Static Structural Analysis on the Rolling Operation on a WorkPiece Made Up of Copper.
Aim :
- To perform Static Structural Analysis on the Rolling Operation on a WorkPiece made of Copper.
Objective :
- To make modifications to the rolling operation model in Space Claim.
- To define appropriate material to the Rolling Operation Model.
- To define connection between them.
- To perform mesh on the Rolling Operation Model
- To define appropriate Boundary Conditions to the Model.
- To request Directional Deformation in the Z axis for the workpiece
- To solve and compare the results of the three cases for Total Deformation, Von-Mises Stress and Equivalent Elastic Strain.
Theoretical FrameWork :
Rolling Process :
- Rolling is defined as a process to form metals where the metal strip is pressed by two or multiple rollers, thus the uniform thickness is formed. To do this, the temperature is essential.
- Rolling is the deformation process of a metal that is widely used in the metal forming process.
- It is done by passing the strip of the metal between the rollers. This paper discussion will be made about the rolling process, the working principle of the rolling process along with that the working principle of the rolling mills.
Working Principle of Rolling Process :
- The rolling process is a metal forming process, in which stock of the material is passed between one or more pairs of rollers in order to reduce and to maintain the uniform thickness.
- This process is mainly focused on the cross-section of the ingot or the metal which is forming. Mainly by this process, we reduce the thickness of the metal workpiece.
- Now, the rolling processes are mainly focused on the increasing length and the decreasing thickness without changing the width of the workpiece.
Types of Rolling Process :
Hot Rolling Process-
- In the hot rolling process, the metal is heated at its desirable temperature, when the metal is properly heated then the metal should be passed between the one or more rolling mills to gain the proper desirable shape.
Cold Rolling Process-
- This rolling process is done below the recrystallization temperature of the metal it varies upon the metal, room temperature can also be a below recrystallization temperature.
- In this process, the force is much more required than the hot working process to pass the metal from the rollers and this process offers good surface finish.
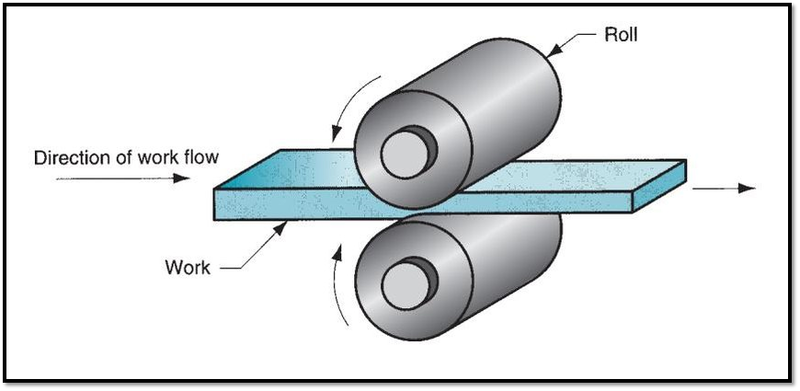
Figure 1-Rolling Process. |
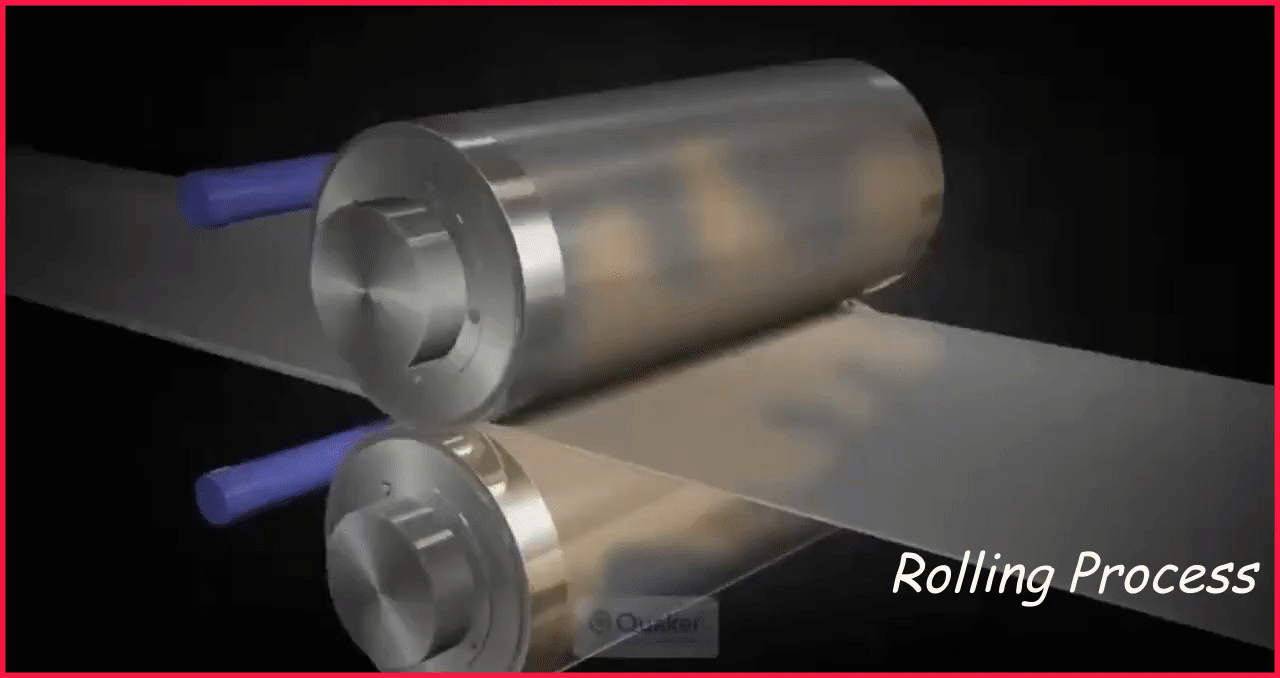
Figure 2-Rolling Process Animation. |
Procedure :
Phase 1- Material Set Up :
- To set up the material for the Rolling Operation Model. First, drag and drop the static structural analysis workspace into the project schematic from the analysis system. This is shown in below Figure 3.
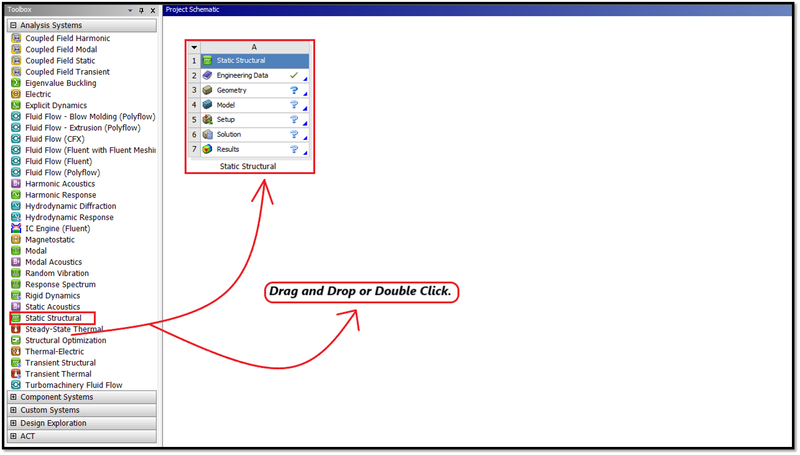
Figure 3-Ansys Workbench Workspace. |
- After deploying the static structural analysis system in the project schematic workspace.
- Define the Engineering Data and geometry, To define the Geometry and Engineering Data, Right Click on the Engineering Data and click to edit, it will take to the Engineering Tab.
- There Right Click on the Material Tab, A window will Pop-Up stating Engineering data sources.
- Click on the Engineering Data Sources, There go and select the material to define the engineering data. This is shown in below Figures 4,5,6.
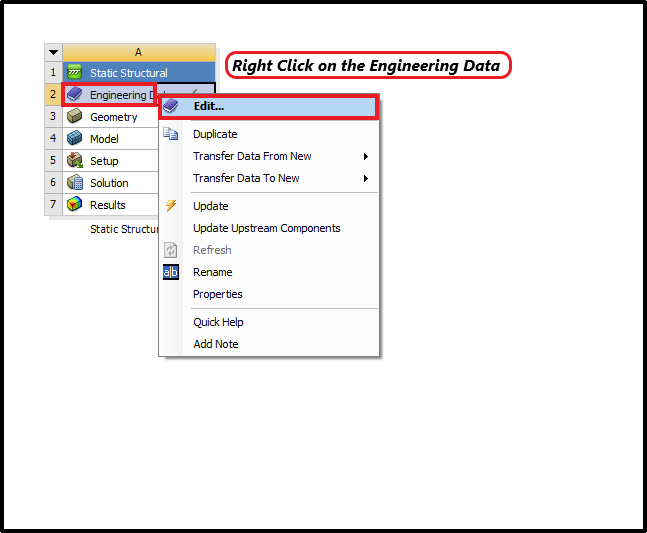
Figure 4-Right Click on the Engineering Data. |
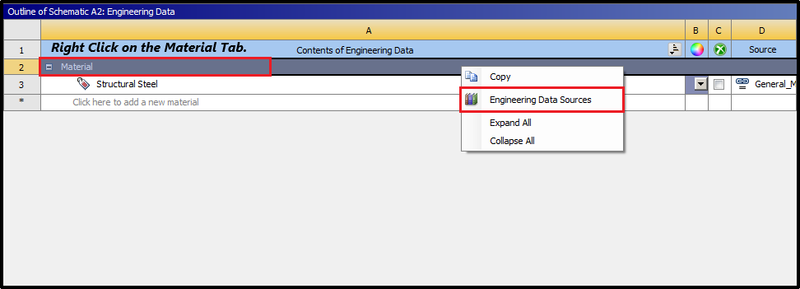
Figure 5-Right Click on the Material Tab. |
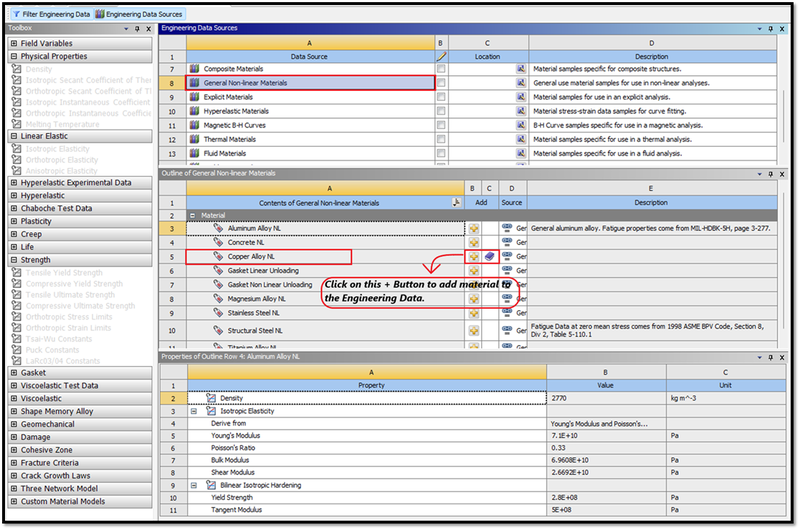
Figure 6-Select this Material to define the Model. |
Phase 2-Geometry Set Up :
- Next set up the geometry. To set up the geometry, Right-Click on the Geometry option >> Import Geometry. This is shown in below Figure 7.
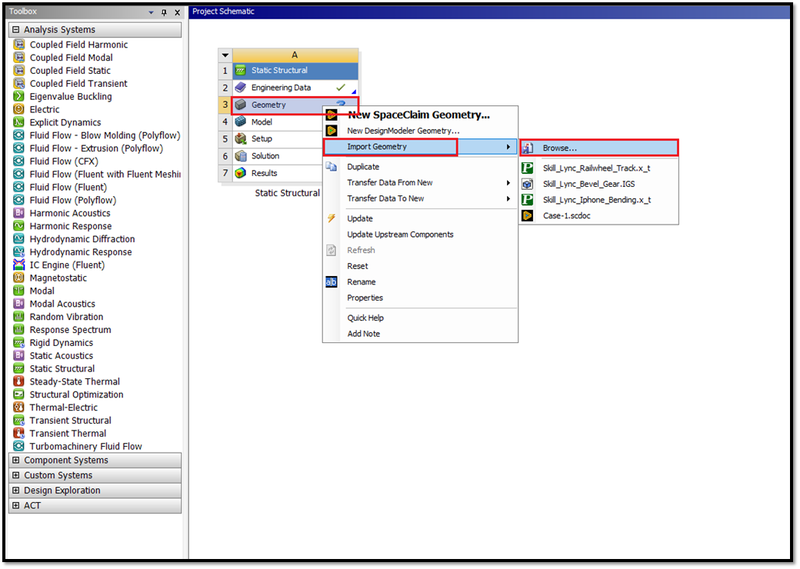
Figure 7-Importing Geometry. |
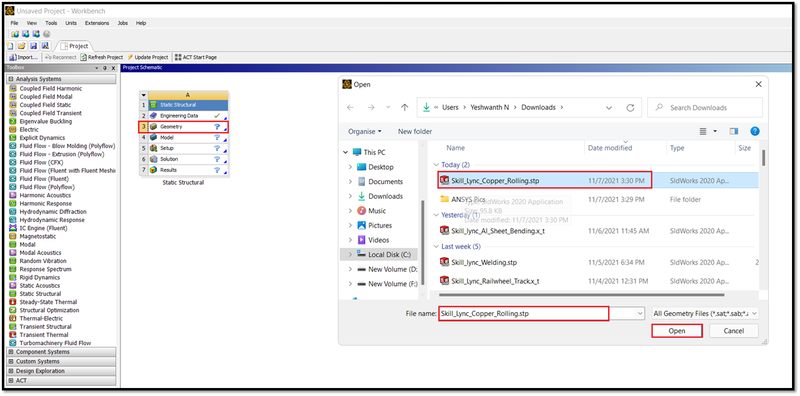
Figure 8-Selecting the Geometry to Import. |
- Next double click on the geometry to check, Whether the model imported is Sheet Metal Bending Model or not. Space Claim Workspace will open.The model will be imported in the space claim,Which is shown in below Figure 9.
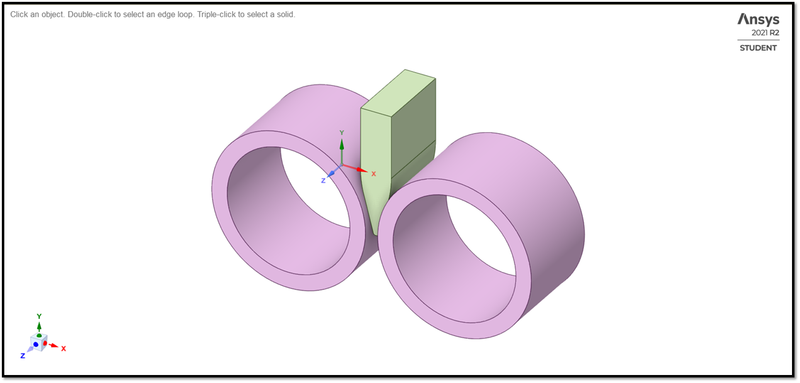
Figure 9-Rolling Operation Model in the Space Claim. |
- Here we have to increase the length of the workpiece by 60mm and decrease its size on both sides by 8mm.
- To increase the length of the workpeice >> Skectch >> Edit >> Pull >> Select the Face >> Drag Up >> Give Value as 60 mm >> Enter.Which is shown in below Figure 10.
- To decrease the length of the workpeice by both sides >> Skectch >> Edit >> Pull >> Select the both Faces >> Drag Up >> Give Value as 8 mm >> Enter.Which is shown in below Figure 11.
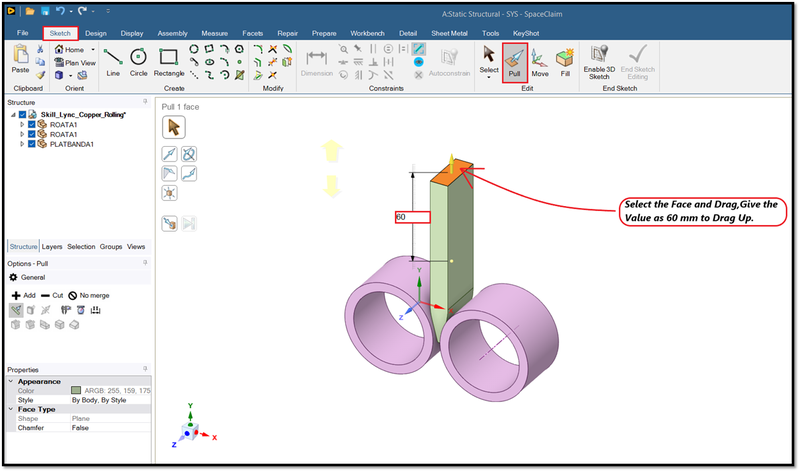
Figure 10-Increase the Length of Workpiece by 60 mm. |
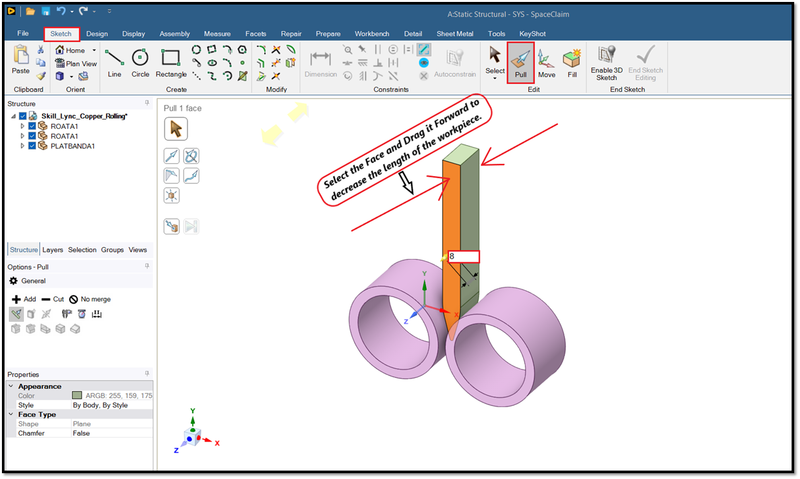
Figure 11-Decrease the Length of Workpiece by 8 mm. |
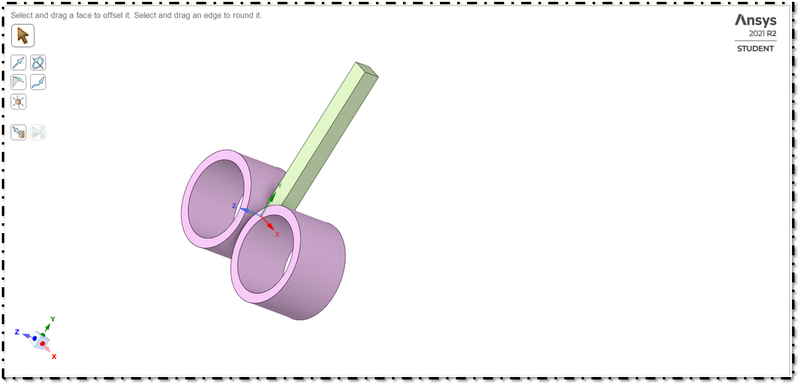
Figure 12-Increased and Decreased the Length of the Workpiece. |
Phase 3-Model Set Up :
- Next, define the model, Double click on the model, The Mechanical Workspace will open, There go and define the material,set up the load case for the model.
- The Model loaded in the mechanical workspace is shown in below Figure 13.
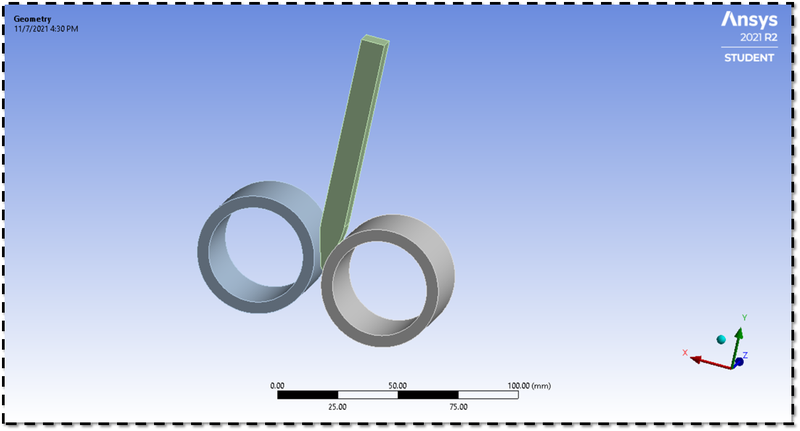
Figure 13-Model Loaded in Mechanical Workspace. |
3:1 Assign Material :
- Next define the material as Copper Alloy for the Workpiece which is shown in below Figure 14.
- Simillarly define the Structural Steel as material for the Wheel 1 and Wheel 2.The material properties is shown in below Figures 15 and 16.
- To assign a material,Click on the Geometry >>Select the Workpeice Geometry >> Parameter Window >> Assignment >>Copper Alloy.
- Simillarly assign for the Wheels also.
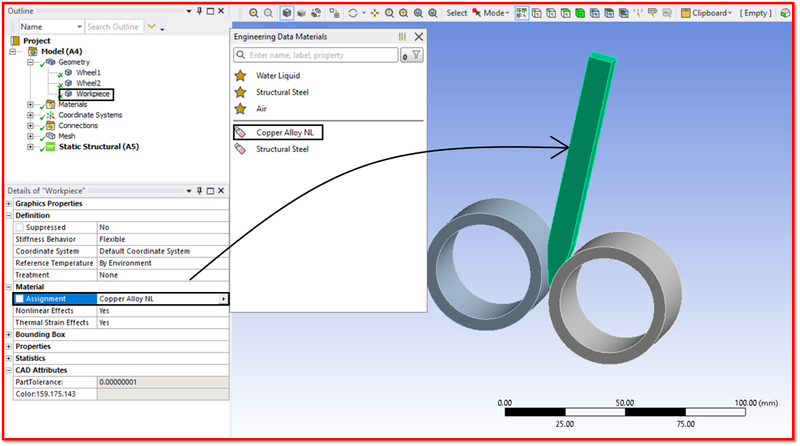
Figure 14-Assign Material to the Workpiece. |
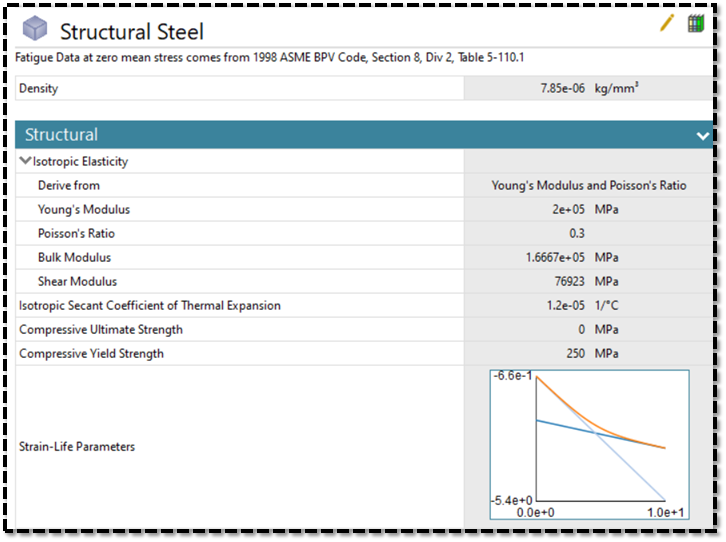
Figure 15-Mechanical Properties of Structural Steel. |
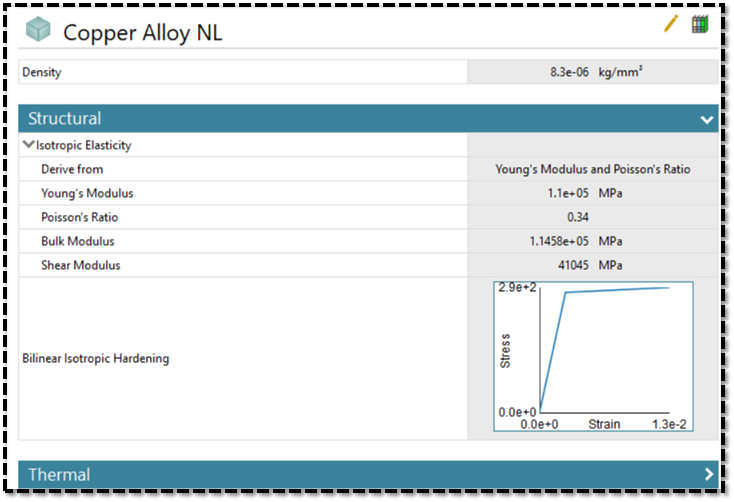
Figure 16-Mechanical Properties of Copper Alloy. |
3:2 Define Connections :
- For this Rolling Operation Model,We have to Create a two contacts, One is between Wheel 1 and Workpiece and the other one is between Wheel 2 and Workpiece.
1) Contact between Wheel 1 and Workpiece :
- Here right-click on the connections and flip the contacts and targets. The wheels need to be the targets and the workpiece should be the contact in both cases.Which is shown in below Figure 17.
- To Flip >> Right Click on Connections >> Flip Contact and Target Bodies,Which is shown in below Figure 17.
- Select the top face of the workpiece as contact and select the outer faces of the wheel 1 as target.Which is shown in below Figure 18.
- Contact Type-Frictional and Coefficient of Friction is 0.2.
- Formulation-Augmented Lagrange.
- Normal Stiffness-Factor and the Corresponding value-0.1.
- Update Stiffness-Each Iteration.
- Interface Treatment-Add Offset, Ramped Effects.
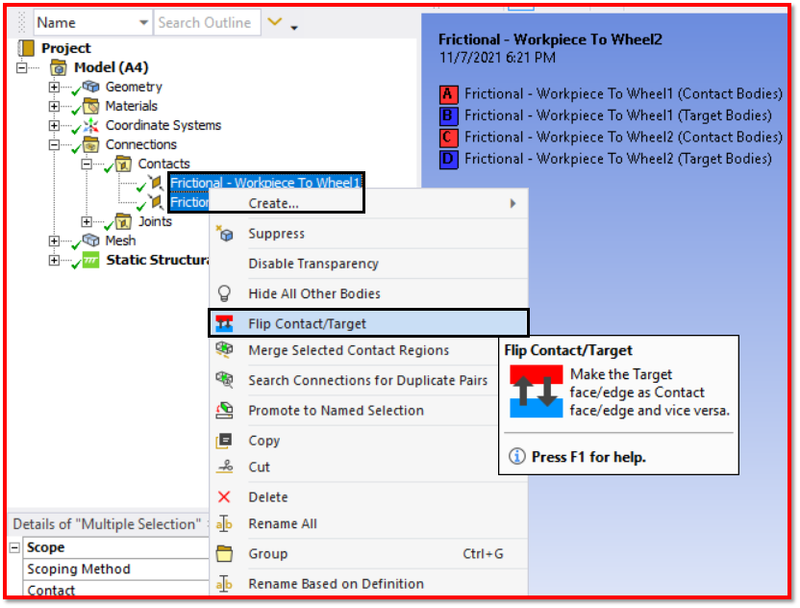
Figure 17-Flip the Connections. |
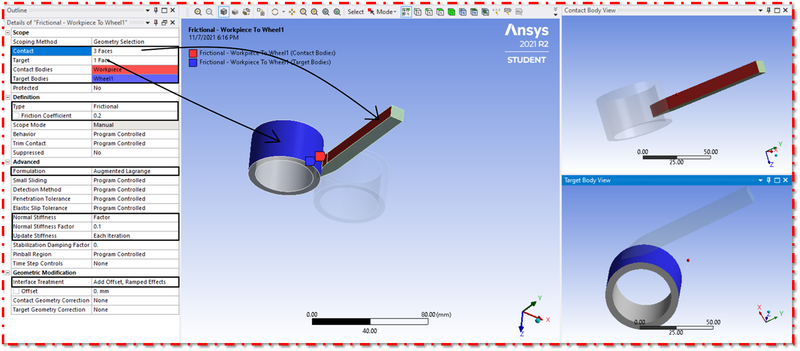
Figure 18-Define the Wheel 1 and WorkPiece Contact. |
2) Contact between Wheel 2 and Workpiece :
- The wheels need to be the targets and the workpiece should be the contact in both cases.Which is shown in below Figure 19.
- Select the top face of the workpiece as contact and select the outer faces of the wheel 2 as target.Which is shown in below Figure 19.
- Contact Type-Frictional and Coefficient of Friction is 0.2.
- Formulation-Augmented Lagrange.
- Normal Stiffness-Factor and the Corresponding value-0.1.
- Update Stiffness-Each Iteration.
- Interface Treatment-Add Offset, Ramped Effects.
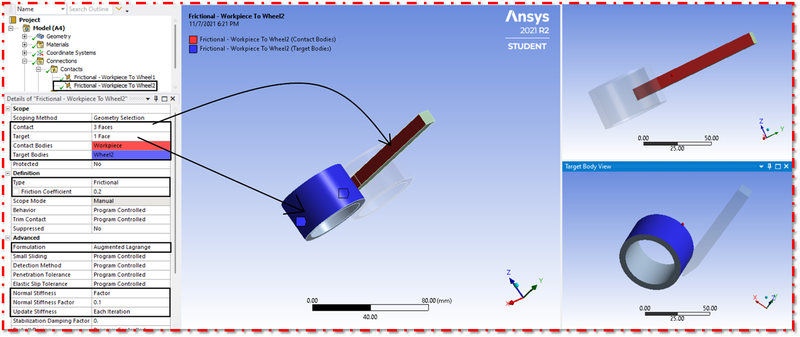
Figure 19-Contact Between Wheel 1 and WorkPiece. |
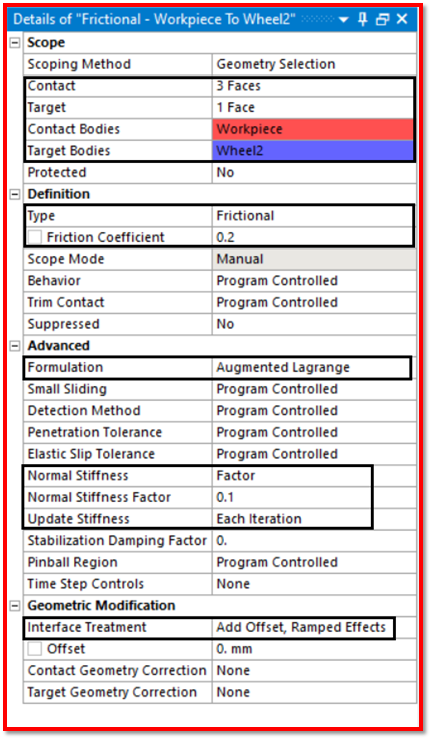
Figure 20-Contact Between Wheel 1 and WorkPiece Parameters. |
3:3 Define Joints :
1) Cylindrical Joint-
- After creating the connections,Go and create a two Cylindrical Joints.
- Select the inner face of the wheel 1 and keep the Type as Body to Ground.
- Type of Joint-Cylindrical.
- Connection Type-Body to Ground.
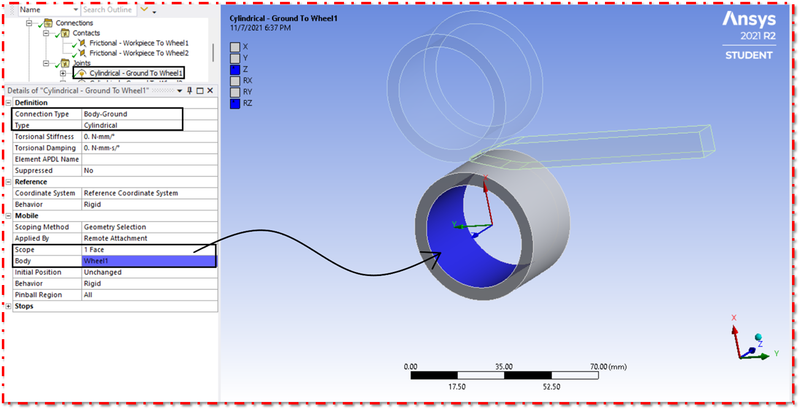
Figure 21-Cylindrical Joint 1. |
2) Cylindrical Joint 2-
- Simillarly create a Cylindrical Joint here also.
- Select the inner face of the wheel 2 and keep the Type as Body to Ground.
- Type of Joint-Cylindrical.
- Connection Type-Body to Ground.
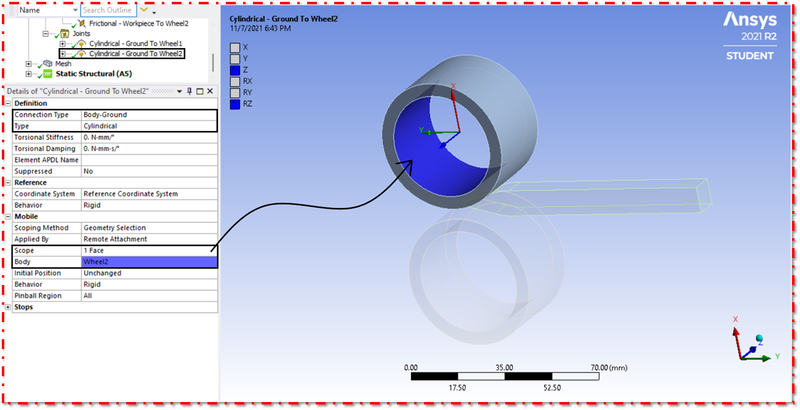
Figure 22-Cylindrical Joint 2. |
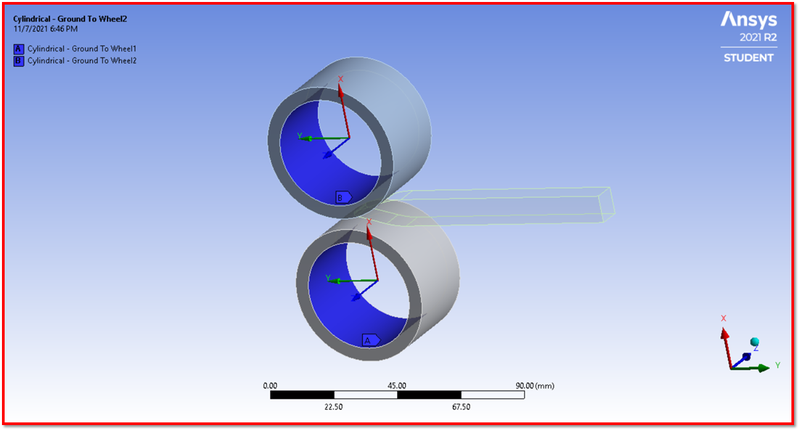
Figure 23-Two Cylindrical Joints Created. |
3:4 Meshing :
- After defining the connections ,We have to define mesh for the Rolling Operation Model.
- There will be default mesh created for the Rolling Operation model.
- But we have to insert body sizing and face sizing to refine the mesh of WorkPiece.
- To Insert Body Sizing >> Right Click on Mesh >> Insert >> Sizing >> Select WorkPiece Body.Which is shown in below Figure 24.
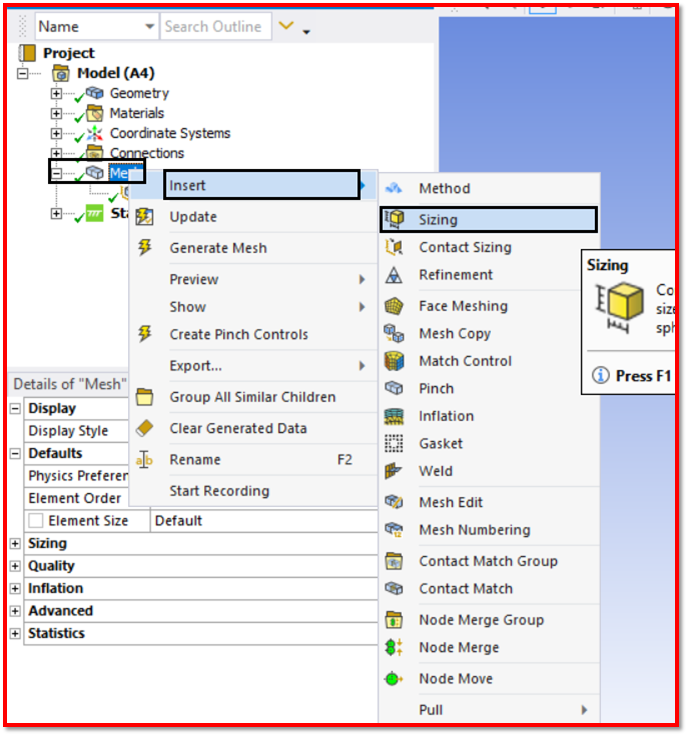
Figure 24-Insert Body Sizing to Refine the Mesh of WorkPiece. |
1) Body Sizing :
- Select the Woekpiece Body and Mesh the WorkPiece with 2 mm Element Size.Which is shown in below Figure 25.
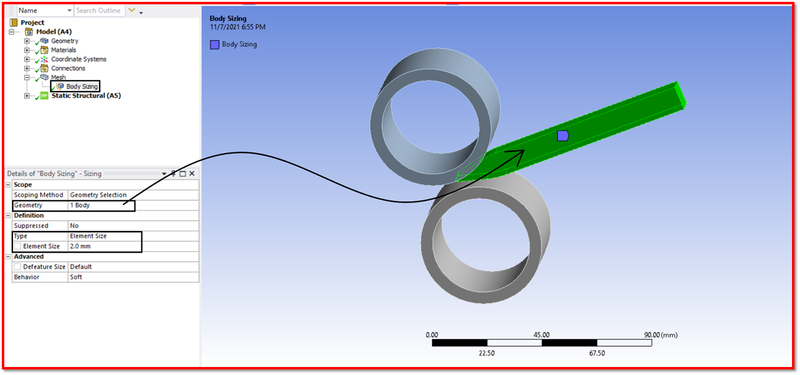
Figure 25-Refining Mesh with 2 mm Element Size. |
- The Whole Rolling Operation Component is Meshed,Which is shown in below Figure 26.
- No of Nodes =9321
- No of Elements =1629
- Wheels-Meshed with Hexahedral Elements.
- Work Piece-Refined Mesh with Hexahedral Elements.
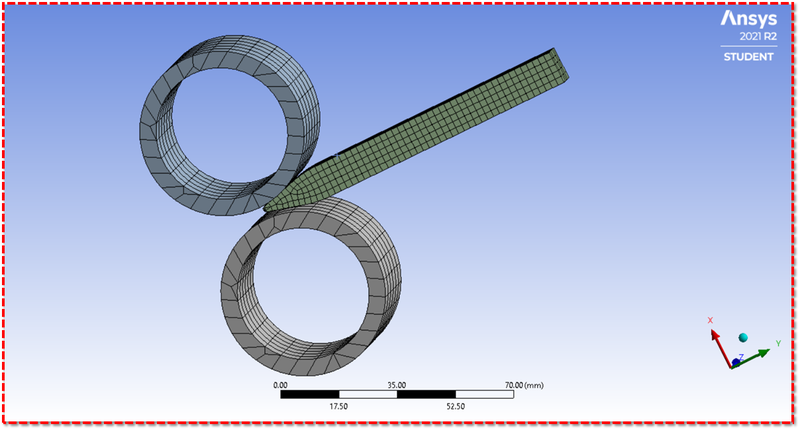
Figure 26-Final Meshed Model. |
3:5 Analysis Settings :
- Here for this Rolling Operation Model,We are giving 14 number of steps to run simulation.
- Auto Time Stepping-Program Controlled.
- Solver Type-Program Controlled.
- Large Deflection-ON
- Stabilization -Constant.
- Method-Energy.
- Energy Dissipation Ratio-0.1
- For the other parameters,Keep as it is default.
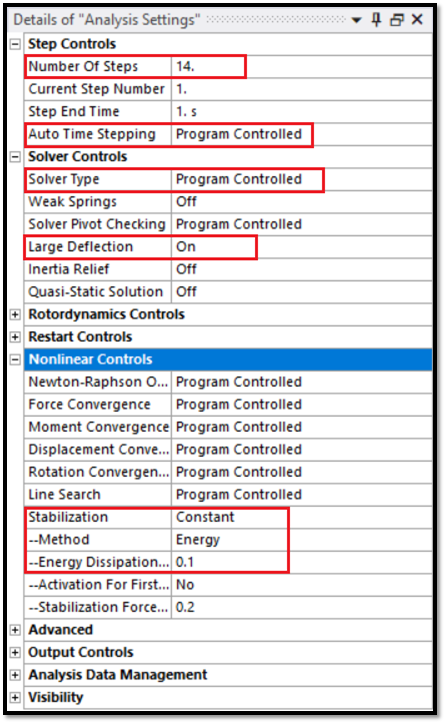
Figure 27-Analaysis Settings. |
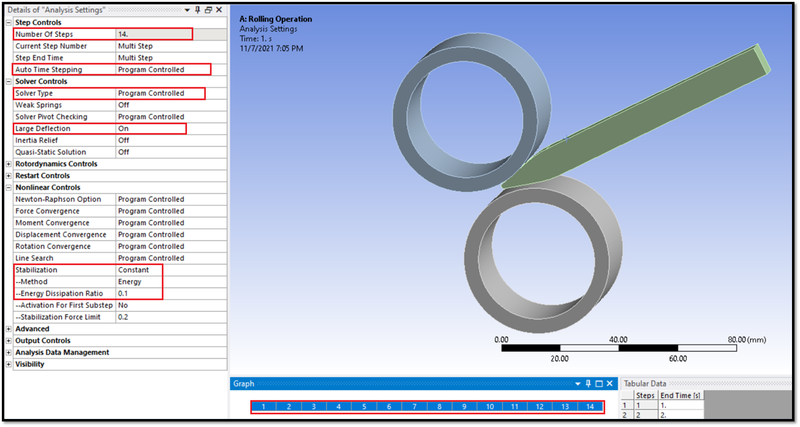
Figure 28-14 Number of Steps. |
3:6 Boundary Conditions :
- After giving some parameters in the analysis settings,We have to give boundary conditions.
- Here we have to create a boundary conditions.
- We have to give displacement and two rotational joints.

Figure 29-Give Displacement to the Rolling Operation Model. |
1) Displacement :
- Here the workpeice is pushed between the wheels,So we need to give displacement.
- Select both the side faces of the workpiece and provide the displacement values on along Negative Y direction from 0 to 90 mm.Keep free for X and Z direction,Cause the workpiece will be moving in only Y direction.
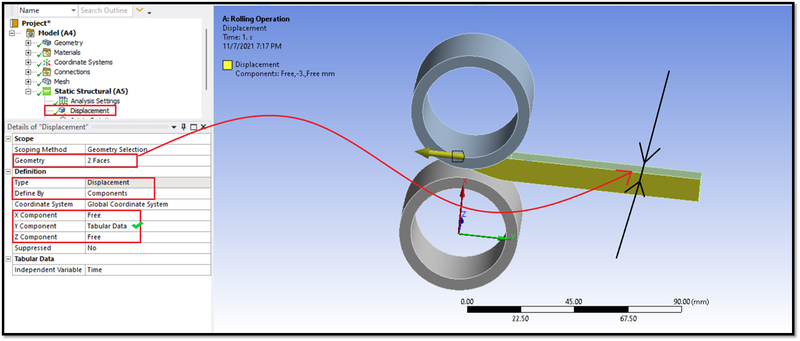
2) Rotational Joint 1 :
- Now create a rotational joint for the wheel 1 and provide a angular displacement from 0 to 195 degree in clockwise direction with the time interval of 14 number of time steps.
- To create a Rotational Joint >> Right Click on Static Structural >> Insert >> Joint >> Change to Rotational Type in Parameter Window.The Magnitude will be in tabular form.Switch to the Tabular Data.
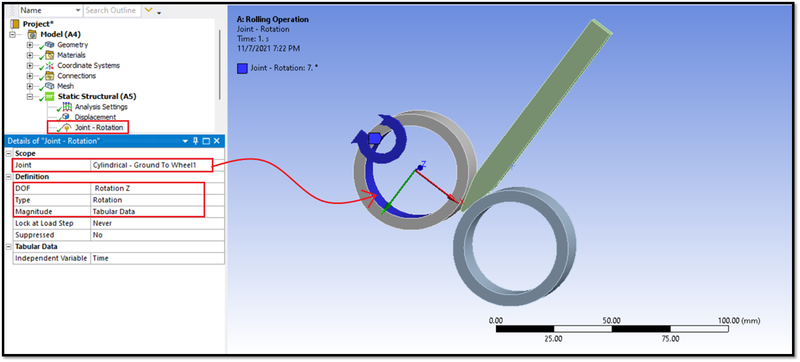
Figure 31-Rotational Joint 1. |
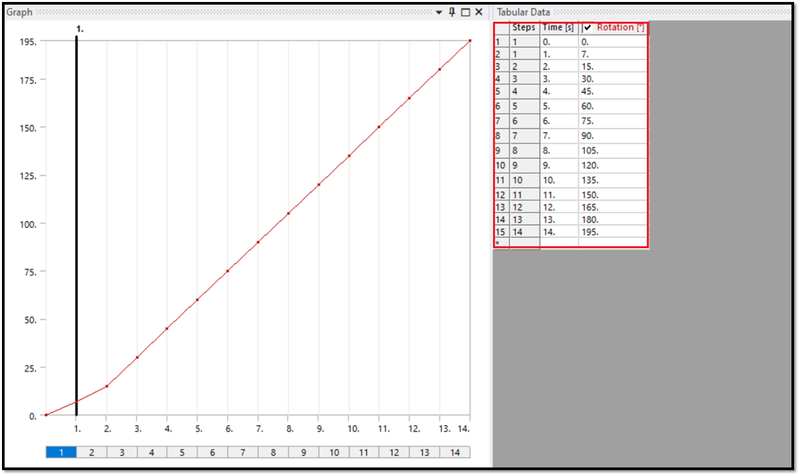
Figure 32-Values given in the Tabular Data. |
- Simillally create another rotational joint.
3) Rotational Joint 2 :
- Now create a rotational joint for the wheel 2 and provide a angular displacement from 0 to 195 degree in counterclockwise direction with the time interval of 14 number of time steps.
- To create a Rotational Joint >> Right Click on Static Structural >> Insert >> Joint >> Change to Rotational Type in Parameter Window.The Magnitude will be in tabular form.Switch to the Tabular Data.
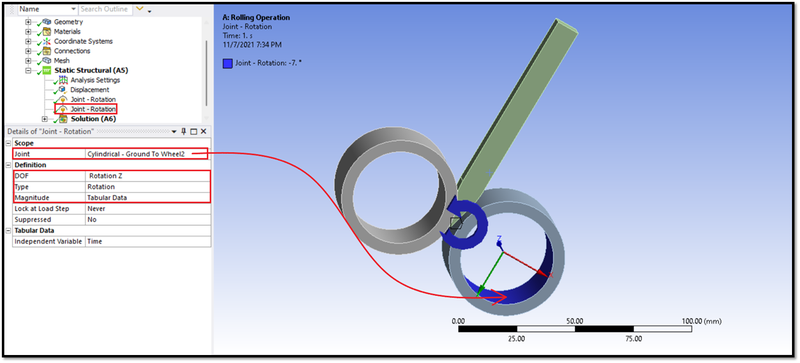
Figure 33-Rotational Joint 2. |
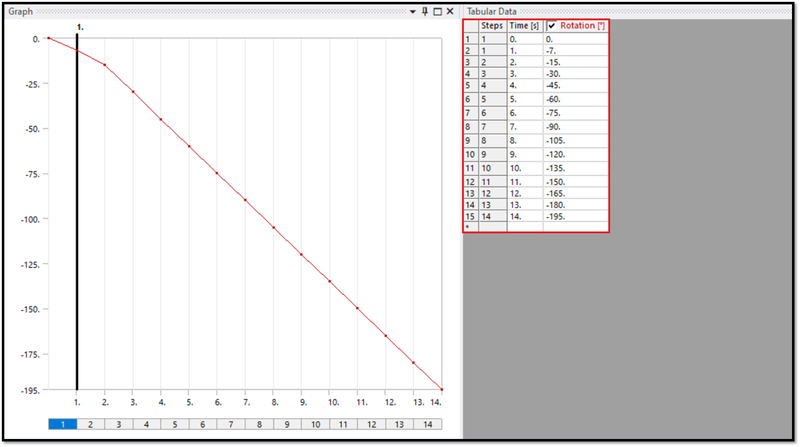
Figure 34-Values given in the Tabular Data. |
Phase 4-Request for the Outputs :
- Here we have to request outputs for the VonMisses Stress, Strain, and for Total Deformation.
- To request Output for Stress,Right Click on the Solution >> Insert >> Stress >> Equivalent Von Misses Stress.
- To request Output for Strain,Right Click on the Solution >> Insert >> Strain >> Equivalent Von Misses Strain.
- To request Output for Total Deformation,Right Click on the Solution >> Insert >> Deformation >> Total Deformation.
- This is shown in below Figure 35.
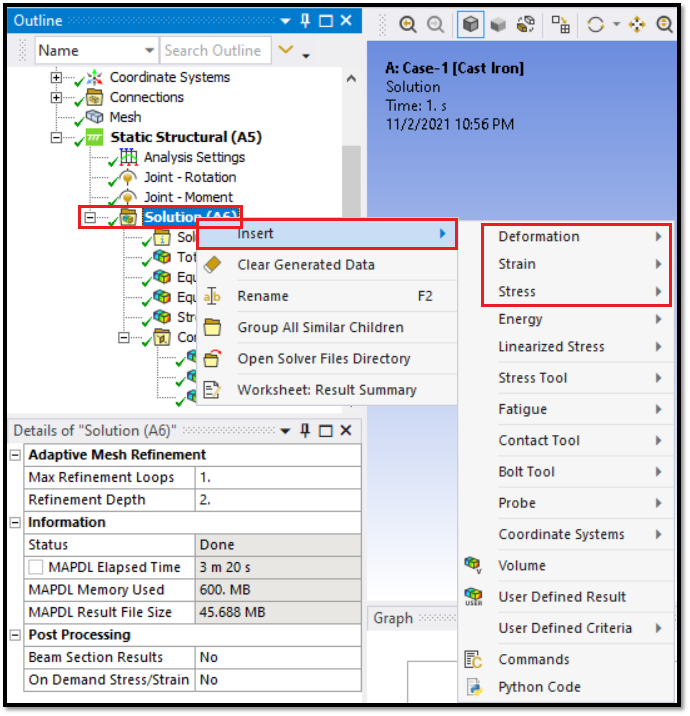
Figure 35-Requesting Outputs for the Stress, Strain, and Deformation. |
- Next request output for the contact.
- To request Contact Tool >> Right Click on the Solution >> Insert >> Contact Tool >> Pressure >> Status,Which is shown in below Figures 36 and 37.
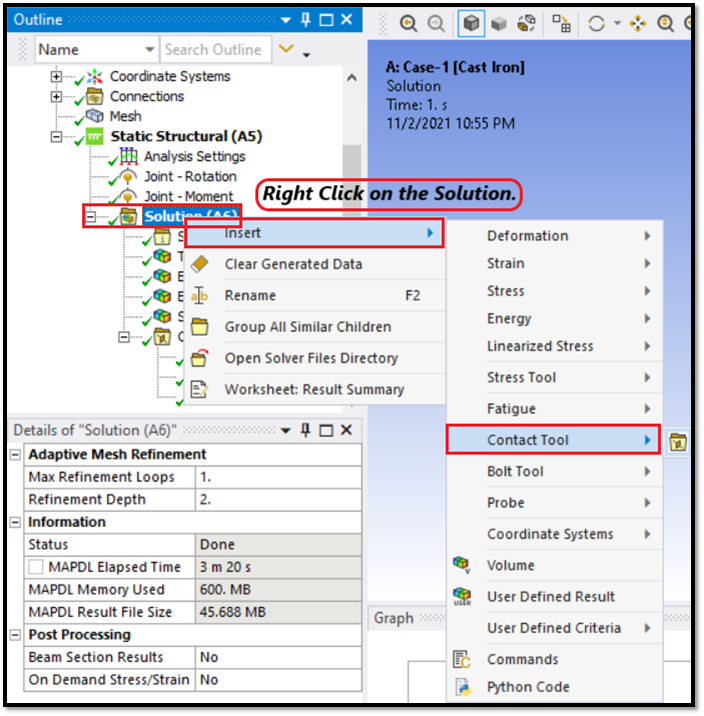
Figure 36-Requesting Output for Contact. |
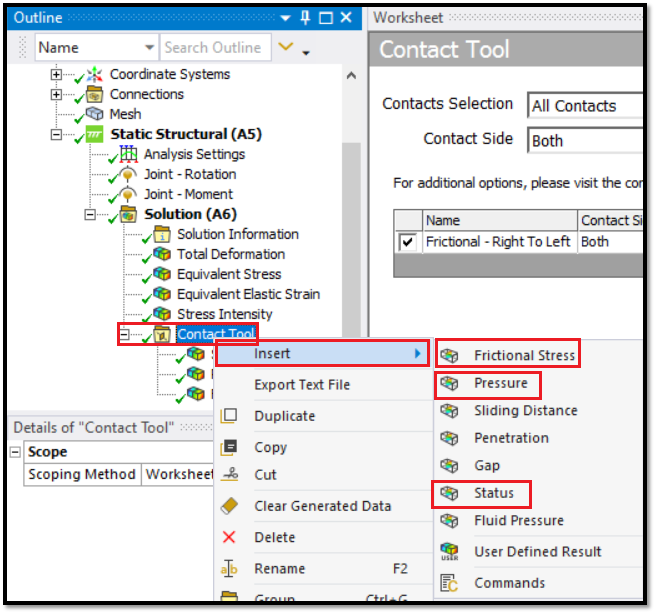
Figure 37-Requesting Outputs for Contact Tool. |
- Simillarly request the output for the Force Reaction.
- The Output requested for the Sheet Metal bending Model is shown in below Figure 38.
- After requesting all the outputs which is shown in below Figure 38. Run the Simulation.
Figure 38-Required Outputs Requested. |
Phase 5-Run the Simulation for all the three Cases :
- To run the simulation, Right Click on the Solution >> Solve. This is shown in below Figure 39.
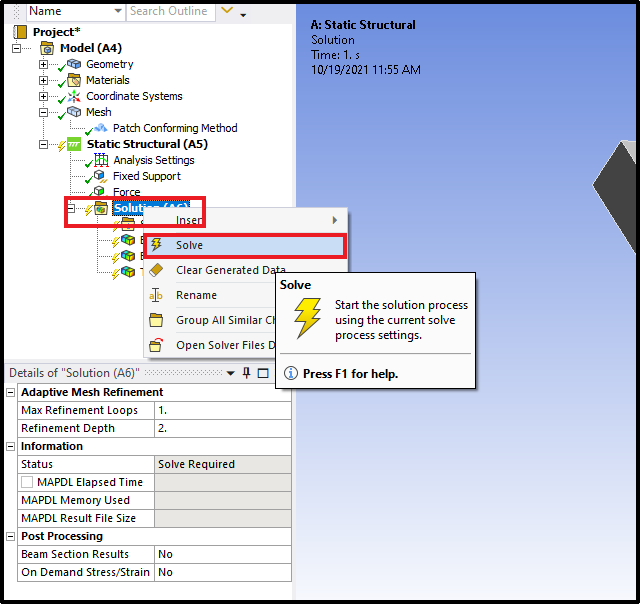
Figure 39-Solve all the Outputs Requested. |
- After solving the outputs requested, the simulation results forthe two cases is shown in the below Figures.
Equivalent Von Misses Stress :
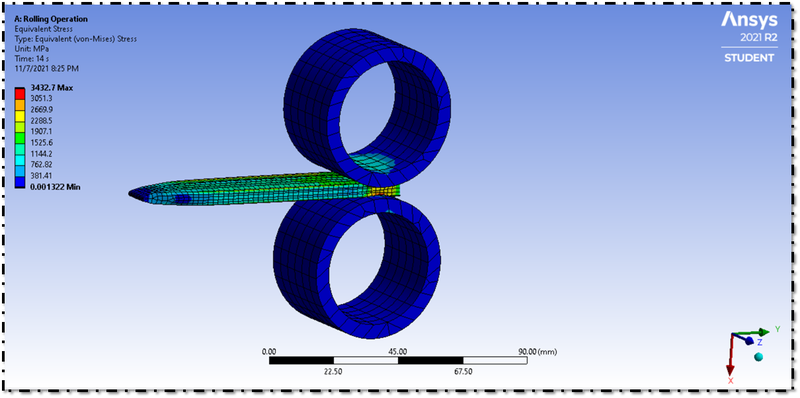
Figure 40-Equivalent Von Misses Stress. |
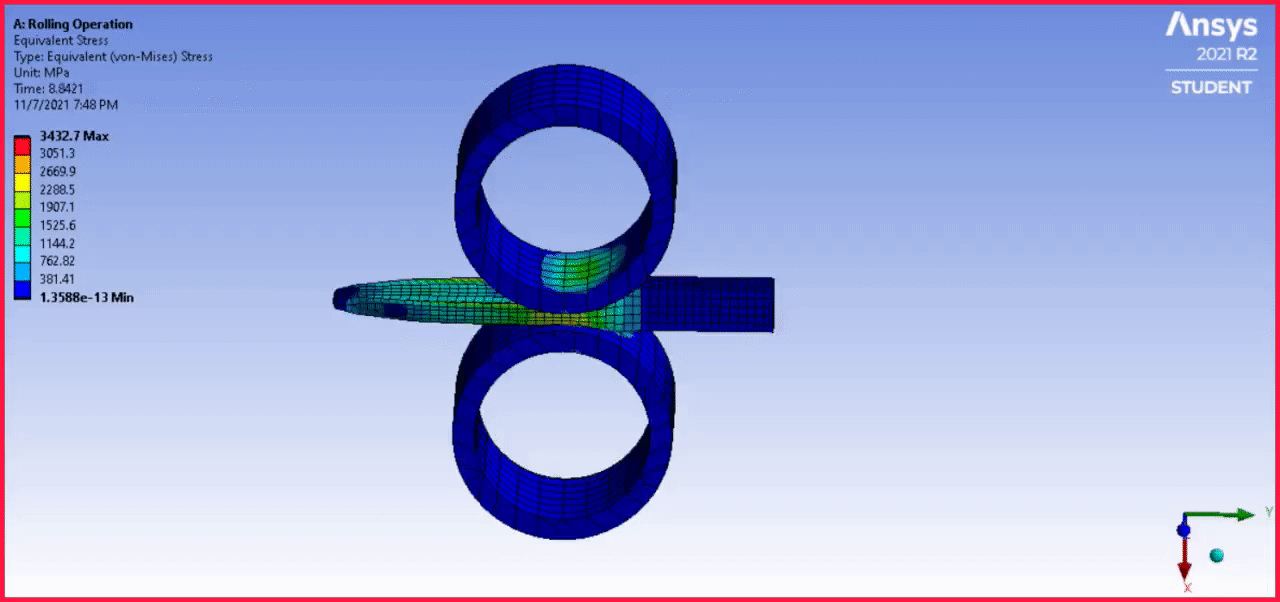
Figure 41-Equivalent Von Misses Stress Simulation Animation. |
Equivalent Plastic Strain :
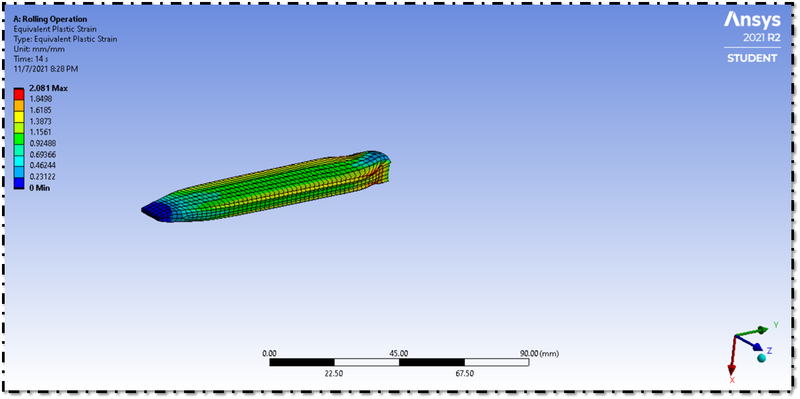
Figure 42-Equivalent Plastic Strain. |
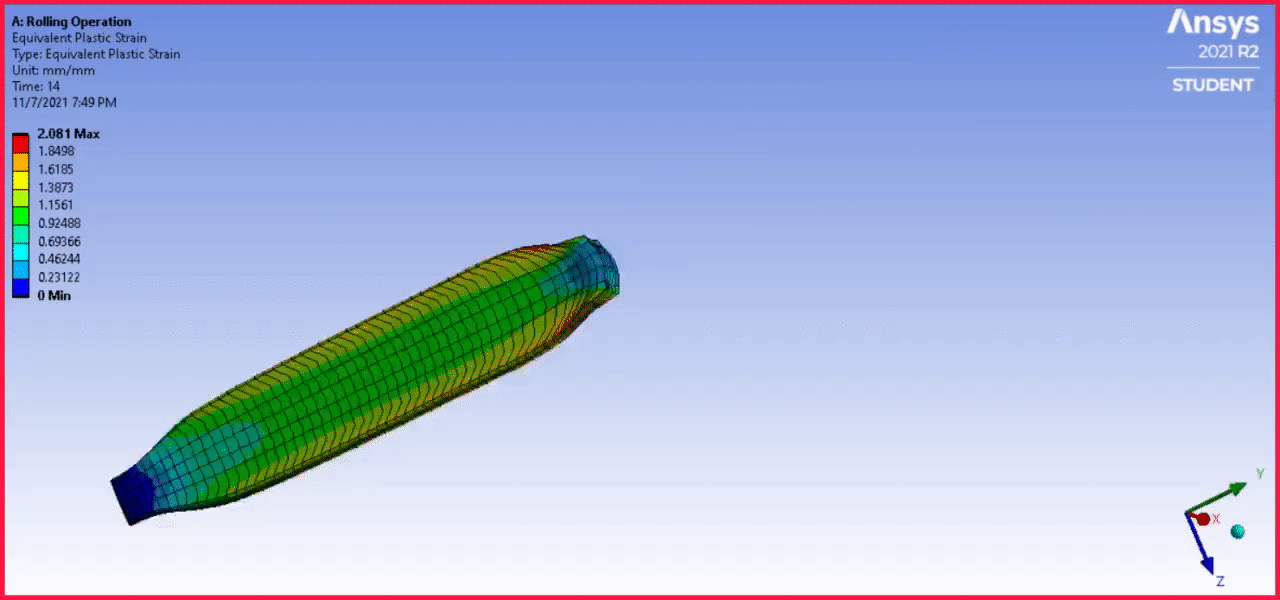
Figure 42-Equivalent Plastic Strain Simulation Animation. |
Total Deformation :
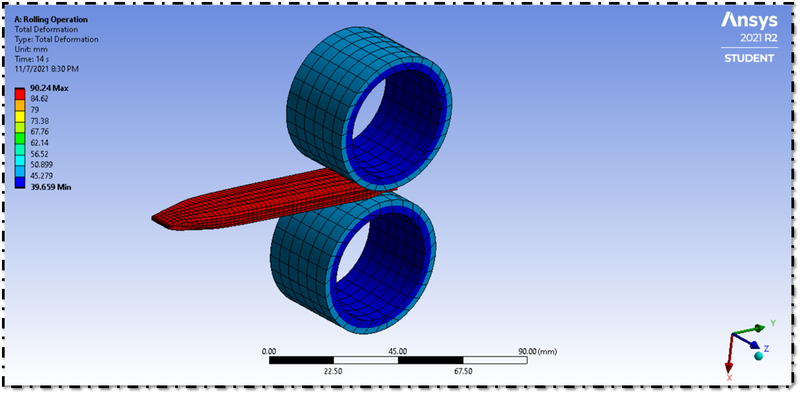
Figure 43-Total Deformation. |
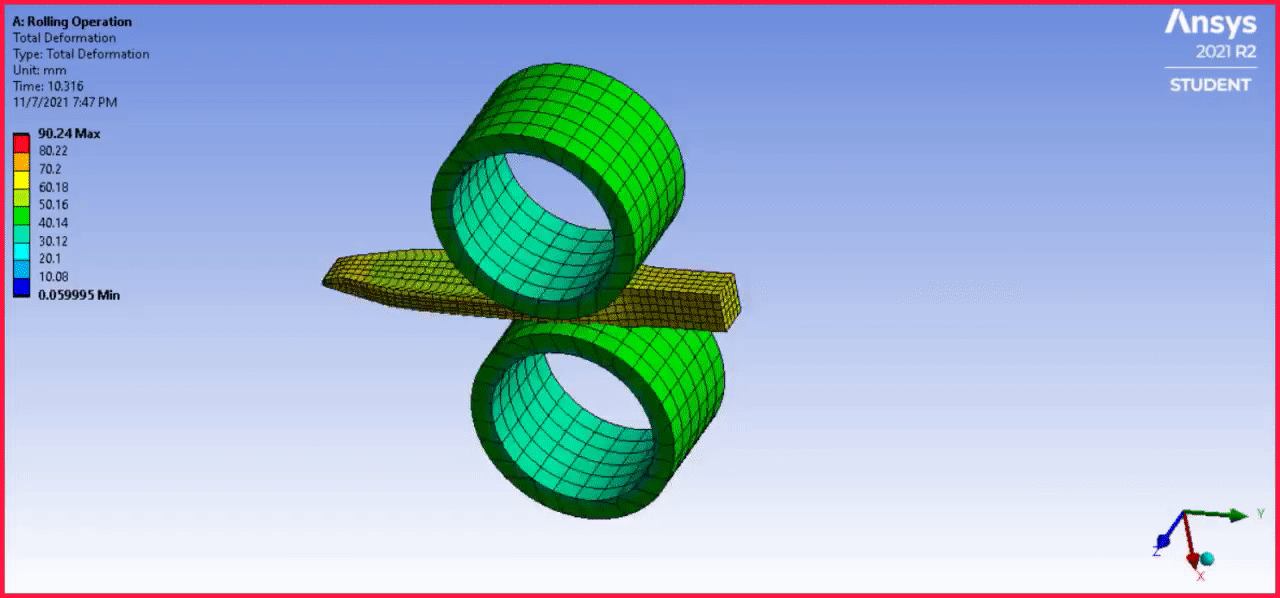
Figure 44-Total Deformation Simulation Animation. |
Directional Deformation of WorkPiece [Z Axis] :
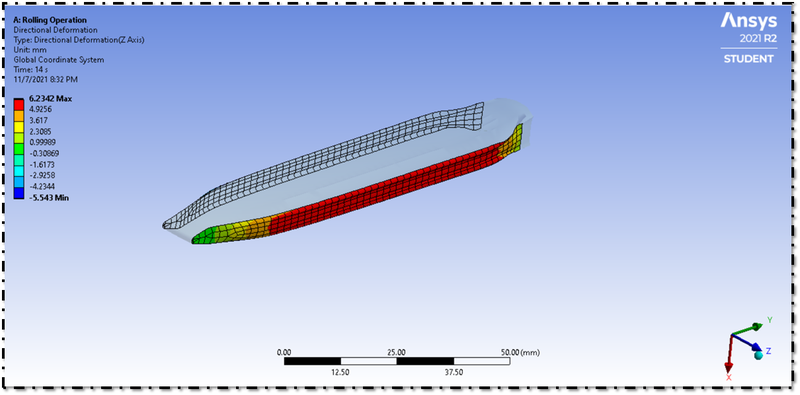
Figure 45-Directional Deformation of WorkPiece [Z Axis]. |
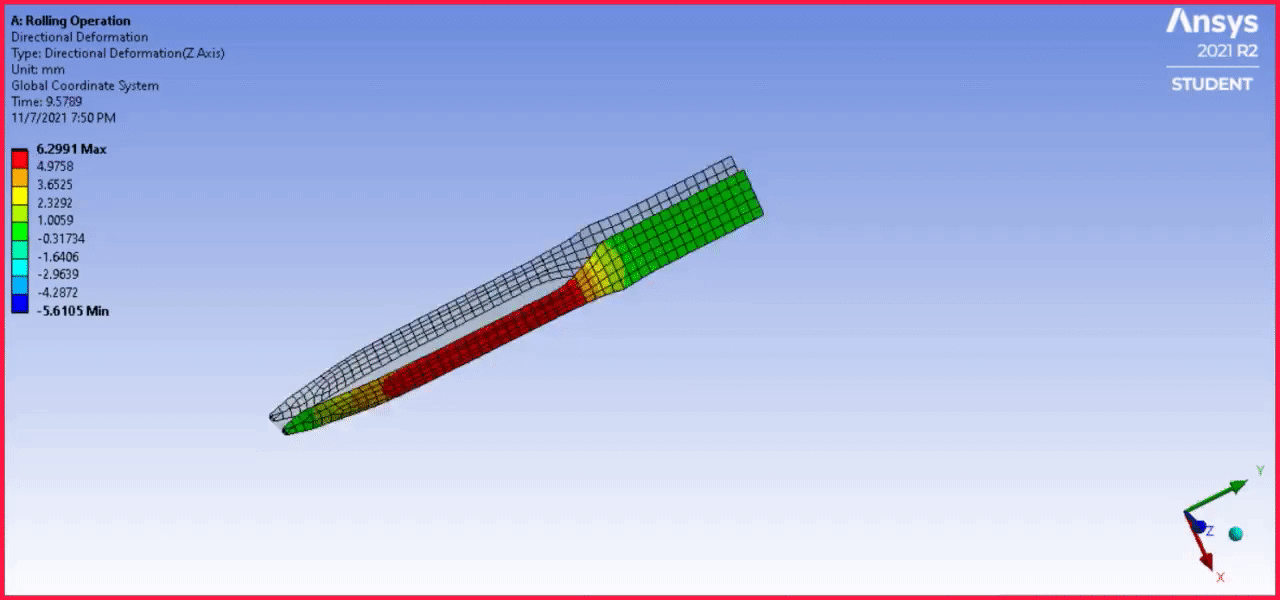
Figure 46-Directional Deformation Simulation Animation of WorkPiece [Z Axis]. |
Directional Deformation of WorkPiece [Y Axis] :
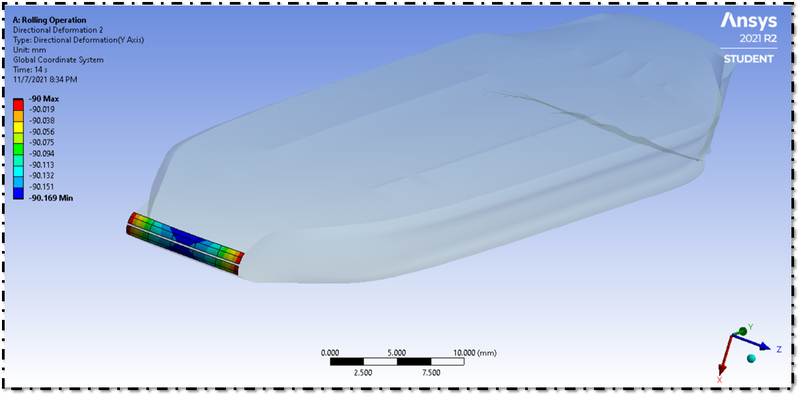
Figure 47-Directional Deformation on WorkPiece [Y Axis]. |
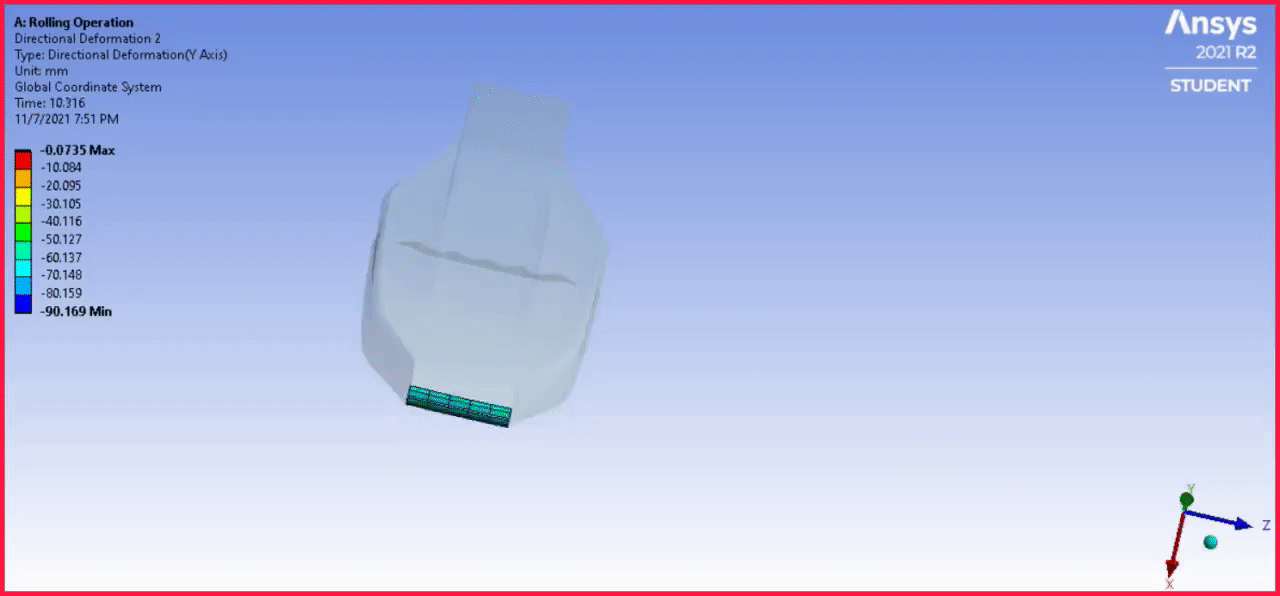
Figure 48-Directional Deformation Simulation Animation of WorkPiece [Y Axis]. |
Force Reaction :
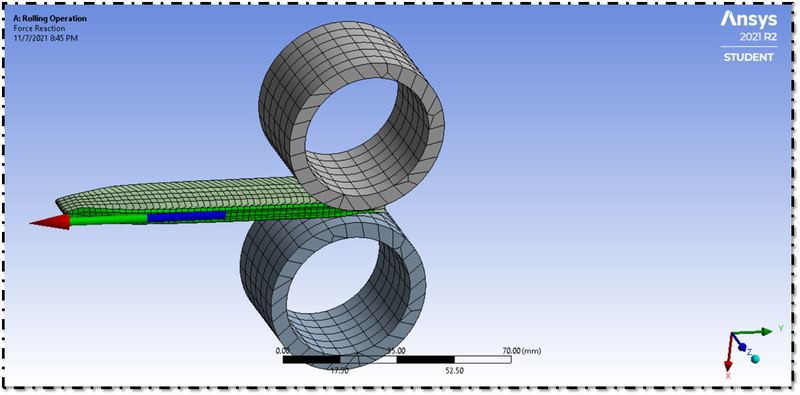
Figure 49-Force Reaction. |
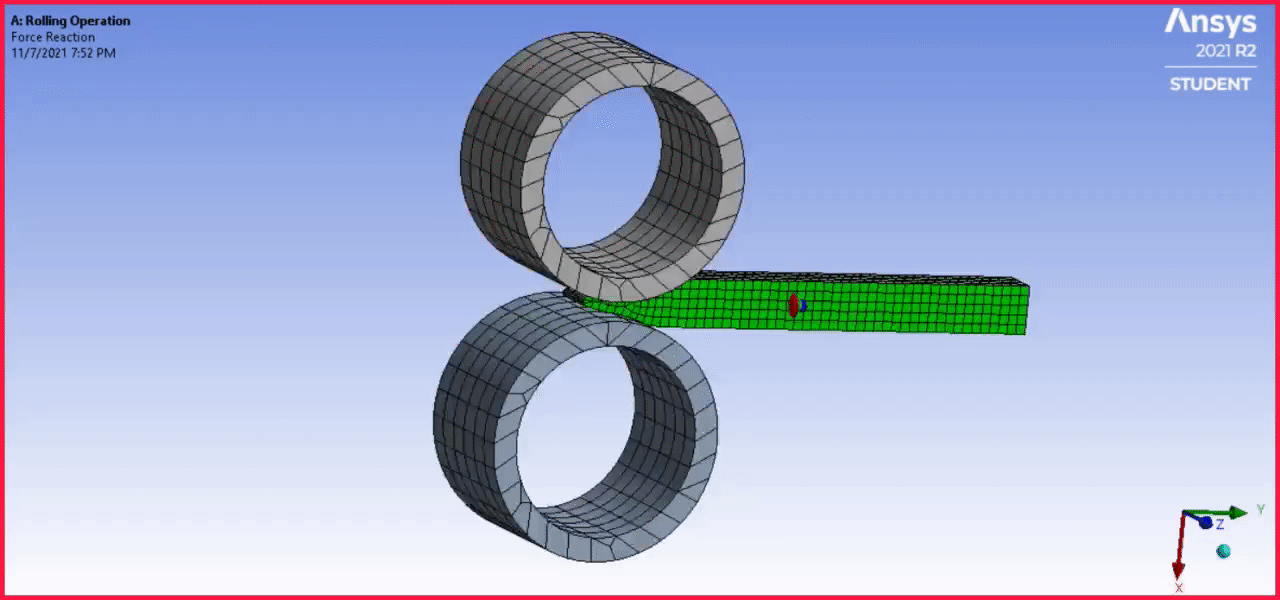
Figure 50-Force Reaction Simulation Animation. |
Moment Reaction :
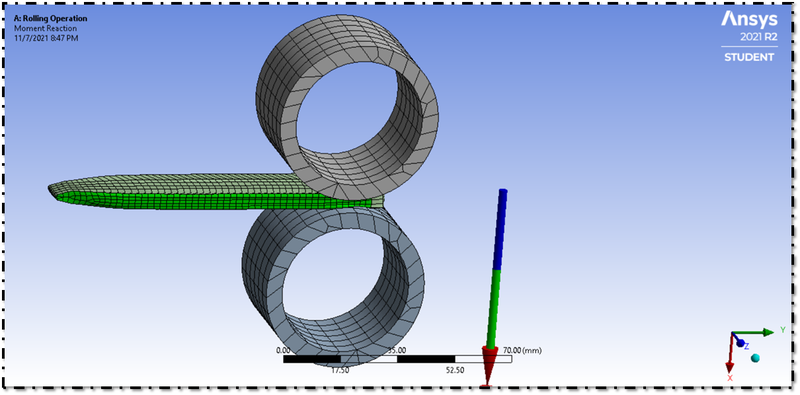
Figure 51-Moment Reaction. |
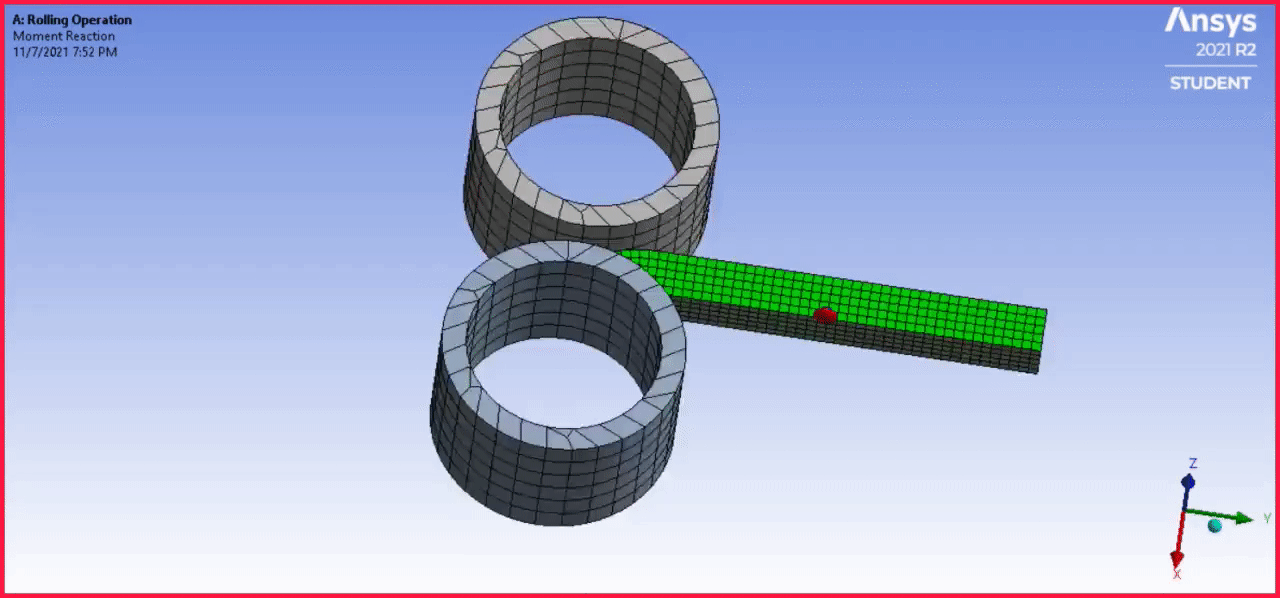
Figure 52-Moment Reaction Simulation Animation. |
Pressure :
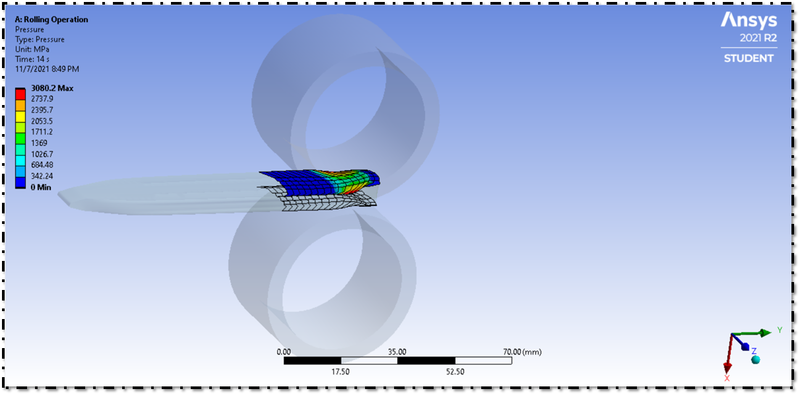
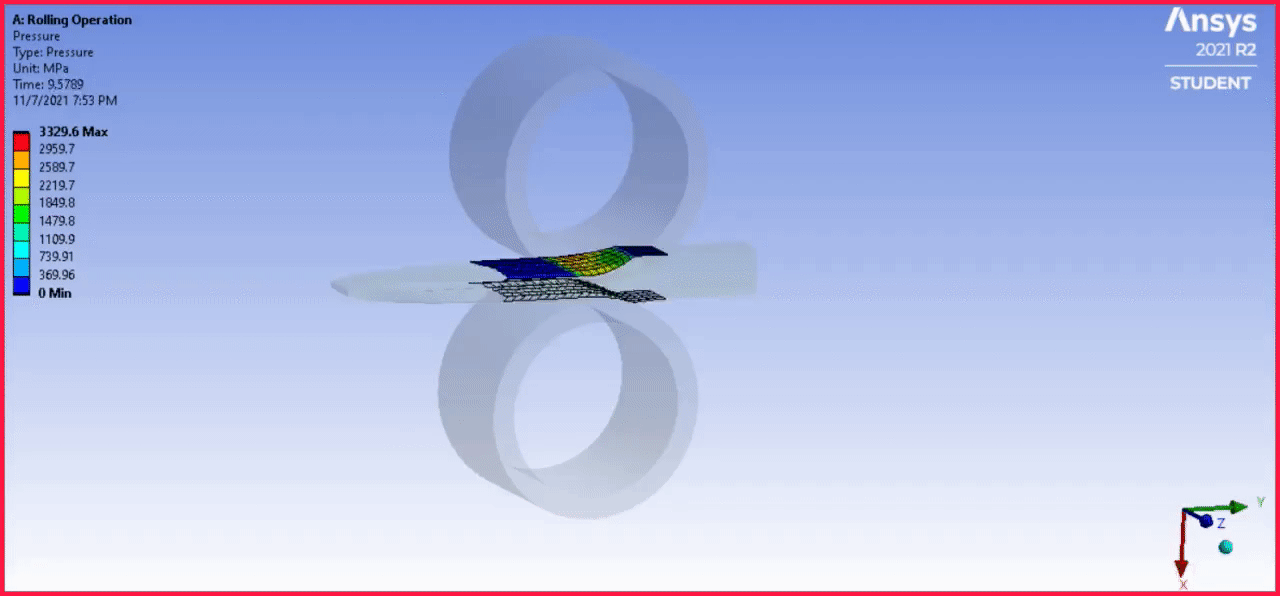
Figure 54-Pressure Simulation Animation. |
Simulation Results :
Case
|
Von-Misses Stress (MPa)
|
Total Deformation (mm)
|
Directional Deformation of WorkPiece [Y Axis]
|
Max.
|
Min.
|
Max.
|
Min.
|
Max.
|
Min.
|
Case-1
|
3432.7 MPa
|
1.322e-003 MPa
|
90.24 mm
|
39.659 mm
|
-90. mm
|
-90.169 mm
|
- Here the Maximum Von_Misses Stress Occured in the Model is 3432.7 Mpa.
- The Maximum Total Deformation occured is 90.24 mm.
- The Directional Deformation is measured along the Y axis.The Maximum Directional Deformation along the Y axis is 90 mm.
- Hence the workpiece is displaced by 90 mm along the Y axis Direction.Which is shown in above Figure 47 and 48.
- Simillarly all the Stress,Strain,Contact Tool,Force and Moment Reaction outputs are requested.Which is shown in above Figures.
Result :
- Hence the model was opened in spaceclaim and the length of the workpiece was increased by 60 mm and it's width was decreased by 8 mm on both sides.
- Hence the material has been defined for Rolling Operation Model.
- Hence the connections were defined to the Rolling Operation Model.
- Hence the model was meshed with hexahedral elements and the workpiece was refined with 2 mm element size.
- Hence the Simulation was ran successfully with 14 number of time steps.
- Hence the model has been solved for Von-Misses Stress, Equivalent Elastic Strain,Stress Intensity,Contact Tool and Directional Deformation by applying appropriate boundary conditions.
- Hence the Directional Deformation along the Z Axis is 6.2342.
- Hence the workpiece is displaced by 90 mm along the Y axis Direction and it is proved.
Conclusion and Learning Outcome :
In this Week 4 Rolling Operation Challenge, I came to know about
- Learned how to give Displacement to the Rolling Operation model.
- Learned to define cylindrical joints.
- Learned the fine meshing of the sheet workpiece will provide more accurate results.
- Learned how to assign materials to the model.
- Learned how to apply boundary conditions to the model.
- Learned to define rotational joints for the wheels.
- Learned how to request outputs and solve them.
- Learned about the Force Convergence.