Challenge 1 – Mixing Tee
Aim – To observe the mixing efficiency in a mixing tee by analysing 2 cases with different lengths (short & long).
Theory & Practical Applications –
- The mixing tee joint is called so since it is responsible for mixing 2 fluids of different temperature using 2 entrances that have an angle of 90° between them
- One of the most common applications of a mixing tee is in household air conditioning systems.
- In a home AC, the refrigeration system can supply air with a very low temperature; probably around 10-15°C.
- Since this temperature is quite less for comfortable living standards, a mixing tee is used to mix ambient air from outside with the air coming from the refrigeration unit.
Solving and Modelling Approach –
- After importing the solid model into Ansys Spaceclaim, the fluid flow domain is selected using an edge select option in SpaceClaim
- The remaining solid is suppressed for physics since it does not contribute to the fluid domain
- After this, the entire fluid domain is meshed. A fine mesh is preferred for accurate results. In this particular case, we will not use inflation layers since we are concerned only about the average outlet temperature and the standard deviation and not about details near the walls
- After meshing the model, it is brought into Ansys setup.
- In the general tab, we will select a pressure-based and steady-state case with no gravity
- The energy equation should also be turned on since we are analysing temperature.
- Furthermore, the boundary conditions are applied as shown below.
- For the cell zone conditions, the entire volume is selected and the air is chosen as the fluid medium.
- Since we want to analyse the standard deviation and area-weighted average of temperature, we can create a separate monitor in report definitions for observing each and every iteration while solving the simulation.
- Finally, hybrid initialisation is carried out on all cases and the problem is solved for 500 iterations.
Case 1 (a) – Short Mixing Tee with momentum ratio = 2
- Length = 192.37783083mm
- temp(hot) = 36 C
- temp(cold) = 19C
- momentum ratio = vel(cold)/vel(hot) = 6/3 = 2
- K-epsilon, Realizable, Standard wall functions turbulence model was used.
Case 1 (b) – Short Mixing Tee with momentum ratio = 4
- Length = 192.37783083mm
- temp(hot) = 36 C
- temp(cold) = 19C
- momentum ratio = vel(cold)/vel(hot) = 12/3 = 4
- K-omega SST turbulence model was used.
Case 2 (a) – Long Mixing Tee with momentum ratio = 2
- Length = 268.32800591mm
- temp(hot) = 36 C
- temp(cold) = 19C
- momentum ratio = vel(cold)/vel(hot) = 6/3 = 2
- K-omega SST turbulence model was used.
Case 2 (b) – Long Mixing Tee with momentum ratio = 4
- Length = 268.32800591mm
- temp(hot) = 36 C
- temp(cold) = 19C
- momentum ratio = vel(cold)/vel(hot) = 12/3 = 4
- K-omega SST turbulence model was used.
Mesh, Geometry, and Fluent Setup –
- Both case1(short tee) and case2(long tee) geometries were meshed with the sizing of 0.025m and 0.02m respectively.
- A finer mesh was applied to the 2nd case to capture finer details of the temperature and velocity in the elements.
- Case 1a was solved using the K-epsilon, Realizable, Standard Wall Functions turbulence model whereas Case 1b was solved using the K-Omega SST model.
- After comparing the results of the 2 models, it was evident that K-Omega SST solution converged earlier and showed more accurate results.
- Hence the K-Omega SST model was used for further Case 2 simulations
- The K-epsilon model is accurate only for completely turbulent flows and flows which are non-separated
- It may also cause stability issues because of stiffness
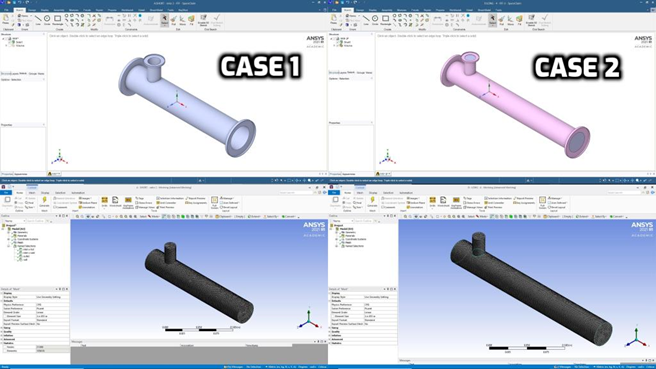
Mesh Metric – Element Quality Analysis
- A mesh metric analysis was conducted on all the 4 cases
- It can be inferred that the minimum quality among all the cases was found to be 25% in Case 2a whereas the maximum quality was 100% in all 4 cases
- Since the minimum quality is not less than 5%, the following mesh can be used for further simulations
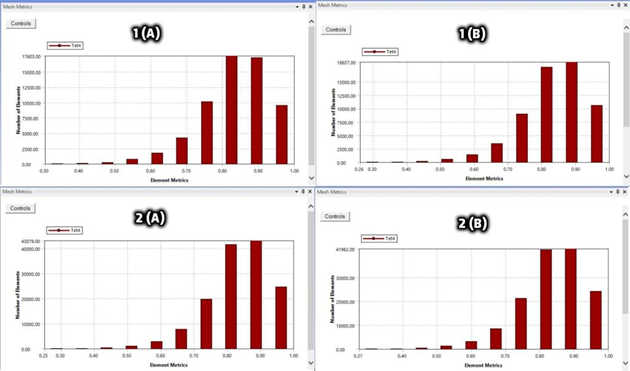
Convergence Plots –
- It can be observed from the diagram below that Case 1a involved a repeating pattern of convergence values.
- This initiated at around 200 iterations and went on up to 500 iterations
- On the other hand, all other cases converged without a repeating pattern
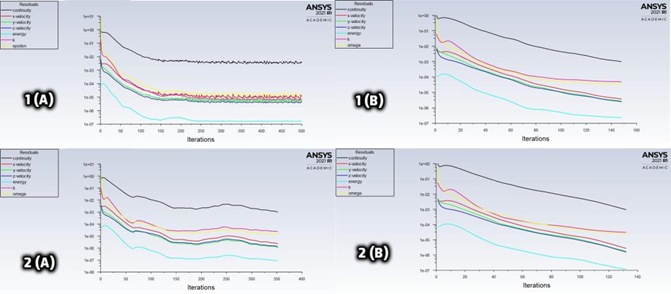
Tabulation –
- Numerous conclusions can be made from the following table regarding the temperature and velocity at the outlet
- It can be observed that Case 2b showed a minimum standard deviation of temperature thus proving efficient mixing at the outlet
- This conclusion also shows that the tee with greater length allowed efficient mixing of fluid thus resulting in a comparatively uniform temperature contour on the outlet plane.
- It can also be observed that cases with a momentum ratio of 4 depicted better mixing as compared to cases with a momentum ratio of 2.
- This is mainly because the cold fluid air flows at a greater velocity from the top in case of a higher momentum ratio.
CASE
|
MESH SIZE(m)
|
NODES
|
ELEMENTS
|
ITERATIONS FOR CONVERGENCE
|
TEMPERATURE STANDARD DEVIATION (C)
|
AVERAGE TEMP (C)
|
AVERAGE VELOCITY(m/s^2)
|
CASE 1 a
|
0.0025m
|
12620
|
61426
|
500
|
1.7873896
|
30.289041
|
4.4938313
|
CASE 1 b
|
0.0025m
|
12590
|
61276
|
148
|
1.2287759
|
27.605166
|
6.0330137
|
CASE 2 a
|
0.002m
|
28372
|
140525
|
352
|
1.0344464
|
30.428691
|
4.4986507
|
CASE 2 b
|
0.002m
|
28551
|
141599
|
132
|
0.50640842
|
27.499947
|
6.0199602
|


_1613479405.png)
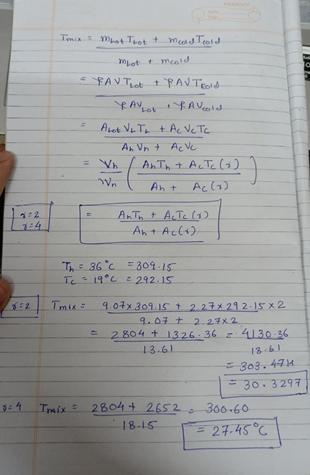
Results and Discussions –
- Temperature contour plane – side view
- The following image gives a clear view of the temperature distribution across the horizontal symmetry plane
- It can be observed that the temperature in cases 1b and 2b reduces from the red region almost half way to the outlet exit
- On the other hand, in cases 1a and 2a, the temperature is in a high zone up till the outlet region
- Thus, it can be inferred that cases 1b and 2b support efficient mixing as compared to the other 2 cases
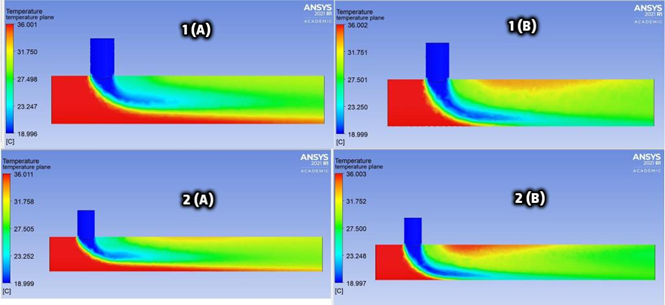
Velocity contour plane – side view
- It can be observed that the colour distribution near the outlet region is quite uniform in cases 1b and 2b, thus proving that a higher momentum ratio supports a comparatively uniform velocity of fluid flow
- On the other hand, the colour distribution in case 1a and 2a is not uniform thus depicting that the velocity distribution is non-uniform.

- Temperature contour line and Velocity contour Line – side view
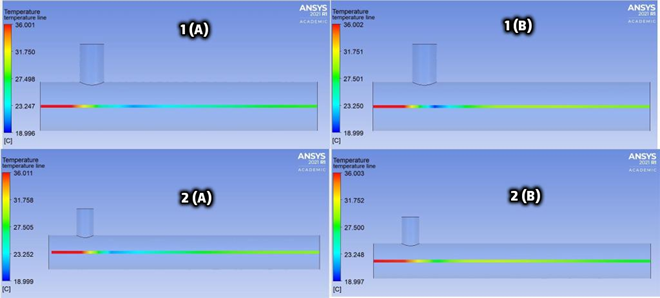
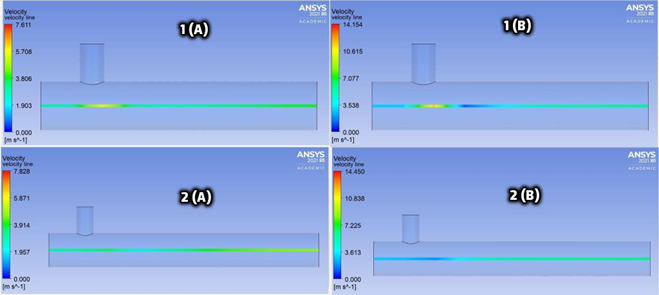
- Temperature outlet contour and Velocity outlet contour – front view
- The temperature distribution on the outlet of the long and short mixing tee can be seen in the figure below.
- It can be observed that simulations involving a momentum ratio of 4 have an average temperature of around 27C
- Whereas, simulations with a momentum ratio of 2 show an average outlet temperature of approximately 30C
- It can also be observed that case 2b shows the most uniform temperature as compared to all other cases.
- This can be verified with the calculations that case 2b has the minimum standard deviation of the temperature of around 0.5 which can be evident from the table shown earlier.
- Case 1b does show signs of efficient mixing, however, case 2b consists purely of green and light blue regions.
- Case 1b shows contours of green, light blue and yellow regions.
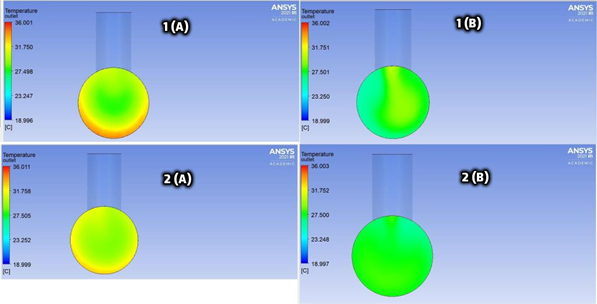
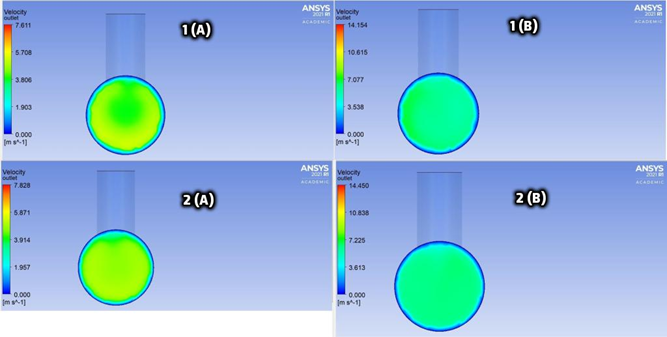
Inferences and Conclusions –
- Higher momentum ratio results in efficient mixing of hot and cold air as compared to a lower momentum ratio
- The length of the mixing tee slightly affects the mixing efficiency of the hot and cold air. Simulations involving a greater length of the mixing tee have shown more efficient mixing since it allows more time for heat exchange and heat transfer
- Using a K-Omega SST model is more apt for mixing tee simulations as it gives accurate results with lesser iterations required for convergence.
- Case 2b – Long mixing tee with momentum ratio = 4 proves to be the best model for industrial purposes.
- Refining the mesh/element size results in a more accurate simulation thus giving accurate results.
References –
- Research Paper - https://www.sciencedirect.com/science/article/pii/S0029549309005676