Aim-
To illustrate the mechanism of spherical, cylindrical, translational and revolute joints between rigid bodies and deformable bodies. The various types of joints can be created in LS-Dyna using the CONSTRAINED_JOINT keyword.
Procedure-
A. Joints between rigid bodies
- The various types of joints between rigid bodies can be created in LS-Dyna using the Constrained_Extra_Nodes keyword.
1. Spherical joint
- The first step is to create two spherical bodies in LS-Dyna using the Entity option under Shape mesher in Element and mesh, and choosing spherical shell. The upper elements of the outer shell are deleted in order to get the required shape.
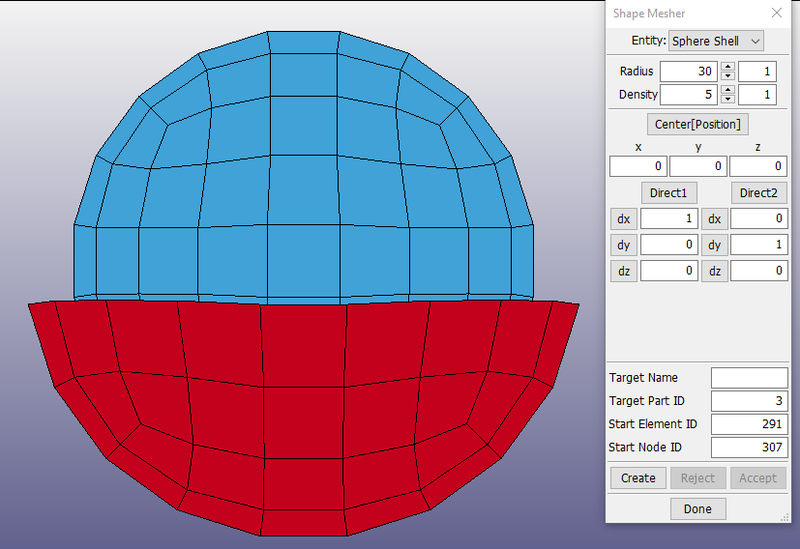
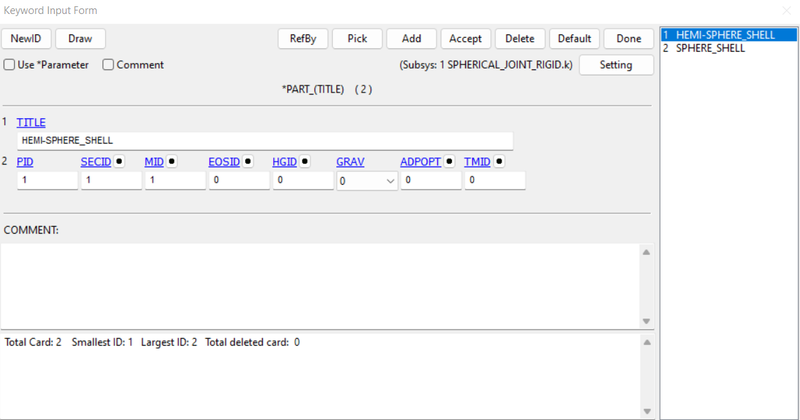
- Two nodes are created for constraining, using Node edit option under Element Tools.
- The first node (305) is constrained to part 1, and the second node (305) is constrained to part 2. using CONSTRAINED_EXTRA_NODES, as shown below
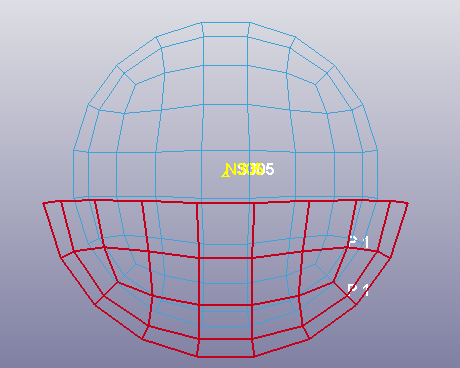
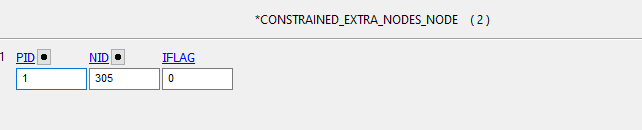
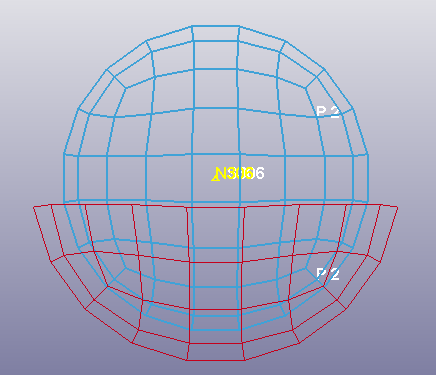

- Now we will create a spherical joint, which is created between them, using the CONSTRAINED_JOINT menu.
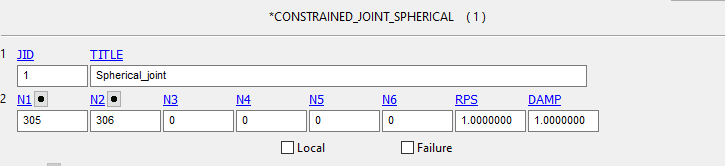
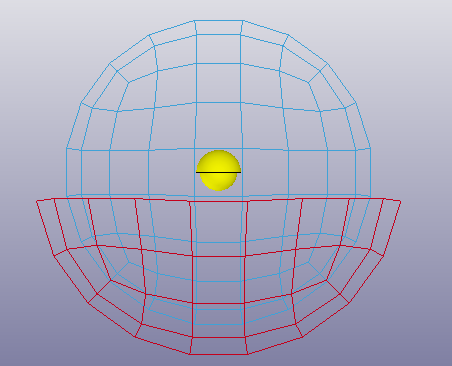
- An initial velocity of 20 mm/ms is applied to the part 2 (inner sphere), in all three rotational directions.
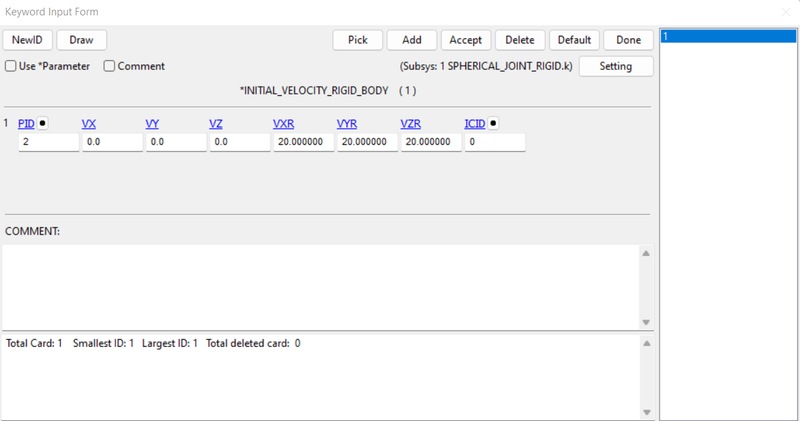
- Now we will give control cards for running the simulation, we will use timestep & termination cards.
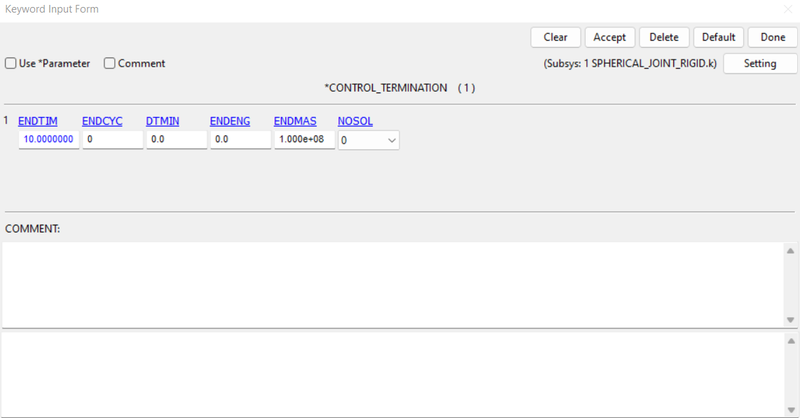
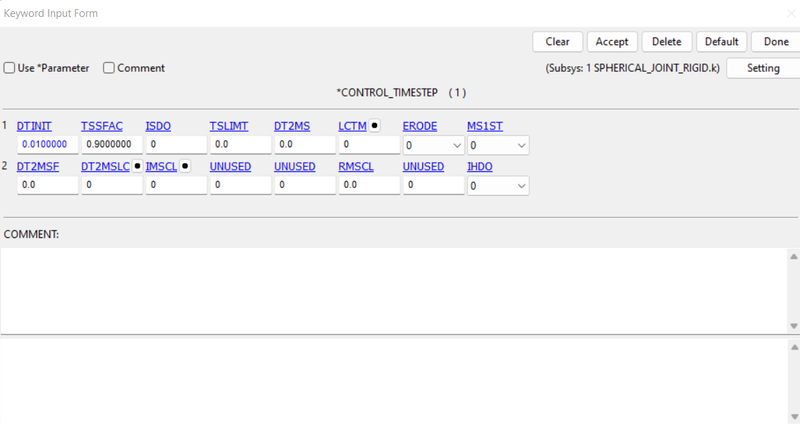
- Now we will check the model for errors and run the simulation.
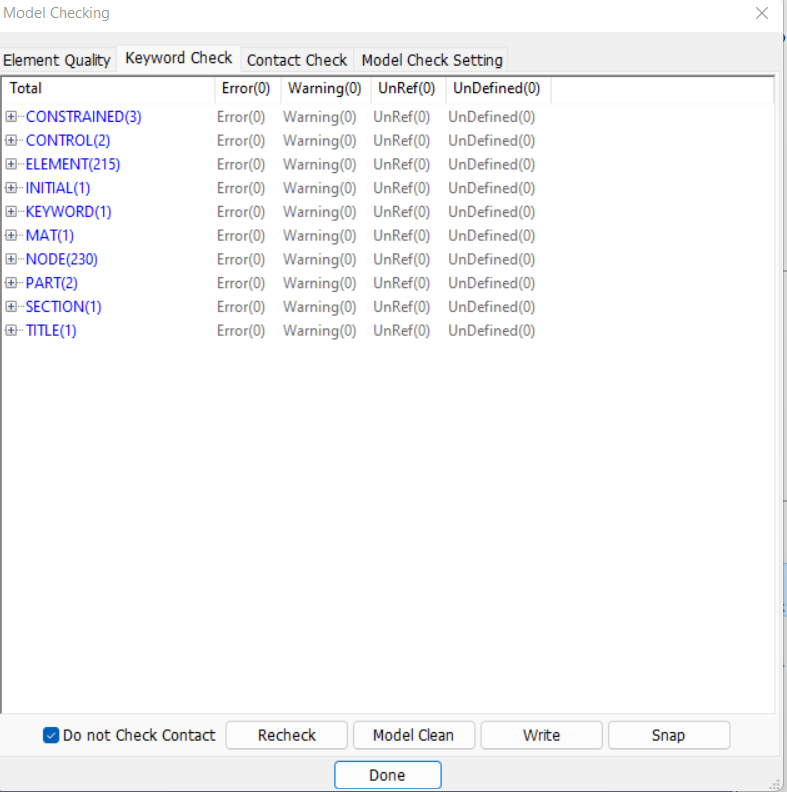
- Since there is no error in the model, so we can run the simulation.
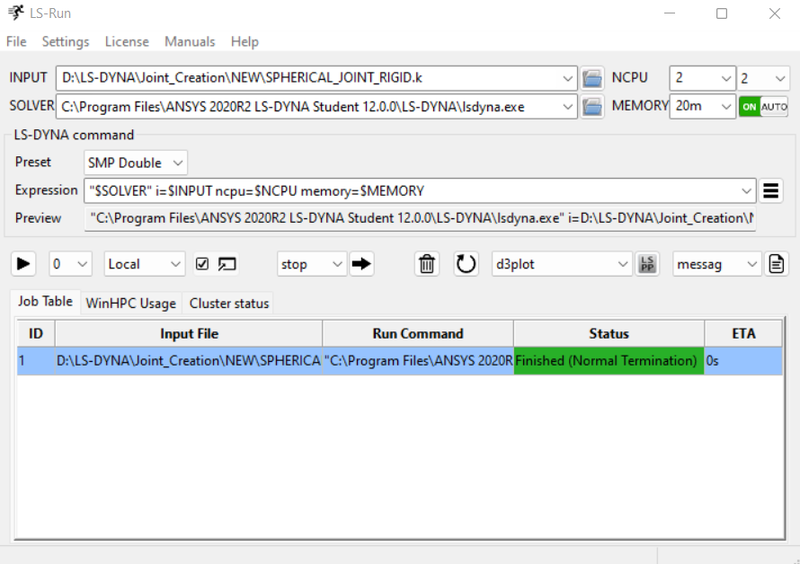
- Since it has run wil normal termination so our consideration is proper.
2. Revolute joint
- The first step is to create two bodies in LS-Dyna using the Entity option under Shape mesher in Element and mesh, and choosing 4N shell.
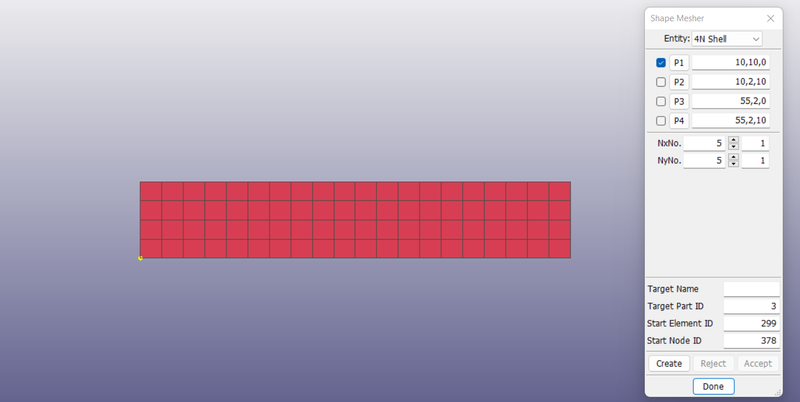
- Now we will copy and offset the given model to get the two parts.
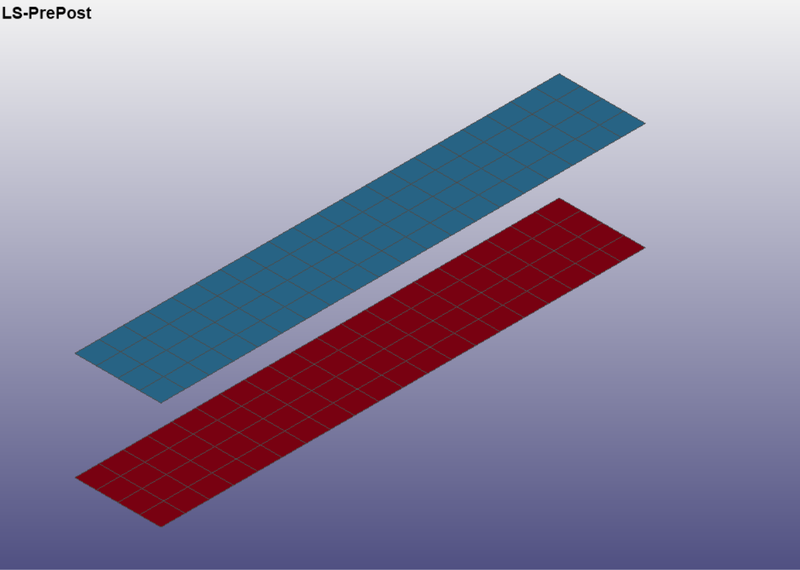
- Two pairs of nodes are created for constraining, using Node edit option under Element Tools. The nodes 101, 102 are constrained to part 1 and 103,104 to part 2 respectively, using CONSTRAINED_EXTRA_NODES card. as shown below.
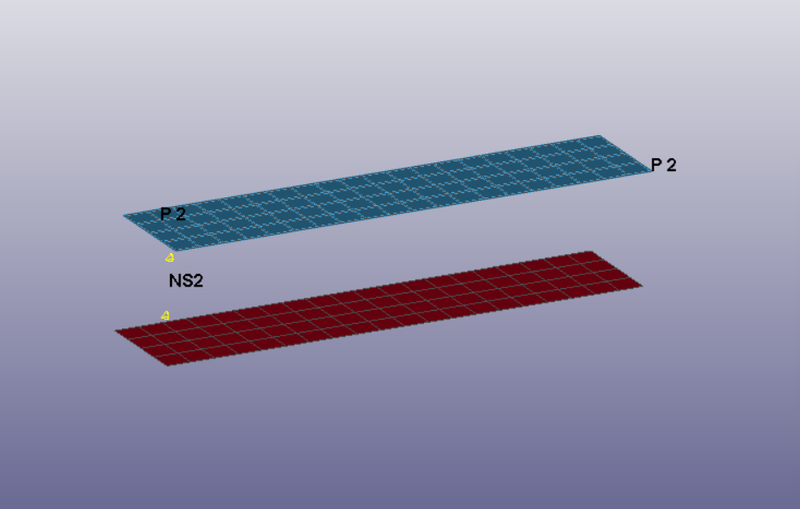

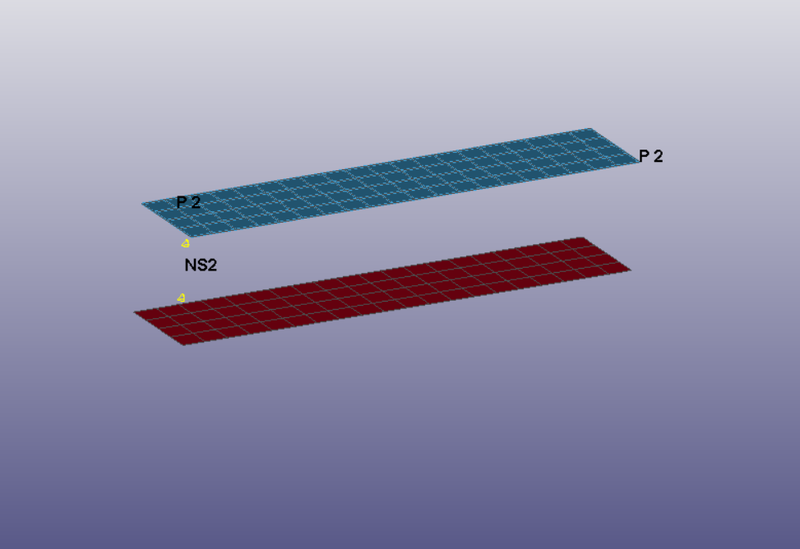

- A revolute joint is then created between them, using the CONSTRAINED_JOINT menu, using nodes 101 and 102 of part 1 and103,104 of part 2.
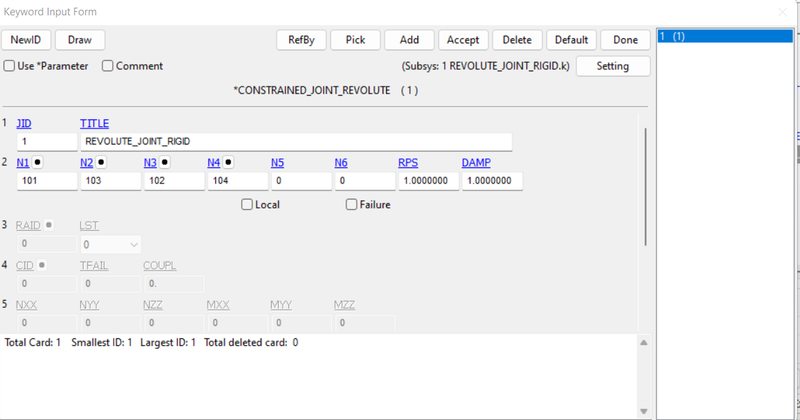
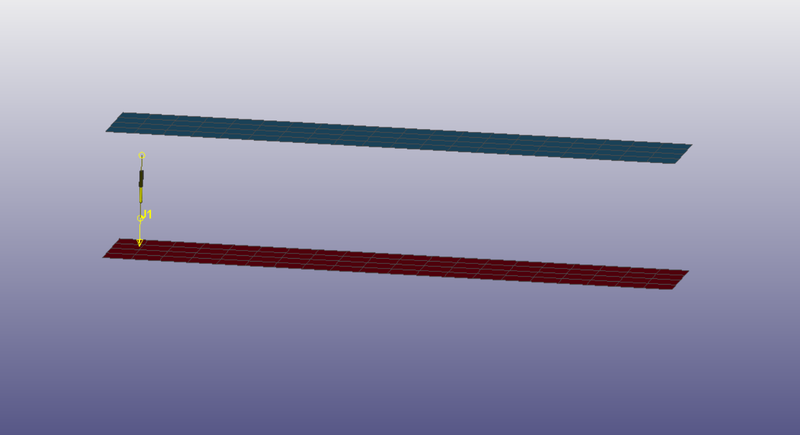
- The material and section properties are the same as that of the spherical joint.
- Now here Part 1 (red) is fixed, and part 2 (blue) is the moving part. The part 1 is fixed with SPC's at all nodes, in order to prevent motion, and a prescribed motion is given to part 2, as shown below.
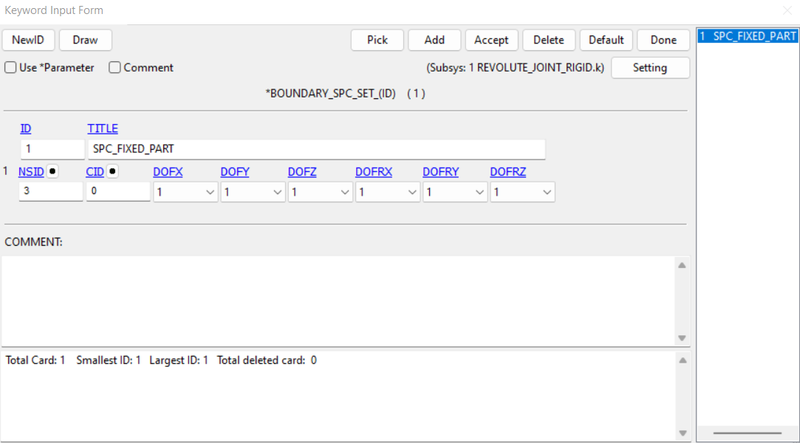
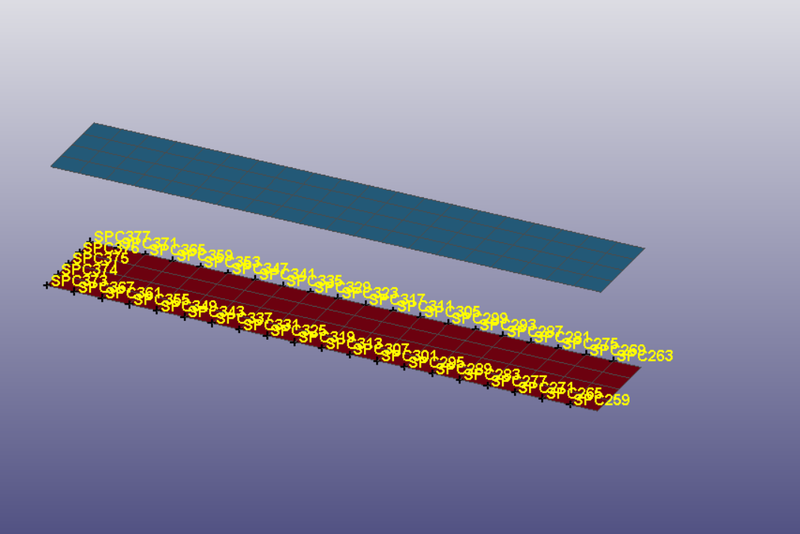
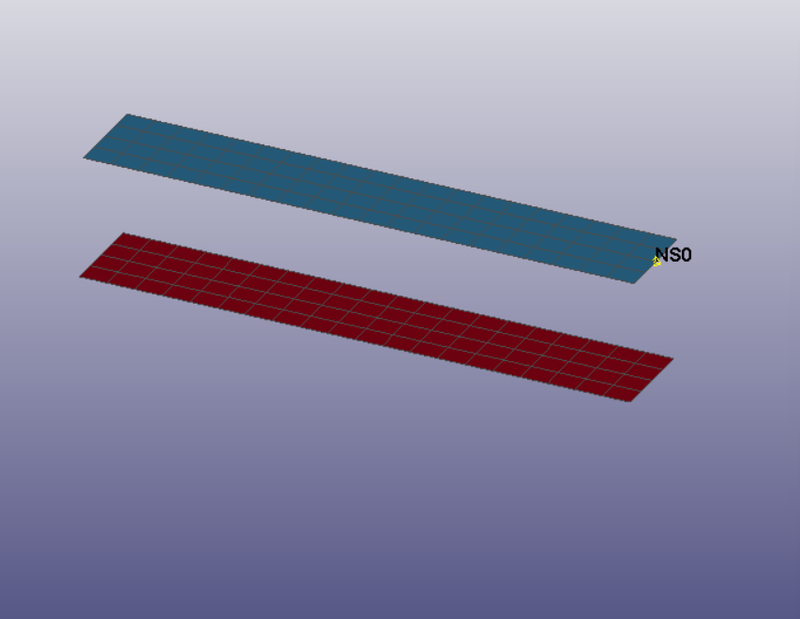
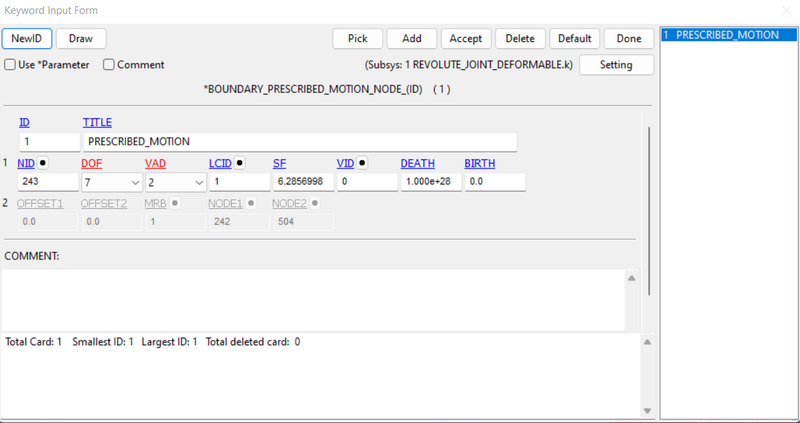
- Here we have defined the curve for motion set from define curve option.
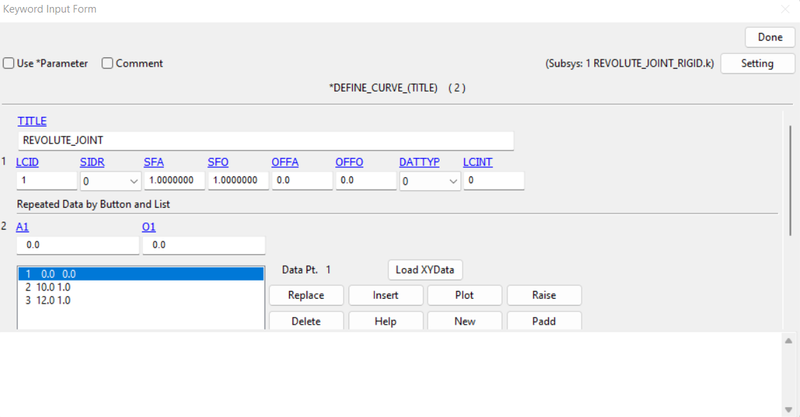

- Now we will define one more curve for timestep.
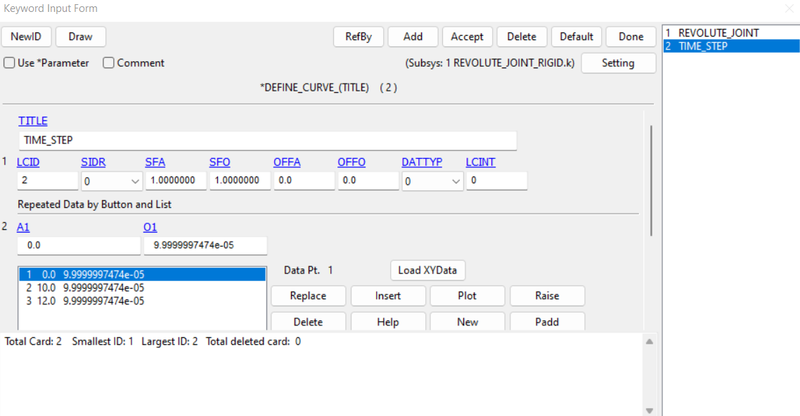
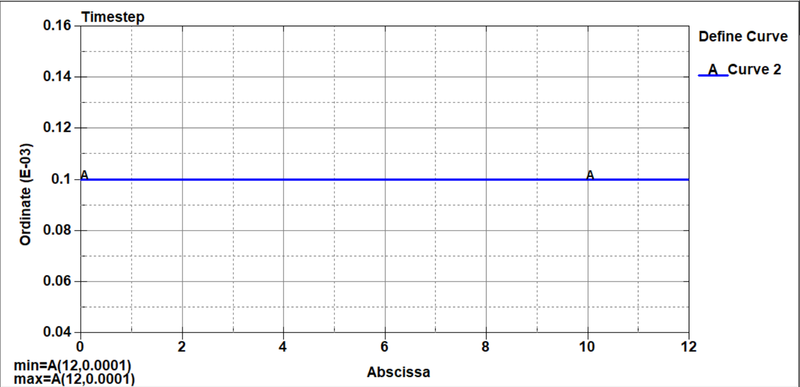
- Now again we will define the control_termination and control_timestep like spherical joint and here for time step we will provide lcid curve we defined earlier.
- Now we will check the model for errors and run the simulation.
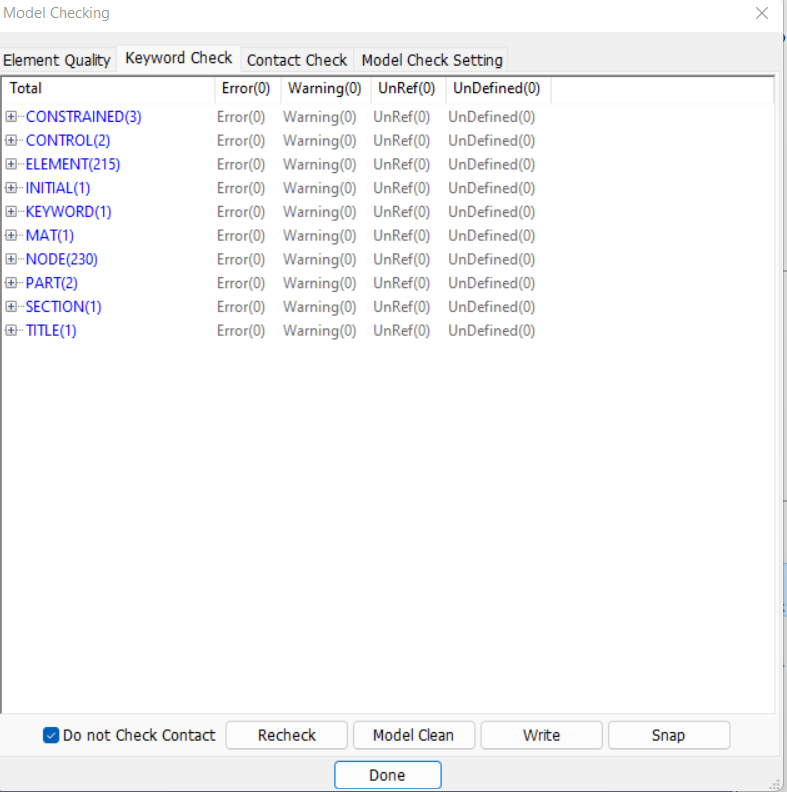
- Since there is no error in the model, so we can run the simulation.
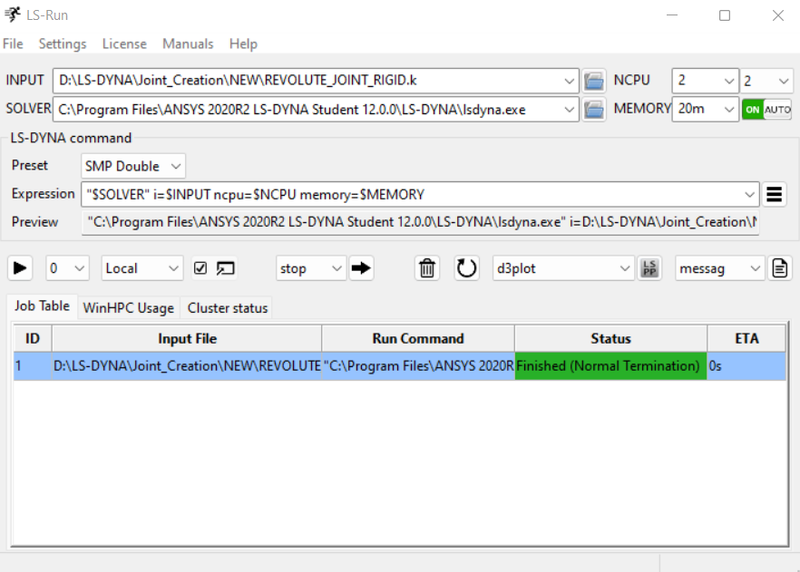
3. Cylindrical Joint
- The first step is to create two bodies in LS-Dyna using the Entity option under Shape mesher in Element and mesh, and choosing cylinder shell.
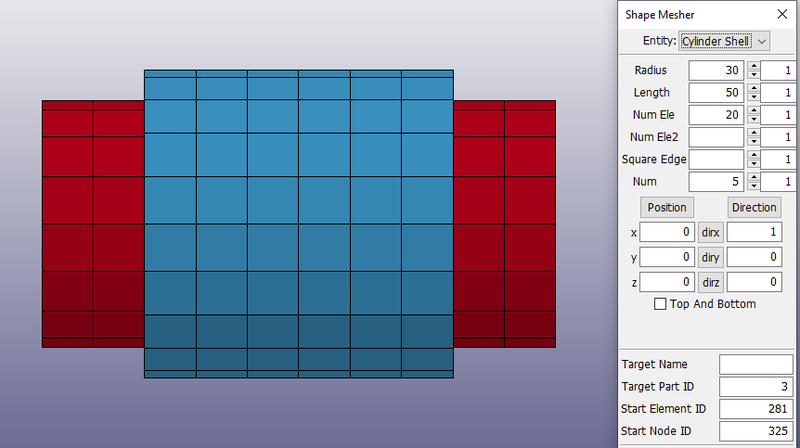
- The material and section properties are the same as that of the spherical joint.
- Now two pairs of nodes are created for constraining, using Node edit option under Element Tools. The nodes 321, 323 are constrained to part 1 and 322,324 to part 2 respectively, using CONSTRAINED_EXTRA_NODES card, as shown below.
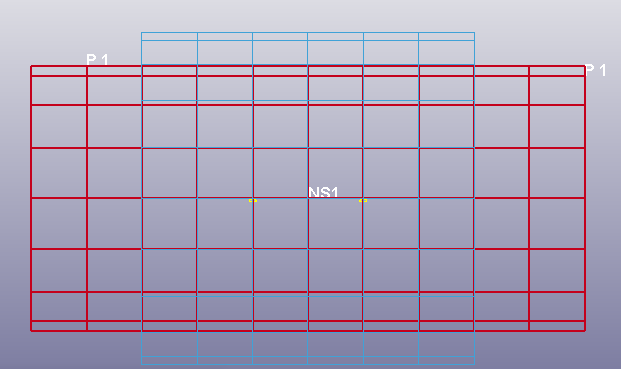

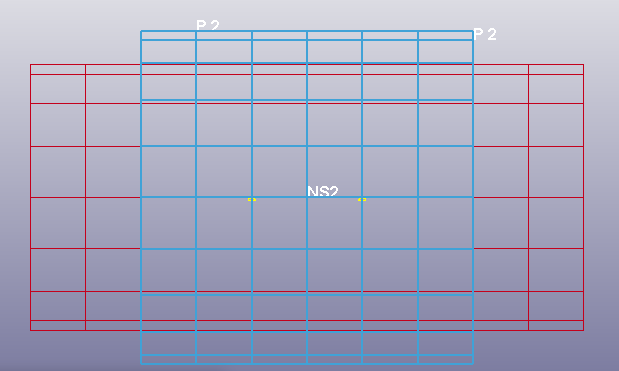
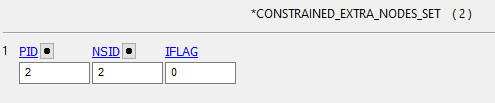
- A cylindrical joint is then created between them, using the CONSTRAINED_JOINT menu, using nodes N1 and N3 of part 1 and N2,N4 of part 2.
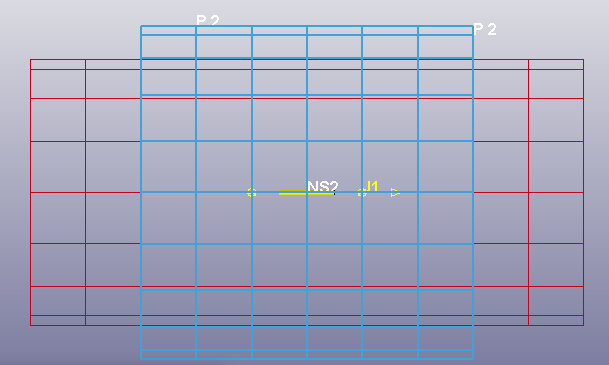
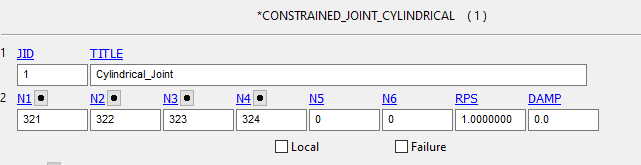
- Now Part 2 (blue) is fixed, and part 1(red) is the moving part. An initial velocity of 10 mm/ms is given to part 1 in the x(translational) direction.

- The simulation is set to run for 10ms, and DTINIT is given as 0.01 ms, by defining control_termination and control_timestep cards.
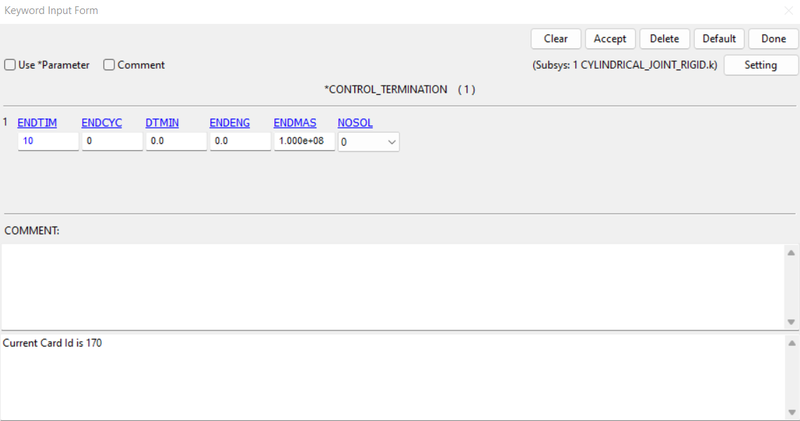
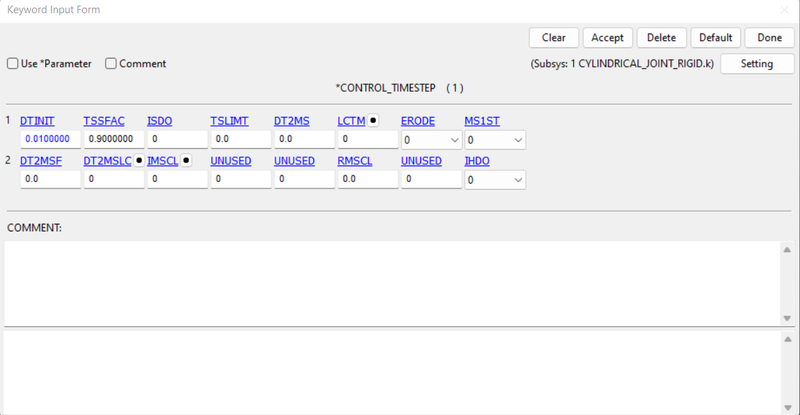
- Now we will check the model for errors and run the simulation.
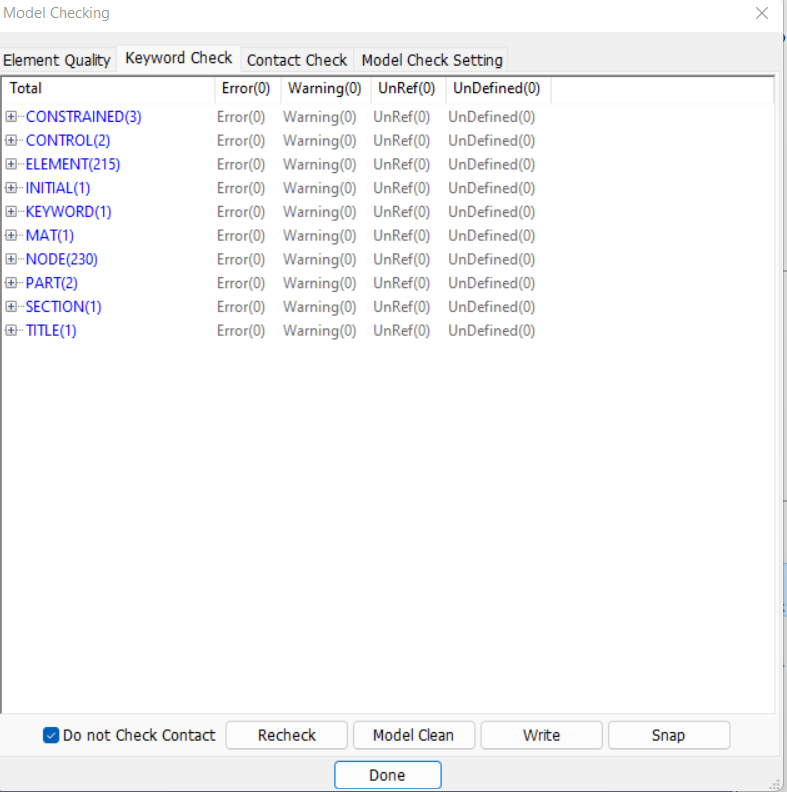
- Since there is no error in the model, so we can run the simulation.
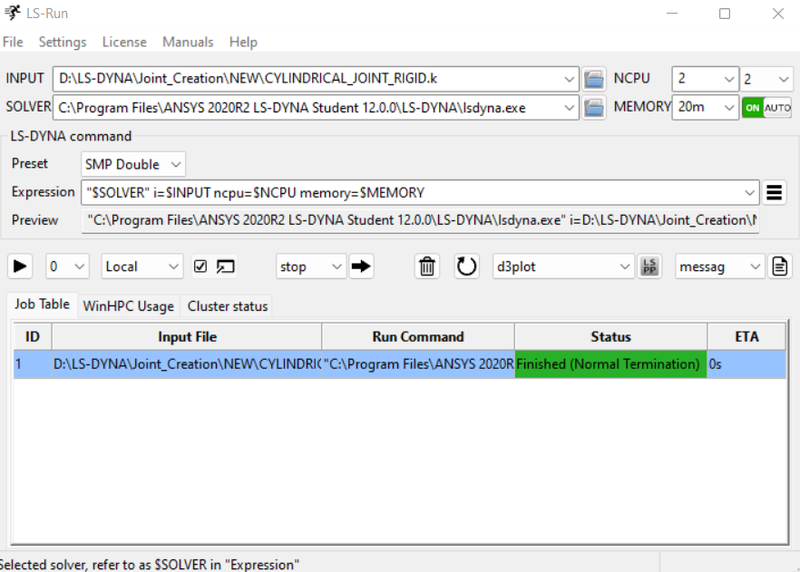
4. Translational Joint
- The first step is to create two bodies in LS-Dyna using the Entity option under Shape mesher in Element and mesh, and choosing box shell.
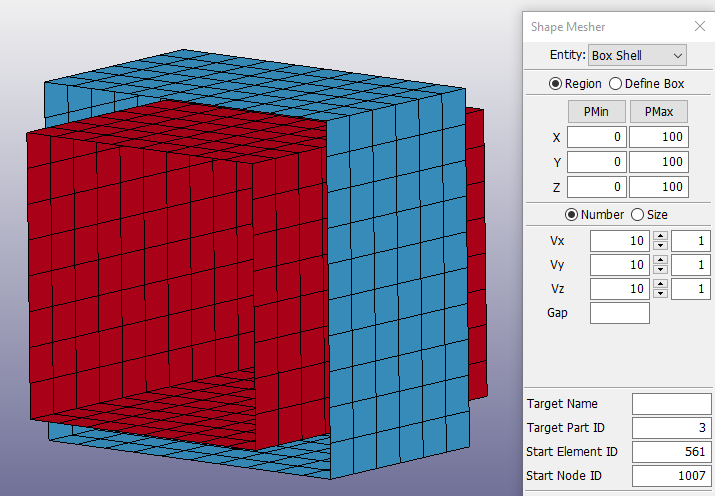
- The material and section properties are the same as that of the spherical joint.
- Three pairs of nodes are created for constraining, using Node edit option under Element Tools. The node pairs 1001,1002 and 1003,1004 are coincident and collinear. The third pair 1005,1006 is coincident, and slightly away from the axis of the other two pairs, in between them. The nodes 1001,1003 and 1005 are constrained to part 1 and 1002,1004 and 1006 to part 2 respectively, using CONSTRAINED_EXTRA_NODES card, as shown below.
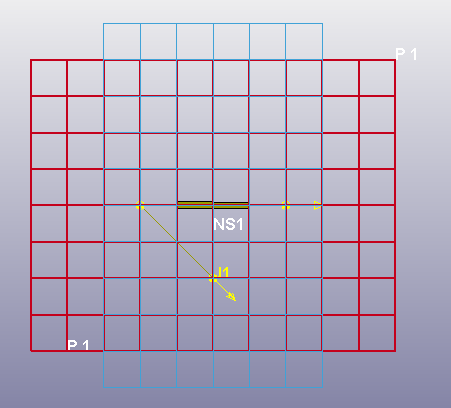
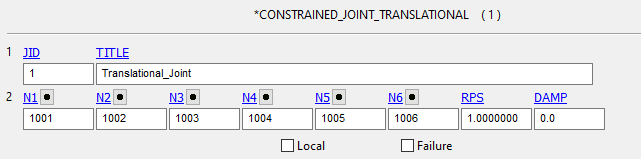
- A translational joint is then created between them, using the CONSTRAINED_JOINT menu, using nodes N1,N3 and N5 of part 1 and N2,N4 and N6 of part 2, as shown above.
- Part 2 (blue) is fixed, and part 1(red) is the moving part. An initial velocity of 10 mm/ms is given to part 1 in the x(translational) direction.

- The simulation is set to run for 10ms, and DTINIT is given as 0.01 ms, by defining control_termination and control_timestep cards.
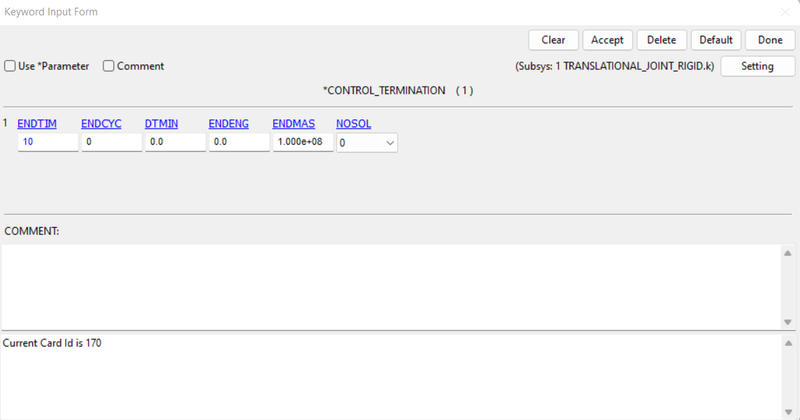
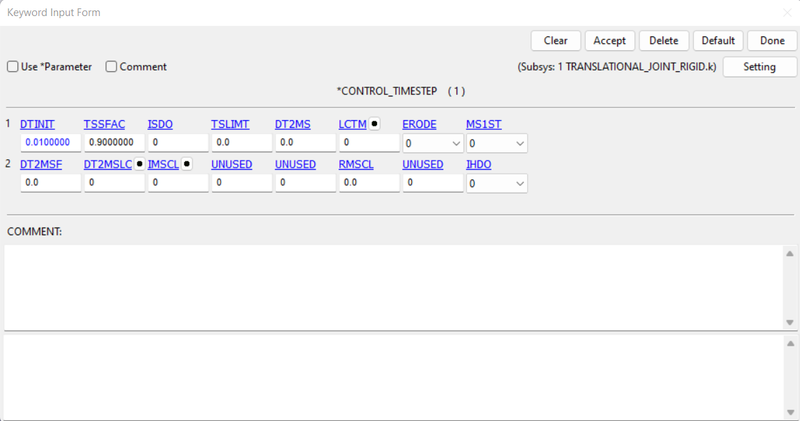
- Now we will check the model for errors and run the simulation.
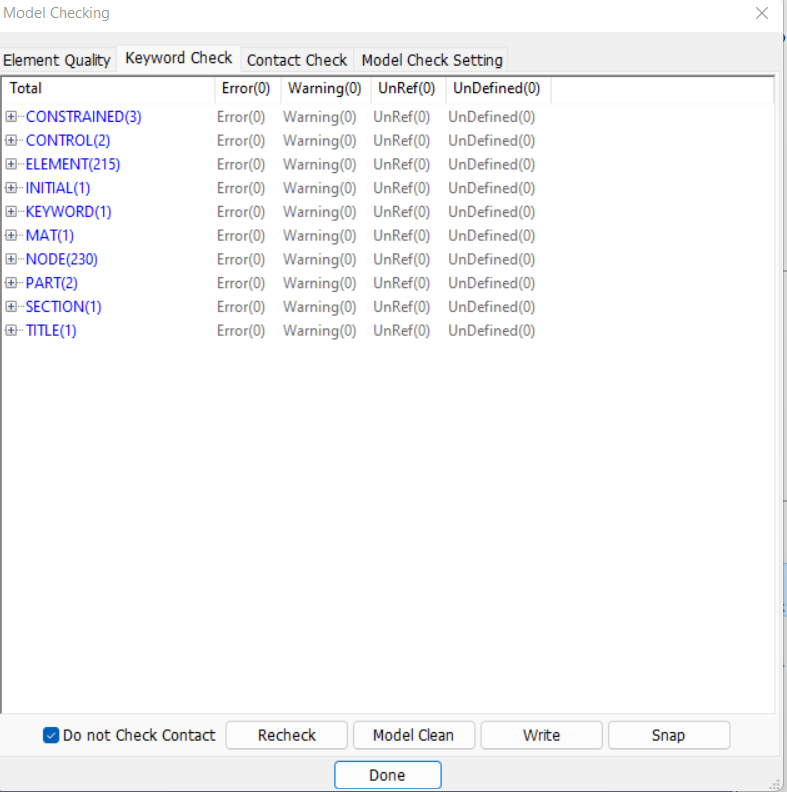
- Since there is no error in the model, so we can run the simulation.
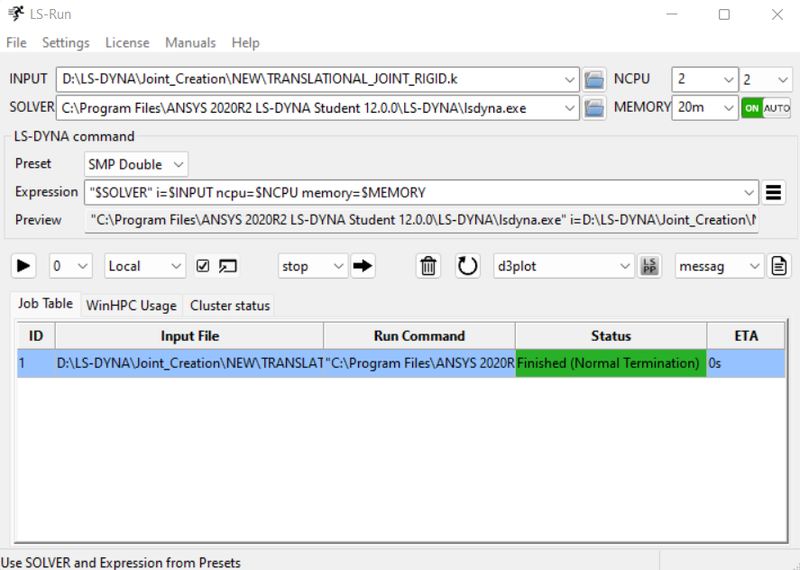
B. Joints between deformable bodies
- The various types of joints between deformable bodies can be created in LS-Dyna using the Constrained_Nodal_Rigid_Body keyword.
1. Spherical Joint-
- The first step is to create two spherical bodies in LS-Dyna using the Entity option under Shape mesher in Element and mesh, and choosing spherical shell. The upper elements of the outer shell are deleted in order to get the required shape.
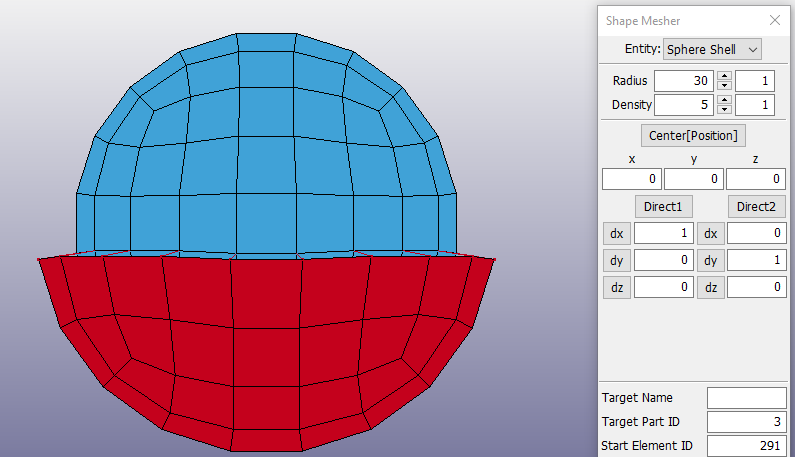
- The material and section properties are the same as that of the rigid spherical joint.
- The CNRB option is used between the peripheral nodes of the outer and inner hemispheres, for connecting them.
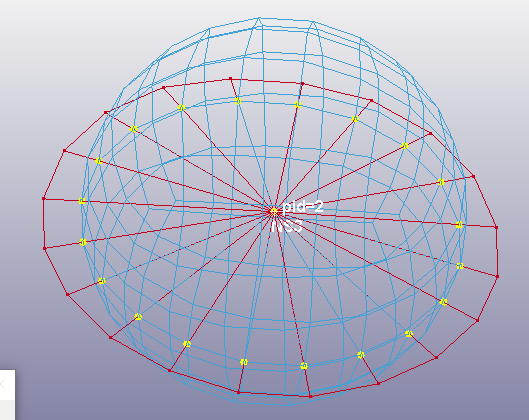
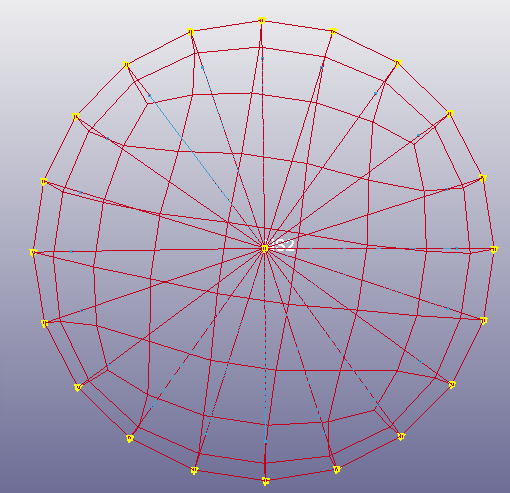
A spherical joint is then created between them, using the CONSTRAINED_JOINT menu.The first node (305) is constrained to part 1, and the second node (306) is constrained to part 2.
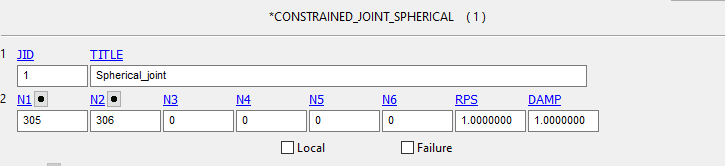
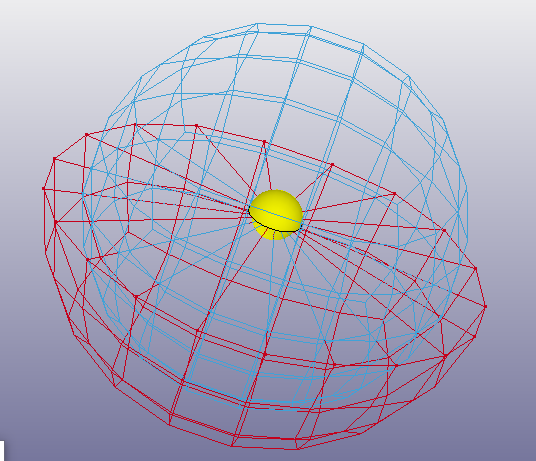
An initial velocity of 20 mm/ms is applied to the part 2 (inner sphere), in all three rotational directions.
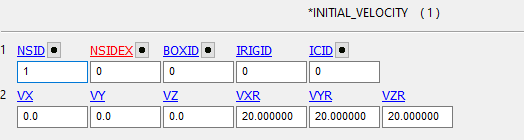
The simulation is set to run for 10 ms, and DTINIT is given as 0.01 ms.
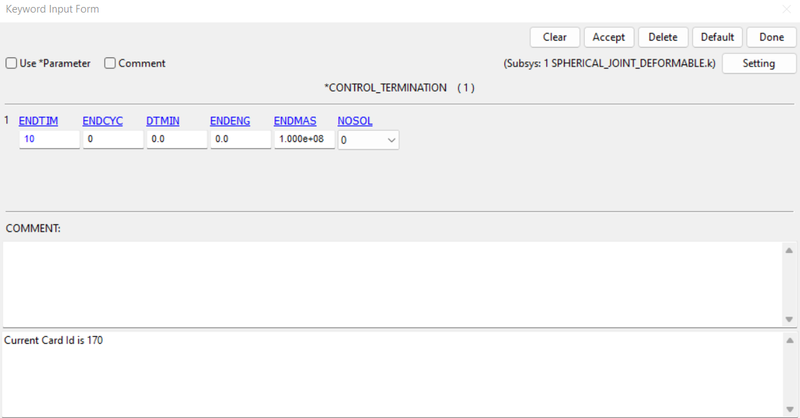
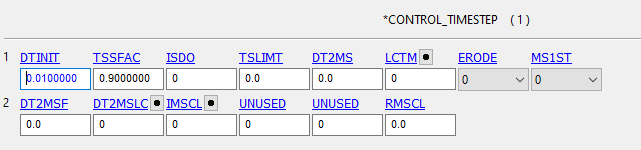
- Now we will check the model for errors and run the simulation.
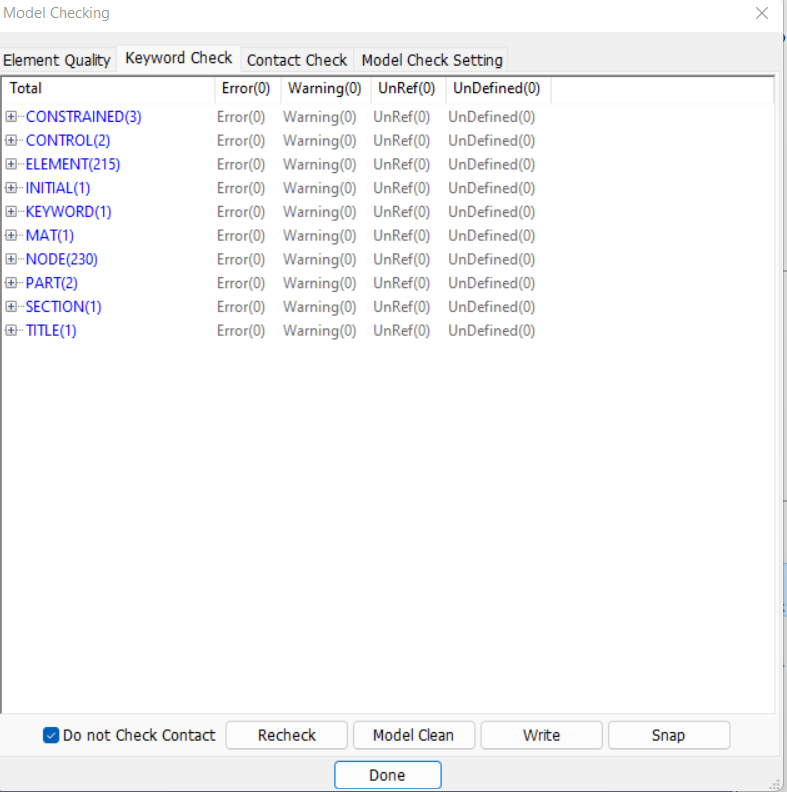
- Since there is no error in the model, so we can run the simulation.
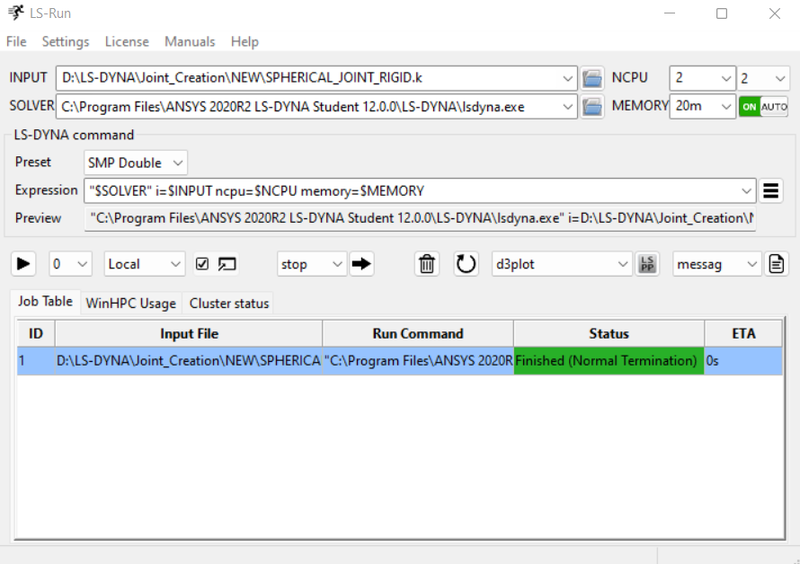
- Since it has run wil normal termination so our consideration is proper.
2. Revolute joint
- The first step is to create two bodies in LS-Dyna using the Entity option under Shape mesher in Element and mesh, and choosing 4N shell.
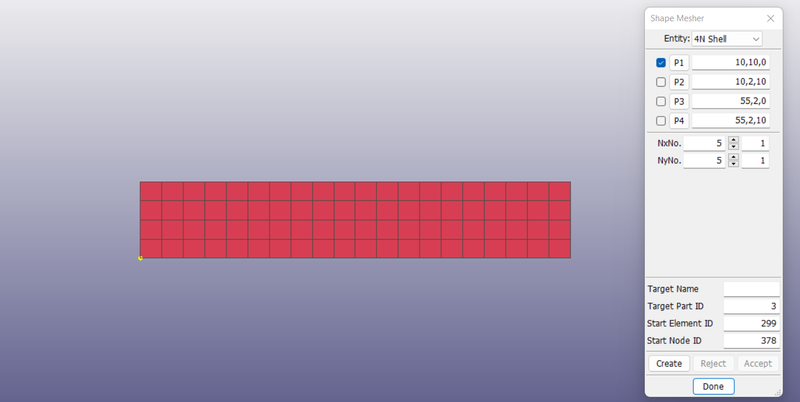
- Now we will copy and offset the given model to get the two parts.
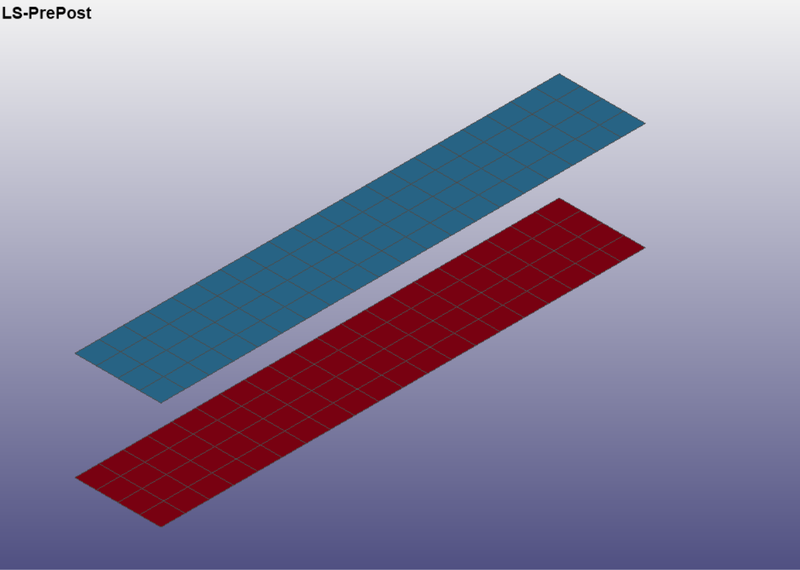
- Two pairs of nodes are created for constraining, using Node edit option under Element Tools. The nodes 501, 502 are constrained to part 1 and 503,504 to part 2 respectively, using CONSTRAINED_EXTRA_NODES card. as shown below.
- By creating CNRB joints.
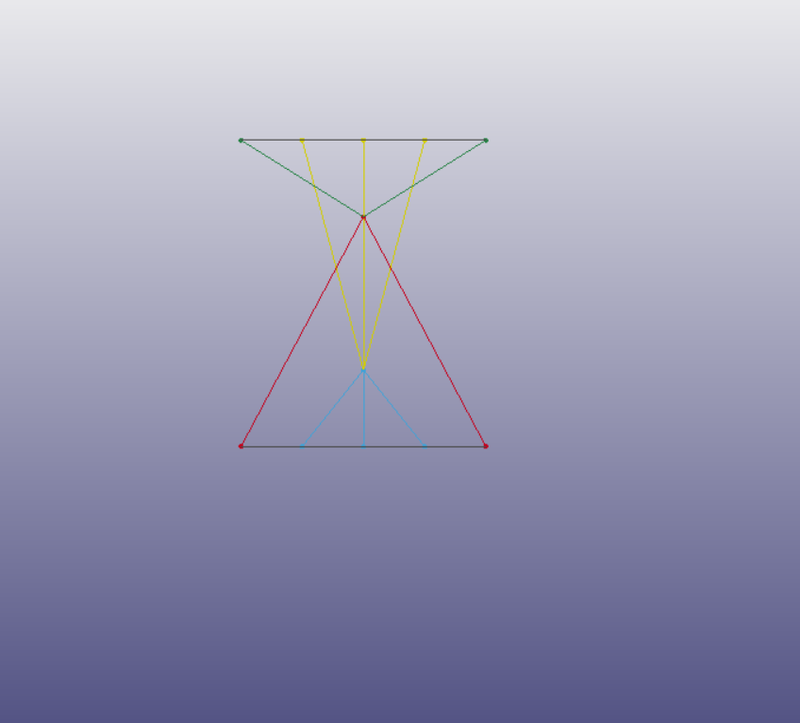
- A revolute joint is then created between them, using the CONSTRAINED_REVOLUTE_JOINT menu, using nodes 501 and 502 of part 1 and 503,504 of part 2.
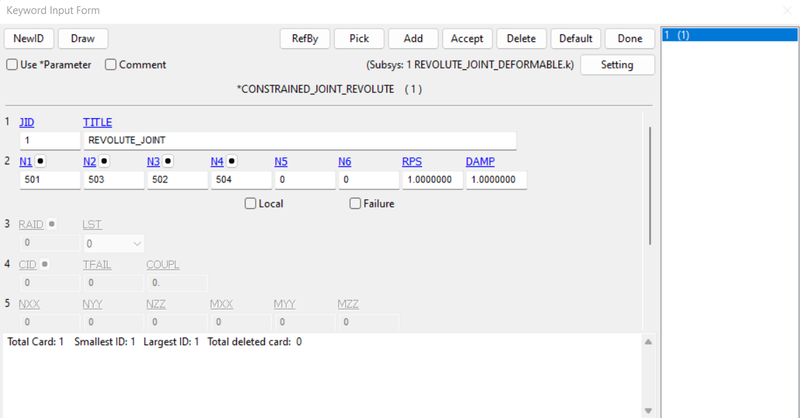
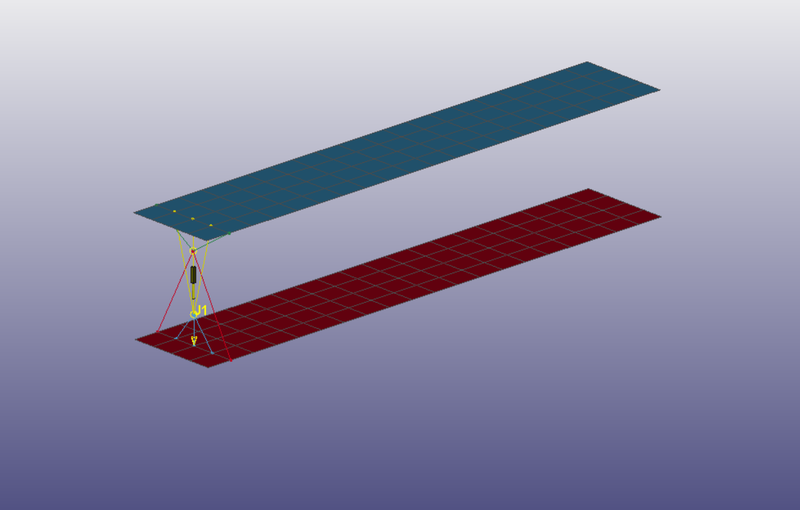
- The material and section properties are the same as that of the spherical joint.
- Now here Part 1 (red) is fixed, and part 2 (blue) is the moving part. The part 1 is fixed with SPC's at all nodes, in order to prevent motion, and a prescribed motion is given to part 2, as shown below.
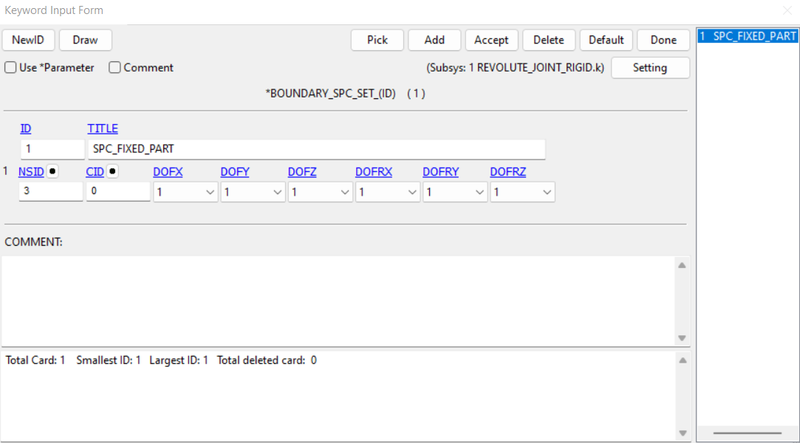
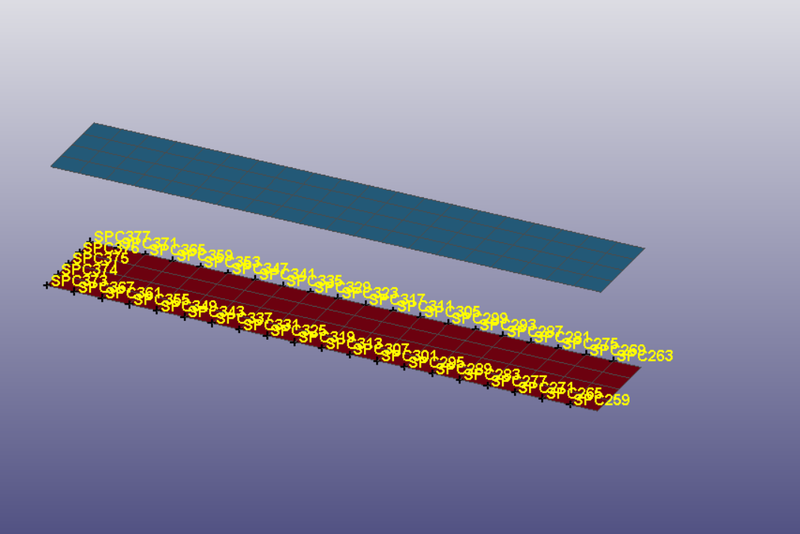
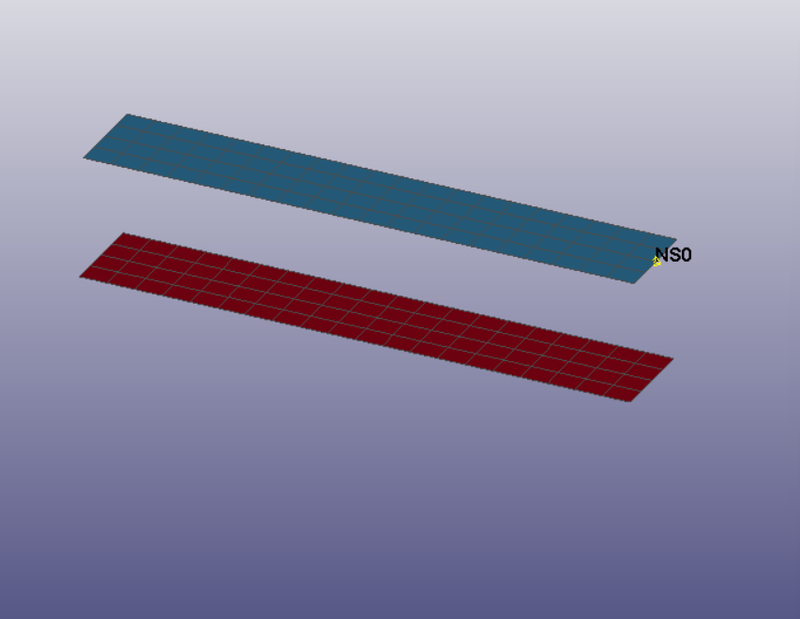
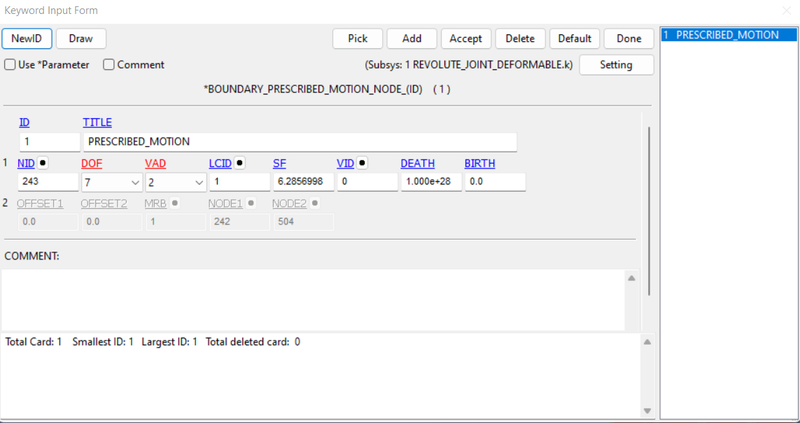
- Here we have defined the curve for motion set from define curve option.
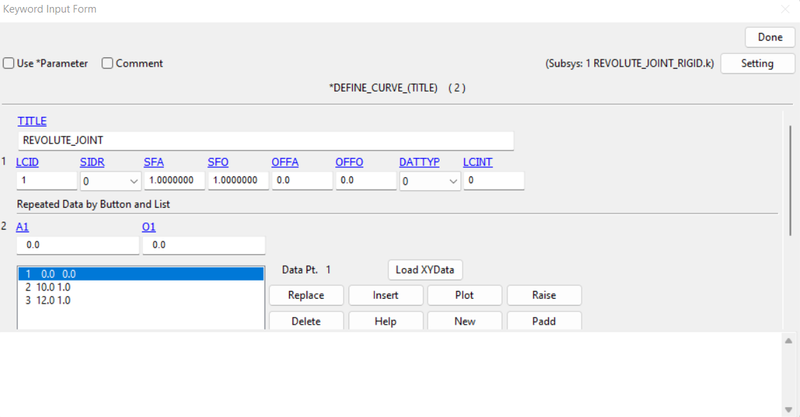

- Now we will define one more curve for timestep.
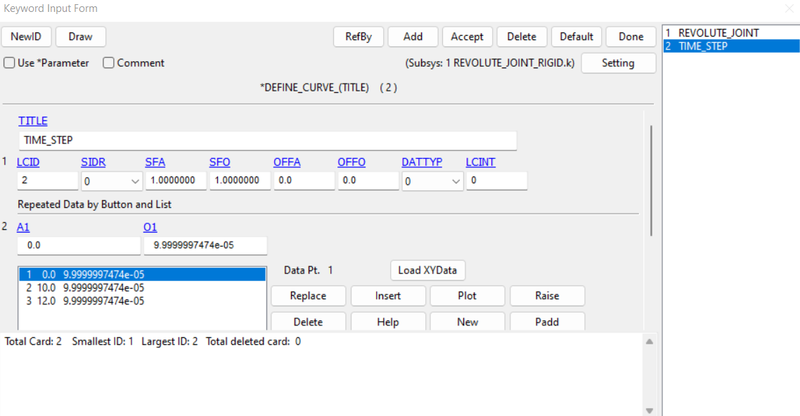
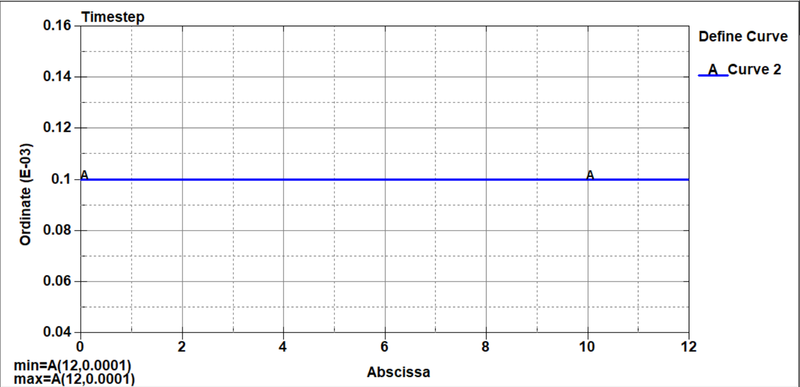
- Now again we will define the control_termination and control_timestep like spherical joint and here for time step we will provide lcid curve we defined earlier.
- Now we will check the model for errors and run the simulation.
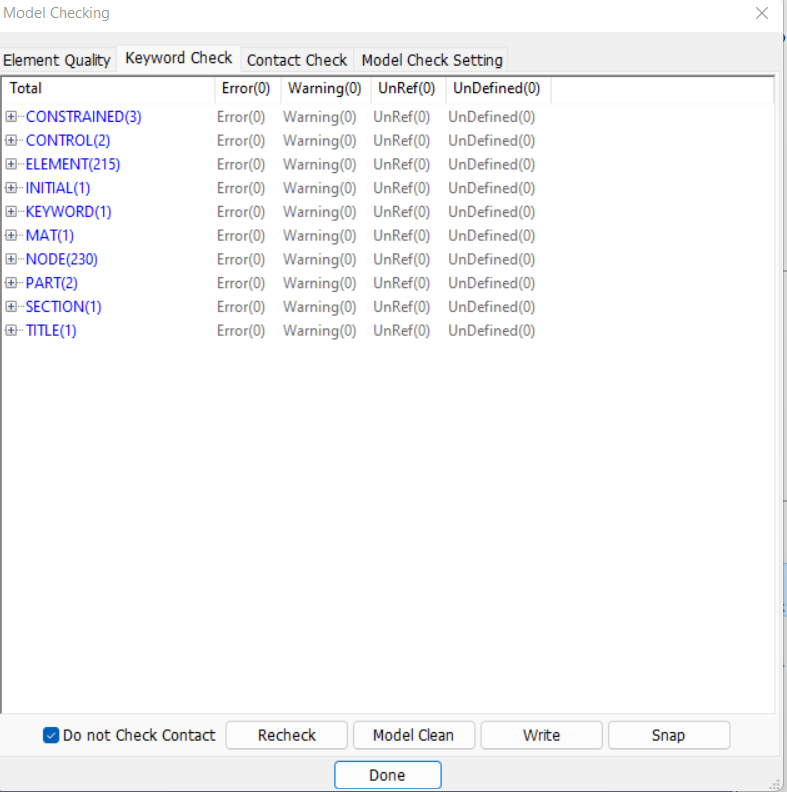
- Since there is no error in the model, so we can run the simulation.
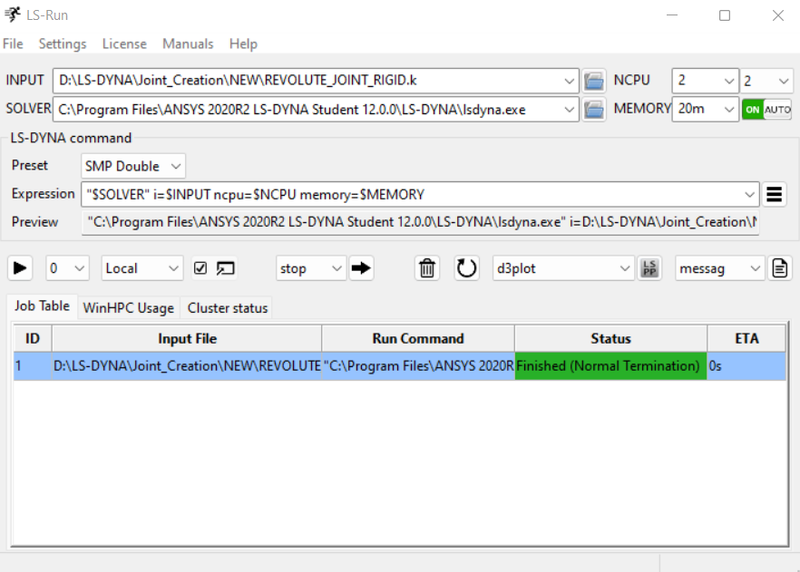
3. Cylindrical Joint
- The first step is to create two bodies in LS-Dyna using the Entity option under Shape mesher in Element and mesh, and choosing cylinder shell.
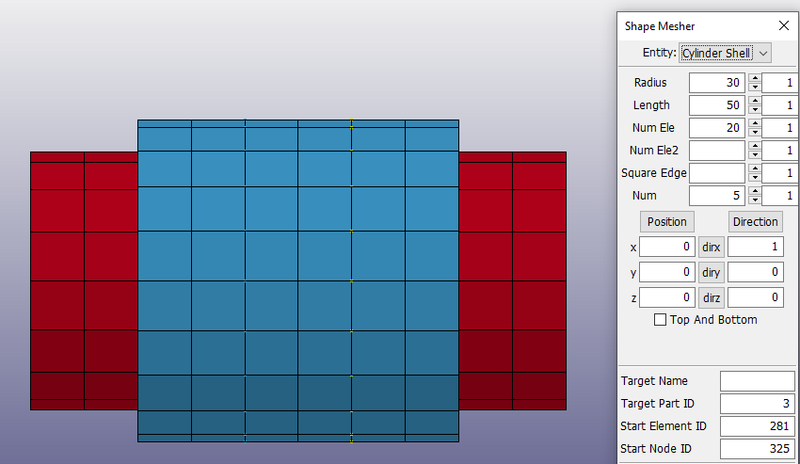
- The material and section properties are the same as that of the spherical joint.
- Two pairs of nodes are created for constraining, using Node edit option under Element Tools. The nodes 321, 323 are constrained to part 1 and 322,324 to part 2 respectively, using CONSTRAINED_NODAL_RIGID_BODY card, as shown below.
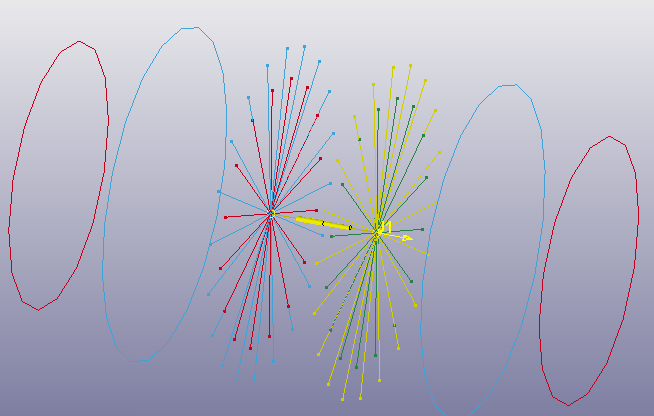
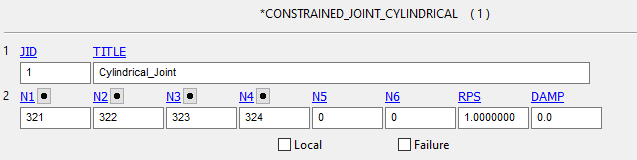
- A cylindrical joint is then created between them, using the CONSTRAINED_JOINT menu, using nodes N1 and N3 of part 1 and N2,N4 of part 2.
- Part 2 (blue) is fixed, and part 1(red) is the moving part. An initial velocity of 10 mm/ms is given to part 1 in the x(translational) direction.
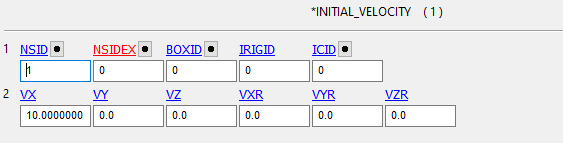
- The simulation is set to run for 10 ms, and DTINIT is given as 0.01 ms.
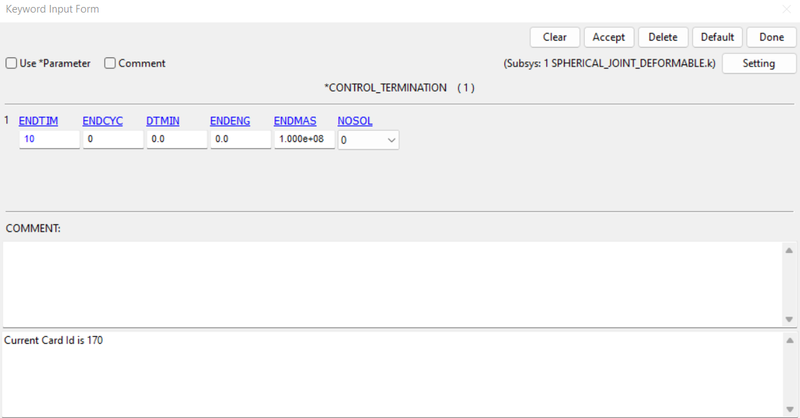
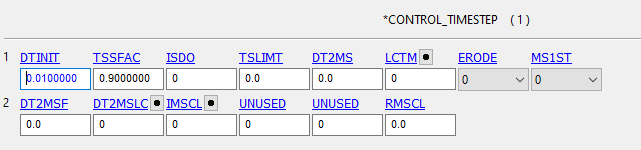
The model is ready to run, and the results of the simulation can be viewed.
- Now we will check the model for errors and run the simulation.
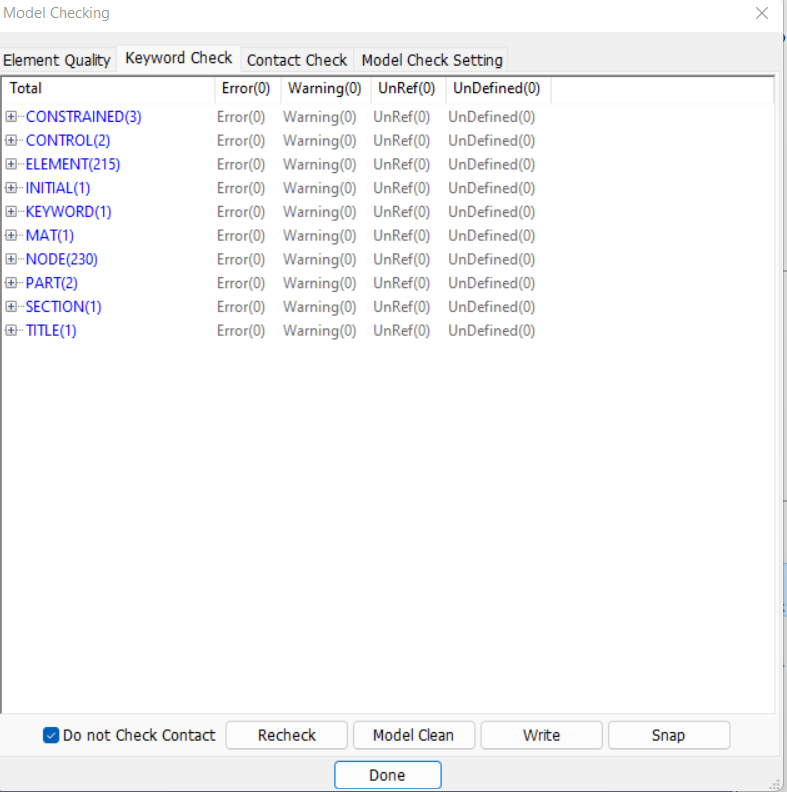
- Since there is no error in the model, so we can run the simulation.
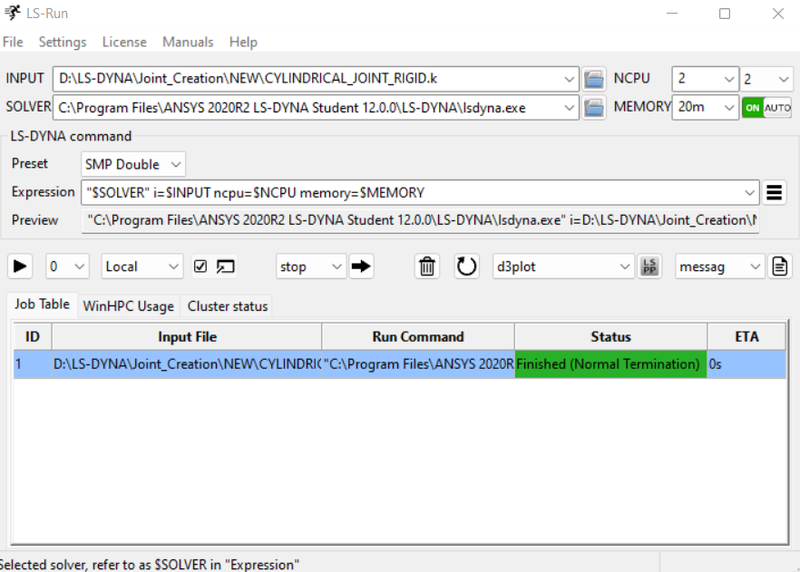
Translational Joint
The first step is to create two bodies in LS-Dyna using the Entity option under Shape mesher in Element and mesh, and choosing box shell.
- The material and section properties are the same as that of the spherical joint.
- Three pairs of nodes are created for constraining, using Node edit option under Element Tools.
- The node pairs 1001,1002 and 1003,1004 are coincident and collinear. The third pair 1005,1006 is coincident, and slightly away from the axis of the other two pairs, in between them.
- The nodes 1001,1003 and 1005 are constrained to part 1 and 1002,1004 and 1006 to part 2 respectively, using CONSTRAINED_NODAL_RIGID_BODIES card, as shown below.
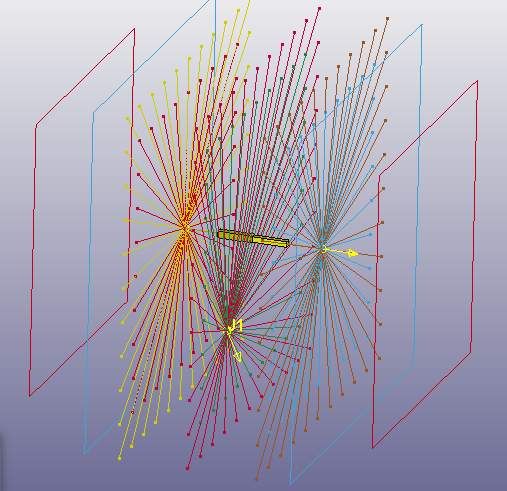
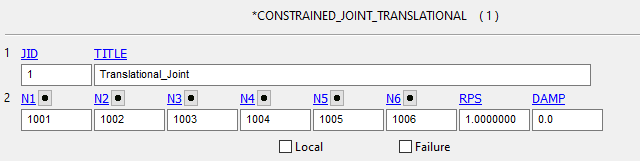
- A translational joint is then created between them, using the CONSTRAINED_JOINT menu, using nodes N1,N3 and N5 of part 1 and N2,N4 and N6 of part 2, as shown above.
- Part 2 (blue) is fixed, and part 1(red) is the moving part. An initial velocity of 10 mm/ms is given to part 1 in the x(translational) direction.
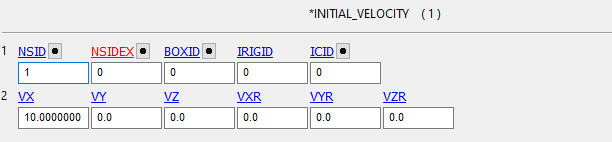
- The simulation is set to run for 10 ms, and DTINIT is given as 0.01 ms.
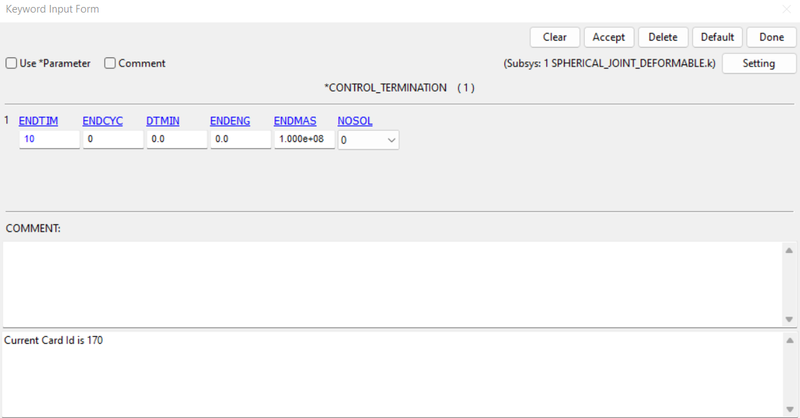
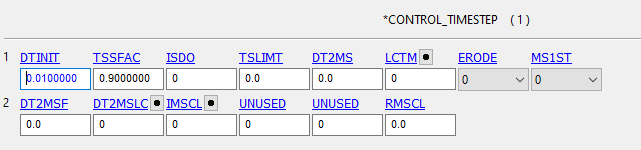
- Now we will check the model for errors and run the simulation.
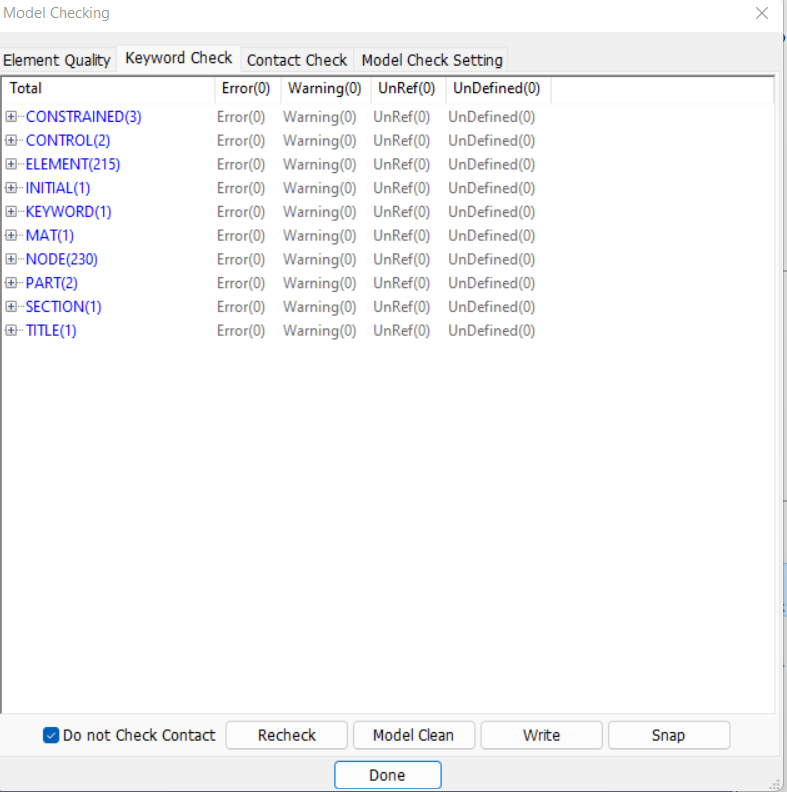
- Since there is no error in the model, so we can run the simulation.
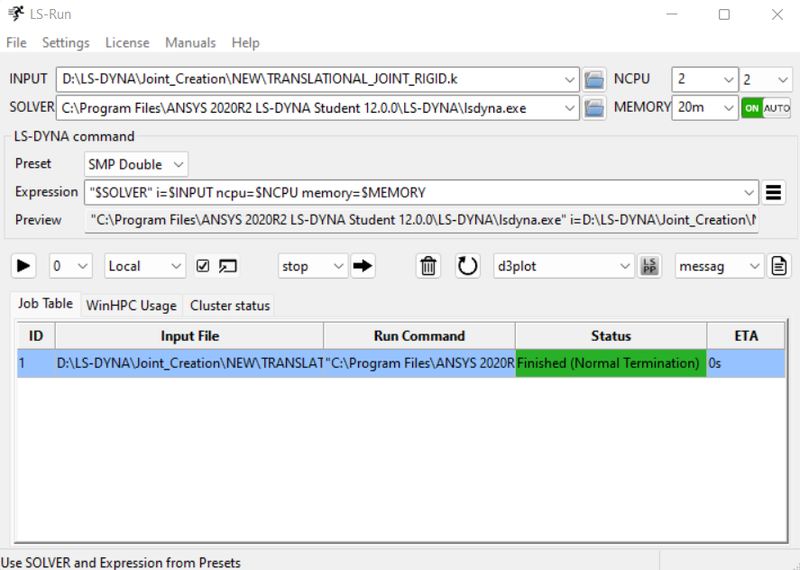
Conclusion-
- The keyword files necessary to demonstrate spherical, revolute, cylindrical, and translational joints between two rigid
bodies and two deformable bodies are created and simulated.
- Learnt to create different types of joints using *CONSTRAINED_EXTRA_NODES and *CONSTRAINED_NODAL_RIGID_BODY between rigid and deformable bodies respectively.
Animations-
Rigid Body Motion-
1. Spherical Joint
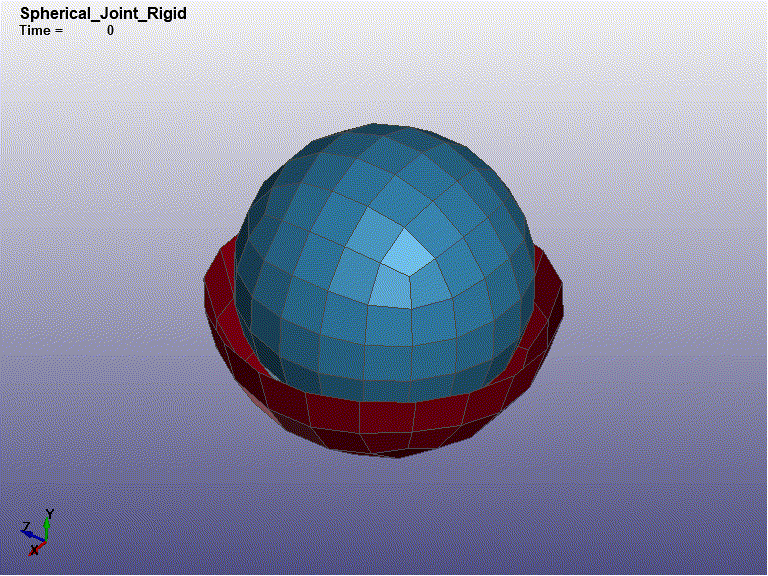
2. Revolute Joint
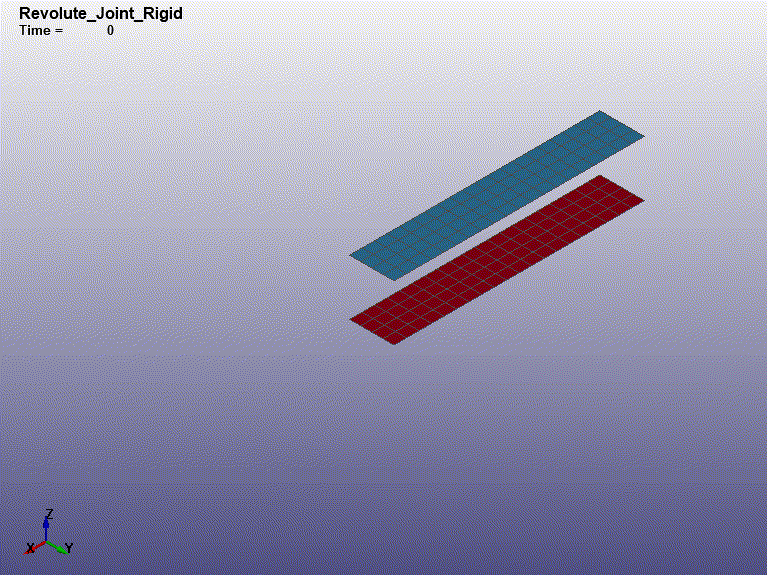
3. Cylindrical Joint
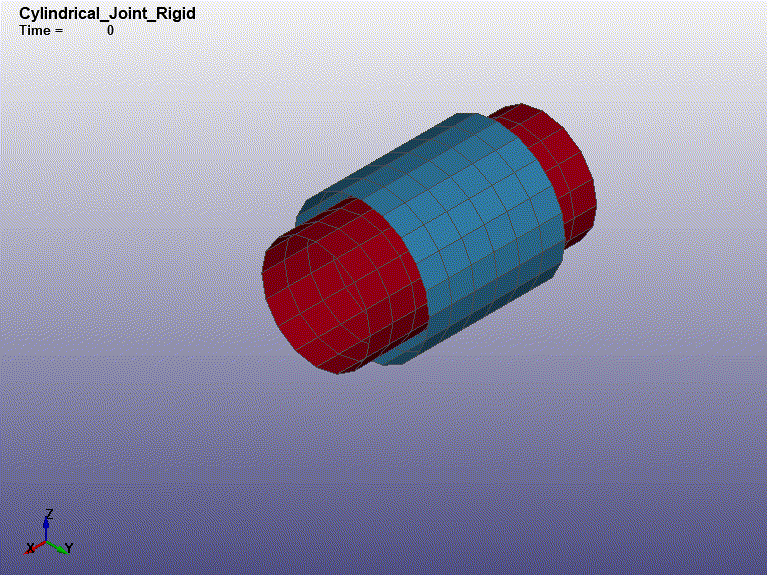
4. Translational Joint
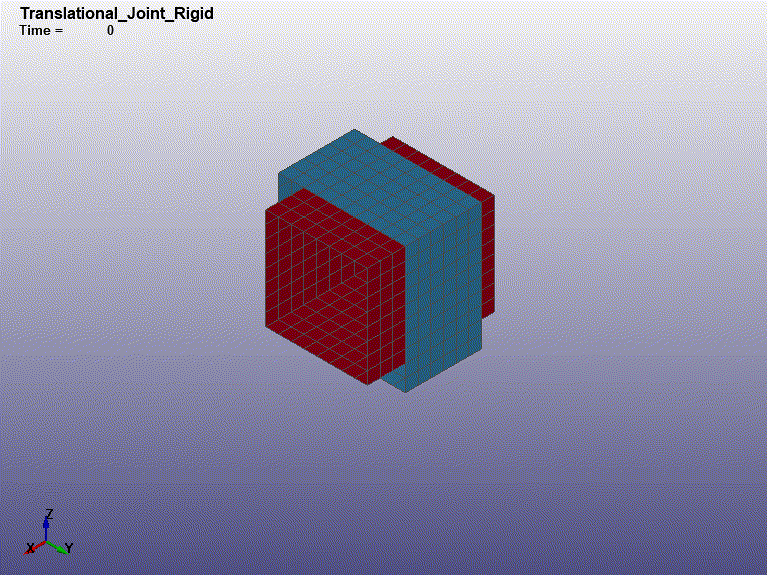
Deformable Body Motion-
1. Spherical Joint

2. Revolute Joint
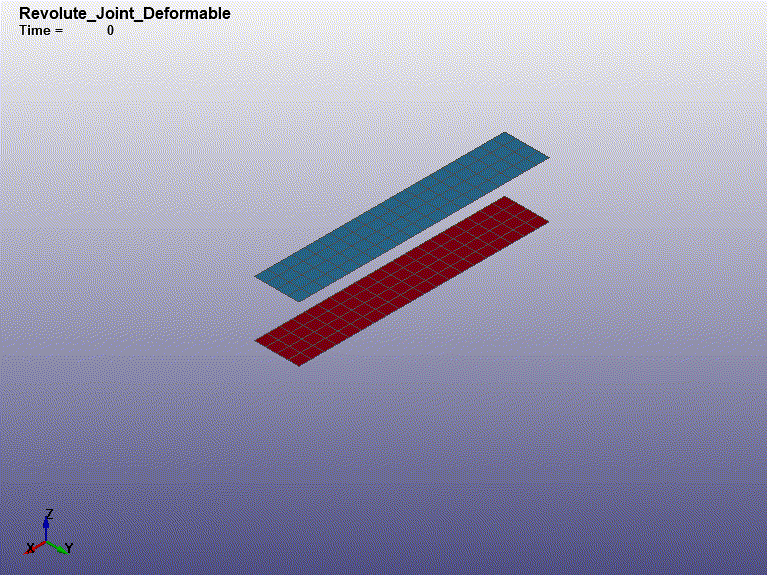
3. Cylindrical Joint
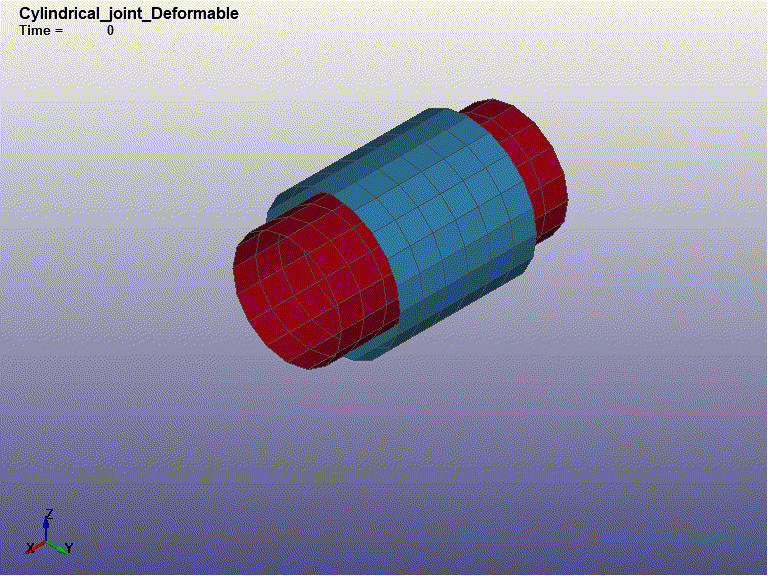
4. Translational Joint
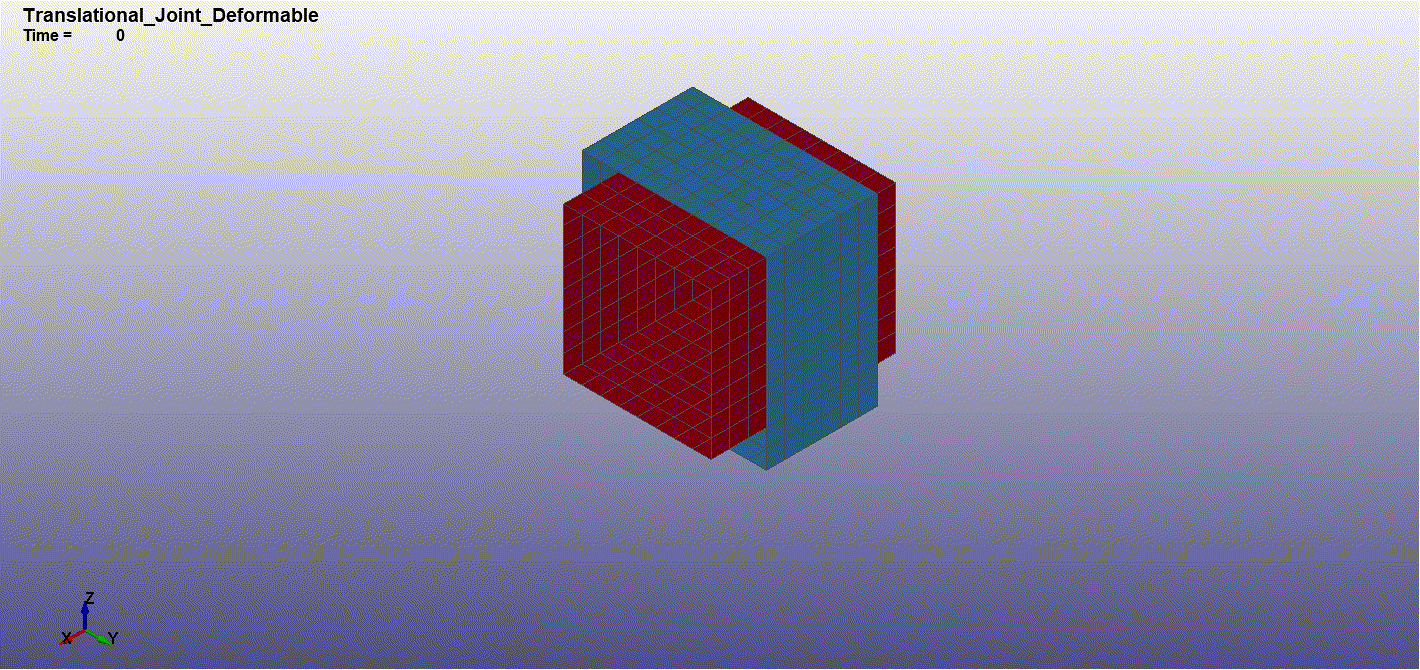