Aim:
To design a Mechanical Design of Battery Pack using the cell- ANR26650M1-B
Objective:
- To create a battery pack drawing of 18KWh using Series and parallel connections of battery modules made up of individual Li-ion cells.
- Li-ion cell used here is ANR26650M1-B
To discuss about the enclosure used for battery pack.
Introduction:
Details of Battery:
Nanophosphate Technology 26650 Lithium Ion Power Cell
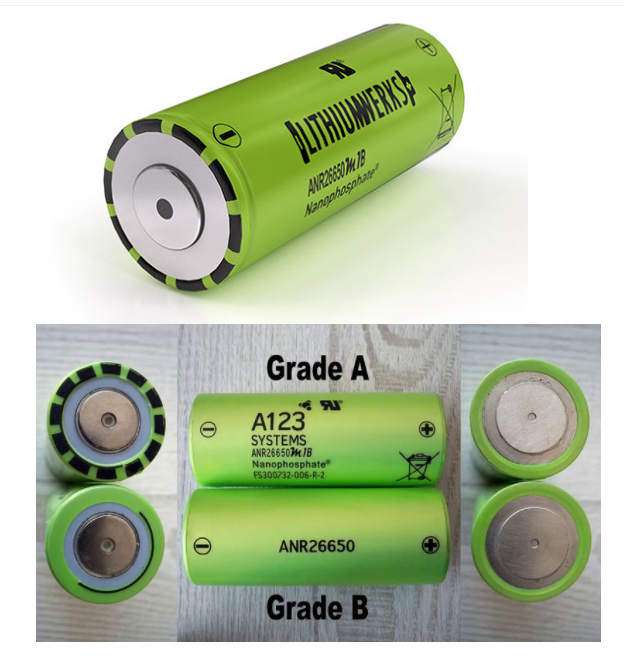
Lithium Ion 26650 cells are capable of delivering very high power due to its use of patented Nanophosphate battery technology Based on Lithium iron phosphate
26650 Lithium Ion Battery Definition:
26650 is a cylindrical lithium battery specification. 26650 battery is applicable to special equipment, medical equipment, instruments, power tools, logistics, security monitoring, exploration and mapping, etc.
26650 lithium battery dimension: The diameter is 26mm, and length is 65mm.
26650 Lithium Ion Battery Advantages:
26650 lithium battery has high energy density, low self-discharge rate, stable charging and discharging performance, no memory effect, no decomposition in heat, high safety performance, long life cycle and high voltage. You can connect 26650 lithium battery in series or in parallel. It is environmental friendly and has no pollution.
- High energy density: theoretical specific capacity 170mAh/g, actual specific capacity ≥140 mAh/g (0.2c, 25°C);
- High safety: the most secure positive electrode material for lithium ion batteries;
- No pollution: does not contain any heavy metal elements that are harmful to human body;
- Long cycle life: it can charge and discharge more than 2000 times under 100%DOD;
- Fast charging performance: Lithium iron phosphate battery can be charged at high rate
Single 26650 Lithium Ion Battery Cell
26650 lithium battery materials are mainly divided into ternary materials and lithium iron phosphate materials.
INR26650 lithium battery has nominal voltage of 3.6V, full charge voltage of 4.2V, and discharge cut-off voltage of 3.0V.
IFR26650 lithium battery has nominal voltage of 3.2V, full charge voltage of 3.65V, and discharge cut-off voltage of 2.0V.
IFR26650 lithium battery capacity includes 2800mAh, 3000mAh, 3200mAh, 3400mAh, 3600mAh, 3800mAh and 4000mAh.
INR26650 lithium battery capacity tends to be 4500mAh, 5000mAh, 5500mAh and 6000mAh
26650 Lithium Ion Battery Positive Electrode Materials
26650 lithium battery positive electrode materials include lithium cobalt oxides, lithium manganese, NCA, NCM and lithium iron phosphate. Material system determines the working voltage and single cell capacity. Various materials manufacturers and cell manufacturers improve the overall indexes, such as battery voltage and capacity, by special material adding, coating process and manufacturing process improvement. Working voltage and theoretical capacity of various materials are normally as follow:
- Lithium cobalt oxides 3.6V, theoretical capacity 274mAh/g
- Lithium manganese 3.7V, theoretical capacity 148mAh/g
- Ternary material 3.65V, theoretical capacity 278mAh/g
- Lithium iron phosphate 3.2V, theoretical capacity 170mAh/g
- The materials determine the cycle life of the battery, so does the manufacturing level of the battery manufacter
Cell Specification:
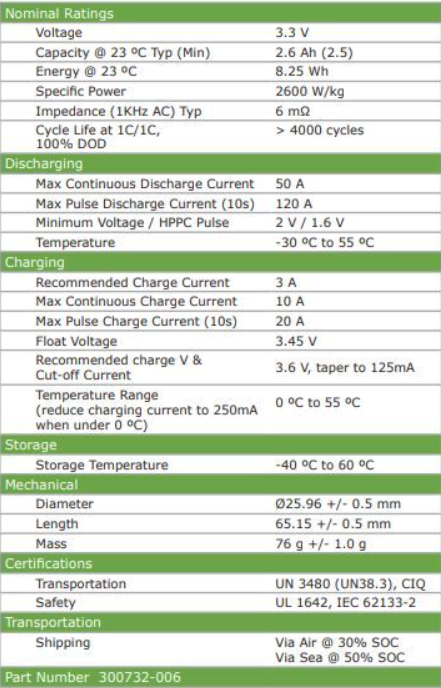
Discharge Voltage Profile and Cycle life with respect to different Operating temperature from datasheet

Energy Required=18kWh.
Number of cells(N)= Energy/(nominal voltage* Capacity)
N= 18000/(3.3*2.5)
N =2182
The minimum cell 2182 is required to get 18kWh energy. When the cells are connected in series the capacity remains the voltage will be the sum of each individual voltage. In parallel connection the voltage remains the same and capacity accumulates.
Nominal voltage of one cell = 3.3v.
Number of cells required to be connected in series connection to produce 330V and the capacity of the module will be 2.5Ah.
Ns(cell in series) = 330/3.3
Ns=100
To find the number of cells connected in parallel.
Np(cell in parallel) = total cell /Ns
Np =2182/100
Np= 21.82
cell architecture = 100S22P where 100 cells in series and 22 cells in parallel.
Battery Capacity:
Capacity = Parallel cell row* individual cell capacity.
Capacity=2.5*22
Capacity = 55Ah.
Current Supplied by the battery:
We have already calculated battery capacity which is 55Ah means it is going to supply 55A current per hour.Which can be Considered as C-rate
Range:
Powertrain energy consumption = 129 Wh/Km at 70% powertrain efficiency.
Range = capacity/ energy consumes per Kilometer
Range= 18000/129
Range =139 Km.
Internal Resistance of Battery:
The entire resistance encountered by a current as if it flows through a battery from the negative terminal to the positive terminal is known as internal resistance of battery.
Battery dimensions:
The below diagram shows where to find width, height and length
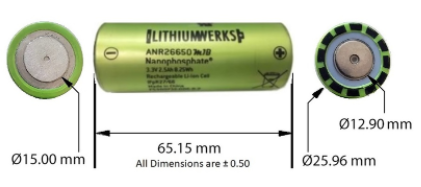
ANR26650M1-B cell has 26mm diameter and 65mm height.
Length of casing(L) = number of cells at mid*(cell diameter(26)+ margin at both side of cell(4))+clearance at side(diameter of edged cell + margin)
L = 98*30+60
L = 3000mm
Breadth of casing(B) = cell diameter(26) + margin at both side of cell(4) + clearance at side(diameter of edged cell + margin)
B = 20*30+60
B = 660mm
Height of casing(H) = 65 + 35 (Height of cell + margin for the cell holder and metal strips)
H = 100mm.
Weight of battery pack:
cell weight = 76g.
Number of cells = 2182.
Battery pack weight(W) = cell weight * number of cells+ weight of accessories.
W = 76*2182+4.5
= 165.8+4.5
=170.3Kg
Materials and process in battery pack construction:
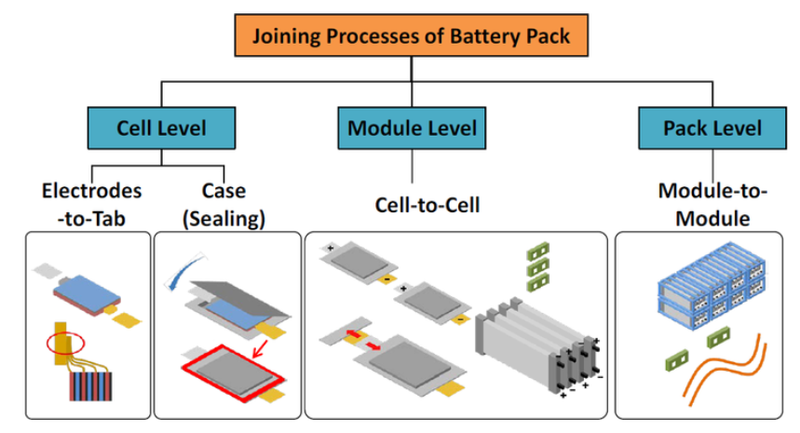
Joining Technologies of cells:
The interconnections between cells/modules are practised by Various welding techniques. Some of them are
An automotive battery pack can be hierarchically decomposed into three levels:
(a) cell level: an individual battery cell is primarily composed of positive and negative electrodes, separators, electrolyte, and case
(b) module level: a collection of multiple cells generally connected in series and parallel, encased in a mechanical structure and
(c) pack level: a battery pack is assembled by connecting modules together, either in series or parallel, with sensors and controllers, and then is encased in a housing structure
Typically, design and construction of an automotive Li-ion battery pack, involve producing robust and reliable joints as per hierarchical levels and types of cells used to build the battery pack. Relying on the geometry and form factor, lithium-ion cells are manufactured as
(i) cylindrical cells
(ii) pouch encased prismatic cell (typically called a pouch cell) and
(iii) solid-container encased prismatic cell (typically called a prismatic cell).
Choice of joining methods is largely based on the type of cell used, and subsequently, to satisfy electrical, thermal, and mechanical key criteria. This paper identifies major and emerging joining technologies with a comprehensive review and provides guidance for appropriate joining method selection.
Battery packs of electric vehicles, and hybrid or plug-in hybrid electric vehicles (EVs/HEVs/PHEVs) (a) joining at hierarchical/assembly levels and (b) cell types
Overview of Key Joining Challenges
Extensive research has been conducted on developing and characterising Li-ion battery cells including modelling and simulation, material development, performance enhancement, and safety. Limited literature is available on joining preferences and addressing their associated challenges, which can be summarised as follows:
-
Electrical and thermal challenges: (i) Producing joints with low electrical resistance—lower electrical resistance at the joint results in low energy loss, low heat generation, and subsequently, lower joint temperature increase during charging and discharging. (ii) Producing joints with low thermal input—low thermal input is preferable, especially when joining with fusion type welding processes, as exposing the cell to high heat may melt or disturb the safety vent, compromise seals, or cause internal shorting. (iii) High thermal fatigue resistance—thermal fatigue resistance of battery interconnects is an important criterion for long-term durability and reliability performance.
-
Material and metallurgical challenges: (i) Compatibility for dissimilar materials joining—dissimilar materials may create intermetallic layers, which are not preferred because of their higher electrical resistance and brittle nature compared with parent materials. Therefore, joints with low intermetallic is preferable. (ii) Variability of materials and surfaces—highly conductive and reflective materials, any surface coatings or oxide layers, joint stack-ups (especially varying thicknesses and/or multiple sheets) also need to be overcome for satisfactory joints.
-
Mechanical challenges: (i) Durable joint strength—the joint area/nugget size that can be achieved by the joining methods should have satisfactory joint strength with low strength variability. (ii) Avoid mechanical and vibrational damage when joining—excessive deformation of, or transmission of vibration into, the cell may damage internal connection. Precautions must be taken to avoid these as induced residual stress or vibrational energy may be released and cause joint failure.
Major and Emerging Joining Technologies:
This section reviews the advantages, disadvantages, limitations, and concerns of major joining technologies including ultrasonic, resistance spot/projection, micro-Tungsten Inert Gas (TIG) welding/pulsed arc welding, ultrasonic wedge bonding, micro-clinching, magnetic pulse welding, laser welding, and mechanical fastening.
- Ultrasonic Welding or Ultrasonic Metal Welding (UMW)
Ultrasonic metal welding (UMW) is one of the most commonly used joining methods for battery systems manufacturing and has been applied to a wide range of metals and thin metal films (e.g., foils). It utilises high frequency ultrasonic vibration, typically 20 kHz or above, to join substrate materials by creating solid-state bonds under a clamping pressure . In principle, high frequency relative motion creates progressive shearing and plastic deformation between mating interfaces and produces an atomic bond at elevated temperature (i.e., typically at 0.3 to 0.5 times the absolute melting temperature of the substrate materials). However, it needs two sided access, as shown in; one side uses an anvil to support the parts to be joined, and the other side a sonotrode that passes ultrasonic energy to the assembly. Ultrasonic welding is applied for joining of multiple thin foils, dissimilar materials, or highly conductive materials (e.g., Al, Cu, or others) especially for pouch cells . However, it may not be suitable for terminal-to-busbar joints of cylindrical or prismatic cells as vibration under pressure may damage structural integrity. UMW has been used for various EVs/PHEVs, including Nissan LEAF, General Motors Chevrolet-Volt, Spark, and Bolt.
Schematic of working principles and applications: (a) ultrasonic welding and (b) resistance/projection welding. RSW—resistance spot welding.
- Resistance Spot/Projection Welding
Resistance spot welding (RSW) works on the principle of electrical resistance at the mating surfaces when high current passes through them, creating localised heating and fusion of materials under pressure . Resistance spot welding is used to join different tab materials, up to 0.4 mm thickness, which are being used for battery connections, including steel, nickel (Ni), copper (Cu), and aluminium (Al). However, RSW of Al and Cu tabs is difficult because of high electric and thermal conductivity and in particular, the presence of an oxide layer on the surface of Al. To overcome these challenges, projection welding, a variant of RSW, shows a significant improvement, where projection on tabs will increase the joint quality and make welding easier. the projections not only act as energy concentrators for the weld, but also greatly increase electrode lifetimes, because a flat-end RSW-electrode can be used instead of a domed one . In spite of easy automation and good quality control, RSW has challenges when applied to battery welding because of RSW-electrode sticking (i.e., pick-up of material on the electrode tips) , highly conductive materials, dissimilar materials having different melting temperatures, and the smaller weld nugget experiencing heat generation during charging–discharging because of the increased current density.
- Micro-TIG or Pulsed Arc Welding (PAW)
Pulsed arc welding, also known as micro-TIG welding, uses a pulsed TIG arc without filler wire to join thin materials by localised fusion. The arc pulse has a very short duration, in tens of milliseconds, such that heat input is much less than in conventional TIG welding, and can be used for welding dissimilar materials However, even with a significantly reduced heat input, it is still crucial to control the welding parameters to avoid overheating of the battery. PAW is suitable for nickel, copper, or steel tabs and copper bus bars. Al tabs and bus bar joining using PAW is difficult and not preferable (because of the typical direct current (DC)–electrode negative configuration). Alternating current (AC) PAW is more typically used for Al welding, this is because of the cleaning mechanism, which breaks down the electrically resistive aluminium oxide skin of aluminium alloys. AC pulsed arc welding has not yet been commercially developed for micro-joining applications. For copper tab to copper bus bar welding, micro-TIG can produce a single spot nugget in diameter up to 4 mm. There is no report of the application of pulsed arc welding for joining of existing EV or HEV battery packs.
Schematic of working principles and applications of (a) pulsed arc welding and (b) ultrasonic wedge bonding. EV—electric vehicle.
Ultrasonic wedge bonding (UWB) is a joining technique typically used for electronic connections between circuit boards or electronic chips . During the welding process, a small (typically <500 μm in diameter) wire (of Al, Cu, or Au) is fed through a welding head; the welding head applies ultrasonic vibration and pressure forcing the wire against the welding target, for example, the battery terminals or bus bar. The main mechanism of UWB is cleaning of mating surfaces and bringing surfaces to the distance required for atomic bonding to create the connections, although other mechanisms, such as inter-diffusion of wire into the mating surface and mechanical interlocking, also contribute to the joining process . UWB can be used for joining of dissimilar materials and the bonded wire can be used as a fuse to protect the battery pack against extreme thermal and mechanical impact or internal defects. However, because transfer of ultrasonic energy into the material to be joined is critical for welding, any significant lateral movement of the welding substrate will be detrimental as it will decrease the vibration amplitude, thereby diminishing the power of the welding operation. Consequently, the cells and the bus bar in the battery module need to be fixed rigidly to allow the technology to be applied. In many cases, adhesives or glues have to be used to enhance the rigidity of cells.
Clinching or micro-clinching is a mechanical interlocking mechanism of sheet metal parts, especially used for automotive body-in-white, domestic appliances, or electronics joining applications Clinching is a joining process in which a mechanical interlock (i.e., local deformation without use of any additional joining elements) is created by a tooling set (a punch and a die). Clinching is a simple technique for point joining of metal sheets typically from 0.2 mm to 4 mm thick, to a total joint thickness of about 6 mm. Using the clinching, tab-to-tab joints are feasible. The feasibility of clinching as an alternative method of joining for pouch cell tab joining has been reported. Clinching may not be feasible for cylindrical/prismatic cells joining as access to the both sides of the assembly is required. Further, clinch joints are prone to becoming loose under vibration, moisture ingress, and so on.
Working principles and applications of (a) clinching and (b) laser welding.
Joining of dissimilar materials using this method is an established and tested technology within the electronics industry. Soldering of a tab to a terminal of a cylindrical cell may be feasible. Soldering directly to a cell is not recommended as it is easy to melt or disturb the safety vent, compromise seals, or cause internal shorting if the heat is too high (i.e., heat input is the key soldering parameter). Further, it is feasible to solder pouch cell tabs if additional filler metal is used between the tabs. Special aggressive fluxes are required for joining aluminium, which is typically considered unattractive because of the potential for corrosion, reduction of joint strength under vibration, and creating debris. Therefore, soldering is unlikely to be of widespread interest for battery joining applications.
Laser welding uses a focused laser beam as a point source of energy to create localised heating to join parts together. Because of the small cross section of the laser beam and its energy concentration, narrow and deep welds can be made with a high welding speed .Also, because of the narrow welds and high welding speed, the process generates a low level of heat in the assembly during welding , which is important for battery tab welding, as the chemicals inside the batteries are very heat sensitive. A schematic of fillet laser welding and application for prismatic cell-to-bus bar joining When welding a tab to a terminal, generally, the tab should be thinner than the battery cell casing terminal. Process parameters need to be controlled to provide weld strength and conductivity without penetrating the battery case/can. Other applications include sealing of the battery casing for prismatic cells, and joining of tab-to-bus bar and bus bar-to-bus bar . As the weld pool from laser welding is very small, it has a very small gap tolerance, subsequently, during tab welding, it may be necessary to clamp the tab to the battery . For oxidisation sensitive materials, such as Al, gas shielding is also required.
- Magnetic Pulse Welding (MPW)/Electromagnetic Pulse Technology (EMPT)
Magnetic pulse welding is a solid state welding process that uses a magnetic pulse to accelerate one part into another, creating a high speed (up to 500 m/s) collision that results in bonding . The advantages of this process include low heat input, high joint strength, and the capability to join dissimilar materials. However, as the technology has the potential to create an induced current in the cell, because of the pulsed magnetic field necessary for the joining process, damage may occur, which renders it unsuitable for battery joining. However, MPW/EMPT has the potential for joining pouch cell tab-to-tab or tab-to-bus bar . Furthermore, detailed investigation is required as induced eddy currents may affect the electrochemistry/physical parts (e.g., potential cracks or internal joining between current collectors, which lead to battery internal short-circuit) of the pouch cell. To mitigate the risk of damaging the pouch cell or module sensors, a specially designed weld head and shielding plate may be required during welding.
Working principles and applications of (a) magnetic pulse welding/electromagnetic pulse technology (MPW/EMPT) and (b) nut and bolt assembly.
Various mechanical fastening methods can be used for battery joining, including nut and bolt, spring clasp, screws or snap-fits, and so on . Nut and bolt joints may be either physically distinct nut and bolt assemblies or a threaded feature, for example, electrode and nut. For battery module level connections, nut and bolt joints are mainly limited to prismatic cellsmand have been used to join electric and hybrid vehicle battery modules. Another example of using mechanical fastening is spring loaded prismatic cells into a custom designed container. Permanent joining, such as welding, may not be suitable for large pack level joining because of battery maintenance and service concerns . Consequently, mechanical nut and bolt assembly has been widely adopted at the pack level.
Continuous advances are being made by battery manufacturers to improve battery pack safety, weight, cost, size, durability, and energy density. Addressing these requirements, this section focuses on cell types and different joining technologies to reflect pack construction and connectivity at their hierarchical levels (i.e., cell, module and pack levels).
Battery Pack Hierarchical Joining
- Joining of Cylindrical Cell Based Battery Pack
Cylindrical cells consist of a tubular cylindrical can and incorporate safety mechanisms that will interrupt current flow and/or enable venting of gas to avoid overpressure of the can. Cylindrical cells have better thermal management efficiency because of small size, but low packaging efficiency because of their round cross-section. However, their relatively small size results in a large number of cells and connections compared with modules composed of pouch/prismatic cells. The suitability of available joining techniques to build battery packs using cylindrical cells at cell, module or pack levels is described as follows:
-
Cell level joining: The assembly process for cylindrical cells requires joining methods at two levels, which are (i) electrode foil-to-tab joining and (ii) terminal welding (i.e., tab-to-case/can). Ultrasonic and resistance spot welding are the most commonly used joining methods for electrode foil-to-tab and terminal welding, respectively . Laser welding is also feasible for electrode foil-to-tab joining, however, tight part-to-part tolerance has to be maintained for satisfactory joints. Terminal welding is not be feasible by laser welding if line of sight is obscured.
-
Module and pack level joining: Because of the physical size and form of a cylindrical cell, external current collectors are added to connect cells. Physical projections reduce the contact area in projection welding, allowing concentrated heat generation at the point of contact, and formation of the weld nugget faster and at a lower current level compared with conventional spot welding , reducing potential damage to the RSW-electrode. Similar to resistance welding, advances in high-frequency power supplies, increased low-current control, and arc stability, have enabled much finer TIG welding, such as pulsed arc welding. Pulsed arc welding offers excellent copper to copper joining with a fairly relaxed process window with respect to part fit-up and positioning tolerances of the electrode to the parts . As ultrasonic welding exerts high frequency vibration under locally applied force, there is a risk that a cell may suffer internal damage to the electrode. Therefore, ultrasonic welding of cylindrical cells at module level may not be appropriate without steps to mitigate the possibility of damage. However, ultrasonic wedge bonding has been used for cell-to-cell connections. In the Tesla battery pack each of the cells has two wires that act as fuses (one each for the anode and cathode) and are connected using ultrasonic wedge bonding. Laser welding is emerging as an efficient alternative for forming joints between cylindrical cell terminals and external current collectors, that is, bus bars. However, part-to-part fit-up needs to be carefully controlled to achieve satisfactory joints using laser welding. By designing proper jigs and fixtures, a large number of cylindrical cells can be connected to produce a battery module. Permanent joining, such as welding, may not be suitable for large pack level joining because of battery maintenance and service requirements As a consequence, mechanical nut and bolt assembly has been widely adopted at the pack level.
- Joining of Pouch Cell Based Battery Pack
In Pouch cells, the internal electrode stack is contained within a soft plastic-aluminium laminate package. Current collectors are welded internally to terminal tabs that protrude through seals to allow external connection. Use of plastic-metal laminates for the cell pouch allows reduction of cell packaging material, higher energy densities, for the same chemistry type (i.e., compared with prismatic cells), but typically requires a more complex module structure to constrain the cells. The suitability of joining methods to build battery packs using pouch cells at cell, module, or pack levels can be summarised as follows:
-
Cell level joining: During fabrication of pouch cells, the joining operations are (i) electrode current collectors to positive and negative terminal tabs, and (ii) case sealing of pouch cell—an automated and standard process under vacuum . Electrode-to-tab welds are conventionally made using ultrasonic technology because of the need to create a joint through a stack of foils. RSW is not appropriate as RSW-electrodes are prone to picking-up highly conductive cell terminal/electrode and tab materials . However, fibre laser welding technology may be used for increased weld quality and strength . The key to successful application of laser welding is to ensure that (a) the foils are in close contact, and (b) a pulsed laser is used to avoid overheating. In the case of pouch cell case sealing, typically, a compact heat sealer is used to seal aluminium–polymer laminate films.
-
Module and pack level joining: Module designs typically position positive and negative terminal tabs either at opposite ends or the same end of the cell based on series or parallel connection requirements. Therefore, the cells are joined either by tab-to-tab or tab-to-bus bar connections. Ultrasonic welding has received significant attention for module level joining as a result of its ability to produce good welds for dissimilar materials and multiple thin layers. RSW or projection welding, pulsed arc welding, and clinching of tab-to-tab or tab-to-bus bar joints are feasible. However, process stability, joint characteristics, thermal input, and process control require further investigation. However, feasible soldering of pouch cell interconnects is not recommended as it raises concerns of joint strength under vibration, neutralisation of fluxes, risk of localised heat damage, and creation of debris in the joint area. As an alternative, MPW/EMPT has the potential for joining pouch cell tab-to-tab or tab-to-bus bar . However, detailed investigation is required for MPW/EMPT application, as induced eddy currents may affect the physical parts/electrochemistry (e.g., potential cracks or internal joining between current collectors that leads to battery internal short-circuit) of the pouch cell. To mitigate the risk of damaging the pouch cell, or module sensors, a specially designed weld head and shielding plate may be required during EMPT welding. Laser welding is another alternative solution for pouch cell tab-to-tab or tab-to-bus bar joining. Fibre lasers are able to weld many material combinations including aluminium to aluminium, aluminium to steel, copper to steel, and copper to aluminium. Further investigations are required for fixture design, process parameter optimisation and process control. Generally, pack level (i.e., module-to-module) connections are made with mechanical fasteners.
- Joining of Prismatic Cell Based Battery Pack
Aluminium or steel cans are typically used for the housing of solid container-encased prismatic lithium-ion cells, more commonly called prismatic cells. The metal can ensure structural stability, mechanical robustness, and humidity protection. In addition, it allows for the use of safety features such as pressure relief vents, which are not possible in pouch cells. In some cases, prismatic cells may allow packaging to be more efficient than cylindrical cells because of their form factor . The suitability of available joining methods to build battery packs using prismatic cells at cell, module, or pack levels is described as follows:
-
Cell level joining: The fabrication of prismatic cells involves similar joining operations to cylindrical and pouch cells (i) between current collector tabs and electrode foil(s), (ii) between collector tab and battery terminal, and (iii) case sealing. Ultrasonic welding is most commonly used for joining current collector tabs with electrode foil(s) . Resistance spot welding is used to connect current collector tabs with the case or with the top cap of the case . Typically, prismatic cell positive and negative terminals are based on mechanical nut and bolt assembly. Laser welding is also used for cell level joining and traditionally case sealing. As reported by Shannon , laser welding has potential for a number of manufacturing applications, such as case sealing and terminal welding.
-
Module and pack level joining: As a result of the stackable form of prismatic cells, battery pack modularity and various design configurations for parallel or series connections are readily achievable. Module and pack level joining is mainly performed with mechanical nut and bolt fasteners or clip fitting. Mechanical nut and bolt assembly has the advantage of easy disassembly and higher joint strength compared with other reported joining techniques. However, there are issues with high contact resistance and maximum torque (to avoid internal damage) that can be sustained by the cell stud. In some cases, laser welding has also been used for connecting cell terminal with bus bar . Ultrasonic wedge bonding and micro-TIG between terminal and bus bar may be feasible for prismatic cells. However, design changes may be required for UWB since cell terminals are not directly connected with bus bars. Application of these methods requires investigation of wire thickness, heat input, current carrying capacity, and so on.
Joining Technology Recommendation for Battery Manufacturing
This section maps joining technologies with manufacturing readiness levels (MRLs) to indicate options and development status of battery joining from a manufacturing perspective . Manufacturing readiness levels (MRLs) are used to provide a relative measure of technology maturity, risk level, and extent of application. Ultrasonic welding, ultrasonic wedge bonding, and mechanical assembly are frequently used in battery pack manufacturing (used by battery manufacturers, original equipment manufacturers, and tier 1 suppliers) and have been demonstrated at the highest level of production (MRLs 8–10). RSW, micro-TIG, micro-clinching, and soldering have demonstrated their capability under laboratory conditions (MRL 4) to produce joints for low or batch volume during module manufacture (MRL 6/7). In contrast, laser welding exhibits a broad range of capability from MRL 4 to MRL 10. For example, laser welding applications for module level joining of cylindrical or pouch cells are in MRL 4–6, whereas laser applications for case sealing or module level joining of prismatic cells have been demonstrated at MRL 10. Another joining technology, MPW/EMPT, has a low MRL as it has only demonstrated limited capability under laboratory conditions to produce tab-to-tab joining.
MRLs for assessing technology maturity of current joining technologies for module level joining
Enclosure:
- Series Connection: Series connection is the connectivity of the components in a sequential array of components.
- Parallel Connection: Parallel connection is the connectivity of the components alongside to other components.
Cells in Series Connection
In series, cells are joined end to end so that the same current flows through each cell. In case if the cells are connected in series the emf of the battery is connected to the sum of the emf of the individual cells. Suppose we have multiple cells and they are arranged in such a way that the positive terminal of one cell is connected to the negative terminal of the another and then again the negative terminal is connected to the positive terminal and so on, then we can that the cell is connected in series.
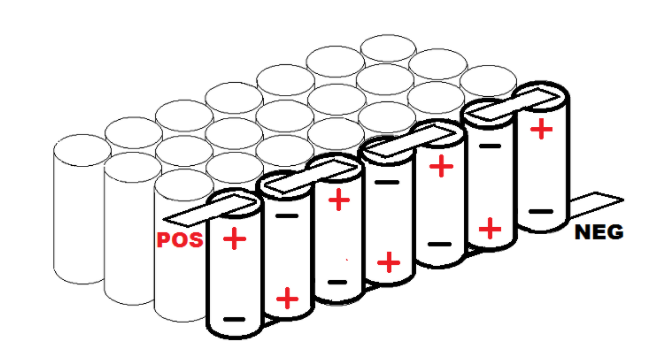
Equivalent EMF/Resistance of Cells in Series
If E is the overall emf of the battery combined with n number cells and E1, E2, E3 , En are the emfs of individual cells.
Then E1 + E2 + E3 + …….En
Similarly, if r1, r2, r3, rn are the internal resistances of individual cells, then the internal resistance of the battery will be equal to the sum of the internal resistance of the individual cells i.e.
r = r1 + r2+ r3 + rn
Cells in Parallel Connection
Cells are in parallel combination if the current is divided among various cells. In a parallel combination, all the positive terminal are connected together and all the negative terminal are connected together.
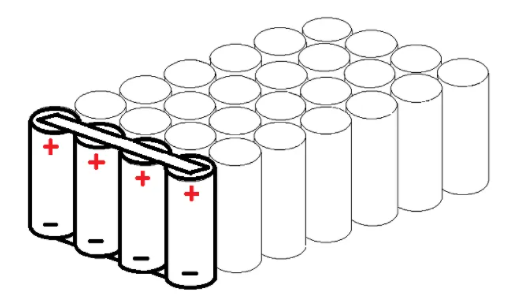
Equivalent EMF/Resistance of Cells in Parallel
r = (1r1 + 1r2 + 1r3 +…….. 1rn )-1
If emf of each cell is identical, then the emf of the battery combined with n numbers of cells connected in parallel is equal to the emf of each cell. The resultant internal resistance of the combination is above
Cell Holders:
These houlders are used for houlding the individual cells in a better posture without mis-assemble.The connection can be made accordingly to make series connection and parallel connection to form the required module dimensions.
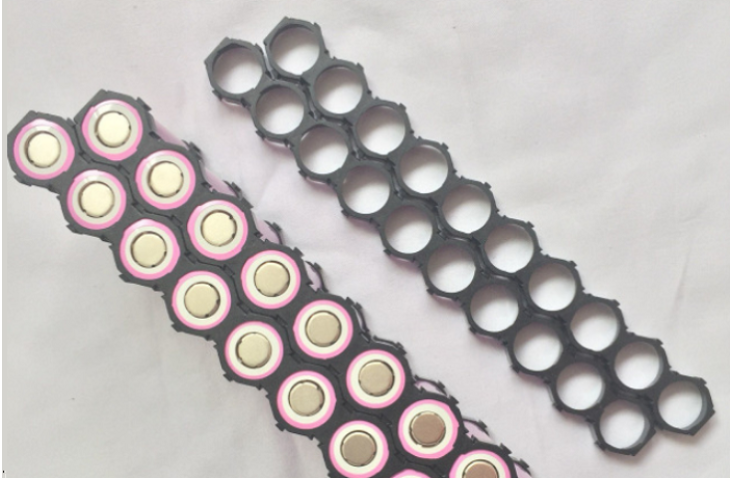
After installed the cells in a individual module the entire maximum positive and maximum negative terminal are made under Single pair of terminals as shown below
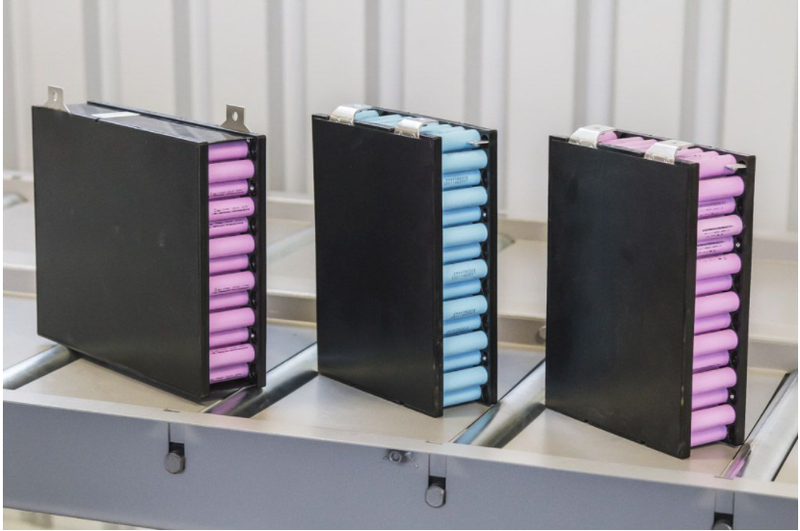
Here shown the cells are arranged and welded without using cell Holders as
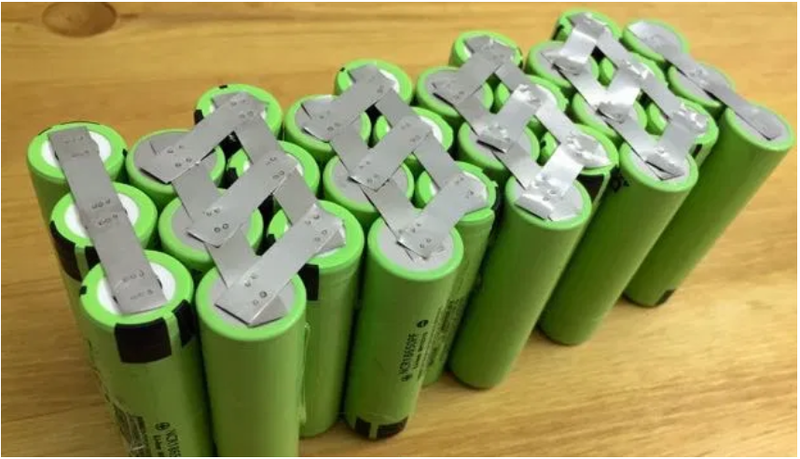
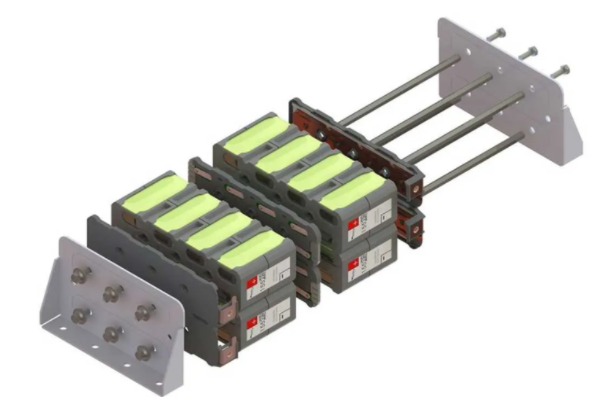
Battery pack arrangement:
Finally the overall battery pack after the arrangement of all cabinet connections with enclosure looks like this as shown below
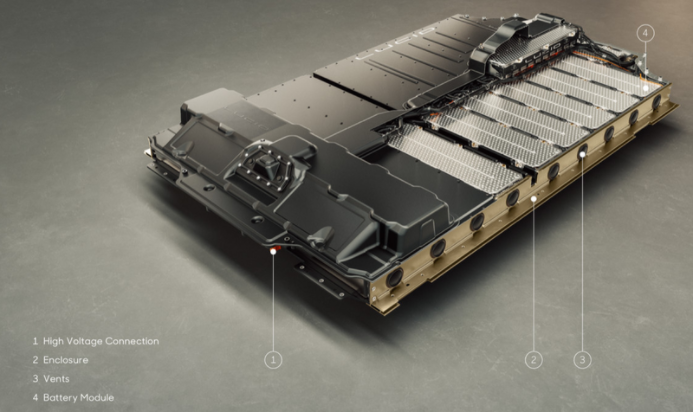
Vents holes are present with enclosure for cooling/ heating the battery pack temperature according to its environment conditions.
The pack construction are different for every Manufactures
Below shown battery pack construction types and process of Tesla, BMW and Nissan Leaf.
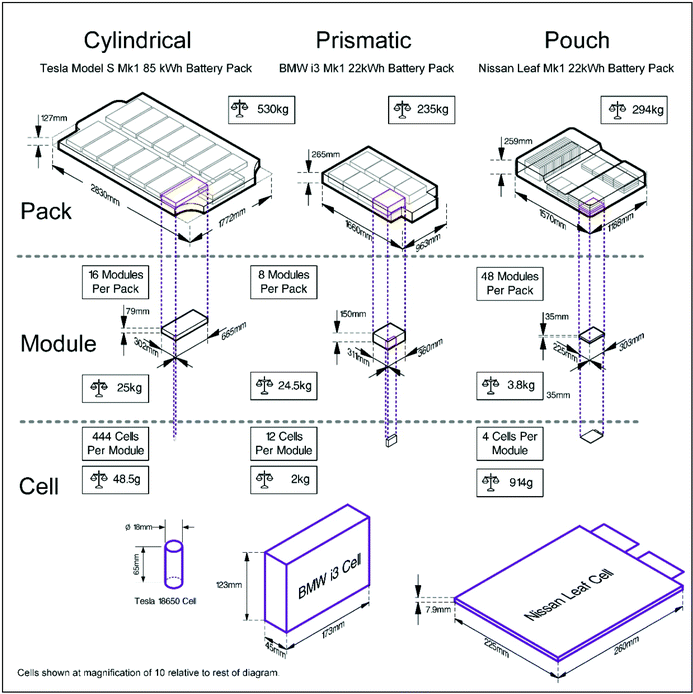
Conclusion:
- We design a Mechanical Design of Battery Pack using the cell- ANR26650M1-B
- Cylindrical, pouch, and prismatic cells, based battery pack construction are discussed in detail, with limitations of the specific technologies identified where their use is infeasible. Further, applicability of joining methods is discussed with hierarchical levels of battery manufacturing.
- Key joining challenges are identified for battery systems manufacture, including electrical, thermal, material, metallurgical, and mechanical challenges.
- Joining techniques are described with respect to MRLs and suitability of the identified joining technologies is quantified. Recommendations for further investigation of joining technologies are made based on Pugh matrix scores, MRLs, and application potential.