Static Structural Analysis on the Rail Wheel and Track :
Aim -
- To perform static structural analysis on the Rail Wheel and Track,and solve for Von Misses Equivalent stress,Equivalent Elastic Strain and Total Deformation.
Objective :
- To perform a Structural Analysis on the Rail Wheel and Track for the two cases with the material Structural Steel.
- To apply bearing load on the railwheel and track setup with 100 KN and 500KN.
- To solve and compare the results of the two cases for Total Deformation, Von-Mises Stress and Equivalent Elastic Strain.
- To implement a User Defined Result and calculate the Total Deformation from this result and check if it is the same as that obtained by the inbuilt result by ANSYS for a load of 100000 N.
Theoretical FrameWork :
- A train wheel or rail wheel is a type of wheel specially designed for use on railway tracks. The wheel acts as a rolling component, typically pushed onto an axle and mounted directly on a railway carriage or locomotive. The powered wheels under the locomotive are called Driving Wheels. Wheels are initially cast or forged and then heat-treated to have a specific hardness.
- New wheels are machined using a lathe to a standardized shape, called a profile, before being installed onto an axle. All wheel profiles are regularly checked to ensure proper interaction between the wheel and the rail. Incorrectly profiled wheels and worn wheels can increase rolling resistance, reduce energy efficiency and may even cause a derailment.
- Rail generally suffers from very high stresses and has complicated stress zone with bending stresses, contact stresses and thermal stresses acting at a time. Continuous interaction of rail wheel interface results in high frictional stress, contact pressure and ultimately wear.
- Wear modifies wheel and rail profile, which as a matter of fact changes the nature of contact between rail and wheel and consequently may increase the Rolling Contact Fatigue rate, and results in shallow crack propagation in rails. Rolling Contact Fatigue can trigger damage and can lead to surface crack by the action of wear on the rail or by plastic deformation of the material.
- Area prone to wear is manifested by loss in material or plastic flow of metal. Thus, the profile of rail gradually changes because of high train traffic, enormous contact stresses, environmental conditions, etc. leading to failure.
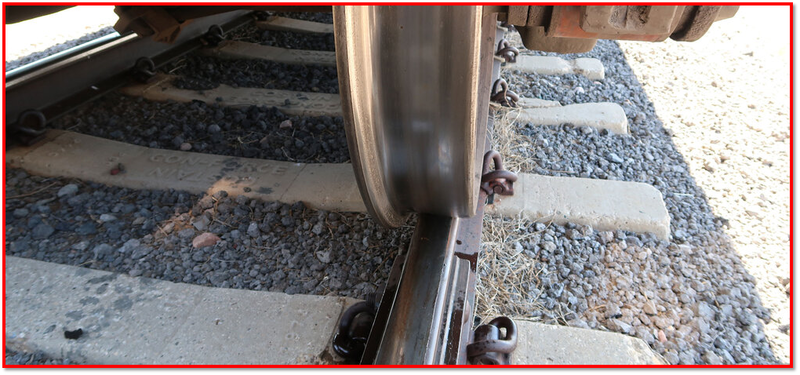
Figure 1-RailWheel and Track. |
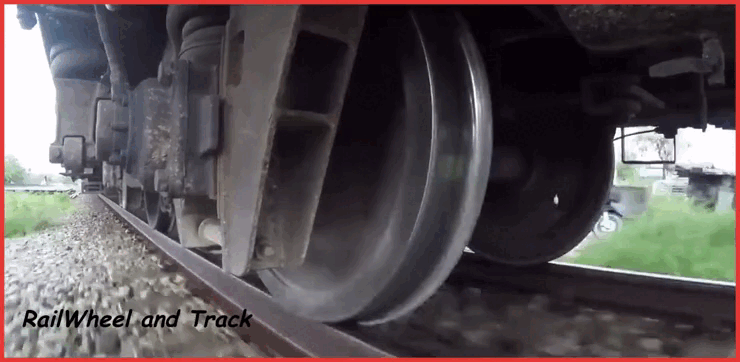
Figure 2-RailWheel and Track Animation. |
Procedure :
Phase 1- Material Set Up :
- To set up the material for the Rail Wheel and Track Model. First, drag and drop the static structural analysis workspace into the project schematic from the analysis system. This is shown in below Figure 3.

Figure 3-Ansys Workbench Workspace. |
- After deploying the static structural analysis system in the project schematic workspace.
- Define the Engineering Data and geometry, To define the Geometry and Engineering Data, Right Click on the Engineering Data and click to edit, it will take to the Engineering Tab.
- There Right Click on the Material Tab, A window will Pop-Up stating Engineering data sources.
- Click on the Engineering Data Sources, There go and select the material to define the engineering data. This is shown in below Figures 4,5,6.
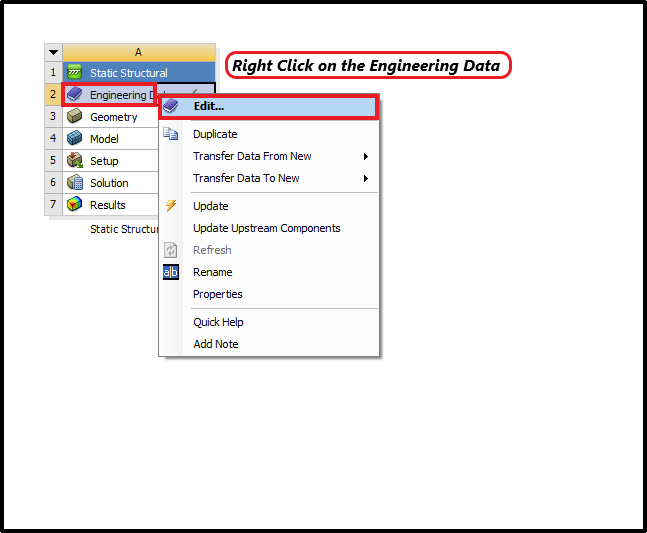
Figure 4-Right Click on the Engineering Data. |
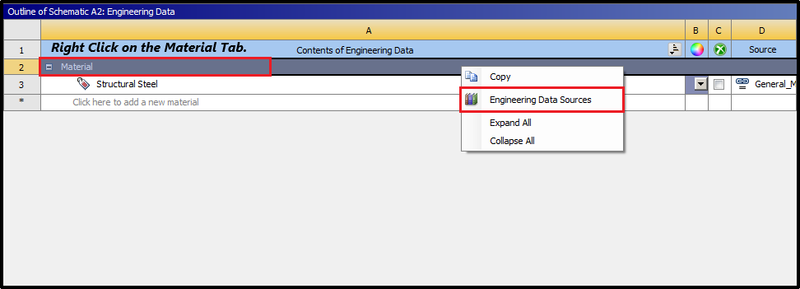
Figure 5-Right Click on the Material Tab. |
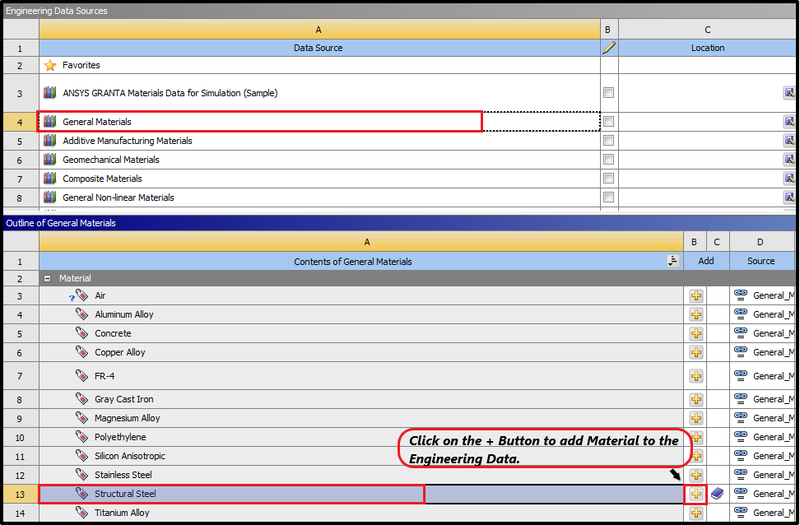
Figure 6-Select the Material as Structural Steel to Define the Engineering Data. |
Phase 2-Geometry Set Up :
- Next set up the geometry. To set up the geometry, Right-Click on the Geometry option >> Import Geometry. This is shown in below Figure 7.
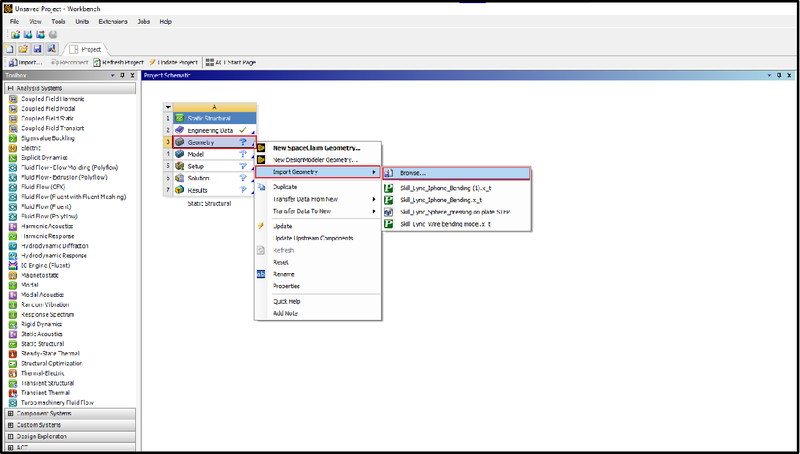
Figure 7-Importing Geometry. |
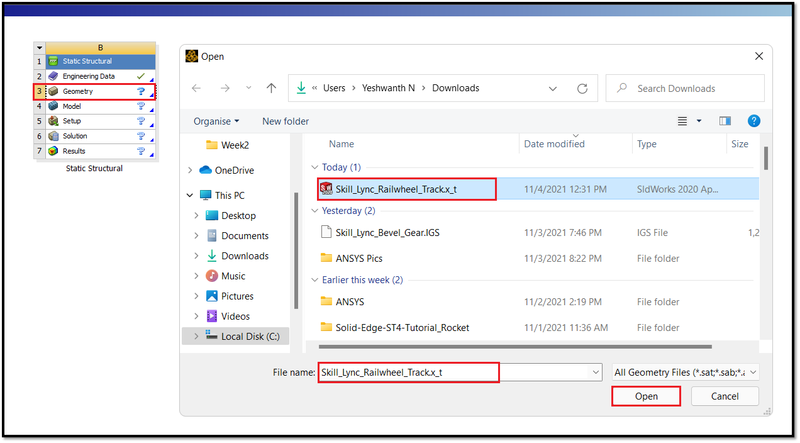
Figure 8-Selecting the Geometry to Import. |
- Next double click on the geometry to check, Whether the model imported is spur gear or not. Space Claim Workspace will open.The model will be imported in the space claim,Which is shown in below Figure 9.
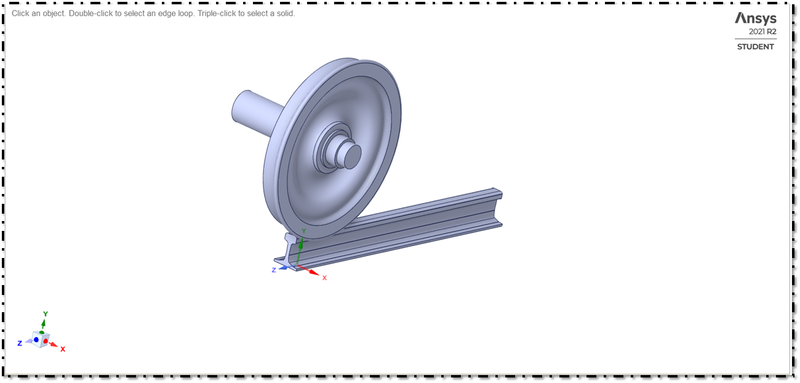
Figure 9-RailWheel and Track in the Space Claim. |
Phase 3-Model Set Up :
- Next, define the model, Double click on the model, The Mechanical Workspace will open, There go and define the material,set up the load case for all three cases.
- The Model loaded in the mechanical workspace is shown in below Figure 10.
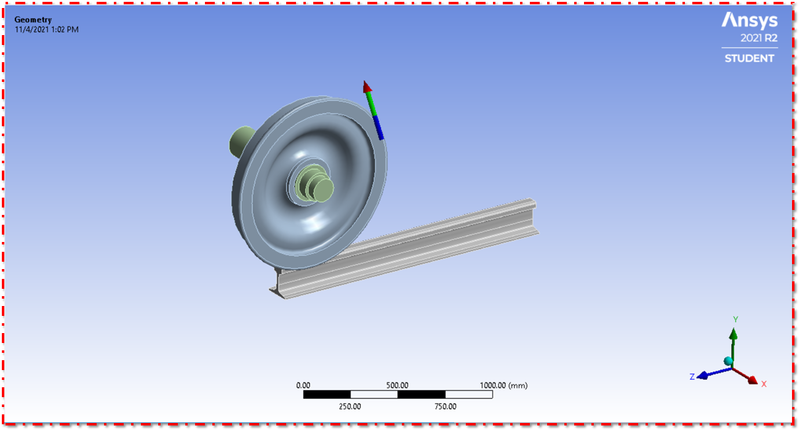
Figure 10-Model Loaded in Mechanical Workspace. |
3:1 Assign Material :
- Next define the material as structural steel for the Rail Wheel and Track which is shown in below Figure 11.
- Simillarly define the material for other case.The material properties is shown in below Figures 12.
- To assign a material,Click on the Geometry Bevel Gear >> Parameter Window >> Assignment >> Structural Steel.
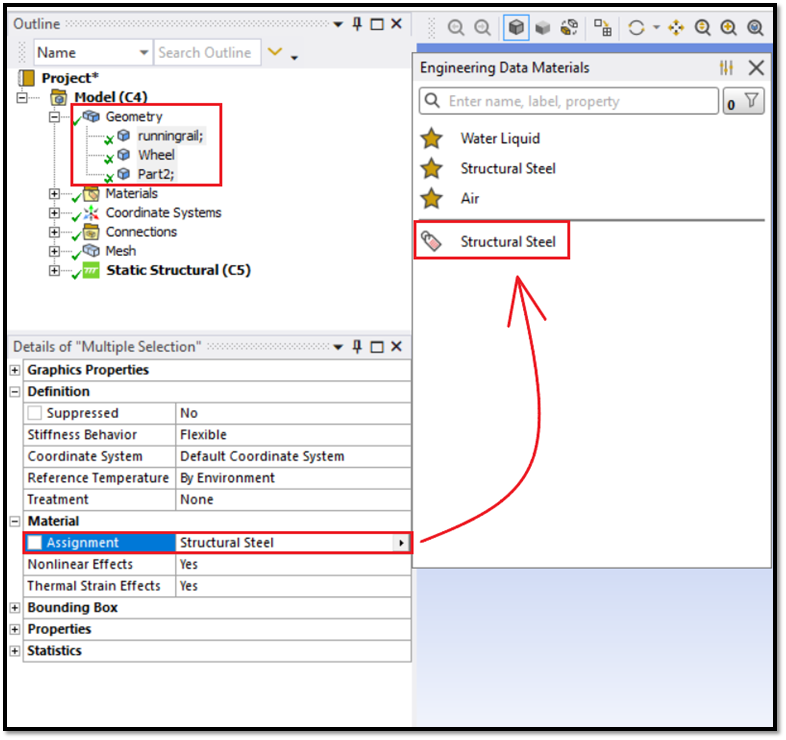
Figure 11-Define Material. |
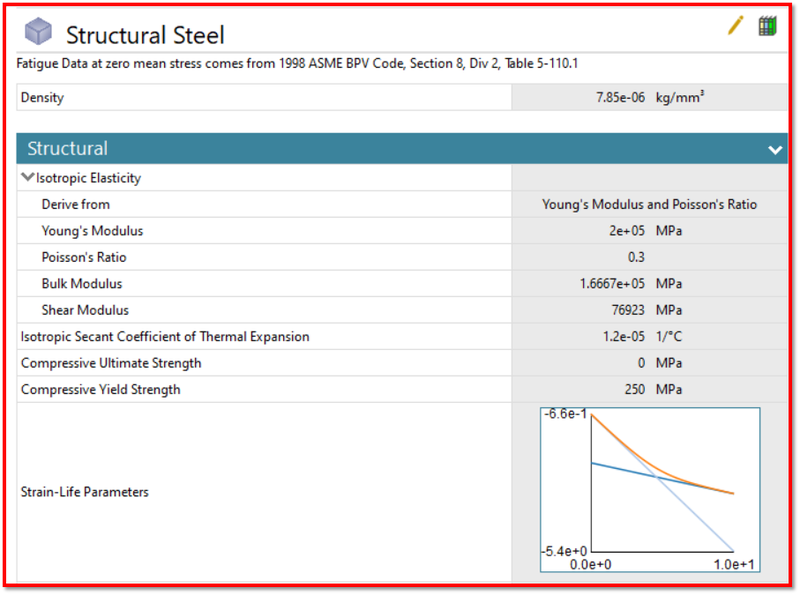
Figure 12-Mechanical Properties of Structural Steel. |
3:2 Define Connections :
- Next after defining the material,Now define the contact for the Rail Wheel and Track.
- To define a contact,First right click on the default contact and rename it as rename based on definition,Which is shown in below Figure 13.
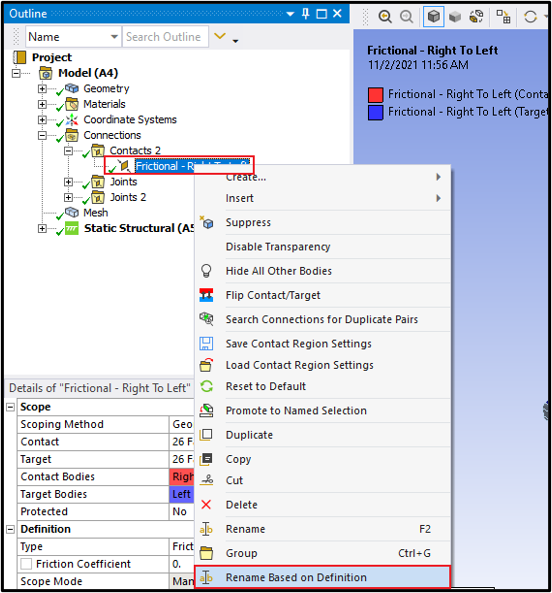
Figure 13-Rename Based on Definition. |
- We can also create the Connections manually,To create the Connections >> Right Click on the Connections >> Insert >> Manual Contact Region.Which is shown in below Figure 14.
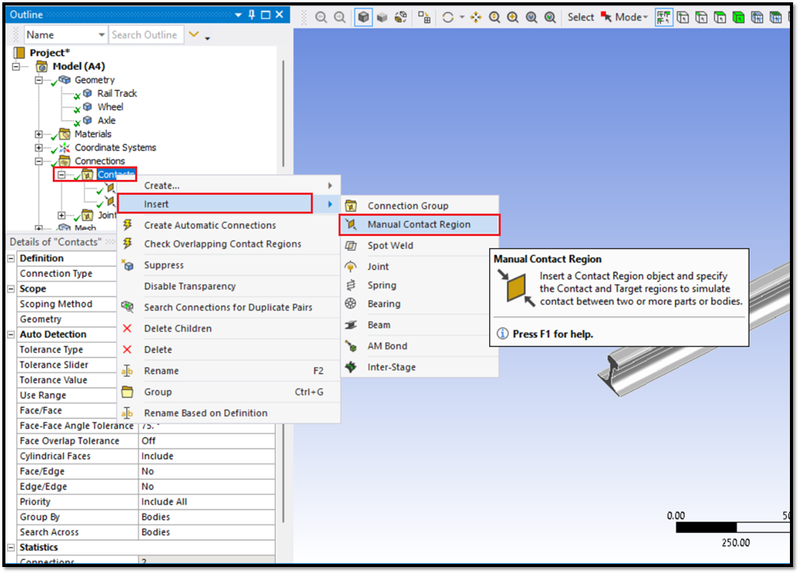
Figure 14-Create the Connections. |
1) Contact Between Wheel and Rail Track :
- Now define the contact which is shown in below Figure 16.
- Select the Contact and Target faces of the Wheel and Rail Track which is shown in below Figure 16.
- Select the wheel outer faces for the contact.
- Select the rail track faces for the target.
- Type of Contact is Frictional with the Frictional Coefficient of 0.3.
- Keep Add Offset, No Ramping for Interface treatment.
- Keep remaining parameters as it is default.
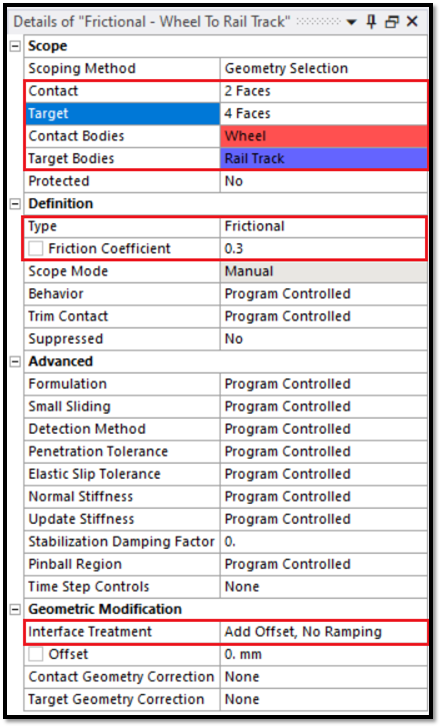
Figure 15-Connection Parameters for Wheel and Rail Track. |
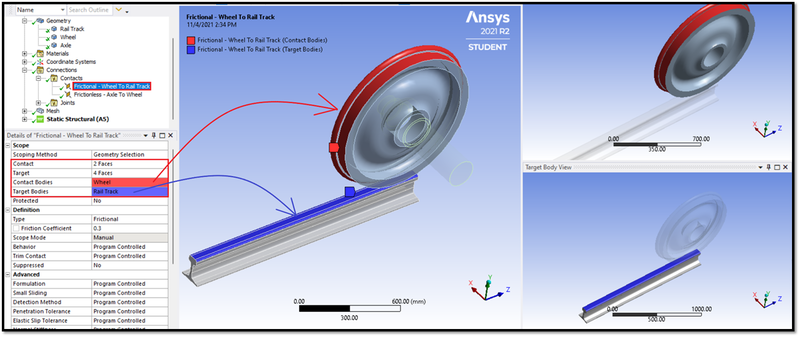
Figure 16-Contact Defined Between Wheel and Rail Track. |
2) Contact Between Axle and Wheel :
- Now define the contact which is shown in below Figure 18.
- Select the Contact and Target faces of the Wheel and Axle which is shown in below Figure 18.
- Select the axle outer faces for the contact.
- Select the wheel inner hole faces for the target.
- Type of contact is Frictionless. Because, it's a dead axle.
- Keep Add Offset, No Ramping for Interface treatment.
- Keep remaining parameters as it is default.
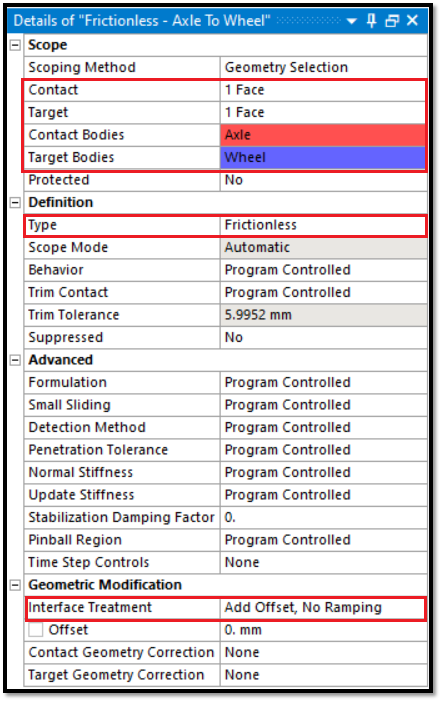
Figure 17-Connection Parameters for Wheel and Axle. |
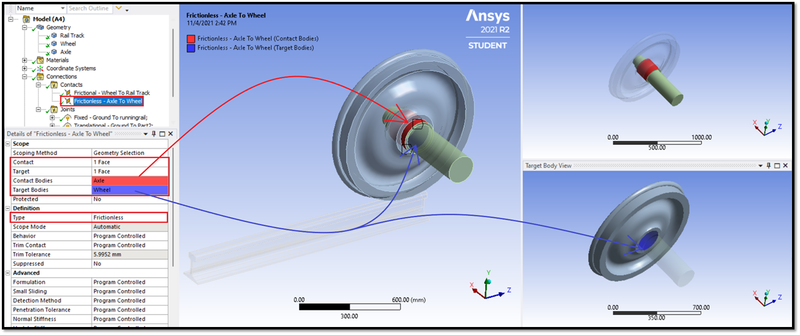
Figure 18-Contact Defined Between Wheel and Axle. |
3:3 Define Joints :
- After defining the contact, We have to deploy joints for the Rail Wheel and Track.
- To create a joints,Right Click on the Connections >> Insert >> Joint.Which is shown in below Figure 19.
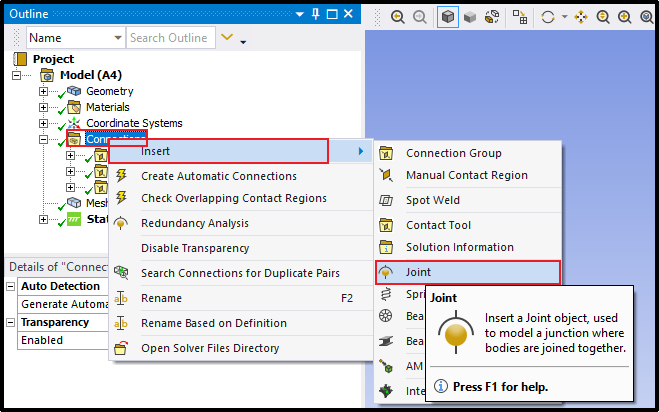
1) Fixed Joint :
- We have to constrain the rail track in all the degree of freedoms by using Fixed Joint.
- We have to fix the rail track to the ground,Which is shown in below Figure 20.
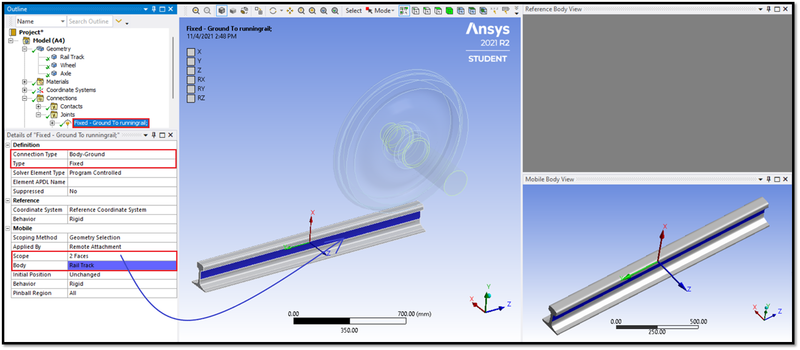
Figure 20-Defined Fixed Joint. |
2) Translational Joint :
- Select the Axle Face,We have to constrain the all degrees of freedome except translation on X direction.Which is shown in below Figure 21.
- Then only the axle can be able to change the position on the x direction either Positive or Negative according to the input.
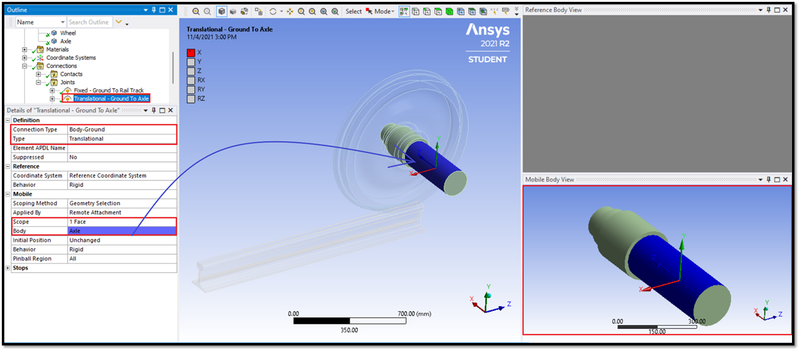
Figure 21-Defined Translational Joint. |
3) Planar Joint :
- In this joint,Select the face of the Wheel,Which is shown in below Figure 22.
- Here we have to constrain the X and Y axis direction,Cause the wheel will be rotating in X and Y axis.
- And we have to constain in the Z axis direction,Cause the wheel will be translating in Z axis.
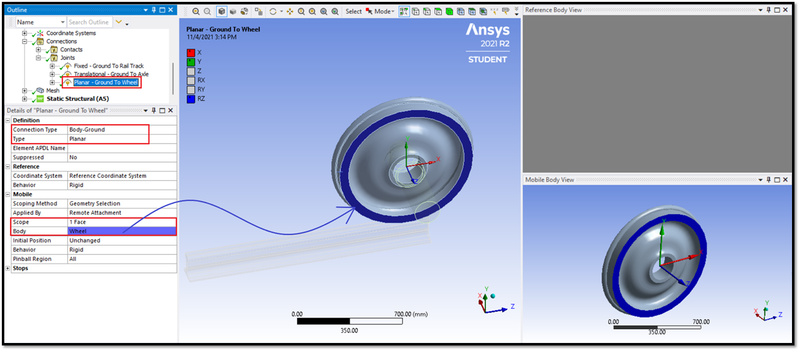
Figure 22-Planar Joint Defined. |
3:4 Meshing :
- After defining the joint in the connections panel,We have to define mesh for the Rail Wheel Track.
- To define Mesh,Click on the Mesh >> Give Mesh Size as 35 mm.Which is shown in below Figure 23.
- Here we are refining the mesh for the Wheel and Rail Track,Cause we have to see the stress developed at the Contact between Wheel and Rail Track faces,So we are refining the mesh for the Wheel and Rail Track Faces.
- To refine a mesh,Click on the Mesh >> Insert >> Sizing >> Select the Faces of Tooth >> Mesh Size as also 35 mm.Which is shown in below Figures 24 and 25.
- Element Size = 35 mm
- Face Mesh Element Size = 35 mm
- Meshing Method = Tetrahedrons
- No of Nodes = 12567
- No of Elements = 6280
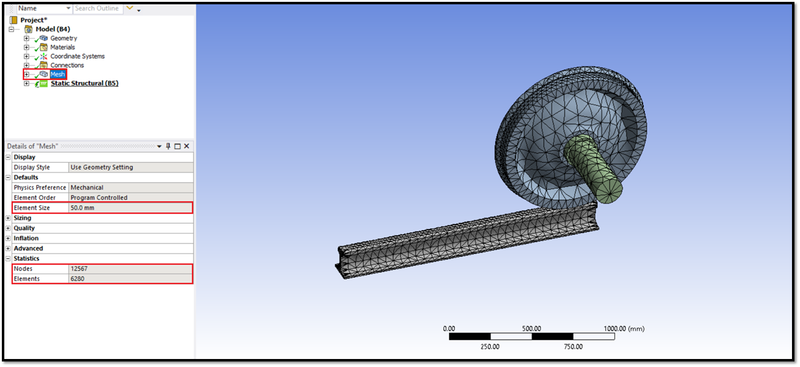
Figure 23-Meshed Rail Wheel and Track with 50 mm Element Size. |
- Now Refine the mesh in the Rail Track and Wheel Faces,Where it Comes to a Contact.
- The refined mesh is shown in below Figure 25.
- To Refine Mesh >> Right Click on Mesh >> Insert >> Sizing >> Face Sizing >> Select Faces of Rail Track and Wheel,Which is shown in below Figure 24.
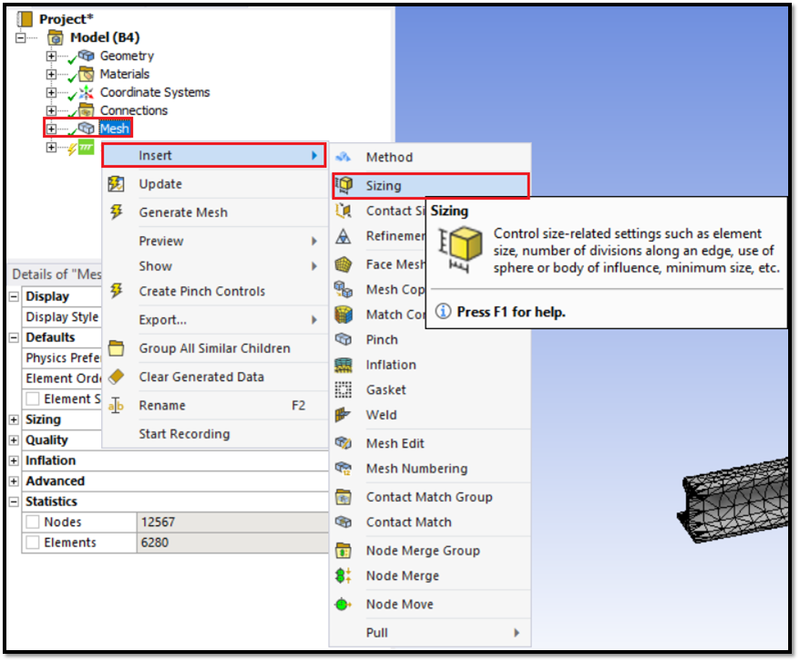
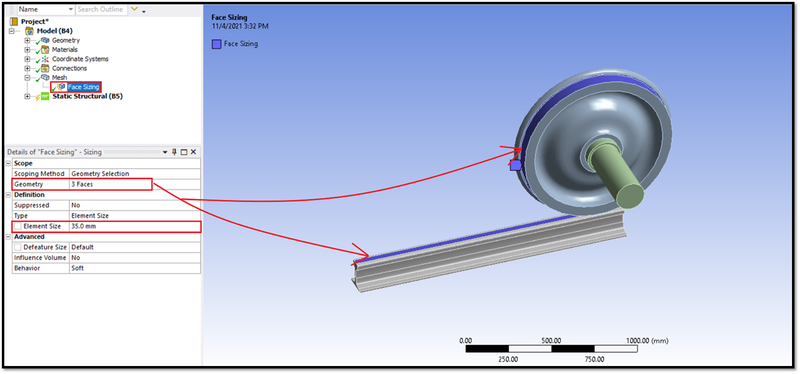
Figure 25-Faces Selected to Refine the Mesh. |
3:5 Analysis Settings :
- Here we are running simulation for the five steps.
Step 1 :
- Auto Time Stepping-Program Controlled.
- Solver Type-Direct.
- Large Deflection-ON.
- Output Controls-Switch to Yes for all parameters in the Output Controls.
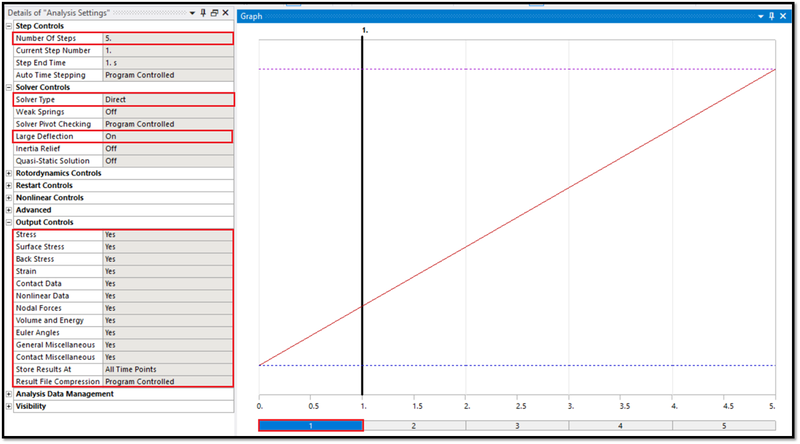
Figure 26-Analaysis Settings for Step 1. |
Step 2 to 5 :
- Auto Time Stepping -ON
- Define By-Time
- Carry Over Time Step-On
- Minimum Time Step-5e-002 sec
- Maximum Time Step is -1 sec
- Solver Type -Direct
- Large Deflection-ON
- Keep other parameters as it is default.
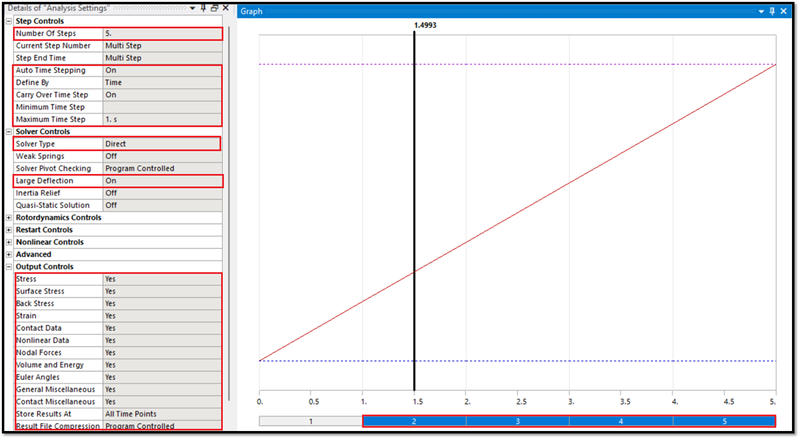
Figure 27-Analaysis Settings for Step 2-5. |
3:6 Boundary Conditions :
- After giving some parameters in the analysis settings,We have to give boundary conditions.
- Create a two Joints Loads,One for Bearing and Other for Displacement, Which is shown in below Figures 28.
- To create Joint Loads, Right Click on the Static Structural >> Insert >> Joint Load.
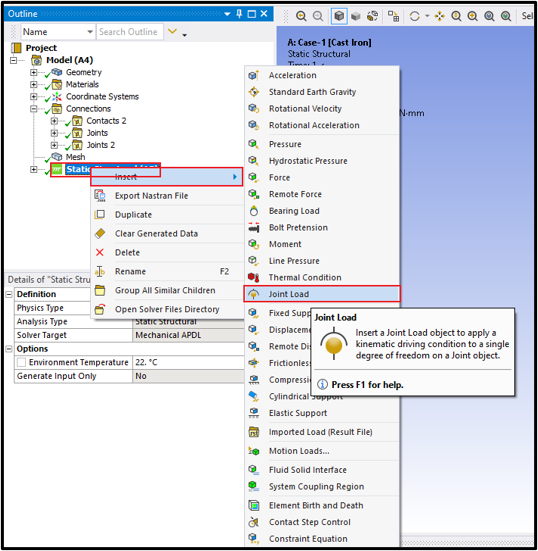
Figure 28-Create Joint Loads. |
1) Bearing Load :
- Here the wheel is in contact with the axle,So here we have applied an 100 and 500 KN as a bearing Load at downwards direction on the inner face of the wheel.
- A same bearing load has been applied on the wheel for all the steps.
- Here we have to give the bearing load in negative values,Cause the load what we are going to apply should be in negative Y direction
- The applied bearing load is shown in below Figure 29.
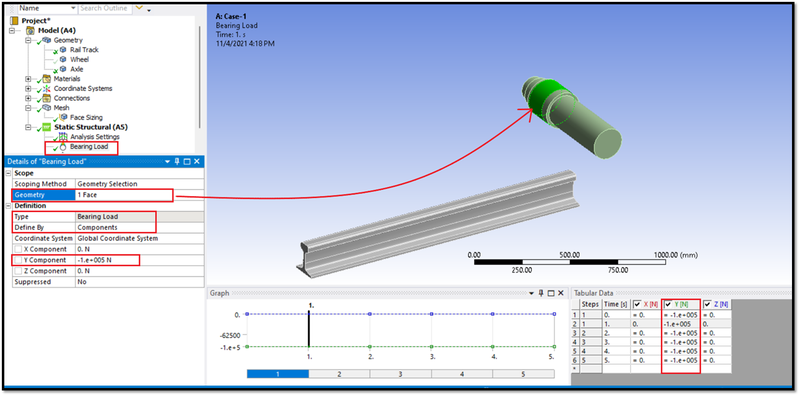
Figure 29-Bearing Load Applied. |
2) Displacement Joint :
- Give the displacement on the X Direction from 0 mm to 500 mm with the interval of 100 mm.
- Here,the wheel is moving in positive X Direction,So we are giving the values for distance in positive numbers,Which is shown in below Figure 30.
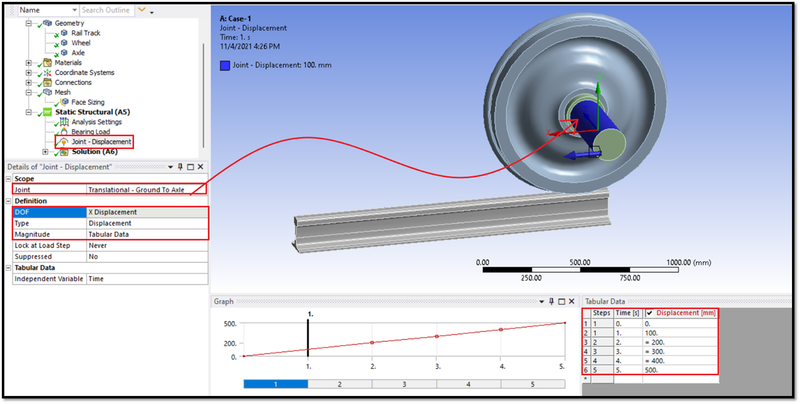
Figure 30-Defined Displacement Joint. |
Phase 4-Request for the Outputs :
- Here we have to request outputs for the VonMisses Stress, Strain, and for Total Deformation.
- To request Output for Stress,Right Click on the Solution >> Insert >> Stress >> Equivalent Von Misses Stress.
- To request Output for Strain,Right Click on the Solution >> Insert >> Strain >> Equivalent Von Misses Strain.
- To request Output for Total Deformation,Right Click on the Solution >> Insert >> Deformation >> Total Deformation.
- This is shown in below Figure 31.
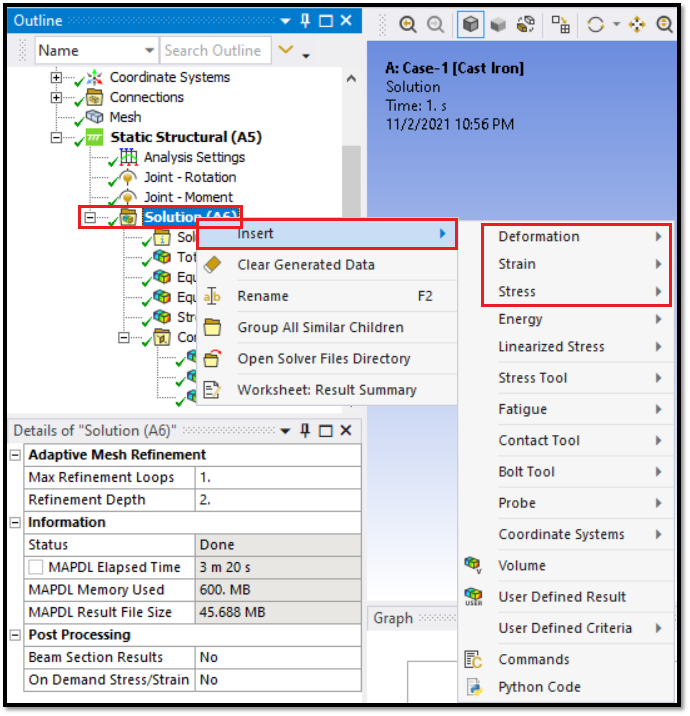
Figure 31-Requesting Outputs for the Stress, Strain, and Deformation. |
- Next request output for the contact.
- To request Contact Tool >> Right Click on the Solution >> Insert >> Contact Tool >> Pressure >> Status,Which is shown in below Figures 32 and 33.
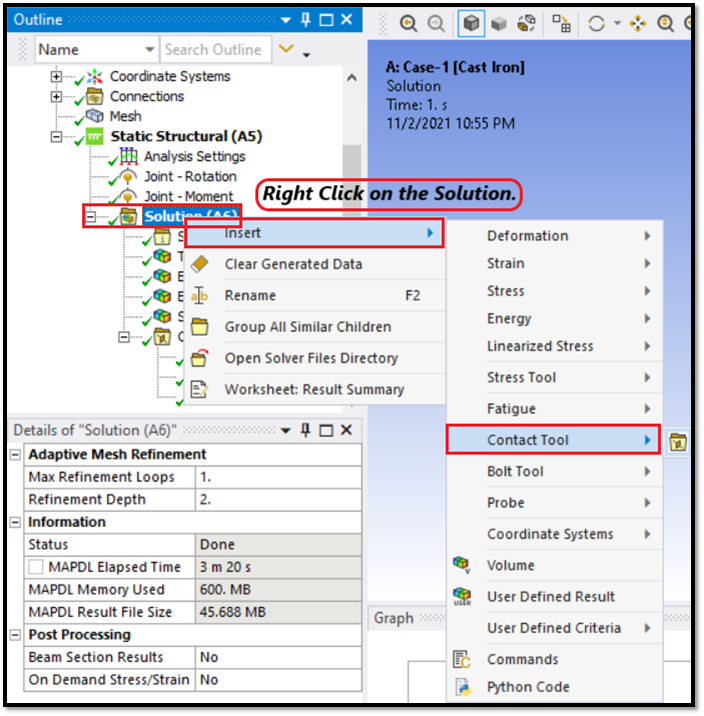
Figure 32-Requesting Output for Contact. |
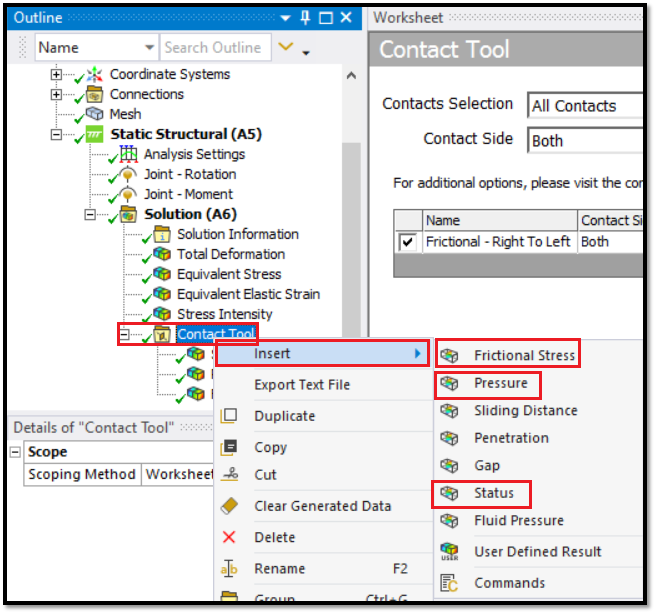
Figure 33-Requesting Outputs for Contact Tool. |
- Simillarly request the outputs for the Stress Tool and Fatigue Tool.
- The Output requested for the Rail Wheel and Track is shown in below Figure 34.
- After requesting all the outputs which is shown in below Figure 34. Run the Simulation.
Figure 34-Required Outputs Requested. |
- The user defined output is requested,Which is shown in below Figure 35.
- To request User Defined Result >> Right Click on Solution >> Insert >> User Defined Result.
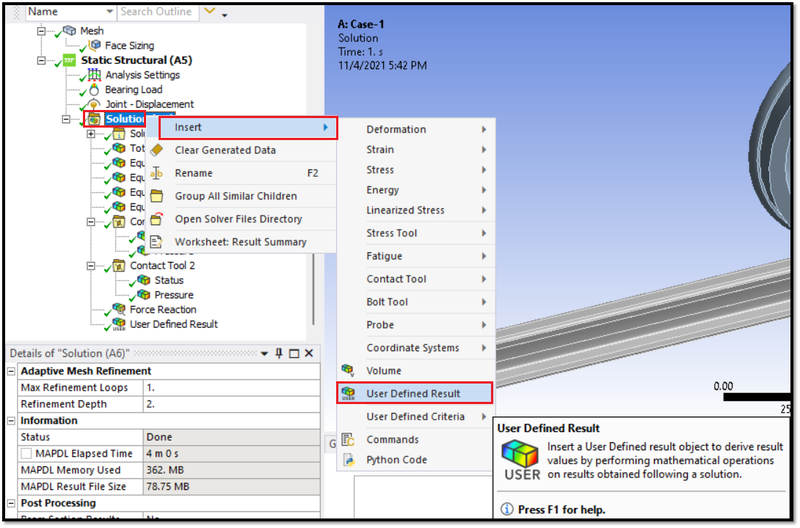
Figure 35-Request User Defined Result. |
- We have to also request a user-defined output result for total deformation in the analysis.
- To Request,Right Click on the Solution > Insert > User Defined Result.
- In the parameter box,We need to define it by giving giving a Total Deformation Expression.Which is shown in below Figure 36.
- U=√Ux2+Uy2+Uz2
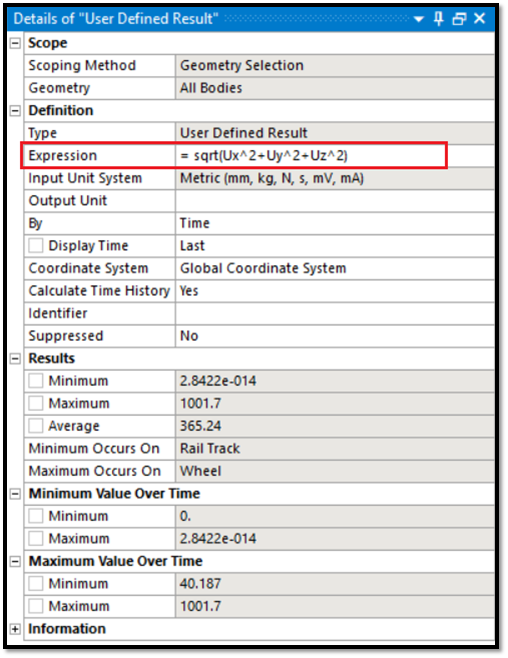
Figure 36-User Defined Result Parameter Window. |
Phase 5-Run the Simulation for all the three Cases :
- To run the simulation, Right Click on the Solution >> Solve. This is shown in below Figure 37.
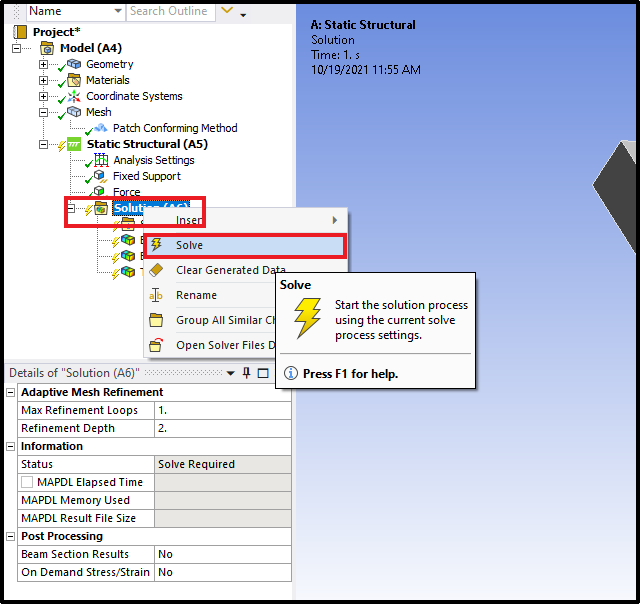
Figure 37-Solve all the Outputs Requested. |
- After solving the outputs requested, the simulation results forthe two cases is shown in the below Figures.
Equivalent Von Misses Stress [Case 1-With 100 KN=100000 N] :
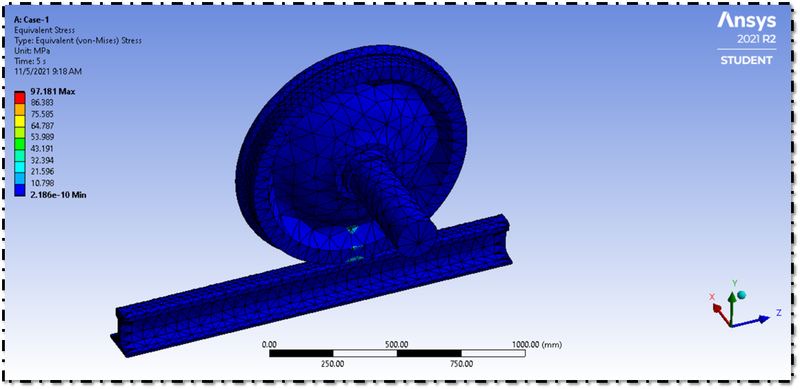
Figure 38-Equivalent Von Misses Stress Case 1 [100000 N]. |
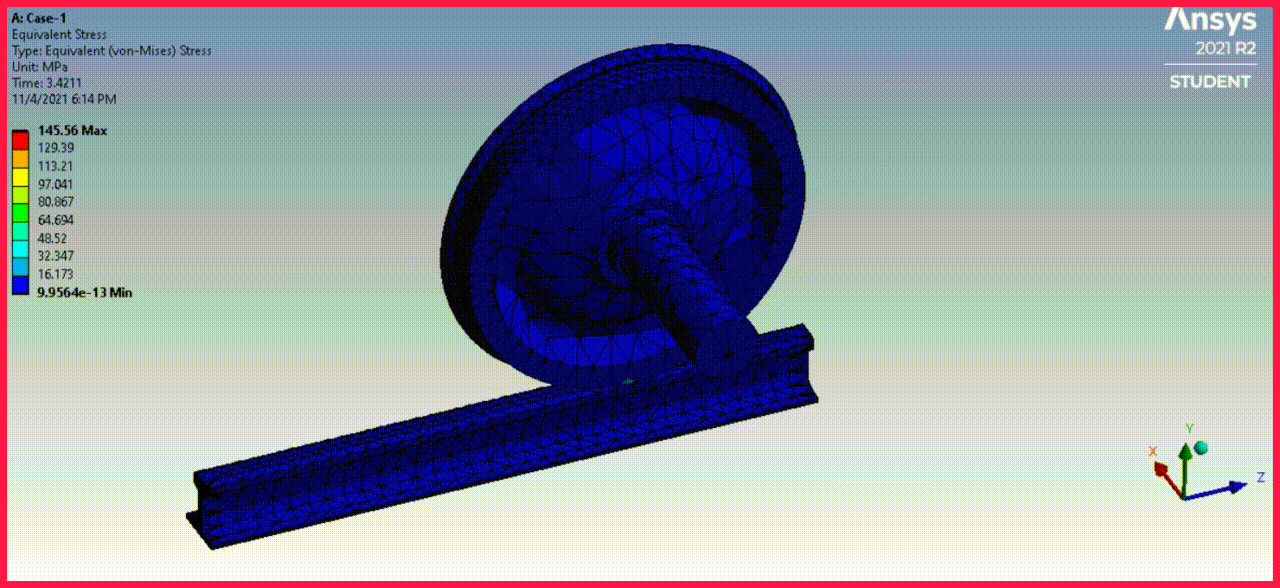
Figure 39-Equivalent Von Misses Stress Simulation Animation Case 1 [100000 N]. |
Equivalent Von Misses Stress [Case 2-500 KN=500000 N] :
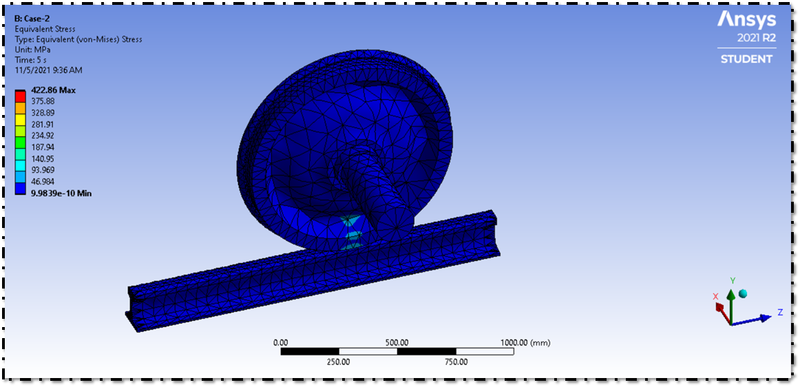
Figure 40-Equivalent Von Misses Stress Case 2 [500000 N]. |
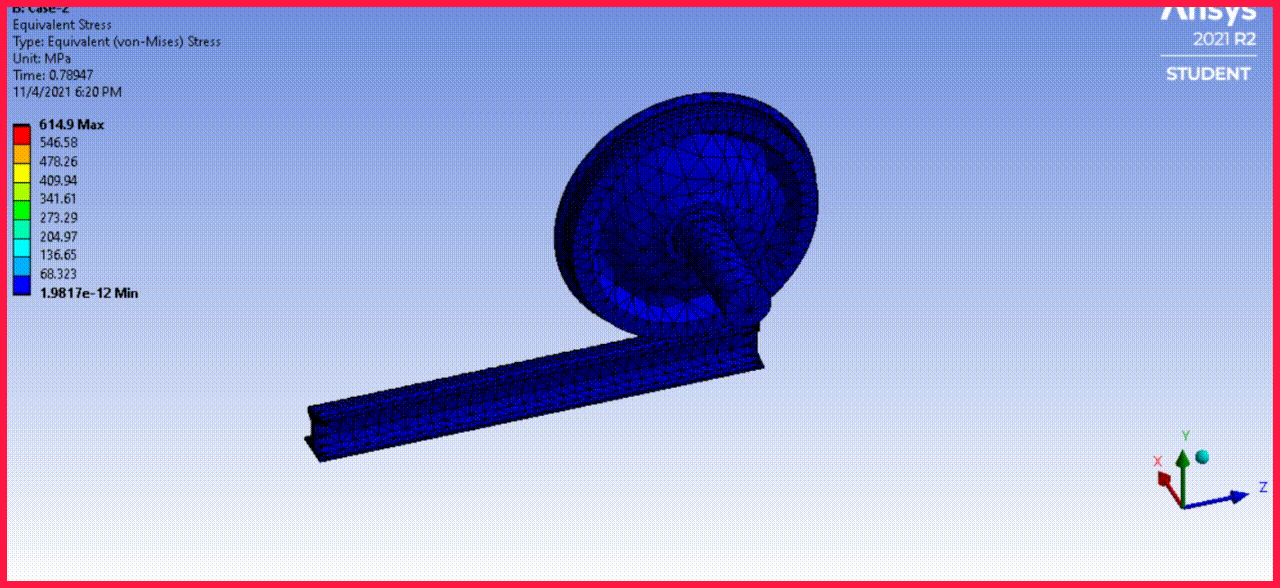
Figure 41-Equivalent Von Misses Stress Simulation Animation Case 2 [500000 N]. |
Equivalent Elastic Strain [Case 1-With 100 KN=100000 N] :
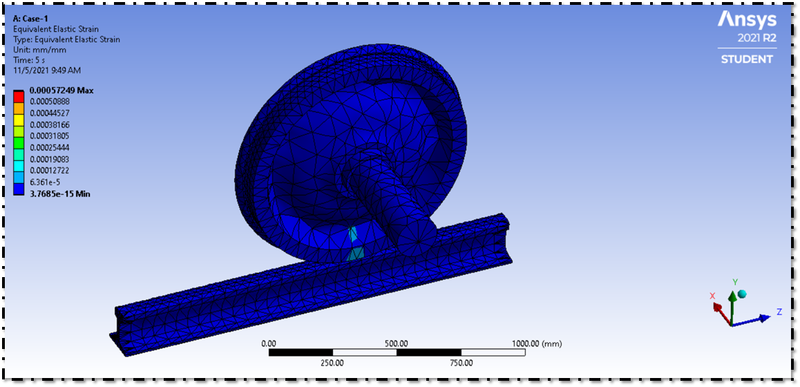
Figure 42-Equivalent Elastic Strain Case 1 [100000 N]. |
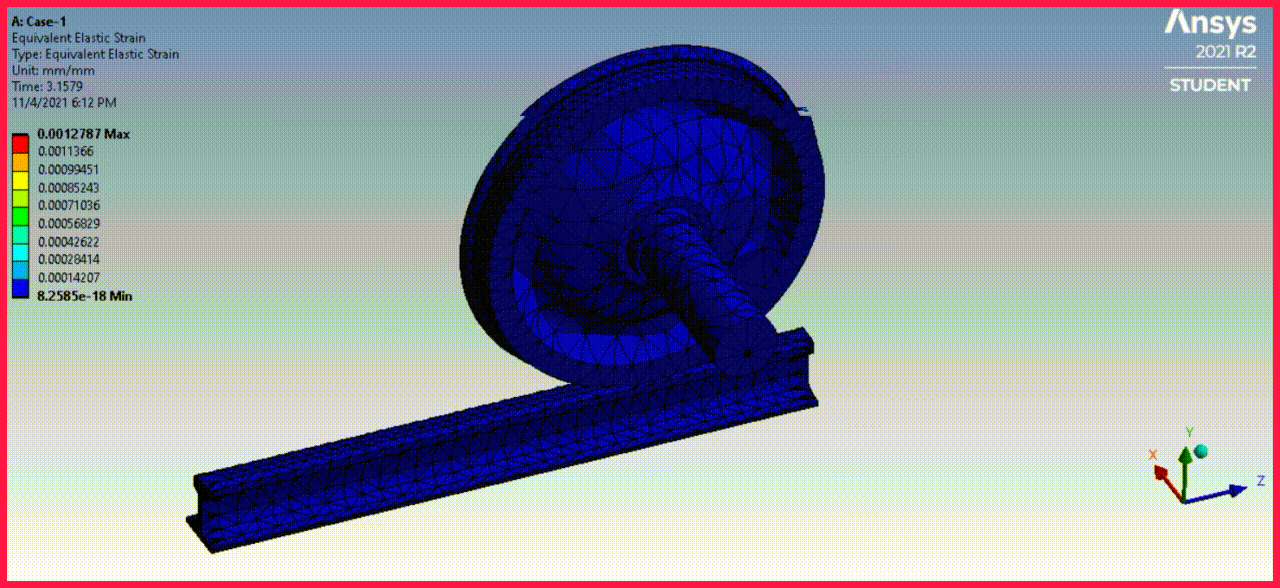
Figure 43-Equivalent Elastic Strain Simulation Animation Case 1 [100000 N]. |
Equivalent Elastic Strain [Case 2-With 500 KN=500000 N] :
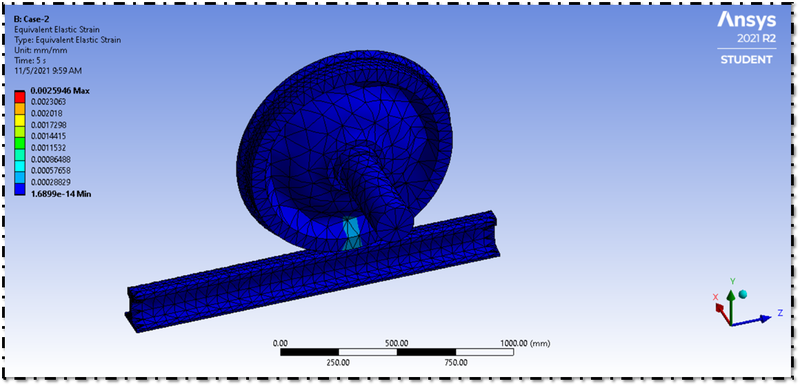
Figure 44-Equivalent Elastic Strain Case 2 [500000 N]. |
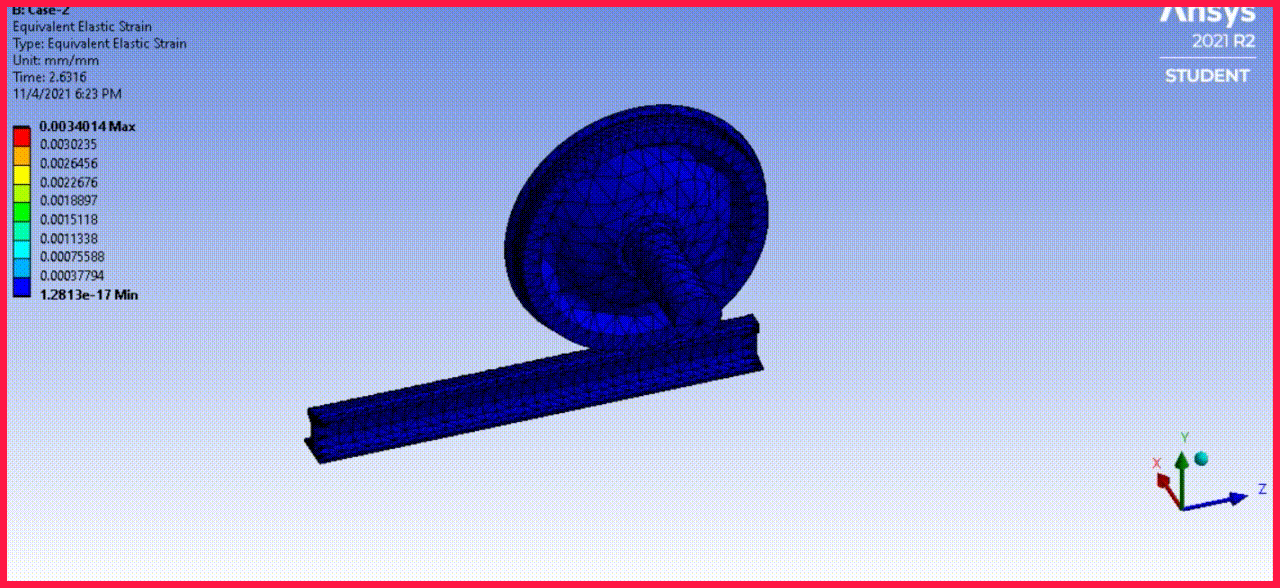
Figure 45-Equivalent Elastic Strain Simulation Animation Case 2 [500000 N]. |
Total Deformation [Case 1-With 100 KN=100000 N] :
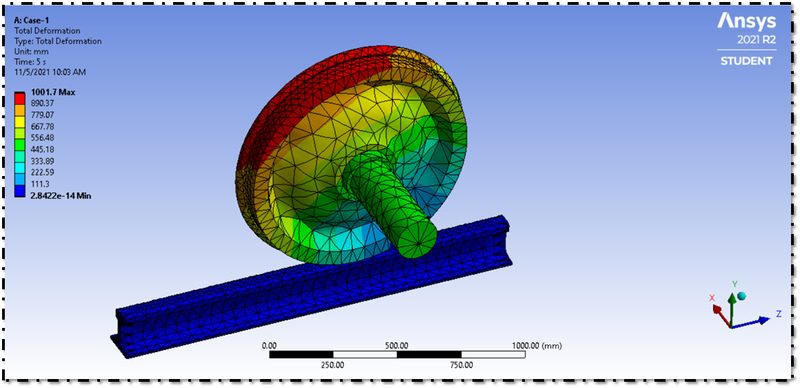
Figure 46-Total Deformation Case 1 [100000 N]. |
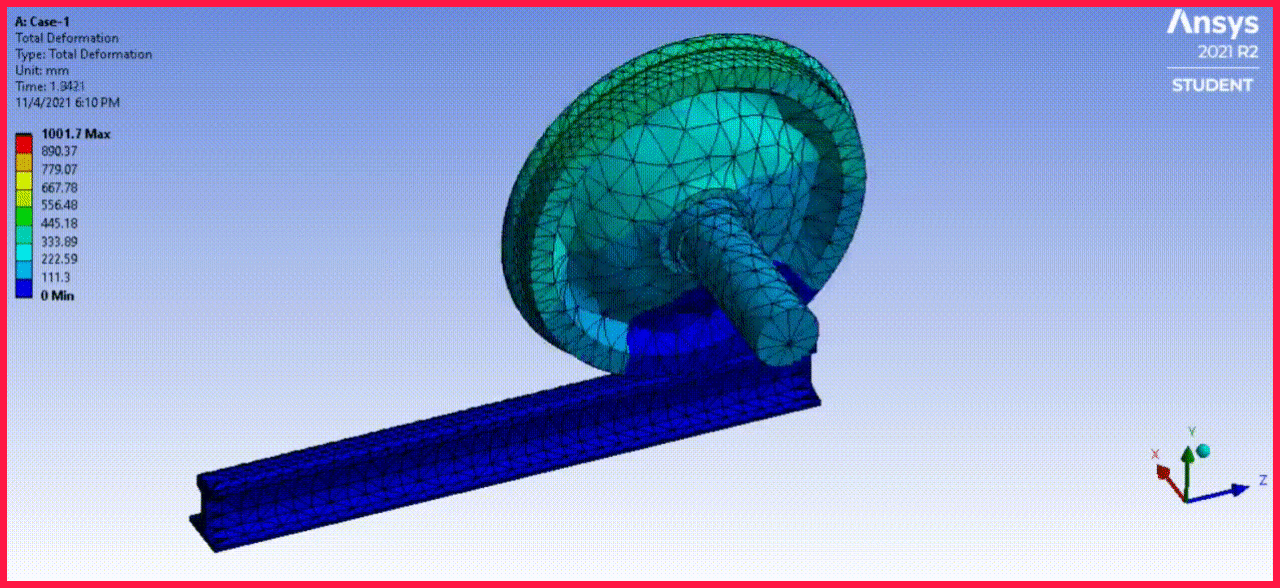
Figure 47-Total Deformation Simulation Animation Case 1 [100000 N]. |
Total Deformation [Case 2-With 500 KN=500000 N] :
Figure 48-Total Deformation Case 2 [500000 N]. |
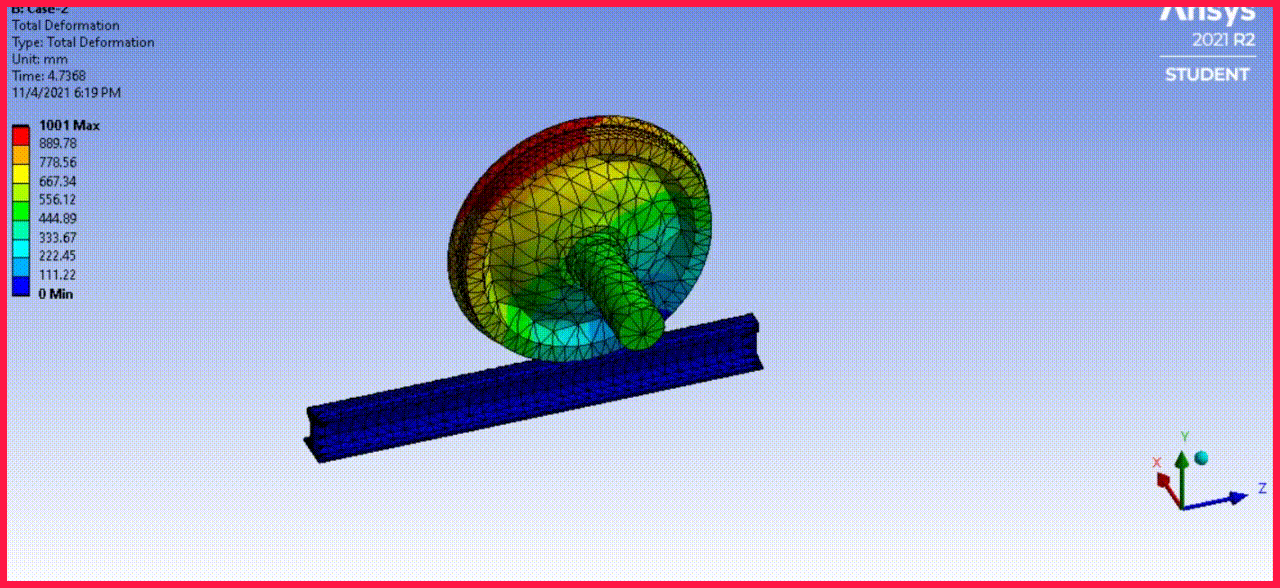
Figure 49-Total Deformation Simulation Animation Case 2 [500000 N]. |
Fatigue Life Case 1-With 100 KN=100000 N :
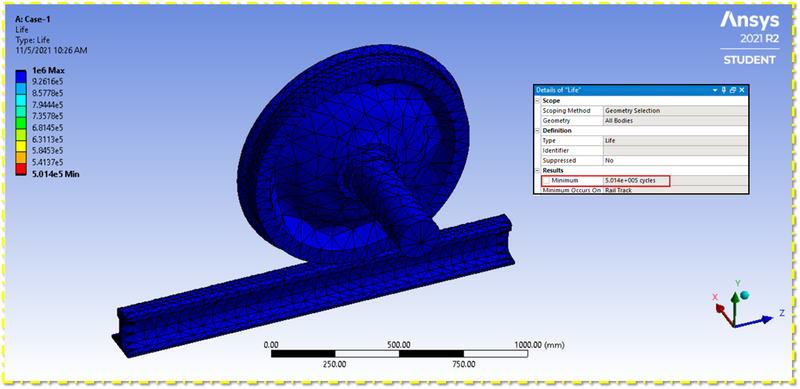
Figure 50-Fatigue Life Case 1 [100000 N]. |
Fatigue Life Case 2-With 500 KN=500000 N :
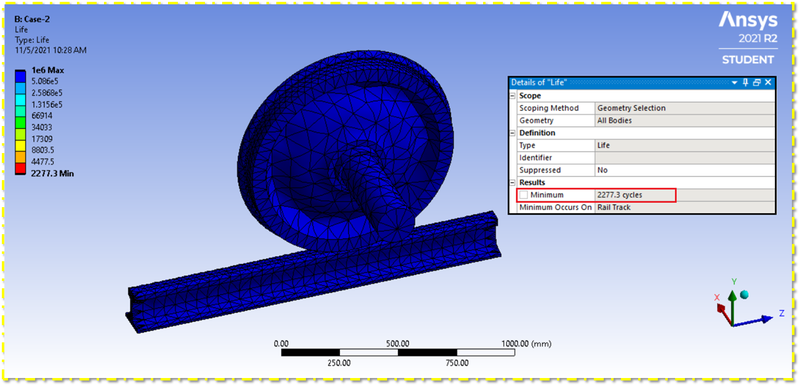
Figure 51-Fatigue Life Case 2 [500000 N]. |
User Defined Result Case 1 [100000 N] :
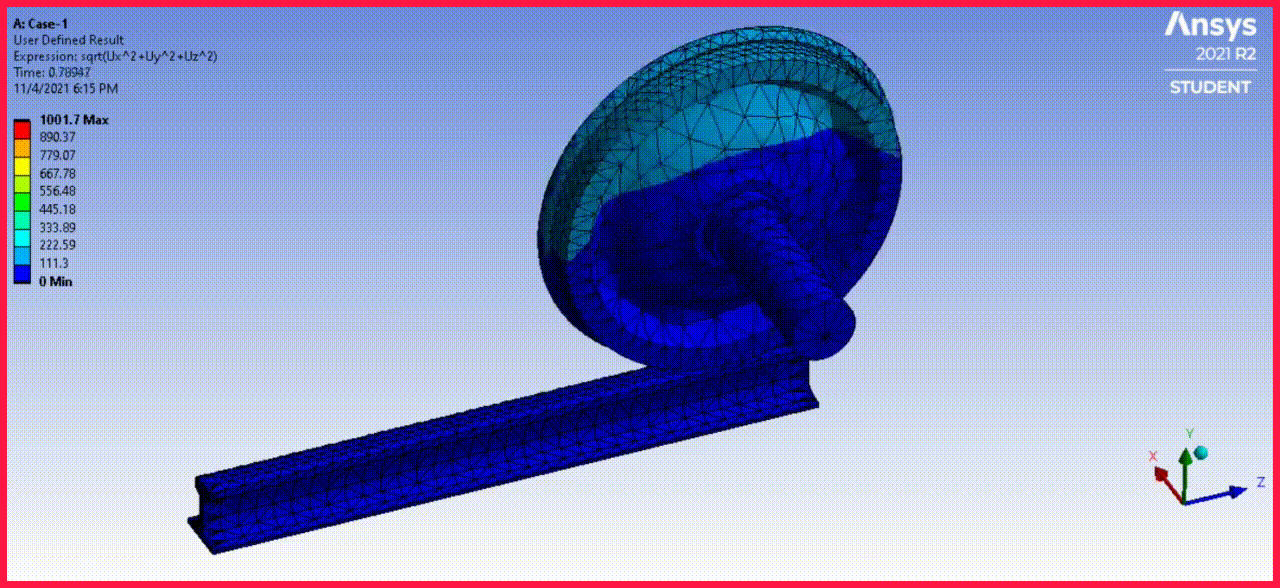
Figure 53-User Defined Result Case 1 [100000 N]. |
User Defined Result Case 2 [500000 N] :
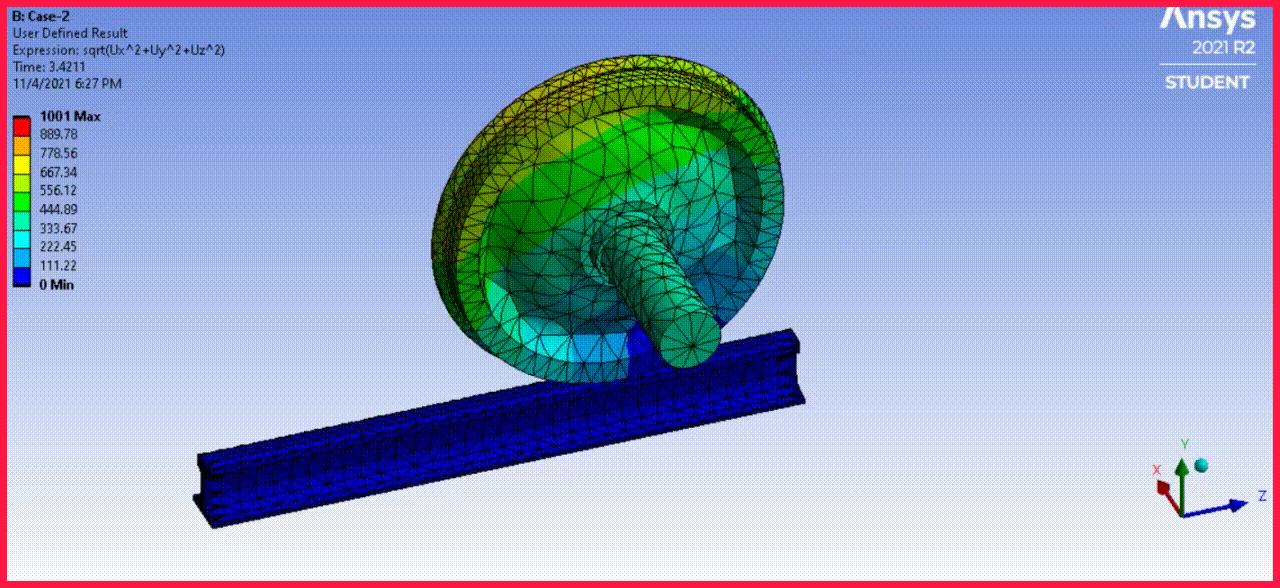
Figure 54-User Defined Result Case 2 [500000 N]. |
Comparison of Results :
Cases
|
Von-Misses Stress (MPa)
|
Total Deformation (mm)
|
Equivalent Elastic Strain (mm/mm)
|
User Defined Result
|
Fatigue Life
|
Max.
|
Min.
|
Max.
|
Min.
|
Max.
|
Min.
|
Max.
|
Min. |
Max. |
Min. |
Case-1 [100000 N]
|
97.181MPa
|
2.186e-10MPa
|
1001.7 mm
|
2.8422e-14 mm
|
5.7249e-004 mm/mm
|
3.7685e-015 mm/mm
|
1001.7
|
2.8422e-014 |
1e6 |
5.014e+005 cycles |
Case-2 [500000 N]
|
422.86MPa
|
9.9839e-10MPa
|
1001.7 mm
|
2.8422e-14 mm
|
2.5946e-003 mm/mm
|
1.6899e-014 mm/mm
|
1001
|
2.8422e-014 |
1e6 |
2277.3 cycles |
- Here we have applied two different bearing loads on the axle face.
- In the first case we have applied 100 KN to the axle face and in the second case we have applied 500 KN to the axle face.
- The maximum von misses stress occured in the first case with the bearing load of 100 KN is 97.181 Mpa.The maximum stress value over time is 145.56 MPa.
- The maximum von misses stress occured in the second case with the bearing load of 500 KN is 422.86 Mpa.The maximum stress value over time is 614.9 MPa
- Here when we compare two cases,the maximum stress value with bearing load of 100 KN is less than the yield stress value of the material,So the rail and wheel track can sustain the load.
- But the maximum stress value with the bearing load of 500 KN is beyond the ultimate stress value of the material,So the Rail and Wheel Track cannot sustain the load,If we appy bearing load as 500 KN.
- The minimum fatigue life of Rail and Wheel Track with bearing load of 100 KN is 5.014e+005 cycles,So Rail and Wheel Track will be having almost infinite life.
- When you take the,The minimum fatigue life of Rail and Wheel Track with bearing load of 500 KN is 2277.3 cycles ,So Rail and Wheel Track will be having finite life.It will leads to failure of the component within short span of the time period.
- Here the Total Deformation Result and User Defined Result is almost similar,So it is fine.If we didn't get the result as same,Then the boundary conditions what we have given will be wrong.
- So here,I will be concluding that Case -1 with bearing load of 100 KN is preferrabel,Cause it will last for long,So it's better to go with Case -1 with bearing load of 100 KN.
[Note: We can't say this case is preferable, this case is not preferable, Anyhow it depends on the application. Here in the report, I have said, Case-1 with bearing load of 100 KN is preferable,Cause it will last long and Case-2 is not preferable,Cause it will leads to failure and it won't last long,Here,I have told the Case-1 is preferrable and other case-2 not preferrable according to the question and the model given to us, But in real life, It entirely depends on the applications.]
Factor of Saftey :
Case-1 [With Bearing Load of 100 KN] :
- The factor of Saftey = Yield Strength/Working Stress
- Tesnsile Yield Strength of Structural Steel=250 Mpa
- Working Stress [Maximum Stress]=97.181 Mpa
- FOS=25097.181
- FOS=2.57
- Here the FOS what we got is 2.57,It is entirley ok,The material will not fail,It is Safe. mm mesh size.The Standard FOS ranges from 1-5 in industries.
Case-2 [With Bearing Load of 500 KN] :
- The factor of Saftey = Yield Strength/Working Stress
- Tesnsile Yield Strength of Structural Steel=250 Mpa
- Working Stress [Maximum Stress]=422.86 Mpa
- FOS=250422.86
- FOS=0.59
- Here the FOS what we got is 0.59,The FOS is less than 1.It is not ok,The material will fail,It is not Safe.If we apply bearing load of 500 KN ,The material will fail.The Standard FOS ranges from 1-5 in industries.
Result :
- Hence the material Structural Steel has been defined for all the two cases.
- Hence the connections were defined to the Rail Wheel and Track.
- Hence the model has been solved for Von-Misses Stress, Equivalent Elastic Strain,Stress Intensity,Contact Tool and Total Deformation by applying appropriate boundary conditions.
- Hence the Bearing Load of 100 KN and 500 KN is applied to the Axle Face.
- Hence the Case-1 with Bearing Load of 100 KN is preferred,Cause it lasts long.
Conclusion and Learning Outcome :
In this Week 2 Rail Wheel and Track Challenge, I came to know about
- Learned how to give Bearing Load to the model.
- Learned how to assign materials to the model.
- Learned how to apply boundary conditions to the model.
- Learned how to request outputs and solve them.
- Learned about the Force Convergence.