Objective:-
- Based on LAW 2 Johnson-Cook Law material card (isotropic, elastoplastic material card)
- To run the model as it is with eps_max =0.15, and with the Johnson failure card and plot energy graphs and conclude results
- To do changes in the Johnson failure Card values of Dadv, Ixfem, and Ifail sh then run the model and conclude results
- To delete the Johnson Failure Card and run the model with EPS_max value only
- Based on LAW 1 Elastic(hooke) material
- Change the given Johnson-Cook material into LAW 1 material by changing the material card
- Based on LAW 27 Brittle material (PLAS_BRIT)
- Use the given LAW 27 starter file
- change the shell element properties
- Then run the model and plot graphs and conclude results
- Based on LAW 36 Tabulated Plasticwise Linear (PLAS_TAB) material
- Use the given Johnson-Cook material Starter file
- and do changes in it such as change the material card to LAW36 (PLAS_TAB)
- then create the curve by using the given values
- add all the values such as E, Nu, initial density, Eps_t, Eps_m, Fscale, etc.
Introduction:-
- Received 2 different starter and engine files
- Starter and Engine file for a LAW 2(johnson-cook) material
- Starter and Engine file for LAW 27(PLAS_BRIT) Aluminium, glass, etc.
- After importing the solver deck in HyperWorks, it was observed that it is mainly about two components
- a rigid ball
- a rupture plate
- Both of the LAW2 and LAW 27 files contain the same assembly of these two same components
- The difference is only in their material card and shell element properties
MODEL IN BOTH STARTER FILES
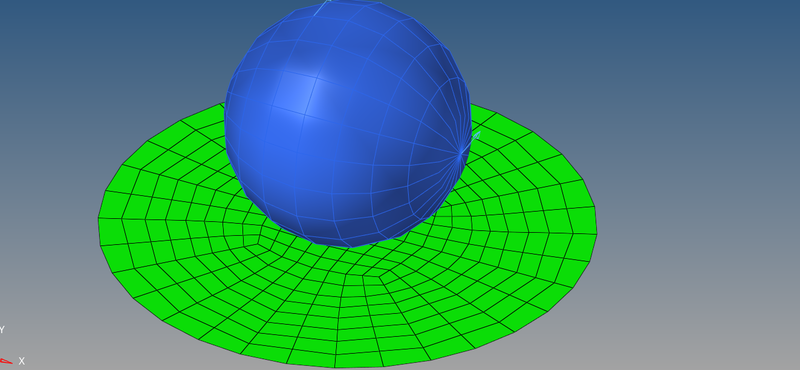
FILES

Theory:-
CASE I: Import the LAW2 Solver deck and Run it as it is
- Which is having the following specifications
- LAW2 material card with Eps_max = 0.151
- and also the Johnson failure card
- after importing the solver deck into HyperWorks and saving the radios files by using the RADIOSS tool in Analysis saved all the radios files in a local directory named the file as "LAW2 eps_max failure".
- Then opened HyperView there opened the h3d file of the saved radioss file saved as "LAW2 eps_max failure".
- then enabled the "shaded elements and mesh lines"
- then ran the simulation and observed the deformation of the plate and then plotted few graphs and concluded few results out of it.
- (Above steps were followed completely same in all of the cases)
- While observing the simulation at a very slow pace (1frame per sec) found that the element getting deleted as soon the strain in the element reaches 15% because the eps_max value is set to 0.151
- So at the very initial stage of simulation, saw that the elements are not getting deleted in a uniform manner this is because the mesh quality was not that good.
elements getting deleted in a non-uniform manner
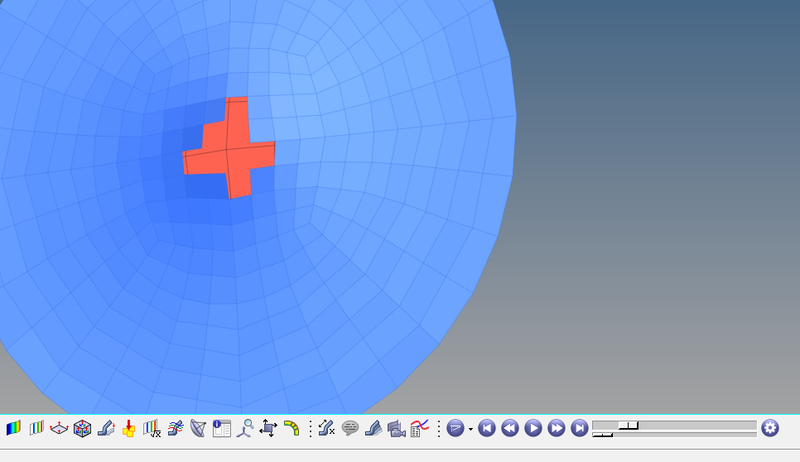
- After this, I plotted the Von-mises Stress contour using the simple averaging method, where it was found that the maximum Von misses stress is 2.725E+02
- Then after opening the 1. out file from the RADIOSS file of the "LAW2 eps_max failure" file Which contains the details about the simulation time, energy error, mass error, number of cycles, etc.
- So the
- energy error was= 1.2 (max) and Mass error was 0 throughout the simulation
- Number of Cycles= 49380
- Simulation time= 60.18 seconds
Contour Plot (Von Mises Stress)
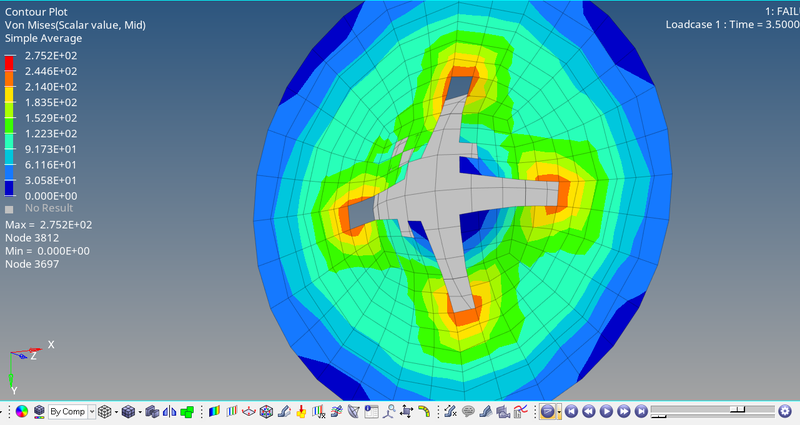
Energy and Mass error
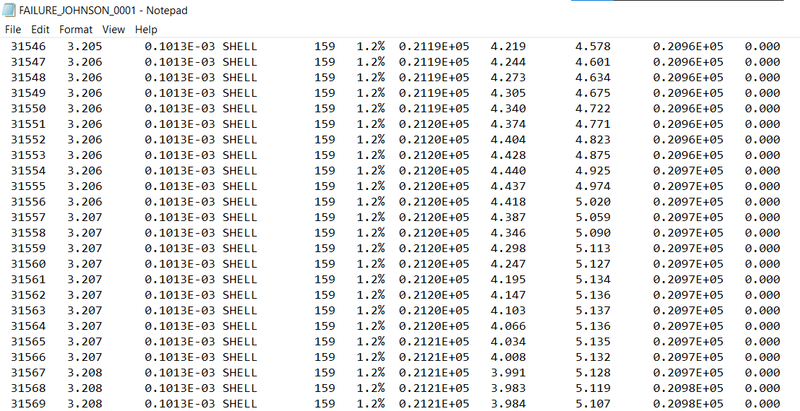
Number 0f cycles and Simulation time taken
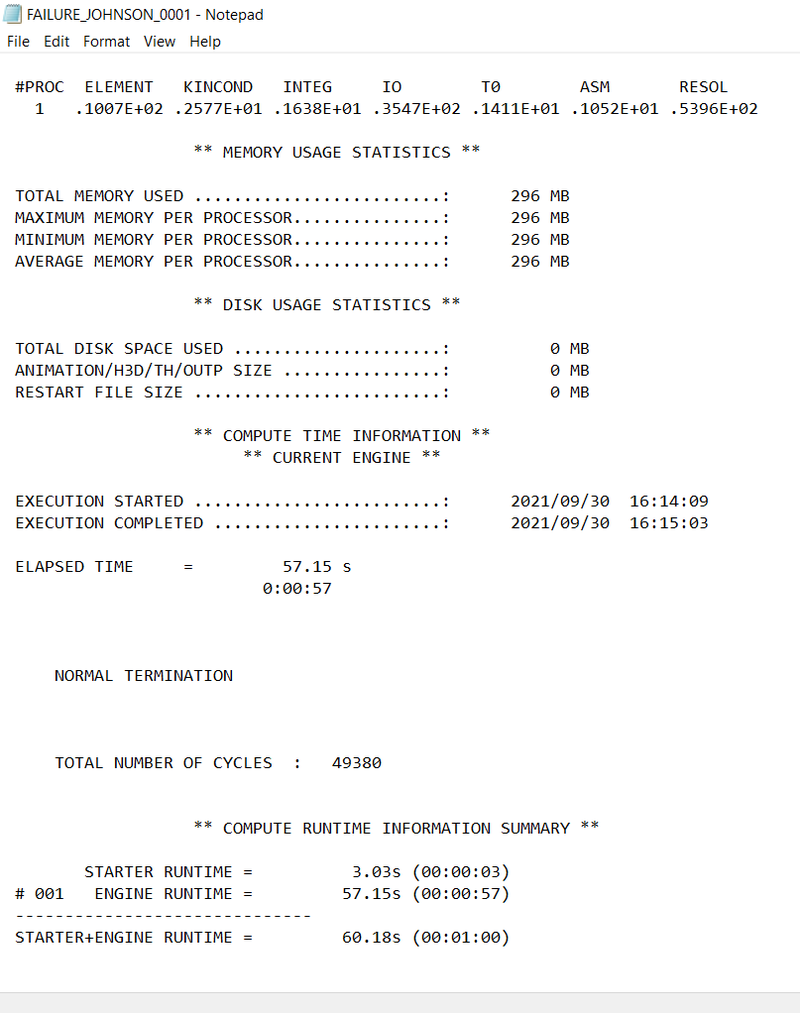
- After doing the solving part, moved to Post Processing part
- plotted few graphs of different types of energies by using HyperGraph2d
- such as Hourglass energy, Total energy, Internal Energy, Contact Energy, and KInetic energy
- these all energies are found in global variables
- to plot the graph, first opened the HyperGraph2d
- then opened the T01 file which contains all these details.
- and hence plotted all graphs
Energy Graph
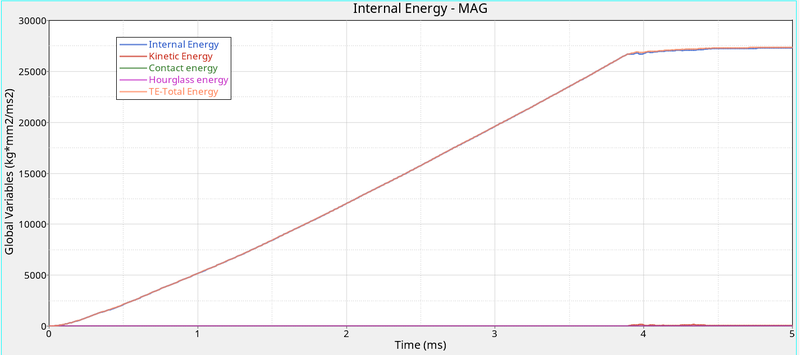
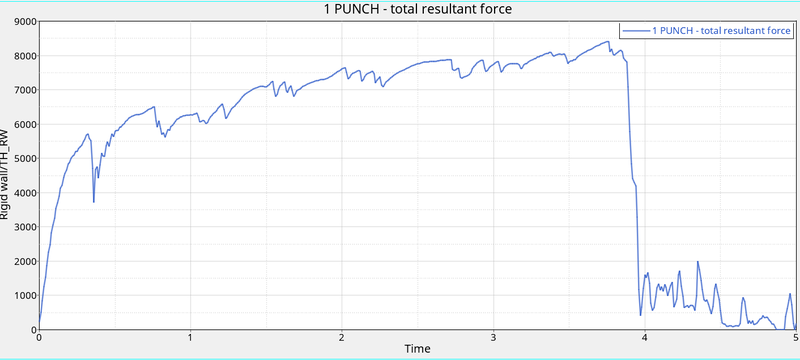
- After this, we can conclude few results such as
- the simulation time taken is very less
- since we used the Johnson-Cook Material model with eps_max= 0.151 so we can see in the rigid wall force plot that
- once the element has developed or absorbed about 15% of strain energy it gets deleted automatically and the rigid wall force drops.
- then we can see that the maximum stress that the element can withhold is also pretty less, it is maybe because the values in the Johnson-failure card is not assigned properly and the only failing criteria for an element is the eps_max value which means as when the element absorbs that percentage of strain energy it automatically gets deleted, that's why the Von Mises stress is quite low.
- There is very little energy error and mass error which is
- energy error= 1.2% and mass error is 0
- as the energy error is less than 5% which means the result is acceptable
- This is because in the shell property the QEPH element is used and Ismtr=2 which means the change in strain of element is taken into consideration as per the instance of time the strain of element is changing, Iplas, and Ithick is also activated which means all the thickness changes are taken into consideration and the thick change is calculated using the iterative method which is quite accurate and this material card mostly works under the plastic region these values are quite effective in obtaining the accurate results.
- Which resulted in 0 hourglass energy formation.
- The above Shell properties are taken the same in all the cases.
- In the Energy graph, we can see that there is some disruption in the plot when the rigid ball has broken the rupture plate completely then some internal energy gets converted into kinetic energy.
- And the number of Cycles were= 49380
CASE II: When Few changes were done in the values of parameters of Failure Johnson Card
- In this case, after importing the RADIOSS file into HyperMesh, did some changes in the Johnson Failure Card
- which are
- Dadv= 1 which is a criterion for crack advancement and at 1 the values it gives are real and this is also used for crack initiation
- Ixfem= 1 this activates the generation of the crack in the elements before failing or reaching the eps_max value which is a real visualization of how the element exactly cracks before breaking but this crack also consumes some energy so for a small model or for few cracks its fine to use this as equal to 1 but not for huge models or for whole crash simulation.
- After making all these changes saved the radioss flle.
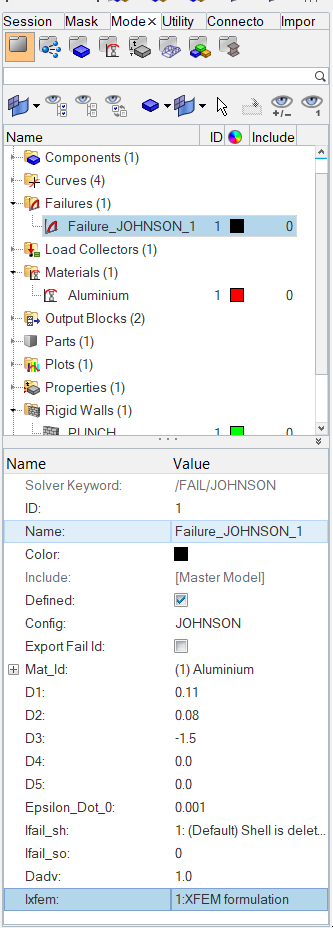
Energy Error = 4.1% which is under acceptable region and Mass error = 0
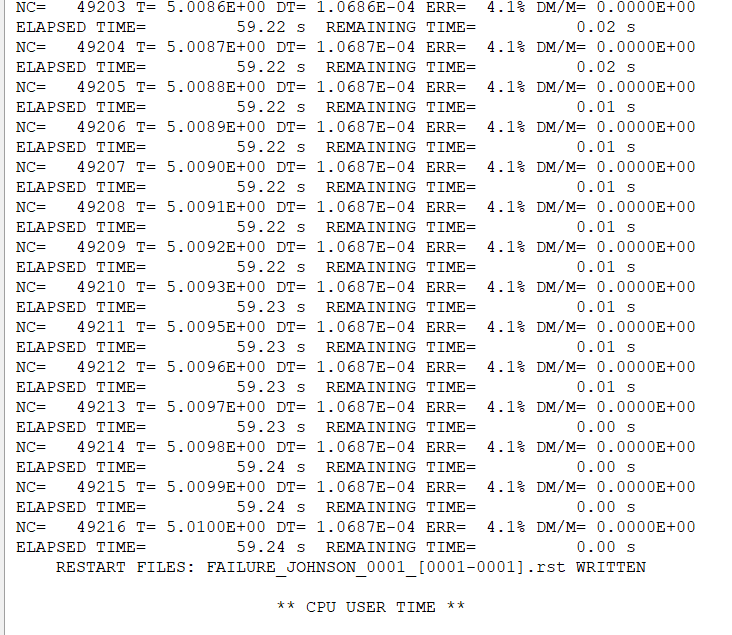
Total Number of Cycles= 49217
Time Elapsed= 59.85 sec
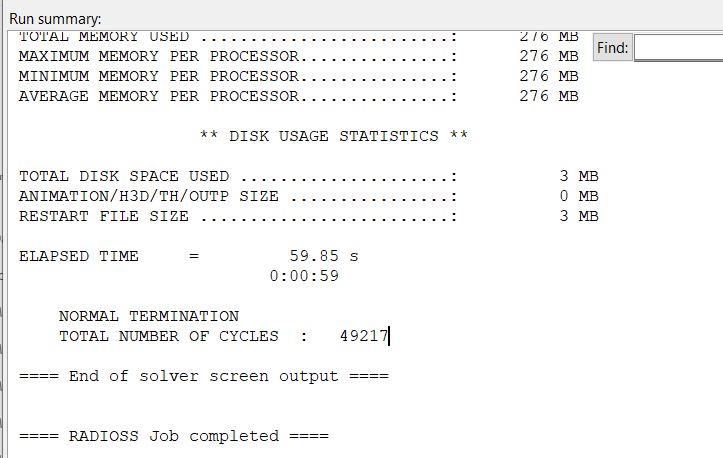
- then by using the HyperView ran the H3d file and observed the crack and failure of elements
Cracks generated before failing of elements

Maxx Von-Mises Stress = 2.572E+02
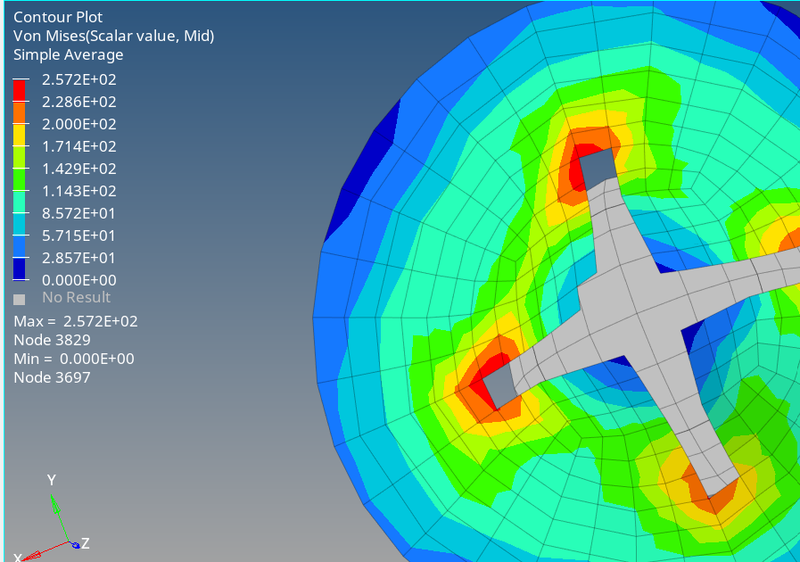
- After observing the failure plotted few graphs in the post-processing from where we can conclude
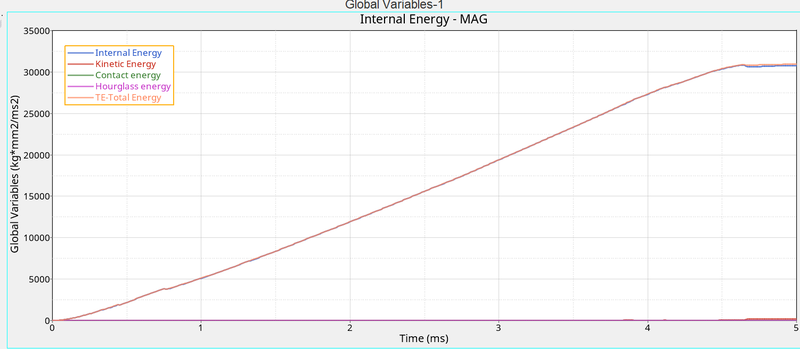
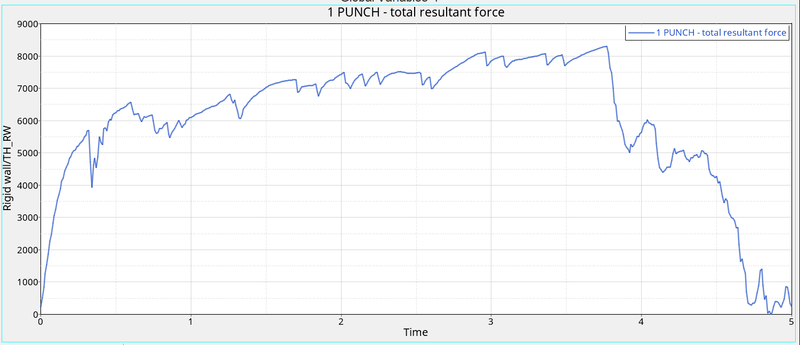
- After plotting these graphs we can conclude few results such as
Conclusions for case 2:-
- The element start cracking before it reaches the failing point and this is because the Ixfem, Davd, and Ishfail card is used
- Due to which we can see that the number of cycles is reduced than the case 1 because some energy is lost in the cracking process of elements SO it is not feasible to use this Ixfem card for huge simulations
- After that, we can notice that the von Mises stress is also less in case 2
- But as this is an elastoplastic material So the results are quite similar to that of real material in this case.
- Simulation time is also fine, the time taken for simulation is 62.57s
- And in the plots
- In the energies graph, we can see that
- hourglass energy is 0
- Kinetic energy is also very minimal
- And internal energy is almost equal to total energy
- this is because in the simulation there is very less disruption and changes in between energies which is a very good sign.
- And in the second pot of rigid wall forces, we can see that when the strain energy inside the element reaches the failing criteria then initially the element cracks that's why the rigid wall force is dropping slowly, and finally after failing the rigid wall force becomes zero.
CASE III: After deleting the /FAIL/JOHNSON card
- In this case, the Failure card is deleted
- So the failure criteria, in this case, is only the EPS_max value
- So when the Plastic strain energy reaches the EPS_max value it fails or gets deleted.
- So because of the presence of only the EPS_max failure option, only the failing of element due to the tensile or bending failure is noted because the EPS_max failure does not note the failure due to compressive load or compression.
(Modal tab) after the deletion of Johnson Failure card
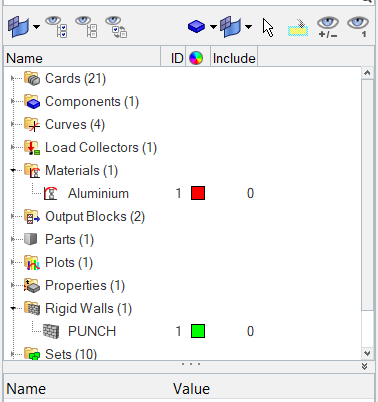
Elements getting deleted without getting cracked because the failure card is deleted so there is no Ixfem card only the EPS_max is the failing criteria
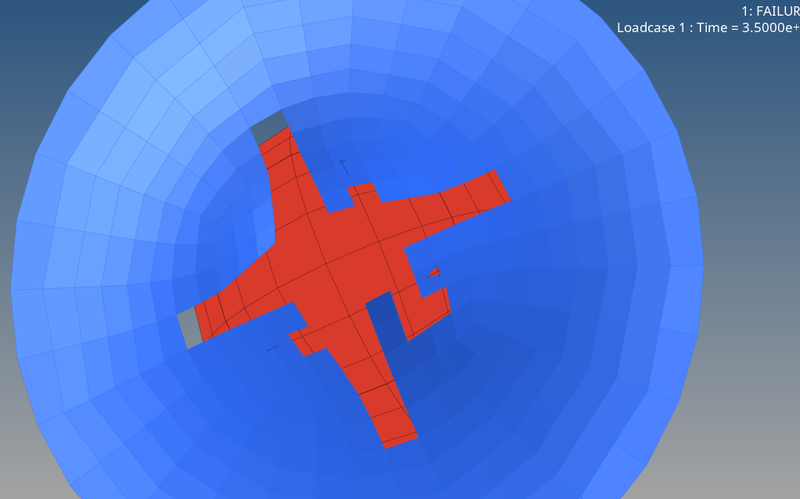
Material Card
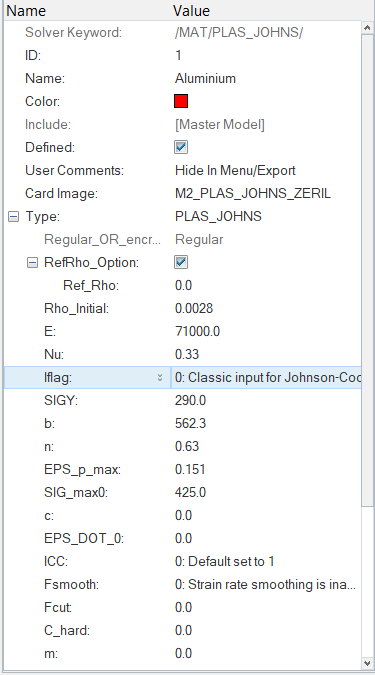
Conclusion:-
Von mises Stress contur where the maximum stress in 2.707E+02

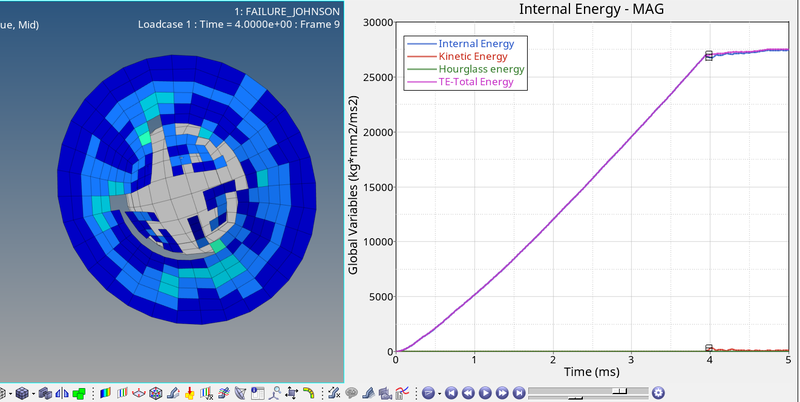
- In this case, the mass error is 0.8%
- And Mass error is 0
- so these values are under the acceptable range
- Simulation Total Time is 63.04 second
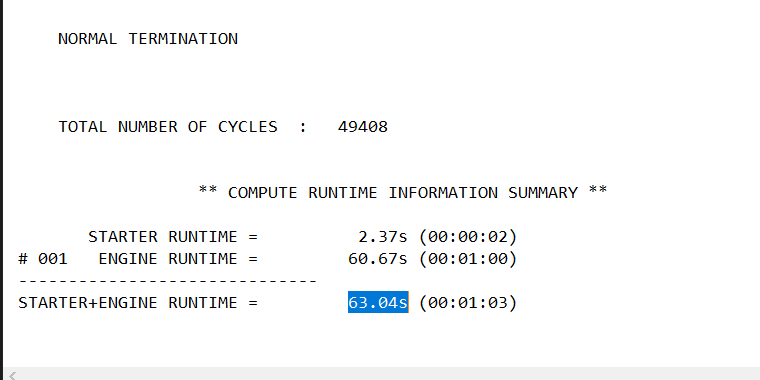
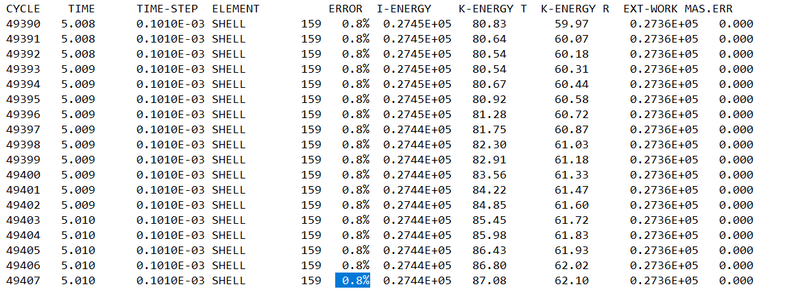
CASE IV: Delete the values of Eps_max and run the model
- So In this case we deleted the only failing criteria left for the elements which was the eps_max value
- So now in the material card, there are no failing criteria for the elements
- So now the elements will go up to the Sig_max value which is the maximum stress value for the elements without breaking, cracking, or getting deleted when the rigid ball will push and put force on the plate
- And the material will behave like an elastic material.
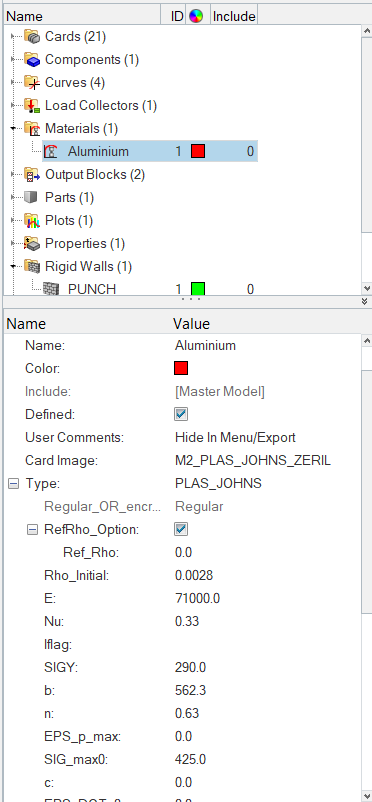
Conclusions:-
- So after deleting the eps_max value the rigid wall force is not dropping at any time like the other Johnson-Cook cases
- The rigid wall force is just increasing with time
- And the internal Energy and total is completely the same because there is no breaking of element
- And the kinetic energy is also changing almost at a uniform rate but with very less magnitude
- And Contact and hourglass energies are completely zero because very good quality of element property is used
- The element reaches up to the maximum stress value which is 4.247+02 without breaking which is very unrealistic
- and the simulation total time is 58 seconds
- and the total number of cycles is 48737
- and the energy error is 3.0%
- And the mass error is zero
- So the mass and energy error is under acceptable values
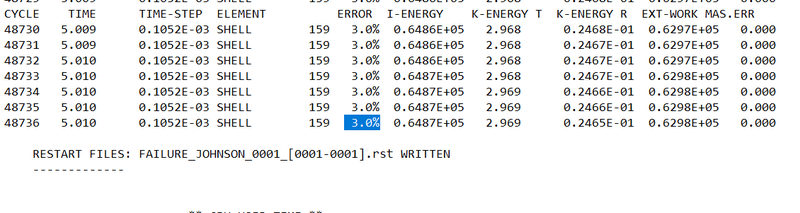
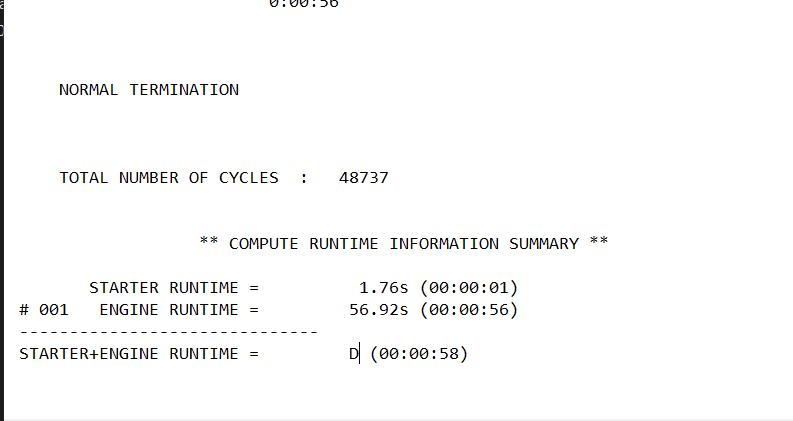

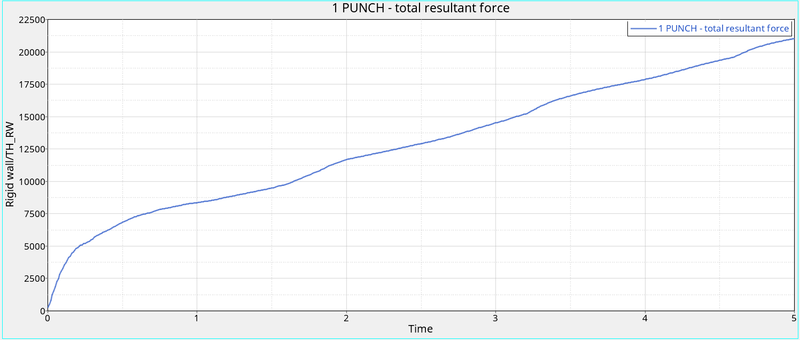
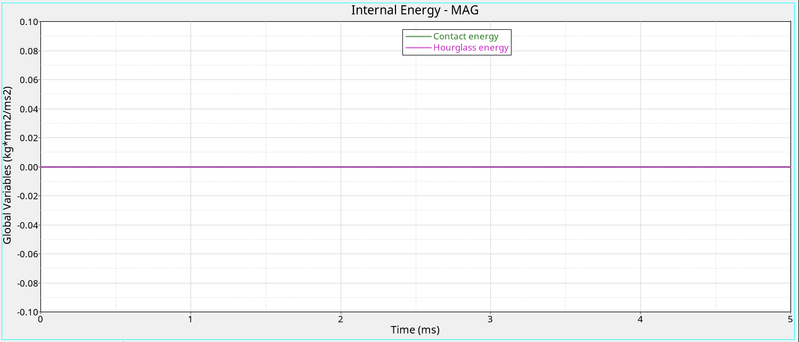
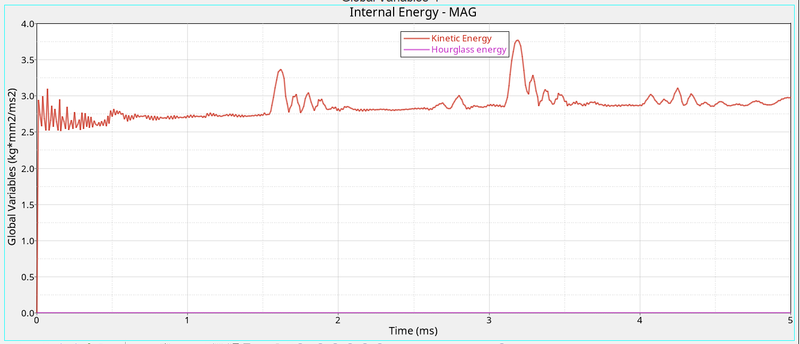
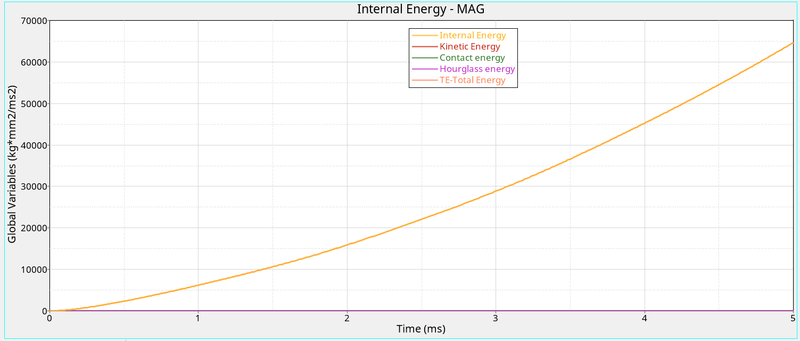
CASE V: Convert this material to LAW 1 elastic with the same density E
- So For changing the Jonhson-Cook material card to LAW 1 elastic
- First changed the card image to M1_ELAST which is nothing but LAW1 material card with the same E and nu values.
- and then saved the RADIOSS file
- then in HyperView saw that the plate is behaving elastically
- This means the plate is undergoing stress without breaking any element
- Where the Von mises stress is 1.089+04
- In an elastic material card, the stress in the element is considered only up to the yield point unlike the LAW 2 card where the stress and strain values are assumed only
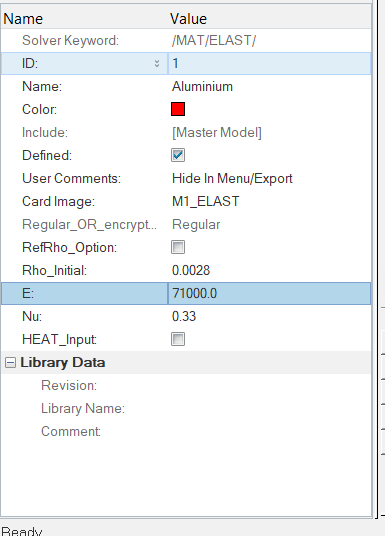
Conclusions:-
- So in this case the material is behaving elastically so only up to the yield point the calculations are taken into consideration
- The simulation total time is 59.18s
- and the mass error is 0
- Energy error is 1.3%
- which is under the acceptable region
- and the total number of cycles is 47969
- And the Rigid wall force is just increasing uniformly because their would not be any breaking of element and this force will go up to yield point only
- And their not much changes between the energies.
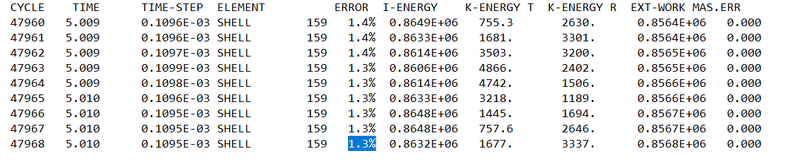
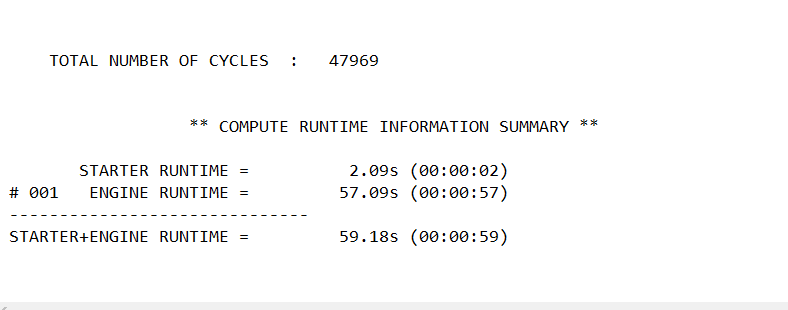
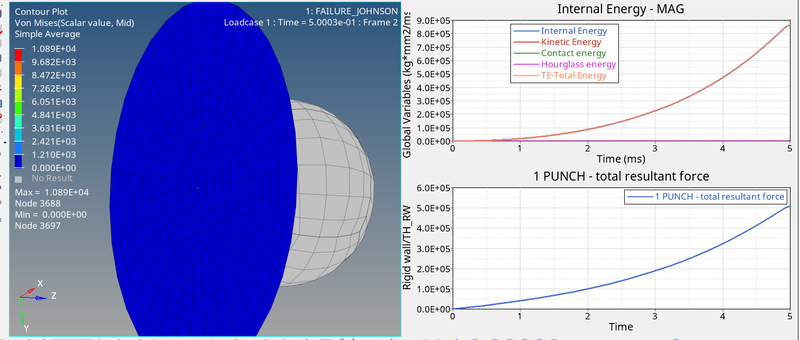
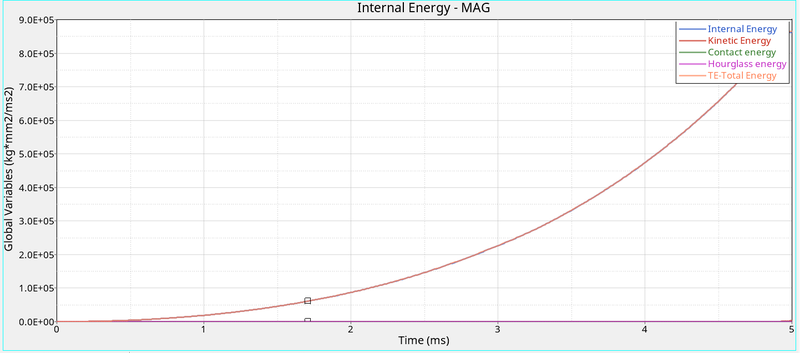
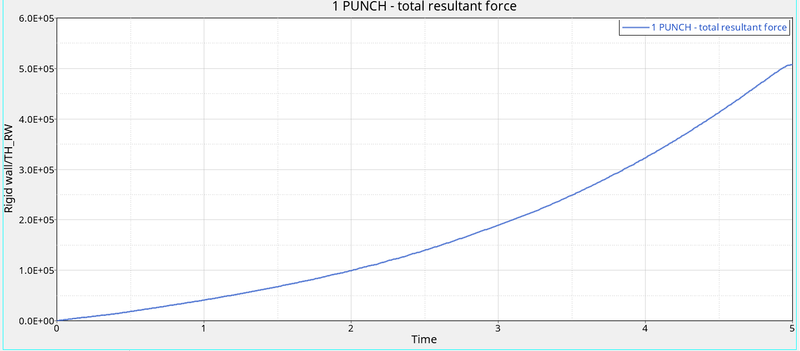
CASE VI: Change the material card to LAW 27 brittle material
- This material card is for brittle materials
- In brittle materials, the plasticity region is very narrow, and in this, the element goes to failure very quickly
- This law is applicable only for shell elements
- Failure of elements only occurs in tension
- So to do the changes first set the material card to M27_PLAS_BRIT which LAW 27 material card image
- And did the changes in the shell element properties to avoid energy error mass error and hourglass energy
- Then did the required changes for LAW 27 material
- And then saved the RADIOSS file
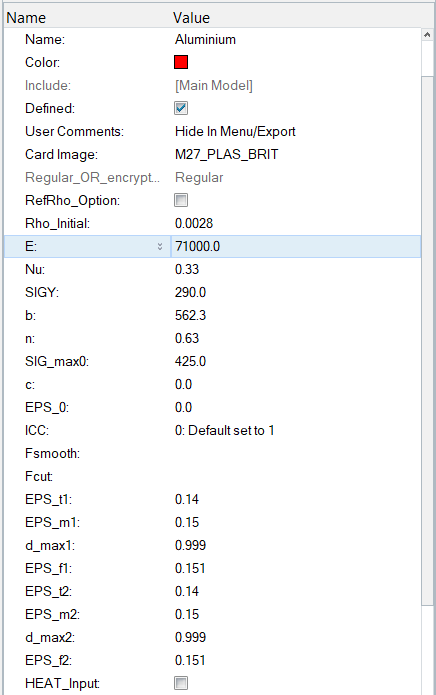
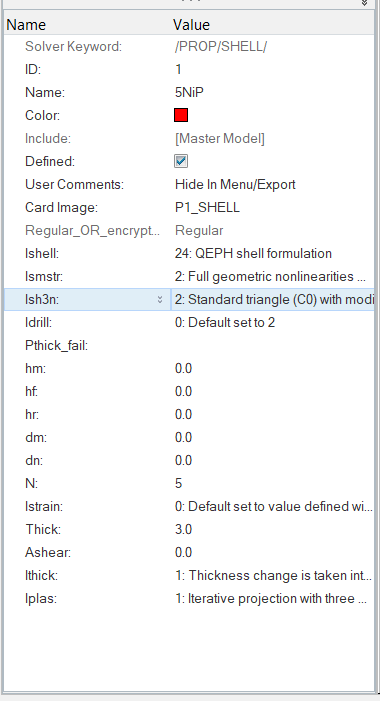
Conclusions:-
- So in this material card, the element breaks very early than in other cases because it is a brittle material
- The fracture in this case happens suddenly
- and the yield point is quite higher in this case
- so it is quite stronger than other materials
- the number of cycles is 49508
- and total simulation time is 63.18s
- The energy error is 0.8%
- Mass error is 0
- Von mises stress 2.875E+02
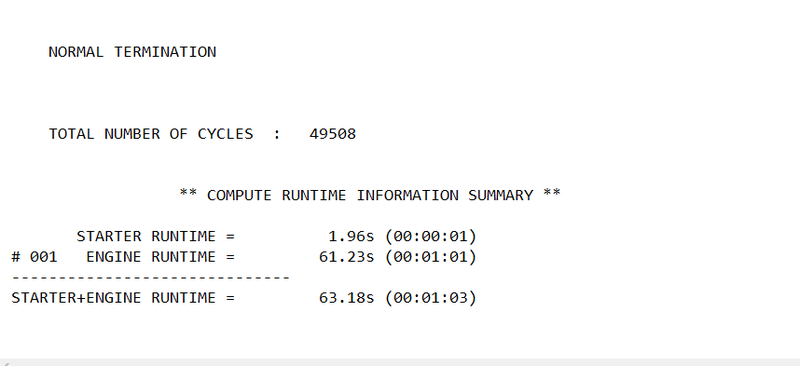

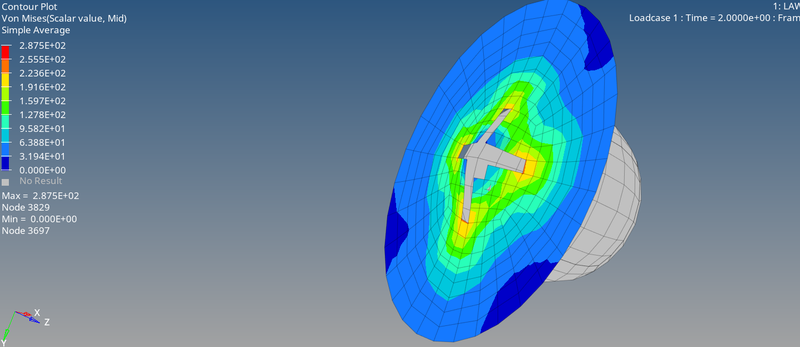
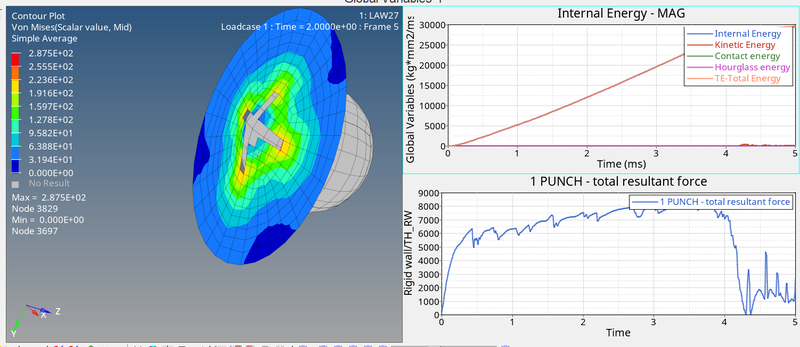
CASE VII: Change the material card to LAW 36 elastic-plastic piecewise material
- This is an Elastic-Plastic material
- To do the changes first changed the material card to M36_PLAS_TAB
- then EPS_t = 0.1 which is tensile failure plastic strain value
- and EPS_max= 0.11
- Then for Function ID defined a curve named LAW36 using the given values of stress and strain after the yield point
- and assigned that curve to the function Id and Saved the RADIOSS file
- In LAW 36 it uses lab data for defining the curve, it uses defined strain rates in the lab
- more the number of strain rates we put in more the number of user-defined functions will be defined which leads to more accuracy and less assumption which is far better than LAW 2
- in this, it defines my curves as assumptions and according to those curves and lab data it defines the curve which is much more accurate
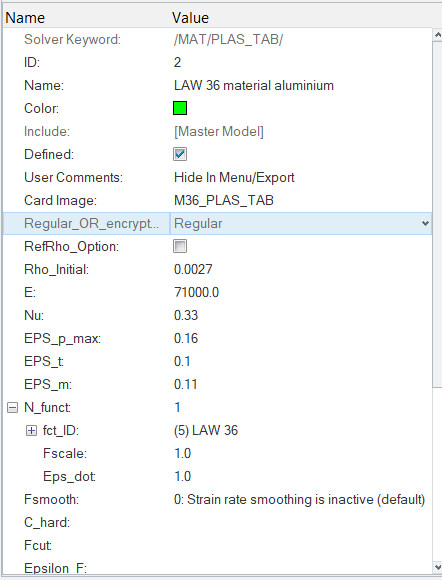
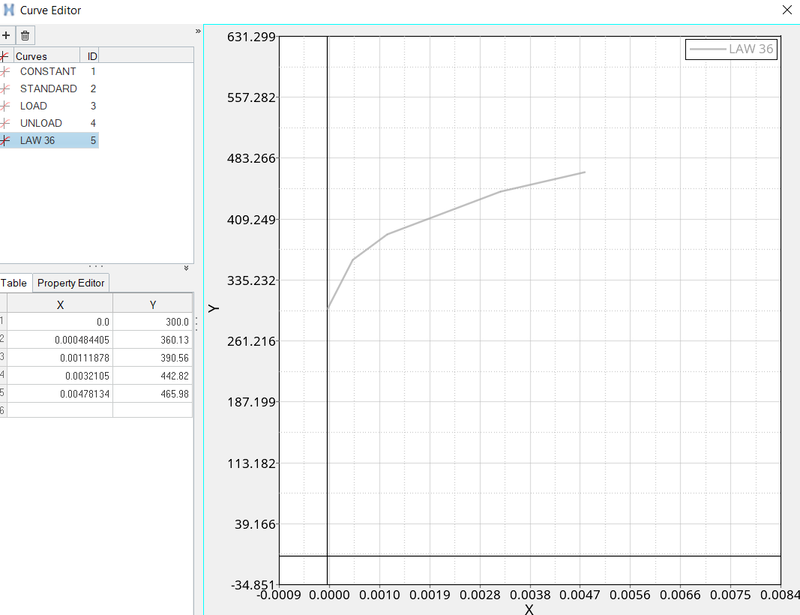
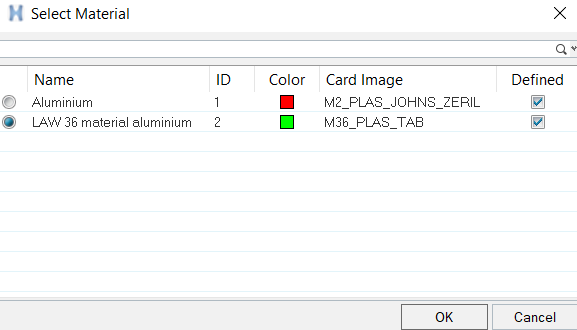
Conclusions:-
- In this, the results are very precise because we used lab data in it
- as we can see in the rigid wall forces the changes look very real and authentic
- And also there are not much changes in between the energies
- and the mass error is 0
- and energy error is -1.3% which much better than other cases
- von mises stress is 8.010E+02 which is very much higher than any other elastic-plastic material card
- The total simulation time is 63.74s which is very less with the accuracy of results
- And the total number of cycles = 53155 which is very much more than any case
- This material is much better than any other material card
- This material can be used for any type of material if right inputs were given
- So according to the results and comparison with other cases
- LAW 36 material card is much better and efficient.
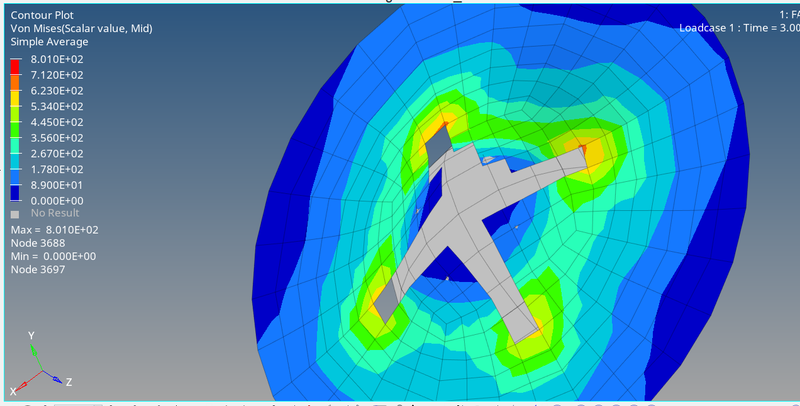
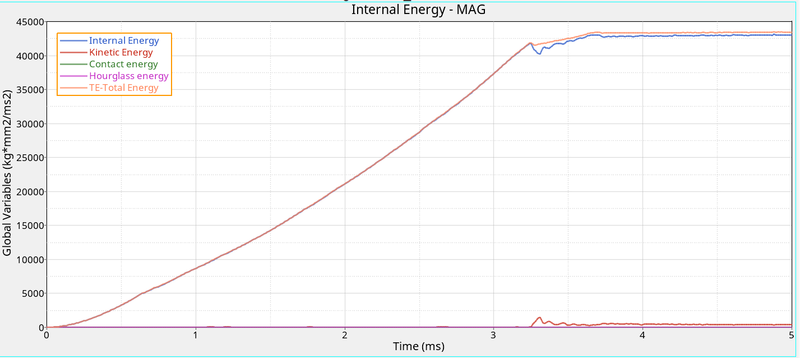
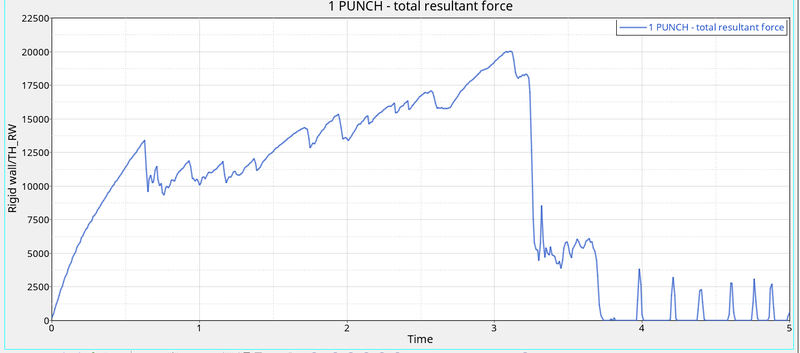
PLEASE GO THROUGH THE FOLLOWING LINK TO SEE ALL THE RADIOSS FILES OF ALL THE CASES
Google drive RADIOSS files of all the cases