AIM: To study the phenomenon of Vortex-Shedding and the Karman Vortex Street at different Reynolds numbers, over a cylinder.
Operating conditions:
The objective of this project is to observe the vortex shedding behind the cylinder, and the operating fluid will be defined by creating a fluid with characterisitics that will allow us to observe the phenomena faster, in order to reduce computational time during the transient simulation. The reason that air has not been used as the operating fluid, is because of the fact that it would take an unreasonable amount of computational time (in a transient simulation, and the dimensions of the geometry being used), at a Reynolds number of 100. The Reynolds number directly affects the velocity, and the velocity required to simulate the flow at said Reynolds number is extremely low, and the transient simulation would take a considerable amount of time to simulate the required phenomena. The fluid characteristics will be displayed below.
1. Density of the fluid : 1 kg/m^3
2. Dynamic viscosity of the fluid : 0.01 N-s/m^2
3. Free stream velocity of the fluid : 0.5 m/s ......... ( Re = 100 )
4. Cylinder diameter : 2 m
5. Length of domain : 60 m
6. Breadth of domain : 20 m
7. Transient flow time period : 800 seconds
8. Iterations(all cases except transient) : 1000 iterations
Domain geometry:
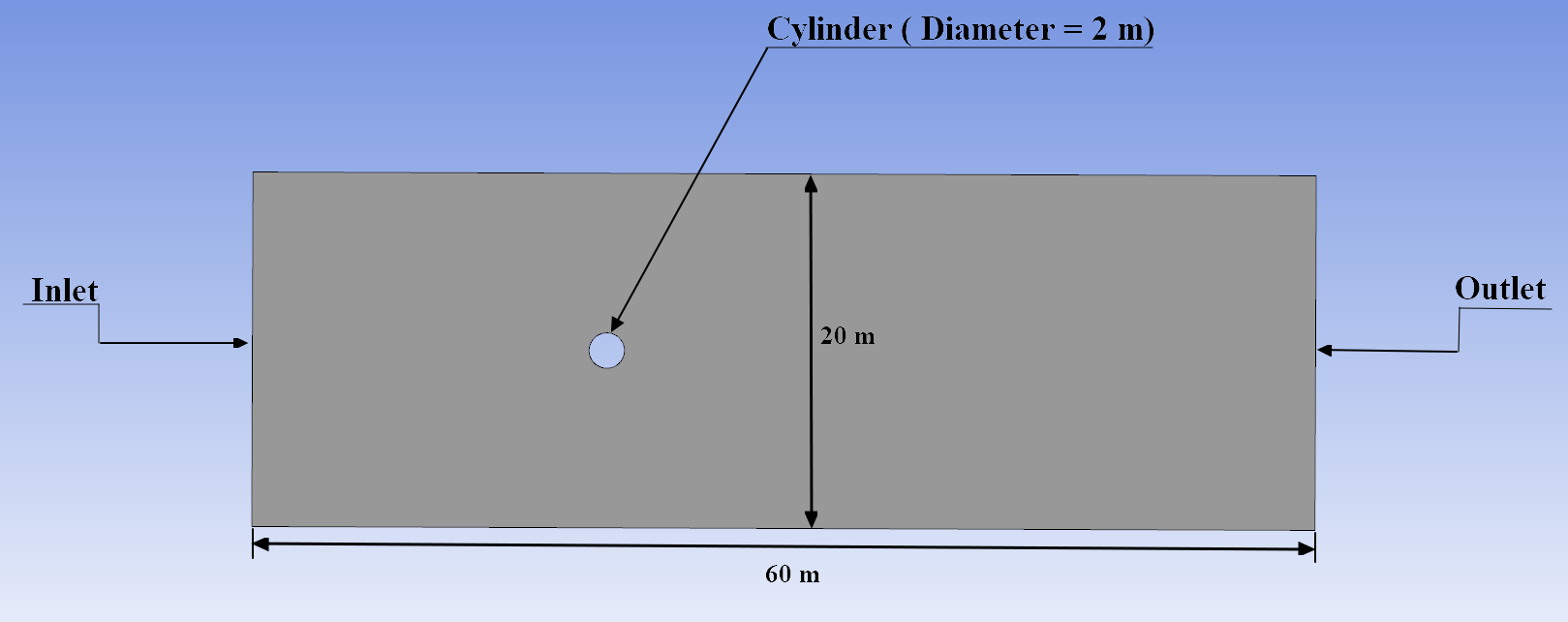
Formulae used to calculate the velocity, according to the Reynolds number of the case:
V = (Re*v)/L
where,
V = velocity of the fluid
Re = Reynolds number
v = kinematic viscosity of the fluid
L = characteristic length( in this case, diameter) = 2
PART-I :
The flow of the fluid is laminar. Upon running this simulation, it is observed that the phenomena of vortex shedding occurs. This will be discussed in detail in the section below.
The simulation has been run for both, steady state and transient cases. The transient simulation offers time accurate results, which in turn, allows us to calculate the Strouhal number for the given Reynolds number accurately.
The steady state and the transient simulations will be elaborated below.
Steady state and transient simulation:
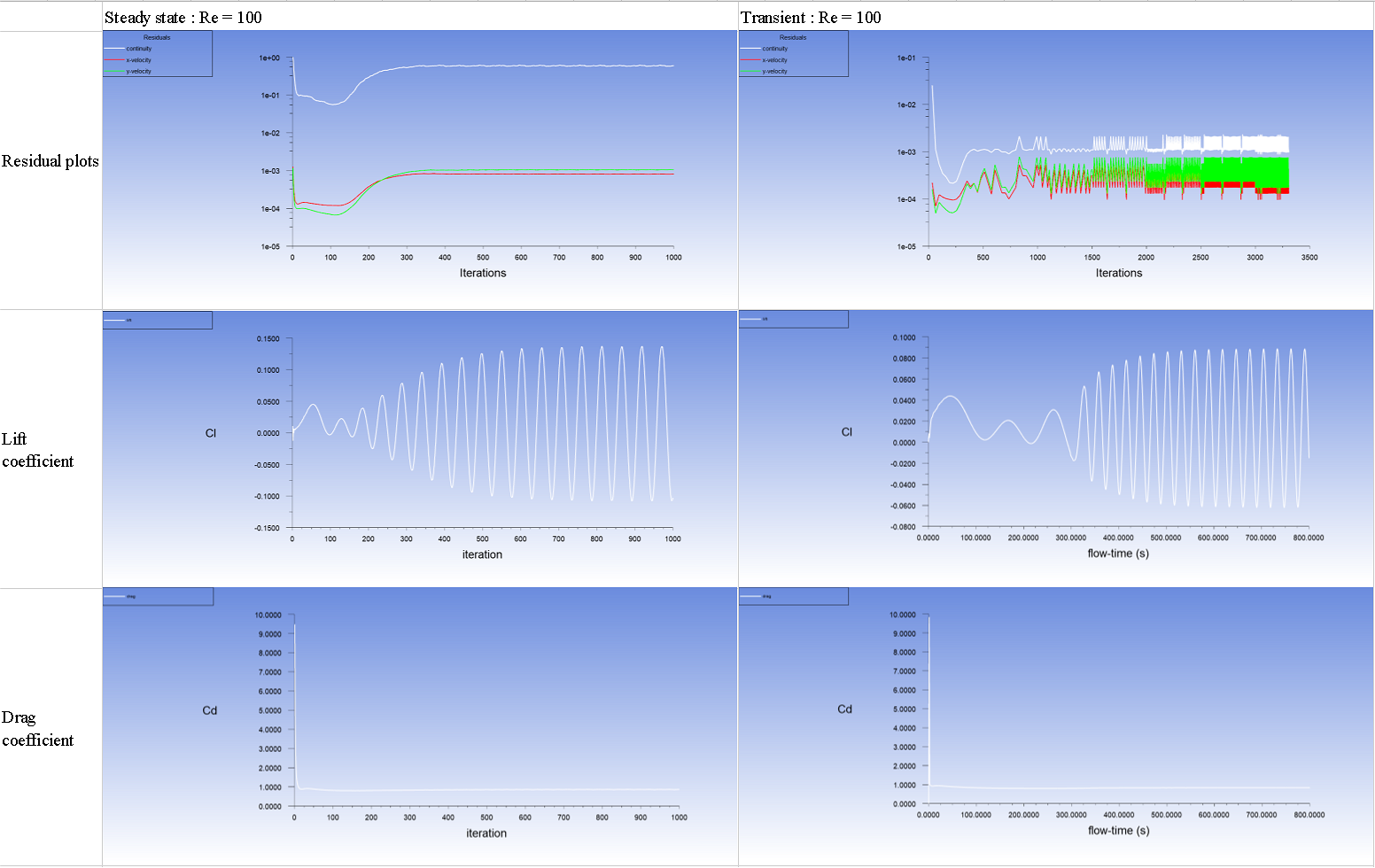
Observations:
- The residuals are sufficient in order to gauge the convergence in the steady state simulation. The X-velocity and the Y-velocity lines in the Residual plot begin exhibiting repetitive patterns at around 550 iterations.
- However, the transient simulation does not provide sufficient clarity regarding the convergence of the flow. There are multiple repetitive patterns that can be observed in the residual plot, and cannot be relied upon. Hence, an alternate variable must be used in order to judge the convergence of the fluid simulation.
- The drag coefficient plot does not seem to aid in the estimation of the convergence point, and can be disregarded for this particular case.
- The lift coefficient plot however, yields results that may aid in the estimation of the convergence iteration and time. Between 500 to 600 seconds, in the transient simulation, the sinusoidal oscillation of the lift coefficient begins to stabilize and shows that the crest and trough of the wave does not exceed 0.09 and -0.06 respectively. The lift coefficient depends upon Re,density, components of shear stress and pressure, normal to the direction of fluid flow. The pressure plays an important role in this case, and will be elaborated upon in the sections below.
- This variable takes into consideration many other factors about the flow, and can be relied upon for observing converegence. Once a repetitive pattern is seen, we can determine at what time step the simulation has converged.
Strouhals number for Re = 100 :
Strouhals number can be determined in Fluent by using the FFT plot in the post-processing suite in Fluent. Strouhals Number uses the frequency provided by the lift coefficient. The following plot shows the Strouhals number at Re = 100.
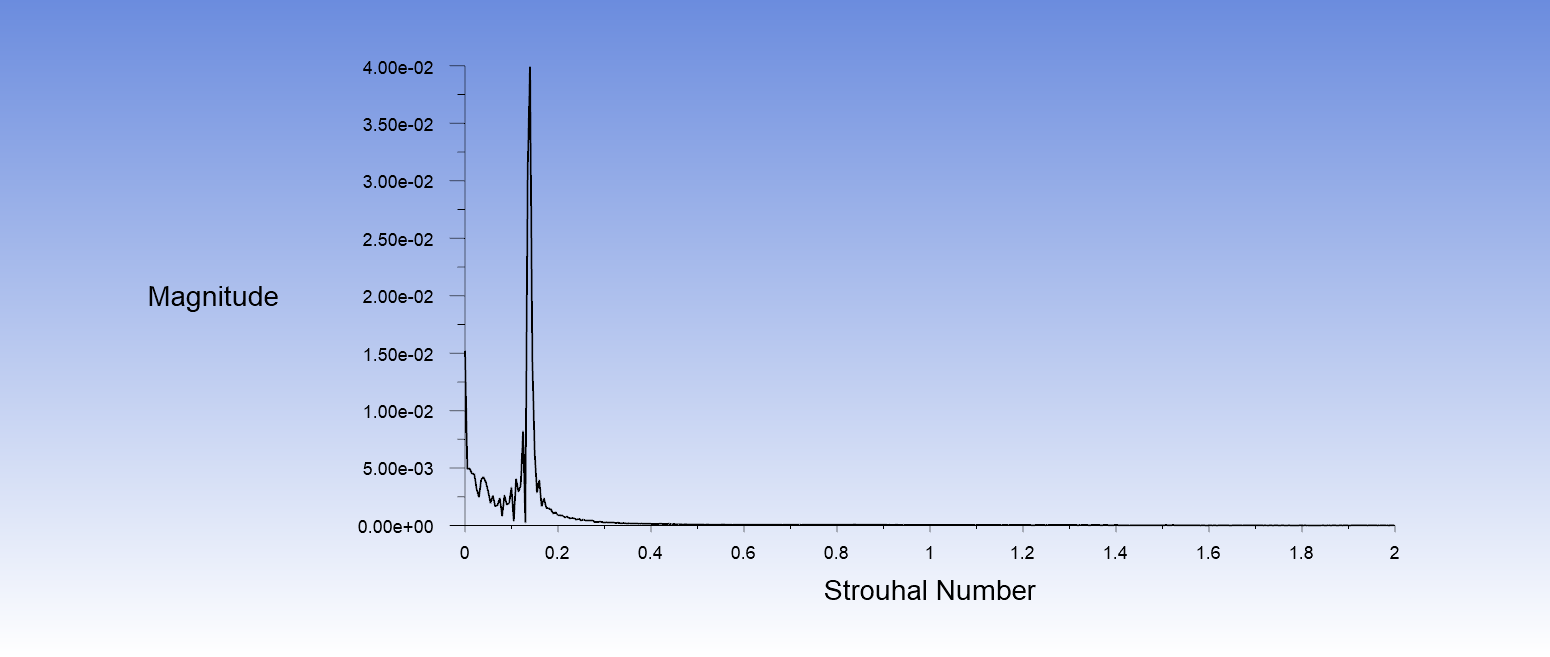
- From the plot shown above, the Strouhals number is around 0.14.
- The Strouhal number is used to anticipate the behaviour of the vortices caused by the flow of the fluid over the cylinder. It is directly related to the frequency of the vortex shedding, the velocity and the diameter of the cylinder. The Karman vortex street formed is directly dependent on the Reynolds number in this particular case.
- The vortex shedding frequency is important to obtain, as the vortex shedding frequency may affect the domain containing the fluid flow, and needs to be monitored.
Strouhal number = f.L/U
where,
f = vortex shedding frequency
L = Characteristic length
U = flow velocity
PART-II:
The following images display the plots for drag and lift, and vertex average of the velocity magnitude of a point 8 meters from the center of the cylinder(displaying vortex shedding).
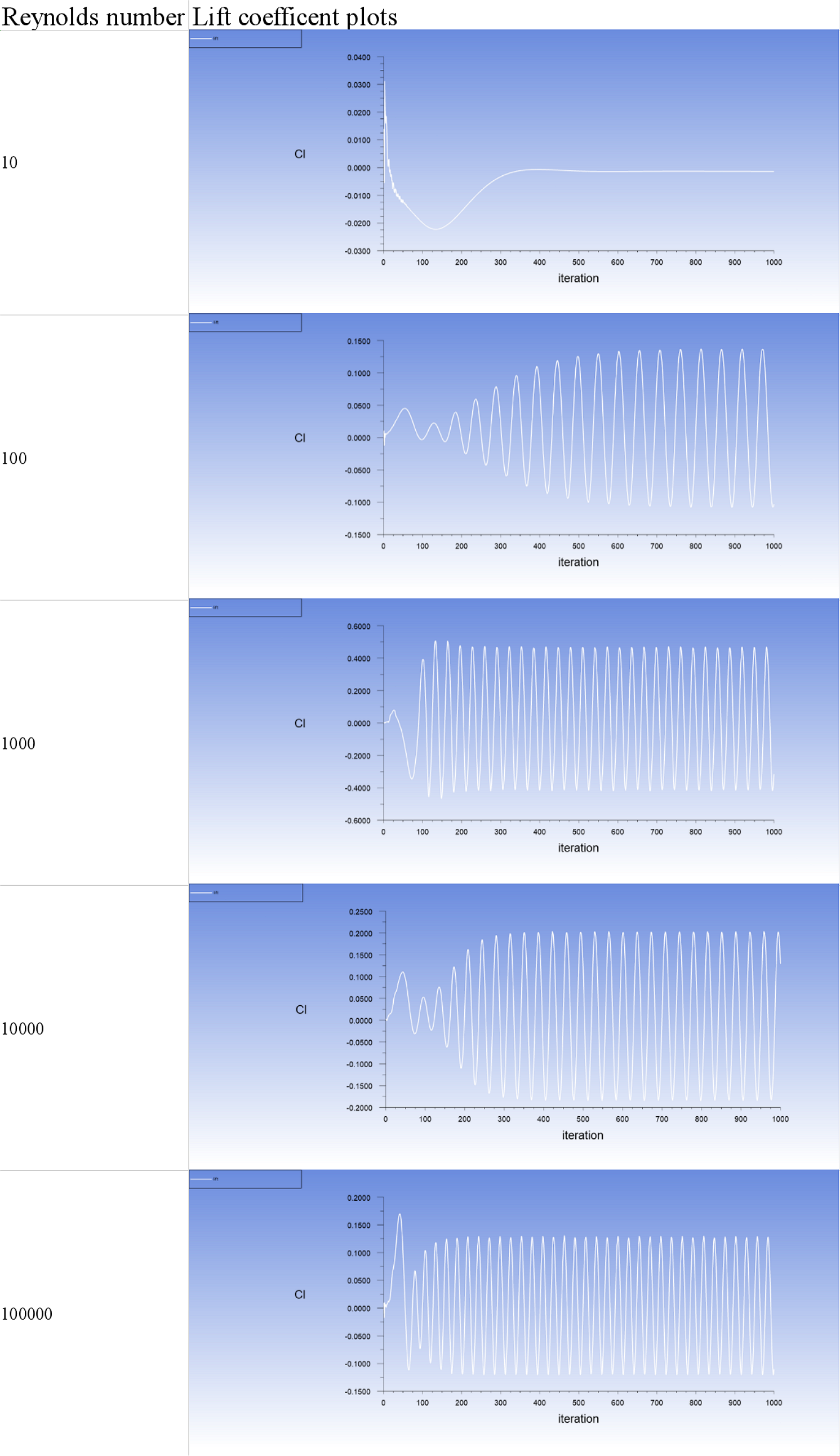
(A)Observations : Lift coefficient
Equation for lift coefficient:
Cl = F(lift)/[(12)⋅ρ⋅v2⋅A⋅(L⋅D)]
where,
Cl = lift coefficient
F(lift) = Forces due to drag
ρ = Density of the fluid
v = Velocity of the fluid
L = Length of the domain
D = Diameter of the cylinder
- On observing the laminar flows(Re = 10, 100 and 1000), it can be observed that the lift coefficient increases with increase in Reynolds number. At these Reynolds numbers, the separated flow region is closed and is short.
- At Re = 10, the separated flow region is very minute, and the pressure drop behind the cylinder is not prominant, due to the fact that the fluid molecules are slow enough to adhere to the surface of the cylinder throughout the flow. As the Re value increases to 100 and 1000, the flow separation can be observed, as the velocity is too high for the fluid to follow the curvature of the cylinder, and meets at a point further from the curvature of the cylinder. The velocity of the fluid in the separated zone is considerably slower due to the obstruction of the cylinder, and this causes a drop in pressure.
- The pressure drop causes an increase in pressure force, and this is an important characteristic.
- At Re = 1000, the lift coefficient at the wall oscillate between -0.4 and 0.4. Compared to the other values in the plots, the lift coefficient value obtained at Re = 1000 are the highest.
- The reason behind this is that the pressure forces influencing lift decrease as the Re is increased. The flow separated zone is still short in length and is close to the cylinder wall. Hence, the eddies within the zone(at very low pressure) induce higher pressure forces on the cylinder, hence affecting the lift force, and consequently, the lift coefficient.
- Another possible reason that this occurs is due to the fact that the fluid does not behave like a laminar fluid, after flowing over the cylinder.
- Observing the turbulent flows(Re = 10000 and 100000), a reduction in the value of the lift coefficient can be seen with the increase of the Reynolds number. This trend can be attributed to the fact that the flow separation zone is lengthened due to the higher velocity of the fluid, causing the reattachment of the fluid flowing over the cylinder at a point much further than the previously mentioned cases. Due to this, the fluid in the separated zone regains some velocity, and the pressure drop is not as intense behind the cylinder, compared to Re = 1000. Hence, the lift coefficient value decreases with the increase of the Reynolds number.
- This point will be made clear in the contour plot section.
- The differences between the vortex shedding for Re = 100 and Re = 1000, will be explained in the section elaborating contours.
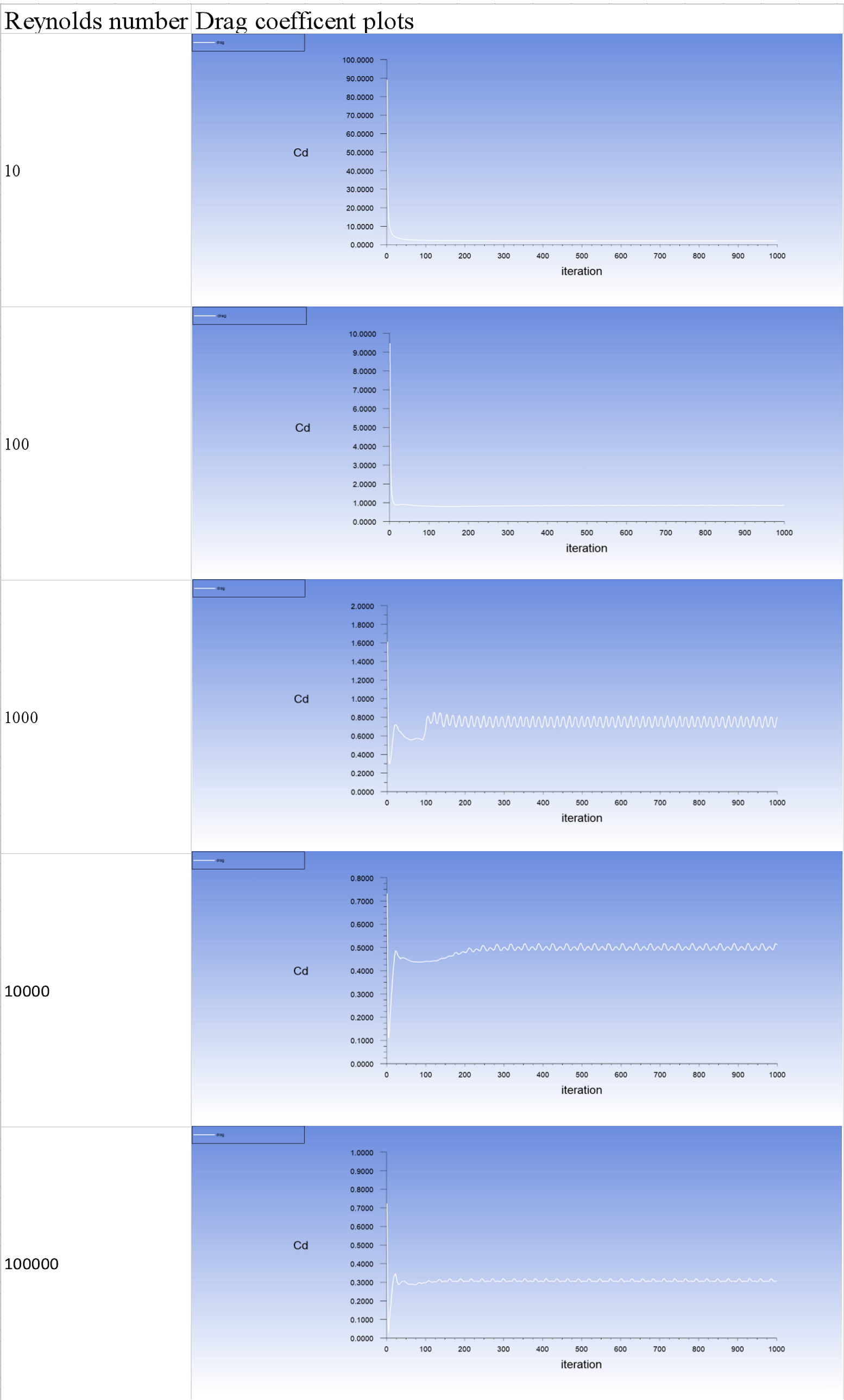
(B)Observations: Drag coefficient
Equation for drag coefficient:
Cd = F(drag)/[(12)⋅ρ⋅v2⋅A⋅(L⋅D)]
where,
Cd = drag coefficient
F(drag) = Forces due to drag
ρ = Density of the fluid
v = Velocity of the fluid
L = Length of the domain
D = Diameter of the cylinder
- In the plots for the drag coefficient, it can be observed that the values of the drag coefficient reduce with increase in the Reynolds number.
- In the plot for Re = 10, the drag coefficient is around 2.1. This suggests that the effects of drag force are high at a low Reynolds number. The drag force is due to friction drag, as the low velocity and effects of the viscosity of the fluid play an important role at this Reynolds number range. The fluid follows the geometry of the cylinder more closely in this range and the fluid simply flows over the cylinder without any major pressure drop near the end of the cylinder. Due to this, a straight line plot is seen, with no oscillations.
- At Re = 100, the vortex shedding in the laminar range begins, and the fluid flow around the center of the body starts oscillating due to the reduced pressure in the separated zone, after the cylinder. This causes the velocity to increase alternatively at the top and the bottom of the cylinder, hence directly affecting the drag forces, and consequently the drag coefficient. The drag coefficient is inversely proportional to the square of the velocity of the fluid, and hence, oscillations are seen in the plots after Re = 100.
- At Re = 1000, trend of the reduction of the drag coefficient with the increase of the Reynolds number is seen, but the oscillations of the drag coefficient in the plot shown above, seem to stand out the most, compared to the other plots. This can be attributed to the introduction of pressure drag at this Reynolds number, causing significant fluctuations in the velocity of the fluid. At this range, the fluid is still under the influence of friction drag, and along with the pressure drag, the drag coefficient oscillates more than the rest. The reason the value of the drag coefficient is not higher than the previously mentioned cases, is because the increased velocity is sufficient enough to negate the effect of the drag forces in the equation, and continues to follow the trend of decreasing drag coefficient values at higher Reynolds numbers.
- At Re = 10000 and Re = 100000, the drag coefficient oscillates around 0.5 and 0.3 respectively, and hence, can be said that the drag forces reduce in turbulent flows.
- This can be explained by the higher velocity of the fluid, as the flow separated zone is longer, because the fluid unable to follow the curvature of the cylinder, causing the drag due to pressure to reduce subtantially. Friction drag does not play a vital role at this range of Reynolds numbers, because of the high velocity of the fluid, and can be disregarded.
- Hence, a primitive conclusion that can be made, is the fact that laminar flows display high drag coefficient values, due to their low velocities and the higher adherence of fluid molecules to the cylinder, following the curvature of the cylinder wall, slowing down the fluid flow. At low Reynolds numbers, the effect of the phenomenon of flow separation is not dominant and this will be observed in more detail in the section that elaborates upon the velocity contours.
- At higher Reynolds numbers, the flow separation is dominant and consequently causes the reduction of drag forces on the cylinder.
- The following image displays the vortex shedding characteristics of the Re numbers mentioned above, following the trends that have been explained in this section.
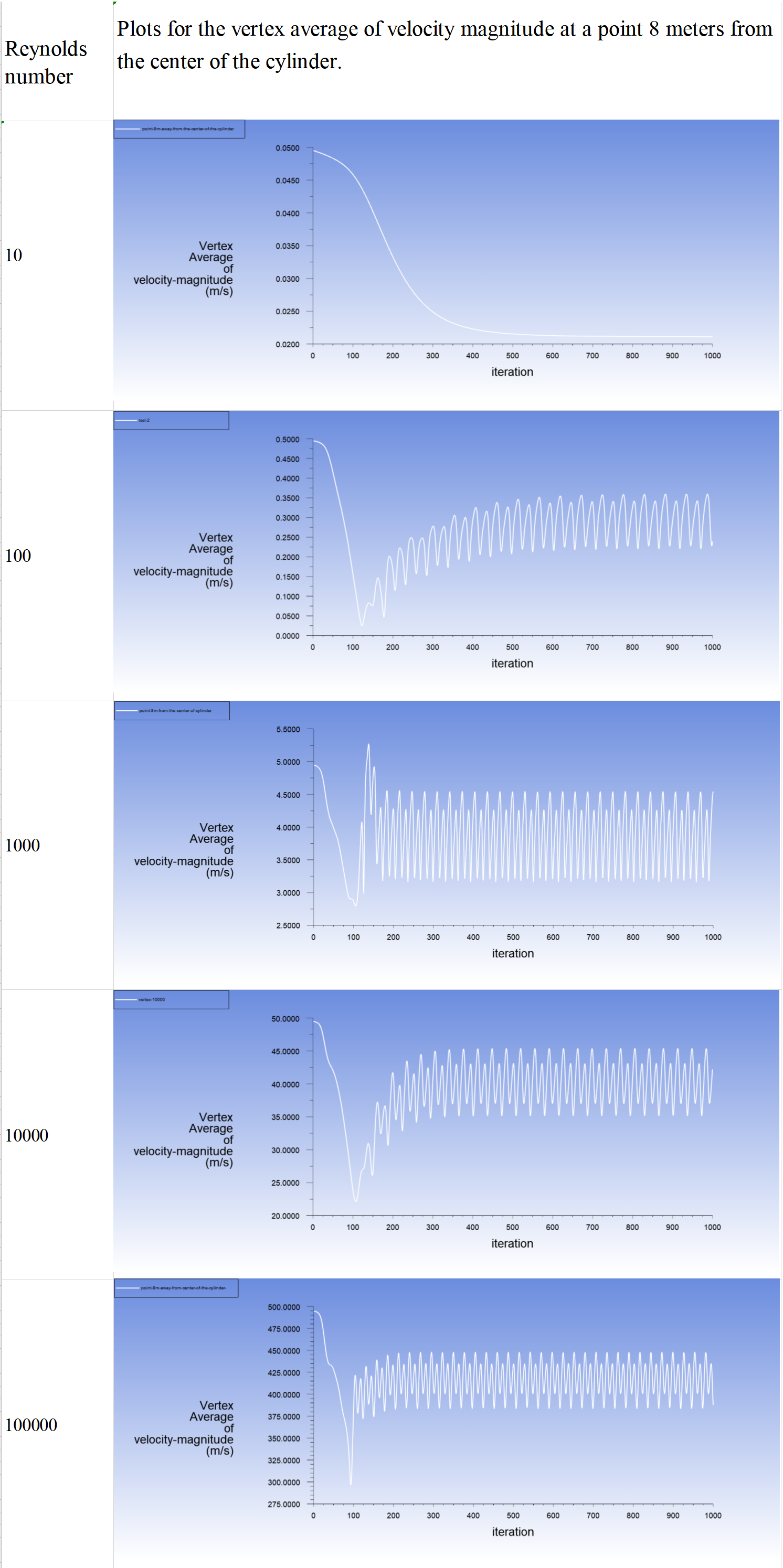
- Observing the image above, at a point 8 meters away from the center of the cylinder, vortex shedding characteristics can be seen after Re = 100.
- At Re = 10, as mentioned in the sections above, the velocity is low, and the fluid follows the curvature of the cylinder throughout.
(C)THE CONCEPT OF VERTEX SHEDDING AND THE KARMAN VORTEX STREET USING PRESSURE COEFFICIENT AND VELOCITY CONTOURS :
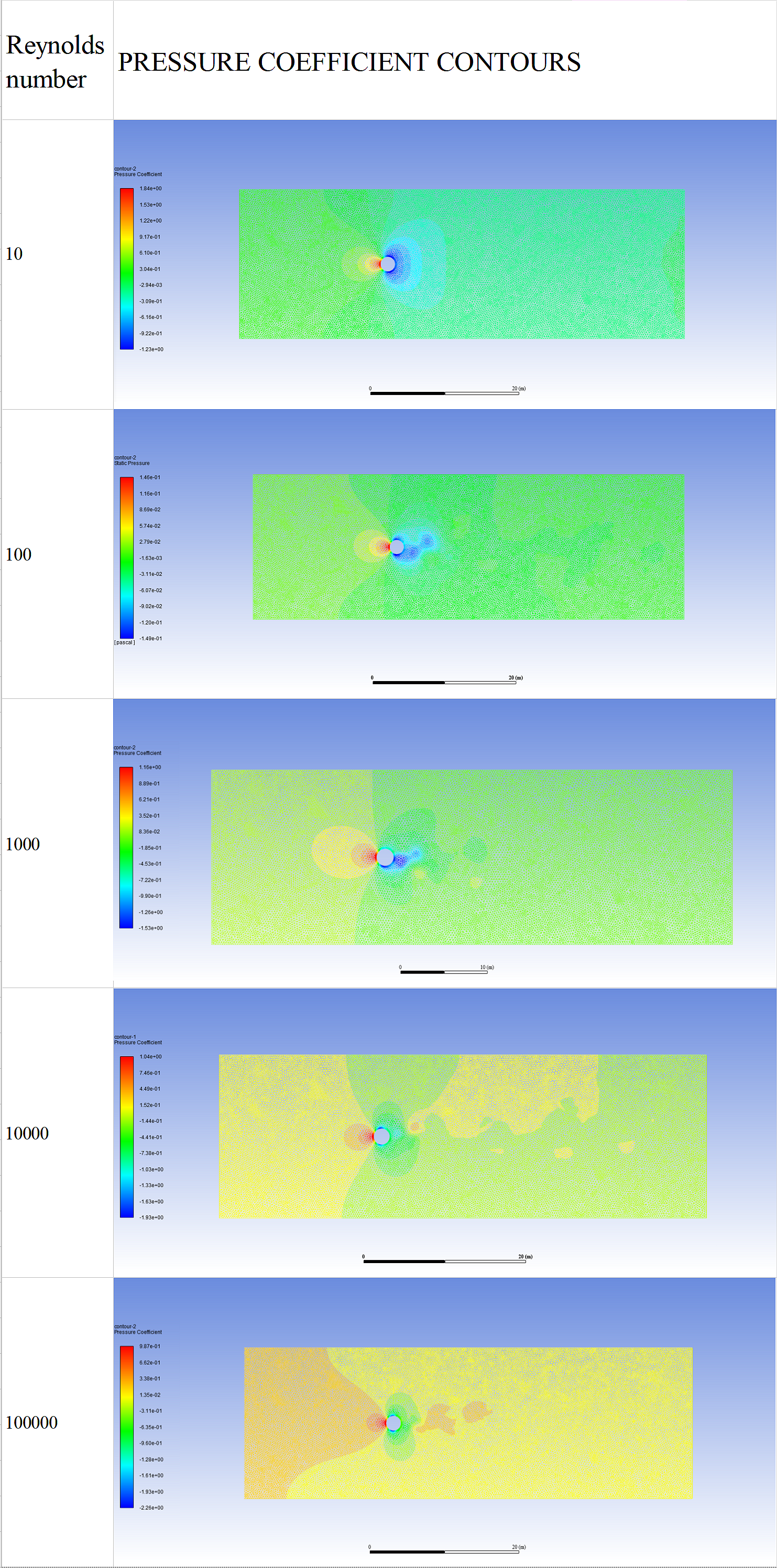
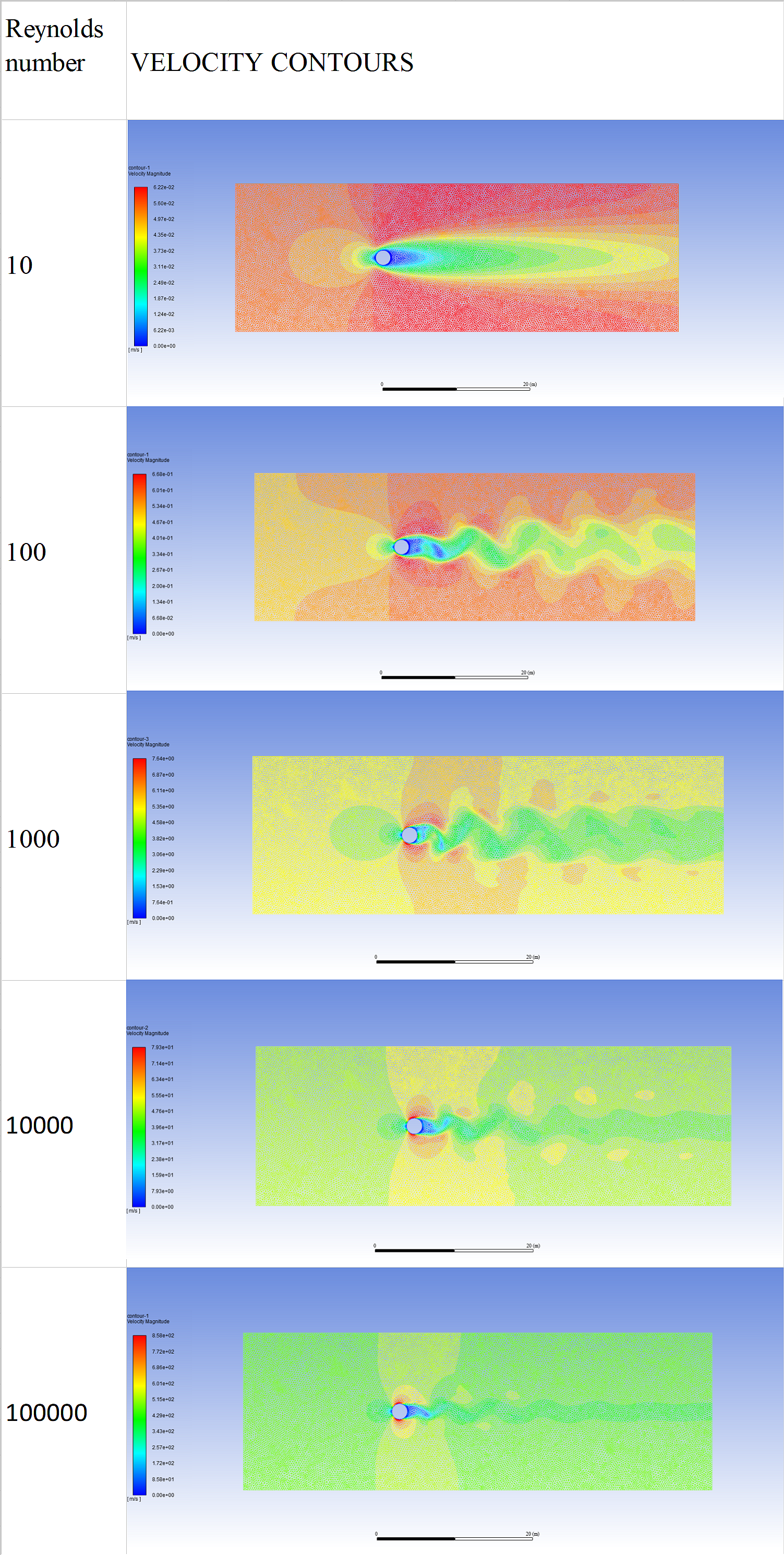
Conclusions:
- The pressure coefficient contours have been utilized for comparison, so that the pressure drop can be compared accurately between cases, and display the behaviour of the fluid, rather than just the values of pressure. Pressure coefficent is dimensionless in nature, and this aids in comparison as well.
- At Re = 10, the pressure distribution is uniform around the cylinder end, and the slight pressure drop does not affect the flow in an adverse manner. The fluid flows over the cylinder curvature, and does not create a significant flow separation zone. This can be seen in the velocity contour, where the flow behaves predictably and gradually regains the velocity lost due to the obstruction of the cylinder, along the center of the domain.
The formation of the Karman Vortex Street:
- At Re = 100, a steeper pressure drop is observed, and this is sufficient for vortex shedding to begin. Again, the pressure drop occurs due to the velocity of the fluid being too high, and is unable to travel along the curvature of the cylinder, creating a flow seperated zone behind the cylinder where the velocity is very low. The pressure drop causes an increase in the velocity of the fluid flowing over the cylinder, and results the formation of vortices behind it. The pressure drop behind the cylinder does not remain at the same area. This in turn, changes the velocity in that area, causing the velocity of the fluid at the top or the bottom side of the cylinder to increase, depending on the area which has a higher pressure drop. The vortex behind the cylinder, begins to oscillate along the curvature of the cylinder, changing its position with respect to the pressure drop. The velocity of the fluid at the along the center of the domain reduces drastically because of the formation of eddies, and consequently, an oscillating flow is observed. The fluid outside the oscillating fluid is at a higher velocity. The following image shows the movement of the vortex along the curvature of the cylinder.
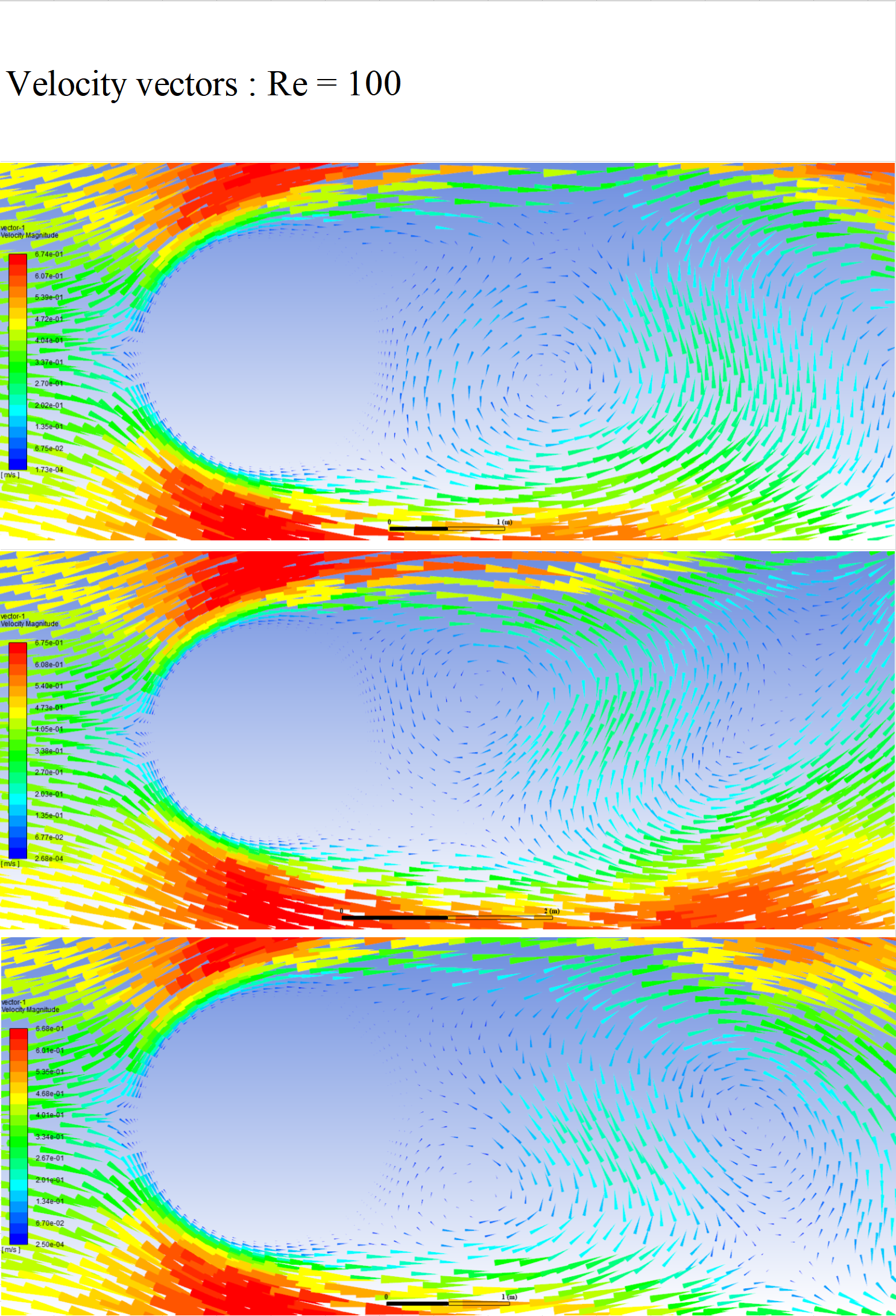
- At this Reynolds number, the flow is relatively smooth, and is still laminar in nature.
- At Re = 1000, some differences can be seen, despite the initial flow being laminar in nature. The first point of difference is the area of effect of the vortex street. The vortex street occupies more space than the other cases shown. That being said, the flow after the fluid flows over the cylinder seems more turbulent in nature, if compared to the contours with Re = 10000 and Re = 10000. So, it is possible that the fluid flow becomes turbulent in nature, as it is unable to maintain the same smooth oscillation of the fluid after the cylinder, as seen in Re = 100. This suggests that the initial velocity at Re = 1000 is sufficient to create turbulent flow after the fluid flows over the cylinder.
- At Re = 10000, a reduction in the intensity of the vortex shedding is observed, and this is made clear by the reduction in the difference of the velocity oscillating along the center of the pipe, and the fluid surrounding it. This is made even more obvious by the reduction in pressure drop after the cylinder, as the pressure distribution is more spread out, and less concentrated in the area just after the cylinder.
- At Re = 100000, this fact is made clear, as the velocity difference outside the oscillating fluid and the oscillating fluid is very subtle. The oscillating fluid along the center is much more smooth compared to Re = 10000, but the amplitude of the oscillation reduces at it reaches the outlet.
Reason for the reduction in amplitude of oscillation at Re = 10000 and 100000, compared to Re = 1000 :
The following image displays the velocity vectors at Re = 1000 and Re = 10000.
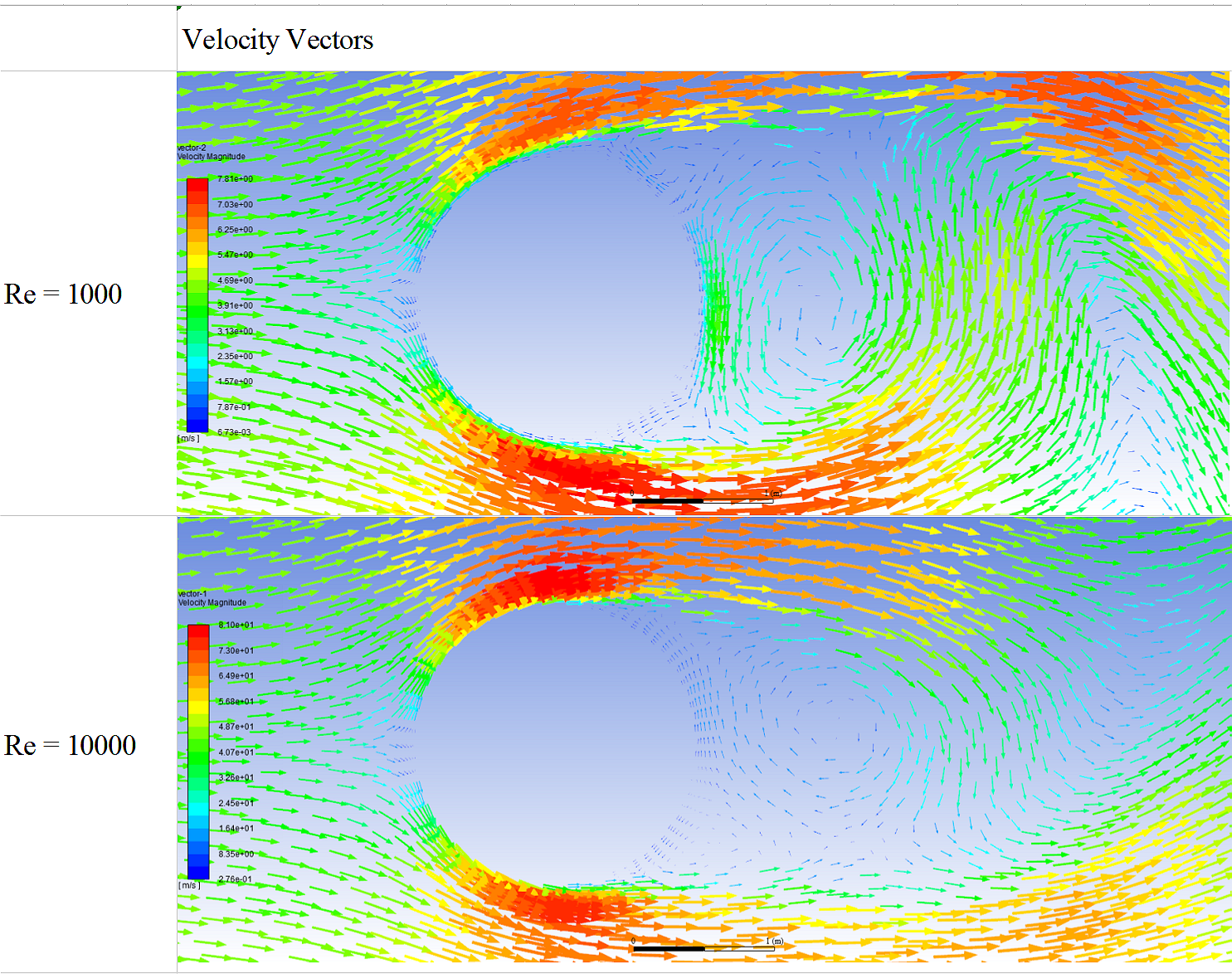
- Observing the image displayed above, it can be seen that the vortex of formed after the cylinder is closer to the cylinder geometry in the case of Re = 1000, compared to Re = 10000. This can be explained by the elongation of the flow separated zone for Re = 10000.
- The increase in the area of the flow separation zone suggests that the reattachment point of the fluid after crossing the cylinder curvature, is further along the length of the domain. This causes a reduction in pressure drop, because the fluid is allowed to regain the velocity lost to an extent, and hence reducing the amplitude of the oscillating flow.
- The shorter flow separated zone in Re = 1000 contains a pressure drop and the creation of the vortices much closer to the cylinder geometry, in turn creating more prominent oscillations of the fluid along the center of the domain.
References:
- 'Fluid Mechanics', Yunus A.Cengel & John M.Cimbala.
- 'Numerical simulation of laminar flow past a circular cylinder', B.N Rajani, A.Kandasamy, Sekhar Majumdar.
- 'Optimal Strouhal Number for swimming animals', Christophe Eloy.
- 'THE SUPPRESSION OF LIFT ON A CYLINDER DUE TO VORTEX SHEDDING AT MODERATE REYNOLDS NUMBERS', C.Dalton, Y.Xu.
Animation Video for velocity, transient simulation, at Re = 100: