Challenge 2 – External flow over a cylinder
Aim – To analyse the external flow over a cylinder, calculate the drag and lift coefficient, and observe the phenomenon of Von Karman Street for varying values of Reynolds number.
Theory and Practical Applications –
- Von Karman Street or most commonly known as vortex shedding is observed when a fluid flow over a body (external flow) and the subsequent vortices start to shed
- This phenomenon starts to occur mainly at a Reynolds number of 90-100.
- These phenomena can be found in rivers or streams as they flow past boulders, and even in the clouds as they move past mountains or islands.
Solving and Modelling Approach –
- For analysing the external flow over a cylinder, a 2D design can be created, instead of a 3D design since the flow properties for each layer in the XY plane will be equal.
- Since the flow over a cylinder is categorised in external flow simulations, an external control volume is required to analyse the flow around the cylinder boundary.
- A 2D sketch was created in Ansys Spaceclaim and the “Pull” feature was used to generate a surface body for the sketch.
- The dimensions of the control volume that were considered can be seen in the figure below.
- After creating the appropriate geometry, a mesh was generated on the surface.
- Since this simulation is about analysing the boundary layer of the cylinder and also the area after the cylinder, an advanced mesh is required to get accurate and precise results.
- The mesh was created using a triangular method, edge sizing, and an inflation layer near the cylinder boundary.
- An edge sizing of 36 was taken along the cylinder boundary, thus, each section has an angle of 10° subtended. A default growth rate of 1.2 was taken into consideration
- An inflation layer with 6 divisions was created to accurately capture the boundary flow. Similarly, a growth rate of 1.2 was used.
- An overall mesh sizing of 0.25m was created to obtain a highly fine mesh.
- The meshed geometry then proceeded for setup in Ansys Fluent.
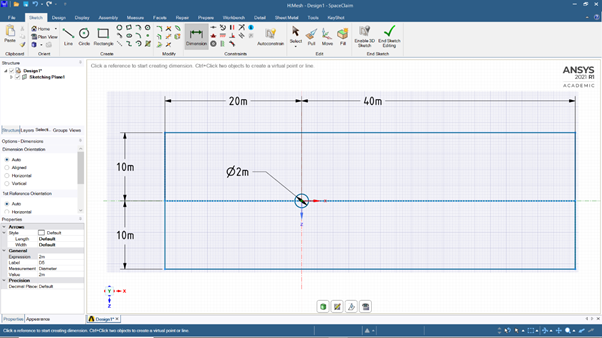
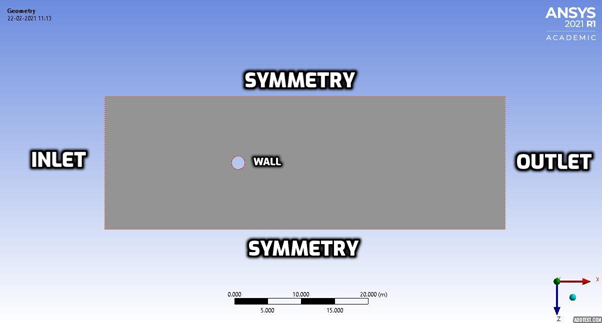
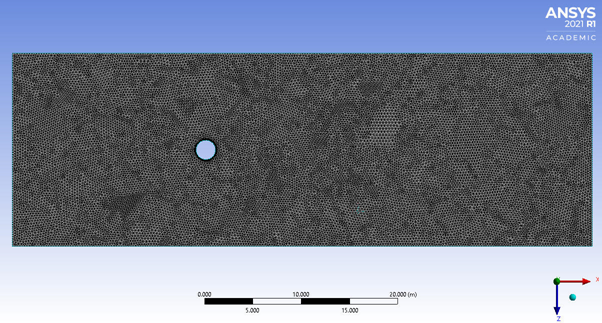
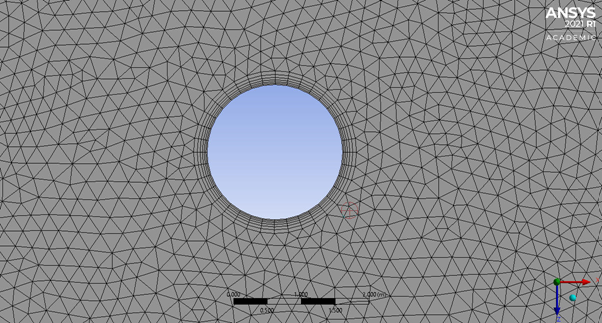
Setting up the case in Ansys Setup –
- A pressure-based solver with absolute velocity formulation and steady-state flow was taken into consideration.
- While analysing vortex shedding (Von Karman Street), a transient solver was used to accurately analyse each time step.
- For simulations with Reynolds number of Re = 10, 100, and 1000, a laminar model was used since Re < 2300.
- For simulations with Reynolds number of Re = 10000 and 100000, a K-omega SST turbulence model was used since Re > 2300.
- A customized material with a viscosity of 0.02kg/ms was created using the create/edit materials tab and the free stream velocity was altered to vary the Reynolds number.
- In cell zone conditions, the entire planar surface was given the properties of the customized material.
- The named selections and boundary conditions are shown in the figures below.
- The inlet velocity was kept as 0.1, 1, 10, 100, 1000 to get a Re = 10, 100, 1000, 10000 and 100000 respectively.
- Since we have to calculate the coefficient of drag and lift, reference values were changed to suite this specific scenario.
- From the results tab, a monitor point was created and the vertex average velocity at that monitor point was calculated by defining a report definition.
- This will be helpful in calculating the Strouhal number for vortex shedding in case of a time dependent transient simulation
- A simple scheme was used, since the coupled scheme is mainly used for compressible flows
- A contour plot of velocity and pressure was created from the graphics option, and a solution animation was also defined for velocity
- Hybrid initialization was done on each case and the solution was calculated for a total of 1000 iterations.
- For transient simulations, the following values were used
- Time step size = 0.1s
- No of iterations per time step = 20
- No of time steps = 500
- Total iterations = 10,000
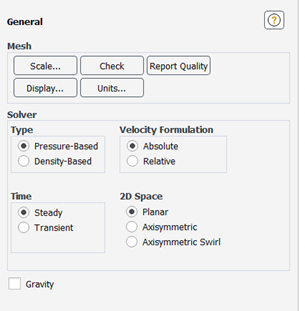

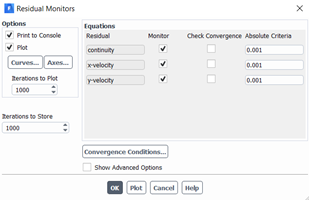
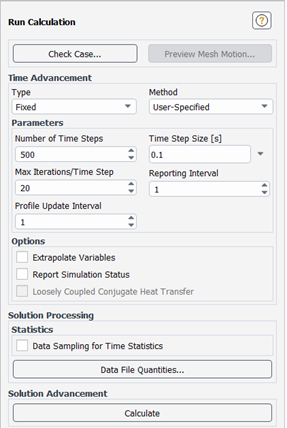
Reference Values –
Area = 2m²
Length = 2m
Depth = 1m
Velocity = varies according to Reynolds number
Temperature = 288.16K
Viscosity = 0.02kg/m. s
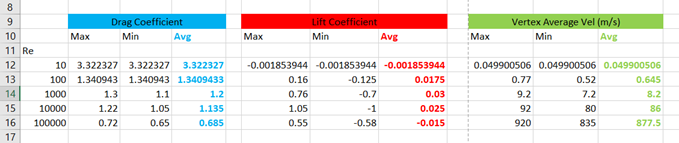
Research Papers for Validation of Values with < 5% error
- Numerous observations can be made from the tabulation above
- It was observed that for simulations involving Re = 10, the drag/lift coefficient and vertex average velocity plots (at monitor point), did not oscillate after a certain number of iterations.
- For Re = 100, the coefficient of drag plot did not show any oscillations, whereas the lift coefficient and vertex average velocity plots oscillated after a specific number of iterations.
- For all simulations with Re > 1000, the drag/lift coefficient and the vertex average velocity plots showed stable oscillations after reaching around 250 iterations.
- It can also be observed that the lift coefficient of the cylinder for all the iterations was near to 0 since the top view of the cylinder symmetrical with 0 gravity.
- It was also observed that the coefficient of drag reduced as the Reynolds number increased with the cylinder having a drag coefficient of 0.685 at Re = 100,000
- Furthermore, from the vertex average velocity plots, it can be inferred that the velocity at the monitor point is around 12% less than the free stream velocity.
Part 1 - Results and Discussions – Steady and Transient case for Re = 100
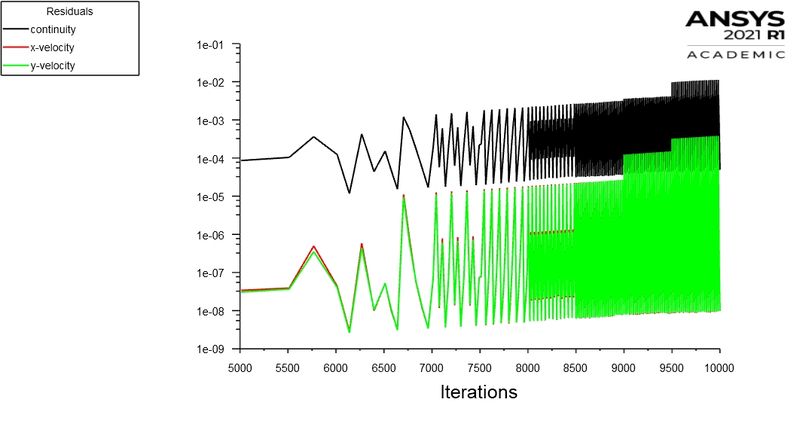
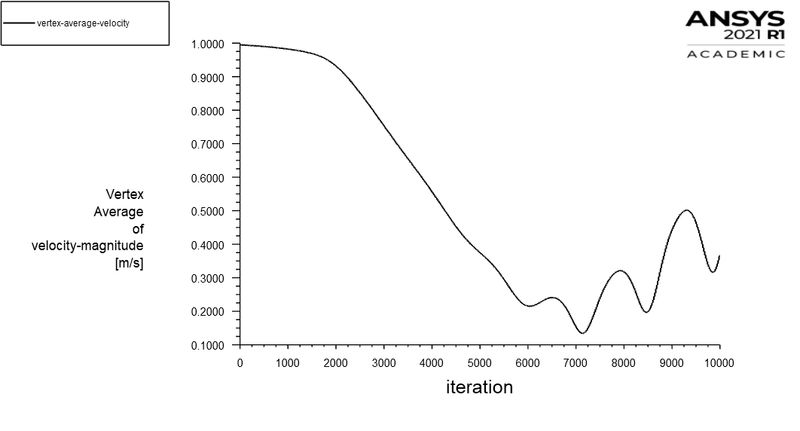
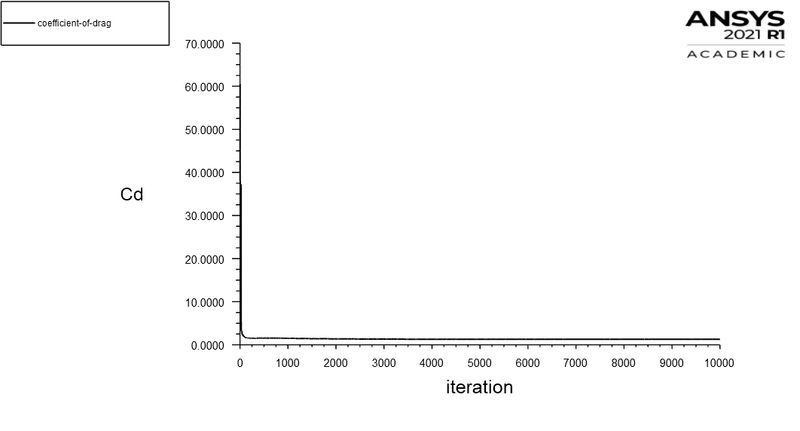
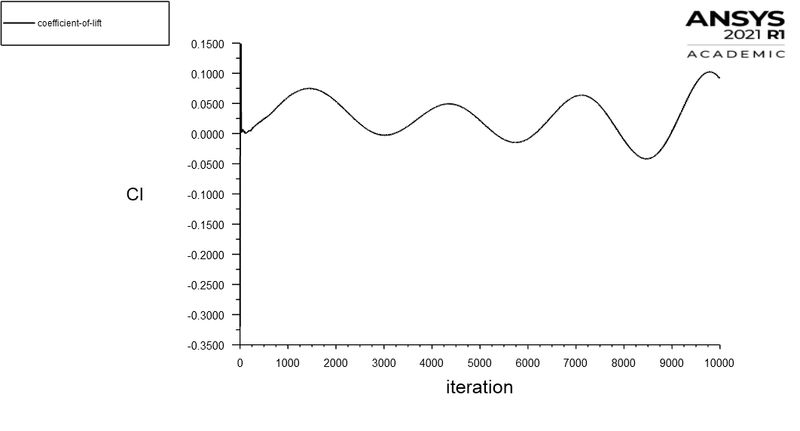
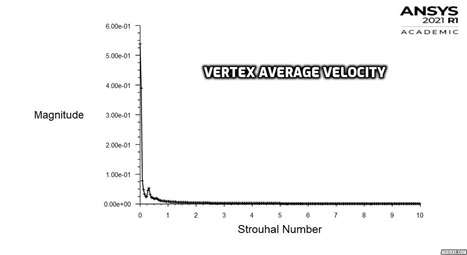
Strouhal Number – 0.42 at peak magnitude
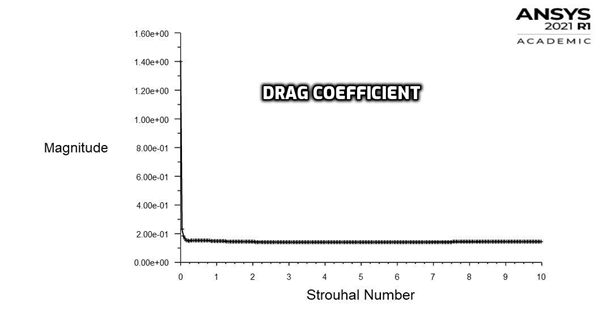
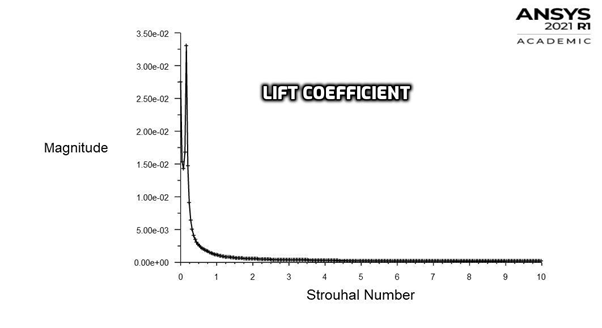
Strouhal Number = 0.374 at peak magnitude
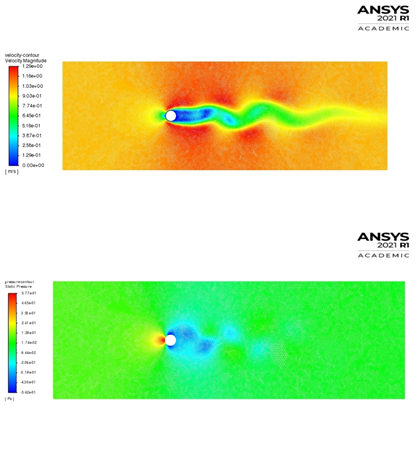
- The K-epsilon model is accurate only for completely turbulent flows and flows that are non-separated.
- It may also cause stability issues because of stiffness
- k- epsilon model predicts well far from the boundaries (wall) and k- omega model predicts well near the wall.
- Even though it depends on Y+, an SST model is a combination of these.
- SST model used good mesh at the boundary and with wall treated usually works in most cases, but again it is problem specific.
Part 2 - Results and Discussions –
Convergence Criteria –
- For the transient simulation with a total number of 500 time steps and 20 iterations for each time step, the residuals oscillate at a constant frequency after a certain amount of iterations
- Considering the steady-state analysis at a Re = 10, the residuals do converge properly since vortex shedding is not observed at Re = 10.
- For simulations involving Re = 100, 1000, 10000, and 100000, the residuals converge by oscillating in a repeated pattern – hence convergence for these cases can be identified
Case 1 à Re = 10
- Free stream velocity = 0.1m/s
- Laminar Model used
- Iterations = 3000
- Diameter of cylinder = 2m
- Density of fluid = 1kg/m^3
- Dynamic viscosity = 0.02kg/m.s
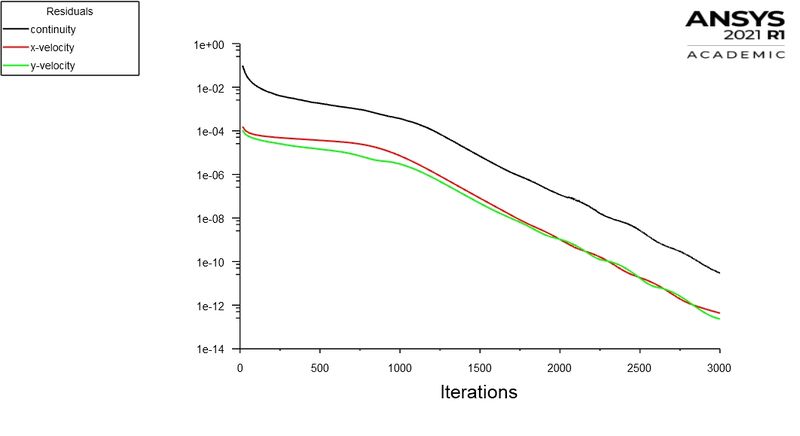
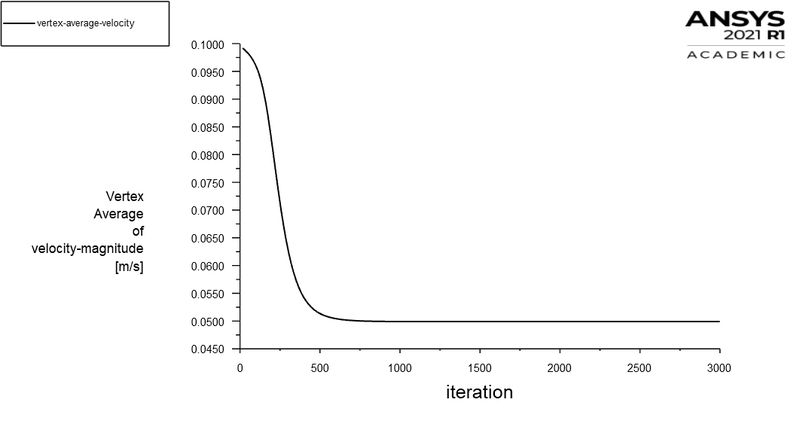
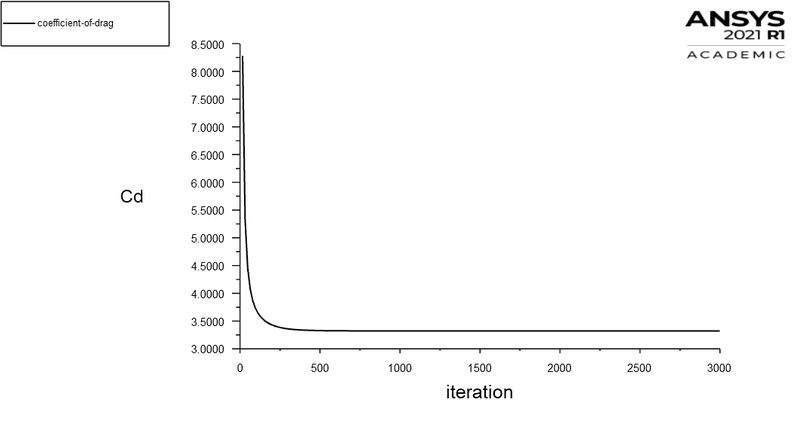
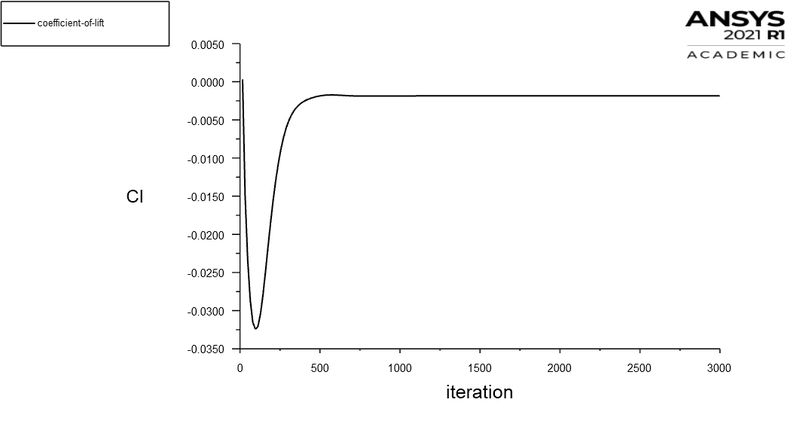
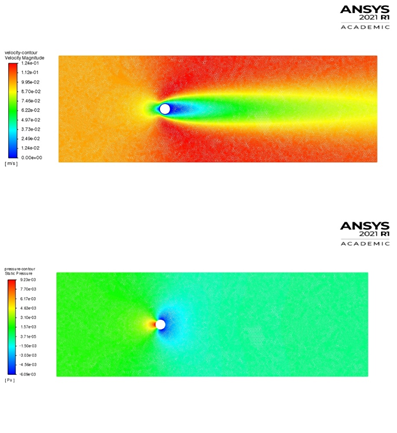
Case 2 à Re = 100
- Free stream velocity = 1m/s
- Laminar Model used
- Iterations = 1000
- Diameter of cylinder = 2m
- Density of fluid = 1kg/m^3
- Dynamic viscosity = 0.02kg/m.s

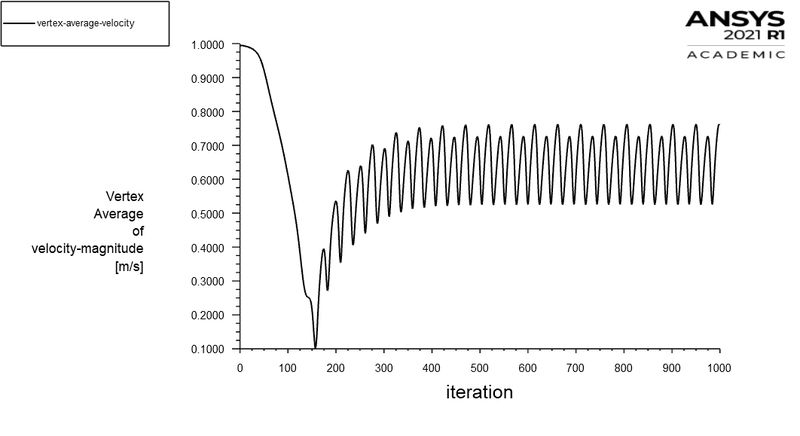
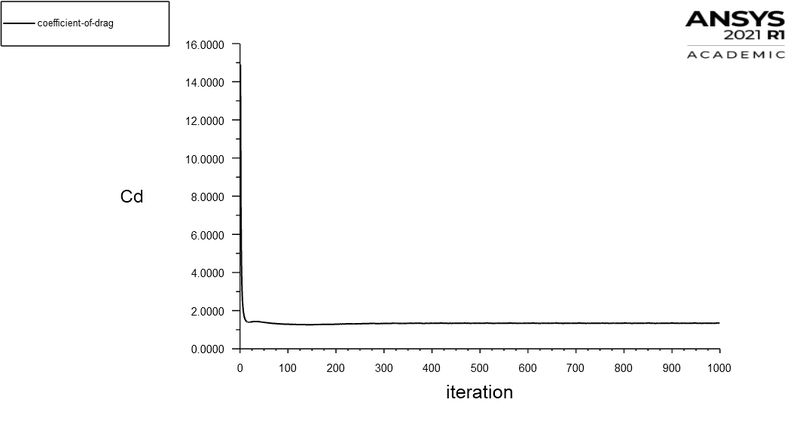

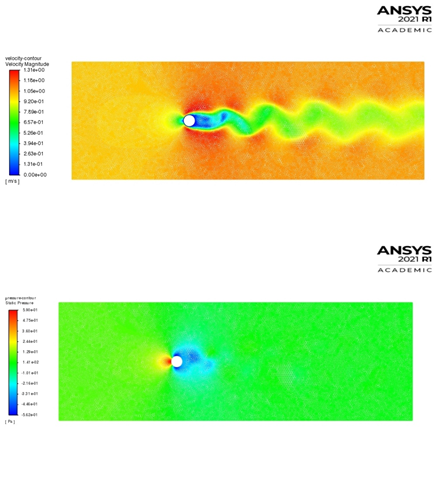
Case 3 à Re = 1000
- Free stream velocity = 10m/s
- Laminar model used
- Iterations = 1000
- Diameter of cylinder = 2m
- Density of fluid = 1kg/m^3
- Dynamic viscosity = 0.02kg/m.s
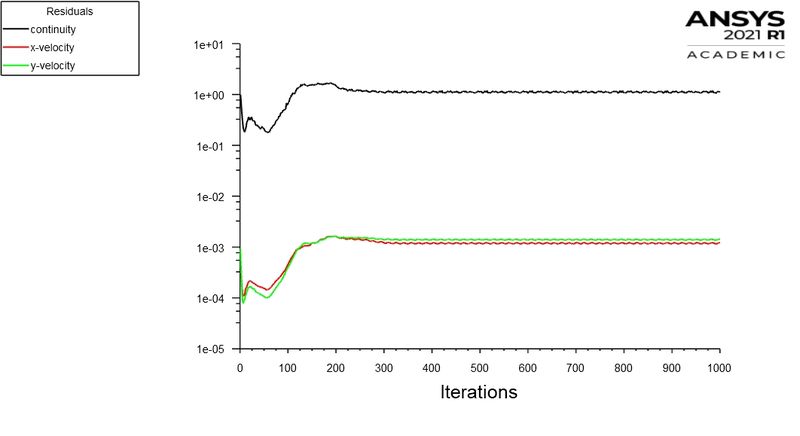

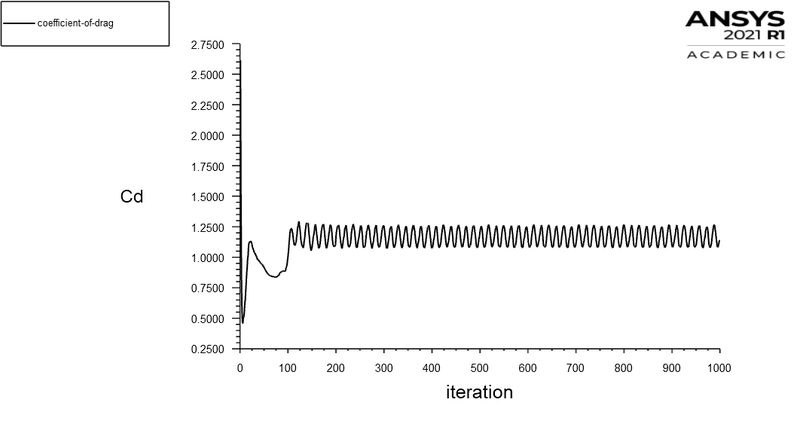
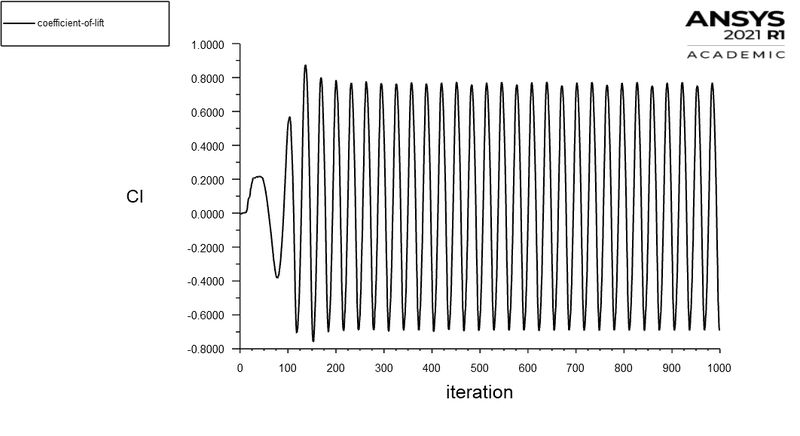
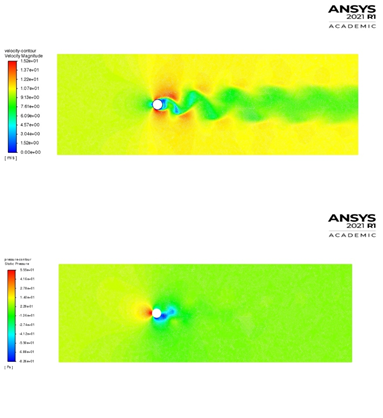
Case 4 à Re = 10,000
- Free stream velocity = 100m/s
- K-omega SST Turbulence model used
- Iterations = 1000
- Diameter of cylinder = 2m
- Density of fluid = 1kg/m^3
- Dynamic viscosity = 0.02kg/m.s
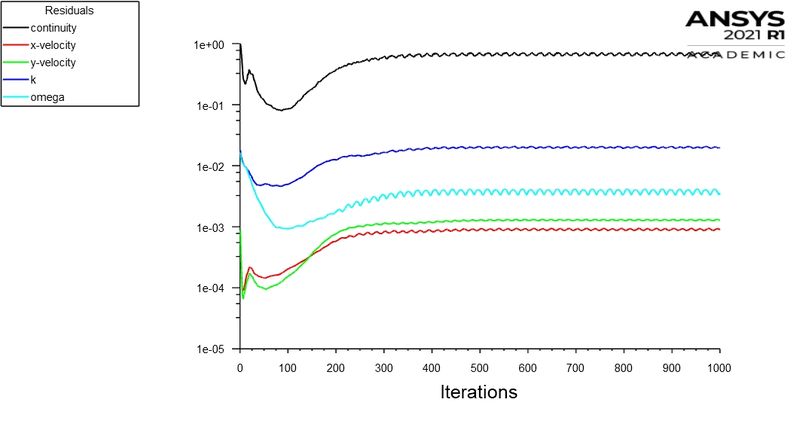
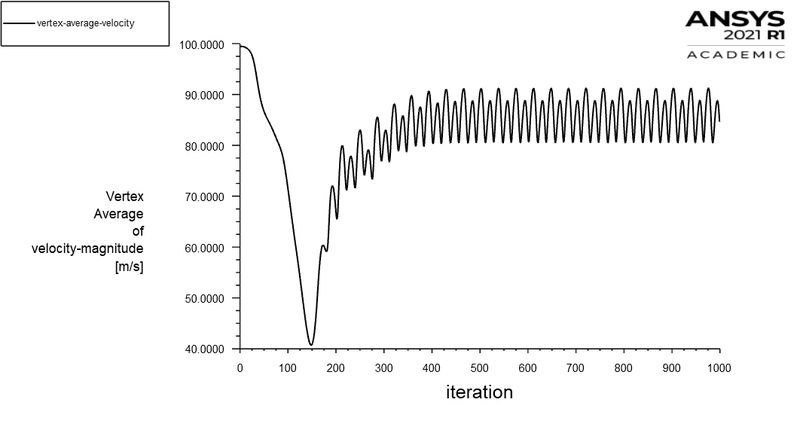
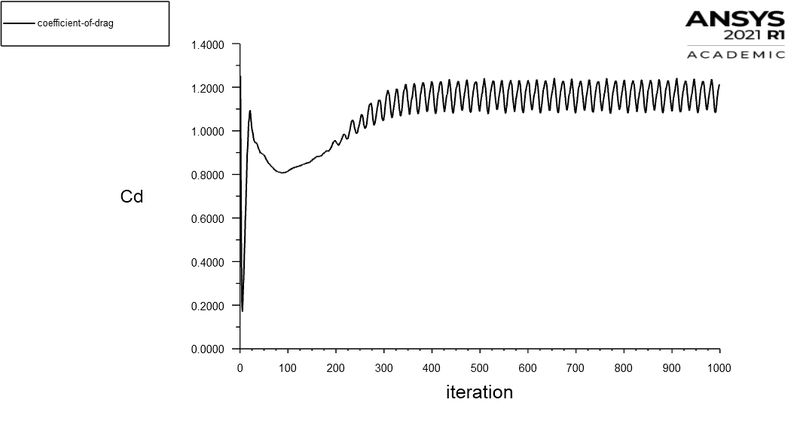
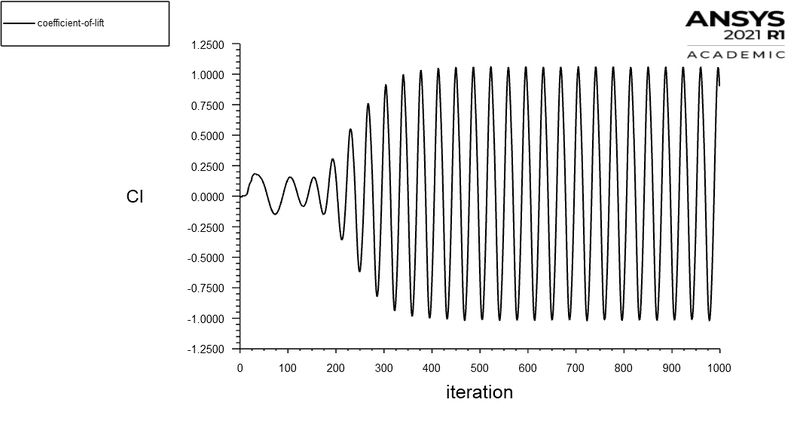
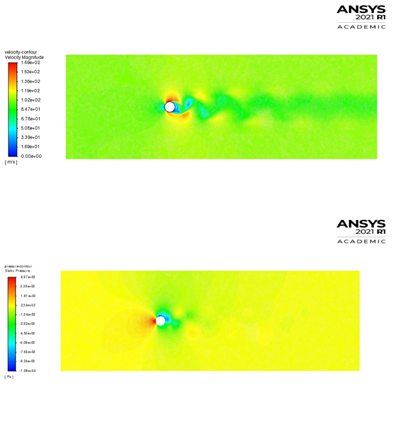
Case 5 à Re = 100,000
- Free stream velocity = 1000m/s
- K-omega SST turbulence model used
- Iterations = 1000
- Diameter of cylinder = 2m
- Density of fluid = 1kg/m^3
- Dynamic viscosity = 0.02kg/m.s
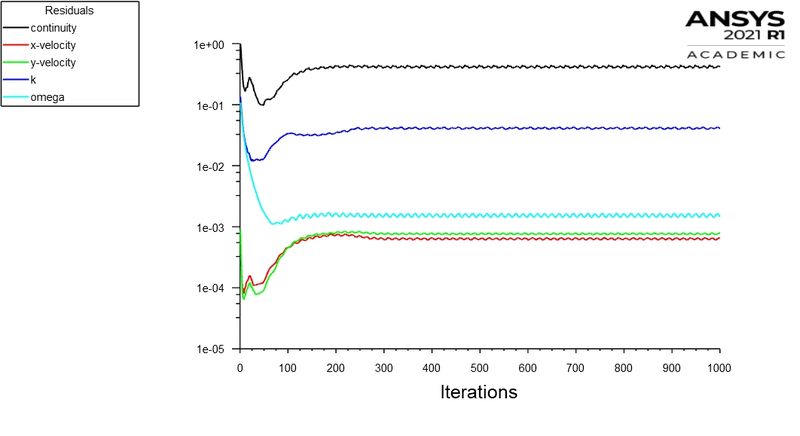
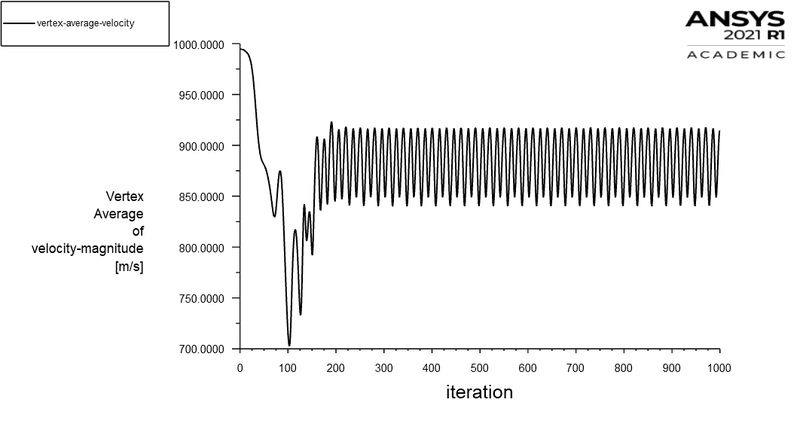
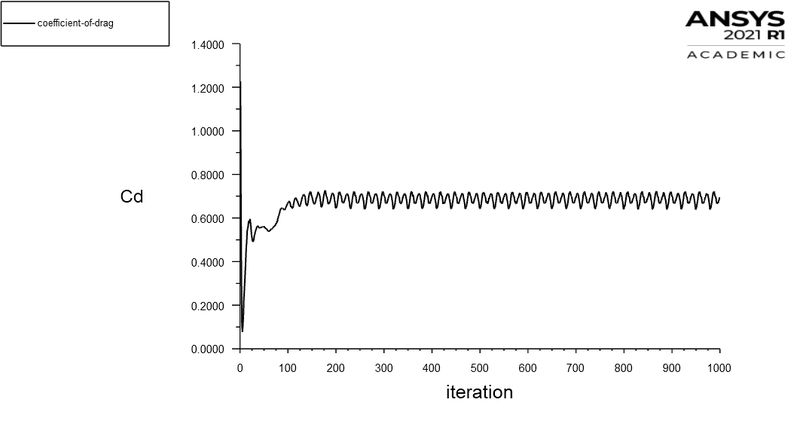
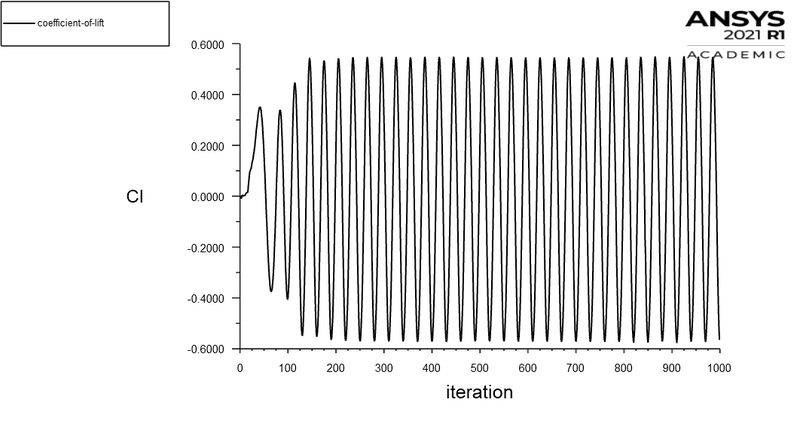
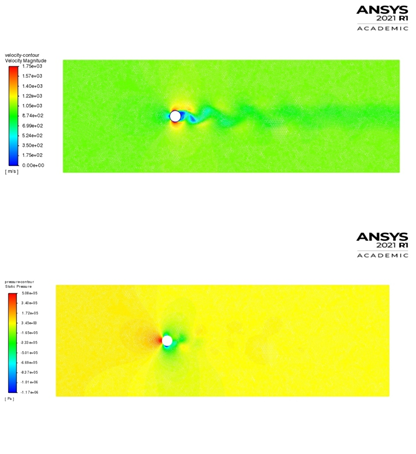
Results and Conclusions –
- It can be observed that vortex shedding starts to occur at a Reynolds number of 100
- For simulations with Reynolds number <100, vortex shedding does not occur
- The coefficient of drag decreases slightly for every increase in Reynolds number
- Since the external body(cylinder) is symmetrical, and there is no gravity, the coefficient of lift nears 0 in all cases
Reference Research Papers –