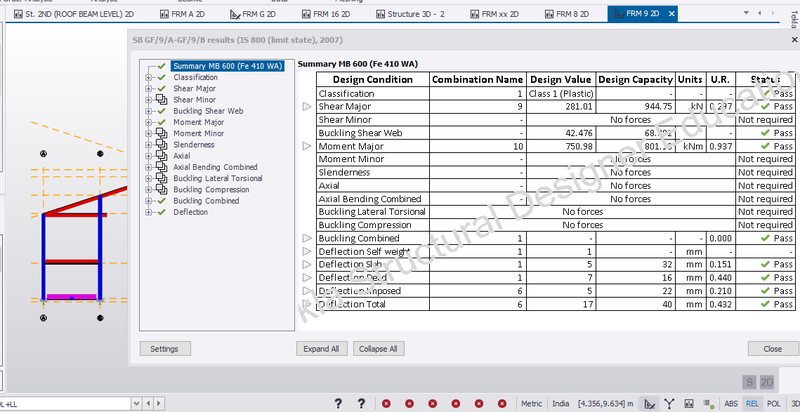
- Next, select beam from the 1st floor and select design member.
- The MB600 does not saatisfy the design condition. Therefore, need to provide higher beam section.
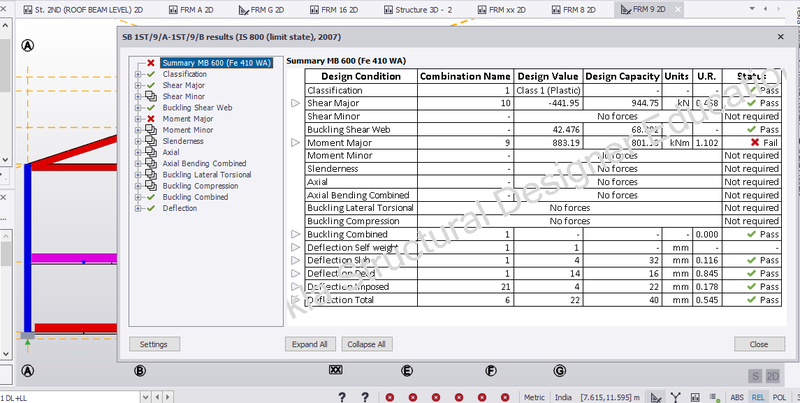
- To provide higher beam, select universal beam from UK from the property window with higher moment section.
- The roof beam MB500 satisfy the design condition
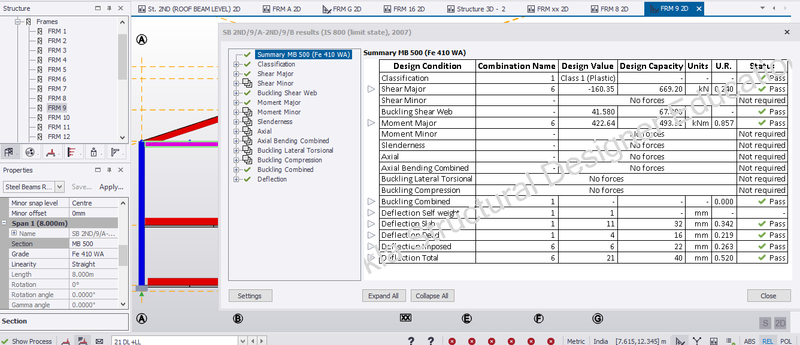
- It is seen that column with sectio MB 600 does not satisfy the design condition.
- Therefore, provide column of section UC 305x 305x 283 and check the design condition of the member
- The member satisfy the design condition
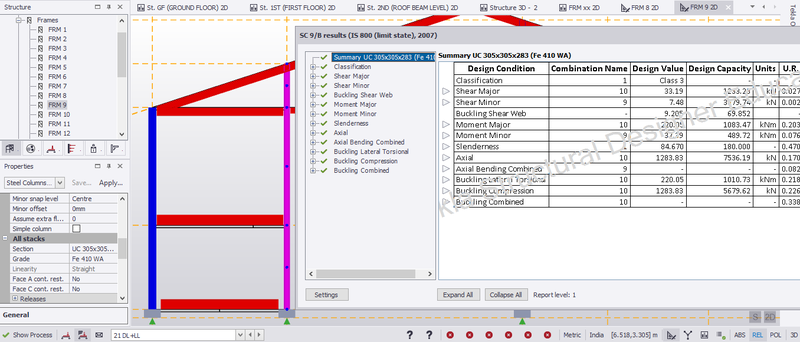
- From frame 1, select the rafter beam with section UC 356x 406x 634 which satisfy design condition as shown below.
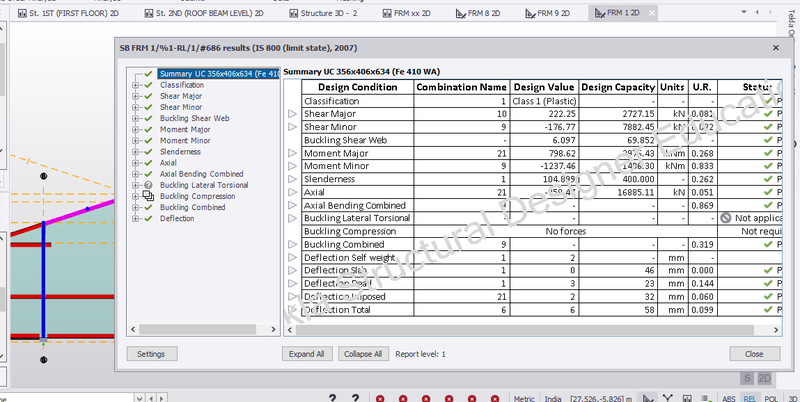
- In frame A, select the braces ISA 75x 75 x8 to check the design condition
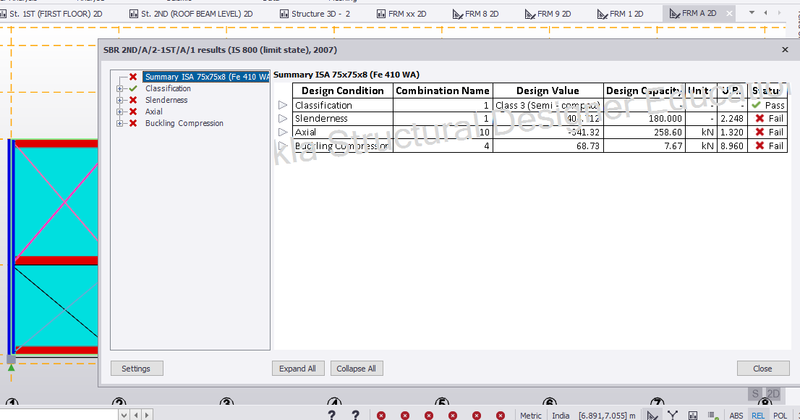
- Next, provide section ISA 180x 180x 20. Hence, section satisfy the design condition.
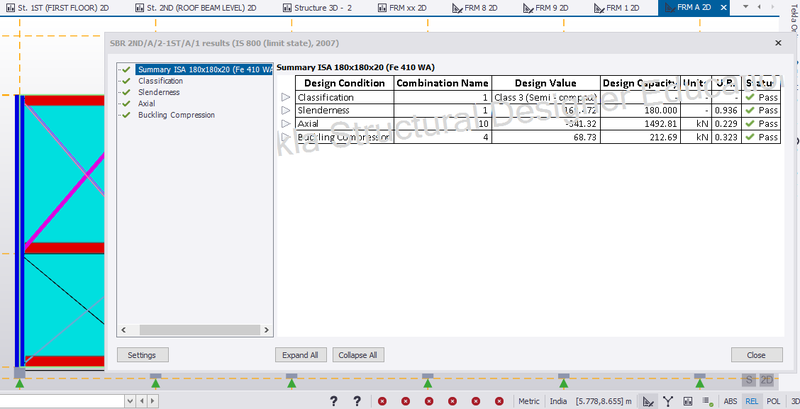
Slab design
- In the review view, Hide the steel beam, steel column, concrete column and steel braces from scene view.
- Pick the slab reinforcement under the review tab. Therefore, slab reinforcement of T10 150mm (524mm^2/m)
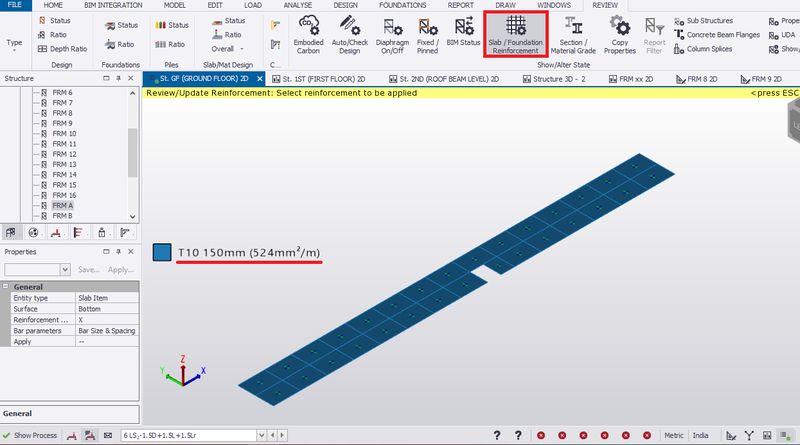
Foundation design
- Go to base level. Under foundation tab, select Pad Base Column .
- Pick isolated pad base location to create isolated pad base.
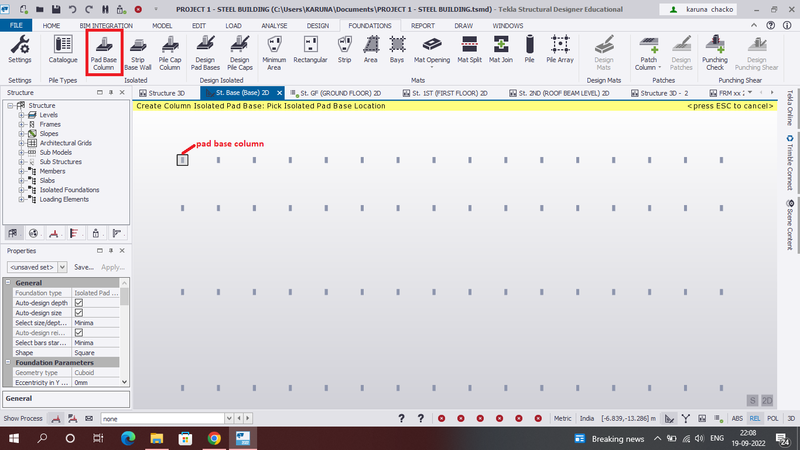
- The footing is automatically designed to a size of (1800x 1800x 750)mm with M20 grade concrete.
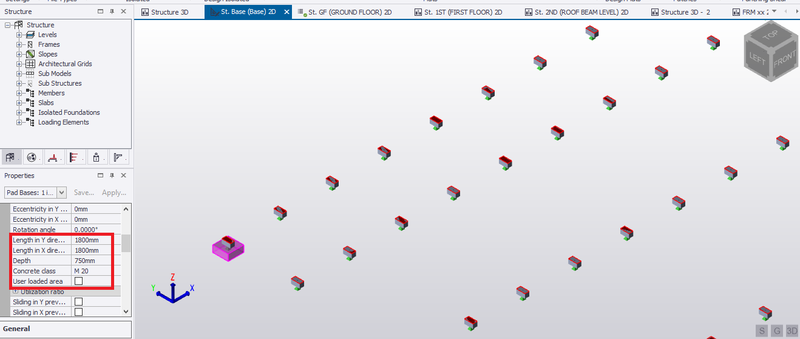
- Redesign the footing with M30 grade concrete of size 4.2m x 4.2m and depth 1000mm and reinforcement size of 20mm and spacing 120mm which satisfy the design condition
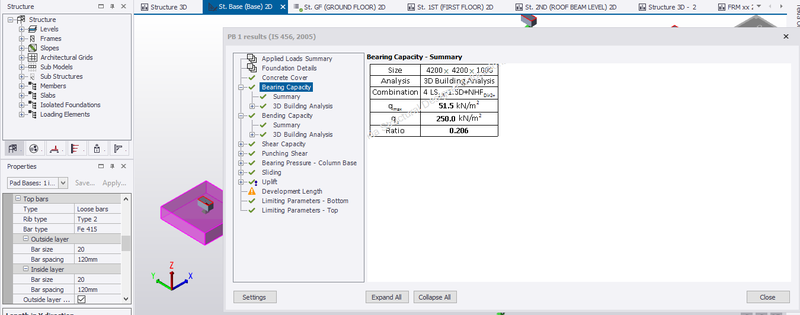
- The reaction acting on the support is obtained from result view by clicking on the supports under the reaction and by selecting a load combination
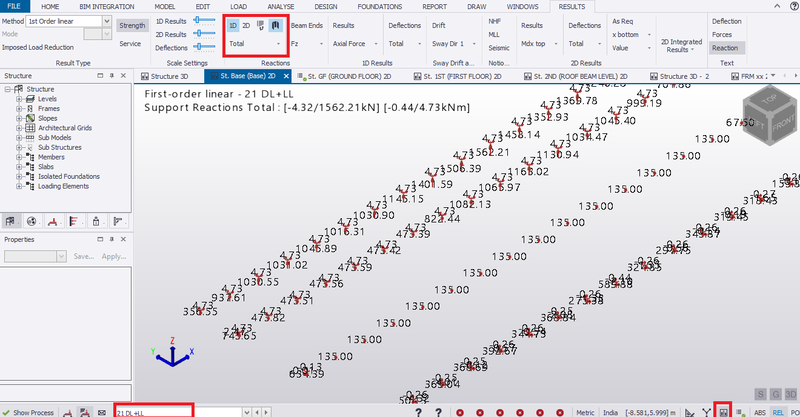
RESULT:- Hence, analyzed and designed a steel building to 10T CRANE as per IS standard code in TEKLA STRUCTURAL DESIGNER by providing braces and moment connections.