RADIOSS Interfaces & Study of Effect of Notches
Aim -
- To run the crash tube model by using differnt types of contact interfaces.
- Mesh the given crash tube model with 6mm size.
Objective -
- Run the crash tube model with and without changing the parameters.
- Remove the notches from the crash tube model,Remove the boundary conditions from rigid body node and then run the simulation.
- Create notches in the middle and in the opposing faces of the crash tube model and then run the simulation.
- Perform geometry clean up on the bumper assembly and mesh the bumper assembly with 6mm size.
Theoretical Framework -
What is Hypermesh and Hypercrash ?
Hypermesh :
- Hypermesh is a generalized preprocessor for many solvers like Abaqus,LS DYNA etc.,
- In hypermesh,we can setup loadcases for Optistruct,Abaqus,ANSYS including Radioss and LS DYNA.
Hypercrash :
- Hypercrash is a specialized preprocessor for radioss.It always exsist as a part of Hyperworks.Hypercrash is mainly used for crash applications.
- Hypercrash supports solvers like Radioss and LS DYNA.The units used in industries are kn,mm,ms,kg.
- In hypercrash we have use only 0000.rad files.Cause hypercrash dosen't have its own file extension.
- Hypercrash only detects the starter files,Cause these are the files only imported into hypercrash.
- We can export bill of materials of all the models or you can also export as radioss file.We can export the model from hypercrash,But it will save the file as FIRST_RUN_0000.rad.It will create a backup file like FIRST_RUN_0000.rad.bak and store the previous file in this .bak file.
- It will also create M000 file.Whenever we export a file from hypercrash,M000 file will be created.The M000 file will only our file structure details and weld data,Whenever we create weld,we will be having weld data.
- If we delete M000 file and import only FIRST_RUN_0000.rad file,We won't be able to see the connection folder in the tree browser.
- But all these connections will be listed as Type 2 Contact Interface.It will be listed in the contact interfaces folder in tree browser.
- In hypercrash engine cards will be represented as control cards.ANIM DT files will be stored in A01 files.Data history files will go in T01 files.
- Rigid Wall Forces,Contact Forces,All Energies ,all those things will go in T01 Files.
Interfaces :
⋆Out of the many interface types, the most used ones for impact simulation are:
⋆Interfaces are defined to model how parts interact when they come into contact with each other.There are common types of interfaces called
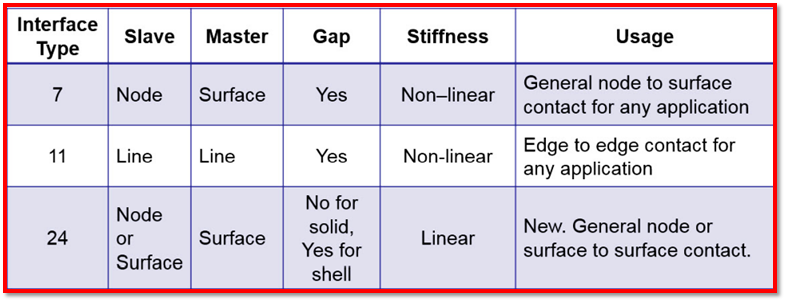
Figure 1-Commonly Used Interfaces Types for Impact Simulations. |
1) Interface Penalty Method
2) TYPE7,Variable Stiffness,Node to Surface Contact.
3) TYPE11,Variable Stiffness,Edge to Edge Contact.
4) TYPE24,Linear Stiffness,Node to Surface and Surface to Surface Contact.
5) TYPE19,Combination of TYPE7 and TYPE11.
1) Interface Penalty Method :
- The penalty method treats the behavior between slave nodes and master segments as springs that generate resistive forces as a function of penetration.
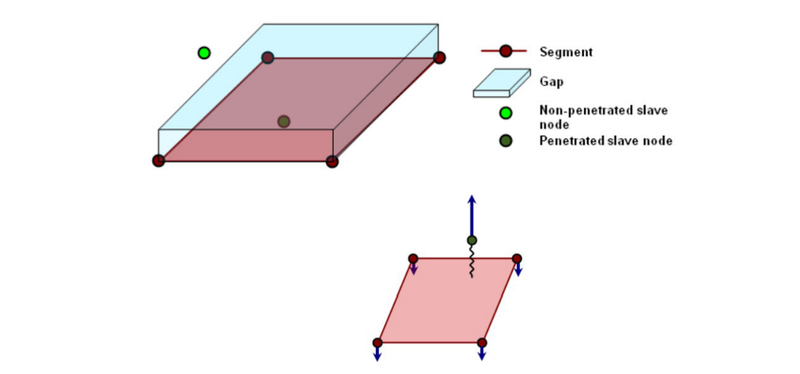
- Here the interfaces are goverened by the penalty method.
- When the parts come into contact,The slave node tries to penetrate the mid surface.
- The solver introduces the 1D spring element once the slave node penetrates the gap.
- The spring stiffness is automatically computed according to the material and property of both master segment and slave node.
- If penetration is zero,the time step will be maximum.As the penetratiom goes on increasing,the time step goes on decreasing.
- Time Step αStiffness.
Time Step for Contact Interfaces :
- Nodal Time Step = Δt≤√2MK
- Kinematic Time Step=Δt≤0.5(g−p)dpdt
- Where dp/dt -Speed of the Sound Wave through the Material.
- g-Gap
- P-Penetration
- Δt-Time Step.
- M-Mass
- K-Stiffness
Interface Type 7 : Nodes to Surface Contact -
- It is a general purpose interface and can simulate all types of impact between a
set of nodes and a master surface.
- Non oriented and slave nodes can belong to the master surface,Hence auto impact possible.
- Automatic node to surface contact interface using penalty method with variable stiffness.
- A gap is defined around the master segment and the slave nodes.
- The contact gap can be constant or variable.
- Resistive forces are applied to keep slave nodes out of the contact gap.
- Interface time step is computed to insure stability.
Important Interface Parameters :
⋆I_gap=Determines how the size of gap is calculated`
⋆Gapmin=Minimum gap for activation of interface.
⋆Inacti=Action to take if initial penetrations exist.
⋆I_stf=Affects how the stiffness of the interface is calculated.
⋆I_Form=Friction formulation.
⋆Stmin=Minimum stiffness to use in the interface.To avoid timestep error.
⋆IDel=What to do with slave nodes and master segments,if elements fails (deleted) that they are attached to or Update for Deleted Elements Due To Failure .
Gap Definitions :
Igap=0 |
Constant Gap |
The gap is defined by Gapmin and is constant for all the contacts.This is default value. |
Igap=1 |
Variable Gap |
The gap varies according to the characteristics of the impacted master surface and impacting slave node. |
Igap=2 |
Variable Gap |
Variable gap with gap scale factor. |
Igap=3 |
Variable Gap |
Variable gap with gap scale factor and with mesh size correction. |
Table-1
Inacti :
- Inacti is nothing but Initial Penetration.
- We will be giving this parameter to get rid off penetration in the model.
Initial Penetration :
- Initial penetration result if a slave node is closer to the master segment than the calculated gap.
- Initial repulsion forces give an error in the energy balance due to the interfaces work.
- There are options in the solver to remove initial penetrations.
- Inacti = 3 may create initial energy if the node belongs to a spring element.
- Inacti = 6 is recommended instead of Inacti =5, in order to avoid high frequency effects into the interface.
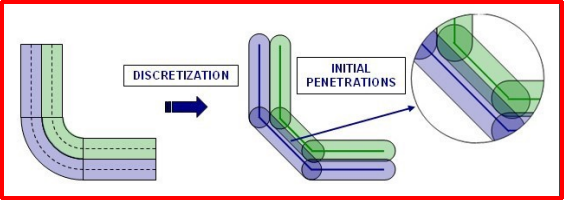
Figure 3-Initial Penetrations. |
Initial Intersections :
- Intersections result if slave nodes are past the master segment (shells or solids).
- This condition can cause locking situations leading to computation failure.
- If slave nodes lie on the master segment an ERROR will occur because of the Type 7 contact stiffness definition.
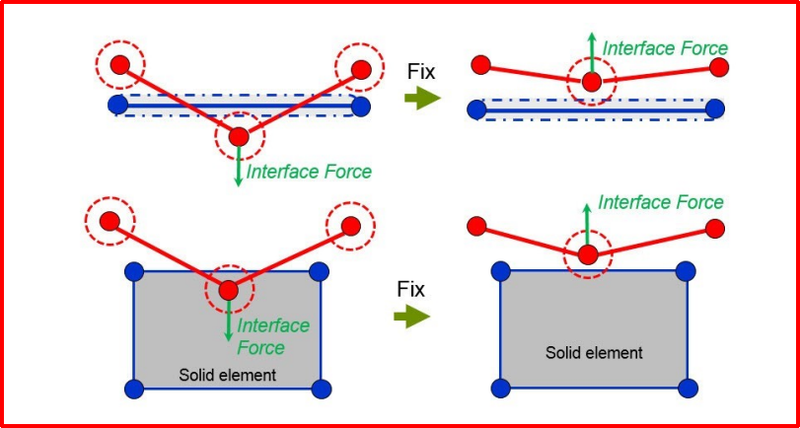
Figure 4-Initial Intersections. |
Options for Removing Initial Penetrations :
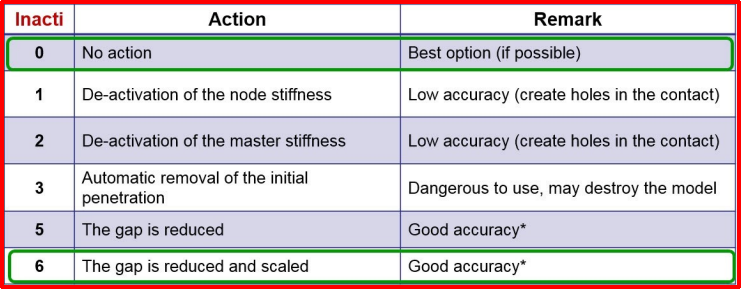
Figure 5-Options for Removing Initial Penetrations. |
Istf Initial Contact Stiffness :
- We will be giving initial contact stiffness to get rid off penetration.
- Like when two components are going to penetrate,To avoid this,we will be giving Initial Contact Stiffness.
- For Example : If the soft component coming into contact with the hard component,the soft component will absorb the resisitive forces.So thats why the stiffnes of the soft component is considered.
- Istf=4 is mostly recommended for the crash applications.
Iform (Sliding Force Computation ) :
- The recommended parameter is Iform=2,Cause the sliding forces are computed using stiffness parameters.
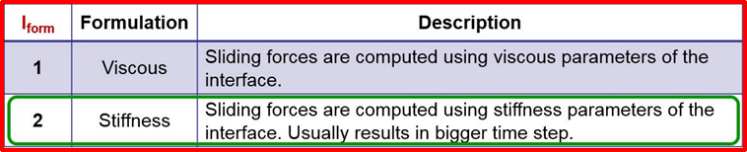
Figure 6-Iform Parameters. |
Idel (Update for Deleted Elements Due To Failure) :
- Idel indicates the update for deleted elements due to failure.
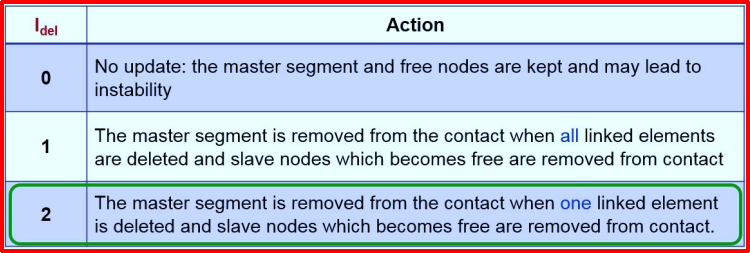
Figure 7-Idel Parameters. |
Recommended Parameters for Crash Applications :
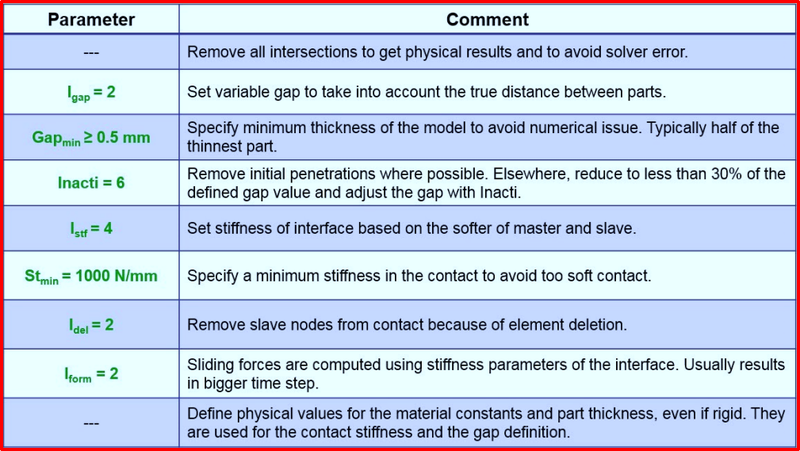
Figure 8-Recommended Parameters for Crash Applications. |
Advantages and Disadvantages of Type 7 Contact :
Advantages :
- Physically correct representation.
- High accuracy for describing self-contact and buckling.
- Best used with shells to shells or solids to shells.
Disadvantages :
- Requires more stringent modeling practices.
- Does not tolerate intersections (slave node passing master segment).
- Time step may reduce due to increasing interface stiffness.
Interface Type 11 (Edge to Edge Contact) :
- Type 11 is similar to the Type 7 Contact.
- This interface simulates impact between edge to Edge or lines. A line can be a beam or truss element or a shell edge or spring elements. In association with interface TYPE7, interface TYPE11 solves the locking cases.
- Defined by identifying master and slave lines (edges)
- Impacts occur between a master and a slave line. A slave line can impact on one or more master lines. A line can belong to the master and the slave side. This allows self-impact.
- Works similar to Type 7 in terms of Penalty formulation, Gap definition and search method.
- Uses complicated mathematical algorithms; therefore, it is strongly advised to use it only when necessary. A huge interface TYPE11 can slow down the computation.
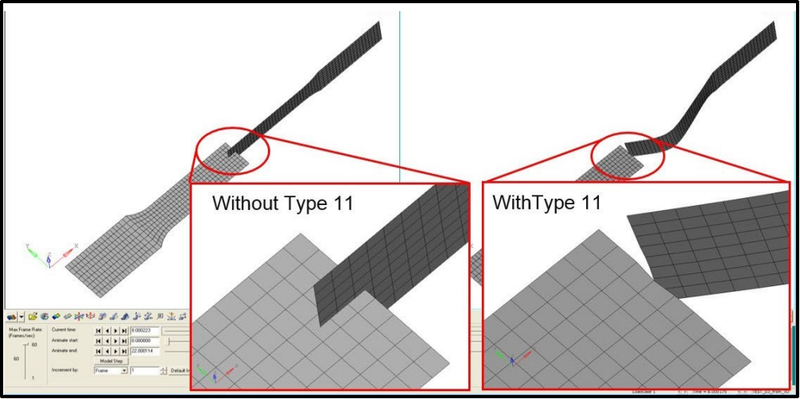
Figure 9-With and Without Type 11 Contact. |
Interface Type 19 (Combination of Type 7+11) :
- Combination of two symmetric TYPE7 interfaces and one TYPE11 interface
- Common input based on the same slave/master surfaces.
- Useful for complex contact problems such airbag unfolding
- Computationally expensive so only problematic segments should be defined
- Edges to edge contact flag Iedge.
Procedure :
1) Mesh the Bumper assembly with 6mm size.
- First import the bumper assembly into the GUI which is shown in below Figure 10.
- Then view the component by topo mode which is shown in below Figure 11.
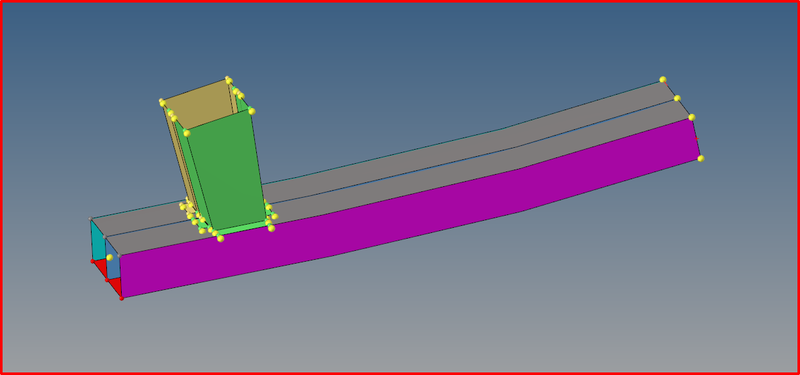
Figure 10-Model Imported into GUI. |
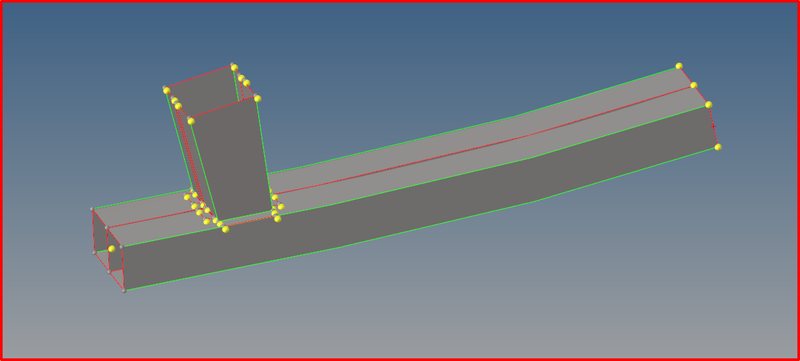
⋆Geometry Cleanup on the Model :
- Now do a geometric cleanup on the model,There are some surfaces which are overlapping and the surfaces which are not equivalenced which is shown in below Figures 12 and 13.
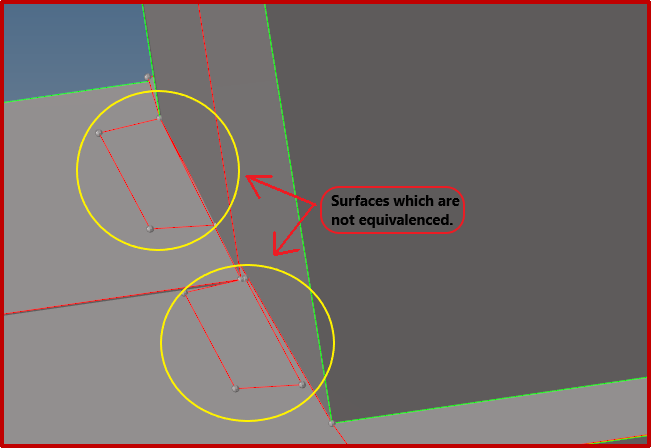
Figure 12-Surfaces Which are not Equivalenced. |
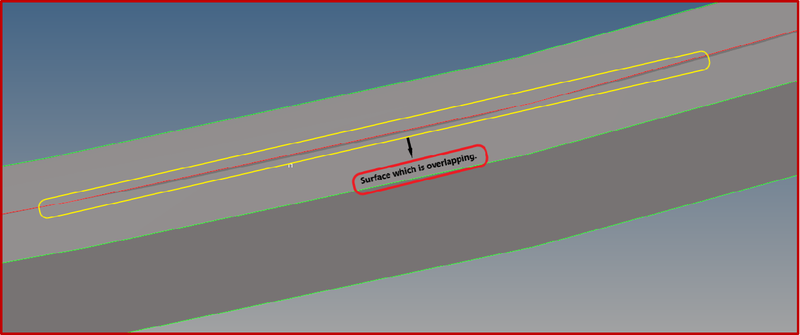
Figure 13-Surface Which is Overlapping. |
- To fix the surfaces which are overlapping and the surfaces which are not equivalenced which is shown in above Figures 12 and 13.
- To equivalence the surfaces,Go to Geometry >> Edge Edit >> Select the Lines Moved Edge and Retained Edge >> Replace.
- We can also fix this by extending the lines over the surface using Extend Tool from Surface Edit Panel.

Figure 14-Geometry Panel. |

Figure 15-Edge Edit Tool Sub Panel. |
- Now select the moved edge and retained edge to equivalence the surfaces which is shown in below Figure 16.
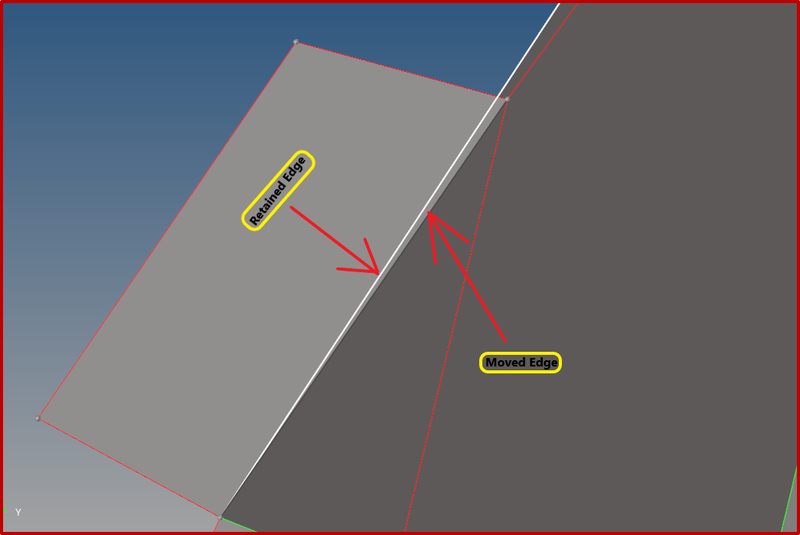
Figure 16-Selecting the Moved Edge and Retained Edge to Equivalence the Surfaces. |
- Surfaces have been connected or equivalenced which is shown in below Figure 17.
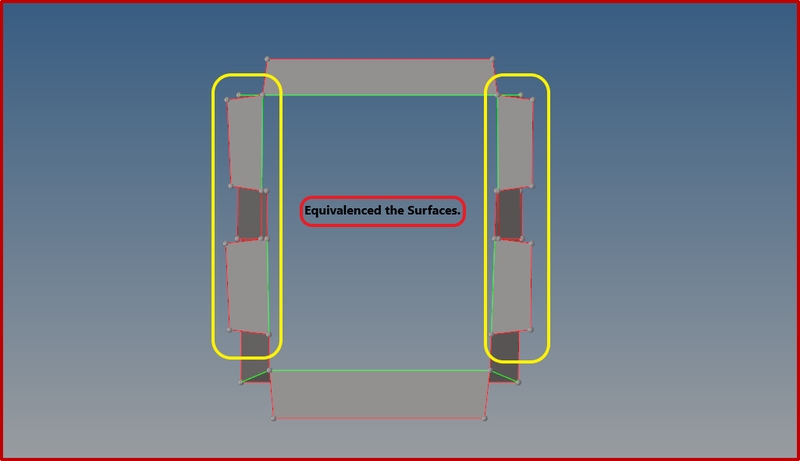
Figure 17-Surfaces Equivalenced. |
- Now intersect the surfaces which are overlapping.
- To intersect the surfaces,Go to Geometry >> Surface Edit >>Trim With Surf/Plane >> Self Intersecting Surfaces >> Select the Two Surfaces >> Trim.
- Select the Surfaces and Trim the Surfaces which is shown in below Figure 20.

Figure 18-Geometry Panel. |

Figure 19-Trim With Surf/Plane Sub Panel. |
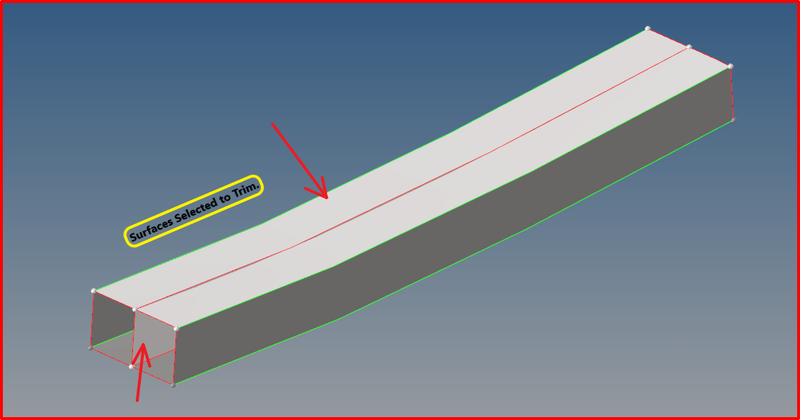
Figure 20-Surfaces Selected to Trim. |
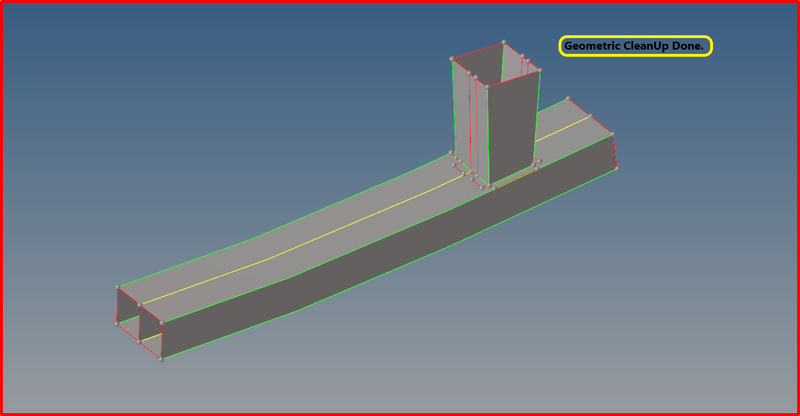
Figure 21-Final Geometric CleanUp on the Bumper Model. |
- Once geometry cleanup is done (e.g. surfaces are stitched together — no unwanted free surface edges inside the geometry), meshing is next.
- Now start meshing on the surfaces which is shown in below Figure 24.
- To mesh,Go to 2D >> Automesh Panel >> Surfaces >> Element size = 6mm >> Mesh Type : Quads or Mixed >> Check for align and size >> Mesh.


Figure 23-Automesh Sub-Panel. |
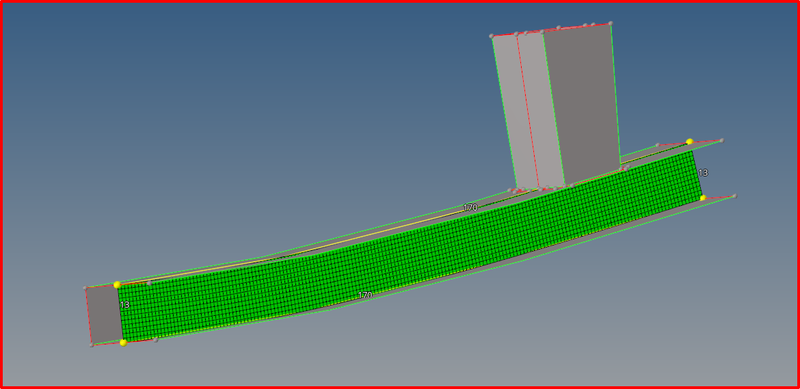
Figure 24-Meshed Surface. |
- After meshing the entire bumper component,The bumper model will be seen as which is shown in belowe Figure 25.
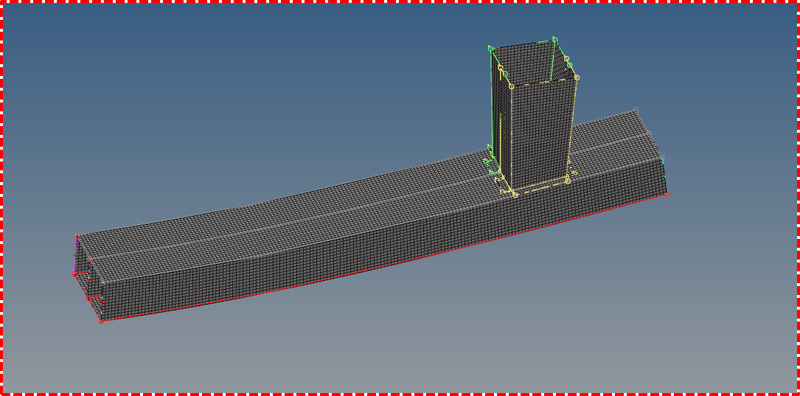
Figure 25-Meshed Entire Component. |
Import the Starter File into the Solver Deck Radioss :
- While opening hypermesh software,A user profile window will pop up,Switch to the radioss user profile as shown in below Figure 26 and start importing the model into the solver deck.
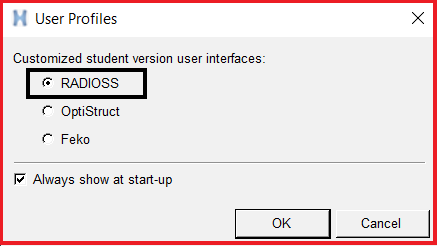
Figure 26-User Profile Window. |
- Now after switch the user profile to radioss,import the model (starter file) into the radioss solver deck.
- To import the model,Go to Standard Panel >> Import >> Import Solver Deck.
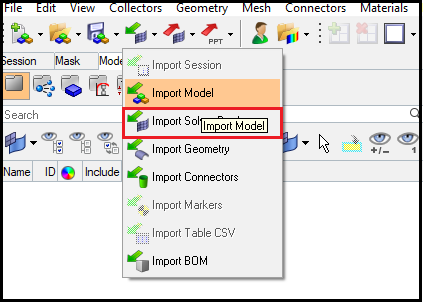
Figure 27-Importing Model into Radioss Block. |
- Import Solver Deck option should be selected to import the radioss starter file.
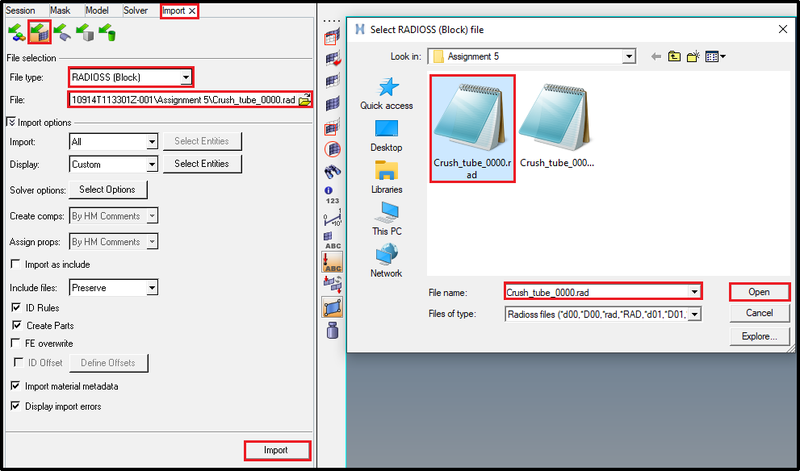
Figure 28-Selecting the Starter File to Import. |
- Here the import browser will appear as shown in above Figure 28,Select the appropriate starter file to import into GUI.
- Switch the File Type to Radioss Block and import the model into GUI.
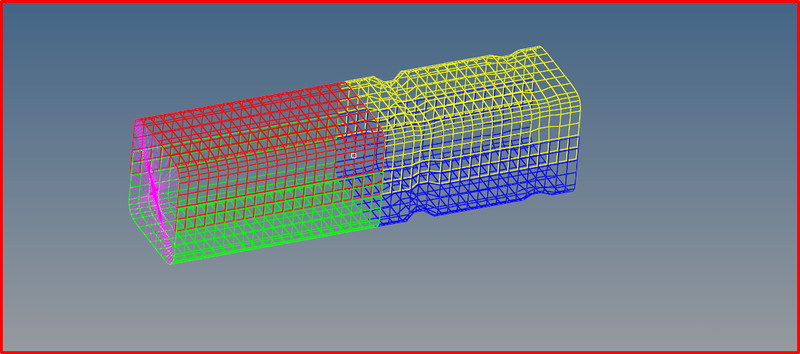
Figure 29-Model Imported into GUI. |
- Here the model is in wireframe mode,Switch to the shaded mode as shown in below figure 5.
- To switch to shaded mode,Go to Visualization Tab >> Shaded Elements and Mesh Lines.
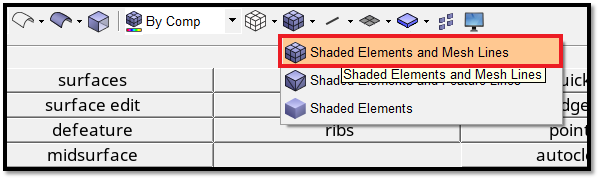
Figure 30-Visualization Tab to Switch to the Shaded Elements and Mesh Lines. |
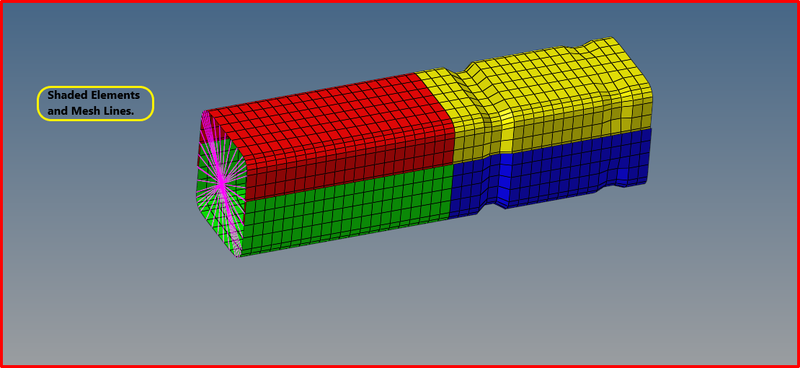
Figure 31-Shaded Elements and Mesh Lines Mode. |
Case-1 Run the Crash Tube Model as it is default :
- Here we have to create TH for the for all the parts.
- Before running the simulation.We have to create TH for the interfaces.It should be followed for all the cases.
- To create TH,Go to Solver Browser >> Right Click on TH >> Create >> Inter,Which is shown in below Figure 32.
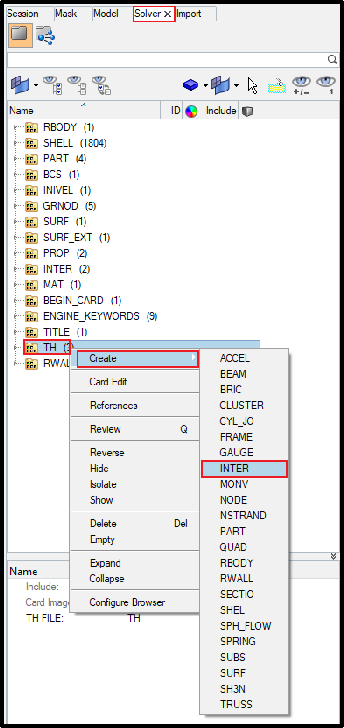
Figure 32-Creation of TH. |
- After creating TH,The contact interfaces should be assigned to that,Which is shown in below Figure 33.
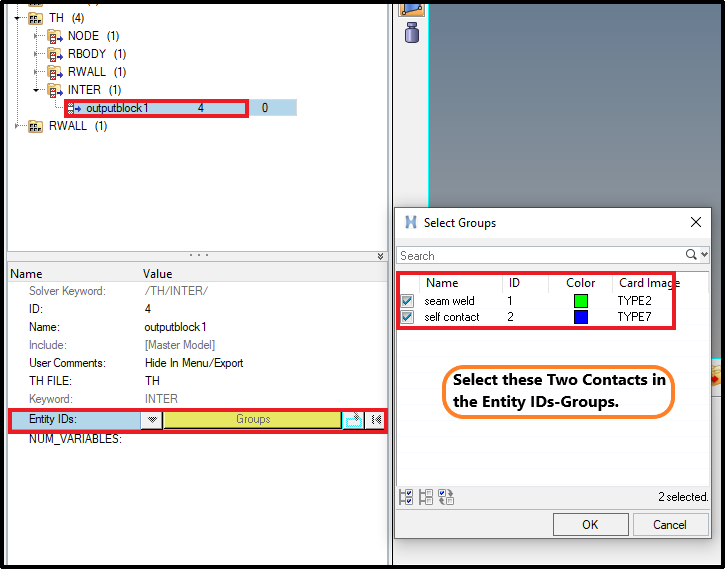
Figure 33-Contacts assigned to the TH. |
- Now run the simulation,To run simulation,Go to Analysis Panel as shown in Figure 34.
- Go to Analysis Panel >> Radioss >> Select the Input File >> Save it in Different Folder and Rename it as Case-1 >> Run.
- Check the Include Connectors,If there are any connectors in the model,The connectors will also be taken into account.
- Type -NT 4 in options tab,This will make the simulation faster.
- Where NT indicates No of threads,4 indicates assigning the task to 4 cores in the system.

Figure 34-Analysis Panel. |

Figure 35-Radioss Sub-Panel. |
- Here save the input file in a different folder, and rename it as case-1 which is shown in below Figure 36.
- Now run the solver by hitting on radioss.
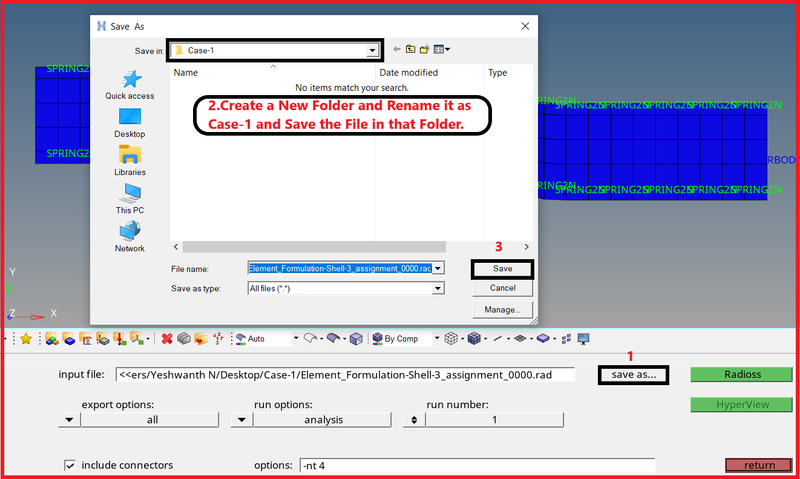
Figure 36-Save the Input (Starter File) in a Separate Folder and Run the Simulation. |
- After completing the simulation,the radioss will pop up a solver window stating Radioss Job Completed which indicates the simulation has been completed,Which is shown in below Figure 37.
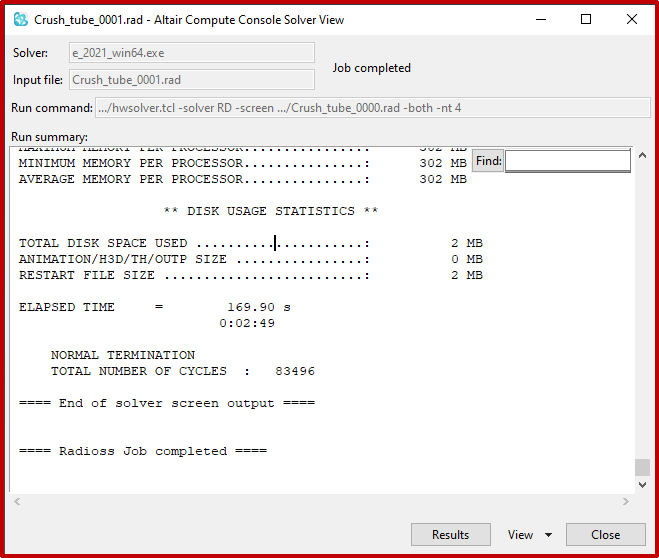
Figure 37-End of Solver Output. |
- After running the simulation,The animation files will be generated where we specified a location to store the files which is shown in below Figure 38.
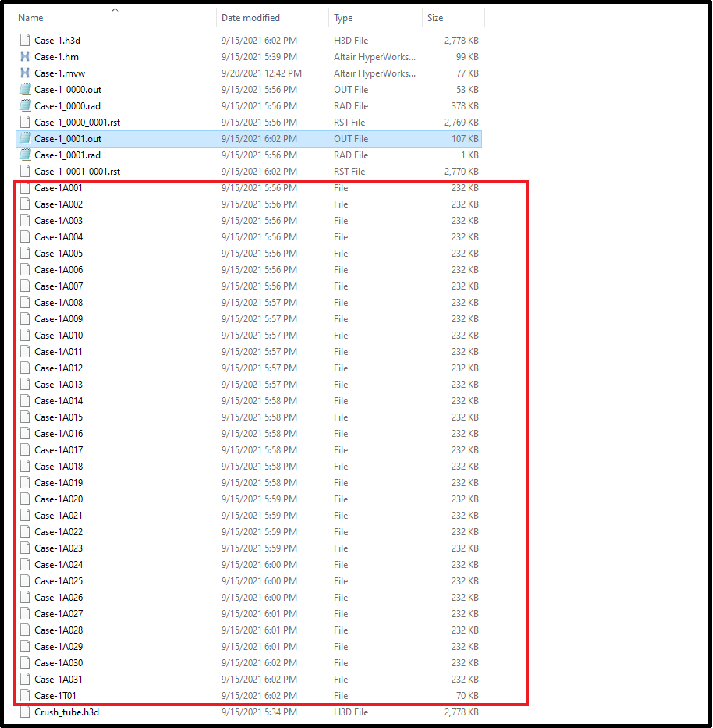
Figure 38-Animation Files. |
- Now go and open the 00001.out file with notepad.
- The obtained values for Energy Error,Mass Error,Internal Energy Error,Kinetic Energy Error and Contact Energy Error has been shown in below Figure 39.
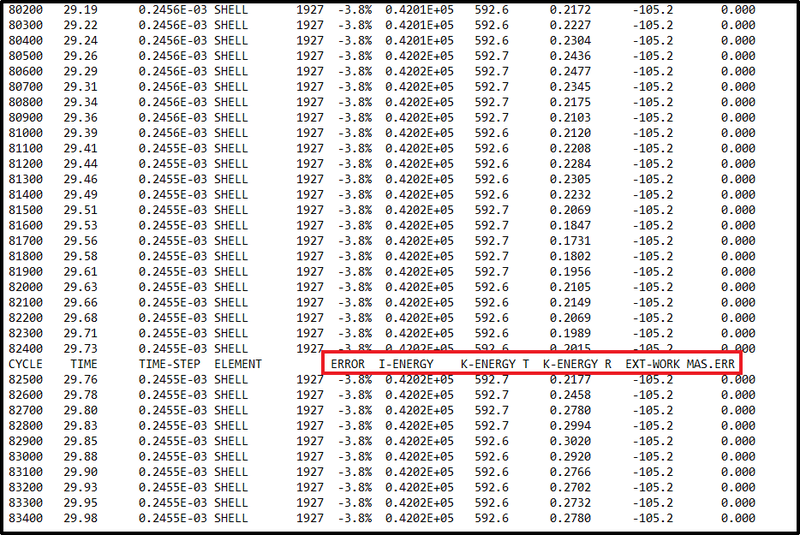
Figure 39-Obtained values for Energy Error,Mass Error,Internal Energy Error,Kinetic Energy Error and Contact Energy Error. |
Postprocessing :
1) Review the Simulation using -HyperView.
2) Plot the graphs using -Hypergraph 2D.
1) Review the Simulation using HyperView :
- Hyperview allows for loading and viewing result files obtained from several sources.
- Based on the solver type of the files and the results you would like to visualize and analyze,there are differnt ways to load the input deck and their corresponding results into hyperview.
- First to begin the postprocessing in the Hypermesh,Split the Screen as shown in below Figure 41.
- Import the animation file .h3d into the hyperview.
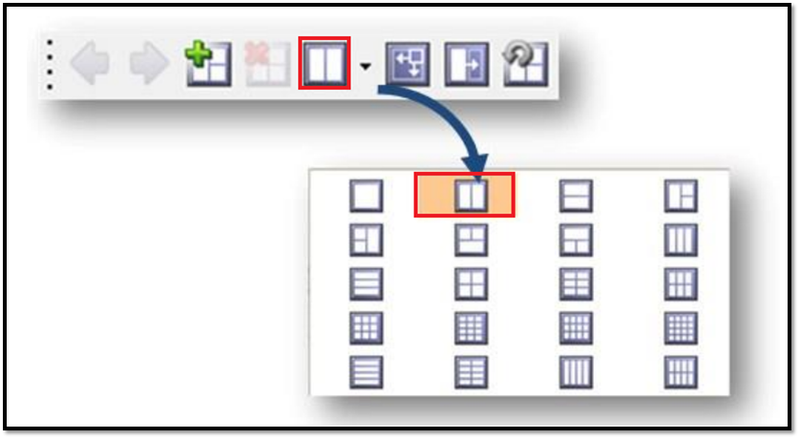
Figure 40-Splitting the Screen. |
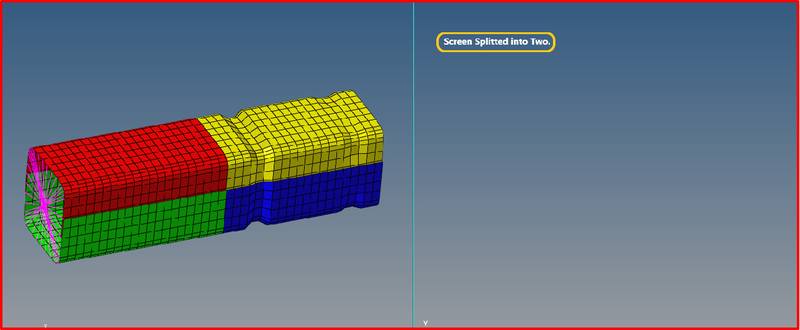
Figure 41-Screen Splitted into Two. |
- And then activate the Client HyperView.

Figure 42-HyperView Panel. |
- To access the load model panel
- Select Load Model Button from the HyperView Panel and open .h3d file as shown in below Figure 43.
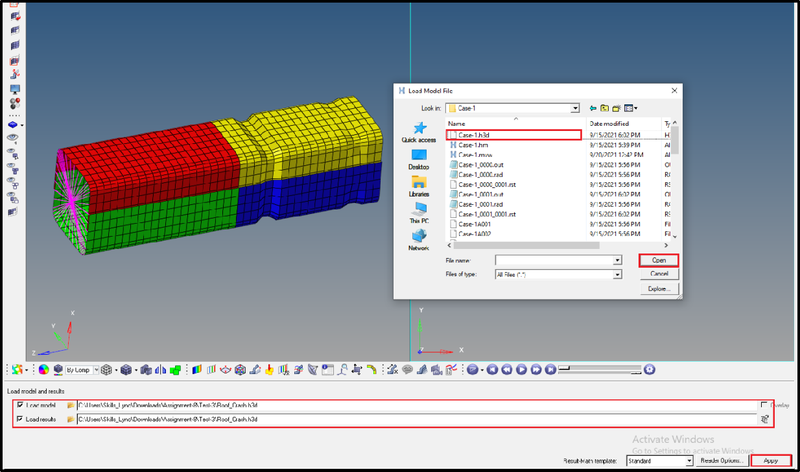
Figure 43-Opening .h3d File. |

- After loading the model into hyperview,It will be represented as shown in below Figure 45.
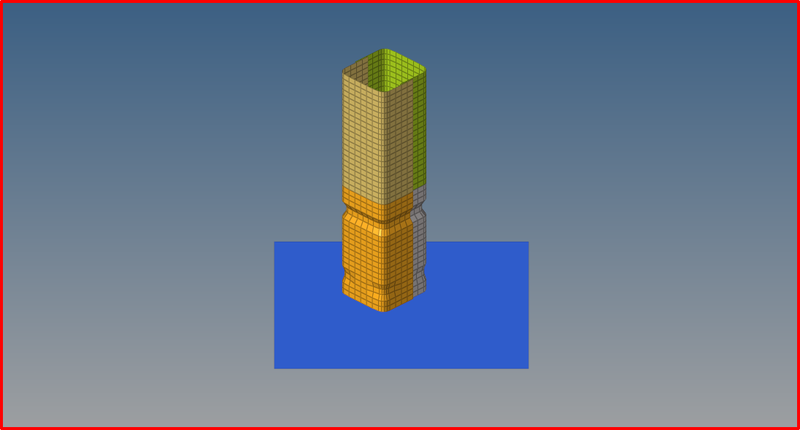
Figure 45-Model Imported into HyperView. |
- After importing the .h3d file into the GUI,Enable the contour.
- The contour tool create contour plots of a model graphically visualize the analysis results.
- To enable contour,Go to Results ToolBar >> Contour
.

- Now switch to the Von Misses Stress in result type and select the component,select the averaging method as simple and then click apply as shown in below Figure 47.

Figure 47-Selecting the Paremeters in Contour Panel. |
- After applying ,Run the Simulation,The Simulation animation is shown in below Figure 48.
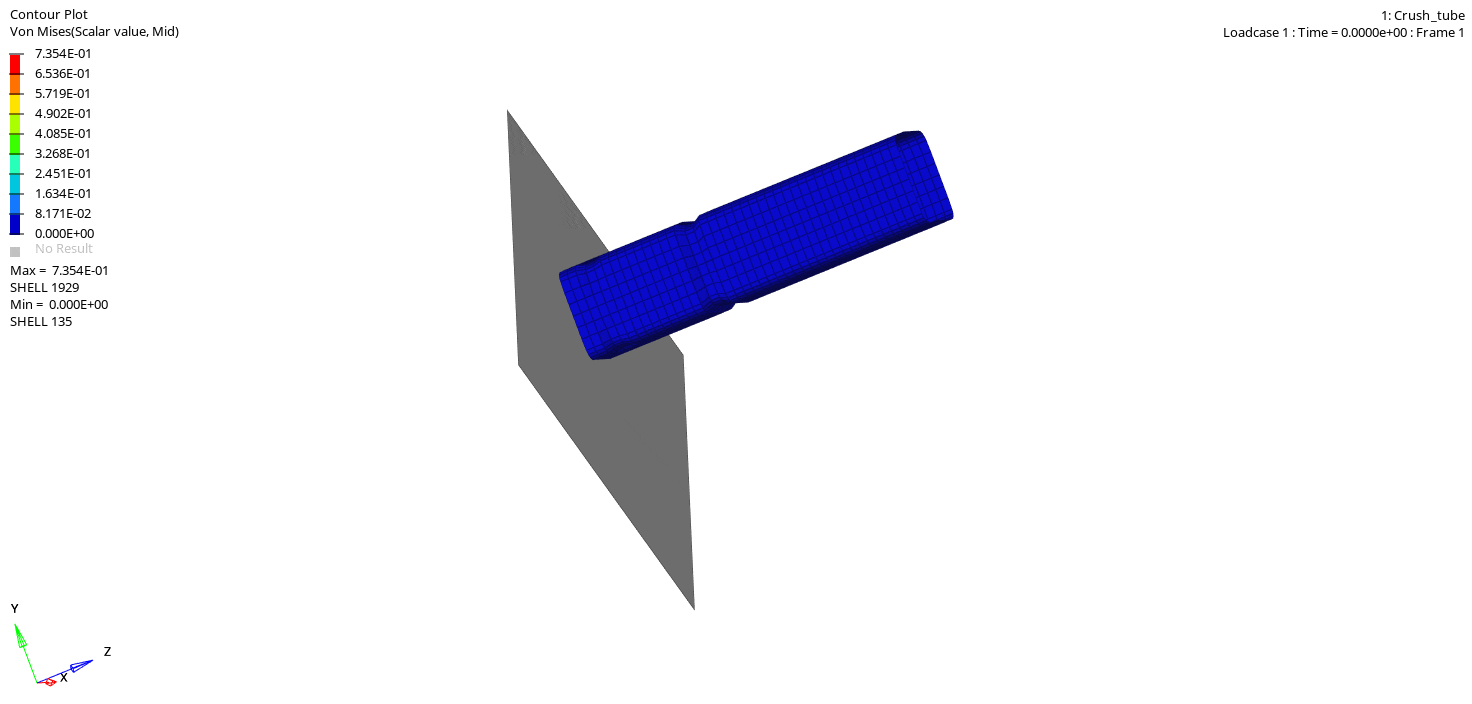
Figure 48-Case 1 Simulation Animation. |
2) Plot the graphs using -Hypergraph 2D.
- Now plot the graphs using Hypergraph 2D,We are plotting the graphs to see what is happening in the rail component.
- Hypergraph 2D is a powerful data analysis and plotting tool with interfaces to many popular file formats.
- It is sophisicated math engine capable of processing even the most complex mathematical expressions.
- Hypergraph 2D combines these features with high quality presentation output and customization capabilities to create a complete data analysis system for any organization.

Figure 49-Switching to Hypergraph 2D. |
- Here switch to the Hypergraph 2D to plot the graphs.
- To switch,Go to Client Selector >> Choose the Hypergraph 2D as shown in above Figure 49.
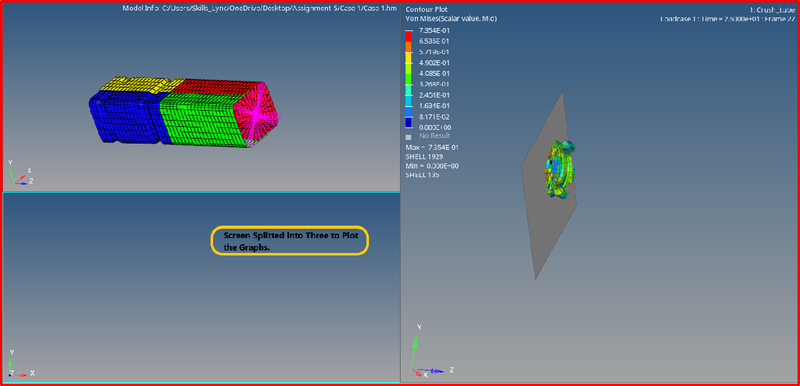
Figure 50-Screen Splitted into Three. |
[Note : Before plotting the graphs,Make sure to split the screen into three or four as shown in above Figure 50 and then plot the graphs.]
- The first graph is plotted for the Rigid Wall Forces.
- To plot the graph,Go to Hypergraph 2D >> Data File >>Crash_TubeT01 >> Apply.
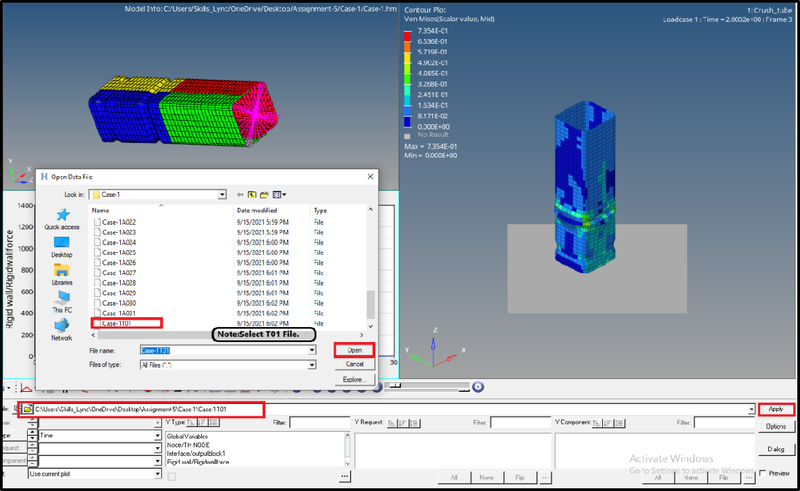
Figure 51-Select the Appropriate T01 File. |

Figure 52-Plotting Graph for Rigid Wall Forces. |
- Here the graph has been plotted for the Rigid Wall Forces as shown in below Figure 54.
- There are various parameters in Rigid Wall like Normal Force,Tangent Force,FX-X Total Force,FY-Y Total Force,FZ-Z Total Force,Total Resultant Force.
- We are selecting only Total Resultant Force,Because we don't know the exact axis of the component placed,So that's why we are selecting Total Resultant Force and then plotting the graph.
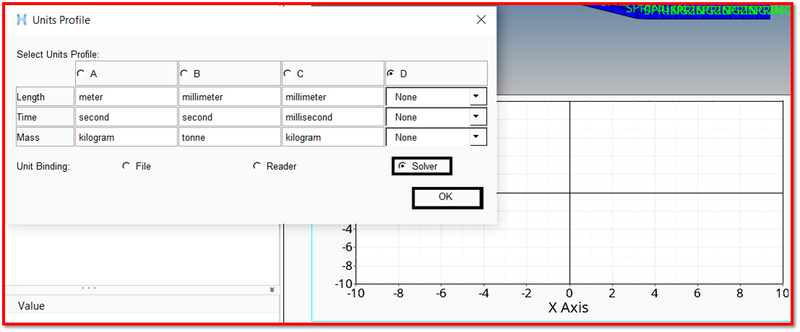
- While plotting the graph,Units profile window will pop up,There select solver units and then plot the graph,Because the graphs will be plotted according to the solver units.
- Now plot the graph for the rigid wall forces which is shown in below Figure 54.
Rigid Wall Forces :
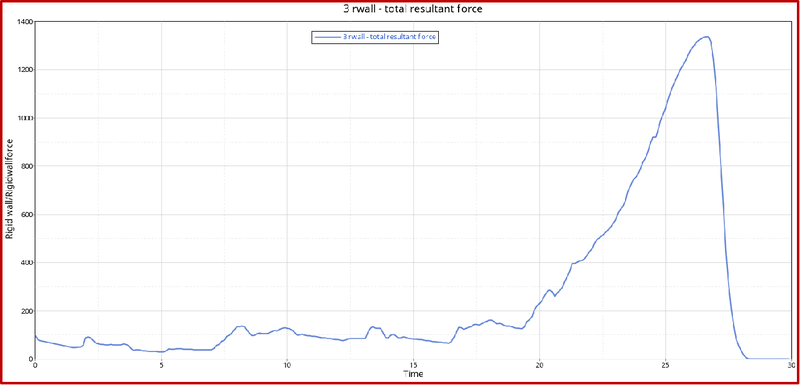
Figure 54-Rigid Wall Forces Graph [Case-1]. |
- Here the rigid wall forces starts from origin,Cause initially there is no contact between the crash tube and rigid wall.
- And it goes on increasing,cause the elements are getting deformed and the rigid wall forces suddenly reaches peak,cause the entire crash tube collides with the rigid wall.
- And again its decreasing,cause after the collision,the entire component will be at rest,So its decreasing.
Contact Forces :
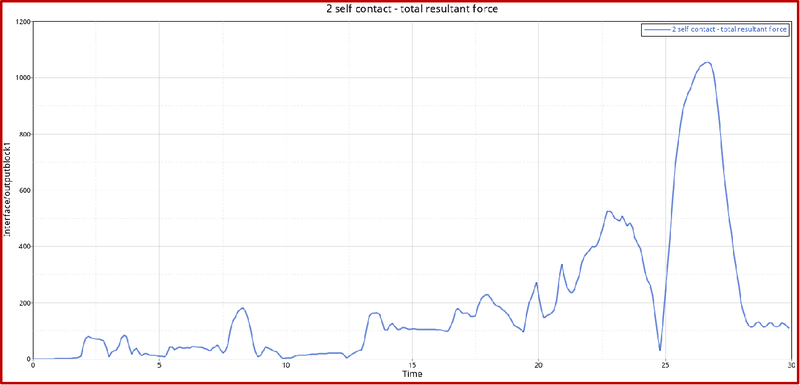
Figure 55-Contact Forces Graph [Case-1]. |
- Here the contact forces are in origin,cause initially there is no contact and impact.
- And it goes on increasing slightly,cause the deformation is happening and suddenly it reaches peak,cause the entire crash tube collides to the rigid wall.
- And it decreases,cause after collision,the crash tube will be at rest.
Kinetic Energy :
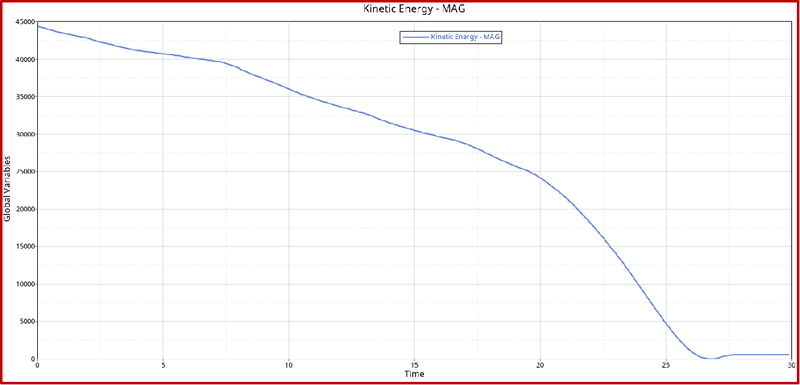
Figure 56-Kinetic Energy Graph [Case-1]. |
- Here kinetic energy is increasing in the beginning itself,Why because the initial velocity is given for the component.
- And it goes on decreasing,cause the deformation is happening to the crash tube,so the kinetic energy is decreasing.
Internal Energy :
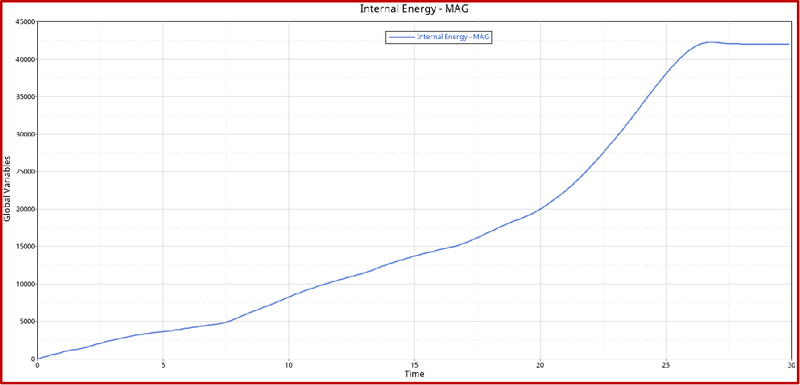
Figure 57-Internal Energy Graph [Case-1]. |
- The formula for Internal Energy is I.E = Q±W.
- Here the heat is neglected,Cause there is no heat transfer,We will be having only workdone.
- W=FxD
- F=ma
- Here the internal energy is in Zero,Because there is no deformation initially,So the internal energy is in Zero and starts from Zero and goes on increasing.
- The internal energy increases because the deformation is happening,there is a displacement,So the internal energy increases,when the displacement or deformation occurs.
Contact Energy :
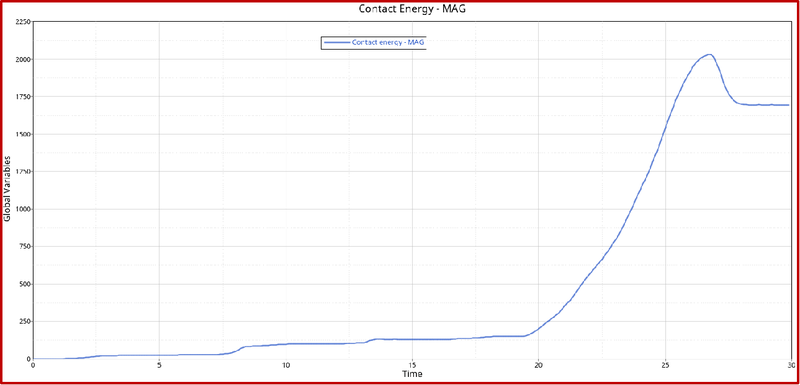
Figure 58-Contact Energy Graph [Case-1]. |
- Here the contact energy starts from origin,Cause the crash tube component is in intial condition.
- Intially there is no contact between the crash tube component and rigid wall.
- There is also no deformation intially,But when the component goes and hits on the rigid wall,The contact energy starts increasing.
- When the deformation or displacement happens to the component,the contact energy increases,cause the crash tube comes into the contact to the rigid wall.So the contact energy goes on increasing.
Total Energy :
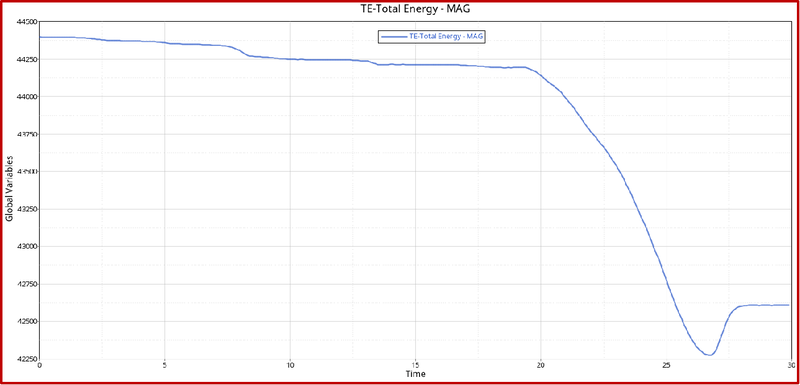
Figure 59-Total Energy Graph [Case-1]. |
- Total Energy is sum of Kinetic Energy+Contact Energy+Hourglass Energy + Internal Energy.
- Here total energy starts from higher value,In starting itself its increasing,Why because the total energy is sum of Kinetic Energy+Contact Energy+Hourglass Energy + Internal Energy.
- All energies are in initial condition except kinetic energy,So kinetic energy is only there
- Total Energy=Kinetic Energy+0+0+0.
- Kinetic enrgy is directly proprtional to the total energy.
- So the total energy is increasing in the beginning.
- And its slightly decreasing,Due to -3.8% of energy error,the total energy is decreasing.
Hourglass Energy :
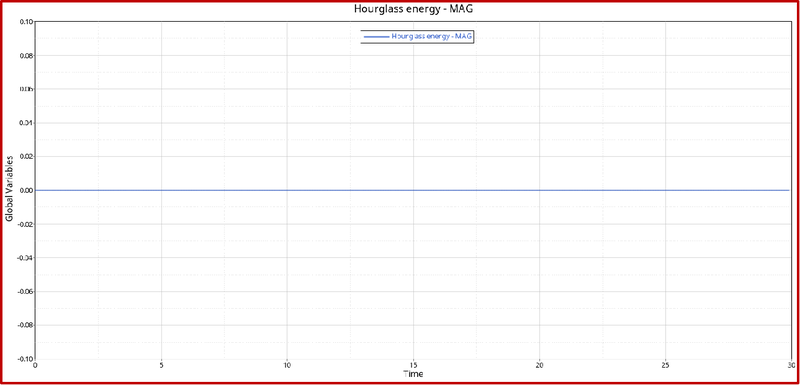
Figure 60-Hourglass Energy Graph [Case-1]. |
- Here the hourglass energy is constant,Because the recommended parameter Ishell=24 has been assigned to the property card,So the hourglass energy is constant.
All Energies :
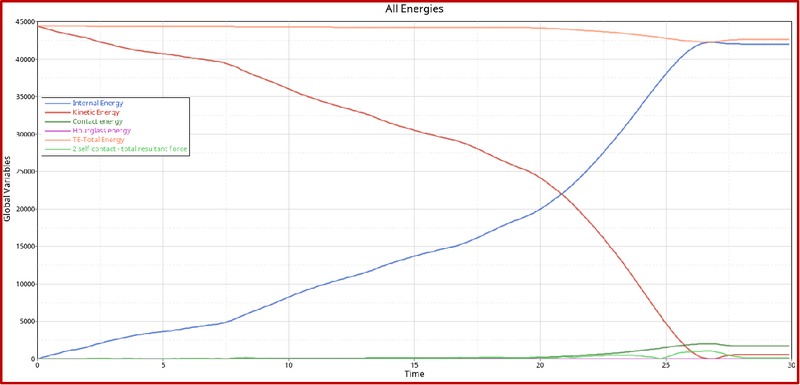
Figure 61-All Energies Graph [Case-1]. |
Case-2 Change the Inacti=6 and run :
- Here change the parameter value as Incti=6,Keep the remaining parameters as it is default.
- When we change the Inacti Parameter=6,It will remove the penetration,the penetration won't happen between the slave and master node.
- It will reduce the gap and adjust the gap.Like the gap will be reduced and scaled.The Iancti value is changed which is shown in below Figure 62.
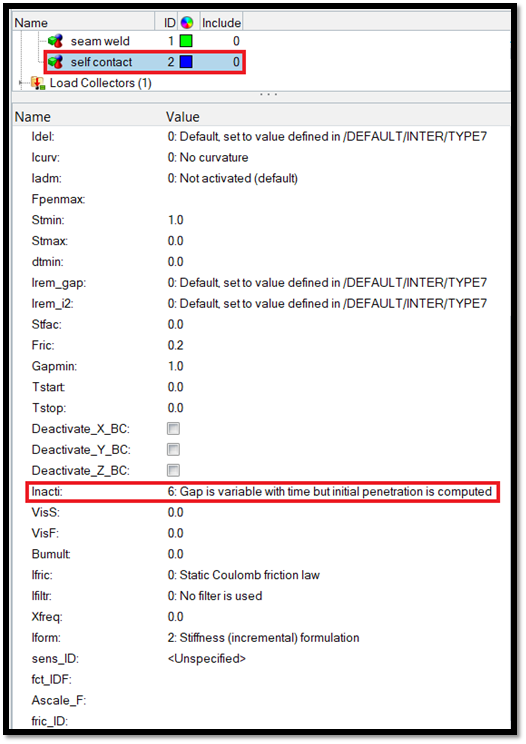
Figure 62-Changed Inacti Parameter Value. |
- Simillalrly,Now run the simulation using radioss,After running the simulation,The animation and TH files will be obtained in a required location,which is shown in below Figure 63.
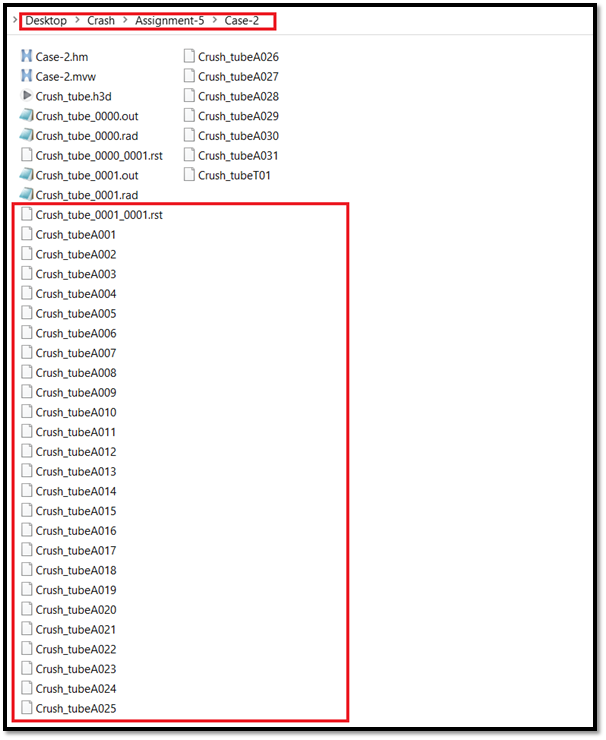
Figure 63-Animation Files Obtained in Required Location. |
- Now go and open the 00001.out file with notepad.
- The obtained values for Energy Error,Mass Error,Internal Energy Error,Kinetic Energy Error and Contact Energy Error has been shown in below Figure 64.
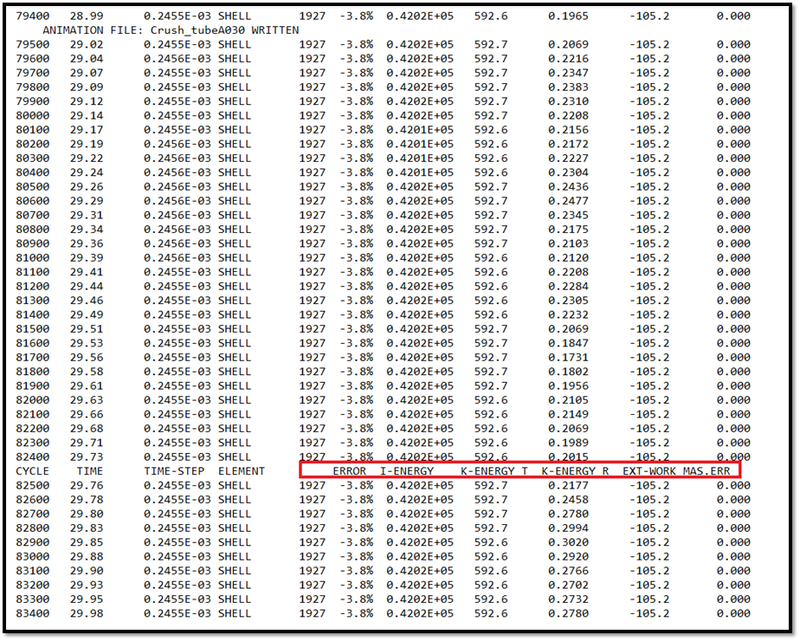
Figure 64-Obtained values for Energy Error,Mass Error,Internal Energy Error,Kinetic Energy Error and Contact Energy Error. |
1) Review the Simulation using -HyperView.
- After completion of running the simulation,Switch to the hyperview.
- Open the appropriate .h3d file to review the simulation.
- The .h3d file is loaded and it is shown in below Figure 65.
- Here the stess generated for this case is 0.73 Mpa.The behaviour is same similar to the previous case 1.
_1632965586.gif)
Figure 65-Case 2 Simulation Animation. |
2) Plot the graphs using-Hypergraph 2D.
- Now switch to the Hypergraph 2D and plot the graphs.
- The rigid wall forces graph is plotted which is shown in below Figure 66.
Rigid Wall Forces :
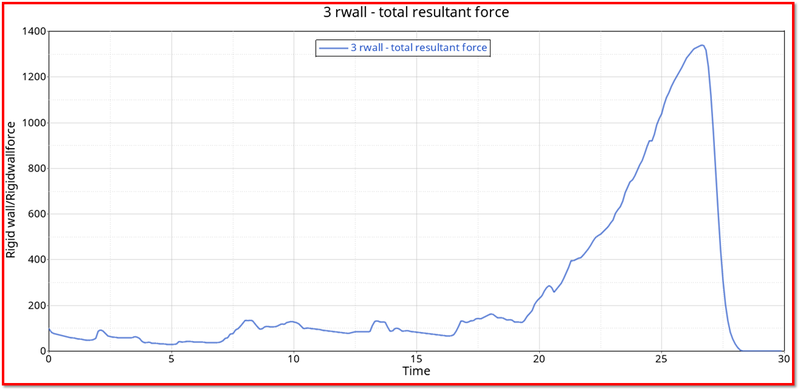
Figure 66-Rigid Wall Forces Graph [Case-2]. |
- The obtained graph for rigid wall forces is shown in above Figure 66.Here The rigid wall forces is similar to the previous case 1.
Contact Forces :
- The obtained graph for contact forces is shown in below Figure 67.Here the contact forces are also some what similar to the previous case 1.
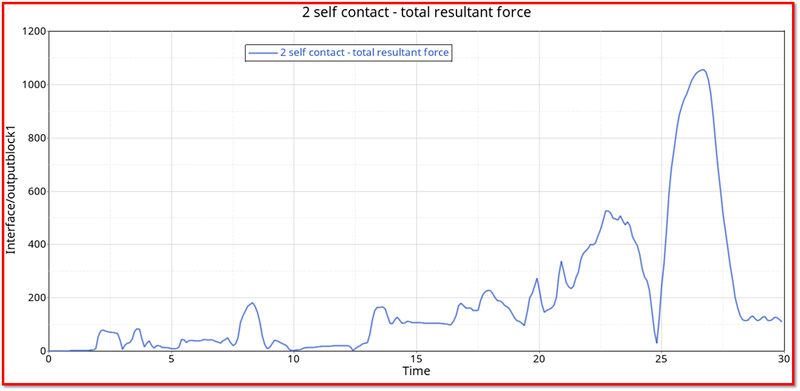
Figure 67-Contact Forces Graph [Case-2]. |
Kinetic Energy :
- The obtained graph for kinetic energy is shown in below Figure 68.Here aslo kinetic energy is similar to the previous case 1.
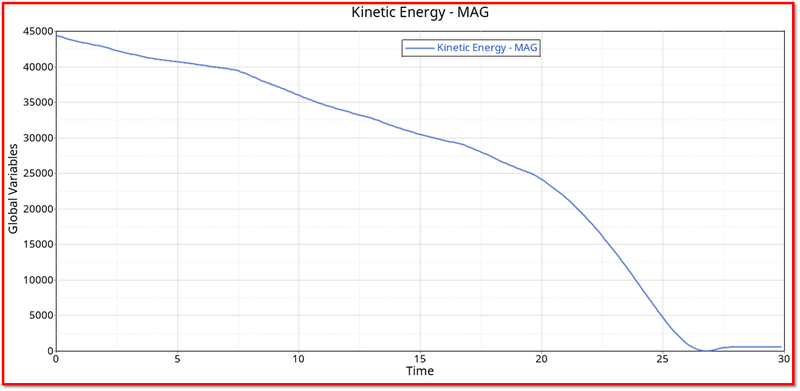
Figure 68-Kinetic Energy Graph [Case-2]. |
Contact Energy :
- The obtained graph for contact energy is shown in below Figure 69.Here aslo contact energy is similar to the previous case 1.
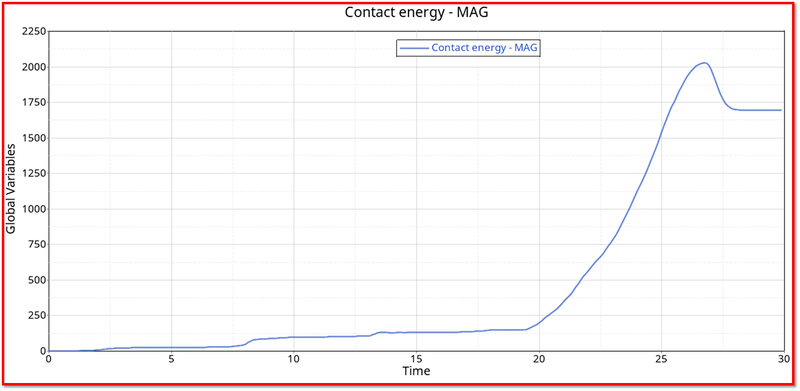
Figure 69-Contact Energy Graph [Case-2]. |
Internal Energy :
- The obtained graph for internal energy is shown in below Figure 70.Here aslo internal energy is similar to the previous case 1.
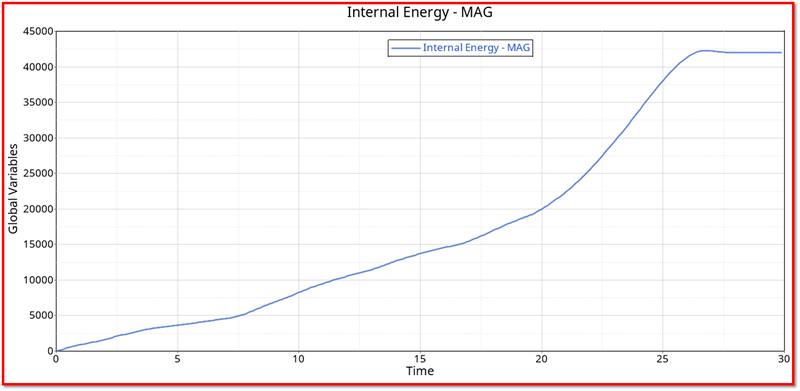
Figure 70-Internal Energy Graph [Case-2]. |
Total Energy :
- The obtained graph for total energy is shown in below Figure 71.Here aslo total energy is similar to the previous case 1.
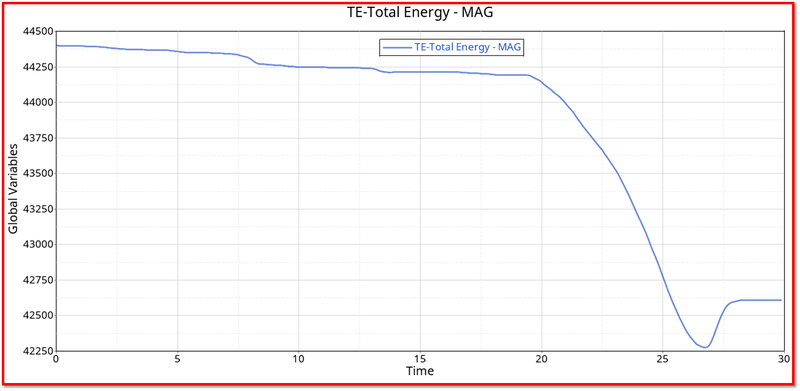
Figure 71-Total Energy Graph [Case-2]. |
Hourglass Energy :
- Here the hourglass energy is constant,Because the recommended parameter Ishell=24 has been assigned to the property card,So the hourglass energy is constant.
[Note : Hourglass Energy is constant for all the 6 cases,Because the recommended parameter Ishell=24 has been assigned to the property card,So the hourglass energy is constant.]
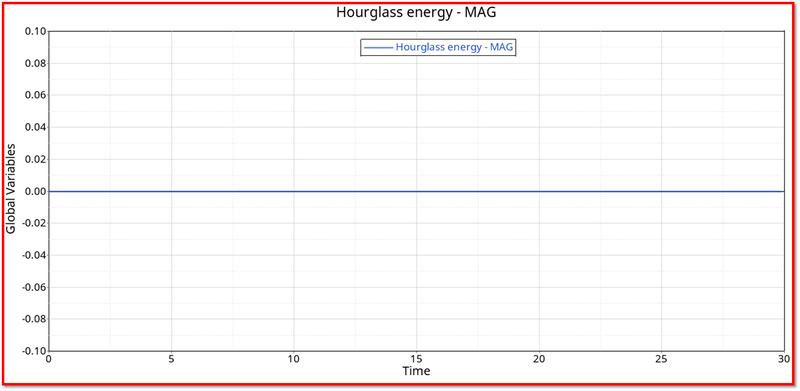
Figure 72-Hourglass Energy Graph [Case-2]. |
All Energies :
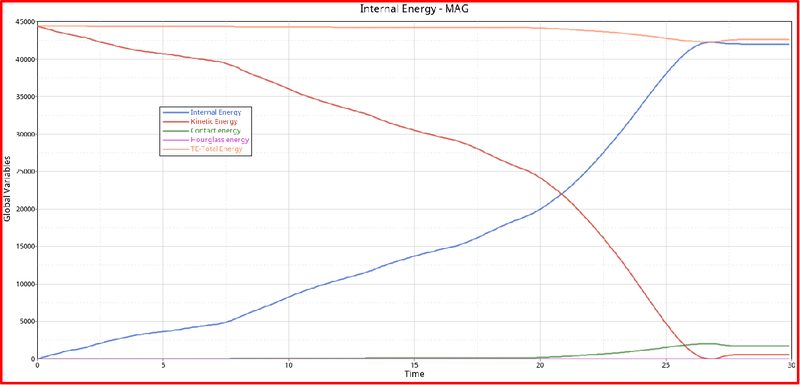
Figure 73-All Energies Graph [Case-2]. |
Case-3 Create the type 11 contact and run :
- Now for this case,we have to create new contact called Type 11 [Edge to Edge Contact].Some parameters should be given which is shown in below Figure 74.
- Here i'm giving type 7 parameters to the type 11,Cause the type 11 is similar to the type 7 contact.
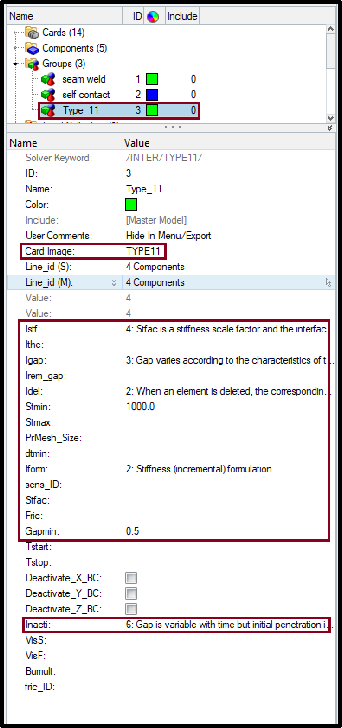
Figure 74-Type 11 Contact. |
- Now define the slave and master for the type 11 contact which is shown in below Figure 75.Select all the elements.
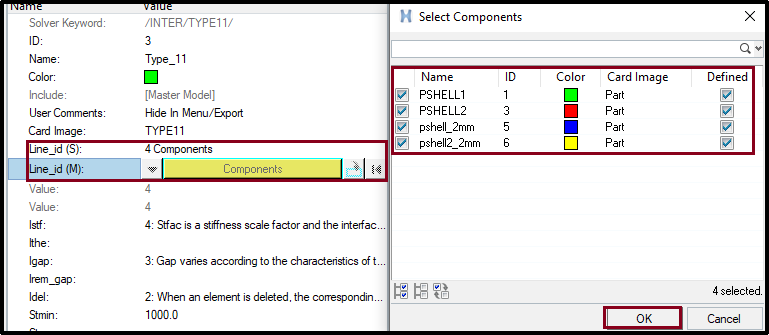
Figure 75-Defining Slave and Masters. |
- Now request for the TH.TH is requested for type 11 contact.While defining TH all the interfaces should be selected which is shown in below Figure 77.
- To create TH,Go to Solver Browser >> Right Click on TH >> Create >> Inter,Which is shown in below Figure 76.
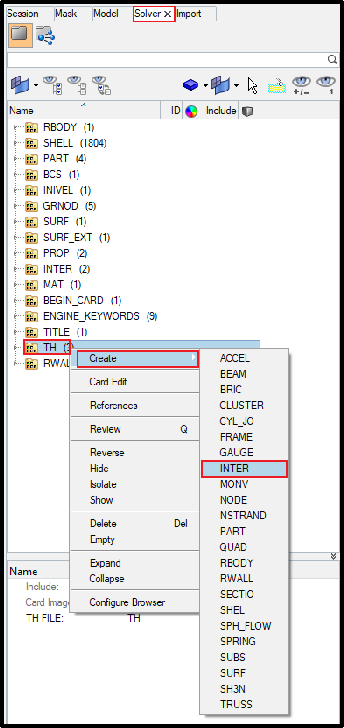
Figure 76-Creation of TH. |
- After creating TH,The contact interfaces should be assigned to that,Which is shown in below Figure 77.
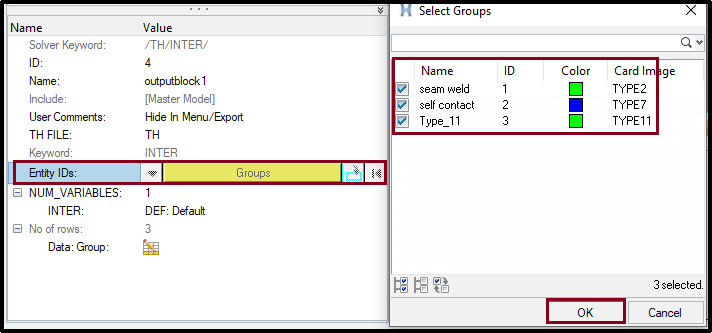
Figure 77-Contacts assigned to the TH. |
1) Review the Simulation using -HyperView.
- Now run the simulation,After running the simulation,Switch to the Hyperview and load the .H3D file to view the results of simulation which is shown in below Figure 78.
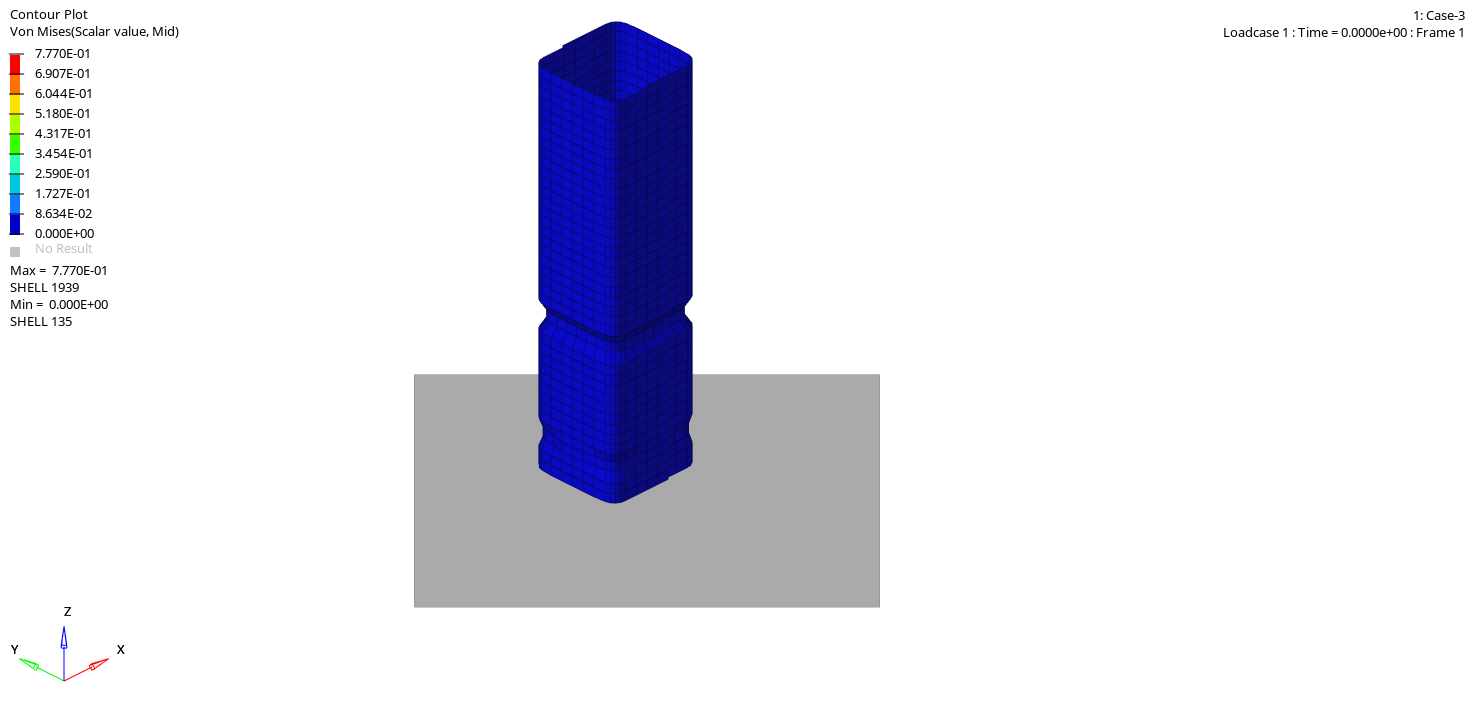
Figure 78-Case 3 Simulation Animation. |
- Now go and open the 00001.out file with notepad.
- The obtained values for Energy Error,Mass Error,Internal Energy Error,Kinetic Energy Error and Contact Energy Error has been shown in below Figure 79.
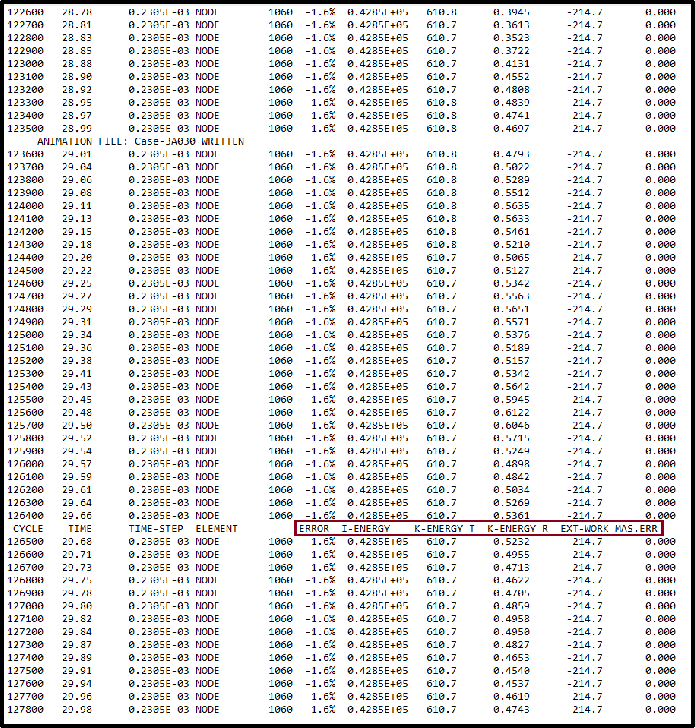
Figure 79-Obtained values for Energy Error,Mass Error,Internal Energy Error,Kinetic Energy Error and Contact Energy Error. |
2) Plot the graphs using -Hypergraph 2D.
- Here the Kinetic,Internal,Contact,Internal and Hourglass Energy is similar to the previous case.
- The graphs plotted for Kinetic,Internal,Contact,Internal and Hourglass Energy is shown in below Figure 80.
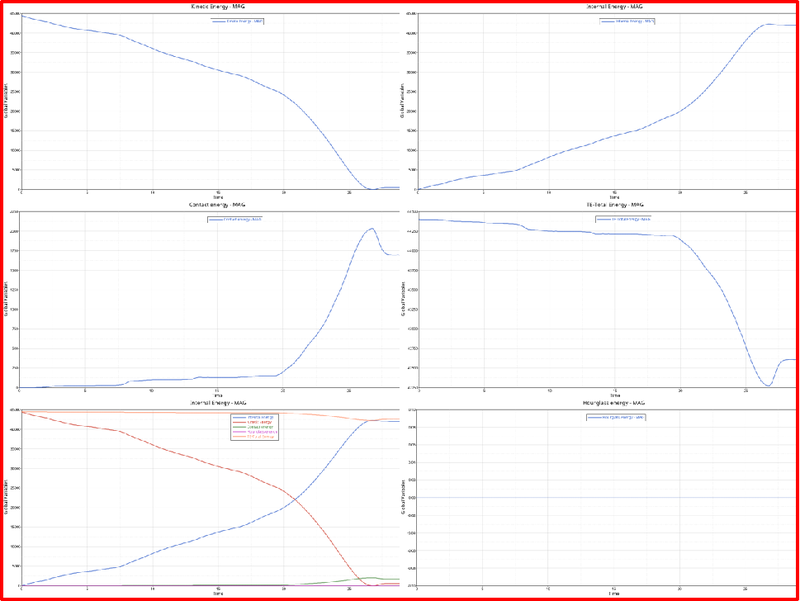
Figure 80-Graph Plotted for Kinetic,Internal,Contact,Internal and Hourglass Energy. |
Rigid Wall Forces :
- The graph obtained for the rigid wall forces is shown in below Figure 81.
- Here the rigid wall forces are increased when compared to the previous case.It is increased between the range of (1400-1600).
- They are increased cause the type 11 contact is also defined with the type 7 contact,so they are increased.
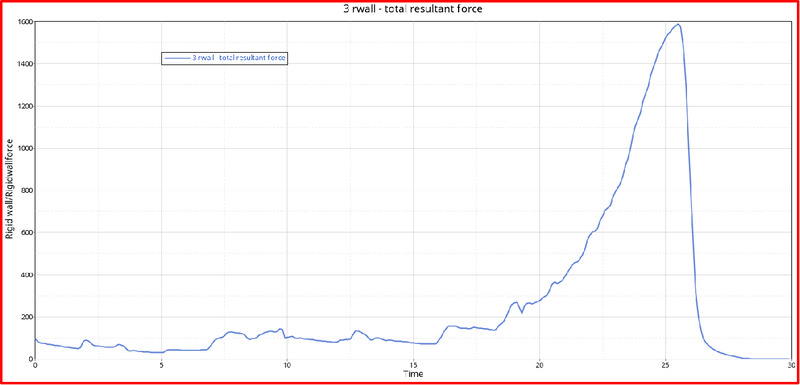
Figure 81-Rigid Wall Forces Graph [Case-3]. |
Self Contact Forces :
- The graph obtained for the contact forces is shown in below Figure 82.
- Here the contact forces starts from origin and suddenly reaches peak,Cause the all the elements come into the contact,In that time the contact forces reaches peak and decreases cause the crash tube will be in rest after collision.
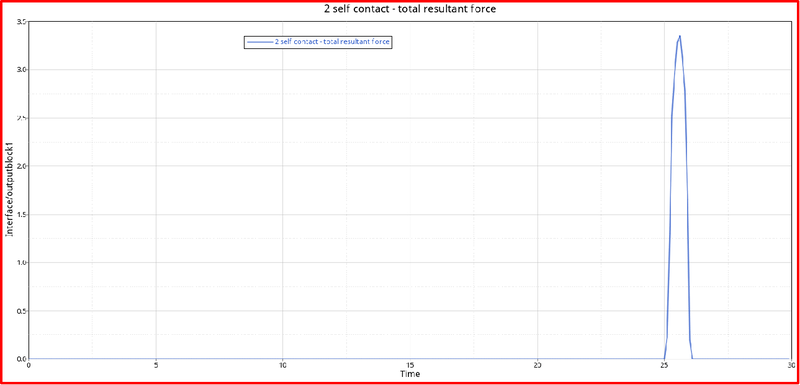
Figure 82-Self Contact Forces Graph [Case-3]. |
Type 11 Contact Forces :
- The graph obtained for the Type 11 Contact Forces is shown in below Figure 83.
- Here the Type 11 Contact Forces are starting from origin and increasing due to the elements come into the contact and its suddenly reaches at peak due to there will be no edge to edge penetration,all the elements come into the contact,So its suddenly reaches the peak.
- And its decreasing after the collison,Cause the crash tube will be at rest.
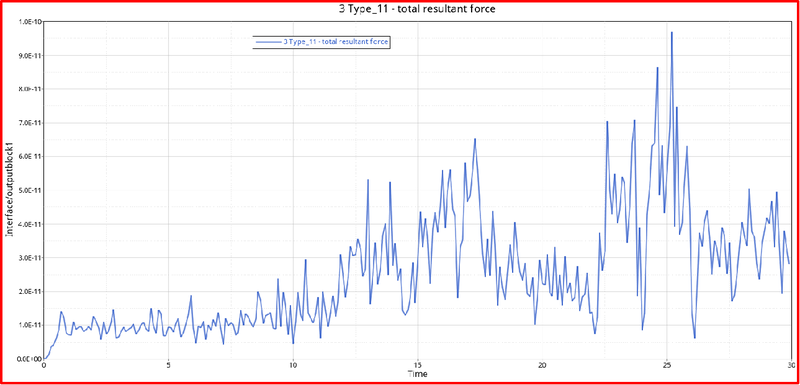
Figure 83-Type 11 Contact Forces Graph [Case-3]. |
Case 4-Remove both notches and remove boundary condition on rigid body node then run :
- Here in this case,We have to remove the notches and boundary conditions as per the question.
- To remove the notches,use align node tool and align them properly to remove the notches.
- To Align,Go to Geometry >> Node Edit >> Node 1,2,3 >> Align Node.
- The notches have been removed for this case,which is shown in below Figure 88.

Figure 84-Geometry Panel. |

Figure 85-Node Edit Sub-Panel. |
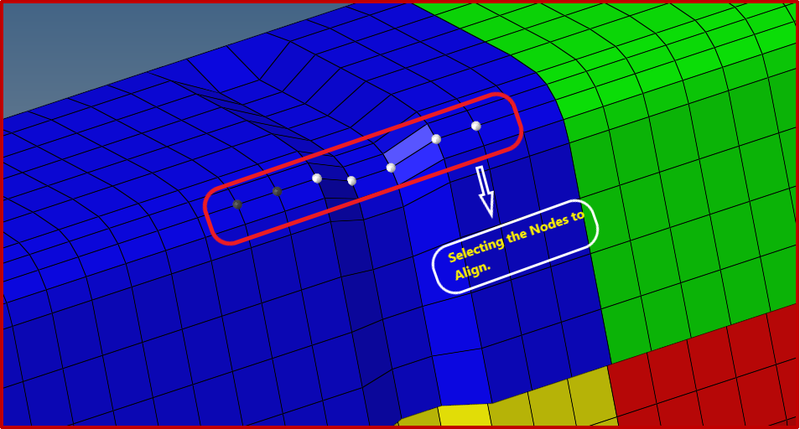
Figure 86-Selecting the Nodes to Line to Remove the Notches. |
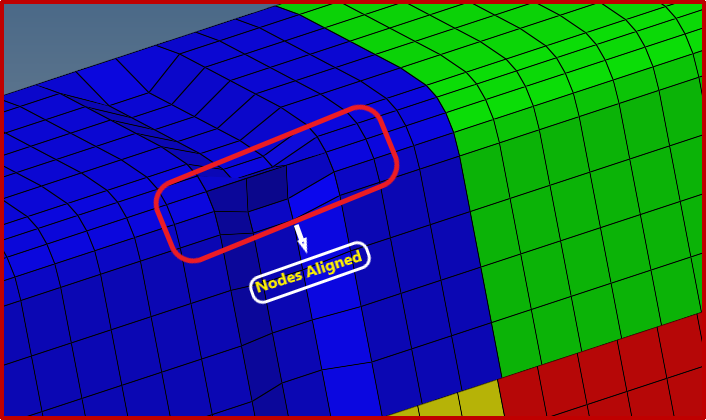
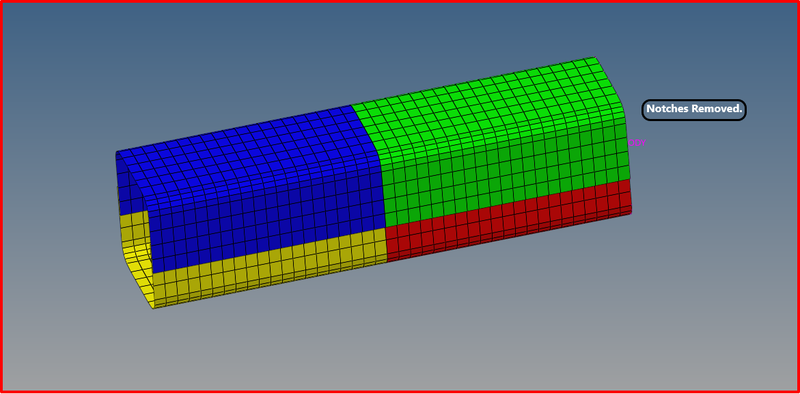
Figure 88-Notches Removed for Case 4. |
- Then Remove the Boundary Condition which is shown in below Figure 89.
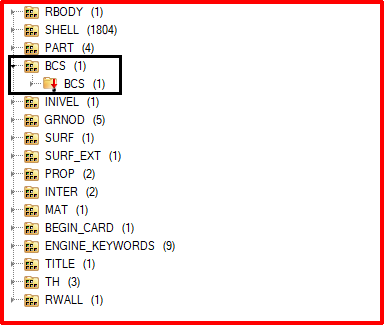
Figure 89-Remove the Boundary Condition. |
1) Review the Simulation using -HyperView.
- Now run the simulation,After running the simulation,Switch to the Hyperview and load the .H3D file to view the results of simulation which is shown in below Figure 90.
- Here the buckling is happening at the contact due to the removal of notches.
- In previous cases buckling was happening,where the notches were.
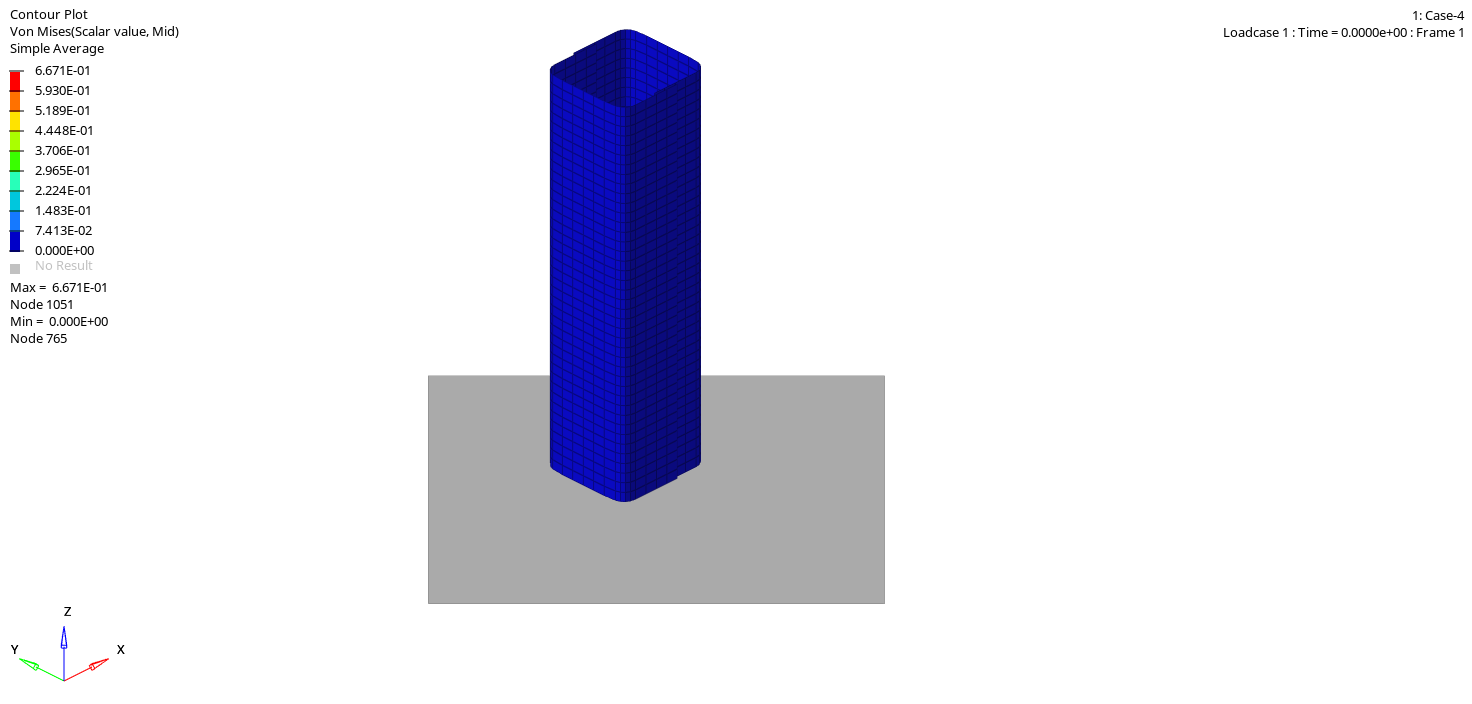
Figure-90 Case 4 Simulation Animation. |
- Now go and open the 00001.out file with notepad.
- The obtained values for Energy Error,Mass Error,Internal Energy Error,Kinetic Energy Error and Contact Energy Error has been shown in below Figure 91.
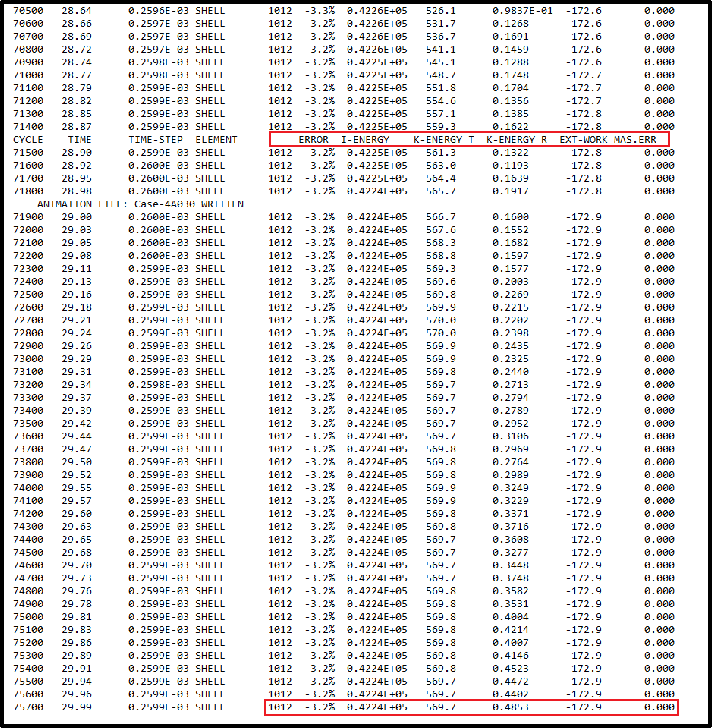
Figure 91-Obtained values for Energy Error,Mass Error,Internal Energy Error,Kinetic Energy Error and Contact Energy Error. |
2) Plot the graphs using -Hypergraph 2D.
Rigid Wall Forces :
- The obtained graph for the rigid wall forces is shown in below Figure 92.
- Here the rigid wall forces is reduced due to the removal of notches.
- The maximum rigid wall forces value obtained in this case is 1213.89.It is low when compared to the previous cases.
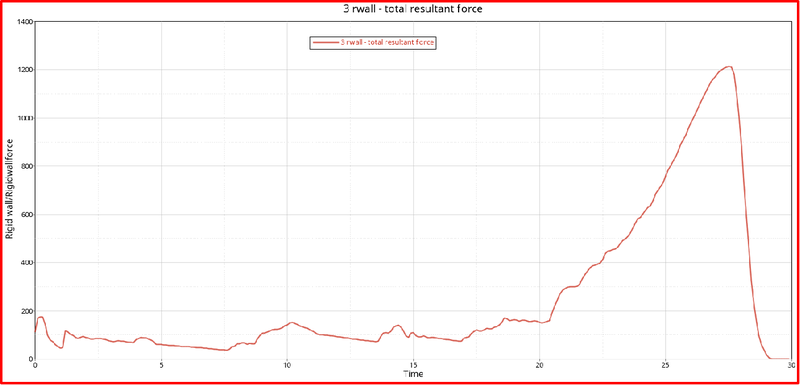
Figure 92-Rigid Wall Forces Graph [Case-4]. |
Contact Forces :
- The obtained graph for the contact forces is shown in below Figure 93.
- Here the contact forces increases faster due to the removal of notches.
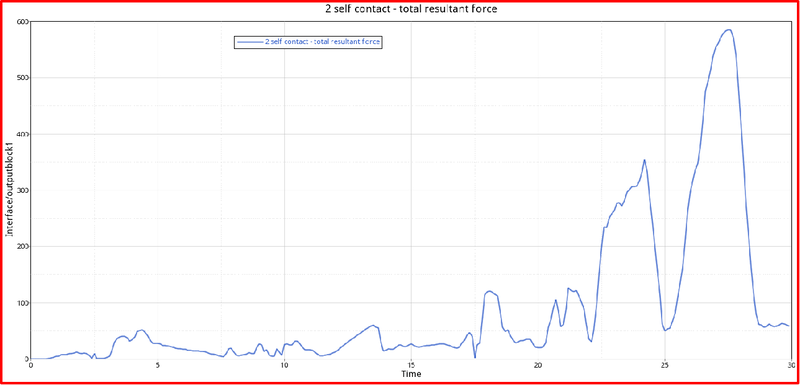
Figure 93-Contact Forces Graph [Case-4]. |
Internal Energy :
- The obtained graph for the Internal Energy is shown in below Figure 94.
- It is similar to the previous case.
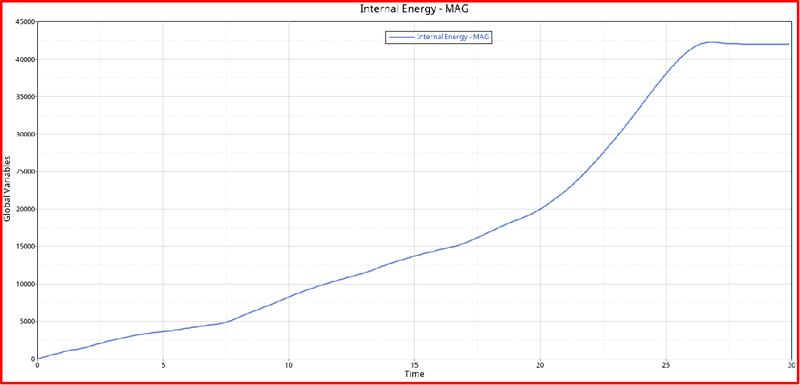
Figure 94-Internal Energy Graph [Case-4]. |
Kinetic Energy :
- The obtained graph for the Kinetic Energy is shown in below Figure 95.
- It is similar to the previous case.
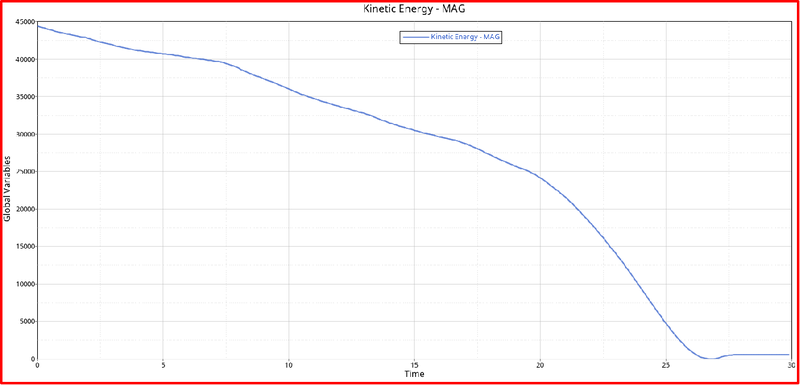
Figure 95-Kinetic Energy Graph [Case-4]. |
Total Energy :
- The obtained graph for the Total Energy is shown in below Figure 96.
- It is similar to the previous case.
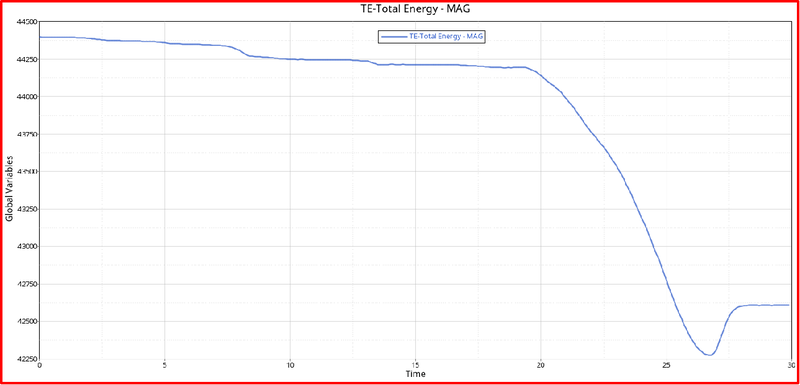
Figure 96-Total Energy Graph [Case-4]. |
All Energies :
- The obtained graph for the All Energies is shown in below Figure 97.
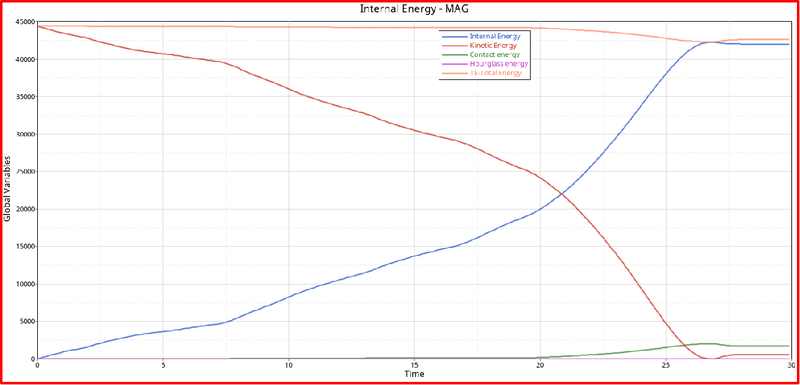
Figure 97-All Energies Graph [Case-4]. |
Case-5 Create a new notch in the middle ,select the whole section and run :
- Here for this case,Create notches in the middle by using element offset.
- To create notches in the middle,Go to 2D panel >> Element Offset >> Select Elements >> Distance=2 >> Offset+.


Figure 99-Element Offset Tool Panel. |
- Here you have to give a distance,To give a distance,Measure the distance between the notches which is shown in below Figure 100.
- Here the distance is 4,You have to offset,So give the distance as 2 to create a notches in the middle which is shown in below Figure 101.
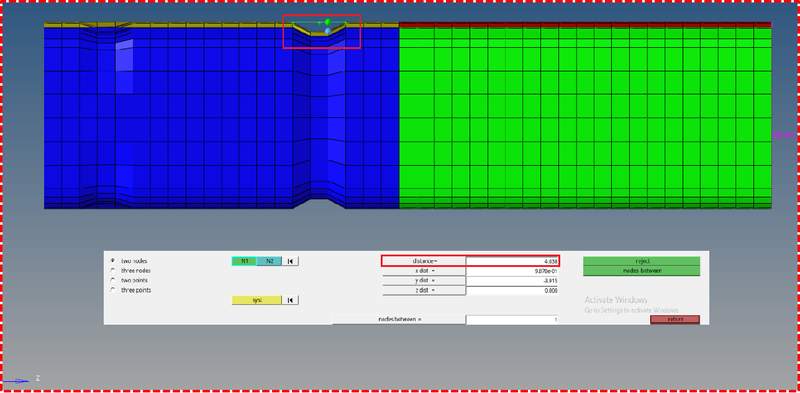
Figure 100-Measuring the Distance Between the Notches. |
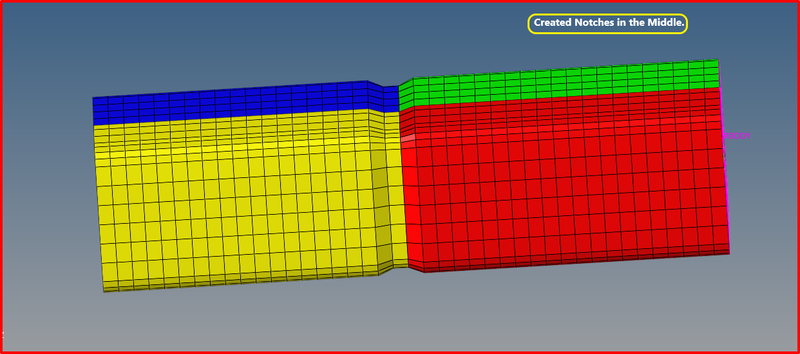
Figure 101-Notches Created in the Middle. |
1) Review the Simulation using -HyperView.
- Now run the simulation,After running the simulation,Switch to the Hyperview and load the .H3D file to view the results of simulation which is shown in below Figure 102.
- Here the buckling is happening,Where the notches exsist.
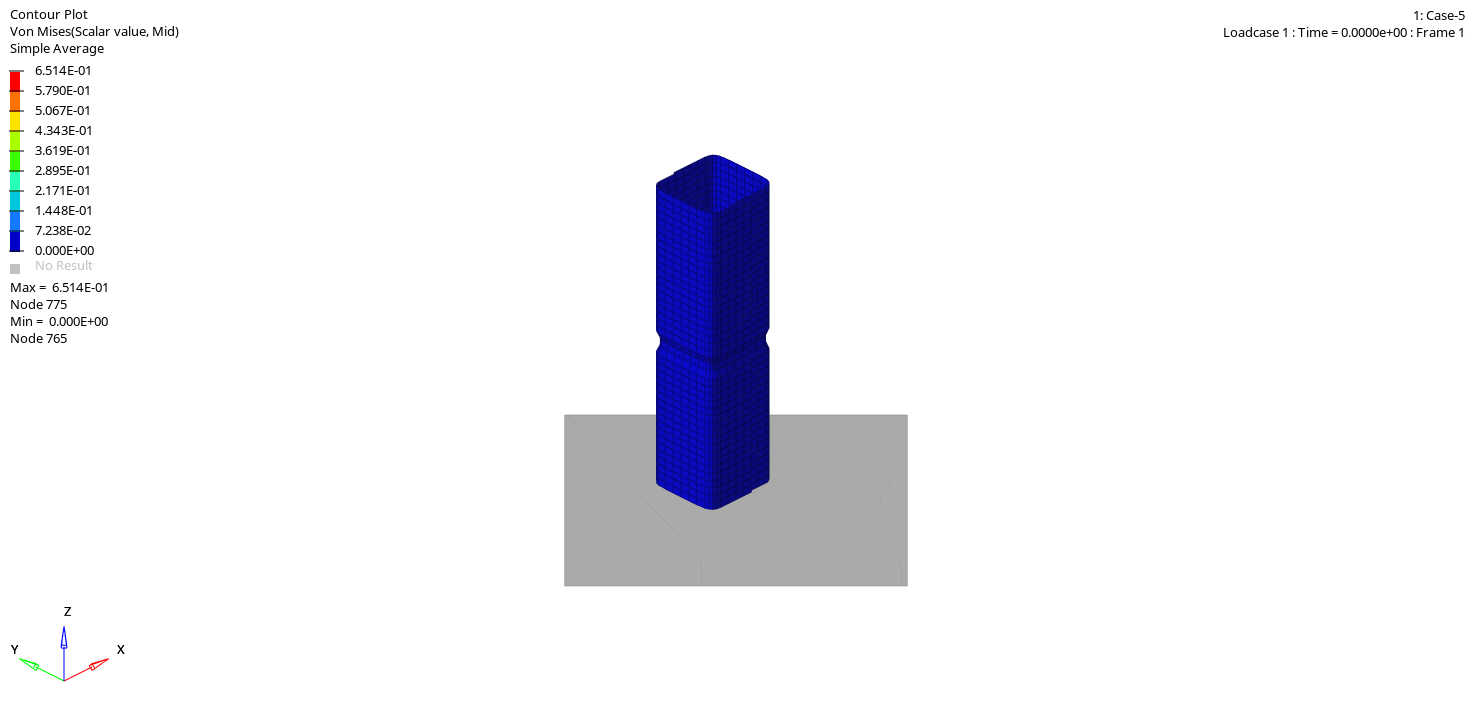
Figure-102 Case 5 Simulation Animation. |
- Now go and open the 00001.out file with notepad.
- The obtained values for Energy Error,Mass Error,Internal Energy Error,Kinetic Energy Error and Contact Energy Error has been shown in below Figure 103.
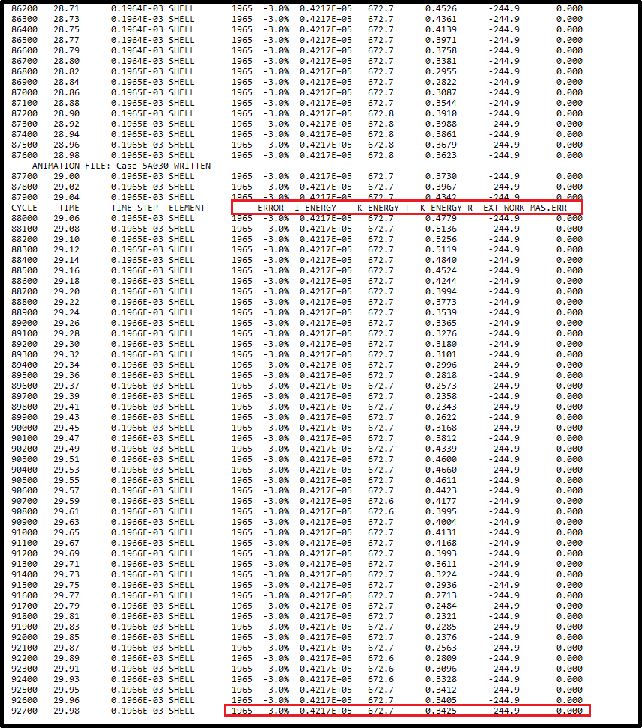
Figure 103-Obtained values for Energy Error,Mass Error,Internal Energy Error,Kinetic Energy Error and Contact Energy Error. |
2) Plot the graphs using -Hypergraph 2D.
Rigid Wall Forces :
- The obtained graph for rigid wall forces is shown in below Figure 104.
- Here the rigid wall froces are similar to the previous case,But the buckling is happeneing where the notches exsist in the crash tube.
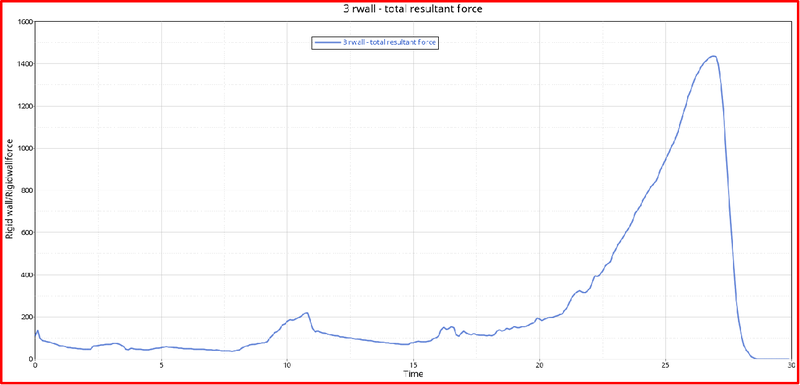
Figure 104-Rigid Wall Forces Graph [Case-5]. |
Contact Forces :
- The obtained graph for the contact forces is shown in below Figure 105.
- Here the contact forces are also some what similar to the previous cases.
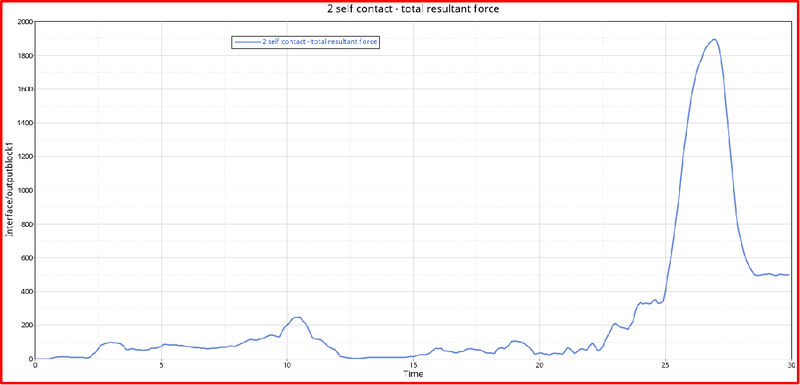
Figure 105-Contact Forces Graph [Case-5]. |
Internal Energy :
- The obtained graph for the Internal Energy is shown in below Figure 106.
- It is similar to the previous case.
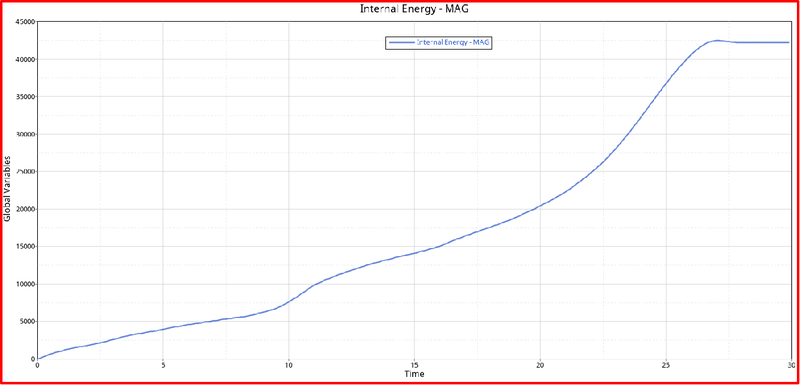
Figure 106-Internal Energy Graph [Case-5]. |
Kinetic Energy :
- The obtained graph for the Kinetic Energy is shown in below Figure 107.
- It is similar to the previous case.
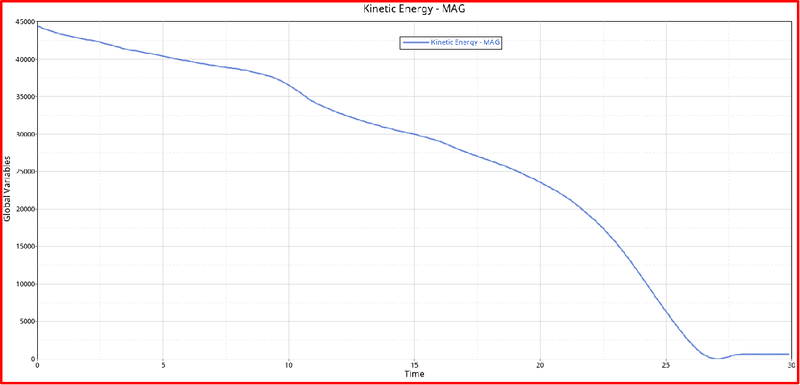
Figure 107-Kinetic Energy Graph [Case-5]. |
Total Energy :
- The obtained graph for the Total Energy is shown in below Figure 108.
- It is similar to the previous case.
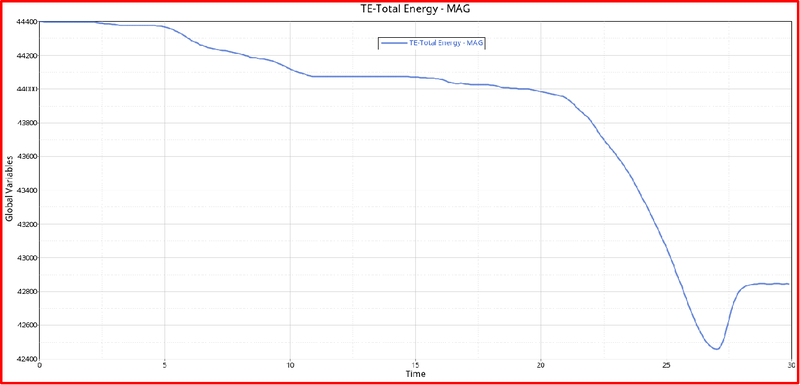
Figure 108-Total Energy Graph [Case-5]. |
All Energies :
- The obtained graph for the All Energies is shown in below Figure 109.
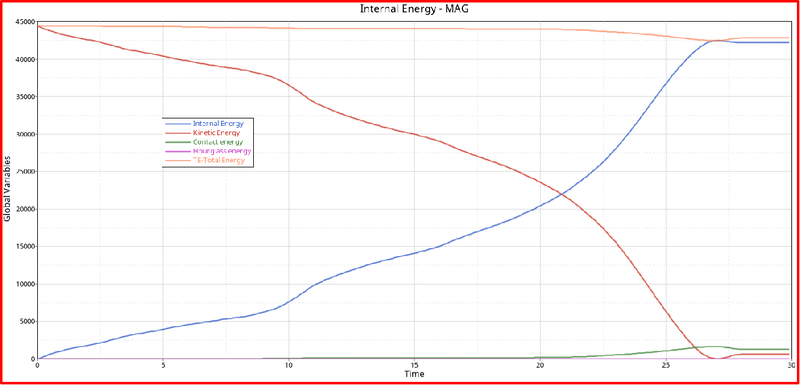
Figure 109-All Energies Graph [Case-5]. |
Case-6 Create a new notch with nodes only from opposing 2 faces and run :
- Here for this case create a notches in the two opposit faces and run the simulation.
- The notches created in the two opposite faces is shown in below Figure 110
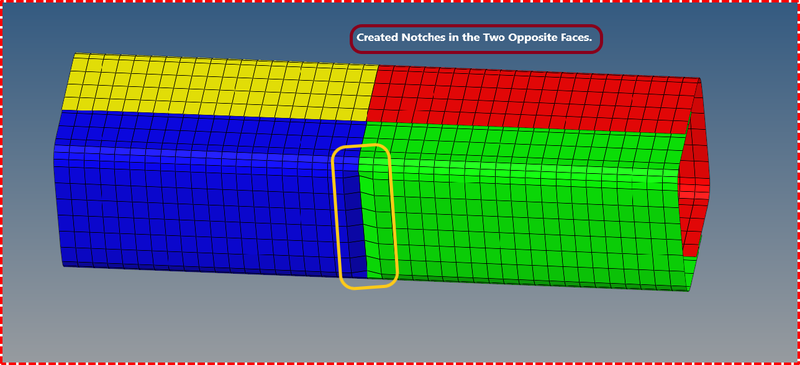
Figure 110-Notches Created in the Two Opposite Faces. |
1) Review the Simulation using -HyperView.
- Now run the simulation,After running the simulation,Switch to the Hyperview and load the .H3D file to view the results of simulation which is shown in below Figure 111.
- Here also the buckling is happening,Where the notches exsist.

_1633009394.gif)
Figure-111 Case 6 Simulation Animation. |
- Now go and open the 00001.out file with notepad.
- The obtained values for Energy Error,Mass Error,Internal Energy Error,Kinetic Energy Error and Contact Energy Error has been shown in below Figure 112.

Figure 112-Obtained values for Energy Error,Mass Error,Internal Energy Error,Kinetic Energy Error and Contact Energy Error. |
2) Plot the graphs using -Hypergraph 2D.
Rigid Wall Forces :
- The obtained graph for rigid wall forces is shown in below Figure 113.
- Here the rigid wall forces are similar to the previous case,But the buckling is happeneing where the notches have been created in the crash tube.
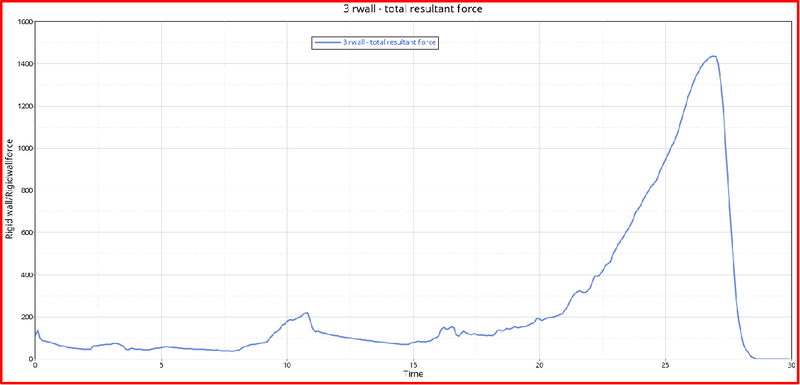
Figure 113-Rigid Wall Forces Graph [Case-6]. |
Contact Forces :
- The obtained graph for the contact forces is shown in below Figure 114.
- Here the contact forces are also some what similar to the previous cases.
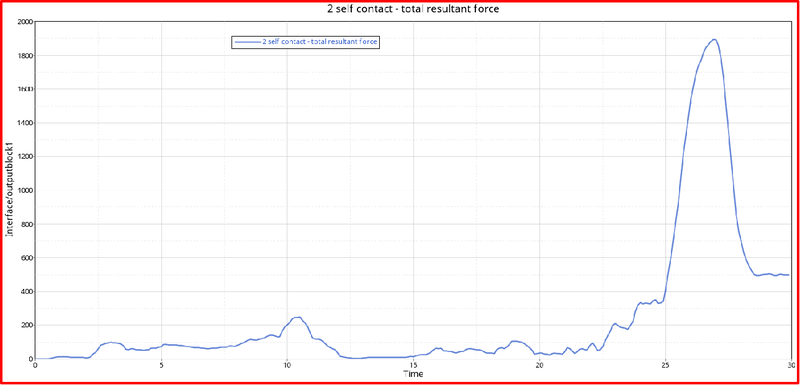
Figure 115-Contact Forces Graph [Case-6]. |
Internal Energy :
- The obtained graph for the Internal Energy is shown in below Figure 116.
- It is similar to the previous case.
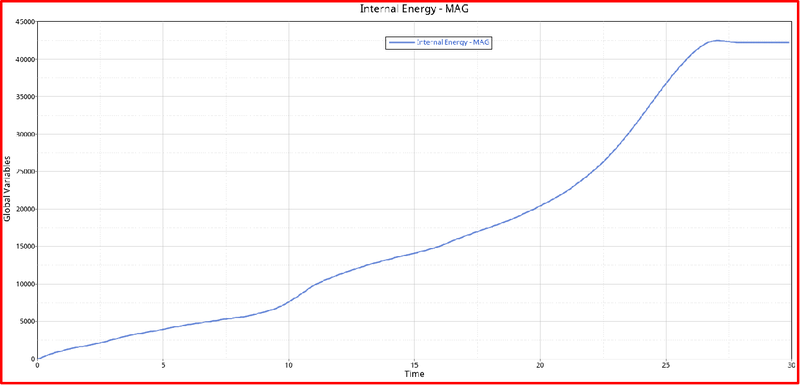
Figure 116-Internal Energy Graph [Case-6]. |
Kinetic Energy :
- The obtained graph for the Kinetic Energy is shown in below Figure 117.
- It is similar to the previous case.
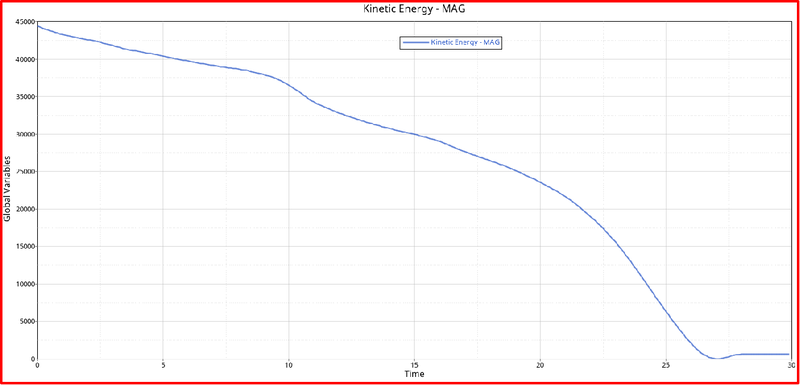
Figure 117-Kinetic Energy Graph [Case-6]. |
Total Energy :
- The obtained graph for the Total Energy is shown in below Figure 118.
- It is similar to the previous case.
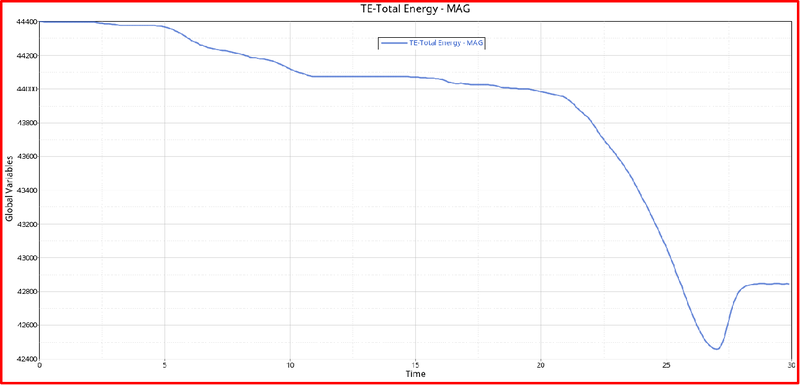
Figure 118-Total Energy Graph [Case-6]. |
All Energies :
- The obtained graph for the All Energies is shown in below Figure 119.
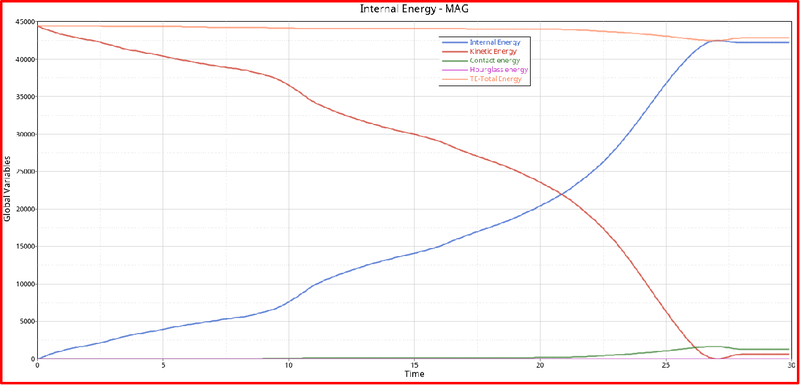
Figure 119-All Energies Graph [Case-6]. |
Comparison of all the Cases -
Cases |
Energy Error |
Internal Energy |
Kinetic Energy |
External Work |
Mass Error |
Elapsed Time |
Total Number of Cycles |
Interface Type |
Changes in Model |
Case-1 |
-3.8% |
0.4202E+05 |
592.6 |
-105.2 |
0.000 |
373.09 s |
83496 |
TYPE 7 |
No Change. |
Case-2 |
-3.8% |
0.4202E+05 |
592.6 |
-105.2 |
0.000 |
197.72 s |
83496 |
TYPE 7 |
Changed into Inacti=6. |
Case-3 |
-1.6% |
0.4285E+05 |
610.7 |
-214.7 |
0.000 |
1313.44 s |
127876 |
TYPE 11 and TYPE 7 |
Changed into Recommended Parameters. |
Case-4 |
-3.2% |
0.4224E+05 |
569.7 |
-172.9 |
0.000 |
487.83 s |
75741 |
TYPE 11 and TYPE 7 |
Removed Notches and Boundary Conditions. |
Case-5 |
-3.0% |
0.4217E+05 |
672.7 |
-244.9 |
0.000 |
572.15 s |
92781 |
TYPE 11 and TYPE 7 |
Created Notches in the Middle. |
Case-6 |
-3.1% |
0.4214E+05 |
532.6 |
-365.6 |
0.000 |
526.16 s |
97519 |
TYPE 11 and TYPE 7 |
Created Notches in the Opposite Faces Only. |
Table-1
Result :
- Hence the simulation for all the cases were carried out with different parameters.
- Hence the simulation for all the cases were runned successfully.
- Hence the simulation for all the cases were reviewed by hyperview.
- Hence the graphs were plotted for all the cases successfully.
- Hence meshed the bumper component with 6 mm size.
- Atlast,Compared all the results for those cases.
Conclusion and Learning Outcome :
- In this challenge,I came to know bout
- The types of interfaces and their applications.
- The effect of notches in the model.
- The penetration causes.
- The diferent parameters for the interfaces.
- The elements deformation during the interface.