Stress Concentration on a Plate with Hole
Aim -
- To perform static analysis on the two models of a rectangular plate with a single hole and multi-holes.
Objective -
- To design a rectangular plate with single and multi holes in space claim for the following cases
- Case 1: Length=300mm, height=120mm, thickness=30mm, the circular hole at the center with diameter=60mm.
- Case 2: Use the same dimensions used for case 1, but add the additional two holes with a diameter of 30mm away from the center.
- To determine and compare the maximum deformation and stress developed on a structural steel model for the two cases.
- To select the design from an analysis point of view.
- To select the design from a manufacturing point of view.
Theoretical FrameWork -
Stress concentration :
- Whenever a machine component changes the shape of its cross-section, the simple stress distribution no longer holds good and the neighborhood of the discontinuity is different.
- It occurs for all kinds of stresses in the presence of fillets, notches, holes, keyways, splines, surface roughness or scratches, etc.
- Stress concentration is defined as the localization of high stresses due to the irregularities present in the component and abrupt changes of the cross-section. In order to consider the effect of stress concentration and find out localized stresses, a factor called the stress concentration factor is used. It is denoted by Kt and defined as,
- Kt=σmaxσo=TmaxTo
- Where σo and τo are stresses determined by elementary equations and σmax and τmax are localized stresses at the discontinuities.
- The subscript ‘t’ denotes the ‘theoretical’ stress concentration factor. The magnitude of the stress concentration factor depends upon the geometry of the component.
- The causes of stress concentration are
- Variation in Properties of Materials
- Load Application
- Abrupt Changes in Section
- Discontinuities in the Component
- Machining Scratches
Methods to reduce stress concentration :
- Although it is not possible to completely eliminate the effect of stress concentration, there are methods to reduce stress concentrations. This is achieved by providing a specific geometric shape to the component.
- There are different methods to reduce the bending of the stress lines at the junction and reduce the stress concentration. In practice, reduction of stress concentration is achieved by the following methods:
- Additional Notches and Holes in Tension Member
- Providing Fillet Radius, Undercutting, and Notch for Member in Bending
- Drilling Additional Holes for Shaft
- Reducing shank diameter in Threaded Members
Procedure -
Phase 1-Design the Rectangular Plate With a Single Hole at Centre in Space Claim :
- To design a rectangular plate with a single hole, Open the ANSYS Workbench.
- In the Ansys Workbench, Go to the Tool Box, In the toolbox, there will be a lot of analysis systems.
- In the Analysis system, Drag and Drop the Static Structural Analysis System into the Project Schematic Workspace which is shown in below Figure 1.

Figure 1-Ansys Workbench Workspace. |
- After deploying the static structural analysis system in the project schematic workspace.
- Define the Engineering Data and geometry, To define the Geometry and Engineering Data, Right Click on the Engineering Data and click to edit, it will take to the Engineering Tab.
- There Right Click on the Material Tab, A window will Pop-Up stating Engineering data sources.
- Click on the Engineering Data Sources, There go and select the material to define the engineering data. This is shown in below Figures 2,3,4.
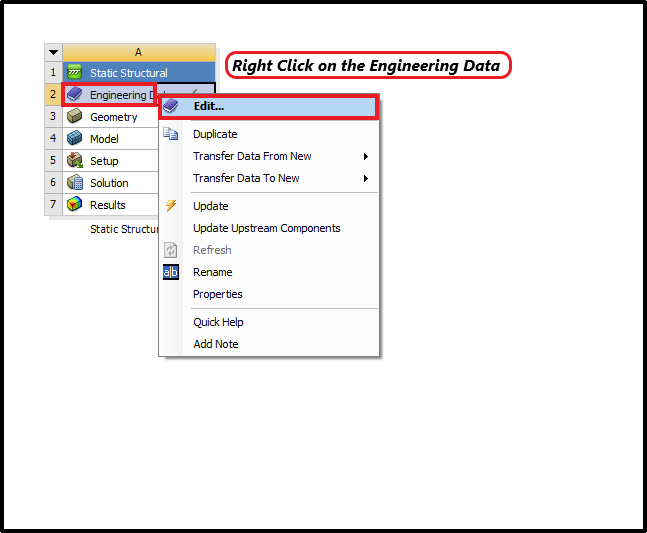
Figure 2-Right Click on the Engineering Data. |
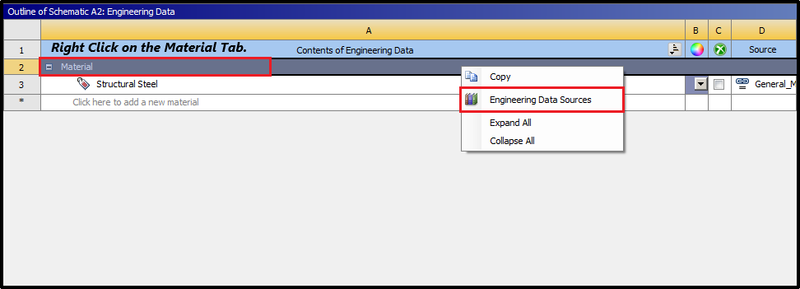
Figure 3-Right Click on the Material Tab. |
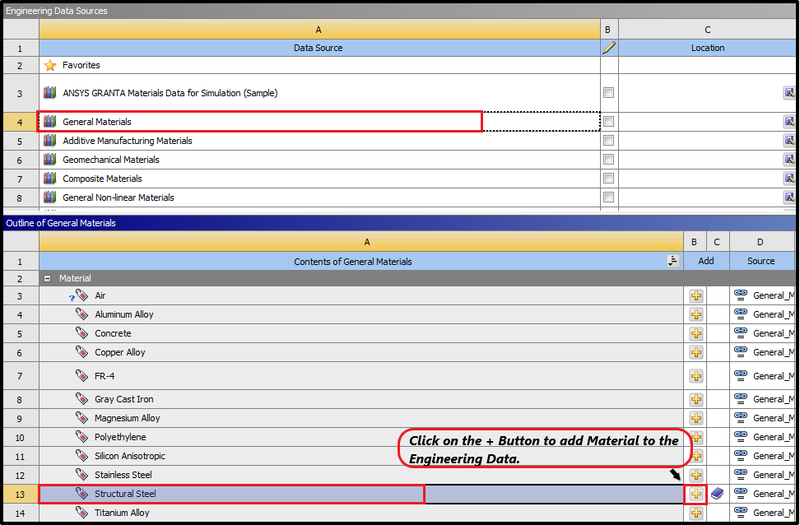
Figure 4-Select the Material as Structural Steel to Define the Engineering Data. |
- Similarly, define the Geometry, Right Click on the Geometry >> New SpaceClaim Geometry. Which is shown in below Figure 5.
- SpaceClaim will open, Design the Rectangular Plate with a Single Hole at the Centre.
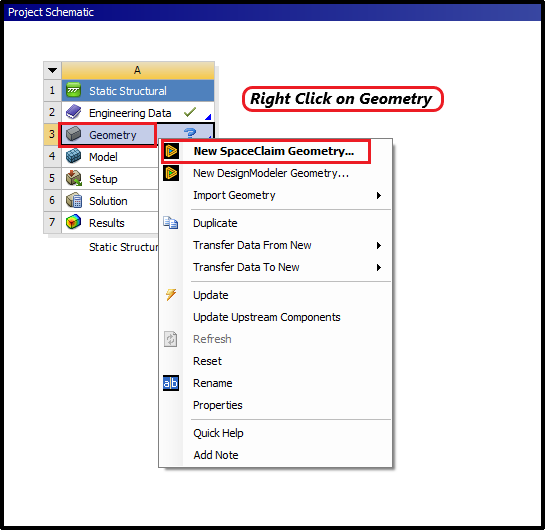
Figure 5-Define the Geometry. |
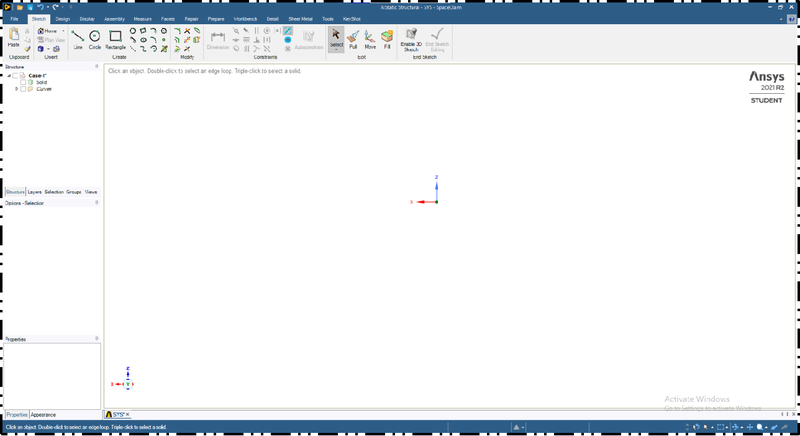
Figure 6-SpaceClaim Workspace. |
- Now sketch the rectangular plate with a single hole for case 1 and rectangular plate with multi holes for case 2, Which is shown in below Figures 7 and 8.
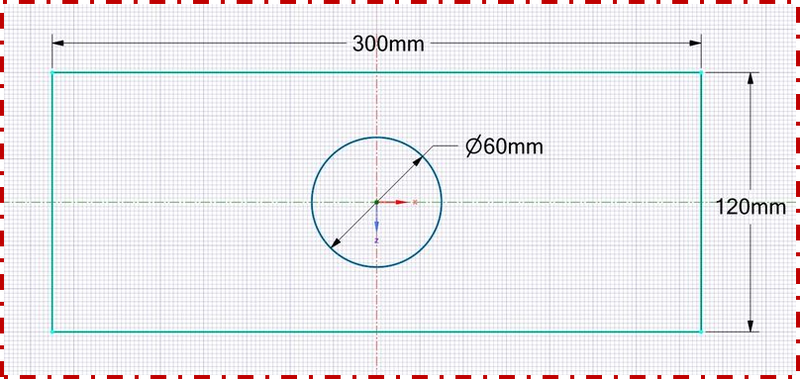
Figure 7-Sketch for Case-1. |
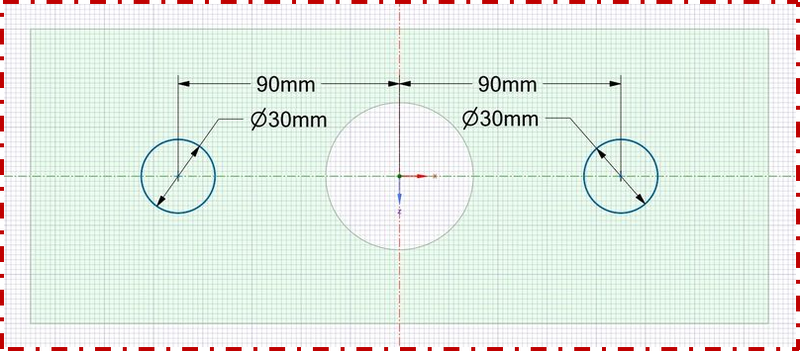
Figure 8-Sketch for Case 2. |
- Now apply the thickness for the sketches. To apply sketch, Go to the Design Menu >> Edit >> Pull >> Give the Value to Extrude.
- The 2D sketch of the plate with a hole having length=300mm, height=120mm, and a circular hole at the center with diameter=60mm is created using tools under sketch option in SpaceClaim. Similarly, for case 2, with the same dimensions as case 1, additional 2 smaller holes are created, having a diameter=30mm away from the center with a distance of 90mm.
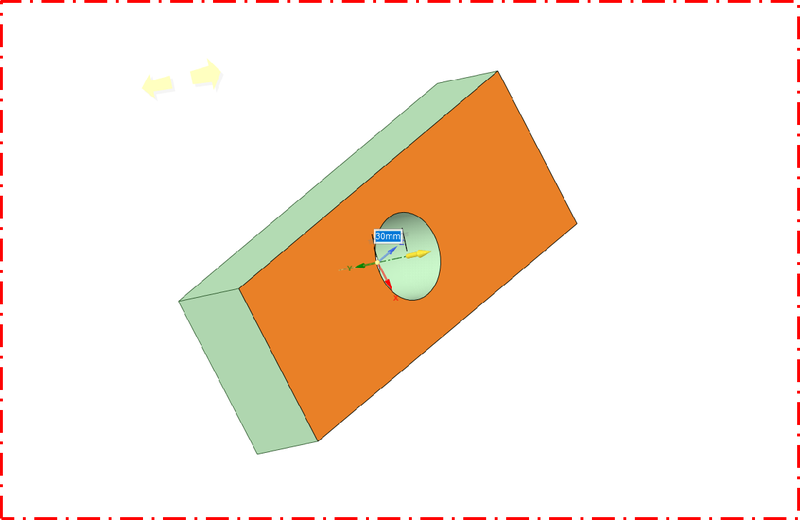
Figure 9-Giving the Value to Extrude for 30 mm. |
- Similarly, do the same thing for Case-2 also.
- The Geometry of Case 1 and Case 2 is shown in below Figures 10 and 11.
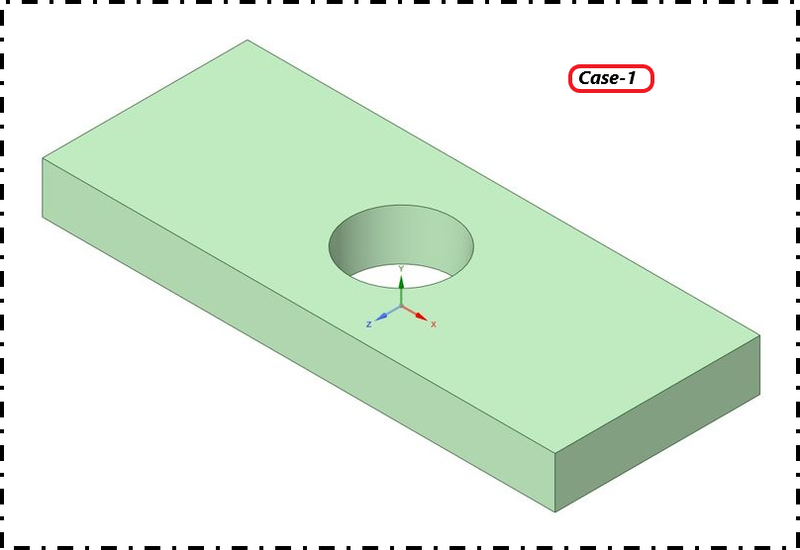
Figure 10-Case 1 Geometry. |

Figure 11-Case 2 Geometry. |
Phase 2- Mesh the Model :
- Now double click on the model or right-click and hot on edit, It will take you to the Mechanical Workspace, Where you have to mesh the model and give the boundary conditions. This is shown in below Figure 12.
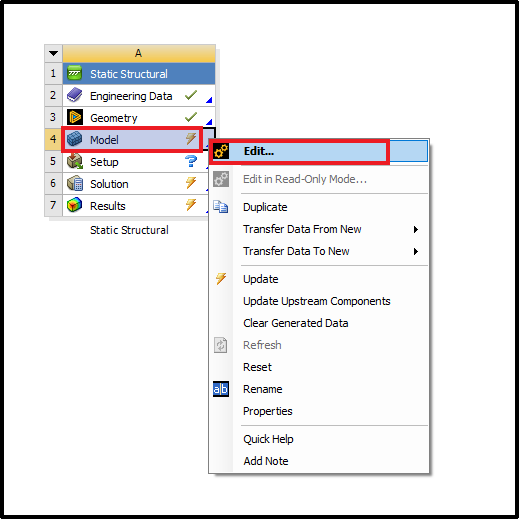
Figure 12-Double Click on the Model to get Mechanical Workspace. |
- Here the mesh will be automatically generated to the model.
- We have to give element size and mesh method to the model.
- To give element size, Click on the Mesh option, The model will appear in the GUI.
- The parameter panel will appear down, There go and change the element size which is shown in below Figure 13.
- To give the mesh method, Right Click on the Mesh >> Insert >> Method >> Parameter Window will Appear Down, There go and change the method to tetrahedrons which is shown in below Figure 14.
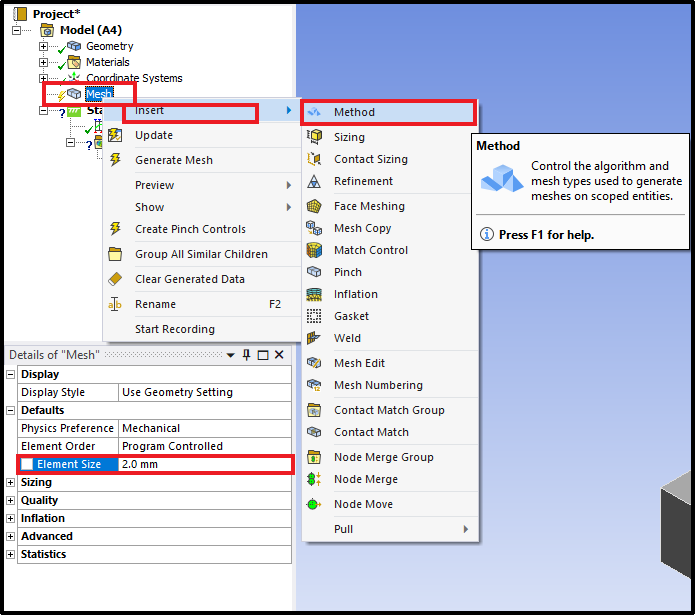
Figure 13-Give the Element Size. |
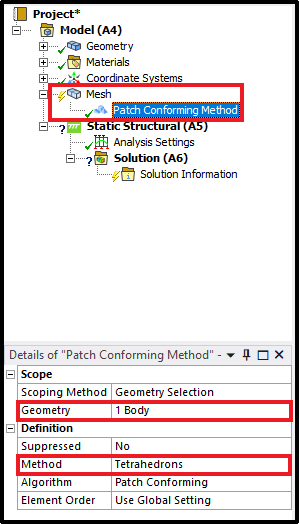
Figure 14-Give Mesh Method as Tetrahedrons. |
- After doing some changes, Right Click on the Mesh and Update or give Generate Mesh which is shown in below Figure 15.
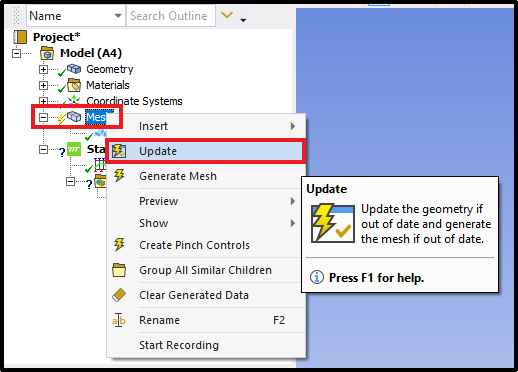
Figure 15-Update the Mesh or Generate Mesh. |
- Meshed Model of Case 1 and Case 2 is shown in below Figures 16 and 17.
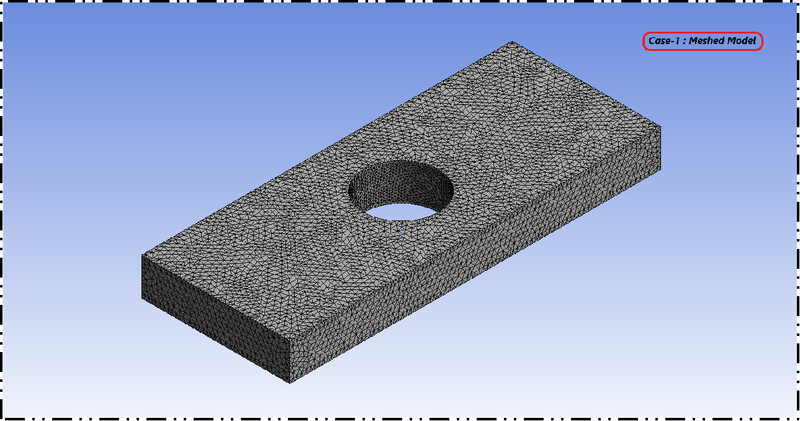
Figure 16-Meshed Model of Case 1. |
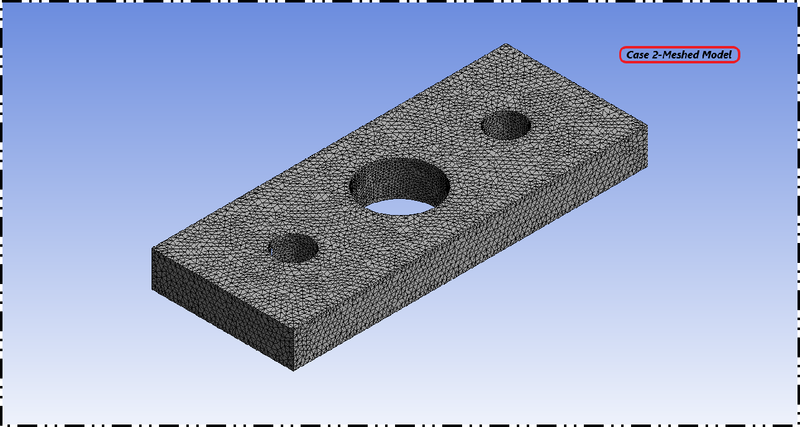
Figure 17-Meshed Model of Case 2. |
Phase 3-Give Boundary Conditions to the Model :
- Here we have to fix the left side of the face for both cases.
- Fix the Left Side face of the Model.
- Give Force as 500 N at the Right Side Face of the Model for both cases. This is shown in below Figure 19.
- To give Fixed Support >> Right Click on Static Structural >> Insert >> Fixed Support.This is shown in below Figure 18.
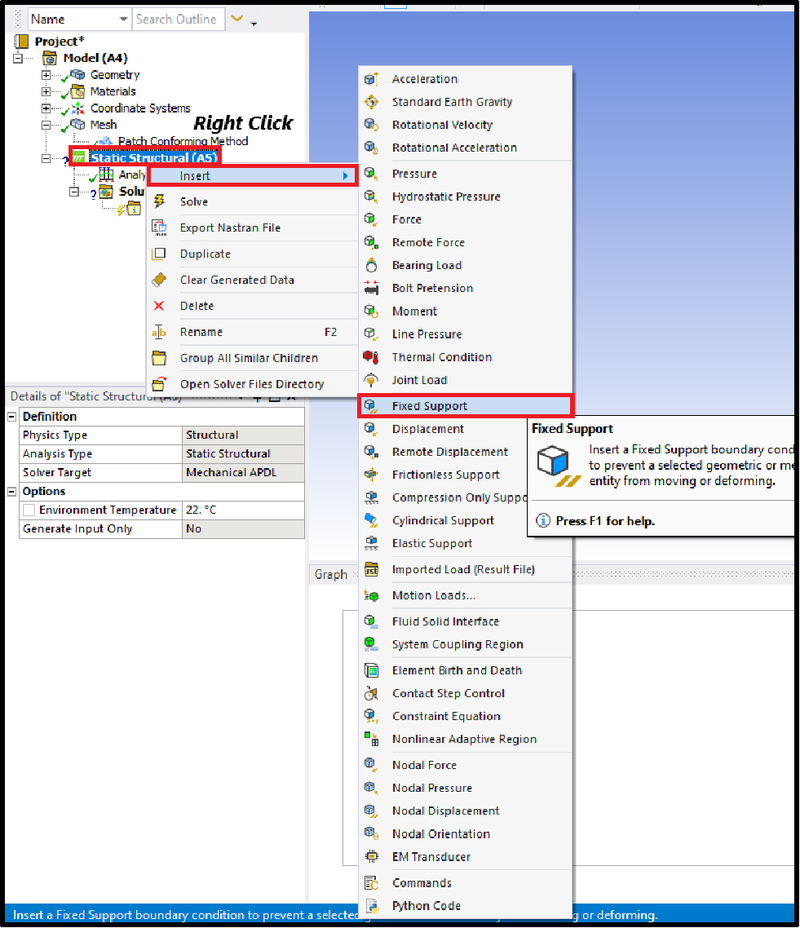
Figure 18-Giving Fixed Support to the Model. |
- The Fixed support given to the model is shown in below Figure 19.
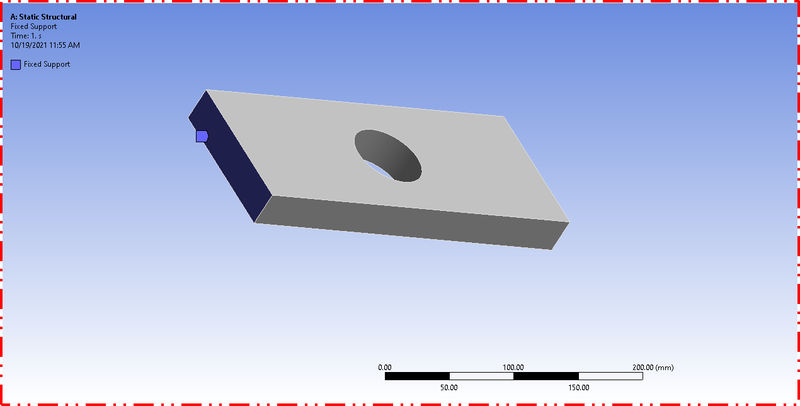
Figure 19-Fixed Support Given to the Model. |
- Similarly give the force to the model,To give Force >> Right Click on the Static Structural >> Insert >> Force >> Select the Face >> Apply >> Magnitude as 500 N.
- Here define the Direction to the Component and give the force value as -500 N>Which is shown in below Figure 20.
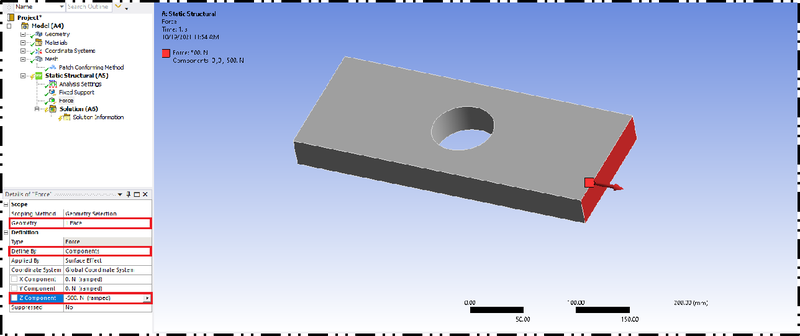
Figure 20-Define the Direction by Components. |
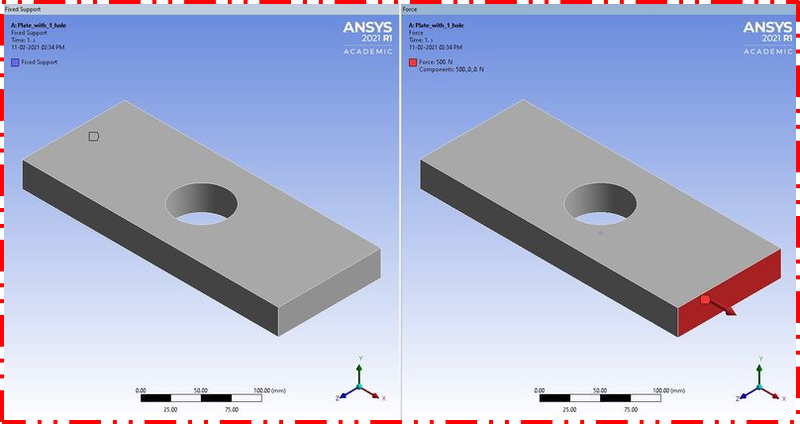
Figure 21-Fixed Support and Force Given to Case 1. |
- Similarly, give the boundary conditions for case 2 also. The boundary conditions have been given to case 2 which is shown in below Figure 22.
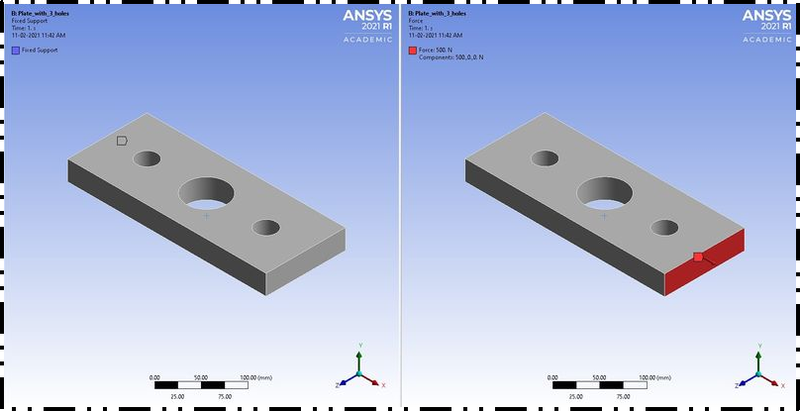
Figure 22-Fixed Support and Force Given to Case 2. |
Phase 4-Request for the Outputs :
- Here we have to request outputs for the VonMisses Stress, Strain, and for Total Deformation.
- To request Output for Stress,Right Click on the Solution >> Insert >> Stress >> Equivalent Von Misses Stress.
- To request Output for Strain,Right Click on the Solution >> Insert >> Strain >> Equivalent Von Misses Strain.
- To request Output for Total Deformation,Right Click on the Solution >> Insert >> Deformation >> Total Deformation.
- This is shown in below Figure 23.
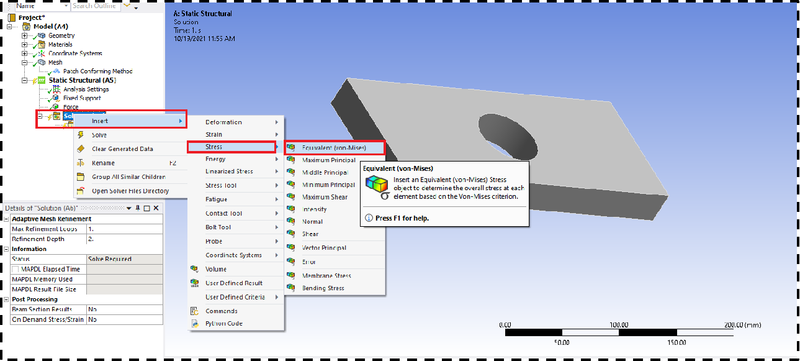
Figure 23-Requesting Outputs for the Stress, Strain, and Deformation. |
- After requesting all the outputs which is shown in below Figure 24. Run the Simulation.
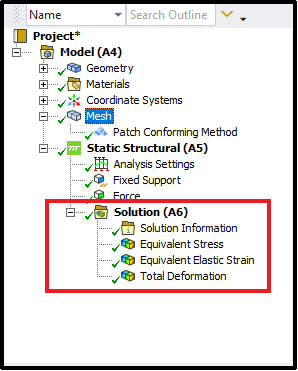
Figure 24-Requested all the Outputs. |
Phase 5-Run the Simulation for both the Cases :
- To run the simulation, Right Click on the Solution >> Solve. This is shown in below Figure 25.
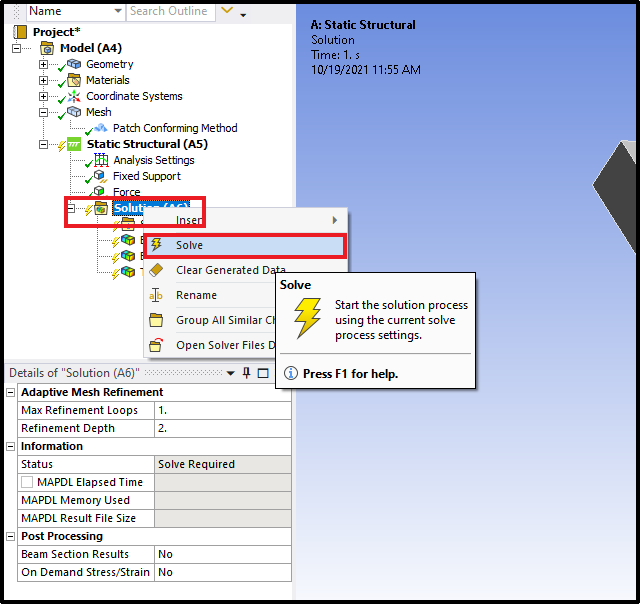
Figure 25-Solving all the Outputs Requested. |
- After Solving the outputs requested, the simulation results for Case 1 and Case 2 is shown in the below Figures.
VonMisses Stress [Case 1] :
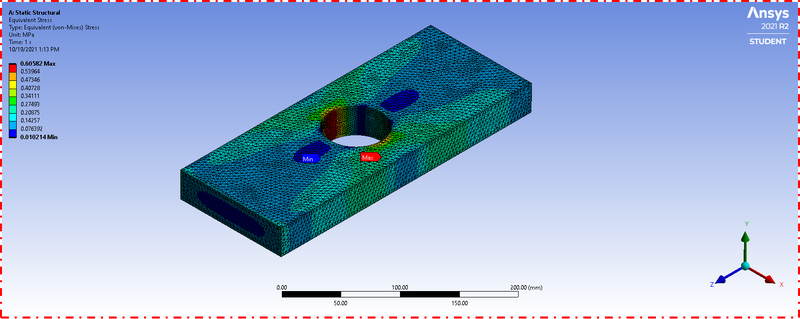
Figure 26-VonMisses Stress Case 1. |
VonMisses Stress [Case 2] :
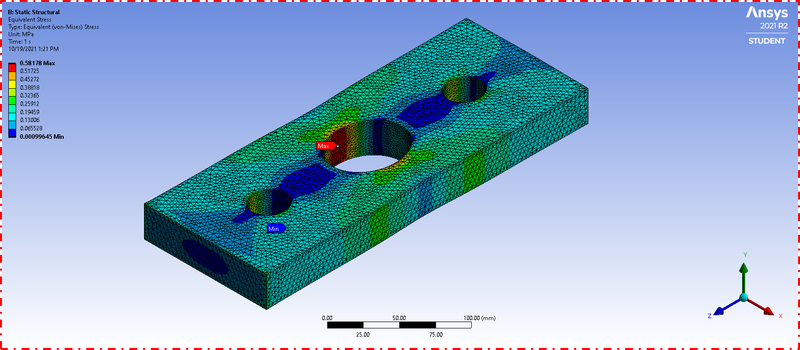
Figure 27-VonMisses Stress Case 2. |
Equivalent Elastic Strain [Case 1] :
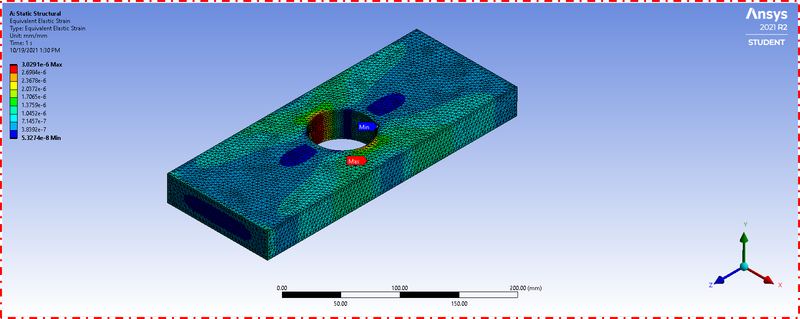
Figure 28-Equivalent Elastic Strain Case 1. |
Equivalent Elastic Strain [Case 2] :
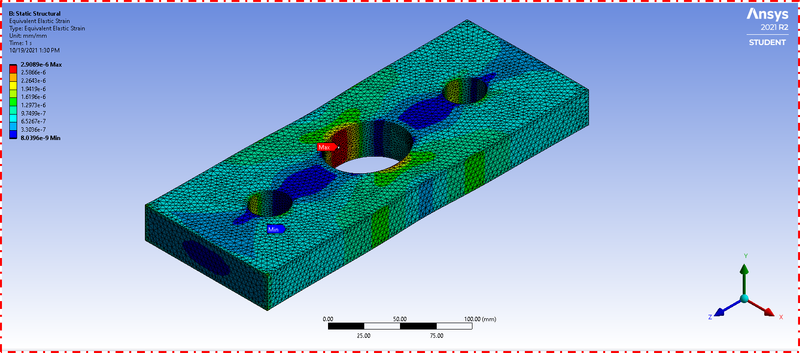
Figure 29-Equivalent Elastic Strain Case 2. |
Total Deformation [Case 1] :
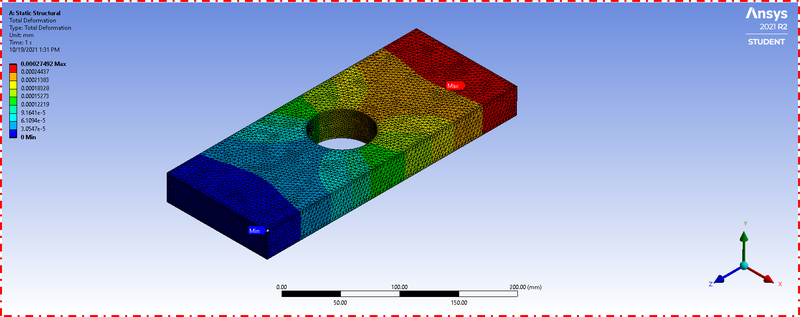
Figure 30-Total Deformation Case 1. |
Total Deformation [Case 2] :
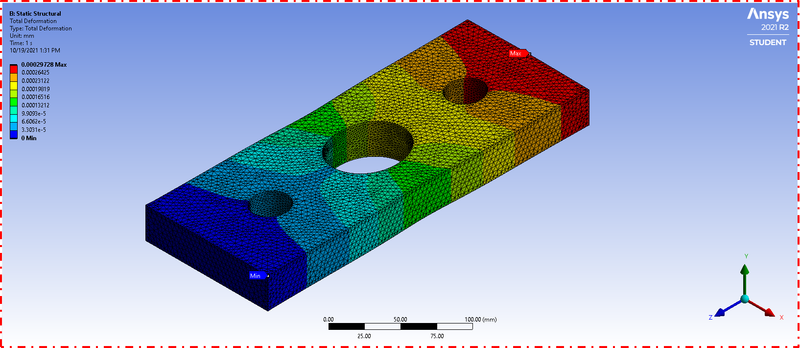
Figure 30-Total Deformation Case 2. |
_1634644029.gif)
Figure 31-VonMisses Stress Case 1 Simulation Animation. |
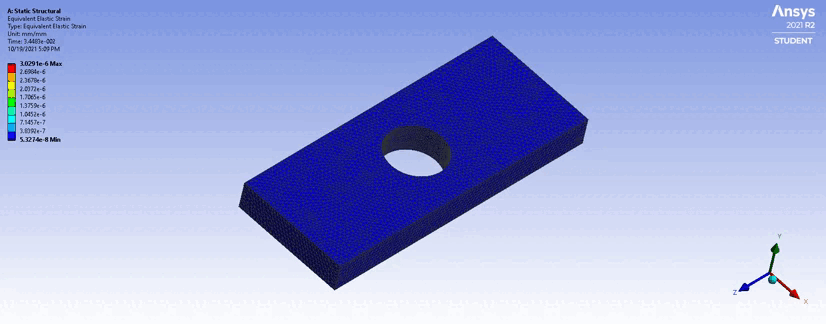
Figure 32-Equivalent Elastic Strain Case 1 Simulation Animation. |
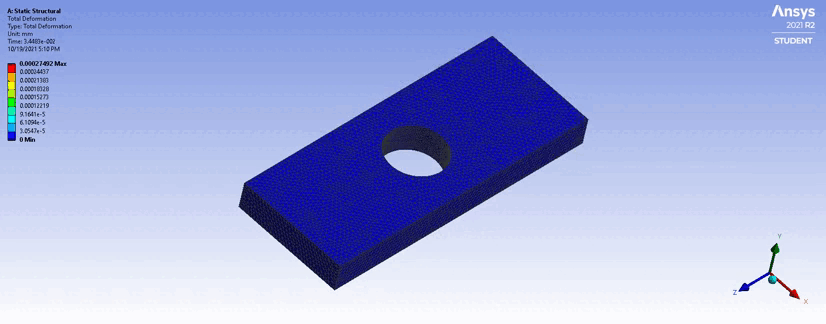
Figure 33-Total Deformation Case 1 Simulation Animation. |
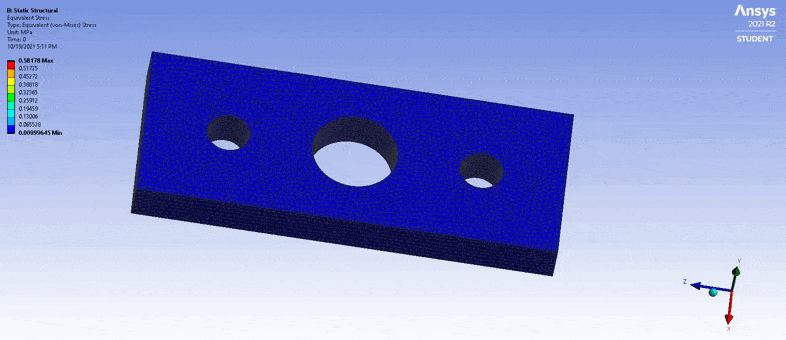
Figure 34-VonMisses Stress Case 2 Simulation Animation. |
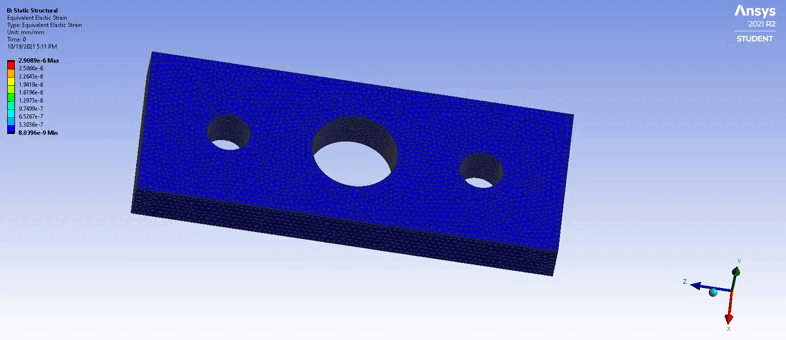
Figure 35-Equivalent Elastic Strain Case 2 Simulation Animation. |
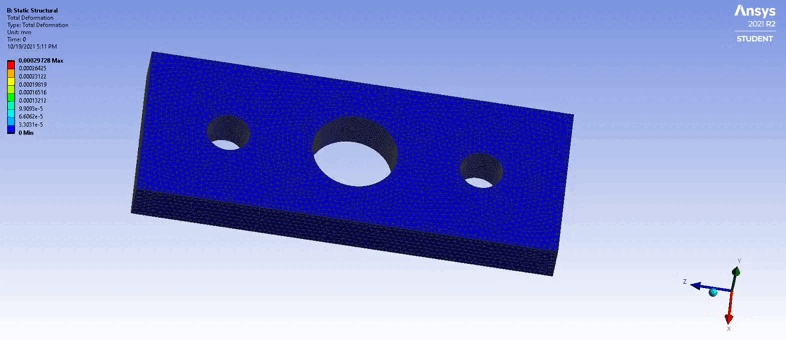
Figure 36-Total Deformation Case 2 Simulation Animation. |
VonMisses Stress :
- From the VonMisses Stress contour plot for Case-1, It is observed that the maximum stress of 0.60582 MPa is developed around the hole region having minimum cross-sectional area and material. The minimum stress of 0.010214 MPa is developed around the hole region having maximum cross-sectional area and material.
- From the VonMisses Stress stress contour plot for Case-2, it is observed that the maximum stress of 0.58178 MPa is developed around the larger hole region having minimum cross-sectional area and material. The minimum stress of 0.00099645 MPa is developed around the smaller hole region having maximum cross-sectional area and material.
- More stress is developed at multiple holes component because while deformation, a cross-sectional area might be decreased. Due to decreasing the cross-section of the component at anywhere with the same magnitude of applied force, by result stresses will increase at the place of less cross-sectional area.
- Due to the presents of multiple holes in the middle of the components in Case 2, more resistance has been created at the top & bottom portions of the model as compared to Case 1. If we take Case 1, stress concentration acting over of the hole at top & bottom portion is less as compared to Case 2.
Total Deformation :
- As we can see from the deformation contour plots, the deformation for multiple holes component has more deform occurs as compared to Single hole model in both Lateral & Longitudinal directional.
- The maximum deformation for the single hole model Case 1 is 0.00027492 mm and for the multiple holes, the model Case 2 is 0.00026425 mm.
- For components, it should resist the deformation when we apply permissible load. In these two cases, Case 1 is better than Case 2 based on the deformation of a component.
Comparison of Results :
- The maximum and minimum values of VonMisses Stress and total deformation is tabulated as shown in below Table 1
Cases
|
Von-Misses Stress (MPa)
|
Total Deformation (mm)
|
Equivalent Elastic Strain
|
Max.
|
Min.
|
Max.
|
Min.
|
Max.
|
Min.
|
Case-1
|
0.60582 MPa
|
0.010214 MPa
|
0.00027492 mm
|
0
|
3.0291e-6
|
5.3274e-8
|
Case-2
|
0.58178 MPa
|
0.00099645 MPa
|
0.00026425 mm.
|
0
|
2.9089e-6
|
8.0396e-9
|
- The maximum value of Von-Misses Stress is developed in Case-1, plate with a single hole because of sudden deviation of stress flow lines around the hole and minimum material in the region of a hole. The minimum value of Von-Misses Stress is developed in Case-2, plate with three holes because of gradual deviation of stress flow lines around the small holes.
- The maximum deformation has occurred in Case-2, plate with three holes because of minimum material condition due to three holes.
From the Analysis Point of View :
- From an analysis point of view, the design of a rectangular plate with three holes, Case-2 is preferred, I will select Case-2, cause Von-Misses Stress developed around the holes is less compared to Case-1.
- The stress concentration is less in Case-2 when compared to Case-1. The computational time required is also less for Case-2 when compared to Case-1. So Case 2 is preferred.
From the Manufacturing Point of View :
- From the manufacturing point of view, the design of a rectangular plate with a single hole, Case-1 is preferred. I will select Case 1, cause the design is simple for manufacturing, only one hole is required to be drilled in the plate when compared to Case-2 design.
- The manufacturing time and labor cost can be minimized by preferring Case-1 design. The stiffness of the Case-1 design is more compared to the Case-2 design because the total deformation that occurred in the Case-1 design is less compared to the Case-2 design.
[Note: We can't say this case is preferable, this case is not preferable, Anyhow it depends on the application. Here in the report, I have said, Case-1 is preferable from a manufacturing point of view and Case-2 is preferable from a design point of view, Cause I have told according to the question and the model given to us, But in real life, It entirely depends on the applications.]
The factor of Saftey = Yield Strength/Working Stress
Yield Strength of Structural Steel=250 Mpa
Working Stress [Maximum Stress]=0.60582 Mpa
FOS=2500.60582
FOS for Case 1=412.663
FOS for Case 2=429.7157
The factor of safety for the two cases is very high, Hence here the model is very safe.
Result :
- Hence the rectangular plate with a circular hole has been designed for two cases
- Case-1: Rectangular Plate with Single Hole.
- Case-2: Rectangular Plate with three Holes.
- Hence the model has been meshed using tetrahedral elements with the minimum element size being 2mm.
- Hence the model has been solved for Von-Misses Stress, Equivalent Elastic Strain, and Total Deformation by applying appropriate boundary conditions.
- Hence the maximum value of Von-Misses Stress is developed in Case-1 [Rectangular Plate with Single Hole].
- Hence the maximum deformation has occurred in Case-2 [ Plate with Three Holes].
- From the Analysis Point of View, the design of a rectangular plate with three holes [Case-2] is preferred because stress concentration around the hole is less compared to the Case-1 design.
- From the Manufacturing Point of View, the design of a rectangular plate with a single hole [Case-1] is preferred because the design is simple for manufacturing. Anyhow keep in mind, it depends on the applications.
Conclusion and Learning Outcome :
In this Week 1 Challenge, I came to know about
- Learned about stress concentration.
- Learned how and where the stress concentration is occurring.
- Learned how to avoid stress concentration.
- Learned how to apply boundary conditions to the model.
- Learned how to design in the SpaceClaim.