Aim: Route the Wiring Harness on given Car body and prepare flatten view drawing in Catia V5
Objective: The objective of this project is to route the wiring harness and prepare flatten view drawing for the tailgate of the car. All types of packaging rules have to be considered while routing the harness and industry based practices shall be demonstrated in harness design. All necessary details like clearance, clipping/clamping selection, harness fixing requirements, harness continuity should be provided in order to design the wiring harness.
Assumptions:
- Wiring harness should be routed in such way that it is easy to assemble and access.
- Easy manufacturing, installation, removal and maintenance have to be considered while designing the wire harness.
- Wiring Harness should be kept away from sharp environment like edges, corners etc.
- Avoid harness routing and clipping in the blind zones or hard to reach areas during harness assembly or service.
- Provide additional slack if needed according to the surrounding and harness bending requirement. If harness is passing through the closures/doors or tail gates then envelope dimensions during opening and closing of doors shall be considered to provide the slack. Check the harness slack requirements with open and close conditions to avoid excess slack.
- Routing through small structural holes and openings shall be avoided. To minimize chaffing and handling of the wiring harness during installation.
- It should be make sure that there is no case of fouling while designing the wiring harness in the CAD environment. Additional mounting equipments like clips/clamps may be used to avoid fouling.
- Use of rubber grommet is recommanded if harness is passing through sheet metal panels. Example- firewall, passing to door, tail gate etc.
- The branch length should be greater than 50mm.
- The minimum distance between the clip and branch point should be at least 25mm.
- The minimum distance between the two branch points should be at least 50mm.
- Clips/clamps used for the wiring harness should be easily available in the market to avoid extra cost for custom mounting solutions.
- Now, we have to route wiring harness for two tail lights and two number plate lights, and connect them to main electrical system of car.
- For two tail lights and two number plate lights, we are using 8-pole connector and 2-pole connector respectively.
- A car body also have an interconnection connector which will connect the wiring harness of tail gate of the car body to the main harness of the vehicle.
- We will use 12-pole electrical connector with a mounting clip as an interconnection connector.
- The bend ratio for all the bundle segment is considered to be 1.4
Step 1: Creating Context Assembly
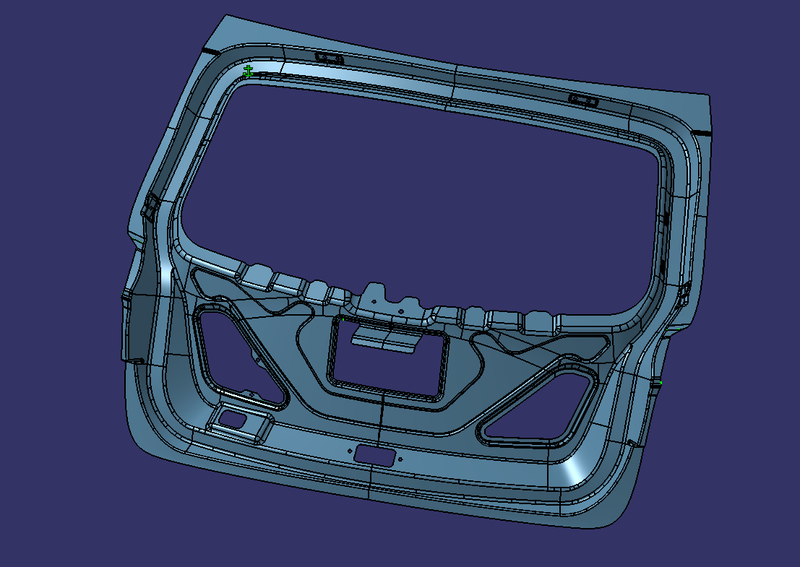
- We have created context assembly for the tail gate of the car as main assembly as shown in above figure.
- This context assembly contains the 3D cad data for the tail gate of the car and car tail gate harness geometrical bundle.
Step 2: Difining 2-pole and 12-pole connectors electrically
- Here, we will use 2-Pole and 8-Pole connectors for this assembly and for that we have downloaded these connectors from TE.Com
- We should have to define it electrically that is to define geometrical parameters, bundle connection point and connector connection point.
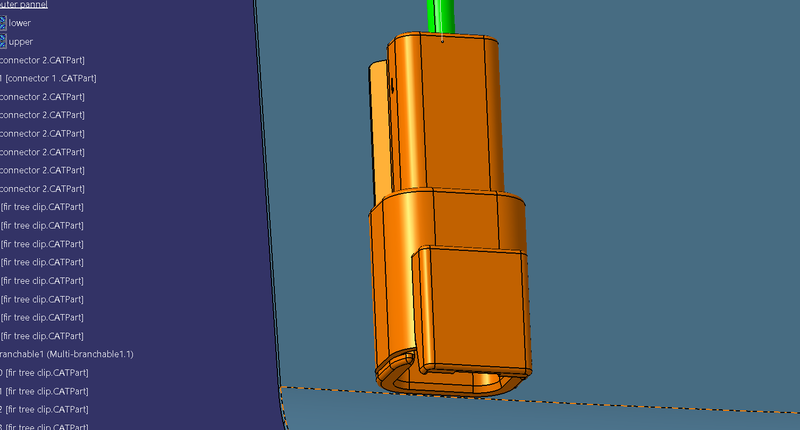
- Here, we have defined 2-Pole connector electrically for two number plate lights of the car as shown in above figure.
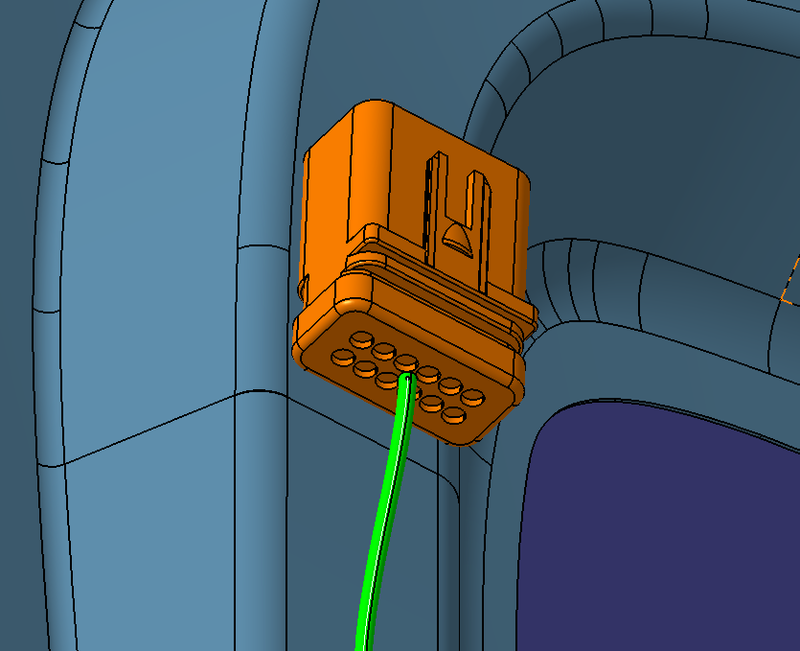
- In above figure, we have defined 8-Pole connector electrically for two tail lights of the car.
Step 3: Adding connectors to the 2 tail lights and 2 number plate lights
- We have added both 2-pole connectors and 8-pole connectors inside the tail gate harness geometrical bundle assembly.
- We have used commands like manipulation, compass, snap and smart move to place all the 4 connectors to their desired location.
- We have placed all the connectors at their desired position as shown in below figures.
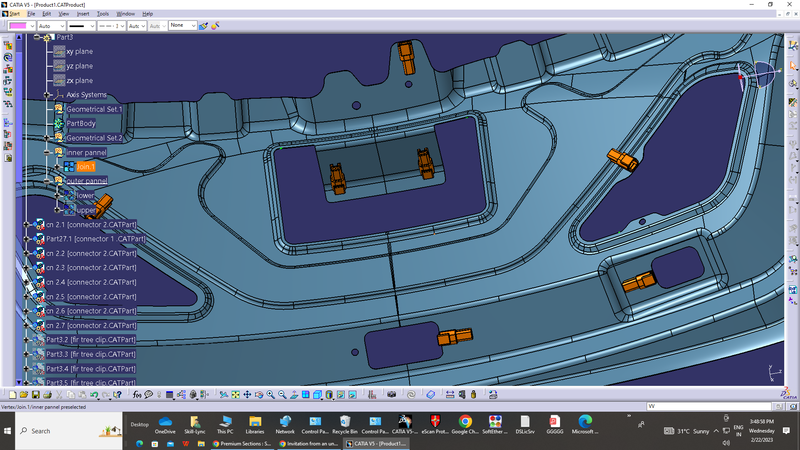
Step 4: Defining and locating FIR TREE CLIP
- IT is used as an interconnection connector and "C-1924487-2" as mounting cavity.
- The 3D CAD data files for interconnection connector and cavity are downloaded from TE.com
- We have defined interconnection connector and mounting cavity electrically in Electrical Part Design workbench as shown in above figure.
- As shown in above figure, we have electrically connected both an interconnection connector and mounting cavity in Electrical Assembly Design workbench.
- After defining an interconnection connector electrically, we have mounted it near top slot on the tail gate of the car as shown in above figure.
Step 6: Mounting Clips at desired location
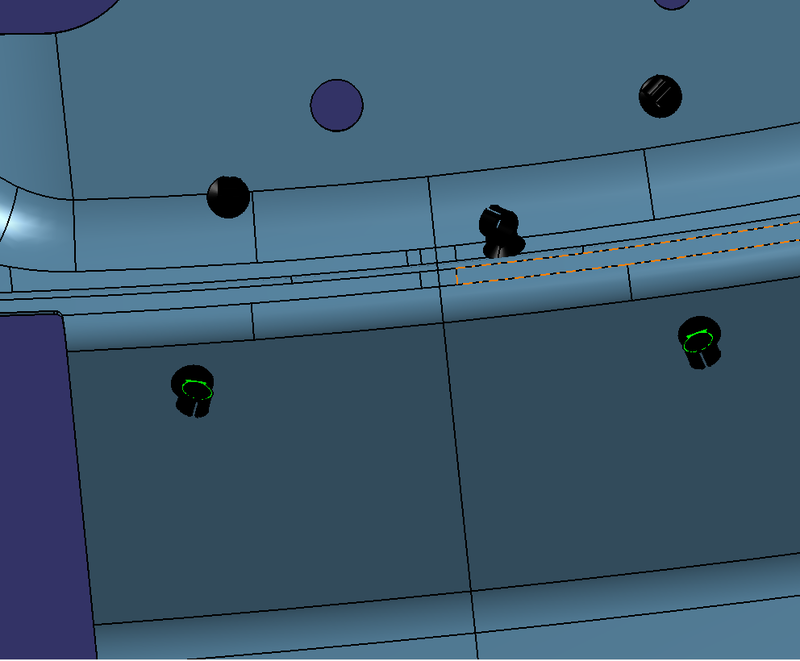
Step 7: Bundle routing
Before, bundle routing we have to make a curve by creating points in hollow part of the given tailgate. So we have made a curve through 11 points from the interconnection connector as shown in below image.
- Now, the car tail gate assembly is ready for the bundle routing as shown in below image.
- Also, we have activated harness assembly as geometrical bundle.
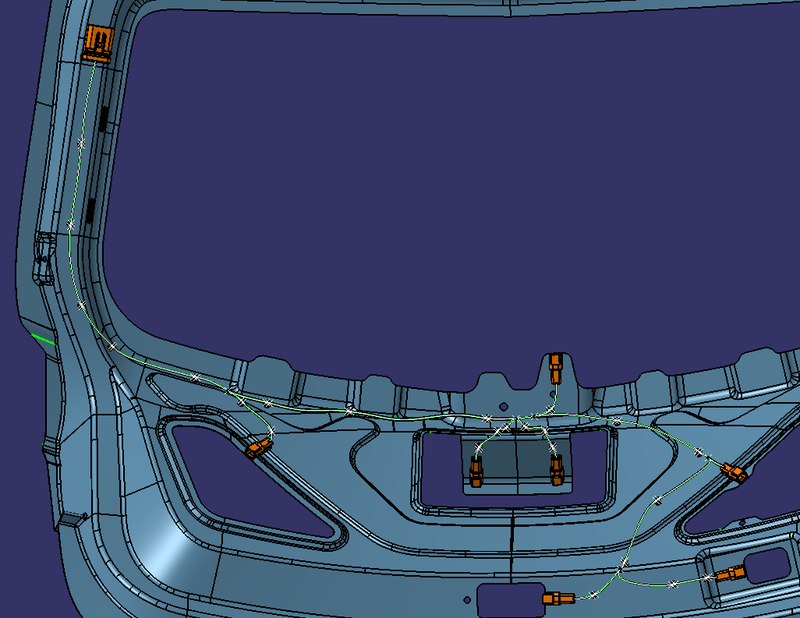
- Let, we have started bundle routing from interconnection connector and assumed diameter of main trunk is 12mm.
- The diameter of bundle leading to 2 tail lights and 2 number plate lights is 8mm and 5mm respectively.
- The bend ratio is assumed to be 1.4 and appropriate slack between 1-10% is given wherever needed.
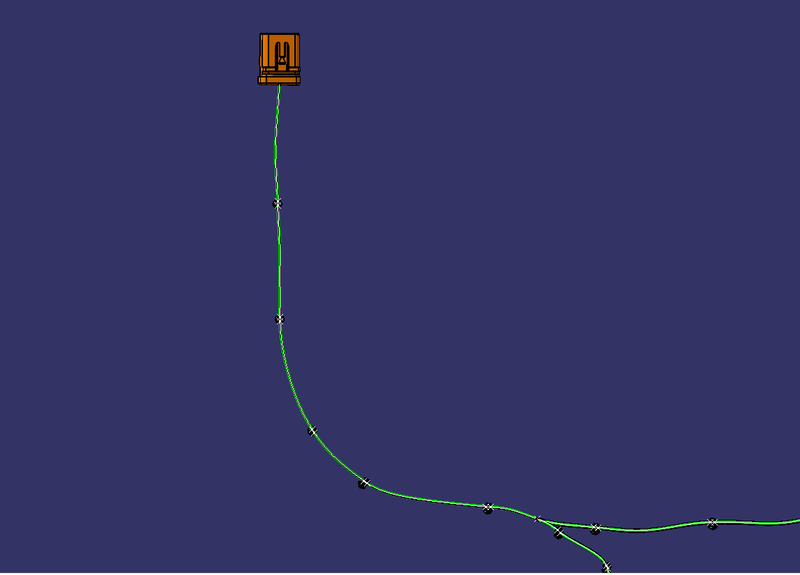
- We have created 3 branch points, from main branch to both tail lights and from tail lights to number plate lights as shown in below images.
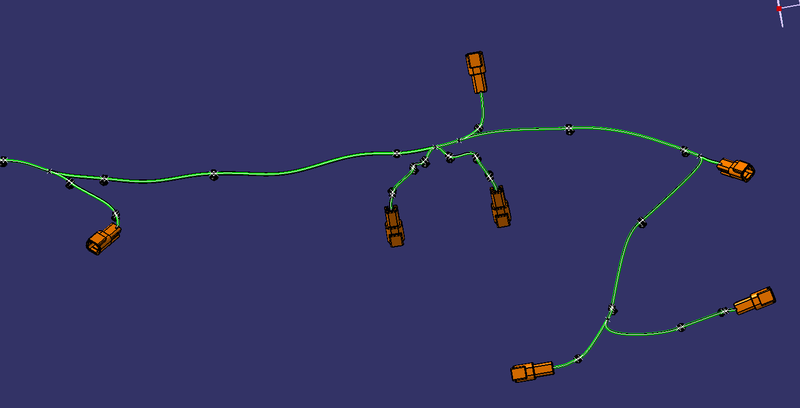
Step 8: Adding protective covering to the harness bundle
- After bundle routing, we have to add protective covering to the harness bundle so that it will get protected from the damage.
- Here, we have used PVC tape for the current harness assembly.
- We have given start and end extremity wherever needed for the PVC tape as shown in below image.
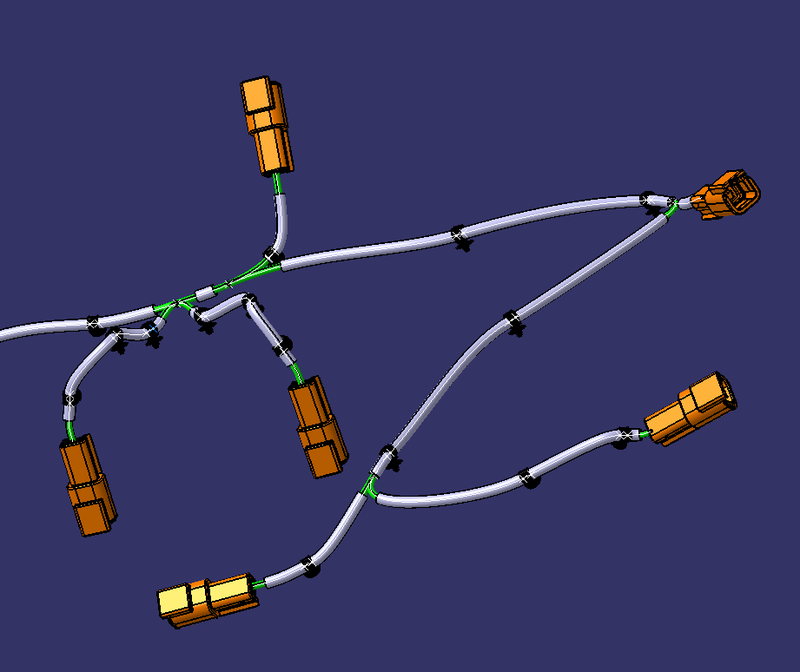
Step 9: Checking bundle continuity
- First, we have to select multi-branchable and go through the sequence as Edit>Search>Advanced>Workbench-Electrical>Type-Bundle Segment>Attribute-Fully Connected.
- After selecting 'True' condition will show all the connected bundle segments while selecting 'False' condition will show all the non-connected bundle segments.
- Here, we have selected 'True' condition and search for the results. All the bundle segments are highlighted and showing that all the bundle segments are connected electrically as shown in below image.
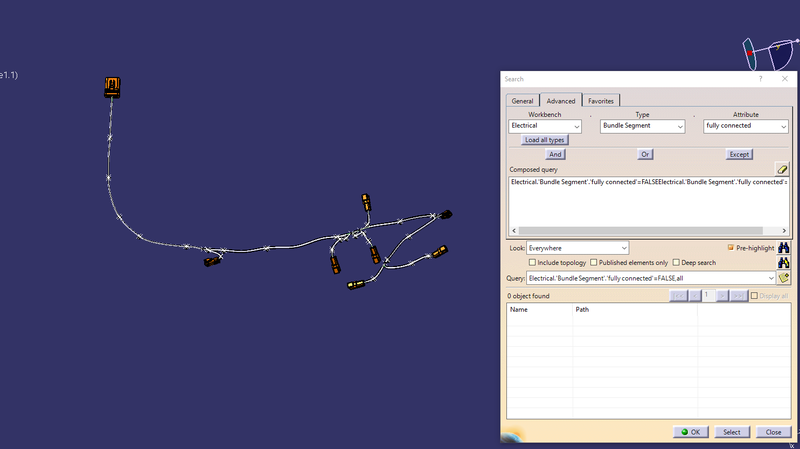
Step 10: Create flatten view of the wiring harness bundle
- To create a flatten view of the harness assembly, we have to work in Electrical Harness Flattening workbench in Catia V5.
- Also, we have to make sure that the flattening file is saved into the same folder where we have all the parts of the harness assembly.
- As shown in below image, while defining the wiring harness flattening parameters make sure to select Single line for bundle segment and Double line for protective covering.
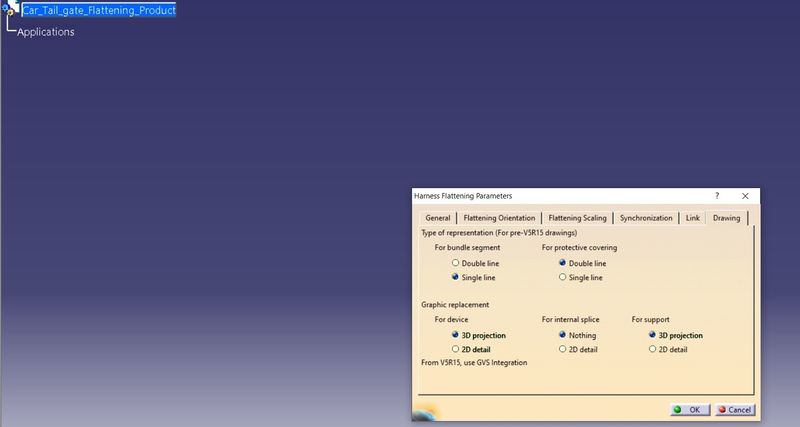
- After that, we have to extract and bring the bundle assembly into the car tail gate flattening product file.
- To flatten the harness assembly, we have selected Face as an active plane and selected all the branches as shown in below image.
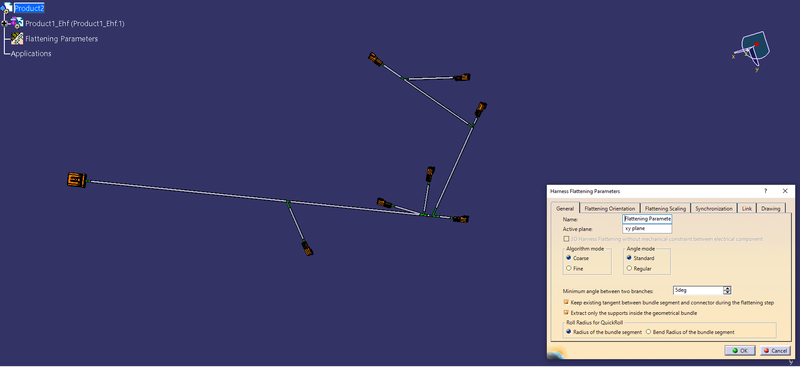
- Now, we have a flatten view of the wiring harness geometrical bundle assembly as shown in below image.
- After creating flatten view, we have to rotate the connectors and clips in right direction along the selected plane using manipulation as shown in below image.
- We have designed the fatten view by using feature like roll for better representation of the harness as shown in below image.
Step 11: Creating a flatten view drawing for the wiring harness assembly
- Now, we have to make new drawing file and define all the necessary drawing parameters as shown in below image.
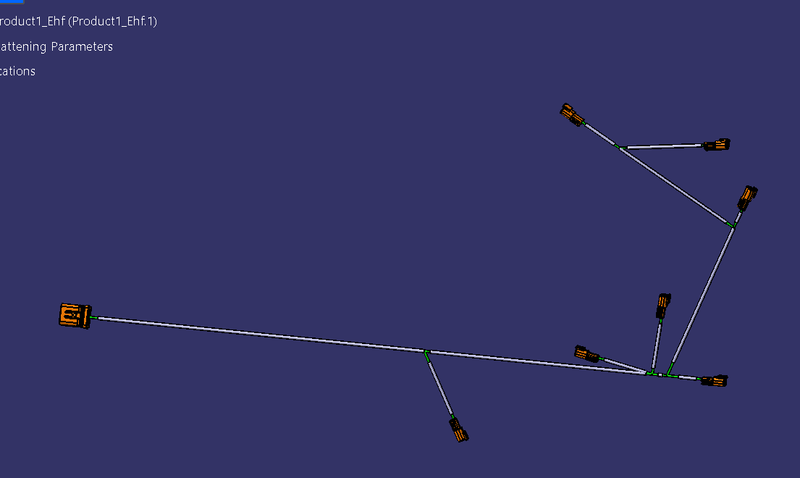
- As shown in below image, we have to insert front view of the harness assembly into drawing file and define drawing properties.
- It should be noted that for the Dress-up feature 3D wireframe is always ON. If this setting is not selected then the bundle segments will not be visible on the drawing view.
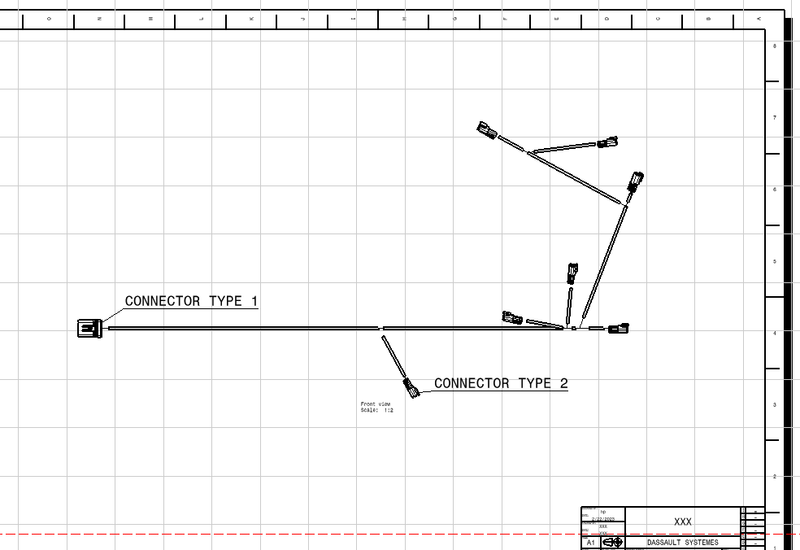
Conclusion:
Routing of the wiring harness for the car tail gate assembly has done and prepared flatten-view drawing in Catia V5. Applied all the packaging rules while routing the wiring harness, implemented industry best practices in the harness design. Also, provided details like clearance, clipping selection, harness fixing requirements, harness continuity in order to design the harness.