Aim:
To run crash analysis on the given model by applying different materials laws available in Radioss and post-process the results.
Objective-
1. The Total number of cycles, Energy error, mass error, and simulation time.
2. Notice the animation of all 5 and describe the animations in brief based on whether the elements are being deleted or cracked.
3. Plot energies and notice any difference.
4. Based on all the results, which case would represent the on-field scenario.
5. Prepare a ppt/Docx and list down case by case results and your conclusion as to why the failure happened.
Procedure-
Case 1-
- Open Hyper mesh, go to >> import >> solver deck option >> browse File > Import. The “FAILURE_JOHNSON_0000.rad” file is selected and “imported” as shown below.
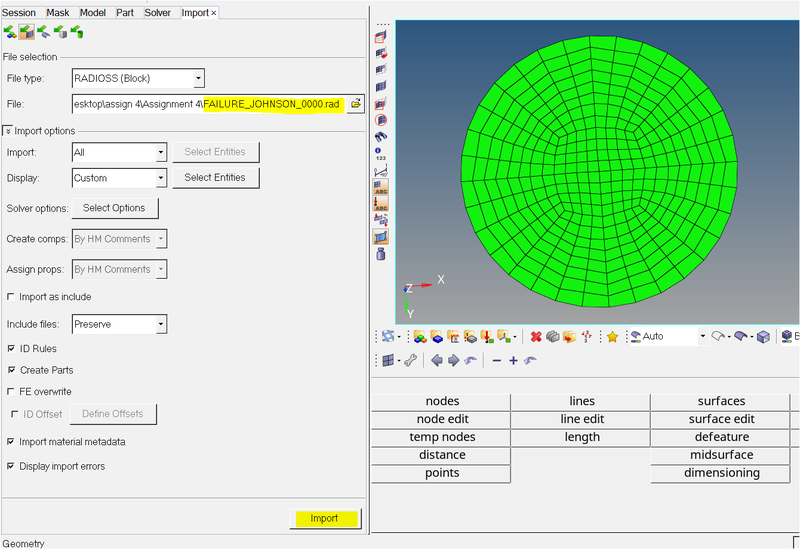
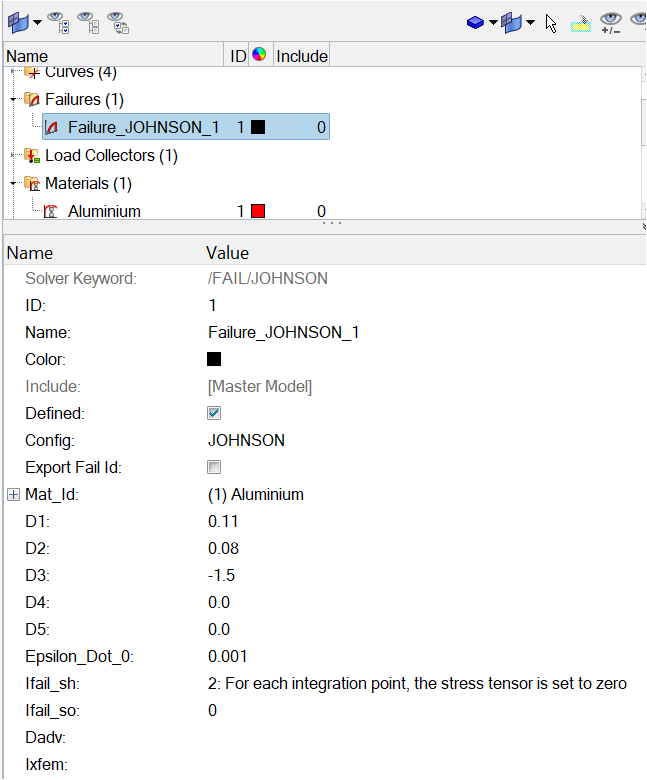
Default Values of Properties, Material, and Failures Cards
- To run the simulation, Go to Analysis >> Radioss. We need to save the output files in a new folder so that we can access them easily. The file is saved as "Law2_epsmax_failure_0000.rad". After saving, tick the 'include connectors' box and type in '-nt 4' in the options text box as shown below, before clicking 'Radioss'
- It is recommended to be written as "-nt 4" as shown in the image below. This means assigning the task to 4 cores in the system, to perform the simulation faster. It depends upon the process of our computer (it has a quad-core processor, then it should be taken as 4. If the system has an octa-core processor, then it is taken as 8). And "nt" means "number of threads". Then click on "Radioss", in order to run the simulation.

- By clicking 'Radioss', we get the solver window as shown below, which basically tells us what the RADIOSS solver is doing. After a few minutes, radios does the job and you can check all the files in the folder which you have saved as.
- The simulation is complete, now we just need to visualize it. For that, we need to switch to the Hyperview utility.
- After accessing Hyperview, we should input the simulation file. For this, use h3d file that was generated when RADIOSS processed the starter file. It is generated in the files swhich are shown in the picture above. After selecting it, we can click 'apply'.
- After accessing Hyperview, we are asked to input the simulation file. For this, we shall be using the h3d file that was generated when RADIOSS processed the starter file (Law2_epsmax_failure.h3d). It should be generated in the same folder. After selecting it, we can click 'apply'. Doing so generates the simulation animation.
- We can change what is being represented by selecting the 'contour' option in the toolbar. In this case, we can change the result type to 'Von Mises' and change the averaging method to simple. Doing so creates the Von Mises stress contours as shown below.
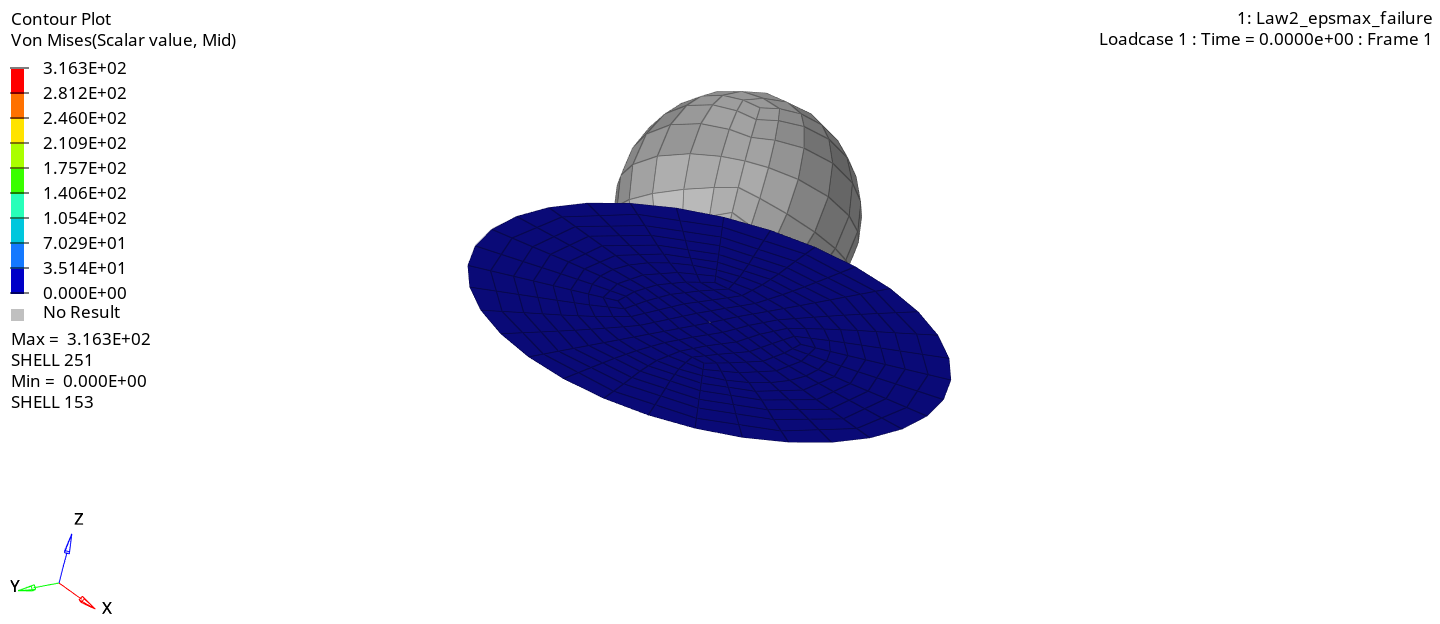
- Next step is to carry out energy error and mass error checks and this is done by analyzing the RADIOSS engine output file. This can be accessed from the same directory as the starter and engine files and is denoted by the '.out' extension. We need to check the file that contains '_0001.out' by using any text editor.
- On opening the file and scrolling down to the end, we can see the final energy and mass error values.
- The final energy error is 0.8%, which is very acceptable. The closer to 0 it is, the better and there is no mass error. Overall, these are very good values.
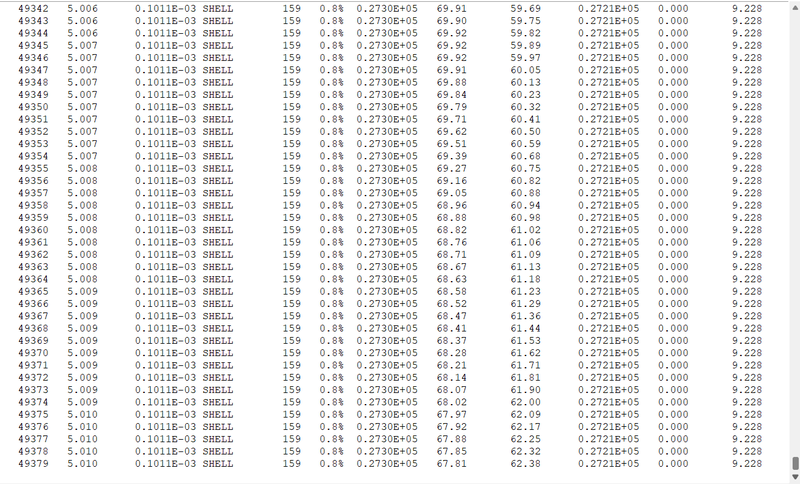

- Now plot the graphs in Hypergraph 2D. We can switch to it using the same client selector option in the toolbar.
- In the Hypergraph section, we need to input a file. For this, we will be using the result file generated by the RADIOSS solver (also known as the 'T01 file'). This file is available in the same directory as the starter, engine, and animation files. The file name ends with 'T01'.
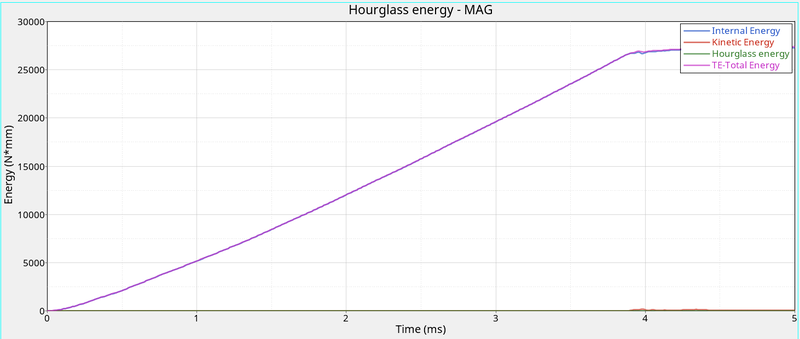
- The above graph shows the internal, kinetic, hourglass and total energy in the simulation. from the graph it can be seen that their is no hourglass energy produced in the simultion, the internal energy increases as time increases this is because of elements absorbing the forces acting on them.
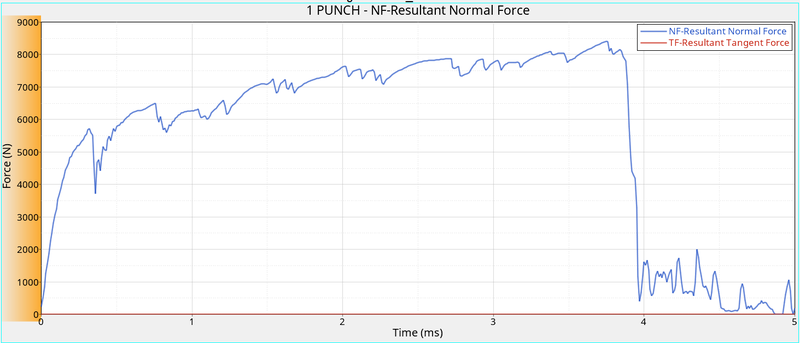
Case 2-
- The process is repeated with slight changes. Just as last time, we import “FAILURE_JOHNSON_0000.rad” via the solver deck.
- This time, we make some changes to the fail/JOHNSON card. It can be accessed via the model tab, under the “Failures” submenu.
- The following values are assigned as shown below (Ifail_sh = 1, Dadv = 1, Ixfem = 1).
- Ifail = 1,which determines the Shell element Failure method. So there are two ways in which we can see the element failing, the element will either get deleted or in some cases the cracking occurs according to the material properties.
- Ixfem: In this, we can choose that if there is any element that is failing we want that element to delete or we want the element to be crack.We are going to take Ixfem=1. Which allow failed element to cracked not to delete.
- Dadv :It gets activated when we have taken Ixfem=1. We are going to takeDadv=1. Which gives the criteria that how much an element can get break into small pieces. If it goes beyond the limit the element gets delete.
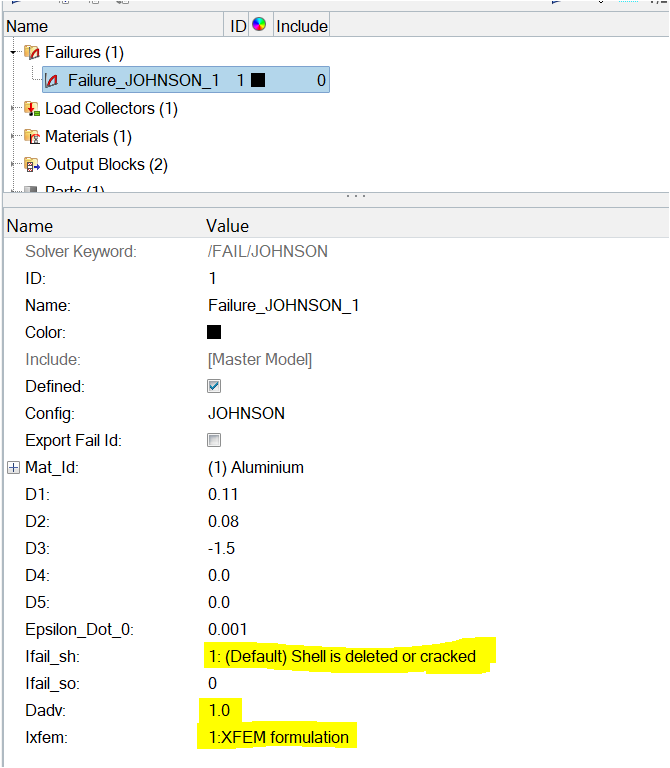
- Now run the analysis and the file is saved as “Law2_epsmax_0000.rad”. With connectors ticked and '-nt 4' typed in the options box, we can click the Radioss button to run the analysis.
- After the solver window completes the analysis, as usual, switch to HyperView window and run the h3d file of the current analysis - Law2_epsmax.h3d and set the Von Mises stress contours:
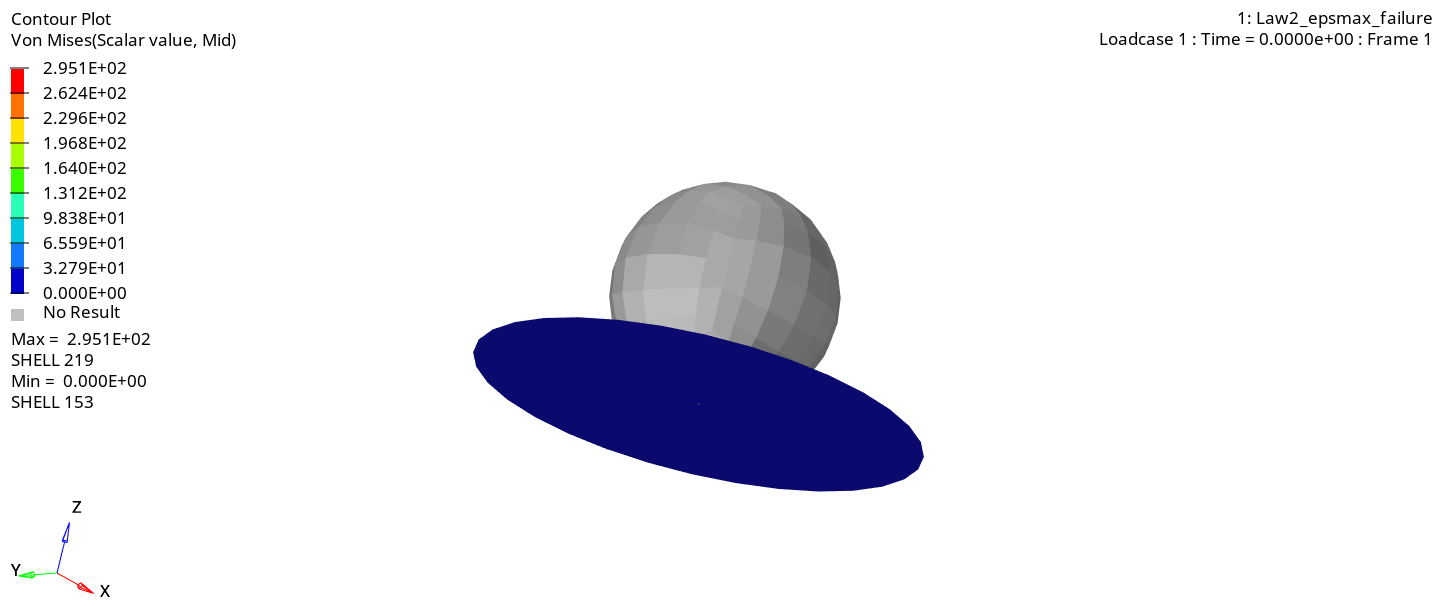
- Now, check the energy and mass error on the RADIOSS output file Law2_epsmax_0001.out
- The energy error is decent enough and is lesser than 5% and mass error is non-existent. We can go ahead and switch to Hypergraph to plot the graphs.
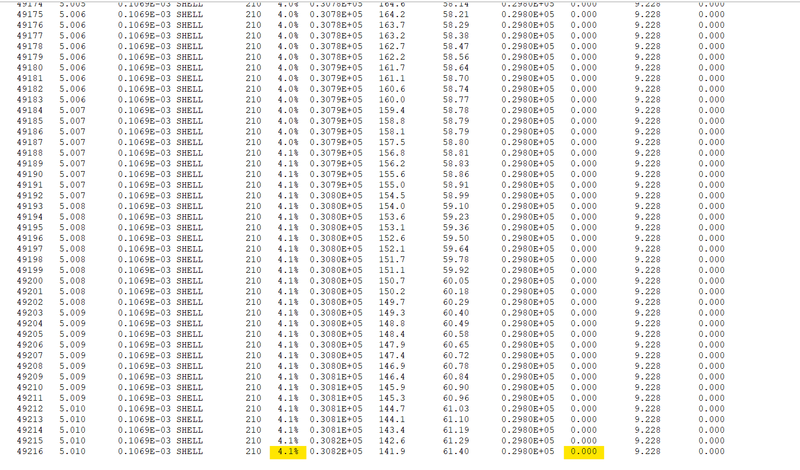

- Now plot the graphs in Hypergraph 2D. We can switch to it using the same client selector option in the toolbar.
- In the Hypergraph section, we need to input a file. For this, we will be using the result file generated by the RADIOSS solver (also known as the 'T01 file'). This file is available in the same directory as the starter, engine, and animation files. The file name ends with 'T01'.
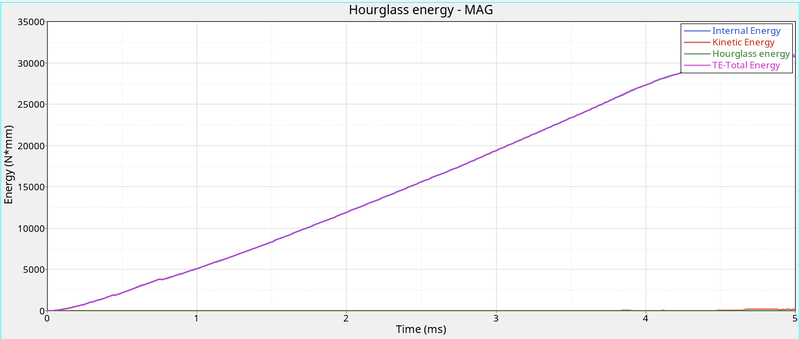
- Hourglass energy in the simulation is zero, the internal energy in the model increses with time similar to both the previous simulations and kinetic and hourglass energies are nearly similar.
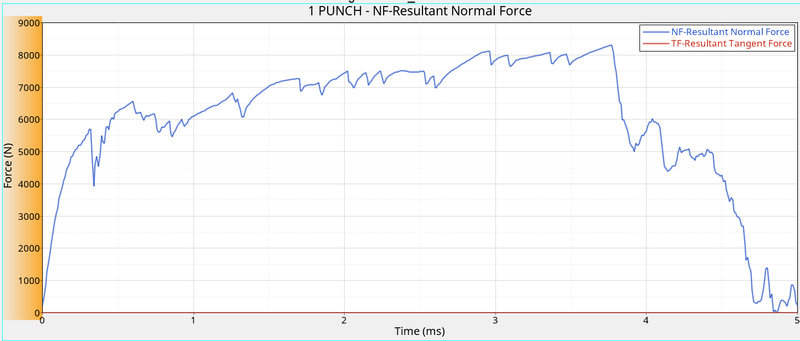
Case 3-
- Again, we need to switch to Hyper works and import the solver deck file “Law2_epsmax_0000.rad”, the starter file created in the previous case.
- In this case delete the fail/JOHNSON card. Go to Failures > Failure_JOHNSON_1.
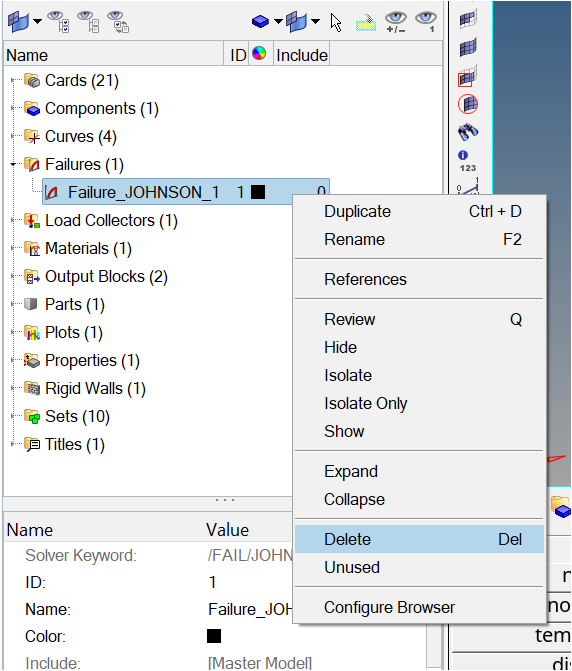
- Now run the analysis and the file is saved as “Law2_epsmax_nofail_0000.rad”. With connectors ticked and '-nt 4' typed in the options box, we can click the Radioss button to run the analysis.
- After the solver window completes the analysis, as usual, switch to HyperView window and run the h3d file of the current analysis - Law2_epsmax_nofail.h3d and set the Von Mises stress contours.
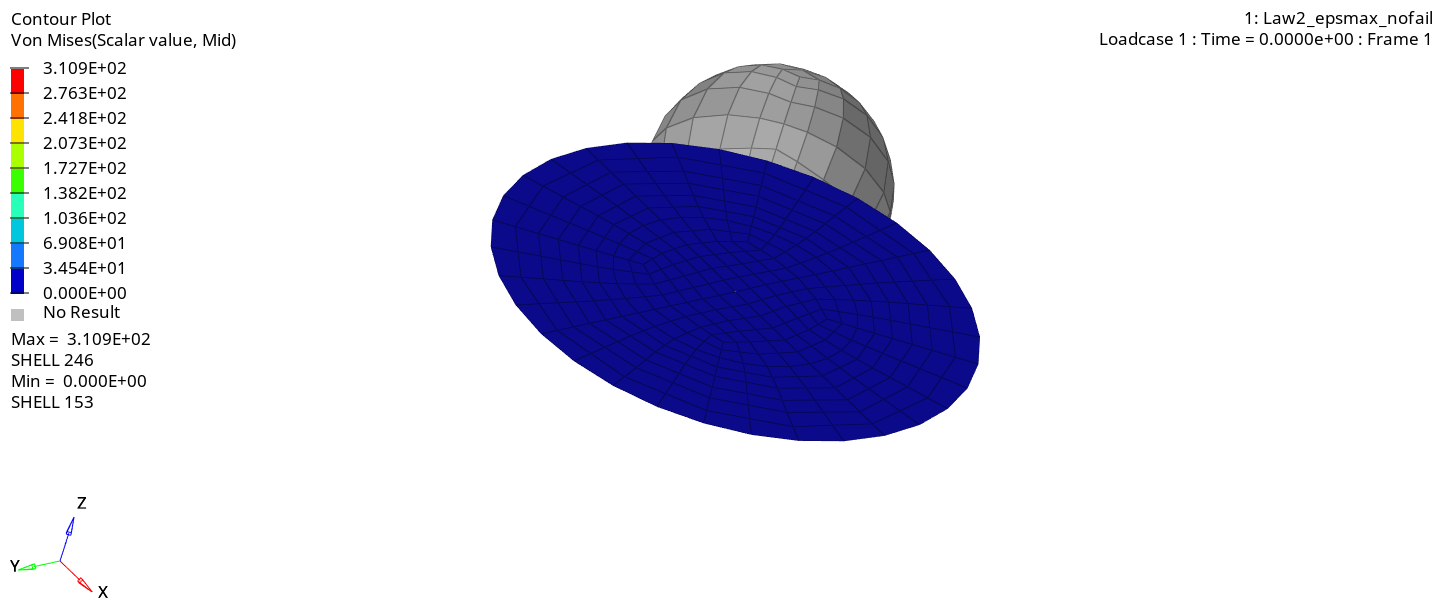
- Now, check the energy and mass error on the RADIOSS output file Law2_epsmax_nofail_0001.out
- The energy error is almost 0.8 and the mass error is non-existent. Now we can switch to Hypergraph to plot the graphs.
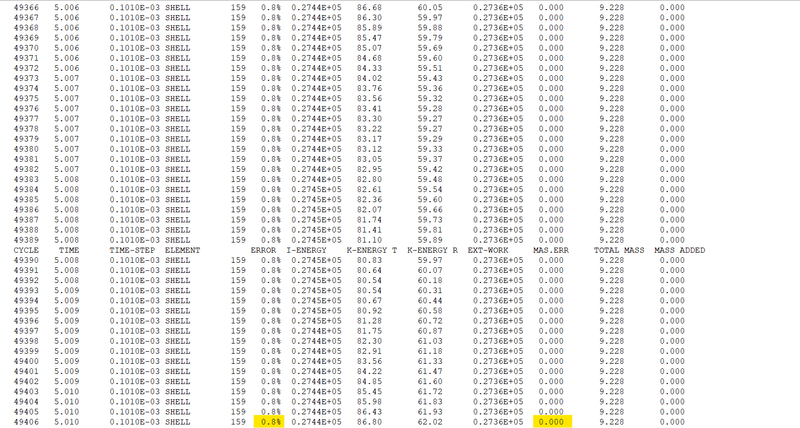

- Now plot the graphs in Hypergraph 2D. We can switch to it using the same client selector option in the toolbar.
- In the Hypergraph section, we need to input a file. For this, we will be using the result file generated by the RADIOSS solver (also known as the 'T01 file'). This file is available in the same directory as the starter, engine, and animation files. The file name ends with 'T01'.
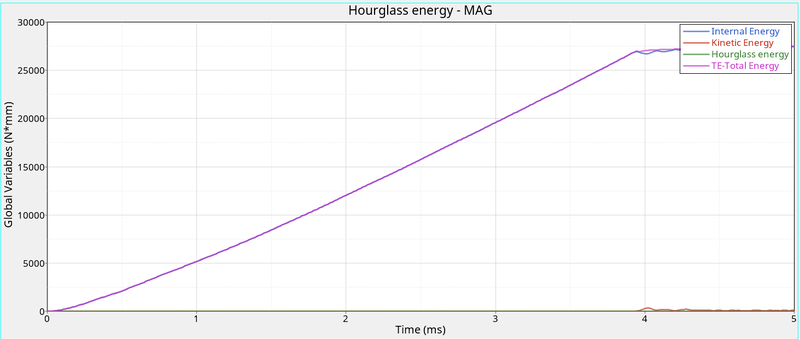
- Hourglass energy in the simulation is almost zero, this is due to QEPH24 element formulation, the internal energy in the model increses with time similar to both the previous simulations.
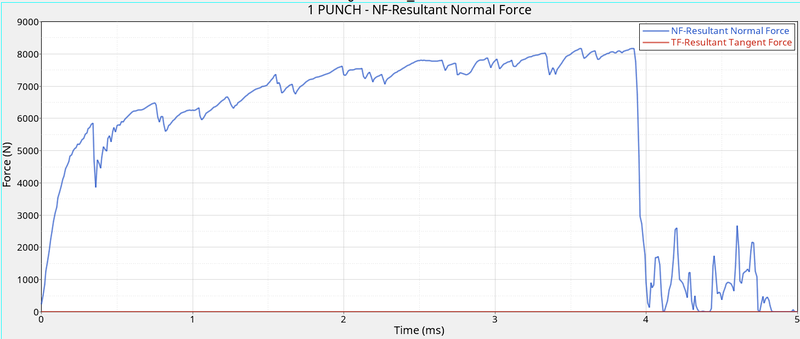
Case 4-
- In this case, import the case 3 starter file - Law2_epsmax_nofail_0000.rad.
- This time, delete the EPS_p_max value (make it as 0). Going to the model tab, we can go to Materials > Aluminium as shown below.
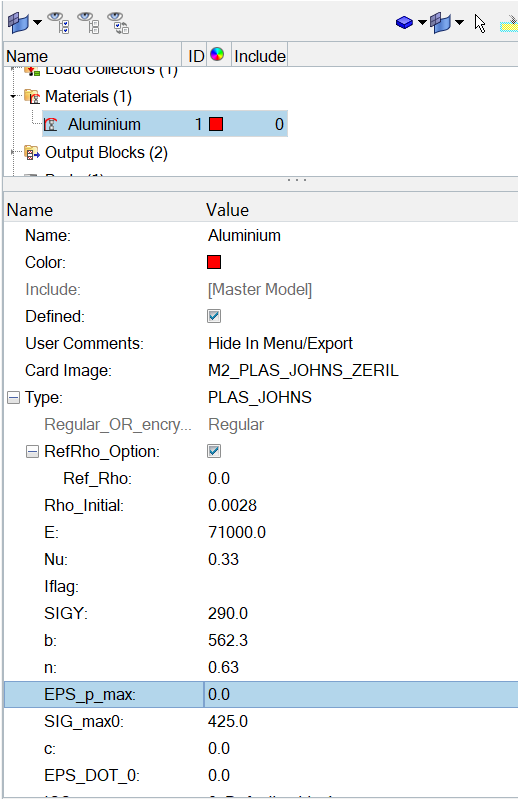
- After that, we can switch to the Radioss analysis section via Analysis > Radioss, save the file as 'Law2_0000.rad', enable connectors and type in '-nt 4' in the options section and run the analysis by clicking 'Radioss'.
- After the solver finishes its analysis, we can switch to Hyperview, run “Law2.h3d”, activate the Von Mises contours and view the simulation.
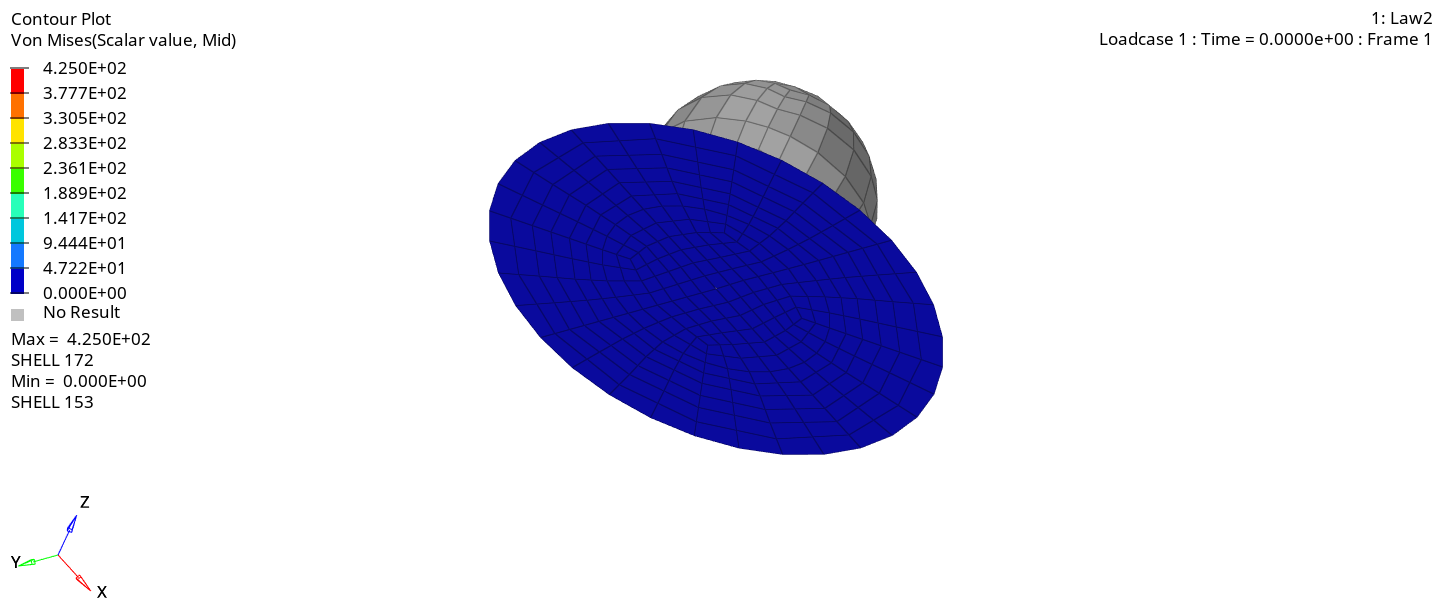
- Now, check the energy and mass errors on “Law2_0001.out”
- The energy error is less than 5% and mass error is non-existent.
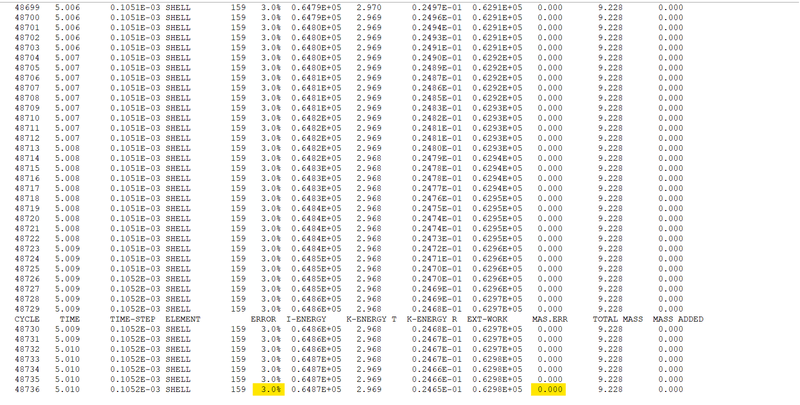

- Now plot the graphs in Hypergraph 2D. We can switch to it using the same client selector option in the toolbar.
- In the Hypergraph section, we need to input a file. For this, we will be using the result file generated by the RADIOSS solver (also known as the 'T01 file'). This file is available in the same directory as the starter, engine, and animation files. The file name ends with 'T01'.
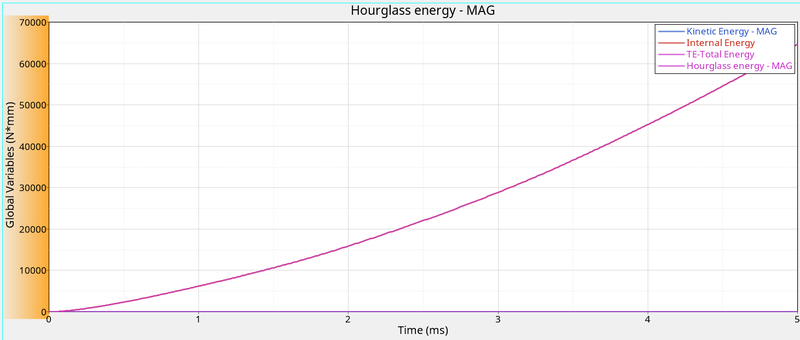
- The above images shows that their is no hourglass energy generated in the simulation and internal energy and total energy of the simulation model intecepts eachother and increases with time.
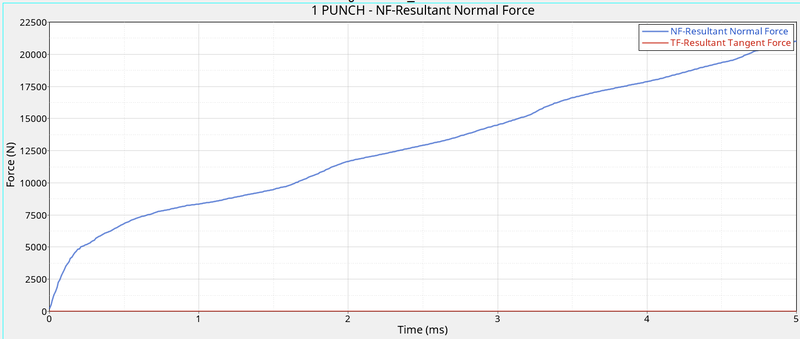
Case 5-
- In this case import the main starter file - FAILURE_JOHNSON_0000.rad.
- After that, go to Materials card > Aluminium and change the card image to M1_ELAST, which is Law 1.
- Also set the values for Rho_Initial, E & Nu as follows:
Rho_initial = 0.0028, E = 71000.00, nu = 0.33.
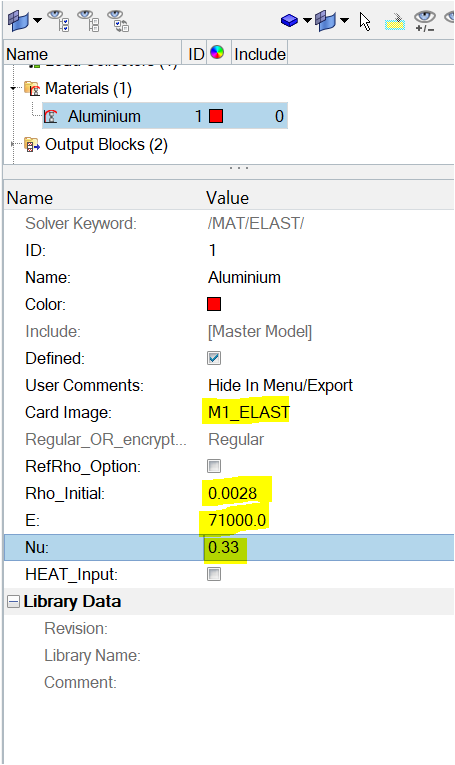
- Now do the analysis and save the file as “Law1_0000.rad”. Just as before, enable connectors and type '-nt 4' in the options box. Then, we can click radioss and let the solver run the analysis.
- After the solver completes the analysis, we can switch to Hyperview, import the 'Law1.h3d' file, enable the Von Mises contours and view the simulation.
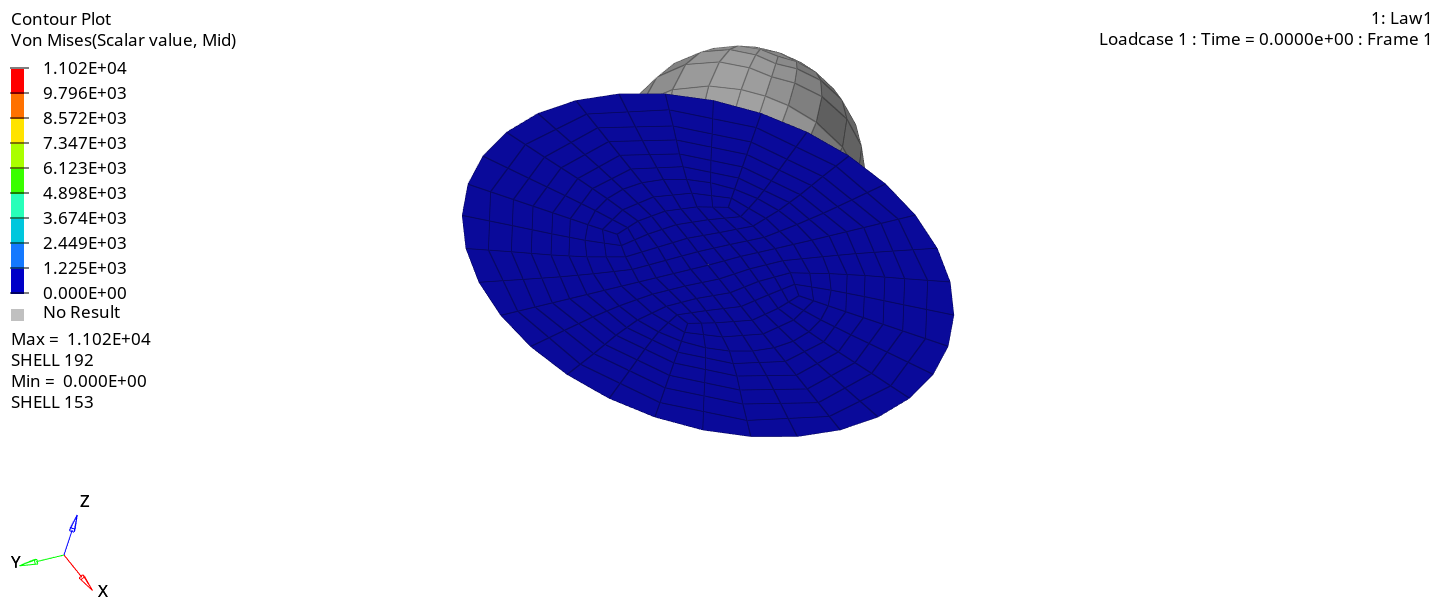
- Now, check the energy and mass error on the RADIOSS output file Law1_0001.out
- The energy error is less than 5% and the mass error is non-existent. We can then switch to Hypergraph to plot the graphs for this simulation.


- Now plot the graphs in Hypergraph 2D. We can switch to it using the same client selector option in the toolbar.
- In the Hypergraph section, we need to input a file. For this, we will be using the result file generated by the RADIOSS solver (also known as the 'T01 file'). This file is available in the same directory as the starter, engine, and animation files. The file name ends with 'T01'.
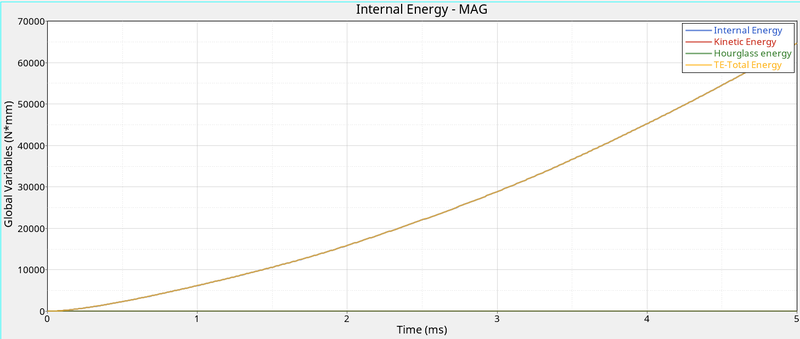
- No hourglass energy generated in the simulation and internal energy and total energy of the simulation model intecepts each-other and increases exponentially with time.
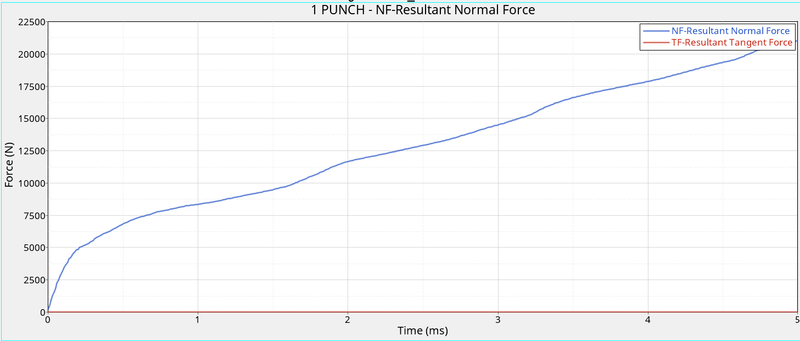
Case 6-
In this case, import the 'Law2_epsmax_failure_0000.rad' file.
- We need to use recommended shell properties in this case & to change the material property to 36 material card and we will keep rest properties as given below,
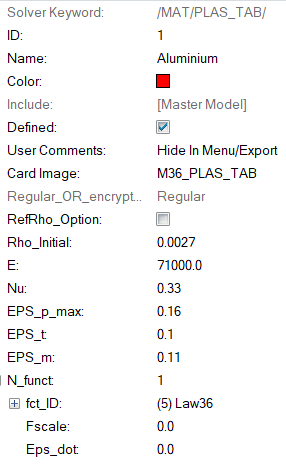
- Now do the analysis and save the file as “Law_36_0000.rad”. Just as before, enable connectors and type '-nt 4' in the options box. Then, we can click radioss and let the solver run the analysis.
- After the solver completes the analysis, we can switch to Hyperview, import the 'Law_36.h3d' file, enable the Von Mises contours and view the simulation.
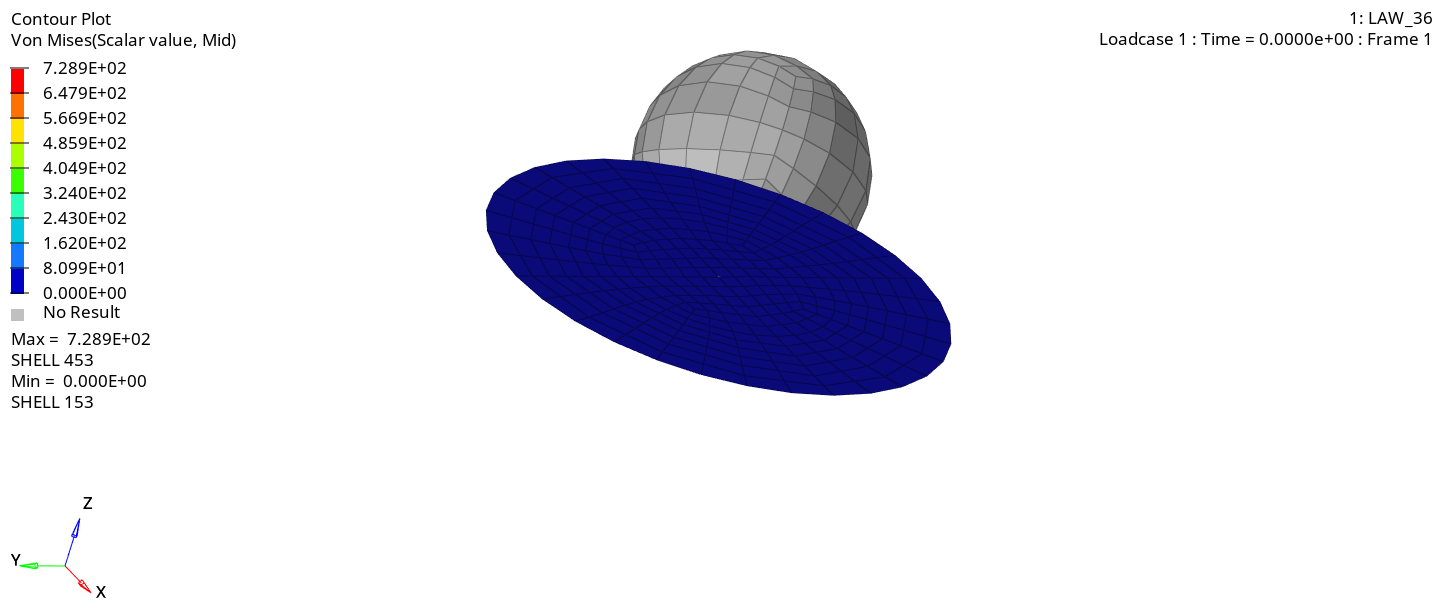
- Now, check the energy and mass error on the RADIOSS output file Law_36_0001.out
- The energy error is less than 5% and the mass error is non-existent. We can then switch to Hypergraph to plot the graphs for this simulation.
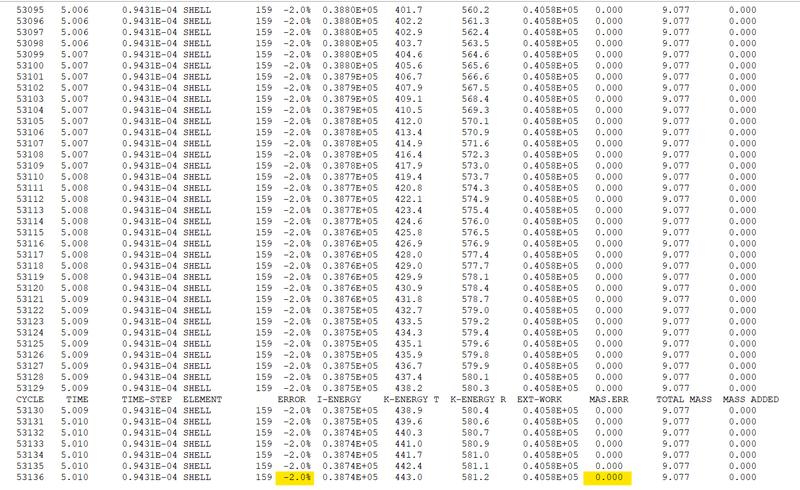
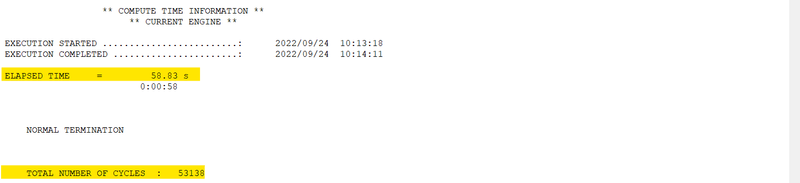
- Now plot the graphs in Hypergraph 2D. We can switch to it using the same client selector option in the toolbar.
- In the Hypergraph section, we need to input a file. For this, we will be using the result file generated by the RADIOSS solver (also known as the 'T01 file'). This file is available in the same directory as the starter, engine, and animation files. The file name ends with 'T01'.
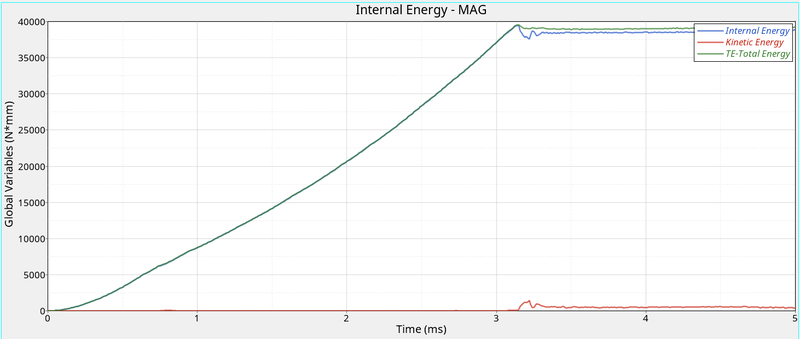
- Their is no hourglass energy generated in the simulation model, the internal energy increases with time as seen in the image.
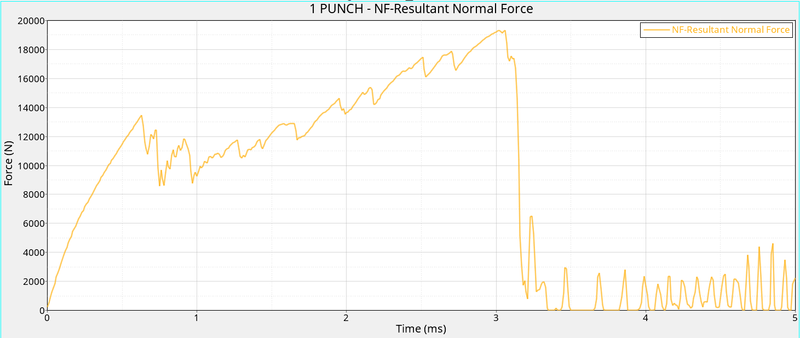
Case 7
- Open the Law27_0000.rad file and perform the simulation with the law 27 material card. Use the recommended shell properties.
- This law combines johnson cook material with the brittle failure method, this law is applicable only for shell elements.
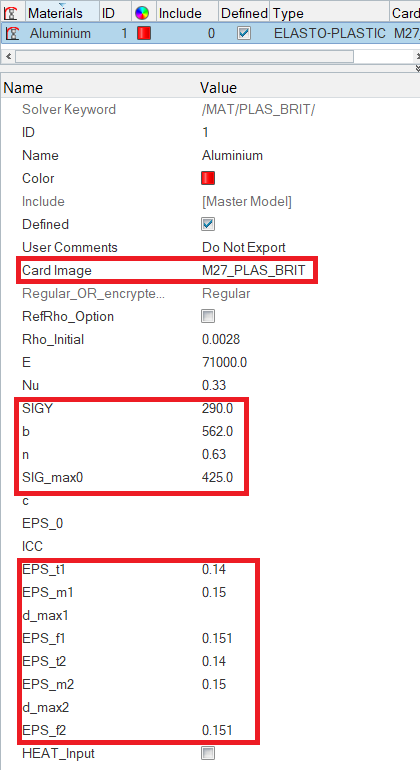
- Now, run the analysis via the Radioss tool. This time, we can save the file as 'Law27_0000.rad'. Just as before, we can enable connectors and type '-nt 4' in the options box. Then, we can click radioss and let the solver run the analysis.
- After it's done, we can generate the simulation via Hyperview with the Von Mises contours enabled as shown.
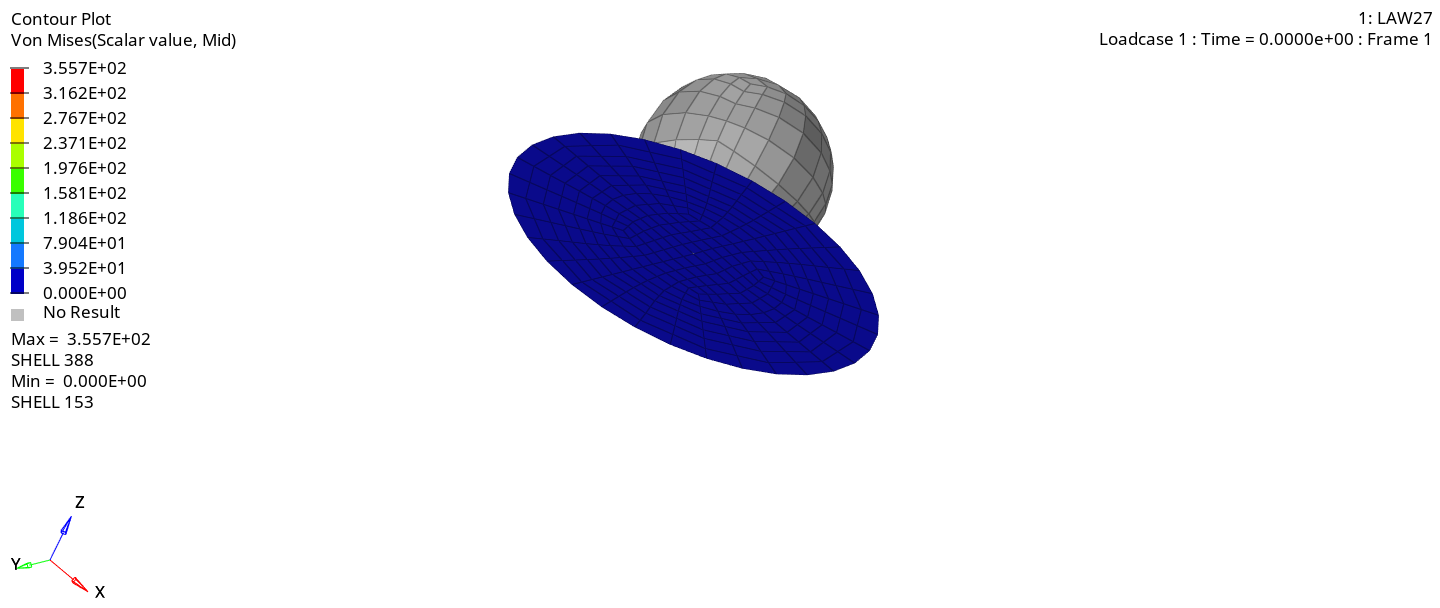
- we can check the energy and mass errors on “Law27_0001.out”
- The energy error is -7.1% and the mass error is non-existent.
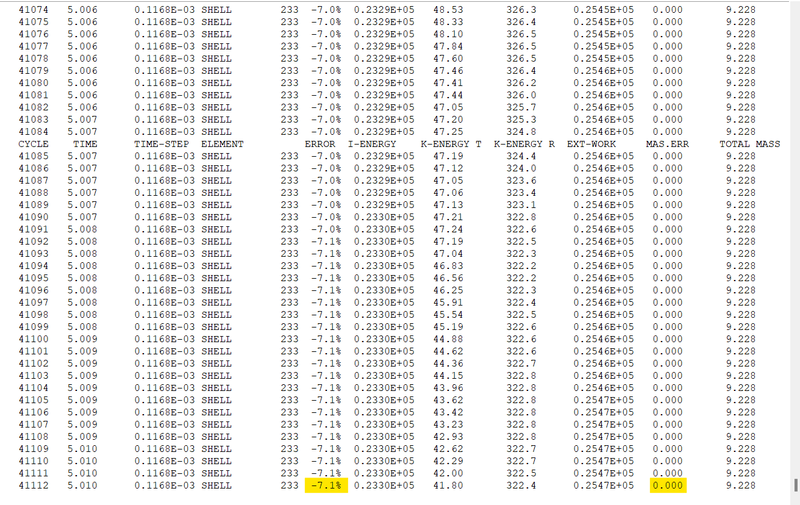
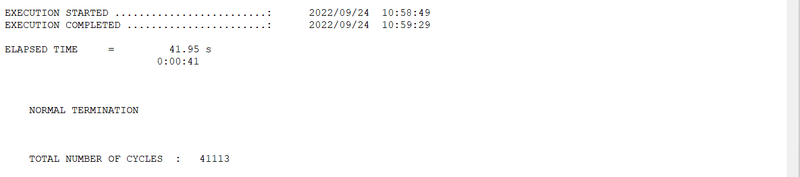
- Now plot the graphs in Hypergraph 2D. We can switch to it using the same client selector option in the toolbar.
- In the Hypergraph section, we need to input a file. For this, we will be using the result file generated by the RADIOSS solver (also known as the 'T01 file'). This file is available in the same directory as the starter, engine, and animation files. The file name ends with 'T01'.
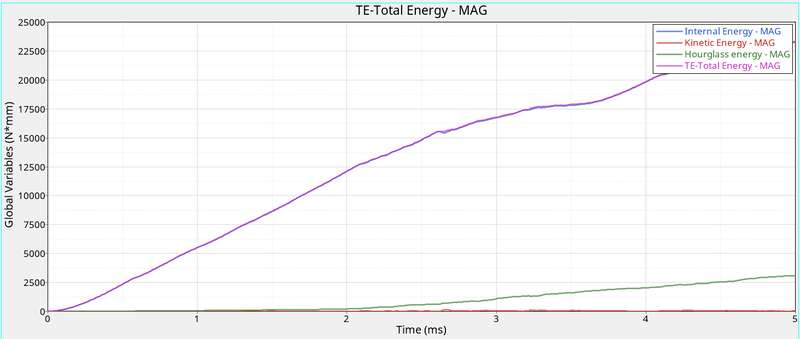
- Their is hourglass energy generated in the simulation model, the internal energy increases with time as seen in the image, also it shows the brittle behaviour.
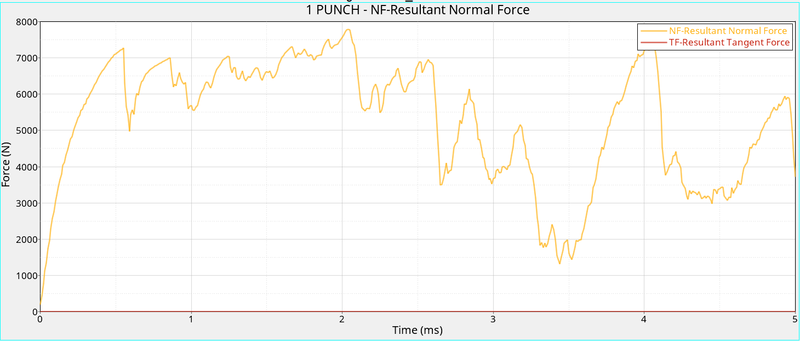
Result-
Case
|
Material law
|
Simulation name
|
Energy error (%)
|
Simulation time (s)
|
Number of cycles
|
Maximum stress value (MPa)
|
Element behaviour
|
1
|
Law 2 (Johnson-Cook model)
|
LAW2_max_failure
|
0.8
|
50.08
|
49380
|
316.3
|
Deleted
|
2
|
Law 2 (Johnson-Cook model)
|
LAW2_max_failure_1
|
4.1
|
51.83
|
49217
|
295.1
|
Cracks first then deleted
|
3
|
Law 2 (Johnson-Cook model)
|
LAW2_max_nofail
|
0.8
|
55.55
|
49408
|
310.9
|
Deleted
|
4
|
Law 2 (Johnson-Cook model)
|
Law 2
|
3.0
|
54.58
|
48737
|
425
|
Preserved
|
5
|
Law 1 (linear elastic material)
|
Law 1
|
1.3
|
55.47
|
47969
|
11020
|
Preserved
|
6
|
Law 36 (elasto-plastic material)
|
Law 36
|
-2.0
|
58.83
|
53138
|
728.9
|
Deleted
|
7
|
Law 27 (brittle failure model)
|
Law 27
|
-7.1
|
41.95
|
41113
|
355.7
|
Deleted
|
- Based on the observation of results: case 2 presents the best on-field scenario in the simulation.
Conclusion:
Selecting a correct material model plays a very important role in simulation. Selecting the wrong material model and doing simulation will also give result but it will not represent the actual situation.
Law 1 is used to model purely elastic materials or materials that remain in the elastic range. To model this we require Poisson's ratio and Young's modulus. This law represents a linear relationship between stress and strain.
Law 2: In this law, the material behaves as linear elastic when equivalent stress is lower than the yield stress. For a higher value of stress, the material behaves like plastic. Failure can be captured better with the help of an optional Fail_Johnson card.
Law 27: Used for brittle materials.
Law 36: The elastic-plastic behavior of isotropic material is modeled with user-defined functions. The stress-strain curve is modeled using E and Poisson's ratio. Therefore, it is the best card because we cannot know the exact failing condition of the material in the other cases, but we can define the stress-strain curve, and then we can decide where the material is failing.