Question
Model a 25 storey building on ETABS with structural properties as specified below. Ground floor or plinth floor level can be taken at a height of 1.5 metres from the base. Each of the successive 25 storeys has a storey height of 3 metres.
Structural Element Sizes:
Beams : 300 × 400 mm
Columns : 800 × 800 mm
Slab: 150 mm thick
Material Properties:
Grade of Concrete: M30
Grade of Steel Reinforcement Bars: Fe 415
Loading:
Dead Load on beams from infill wall: 10 kN/m (Let us assume the same for the roof floor given parapet)
Live load on the floor : 3 kN/m2 (Let us assume the same for the roof floor)
a) Buildings are assumed to be pinned at the base
b) All columns in all stories are of the same size
c) All beams in all stories are of the same size
d) Building is located on Soil type II and in Zone III. Assume other factors if required.
Carry out the following exercises:
Check if the translational fundamental natural period of vibration in both the x and y direction is approximate: where Tx1= 4.4 seconds and Ty1= 4.2 second
This check will help confirm if the modeling is done correctly. Some deviations from the above values are possible (± 2%). But any major deviation will suggest an error in modeling.
Check if the following provision in Table 5 of IS 1893 (part 1) – 2016, on torsional irregularity is satisfied:
The natural period corresponding to the torsional mode of oscillation must be less than the two fundamental translational modes of oscillation along each principal plan direction.
Check if the two provisions of clause 7 in Table 6 (shown below) of IS 1893 (part 1) – 2016, regarding vertical irregularity is satisfied
Check if the provision on inter-story drift limitations in clause 7.11.1.1 is satisfied. Please note that this check is for Serviceability Limit State and hence is for the situation when the structure is subjected to unfactored seismic base shear
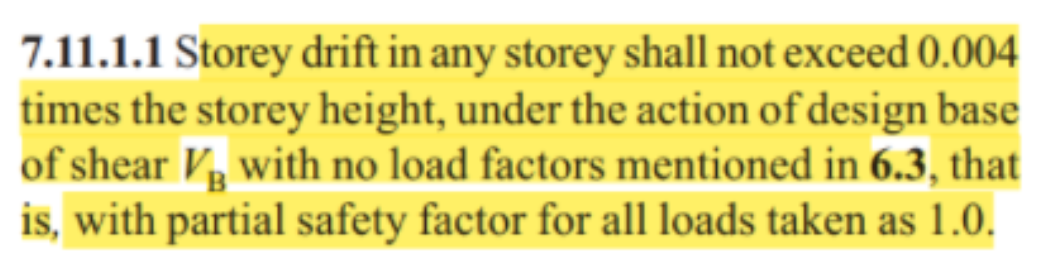
Ans:
Aim: Modeling of a 25-storey ETABS building whose feature meets the requirements and whose base or plinth level can be achieved at a height of 1.5 meters from the floor. The floor height of 25 consecutive floors is 3 meters.
Introduction:
ETABS is the abbreviation of "Three Dimensional Analysis at Home". ETABS is a product of Computers and Structures, Inc., recognized worldwide as a leader in structural engineering and software development for structural and earthquake engineering.
ETABS is an engineering software tool for the analysis and design of multi-storey buildings. Modeling tools and models, model-based models, analytical models, and problem-solving techniques are all coordinated with the grid-like geometry inherent to this type of model. Basic or higher level systems under static or dynamic conditions can be evaluated using ETABS.
Procedure:
Step 1
- Open the ETABS software on the desktop
- Click on the menu and select Create New Template
- After selecting a new model, the model initialization dialog box will appear
- Select the built-in option as a preset
- Selected Mills as per Metric SI, Regional Materials as per India, Steel Database as per India, Steel Design Code as per IS 800:2007, Design Code as per IS 456:2000
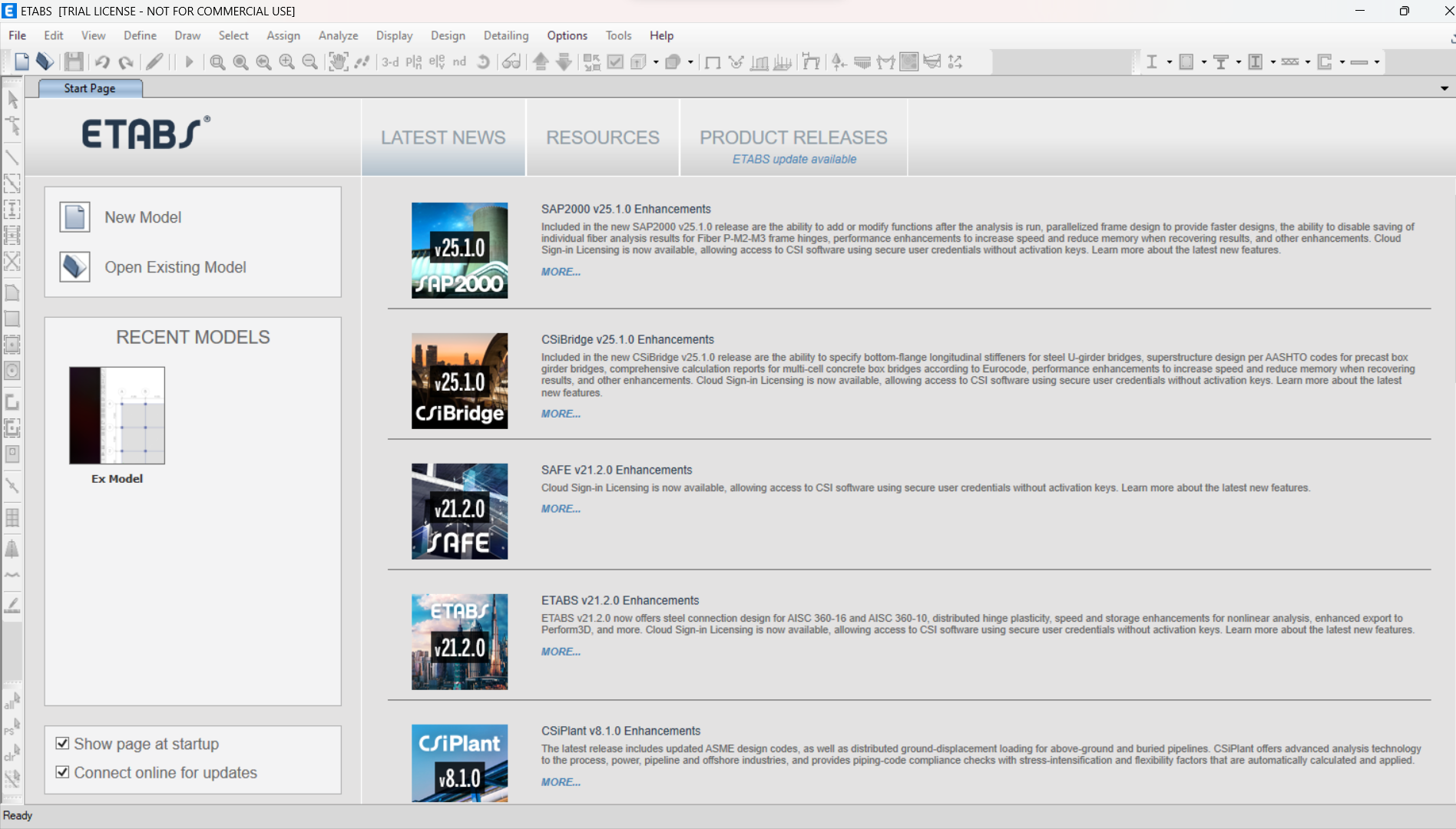
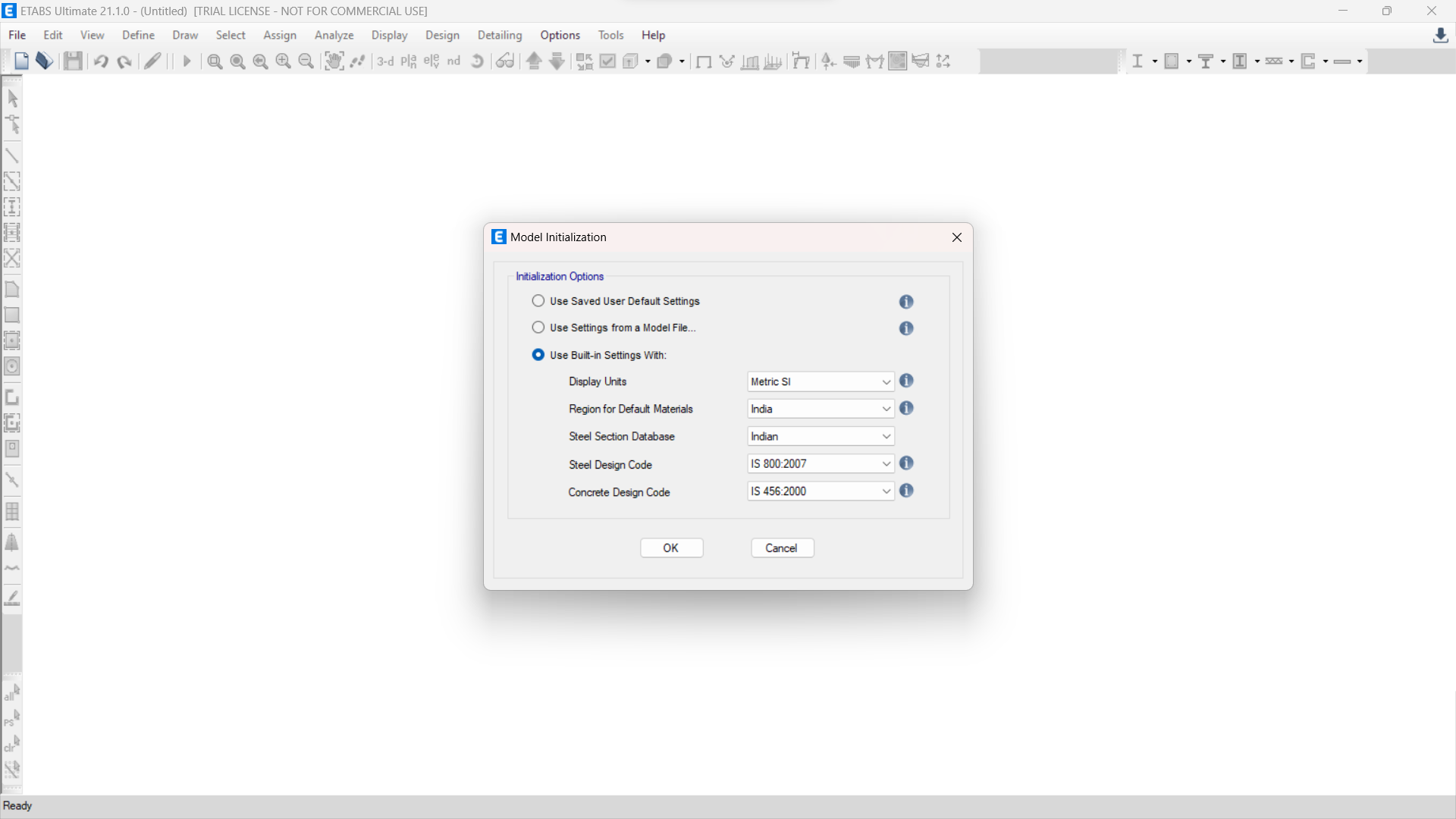
Step 2
- After selecting the default settings, a dialog box will appear containing the contents of the "New Model Quick Template"
- Select the Custom Grid Spacing option and set the X grid data to A-0, B-4, C-8, D-12, E-16
- Also change the Y grid data to 1-0, 2-4, 3-8, 4-12 as shown in the image below.
- Now click on Ok and Select the custom story data option
- Edit the Custom story data as per the number of stories
- Edit the first story as plinth level and give height as 1.5m
- Add another 25 stories with a height of 3m
- Phase 1 is labeled as the main story, all other stories above are labeled similar to the image below
- When all 25 stories have been added and edited, click OK
- In addition to the project shown below, another 25 floors have been completed
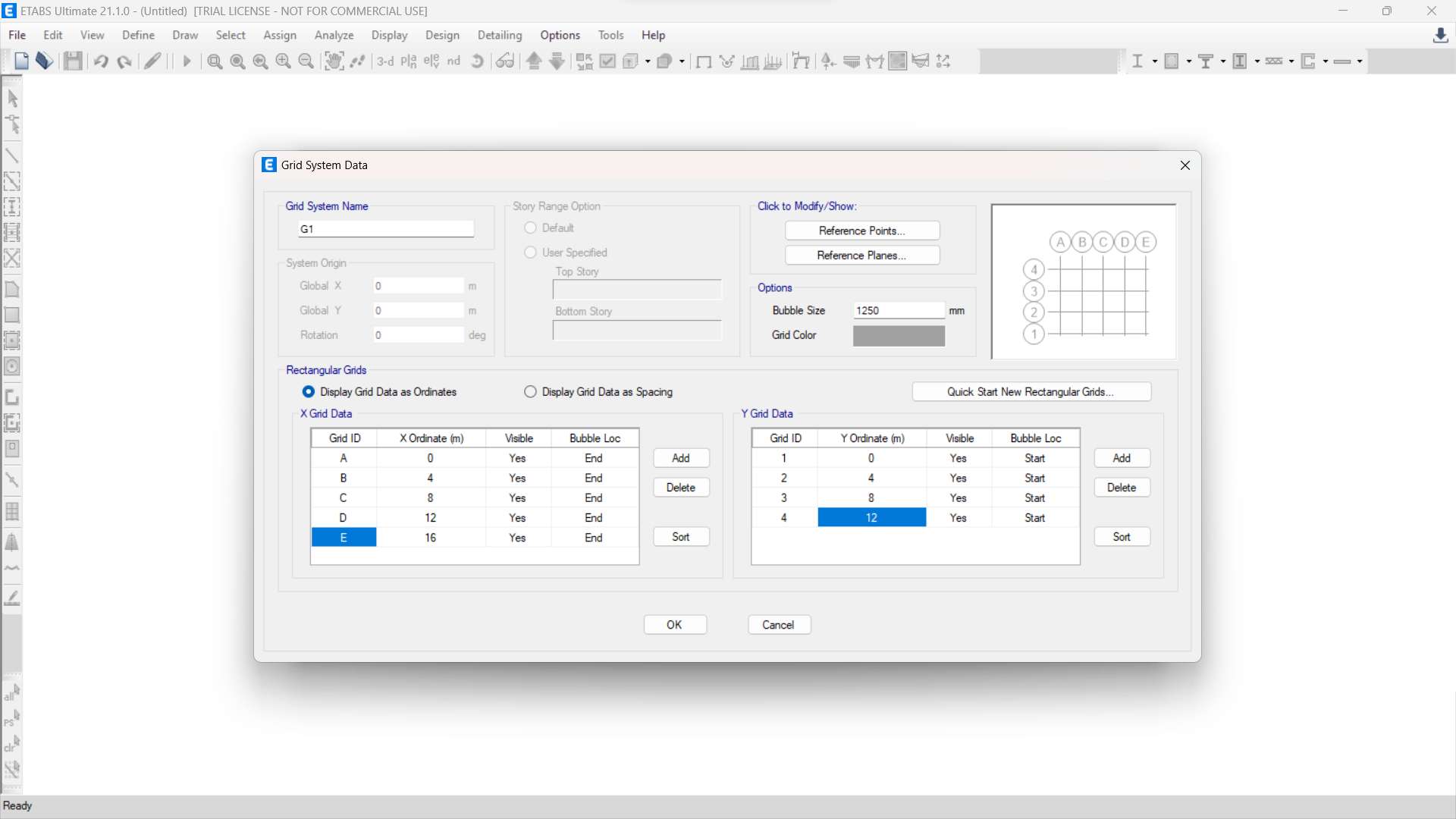
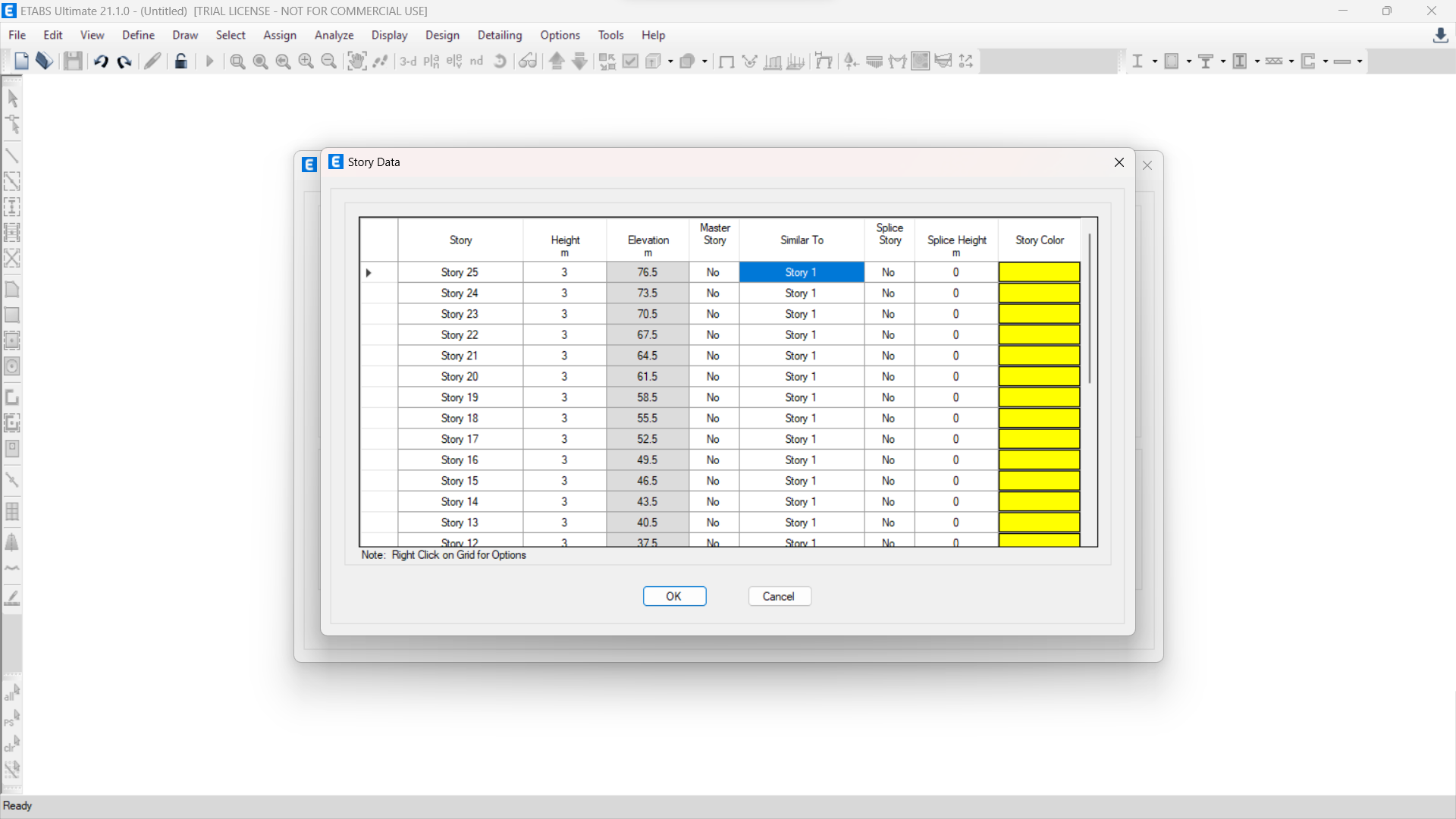
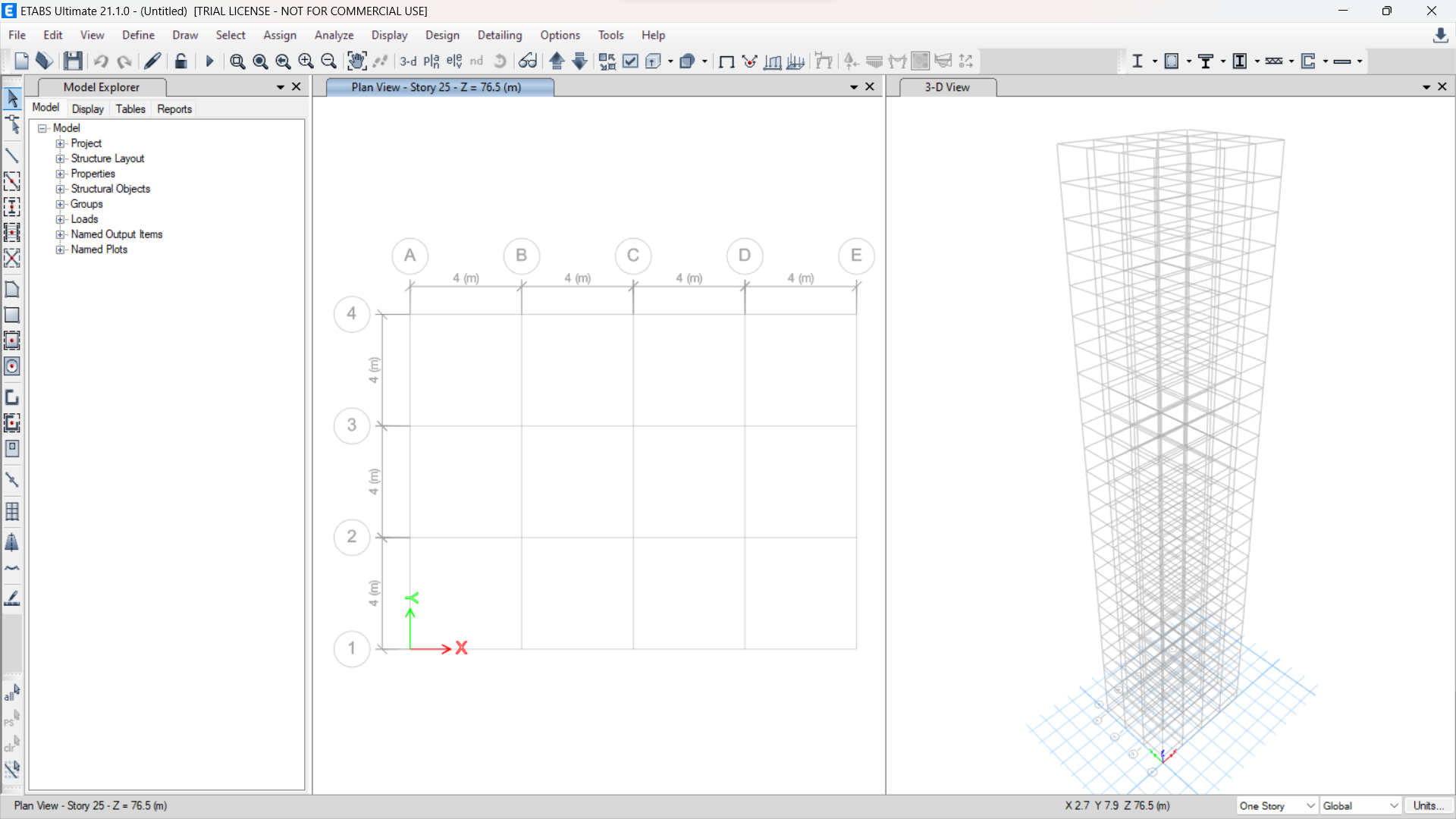
Step 3
- Go to the description tab and select the property option
- Click Add Material
- Add new concrete material, select "Country" as "India", "Material" as "Concrete", "Standard" as "India" and "Class" as "M30"
- Click OK after selecting all options
- Also add the steel material, select "Country" as "India", "Product" as "Rebar", "Standard" as "India" and "Grade" as HYSD Grade 415
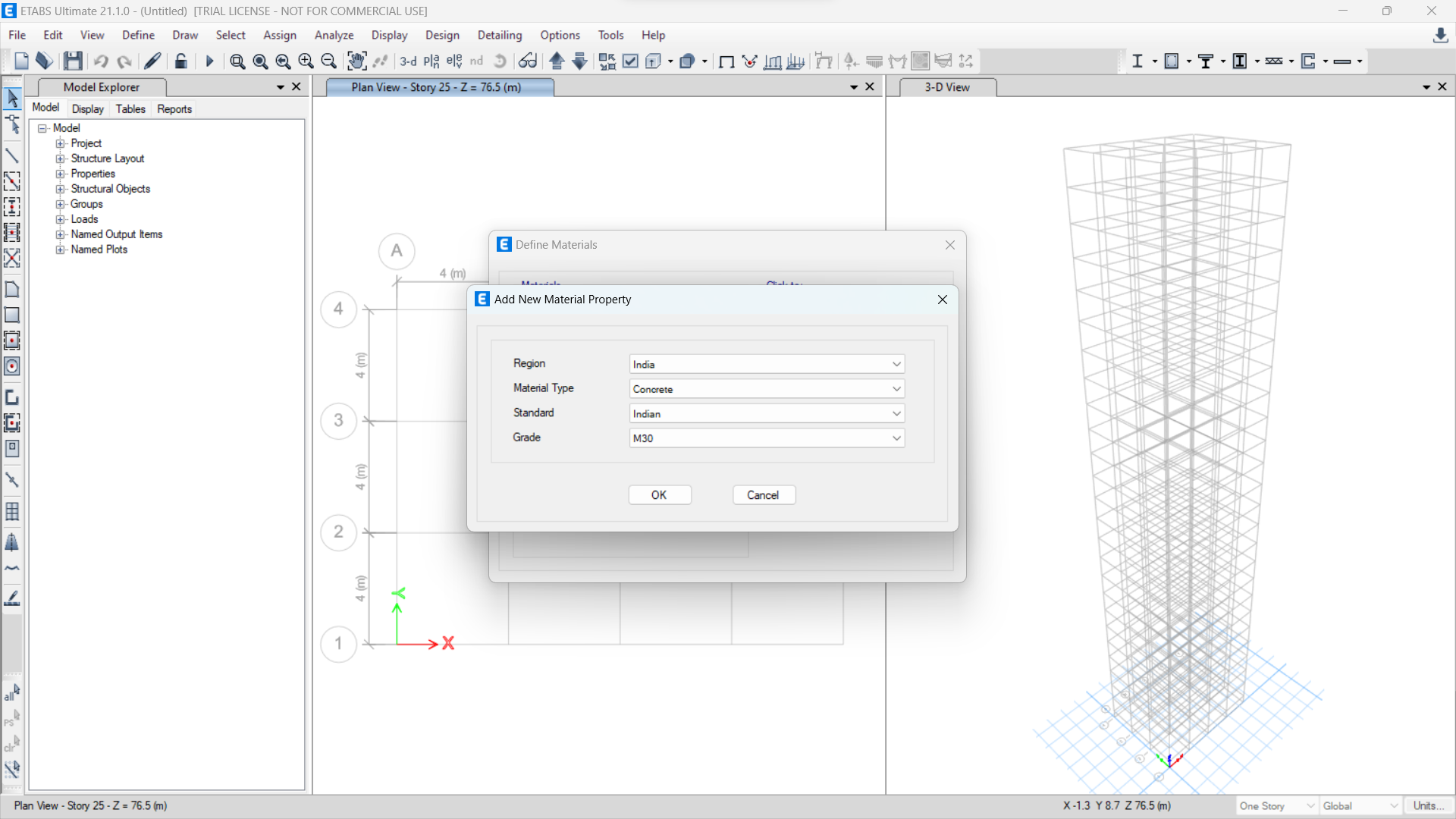
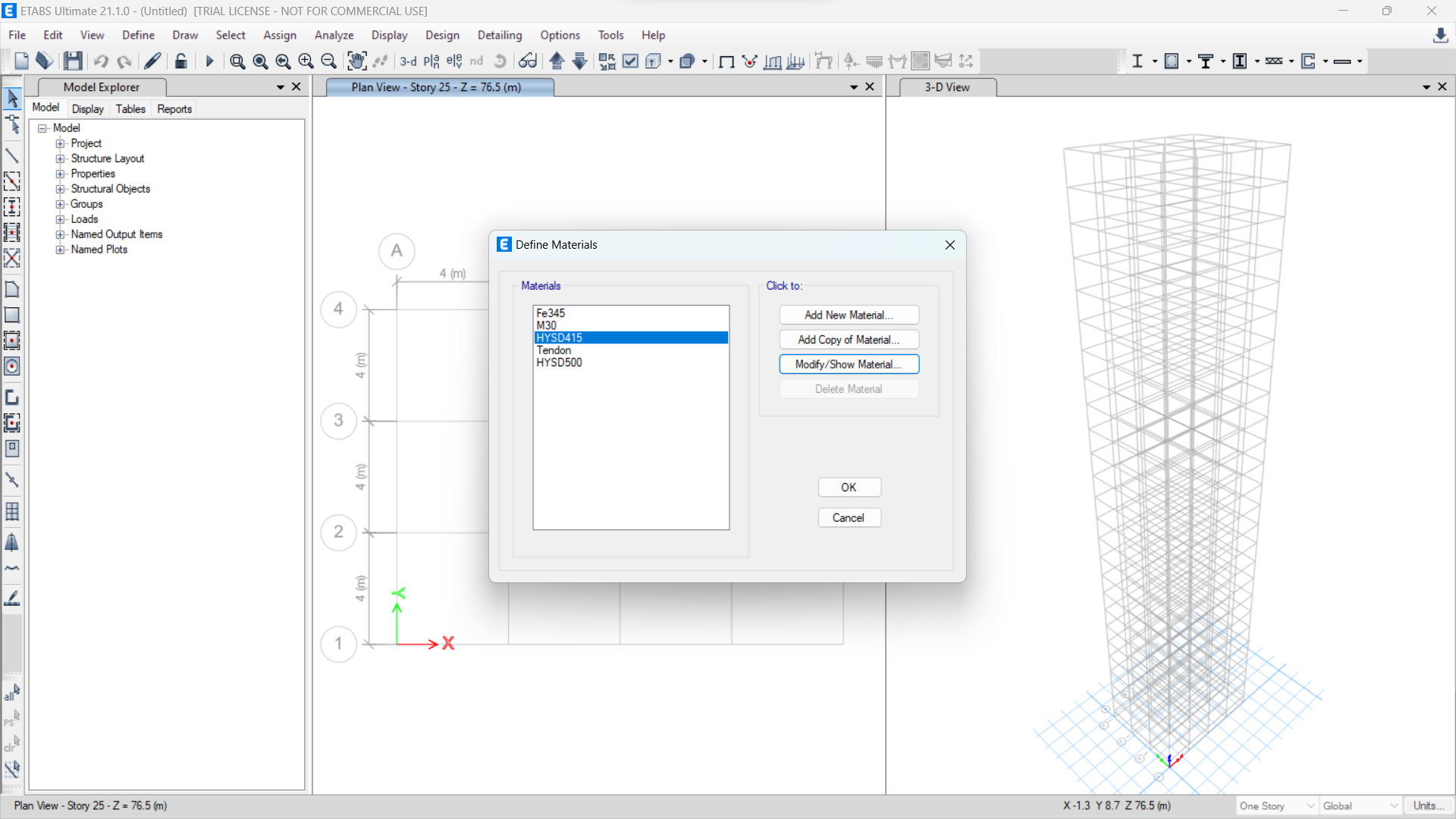
Step 4
- Now we need to define the rest of the beams and columns
- Go to the specified tab and select the Edge Material After Frame section
- Click on add new material
- Then select the section shape as Concrete Rectangular and Shape type as shown in the figure below
- After clicking ok, a new dialog box will appear as frame section property data
- Select the property name as B300x400, Material as M30
- Take the section length with width 400 mm and depth 300 mm
- Then click on "Change/Show Rebar" and a new box will appear containing the content of "Frame Section Properties Reinforcement Data".
- Select only M3 design (beam) as the design type and select HYSD 415. Steel as material as shown in the figure below
- Likewise, we must add a new system.
- Click Add Item
- Then select the section shape as Concrete Rectangular and Shape type as shown in the figure below
- After clicking ok, a new dialog box will appear as frame section property data
- Select the property name as C800x800, Material as M30
- Give the section dimensions of width 800mm and depth 800mm
- Then click on modify/show rebar option, and a new dialog box will appear as Frame section property reinforcement data
- Select the design type according to P-M2-M3 design (column) and steel material according to HYSD 415 as shown in the picture below
- Click OK after providing all the information
- Then the Beam and Column equipment is completed.
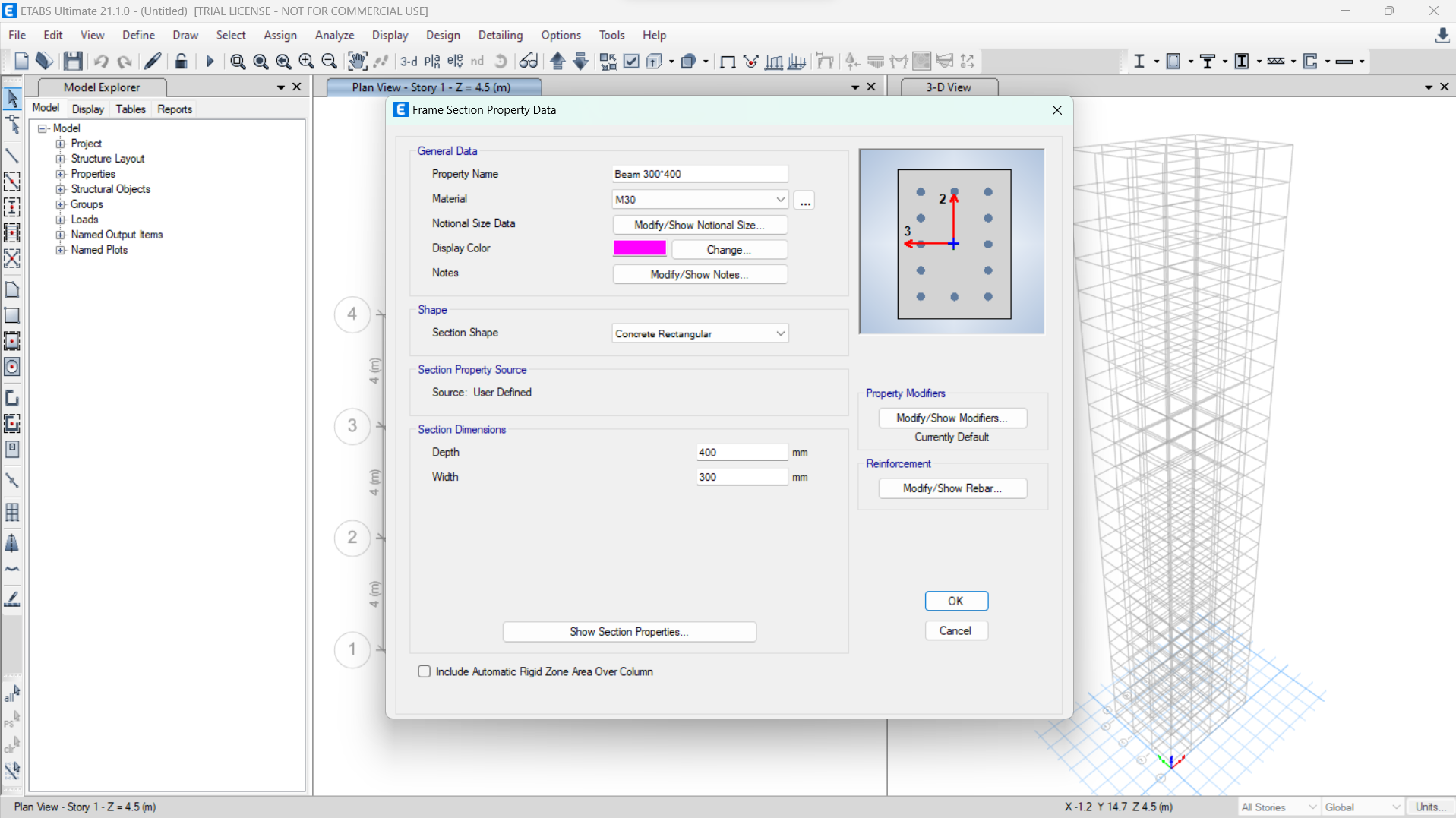
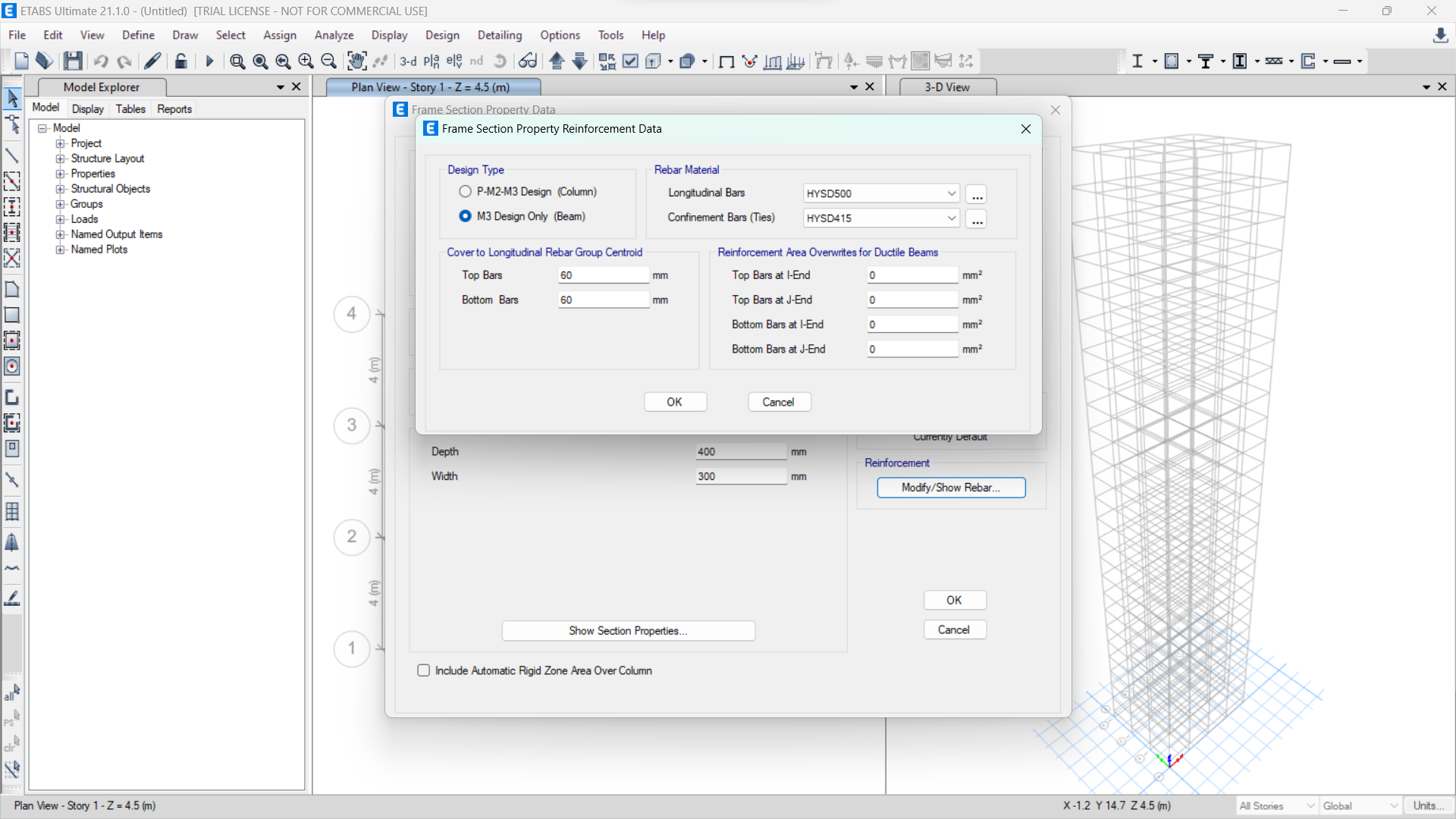
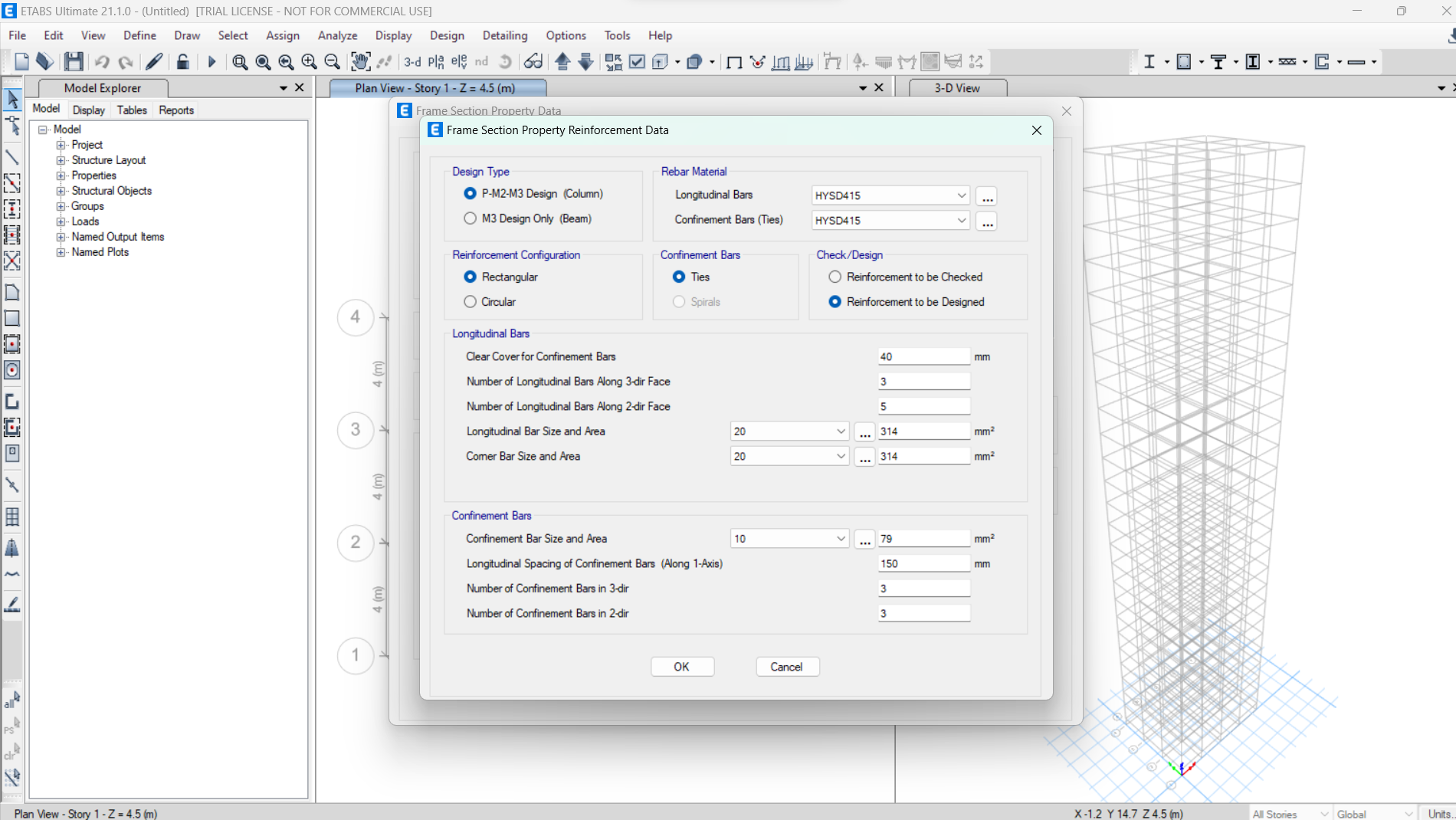
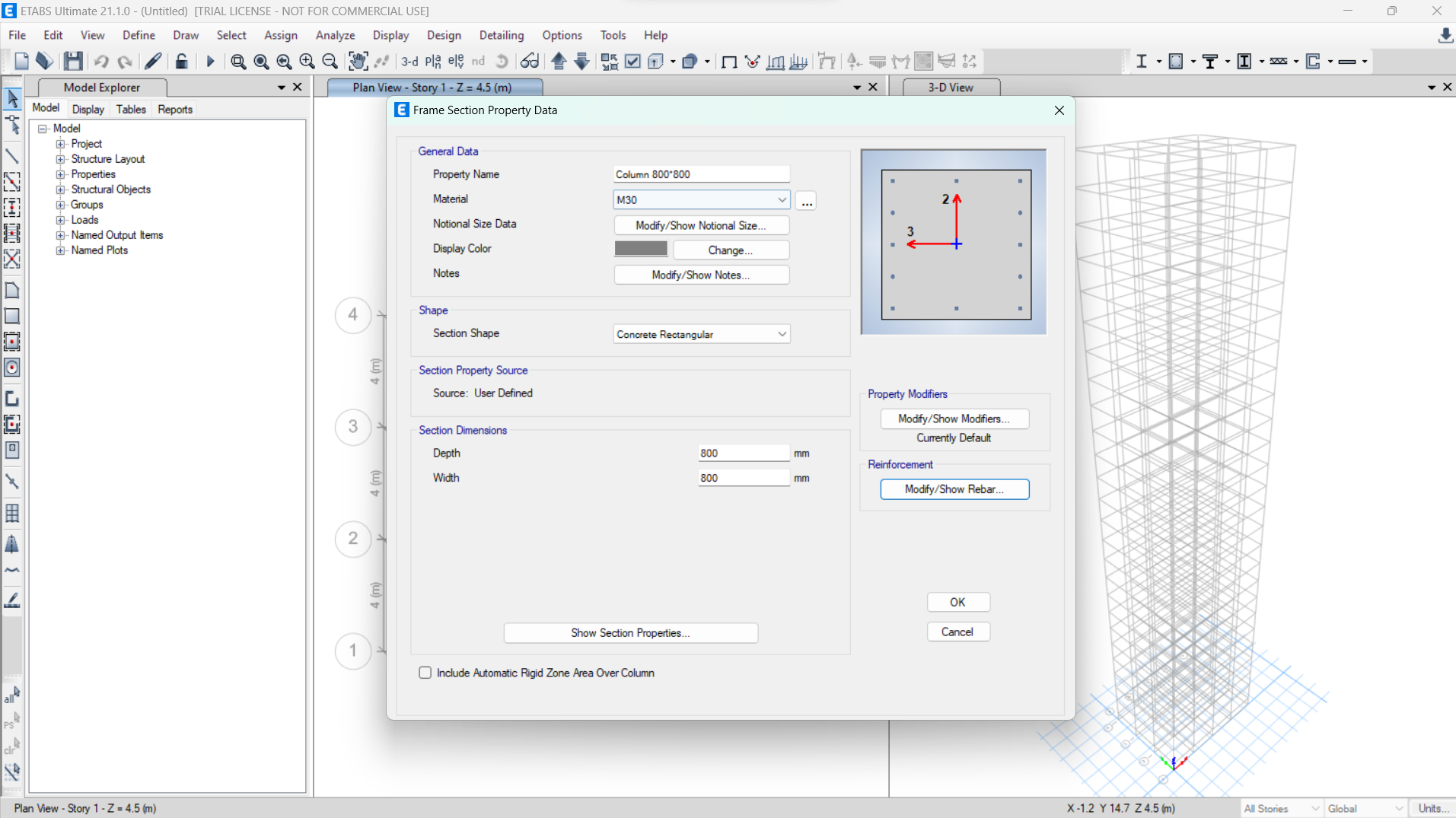
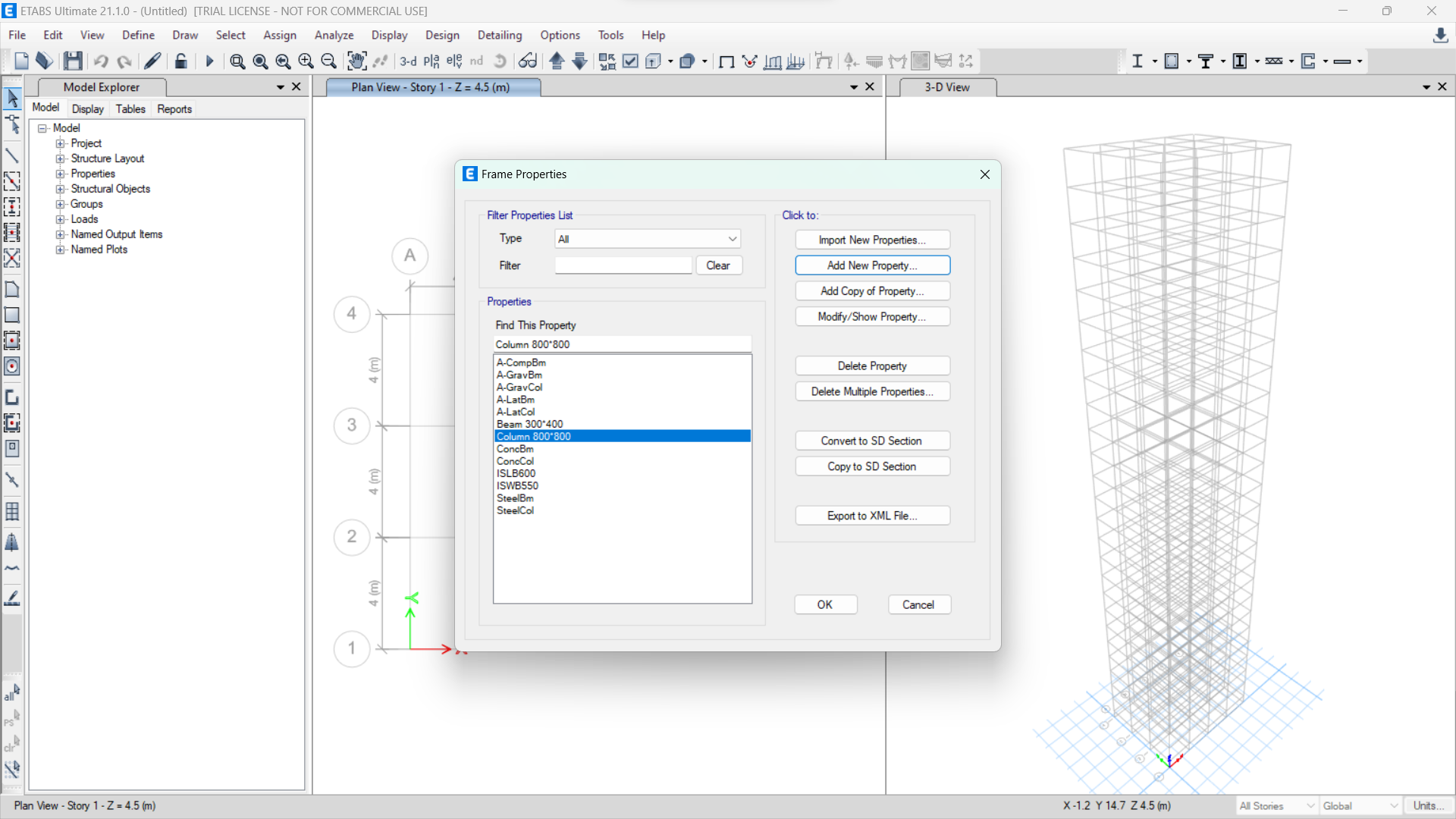
Step 5
- Now we have to define the slab property
- Go to the defined tab, select the section properties, and then select slab sections
- Select Add new property
- Give the property name as slab150 and slab material as m30
- Select the modifying type as membrane
- Then select the property data of type as slab and give thickness as 150mm as shown in the figure below
- After giving all the data, click on press ok
- The slab material has been successfully added
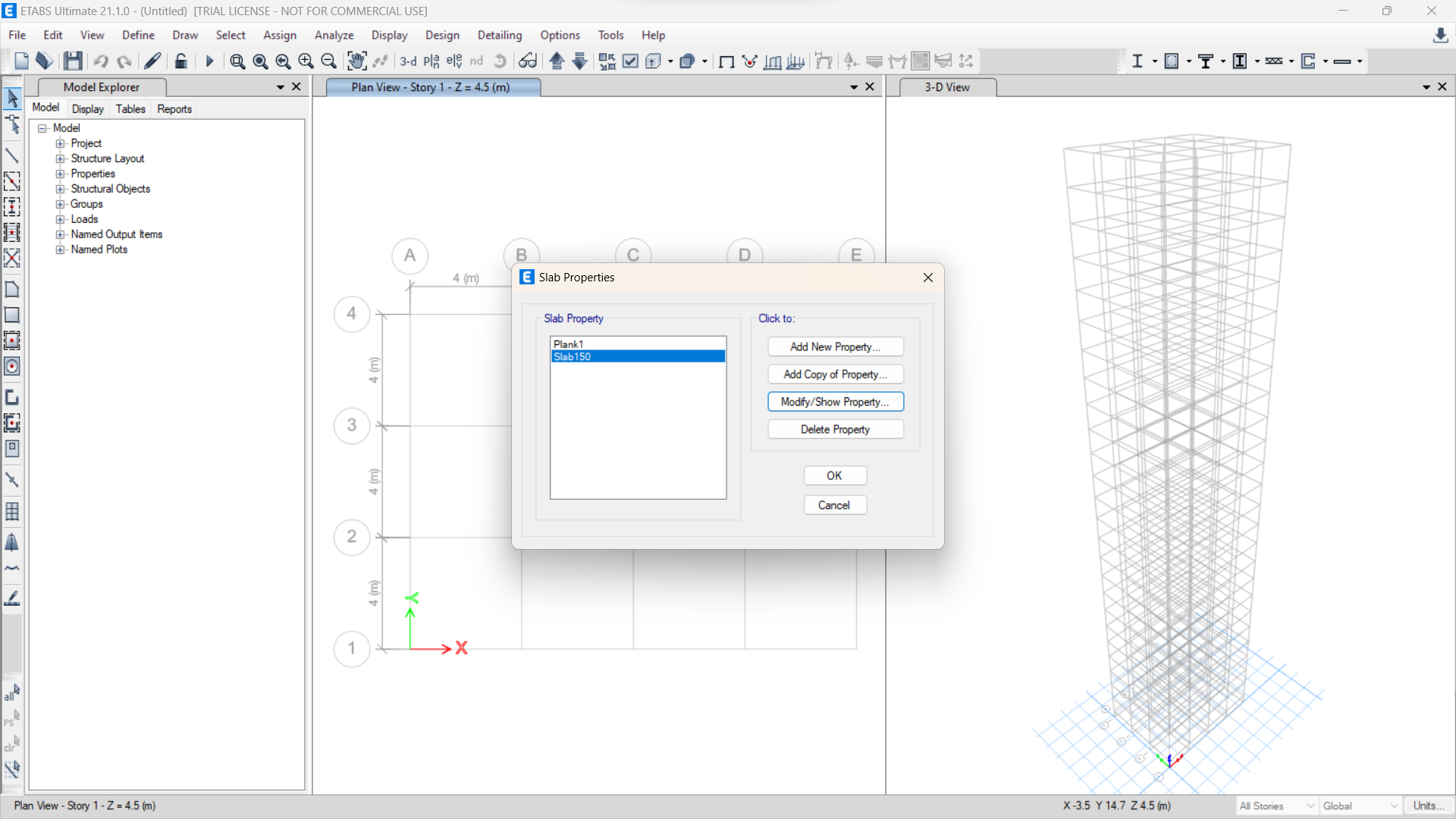
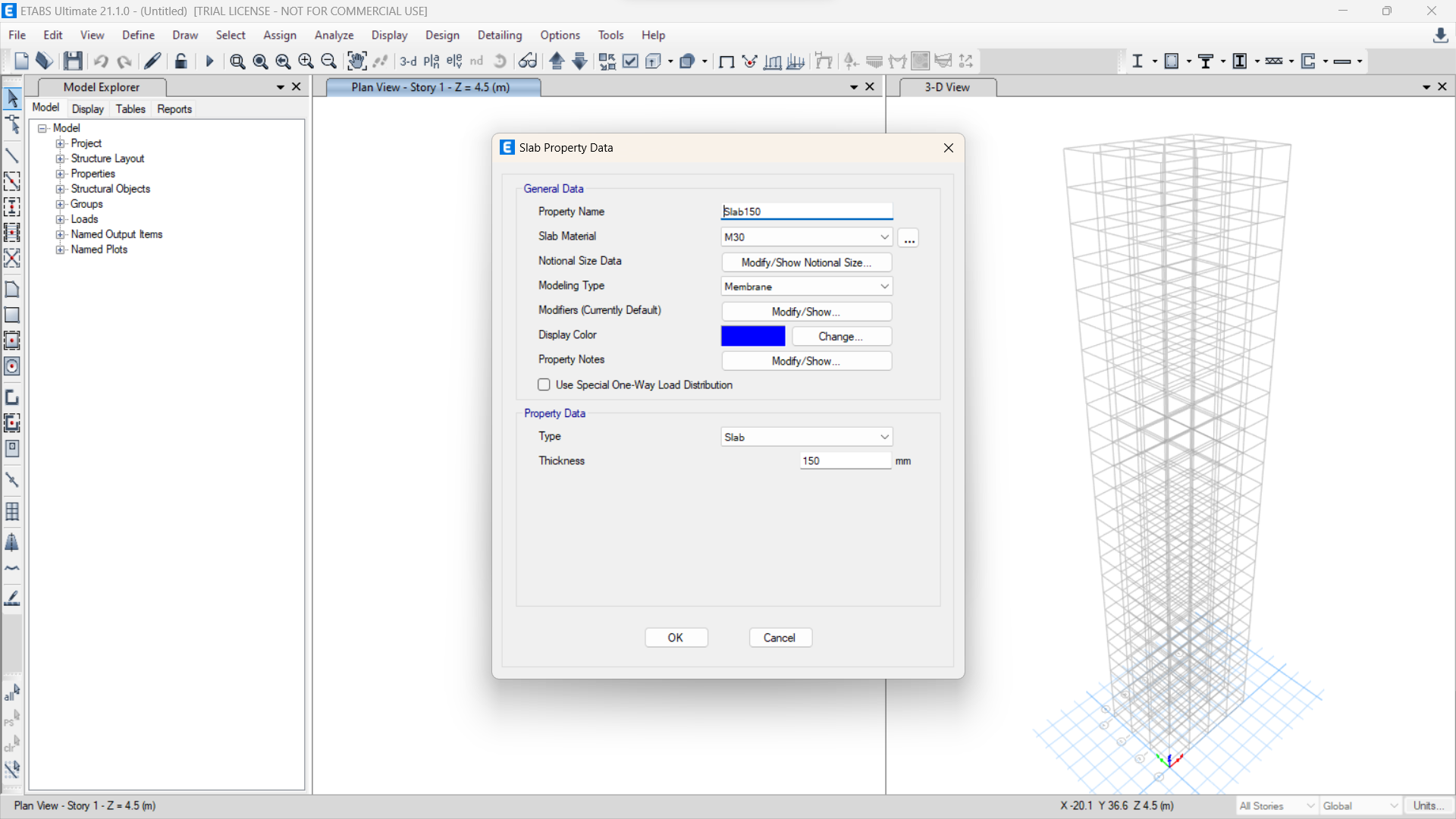
Step 6
- Now we have to define various load patterns and load combinations
- Go to the said tab and select the Installation mode option.
- There is a dead load and live load preset, now we need to add other loads
- Select the name of the load wall, super dead type and click New Load.
- Similarly add EQX and EQY loads by selecting IS 1893:2016
- Earthquake type and automatic lateral loads. Select the EQX load and click Change settings
- Then select “X Direction” under Direction and Eccentricity
- In this case, the seismic zone coefficient is given as 0.16 and the location type is given as zone 2.
- Also select the EQY load and click Change Side Load
- Then in the Direction and Eccentricity
- Section, just select “Y Direction”. In this case, the seismic zone coefficient is given as 0.16 and the ground type is given as zone 2
- After adding all the payments, click OK
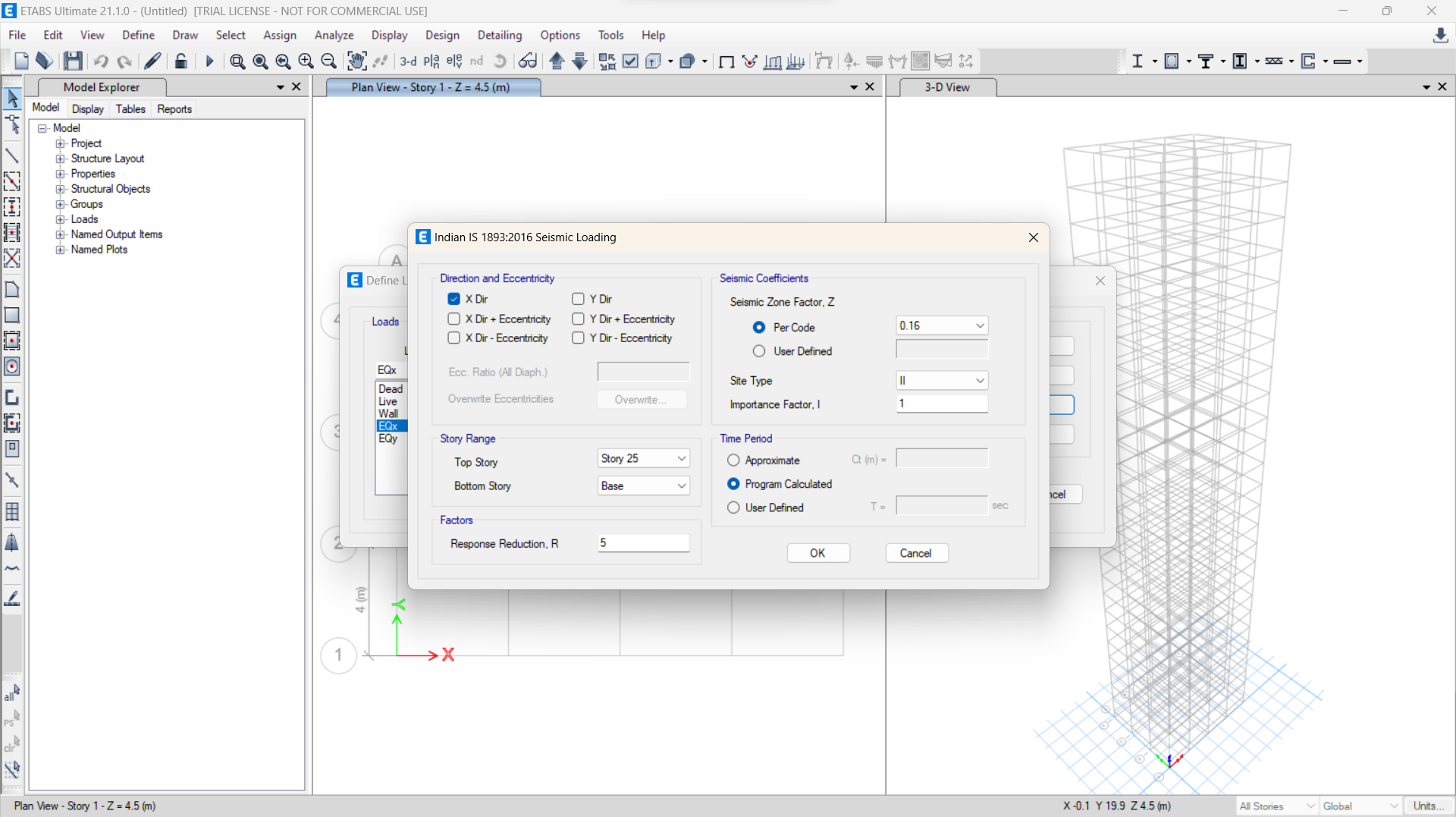
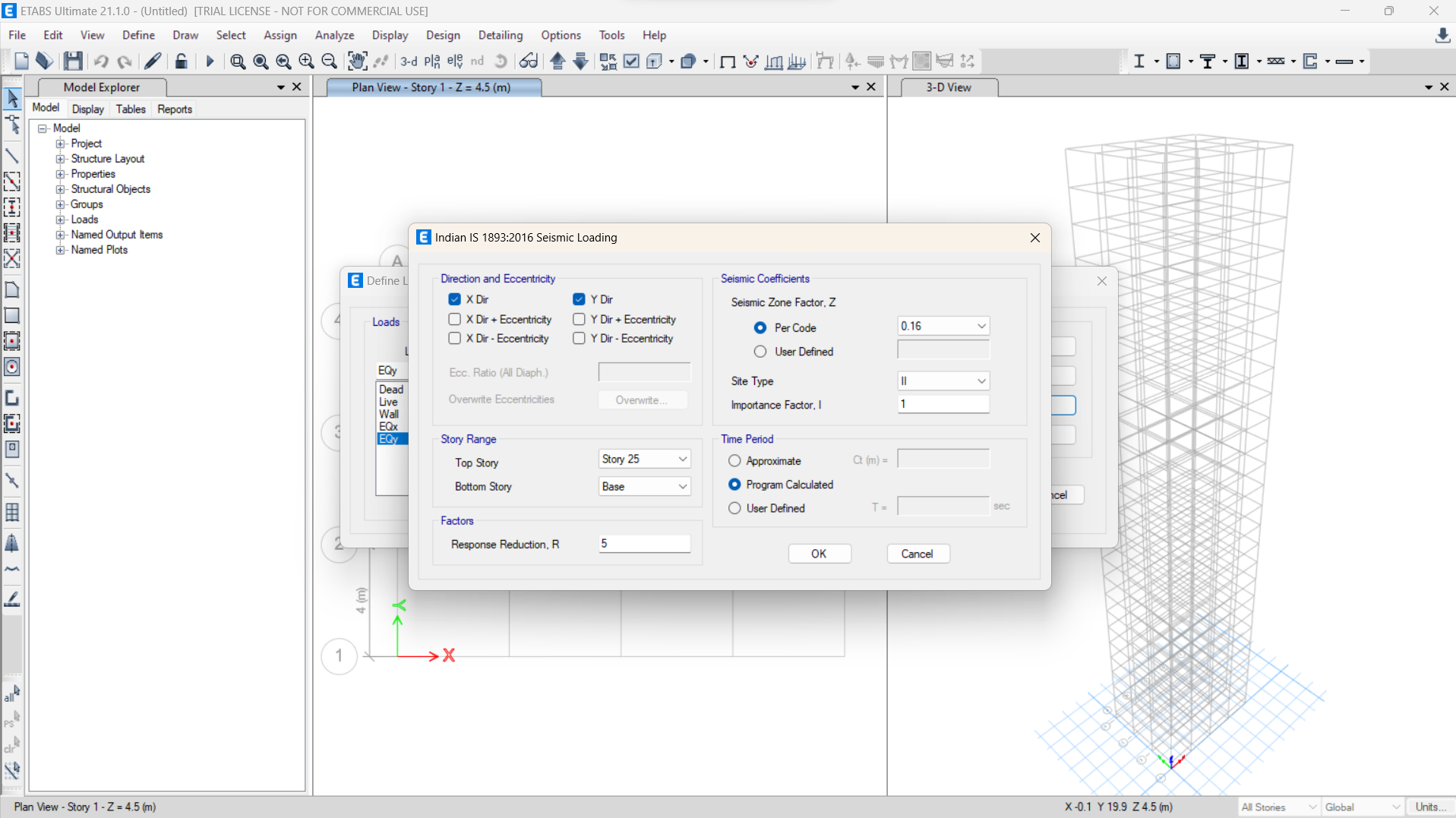
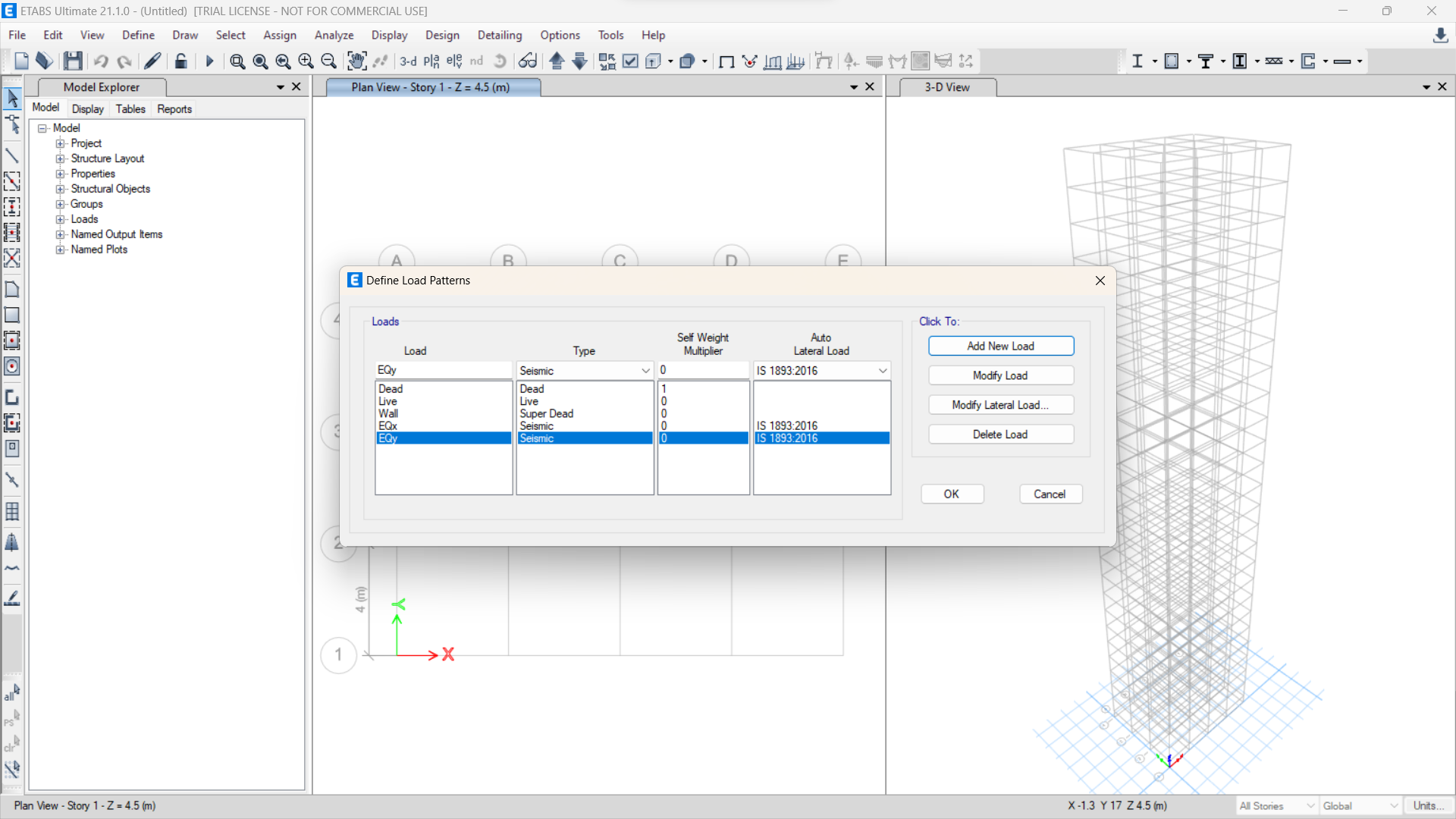
Step 7
- Go to the Define tab and select mass source
- Click 'Add property
- Select the size of the item based on the specified load type
- Add an equal number of load models by selecting Dead Load as 1, Live Load as 0.25, and Wall Load as 1
- Click OK after changing
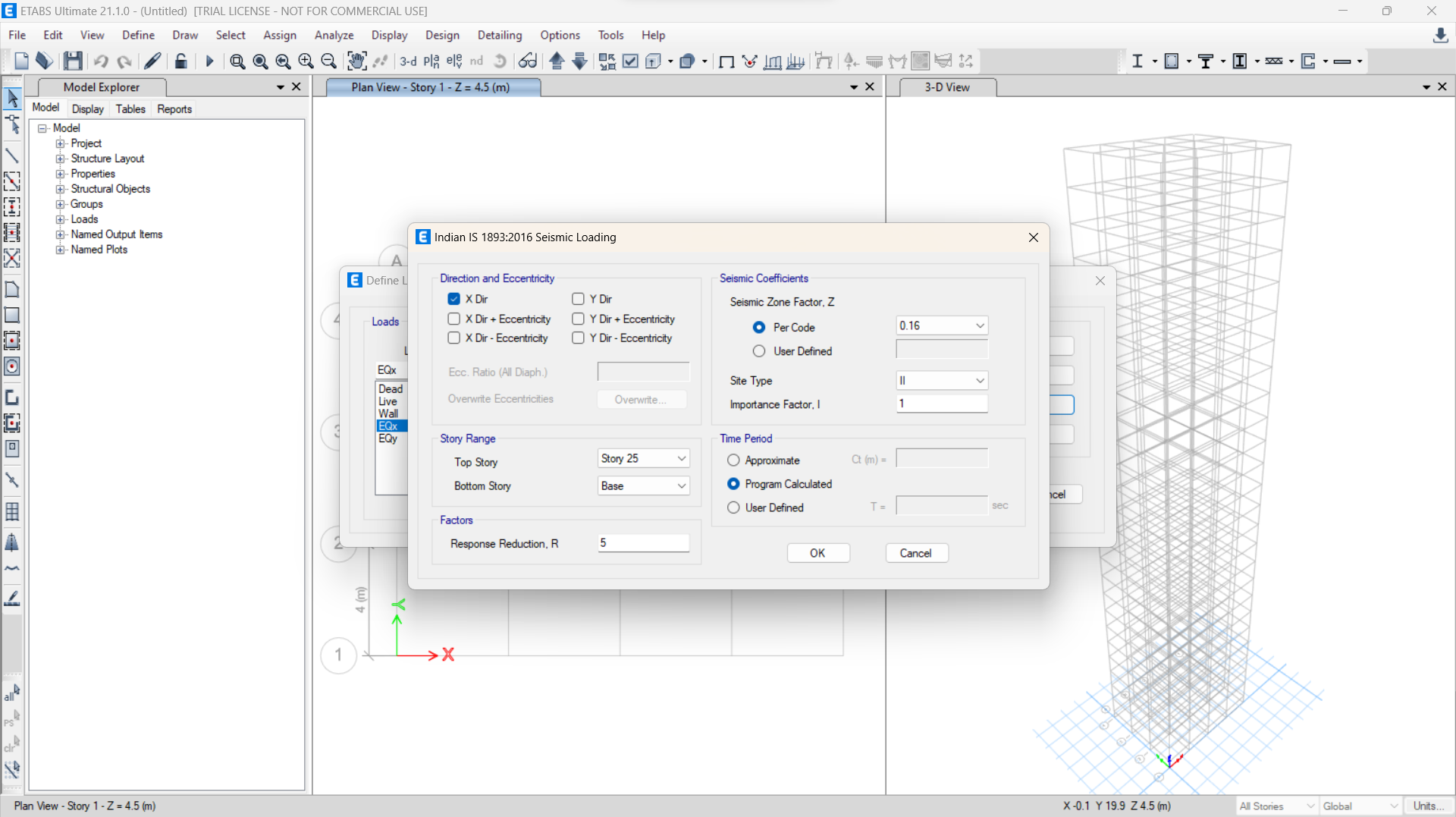
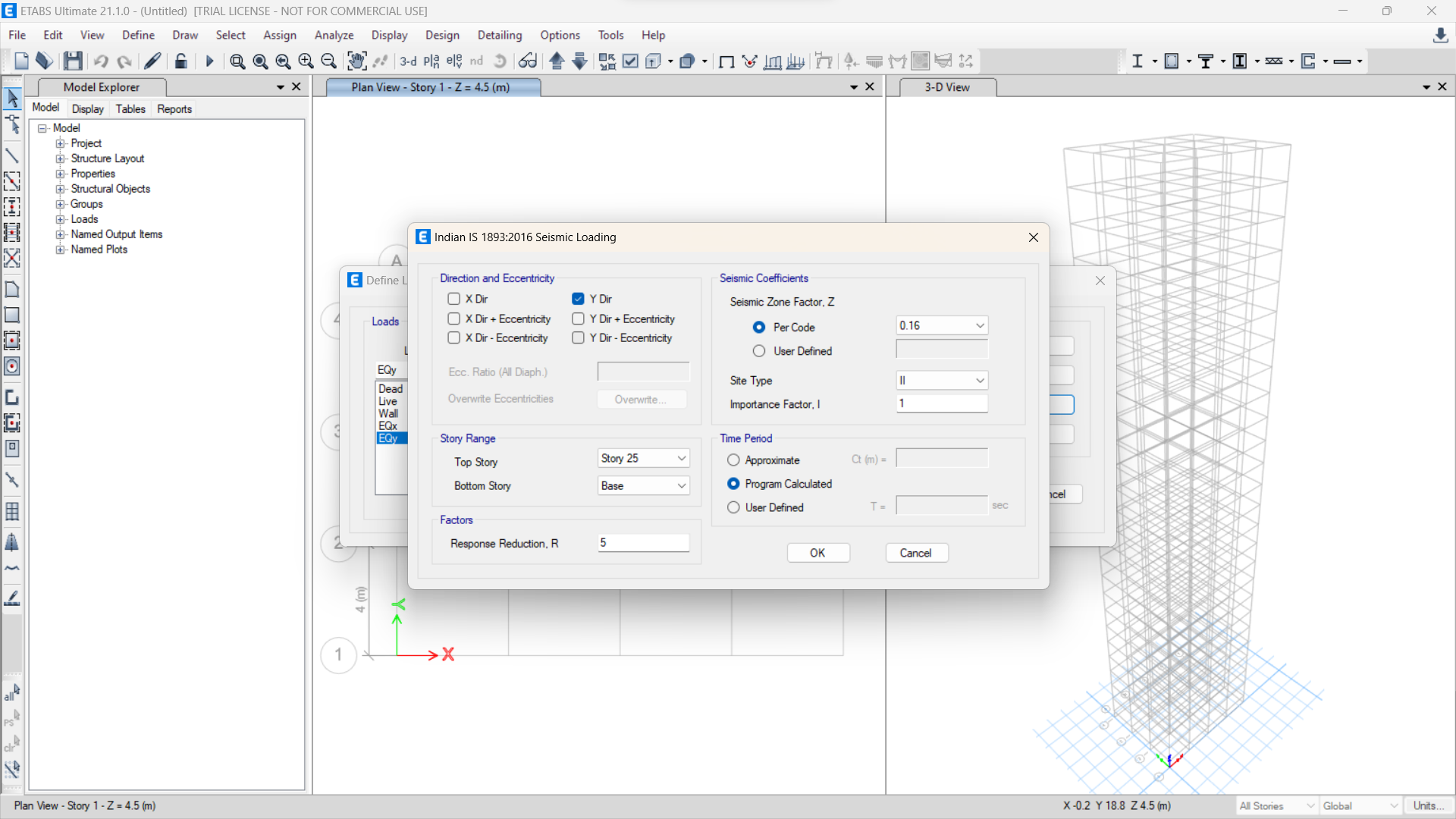
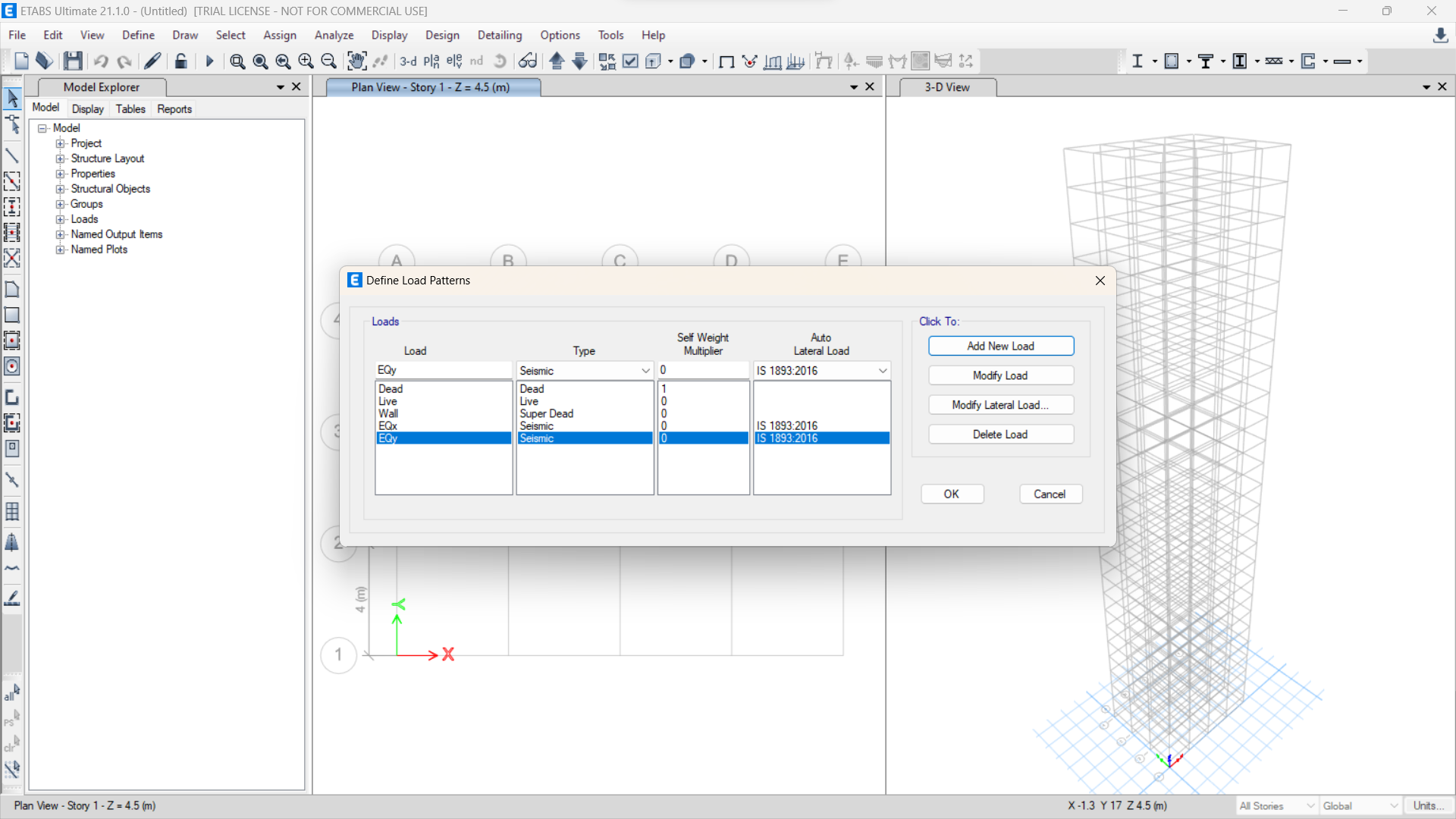
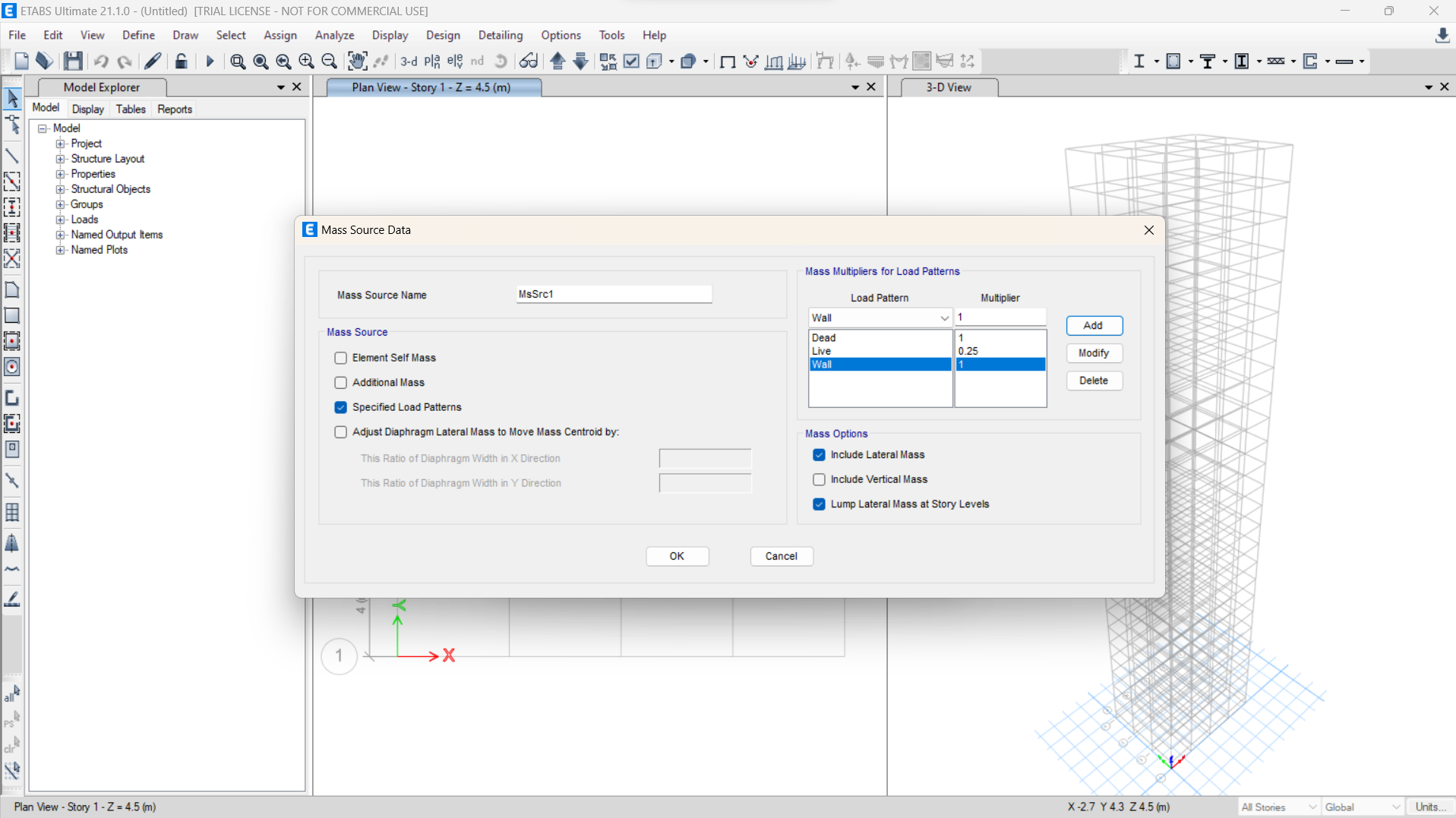
Step 8
- Go to the Definition tab and select Load Case
- Check if all loads are present
- Then click OK after checking all loads
- Then go to the mentioned tab again and select the co-install option
- Select additional option for pre-assembled design
- Choose the design of stone design combination
- Then turn on Switch to User Interface (editable) and click OK
- All connections completed successfully
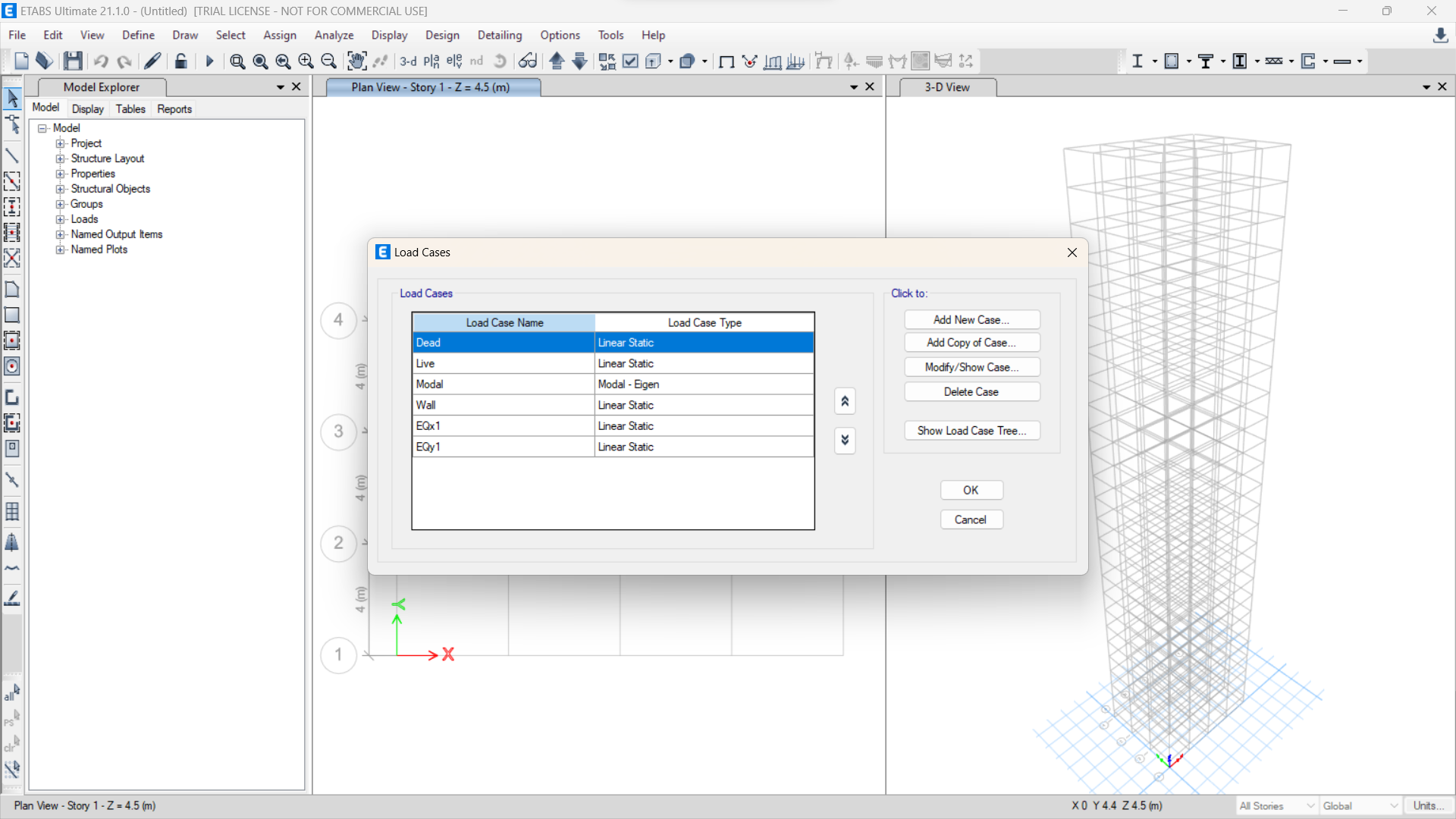
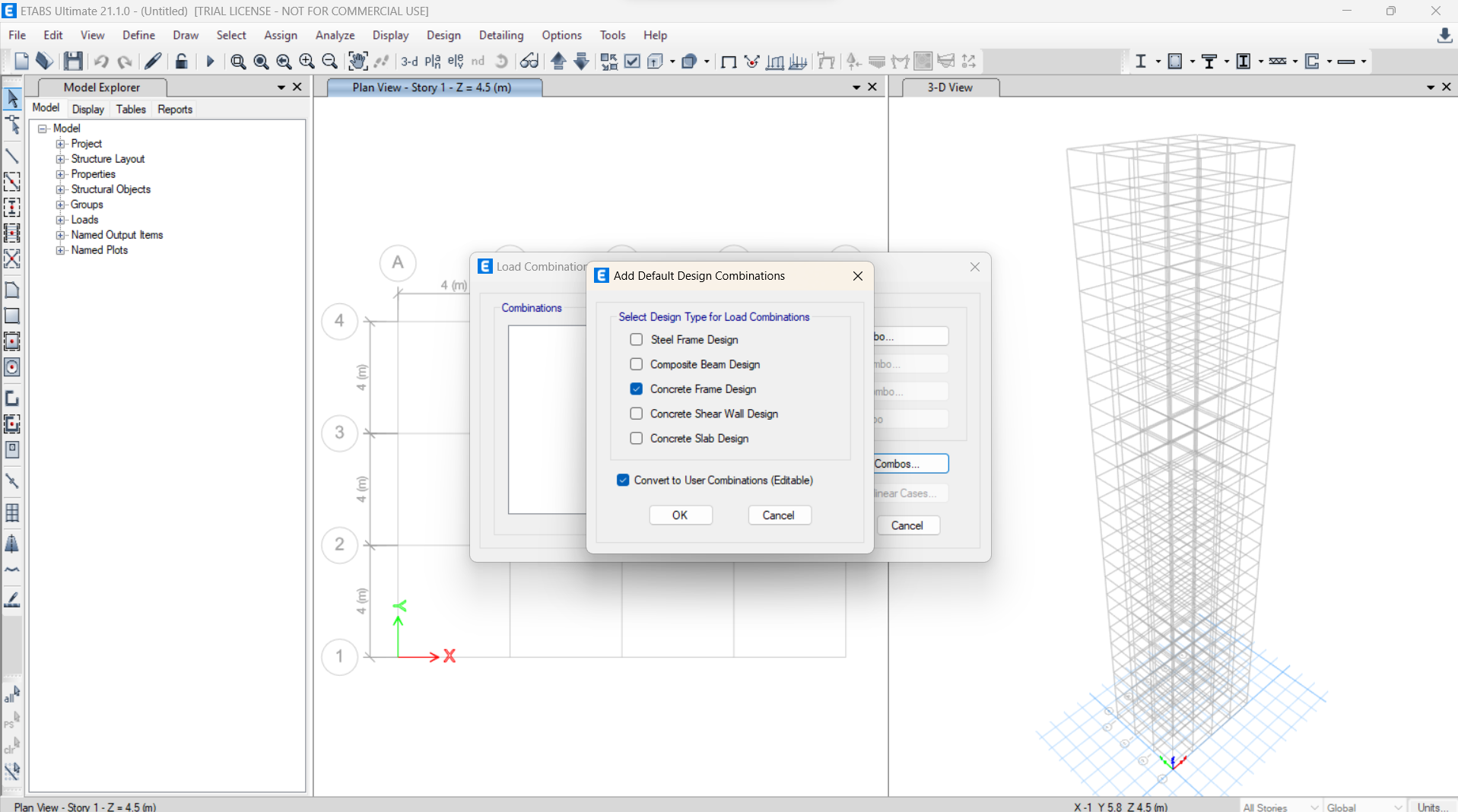
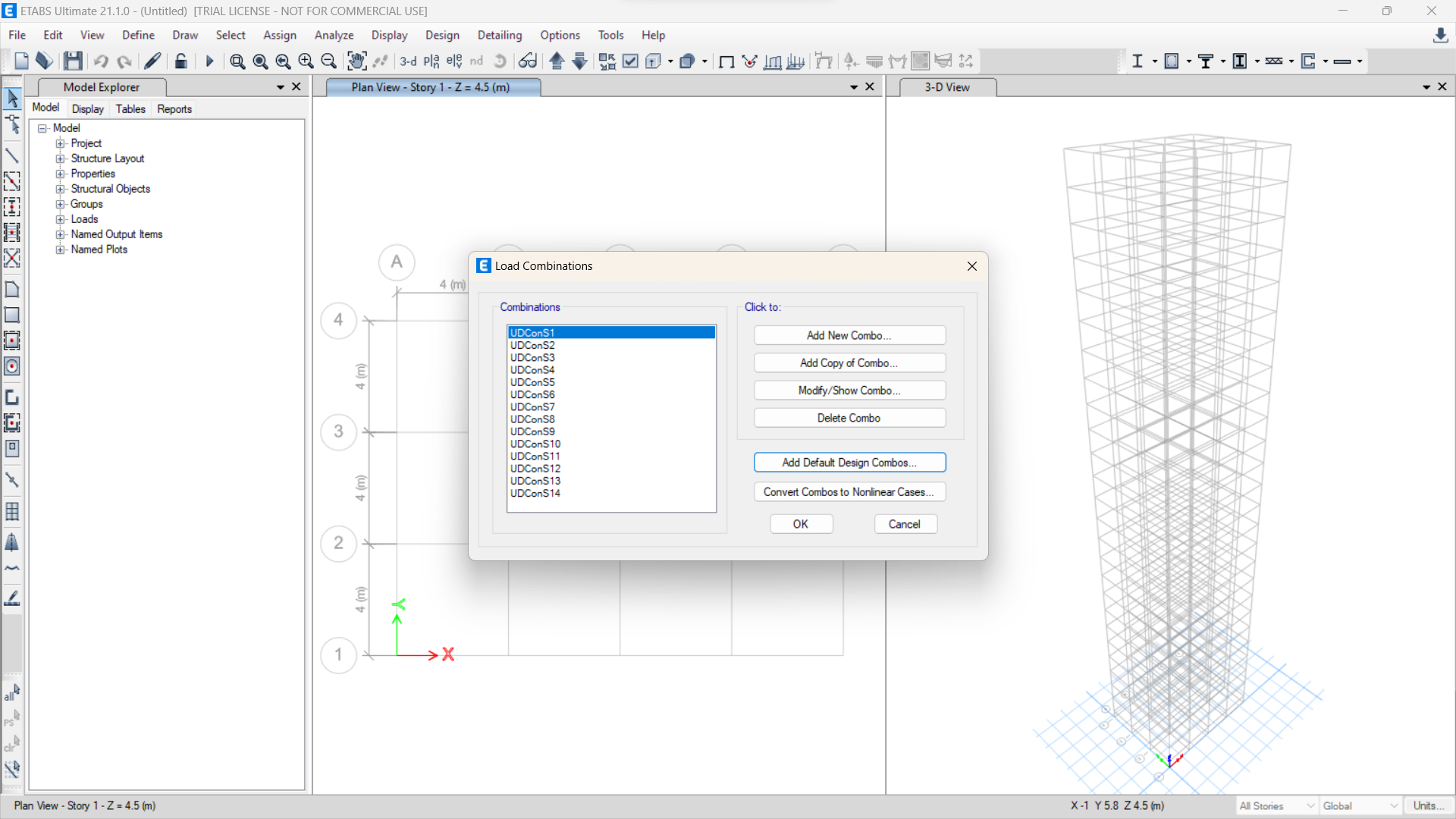
Step 9
- Now we need to model the column, beam and slab selection
- Select the Quickdrawdraw column in the toolbar
- Select the product's feature as C800x800 as shown below
- We must model every line of every story
- So select all story options on the right side of the screen
- As you select each grid, each row will be placed in that grid
- Also select all the lines we want to draw lines
- The columns are listed in the grid as shown in the image below
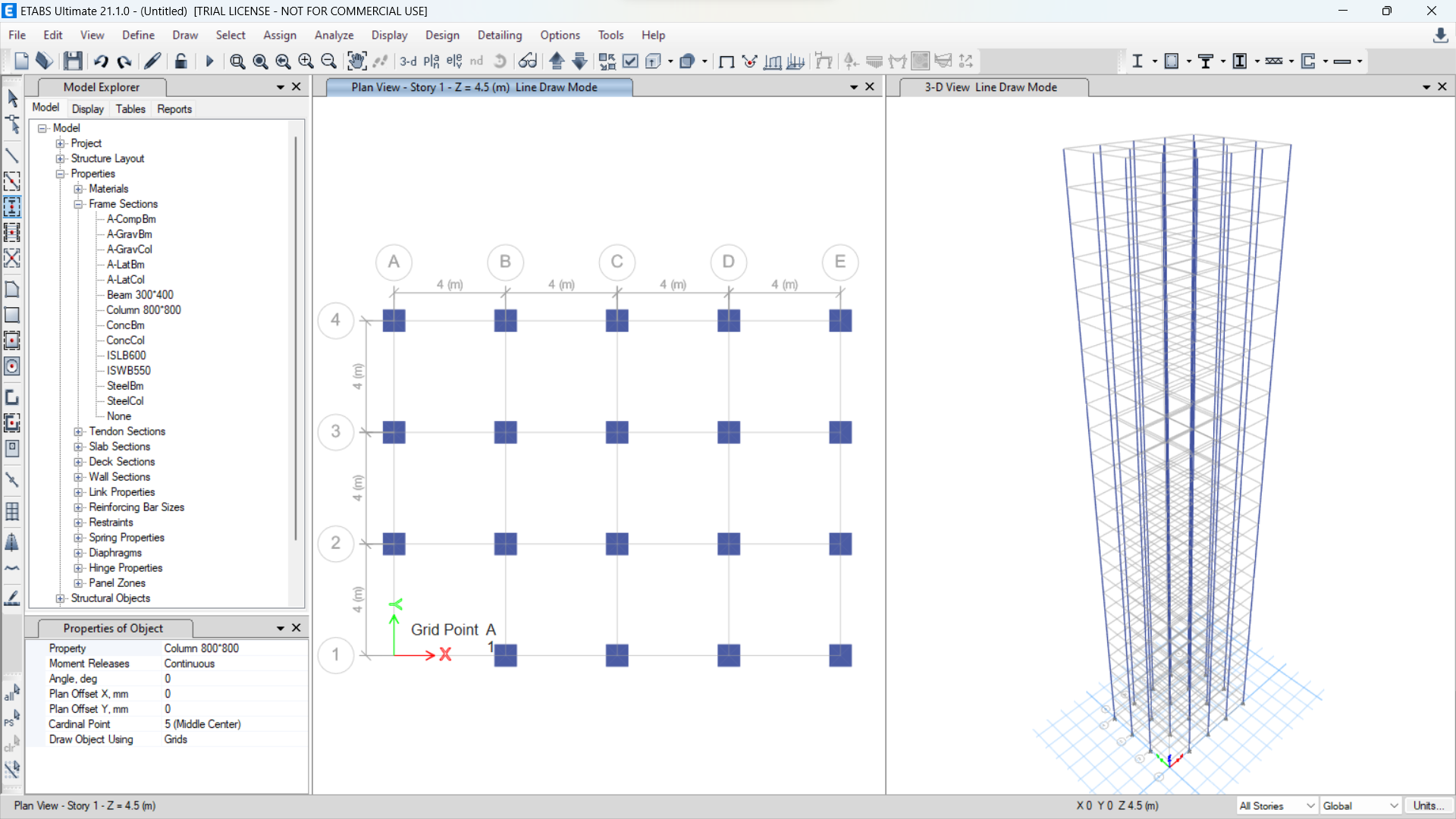
Step 10
- Now we need to model the beam
- Select Quickdrawdraw Beam
- From the toolbar. The specification of the selected item is B300x400
- Select the lines we want to draw lines
- Here we show the beams for the left column and the top column
- Now we need to print the same content in each column
- Go to the Edit tab and select Copy
- Select Y increment data as -4, number as 3 and press OK
- Select the Copy tool again and now set the Delta X data to 4 and the Count to 4
- Then click OK. All properties are listed in the row as shown in the figure below
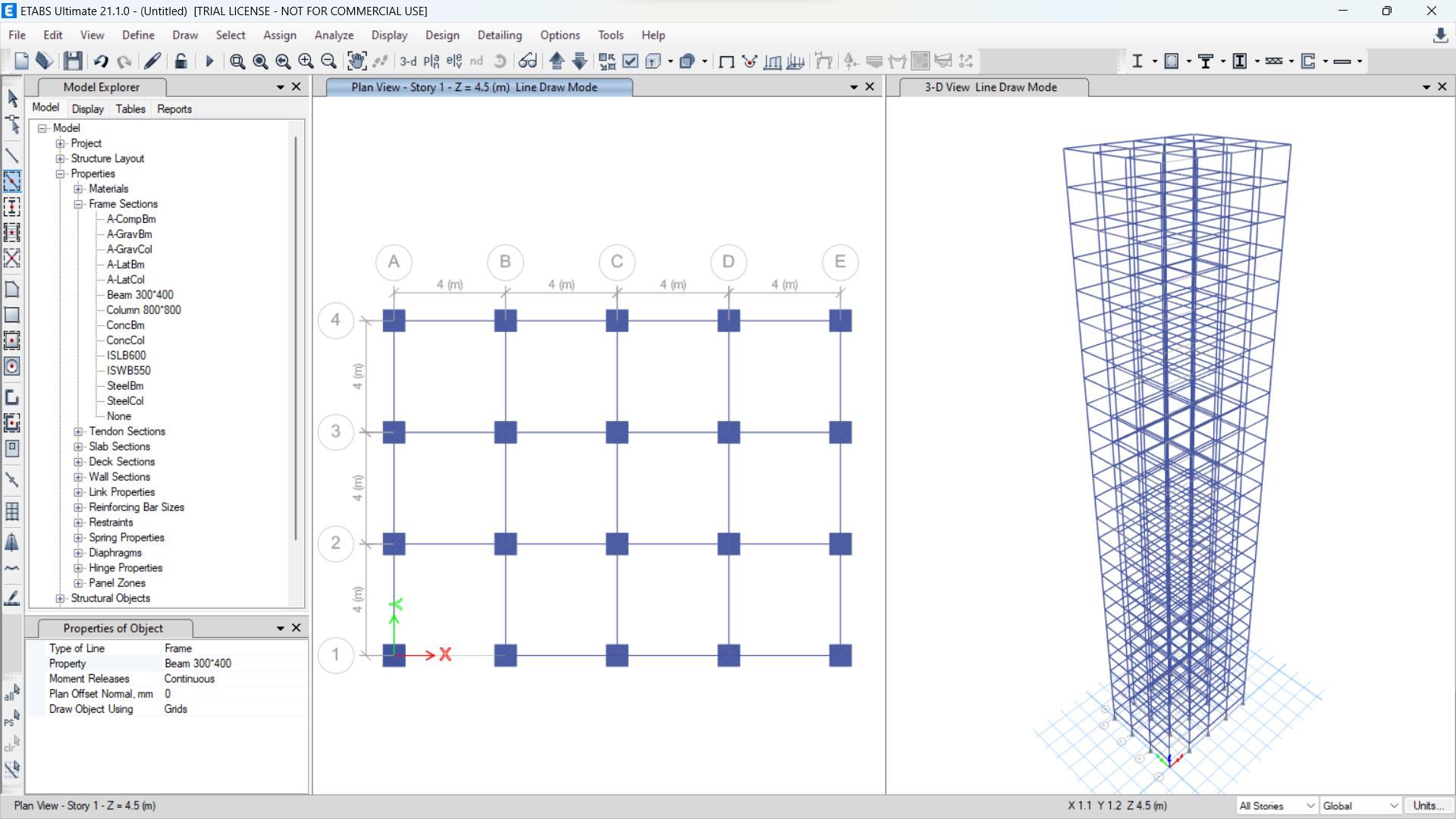
Step 11
- Now we need to model the slab between the plates
- But we need to model the slab above level
- Go to the menu and select the plan
- Select the 1st floor in the floor plan and click OK
- Replace the story in the corner of the screen with a similar story
- Now select the QuickdrawFloor/wall option from the toolbar
- The product of the selected product is Slab150
- Select the center of each grid to draw the board
- The board will automatically draw on each grid as shown below.
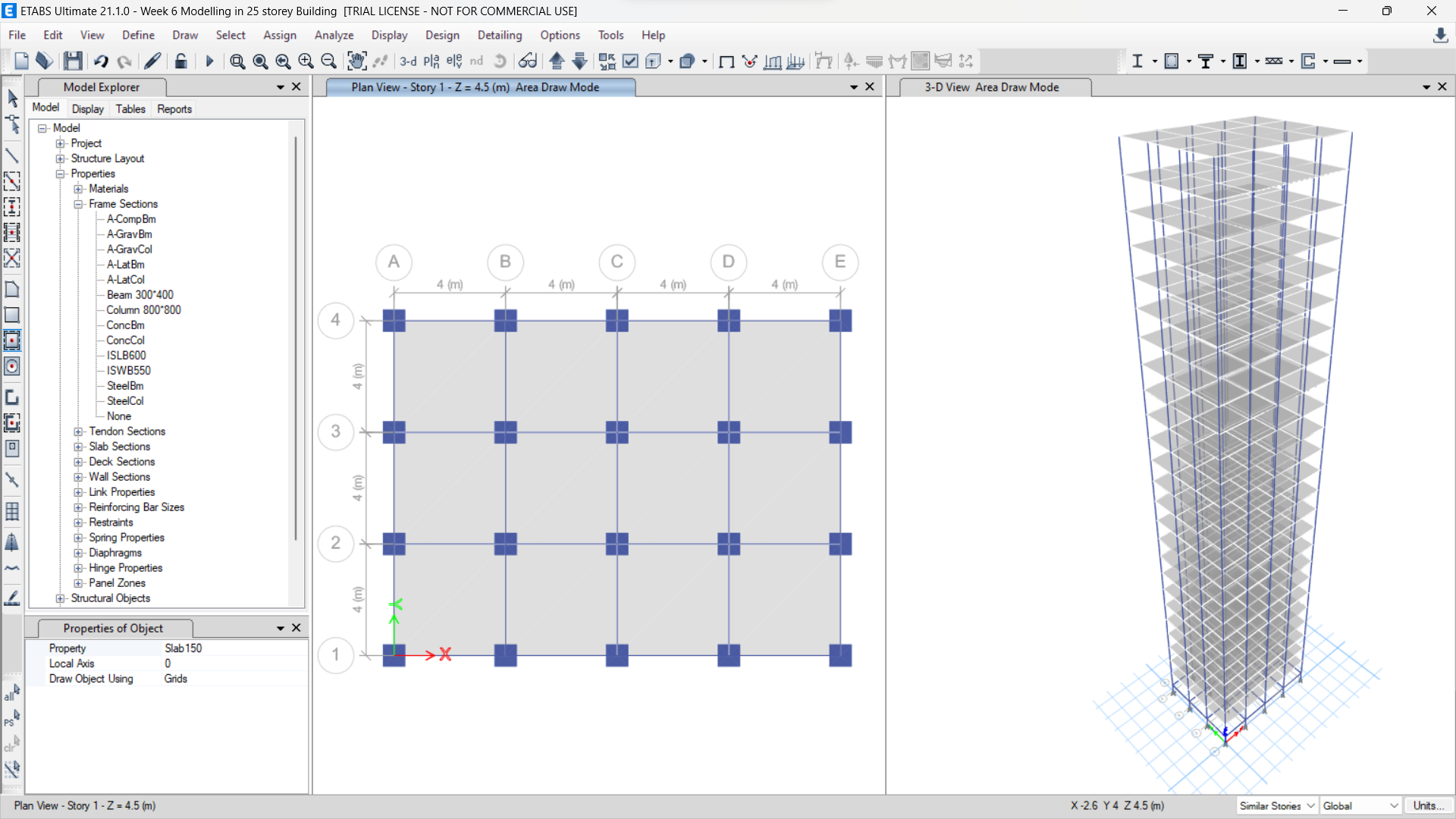
Step 12
- Go to the Options tab in the menu bar and select Properties
- Then select the option frame section
- When the frame is selected correctly a dialog box will appear
- Select Beam as B300x400 and click Select
- Then go to the distribution tab and select the frame payload and then the distribution.
- A new dialog box named "Framework Load Distribution - Distributed"
- Will open. Select the Load Pattern Name as Wall and set the Uniform Load value to 10 Kn/m
- Then click OK
- Then go to the Selection tab again and select Properties, then select Plate Section
- A new dialog box will open showing "Select from Card Properties"
- Select Slab150 and click select
- Then go to the Assigned Symbols tab and select Shell Loads, then Uniform
- A new dialog box will open showing Load Assignment for Shell - Uniform
- Select the Load Type name live and specify the load value as 3 Kn / m^2
- Then click OK
- Then go back to the settings tab and select "Shell" and then select the aperture
- A new forum will be opened called Shell - Diaphragms
- Select option D1 and click OK
- All loads and diaphragms are assigned to the model
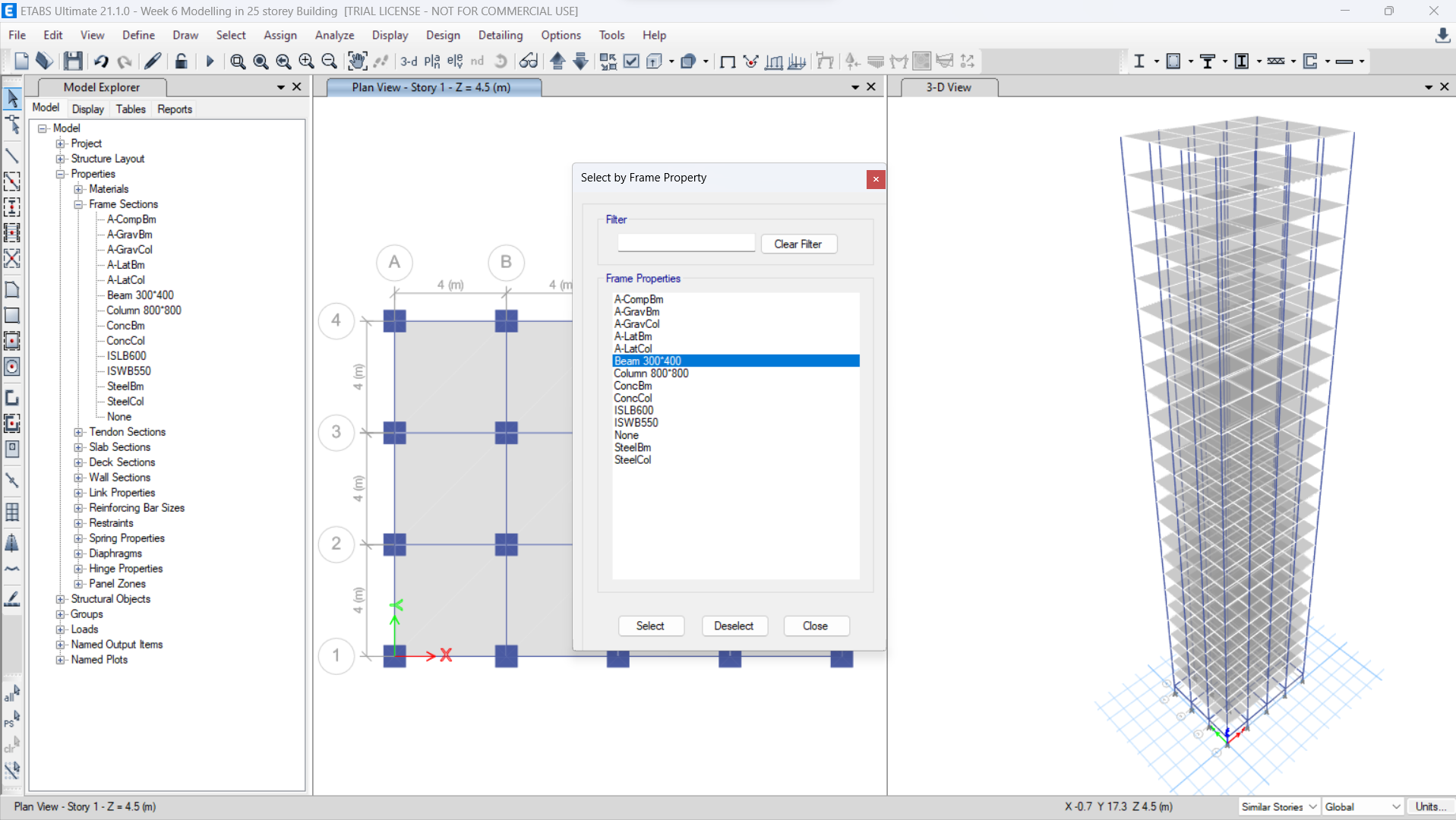
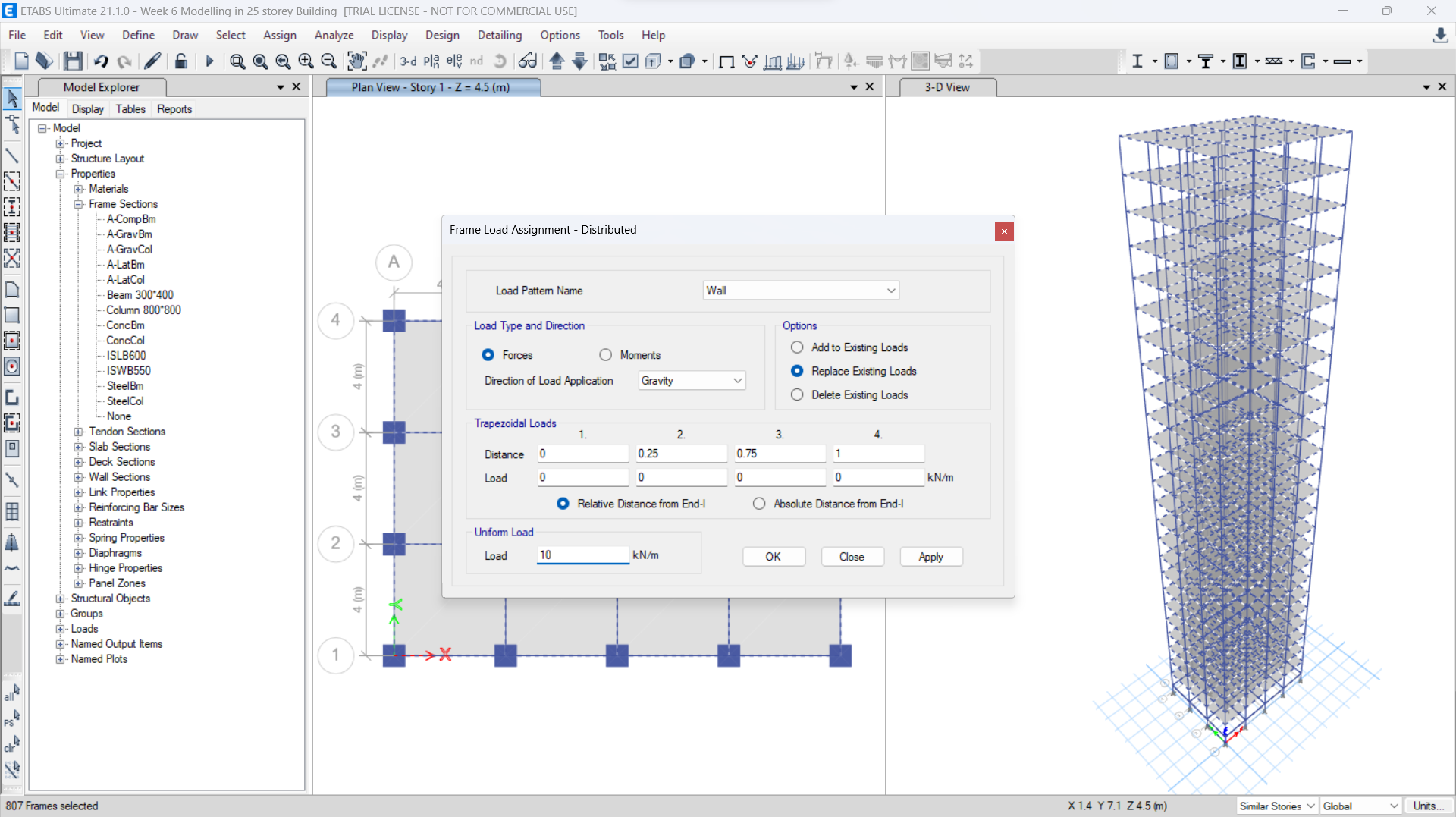
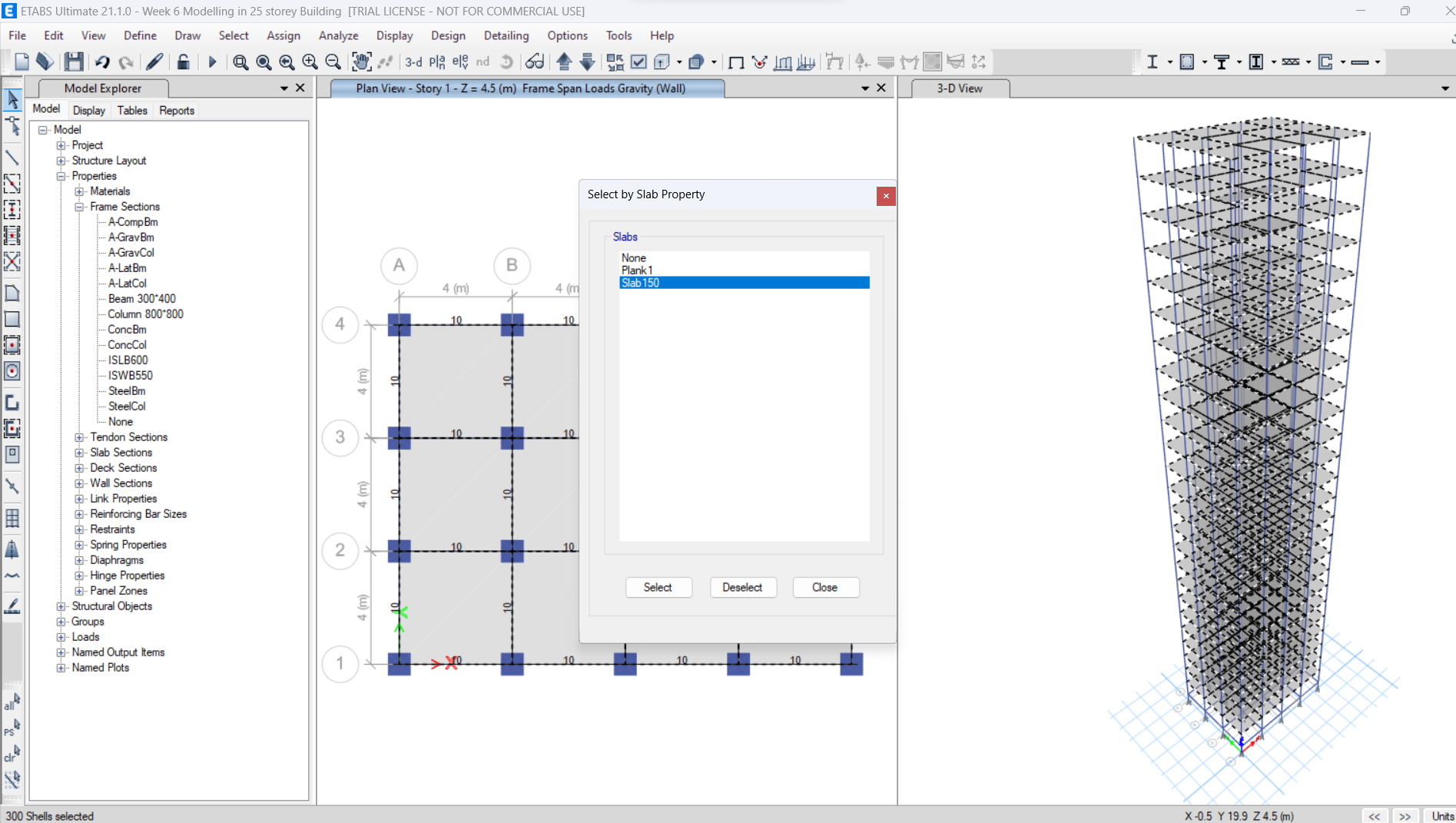
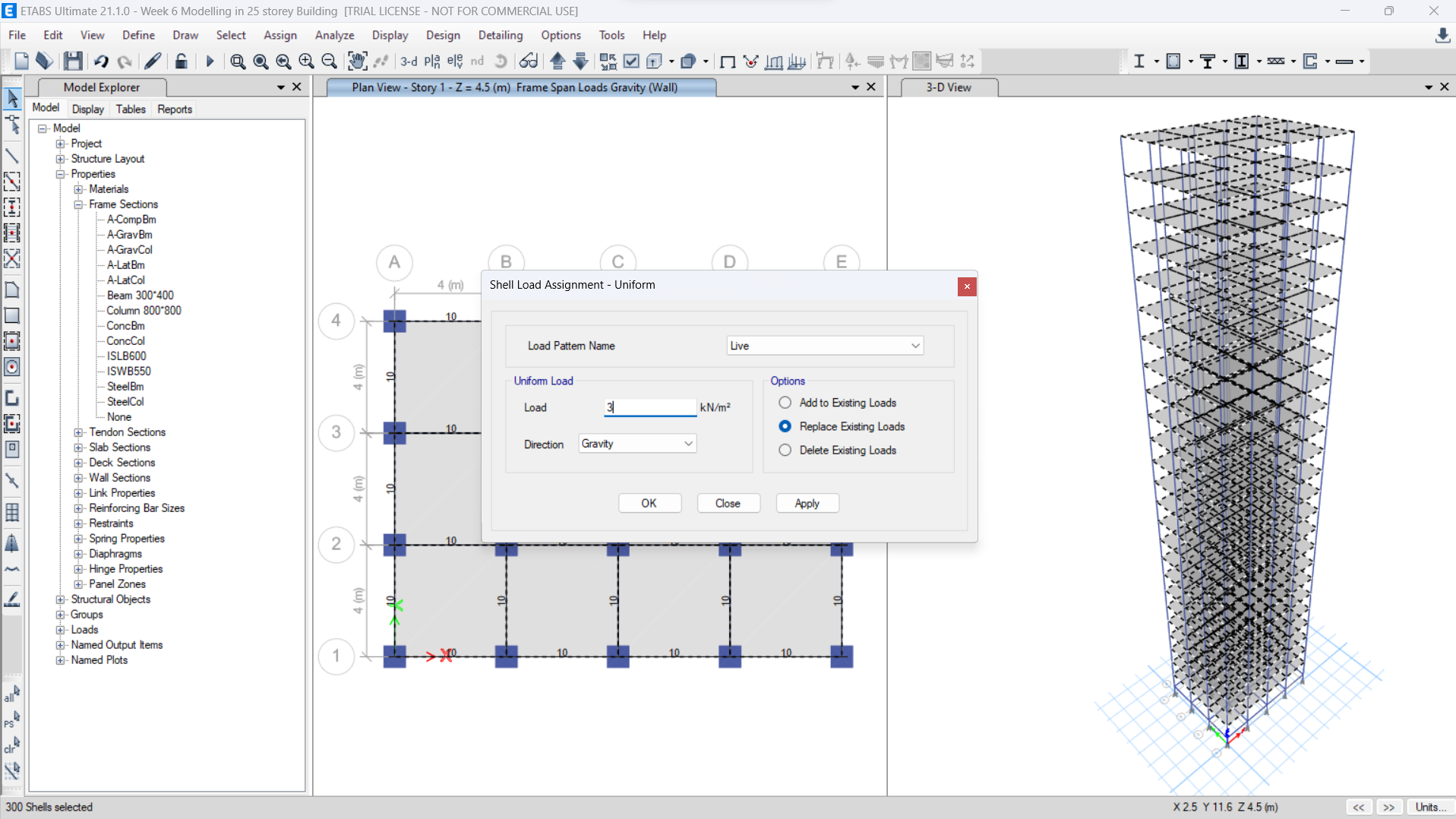
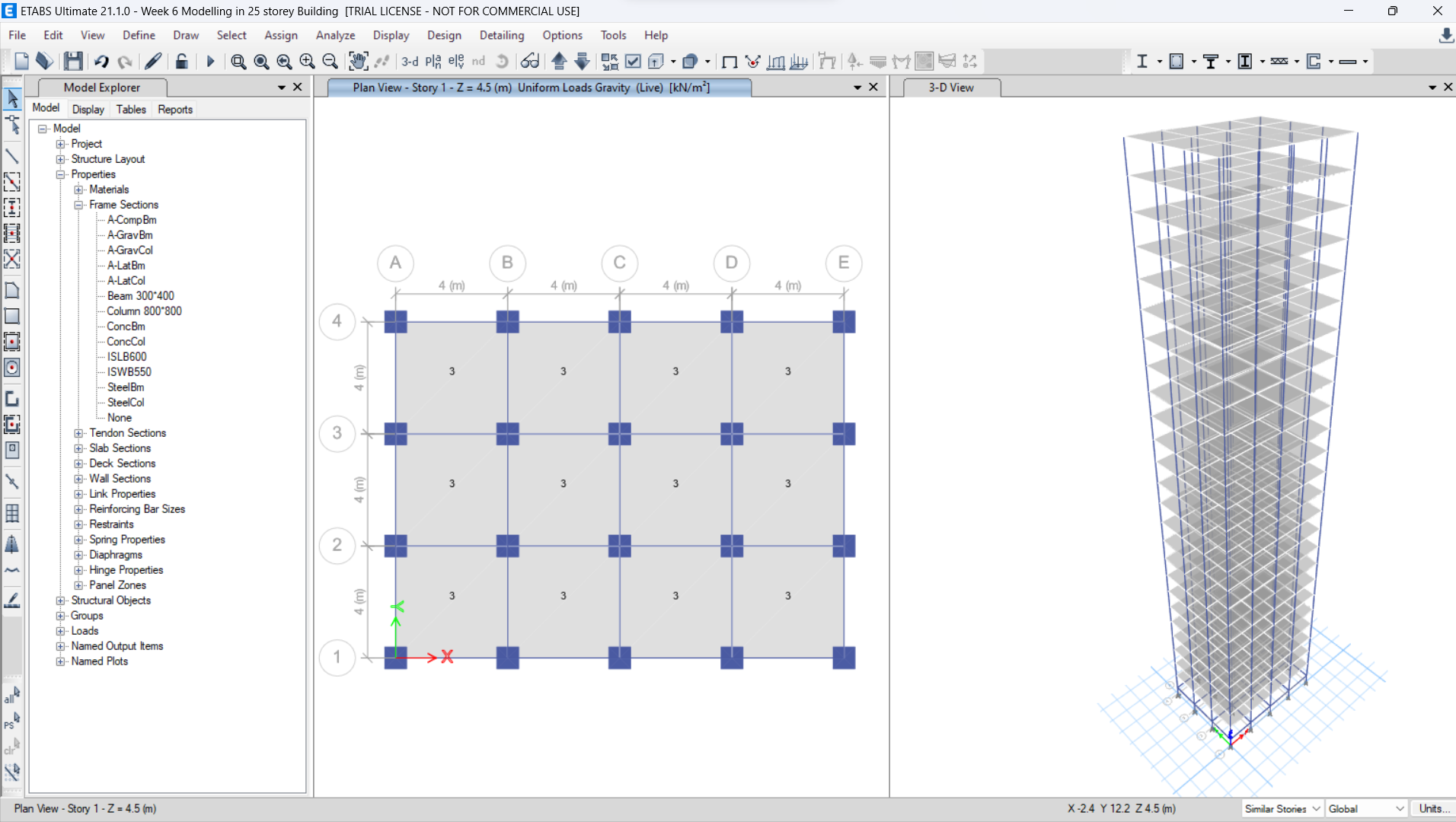
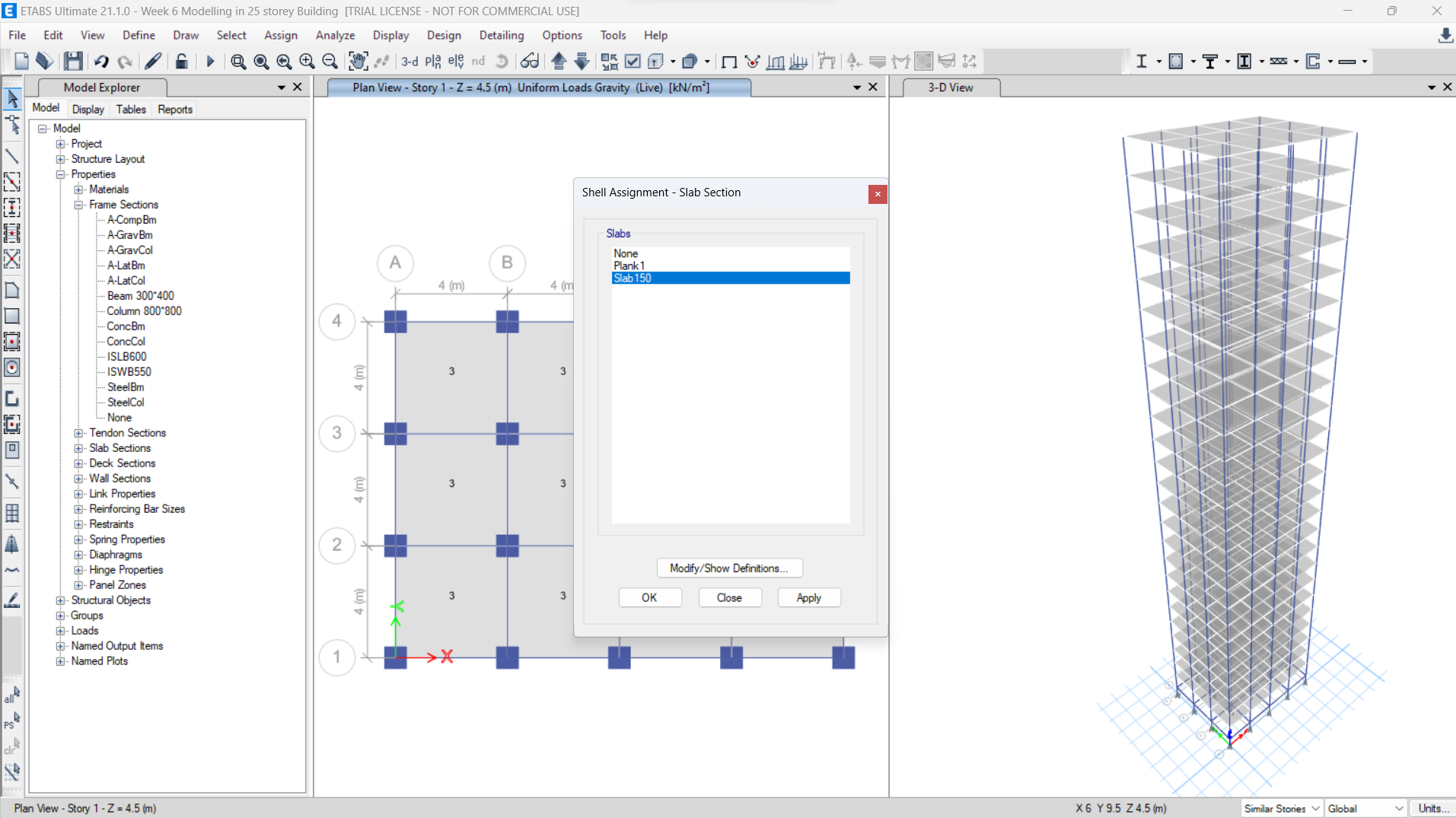
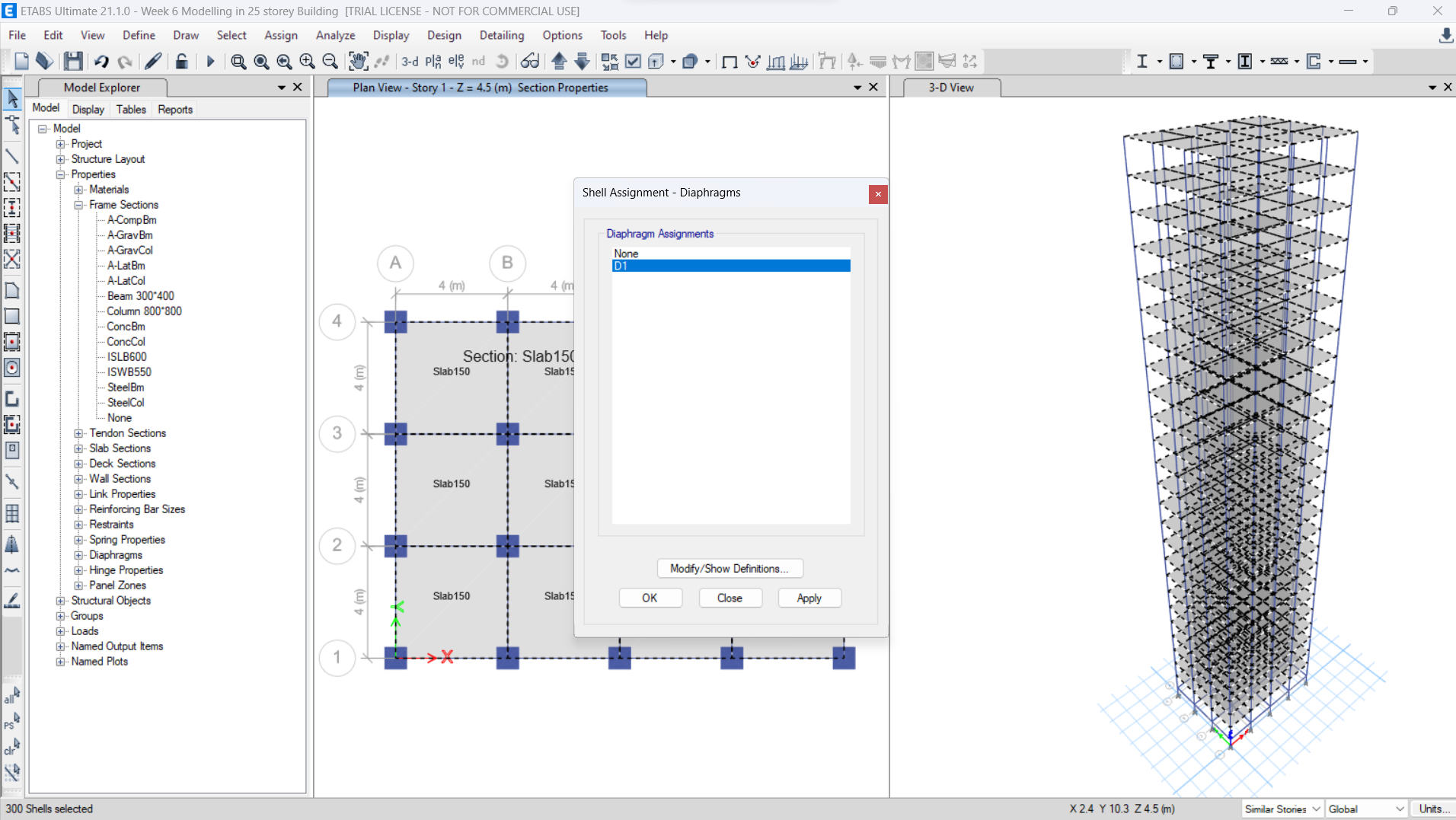
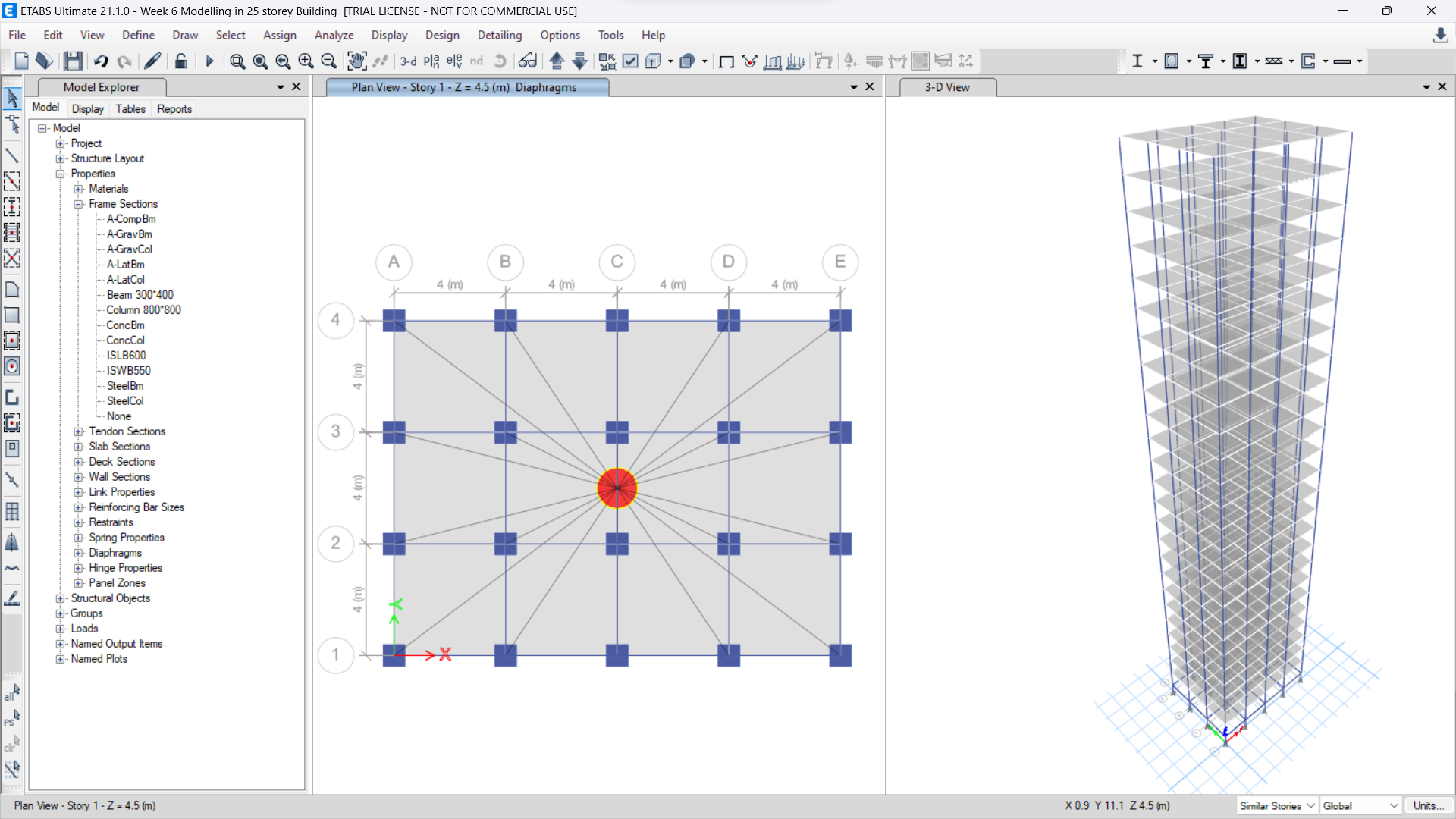
Step 13
- Then verify and Run the analysis
- The model examines deviation patterns and logically cross-checks them.
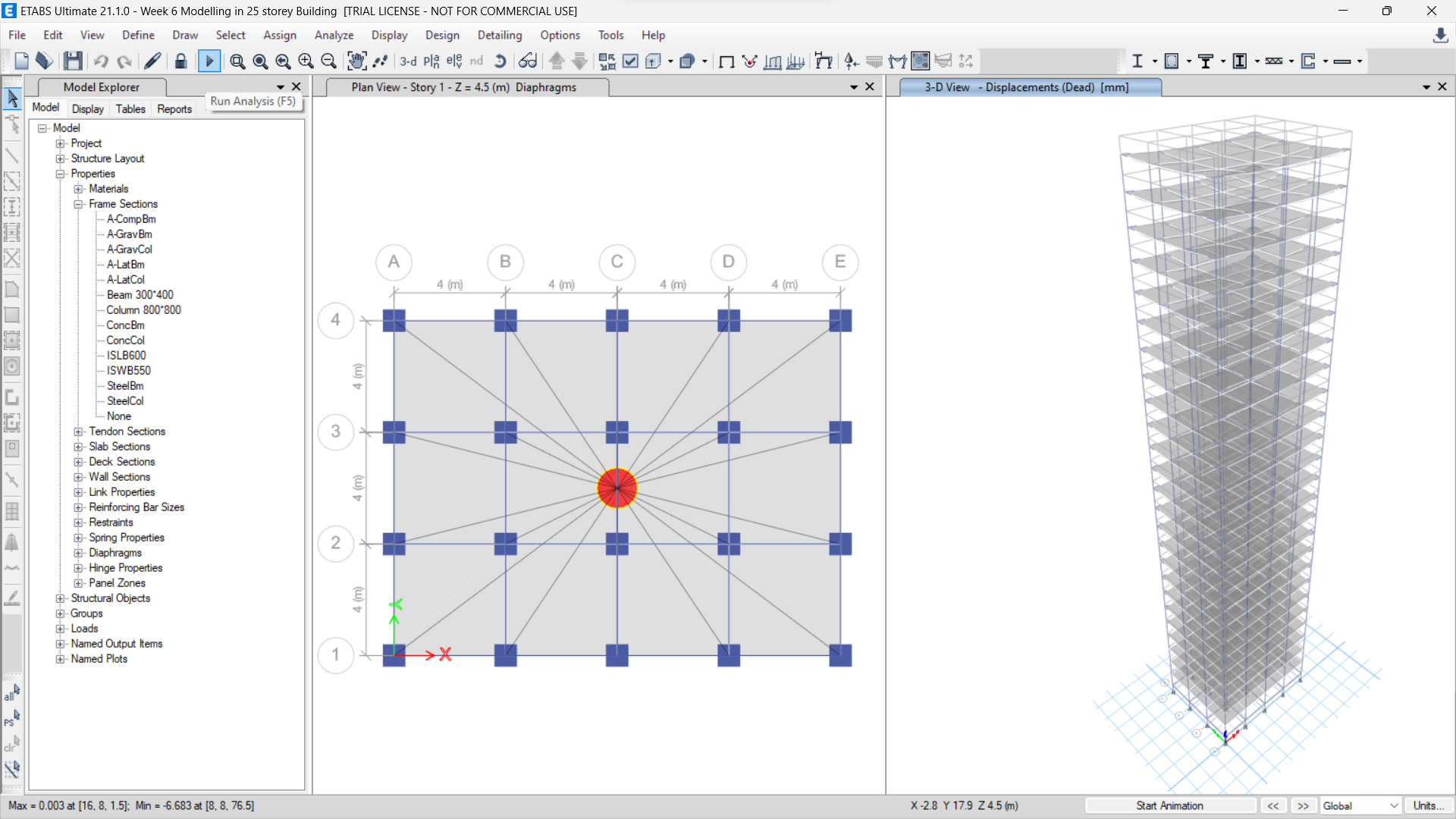

Results:
Fundamental Translation natural period
- Now go to the model explorer and click on Tables Analysislsis results - > Structure output - > Model Information and then select model periods and frequencies
- Time Periods Fundamental model mode1 Y direction and mode1 X direction are noted from the table and are as follows
- Go to Tables Analysislsis results - > Structure output - > Model Information and then select model participation pass mass ratio
- Tx1 = 4.414s and Ty1 = 4.22s
- From the table, the natural period for Mode1 and Mode 2 is shown below
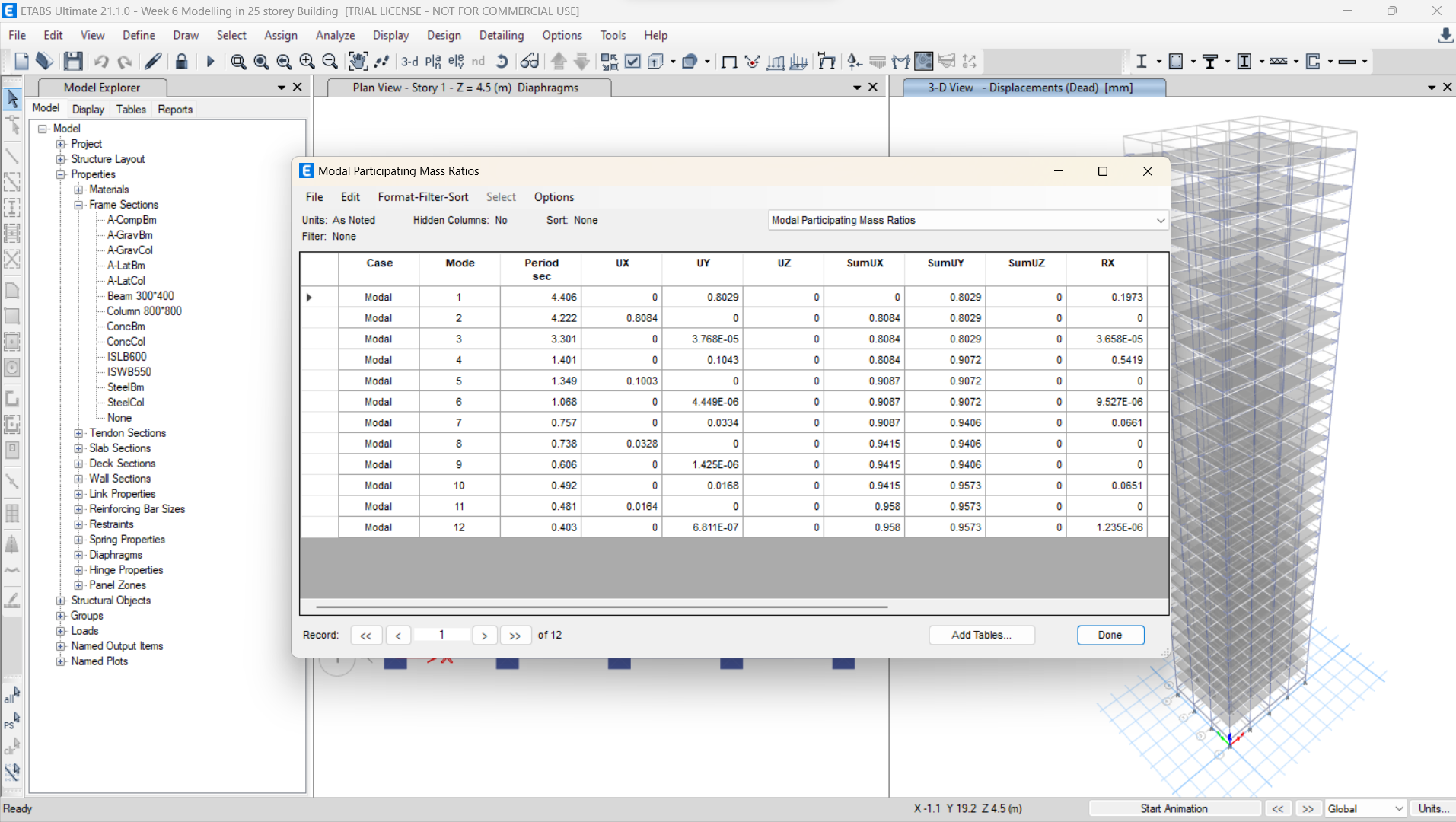
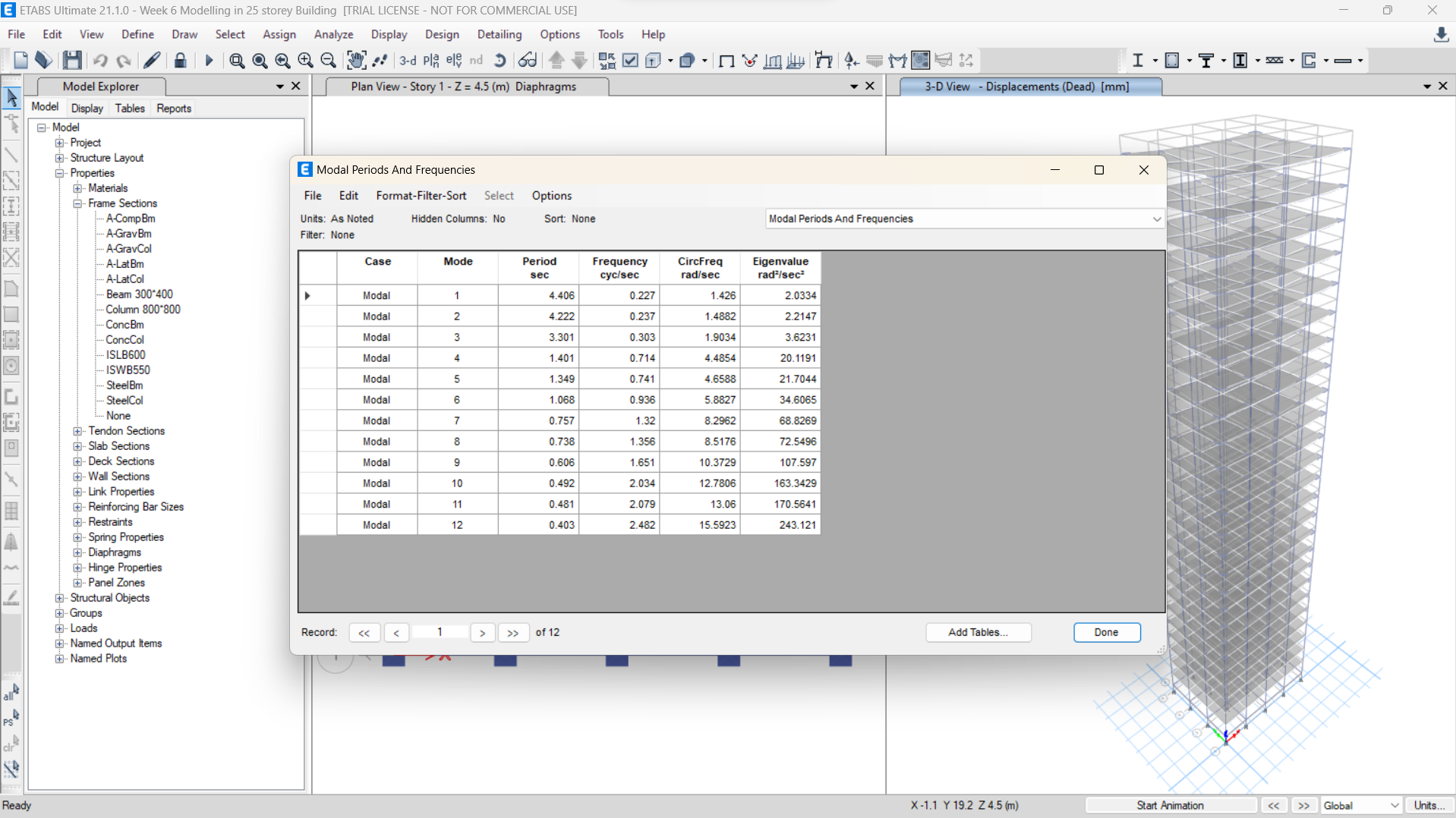
Torsional Irregularity
- Tx1= 4.414s and Ty1= 4.22s and Txy1 = 3.309s.
- So from the result it is clear that the torsion period is less than two translation periods as required by IS 1893 provision Table:5.
- The natural period corresponding to the torsional mode of oscillation must be less than the two fundamental translational modes of oscillation along each principal direction.
Vertical Irregularity
- Check if the two provisions of clause 7 in Table 6 (shown below) of IS 1893 (part 1) – 2016, regarding vertical irregularity is satisfied
- For mode1 and mode2, It's nearly 80% of the mass ratio which means it occupies 80% of the mass itself in the first mode. So, we don't need to add a second and third mode
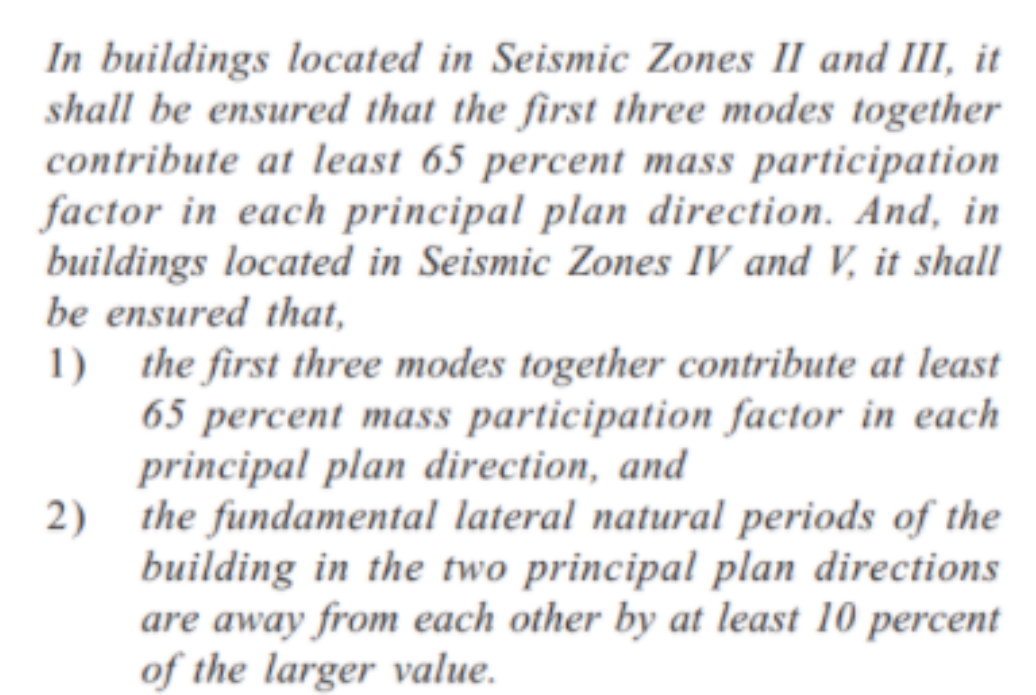
Inter-storey Drift
- Check the if provision inter-story drift limitations in clause 7.11.1.1 are satisfied. Please note that this check is for Serviceability Limit State and hence it is for the situation when the structure is subjected to unfactored seismic base shear
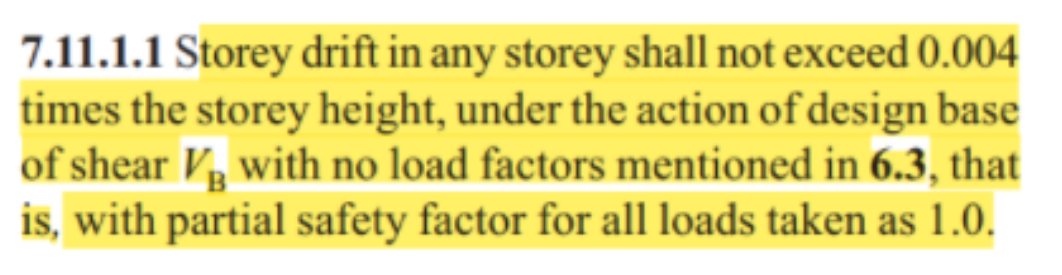
- The story drift serviceability base shear case is tabulated from the tool plots.
- Go to display and then select story response plots.
- Keeping load case to EQX and EQY, the maximum drift value noted for EQX is between 1.35 to 1.50 and EQY is between 1.40 to 1.60
- So as per the clause 7.11.1.1, the maximum inter-storey drift is limited to 0.004 for each story height, So it is satisfied
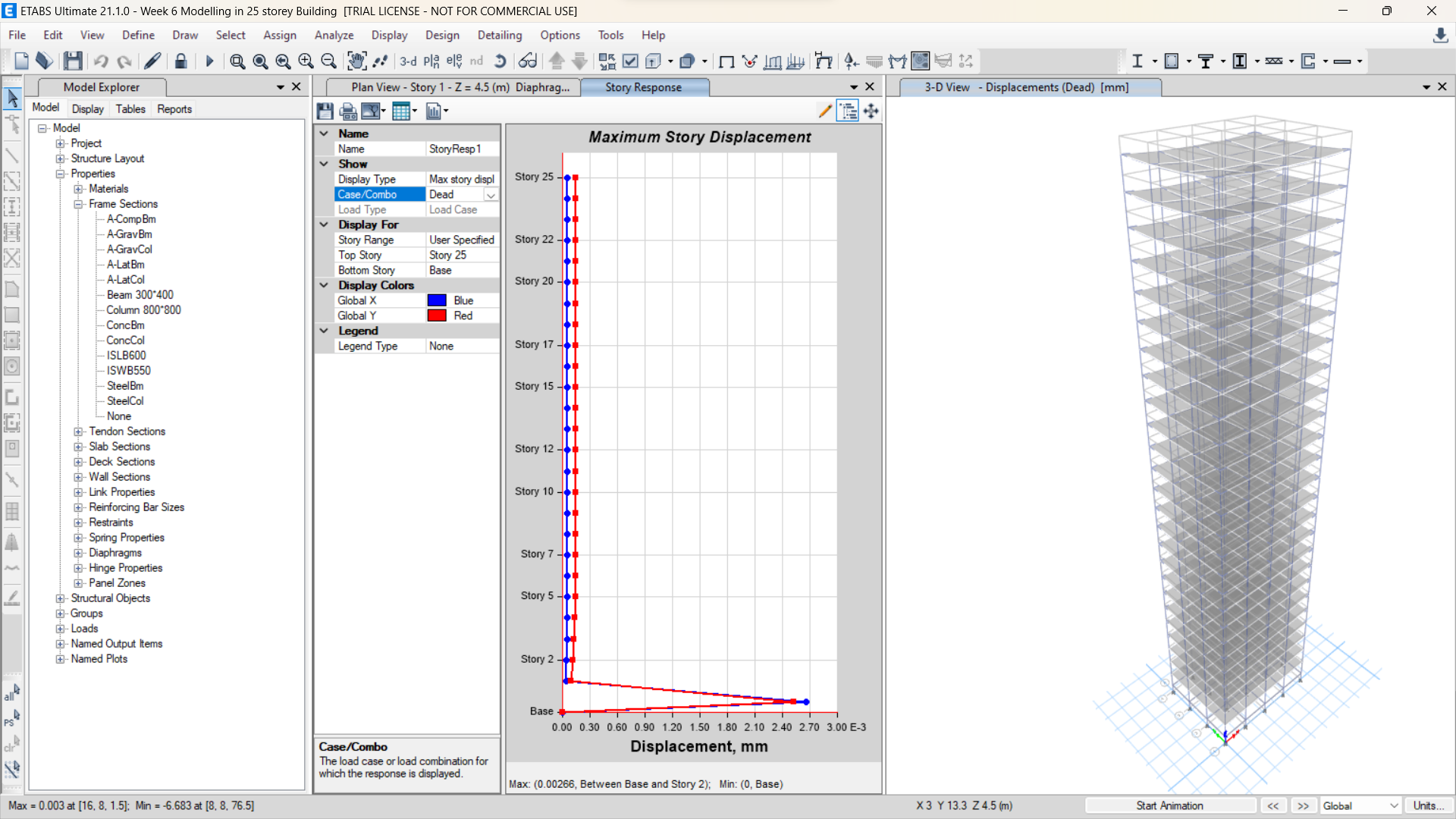
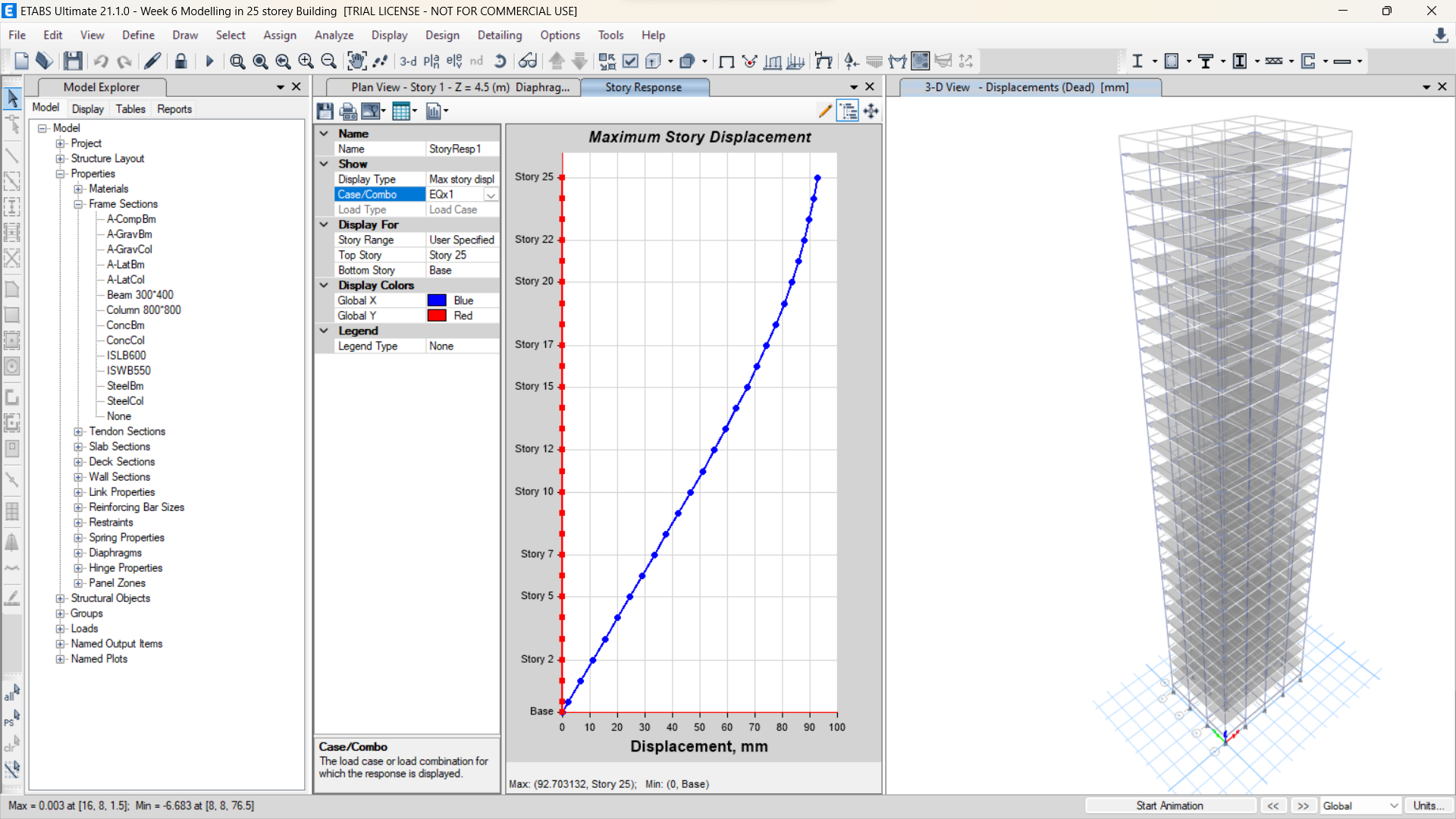
Conclusion:
The modelling is completed and analysed in ETabs, The results are within the given range
CRITERIA |
|
DESIRABLE SOLUTION |
EXERCISE RESULT |
Fundamental Translation natural period |
X - Direction |
4.4 Second |
4.319 |
Y - Direction |
4.2 Second |
4.13 |
Torsional Irregularity |
IS1893:2016(Part 1)
Table -5
|
Torsional mode time period should be lesser than X and Y direction time periods |
Yes |
Vertical Irregularity |
IS1893:2016(Part 1)
Table -6 Clause -7
|
First three modes should together should contribute at least 65% in mass participation factor in each principal |
Yes |
|
Fundamental lateral natural periods in two principal plane directions are away from each other by at least 10% |
No |
Inter-storey Drift |
IS1893:2016(Part 1)
Clause -7.11.1.1
|
Storey drift shall not exceed 0.004 times the storey height for base shear with no load factors (4*103) |
Yes |