OBJECTIVE:
The main aim of this project is to analyze the different material card cases given and to derive the case which represents the on-field scenario.
_1604855345.jpg)
_1604855378.jpg)
DESCRIPTION:
case1:
- imported the given failure_johnson_0.rad file in the hypermesh GUI.
- simulation is done with the material card of law2_PLAST_JOHNS and failure johnson card shown below.
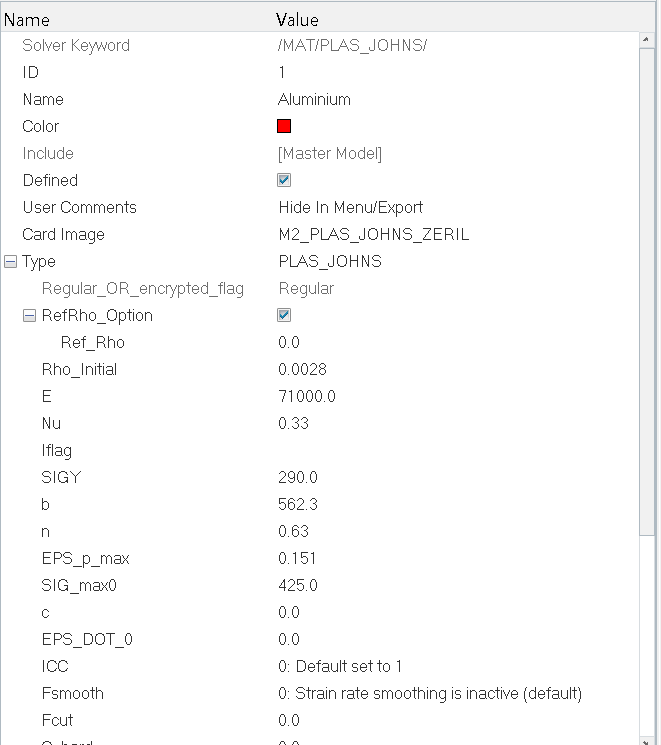
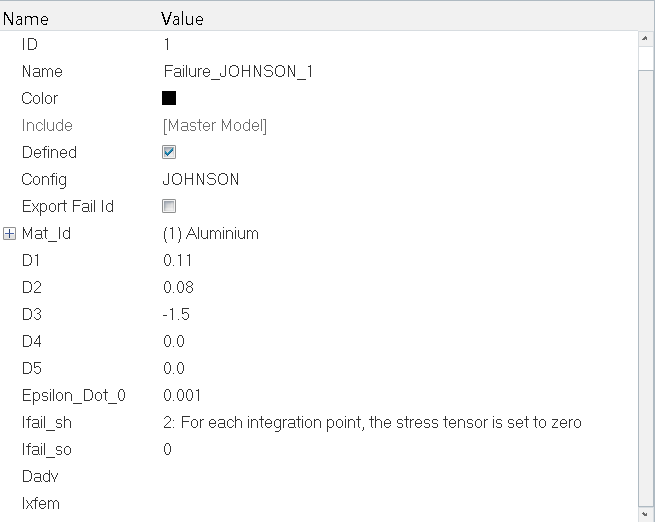
- imported the .h3d file in the Hyperview and .T01 in Hypergraph.
- the animation for vonmesis stress is observed and the graph for internal energy, kinetic energy, contact energy, hourglass energy, total energy are plotted.
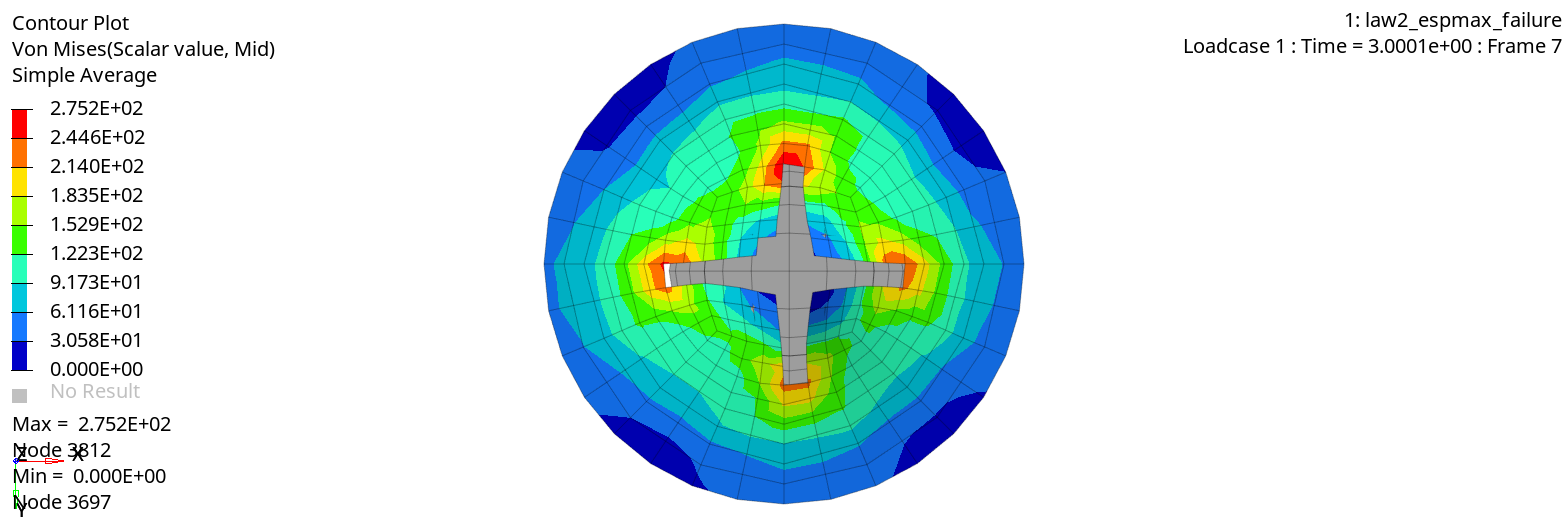
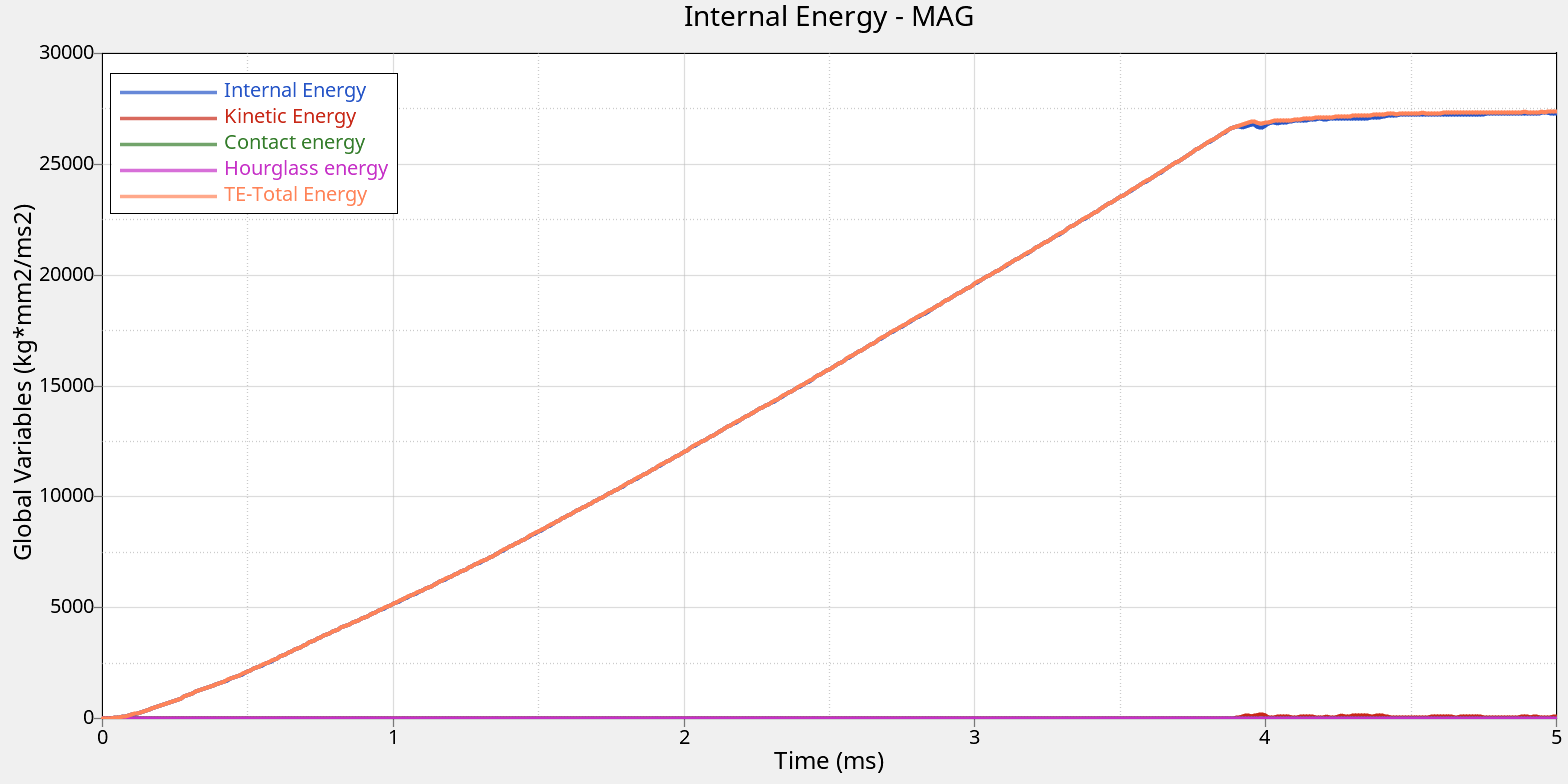
Observation:
- the material seems to be stiff.
- there is a sudden rupture at 4.0001e+00 ms.
- where the internal energy increases gradually until the material gets rupture.
- the maximum vonmises stress observed is 2.752E+02 i,e.275.2 N/mm^2.
- there is a small peak in kinetic energy at the time of rupture.
- the number of cycles for the simulation is 49379.
- the energy error ranges from -0.6% to 1.3%.
- there is no amount of mass added to the material, mass error=0.
- the simulation time is 5.010 ms.
- the removal of elements is due to the values Ixfem=0(elements get removed) and equivalent plastic strain,eps_p_max=0.151 i,e.15.1%.
- the contact energy and hourglass energy is removed completely.
- the total energy increases gradually as shown in the plot, approximately follows the same path as the internal energy develops.
case2:
- modifications to the failure johnson card are done as shown below.
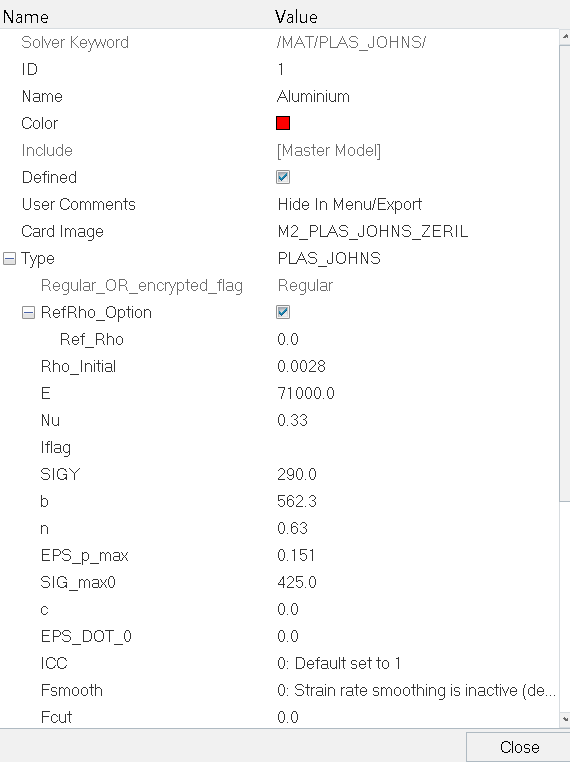
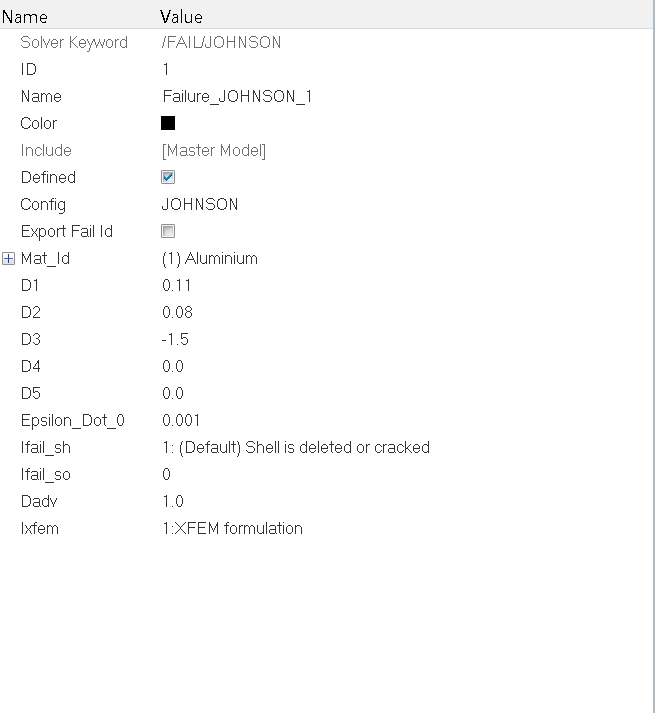
- imported the .h3d file in the Hyperview and .T01 in Hypergraph.
- the animation for vonmesis stress is observed and the graph for internal energy, kinetic energy, contact energy, hourglass energy, total energy are plotted.
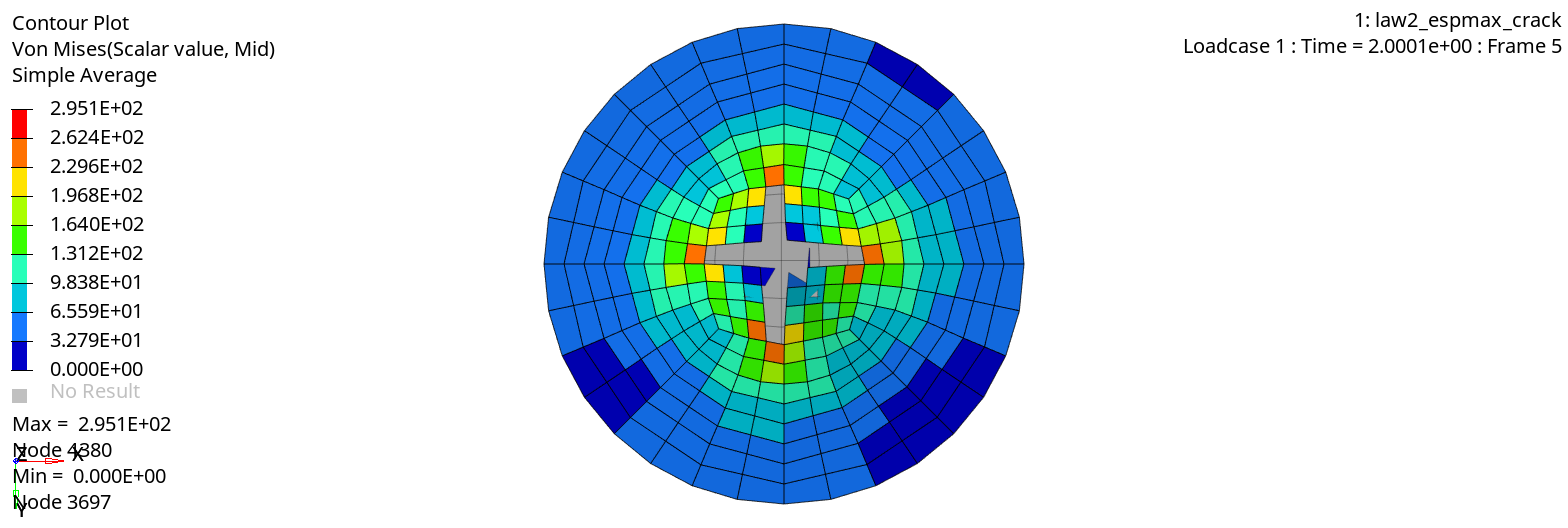
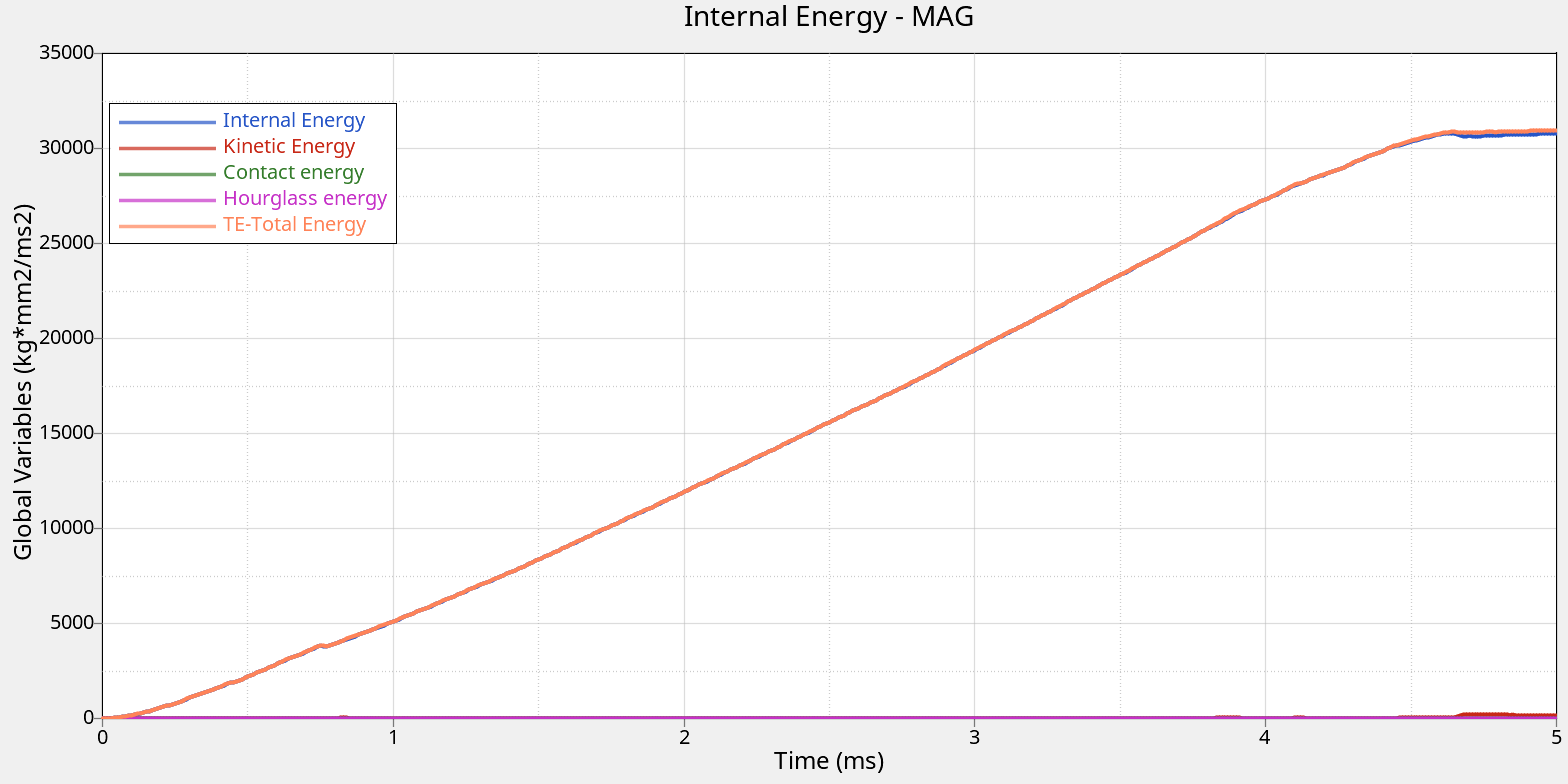
observation:
- Here, the crack in the elements occurs at the beginning as shown below, due to the value Ixfem=1.
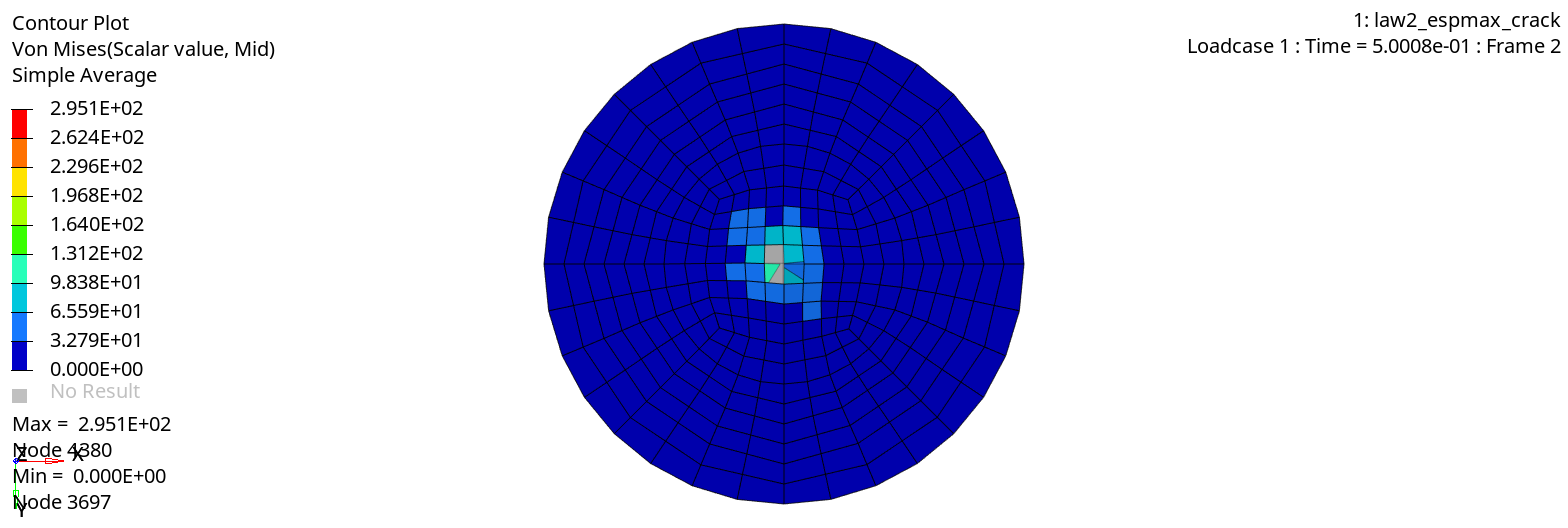
- but the equivalent plastic strain eps_p_max=0.151 makes the deletion when the plastic strain reaches 15.1%.
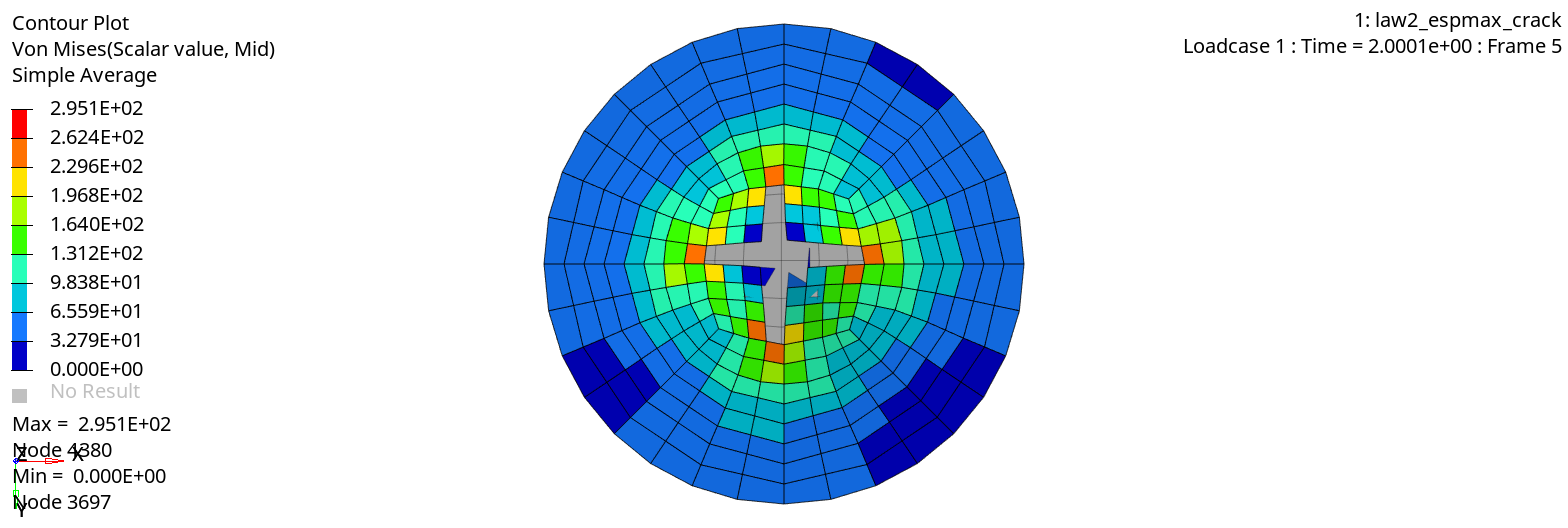
- also done observation by assigning eps_p_max=0.80 and ixfem=1, where the crack develops when the elements fail before it reaches 80%.
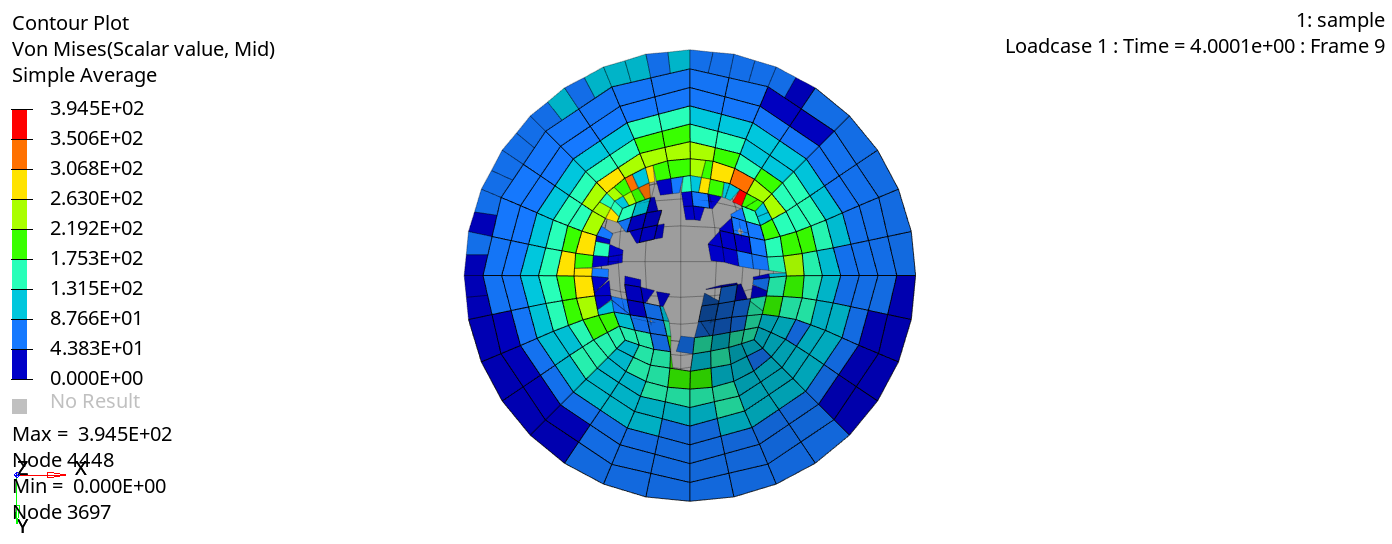
- where the internal energy increases gradually until the material gets rupture.
- the rupture happens at 4.5ms.
- the maximum vonmises stress observed is 2.951E+02 i,e.295.1 N/mm^2.
- the number of cycles for the simulation is 49216.
- the energy error ranges from -1.1% to 5.9%.
- there is no amount of mass added to the material, mass error=0.
- the simulation time is 5.010 ms.
- the contact energy and hourglass energy is removed completely.
- the total energy increases gradually as shown in the plot, approximately follows the same path as the internal energy develops.
- there is a small peak in kinetic energy at the time of rupture.
case3:
- simulation is done with the material card as shown below, but not with the failure johnson card.

- imported the .h3d file in the Hyperview and .T01 in Hypergraph.
- the animation for vonmesis stress is observed and the graph for internal energy, kinetic energy, contact energy, hourglass energy, total energy are plotted.
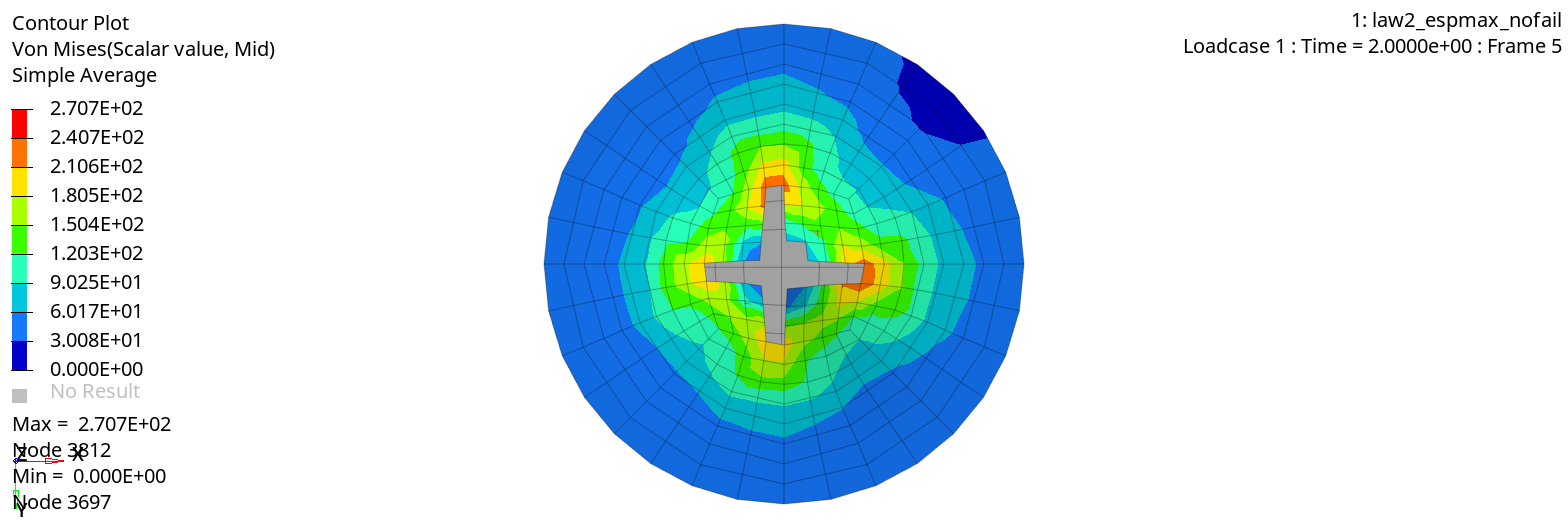
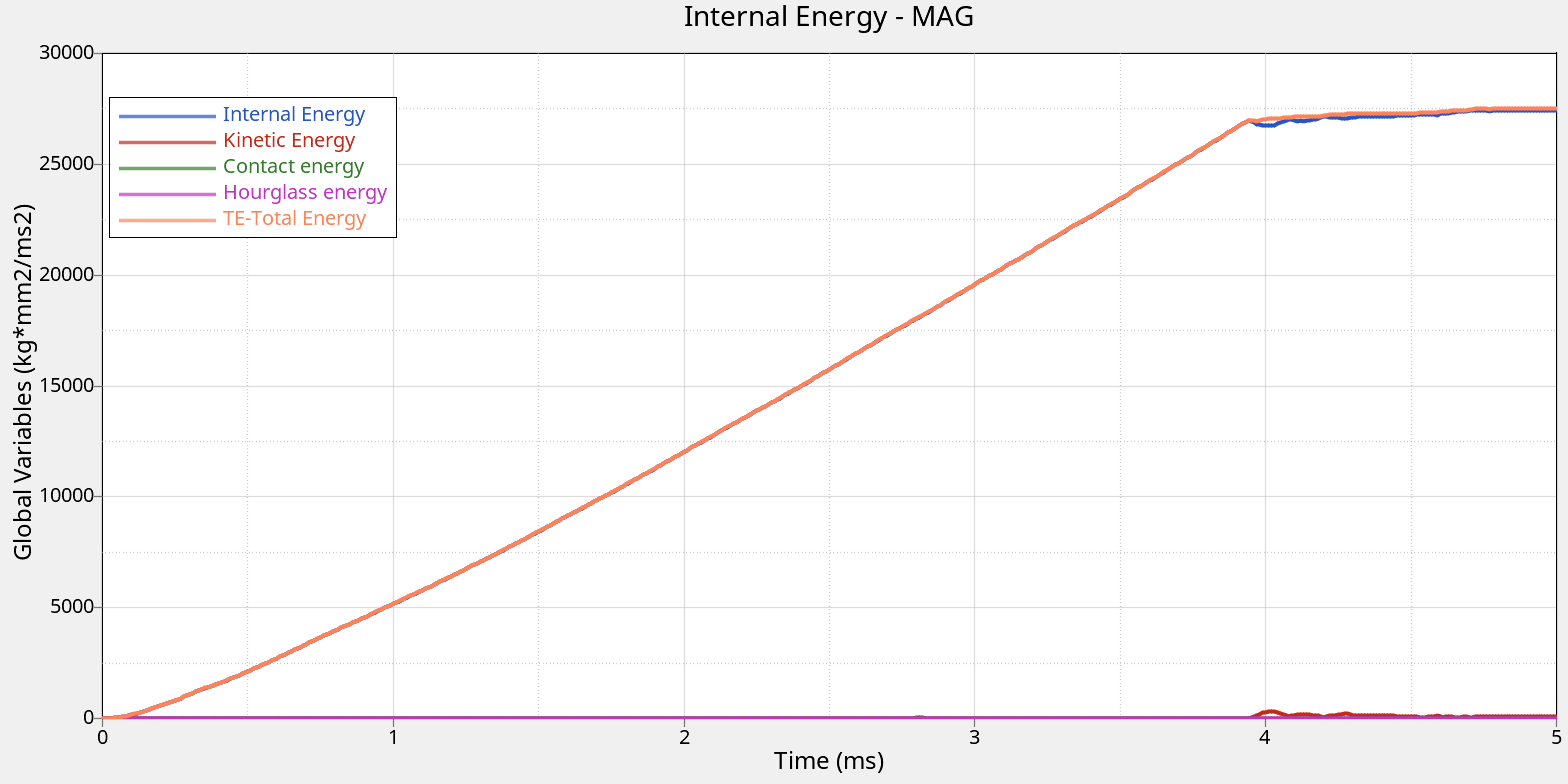
observation:
- the removal of elements is due to the value equivalent plastic strain,eps_p_max=0.151 i,e.15.1%.
- the maximum vonmises stress observed is 2.707E+02 i,e.270.7 N/mm^2.
- the rupture starts at 4ms.
- the number of cycles for the simulation is 49407.
- the energy error ranges from -0.6% to 1.2%.
- there is no amount of mass added to the material, mass error=0.
- the simulation time is 5.010 ms.
- where the internal energy increases gradually until the material gets rupture.
- the contact energy and hourglass energy is removed completely.
- the total energy increases gradually as shown in the plot, approximately follows the same path as the internal energy develops.
- there is a small peak in kinetic energy at the time of rupture.
case4:
- simulation is done with the eps_p_max=0 in the material card and with the failure johnson card as shown below
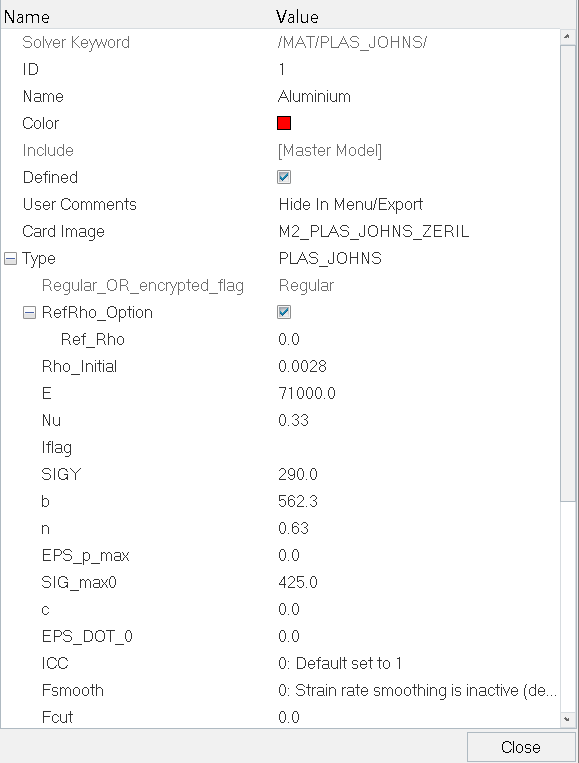
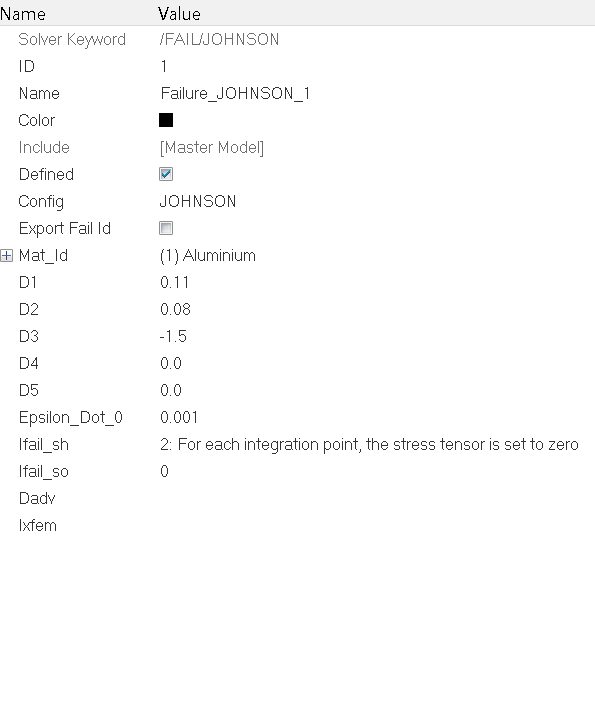
- imported the .h3d file in the Hyperview and .T01 in Hypergraph.
- the animation for vonmesis stress is observed and the graph for internal energy, kinetic energy, contact energy, hourglass energy, total energy are plotted.
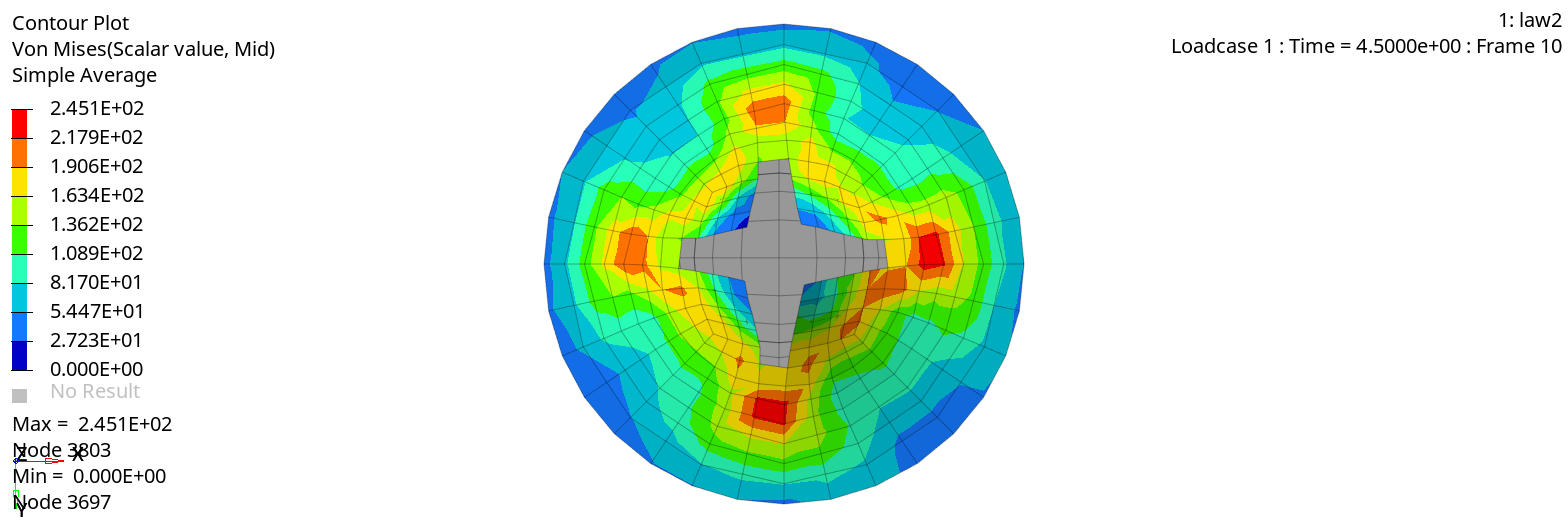
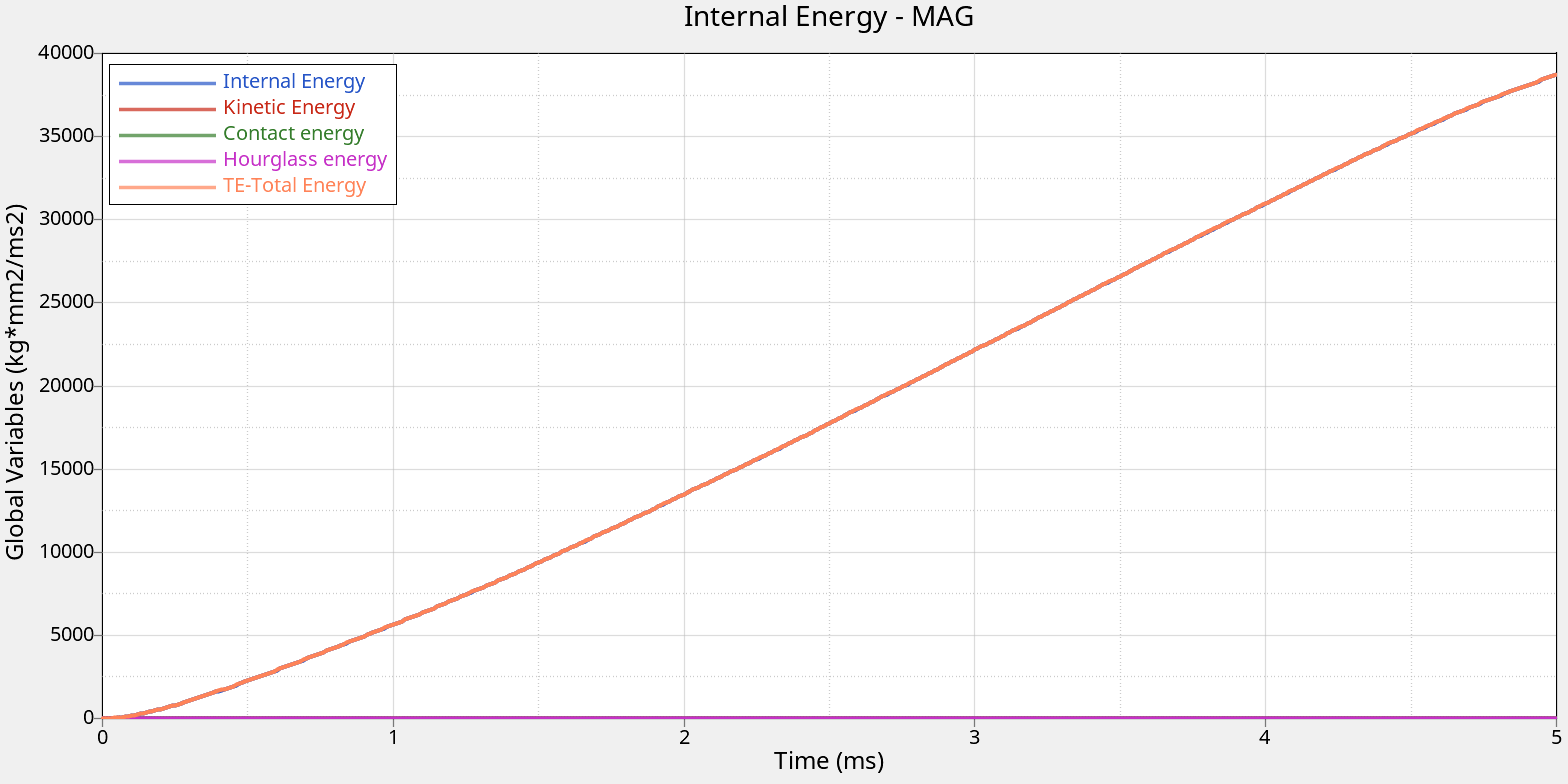
observation:
- there is no sudden rupture happening in the aluminum material.
- the internal energy increases gradually throughout the simulation of 5ms.
- the maximum vonmises stress observed is 2.451E+02 i,e.245.1N/mm^2.
- the removal of elements is due to the value Ixfem=0(just remove the elements).
- the number of cycles for the simulation is 49303.
- the energy error ranges from -0.6% to 1.2%.
- there is no amount of mass added to the material, mass error=0.
- the simulation time is 5.010 ms.
- the kinetic energy, contact energy, and hourglass energy is removed completely.
- the total energy increases gradually as shown in the plot, approximately follows the same path as the internal energy develops.
case5:
- converted the material card to law1 elastic, as shown below.
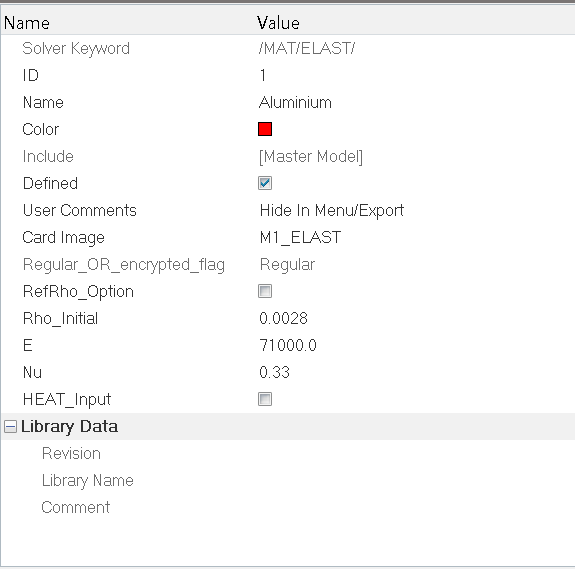
- imported the .h3d file in the Hyperview and .T01 in Hypergraph.
- the animation for vonmesis stress is observed and the graph for internal energy, kinetic energy, contact energy, hourglass energy, total energy are plotted.
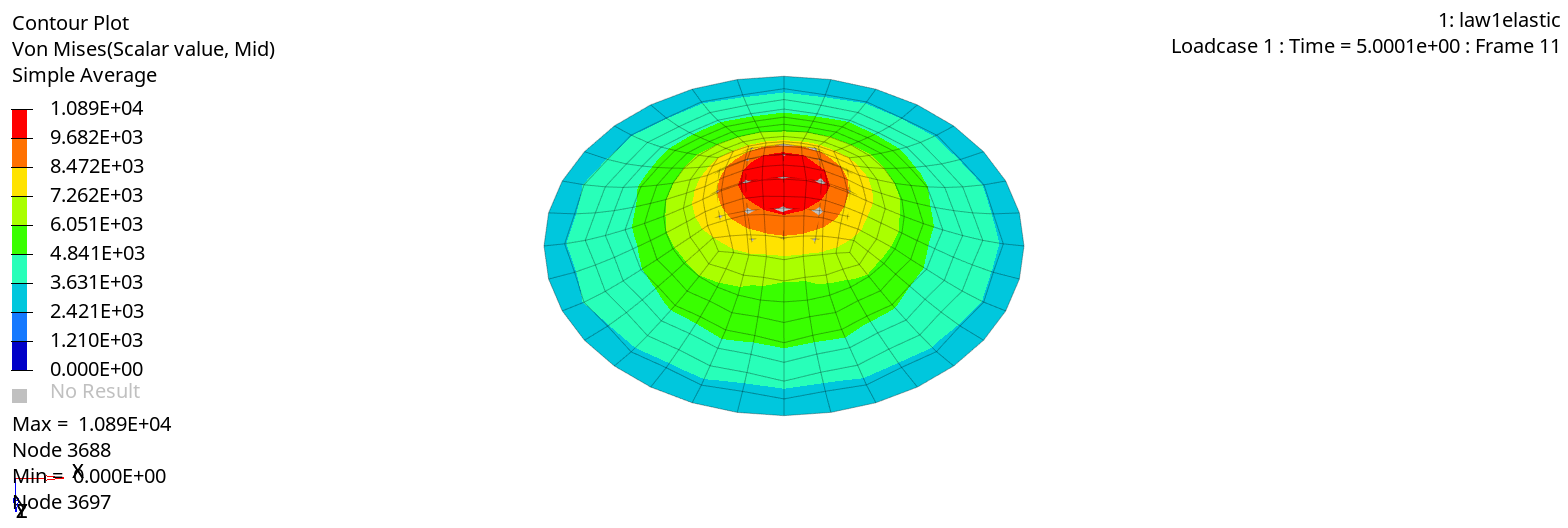
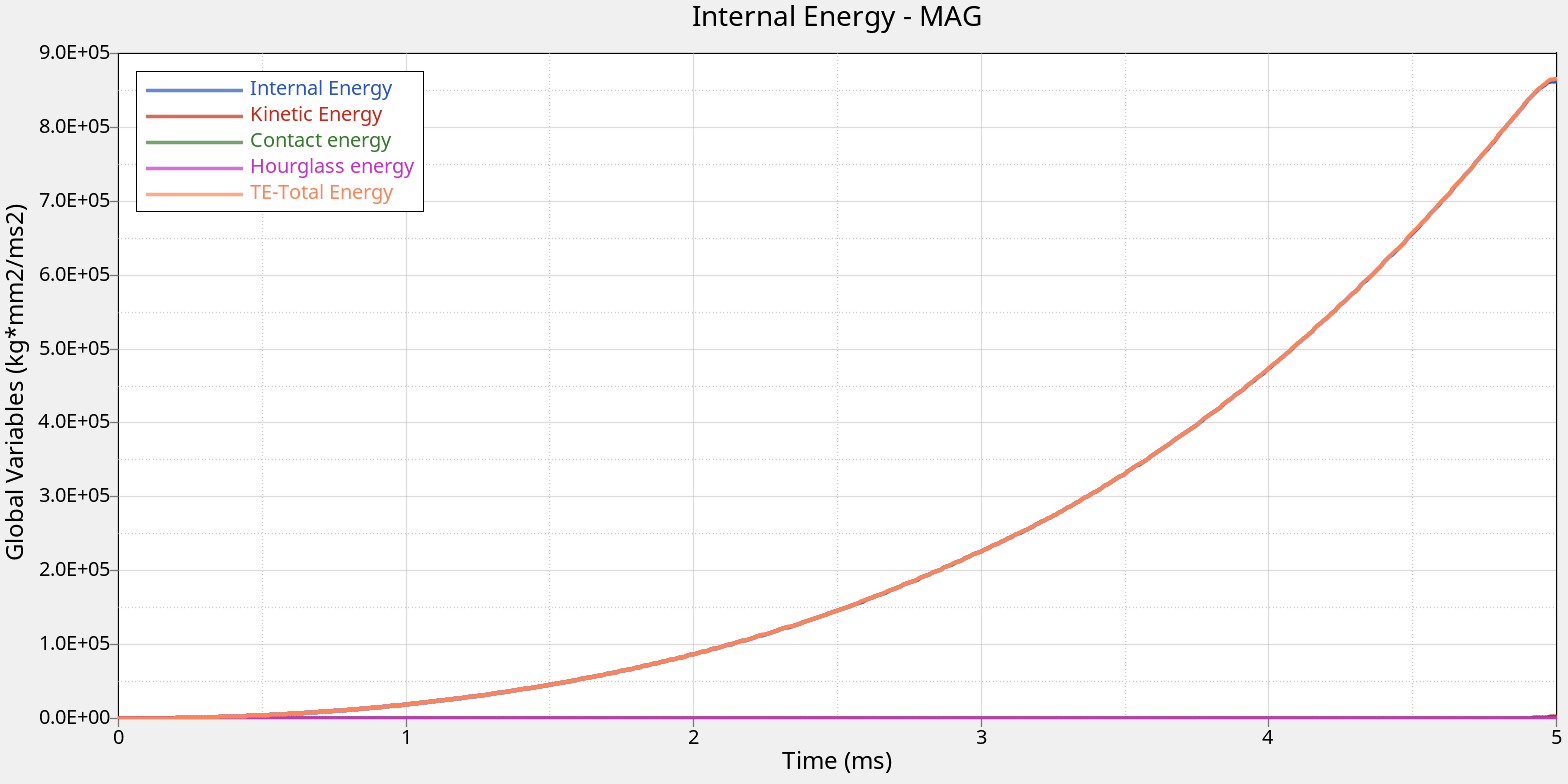
observation:
- there is no rupture in the material.
- the maximum vonmises stress observed is 1.089E+04 i,e.10890 N/mm^2.
- the element removal or cracks are absent in this case, because of law1-isotropic linear material stressed within hooks law.
- the number of cycles for the simulation is 47968.
- the energy error ranges from -0.6% to 4%.
- there is no amount of mass added to the material, mass error=0.
- the simulation time is 5.010 ms.
- the internal energy increases gradually throughout the simulation of 5ms.
- there is a small peak in kinetic energy at the end of the simulation.
- the total energy increases gradually as shown in the plot, approximately follows the same path as the internal energy develops.
- the kinetic energy, contact energy, and hourglass energy is removed completely.
case6:
- simulation is done with the material card of law-27_PLAST_BRIT, as shown below.
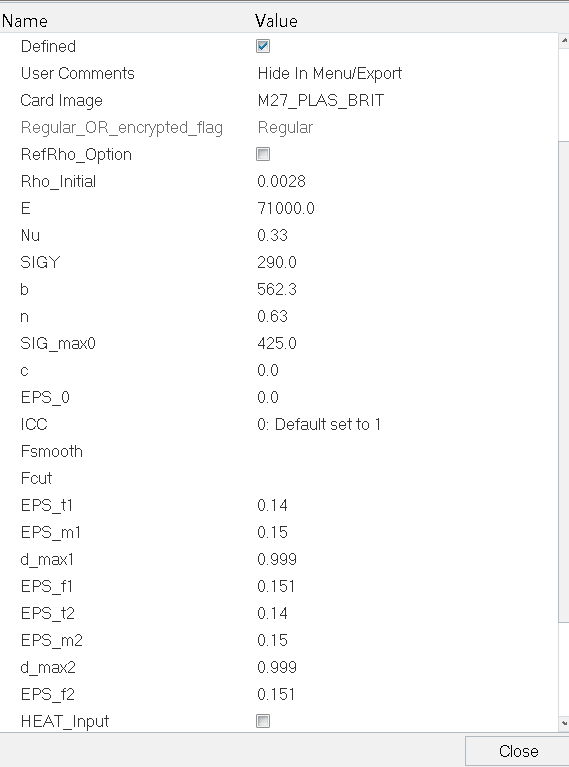
- imported the .h3d file in the Hyperview and .T01 in Hypergraph.
- the animation for vonmesis stress is observed and the graph for internal energy, kinetic energy, contact energy, hourglass energy, total energy are plotted.

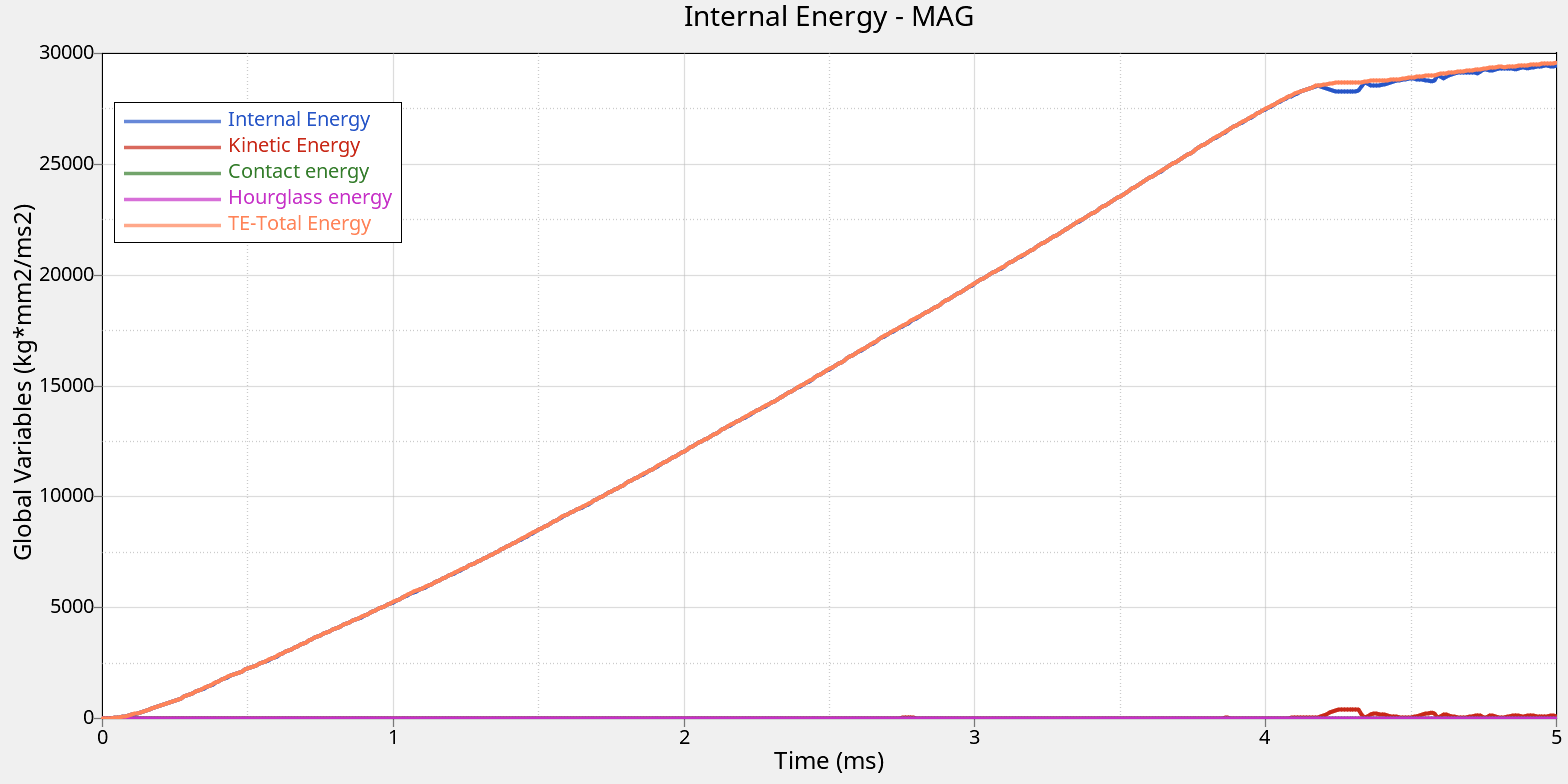
observation:
- the internal energy increases gradually until the material gets rupture.
- comparing the effect of rupturing in material, here the rupture seems to be high.
- the elements which fail get deleted, because of the brittle failure mode eps_t,eps_m,eps_f, and d_max.
- the maximum vonmises stress observed is 2.875E+02 i,e.287.5N/mm^2.
- the number of cycles for the simulation is 49506.
- the energy error ranges from -0.6% to 1.1%.
- there is no amount of mass added to the material, mass error=0.
- the simulation time is 5.010 ms.
- where the internal energy increases gradually until the material gets rupture.
- there is a small peak in kinetic energy at the time of rupture.
- the total energy increases gradually as shown in the plot, approximately follows the same path as the internal energy develops.
- the contact energy and hourglass energy is removed completely.
case7:
- simulation is done with the law-36 PLAST_TAB material card with the input stress strain curve as shown below.
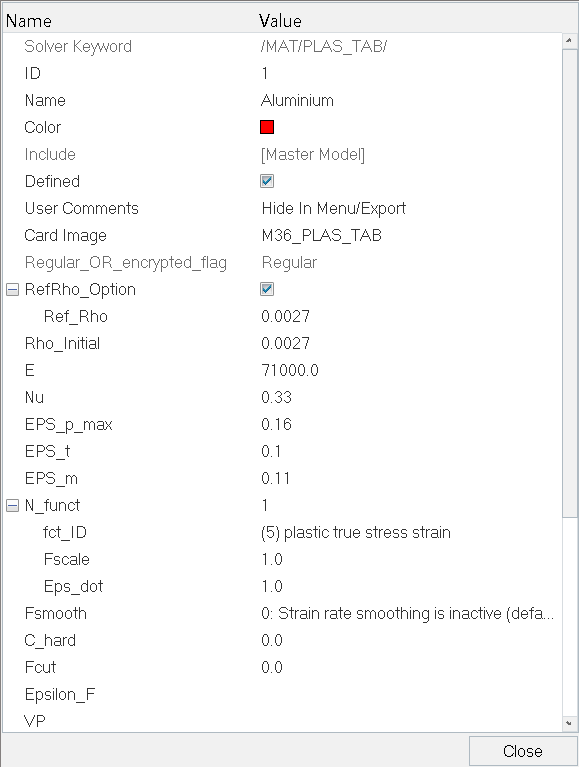
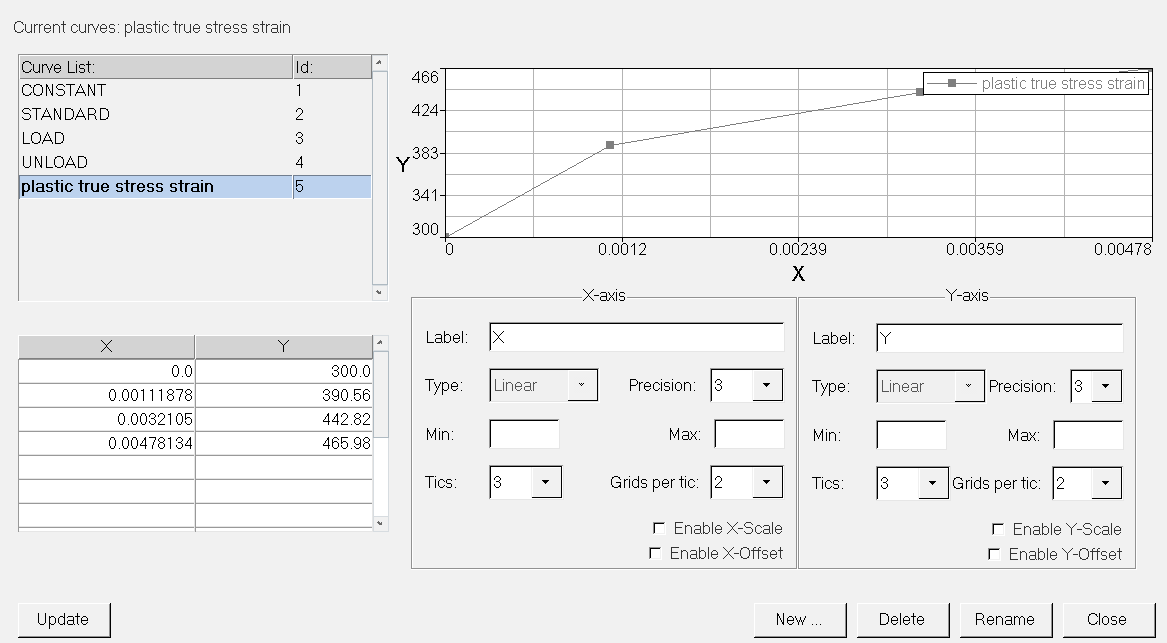
- imported the .h3d file in the Hyperview and .T01 in Hypergraph.
- the animation for vonmesis stress is observed and the graph for internal energy, kinetic energy, contact energy, hourglass energy, total energy are plotted.
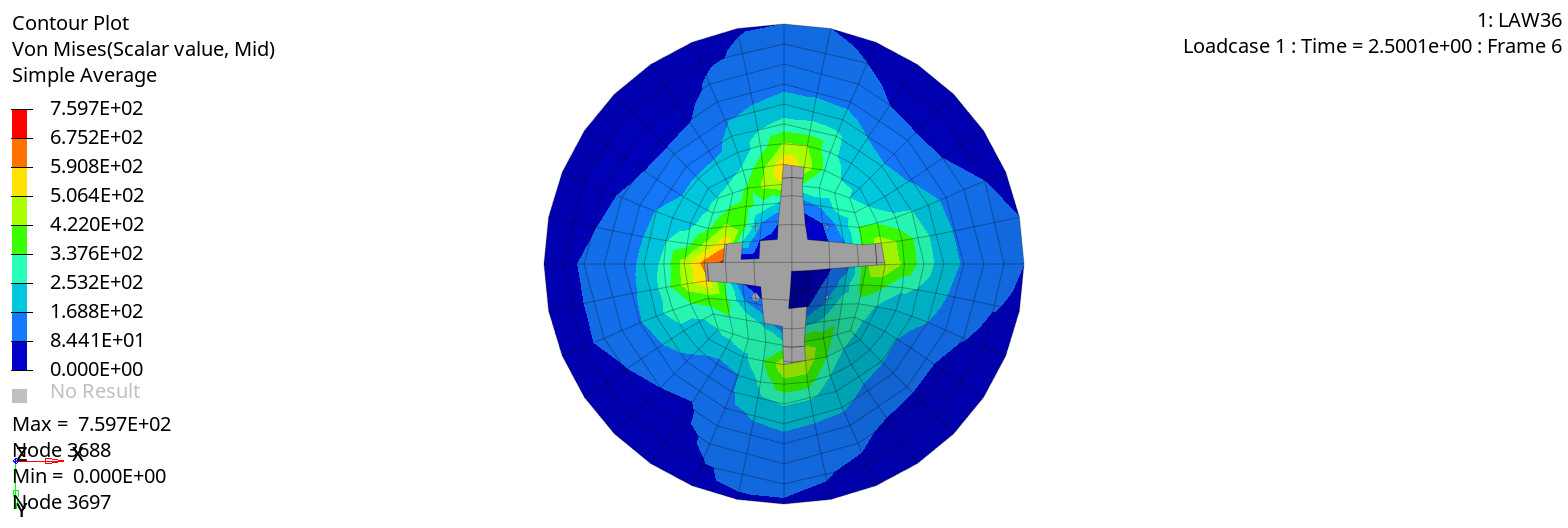
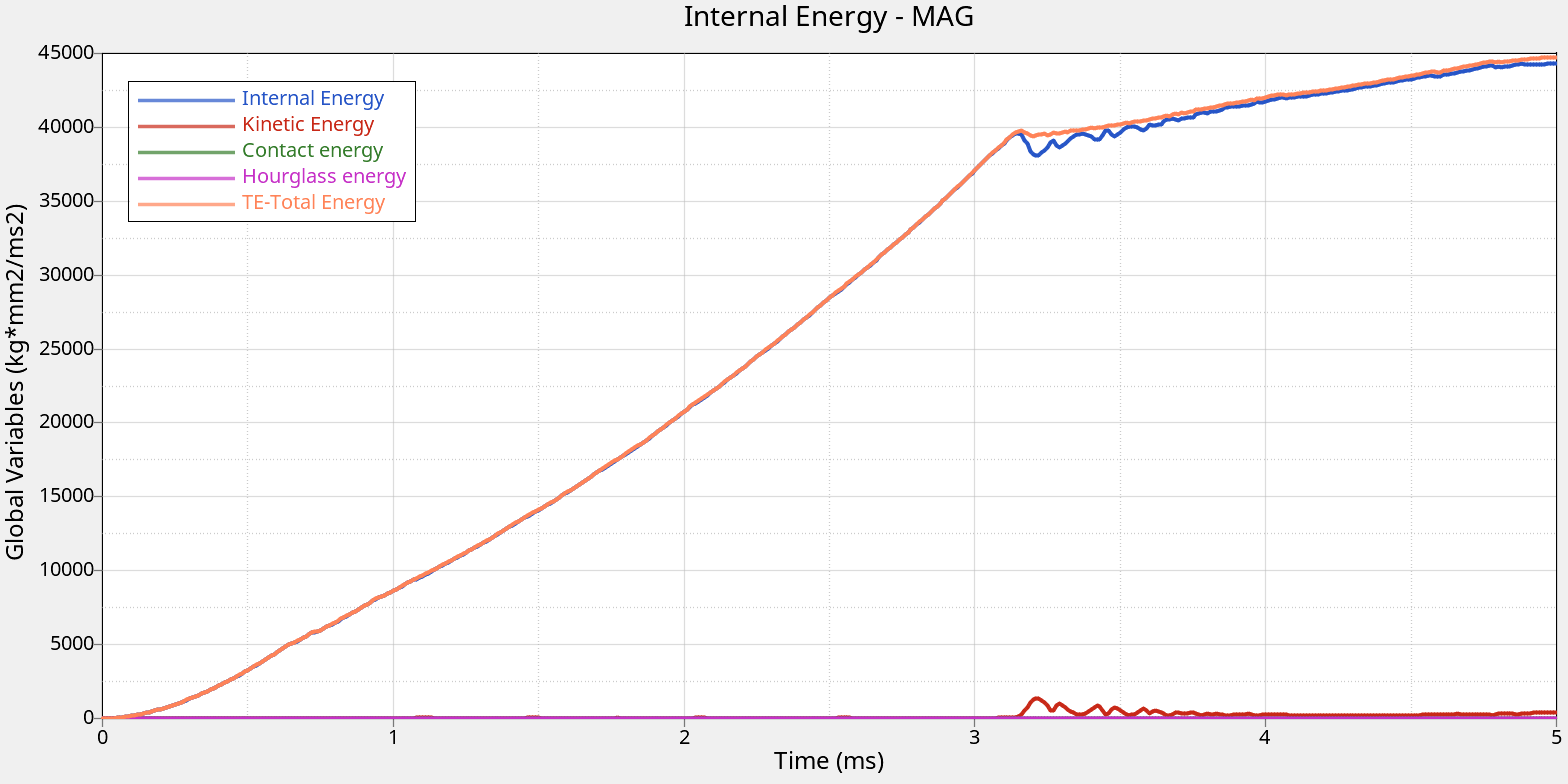
observation:
- here the material seems to be very stiff comparing with before cases.
- the material rupture at 3.5ms
- the maximum vonmises stress observed is 7.597E+02 i,e.759.7N/mm^2.
- the internal energy increases gradually until the material gets rupture.
- the elements which fail get deleted, because of the values eps_t,eps_m,eps_f.
- the number of cycles for the simulation is 53134.
- the energy error ranges from -1.1% to 0.7%.
- there is no amount of mass added to the material, mass error=0.
- the simulation time is 5.010 ms.
- the internal energy increases gradually until the material gets rupture.
- there is a small peak in kinetic energy at the time of rupture.
- the total energy increases gradually as shown in the plot, approximately follows the same path as the internal energy develops.
- the contact energy and hourglass energy is removed completely.
COMPARISION BETWEEN THE CASES:
parameters |
case1-no change in the material card,failure card given |
case2-modifications to the failue card |
case3-without the failure card |
case4-assigning maximum plastic strain value zero |
case5-law1 elastic material card |
case6-law27 PLAST_BRIT material card |
case7-law36 PLAST_TAB material card |
energy error,mass error,simulation time,no.of cycles |
E.E--0.6% to 1.3%
M.E-0
time-5.010ms
no.of cycles-49379
|
E.E--1.1% to 5.9%
M.E-0
time-5.010ms
no.of cycles-49216
|
E.E--0.6% to 1.2%
M.E-0
time-5.010ms
no.of cycles-49407
|
E.E--0.6% to 1.2%
M.E-0
time-5.010ms
no.of cycles-49303
|
E.E--0.6% to 4%
M.E-0
time-5.010ms
no.of cycles-47968
|
E.E--0.6% to 1.1%
M.E-0
time-5.010ms
no.of cycles-49506
|
E.E--1.1% to 0.7%
M.E-0
time-5.010ms
no.of cycles-53134
|
cause for the element failure |
ixfem=0
eps_p_max=0.151
|
ixfem=1
eps_p_max=0.151
|
eps_p_max=0.151 |
ixfem=0
|
NIL |
values of eps_t,eps_m,eps_f,d_max
|
values of eps_t,eps_m,eps_f
|
energy plots |
I.E-increases gradually upto 4ms then stays constant with fluctuations.
K.E-small rise with fluctuations at 4ms
T.E-approx follows the path of I.E
C.E-totally removed
H.E-totally removed
|
I.E-increases gradually upto 4.5ms then stays constant with fluctuations.
K.E-small rise with fluctuations at 4.5ms
T.E-approx follows the path of I.E
C.E-totally removed
H.E-totally removed
|
I.E-increases gradually upto 4ms then stays constant with fluctuations.
K.E-small rise with fluctuations at 4ms
T.E-approx follows the path of I.E
C.E-totally removed
H.E-totally removed
|
I.E-increases gradually throughout the whole simulation
K.E-totally removed
T.E-approx follows the path of I.E
C.E-totally removed
H.E-totally removed
|
I.E-increases gradually with a drop at 5th ms.
K.E-small distrubance at the end
T.E-approx follows the path of I.E
C.E-totally removed
H.E-totally removed
|
I.E-increases gradually upto 4.3ms then turns with fluctuations.
K.E-small rise with fluctuations at 4.3ms
T.E-approx follows the path of I.E
C.E-totally removed
H.E-totally removed
|
I.E-increases gradually upto 3.2ms then turns with fluctuations.
K.E-small rise with fluctuations at 3.2ms.
T.E-approx follows the path of I.E
C.E-totally removed
H.E-totally removed
|
max vonmises stress |
275.2 N/mm^2
|
295.1 N/mm^2
|
270.7 N/mm^2
|
245.1N/mm^2
|
10890 N/mm^2
|
287.5N/mm^2
|
759.7N/mm^2
|
- in energy error perspective, case7 has 1.1% of dissipation and 0.7% of energy addition, in comparing with other cases it has high dissipation and low energy addition.
- in no.of cycles perspective, case5 has 47968 no.of cycles and is the lowest number in comparing with other cases.
- in max vonmises stress perspective, case4 has the stress value of 245.1N/mm^2, is the least value in comparing with other cases.
result:
- So, in confronting the best case on behalf of von mises stress value, case 4 has the best maximum von mises stress value and energy added to the material is 1.2% also within the limit of 5% and it takes 49303 cycles for the simulation, is the third smallest value in comparison with the other cases.
CONCLUSION:
Hence, the run of simulation for all seven cases has been completed, analyzed and derived the best representation of the on-field scenario as case4 successfully.