1.What are the drawing templates?
A) Drawing Templates:
If compared with the verbal or written description, drawing offers a far better idea about the shape, size & appearance of any object or simulation or location, that too in quite less time. Hence it has become the best media of communication not only in engineering but in almost all fields.
Drawing templates:
- Drawing templates are basically the drawing standards as per the customer’s specifications.
- Drawing templates are a format that is used for detailing different parts or units of the fixture.
- A drawing template file is a drawing file that has been saved with a .dwt file extension, and it specifies the styles, settings, and layouts in a drawing, including title blocks.
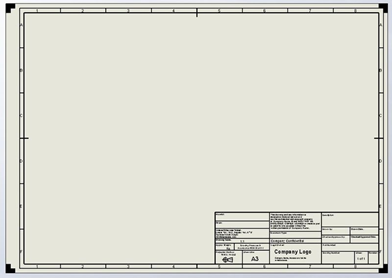
- There are ‘n’ numbers of details that are already available on the template & are useful for various manufacturing processes, such as, machining finish, tolerances, surface treatments, material, name of the parts, name of the assemblies, etc.
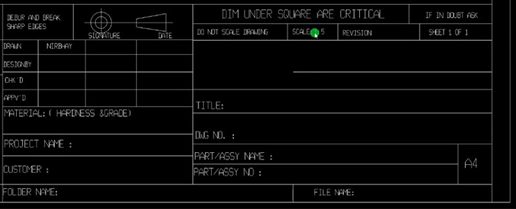
- Preparing a drawing template at the start of the project can help us save time, as these templates can be used as a starter model for detailing for different parts.
- Drawing templates also give information about the angle of projection to be used, views to be considered, scaling of the drawing as per the part or unit.
- A separate template is prepared for each sheet size like A1, A2, A3, A4 & so on.
Drawing templates may be referenced when creating a new drawing. They automatically create the views, set the desired view display, create snap lines, and show model dimensions based on the template.
Drawing templates contain three basic types of information for creating new drawings.
- The first type is basic information that makes up a drawing but is not dependent on the drawing model, such as notes, symbols, and so This information is copied from the template into the new drawing.
- The second type is instructions used to configure drawing views and the actions that are performed on that The instructions are used to build a new drawing with a new drawing object.
- The third type is parametric Parametric notes are notes that update to new drawing model parameters and dimension values. The notes are re-parsed or updated when the template is instantiated.
Use the templates to:
- Define the layout of views.
- Set view display.
- Place notes.
- Place symbols.
- Define tables.
- Show dimensions.
You can also create customized drawing templates for the different types of drawings that you create. For example, you can create a template for a machined part versus a cast part. The machined part template could define the views that are typically placed for a drawing of a machined part, set the view display of each view, place company standard machining notes, and automatically create snap lines for placing dimensions. Creating a template allows you to create portions of drawings automatically, using the customizable template.
Drawing templates has n number of information such as:
- Company name.
- Project Name.
- Sheet size.
- Sheet number.
- The angle of projection.
- Revision Number/latter (if its revision drawing)
- Signature or name of drawn by, checked by, responsible engineer, and approved by.
- Parts detail.
- Quantity.
- Additional notes (Surface finish, heat treatment, material detail, etc.).
- Scale, date, unit of measurement.
2)What do you understand by angle of projection?
A) The angle of projection:
- The angle at which an observer draws an object to convert it from 3D to a 2D plane such as a real object image to a plain paper is known as the angle of projection.
- This is such a type of drawing in which Parallel Projection is used for the preparation of the drawing of an object.
- These lines are perpendicular to the plane.
- In this drawing, it is assumed that the object is at infinity.
- The shape of an object is seen in actual size in such a drawing.
- A plane is an imaginary surface on which pictures are prepared imaginably. Then it is transferred to the paper.
- This plane is faced toward the object whose view is to be prepared.
- Generally, three views of an object are prepared. These are Top View, Front View, and Side View.
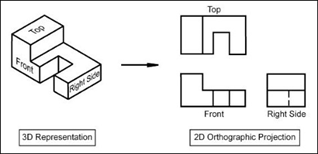
- If the plane is kept in a vertical position, then it is called the vertical plane.
- If the plane is kept in a horizontal position, then it is called the horizontal plane.
- The plane, horizontal or vertical, which are kept perpendicular to each other are called Principal Planes.
- These include the Frontal Plane, Profile Plane, and Horizontal Plane: In addition to this, if a plane is placed at any other place, then it is called an Auxiliary plane.
- These are used to draw inclined surfaces of an object. If these are placed in such a way that they form four Quadrants, then this figure is called the Dihedral angle.
- If these are placed in such a way that they form eight quadrants, then this figure is called the Trihedral angle.
- If the first Quadrant is used to draw the projections, then this system is called First Angle System.
- If the third quadrant is used, then this system is called the Third Angle System.
- In the First Angle System, the top view is placed below while the front view is upward and the side view is by the side of the front view.
- In the Third Angle System, the top view is upward while the front view is downward and the side view is towards, aside from the front view.
Views of Orthographic Projection.
Following views are formed of an object in Orthographic Projection.
- Front View.
- Top View.
- Back View.
- Bottom View.
- Right Side View.
- Left Side View.
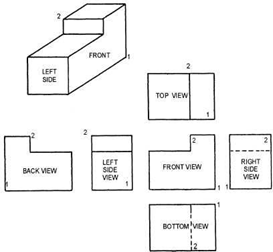
Generally, the Following Three views are prepared in the orthographic drawing.
1. Front View:
- This view is prepared by placing the object in front. The length and height of an object are shown in this view.
2. Top View:
- This view is prepared by looking at the object from the upper side. The length and breadth of the object are shown in it.
3. Side View:
- This view is prepared by looking at the object from the right side or left side. The breadth and height of the object are shown in it.
Principal Plane.
- A plane is an imaginary and invisible clear surface. The drawing constructed on this imaginary curtain is transferred on the drawing sheet.
- For example, if we look at some object through glass or plastic pieces, then the picture of the object will be seen there. This piece will work as a plane.
- However, this plane is not a material body.
- It is only an imaginary curtain, which is used to give the shape of a drawing by placing it in different positions. This plane can be put in different positions.
However, the plane placed in the following positions is called the Principal Plane. Besides such positions, the plane will be called Auxiliary Plane.
- Frontal Plane.
- Profile Plane.
- Horizontal Plane.
1. Frontal
- Such a plane that is placed in front of an object, while projections are drawn, is called the Frontal plane.
2. Profile
- Such a plane is placed to the right or left of an object. A side view of the object is drawn on this plane.
3.Horizontal
- This is a plane that is placed upward or downward in the horizontal position of an object. The top view of the object is constructed on this plane.
Drawing of Orthographic Projection.
For drawing Orthographic Projection, different planes are placed in a particular order. Then a specific view is drawn through every plane.
A plane is placed in the following two Methods.
- Dihedral Angle.
- Trihedral Angle.
1. Dihedral
- In this method, two principal planes are kept perpendicular to each other. One of these planes is Frontal, while the other is horizontal.
- Four right angles are obtained in this way which is called Dihedral Angle.
- Each right angle is called a quadrant. The object is placed in any of these right angles to take orthographic projection.
- The front view is taken on the frontal plane, and the top view is taken on the horizontal plane.
- Profile plane is used to take side views.
- This plane is held perpendicular at the ends of the other two planes.
2. Trihedral
- In this method, all the three Principal planes are taken perpendicular to one another, and eight right angles are formed. Thus, these are called Trihedral angles.
- Each right angle is called an Octant. An object is placed in any of these right angles to take orthographic projection.
- The front view is taken on the frontal plane, and the top view is taken on the horizontal plane. Profile plane is used to take side views.
Systems of Orthographic Projection.
To prepare an orthographic drawing, the selection of one quadrant of dihedral and or one octant of a trihedral angle is made.
In this way the following four systems are formed:
- First Angle System.
- Second Angle System.
- Third Angle System.
- Fourth Angle System.
Generally, First Angle System and Third Angle System are used. It is because in the Second Angle System and Fourth Angle System, the lines of view of the object overlap.
Therefore, clear pictures cannot be obtained.
1.First Angle System:
- The views of an object should be taken by placing it in the first quadrant of dihedral and or first octant of a trihedral angle. Such a system is called First Angle System.
- By taking the Front view on the frontal plane, top view on the horizontal plane, and side view on the Profile plane, the planes are then straightened by rotation.
- In this way, the front view comes over the top view; the side view comes beside the front view.
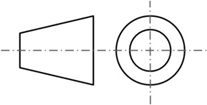
Characteristics of First Angle Projection:
- The front view always comes over the top view.
- The top view always comes under the front view.
- The right side view always comes to the left at the front view.
- The left side view always comes to the right of the front view.
- The view is always in opposite direction to the observer.
- The object is always in the middle of the view and the observer.
2.Third Angle System:
- If the views of an object are taken by placing it in the third quadrant of dihedral or third octant of a trihedral tingle. Such a system is called Third Angle System.
- Here, the front view forms on the frontal plane, the top view forms on the horizontal plane, and the side view from on the profile plane. After making the views, the planes are set straight by rotation.
- In this way, the top view comes over the front view, while the side view forms by the side of the front view.
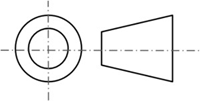
Characteristics of Third Angle Projection:
- The top view always comes over the Front view.
- The front view always comes under the top view.
- The right side view always comes to the right of the front view.
- The left side view always comes to the left of the front view.
- The view is always formed to the side of the observer.
- The view is always in the middle of the object and the observer.
Rules of Orthographic Drawing:
Following rules should be followed while forming orthographic drawings.
- The front view and top view always form over/under each other.
- The front view shows the length and height of an object.
- The side view shows the breadth and height of an object.
- The top view shows the length and breadth of an object.
- The side view always forms beside the front view.
- The projection line always forms by the meeting of two surfaces.
- The hidden detail of an object is always shown by a dotted line.
Selection of View:
Following points should be kept in mind at the selection of view,
- A more detailed view should be selected.
- The selection of views with maximum detail should be made.
- The selection of views with more internal details should be made.
- The selection of view of required details should be made.
3)What is the First angle & Third angle projection? and why can't we use the 2nd and 4th angle of projection?
A)
The orthographic projection system is used to represent a 3D object in a 2D plane. The orthographic projection system utilizes parallel lines, to project 3D object views onto a 2D plane. According to the rule of orthographic projection. To draw a projection view of a 3D object on a 2D Plane. The horizontal plane is rotated in the clockwise direction.
Types of Orthographic projection systems are first angle and third angle projection.
First Angle Projection:
In the first angle projection, the object is placed in the 1st quadrant. The object is positioned at the front of a vertical plane and top of the horizontal plane. First angle projection is widely used in India and European countries. The object is placed between the observer and projection planes. The plane of projection is taken solid in 1st angle projection.
Third Angle Projection:
In the third angle projection, the object is placed in the third quadrant. The object is placed behind the vertical planes and the bottom of the horizontal plane. Third angle projection is widely used in the United States. The projection planes come between the object and the observer. The plane of projection is taken as transparent in 3rd angle projection.
Difference between First Angle Projection and Third Angle Projection:
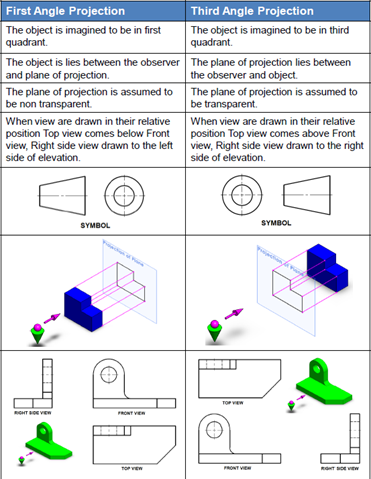
Following are the detailed description of first angle projection vs third angle projection gave in-text notes from the above table for better readability.
First Angle Projection:
- The object is imagined to be in the first quadrant.
- The object is lies between the observer and the plane of projection.
- The plane of projection is assumed to be non-transparent.
- When the view is drawn in their relative position Top view comes below the Front view, the Right side view drawn to the left side of elevation.
- A First Angle Projection drawing is identified by the first angle projection symbol. The angle of projection symbol typically appears in the angle of the projection block near to Title block.
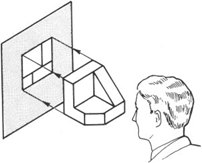
Third Angle Projection:
- The object is imagined to be in the third quadrant.
- The plane of projection lies between the observer and the object.
- The plane of projection is assumed to be transparent.
- When the view is drawn in their relative position Top view comes above the Front view, the Right side view drawn to the light side of the elevation.
- A Third Angle Projection drawing is identified by the third-angle projection symbol. The angle of projection symbol typically appears in the angle of the projection block near to Title block.
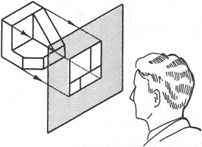
Differences between First and third angle Projection on basis of comparison:
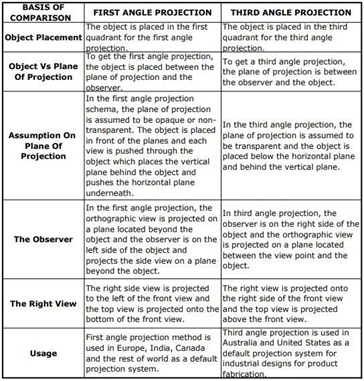
Similarities Between First Angle and Third Angle Projection
- Both are graphical methods used in engineering drawings.
- Both are schemes used for Multi-view projection of three-dimensional objects using a series of two-dimensional drawings.
- Both methods of orthographic projection result in the same six principal views of the object except the arrangement of views and the state of the plane of projection.
- Both are used to obtain engineering drawings for clarity.
Reason for not using Second and Fourth Angle Projection:
The second and fourth angle projection system has some limitations. Therefore only First and Third angle projection Systems are used to prepare engineering drawings.
To understand why 2nd and 4th angle projection are not used? Firstly we need to understand the concept behind the orthographic projection system.
How does Projection System work?
Let’s consider a point in A and B in the 1st and 3rd quadrant respectively. As per the rule of projection, to bring drawing views from three-dimensional to two-dimensional planes. The horizontal plane (HP) is rotated in the clockwise direction.
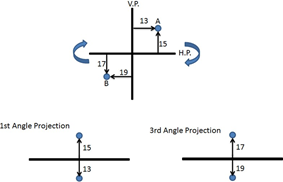
As shown, Point A in the 1st quadrant lies in between the observer and projection plane. Therefore, the Front view of point A will be in a vertical plane (V.P.) and the top view will be on a horizontal plane.
Similarly, Point B in the 3rd quadrant can be projected on the horizontal and vertical plane.
Why Second and Fourth angle Projection Systems are not used?
To understand why the 2nd and 4th angle projection systems are not used. We will repeat the above experiment in the second and fourth quadrant.
Let’s consider rectangular parts X and Y are placed in the 2nd and 4th quadrant respectively.
In the second quadrant, the vertical plane (VP) lies in between object X and the observer. Therefore, the front view of object x will lie on a vertical plane whereas the top view will lie on a horizontal plane. As per the rule of projection when a horizontal plane is rotated 90 degrees in a clockwise direction, the top and front views will overlap.

Overlapping projection views create confusion in the drawing. Therefore the 2nd angle projection system is not used.
Similarly, when the object is placed in the 4th quadrant both the top and front views will overlap. Therefore, fourth angle projection is also not used.
Hence, Because of the overlapping of front and top views 2nd and 4th angle projections are not used.
4)What is GD&T? What are the Benefits of GD&T?
A) Geometric Dimensioning and Tolerancing (GD&T):
Geometric Dimensioning and Tolerancing (GD&T) is a system for defining and communicating engineering tolerances. It uses symbolic language on engineering drawings and computer-generated three-dimensional solid models that explicitly describe nominal geometry and its allowable variation. It tells the manufacturing staff and machines what degree of accuracy and precision is needed on each controlled feature of the part. GD&T is used to define the nominal (theoretically perfect) geometry of parts and assemblies, to define the allowable variation in form and possible size of individual features, and to define the allowable variation between features.
- Dimensioning specifications define the nominal, as-modeled, or as-intended geometry. One example is a basic dimension.
- Tolerancing specifications define the allowable variation for the form and possibly the size of individual features, and the allowable variation in orientation and location between features. Two examples are linear dimensions and feature control frames using a datum reference.
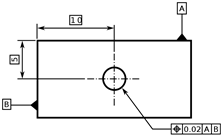
There are some fundamental rules that need to be applied:
- All dimensions must have a tolerance. Every feature on every manufactured part is subject to variation, therefore, the limits of allowable variation must be specified. Plus, and minus tolerances may be applied directly to dimensions or applied from a general tolerance block or general note. For basic dimensions, geometric tolerances are indirectly applied in a related Feature Control Frame. The only exceptions are for dimensions marked as a minimum, maximum, stock, or reference.
- Dimensions define the nominal geometry and allowable variation. Measurement and scaling of the drawing are not allowed except in certain cases.
- Engineering drawings define the requirements of finished parts. Every dimension and tolerance required to define the finished part shall be shown on the drawing. If additional dimensions would be helpful but are not required, they may be marked as references.
- Dimensions should be applied to features and arranged in such a way as to represent the function of the features. Additionally, dimensions should not be subject to more than one interpretation.
- Descriptions of manufacturing methods should be avoided. The geometry should be described without explicitly defining the method of manufacture.
- If certain sizes are required during manufacturing but are not required in the final geometry they should be marked as non-mandatory.
- All dimensions and tolerance should be arranged for maximum readability and should be applied to visible lines in true profiles.
- When geometry is normally controlled by gage sizes or by code, the dimension shall be included with the Gage or code number in parentheses following or below the dimension.
- Angles of 90° are assumed when lines are shown at right angles, but no angular dimension is explicitly shown. (This also applies to other orthogonal angles of 0°, 180°, 270°, etc.)
- Dimensions and tolerances are valid at 20 °C (68 °F) and 101.3 kPa (14.69 psi) unless stated otherwise.
- Unless explicitly stated, all dimensions and tolerances are only valid when the item is in a free state.
- Dimensions and tolerances apply to the length, width, and depth of a feature including form variation.
- Dimensions and tolerances only apply at the level of the drawing where they are specified. It is not mandatory that they apply at other drawing levels unless the specifications are repeated on the higher-level drawing.
Benefits of GD & T :
- Saving Money: GD&T enhances design accuracy by allowing for appropriate tolerances that maximize production. For many projects, the process provides extra or bonus tolerances, further increasing cost-effectiveness.
- Ensuring Dimensional and Tolerance Requirements: By explicitly stating all design requirements, a thorough GD&T process guarantees accurate fulfillment of all dimensional and tolerance specifications.
- Assisting Digital Design Methods: Clear, concise GD&T data is readily adaptable to digital design programs, including nearly universally used 2D and 3D CAD files.
- Offering Uniformity and Convenience: As a single, consistent language, GD&T reduces guesswork and interpretation while ensuring consistent geometries across design and manufacturing.
- Providing Accurate Communication: Today’s intricate designs demand the most accurate and reliable communication. GD&T enables designers, manufacturers, and inspectors to communicate clearly with one other, saving time and making the process more efficient.
5) Explain all the symbols used in GD&T?
A) Symbols used in GD&T:
GD&T has 14 symbols out of which 10 are the most commonly used features. They are categorized base on a form, orientation, location, profile, and run out. They are described below.
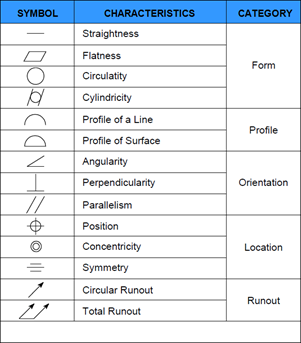
Form:
Form controls the shape of surfaces. It does allow datum reference.
1) Flatness
- In this feature, all the elements are supposed to be the same Flatness error is calculated by the difference in the highest and lowest points on the plane. You are trying to make sure that any point along the surface does not go above or below the tolerance zone. This feature doesn't require any reference.
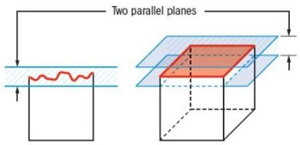
2) Straightness
- In this feature, all the elements are supposed to be in a straight It is used for a line to communicate the variation allowed in a line, hence maintaining it straight. It doesn't require a datum. If it is to be used for a cylinder, it is given along with the diameter dimension. It controls each dimension separately.
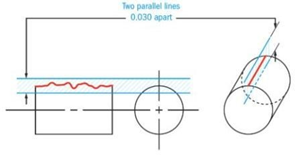
3) Cylindricity
- This feature ensures that the surface of the cylinder is smooth and within the tolerance, Each surface is at a fixed distance from the axis of the cylinder in this feature. It does not require a datum.
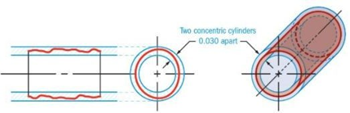
4) Circularity
- Circularity requires no Circularity ensures all the points to be equidistant from the center. Circularity error is the radial distance between coaxial diameters. it limits the circularity error.
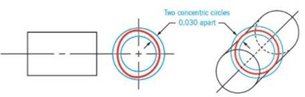
5) Perpendicularity
- When this feature is applied to a surface, the tolerance zone is between two parallel surfaces perpendicular to the datum It requires a datum surface.
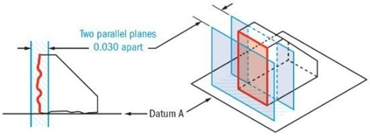
6) Parallelism
- When this feature is applied to a surface, the tolerance zone is between two parallel surfaces parallel to the datum It basically ensures that all the points on the referenced surface lie in the tolerance zone at a certain distance away from the datum surface. It also ensures that the surface to be referenced is parallel to the datum surface. Parallelism is quite simple to measure.
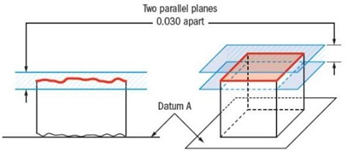
7) Angularity
- Angularity is a feature that is specified between two It requires a datum reference from which the angular tolerance is maintained. In the case of a plane, the angularity feature maintains the angular tolerance between two planes.
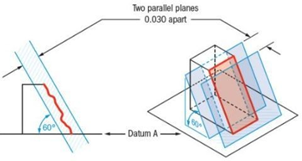
8) Position
- Position tolerance shows the exact location of a FOS(a feature of size) with respect to an It tells us how far a feature location can vary from its true position. It requires datum for reference.
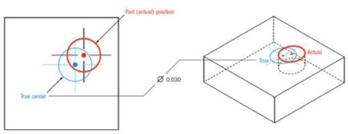
Profile:
9) Profile of a surface
- Profile of a line is usually used at a place where we require a surface to be in the tolerance In this case, the profile directly mimics the design of the surface. Every point of the surface should fall within the tolerance zone. For example, if a callout is given on the fillet of a weldment, each point on the surface should fall in the tolerance zone. It is used only for advanced curve surfaces. A CMM is used to track the entire surface.
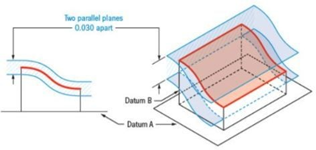
10) Profile of Line
- This feature is used at places where a curve is to be maintained within the tolerance The tolerance zone is two parallel curves from the main curve. It is used for advanced curves. This tolerance zone may or may not be referenced by a datum.
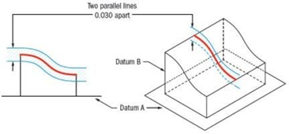
Runout:
11) Total Runout
- Total Runout is how much a surface or feature varies with respect to a datum when the part is rotated 360 degrees about datum It controls both amounts of variation in the surface when the part is rotated and also the variation in the axial dimension.
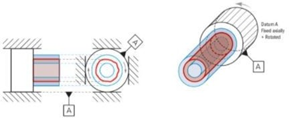
12) Circular Runout
- Runout feature is used to check how much one feature of a part varies with respect to another when the part is rotated about a datum It is basically used to check how much a part wobbles. Runout can be called out on any feature that is rotated about an axis. Runout is measured using a simple height gauge on the reference surface.
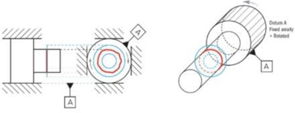
Location(Derived Median points):
13) Concentricity
- The concentricity feature ensures the smoothness of a cylindrical surface with respect to a datum A surface is chosen as a datum. The axis about which this surface acts as a datum axis for the feature we wish to control. The feature must fall in the tolerance zone. It is very difficult to maintain concentricity as it is not to be checked directly w.r.t a surface but w.r.t an axis derived from another surface.
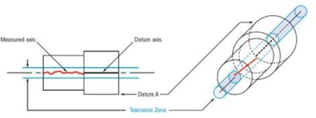
14) Symmetry
- Symmetry feature ensures symmetry of a 3d object about a virtual datum Points from either surface are calculated using the CMM and checked if they fall in the positive and negative side of the tolerance zone. Symmetry is very difficult to calculate as it does not have a fixed surface about which we can check the deviation.
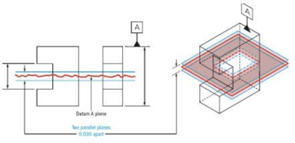
Some other symbols used in GD&T other than the above:
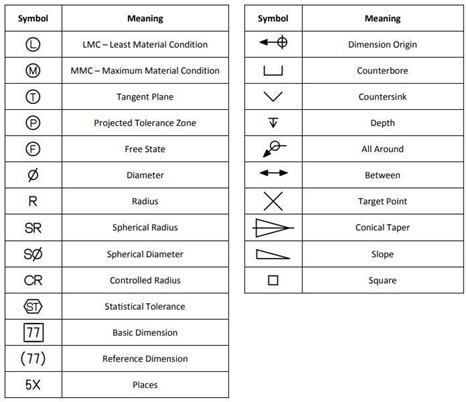