Interfaces & Study of Effect of Notches Challenge - Crashworthiness using RADIOSS
Assignment-5
Aim:
- Create the mesh for bumper assembly, mesh size should be 6mm.
- Run the Crash tube model with 6 different cases as given below and compare.
Objective:
- Run the crash tube model as it is.
- Change the Inacti=6 and run.
- Create the type 11 contact and run.
- Remove both notches and remove boundary condition on rigid body node then run.
- Create a new notch in the middle, select the whole section and run.
- Create a new notch with nodes only from opposing 2 faces and run.
Procedure:
Meshing and Connecting Bumper:
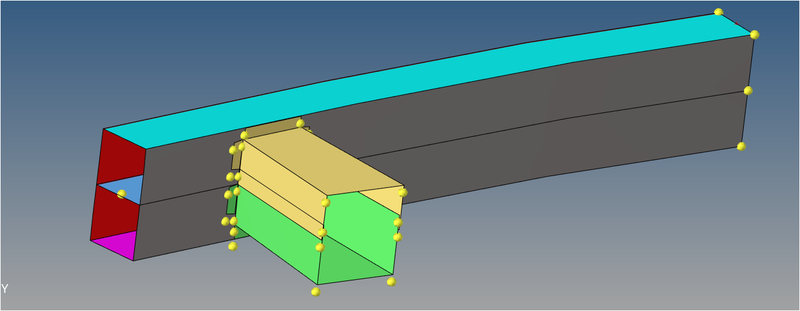
Imported Model
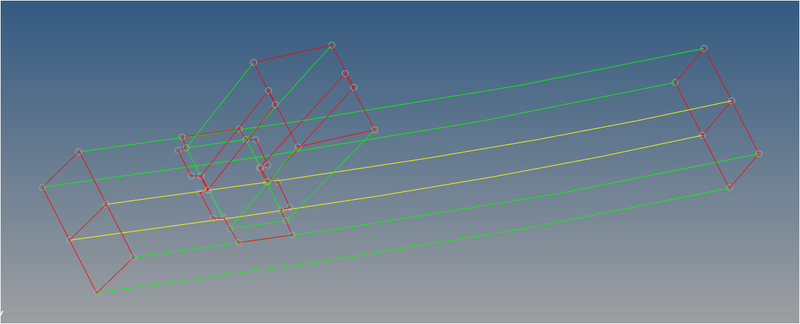
Geometry Clean-up is Done
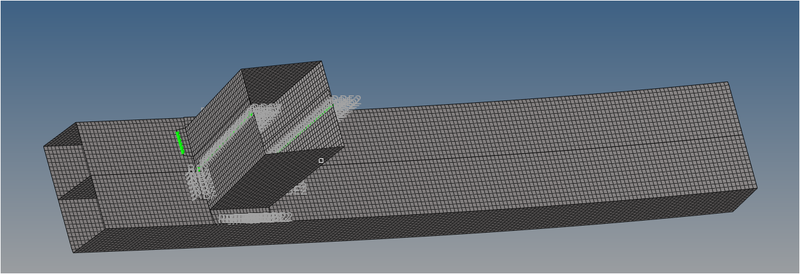
Meshing and connections are done
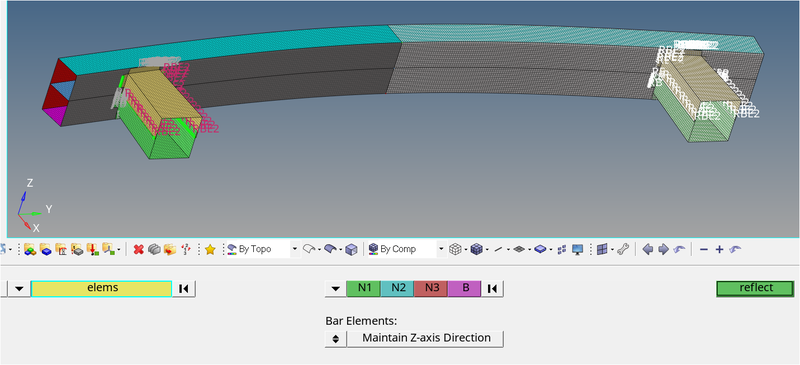
Reflecting the geometry to make a complete bumper
CASE 1: Run the crash tube model as it is
- In this case, we need to run the simulation on the crush tube as is. we will be discussing the Type 7 interface when inacti is set to 0 (Default).
- From the animation, we can clearly see that the deformation taking place at the middle notch first due to applied velocity
- Once mid notch deforms the next deformation occurs in the second notch which is near to rigid wall this is because the thickness is less at bottom
- Here notch elements deforming inside and the rest flat elements are coming outside. This region does not require more force to deform the elements
- It is evident that the presence of notch leads to stress concentration in those regions. So, the buckling occurs first. This will happen in all the cases which have notches.
- As we can see, the energy error is -3.8%. It is acceptable since it is below -15%. In addition to that, there is no mass error (0%)
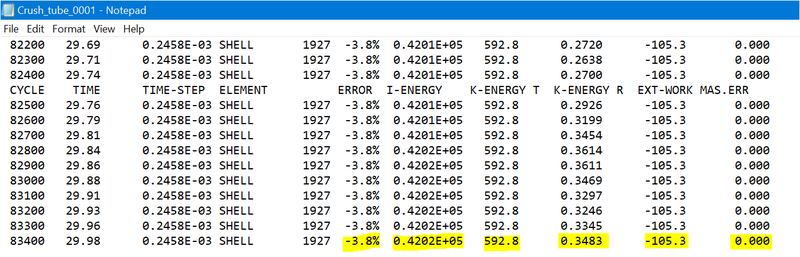
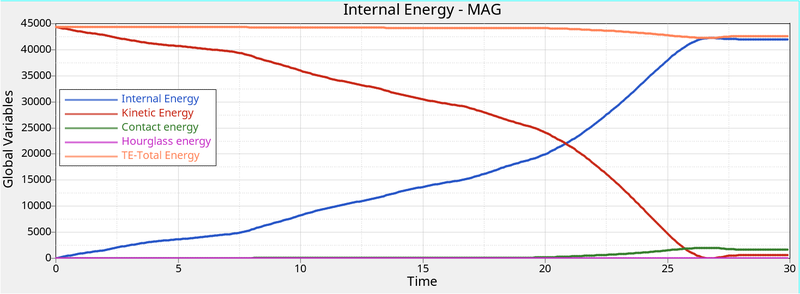
- Internal energy keeps increasing because the tube continuously absorbs energy while crashing onto the rigid wall, which results in deformation. You can see at last when the deformation completes, the internal energy goes constant.
- Kinetic energy keeps decreasing due to the initial velocity on the tube. The curve starts from high values and decreasing to low due to the deformation. There is a slight increase afterward due to rebound after deformation.
- Contact energy is a type of energy that is created when one element contacts neighboring elements. The opposing force created by the element is called contact energy. There is no contact in the initial stage, so that’s why the graph goes constant. After some time, the graphs slightly increase due to the buckling of elements. While the entire tube pressing on the rigid wall, the buckled elements are forced into contact.
- Total energy decreases at some point due to increasing of contact energy at the same time. so, the contact energy affects the total energy.
- Hourglass energy is constant due to the presence of recommended properties.
- Now next step is to plot the rigid wall resultant force graph for case 1 simulation, so select variable as rigid wall and parameter as resultant force and apply to plot the graph.
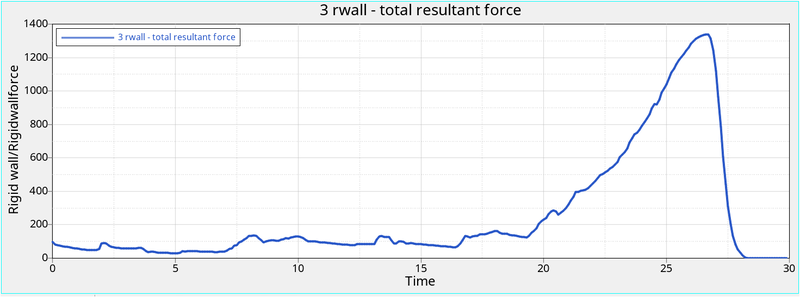
- It is evident that the rigid wall experiences some forces suddenly, due to the crush tube crash over the rigid wall and absorb the energy from crush tube. after the deformation completes, the rigid wall force is decreased immediately due to the energy transferred completely.
Self-Contact Force
- The self-contact force from the TH inter card helps identify the forces due to the Type 7 contact formulation.
- The max self-contact force is 133.18N, which occurs at the end of the simulation, this is the point where a maximum number of master and slave segments are in contact with each other.
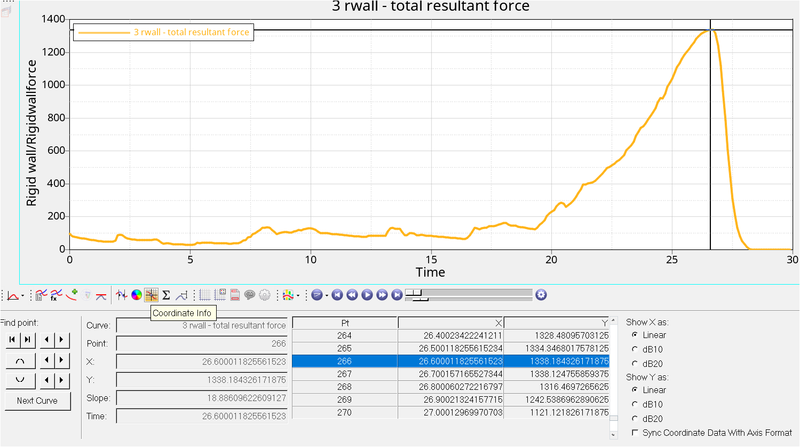
CASE 2: Change the Inacti=6 and run
- In this case, we shall be using Hyper Crash. We can import the given crush tube model using file > Import or we can directly drag .rad file into hyper crash to open.
- After importing, we can go ahead and switch to the model browser tab. After that, we can move on to contact interface > self-contact and then right-click >> self-contact and select the option see in the panel as shown below.
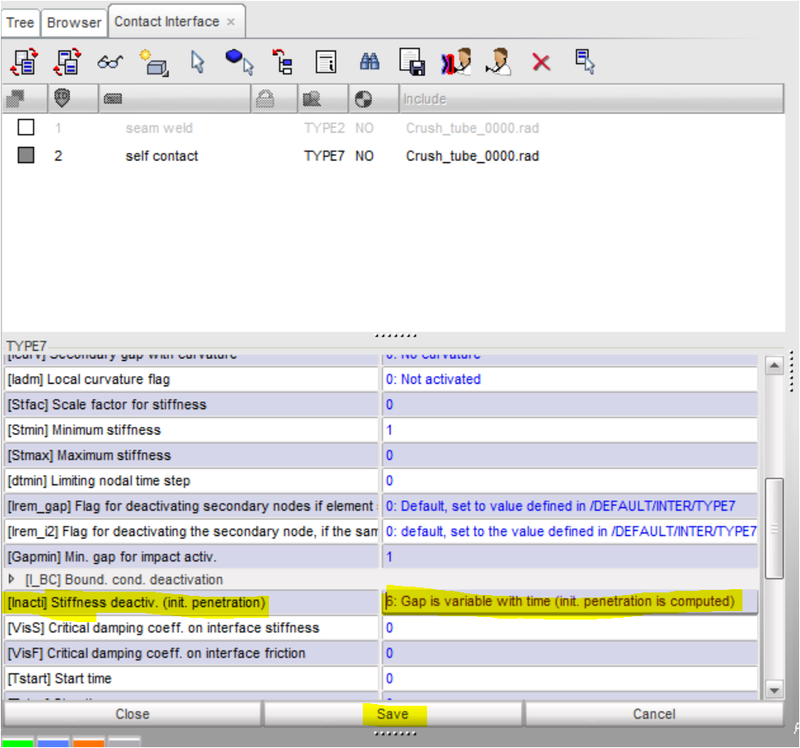
Editing Inacti in Hypercrash
- After that, we can export the model from hyper crash with an appropriate file name and then we can run the analysis on that saved file in Hypermesh. We can also edit the inacti = 6 value in hypermesh directly.
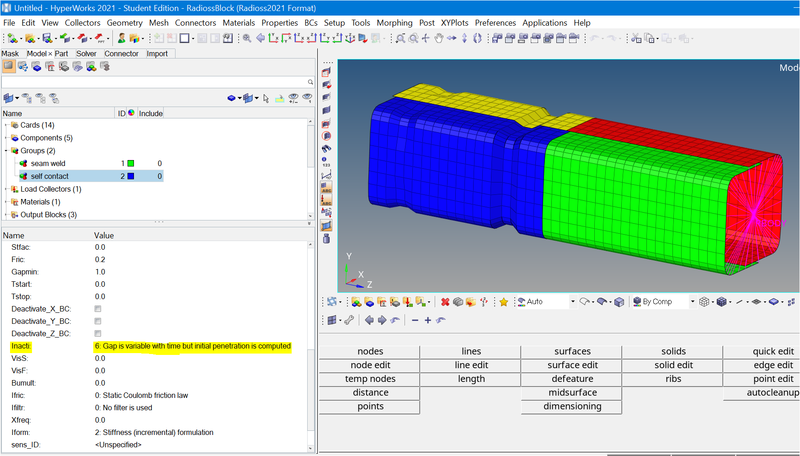
Editing Inacti in Hypermesh
- After analysis, switching to Hyperview, the animation is as follows:
- There isn't any discernible difference between case 1 and case 2 animations, they're both very similar. Even though the Inacti parameter was changed, it didn’t have any effect on the simulation as there was no initial penetration to manage in the first place.
- Next, we can look at the output file which is shown below:
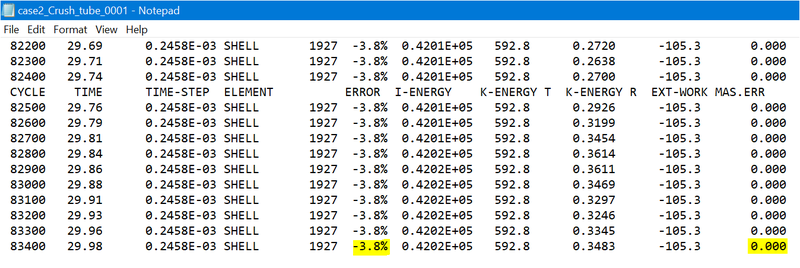
- As we can see, the values are the same as in case 1. The energy error is the same -3.8% (also the same mass error of 0%). Moving on to the plots:

- There isn't much difference in the graphs, they are exact copies as that of case 1. The only thing we have learned from the energy plot is that there is no initial penetration since there is no difference between case 1 and case 2 energy plots (since the simulation was tweaked to detect such penetrations through the inacti function). If any initial penetrations existed, internal energy would start from a non-zero value.
- RWall forces also exhibit the same characteristics as of case 1 as shown below
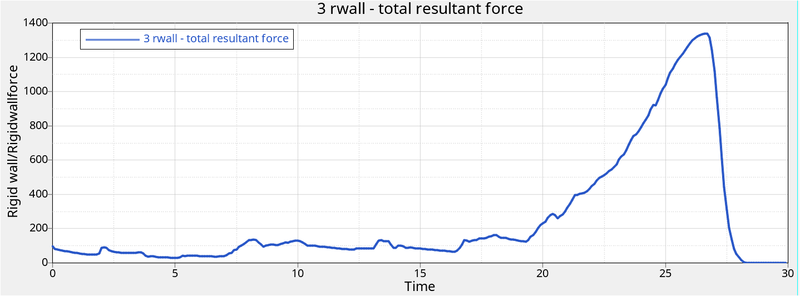
- The forces being plotted in the Rigid Wall Forces plot are the Usual Forces applied to the crash tube by the Rigid Wall. So as the contact energy increases, the Rigid Wall forces will also increase, and we can see that the Rigid Wall Forces also decrease at the point where the Contact energy flat and finally when the specimen loses contact with the Rigid Wall, the Rigid Wall Forces become Zero
SELF CONTACT FORCE
- The self-contact force from the TH inter card helps identify the forces due to the Type 7 contact formulation
- The max self-contact force is 1338.18N, which occurs at the end of the simulation, this is the point where maximum number of master and slave segments are in contact with each other.
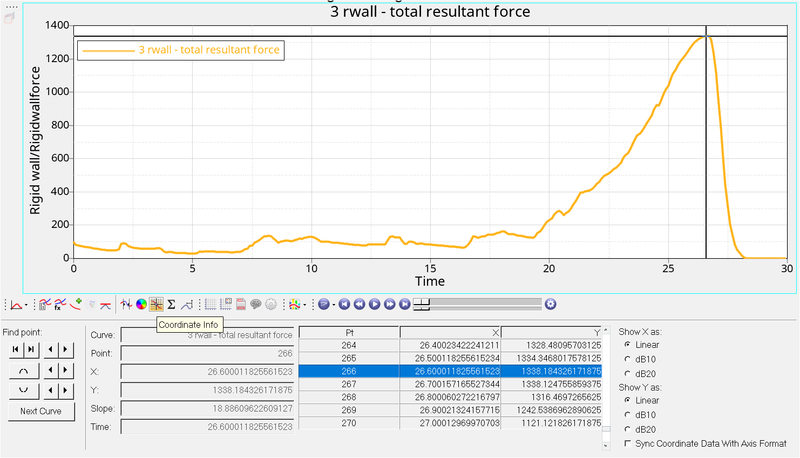
CASE 3: Create the type 11 contact and run
- In this case, we need to input type 11 interface to the case 2 solver deck file. After importing it in Hypermesh, Right-clicking the section, we can select Create >> Contact. After that, we can define this newly created contact and assign it the following values as shown below
- For both Line_id (S & M) attributes, all the components of the model will be selected. The other values are recommended settings for Type 11.
- Then, as usual, the file can be processed using the radioss solver. The remaining steps are followed as given.
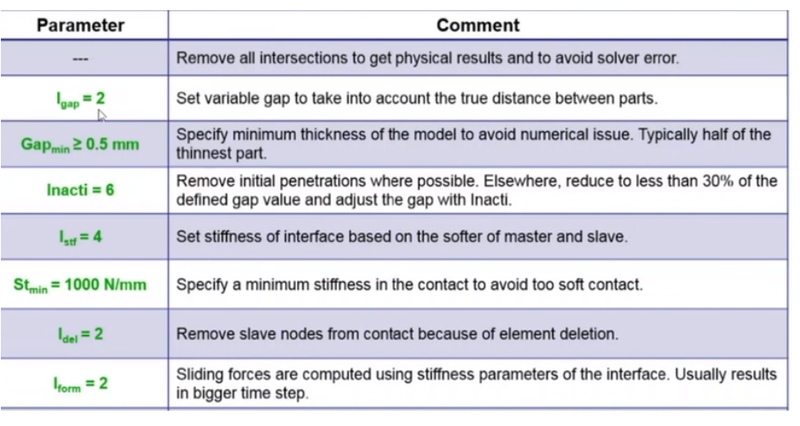
Recommended values
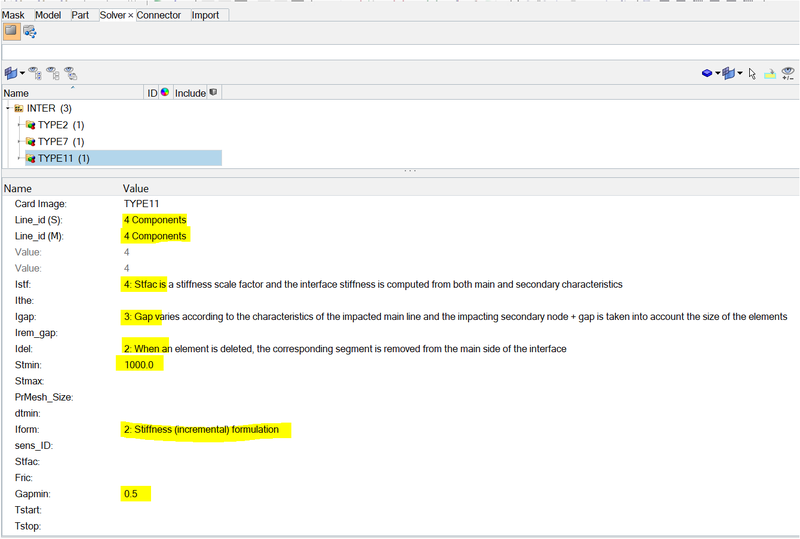
Recommended values assigned in TYPE 11 Interface
- Now, run the analysis and open it in hyperview
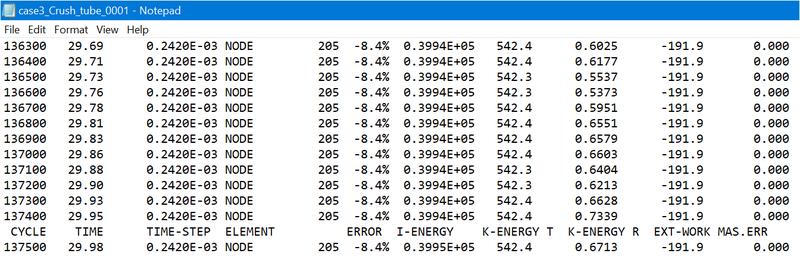
- Energy error is still within the -15% limit at -4%. Mass error is non-existent.
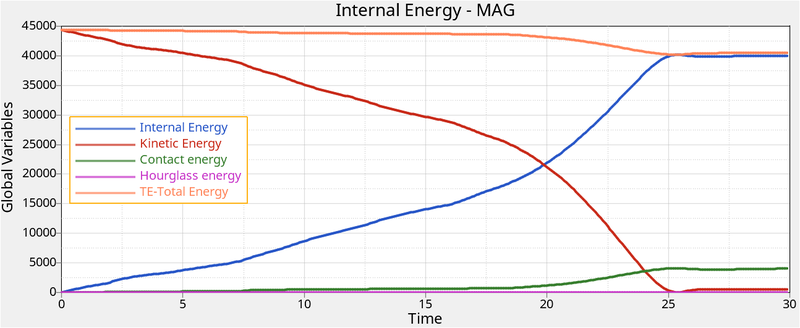
- The internal energy, which is representative of the energy absorbed, increases with time, as the tube contacts the rigid wall. We can observe a small peak and a drop off at around 26 seconds, which is the time when the tube is completely crushed and no more energy can be absorbed by the system.
- The hourglass energy is zero since the QEPH 24 element formulation has integrated hourglass control.
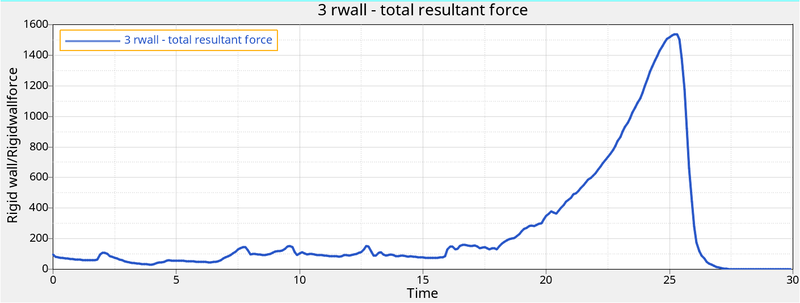
- Here, the deformation characteristics are like what was observed in previous cases. There is no discernible difference between the energy and rigid wall plots of this case and previous cases. Therefore, we can conclude that there was no edge-to-edge penetration in this model.
Case 4: Remove both notches and remove boundary condition on rigid body node then run.
- Import the 0000.rad file. Then remove the notch in the model using Align option. select reference nodes as 1st node and 2nd node. after that select the nodes that need to be aligned. now select align
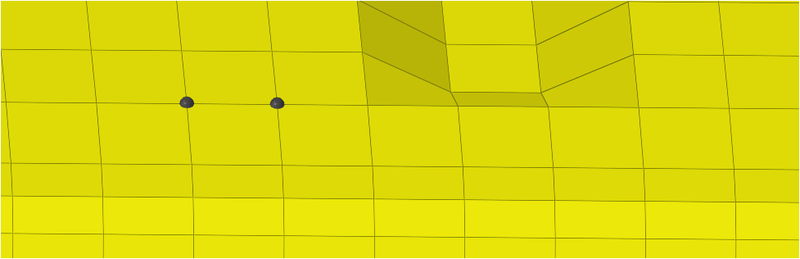
Removing notches using Align Option
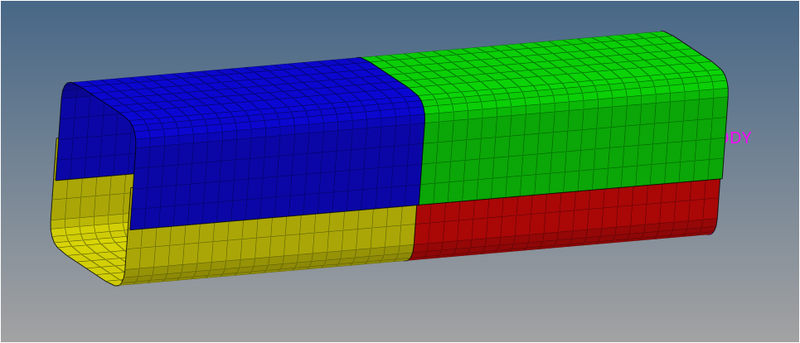
All the notches are removed successfully
- There is no notch present in the model, the buckling started at the contact takes place in rigid wall and tube. In previous cases, buckling started at notch areas.
- Here we can switch to hypergraph 2D panel for plotting graph via client selector. In this panel, we need to load T01 file in file directory. Now select variable as Internal Energy, Kinetic Energy, total energy, contact energy, hourglass energy and select parameter as MAG and apply for plotting the graph.
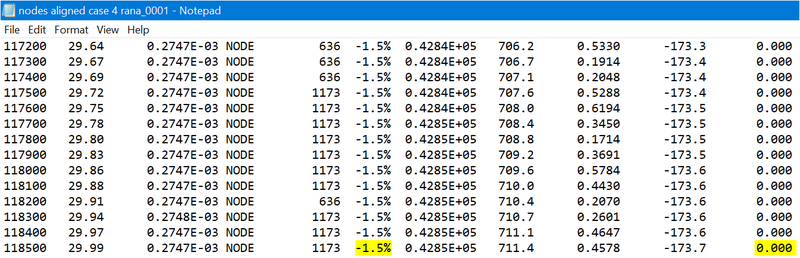
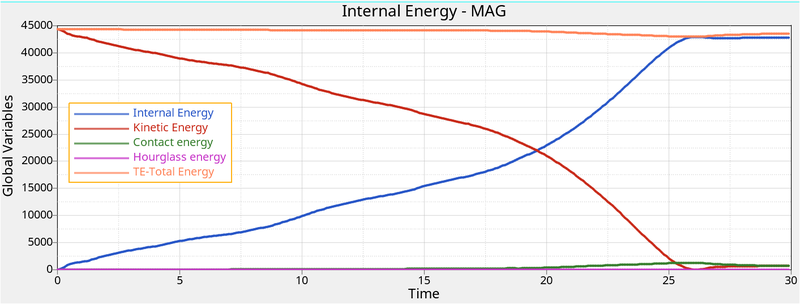
- Internal energy keeps increasing at some point due to the buckling of the tube. the more energy absorbed by the tube when deformation takes place. that's why the internal increases after some point.
- Kinetic energy decreases from maximum due to internal energy increases.
- Compared to previous cases, Contact energy slightly decreased after some point due to the absence of notches.
- Total energy also slightly decreased after some point due to contact energy. Hourglass energy is constant due to the presence of recommended properties.
- Next is to plot rigid wall resultant force graph for case 4 simulation, so select variable as rigid wall and parameter as resultant force and apply to plot the graph.
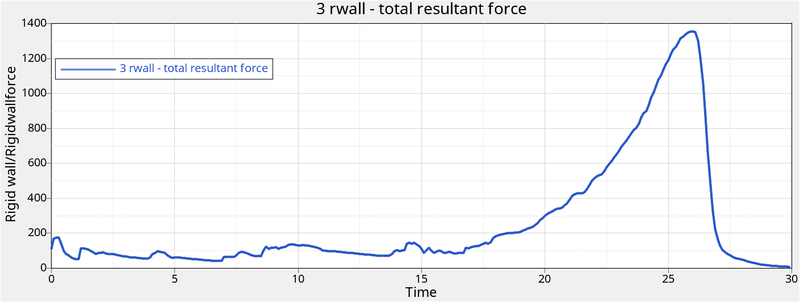
- In this case, the RWALL force graph peaks after some point due to a large amount of force is transferred to the rigid wall during the collision of the crush tube. After the deformation was completed, the graph decreased suddenly. and got a constant value after the deformation. The total resultant force peaks at 1350N.
CASE 5: Create a new notch in the middle, select the whole section and run
- For this case, we shall be using the starter file of case 4. So, there are no notches or boundary conditions. But the case requires us to create a notch through the middle section of the crush tube. For this, I have used the translate tool in Hypermesh. Go to tools > translate.
- We can either select elements or nodes to translate. After assigning the direction of translation (using an axis or a vector), we then need to assign a magnitude. Depending on the global axis, we then must either click 'translate+' or 'translate-'. This creates the depression
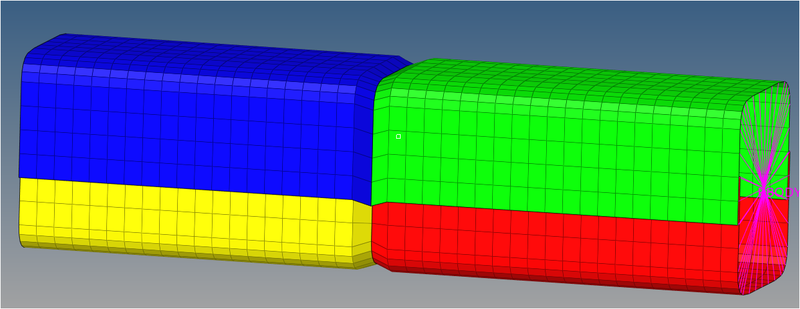
Notch Created in the middle
- Just as in the first 3 cases, the notch is the region where the tube undergoes deformation first. Then the region closer to the rigid wall is deformed next, which would be the lower half of the tube. Around the 8-12ms mark, when the lower half is mostly deformed, the upper half undergoes proper, visible deformation very rapidly until the entire tube is crushed completely.
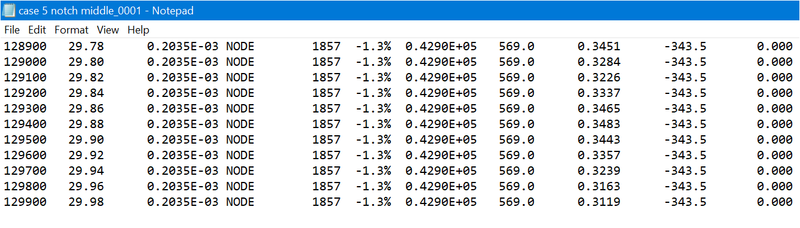
- Energy error is still within the -15% limit at -4%. Mass error is non-existent
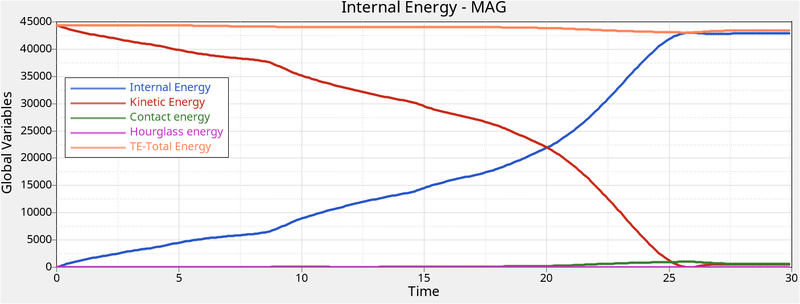
- As we have seen in previous cases, Internal energy keeps increasing due to the deformation that takes place. Kinetic energy also decreases due to increase in internal energy. while contact energy slightly changed in early and also noticeable. it because the depth of the notch increased from previous cases. Total energy also increases earlier due to increasing in contact energy. Hourglass energy is constant due to the presence of recommended properties.
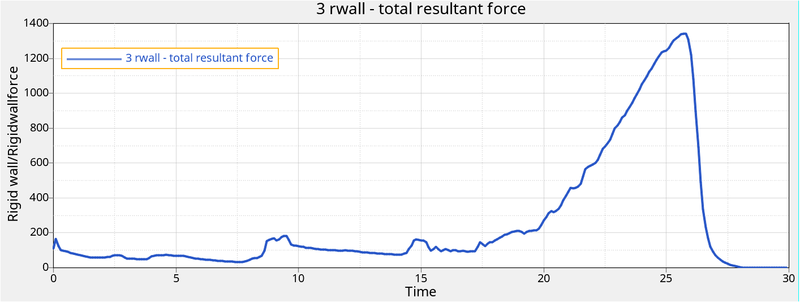
- There is no noticeable difference between case 4 and case 5. it’s almost similar. After some point, RWALL force peaks at some value due to the absorption of energy created during collision and when the tube crushed completely, the value decreased and got constant.
- Contact Energy is the energy acting opposite to the system to prevent the penetration acting on the system. When the force is applied to the body, the crush tube starts to deform but the penetration happening is low in the initial stage. The contact energy will be low.
- Once the deformation is maximum, the elements will be forced to penetrate but the opposite force which is contact energy will also increase which helps in the prevention of penetration. Once the deformation ends, the contact energy will become zero again.
- In this case, the contact energy incurred is more when compared to case 1 and case 2. This is due to only one notch at the center which increases the rate of deformation, which intern increases the rate of penetration.
- The obtained graph for internal energy. There will be a change in the internal energy. Because, as there is a notch only at the middle. The elements will be impacted without any deviation, as of in the previous cases in which the notch is present at the beginning. There will be a drop in the internal energy at the middle. Due to the model moves back after hitting the rigid wall. And there will be a rise again. But in this case the notch will prevents the model to rise back again.
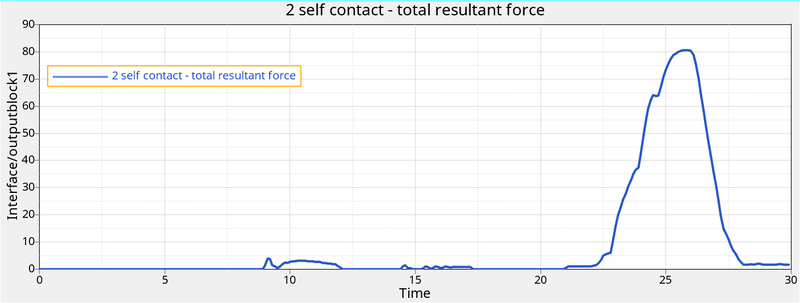
- The below type 11 graph depicts the edge-to-edge contact. The fluctuations start from the beginning because of the notch and the edges of the elements come into contact gradually from the beginning and continue to reach their peak value. After the entire collision, it will decrease to some extent.
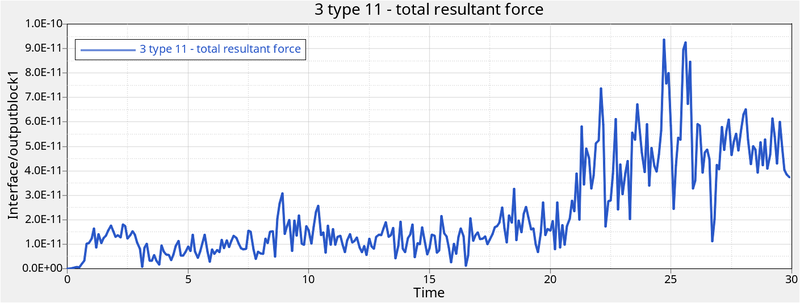
Case 6: Create a new notch with nodes only from opposing 2 faces and run.
- Import the 0000.rad file in case 4 directory by selecting import >> solver deck.
- Use translate option as in the earlier cases to create notches on the opposite faces
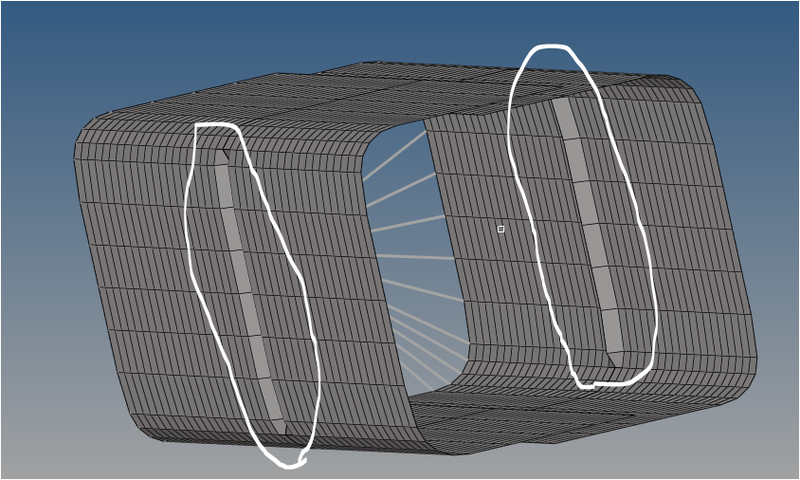
Notches Created on opposite faces
- After that run the simulation by following the procedure of previous cases.
- Now open the 0000.out file in file directory to check the energy errors, no. of. cycles and elapsed time in the simulation file.
- As We can see the energy error is -1.1% and it is acceptable since it is below -15%. there is no mass error (0%).
- Now run the animation by selecting HyperView in client selector. After that load the .h3d file.
- To run the animation, the contour panel should be selected. after that select parameters such as result type as von mises, selection as components, averaging method as simple and then select apply to run the animation.
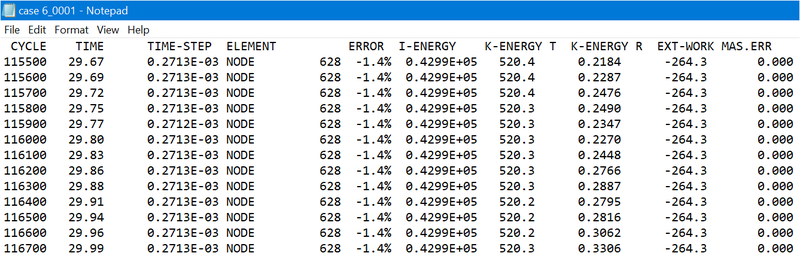
- Like the previous case, buckling occurs at first in the region where the notch is present, after that lower part of the tube is deformed. Finally, the upper part deformed completely after some point.
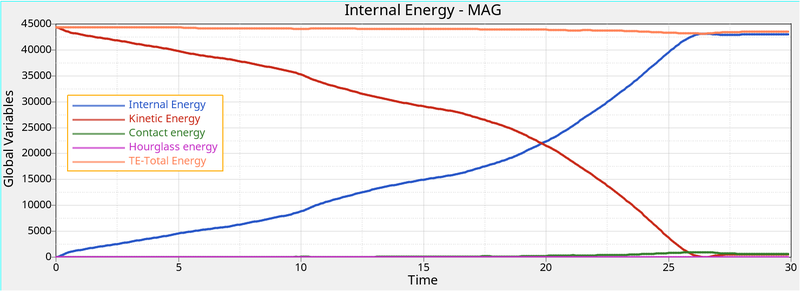
- Like in previous cases, the internal energy increases due to the deformation occur. kinetic energy decreases from high value due to increase in internal energy. The contact energy also noticeably increases due to the depth of the notch. Total energy increases due to contact energy increases after some point. Hourglass energy is constant due to the presence of recommended properties.
- Next is to plot rigid wall resultant force graph for case 6 simulation, so select variable as rigid wall and parameter as resultant force and apply to plot the graph.
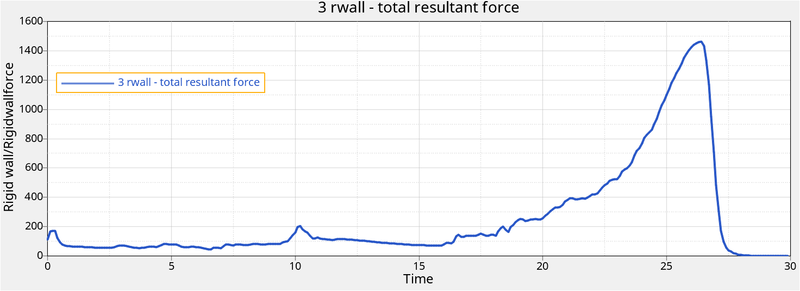
- Again, the plotted RWALL graph is similar like previous case. In this case, the peak value is slightly decreased due to the presence of notch only in opposing faces. After buckling process, the peak value drops to lesser and got constant after the tube crushed completely
Conclusion:
From all the cases we can say that criteria "Inacti" is required to be defined as it removes any initial intersections in the model if they exist. It helps to obtain a more accurate result and also reduces the no. of cycles & time taken to solve. The type 11 contact is given between 2 edges and requires lesser parameters to be defined and also takes comparatively lesser time to be solved than a type 7 contact. Notches are an important part of the model which helps in directing deformation when a load is applied. They help in making the component absorb maximum energy when a load is applied.