OBJECTIVE:
The main aim of this project is to connect the FE model of the rear door of a car in Nastran deck for NVH domain.
PRE-REQUISITES:
- NVH domain study about the natural frequency of the body at which it vibrates, so for the basic simulation mechanisms in the system are not need to be defined (case specific).
- Basically, the model has to be rigid for the NVH analysis, so the parts that undergoes mechanism can be connected using rigids like RBE2.
- The rear door itself is a system that houses subsystems like Hinge mechanism, lock mechanism, door glass slider mechanism etc.
- The components like glass are bit complicated to connect, since it is a brittle material it cannot be bolted or joined by adhesives in door.
- But in car we have windshield and rear glass, to join that type of glasses adhesives can be used since those are not movable glasses.
- But in doors, we have movable glasses with the mechanism to move up and down, so it is important to model with the mechanism.
- The motors for that mechanism can be modeled as fixed mass for the analysis, it is not important to model as a structural part.
- The door glasses will be modeled in closed position, the rubber beads around the window glass technically called as weather strips which restricts the heat transfer between the cabin and outside the atmosphere.
- The rubber strips are soft in nature, it has damping factor prevents the glass from damage.
- In order to achieve all these, we have different t types of connections like seam weld, bolt joints, spot joints, rigid joints to prepare Nastran deck for NVH analysis.
PROCEDURE:
- Imported the Nastran file .nas in the ANSA GUI using file>input>Nastran.
- The parts in the given rear door model with one property card are shown below,
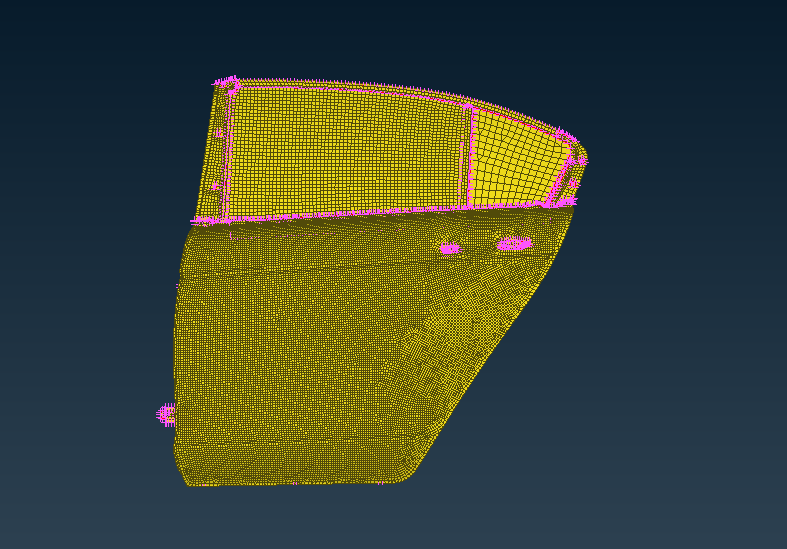
- To provide connections, it is important to organize the parts with separate property cards as shown below,
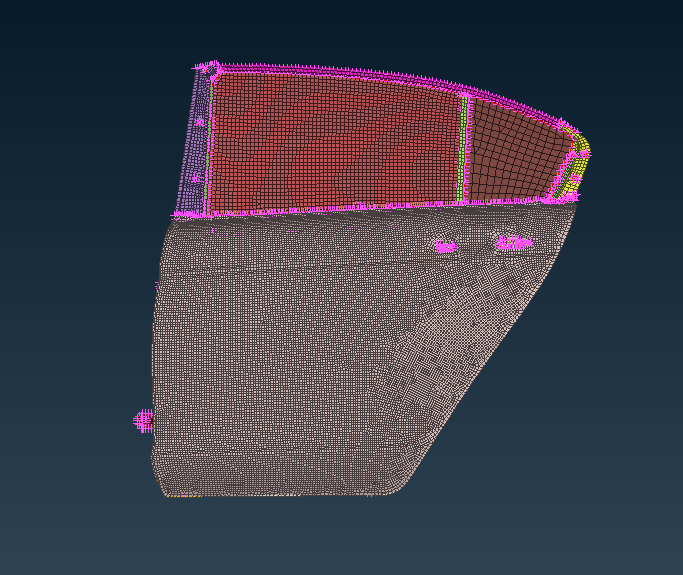
Hinge connection:
- The Hinges are the area where the door clings to body, which the help of bolt connections.
- The bolts can be represented as rigids, it can be modeled with RBE2 elements.
- Here, the automatic blot representation method is used.
- To create that, a 3D point has to be created on the hole COG as shown below using Topo>points>on COG.
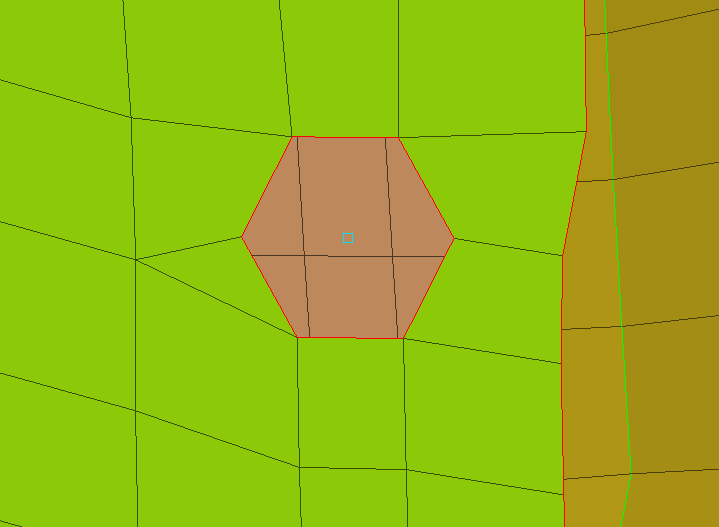
- Then the 3D point has to be converted as blot representation using convert>3D point>bolts in assembly toolbar as shown below,
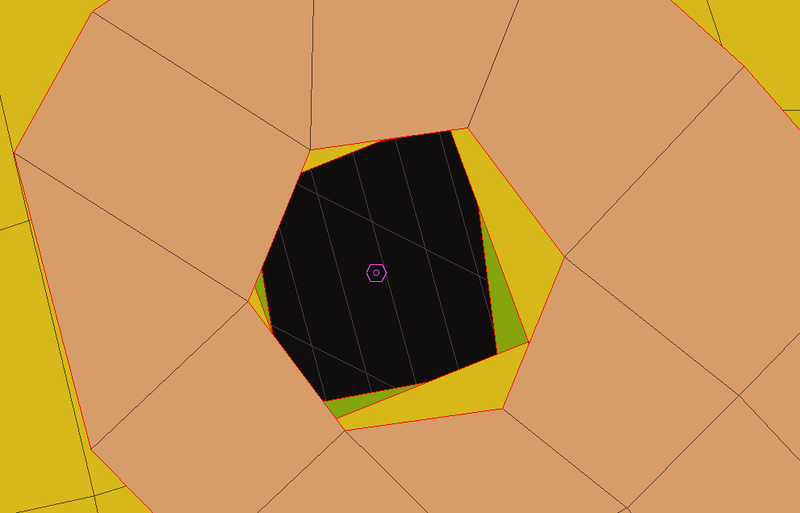
- Then the connection manager in the assembly toolbar is used and required inputs are provided for the bolt representation as shown below,
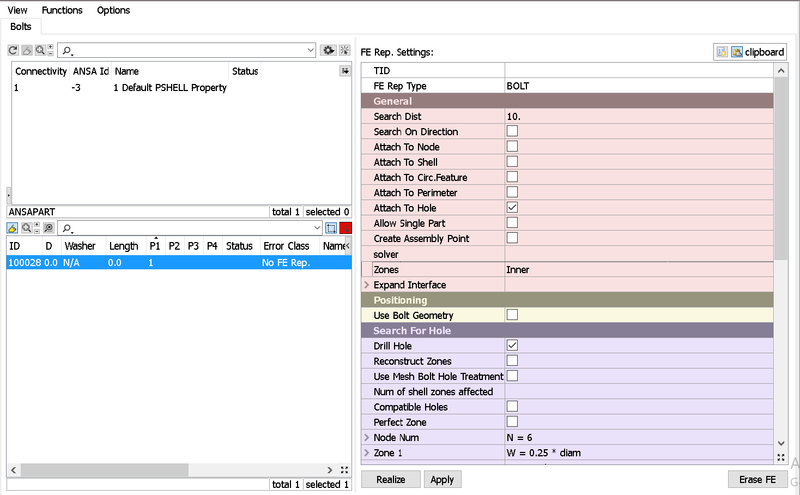
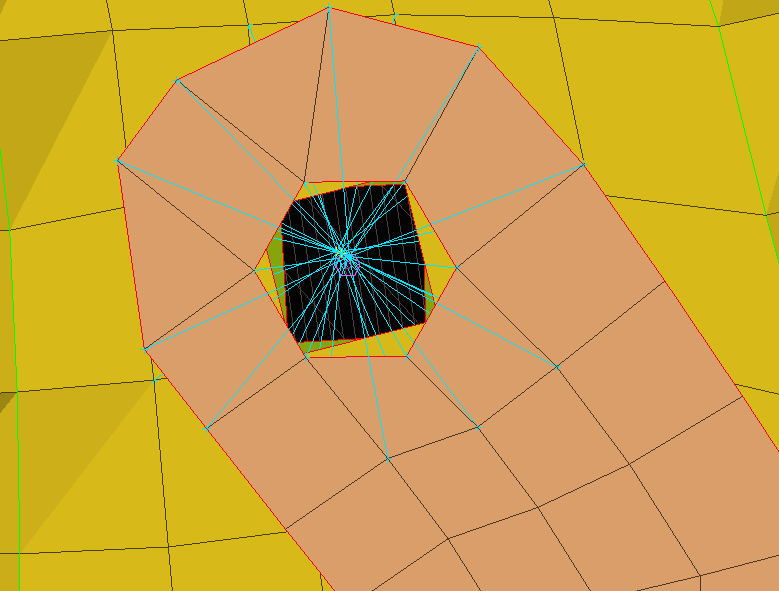
- The hinge part that is connected with the body, has not be constrained in all DOF, since it has the movement for opening and closing the door.
- The region is modeled with the rigids manually using Nastran deck>elements>RBE2 as shown below,
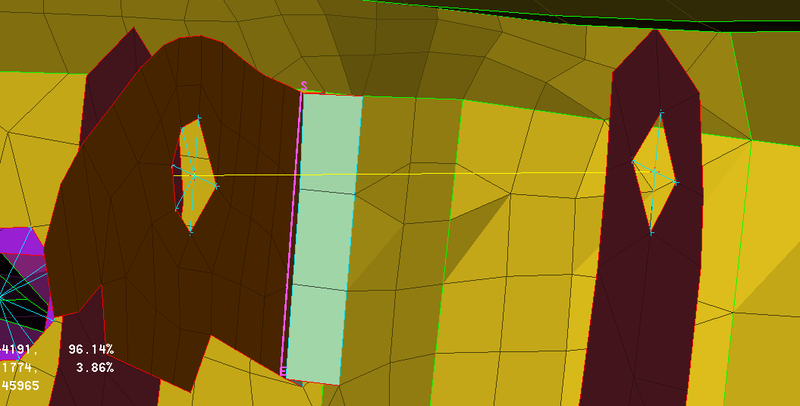
- The opening and closing movement can be made possible by using Nastran> elements>RBE2>two nodes and by setting coordinate movements as 12345.
- Where 12345 represents, the translation in x, y, z axes and the rotation about x, y axes are constrained.
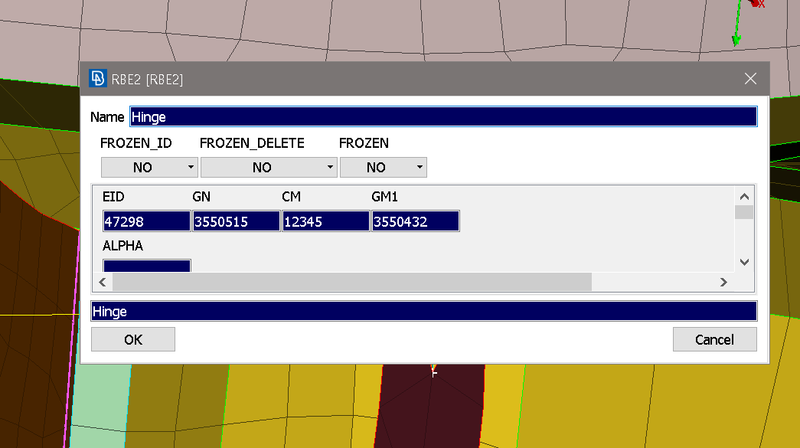
Manual Bolt connection:
- Bolt connections are provided to the holes, where the parts are to be connected with bolts.
- That can be identified when the part holes are located next to each other.
- It is recommended that the bolt representation to the holes can be captured using washer split of one layer.
- Generally, bolts can be represented as cluster RBE2 as well as two node RBE2 connecting the master nodes of spider RBE2s.
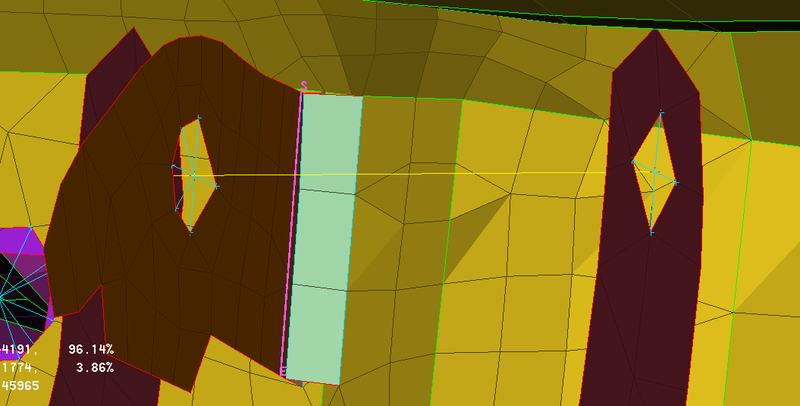
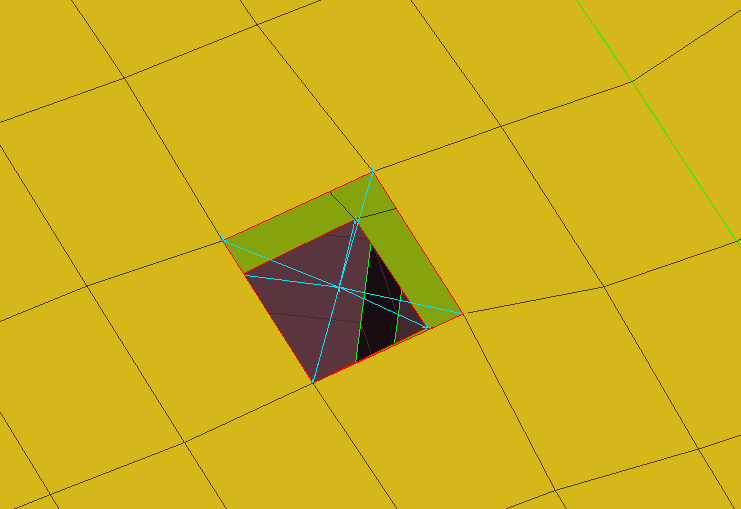
- Generally, these bolt representations are done manually using Nastran deck>elements>RBE2.
Door rail mechanism:
- The rail component is connected to the inner panel using the cluster RBE2 as shown below,
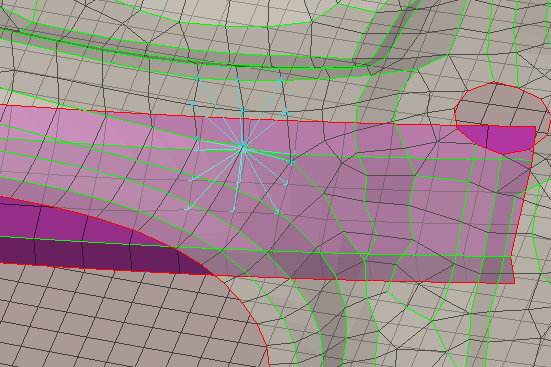
- The spot welds are used to connect the bracket of the mechanism to the inner panel.
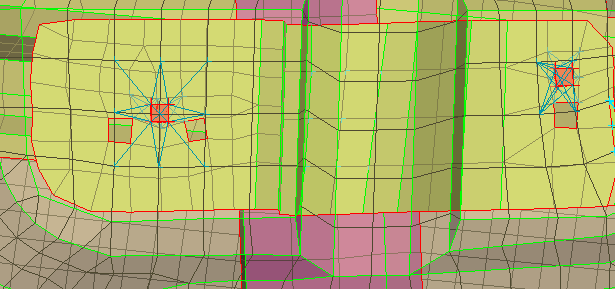
- To model the door glass rigidly, the rail frame is extended using mesh>grids>move free option, this is an adjustment has to done for FE modelling.
- After that the extended elements are reconstructed and connected with the glass with rigids RBE2 as shown below,
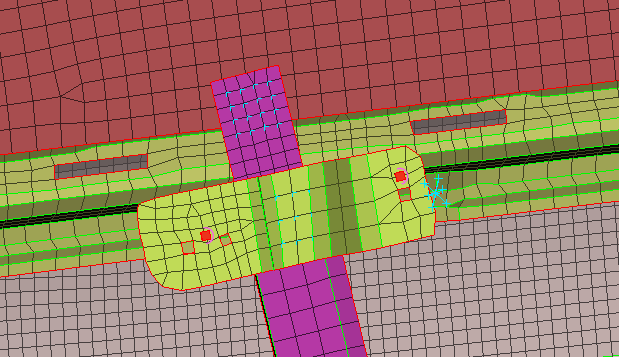
Spot weld connection:
- Spot welds are used to connect the parts at the point.
- In ANSA, the spot welds are represented as RBE3 elements with solid element connecting the parts.
- Difference between the RBE2 and RBE3 elements is, in cluster RBE2 the slave nodes forms the spider and the master node at the center but in RBE3, the master nodes connects the node spots and slave node at the center connect the parts.
- To create that, a 3D point has to be created at an element COG as shown below using Topo>points>on COG.
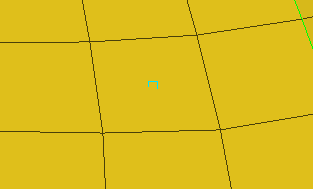
- Then the 3D point has to be converted as spot point representation using convert>3D point>bolts in assembly toolbar as shown below,
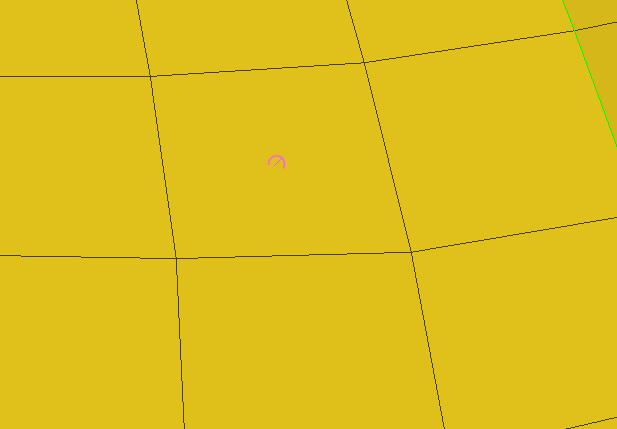
- Then the connection manager in the assembly toolbar is used and required inputs are provided for the spot weld representation as shown below,
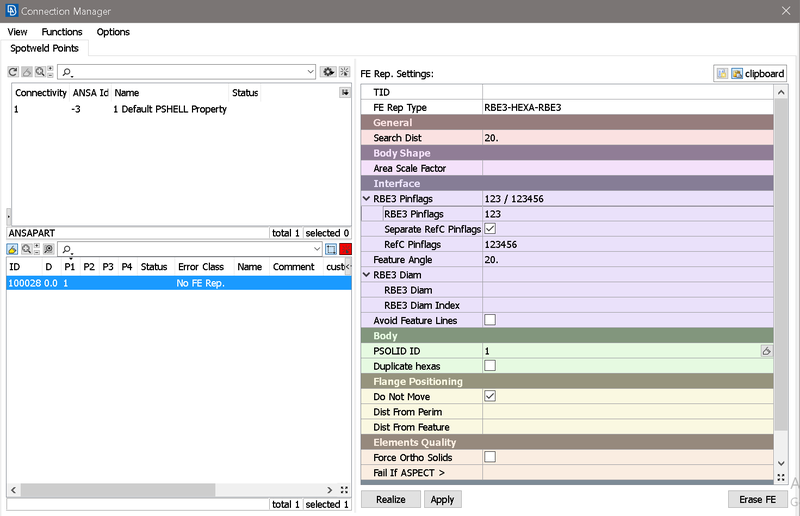
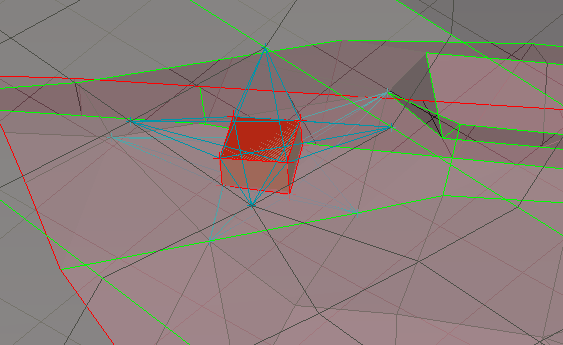
Door handle:
- Generally, Door handle is modeled as fixed mass element, the complete structural modeling of the handle is not done for FE modeling.
- The modeling of the handle is done by connecting two node rigid element to the master nodes of cluster rigids.
- It can be done using Nastran desk>elements> RBE2 as shown below,
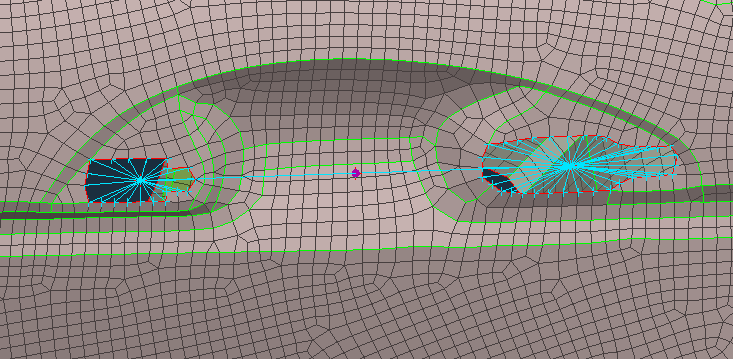
- The mass of the handle 100 grams is applied to the master node of the two node rigid element.
- That can be done using CONMi>CONM2>nodes in Nastran deck under elements.
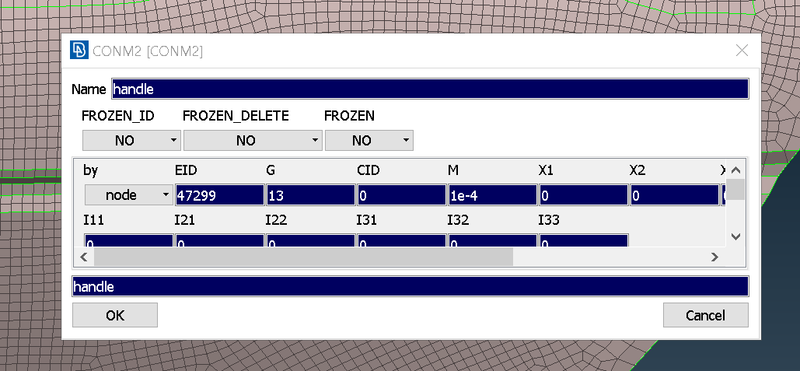
- Here, the weight of the handle has mentioned in tonnes.
Weatherstrip connection:
- The window glass line at the bottom is the region where the damping component present at both inner and outer side of the door.
- The other three peripheries acts as guides, where the glass slides. On those regions the connections are provided on the outer side only.
- To define the connection the outline of the glass element is taken using the mesh module>perimeters>feature2 curve
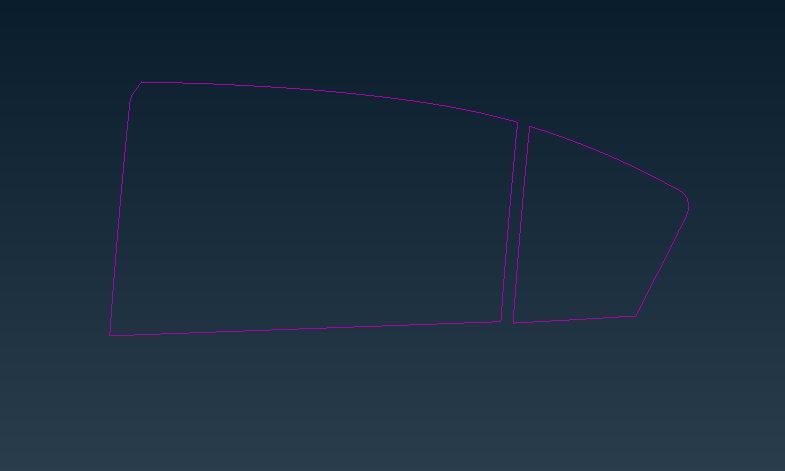
- The curves generated at the edges of the glass, are converted as spot lines using assembly toolbar as shown below,
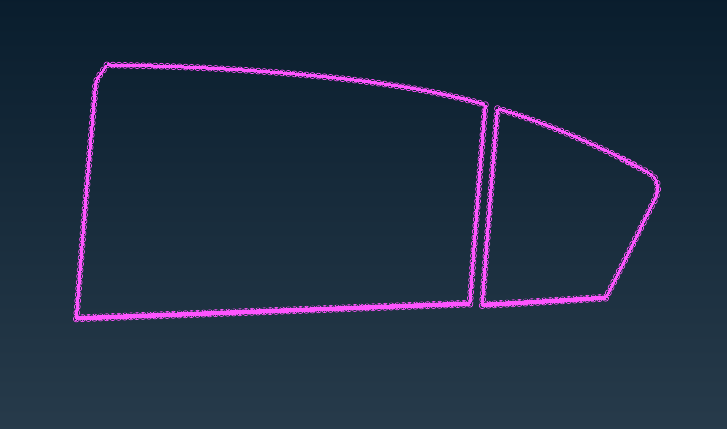
- Since, the glass line at the bottom has the connection from inner side, the curve generated as shown below with 5 mm distance in order to make the bush elements at the center,

- Then the connection manager in the assembly toolbar is used and required inputs are provided for the weather strip representation as shown below,
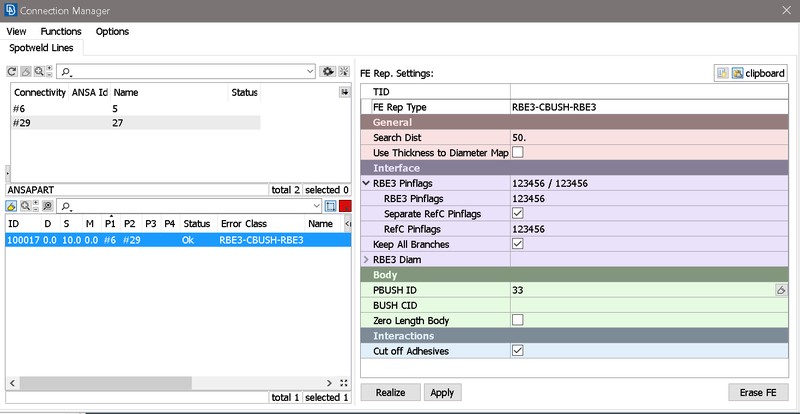
- When assigning the property id for Bush elements, the stiffness values has to be provided which is pre-calculated.
- Since, the bush elements is generally the spring element, it has damping coefficient and stiffness values in all three directions.
- The local coordinate of the bush elements can be converted to global coordinates using the modify option as shown below,
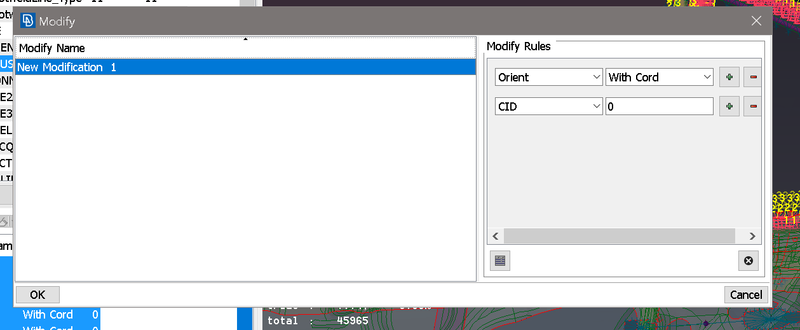
- The bush representation of the weather strip as shown below,
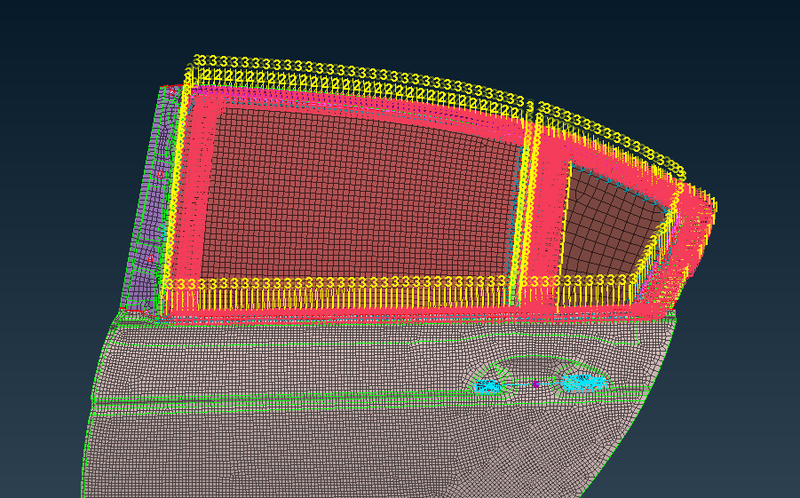
Seam weld:
- Seam weld is used to connect the parts in continuous seam line.
- It provides more structural rigidity to the system.
- To generate seam weld, the seam data has to be obtained and then curve is created along the length to represent the seam length.
- Then the curve has to converted into seam line using the assembly toolbar convert>curves> seam line.
- Then the seam line can be realized using connection manager from assembly toolbar and inputs are provided as shown below,
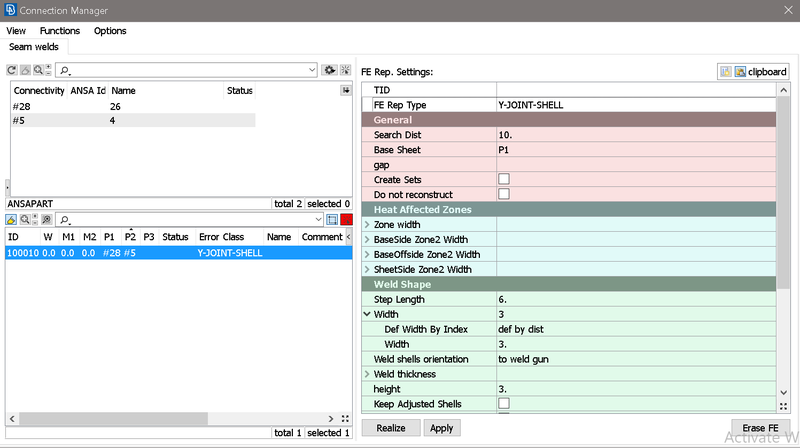
- The seam weld representation as follows,
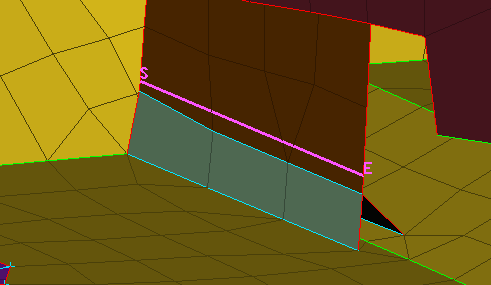
- Basically, if the parts are parallel to each other, then the FE rep type has to chosen as overlap shell.
- If the parts are perpendicular to each other, then the FE rep type has to chosen as Y-joint shell.
- Since here the parts are perpendicular the Y-joint shell type representation is used.
- The remaining areas in the model are connected with appropriate connectors.
- Finally, save the file.
RESULT:
Hence, the FE model of the rear door of a car is connected with appropriate connection in Nastran deck for NVH domain.
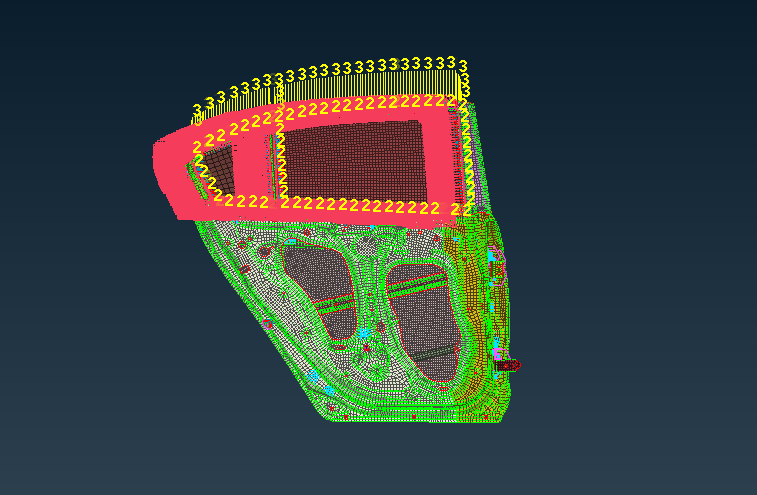
Link to view the model:
REAR DOOR CONNECTION