Batch Meshing and Assigning Non-Linear Material to the Component's.
Objective -
- To perform a batch mesh for the given component's.
- To assign a non-linear material and property cards for the component's.
- To create a parrameter and criteria file for batch meshing.
Procedure -
Hood Model
Phase 1-Importing
- Hence we are importing a given CAD geometry into hypermesh.
- There are file formates like IGES,STEP,Parasolid where we can import these file formats into any CAD,CAE Softwares.
- But in hypermesh we can only import three file formates like
- IGES [Initial Graphics Exchange Specification].
- STEP [Standard for the Exchange of Product Model Data].
- Solidworks.
- IGES,STEP,These two are standard file formats which are used most in industries.But now a days in industries,they are aslo using parasolid file format.
Figure 1-Imported Hood Model |
Phase 2-Examining
- Before working on the model.We have to check the geometry if there are any errors like
- Damaged Geometry.
- Free edges in unnecessary areas.
- Unnecessary points on the lines.
- Unnecessary Connections and connectivity error.
[Note:For this challenge,No need to examine all those things which are mentioned above,We are focussing on only batch meshing,So no need to examine.]
- By assessing the hood model.We can see there will be four components in the hood.
- Inner Extract Body
- Outer Extract Body
- Hinge Reienforcement Extract Body
- Latch Reienforcement Extract Body
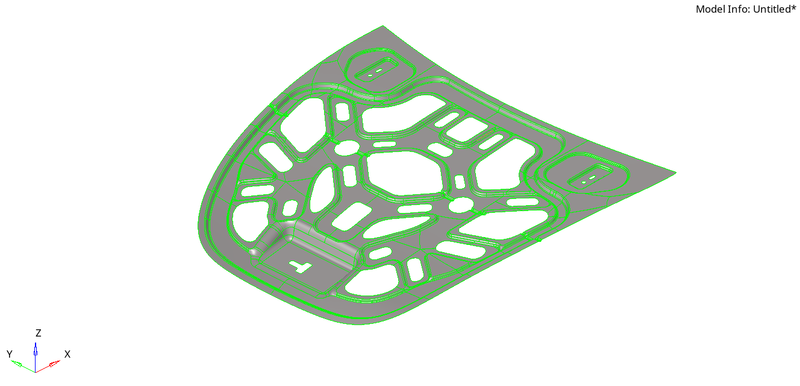
Figure 2-Inner Extract Body |
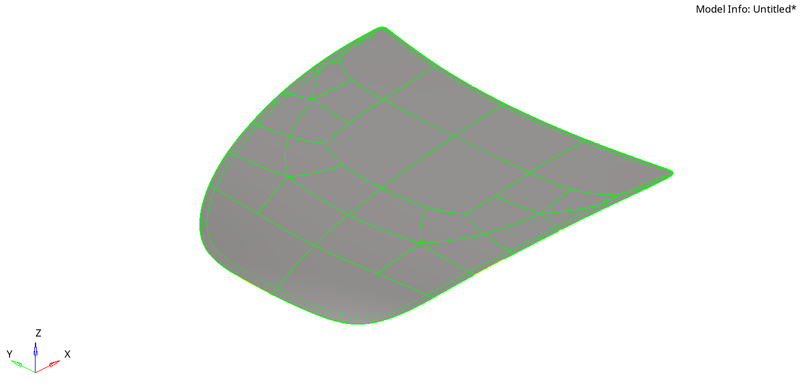
Figure 3-Outer Extract Body |
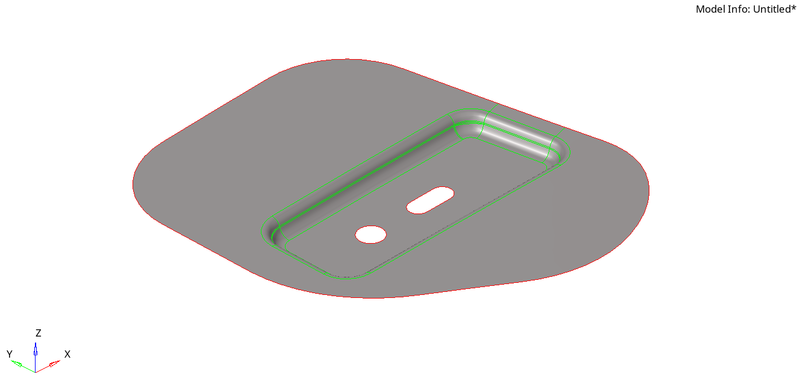
Figure 4-Hinge Reienforcement Extract Body |
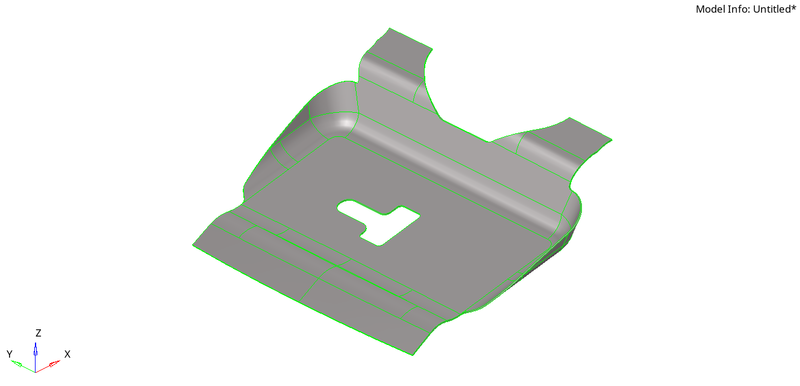
Figure 5-Latch Reienforcement Extract Body |
Phase 3-Batch Meshing
- A Brief Introduction to Batch Meshing-
- What is Batch Meshing ?
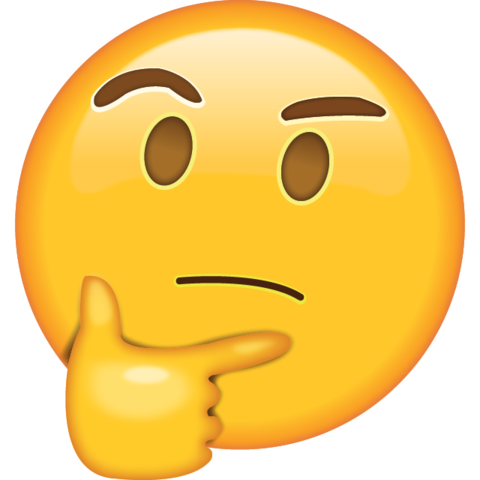
- Batch Meshing is the fastest way to meah the component's.Not only mesh,It will do many things.
- It can perform geometry cleanup and automeshing (in batch mode) for given CAD files.
- Batch Mesh performs a variety of geometry cleanup operations to improve the quality of the mesh created for the selected element size and type.
- It will do cleanup operations like
- Equivalencing of "red" free edges,
- Fixing small surfaces (relative to the element size),
- Detecting features.
- Batch Mesh also performs specified surface editing/defeaturing operations such as
- Removal of pinholes (less than specified size), removal of edge fillets, and addition of a layer of washer elements around holes.
- It will also add washers around the bolted locations.
- It will mesh the model with special optimization routines to create the best quality elements.
- It will run in GUI mode or a fully automatic batch mode,both requiring minimal inputs for automatic meshing.
- There are two main inputs for a user to run batchmesh and get the proper mesh flow one is called as criteria file(.criteria) and another is parameter file(.param), where in param file will be having all the options that the batchmesher has to run during the topology clean up post mid surface extraction, like
- Adding washer around holes,
- Maintain the number of elements on fillet,
- Global geometry stitch tolerance,
- Element movement to assist auto clean up all this data are feed on the parameter tab and saved as .param file which can be opened in any text-pad editor, on the other end criteria file will have all the element quality criteria.
- In the run status on the batchmesh,User can see the quality report of how many failures happenes at each stage of cleanup or iterations it goes on.
- Additional Thing [QI Optimization]-
- All user-defined criteria determine the quality index (QI) of a model.
- The QI value is used to assess thepotential of each geometry cleanup and meshing tool, and apply them accordingly.
- QI optimized meshing and node placement optimization are performed to obtain the best quality meshing.
- Finalresults are stored in a HyperMesh database file.
Phase 4-Start Batch Meshing
4:1 Batch Mesh/QI Optimize Sub Panel-
- Use the Batchmesh/QI Optimize subpanel to perform Quality Index meshing, an iterative automatic mesh generation method driven by element quality criteria.
- During the mesh generation process, the quality index of the mesh is determined by evaluating each element against a set of element quality tests. If all required element quality criteria are passed, then that element has a perfect quality index of zero.
- As the element quality deteriorates, the quality index value increases; a lower quality index score indicates an element more closely meets the ideal quality requirements.
- The compound quality index sum of the quality index values for each of the elements is included in the current meshing area.
- The quality index value itself has no direct physical meaning; it is a way to compare one generated mesh pattern against another pattern generated for that same area.
- The quality index based mesh optimization routine attempts to modify the mesh pattern and apply node smoothing routines to obtain a lower overall quality index value.

Figure 6-Batch Mesh Sub panel |
- Go to 2D >> Automesh >> Switch to Batch Mesh/QI Optimize >> Surface >> Disaplayed >> Batch Mesh in Drop Down Menu >> Parameter File >> Criteria File >> Mesh.
- Select the parameter file and criteria file.
- To select parameter file.Go to Local Disk ‘C’ → Program Files → Altair → 2020-edu → hwdesktop → hm → Batchmesh.
- To select criteria file.You have to create a criteria file.
4:2 How to Create a criteria file ? 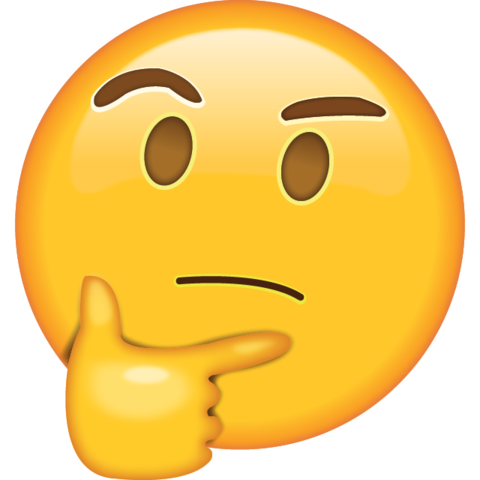
- Go to User Interface panel >> Preferences >> Criteria File Settings >> Criteria Panel Will Open.Give the values to the parameter's and save it in your disk.
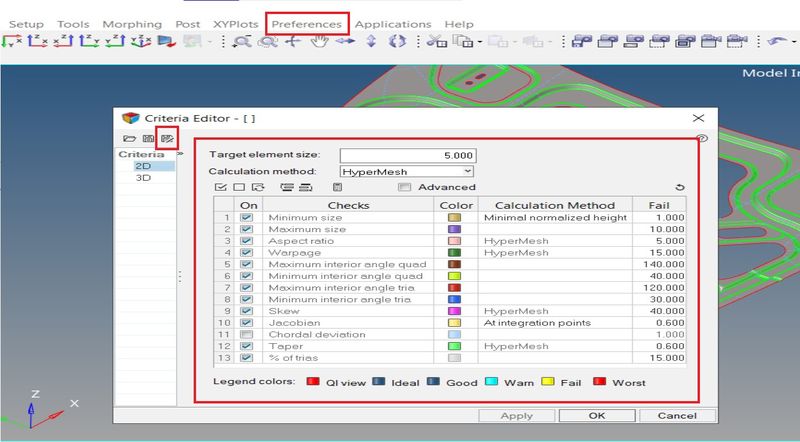
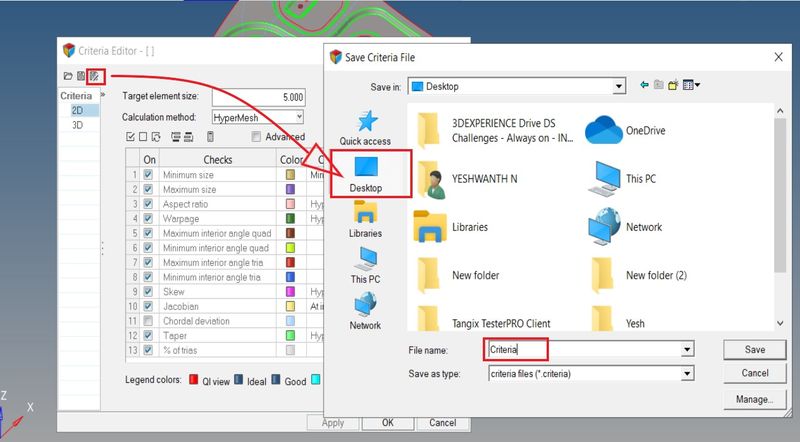
Figure 8-Creating and Saving Criteria File in Desktop |
4:3 How to Create a parameter file ? 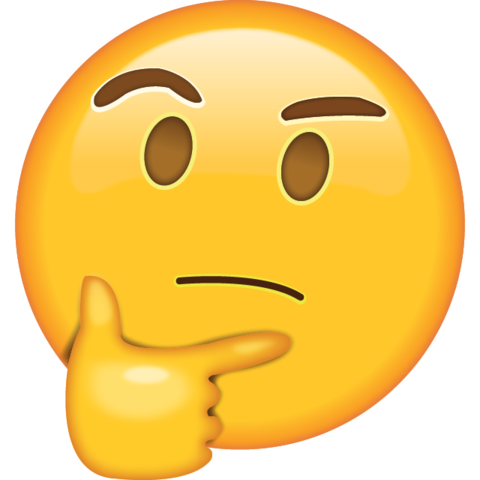
- Go to User Interface panel >> Preferences >> Parameter File Settings >> Parameter.Parameter Panel Will Open.Give the values to the parameter's and save it in your disk.
- For this challenge,We will not be creating a parameter file.We will be select the file from Local Disk ‘C’ → Program Files → Altair → 2020-edu → hwdesktop → hm → Batchmesh.
- If we want we can create parameter file and save it in our disk.
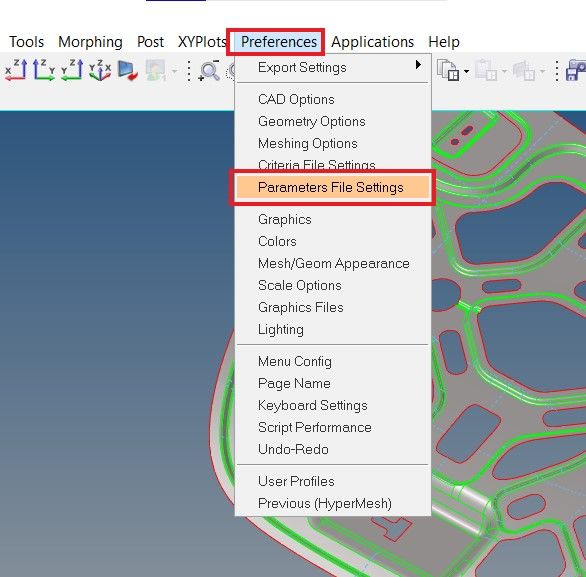
Figure 9-Parameter File Settings |
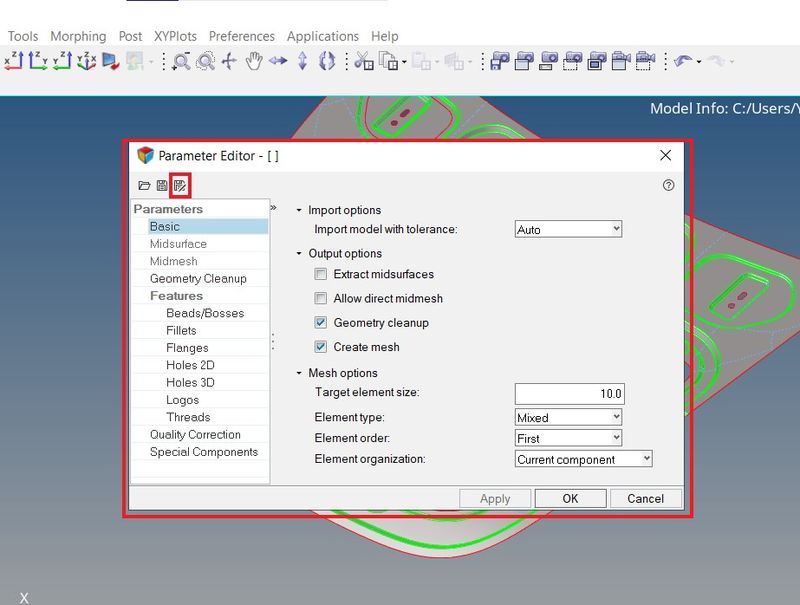
Figure 10-Give Approproiate Values to the Parameters and Tick Checkbox for Appropriate Parameters |
Figure 11-Selecting the parameter file |
- While doing Batch Mesh for the component's.
- Make Sure,To create the duplicate collectors and organize the surfaces to that collector.
4:4 Is it necessary to create duplicate collectors ? 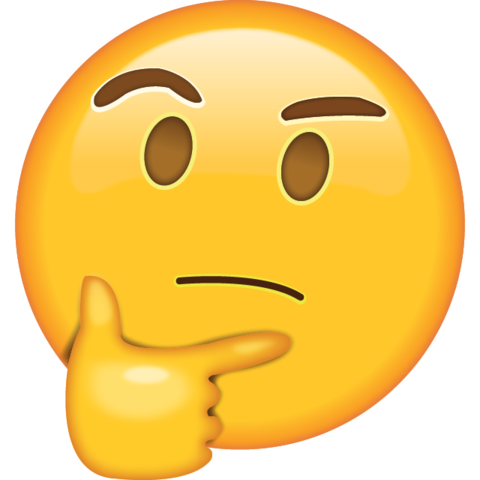
- If we want,We can create the collector's to keep the parent component in that.
- While Batch meshing,It will create the Mid surface,Do some geometry clean up,Delete parent component and mesh on the mid surface.
- To check whether the batch mesh is creating the mid surface in the middle of the component or not.
- To check this one,We are creating a collector and organizing it to that collector.
4:5 How to Create Duplicate Collector's ? 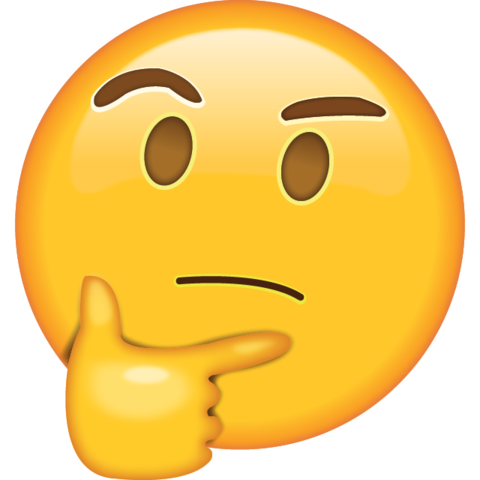
- Right click on the component and make it as duplicate,The collector will be created and it will show in the browser.
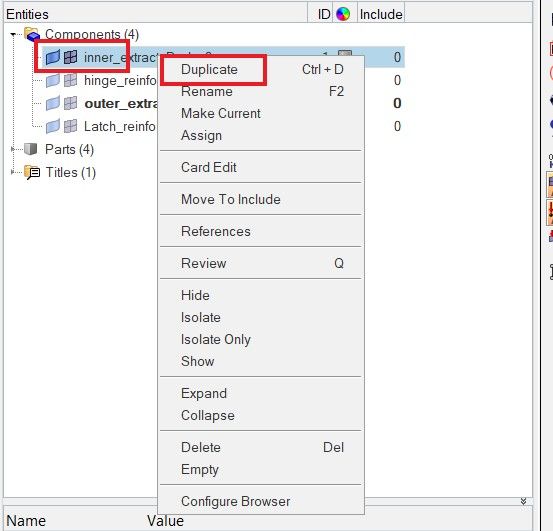
Figure 12-Making Component Duplicate to Create New Collector. |
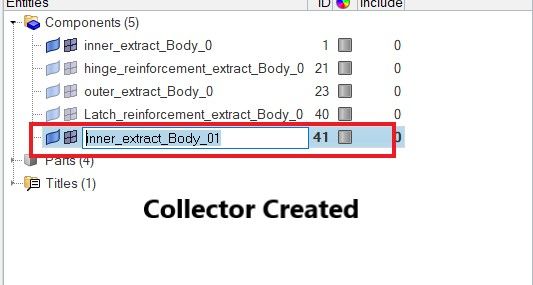
- Now Organize the Parent component to the new collector.
- While organizing,make sure to make it as duplicate and organize it to the new collector.
- Go to Tool >> organize >> collector:surface by displayed and make it as duplicate from orginal component >> dest component:inner_extract_Body_01 >> Move.

Figure 16-Surface has been duplicated |
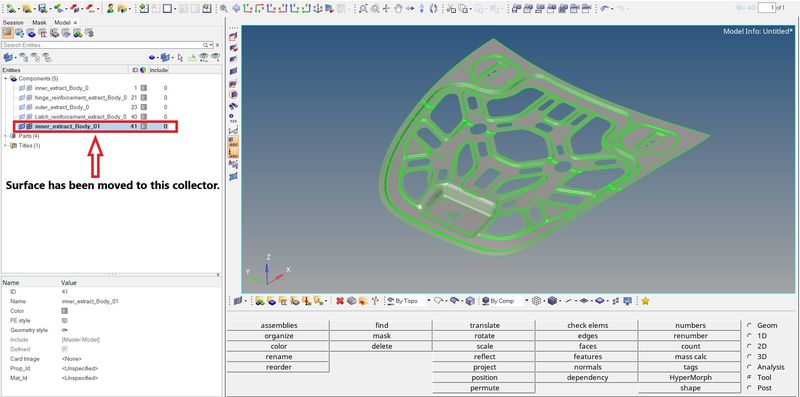
Figure 17-Surface moved to the collector |
- Batch Mesh-2D >> Automesh >> Switch to Batch Mesh/QI Optimize >> Surface >> Disaplayed >> Batch Mesh in Drop Down Menu >> Parameter File >> Criteria File >> Mesh.
- Select the Parameter and Criteria File.
- Param_File_Path-Name of the text file containing parameters for meshing. If this parameter is NULL then parameters specified by members element_size, element_order, mesh_type, and mesh_option_flags are used to control mesh generation.
- Criteria_File_Path-Name of the text file containing criteria parameters for meshing.
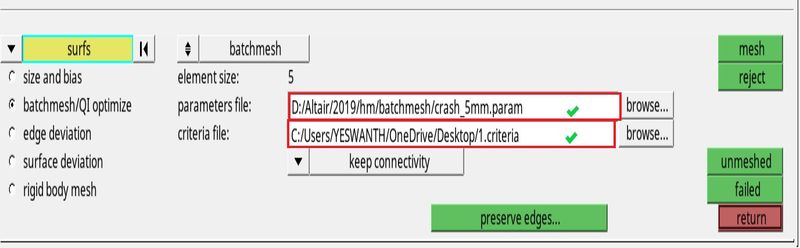
Figure 18-Parameter and Criteria File Selected |
- Select the surfaces by displayed and start Batch Meshing the component Hood given to us.
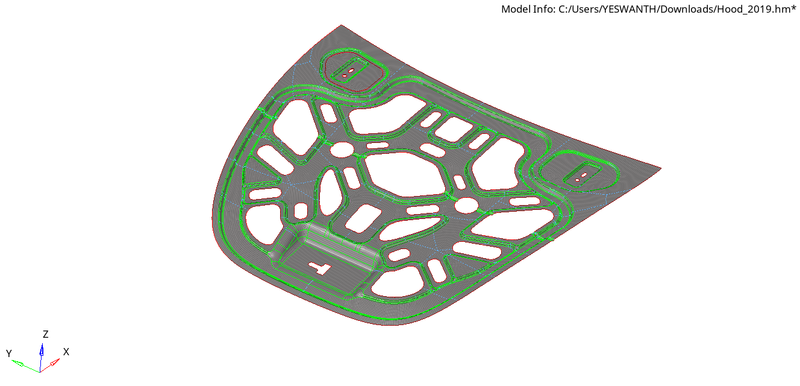
Figure 19-Batch Mesh Done on Inner Extract Body |
- Now the batch mesh has been done for the Inner Extract Body,Do the same thing for other component's also.
[Note:Batch Mesh dosen't work for every component.It will work for some simple models.If we do batch mesh on the complex geometry,It will create lot trias,So this the reason,why batch mesh is not trusted for the complex geometries.]
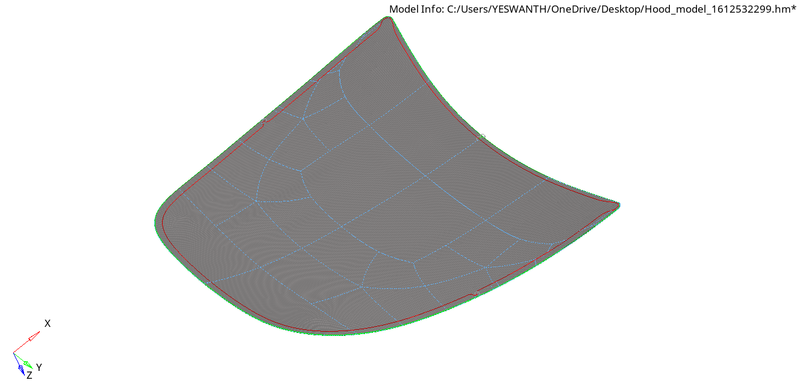
Figure 20-Batch mesh Done on the Outer Extract Body |
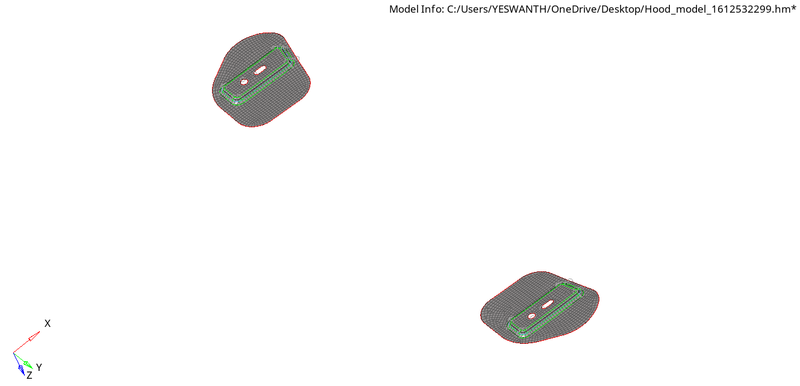
Figure 21-Batch mesh Done on the Hinge_Reinforcement_Extract |
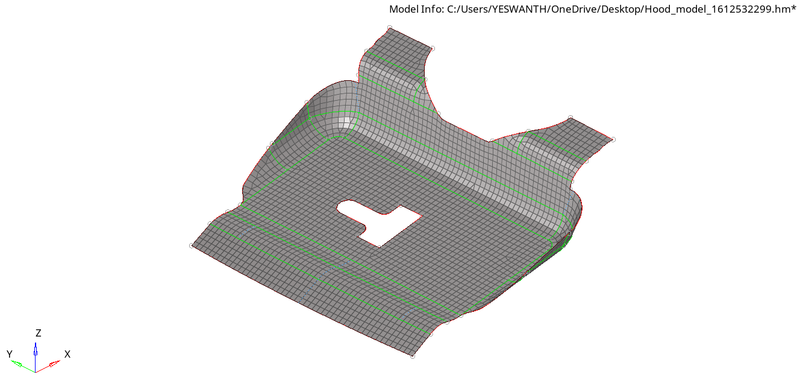
Figure 22-Batch mesh Done on the Latch_Reinforcement_Extract |
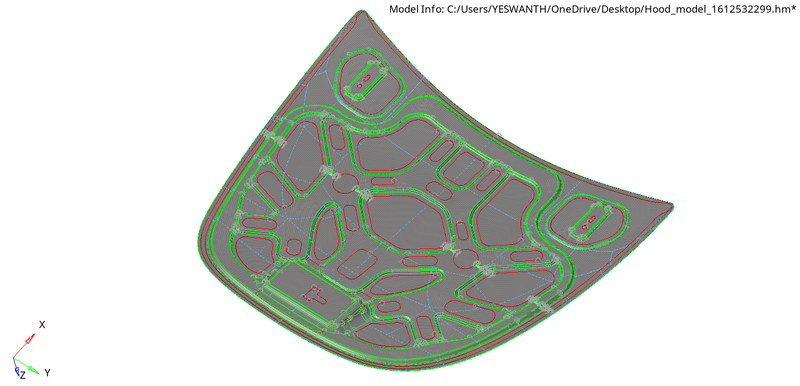
Figure 23-Batch Mesh Done on Hood |
- Do the same procedure to the Fender Model also,what you done for the previous component.
Fender Model
- Batch Mesh-2D >> Automesh >> Switch to Batch Mesh/QI Optimize >> Surface >> Disaplayed >> Batch Mesh in Drop Down Menu >> Parameter File >> Criteria File >> Mesh.
- Select the Parameter and Criteria File.
- Param_File_Path-Name of the text file containing parameters for meshing. If this parameter is NULL then parameters specified by members element_size, element_order, mesh_type, and mesh_option_flags are used to control mesh generation.
- Criteria_File_Path-Name of the text file containing criteria parameters for meshing.
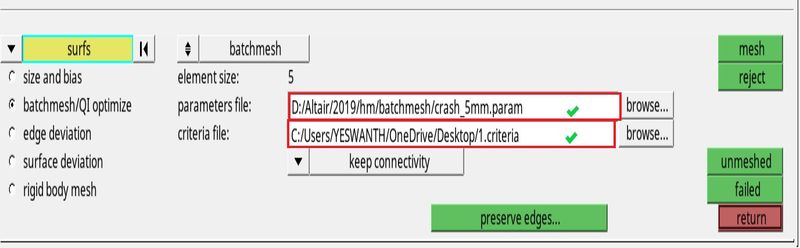
Figure 24-Batch Mesh Sub Panel |
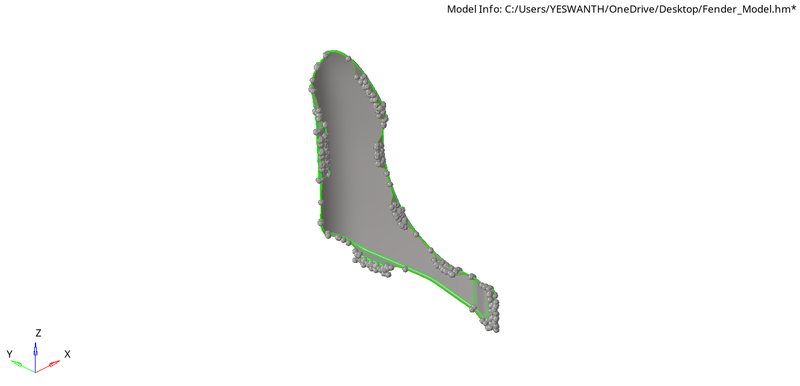
Figure 25-Imported Fender Model |
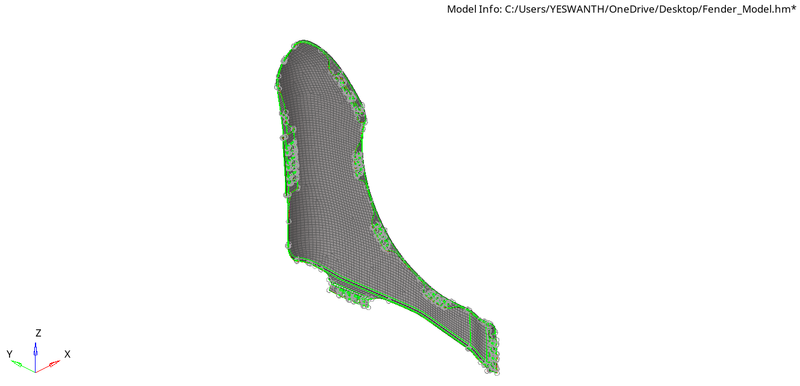
Figure 26-Batch Meshed Hood Model |
Phase 5 - Assign Non-Material to the Component's
5:1 Intro to Non-Materials-
- Material nonlinearity is a concern whenever the response at the operating loads causes strain levels in a material beyond the portion of the stress-strain curve that can reasonably be approximated as linear.
- Many materials have curves that deviate small amounts from linear for large amounts of strain so that, with all the other uncertainty in the model, there would be little value in a nonlinear material model.
- On the other hand, many curves deviate from linear almost immediately to such a degree that only the roughest trend studies can be made with a linear approximation.
- The constant of proportionality in a linear material model is Young’s Modulus. This represents the slope of the linear portion of the stress-strain curve (see image below).
- For highly non-linear materials, this modulus may only be applicable at very low strains.
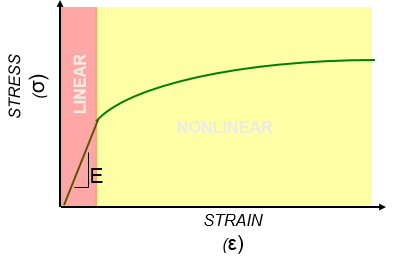
Figure 27-Stress Strain Curve |
- Nonlinear material models of common engineering materials are defined by specifying their stress-strain curves.
- Most stress-strain curves represent only the tensile response. When a material has the same response in tension and compression, it is said to be symmetric.
- Cast iron is a good example of an asymmetric stress-strain behavior as it is stronger in compression than tension.
5:2 Types of Non-Linear Materials-
- Nonlinear elastic
- Bi-linear elasto-plastic
- Multi-linear plastic
- Hyperelastic
- Viscoelastic
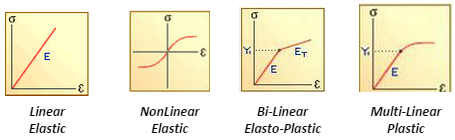
Figure 28-Stress Strain Curves for Non-Linear Materials |
- A nonlinear material model can be defined as nonlinear elastic where the part returns to a zero strain state when the load is removed, or elasto-plastic where permanent strain begins to accumulate after reaching the yield strength of the material.
- Additionally, an elasto-plastic stress-strain curve can be input as bi-linear, where only an elastic modulus and a plasticity or hardening modulus are entered. It can also be defined as a multi-linear stress-stress curve where the true nonlinearity of the plastic range can be captured with a series of points.
Phase 6-How to Create Material & Property Card for the Component's ? 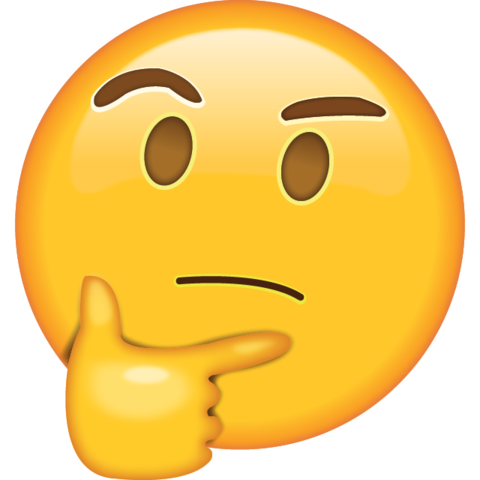
[Note:Matrial Card is Purely Solver Oriented.For Different Solvers,The Name of the Material will be Different.]
- Right Click on Browser >> Create >> Material.
- After creating a material,rename it as steel,Cause you will be giving mechanical propeties of steel.
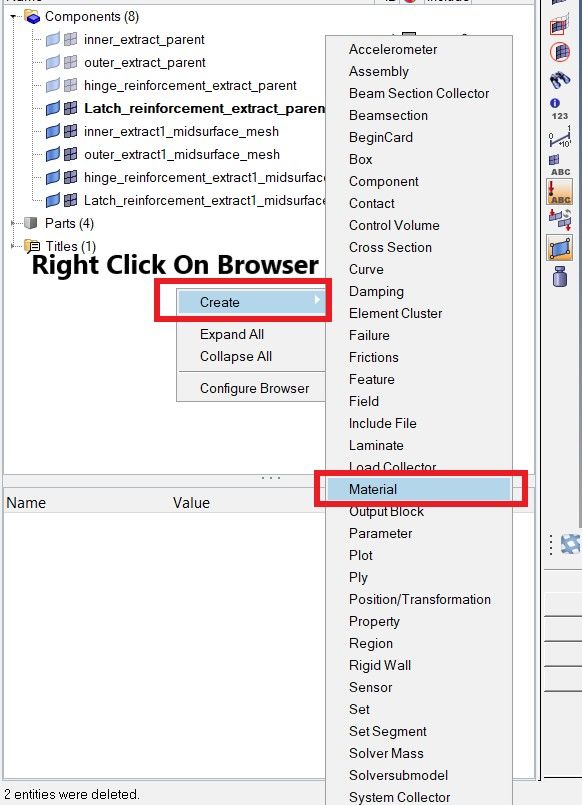
Figure 29-Material Creation |
- If you click on the material steel,You will be seeing the property panel for the material steel.
- Give the mechanical properties of steel in the property panel.
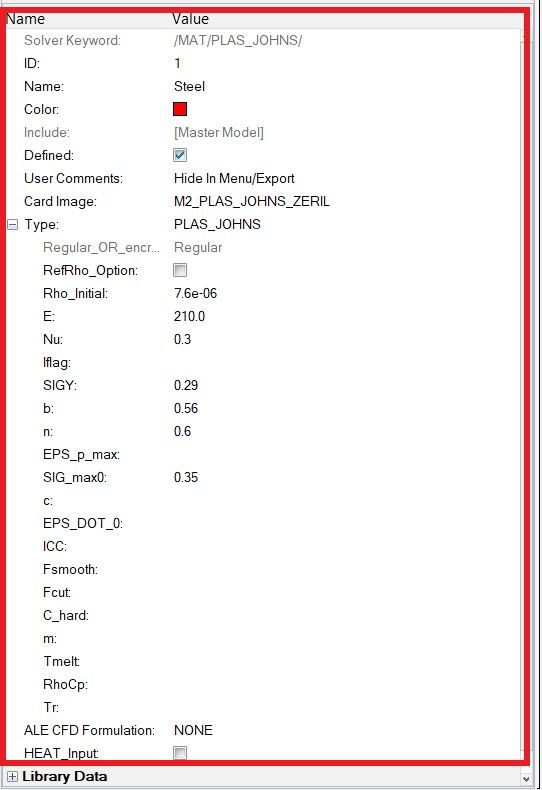
Figure 30-Mechanical Properties of Steel |
- Here we will be giving Card Image as M2_Plas_JOHNS-ZERIL.
- The Card Image is the type of a specific entity.
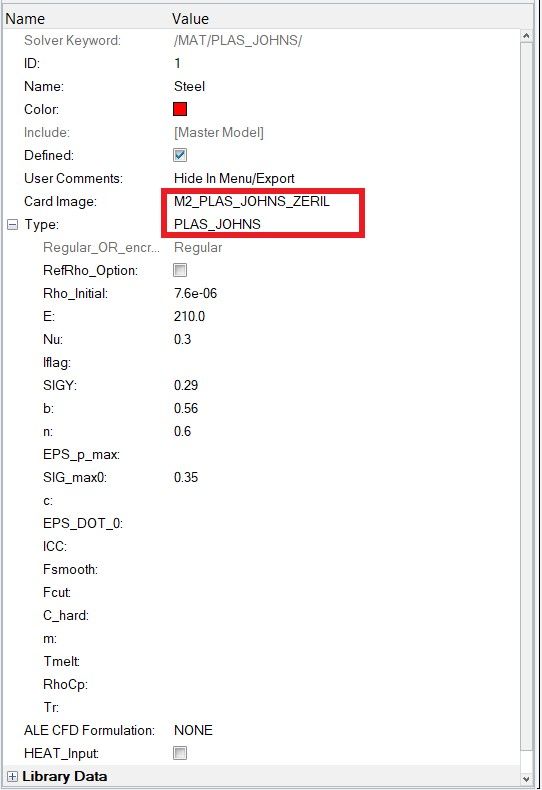
Figure 31-Card Image_M2_Plas_JOHNS-ZERIL |
Parameters Terms in Material Card Image Panel-
- Rho_Initial-Initial Density
- E-Young's Modulus
- Nu-Poisson Ratio
- Iflag-Input type flag
- SIGY-Yield Stress
- b-Hardening
- n-Hardening Exponent
- EPS_P_Max-Failure Plastic Strain
- SIG_Max0-Maximum Stress
- c-Strain Rate Coefficient
- EPS_DOT_0-Reference Strain Rate
- Fcut-Cutoff Frequency for Smoothening
- Chard-Hardening Coefficient
- m-Temperature Exponent
- Tmelt-Melting Temperature
- RhoCp-Specific Heat Per Unit of Volume
- Tr-Initial Temperature
M2_PLAS_JOHNS-ZERIL-
- This law represents an isotropic elasto-plastic material using the Johnson-Cook material model.
- This model expresses material stress as a function of strain, strain rate and temperature. A built-in failure criterion based on the maximum plastic strain is available.
- After creating the material card,Assign it to the component's.
- To assign material to the component's,Right Click on the Meshed Component >> Create >> Material.
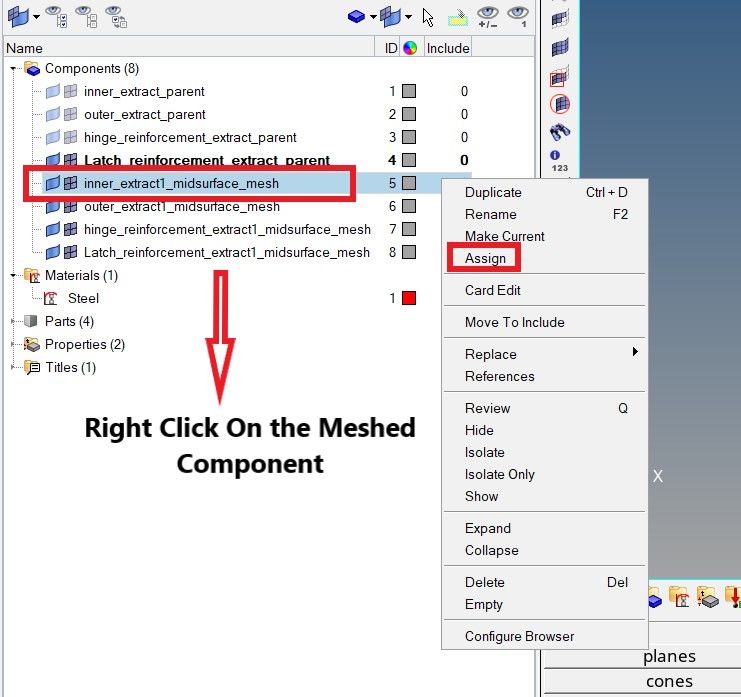
Figure 30-Assigning Material |
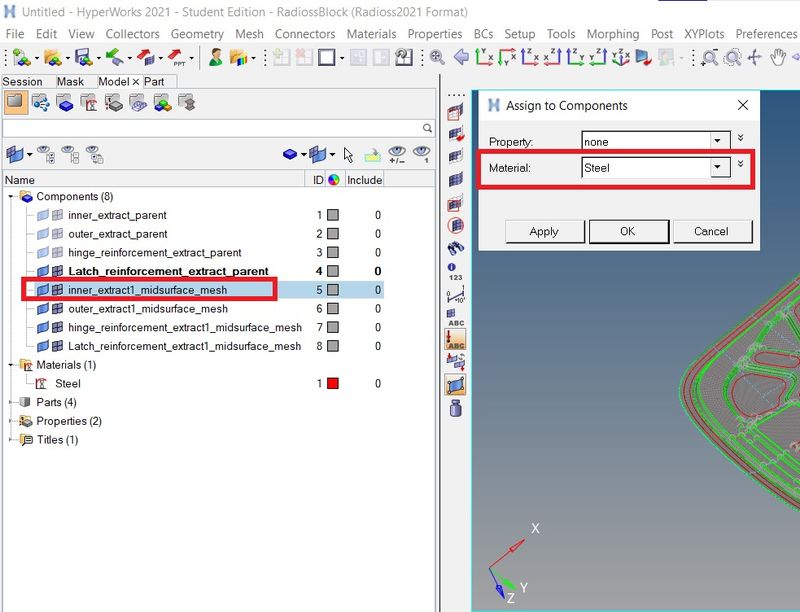
Figure 31-Assigning Material to the Meshed Component |
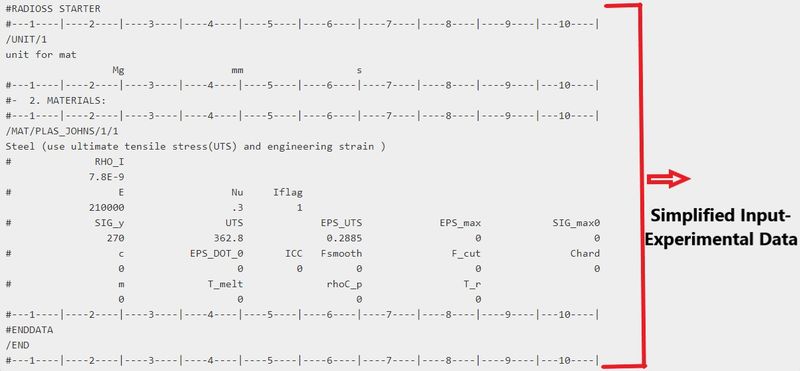
Figure 32-Simplified Input |
6:1 How to Create Property Card for the Component's ? 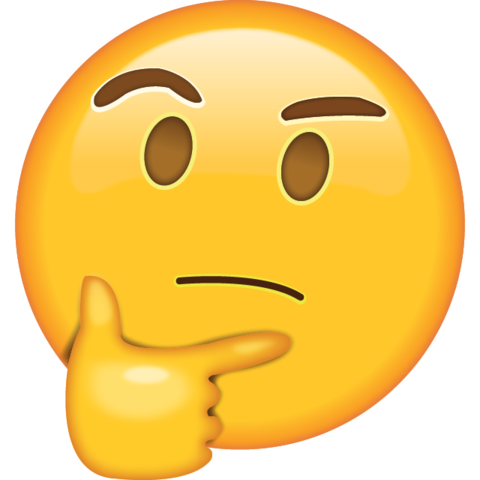
- Right Click on Browser >> Create >> Property.
- After creating a property,Rename it as Inner_Extract_Midsurface_Mesh.
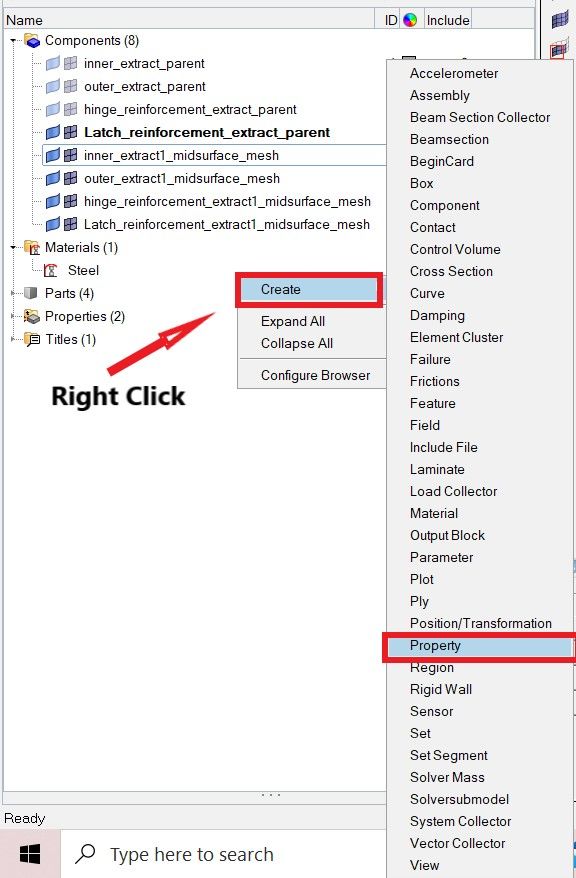
Figure 33-Creating Property |
- Before creating property,Measure the thickness of the component to give a thickness value in the shell thickness parameter and then create a property.
- Create a two properties,Cause you have shell thickness for the Inner_Extract and Outer_Extract - 0.75 & Hinge and Latch Reienforcement Extract-1.2.
- So Create two property card.
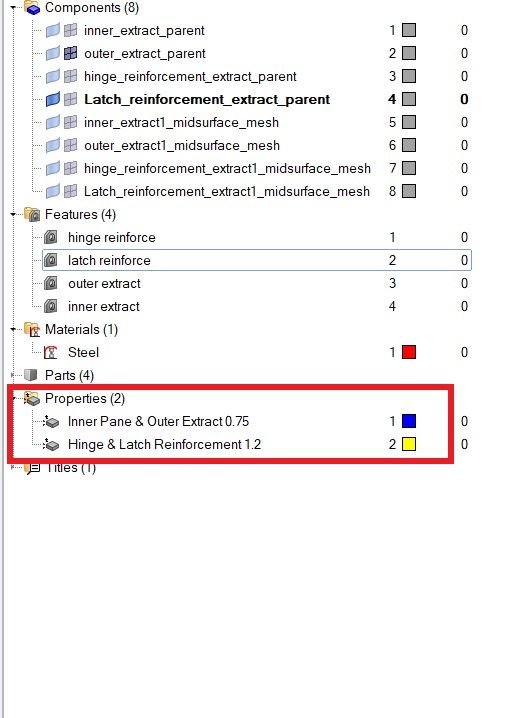
Figure 34-Two Property Card |
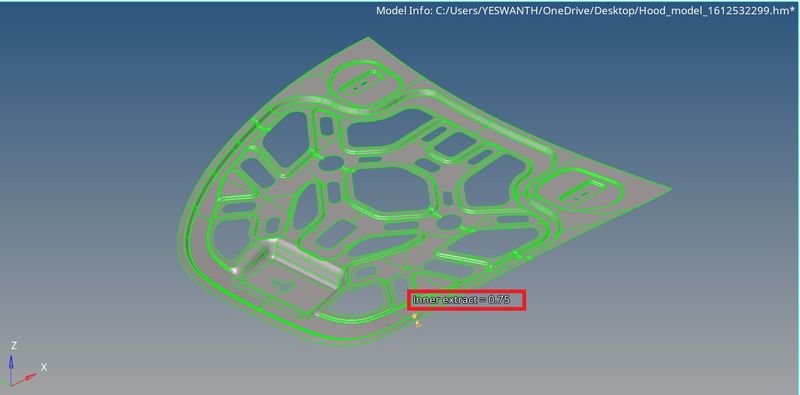
Figure 35-Inner Extract Thickness-0.75 |
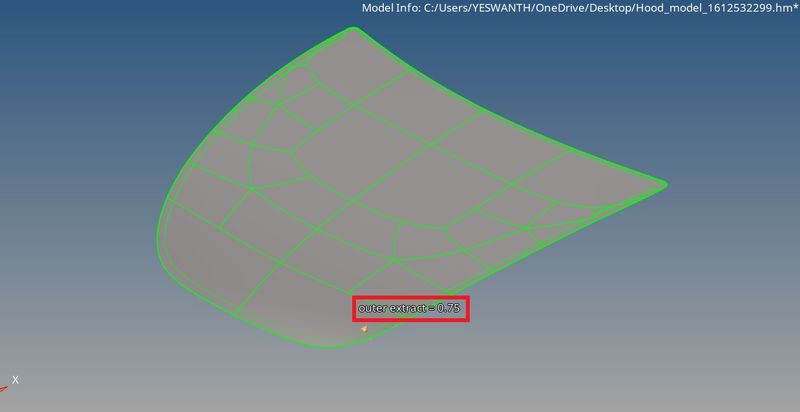
Figure 36-Outer Extract Thickness-0.75 |
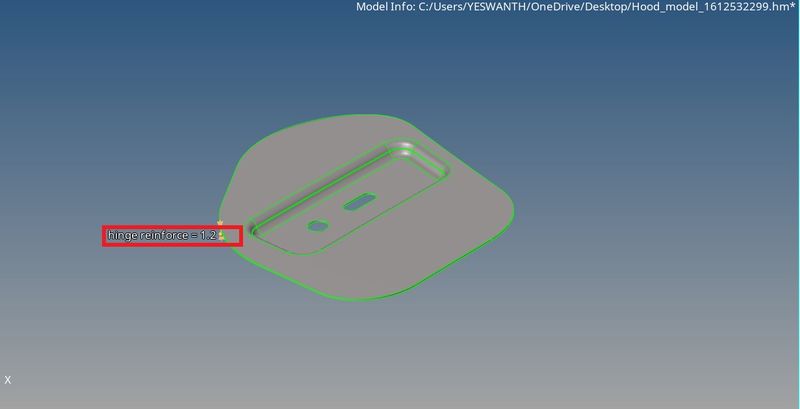
Figure 37-Hinge Thickness-1.2 |
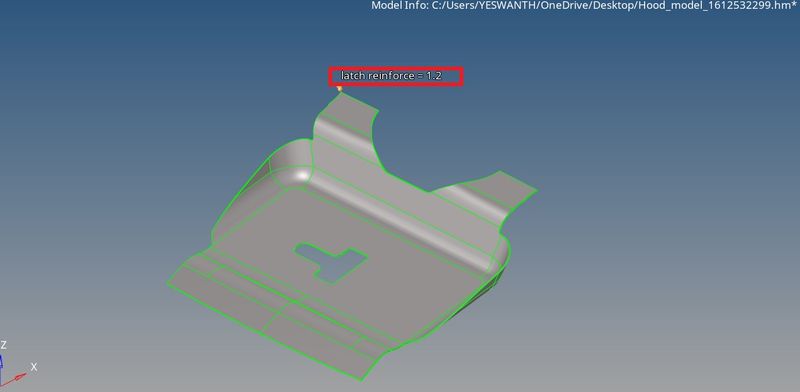
Figure 38-Latch Thickness-1.2 |
Parameters Terms in Property Card Image Panel-
- Describes the shell property set which is used for 3-node or 4-node shell element. Belytschko, QBAT or QEPH shell formulation are available.
- PSHELL 1 property card image id given only for the 2D Shell Elements.
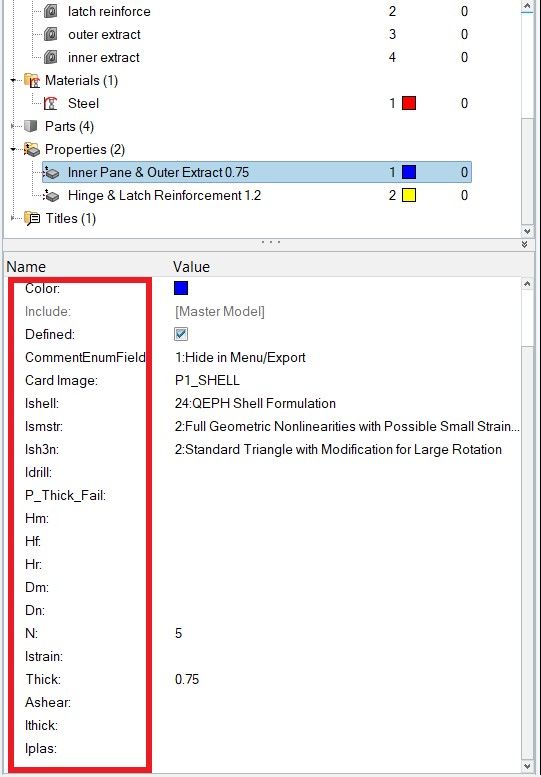
Figure 39-Property Card Parameters |
- Ishell-4 node shell element formulation flag.
- Ismstr-Shell small strain formulation flag.
- Ish3n-3 node shell element formulation flag.
- Idril-Drilling degree of freedom stiffness flag.
- P_thickfail-Percentage of through thickness integration points that must fail before the element is deleted.
- hm-Shell membrane hourglass coefficient.
- hf-Shell out-of-plane hourglass.
- hr-Shell rotation hourglass coefficient.
- dm-Shell Membrane Damping.
- dn-Shell numerical damping.
- N-Number of integration points through the thickness with 0 < N < 10.
- Istrain-Compute strains for post-processing flag.
- Thick-Shell thickness.
- Ashear-Shear factor.
- Ithick-Shell resultant stresses calculation flag.
- Iplas-Shell plane stress plasticity flag.
- If you want to create a property card in material in radioss profile.Then maintain these conditions while creating property card in radioss profile
- Ishell-24 QEPH Shell Formulation.
- Ismstr-2 Full Geometric Nonlinearies with Possible Small Strain.
- Ish3n-2 Standard Triangle with Modification for large Rotation.
- No of Integration Points-5
- Thickness-Give the thickness-0.75,1.2.
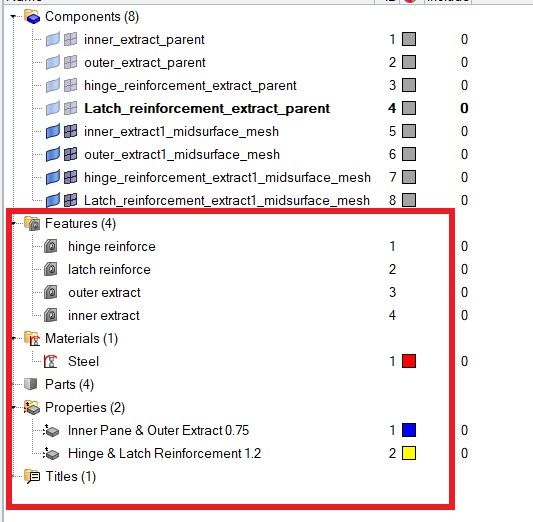
Figure 40-Property Card's Has Been Successfully Created |
Property Card Brief Information Link - https://documentcloud.adobe.com/link/track?uri=urn:aaid:scds:US:0af994a8-110a-4532-af05-d57286b5c10c
Fender Model-
- For Fender Model also,Do the same procedure done for the previous hood model.
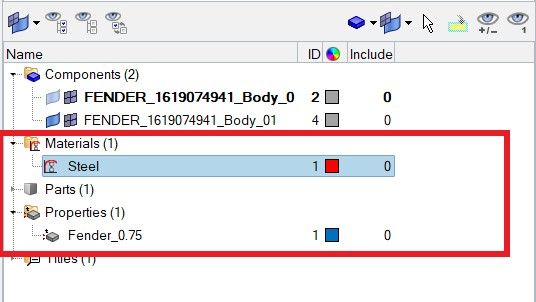
Figure 41-Material and Property Card Has Been Successfully Created For Fender Model |
Phase 7 - Check Whether the Material Card is Applied to the Component's or Not
- To Check Whether the Material Card is Applied to the Component's or Not.Go to the toolbar panel.
- In the mode selection.Go and Switch to the By Material Mode.
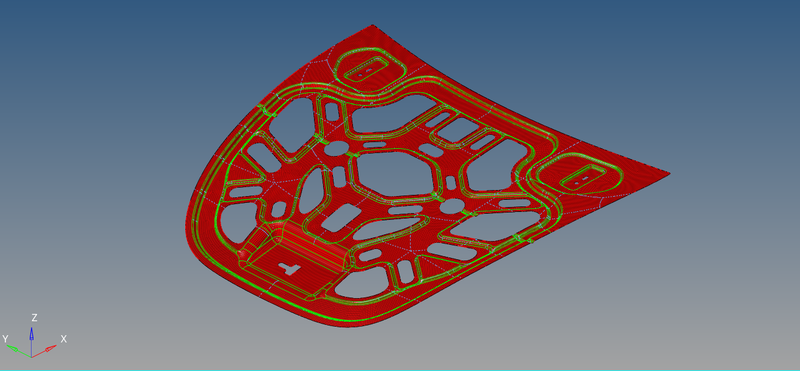
Figure 42-Inner Extract By Material Mode |
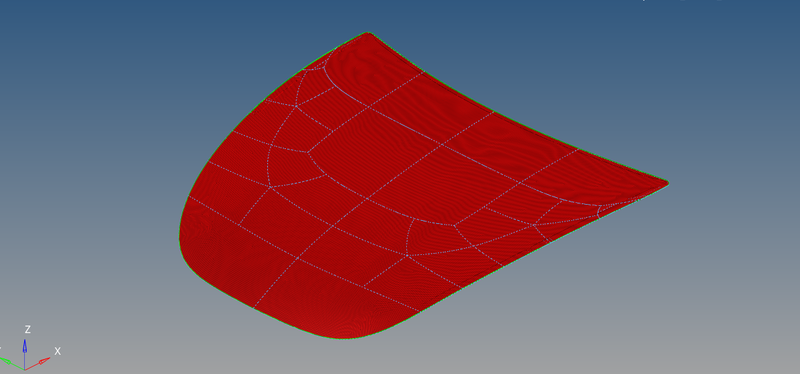
Figure 43-Outer Extract By Material Mode |
Figure 44-Hinge Reinforcement Extract By Material Mode |
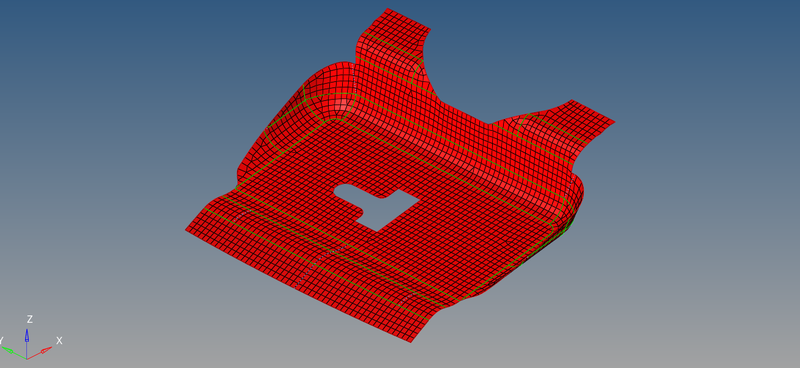
Figure 45-Latch Reinforcement Extract |
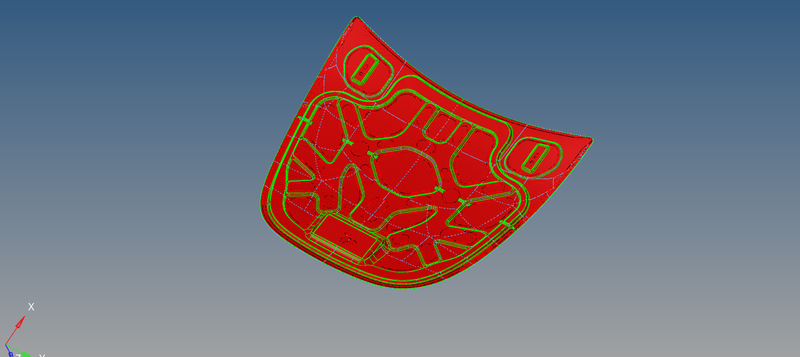
Figure 46-Complete Component Check. |
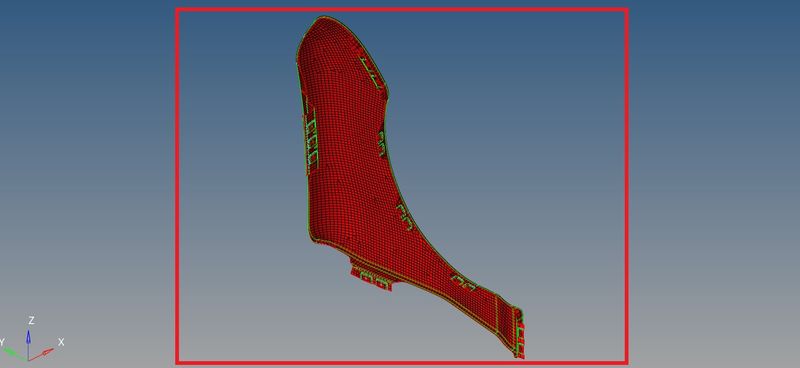
Figure 47-Fender Model by Material Mode |
- Sucessfully Checked For Material,Whether it has been properly assigned to the fender model or not.
- Material has been assigned to the fender model successfully.
Phase 8 - Check Whether the Property Card is Applied to the Component's or Not
- To Check Whether the Property Card is Applied to the Component's or Not.Go to the toolbar panel.
- In the mode selection.Go and Switch to the By Property Mode.
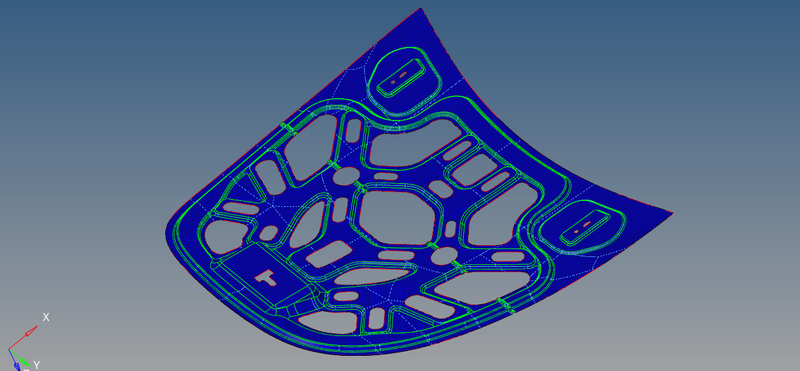
Figure 48-Inner Extract By Property Mode |
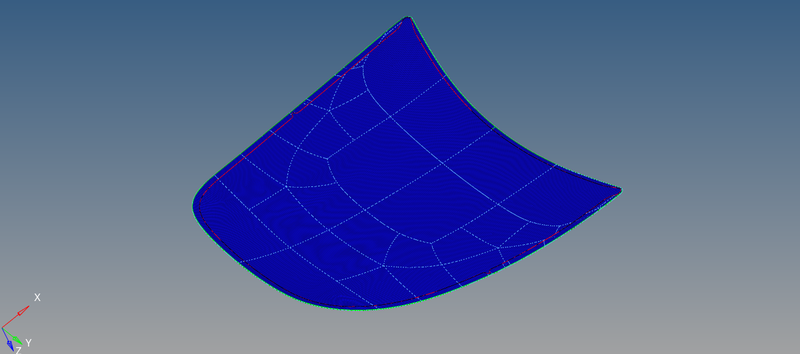
Figure 49-Outer Extract By Property Mode |
Figure 50-Hinge Reinforcement Extract By Property Mode |
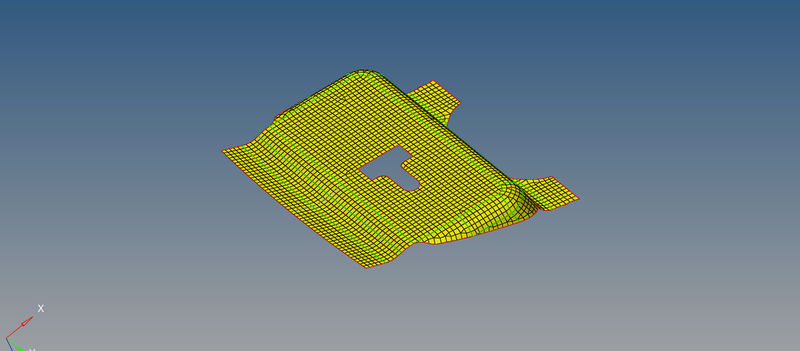
Figure 51-Latch Reinforcement Extract By Property Mode |
- Here the property card colour is in yellow,So the component's are displayed in yellow colour by property mode.
Fender Model-
- Do the same procedure for fender model,what you done for hood model.
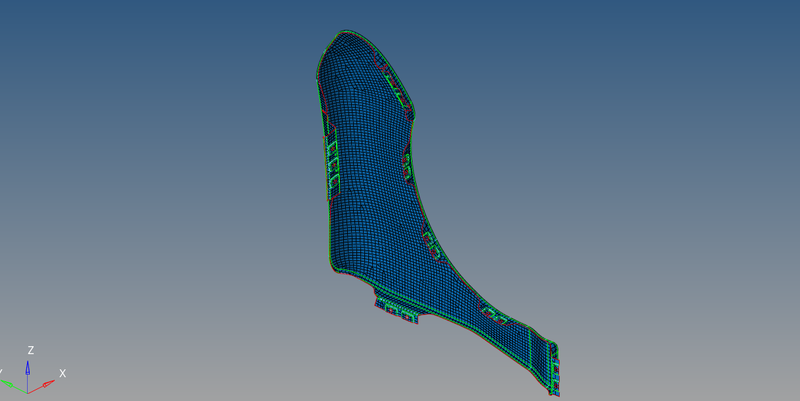
Figure 52-Fender Model By Property Mode |
[Note:The material & property card creation is solver oriented,Different solvers have different methods of creating or building the material & property card.]
Final CAD Model Image-
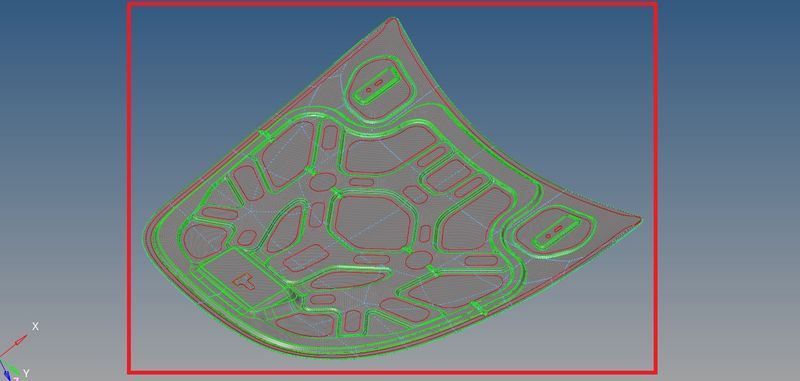
Figure 53-Completed Hood Model |
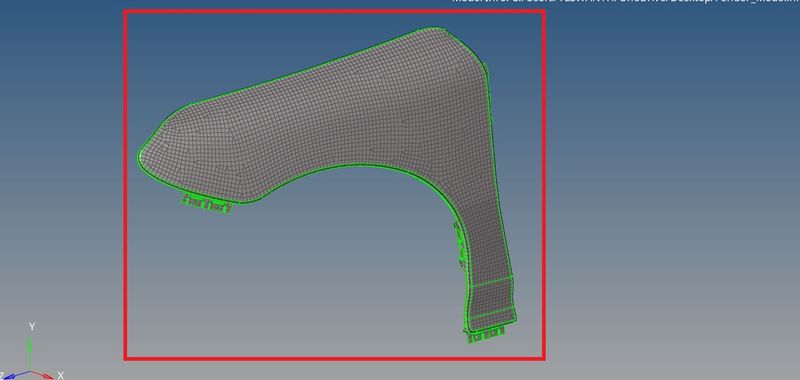
Figure 54-Completed Fender Model |
Result -
- From this we can conclude that material card and property card assigned to the component.
- Hence the batch mesh for the hood model and fender model has been completed successfully.
- Hence the material and property card has been assigned to the components successfully.
Benefit's of Batch Mesh -
- This type of method creates a meshing thing within a few minutes rather than hour's.
- No need to do manual meshing.
- It will maintain the quality criteria and provides a good quality mesh and proper mesh flow based on the criteria given to that.
- No need to do manual cleanup.
- Save our time while meshing.
Drawback's of Batch Mesh -
- This type of meshing is only suitable for the simple geometry.
- It is not suitable for the complex geometry.
- If we do this type of meshing for the complex geometries.It will create lot of trias to maintain the quality criteria.The mesh flow won't be proper.The mesh density will not be uniform.
Conclusion and Learning Outcome -
- From this week 10 challenge,I came to know,How to perform a batch mesh to the components.
- How to create a parameter file and criteria file.
- How to create a material card and property card for the components.
- How to assign material and property card to the components.
Note:Important Links for Material and Property Card-
Property Card-https://documentcloud.adobe.com/link/track?uri=urn:aaid:scds:US:0af994a8-110a-4532-af05-d57286b5c10c
Material Card-https://documentcloud.adobe.com/link/track?uri=urn:aaid:scds:US:2a595532-3d92-41db-83f9-69778f0bd635