2D meshing on the instrumental Panel
Aim -
- To perform mid surface extraction and 2D meshing on the instrument panel according to the given quality criteria.
Objective -
- To do geometric cleanup on the component.
- To generate a mid surface from the parent component.
- To Mesh the component according to the given quality criteria.
- To get a proper mesh flow and solve the off elements in the fillet and rib regions as much as possible.
- To Create separate property ID's for the ribs and assigning thickness to them.
Theoretical FrameWork -
- A dashboard (also called dash, instrument panel (IP), or fascia) is a control panel set within the central console of a vehicle or small aircraft. Usually located directly ahead of the driver (or pilot), it displays instrumentation and controls for the vehicle's operation.
-
Where the dashboard originally included an array of simple controls (e.g., the steering wheel) and instrumentation to show speed, fuel level and oil pressure, the modern dashboard may accommodate a broad array of gauges, and controls as well as information, climate control and entertainment systems.
-
Contemporary dashboards may include the speedometer,tachometer,odometer,engine coolant temperature gauge, and fuel gauge turn indicators, gearshift position indicator, seat belt warning light, parking-brake warning light,and engine-malfunction lights. Other features may include a gauge for alternator voltage, indicators for low fuel, low oil pressure, low tire pressure and faults in the airbag (SRS) systems, glove compartment,ashtray and a cigarette lighter or power outlet – as well as heating and ventilation systems, lighting controls, safety systems, entertainment equipment and information systems, e.g.,navigation systemes.
-
Instrument panels are often made of acrylonitrile-butadiene-styrene (ABS), ABS/polycarbonate alloys, polycarbonates, polypropylene, modified polyphenylene ether (PPE) and SMA (styrene-maleic anhydride) resins. These plastics allow for complex designs in items such as airbag housings, center stacks for instrument panels, and large, integrated instrument panel pieces.
-
Wholly integrated single-piece units can be manufactured from all-urethane and all-polypropylene resins. This results in a seamless instrument panel with greatly reduced NVH levels, molded-in color and with significant cost savings for the manufacturer. Cost effective post-consumer and in-plant recycling are also achievable.
_1629025518.png)
Figure 1-Toyota,Koenigsegg,Benz,Tesla Dashboard. |
_1629025912.png)
Figure 2-Instrumental Panels. |
Procedure -
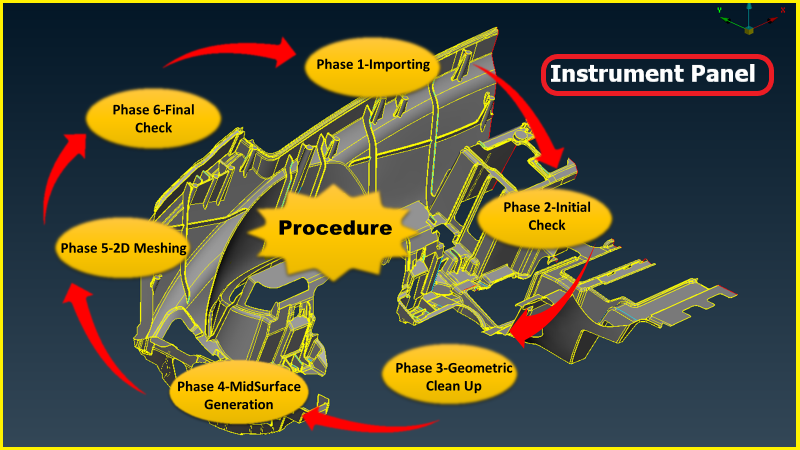
Phase 1-Importing the CAD Model
- Hence we are importing a given CAD geometry into the ANSA.
- There are file formates like IGES,STEP,Parasolid where we can import these file formats into any CAD,CAE Softwares.
- In ANSA we can import all the CAD Software file formates like
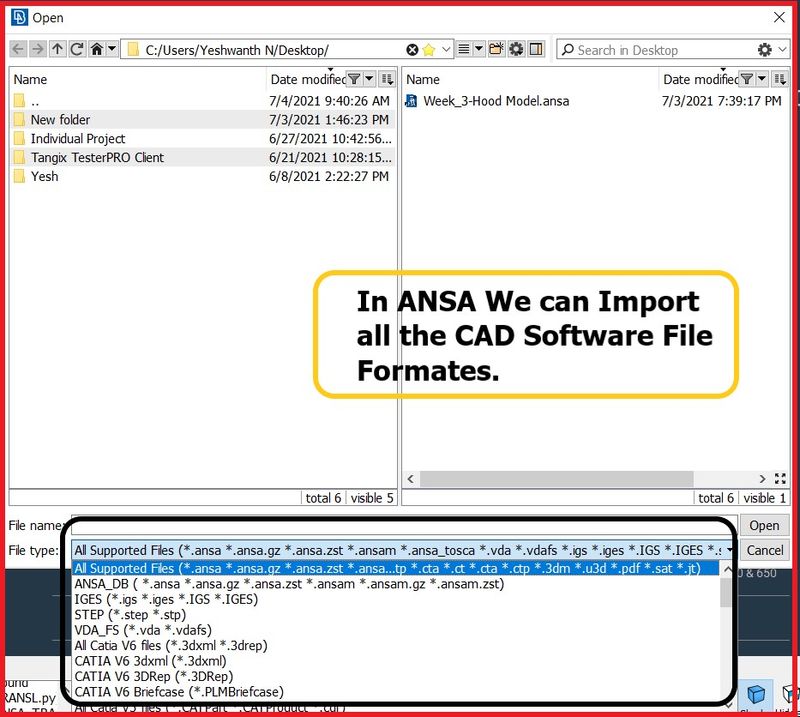
Figure 4-Supported File Formats. |
- IGES [Initial Graphics Exchange Specification].
- STEP [Standard for the Exchange of Product Model Data].
- Solidworks.
- Catia V5,V6
- Simens NX CAD
- Inventor
- Creo
- Solid Edge
- Rhinoceros 3D
- IGES,STEP,These two are standard file formats which are mostly used in industries.But now a days in industries,they are aslo using parasolid file format.
- Now import the model into ANSA GUI.The Model given to us is in STEP File Format.
- Go to Main Pull Down Menu >> File >> Open.

Figure 5-Importing/Opening the Model. |
_1629035641.png)
Figure 6-Model Imported into GUI. |
- Here,after importing the model into GUI.
- We can see the macros are not connected and there are free edges present in the model.
- To get rid off this or to get equivalence,Do topo on the model by window selection.
- To do Topo,Go to Topo Module >> Faces >> Topo >> Window Selection.
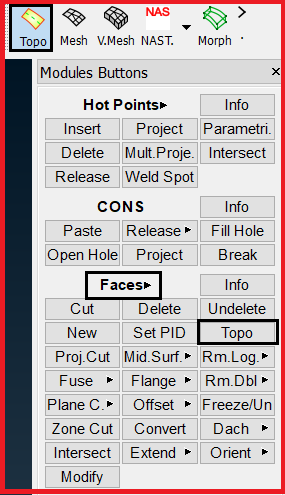
- After doing topological clean up,you can see the model without free edges shown in figure 8.
_1629035919.png)
Figure 8-After Doing Topo. |
Phase 2-Initial Check
- Before working on the model.We have to check the geometry if there are any errors like
- Damaged Geometry.
- Free edges in unnecessary areas.
- Unnecessary points on the lines.
- Unnecessary Connections and connectivity error.
- By assessing the Instrument Panel model there are errors in the geometry.
- If there are any unnecessary properties in the property browser,Delete them and then proceed.
- We have to do some geometry clean up on the model,Cause there will be some minimal errors in the model.To solve that we should do some geometry clean up on the model.
Phase 3-Geometric Clean Up on the Parent Component
- Here we will be doing some geometry checks on the parent component.
- We have to fix the geometrical errors in the parent component,Then only we will be able to extract auto midsurface using skinoffset.
- To fix the geometry checks go to Tool Bar >> Checks >> Geometry.
Step-1
_1629036319.png)
- After clicking on the check geometry,The geometric errors will be displayed.
- We can fix that geometric errors by manually or automatically.
- For this hood model,We can fix that errors automatically by auto fix.
- While checking for errors in the geometry make sure to check this options in the checks manager.
Step-2
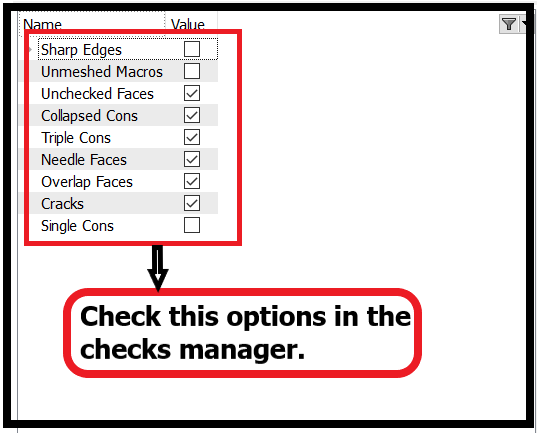
Figure 10-Check Geometry Options. |
Terminologies for Geomerty Options -
- Unchecked faces - Faces that failed for the shadow operation.
- Needle Faces - Degenerated faces are faces that have their opposite CONS coincident.
- Collapsed Cons - A CONS where it's starting and ending position coincide.
- Triple Cons - Areas where three or more faces have a common boundary.
- Cracks - Red CONS at inner areas.[Holes are excluded].
- Single Bounds - Red CONs at outer areas.[Holes included].
Step-3
_1629039717.png)
Figure 11-ANSA Checks Manager. |
Step-4
_1629039937.png)
Figure 12-Geometric Errors. |
- Here in the Checks window all problems are reported with red color.
- Under Description column the kind of problem is explained.
- Focus functions are available in order to isolate geometrical problems and handle them easier.Select to fix all or specific reported problems by pressing right mouse button on the header of the list or one or more highlighted problems.
Step-5
_1629041175.png)
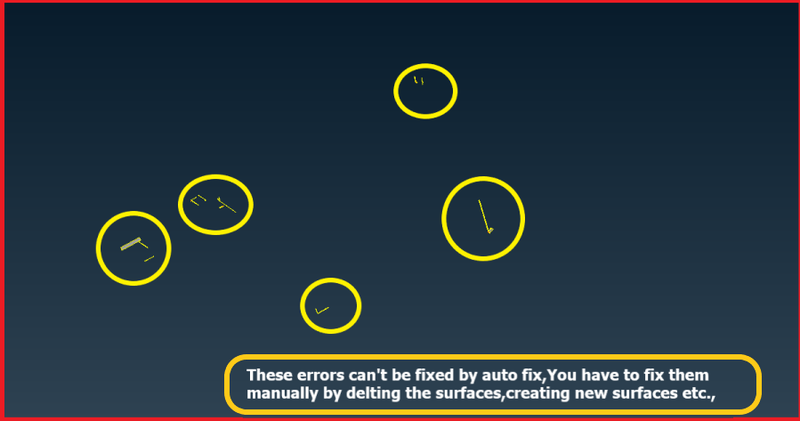
Figure 14-Errors that should be Fixed by Manually. |
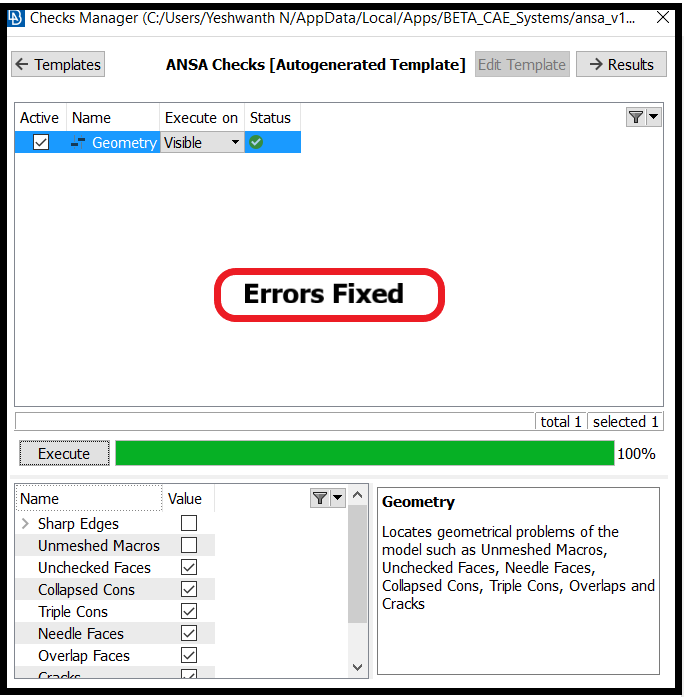
- [Note: All problems except triple CONS can be fixed by the automatic fixing.]
- [Note: Right mouse clicking on Check Geometry line, performs an action to all listed problems.In case where not all problems are fixed automatically, retry or proceed to fix them manually.For this component no need to fix manually because all the errors have been fixed with auto fix.]
- Similarly do the same process for the Outer Extract,Hinge Reinforcement Extract and Latch Reinforcement Extract.
- Here for the Outer Extract we have toggle the lines in the hemming regions because that hemming lines will be failing for minimum length,So we have to toggle that lines while meshing on it.
Phase 4-MidSurface Generation
- Before extracting the mid surface for the components we need to give perimeter and macros length on the components while extracting mid surface.
- This makes the component to get a desired shape,So it will be easy to extarct a midsurface without any errors.The possiblities of errors will be less.
- To give perimieters and macros length on the componets,
- Go to Mesh Module >> Perimeters >> Length.
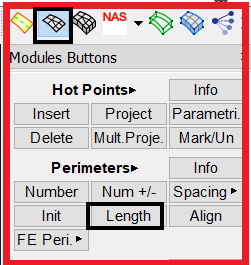
Figure 16-Permieter Length Tool. |
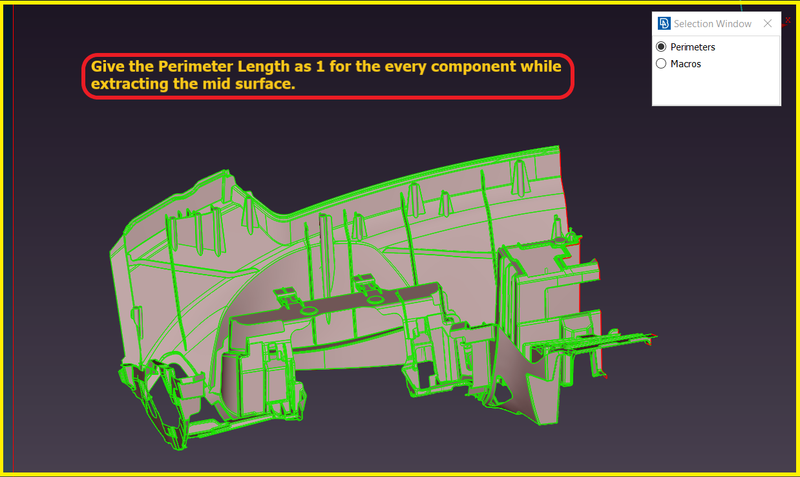
Figure 17-Selecting the CONS to give Perimeter Length. |
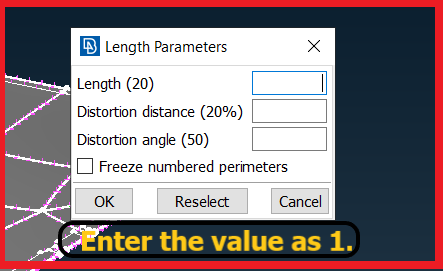
Figure 18-Enter the Value as 1 according to the component size. |
- Simillarly do the same thing for the macros also.
- Mesh Module >> Perimeters >> Length.
- This tool defines the element length on selected perimeter segments or macro areas.
- The element length may be explicitly declared or may be declared as a factor to be multiplied by the existing element length.
- We can Extract Mid Surface by Two Methods called
- Using Skin MidSurface Option in Faces Panel in Topo Module.
- Using Offset Tool in Faces.
- But for this component,We will be extracting midsurface by using offset tool in faces anf for the ribs,we will be extracting midsurface manually.
4:1 Why to Extract Mid Surface ?
- Before extracting the mid surface for every component,We should measure the thickness of the component and then we have to proceed to extract the mid surface.
- If the component thickness is less than 6mm then we will come to know it is a sheet metal component.
- For sheet metal and plastic components,Mid Surface extraction is must.
4:2 Generate Mid Surface
- To generate midsurface
- Go to Topo Module >> Faces >>Offset >> Faces >> Feature >> Select the Face >> Give Offset Value and Direction.
- This tool turns the solid description of a thin part into thin shell description by isolating the outer or inner skin of the solid description.
[Note:While extracting the midsurface,make sure to uncheck delete original faces option.]
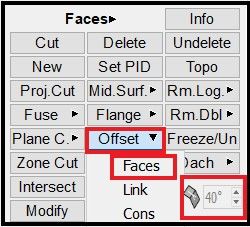
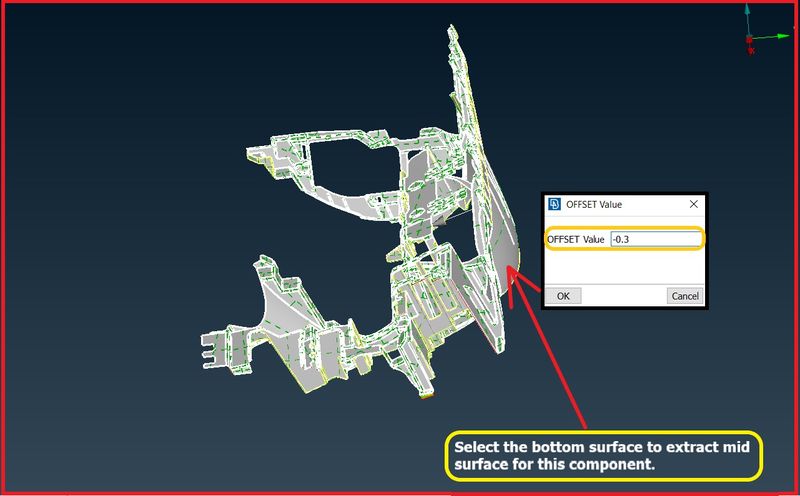
Figure 20-Selecting the Bottom Face to extract a mid surface using offset tool from faces. |
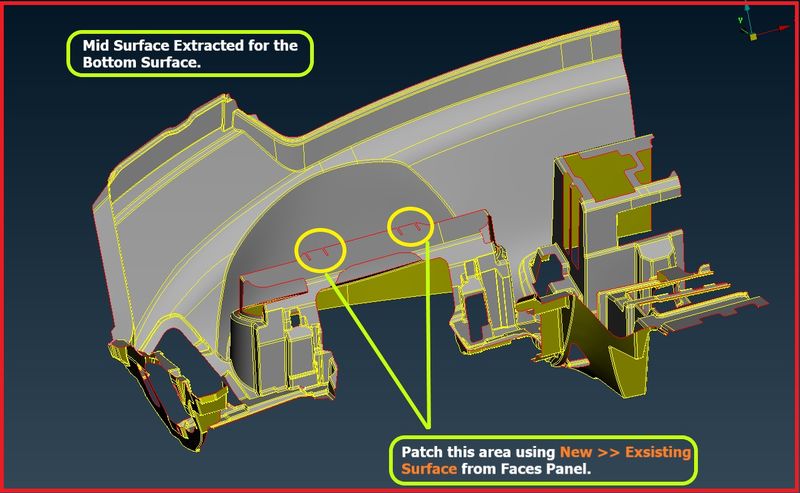
Figure 21-Mid Surface Extracted for the Bottom Surface. |
- Here the midsurface has been extracted for the bottom surface only,Now extract the midsurface for the Ribs and DogHouses.
- Now hide the parent component using NOT tool from focus panel.
- And set the different PID for the Mid Surface alone.
- To set PID,Go to Topo Module >> Faces >> Set PID >> Window Selection on Mid Surface >> Create New Property >> Double Click.
Step-1
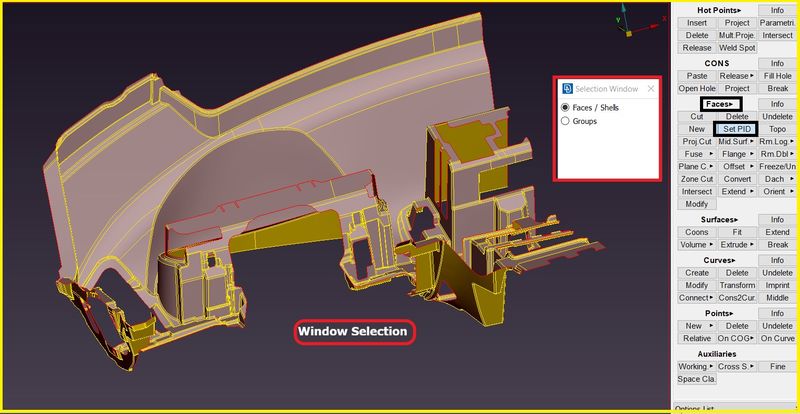
Step-2
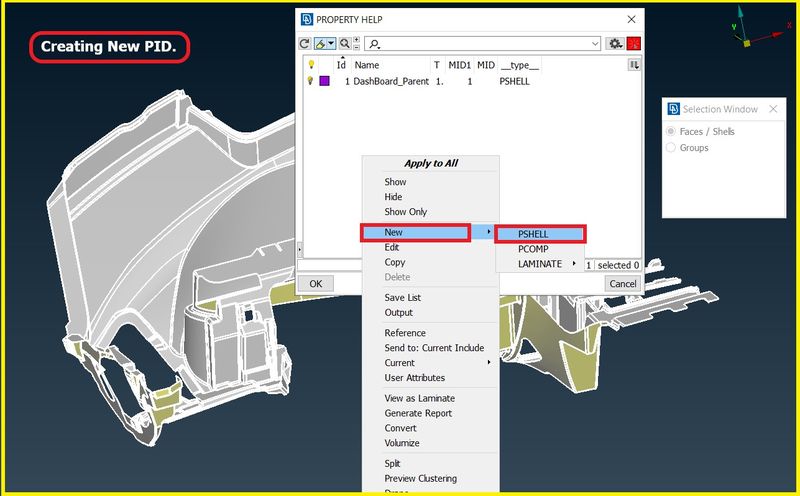
Figure 23-Creating New PID. |
Step-3
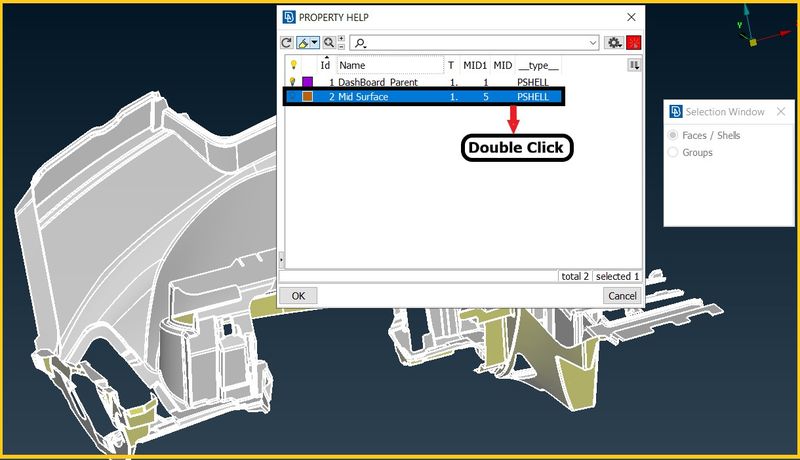
Figure 24-New PID Created. |
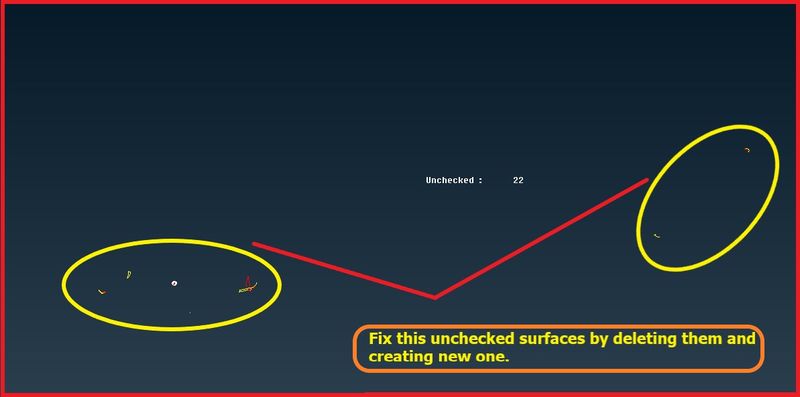
Figure 25-Fix these Unchecked Faces by Deleting them and Creating New One. |
- Fix these Unchecked Faces by Deleting them and Creating New One as shown below in Figure 26.
_1629052292.png)
Figure 26-Fixing the Unchecked Faces. |
- There are two approaches of extracting a mid surface for dog houses.
1) Approach A-Cross Pattern.
2) Approach B-Make 0.5 mm Offset.
- In Approach A,To extract a mid surface as cross pattern for dog houses,There are five methods to extract a mid surface for dog houses in a cross pattern manner.
1) Creating a Curve by selecting Mid Point.
2) Creating a Middle Curve using Middle from Curves Panel.
3) Creating a Cut by selecting a Mid Point and converting it as curve by CONS to Curve Tool from Curves Panel.
4) Extracting a Mid Surface by using Offset >> Faces from Faces Panel.
5) Extracting a Mid Surface by using Middle >> Single from Faces Panel.
1) Approach A-Cross Pattern.
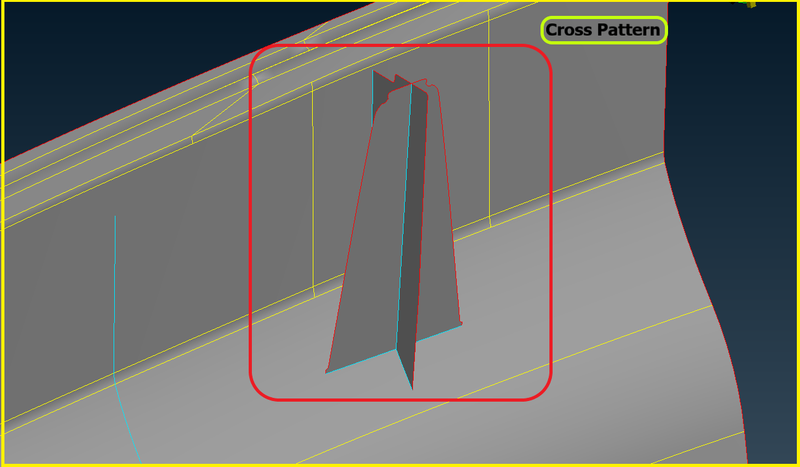
- In this approach,they are 5 methods to extract a mid surface.
1) Creating a Curve by selecting Mid Point.
- To create a curve,Go to Topo Module >> Curves >> Create >> Select Midpoint and Start Creating.
Step-1
_1629088466.png)
Figure 28-Creating Curve. |
Step-2
_1629088509.png)
Figure 29-Projecting the curve to the surface. |
Step-3
_1629088605.png)
Figure 30-Creating Surface. |
Step-4
_1629088665.png)
Figure 31-Deleting Unwanted Surface. |
Step-5
_1629088739.png)
Figure 32-MidSurface Extracted for Dog House. |
2) Creating a Middle Curve using Middle from Curves Panel.
- To create a Mid Curve,Go to Topo Module >> Curves >> Middle >> Select First and Second Group Cons.
Step-1
_1629093687.png)
Figure 33-Creating Mid Curve. |
Step-2
_1629093759.png)
Figure 34-Projecting Curve on Surface. |
Step-3
_1629093828.png)
Figure 35-Mid Surface Extracted for Rib. |
3) Creating a Cut by selecting a Mid Point and converting it as curve by CONS to Curve Tool from Curves Panel.
- To create a cut,Go to Topo Module >> Faces >> Cut.
Step-1
_1629111051.png)
Figure 36-Creating Mid Curve. |
Step-2
_1629111323.png)
Figure 37-Mid Curve Created Using Cons to Curve. |
Step-3
_1629111436.png)
Figure 38-Creating a Surface. |
Step-4
_1629112076.png)
Figure 39-MidSurface Created for Rib. |
4) Extracting a Mid Surface by using Offset >> Faces from Faces Panel.
- To extract a midsurface using offset,Go to Topo Module >> Faces >> Offset >> Faces.
Step-1
_1629114713.png)
Figure 40-Extracting Mid Surface for Rib. |
Step-2
_1629115187.png)
Figure 41-Extending the Surface to Parent Component and Releasing the Triple Cons. |
Step-3
_1629115666.png)
Figure 42-Doing Topo on the Parent Rib. |
Step-4
_1629116177.png)
Figure 43-Mid Surface Extracted for Rib. |
5) Extracting a Mid Surface by using Middle >> Single from Faces Panel.
- To Extract a Mid Surface by using Middle,Go to Topo Module >> Faces >> Middle >> Single.
Step-1
_1629116399.png)
Figure 44-Extracting Mid Surface. |
Step-2
_1629116477.png)
Figure 45-Surface Created. |
Step-3
_1629116528.png)
Figure 46-Selecting the Edge to Extend Over Surfaces. |
Step-4
_1629116616.png)
Figure 47-Mid Surface Extracted for the Rib. |
Final Mid Surface of Approach A -
_1629117154.png)
Figure 48-Final Mid Surface of Approach A. |
2) Approach B-Make 0.5 mm Offset.
- In this approach,Offset 0.5 mm for all the doh house and create a rib and extend them over to the surfaces.
Step-1
_1629122203.png)
Figure 49-Creating Surface. |
Step-2
_1629122560.png)
Figure 50-Extending Surface. |
Step-3
_1629122648.png)
Figure 51-Intersecting the Surfaces and Deleting Unwanted Surfaces. |
Step-4
_1629122979.png)
Figure 52-Mid Surface Extracted for the Dog House. |
Final Mid Surface of Approach B-
_1629123268.png)
Figure 53-Final Mid Surface of Approach B. |
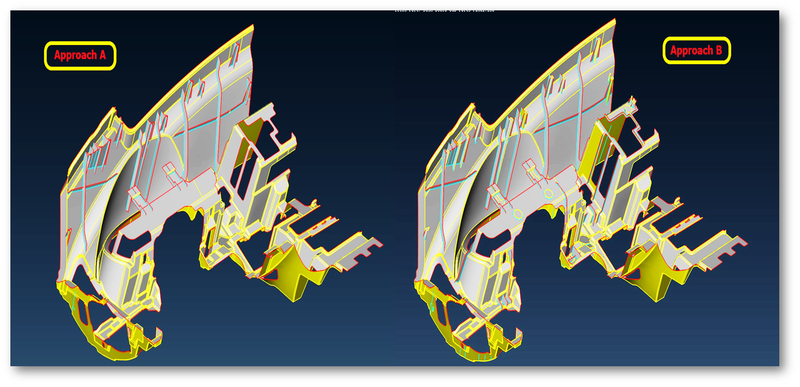
Figure 54-Final Mid Surface of Approach A and B. |
Step-1
Figure 55-Projecting the Cons to the Bottom Surface to Extract Mid Surface. |
Step-2
_1629174766.png)
Figure 56-Extracting Mid Surface. |
Step-3
_1629174910.png)
Figure 57-Mid Surface Extracted for this Region. |
4:3 Geometric Clean Up on the Mid Surface -
- Here there are two approaches of geometric clean up.
1) Approach A-Mid Line Extraction
2) Approach B-Toggling One Line and Keeping Other Line.
_1629176178.png)
Figure 58-Approach A & B. |
- Rearrange the lines to get proper mesh flow like shown in below Figure 59.
_1629176260.png)
Figure 59-Rearranging the Lines. |
Final Geometric Clean Up on the Mid Surface-
_1629176675.png)
Figure 60-Final Geometric Clean Up on Mid Surface. |
Phase 5-2D Meshing
- Once geometry cleanup is completed (e.g. surfaces are stitched together — no unwanted free surface edges inside the geometry), meshing is next.
Some rules of thumb when meshing:
- The mesh should look rather smooth and regular (keep in mind that the analysis is based on your mesh and the mesh quality is key.
- Use the simplest element type suited for the problem.
- Start with a coarse mesh and understand the modeling results; then use a finer mesh if needed.
- Try to keep mesh related uncertainties to a minimum if possible. Keep it simple as it can get more complicated on its own.
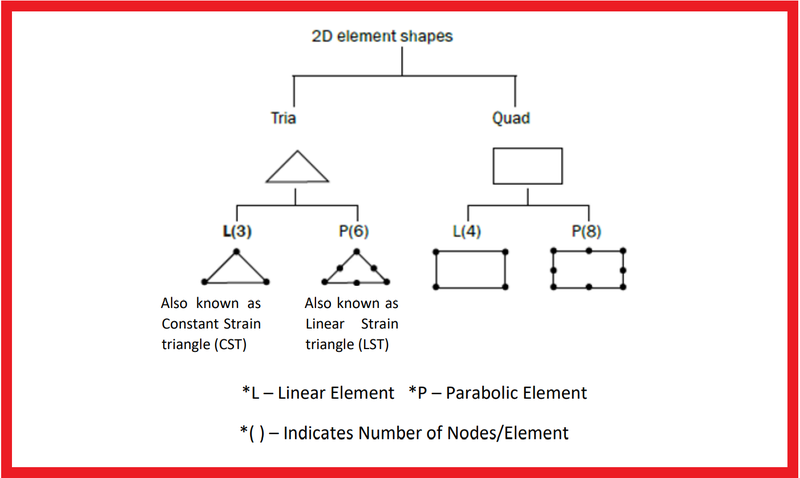
Figure 61-2D Element Shapes. |
- Different Element Type Options for Shell Meshing:
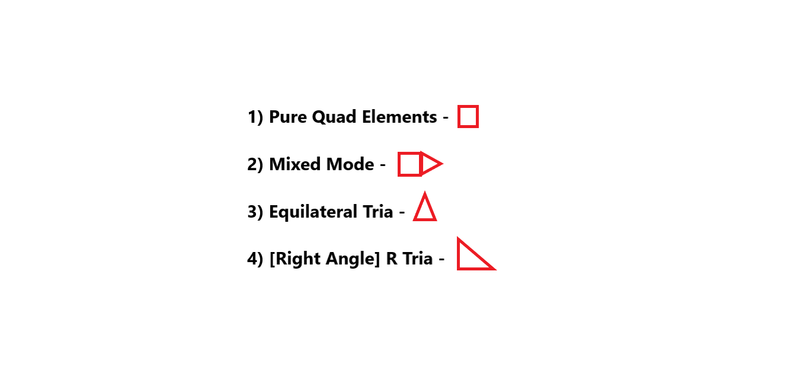
5:1 Enter the Parameter quality criteria what they given for the Hood Model
- Select and set the respective quality criteria for the corresponding elements to perform the Quality Checks (Hidden Mode). Also set the general presentation settings concerning the ANSA workspace
- Use the F11 key to open the Quality Criteria and Presentation Parameters management window (F11 Menu).
- Tool Bar >> Quality Criteria (F11) >> Enter the Values.
- Tool Bar >> Parameter >> Enter the Values.
Target/Average Length- 4 Units
Sl. No. |
Quality Criteria |
Function / Definition |
Value |
1 |
Aspect Ratio Ratio |
Ratio of Max. Length by Min. Length |
3 |
2 |
Skewness |
Deviation from the ideal shape |
45 |
3 |
Warping |
Angle between the 2 planes of the same element(Quad) |
15 |
4 |
Jacobian |
Transformation of Coordinate System. |
0.7 |
5 |
Min. Length |
Shortest length of any given element |
2 |
6 |
Max. Length |
Longest length of any given element |
6 |
7 |
Min angle Quad |
Minimum angle in any given Quad element |
45 |
8 |
Max angle Quad |
Maximum angle in any given Quad element |
135 |
9 |
Min angle Tria |
Minimum angle in any given Tria element |
30 |
10 |
Max angle Tria |
Maximum angle in any given Tria element |
120 |
11 |
Tria % |
Percentage of Tria on any meshed surface |
15 |
Figure 63-Quality Criteria. |
- Now enter the Mesh Parameters
- Go to Tool Bar >> Mesh Parameters >> Enter the Values.
_1629179033.png)
Figure 64-Mesh Parameters. |
[Note : Save the Mesh Parameter and Criteria file for that component and save it in any other drives,Cause whenever we open that component,we can open the Element Criteria file and Parameter file,So criteria and mesh paremeters will be applied habitually instead of entering again.]
1) Aspect Ratio
- This is the ratio of the longest edge of an element to either its shortest edge or the shortest distance from a corner node to the
opposing edge ("height to closest node").
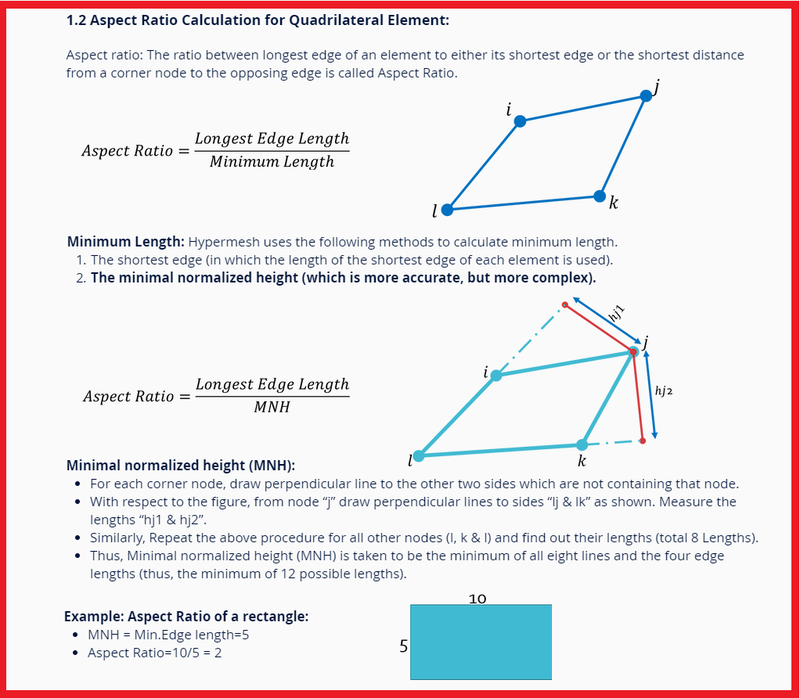
Figure 65-Aspect Ratio Calculation. |
2) Skewness
- Skew of triangular elements is calculated by finding the minimum angle between the vector from each node to the opposing
mid-side, and the vector between the two adjacent mid-sides at each node of the element.
- For Skewness: Ideal=0,But < 45 is acceptable.
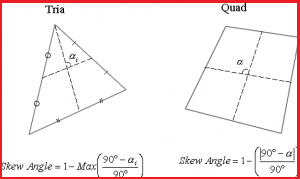
3) Warping
- This is the amount by which an element (or in the case of solid elements, an element face) deviates from being planar. Since
three points define a plane, this check only applies to quads. The quad is divided into two trias along its diagonal, and the angle
between the trias’ normals is measured.

4) Taper
- Taper ratio for the quadrilateral element is defined by first finding the area of the triangle formed at each corner grid point.These
areas are then compared to one half of the area of the quadrilateral.
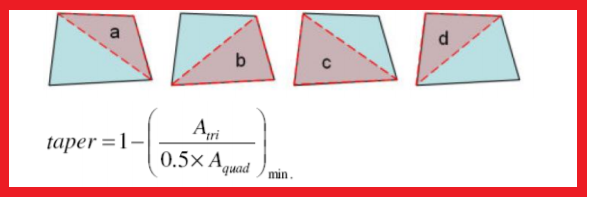
5) Minimum and Maximum Length
- The shortest distance from a corner node to its opposing edge (or face, in the case of tetra elements) referred to as height to
closest node.
5:2 Conditions to be followed while meshing
- Feature capturing is must while meshing.All the nodes must be connected to the shared edges.
- Avoig higher number of trias.
- Important Parameter's in tria management
- No trias in corner's or edge's.
- No opposite trias.
- No back to back trias.
- No trias in fillets or hemmings(We can have minimum but anyhow try to avoid).
- No rotational quads.
- No trias should share a boundary with feature line.
- Connectivity between elements.
- Split and perform the mesh.
- Use mixed type mesh for irregular shaped surfaces and quads only for rectangular/square surfaces(Opposite sides should be parallel and equal).
5:3 Begin meshing the surfaces
- Start meshing from the centre regions or from least free edges.You will get proper mesh density and proper mesh flow.
Why Meshing is Needed ?
- Finite Element Method reduces the degrees of freedom from infinite to finite with the help of discretization or meshing (nodes and elements). One of the purposes of meshing is to actually make the problem solvable using Finite Element. By meshing, you break up the domain into pieces, each piece representing an element.
How to Begin Mesh ?
- Start meshing form the least free edges,Like start meshing from the center.
- It will be easy to get proper mesh flow and we will get uniform mesh density.
- Don't mesh form the edges,It will be difficult and you will get many error,So start meshing from the center.
- Choose the element type while meshing.
- For this component we will be using mixed element type and working on it.
- We can also quads element type.This type can be used when we have rectangular surface.
- We can use Tria Element type.This type can be used for 3d tetra meshing.
Start Meshing
- To begin mesh,Switch form topo module to the mesh module.
- Before Meshing set the perimeter and macro length to the component.
- Here set the perimeter and macro length as target element size.
- It will split according to the target element size,So it will be easy for us to mesh.
- To Mesh >> Go to Mesh Module >> Mesh Generation >> Best Mesh >> Select the area.
- While Meshing Switch from shaded mode to the hidden mode,Then only we will be able to see the visibility element quality.
_1625413486.png)
Figure 69-Drawing Styles Panel. |
- Here for this component,I have used different mesh algorithms like
1) Best Mesh
- This type of mesh automatically meshes Macro Areas using all alternative meshing algorithms and keeps only the mesh of highest quality according to QCHECK.
- The Best function may be applied to selected unmeshed Macros, or to all visible Macros according to the chosen option (Selected or Visible respectively).
2) Batch Mesh
- This type of mesh automatically meshes Macro Areas and FE shell areas using the Batch meshing method, but with taking into account the global defined meshing parameters.
- The meshing algorithm may be applied to selected or visible unmeshed or meshed Macros or FE shell elements, according to the chosen option (Selected or Visible respectively).
3) Spot Mesh
- This Mesh Generation>Spot-Mesh algorithm generates more elements than the Free algorithm and brings better results to Macro Areas that have Weld or Connecting Spots on them.
4) Free Mesh
- This type of Mesh [Generation>Free algorithm] generates as few elements as possible, trying to maintain the best quality possible.
5) Advance Front Algorithm
- This type of mesh automatically meshes Macro areas and FE shell mesh areas using the Advancing Front meshing method, taking into account the element type already selected.
- The Advancing Front meshing method generates elements beginning from the boundaries of a Macro-Area, taking into account the shell element distortion and minimum length.
- The resulting shell elements are of first or second order shell elements according to the status of the 2nd Ord flag.
_1629180286.png)
Figure 70-Meshed Regions. |
- Here the elements will fail in the rib regions as shown in Figure 71,Cause there are triple cons,So elements will fail,We can't do anything,So accept the elements failing and proceed to mesh.
_1629180778.png)
Figure 71-Off Elements in Rib Regions. |
_1629181018.png)
_1629181537.png)
Figure 73-Completley Meshed on the Component. |
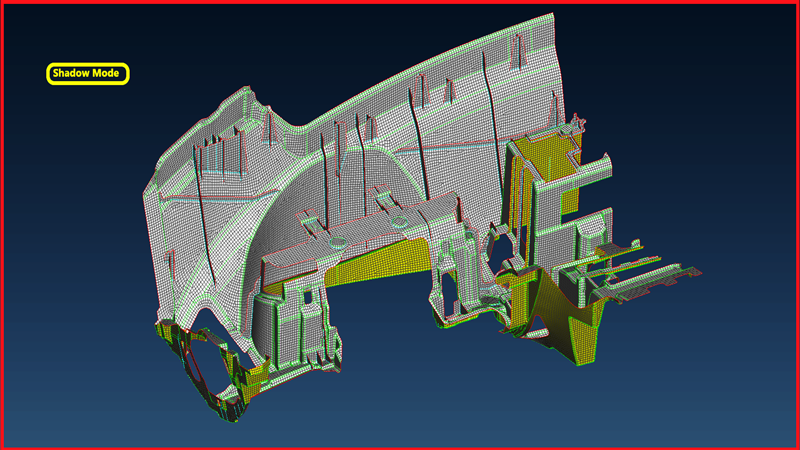
5:4 Assign Thickness to the Components
- Go and assign thickness to the components.
- Go to properties browser and double click on the component which you want to assign the thickness,A new window will pop on the GUI.Give thickness value there.
- Simillarly do the same process for every component.
_1629182247.png)
Figure 75-Property Browser. |
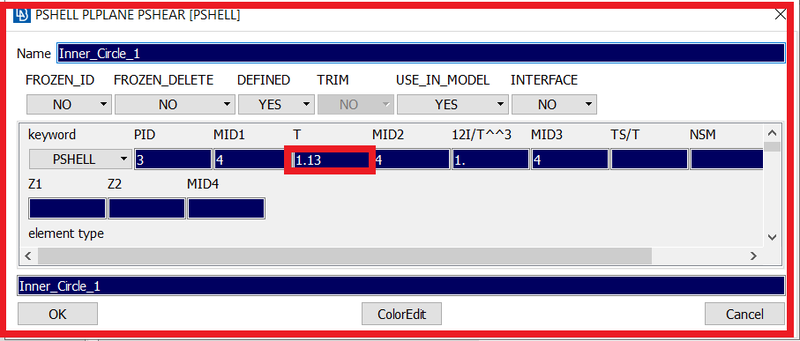
Figure 76-Thickness Assigned to one particular surface. |
- Simillarly assign the thickness for the every region which have varying thickness.
Phase 6-Final Check
- After Assigning Thickness,Check whether the thickness have been appplied or not.
- To check Go to Utilities >> Quality Criteria >> Presentation Parameters >> Draw Shell as Solid.
_1629182687.png)
Figure 77-Quality Criteria Panel. |
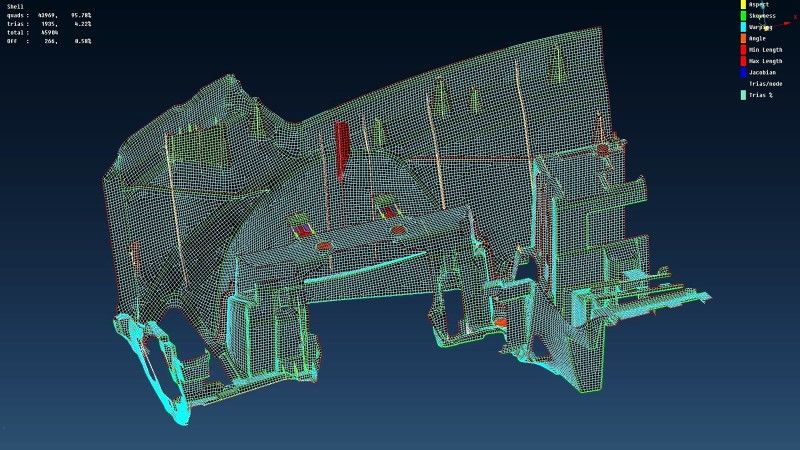
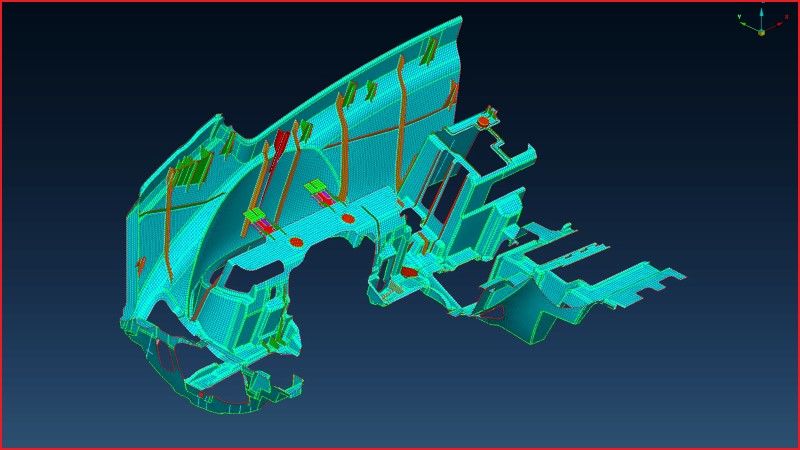
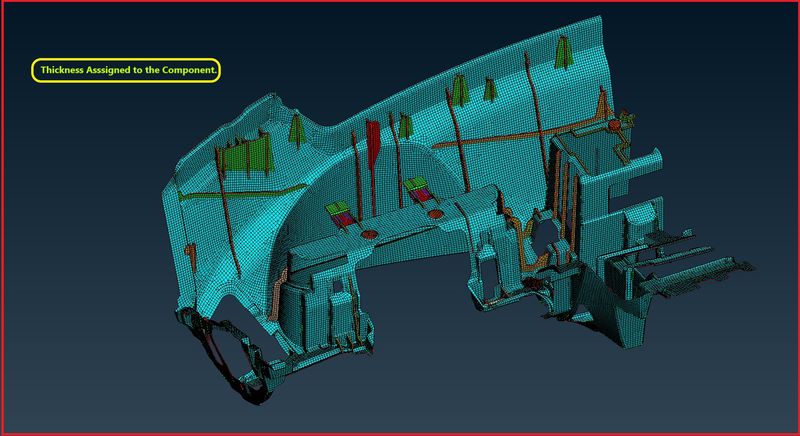
Figure 80:1-Thickness Assigned to the Component. |
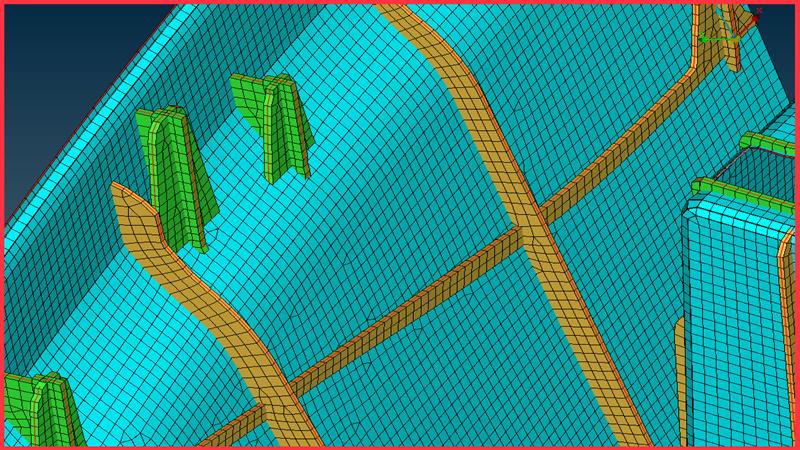
Figure 80:2-Thickness Assigned to the Component. |
- In this component many Trias will be touching each other,We cannot drag them in the rib and chamfer regions.
- Every trias are touching each other in the chamfer and rib region.
- This is because of triple cons in the rib region.
- If we try to eliminate that trias in the rib regions,The elements will be failing for jacobian,warping,So accept that trais and proceed.
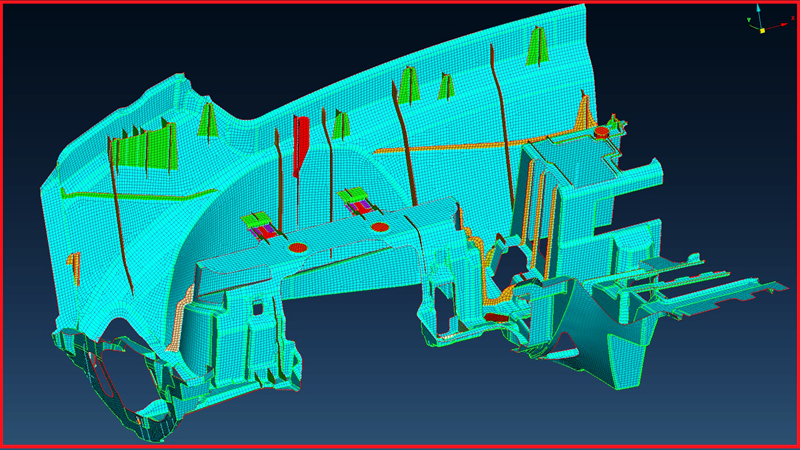
Figure 81-Instrument Panel With PID View. |
Final CAD Model Images -
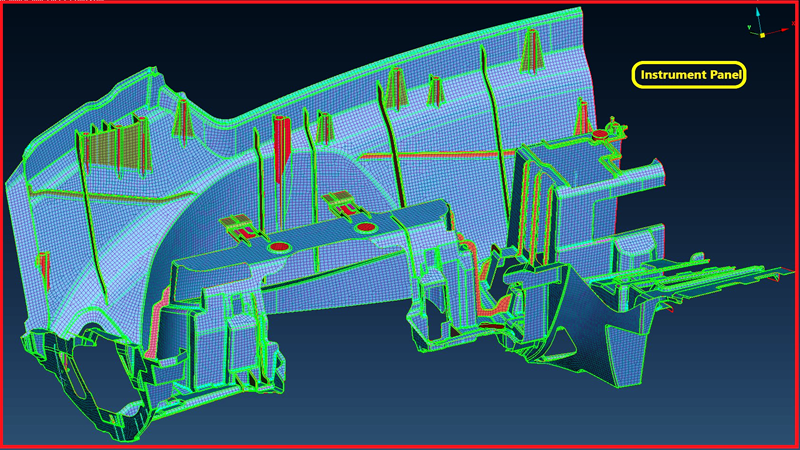
Figure 82-Final CAD Model Image 1:1. |
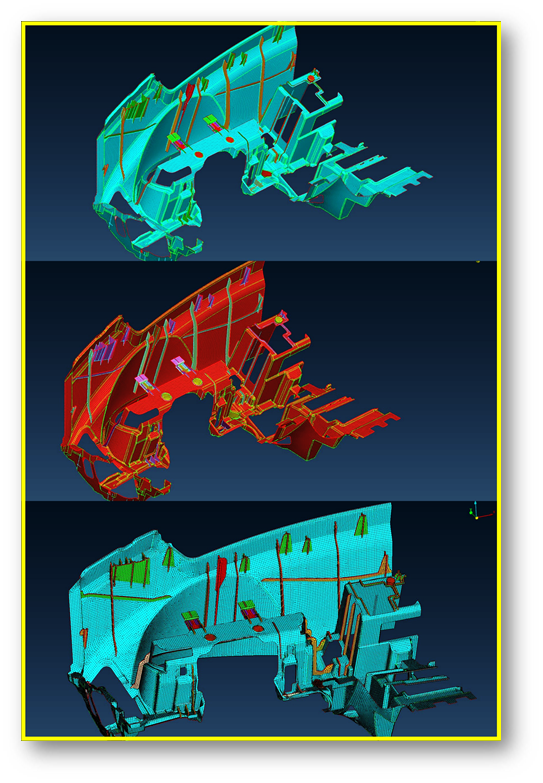
Figure 83-Final CAD Model Image 1:2. |
Result -
- Hence the mid surface has been extracted to the parent component.
- Hence there are no surface deformations in the geometry.
- A well connectivity has been established between the surfaces.
- The features have been captured properly.
- A good mesh flow have been achieved.
- Hence thickness have been assigned successfully to the component.
Learning Outcome and Conclusion -
- In this project 1,I came to know
- How to extract the mid surface manually for the complex components.
- How to clean complex geometry .
- How to generate a proper mesh flow with low tria percentage.
- How to extract a mid surface for doghouses in cross pattern
- How to assign thickness to the components.