Static Structural Analysis on Weld Joints :
Aim :
- To perform static structural analysis on the welding model using three different weld materials.
Objective :
- To define three different materials for the welding Model.
- To define appropriate material to the component.
- To define connection between the contact surfaces.
- To perform mesh on the component.
- To define Fixed Support and apply Force on the plate.
- To solve and compare the results of the three cases for Total Deformation, Von-Mises Stress and Equivalent Elastic Strain.
Theoretical FrameWork :
Welding :
- Welding is a fabrication process that joins materials, usually metals or thermoplastics, by using high heat to melt the parts together and allowing them to cool, causing fusion. Welding is distinct from lower temperature metal-joining techniques such as brazing and soldering, which do not melt the base metal.
- A weld joint is an area where the faying surfaces of two or more materials are joined together by a welding process with or without the addition of filler material. Pressure may or may not be used when making a weld at the weld joint.
- A weld joint may be either a fillet weld joint or a groove weld joint. These two joints include the following types: butt joint, lap joint, edge joint, tee joint and corner joint.
- Surface preparation is often required when thick materials are joined by groove welding to ensure the weld joint is completely penetrated. Weld joints are often coated after they are cleaned to resist certain types of corrosion.
- Weld joints can consist of similar and dissimilar metals. If joining dissimilar metals, extra considerations must be taken to avoid negative side effects such as galvanic corrosion. Also, it is important to select the proper filler material; otherwise the mechanical and chemical properties of the resultant weld could be negatively affected.
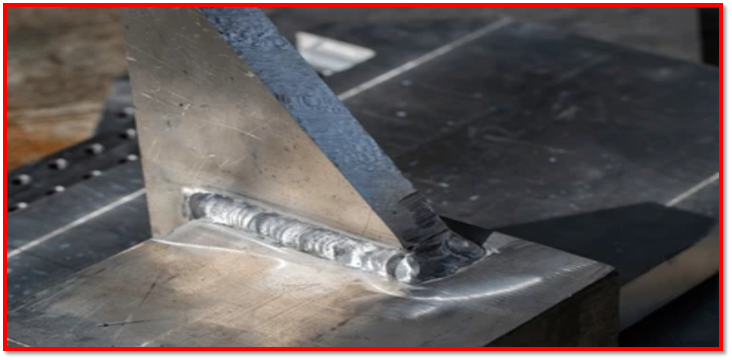
Procedure :
- To set up the material for the Weld Joints Model. First, drag and drop the static structural analysis workspace into the project schematic from the analysis system. This is shown in below Figure 2.
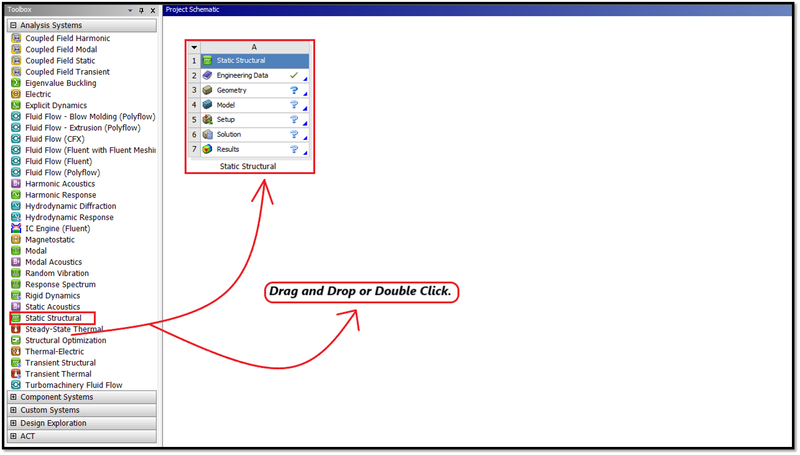
Figure 2-Ansys Workbench Workspace. |
- After deploying the static structural analysis system in the project schematic workspace.
- Define the Engineering Data and geometry, To define the Geometry and Engineering Data, Right Click on the Engineering Data and click to edit, it will take to the Engineering Tab.
- There Right Click on the Material Tab, A window will Pop-Up stating Engineering data sources.
- Click on the Engineering Data Sources, There go and select the material to define the engineering data. This is shown in below Figures 3,4,5.
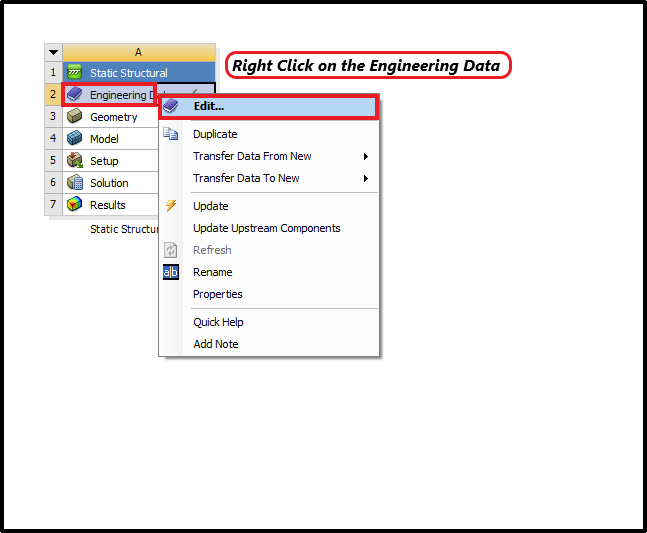
Figure 3-Right Click on the Engineering Data. |
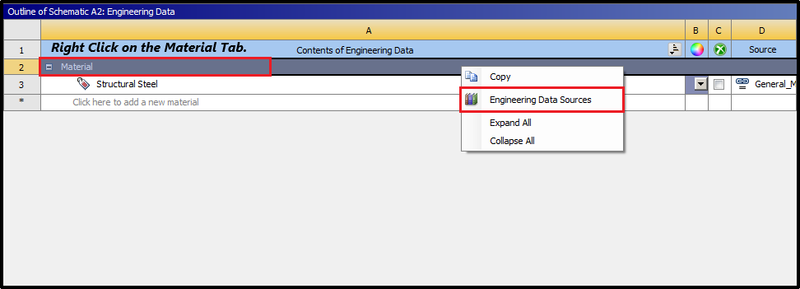
Figure 4-Right Click on the Material Tab. |
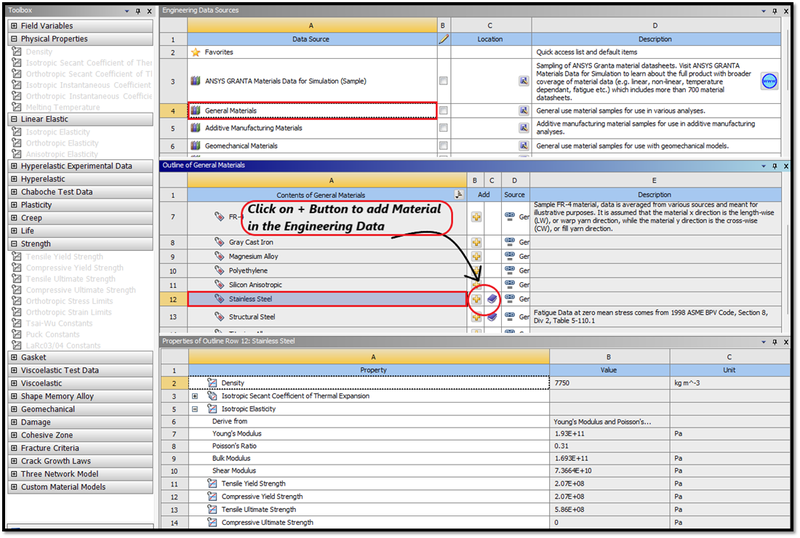
Figure 5-Select the Material as Stainless Steel to add it in the Engineering Data. |
- For this Welding Model,Create a material cards for the Cast Bronze and Aluminium Alloy [High Strength and Wrought].
- To create a custom material,First create a custom material library,In that library create all those three material cards.
- To create a new library,Click on the option click here to add new library and name it as spur gear materials which is shown in below Figure 6.
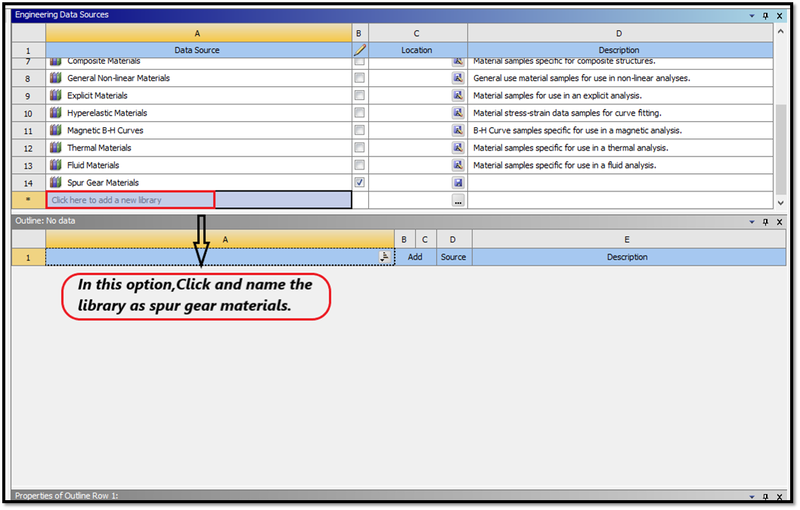
Figure 6-Create a New Library. |
- After creating a new library,In that library go and add the materials and properties,Which is shown in below Figure 7.
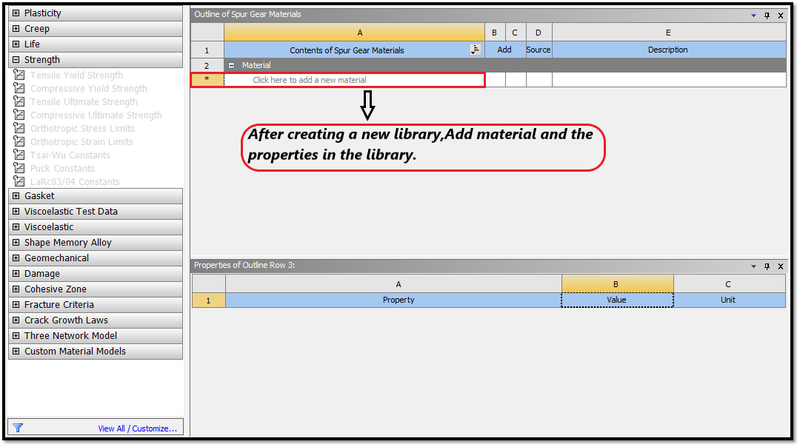
Figure 7-Add a New Material. |
- Add the properties to all the materials created,To add the materials,Drag and drop the material proprties or double click on the properties to add them to the material.Which is shown in below Figure 8.
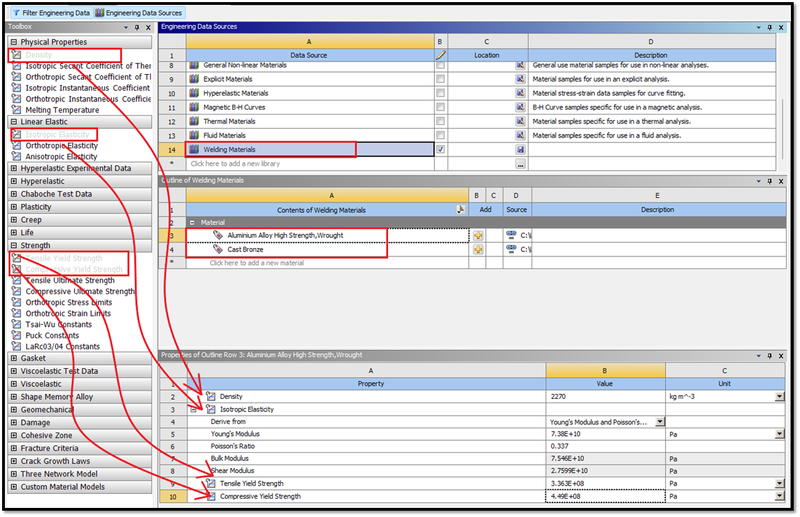
Figure 8-Drag and Drop or Double Click on the Properties to Add. |
- Atlast save the Material Cards in to a new location,Which is shown in below Figure 9.
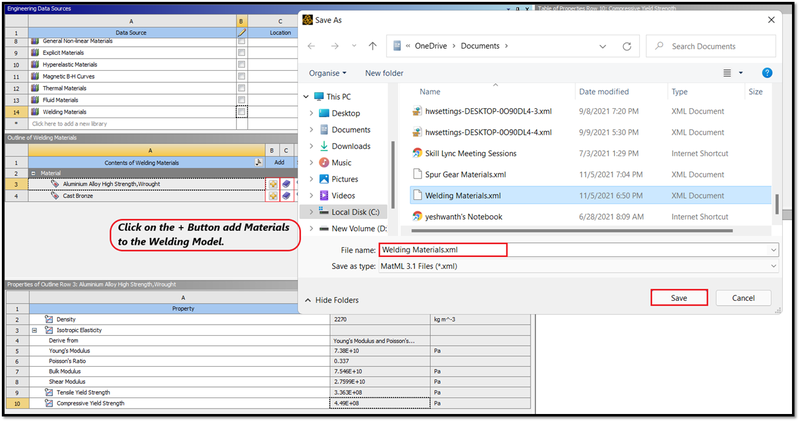
Figure 9-Save the Material Card into a New Location. |
Phase 2-Geometry Set Up :
- Next set up the geometry. To set up the geometry, Right-Click on the Geometry option >> Import Geometry. This is shown in below Figure 10.
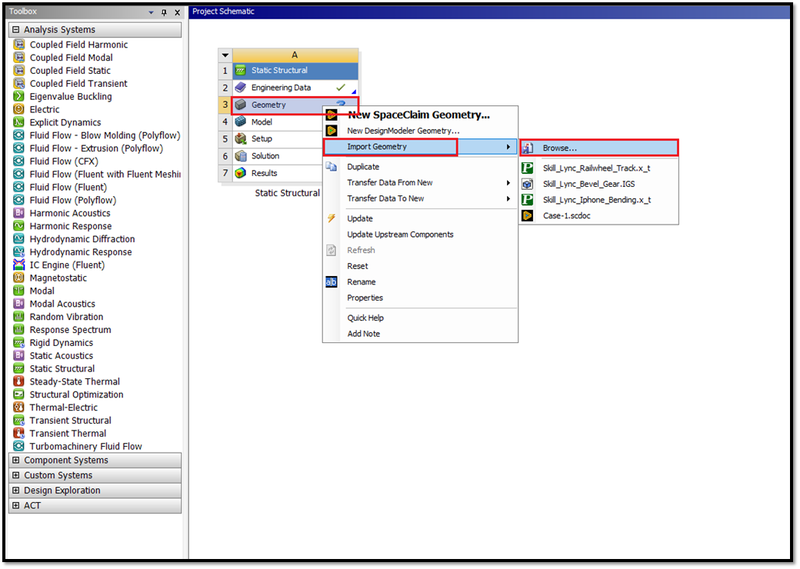
Figure 10-Importing Geometry. |
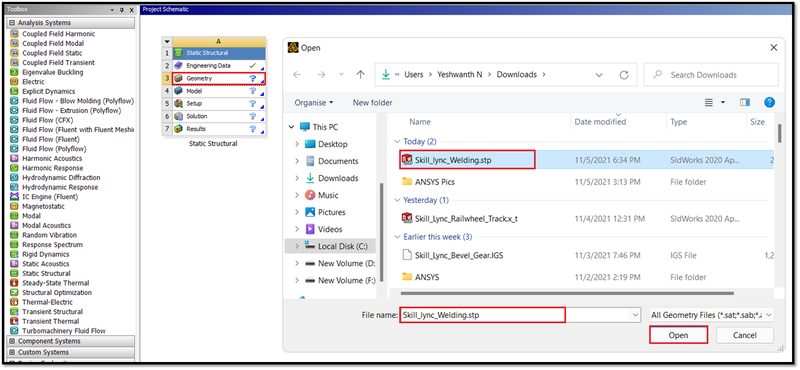
Figure 11-Selecting the Geometry to Import. |
- Next double click on the geometry to check, Whether the model imported is Welding Model or not. Space Claim Workspace will open.The model will be imported in the space claim,Which is shown in below Figure 12.
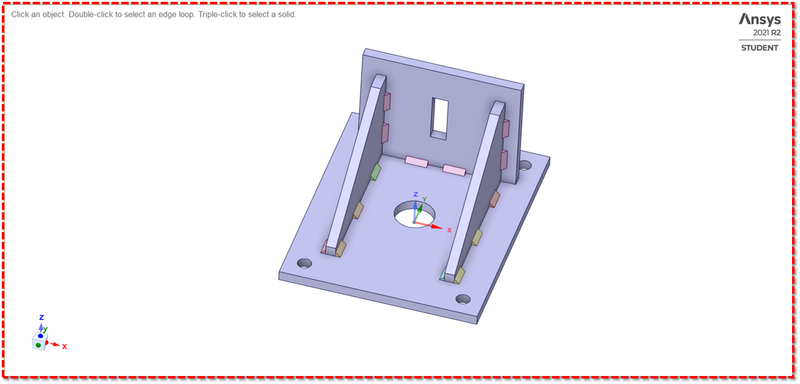
Figure 12-Welding Model in the Space Claim. |
Phase 3-Model Set Up :
- Next, define the model, Double click on the model, The Mechanical Workspace will open, There go and define the material,set up the load case for all three cases.
- The Model loaded in the mechanical workspace is shown in below Figure 13.
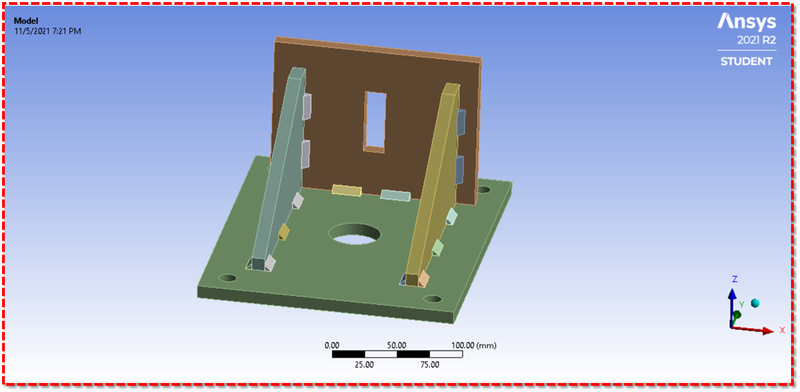
Figure 13-Model Loaded in Mechanical Workspace. |
3:1 Assign Material :
- Next define the material as stainless steel for whole component which is shown in below Figure 14.
- Simillarly define the material for other two cases.The material properties is shown in below Figures 15,16,17 and 18.
- To assign a material,Click on the Geometry >>Select all the Welded Joints,Big,Small Plate and Ribs >> Parameter Window >> Assignment >> Stainless Steel.
Case 1 :
- Assign the Stainless steel as a material for whole welding model [Welded Joints,Big and Small Plate,Rib 1 and Rib 2].
Case 2 :
- Assign the Aluminium Alloy (High Strength and Wrought) as a material for all the Welded Joints and assign the Stainless Steel as a material for Big Plate, Small Plate and Ribs.
Case 3:
- Assign the Cast Bronze as a material for all the Welded Joints, then assign the Stainless Steel as a material for Big Plate and Small Plate and then assign the Copper as material for Ribs.
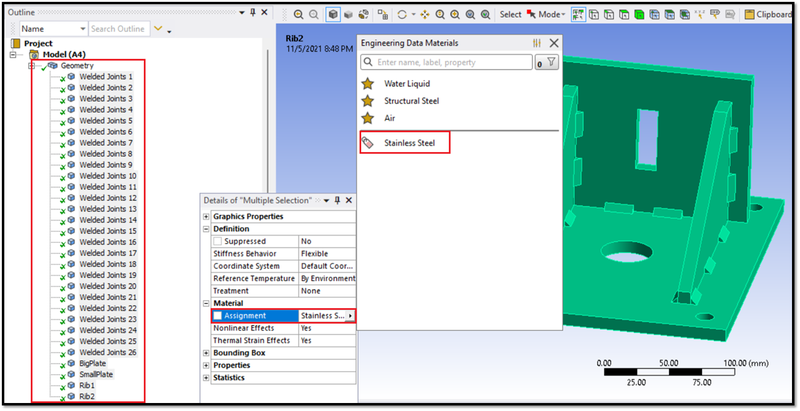
Figure 14-Define Material. |
- Simillarly define the material for other two cases.
Figure 15-Mechanical Properties of Stainless Steel. |
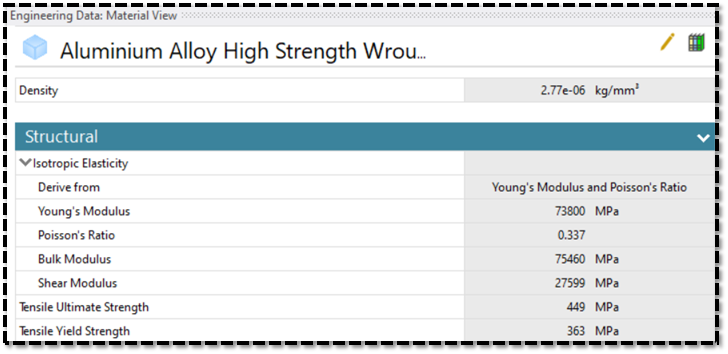
Figure 16-Mechanical Properties of Aluminium Alloy (High Strength and Wrought). |
Figure 16-Mechanical Properties of Copper Alloy. |
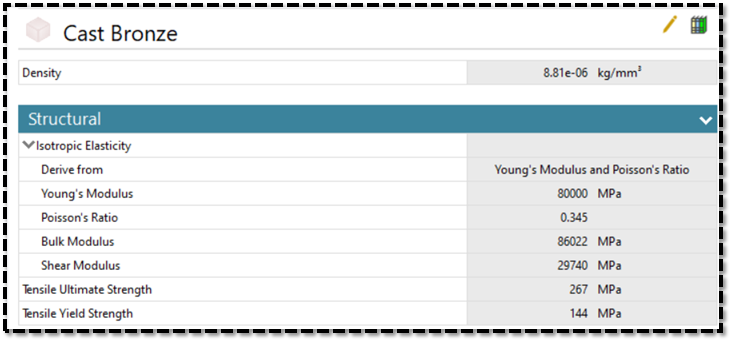
Figure 17-Mechanical Properties of Cast Bronze. |
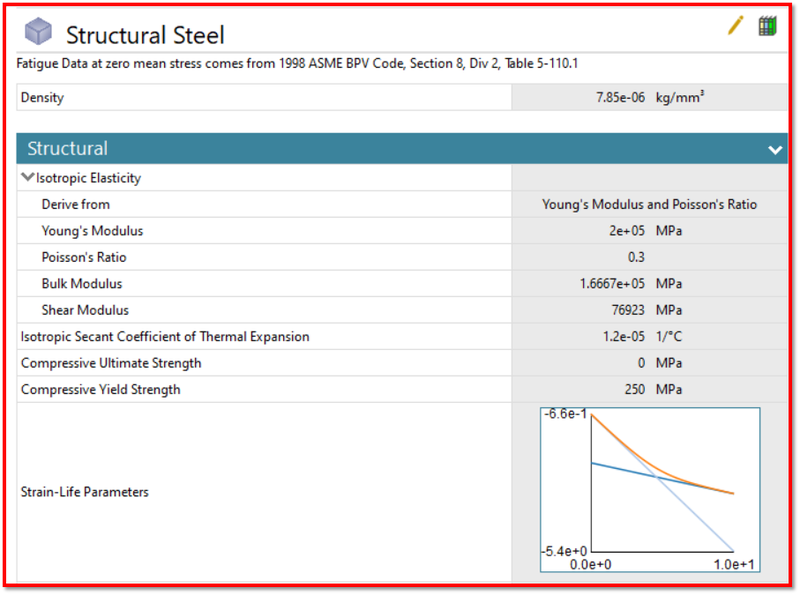
Figure 18-Mechanical Properties of Structural Steel. |
3:2 Define Connections :
- While opening the Mechanical Model Workspace,There will be a contacts created default.No need to create any contacts manually.
- But we have to use two different contact type,One is Bonded Contact Type and Frictional Contact Type with Frictional Coefficeint of 0.2.
- Keep Bonded Contact Type between all the Welded Joints and Plates.
- Keep Frictional Contact Type between Plates and Surfaces.
1) Contact Between Welded Joints and Plates :
- Here the contact type has been selected as Bonded Contact Type ,Cause the weld joints are permanent joints and their will be no movement or sliding motion.
- So we have selected the Contact Type as Bonded,Cause it won't allow any movement or sliding motion.
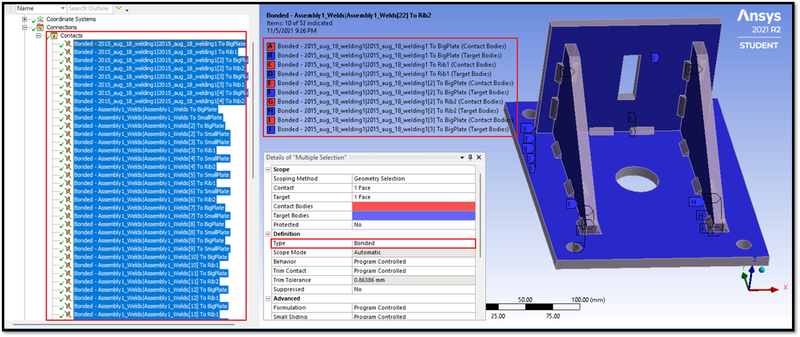
Figure 19-Contact Between Welded Joints and Plates. |
2) Contact Between Big Plate and Small Plate :
- Here the Contact has been created between Big Plate and Small Plate.
- The Contact Type is selected as Frictional with Frictional Coefficient of 0.2.The contact created is shown in below Figure 20.

Figure 20-Contact Between Big Plate and Small Plate. |
3) Contact Between Big Plate and Rib 1 :
- Here the Contact has been created between Big Plate and Rib 1.
- The Contact Type is selected as Frictional with Frictional Coefficient of 0.2.The contact created is shown in below Figure 21.
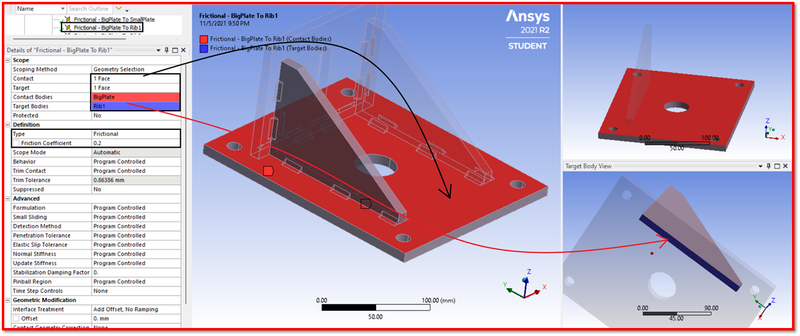
Figure 21-Contact Between Big Plate and Rib 1. |
4) Contact Between Big Plate and Rib 2 :
- Here the Contact has been created between Big Plate and Rib 2.
- The Contact Type is selected as Frictional with Frictional Coefficient of 0.2.The contact created is shown in below Figure 22.
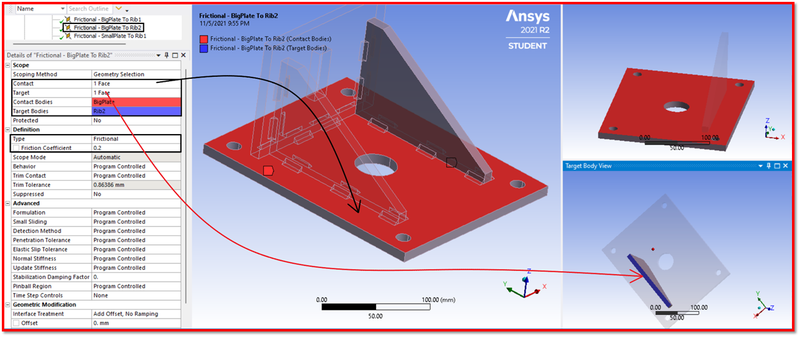
Figure 22-Contact Between Big Plate and Rib 2. |
5) Contact Between Small Plate and Rib 1 :
- Here the Contact has been created between Small Plate and Rib 1.
- The Contact Type is selected as Frictional with Frictional Coefficient of 0.2.The contact created is shown in below Figure 23.
Figure 23-Contact Between Small Plate and Rib 1. |
5) Contact Between Small Plate and Rib 2 :
- Here the Contact has been created between Small Plate and Rib 2.
- The Contact Type is selected as Frictional with Frictional Coefficient of 0.2.The contact created is shown in below Figure 24.
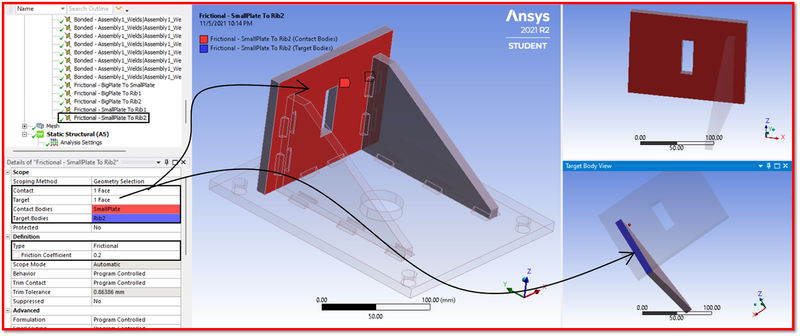
Figure 24-Contact Between Small Plate and Rib 2. |
3:3 Meshing :
- After defining the connections ,We have to define mesh for the Welding Model.
- To define Mesh,Click on the Mesh >> Default.Which is shown in below Figure 25.
- Here we are refining the mesh for the Big and Small Plates,Cause we have to see the stress developed at the Contact between Big and Small Plates Bodies,So we are refining the mesh for the Big and Small Plates Bodies.
- To refine a mesh,Click on the Mesh >> Insert >> Sizing >> Select the Big and Small Plate by using Solid Filter >> Mesh Size as 7 mm.Which is shown in below Figures 26 and 27.
- Element Size = Default
- Body Mesh Element Size = 7 mm
- Meshing Method =Hexahedrons
- No of Nodes = 24913
- No of Elements = 3976
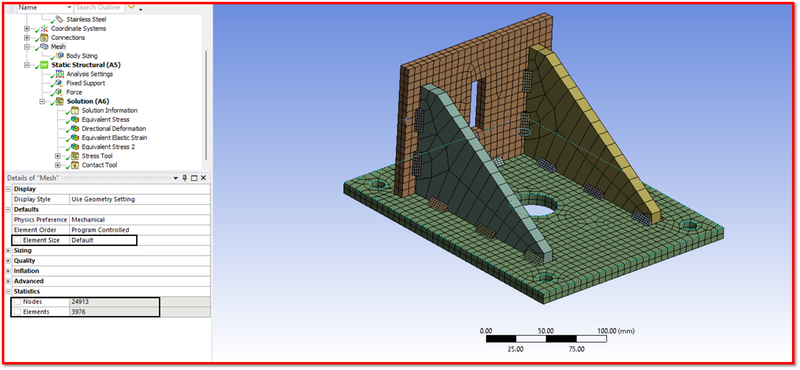
Figure 25-Meshed Welding Model as Default . |
- Now Refine the mesh in the Big and Small Plate Faces,Where it Comes to a Contact.
- The refined mesh is shown in below Figure 25.
- To Refine Mesh >> Right Click on Mesh >> Insert >> Sizing >> Body Sizing Mesh Size=7 mm >> Select Bodies of Big and Small Plate,Which is shown in below Figure 27.
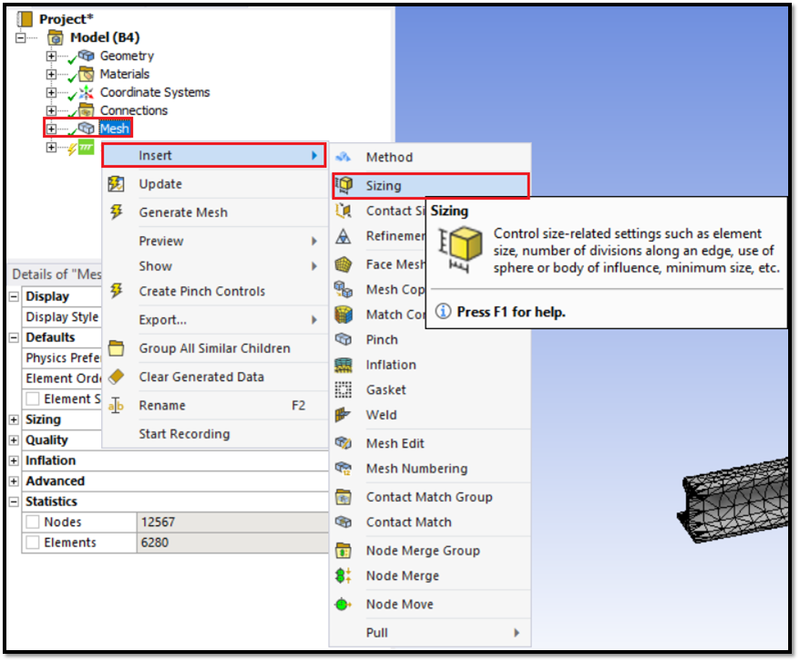
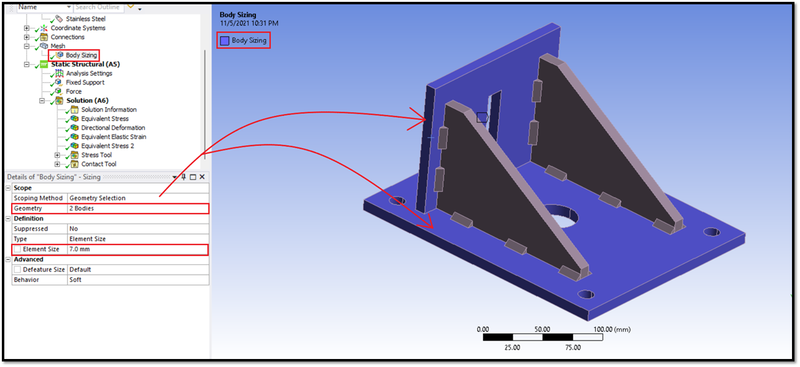
Figure 27-Bodies Selected to Refine the Mesh. |
3:4 Analysis Settings :
- Here for this Welding Model,We are giving just only one number of step for this simulation.
- Auto Time Stepping-Program Controlled.
- Solver Type-Program Controlled.
- Large Deflection-ON.
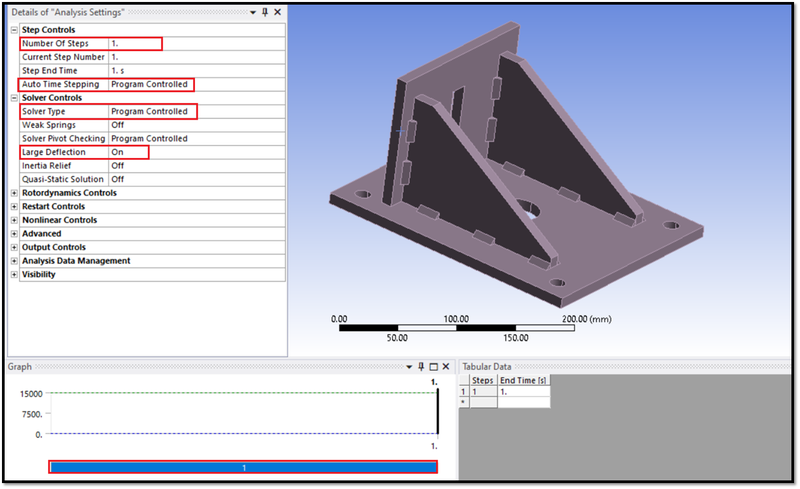
Figure 28-Analaysis Settings. |
3:5 Boundary Conditions :
- After giving some parameters in the analysis settings,We have to give boundary conditions.
- Here we have to create two boundary conditions,One is Fixed Support and other is we have to give force.
- To give fiixed support and force,Right Click on the Static Structural >> Insert >> Force and Fixed Support.Which is shown in below Figure 29.
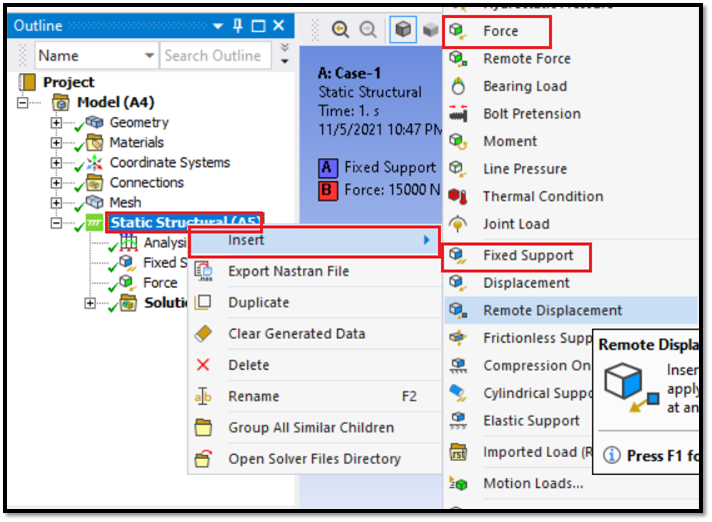
Figure 29-Give Fixed Support and Force. |
1) Fixed Support :
- Here we are fixing the big plate,To fix the bigger plate,We are selecting all the mounting hole faces.
- The fixed support of the bigger plate is shown in below Figure 30.
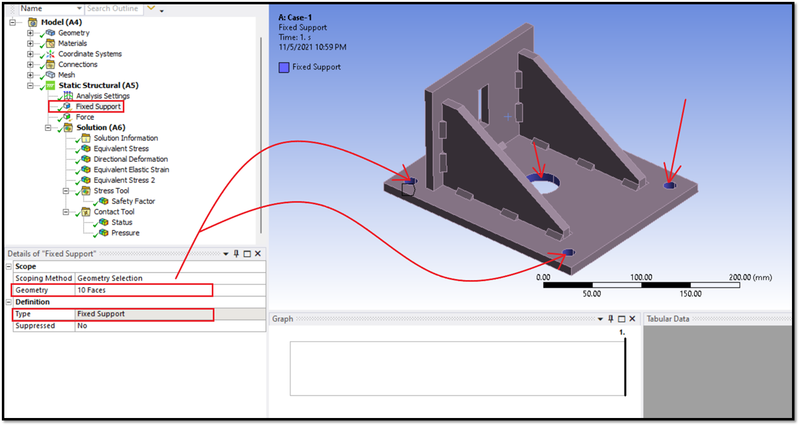
2) Force :
- Here apply a 1500000 N load on a Rectangular Hole Inner Face in the smaller plate which is shown in below Figure 31.
- The applied Force of 1500000 N on Rectangulr Hole Inner Face is shown in below Figure 31.
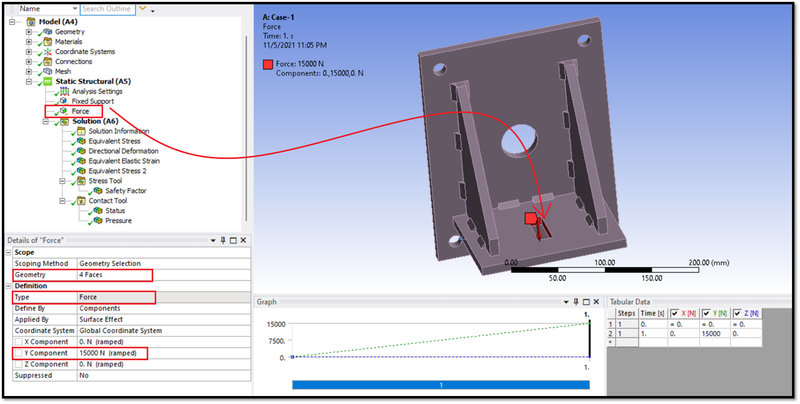
Figure 31-Force Applied on the Rectangular Inner Face. |
Phase 4-Request for the Outputs :
- Here we have to request outputs for the VonMisses Stress, Strain, and for Total Deformation.
- To request Output for Stress,Right Click on the Solution >> Insert >> Stress >> Equivalent Von Misses Stress.
- To request Output for Strain,Right Click on the Solution >> Insert >> Strain >> Equivalent Von Misses Strain.
- To request Output for Total Deformation,Right Click on the Solution >> Insert >> Deformation >> Total Deformation.
- This is shown in below Figure 32.
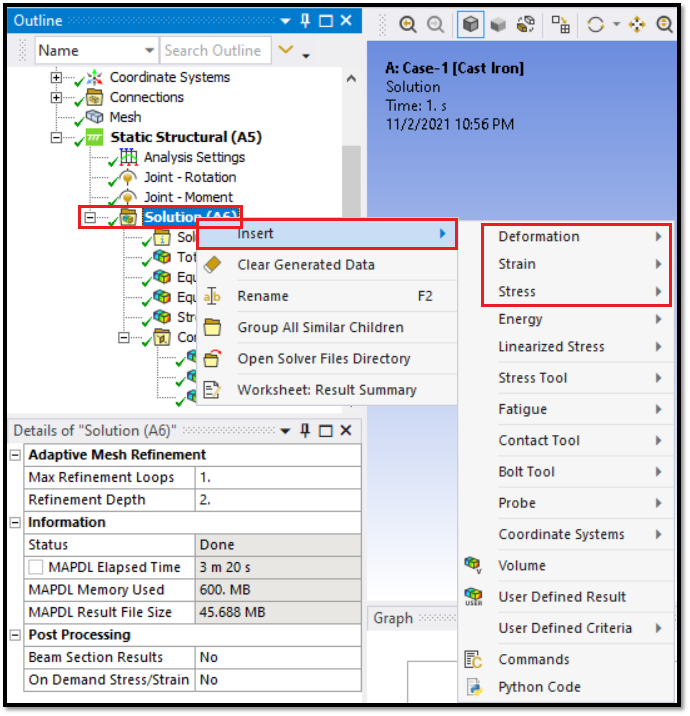
Figure 32-Requesting Outputs for the Stress, Strain, and Deformation. |
- Next request output for the contact.
- To request Contact Tool >> Right Click on the Solution >> Insert >> Contact Tool >> Pressure >> Status,Which is shown in below Figures 33 and 34.
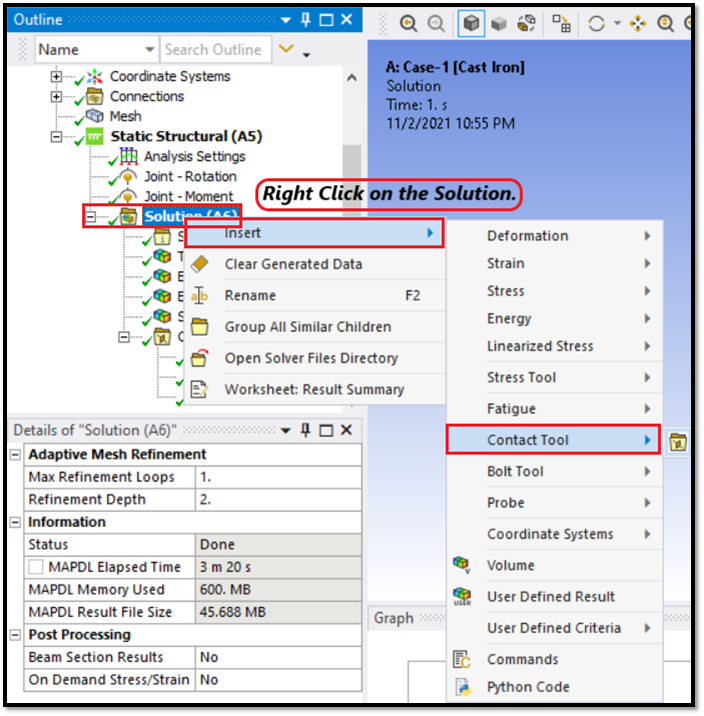
Figure 33-Requesting Output for Contact. |
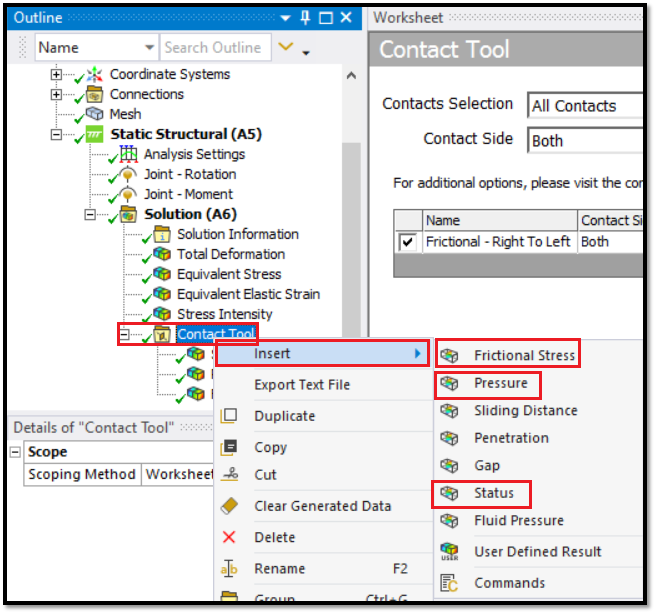
Figure 34-Requesting Outputs for Contact Tool. |
- Simillarly request the outputs for the Stress Tool.
- The Output requested for the Welding Model is shown in below Figure 35.
- After requesting all the outputs which is shown in below Figure 35. Run the Simulation.
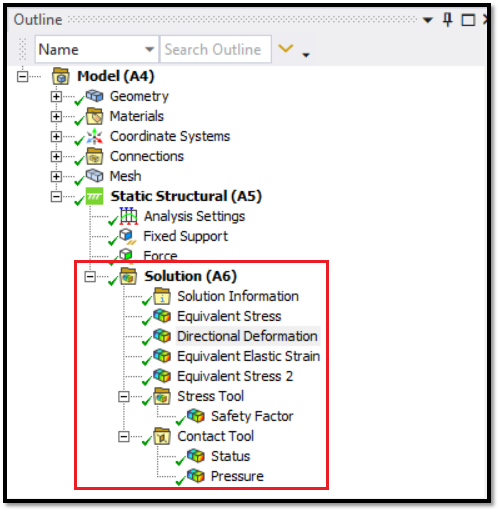
Figure 35-Required Outputs Requested. |
Phase 5-Run the Simulation for all the three Cases :
- To run the simulation, Right Click on the Solution >> Solve. This is shown in below Figure 36.
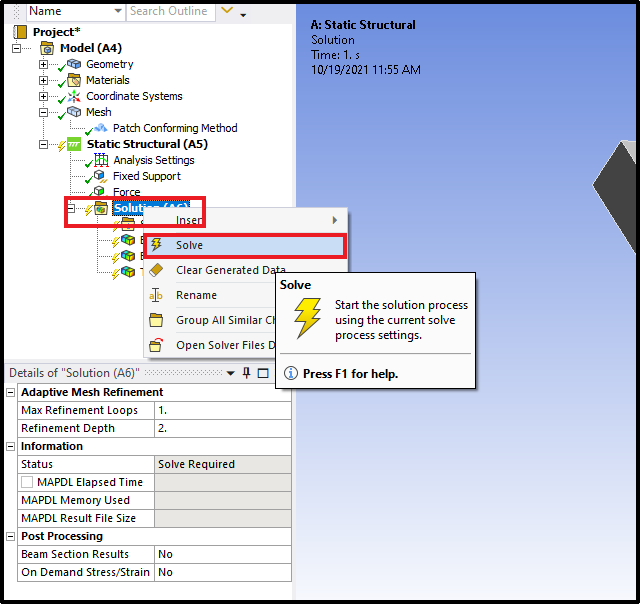
Figure 36-Solve all the Outputs Requested. |
- After solving the outputs requested, the simulation results forthe two cases is shown in the below Figures.
Equivalent Von Misses Stress [Case 1 : Stainless Steel-Welded Joints,Plates and Ribs] :
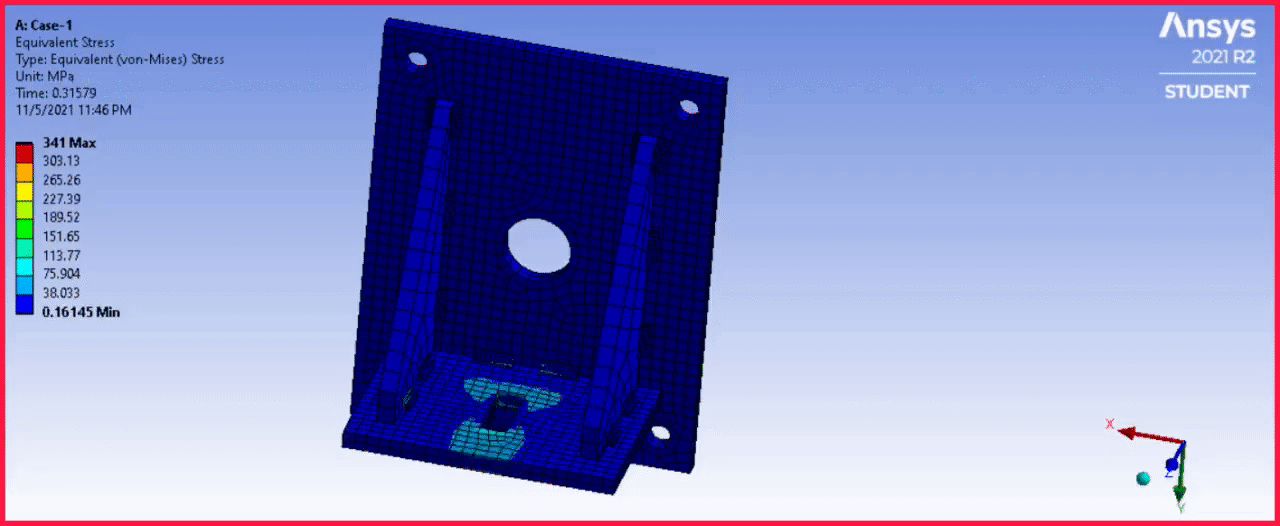
Figure 37-Equivalent Von Misses Stress [Case-1]. |
Equivalent Von Misses Stress [Case 2 : Aluminium Alloy (High Strength and Wrought)-Welded Joints,Stainless Steel-Big Plate, Small Plate and Ribs] :
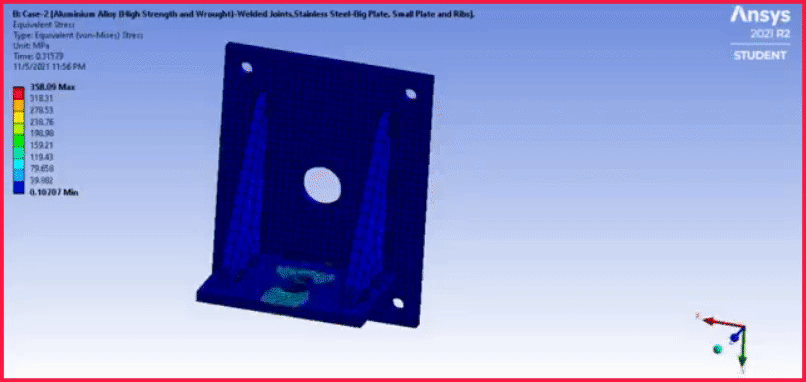
Figure 38-Equivalent Von Misses Stress [Case-2]. |
Equivalent Von Misses Stress [Case 3: Cast Bronze -Welded Joints,Stainless Steel-Big Plate and Small Plate,Copper-Ribs] :
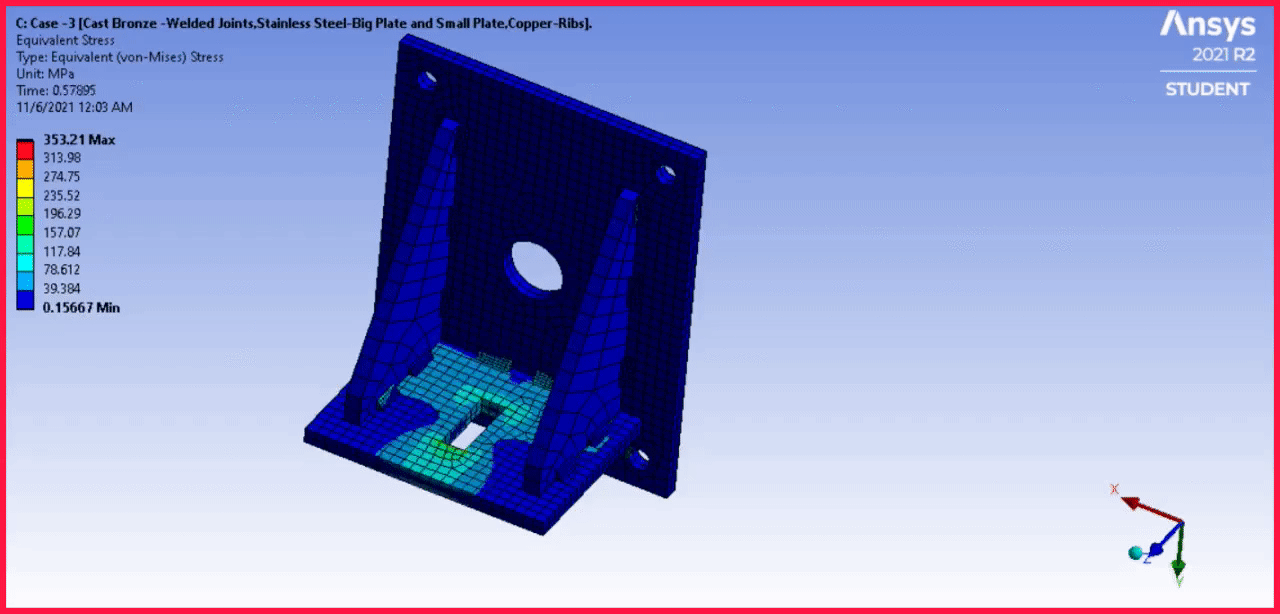
Figure 39-Equivalent Von Misses Stress [Case-3]. |
Equivalent Elastic Strain [Case 1 : Stainless Steel-Welded Joints,Plates and Ribs] :
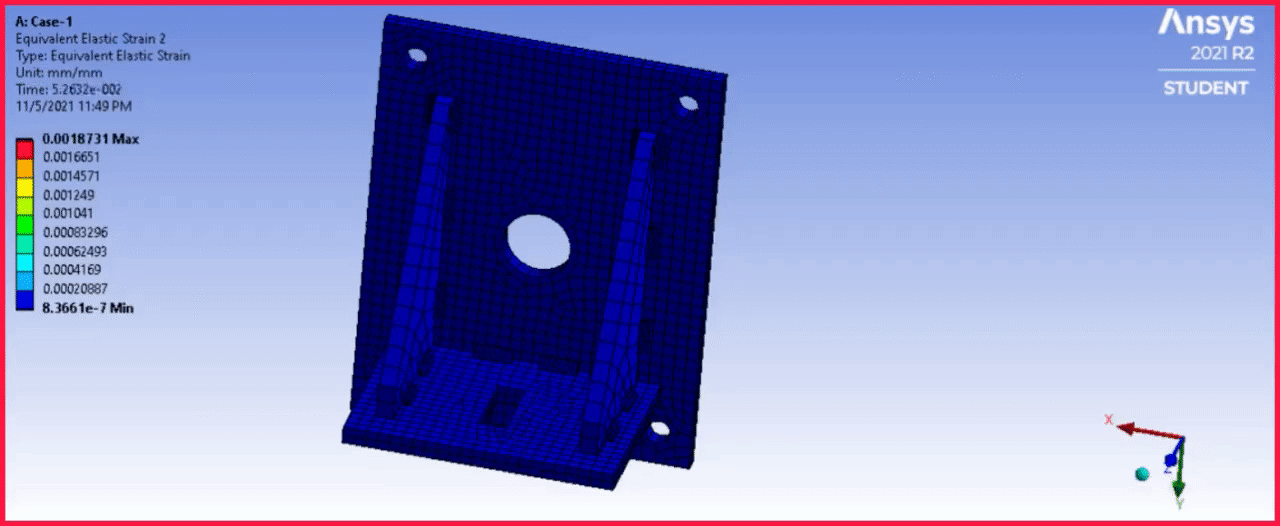
Figure 40-Equivalent Elastic Strain [Case-1]. |
Equivalent Elastic Strain [Case 2 : Aluminium Alloy (High Strength and Wrought)-Welded Joints,Stainless Steel-Big Plate, Small Plate and Ribs] :
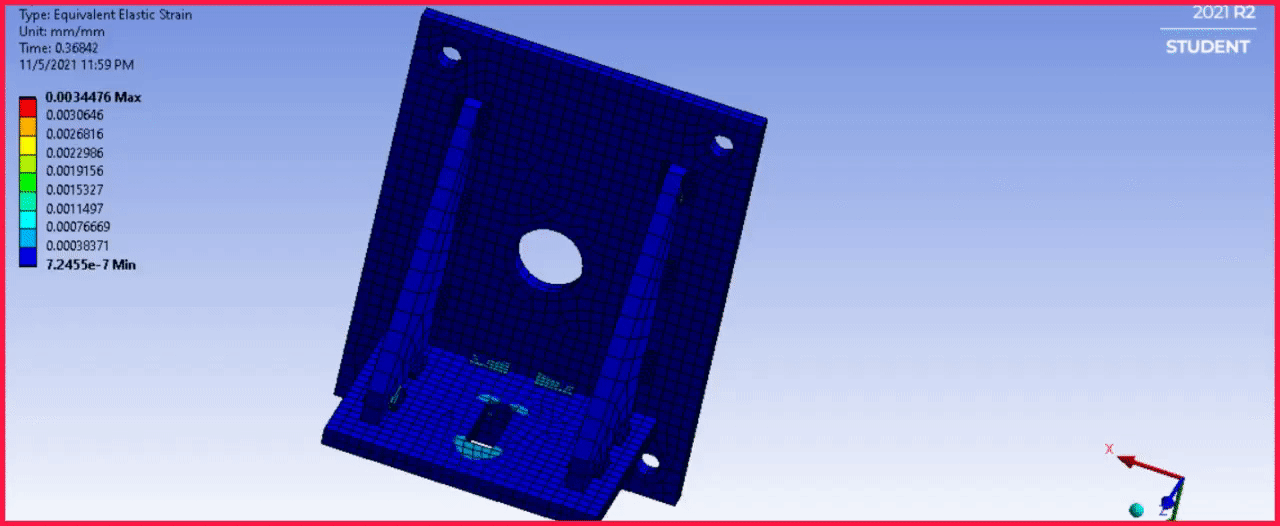
Figure 41-Equivalent Elastic Strain [Case-2]. |
Equivalent Elastic Strain [Case 3: Cast Bronze -Welded Joints,Stainless Steel-Big Plate and Small Plate,Copper-Ribs] :
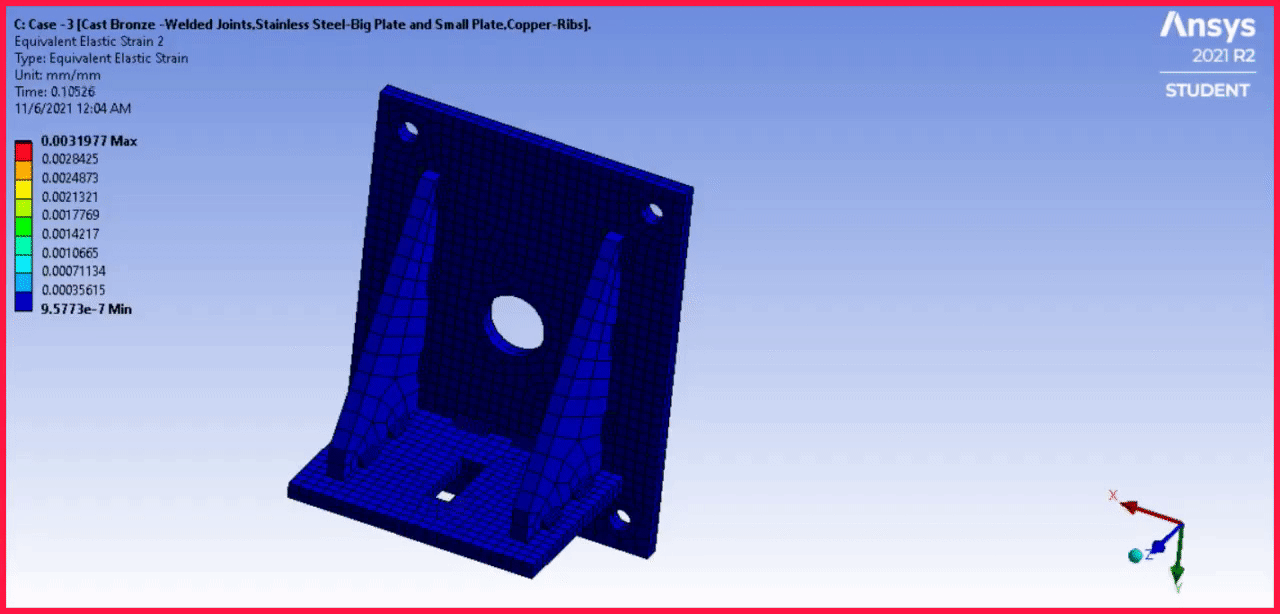
Figure 42-Equivalent Elastic Strain [Case-3]. |
Directional Deformation Case-1 :
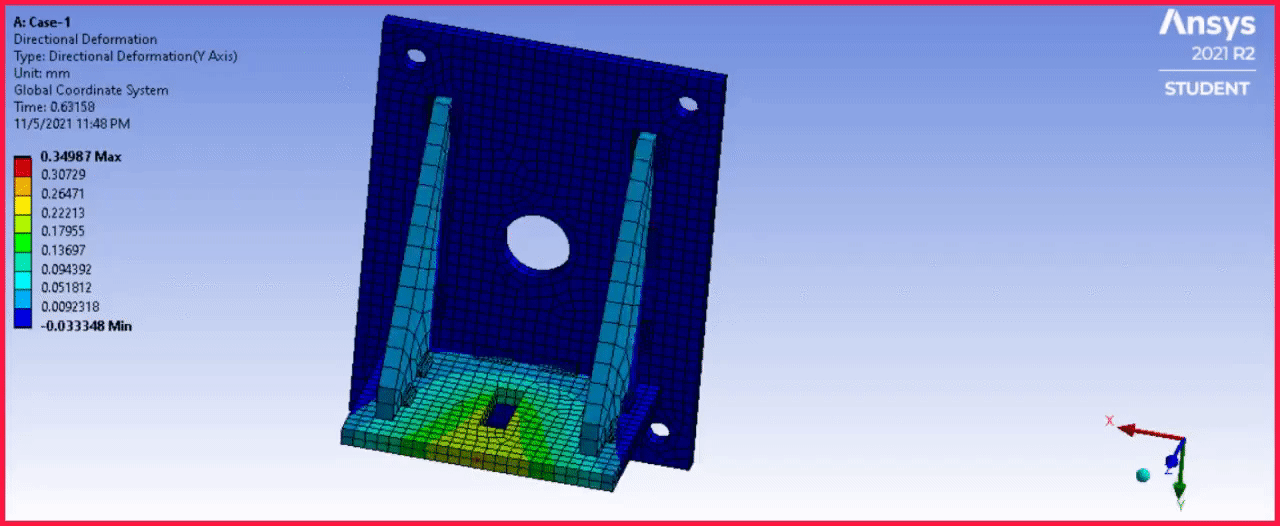
Figure 43-Directional Deformation [Case-1]. |
Directional Deformation Case-2 :
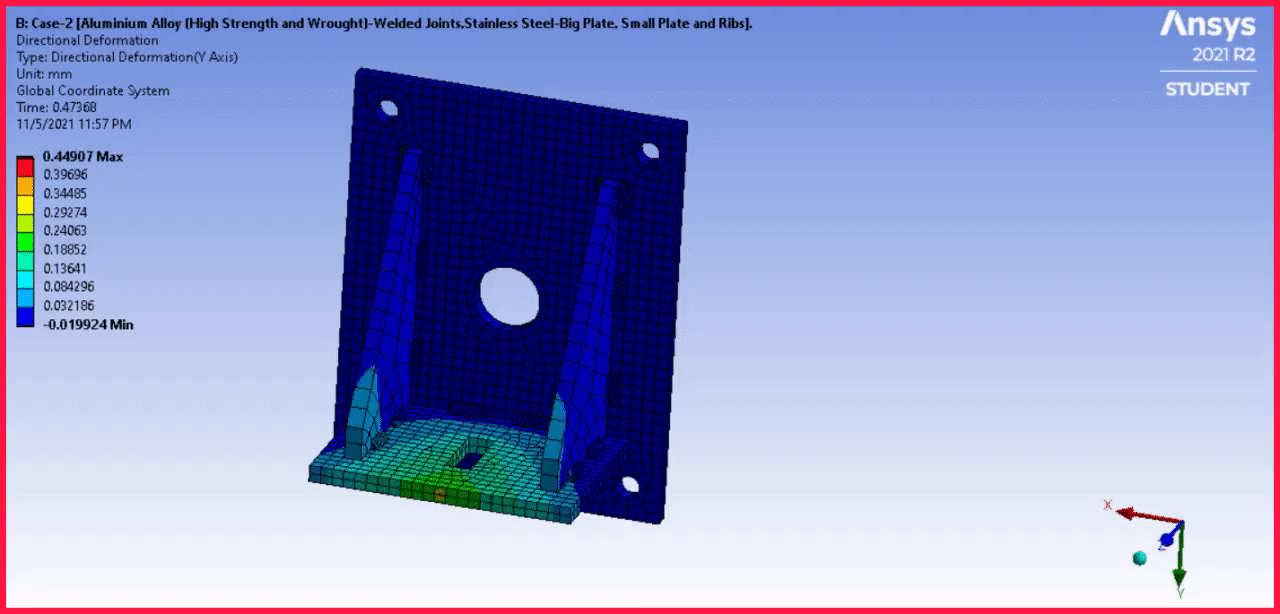
Figure 44-Directional Deformation [Case-2]. |
Directional Deformation Case-3 :
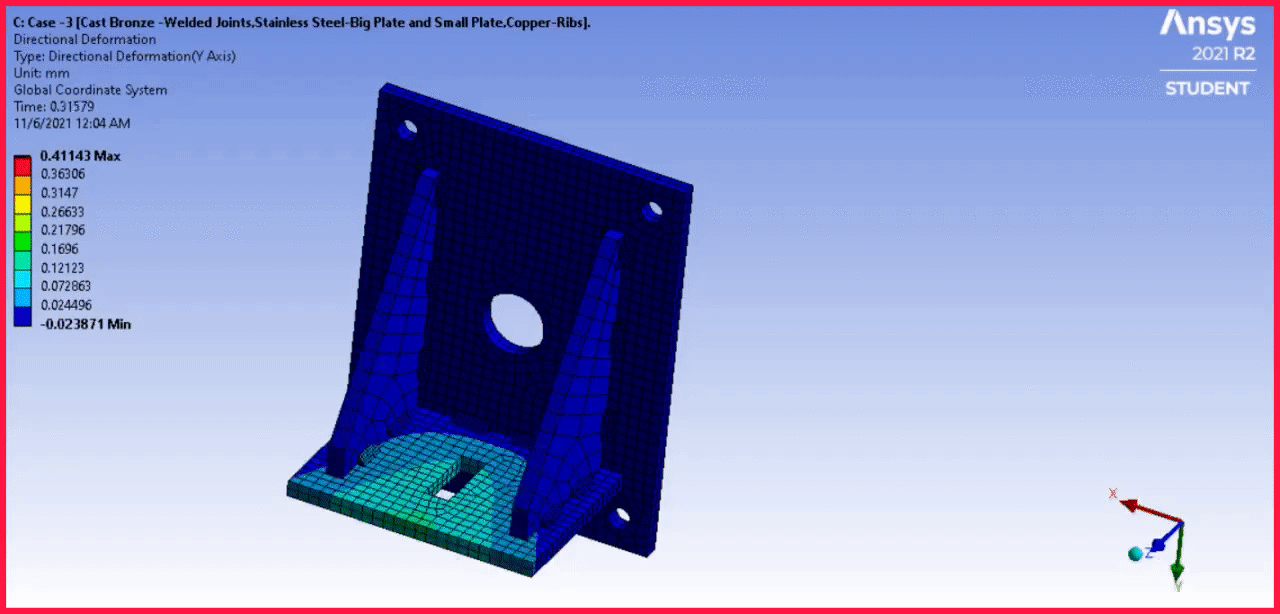
Figure 44-Directional Deformation [Case-3]. |
Equivalent Stress Welded Joints Case-1 :
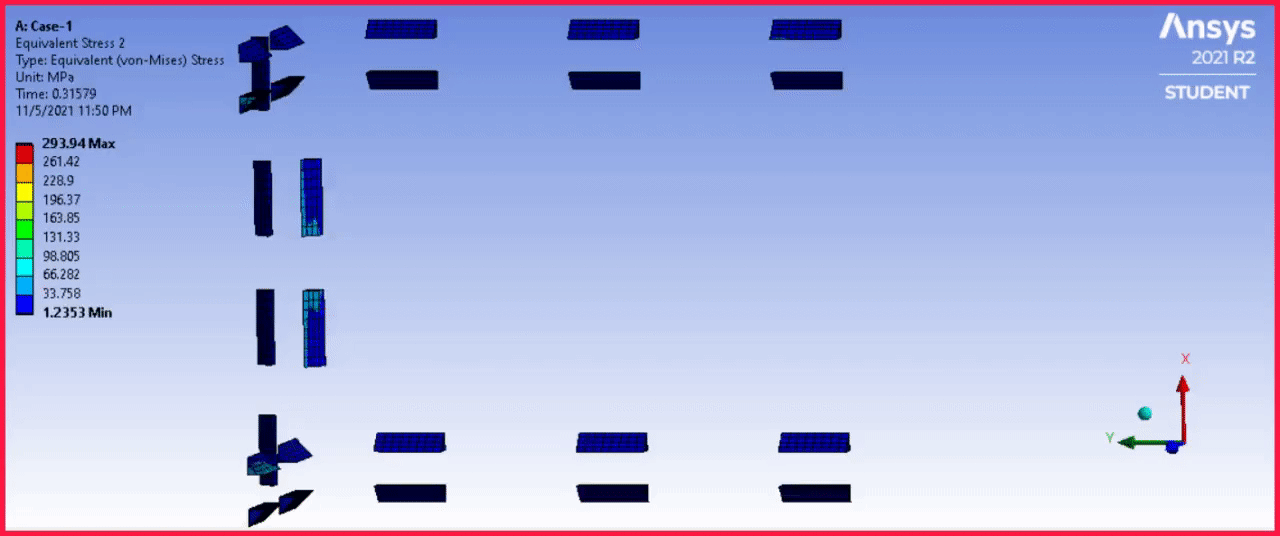
Figure 45-Equivalent Stress Welded Joints [Case-1]. |
Equivalent Stress Welded Joints Case-2 :
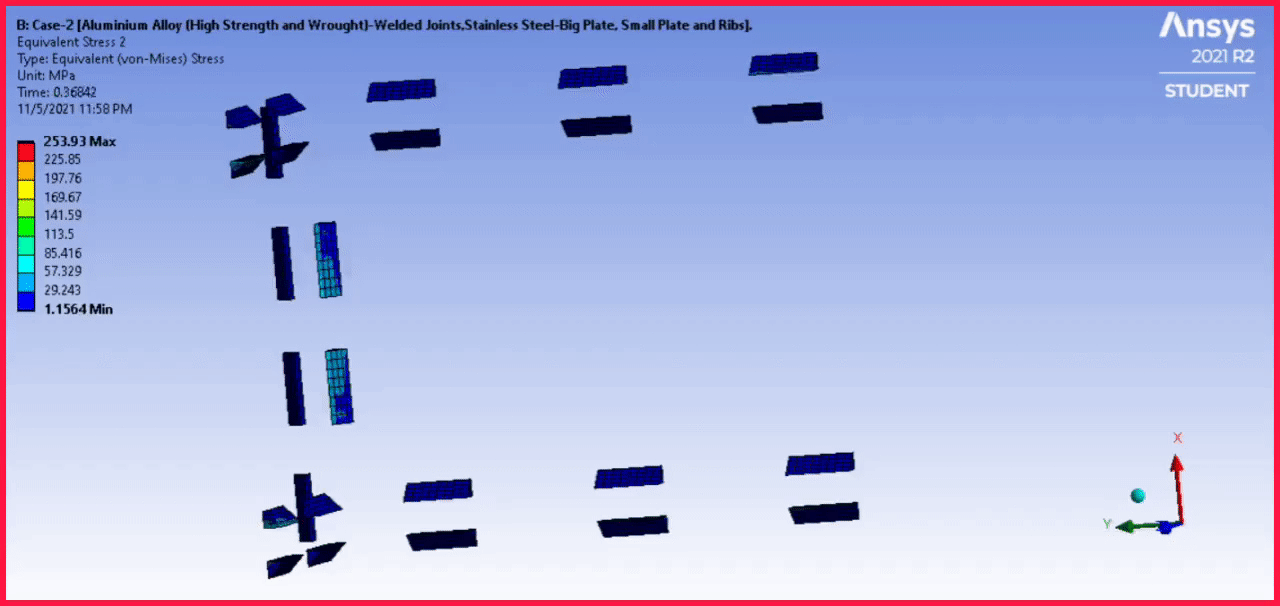
Figure 46-Equivalent Stress Welded Joints [Case-2]. |
Equivalent Stress Welded Joints Case-3 :
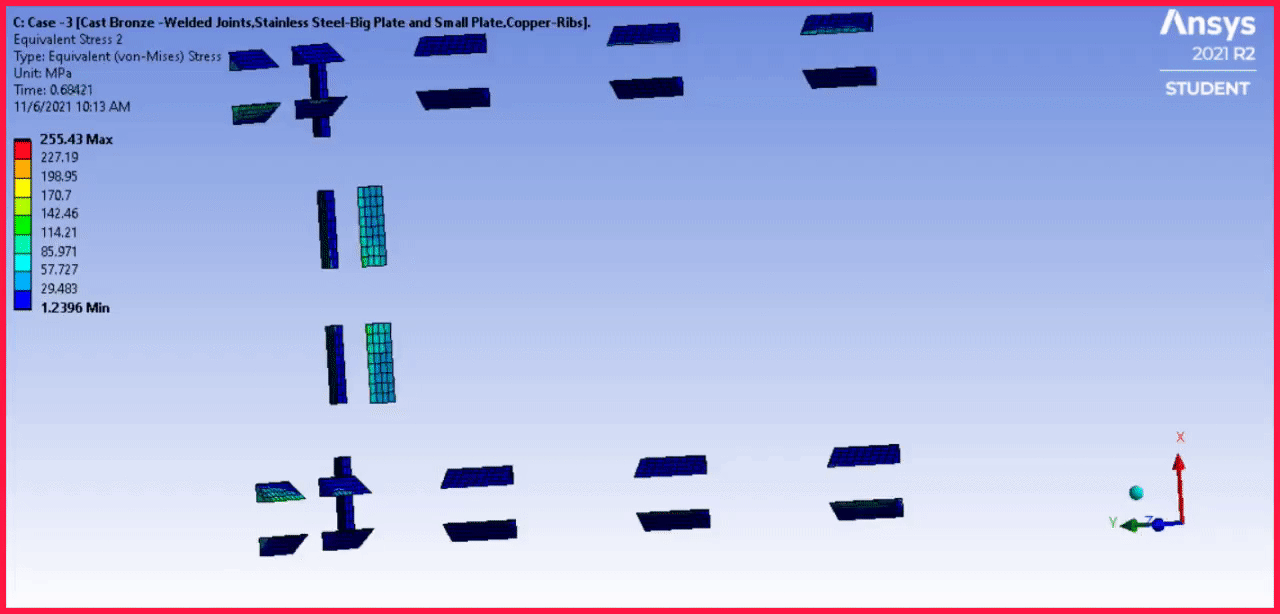
Figure 47-Equivalent Stress Welded Joints [Case-3]. |
Saftey Factor Case-1 :
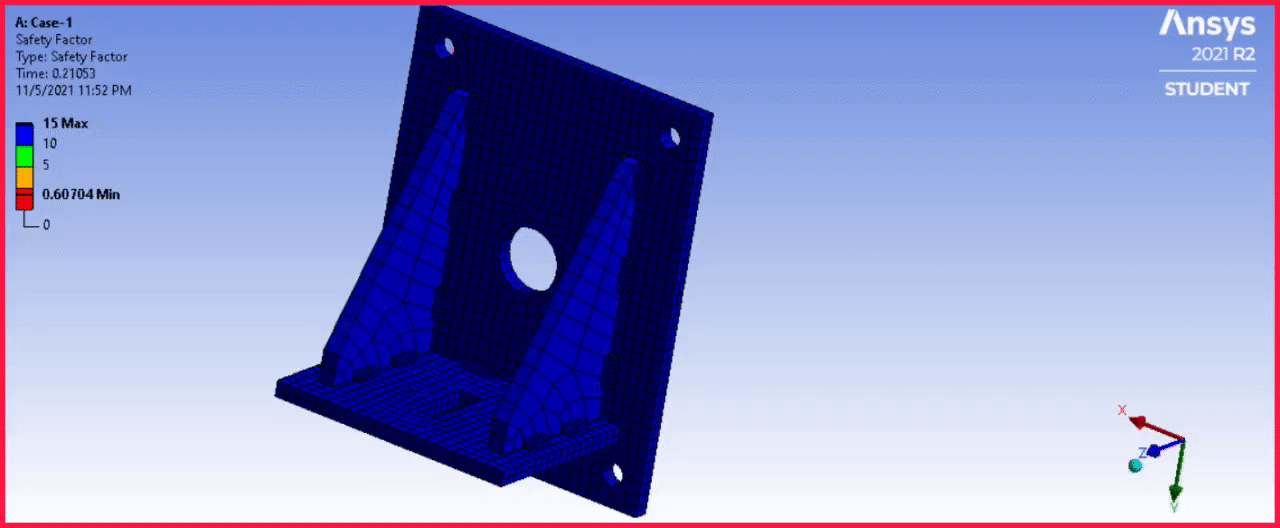
Figure 48-Saftey Factor [Case-1]. |
Saftey Factor Case-2 :
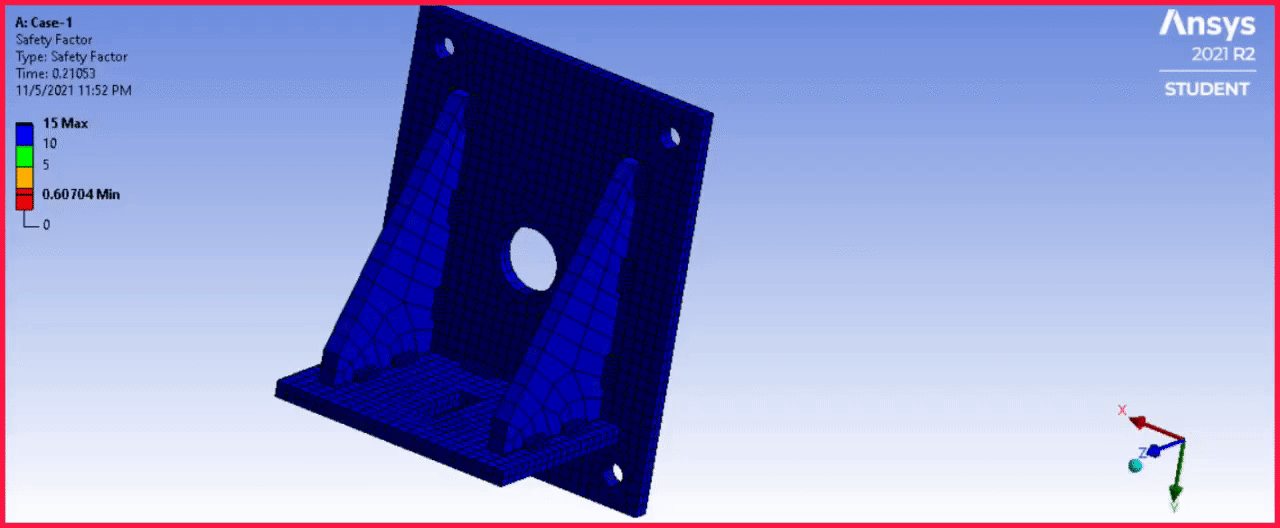
Figure 49-Saftey Factor [Case-2]. |
Saftey Factor Case-3 :
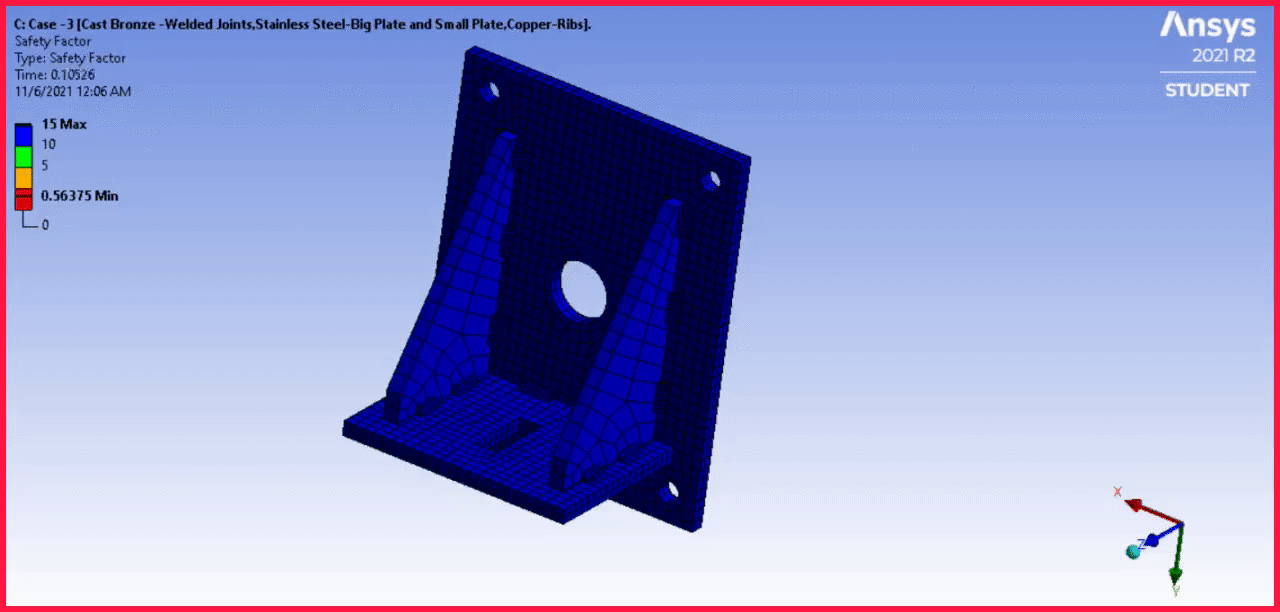
Figure 50-Saftey Factor [Case-3]. |
Comparison of Results :
Cases
|
Von-Misses Stress (MPa)
|
Directional Deformation (mm)
|
Equivalent Elastic Strain (mm/mm)
|
Equivalent Von Misses Stress for Welded Joints
|
Saftey Factor
|
Max.
|
Min.
|
Max.
|
Min.
|
Max.
|
Min.
|
Max.
|
Min. |
Max. |
Min. |
Case-1 [Stainless Steel for Welded Joints,Ribs and Plates]
|
341MPa
|
0.16145MPa
|
0.34987 mm
|
-3.3348e-002 mm
|
0.0018731 mm/mm
|
8.3661e-007 mm/mm
|
293.94 MPa
|
1.2353 MPa |
15 |
0.60704 |
Case-2 [Aluminium Alloy-Welded Joints,Satinless Steel-Ribs and Plates]
|
358.09 MPa
|
0.10707 MPa
|
0.44907 mm
|
-1.9924e-002 mm
|
0.0034476 mm/mm
|
7.2455e-007 mm/mm
|
253.93 MPa
|
1.1564 MPa |
15 |
0.57807 |
Case-3 [Cast Bronze-Welded Joints,Copper-Ribs,Stainless Steel-Plates]
|
353.21 MPa
|
0.15667 MPa
|
0.41143 mm
|
-2.3871e-002 mm
|
0.0031977
|
9.5773e-007 mm/mm
|
255.43 MPa
|
1.2396 MPa |
15 |
0.56375 |
- Here the maximum deformation is occured in the Case-2,The Maximum Directional Deformation occured in the Case-2 is 0.44907 mm.The deformation is high when compared to the two cases.
- The Welding model with Stainless Steel deformation is less when compared to the two other cases.The Maximum Deformation occured in the Case-1 [Stainless Steel] is 0.34987 mm.
- The maximum equivalent elastic strain developed in the stainless steel weldments is low when compared to the two other cases.
- The maximum equivalent stress developed in the stainless steel welded joints is 293.94 Mpa,It is high when compared to the two other cases.The tensile yield strength value of stainless steel is 207 Mpa,Here the stress developed in the stainless steel welded joints is beyond the yield strength of the material,Here the material will fail and it undergoes plastic deformation.
- Simillarly the stress developed in the cast bronze welded joints is 255.43 Mpa.The yield strength of the cast bronze is 144 Mpa,The stress developed in the welded joints is more than the yield strength of the matreial,It will also fail and it undergoes plastic deformation.
- But the stress developed in the Aluminium Alloy Welded Joints is 253.93 Mpa,The yield strength of the Aluminium Alloy is 363 Mpa,The stress developed in the weldd joints is less than the yield strength of the material.If we chooses aluminium alloy as a material for the welded joints,It will not fail and it will not undergo plastic deformation.
- So I'm concluding that,Aluminium Alloy is prefferable material for Welded Joints,Because the stress developed in the aluminum alloy dosen't go beyond the yield strength of the material,There will be no plastic deformation,So preferred choice is Aluminium Alloy.
[Note: We can't say this case is preferable, this case is not preferable, Anyhow it depends on the application. Here in the report, I have said, Case-2 with Aluminium Alloy is preferable,Cause it won't undergo plastic deformation and it won't leads to failure.But other two cases will undergo plastic deformation and leads to failure,So here,I have told the Case-2 is preferrable and other two cases are not preferrable according to the question and the model given to us, But in real life, It entirely depends on the applications.]
Case-1 [Welded Joints with Stainless Steel] :
- The factor of Saftey = Yield Strength/Working Stress
- Tesnsile Yield Strength of Stainless Steel=207 Mpa
- Working Stress [Maximum Stress]=293.94 Mpa
- FOS=207293.94
- FOS=0.70
- Here the FOS what we got is 0.70,It is not ok,The material will fail,It is not Safe.The Standard FOS ranges from 1-5 in industries.
Case-2 [Welded Joints with Aluminium Alloy] :
- The factor of Saftey = Yield Strength/Working Stress
- Tesnsile Yield Strength of Aluminium Alloy=363 Mpa
- Working Stress [Maximum Stress]=253.93 Mpa
- FOS=363253.93
- FOS=1.42
- Here the FOS what we got is 1.42,The FOS is greater than 1.It is ok,The material will not fail,It is Safe.If we choose Aluminium Alloy as Material for the Welded Joints,The material will not fail.The Standard FOS ranges from 1-5 in industries.
Case-3 [Welded Joints with Cast Bronze] :
- The factor of Saftey = Yield Strength/Working Stress
- Tesnsile Yield Strength of Stainless Steel=144 Mpa
- Working Stress [Maximum Stress]=255.43 Mpa
- FOS=144255.43
- FOS=0.56
- Here the FOS what we got is 0.56,It is not ok,The material will fail,It is not Safe.The Standard FOS ranges from 1-5 in industries.
Result :
- Hence the material has been defined for all the three cases.
- Hence the connections were defined to the Welding Model.
- Hence the model has been solved for Von-Misses Stress, Equivalent Elastic Strain,Stress Intensity,Contact Tool and Directional Deformation by applying appropriate boundary conditions.
- Hence the Fixed Support was applied to all the Mounting Holes to fix the welding model.
- Hence the force was given in the rectangular inner face.
- Hence the Welded Joints with Aluminium Alloy is preferred one,Cause the maximum stress developed is less than the yield strength of the material and it will not undergo plastic deformation and it will not lead to failure.
Conclusion and Learning Outcome :
In this Week 3 Verification of Weld Joints Challenge, I came to know about
- Learned how to give Fixed Support and Force to the model.
- Learned how to assign materials to the model.
- Learned how to apply boundary conditions to the model.
- Learned how to request outputs and solve them.
- Learned about the Force Convergence.