The meshing of Car Side Door [Inner Panel]
Aim -
- To perform preprocessing on the given car side door [Inner Panel] plastic component using hypermesh preprocessing software.
Objective -
- To generate the mid surface manually and do a geometry clean up on the component.
- To generate a mesh and to get a proper mesh flow on the given component with low tria concentration.
- To check the the elements quality according to the given quality criteria.
- To create a different collectors and organize the elements to that collectors to assign a thickness.
Theoretical Framework -
- Door panels serve as an interface between the interior of the car and the inner workings of the door, and between vehicle occupants and the door.
- They are expected to meet a variety of design specifications regarding safety, aesthetics, and functionality. In addition, they are expected to continue the material theme of the dashboard and pillars while concealing intricate electrical and mechanical components for operating locks, windows, and other features.
- The door panel has evolved from a simple two-part system of latch and simple winding mechanism to a more sophisticated enclosure.
- Doors currently have an inner full-width panel consisting of electronic windows, central locking system, and speakers. These panels typically consist of a foamed core covered with either textiles or plastics.
- Door panels were formerly made of cardboard with an upholstered interior finish of vinyl, leather, cloth, carpet, or other materials for the decorative trim. Modern cars typically have door cards made of plastic, most often using injection moulding, as well as incorporating other decorative materials.
- The design should incorporate both the necessary service amount and the functional unit (such as "it is strong" and "it looks and feels good") so that a given car door panel "would service a car body's life span of 200,000 kilometres (124,274 mi).The door panel typically incorporates other parts that contribute to the appearance, functionality, and ergonomics of the vehicle. These include armrests, switches or other controls for windows and the locking mechanism, convenience lights, audio speakers, storage compartments, and other features.
- In most cases, the door card is attached to the car's door frame by visible screws and ones hidden behind decorative plugs or under the armrest, as well as spring clips.
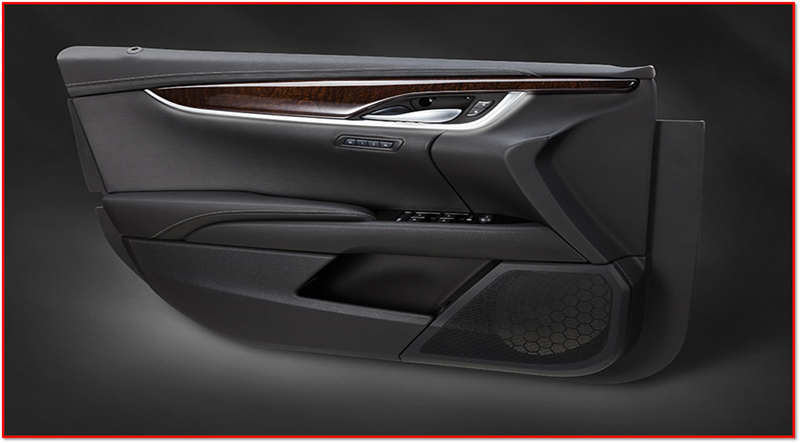
Figure 1-Door Interior Panel |
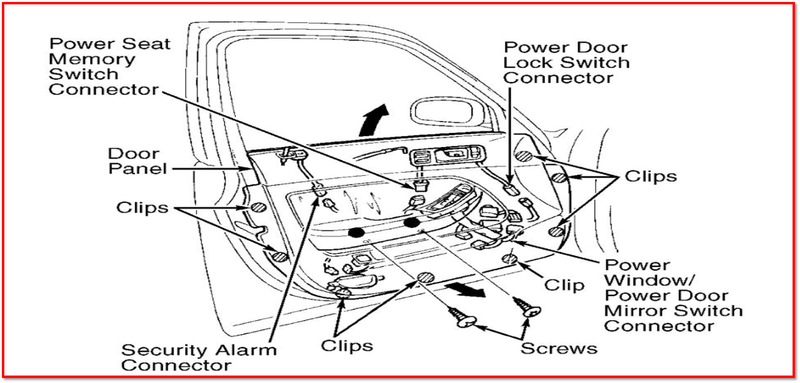
Figure 2-Door Trim Panel Parts |
Introduction -
- The Door Trim is a key component of the closure
- Door Trim ia an interior component attached to the inner side of the door. This product does more than merely improve the appearance of the vehicle interior. Rather, it is a vital module component that creates a more comfortable interior by providing a variety of accouterments and functions.
- These car door trim panels are made up of platic materials like Acrylonitrile-butadiene-styrene (ABS), ABS/polycarbonate alloys, polycarbonates, polypropylene, modified polyphenylene ether (PPE) and SMA (styrene-maleic anhydride) resins.
- The model given to us to be meshed and the midsurface should be extracted manually cause the model given to us is a plastic and these plastic components will have varying thickness.So the midsurface should be extracted manually.
- This Door trim model will be analyzed in the solver,The crash analysis will be done for this model.So for crash analysis,Try to eliminate the rotational quads as much as possible.
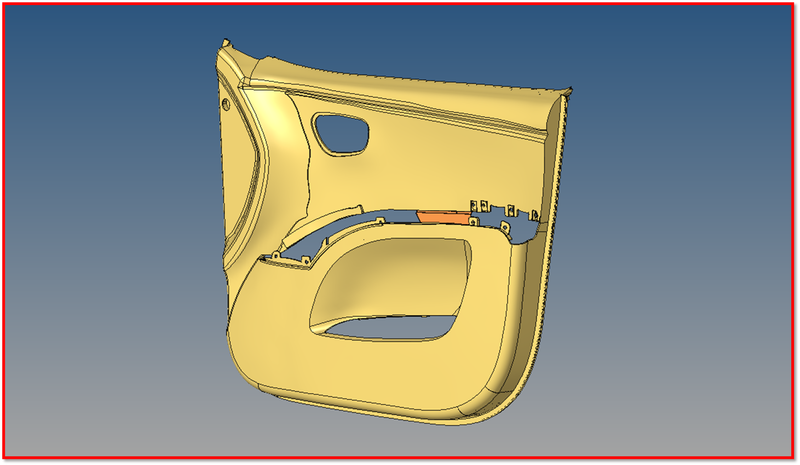
Figure 3-Side Door Inner Panel. |
Procedure -
Phase 1-Importing
- Hence we are importing a given CAD geometry into hypermesh.
- There are file formates like IGES,STEP,Parasolid where we can import these file formats into any CAD,CAE Softwares.
- But in hypermesh we can only import three file formates like
- IGES [Initial Graphics Exchange Specification].
- STEP [Standard for the Exchange of Product Model Data].
- Solidworks.
- IGES,STEP,These two are standard file formats which are used most in industries.But now a days in industries,they are aslo using parasolid file format.
- While importing the file into the graphical user interface,Be sure whether the file is .step or .iges file.
- File > Import > Import Model > File type > Open File > Import File.
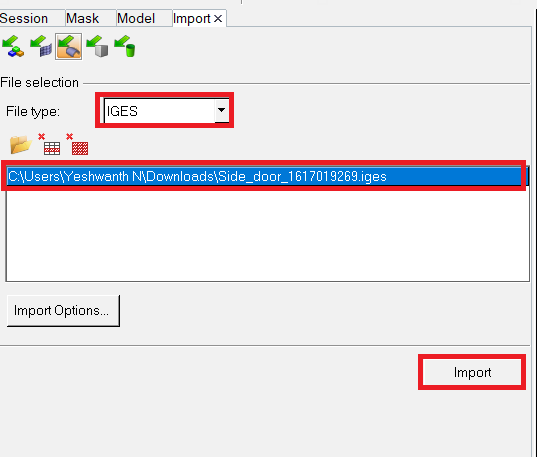
Figure 4-Importing Model into GUI |
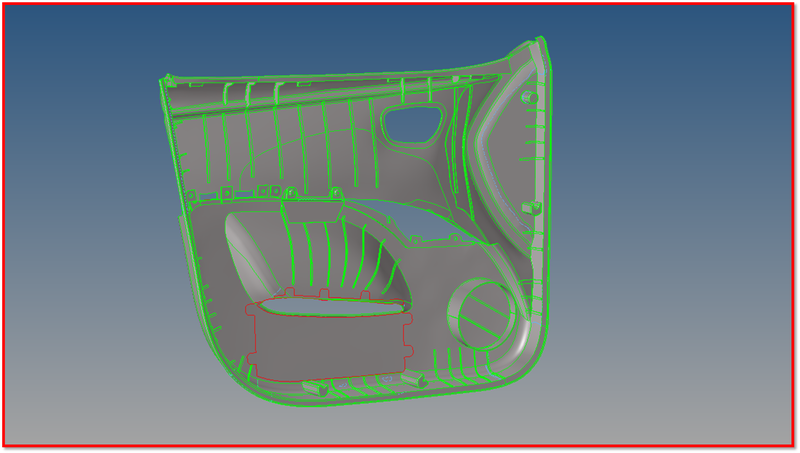
Figure 5-Imported Model into GUI |
- Switch to the topo mode and examine whether the solid exsist in the component or not,If solids exsist,Delete the solids cause we are doing 2d meshing on the component.
- You can find topo mode in the tool bar panel.
- Delete [F2] >> Solids >> Select by box selection >> Delete Entity.
- If solids exsist,It will be highlighted in the green colour.
Example -
[Note:This Model is for only Example]
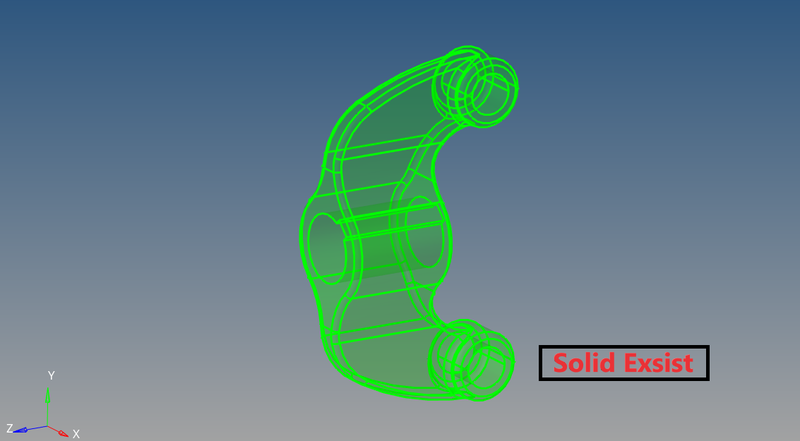
Figure 6-Before Deleting the Solids |
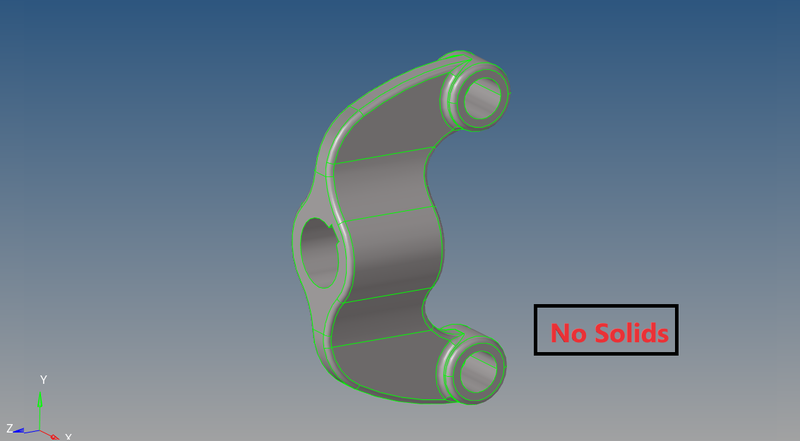
Figure 7-After Deleting the solids |
Phase 2- Examining
- Before working on the model.We have to check the geometry if there are any errors like
- Damaged Geometry.
- Free edges in unnecessary areas.
- Unnecessary points on the lines.
- Unnecessary Connections and connectivity error.
- By assessing the Car Side Door [Inner Panel] Model,The other components dosen't exsist in the model.
- There are some free edges in the inner surfaces,Clear that free edges.
- There are some features present in the side door inner panel model like
- Door Handle
- Speaker Housing
- Space for Placing our things like water bottle,etc.
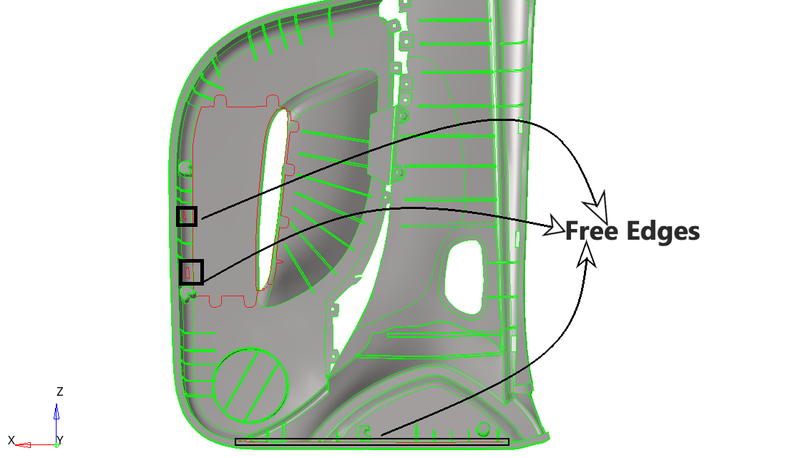
Figure 8-Free Edges Present in the surfaces |
2:1 Inspecting
- While examining,We can observe that there are plastic rivets.
- Now we are having two components in the model.
- But due to some scanning issue,the software shows us only one component.
- Now we have to detach the component and move to a separate collector in the model browser.
- To create a new collector in the model browser - Right Click on Model Browser > Create > Component > Sometimes the software itslef assign a different colour or Give a different colour.
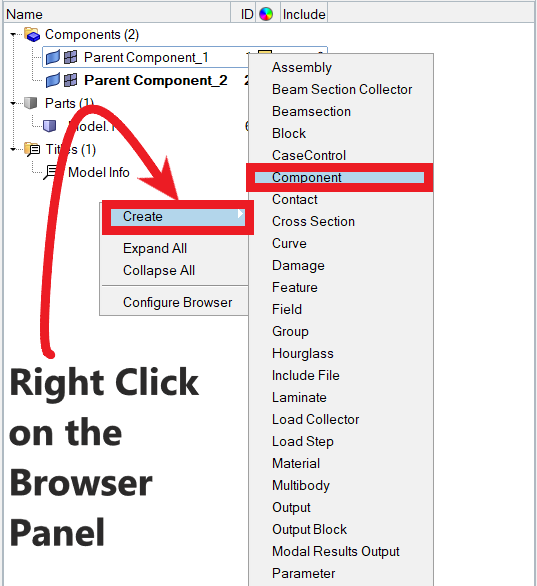
- The new component which we have created will be automatically assigned as a current component.
- Now organize the component consisiting rivets to the newly created component.
- To organize a component-Tools > Organize > Surfs (Select Manually) > Current Comp > Move.
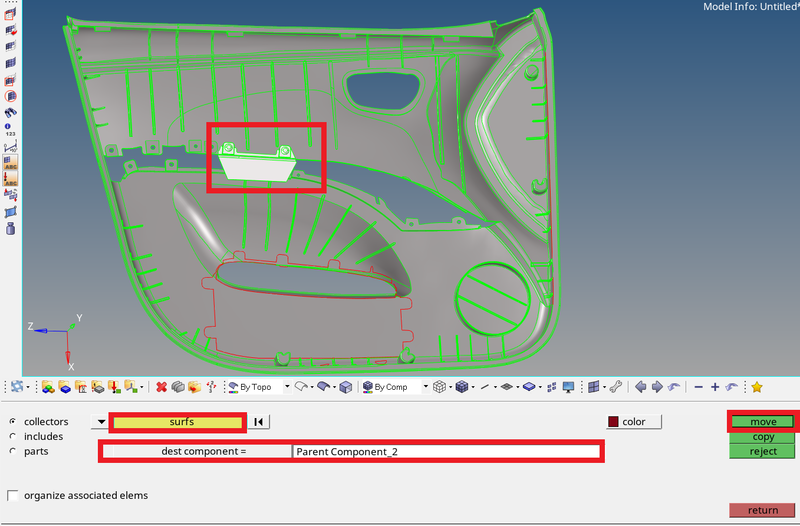
Figure 10-Organizing the component to new collector |
- After organizing,Check whether any other surfaces are selcted to the new component.
- Switch to the "By component" mode and view the model.Different colour will be displayed to the two components.
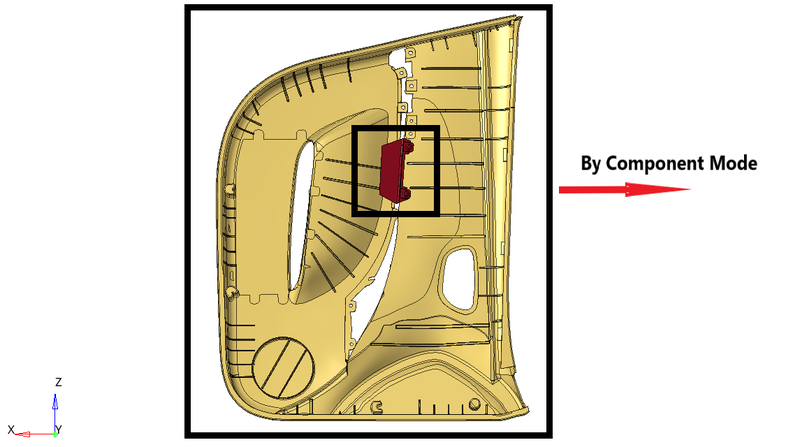
Figure 11-By Component Mode |
2:2 Checking Thickness
- Now go and measure the distance in every region.
- Cause this an plastic component,The plastic component will be having varying thickness.
- We are ensuring whether some regions of this component having uniform thickness or not.
- You can measure the thickness by two methods
i) Geometry > Dimensioning > Select the Point1 and Point2.

Figure 12-Dimensioning Panel |
ii) Tool [F4] > Distance > Points > Select the Point1 and Point2.

Phase 3 - Geometric Clean Up on the Parent Component
- If we want we can do geometry clean up on the parent component or after extracting the midsurface we can do geometry clean up on mid surface.
3:1 Defeaturing Ribs Fillet Regions
- For this component we will be doing 2D Mesh so it cannot capture the fillet feature properly,So we are defeaturing it.
- We are going to generate a mid surface between two flat surfaces,So no need of curved (fillet) regions,we can eliminate it.
- Since it will effect while extracting the mid surface.
- So defeature the fillets to get sharp edges,If we get the sharp edges,we can extract mid surface very easily.
3:2 How to Use Defeature Tool
- Geom > Defeature > Surface Fillets > Find Fillets in Selected

Figure 14-Defeature Panel |
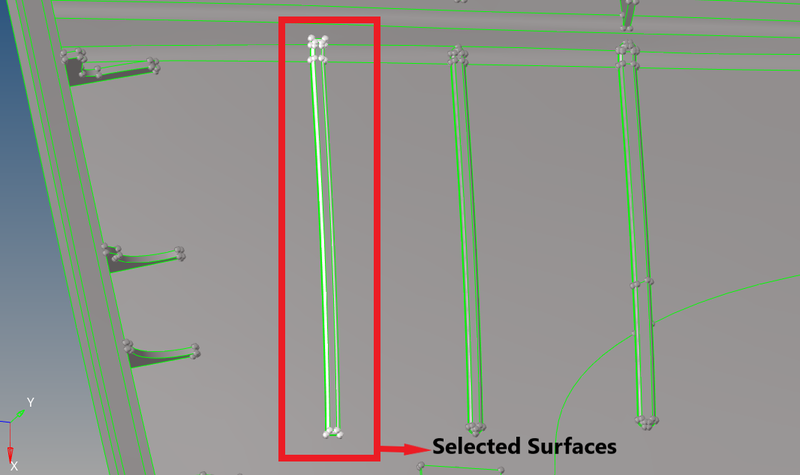
Figure 15-Selected Surfaces |
- After Selecting the surfaces.
- Enter the boundry conditions,Then only software can predict the fillet regions in the component.
- Enter Min radius as 0.1mm and Max radius as 5mm
- Click Find
- After clicking the software will predict the filets with the tolerance value of minimum and maximum radius.
- The fillets with the tolerance value of minimum and maximum radius will be highlighted.
- At last click to remove the fillets.

Figure 16-Defeature Panel |
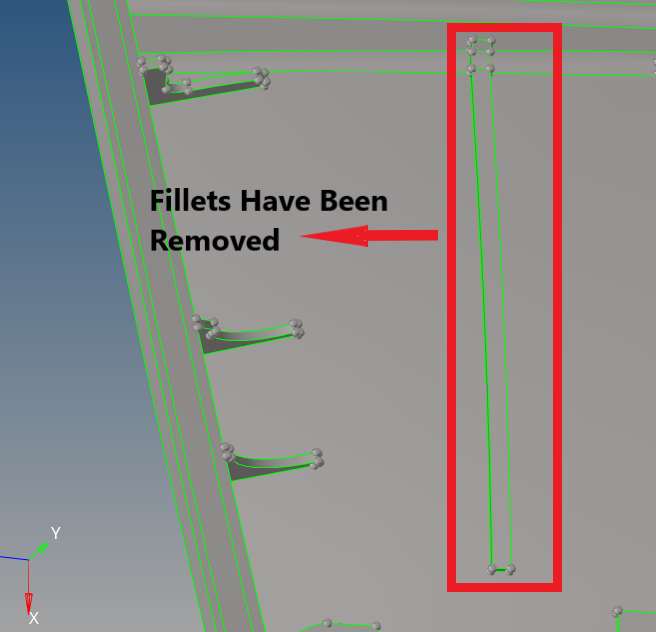
Figure 17-Fillets have been removed |
3:3 Limitations for the defeature tool-
- The fillets can be defeatured only along straight edges.
- Some fillets extend upon curved surfaces and edges so defeaturing may not work in those regions.
- Therefore we have to manually defeature the curved fillets.
3:4 Defeaturing the Ribs Fillets Manually-
- We have to delete the corner edges and replace with straight edges.
- Once we delete the edges a gap will be present and we will fill the gap by extending the ribs.
- Based on or conditions there are three options to extend the ribs, Drag along Line and Drag along Vector,Extend Over Edges.
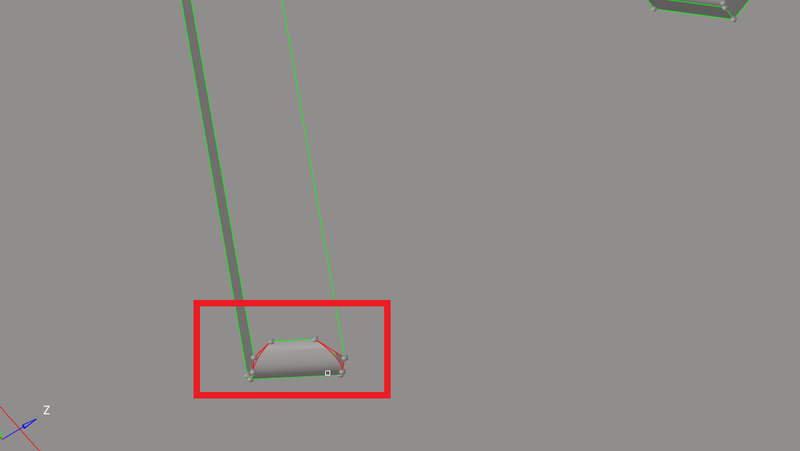
Figure 18-After Defeaturing some surface,It will result like this |
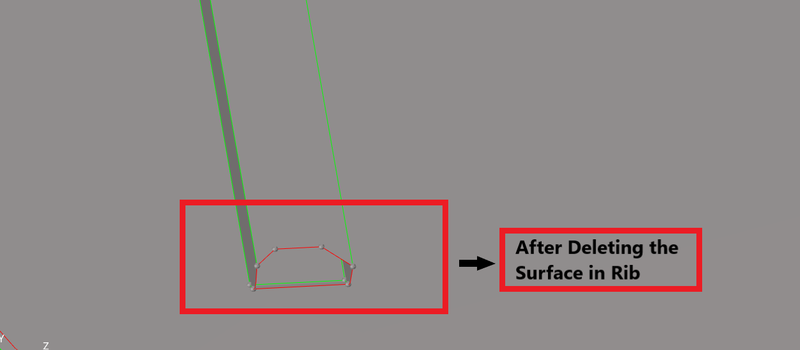
Figure 19-Delete the Surface in the rib |
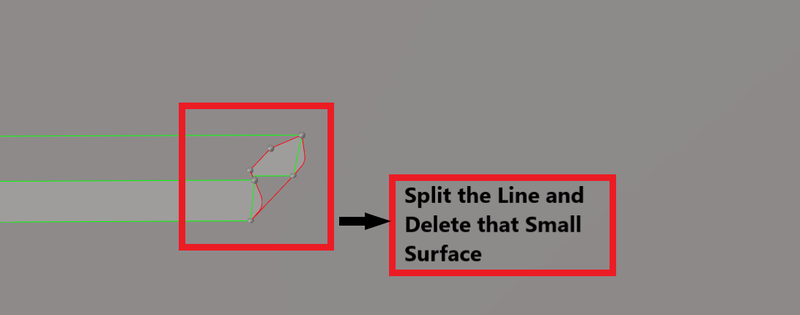
Figure 20-Split the line perpendicularly |
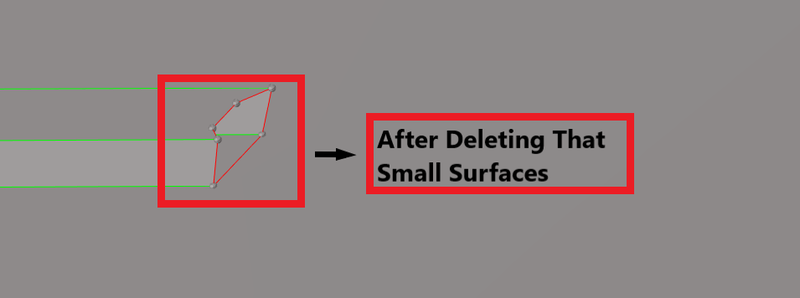
Figure 21-Delete the surface which has been splitted |
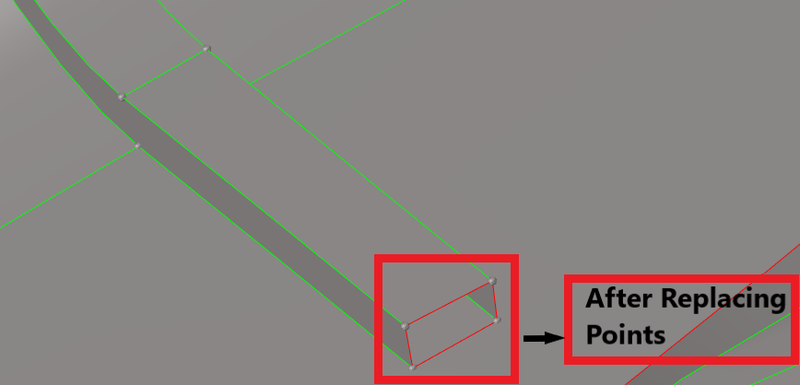
Figure 22-After replacing the points,It will result like this |
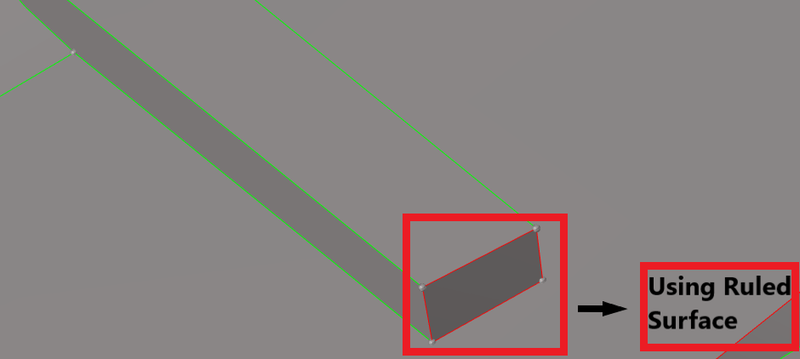
Figure 23-After Filling the Surface Using Ruled Surface Tool |

Figure 24-After toggling the free edges |
3:4 Using Drag Along Line,Drag Along Vector,Extend Over Edges-
i) Drag Along Vector-
- We can use the Drag Along Vector subpanel to create surfaces by dragging lines or a node list along a vector.
- Select the lines or node list to drag.
- If a node list is specified, a line will first be fit through the specified nodes.
- Geometry > Surfaces > Drag Along Vector > Lines > N1,N2,N3 > Distance > Drag +.

Figure 25-Drag Along Vector Sub Panel |
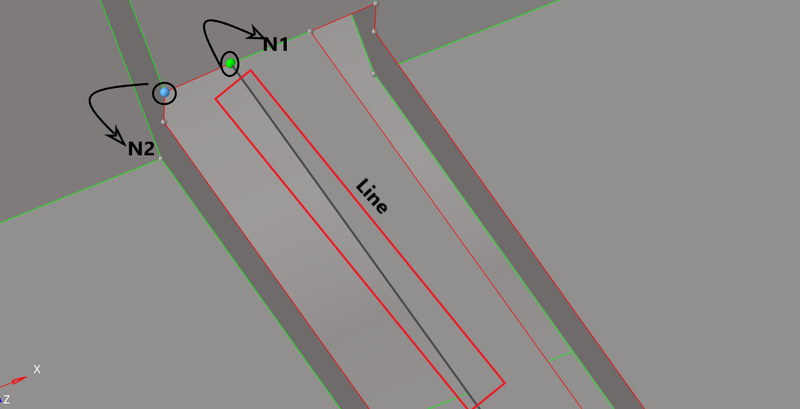
Figure 26-Drag Along Vector Process |
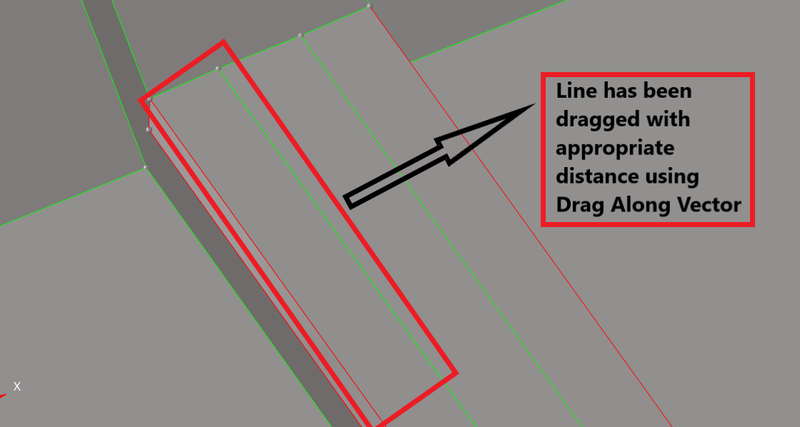
Figure 27-Surface has been dragged using Drag Along Vector tool |
ii) Drag Along Line-
- We can use the Drag Along Line subpanel to create surfaces by dragging lines or a node list along another line, called the "drag line".
- Lines/Nodes List-Select the lines or node list to drag.If a node list is specified, a line will first be fit through the specified nodes and then dragged.
- Line List-Select the lines that the drag will follow. This can also be a series of connected lines.
- Geom > Surfaces > Drag along Line > Line list 1 > Line list 2 > Drag+.
- Lines-Specifies surface that you are going to extend by selecting the line of extension.
- Line list-Specifies the Line along which you are going to extend i.e., Direction you are extending.

Figure 28-Drag Along Line Sub Panel |
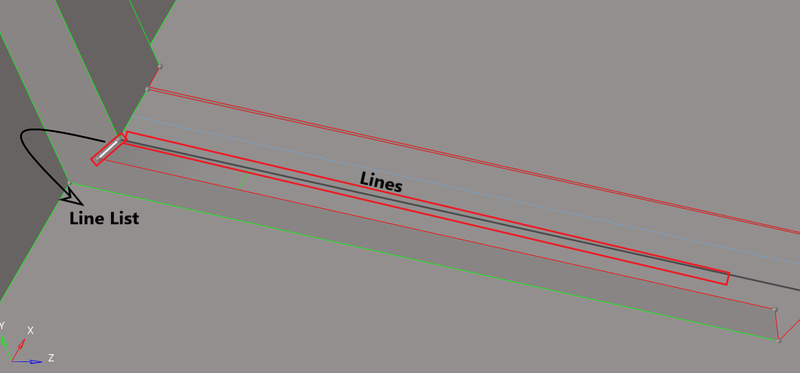
Figure 29-Drag Along Line Process |
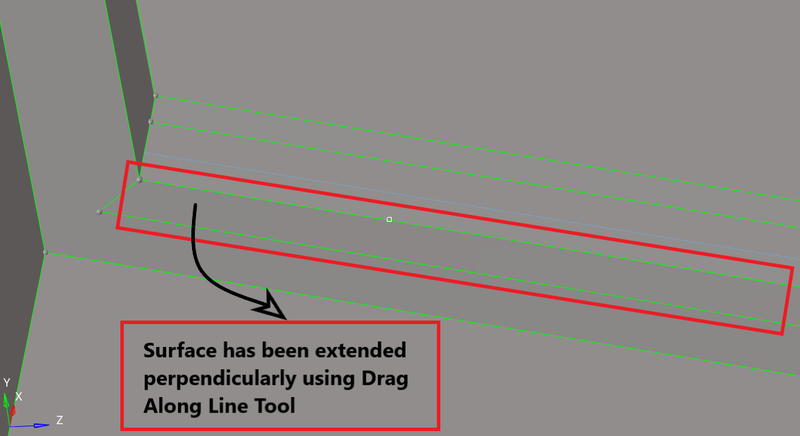
Figure 30-Surface has been extended perpendicularlly using Drag Along Line Tool |
iii) Extend Over Edges-
- Extend Over Edges is used to Extend a surface over edges to another surface.
- Geometry > Surface Edit > Extend > Extend Over Edges > Lines:Extend Over > Surfaces to Extend > Surface: to Target > Extend.
- Lines: to extend over-Select edges to extend. Surfaces will be extended across these lines. If you select a free edge, this also selects and highlights the corresponding surface.
- Surfs: to extend-Select surfaces to extend.
- Surfs: to target-Extend the extended surfaces in the direction of the selected surfaces.

Figure 31-Extend Tool Sub Panel |
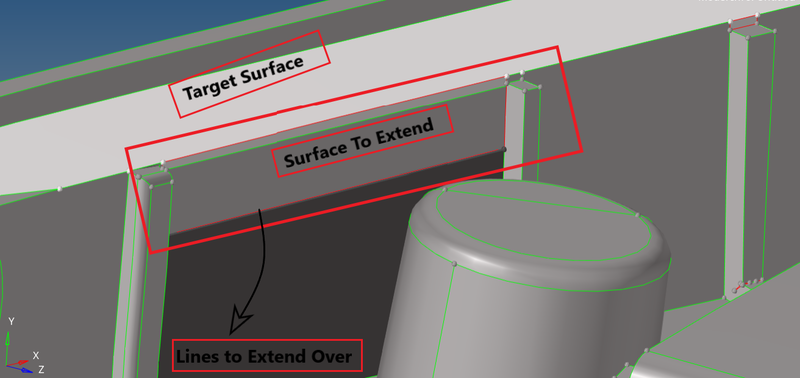
Figure 32-Extend Over Edges |
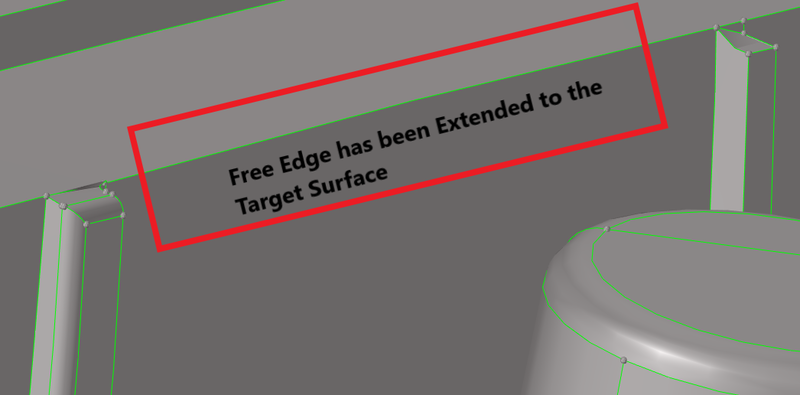
Figure 33-Edge has been Extended |
3:4 Projecting the Holes to the Parent Component-
- There are two methods of projecting the holes
i) You can project the hole from riveted surface to the parent surface.
ii) You can project the hole from rivetd surface to the mid surface after extracting the mid surface.
- You can see in the below Figure 34.The hole is present on the riveted surface.
- We are going to delete that riveted surface and we are going to project that hole in the parent surface.
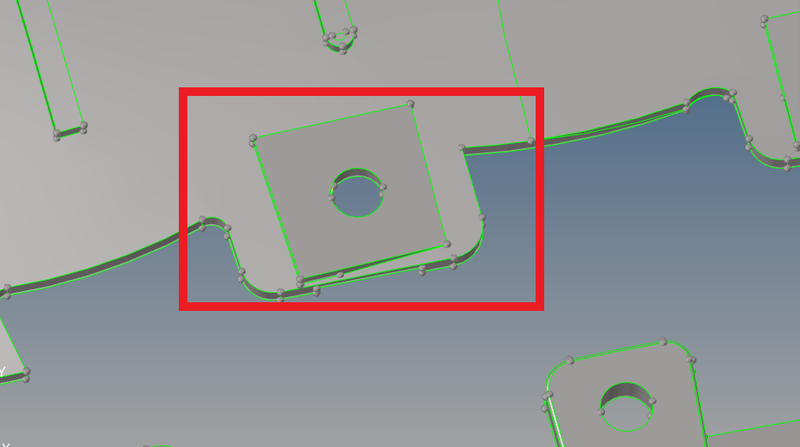
Figure 34-Hole on Riveted Surface |
Figure 35-Surfaces has been deleted |
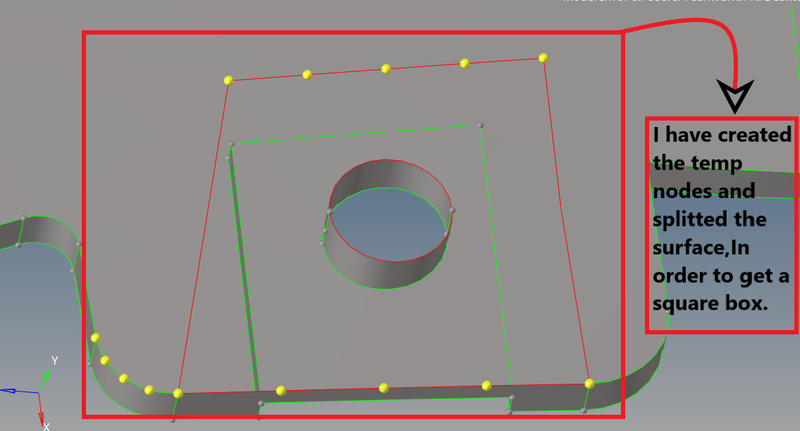
Figure 36-Surface has been splitted and deleted. |
Figure 37-Surface has been created. |
- Now project the free edge surface to the parent surface using trim with lines.
- Geom > Surface edit > Trim with lines > With Lines > Surfs (Select) > Free Edges (Select) > Normal to Surface > Entire surface > Trim.

Figure 38-Trim With Lines Sub Panel |
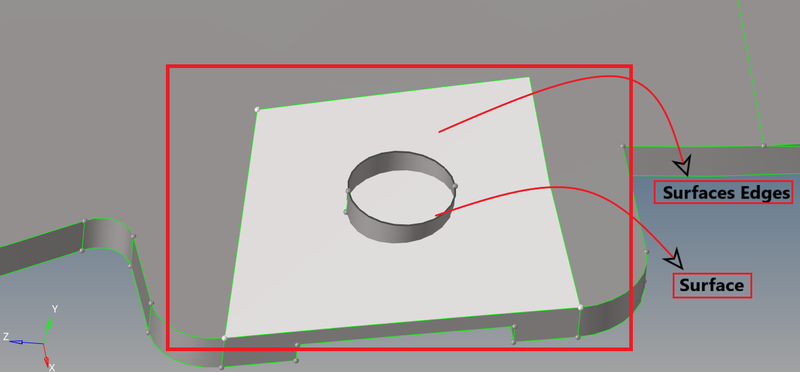
Figure 39-Trim With Lines Process |
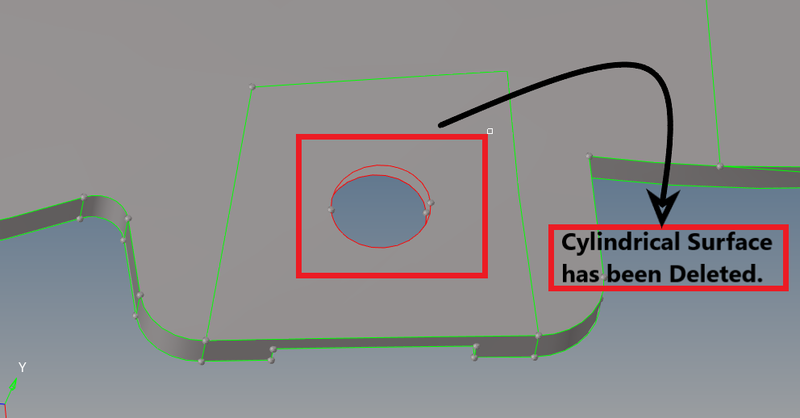
Figure 40-Cylindrical Surface has been Deleted |
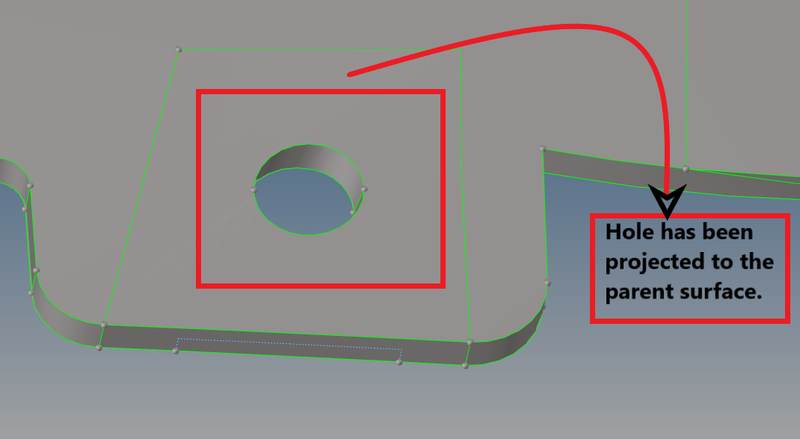
Figure 41-Hole has been projected. |
3:5 Fixing Overlapping Surfaces-
- Here the surfaces have been overlapped.
- To fix this surfaces,We can release the points and we can fix it by extending over edges,toggling edges,replacing the points,replacing edges.
- Geom > Quick edit [F11] > Release Point > Select.
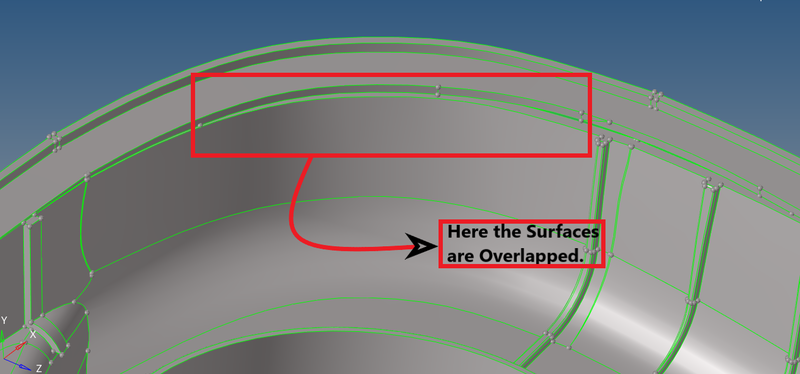
Figure 42-Surfaces has been Overlapped. |
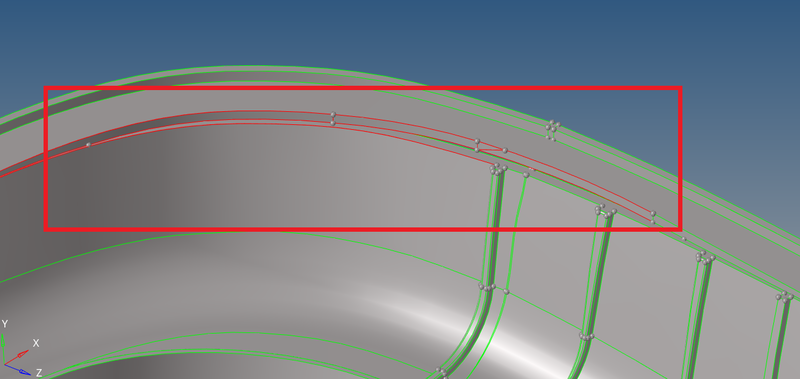
Figure 43-Points have been released. |
- Here we can toggle the some edges,If it dosen't work,try to use replace points.
- I'm going to delete some surfaces and then i'm going to connect them using extend over edges tool,ruled surface tool,drag along line tool,toggle edge tool.
- Mask some regions and try to connect them,So we can the surfaces properly.
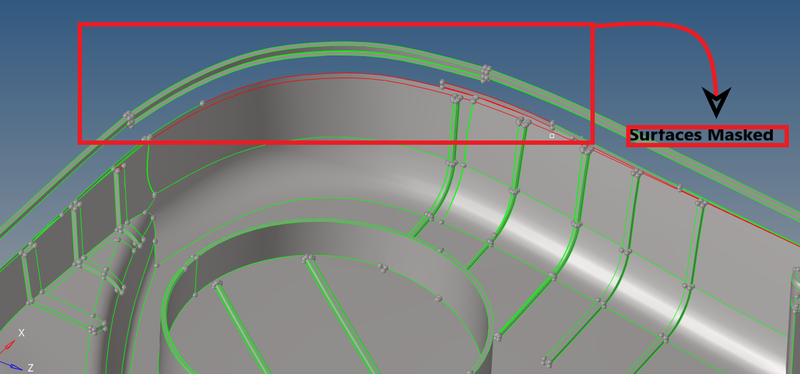
Figure 44-Surfaces Masked. |
- Here im extendin edges to the surface using extend tool.
- Geometry > Surface Edit > Extend > Extend Over Edges > Lines:Extend Over > Surfaces to Extend > Surface: to Target > Extend.
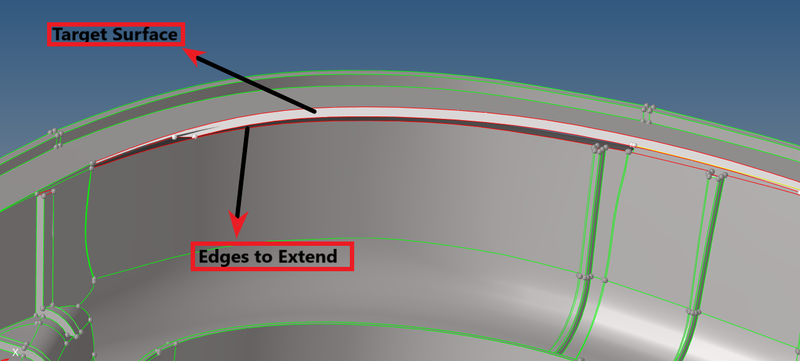
Figure 45-Extend Over Edges Process. |
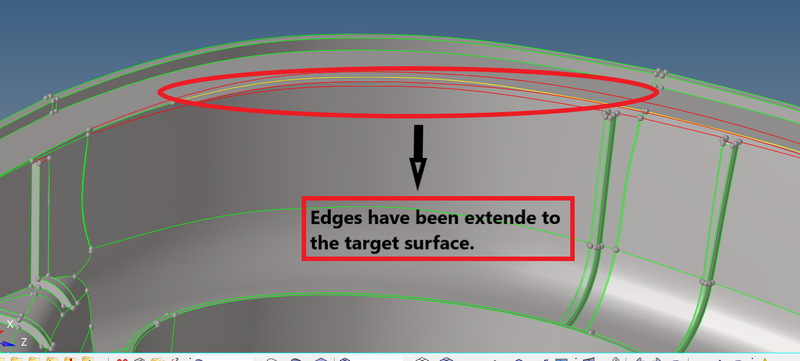
Figure 46-Edges Have been Extended. |
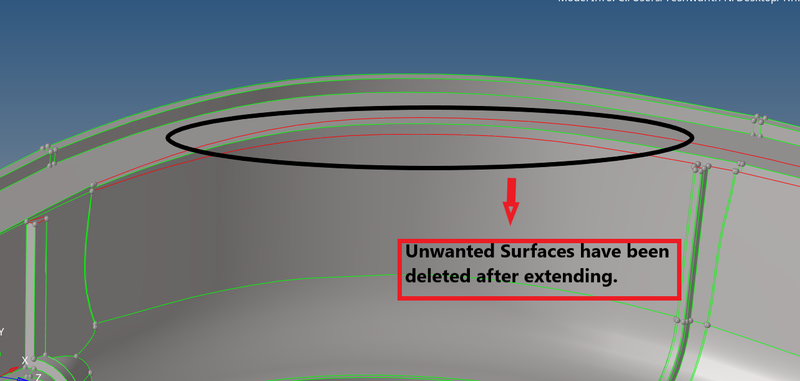
Figure 47-Unwanted Surfaces has been deleted. |
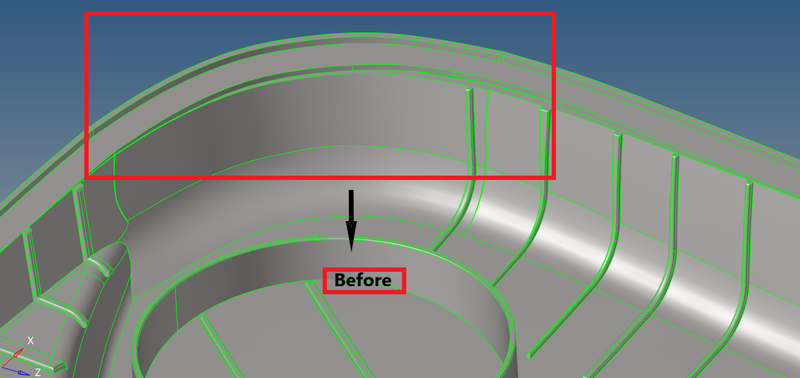
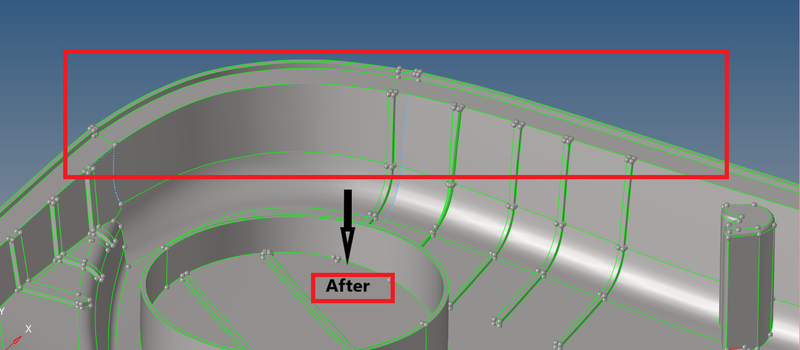
3:6 Fixing Damaged Geometry in surfaces.
- Deformed surfaces occur due to the following reasons like
- Overlapping surfaces
- Connectivity issues
- Sometimes this issue occurs due to replacing the points multiple times
- These issues can be rectified by using the tools called
[Note:Try to avoid replacing points.Instead of that split the surface and connect.]
- We can fix the geometry by quick edit tool.
- There some sub tools in the quick,I have described every too below,Have a look.
i) Geometry → quickedit → split surface node.
- Select two locations of the nodes to split the surface and then select an additional node to continue to split the surface.
ii) Geometry → quickedit → Split surf-line
- In this,select a node and select a line to split the surface,here the split will be perpendicular to the line chosen.
iii) Geometry → quick edit → Adjust/set density.
- After meshing a particular surface.We can adjust the mesh density by using this tool.While meshing we will increase the
nodes to get a proper mesh flow.We can also increase nodes after meshing by using this tool.
iv) Geometry → quick edit → release points.
- Drag and select the surface,where you want release the points.After releasing the points.The free edges will exsists.
v) Geometry → quick edit →replace points.
- Move points from their current locations to the locations of other points,where we want them to replace it.
vi) Geometry → quick edit → add/remove points.
- Use window selection (with the left mouse button and right mouse button ) to add and remove any points within the
selection box.
vii) Geometry → quick edit →add points on line.
- Specify the number of points that we wish to add to that line, and then select the desired line in our model.
viii)Geometry → quick edit → delete surface.
- Select the surface which we need to eliminate and delete it.
Phase 4-Extracting the Midsurface
- The midsurface has been extracted to the components which have less than 6mm thickness.
- We will be extracting midsurface for the sheetmetal and plastic components.
Why to Extract Mid Surface ?
- Before extracting the mid surface for every component,We should measure the thickness of the component and then we have to proceed to extract the mid surface.If the component thickness is less than 6mm then we will come to know it is a sheet metal component or plastic Component.
- For sheet metal and plastic components,Mid Surface extraction is must.
Midsurfacing: Process & Strategy-
1.Obtain a closed volume of surfaces or solids
- Midsurface : auto midsurface requires an enclosed volume.
- Use topology repair techniques if needed.
2. For complex parts, try defeaturing the surface defining the volume
- This simplifies the part and may give better results with create solid.
3. Generate the midsurface using midsurface : auto midsurface
- Use surface pair for areas that need more control.
- Use midsurface : editing tools for midsurfaces that need fine tuning.
4. View the midsurface and correct errors using the midsurface editing functionalities
- Can generally use quick edit.
4:1 Check the thickness of the parent component
- The component given to us is a side door interior trim.
- This component is a plastic component,The plastic components will have varying thickness,We have to check whether it has varying thickness or uniform thickness.
- In some regions the plastic component will have avrying thickness but in ome regions it will have uniform thickness.
- While checking the thickness of the parent component,Display fixed points and then check.
- Now project the points to the bottom surface and check the thickness in the middle regions.
- To project the points-Go to Tools > Project (Shift + F7) > To Surface > Ponts (Duplicate > Surfs (Select) > Normal to Surface > Project.
- Now measue the distance between the two points using Distance Tool (F4) or Dimensioning Tool.
- Geometry > Dimensioning > Point1 > Point2 > Create.
- Geom > distance [F4] > Two Points > Point1,Point2 > Middle Click.

Figure 50-Distance Panel. |
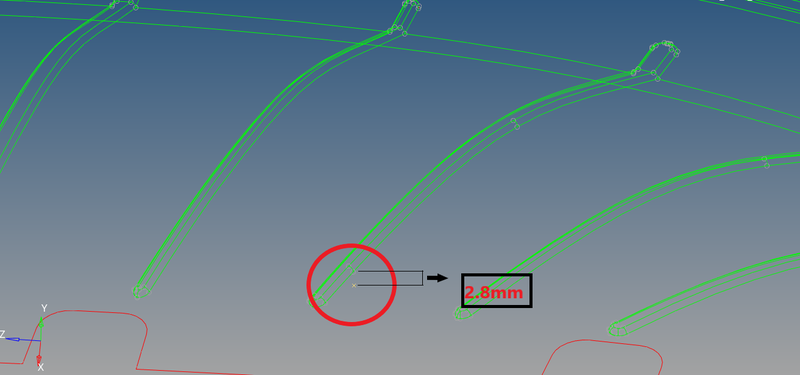
Figure 51-Thickness of Middle Region |
- Now we have measured the thickness.The thickness for the entire base surface is 2.8mm.
- The side ribs,square ribs,cylindrical ribs have varying thickness.
4:2 Extract the Mid Surface
- For this Base surface,I'm using auto extraction with the skin offset.
- In some cases skin offset might work or might not work.
- For this component,I have used skin offset,But for other regions,we should extract the mid surface manually for the ribs and for the corner regions.
4:3 Extract Mid the Surface Manually Using Offset
- Geom > Surface Edit [Shift + F9] > Offset > surfs > by Face > Duplicate to Current Component > Offset = 1.4mm.
- If the arrow points outward, give for reverse normal to make the arrows point inward.
- Vector Normal (If Outward) - Reverse Normal.
- Blue indicates towards the screen or inward.
- Red indicates away from the screen or outward.
- If it shows Red, give for reverse normal and it should show blue.
- Color Normal [If Red] - Reverse Normal.
- Color Normal [If Blue] - Offset.

Figure 52-Offset Sub Panel. |
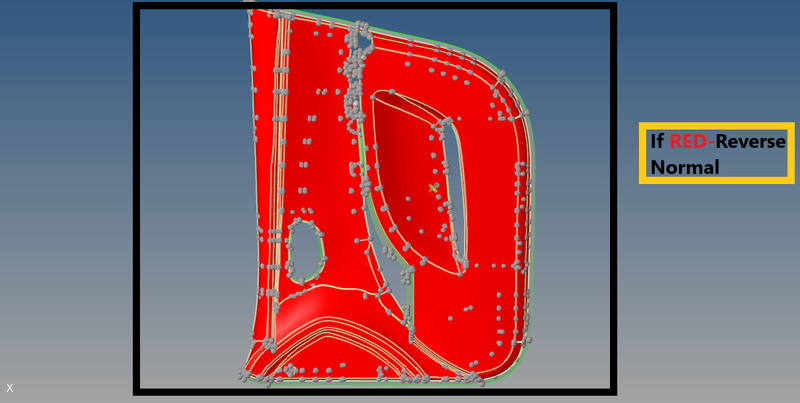
Figure 53-Red:Reverse Normal. |

Figure 54-Blue:Towards Screen[Offset]. |
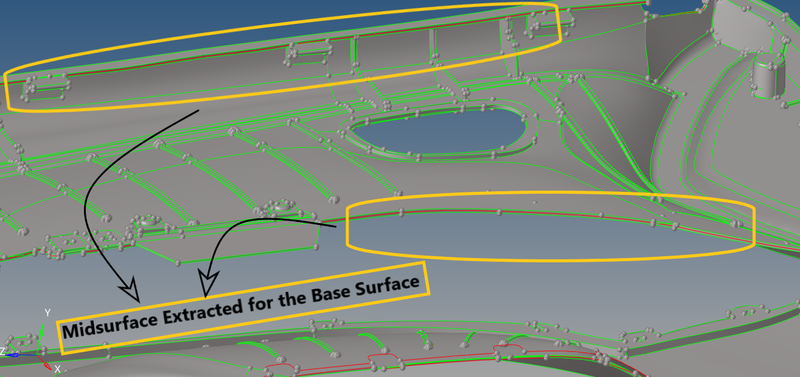
Figure 55-Midsurface Extracted for the Base Surface. |
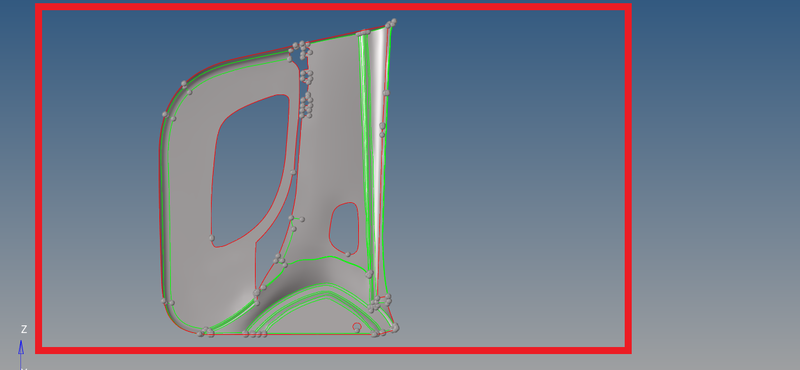
Figure 56-Proper Representation of Mid Surface Extracted for the Base Surface. |
- Create a Component before extracting the midsurface.
- If you extract mid surface without creating a component,It will result in the parent component.
- Then you have to create a new component and you have to organize the mid surface to that newly created component.
4:4 Extractig Mid Surface for the ribs
- We can extract mid surface for ribs by three methods
i) By Using Final Edit Tools for the defeatured ribs.
ii) By Using Offset Tool for the defeatured ribs.
iii) By Extracting Midline on the ribs and projecting it to the mid surface and create a surface using ruled surface.
i) By Using Final Edit Tools for the defeatured ribs.
- We can use the Final Edit tools repair surfaces, modify targets, and imprint surfaces after the midsurface has been extracted and you do not need to make further changes that require the midsurface to be re-extracted.
- Geom > Mid surface > Final Edit Tools > Surface Pair > Side 1 [Select Surf] > Side 2 [Select surf] > Extract.

Figure 57-Final Edit Tools Sub Panel. |
- Side 1: surfs selector-Select a surface that represents one side of the solid.
- Side 2: surfs selector-Select a surface that represents the second side of the solid.
- Extraction Options-Select extraction options accordingly to define which surfaces to take into account when constructing midsurface.By default, only two surfaces that are selected with the side1 and side2 surf selectors are considered.To take into account offset directions of the adjacent pre-existing midsurfaces, select the use adjacent midsurfaces checkbox.To allow modifying pre-existing adjacent midsurfaces, select the combine with adjacent midsurfaces checkbox.
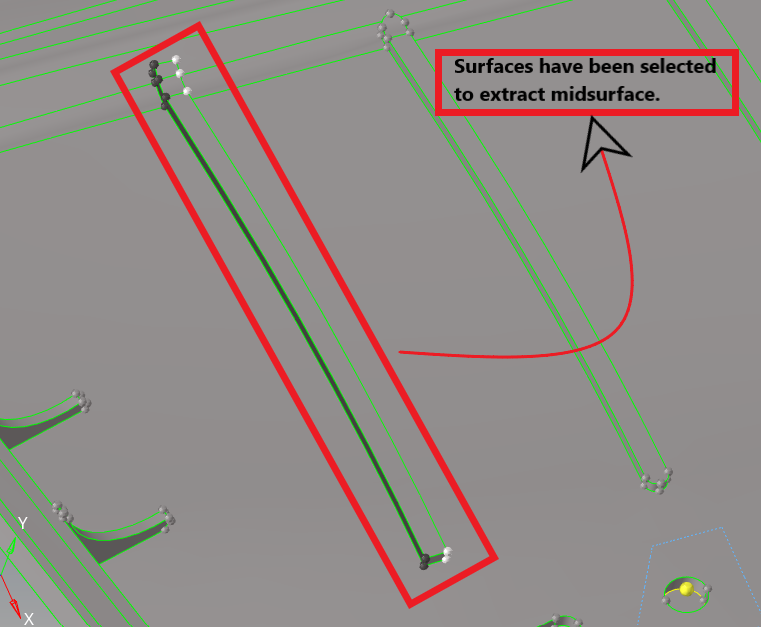
Figure 58-Surfaces Selected to Extract Mid Surface for Rib. |
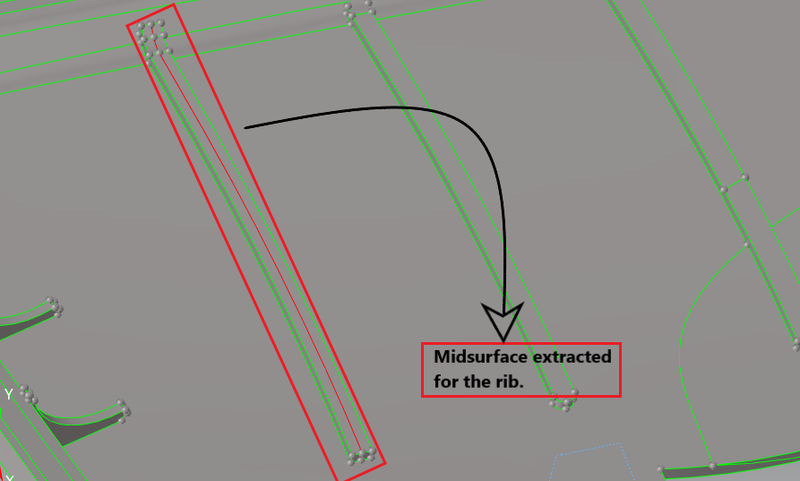
Figure 59-Surface has been Extracted for Rib. |
ii) By Using Offset Tool for the defeatured ribs.
- Geom > Surface Edit [Shift + F9] > Offset > surfs > by Face > Duplicate to Current Component > Offset = 1.4mm.
- First measure the thickness between the ribs and then select the surface and duplicate it from the current or orginal component and then extract the mid surface using offset tool.
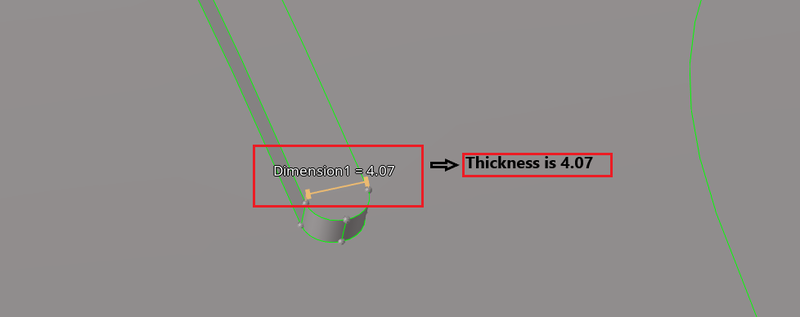
Figure 60-Thickness of Rib. |

Figure 61-Offset Sub panel. |
_1623675771.png)
Figure 62-Surface Exracted to the Rib. |
iii) By Extracting Midline
- Geometry >> Lines >> Midlines >> Line List 1,2 >> Create.
- We can use the Midline subpanel to create lines by interpolating between existing lines.

Figure 63-Midline Sub Panel. |
- Two options are required to create a line using this method.
- Select a line list to use for the first side.
- Select a line list to use for the second side.
- The result depends on the order of the input lines selection. If the shorter of the two line segments is input as the first list and the longer one as the second, the midline is generated with a length similar to the shorter line.
- In addition, the midline is created only between the first line segment and a portion of the second line segment.
- If the longer line segment is input as the first selection, the length of the midline generated is an average of the two line lengths.
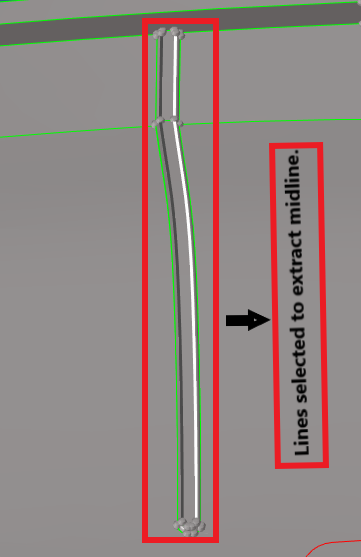
Figure 64-Lines Selected to Extract Midline. |
- Now extract the midline for every region.
- And to project that lines to the mid surface.
- Use trim with lines tool to project on the mid surface.
- Make sure to set mid surface component as a current component,Then only the lines will exsist in that component.
- After that hide the parent component before projecting lines to the mid surface.
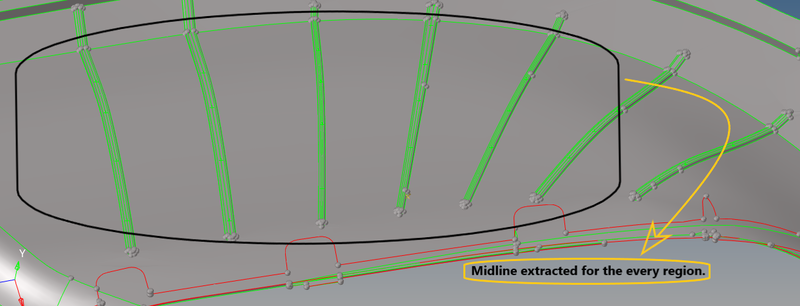
Figure 65-Midline Extracted for Every Region. |
- Now hide the parent component and project the lines to the mid surface.
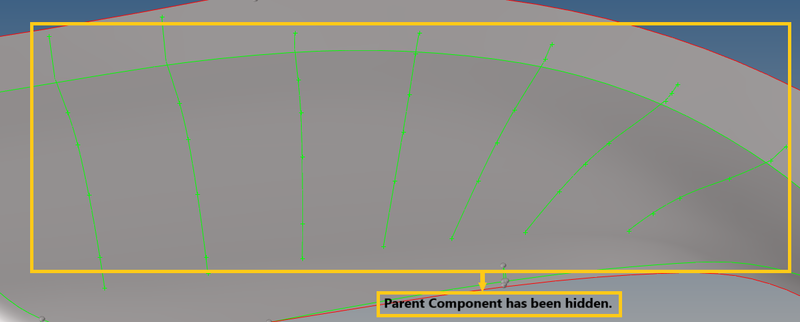
Figure 66-Parent Component has been Hidden. |
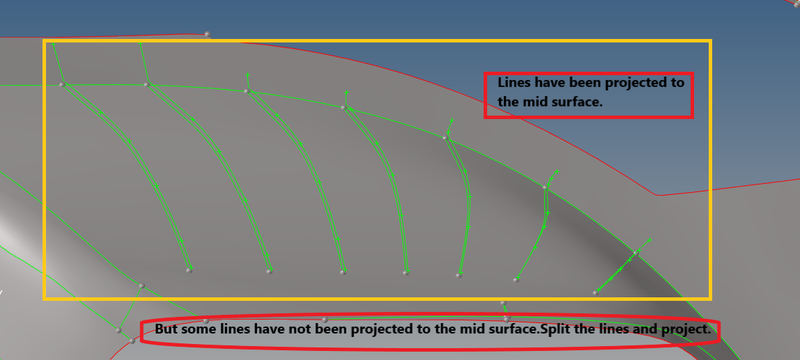
Figure 67-Lines Projected to the Mid Surface. |
- Here front edges have not been projected,So split the lines using line edit tool and project it.
- We can use the Line Edit panel to split, join, or extend lines.
- Geometry >> Line Edit >> Split at Point >> Select Line >> Select Point >> Click.
- We can use the Split at Point subpanel to split an existing line into two separate line segments. The split occurs at a point which you select by clicking the line.
- Line-Select an input line. The selected line will remain highlighted. Click the point on the line where you wish the split to occur. The split will be made automatically.

Figure 68-Lines have been splitted and projected. |
- After Projecting the lines.
- The splitted lines are combined using combine tool in line edit panel.
- Now the surface has been created using the ruled s,urface tool in surface panel.
- Geometry >> Surfaces >> Ruled Surface >> Select Line1,Line2 >> Create.
- We can use the Ruled subpanel to create surfaces by interpolating linearly between lines or nodes.
- In the Line List,Use the first selector to define the first edge of the surface to create. Use the second selector to define the second edge of the surface to create.

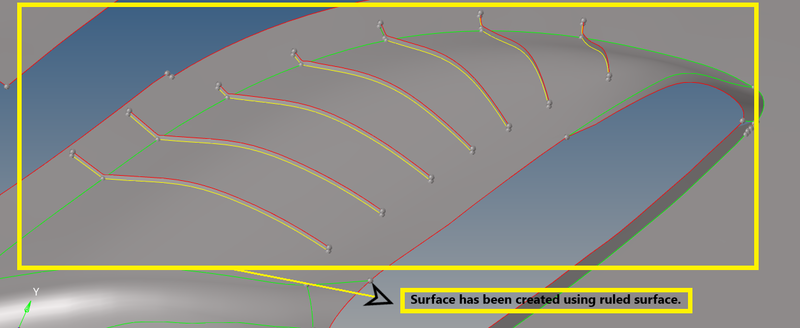
Figure 70-Surface Created using ruled surface. |
[Note: In my perspective,What I noticed is,extract the midline in the rib region.While extracting midline,Make the mid surface you extracted for the base surface and make that component as current and extract.If you do like this,It will be very easy to create a mid surface to the ribs.Go with this method.Other two methods are fishy.You have to the extend over the edges and then you have to go on,So follow this method fpr every rib region.]
4:5 Projecting the holes to the Mid Surface
- Before projecting the holes to the mid surface
- Create a surface to fill the gaps using ruled surface.
- Before creating a surface add points at the corner to split the edges and then create a surface using ruled surface tool.
- Geometry >> Quick Edit >> Add Points.
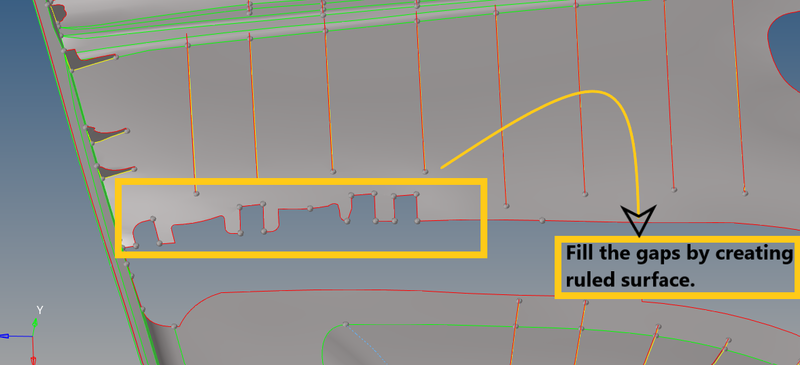
Figure 71-Fill the gap using ruled surface. |
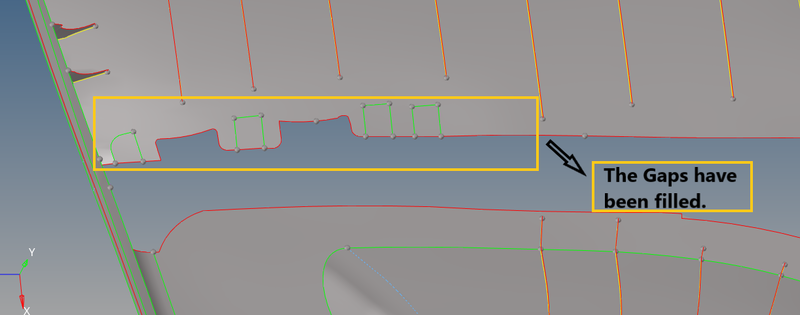
Figure 72-Gaps have been filled. |
- Now project the holes to the mid surface,Make the mid surface as the current component and project it.
- Project the holes with trim with lines.
- Geometry >> Surface Edit >> Trim with Lines >> With Lines:Surfaces >> Surface Edges >> Trim.
- Hide the parent component and select the surfaces for midsurface and surfaces edges for circle edges and click trim.
- The Circular holes will be projected to the mid surface.
[Note:Make the Mid Surface as Current Component and Project the Holes.]
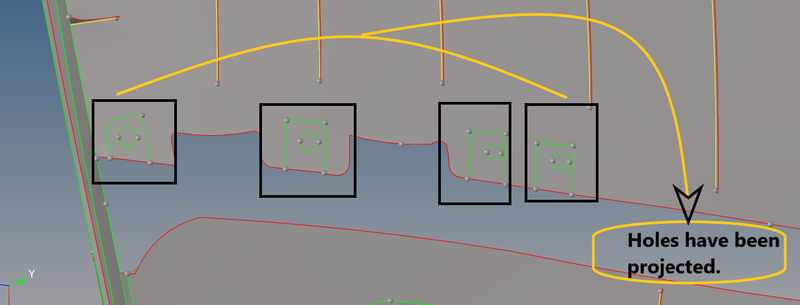
Figure 73-Holes Projected. |
- Now delete the holes in the mid surface.
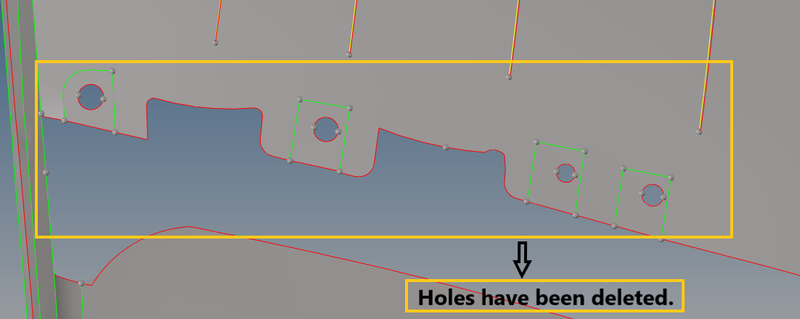
Figure 74-Holes have been deleted. |
4:6 Extracting Mid Surface for the Cylindrical Ribs.
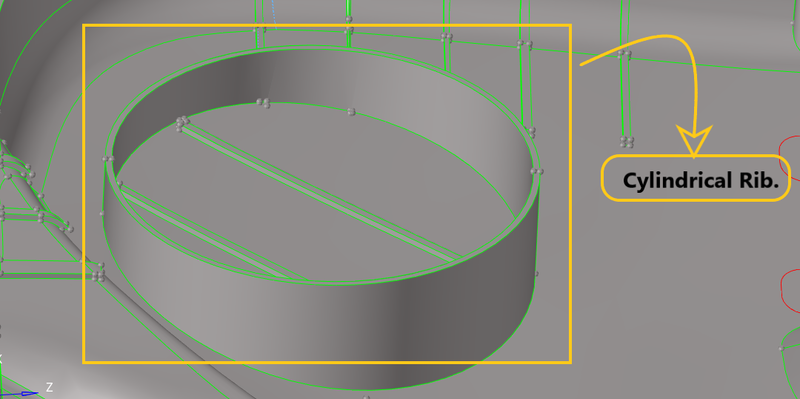
Figure 75-Cylindrical Rib. |
- For this cylindrical rib,I'm extracting mid surface using Final Edit Tools.
- We can use the Final Edit tools repair surfaces, modify targets, and imprint surfaces after the midsurface has been extracted and you do not need to make further changes that require the midsurface to be re-extracted.
- Geometry >> Mid Surface >> Surface Pair >> Side1-Surface >> Side2-Surface >> Extract.
- Side 1: Surfs selector-Select a surface that represents one side of the solid.
- Side 2: Surfs selector-Select a surface that represents the second side of the solid.
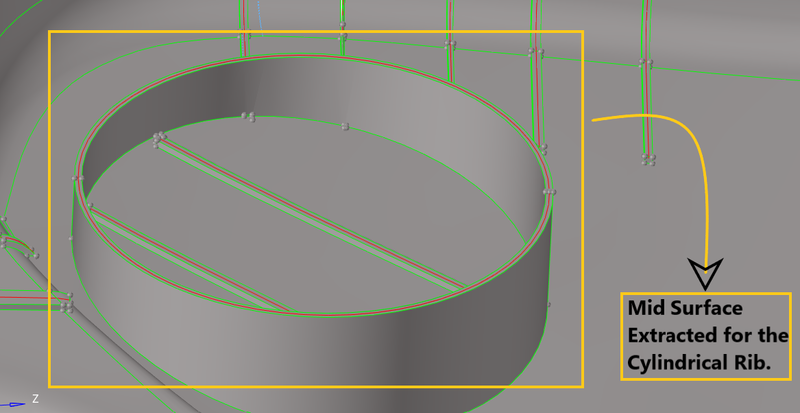
Figure 76-Mid Surface Extracted for the Cylindrical Rib. |
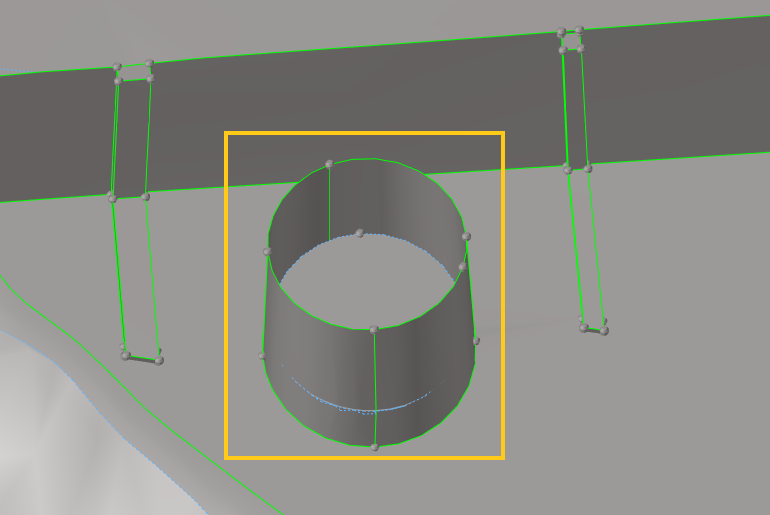
Figure 77-Cylindrical Volume. |
- This cylindrical rib has no thickness.For this cylindrical rib,We are taking mid surface randomly.To consider that there is feature prsent in that region.
- We are splitting the surfaces and we are taking mid surface using ruled surface.
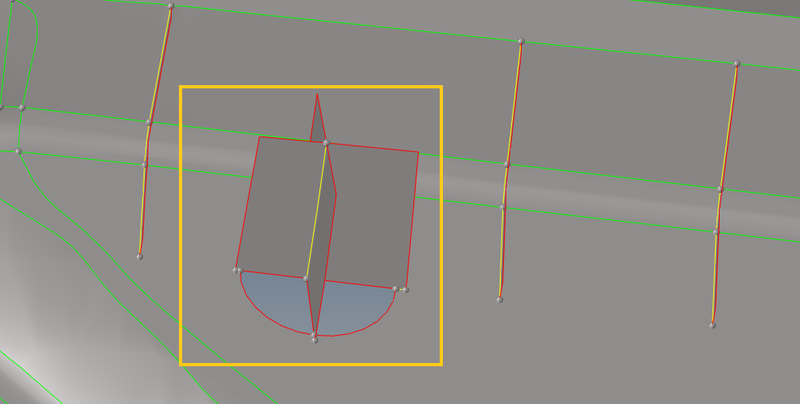
Figure 78-Mid surface has been taken randomly. |
- Now fill that hole using ruled surface.
- Mask that four surface and fill the hole using ruled surface.
Figure 79-Hole has been filled with ruled surface tool. |
- Simlarly do that same thing for every cylindrical volumes as shown in the fig 79.
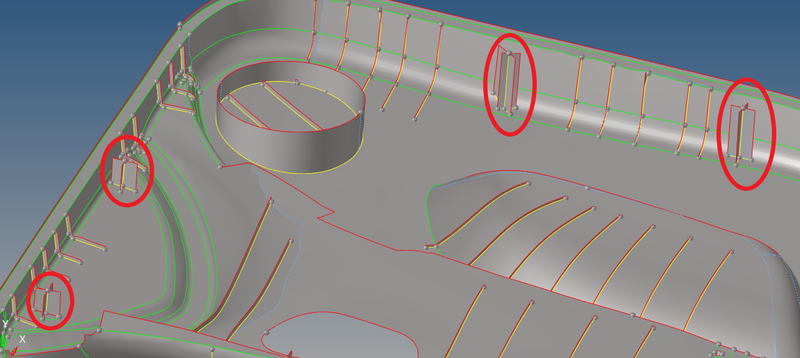
Figure 80-Surfaces Created for the Cylindrical Volumes. |
4:7 Final Geometry Clean Up and Mid Surface
- If there are any glitches or any damaged surfaces in the Mid Surface geomerty,Clear that.
- If there are any unnescessary shared edges,toggle them.
- If the edges are failing for minimum and maximum length,then toggle that edges or split that edges with a particular region.
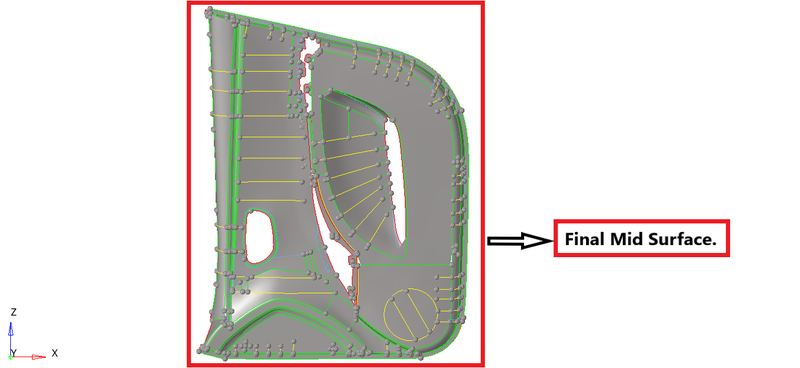
Figure 81-Final Mid Surface. |
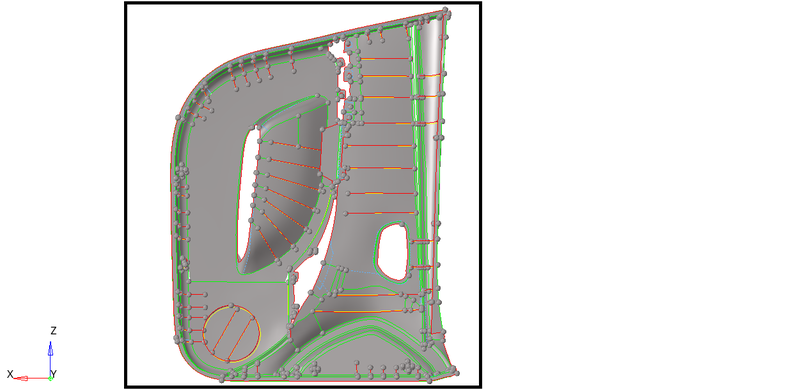
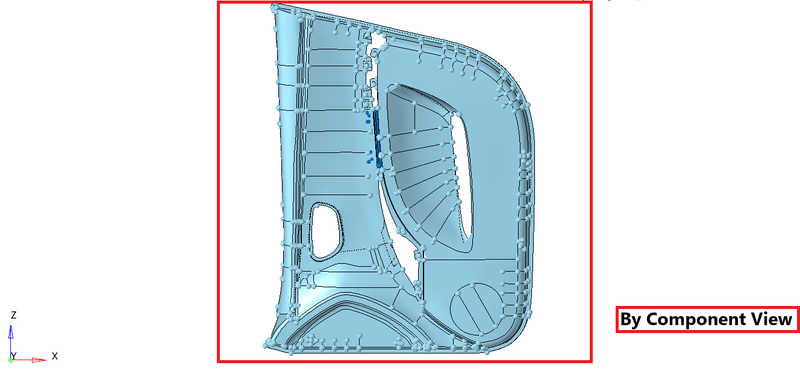
Figure 83-By Component View. |
Figure 84-By Component View [Front View]. |
Phase 5 - Perform Mesh on the Surfaces
- Once geometry cleanup is completed (e.g. surfaces are stitched together — no unwanted free surface edges inside the geometry), meshing is next.
Some rules of thumb when meshing:
- The mesh should look rather smooth and regular (keep in mind that the analysis is based on your mesh and the mesh quality is key.
- Use the simplest element type suited for the problem.
- Start with a coarse mesh and understand the modeling results; then use a finer mesh if needed.
- Try to keep mesh related uncertainties to a minimum if possible. Keep it simple as it can get more complicated on its own.
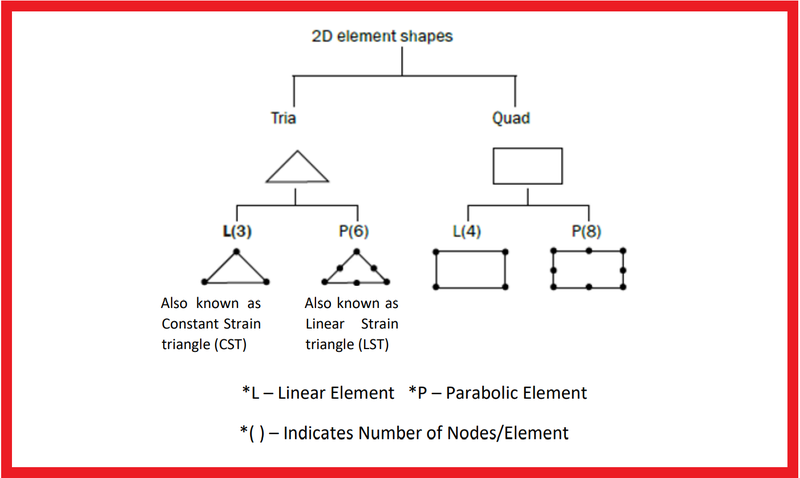
Figure 85-2D Element Shapes. |
- Different Element Type Options for Shell Meshing:
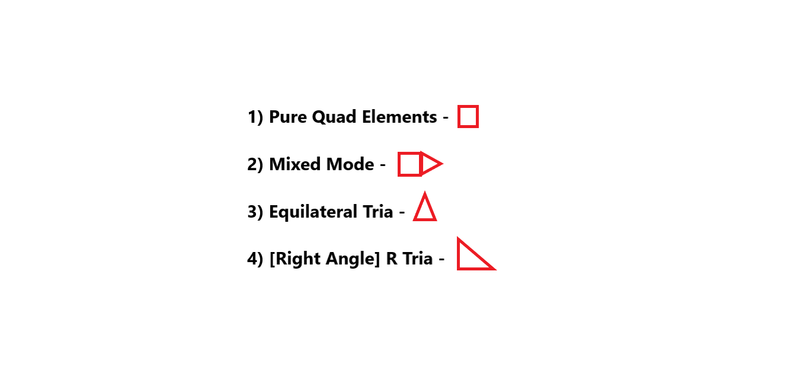
5:1 Enter the quality criteria what they given for the component's
- Tool bar → preferences → criteria file settings → checks for the element criteria →Enter values → apply → ok.
- Before generating a mesh on the surfaces.Enter the quality criteria given tou us in the question.
- You can go and enter quality criteria in Tool bar → preferences → criteria file settings → checks for the element criteria →Enter values → apply → ok.
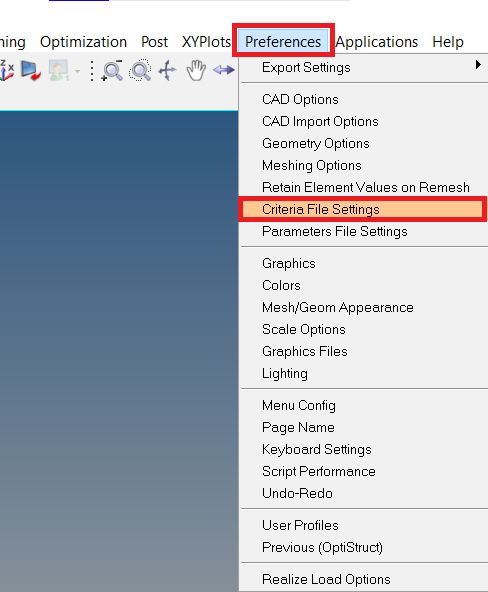
Figure 87-Tool Bar Panel. |
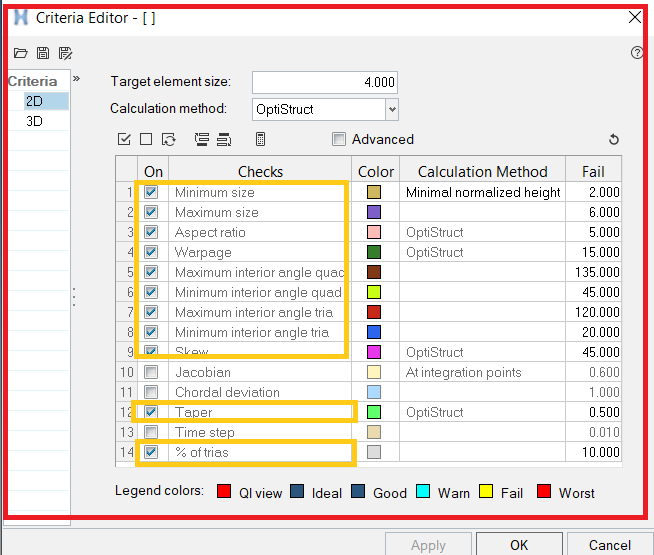
Figure 88-Criteria File Settings. |
[Note : Save the criteria file settings for that component and save it any other drives,Cause whenever we open that
component,we can open the element criteria file and criteria will be applied habitually instead of entering again.]
Target Element Size - 4 Units
Sl. No. |
Quality Criteria |
Function / Definition |
Value |
1 |
Aspect Ratio Ratio |
Ratio of Max. Length by Min. Length |
5 |
2 |
Skewness |
Deviation from the ideal shape |
45 |
3 |
Warping |
Angle between the 2 planes of the same element(Quad) |
15 |
4 |
Taper |
Convergence of a Quad element |
0.5 |
5 |
Min. Length |
Shortest length of any given element |
2 |
6 |
Max. Length |
Longest length of any given element |
6 |
7 |
Min angle Quad |
Minimum angle in any given Quad element |
45 |
8 |
Max angle Quad |
Maximum angle in any given Quad element |
135 |
9 |
Min angle Tria |
Minimum angle in any given Tria element |
20 |
10 |
Max angle Tria |
Maximum angle in any given Tria element |
120 |
11 |
Tria % |
Percentage of Tria on any meshed surface |
10 |
1) Aspect Ratio
- This is the ratio of the longest edge of an element to either its shortest edge or the shortest distance from a corner node to the
opposing edge ("height to closest node").
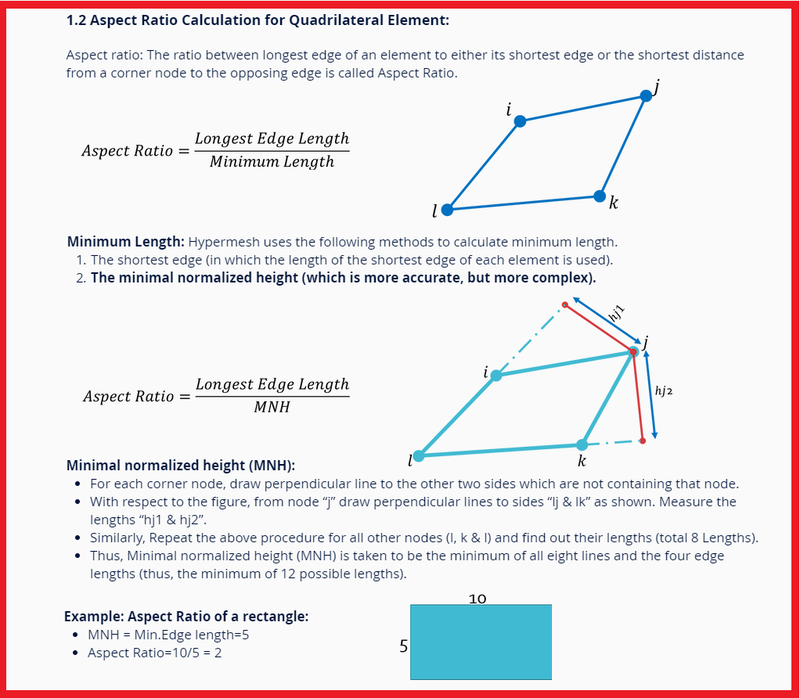
Figure 89-Aspect Ratio Calculation. |
2) Skewness
- Skew of triangular elements is calculated by finding the minimum angle between the vector from each node to the opposing
mid-side, and the vector between the two adjacent mid-sides at each node of the element.
- For Skewness: Ideal=0,But < 45 is acceptable.
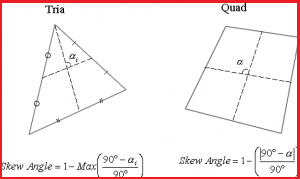
3) Warping
- This is the amount by which an element (or in the case of solid elements, an element face) deviates from being planar. Since
three points define a plane, this check only applies to quads. The quad is divided into two trias along its diagonal, and the angle
between the trias’ normals is measured.

4) Taper
- Taper ratio for the quadrilateral element is defined by first finding the area of the triangle formed at each corner grid point.These
areas are then compared to one half of the area of the quadrilateral.
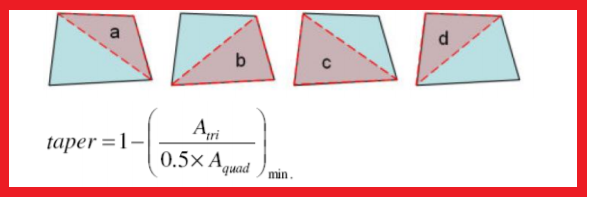
5) Minimum and Maximum Length
- The shortest distance from a corner node to its opposing edge (or face, in the case of tetra elements) referred to as height to
closest node.
5:2 Conditions to be followed while meshing
- Feature capturing is must while meshing.All the nodes must be connected to the shared edges.
- Avoig higher number of trias.
- Important Parameter's in tria management
- No trias in corner's or edge's.
- No opposite trias.
- No back to back trias.
- No trias in fillets or hemmings(We can have minimum but anyhow try to avoid).
- No rotational quads.
- No trias should share a boundary with feature line.
- Connectivity between elements.
- Split and perform the mesh.
- Use mixed type mesh for irregular shaped surfaces and quads only for rectangular/square surfaces(Opposite sides should be parallel and equal).
5:3 Begin meshing the surfaces
- Start meshing from the centre regions or from least free edges.You will get proper mesh density and proper mesh flow.
Why Meshing is Needed ?
- Finite Element Method reduces the degrees of freedom from infinite to finite with the help of discretization or meshing (nodes and elements). One of the purposes of meshing is to actually make the problem solvable using Finite Element. By meshing, you break up the domain into pieces, each piece representing an element.
How to Begin Mesh ?
- Start meshing form the least free edges,Like start meshing from the center.
- It will be easy to get proper mesh flow and we will get uniform mesh density.
- Don't mesh form the edges,It will be difficult and you will get many error,So start meshing from the center.
- Choose the element type while meshing.
- For this component we will be using mixed element type and working on it.
- We can also quads element type.This type can be used when we have rectangular surface.
- We can use Tria Element type.This type can be used for 3d tetra meshing.
Start Meshing
- Now start meshing on the surfaces,Go to 2D >> Automesh Panel >> Surfaces >> Element size = 4mm > Mesh Type : Quads or Mixed > Check for align and size > Mesh.

Figure 93-Automesh Panel. |
- Select the appropriate mesh type based on the shape of the surface.
- Once we give for mesh, we can edit the mesh density by changing the number of nodes.
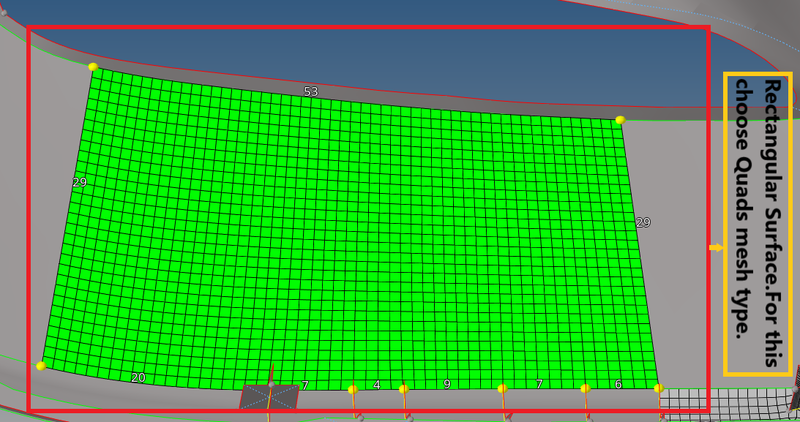
Figure 94-Mesh on the rectangular surface. |
- Here i have splitted the surface to rectangular surface and meshed to get proper mesh flow.
- Make sure to check the Link Opposite Edges with AR.
- This option is to be checked when your are meshing on the rectangular surface.
- Link Opposite Edges with AR-[Eg:If we have 29 nodes on left side edge,It will project the same 29 nodes on right side edge.]
- Now if we mesh on the curved surfaces,Choose the mesh type as mixed and mesh.
- If we choose quad mesh type,The mesh will fail,It won't occur on the surfaces.
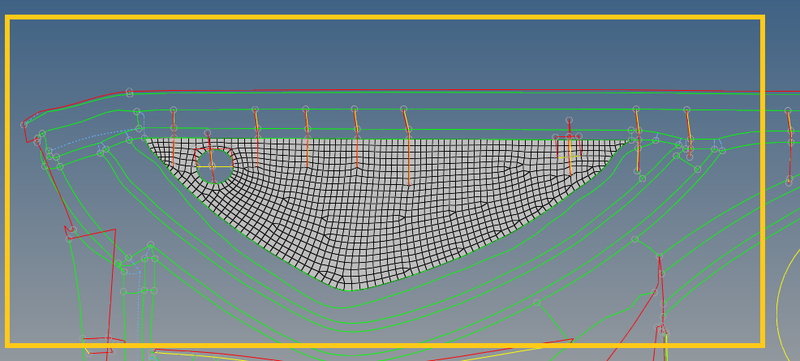
Figure 95-Mesh on the curved surface. |
5:4 Remesh and Rebuild Mesh
Remesh-
- Remesh is used to generate a mesh of plate elements using surface geometry or existing shell elements to define the mesh area.
- Elements are remeshed with the use of the HyperMesh inferred surface algorithm, if geometry for theselected elements needs to exist in the model.
- The inferred surface algorithm interpolates geometry datafrom the selected elements in order to create new mesh.
- When elements are selected to be remeshed, there is the break connectivity option and the vertex angle parameter. The break connectivity option detaches the node connectivity between adjacentselected and unselected elements. This allows you to adjust the node densities along the boundary ofthe selected elements.
- The vertex angle parameter defines the placement of vertices along theboundary of the selected elements. If the angle between two adjacent element edges along the boundaryis less the specified angle, a vertex is placed at the meeting point of the two edges.
- Anchor nodes create the effect of a fixed point on the inferred surface (which is derived from the existing mesh) and keep the location of the anchor nodes intact.
Rebuild Mesh-
- It is the process of remeshing existing meshes to generate a new mesh with good quality and flow.
- The rebuild mesh functionality utilizes the same parameter and criteria files used by BatchMesher to define the quality criteria and relevant mesh parameters.
- This algorithm saves significant time over the traditional automesh and quality correction approach.
- Rebuild is currently supported for first-order 2D meshes that are not attached to 3D element faces.
- The rebuild algorithm is useful for many different applications like
1) Remesh to adjust size, quality, and flow.
2) Change to a different element type.
3) Add or remove washer layers around holes, change the nodal density of a hole, adjust a hole diameter, or remove a hole.
4) Locally correct areas with bad mesh flow.
5:5 Meshing Surfaces in Circulare Free Edges
- While meshing the surfaces having circular hole.
- Make sure to create even number of nodes.
- For this component and for this circular holes i will be creating 6 even number of nodes,You can also go with 4.
- Make sure that the element edge should be aligned parallel to the shared edge.
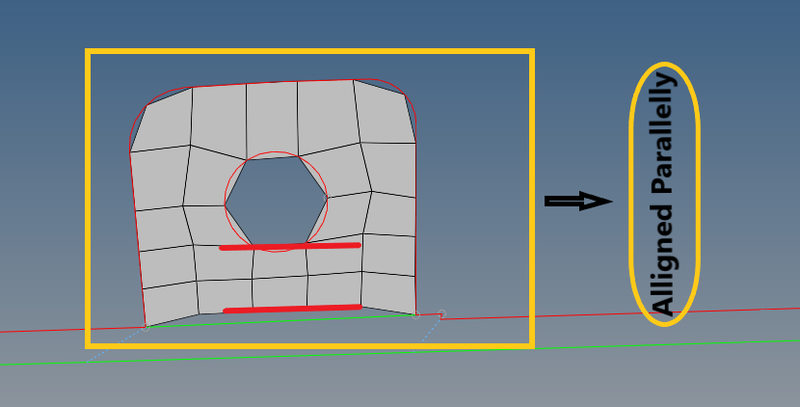
Figure 96-Meshed in Circular Region. |
- Here the elements are alligned parallelly.
- If the elements are not aligned,Rotate the elements and allign using rotate tool.
- In order to rotate,First we have to create a node in the centre of the circle using arc centre tool.
- To create go to Geom > Nodes > Arc Center > Lines > Select the Red Circle (Free edge) > Create.
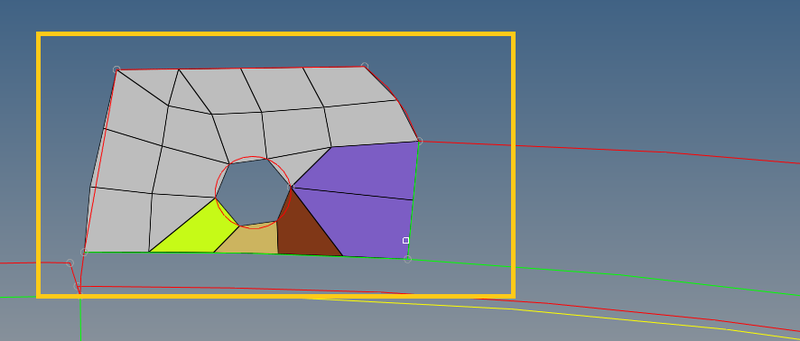
- Here we can see the elements are not aligned and they are failing.
- Now we have to align the elements by using rotate tool.
- First we have to create a node in the centre of circle.
- To create go to Geom > Nodes > Arc Center > Lines > Select the Red Circle (Free edge) > Create.

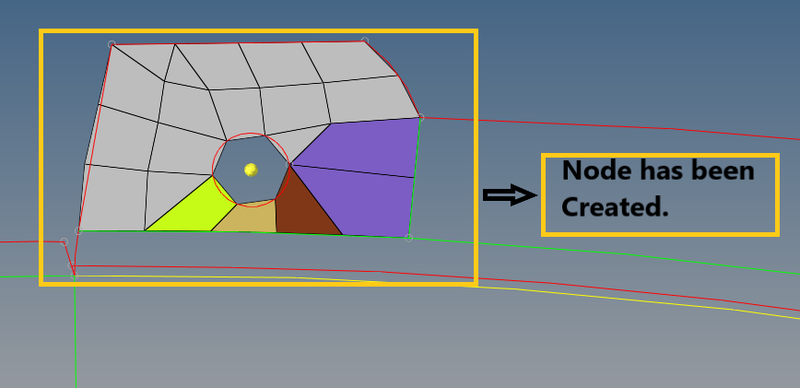
- Tools > Rotate > Nodes [to be rotated] > Select N1, N2 & N3 > Select B > Enter Angle > Rotate +/-.

Figure 101-Rotating the nodes using rotate tool. |
- After rotating the nodes to get proper allignment.Now remesh the elements.
- To remesh Go to 2D > Automesh > Elements > Select Anchor Nodes > Mesh.

Figure 102-Automesh Panel. |
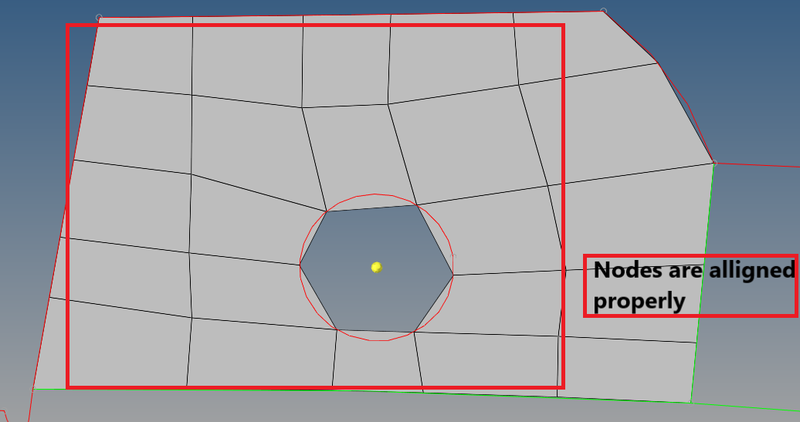
Figure 104-Nodes Alligned Properly. |
5:6 Using quality index clean up tools
SI.NO |
Tool |
Purpose of the tools |
1 |
Place Node |
Move the node along the plane or curvature of the surface or away from surface. |
2 |
Swap Edge |
Each time if we click an edge, it switches to the next valid configuration. |
3 |
Element Optimize |
To move the midnodes attached to the element we are optimizing, enabled the with attached midnodes checkbox. |
4 |
Smooth |
It is used to improve the element quality of the surface. |
5 |
Split/Collapse Edge |
To use the split edge tool, left-click on an edge. HyperMesh splits the elements that share the selected edge in a way that will achieve the optimum quality. |
6 |
Drag Tria Element |
To use the drag tria element cleanup tool, left-click on a tria element and drag it to a desired location. HyperMesh highlights the selected tria element in pink.Drag both trias to combine when they are facing opposite direction. |
7 |
Split Quad Element |
To split a quad element, left-click on the quad element you wish to split. HyperMesh splits the quad element into two tria elements. |
8 |
Combine Tria Element
|
To combine two tria elements, left-click on their shared edge. HyperMesh combines the two tria elements into one quad element. |
5:7 How to get Proper Mesh Flow ?
- After fixing the quality in mesh.Do the smooth operation on the meshed regions.
- You will get a proper mesh flow,While smoothening some elements may fail like 1 or 2,So try to clear them with distance tool.
- To use smooth tool,Go to 2D >> Smooth >> Elements >> Size Corrected >> Smooth.
- Smooth tool will improve element quality in a surface-based mesh or a mesh of solid elements using one or more algorithms that adjust node positions to moderate sharp variations in size or quality in adjacent elements.
- Iterations specifies the number of passes you wish the smoothing algorithm to run.

[Note: Smooth every region after meshing every region,Then only you will get good mesh flow.]
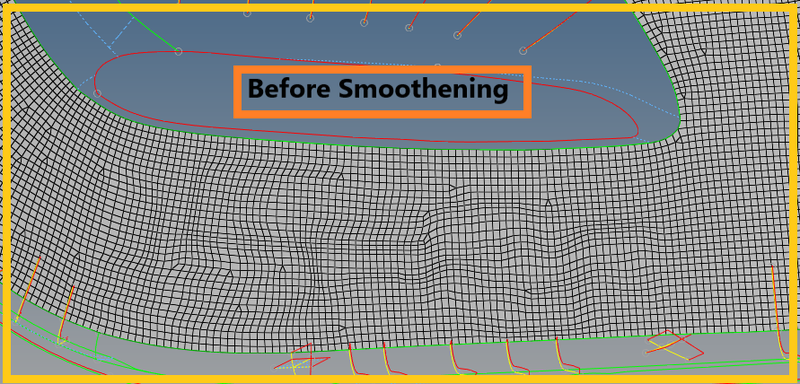
Figure 106-Before Smoothening. |
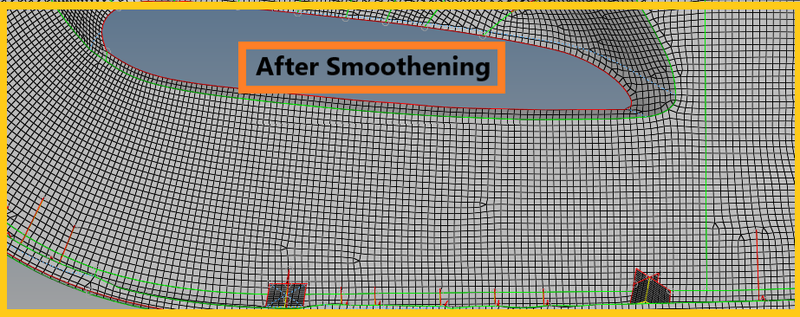
Figure 107-After Smoothening. |
5:8 Aligning the nodes across edges and align nodes to get proper mesh flow
- After smoothening the elements,Some elements may not be aligned.
- To make them align we can use align nodes tool to align them.
- Go to Geometry >> Node Edit >> Align >> 1st Node >> 2nd Node >> Align.
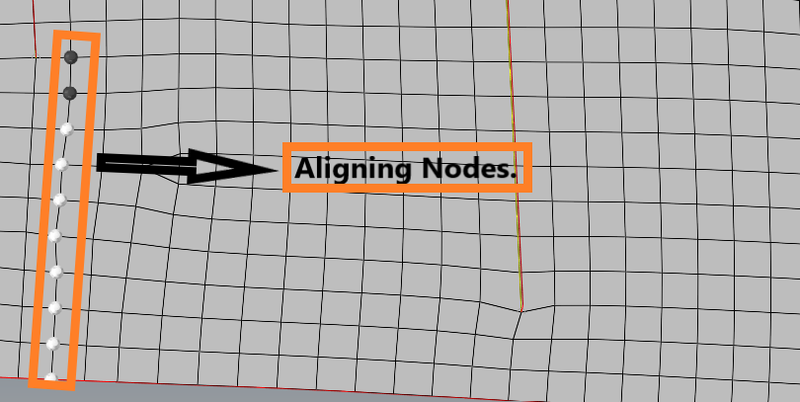
Figure 108-Alignining Nodes. |
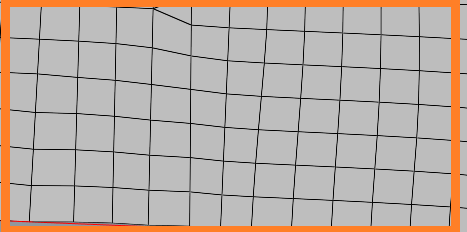
Figure 109-Aligned Nodes. |
- Align Nodes across edges - If the nodes are not projected to the edges,then you can use project tool to project or align them cross edges.
- To Project go to Tools >> Project >> To Line >> Select Nodes >> Normal Lines.
- It is used to project nodes or points to a line along a user-defined direction or the normal to the line selected.

Figure 110-Project Panel. |
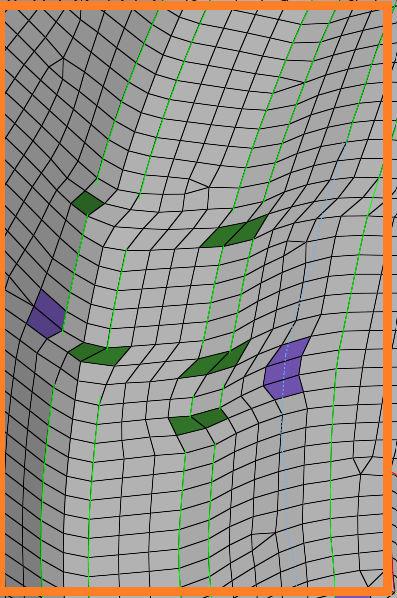
Figure 111-Element nodes are not projected to the feature lines. |
- Here this happens due to dragging trias from the feature lines.
[Note:Don't drag the trias away from the feature lines,If you drag,there will be no feature capturing.]
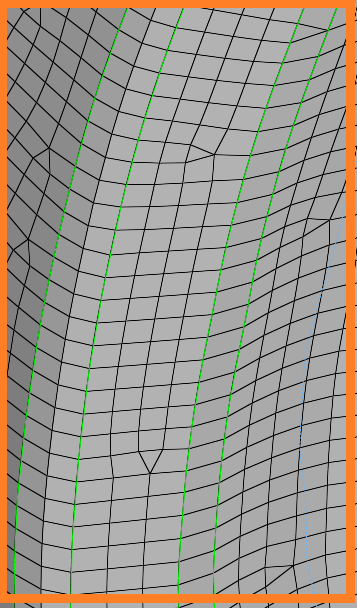
Figure 112-Projected to the shared edges using project tool. |
5:9 Manual Clean Up Using Distance[F4] and Translate[Shift +F4].
- We can use the Distance tool to determine the distance between two nodes/points or the angle between three nodes/points, or to change distances or angles.
- We can also fix the elements failing for the quality like
i) Minimum and Maximum Length
ii) Minimum and Maximum Quad
iii) Minimum and Maximum Tria
iv) Aspect Ratio
- Sometimes we can also fix warpage using distance tool.
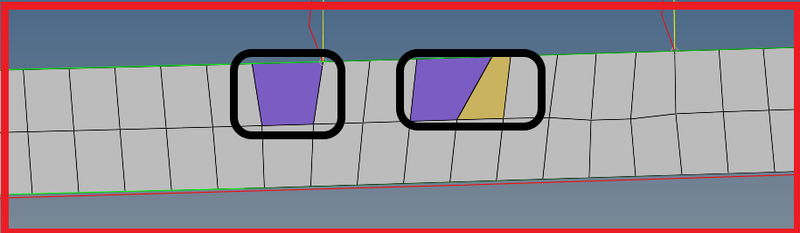
Figure 113-Elements Failing for Min and Max Length. |
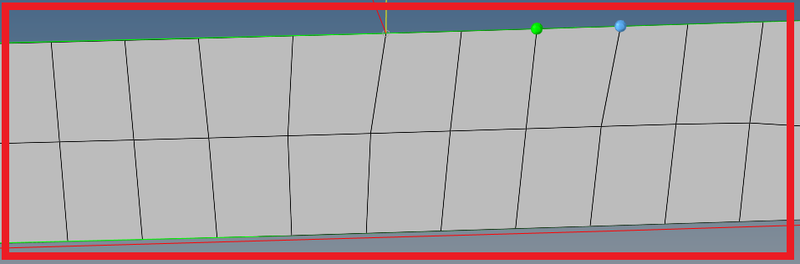
Figure 114-Elements failing for min and max length have been solved using distance tool. |
- Similarly we can fix elements failing for min and max quad,min and maax tria ,aspect ratio using distance tool,Sometimes we can also fix warpage.
- But better to use translate tool to fix warpage.
- We will be translating the some warpage angle to the neighbour element,by using translate tool we can easily fix the warpage.
5:10 Fix Warpage
- We can fix warpage by using translate tool.
- We will be translating the some warpage angle to the neighbour element.
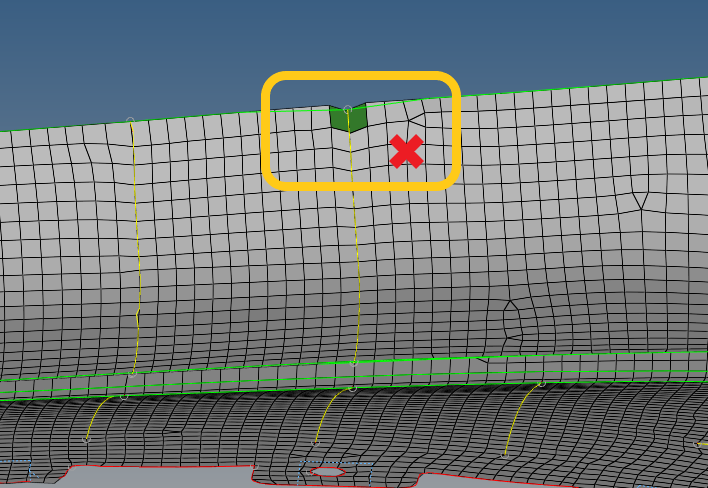
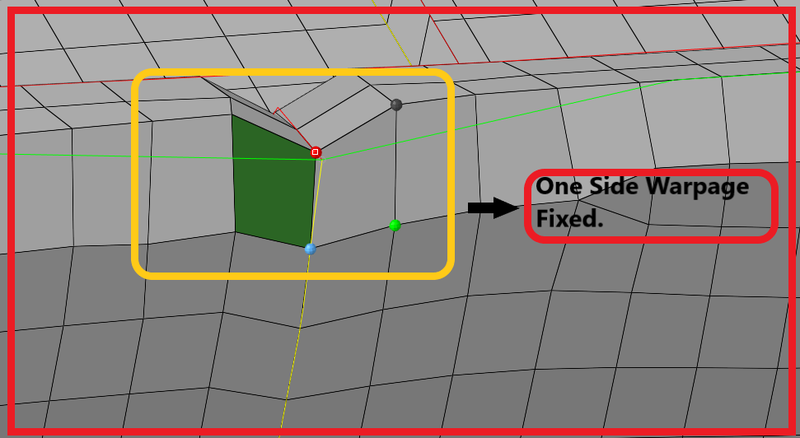
Figure 116-One side of warpage fixed. |
Figure 117-Both sides warpage has been fixed. |
- We can check the warpage angle using check elements [F4].
- Check warpage angle for neighbouring elements also.
- If the neighbouring elements have less warpage angle,we can translate some angle to that element.And then we can clear warpage.
- Go to Tools >> Check Elements >> Warpage.

Figure 118-Check Elements Panel. |
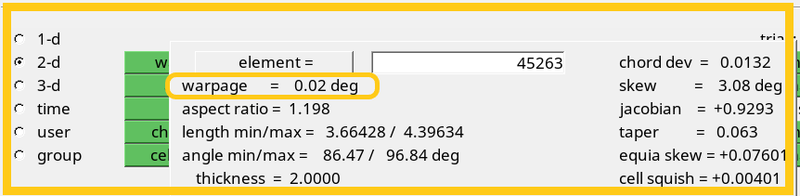
Figure 119-Warpage Angle. |
- If you click on the element failing for warpage,It will show the warpage angle.Here i clicked on the element which is not failing for the warpage angle.So the value is too less and it not failing.
- Now after meshing the entire component,Check for
i) Connectivity [Free Edges]
ii) Duplicates
iii) Normals
1) Check for Connectivity [Free Edges]
- Edge Tool will help us to find this error.
- Go to Too >> Edge >> Elements >> Find Edges.

- If we get the the edges with connectivity,there is no problem,If you get edges without connectivity,then you have to manually connect them with using replace tool.
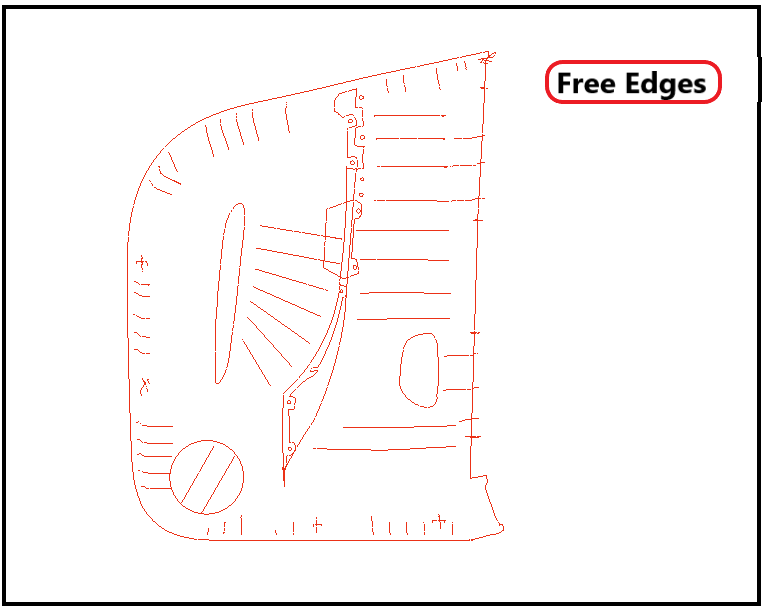
[Note:While checking free edges,Give the tolerance value as .01.If it is an assembly component,Give tolerance value as .01.It should not exceed more than .01 for assembly check.
If you give high tolerance and click preview equivalence,the software willl show you,many nodes are connected.So go give lower tolerance for the assembly components.]
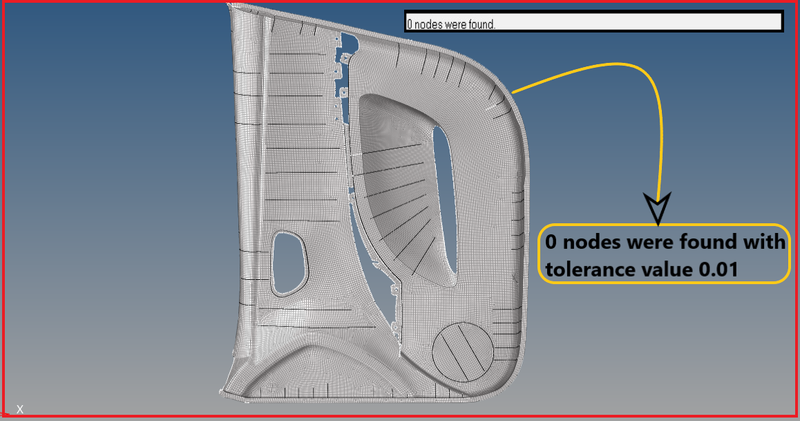
Figure 122-0 Nodes Found With Tolerance Value-0.01. |
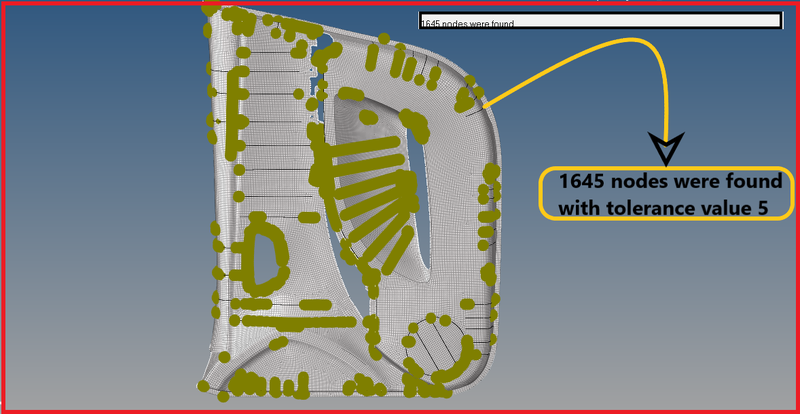
Figure 123-1645 Nodes Found With Tolerance Value 5. |
[Note:Give the tolerance value-0.01 for the assembly check.Don't give higher tolerance,If you give higher,it will result as shown in fig 123.]
2) Check for Duplicates
- Now check for the duplicate elements
- To check duplicates,Go to Tool >> Check Elements >> Duplicates.
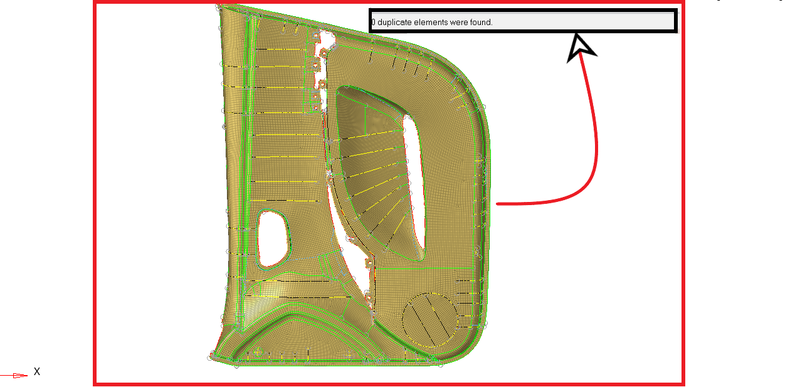
Figure 124-0 Duplicates Were Found. |
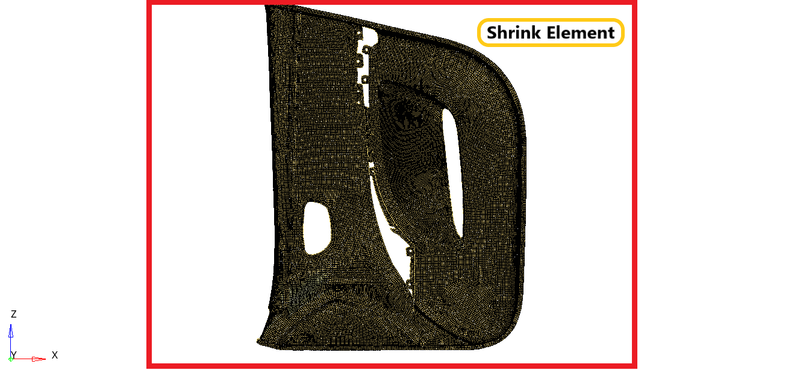
Figure 125-Shrink Element. |
- We can aslo check duplicate elements by switching to the shrink elements.
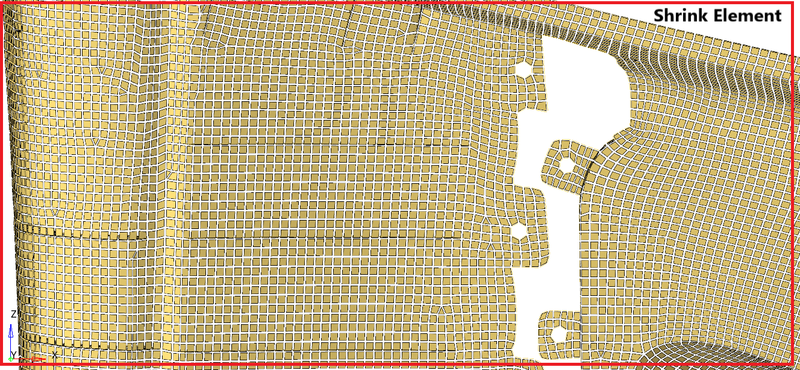
Figure 126-Proper Representation of Shrink Element Mode. |
3) Check for Normals
- We can Use the Normals to display and reverse the normals of elements or surfaces. The orientation of element normals can also be adjusted. The normal of an element is determined by following the order of nodes of the element using the right-hand rule.
- Normals can be reviewed showing a vector or by colors. A vector shows in positive normal direction, while the color mode shows the positive side of a shell or surface in red and the negative side in blue.
- To check normals go to Toolbar >> Mesh >> Check >> Elements >> Normals.
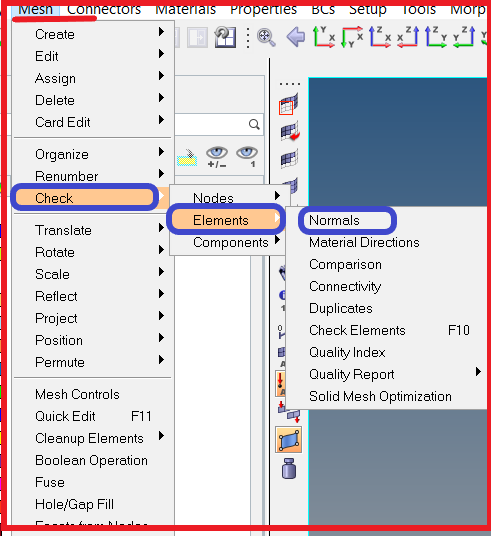
Figure 127-Check for Normals. |

Figure 128-Normals Panel. |
Figure 129-Checking for Normals View 1. |
Figure 130-Checking for Normals View 2. |
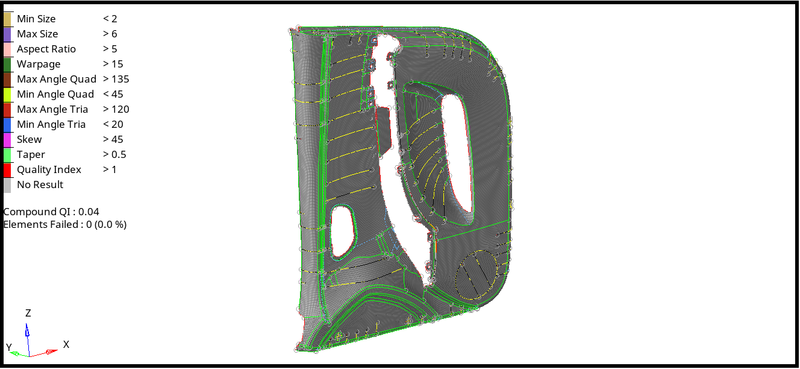
Figure 131-Final Mesh Model. |
Figure 132-Low Tria Percentage-1.4% |
Phase 6 - Assigning Thickness to the Elements
6:1 Check thickness in geometry
- First check the thickness in every region and then assign a thickness by creating a collectors and organize it to that newly created collectors.
- Check thickness by distance tool or by dimensioning tool.
- Geometry >> Distance >> Two Points >> Point1,2.
- Geometry >> Dimensioning >> Point1 >> Point 2.
6:2 Create a Collector
- After measuring thickness,Create a component and rename it as Middle Surface_1 2.8mm [Base Surface].
- Don't organize elements in the base surface,Just rename it as Middle Surface_1 2.8mm.
- Organize the elements in ribs and cylindrical ribs to the newly created collectors.
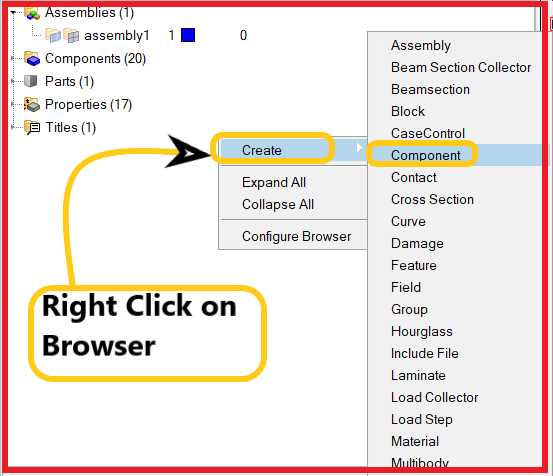
Figure 133-Browser Panel. |
- Take a average thickness and assign it to the elements.
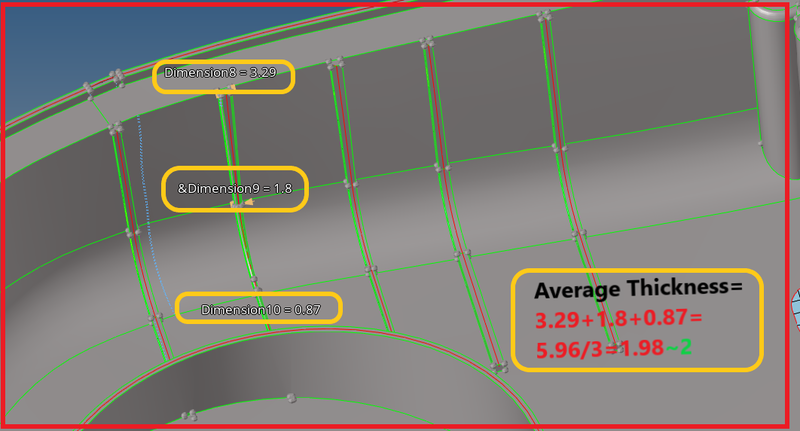
Figure 134-Average Thickness. |
- Take thickness as shown in the fig 134.
- Take the tolerance value as .2 and proceed.
- Now organize the elements in the ribs to the newly created collector called Rib_2mm.
- Similarly do the same thing for every rib region in the component.
6:3 How to Organize Elements
- We can use the collectors to organize entities such as elements, loads, and systems into their corresponding components, load collectors, system collectors, and so on.
- Select an entity type to copy/move, then use the selector to select specific entities to copy/move. The current collector serves as the default destination.
- Go to Tools >> Organize >> Elems [Select by Face/Geom] >> Check Current Comp >> Move.

Figure 135-Organize Panel. |
6:4 Assign Property to the Components
- First Create a property on the browser.
- To create a property,Right click on browser >> Create >> Property.
- After Creating a property rename it and start assigning thickness to the components.
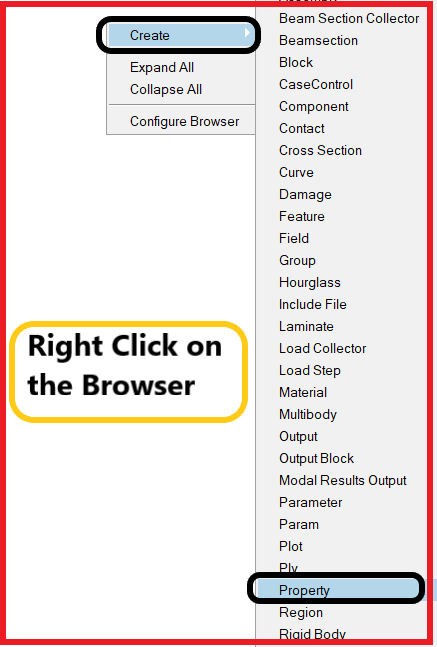
Figure 136-Browser Panel. |
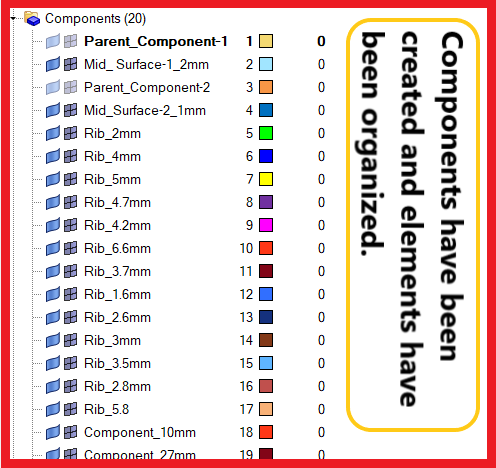
- Now switch to the component view mode and check the model whether the elements are organized properly to the respective collectors which created newly.
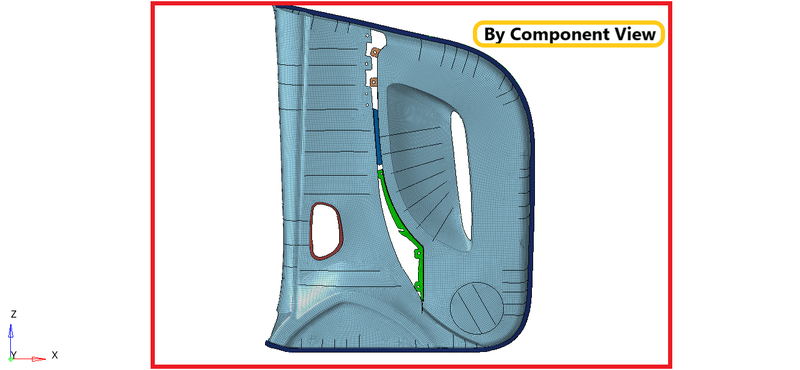
Figure 139-By Component View 1. |
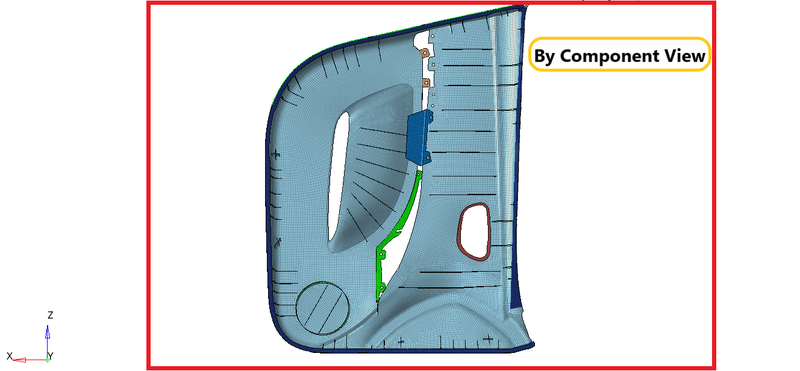
Figure 140-By Component View 2. |
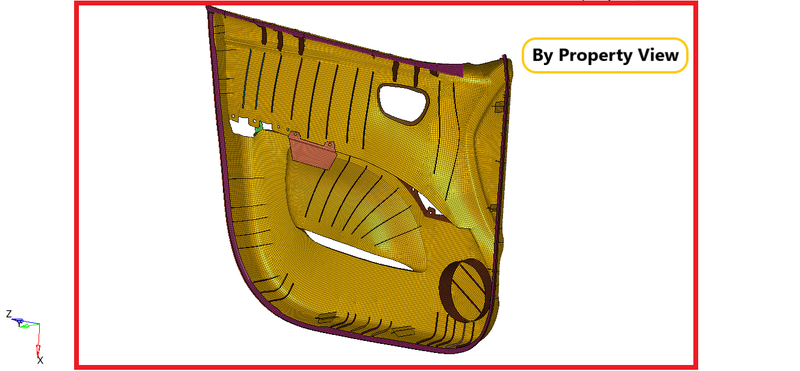
Figure 141-By Property View |
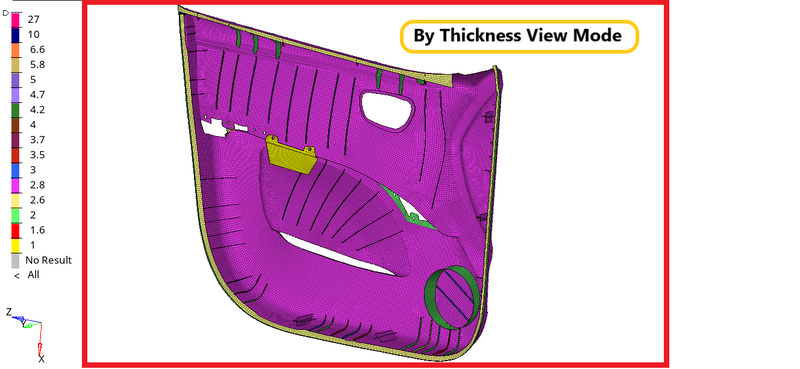
Figure 142-By Thickness View. |
- Now check the complete model,Whether every property has been assigned to the collectors.
- To Check Go to Menu Bar >> Tools >> Component Table.
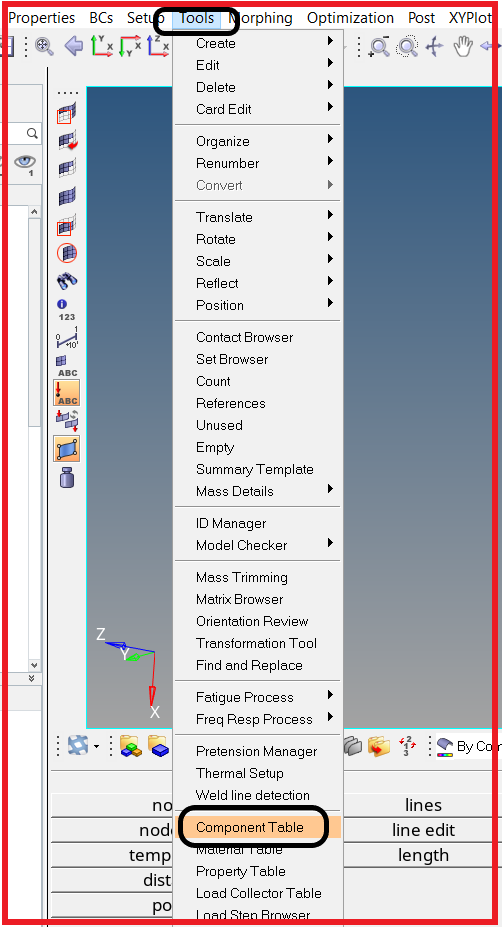
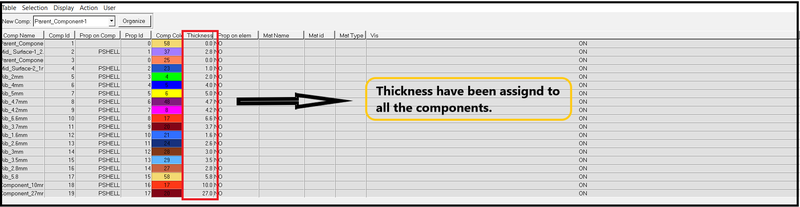
Figure 144-Component Table. |
- Now Switch to the 2D Detailed Element Representation,The thickness have been applied to the every region.
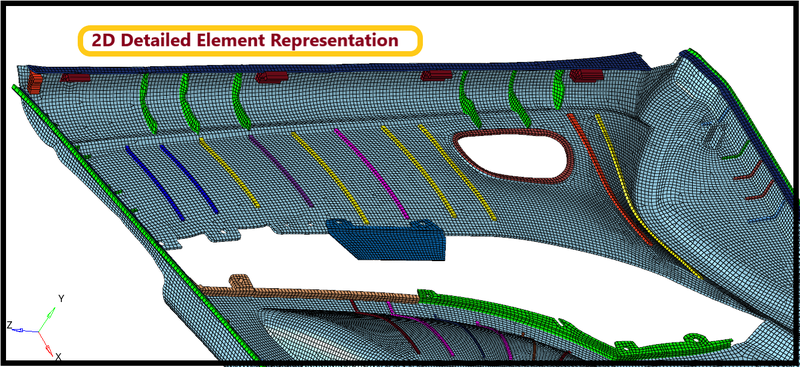
Figure 145-2D Detailed Element Representation. |
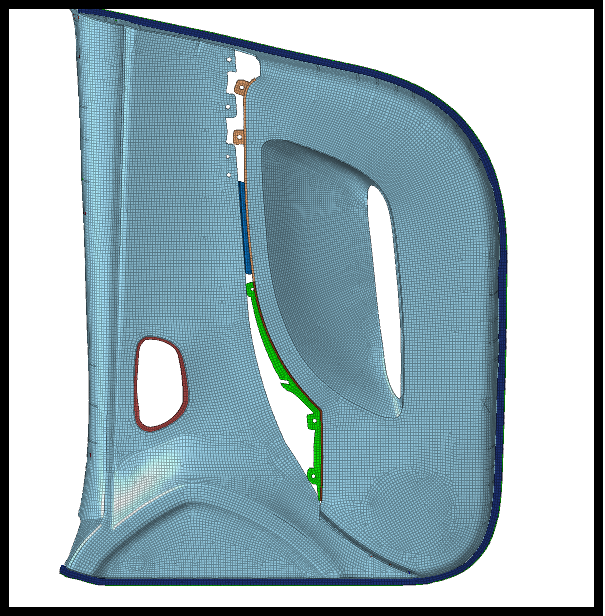
Figure 146-Detailed Representation View 1. |
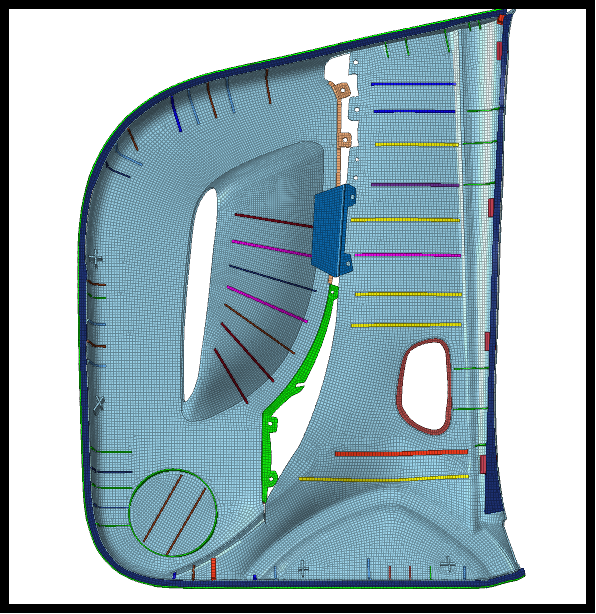
Figure 146-Detailed Representation View 2. |
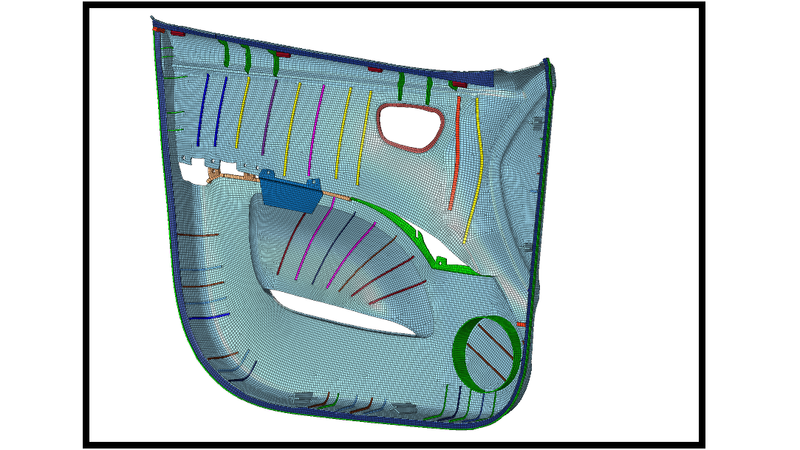
Figure 147-Isometric View. |
Phase 7 - Final Cad Model Image
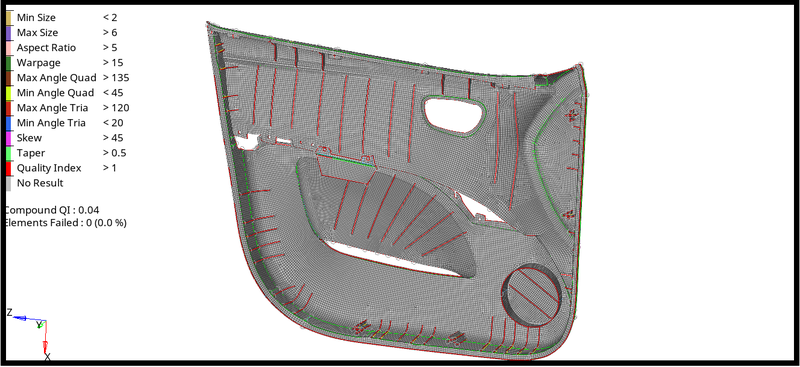
Figure 148-Final Meshed FE Model. |
_1623779814.png)
Figure 149-Final Geometry Clean Up. |
_1623779941.png)
Result -
- Hence the mid surface has been extracted to the parent component.
- Hence there are no surface deformations in the geometry.
- A well connectivity has been established between the surfaces.
- The features have been captured properly.
- A good mesh flow have been achieved with the zero elements failing for quality
- Hence tria percentage with 1.4 % have been achieved.
Learning Outcome and Conclusion -
- In this project,I came to know
- How to extract the mid surface manually for the complex plastic components.
- How to clean complex geometry .
- How to generate a proper mesh flow with low tria percentage.
- How to assign thickness to the components.