Static Structural Analysis on Spur Gear
Aim :
- Run the simulation for the spur gear with different materials and find out the Total Deformation, Equivalent stress, and Stress Intensity.
Objective :
- To perform a Structural Analysis on the spur gear for all three cases with different materials such as Cast Steel, Cast Bronze, and Cast Iron.
- To add the required materials to the case set up from the Engineering data source.
- To find the location of the fracture, Where it occurs on the gear.
- To compare the simulation results for those three materials.
- To find out the stress intensity in the spur gear.
- To recommend the material based on the results.
Theoretical FrameWork :
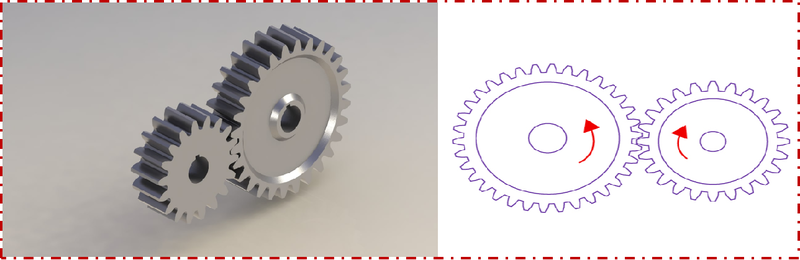
- Spur gears are a cylindrical-shaped toothed component used in industrial equipment to transfer mechanical motion as well as control speed, power, and torque. These simple gears are cost-effective, durable, reliable, and provide a positive, constant speed drive to facilitate daily industrial operations.
- Spur gears are one of the most popular types of precision cylindrical gears. These gears feature a simple design of straight, parallel teeth positioned around the circumference of a cylinder body with a central bore that fits over a shaft. In many variants, the gear is machined with a hub that thickens the gear body around the bore without changing the gear face. The central bore can also be broached to allow the spur gear to fit onto a spline or keyed shaft.
- Spur gears are used in mechanical applications to increase or decrease the speed of a device or multiply torque by transmitting motion and power from one shaft to another through a series of mated gears.
Industrial applications of Spur Gear :
- Transmissions.
- Conveyor systems.
- Speed reducers.
- Engines and mechanical transportation systems.
- Gear pumps and motors.
- Machining tools.
Stress Intensity :
- The stress intensity factor is a concept in Fracture Mechanics that is used to measure the stress concentration at a crack tip. In safety design, It is compared to a critical value and evaluates whether a component or structure is prone to fracture.
- The critical value is typically a material parameter and varies from material to material. Stress at a point in a structure due to pressure resulting from combined tension (positive) stresses and compression (negative) stresses.
Procedure :
Phase 1-Material SetUp :
- To set up the material for the spur gear model. First, drag and drop the static structural analysis workspace into the project schematic from the analysis system. This is shown in below Figure 2.

Figure 2-Ansys Workbench Workspace. |
- After deploying the static structural analysis system in the project schematic workspace.
- Define the Engineering Data and geometry, To define the Geometry and Engineering Data, Right Click on the Engineering Data and click to edit, it will take to the Engineering Tab.
- There Right Click on the Material Tab, A window will Pop-Up stating Engineering data sources.
- Click on the Engineering Data Sources, There go and select the material to define the engineering data. This is shown in below Figures 3,4,5.
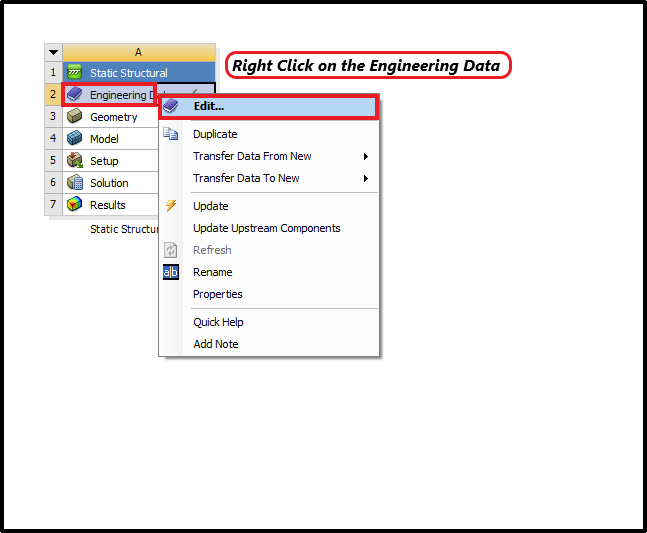
Figure 3-Right Click on the Engineering Data. |
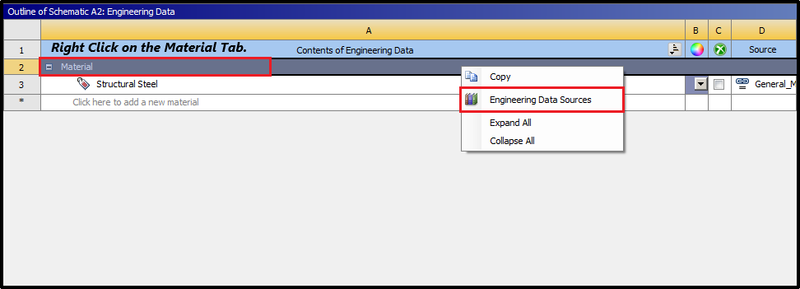
Figure 4-Right Click on the Material Tab. |
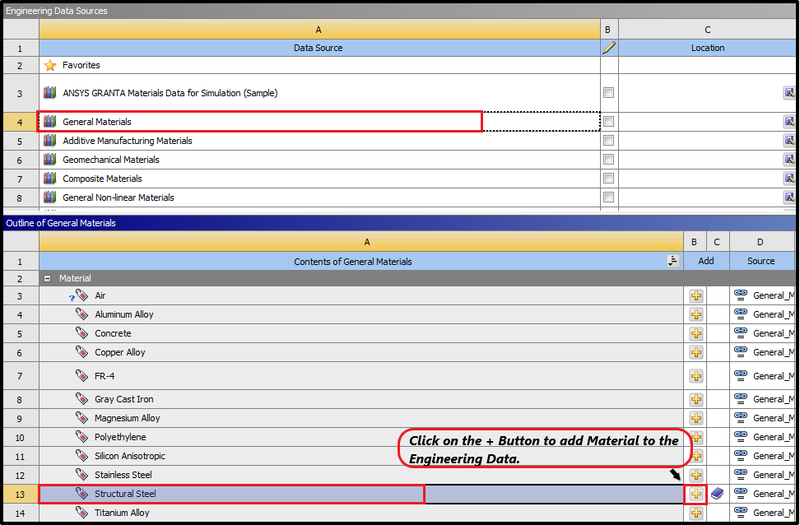
Figure 5-Select the Material as Structural Steel to Define the Engineering Data. |
- For this spur gear model,Create a material cards for the Cast Steel,Cast Bronze and Cast Iron.
- To create a custom material,First create a custom material library,In that library create all those three material cards.
- To create a new library,Click on the option click here to add new library and name it as spur gear materials which is shown in below Figure 6.
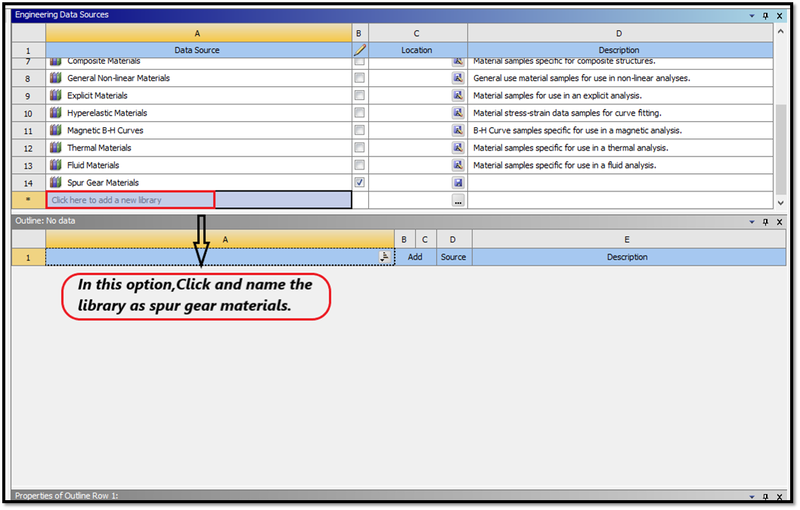
Figure 6-Create a New Library. |
- After creating a new library,In that library go and add the materials and properties,Which is shown in below Figure 7.
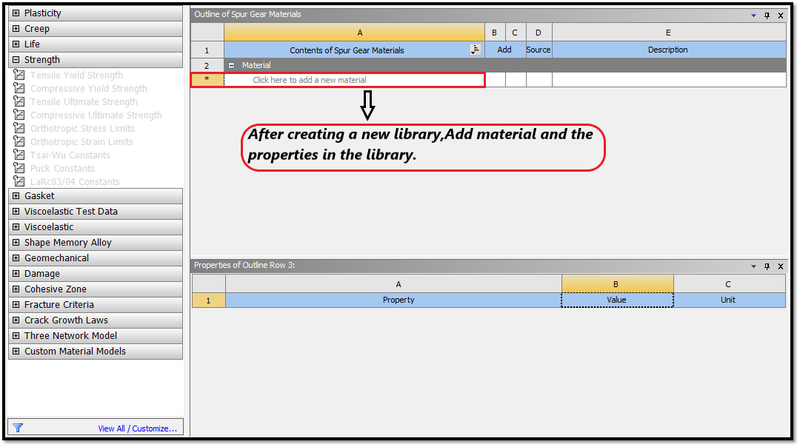
Figure 7-Add a New Material. |
- Add the properties to all the materials created,To add the materials,Drag and drop the material proprties or double click on the properties to add them to the material.Which is shown in below Figure 8.
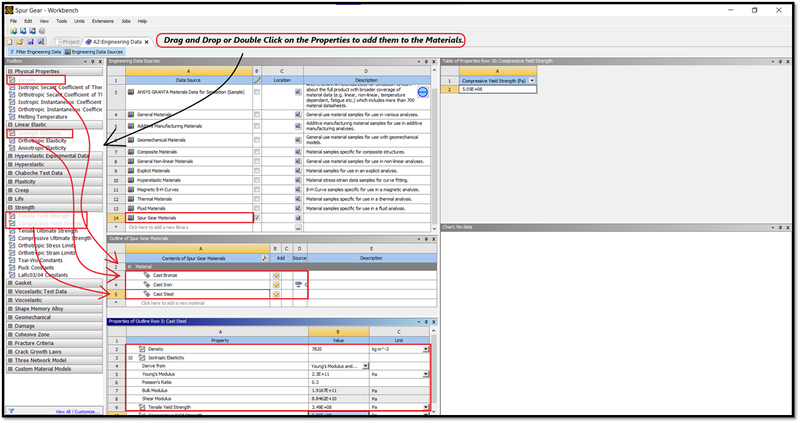
Figure 8-Drag abd Drop or Double Click on the Properties to Add. |
- Atlast save the Material Cards in to a new location,Which is shown in below Figure 9.
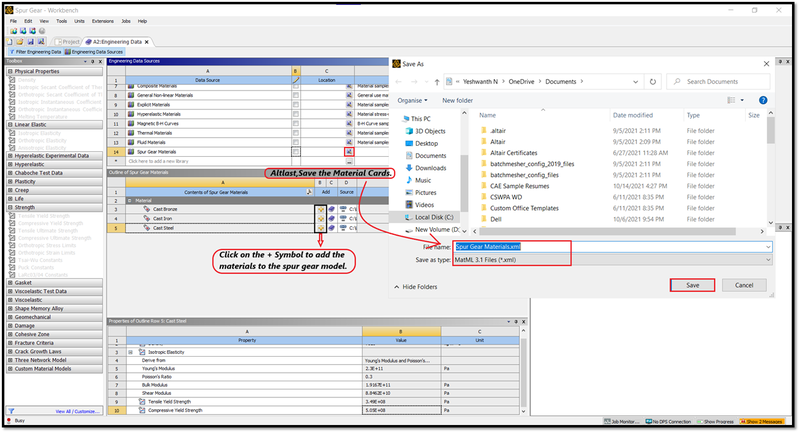
Figure 9-Save the Material Card into a New Location. |
Phase 2-Load Case Set-Up :
- Next set up the geometry. To set up the geometry, Right-Click on the Geometry option >> Import Geometry. This is shown in below Figure 10.
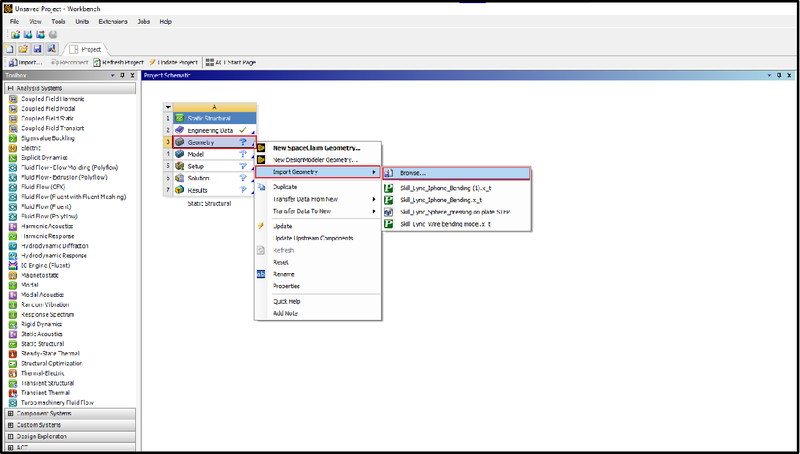
Figure 10-Importing Geometry. |
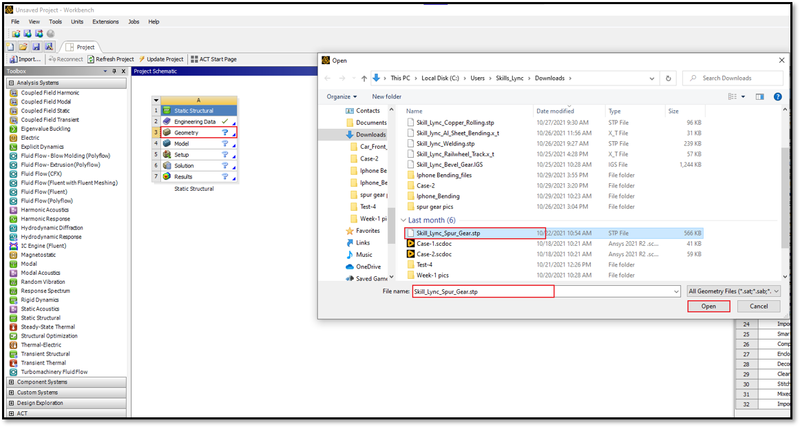
Figure 11-Selecting the Geometry to Import. |
- Next double click on the geometry to check, Whether the model imported is spur gear or not. Space Claim Workspace will open.
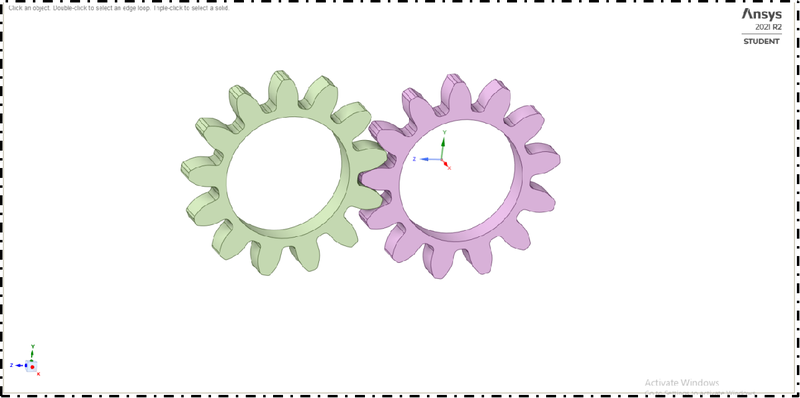
Figure 12-Spur Gear in the Space Claim. |
- Next, define the model, Double click on the model, The Mechanical Workspace will open, There go and set up the load case for all three cases.
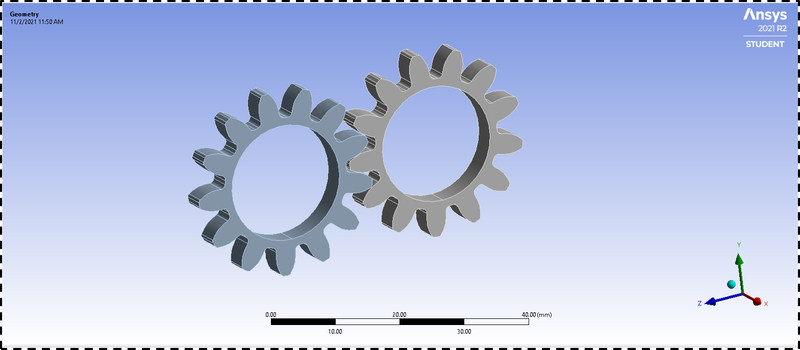
Figure 13-Model Loaded in Mechanical Workspace. |
- Next define the , material as cast iron for the spur gear which is shown in below Figure 14.
- Simillarly define the material for all the cases.The material properties is shown in below Figures 15,16 and 17.
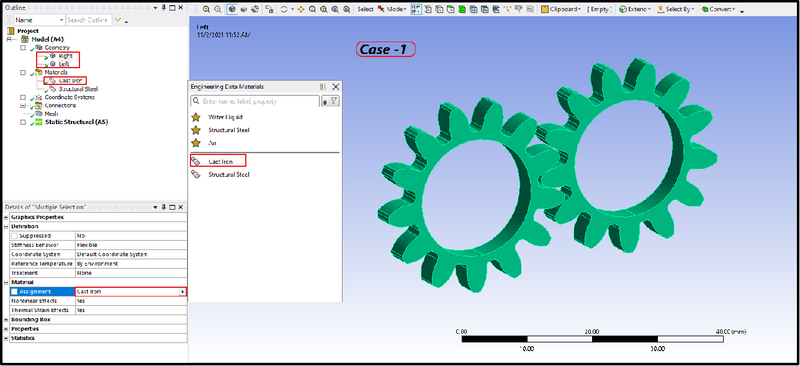
Figure 14-Define Material. |
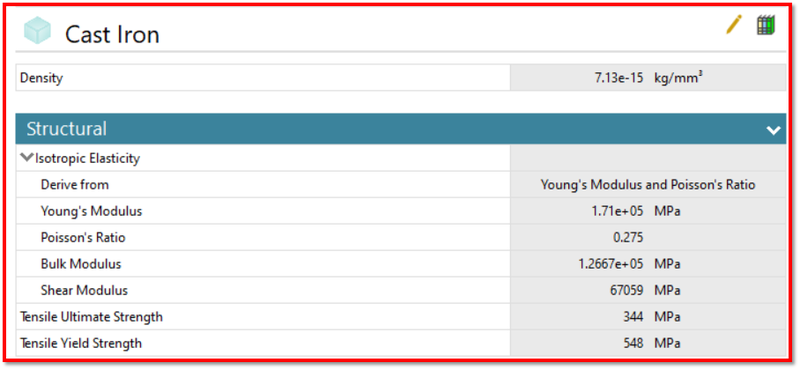
Figure 15-Cast Iron Material Properties. |
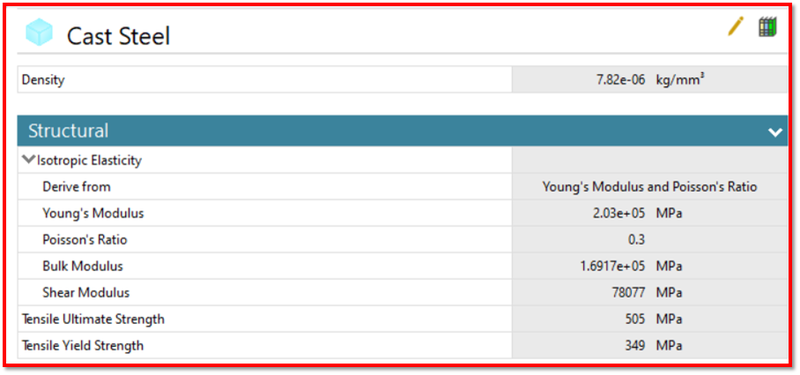
Figure 16-Cast Steel Material Properties. |
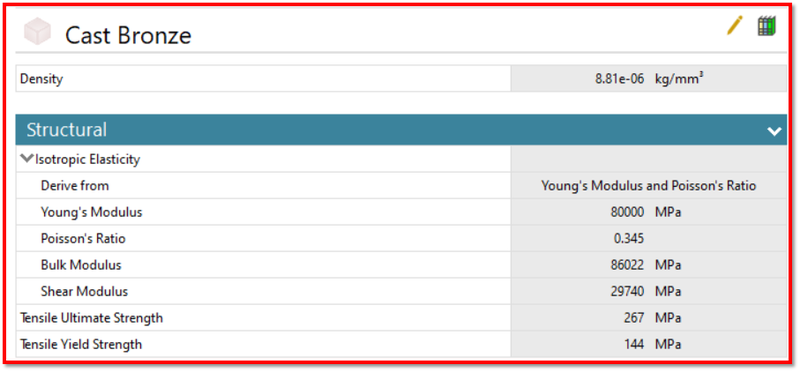
Figure 17-Cast Bronze Material Properties. |
- Next after defining the material,Now define the contact for the spur gear.
- To define a contact,First right click on the default contact and rename it as rename based on definition,Which is shown in below Figure 18.
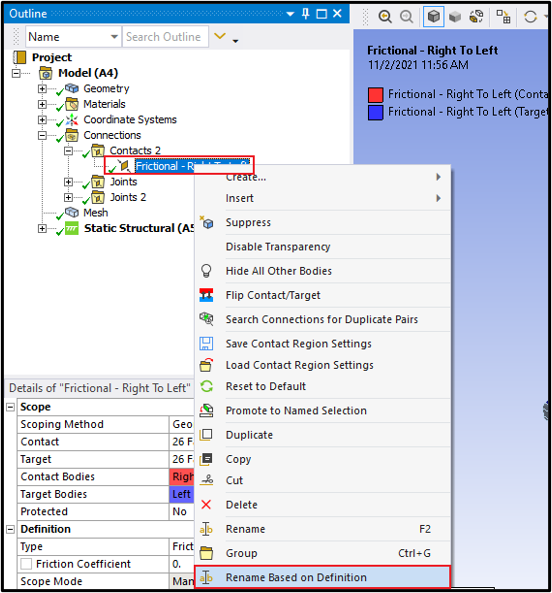
Figure 18-Rename Based on Definition. |
- Now define the contact which is shown in below Figure 19.
- Select the Contact and Target faces of the gear which is shown in below Figure 19.
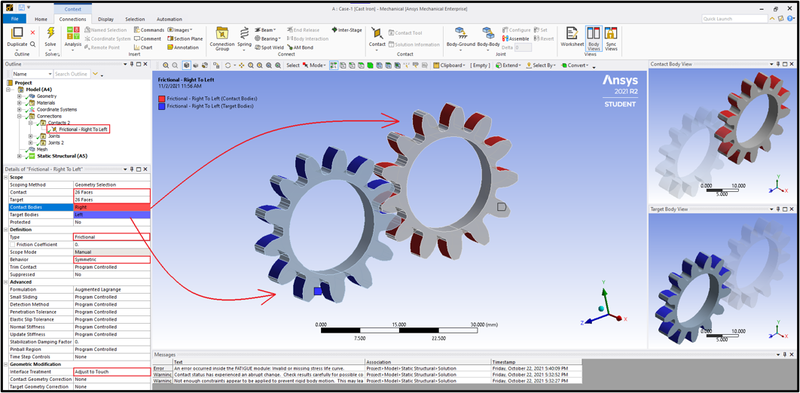
Figure 19-Define the Contact. |
- After defining the contact, We have to deploy joints for the spur gear.
- To create a joints,Right Click on the Connections >> Insert >> Joint.Which is shown in below Figure 20.
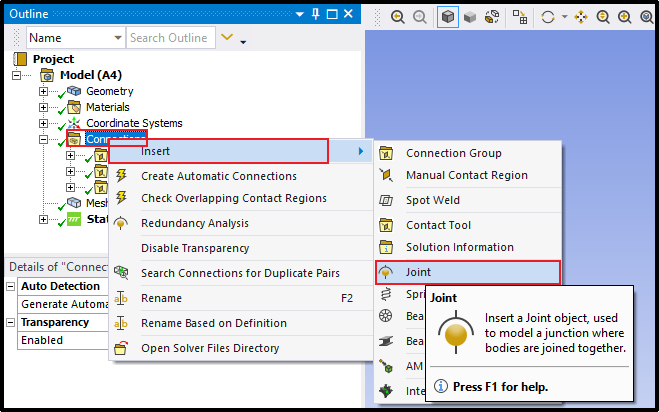
- Next in the parameters window, We have to select the type as Body-Ground for both joints in the connections panel.
- And select the scope, Which is shown in below Figure 21.
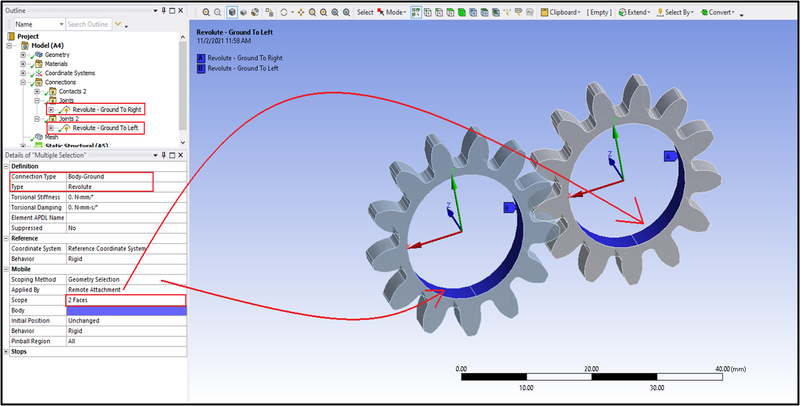
Figure 21-Select the Faces for the Scope. |
- After defining the joint in the connections panel,We have to define mesh for the spur gear.
- To define Mesh,Click on the Mesh >> Give Mesh Size as 2mm.Which is shown in below Figure 22.
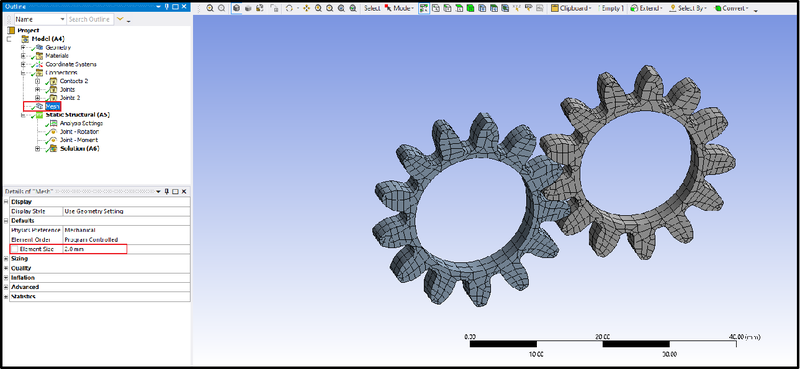
Figure 22-Meshed Spur Gear with 2mm Size. |
- Create a two joints,One for Rotation and Other for Moment, Which is shown in below Figures 23 and 24.
- To create Joint Loads, Right Click on the Static Structural >> Insert >> Joint Load.
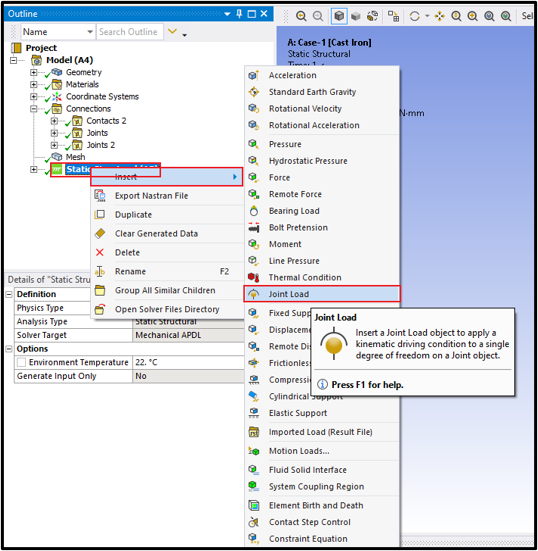
Figure 23-Create Joint Loads. |
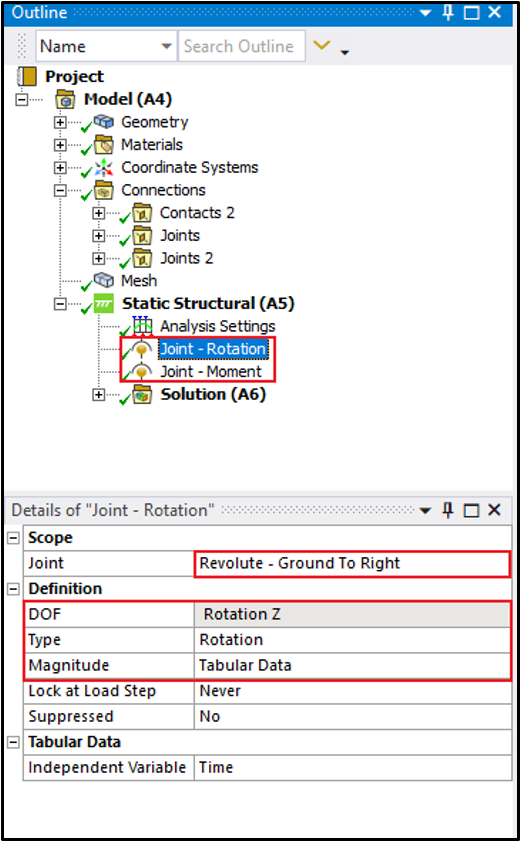
Figure 24-Joint Load for Rotation. |
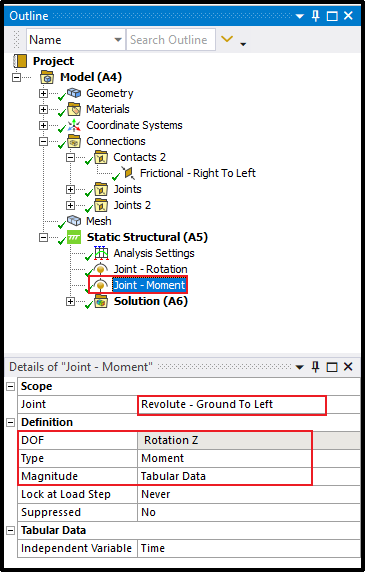
Figure 25-Joint Load for Moment. |
- Next, select the Joint Load Rotation, We have to give values for that, Which is shown in below Figure 26.
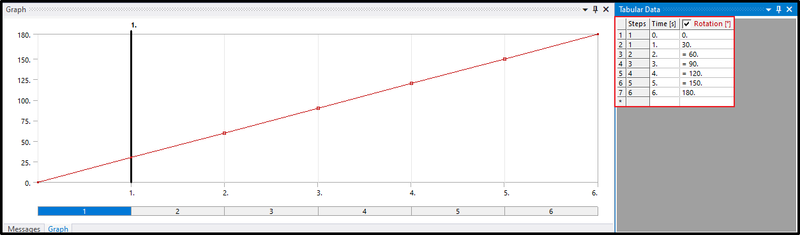
Figure 26-Give the Values for the Rotation. |
- Next, select the Joint Load Moment, We have to give values for that, Which is shown in below Figure 27.
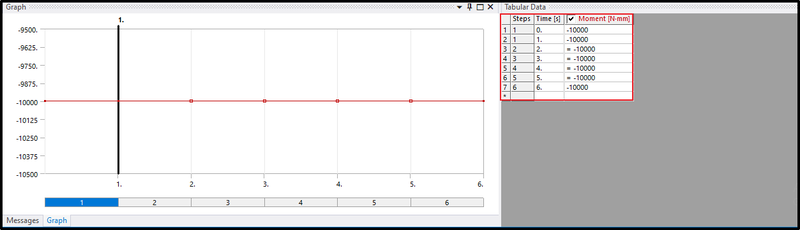
Figure 27-Give the Values for the Moment. |
- The Joint Loads created is shown in below Figure 28.
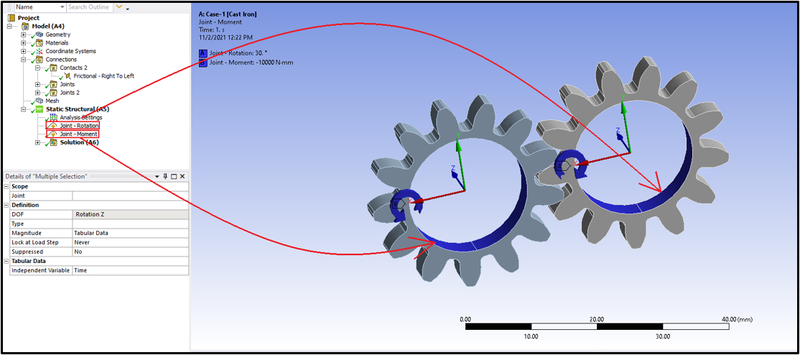
Figure 28-Joint Loads Created. |
- Next, we have to give some parameters in the analysis settings.Which is shown in below Figure 29.
- To give the parameter's value, Click on the analysis Settings and the give the values.
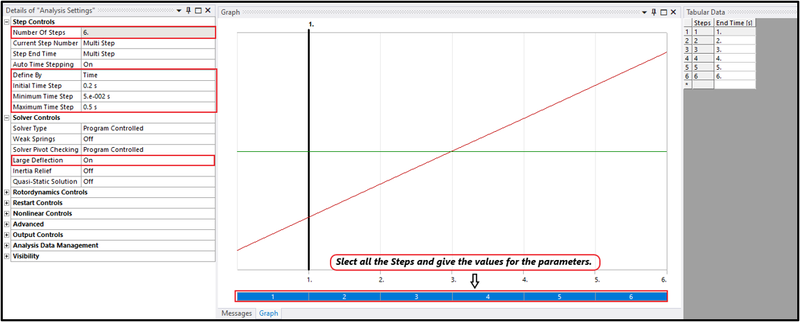
Figure 29-Values given for the Parameters in the Analysis Settings. |
Phase 3-Request for the Outputs :
- Here we have to request outputs for the VonMisses Stress, Strain, and for Total Deformation.
- To request Output for Stress,Right Click on the Solution >> Insert >> Stress >> Equivalent Von Misses Stress.
- To request Output for Strain,Right Click on the Solution >> Insert >> Strain >> Equivalent Von Misses Strain.
- To request Output for Total Deformation,Right Click on the Solution >> Insert >> Deformation >> Total Deformation.
- This is shown in below Figure 30.
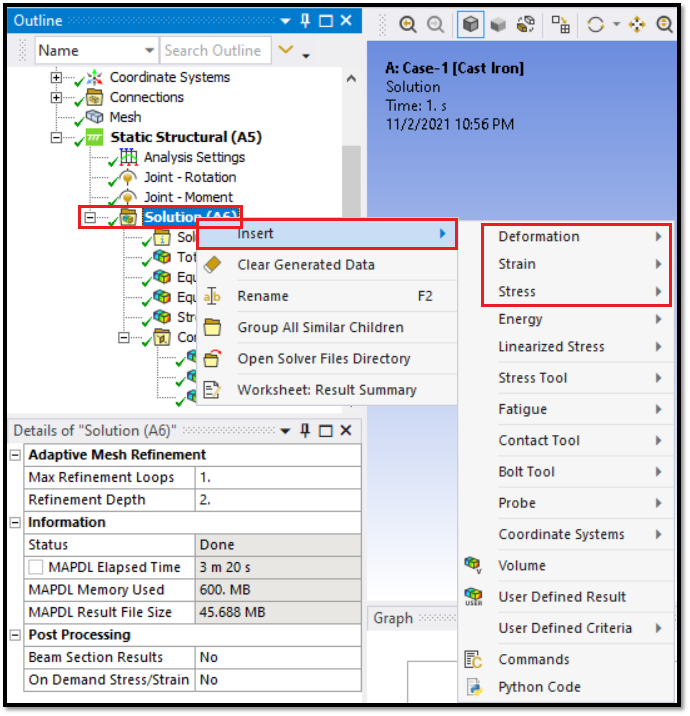
Figure 31-Requesting Outputs for the Stress, Strain, and Deformation. |
- Next request output for the contact.
- To request Contact Tool >> Right Click on the Solution >> Insert >> Contact Tool >> Pressure >> Status >> Frictional Stress.Which is shown in below Figures 32 and 33.
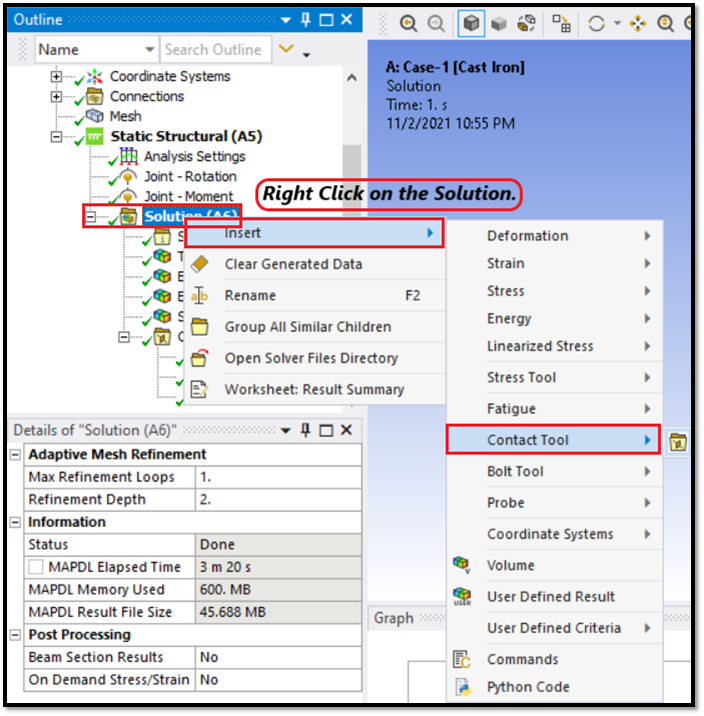
Figure 34-Requesting Output for Contact. |
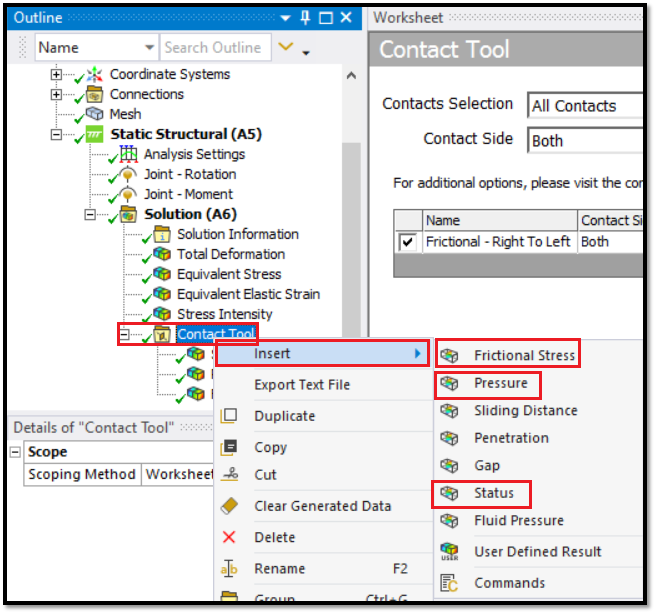
Figure 35-Requesting Outputs for Contact Tool. |
- Next request for the Stress Intensity,To request Stress Intensity >> Right Click on Solution >> Insert >> Equivalent Stress >> Type >> Stress Intensity.Which is shown in below Figure 36.
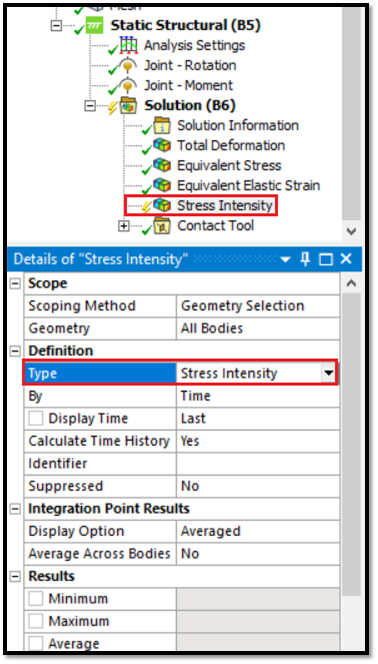
Figure 37-Stress Intensity Requested. |
- The Output requested for the Spur Gear is shown in below Figure 38.
- After requesting all the outputs which is shown in below Figure 38. Run the Simulation.
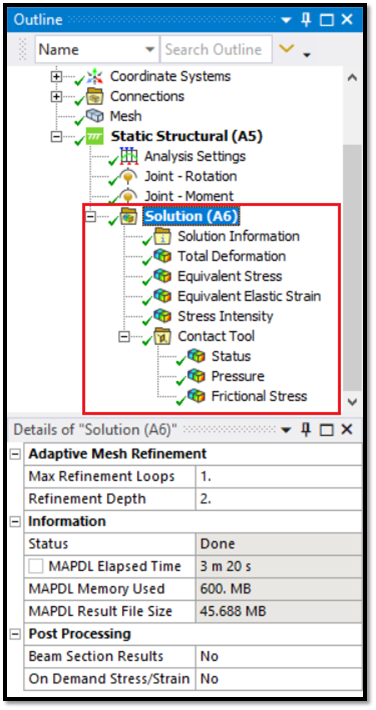
Figure 38-Required Outputs Requested. |
Phase 4-Run the Simulation for all the three Cases :
- To run the simulation, Right Click on the Solution >> Solve. This is shown in below Figure 39.
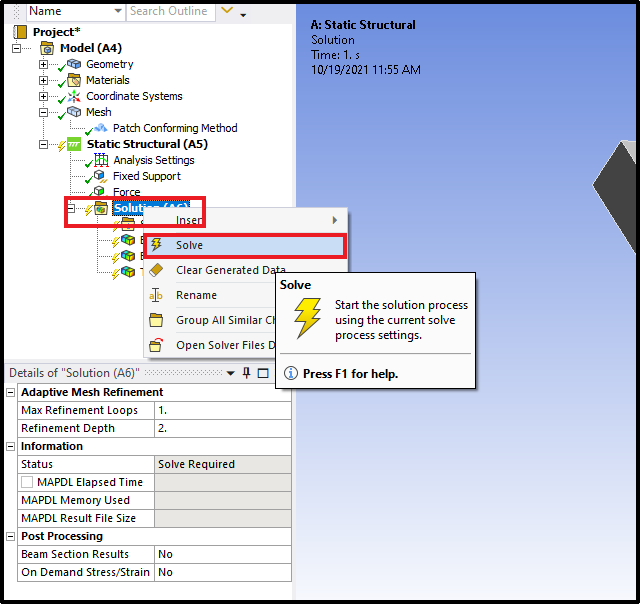
Figure 39-Solve all the Outputs Requested. |
- After solving the outputs requested, the simulation results for all the three cases is shown in the below Figures.
Equivalent Von Misses Stress [Case 1] :
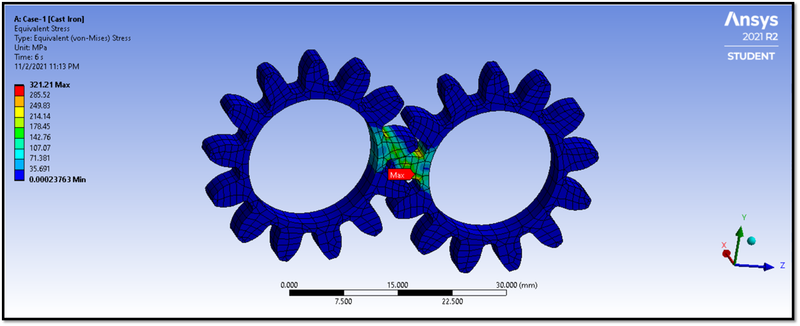
Figure 40-Equivalent Von Misses Stress Case 1. |
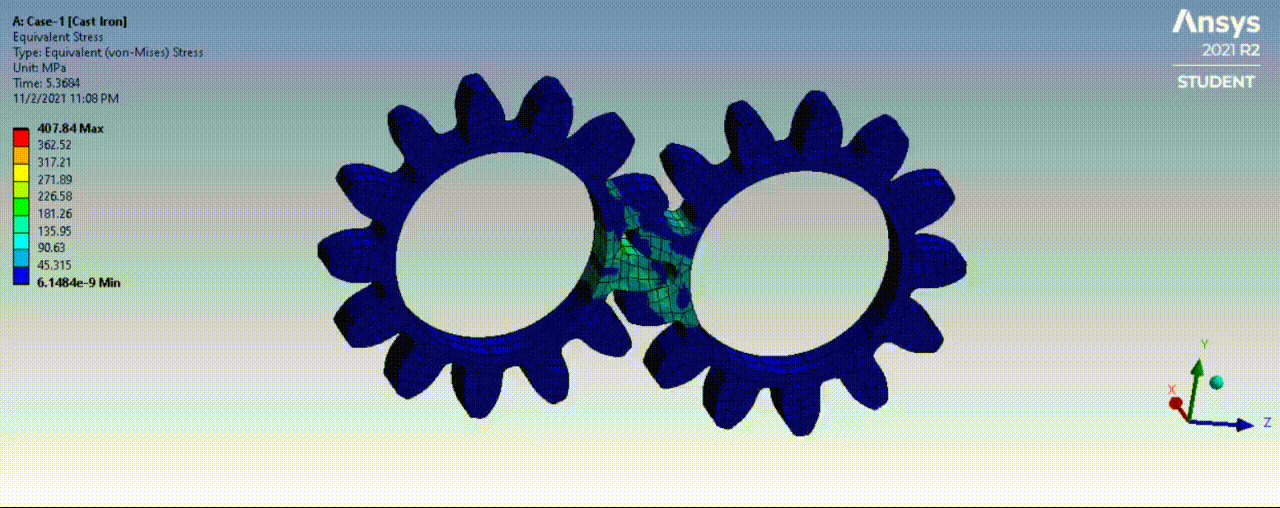
Figure 41-Equivalent Von Misses Stress Animation Case 1. |
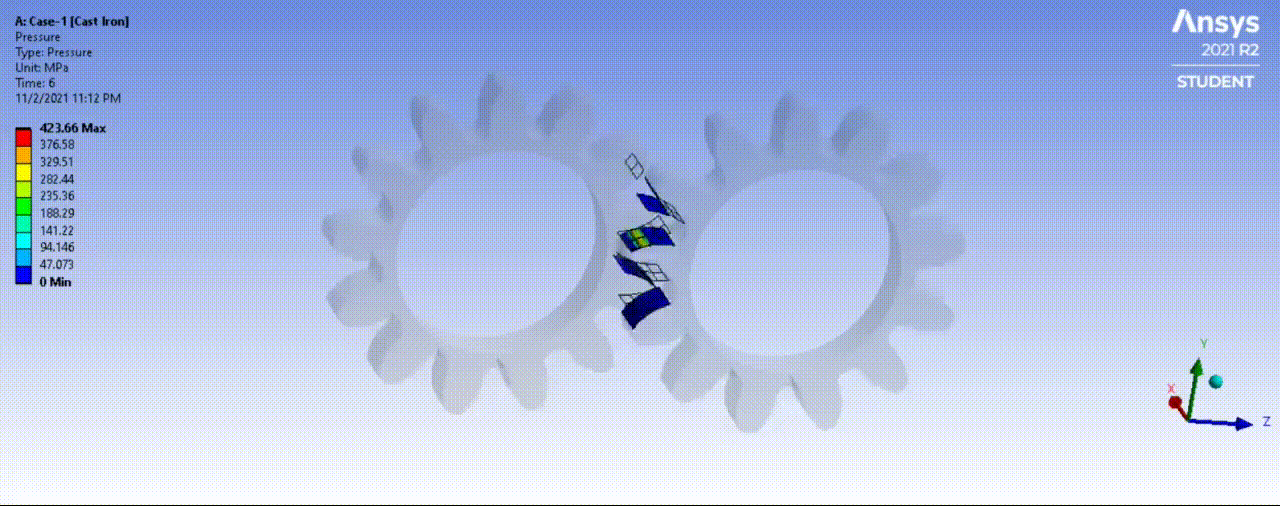
Figure 41:1-Contact Tool [Pressure] Animation Case 1. |
Equivalent Von Misses Stress [Case 2] :
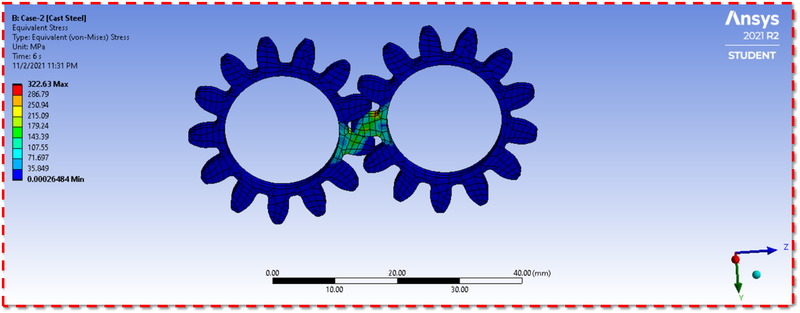
Figure 42-Equivalent Von Misses Stress Case 2. |
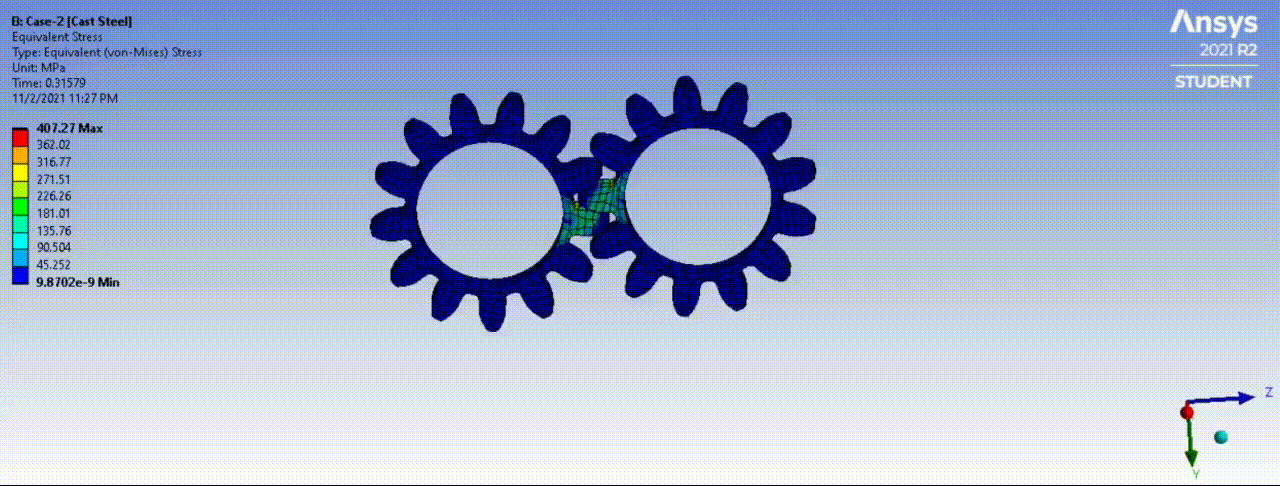
Figure 43-Equivalent Von Misses Stress Animation Case 2. |
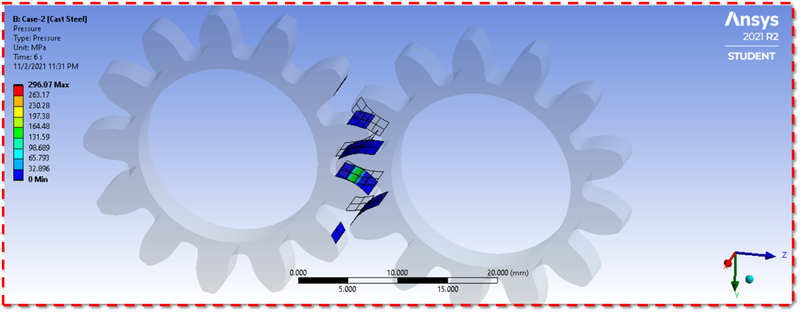
Figure 43:1 Contact Tool [Pressure] Case-2. |
Equivalent Von Misses Stress [Case 3] :
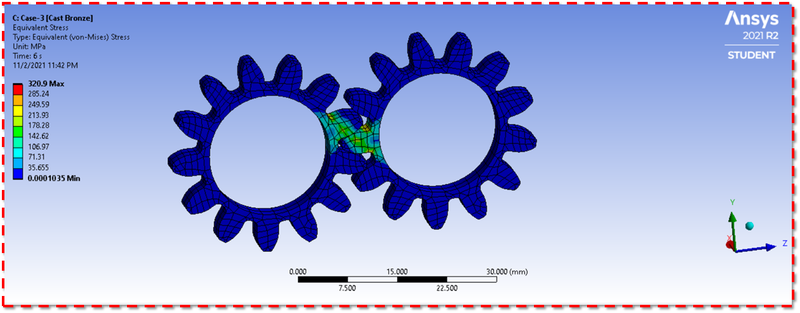
Figure 44-Equivalent Von Misses Stress Case 3. |
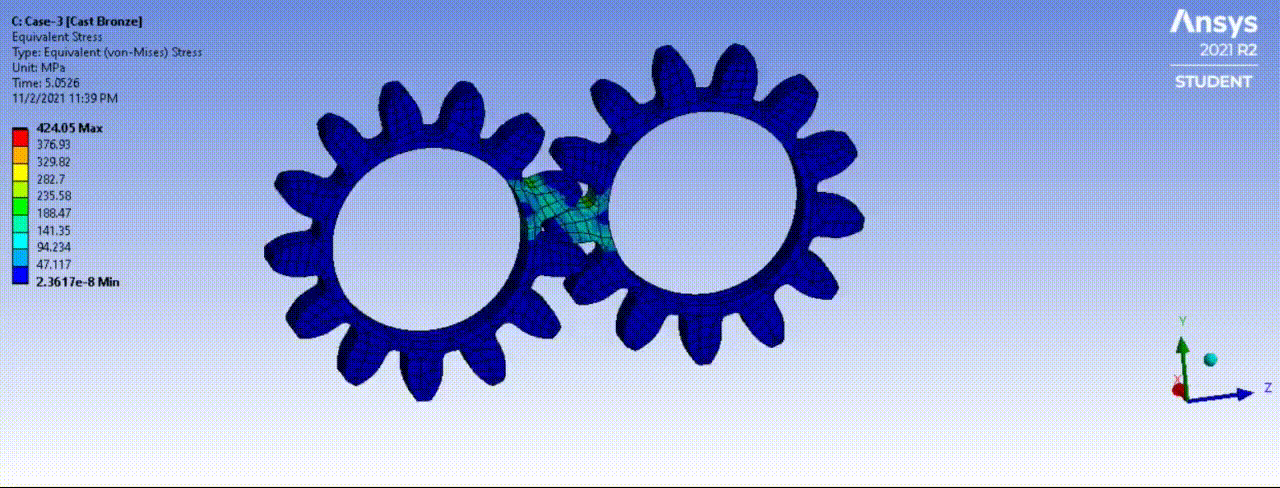
Figure 45-Equivalent Von Misses Stress Animation Case 3. |
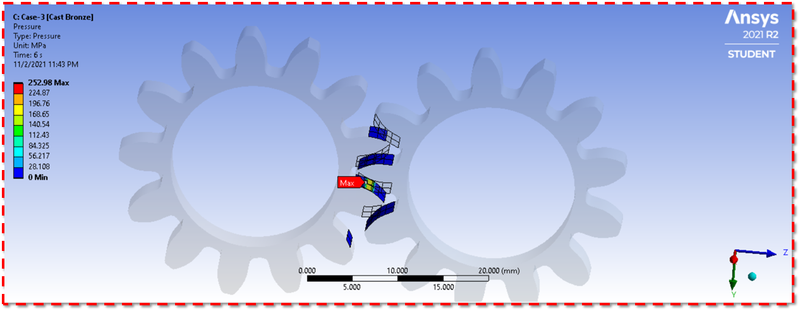
Figure 45:1 Contact Tool [Pressure] Case-3. |
Equivalent Elastic Strain [Case 1] :
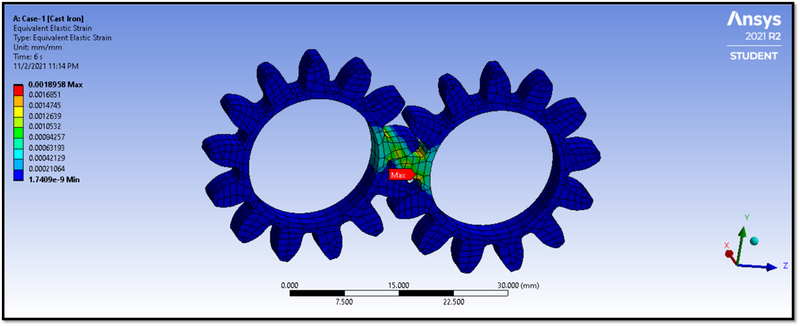
Figure 46-Equivalent Elastic Strain Case 1. |
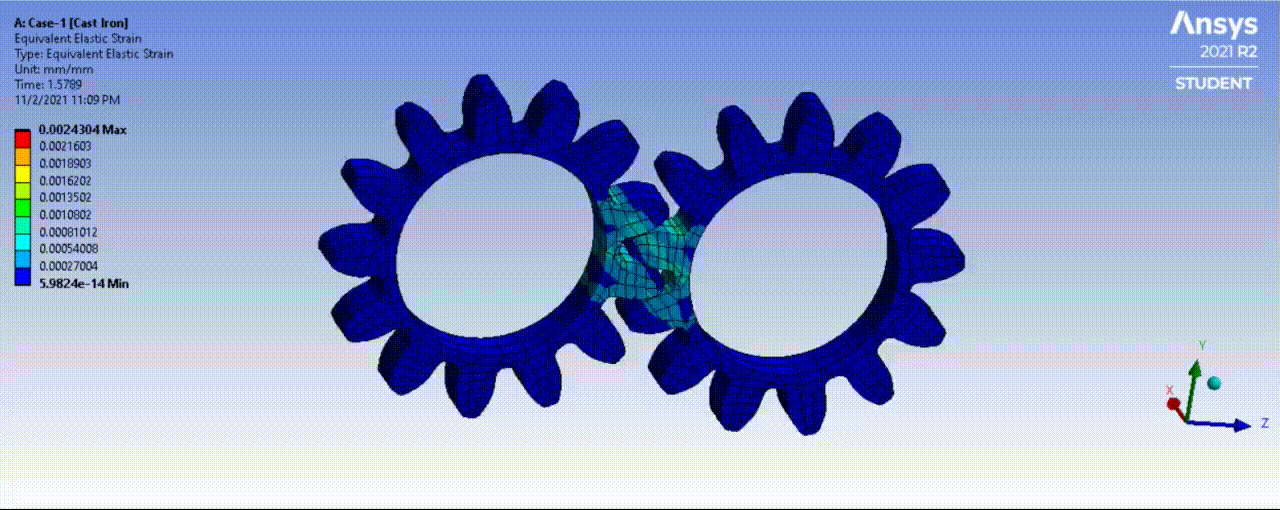
Figure 47-Equivalent Elastic Strain Animation Case 1. |
Equivalent Elastic Strain [Case 2] :
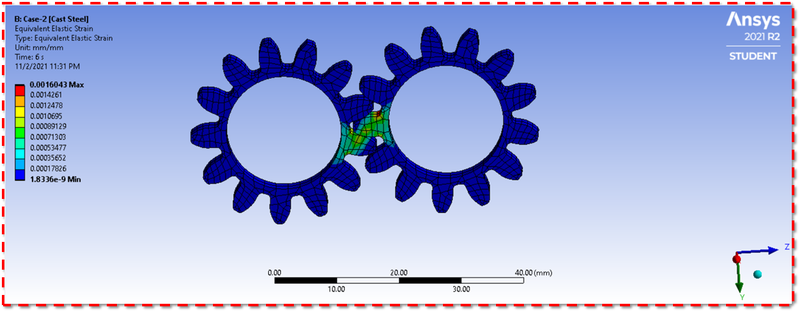
Figure 48-Equivalent Elastic Strain Case 2. |
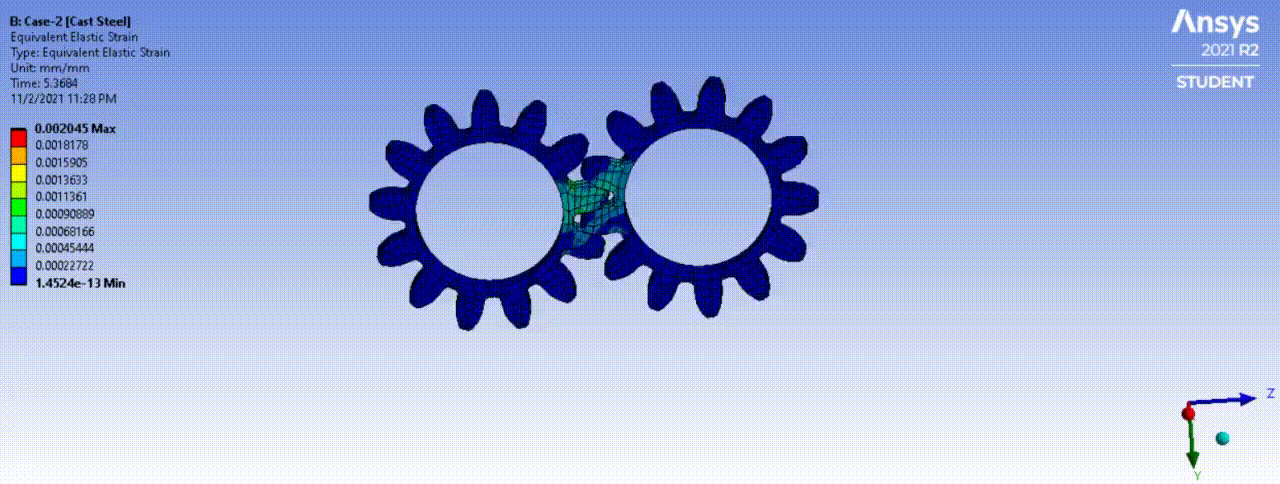
Figure 49-Equivalent Elastic Strain Animation Case 2. |
Equivalent Elastic Strain [Case 3] :
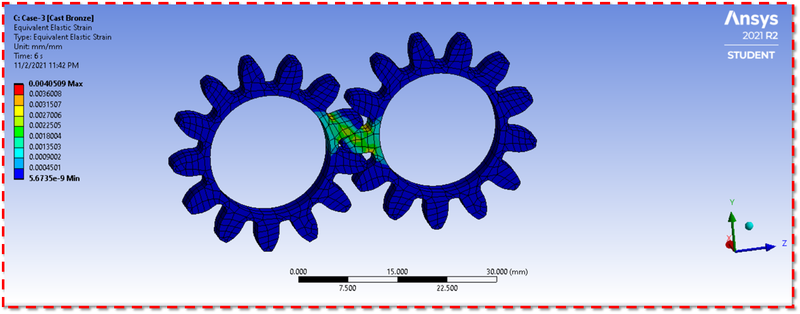
Figure 50-Equivalent Elastic Strain Case 3. |
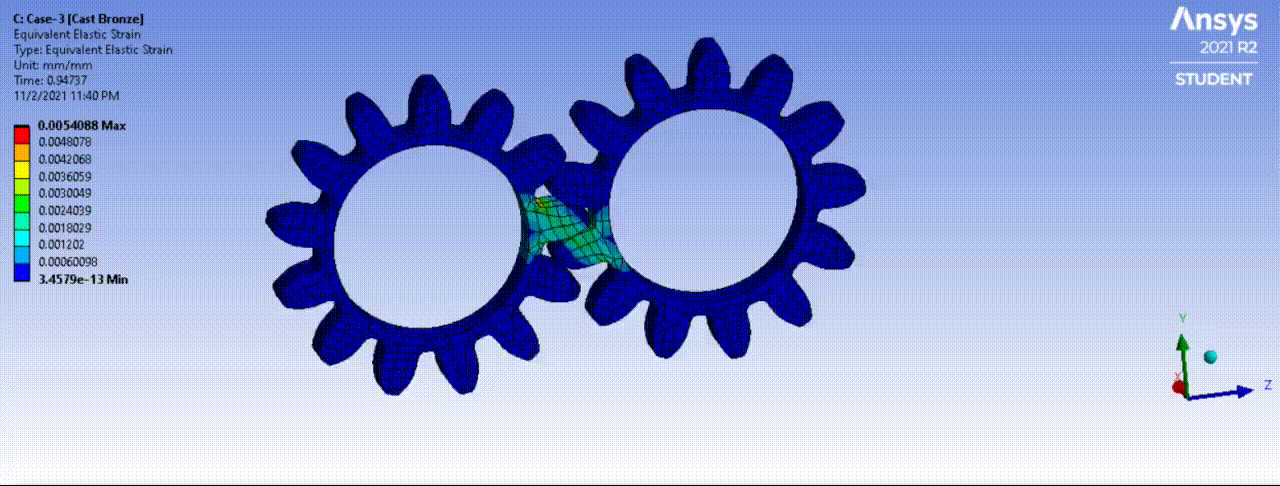
Figure 51-Equivalent Elastic Strain Animation Case 3. |
Total Deformation [Case 1] :
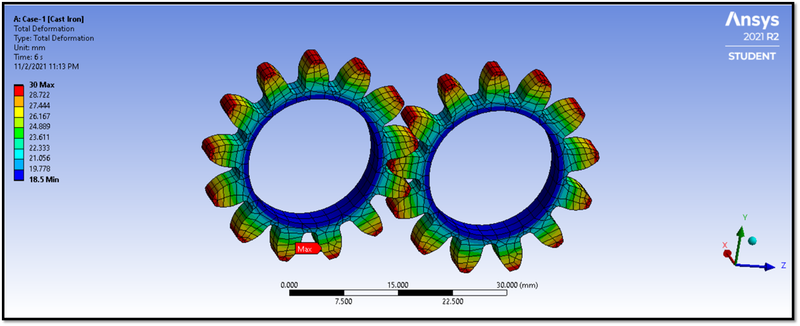
Figure 52-Total Deformation Case 1. |
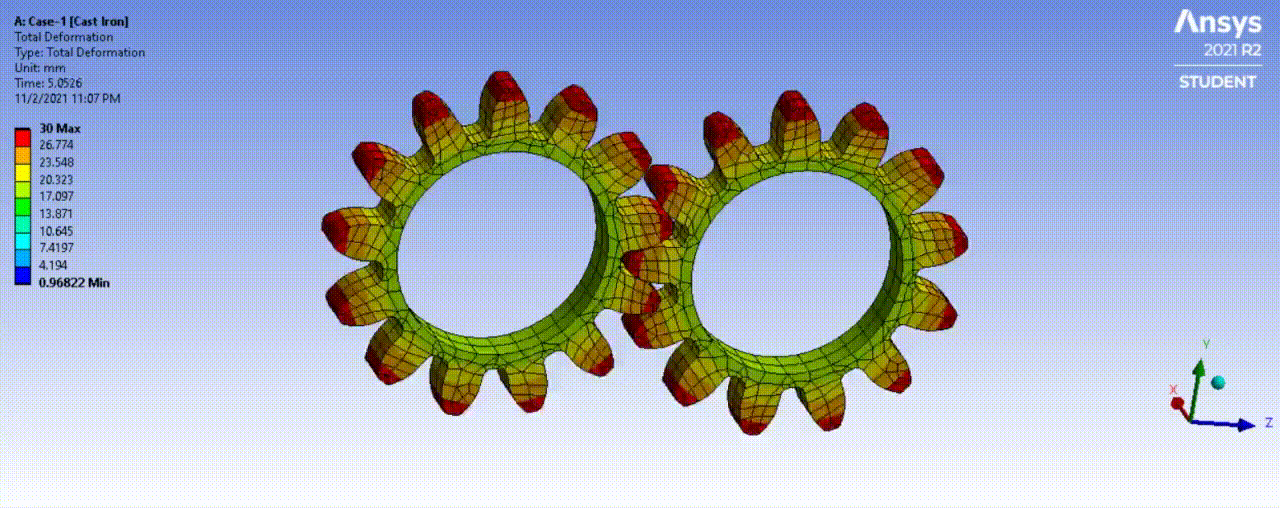
Figure 53-Total Deformation Animation Case 1. |
Total Deformation [Case 2] :
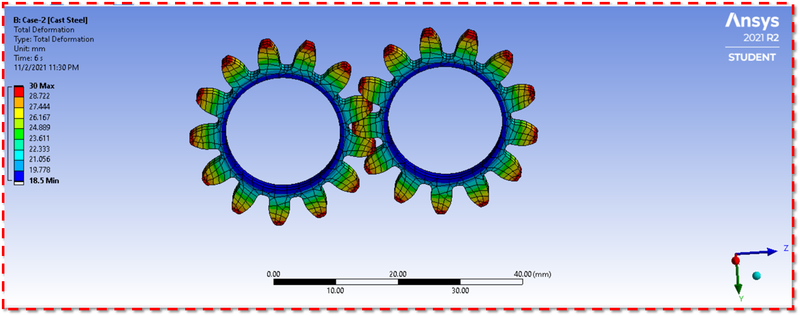
Figure 54-Total Deformation Case 2. |
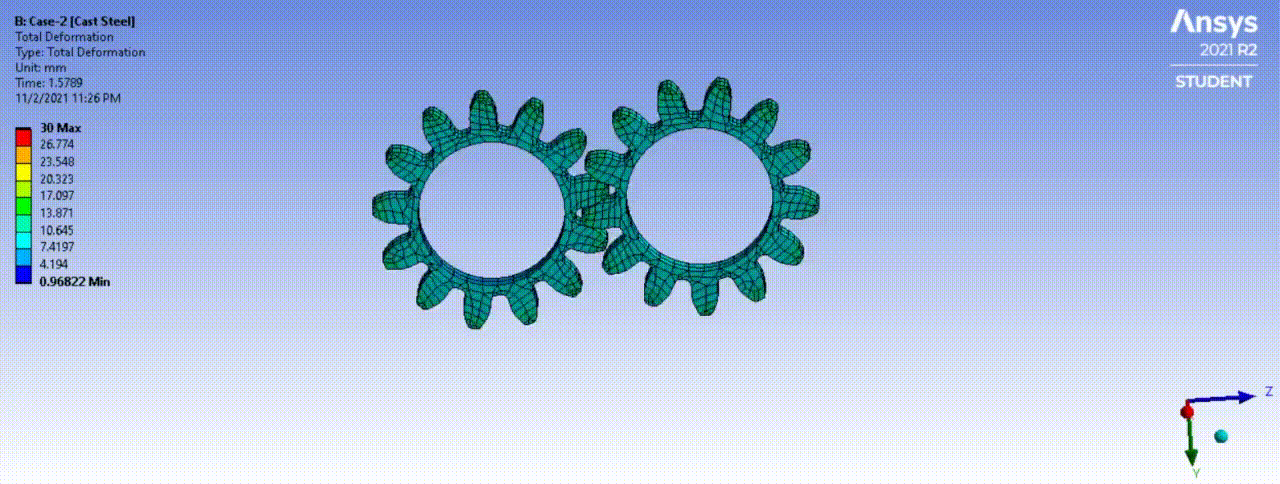
Figure 55-Total Deformation Animation Case 2. |
Total Deformation [Case 3] :
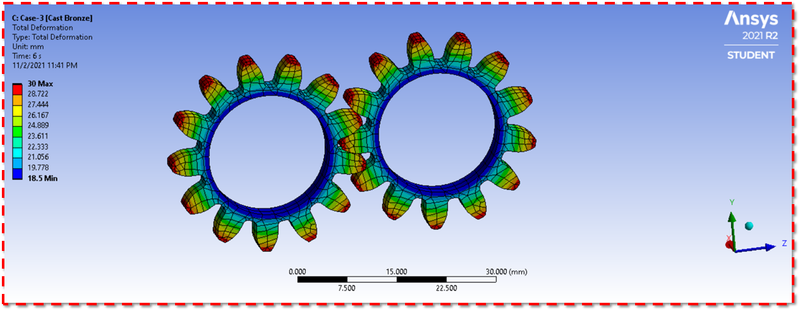
Figure 56-Total Deformation Case 3. |
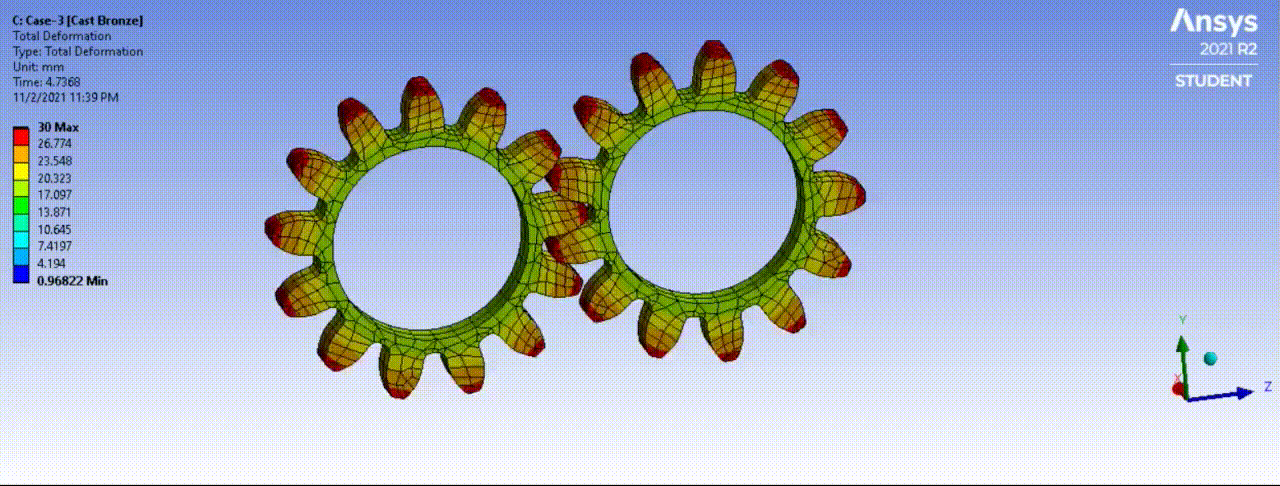
Figure 57-Total Deformation Animation Case 3. |
Stress Intensity [Case -1] :
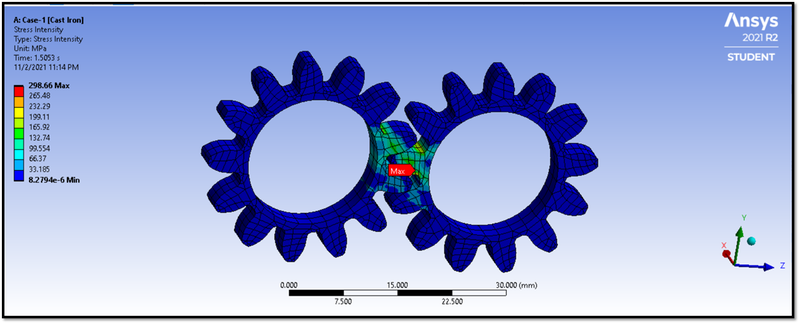
Figure 58-Stress Intensity [Case-1]. |
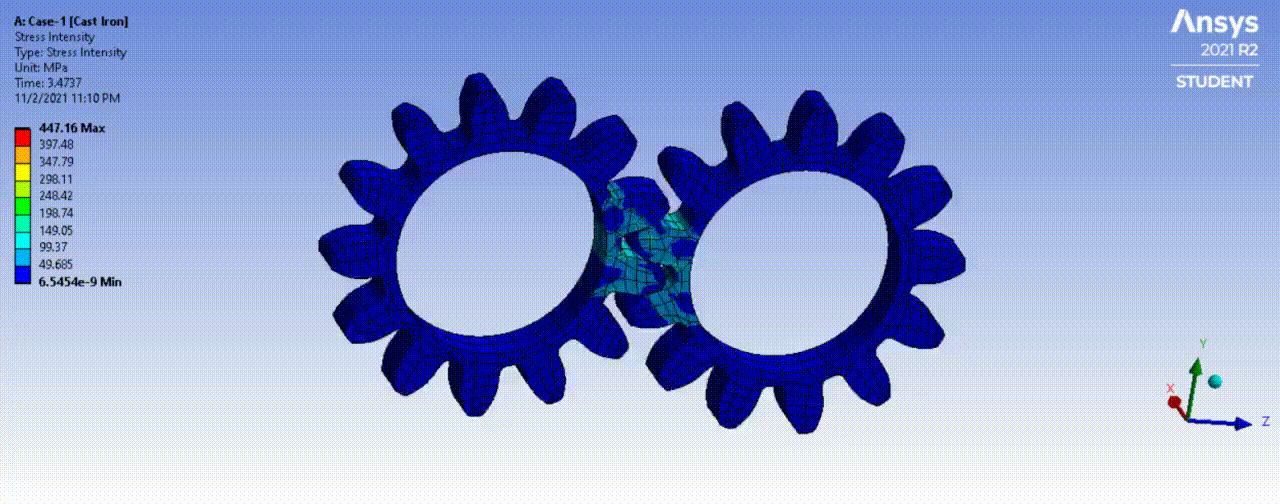
Figure 59-Stress Intensity Animation [Case-1]. |
Stress Intensity [Case-2] :
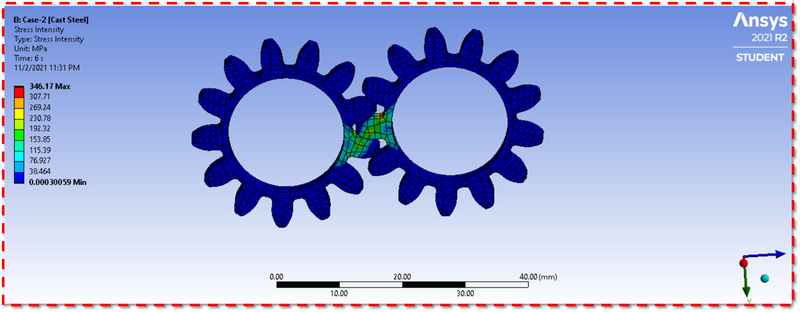
Figure 60-Stress Intensity [Case-2]. |
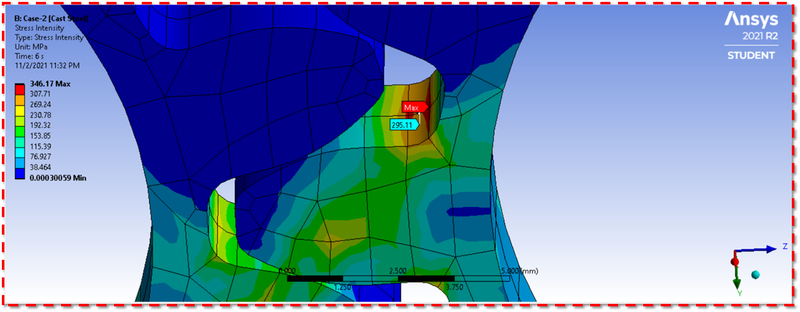
Figure 60:1 -Stress Intensity [Case-2]. |
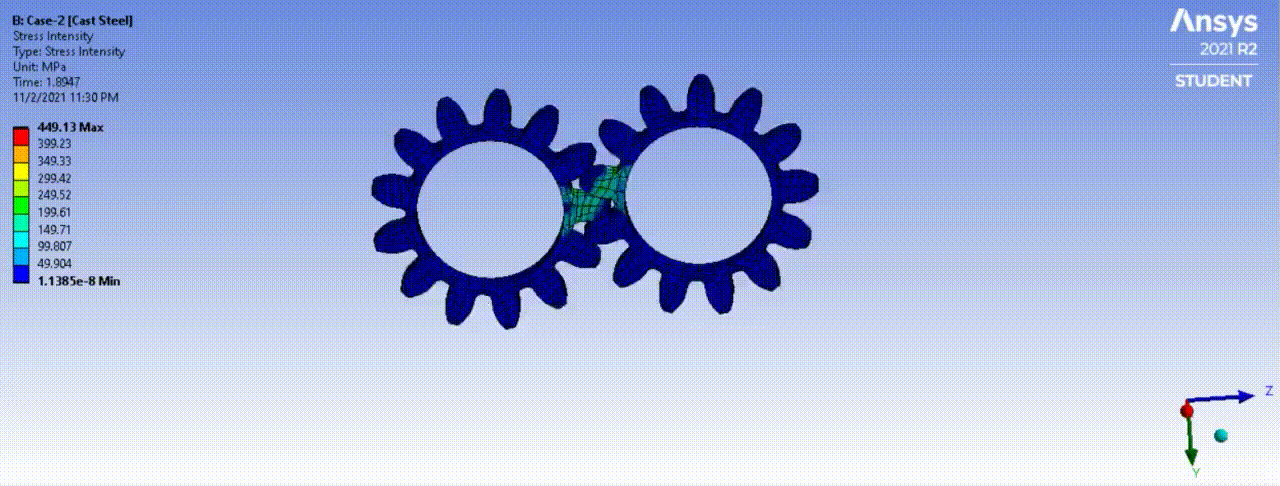
Figure 61-Stress Intensity Animation [Case-2]. |
Stress Intensity [Case-3] :
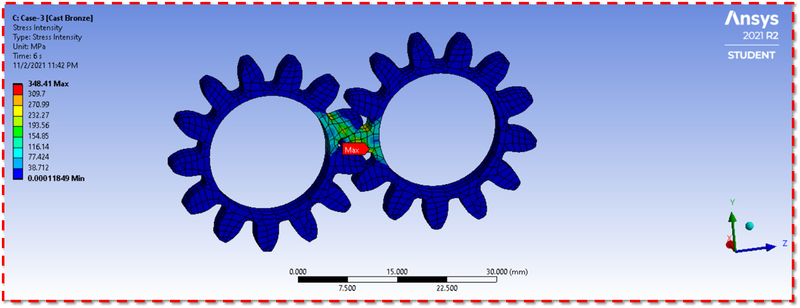
Figure 62-Stress Intensity [Case-3]. |
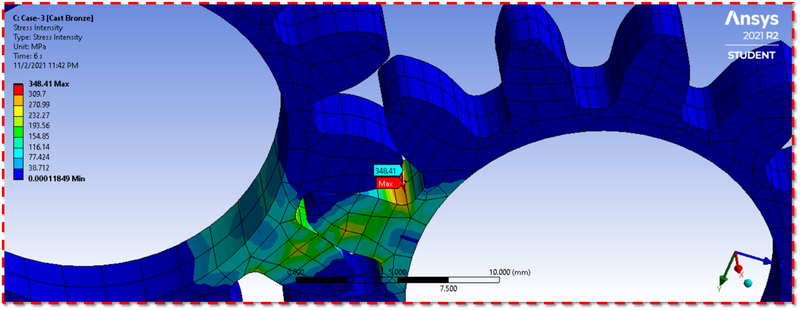
Figure 62:1-Stress Intensity [Case-3]. |
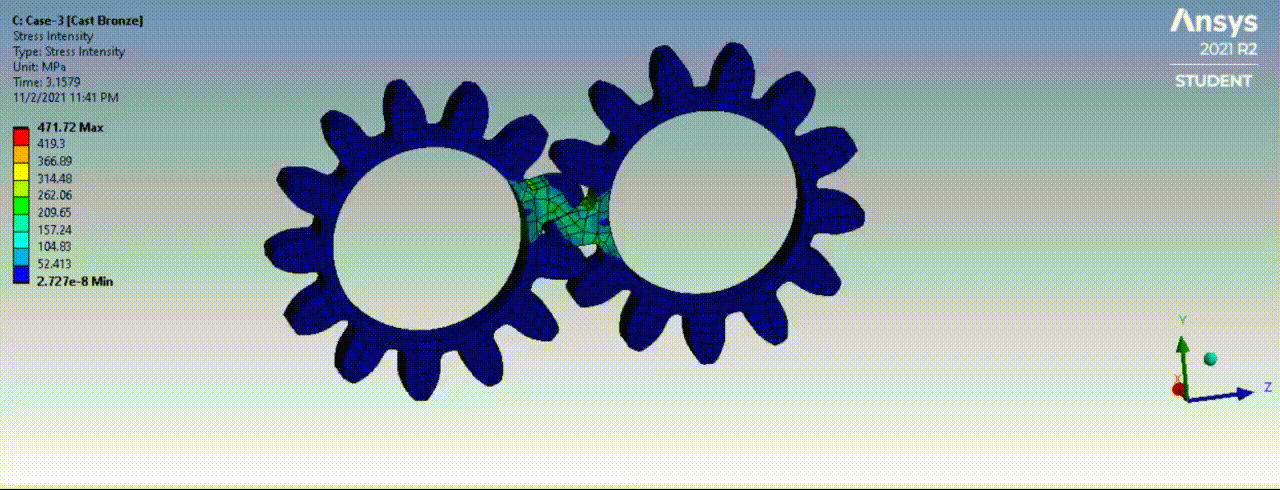
Figure 63-Stress Intensity Animation [Case-3]. |
Force Convergence Graph [Case-1] :
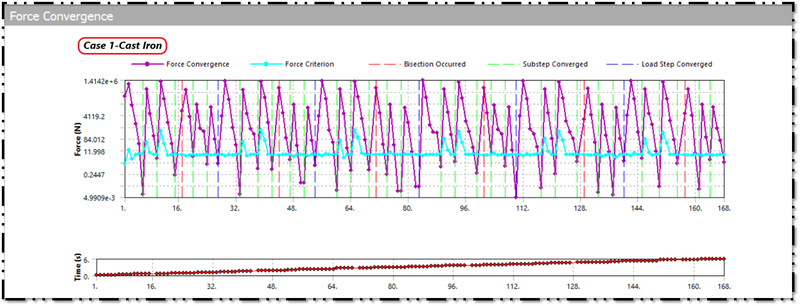
Figure 64-Force Convergence Graph [Case-1]. |
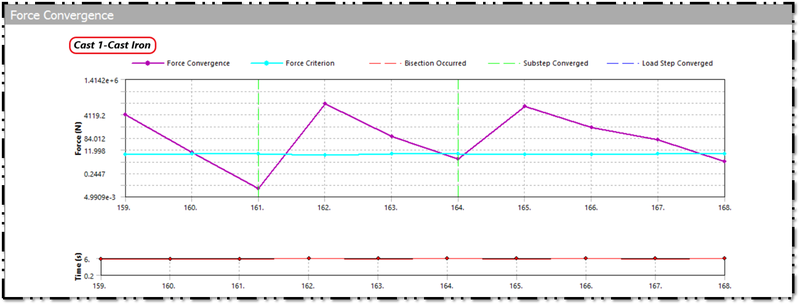
Figure 64:1-Force Convergence Graph [Case-1]. |
Force Convergence Graph [Case-2] :
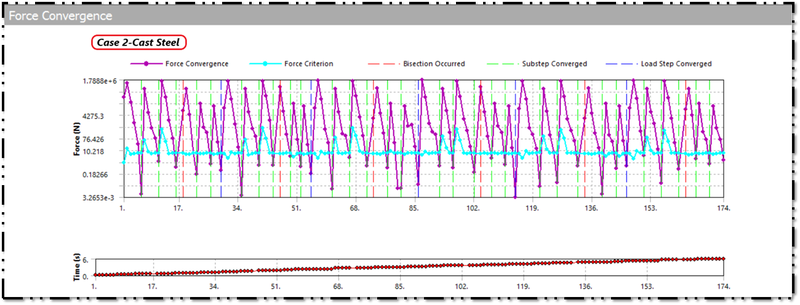
Figure 65-Force Convergence Graph [Case-2]. |
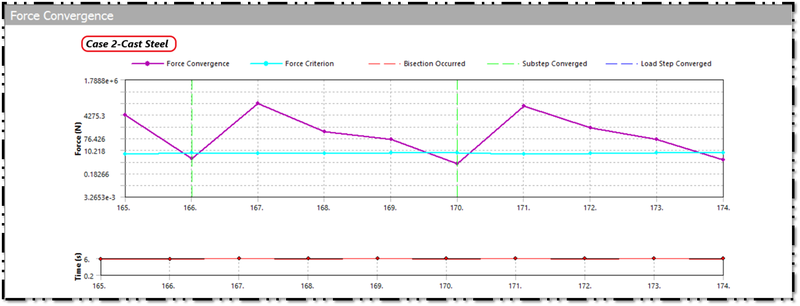
Figure 65:1-Force Convergence Graph [Case-2]. |
Force Convergence Graph [Case-3] :
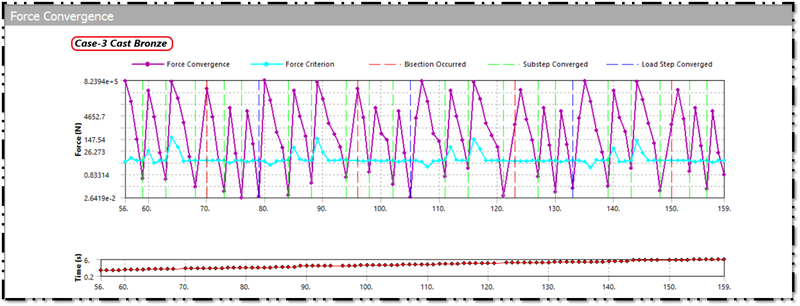
Figure 66-Force Convergence Graph [Case-3]. |
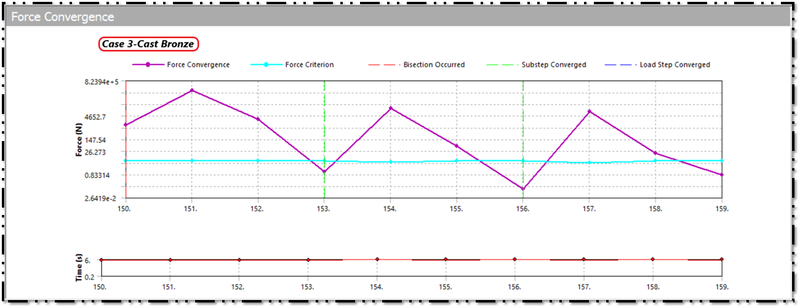
Figure 66:1-Force Convergence Graph [Case-3]. |
Comparison of Results :
Cases
|
Von-Misses Stress (MPa)
|
Total Deformation (mm)
|
Stress Intensity (MPa)
|
Max.
|
Min.
|
Max.
|
Min.
|
Max.
|
Min.
|
Case-1
|
321.21 MPa
|
0.00023763 MPa
|
30 mm
|
18.5 mm
|
298.66 Mpa
|
8.2794e-6 Mpa
|
Case-2
|
322.63 MPa
|
0.00026484 MPa
|
30 mm
|
18.5 mm
|
346.17 Mpa
|
0.00030059 Mpa
|
Case-3
|
320.9 Mpa
|
0.0001035 Mpa
|
30 mm
|
18.5 mm
|
348.41 Mpa
|
0.00011849 Mpa
|
Here while comparing the results,
- The maximum value of Von-Misses Stress is developed in Case-2,The minimum value of Von-Misses Stress is developed in Case-3.
- The maximum and minimum deformation is same for all the three cases.
- The maximum stress intensity is occured in the Case-3 and the minimum stress intensity is occured in Case-1.
- According to the simulation results for the each case,I'm concluding that Cast Bronze is best in the strenght of materials point of view,Cause the maximum stress developed in the Case-3 (Cast Bronze) is very less when compared to the other two cases and materials.
- When you see in the fracture point of view,The Cast Iron is preferrable,Cause the stress intensity is very low when you compared to the other two cases and materials.
- The fracture will be occuring at the teeth,Where the gears tooths will be having contact with each other in the spur gears.
- The preferrable material according to the simulation results is Cast Iron,Cause the Stress Intensity is low when compared to the other two cases and if we use Cast Iron as the material for the gears,It lasts longer life.
[Note: We can't say this case is preferable, this case is not preferable, Anyhow it depends on the application. Here in the report, I have said, Case-1 Cast Iron is preferable from a Fracture point of view and Case-3 is preferable from a Strength of Materials point of view, Cause I have told according to the question and the model given to us, But in real life, It entirely depends on the applications.]
Case-1 [Cast Iron] :
- The factor of Saftey = Yield Strength/Working Stress
- Yield Strength of Structural Steel=548 Mpa
- Working Stress [Maximum Stress]=321.21 Mpa
- FOS=548321.21
- FOS=1.706 [Cast Iron].
- Here the FOS what we got is 1.706,It is somewhat ok,The material will not fail,If we use cast iron as material for spur gear.The Standard FOS ranges from 1-5 in industries.
Case-2 [Cast Steel] :
- The factor of Saftey = Yield Strength/Working Stress
- Yield Strength of Structural Steel=349 Mpa
- Working Stress [Maximum Stress]=322.63 Mpa
- FOS=349322.63
- FOS=1.08 [Cast Steel].
- Here the FOS what we got is 1.08,It is also somewhat ok,The material will not fail,If we use cast steel as material for spur gear.The Standard FOS ranges from 1-5 in industries.
Case-3 [Cast Bronze] :
- The factor of Saftey = Yield Strength/Working Stress
- Yield Strength of Structural Steel=144 Mpa
- Working Stress [Maximum Stress]=320.9 Mpa
- FOS=144320.9
- FOS with Yield Strength=0.448 [Cast Bronze]
- Here the FOS what we got is 0.44,It is not ok,The material will fail,If we use cast broze as material for the spur gear.The Standard FOS ranges from 1-5 in industries.But here the factor of saftey is very low,It is less than 1.The Cast Bronze is not preferred material for spur gear.
- So lets calculate FOS with ultimate yield strength.
- FOS=267320.9
- FOS with Ultimate Strength=0.83 [Cast Bronze].
- So here also the factor of saftey is less than 1,So the cast broze material is not preferred.
- We will be checking FOS with yield strength to check whether the plastic deformation occurs in the material,If the FOS saftey value is less than 1,the material will fail.
- We will be checking FOS with ultimate strength to check whether the fracture occurs in the material,If the FOS saftey value is less than 1,the material will fail.
- We will be only considering plastic deformation in the static structural analysis.
Result :
- Hence the material has been defined for all the three cases.
- Hence the model has been meshed with the element size 2mm.
- Hence the model has been solved for Von-Misses Stress, Equivalent Elastic Strain,Stress Intensity,Contact Tool and Total Deformation by applying appropriate boundary conditions.
- Hence the maximum value of Von-Misses Stress is developed in Case-2 [Cast Steel].
- Hence the maximum deformation has occurred in all the three cases.
- From the Strength of Materials Point of View, [Case-3] is preferred because maximum stress is low when compard to the other two cases.
- From the Fracture Point of View, [Case-1] is preferred because the stress intensity is low when compared to the other two cases. Anyhow keep in mind, it depends on the applications.
Conclusion and Learning Outcome :
In this Week 1 Spur Gear Challenge, I came to know about
- Learned about stress intensity.
- Learned how and where the stress intensity is occurring.
- Learned how to create manual material cards.
- Learned how to apply boundary conditions to the model.
- Learned how to request outputs and solve the